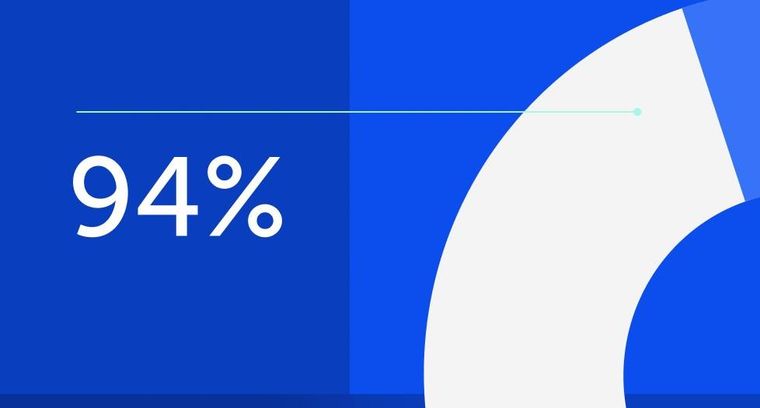
94% of researchers rate our articles as excellent or good
Learn more about the work of our research integrity team to safeguard the quality of each article we publish.
Find out more
ORIGINAL RESEARCH article
Front. Mech. Eng., 31 March 2025
Sec. Vibration Systems
Volume 11 - 2025 | https://doi.org/10.3389/fmech.2025.1553759
This article is part of the Research TopicRecent Advances in Mechanical Design and VibrationView all articles
This article presents experimental results on the algebraic identification of the magnitude and phase angle of unbalance in a rotor-bearing system in a Jeffcott configuration. The algebraic identifier is designed based on a simplified mathematical model of the system and it uses only the measurement of the lateral vibration amplitude of the rotor. The proposed algebraic identifier is first validated by numerical simulation. For experimental implementation, a SpectraQuest Machinery Fault and Rotor Dynamics Simulator is used. The designed identifier is evaluated in two scenarios. In the first, the rotor-bearing system is balanced using the traditional coefficients of influence method, after which a known unbalance is induced and compared with the identified magnitude and phase values. In the second case, the unbalance magnitude and phase values obtained by the algebraic identifier from an unknown original unbalanced configuration are used to balance the rotor-bearing system. The vibration amplitude reduction is quantified to evaluate the identified values. The main contribution of this work is the discussion of practical aspects that cannot be appreciated in simulation, but must be considered in the experimental implementation of the algebraic identification method, as they can limit the performance of the designed identifiers.
Unbalance is an inherent phenomenon in rotating machinery and is one of the most common vibration sources in turbomachines. Rotor unbalancing is caused by an asymmetric mass distribution, which can result from many diverse factors: manufacturing imperfections, design tolerances, non-homogenous materials, thermal distortion, eccentricity, geometrical discontinuities, corrosion, or wear (Muszynska, 2005; Novillo, 2022; Subbiah and Littleton, 2018). Unbalance occurs when the center of rotation and the center of gravity of the rotor are not coincident. In this case, unbalance is modeled as a concentrated mass located at a certain distance from the center of rotation (called eccentricity). The product of these parameters (mass and eccentricity) is known as the unbalance magnitude, and the angular location of the unbalance mass relative to a reference system provides the unbalance phase angle. Knowledge of unbalance parameters is necessary to apply balancing methods to attenuate vibration amplitudes during operation of rotating machinery (Li et al., 2021; Schneider, 2023), but also to create more accurate models to analyze and predict the dynamic behavior of rotating systems (Bera et al., 2023; Lalanne and Ferraris, 1998; Tiwari, 2018).
In recent years, unbalance identification has been a very active area of rotordynamics research. Mao et al. (2016) proposed an indirect method for identifying unbalance parameters. The authors considered the eccentricity parameter as known, and the identification of the mass and phase angle is formulated as the unbalance force reconstruction problem. First, the unbalance force is reconstructed from the transient system response, and then the unbalance mass and phase angle are identified from the unbalance force reconstruction. The proposed method is evaluated numerically and experimentally. In the test rig, the identified unbalance parameters were used for balancing the rotor system, achieving a vibration attenuation of about
On the other hand, the algebraic identification method has been recently explored in rotordynamics. Mendoza-Larios et al. (2021) used the algebraic identification approach to estimate the stiffness and damping rotordynamic coefficients in a rotor-bearing system under the assumption that the elasticity and dissipative forces are linear. The proposed identifiers are validated only numerically in two scenarios, constant and variable rotational speed of the rotor-bearing system. The simulation results indicate fast convergence in the identification of stiffness and damping parameters, taking less than
As can be noted, the algebraic identification method has been widely used for parameters estimation in rotordynamics. This is mainly due to its advantages over other methods: robustness against structured perturbations and noise, high convergence velocity, and it does not require the classical “persistency of excitation condition” (Fliess and Sira-Ramírez, 2003; Sira-Ramírez et al., 2014; Trapero et al., 2008). These properties have been extensively proven by numerical simulation in rotor-bearing systems. Baltazar-Tadeo et al. (2024) showed through numerical simulations that the algebraic identification method is sensitive to noise in vibration signals obtained from rotordynamic systems, and the parameters identified by this approach can be strongly affected by the presence of high levels of noise; therefore, the use of filtering techniques is recommended. Moreover, to the knowledge of the authors, experimental implementation of algebraic identification in real rotordynamic systems has not yet been carried out.
In this work, the experimental implementation of the algebraic identification of magnitude and phase of unbalance in a rotor-bearing system in a Jeffcott configuration is presented. The algebraic identifier is designed based on a two-degree-of-freedom system model and requires only the measurement of the lateral vibration amplitude of the rotor. The proposed algebraic identifier is numerically validated by considering two different operating conditions: constant and variable rotational velocity. After that, a SpectraQuest Machinery Fault and Rotor Dynamics Simulator is used for the experimental implementation of the algebraic identifier. For this case, the identifier is evaluated in two scenarios. Firstly, the rotor-bearing system is balanced using the traditional coefficients of influence method, and then a known unbalance is induced, with the identified balance (magnitude and phase) compared to this. In the second case, the rotor-bearing system starts in an unknown unbalanced condition, and the unbalance magnitude and phase values obtained by the algebraic identifier are used to balance the rotor-bearing system. The vibration amplitude reduction is quantified to evaluate the identified values. Finally, important remarks on practical aspects about experimental implementation of algebraic identifier are provided.
Algebraic identification is a model-based method, and the classical Jeffcott rotor model is used to develop the identifier for the unbalance parameters. Different approaches have been proposed for Jeffcott rotor modeling (Friswell et al., 2010; Subbiah and Littleton, 2018; Tiwari, 2018; Vance et al., 2010), but all of them agrees on the idea of a disk with an unbalanced mass at a certain distance (eccentricity) from the geometrical center, as shown in Figure 1, where
where
For the development of the algebraic identifier, the time-domain methodology explained by Sira-Ramírez et al. (2014) is followed.
First, both sides of Equations 1, 2 are multiplied by
After that, the obtained Equations 3, 4 are integrated with respect to
To solve Equations 5, 6, the four terms from each equation are separated and solved individually as it is shown in Equations 7-14.
The integration by parts method is used to integrate the three terms on the left side of Equation 5, resulting in
In an analogous manner, for Equation 6, we have
For the right-side term in Equation 5, the integration by parts method is applied by considering
In a similar way, for the right side on Equation 6, we use
Finally, the global solutions for Equations 5, 6 are
Regrouping and renaming terms as
Equations 15, 16 can be rewritten as
The linear Equation 23 can be solved using the Cramer’s rule (Strang, 2023) to obtain
From the obtained values in Equations 24, 25, magnitude
As can be appreciated in Equations 15–27, the algebraic identifier developed to estimate the unbalance parameters is in terms of
In order to prove the algebraic identifier’s performance by simulation, the rotor-system dynamics given by Equations 1, 2 were numerically solved using Matlab-Simulink with the numerical parameters presented in Table 1. The obtained lateral vibration system response is shown in Figure 2. As can be observed, the amplitudes on the
Results for the identification of unbalance magnitude and phase angle at constant rotational velocity are shown in Figure 4. As can be observed, the identified unbalance parameters rapidly converge to the values considered for simulation in Table 1. It is important to note the high resolution on the vertical scale in both figures, which allows for the precision of the calculated values to be appreciated.
Numerical simulations were carried out at variable rotational velocity of the rotor-bearing system to prove the algebraic identifier’s performance for this operating condition. In this case, a ramp velocity with an angular acceleration of
For experimental implementation of the proposed algebraic identifier, the SpectraQuest Machinery Fault and Rotor Dynamics Simulator shown in Figure 7 was used. Vibration amplitudes were measured by two Eddy current proximity probes (1) by SpectraQuest, located perpendicularly to each other, and the measuring kit includes a signal conditioner (2) that transduces displacement into a voltage signal. A DAQ 6024E data acquisition card by National Instruments (3) was used to acquire the proximity probe signals. The acquired data are processed in Matlab Simulink (4) software to be used in the experimental validation of the algebraic identifier. Finally, an infrared sensor was utilized to generate a pulsing signal to be used as a reference to measure the phase of the proximity probe signals.
Mass, damping and stiffness parameters given in Table 1 were experimentally estimated. The mass of the rotor-bearing system
where
For damping
and
The damping ratio
where
From Figure 8, we can obtain the following values:
The equivalent stiffness coefficient can be obtained from the natural frequency definition (Rao, 2017) given in Equation 31.
and substituting the mass and natural frequency values:
Finally, the equivalent damping coefficient is obtained from the critical damping
Once the rotor-bearing system has been characterized, the proposed algebraic identifier is experimentally proven for two cases. In the first, the rotor-bearing system is balanced, and then a known unbalance is induced. In the second scenario, the algebraic identifier is used to estimate the unbalance parameters of an unknown unbalanced condition, and the identified parameters are used to balance the rotor-bearing system.
The rotor-bearing system was balanced using the well-known influence coefficients method (Bently and Hatch, 2002; Lees, 2016). It is important to mention that this method requires a reference signal to measure the phase angle, which was obtained from the infrared sensor mentioned in the previous section. This reference signal is also used to measure the unbalance phase angle estimated by the algebraic identifier.
From this balanced condition, a heavy spot was induced. For the first case, an unbalance mass
As can be appreciated, the unbalance parameter values do not converge to any value. This is mainly because the influence of noise in the acquired data from the proximity probes. Some digital filtering techniques were applied to the raw signals; however, the identifier performance could not be improved because digital filters induce delays in the filtered signals. This characteristic affects the phase angle of the acquired signals and, as a consequence, the identifier’s performance. Results of the identified values with filtered signals are included as Supplementary Material. Experimental filtered signals used as input to the algebraic identifier are presented in Supplementary Figures S1, S2, and the obtained results for the identified values of the unbalance parameters are shown in Supplementary Figures S3, S4.
As a solution for this problem, we propose a signal reconstruction procedure to obtain the system response free of noise and without any delay that could affect the identifier’s performance. Firstly, the raw signals are filtered. Then, amplitude, frequency and phase angle of the signals are obtained by analyzing the first two cycles, since according to Baltazar-Tadeo et al. (2023), the unbalance parameters can be obtained with the algebraic approach using just a small fraction of the system response. The reconstructed signals of the rotor-bearing system response are presented in Figure 11. These data were used as input for the algebraic identifier, and the corresponding identified values for unbalance magnitude and phase angle are shown in Figure 12.
The identified unbalance parameter values converge rapidly (in
This value is compared with the induced unbalance mass
The obtained differences may be due to various factors, such as the residual unbalance after the rotor balancing by the influence coefficient method (the rotor cannot be perfectly balanced), the consideration of a simplified symmetric mathematical model when the obtained experimental system response is asymmetric, a possible shaft runout, and other unmodeled dynamics. Moreover, it was not possible to obtain balancing masses with the exact calculated values, and only approximated values were used.
More experimental tests were carried out with the same unbalance mass at different angular locations, following the procedure for the system response signals reconstruction. The obtained results for the identified unbalance mass and phase angle are summarized in Table 2. These values were used for rotor balancing by locating a similar mass 180° from the identified value for the unbalance phase angle. In Table 3 the balancing mass and angular location as well as the vibration attenuation percentages for each experimental test, are presented. Graphical results for vibration amplitude attenuation in the case of the first row in Table 3 are shown in Figure 13 for x and y-axes. It is important to mention that all the signals in Figure 13 were digitally filtered to improve visualization and comparison, as well as to facilitate the quantification of vibration attenuation.
For the second scenario, all the trim, balancing and unbalance masses were removed from the disk of the rotor-bearing system. From this original unbalanced condition, the vibration system response was obtained, and following the reconstruction signal procedure described in the previous section, the unbalance parameters were estimated by the proposed algebraic identifier. The resulting balancing parameters were: a balancing mass of
In this article, an identifier for the unbalance parameters of a Jeffcott-like rotor-bearing system based on the algebraic method was developed. A simplified mathematical model for the rotor-bearing system and Matlab Simulink software were employed to design and numerically prove the proposed identifier, finding a rapid convergence of the estimated parameters to the correct values. In experimental testing, however, the designed identifier was negatively affected by the inevitable noise in the measured signals needed for the identification procedure, finding that in presence of noise, the identified unbalance parameters did not converge to any constant value. Digital filtering techniques were not effective because the induced delay in the filtered signals affected the estimated values, mainly the unbalance phase angle. Taking advantage of the velocity convergence of the algebraic identification method, a reconstruction signal procedure was proposed in order to decrease the noise influence on the identifier’s performance without phase delay effects. By applying the reconstruction signal procedure, the identifier performance was improved, achieving a rapid convergence of the estimated unbalance parameters. This procedure has resulted a viable and practical approach for off-line rotor balancing using algebraic identifiers, but its applicability in cases of on-line balancing must be addressed both numerically and experimentally to verify the scope and limitations.
The proposed algebraic identifier was evaluated by using the estimated unbalance parameters for rotor balancing. Experimental results showed vibration amplitude attenuations around
The obtained results could be improved by using a more complex mathematical model of the rotor-bearing system that considers dynamical effects ignored by the simplified model used here. Moreover, the importance of properly measuring the phase of signals was noted in the experimental tests. It is necessary to have the same reference for both numerical data obtained by mathematical model simulation and experimental signals. This is achieved by placing the infrared sensor in a correct location, in this case, in the same angular position than proximity probe used to measure the vibration amplitudes in y-axis. Since algebraic identification is a model-based identification method, as a future work we propose the consideration of finite element (FE) models which describes more precisely the dynamics of the real system. FE models can include various characteristics ignored by the Jeffcott model such as more inertial disks along the shaft, changes in the shaft diameter, gyroscopic effects, anisotropy in bearings and shaft properties. These models have already been used in the development of unbalance parameters identifiers using the algebraic identification method (Arias-Montiel et al., 2014; Mendoza-Larios et al., 2016; Baltazar-Tadeo et al., 2023; Baltazar-Tadeo et al., 2024) but the reported results are only in numerical simulations. Besides, some additional problems have emerged by the use of this kind of model, mainly the need to measure a great amount of vibration amplitudes along the shaft. Some solutions for this problem has been reported as the use of state observers (Arias-Montiel et al., 2014) or pseudo-modal models (Baltazar-Tadeo et al., 2024). However, these proposals have been evaluated only numerically. Therefore further experimental work is required to overcome these difficulties and achieve the implementation of algebraic identification in more complex systems. Theoretically, the algebraic identification method is robust against the noise in the acquired signals (Fliess and Sira-Ramírez, 2003; Sira-Ramírez et al., 2014; Trapero et al., 2008), but in our experience, noise is an important factor which negatively affect the estimated parameters value. Thus, we believe that more experimental evidence is needed about the influence of noise in the measured signals on the performance of identifiers based on algebraic method, in order to verify its robustness in comparison with other methods in real systems applications.
The datasets presented in this study can be found in online repositories. The names of the repository/repositories and accession number(s) can be found below: Google drive https://drive.google.com/drive/folders/1UXa3e1aIR2iBXHUSbaRpMKoVKb0bAJRN.
JQ-B: Investigation, Software, Validation, Writing–review and editing. MA-M: Conceptualization, Formal Analysis, Methodology, Project administration, Resources, Writing–original draft, Writing–review and editing. JM-L: Conceptualization, Formal Analysis, Methodology, Resources, Writing–review and editing. LV-S: Formal Analysis, Resources, Writing–review and editing.
The author(s) declare that no financial support was received for the research and/or publication of this article.
The authors thank the Universidad Tecnológica de la Mixteca for its support in the development of this project.
The authors declare that the research was conducted in the absence of any commercial or financial relationships that could be construed as a potential conflict of interest.
The author(s) declare that no Generative AI was used in the creation of this manuscript.
All claims expressed in this article are solely those of the authors and do not necessarily represent those of their affiliated organizations, or those of the publisher, the editors and the reviewers. Any product that may be evaluated in this article, or claim that may be made by its manufacturer, is not guaranteed or endorsed by the publisher.
The Supplementary Material for this article can be found online at: https://www.frontiersin.org/articles/10.3389/fmech.2025.1553759/full#supplementary-material
Abbasi, A., Firouzi, B., Sendur, P., Ranjan, G., and Tiwari, R. (2022). Identification of unbalance characteristics of rotating machinery using a novel optimization-based methodology. Soft Comput. 26, 4831–4862. doi:10.1007/s00500-022-06872-9
Arias-Montiel, M., Beltrán-Carbajal, F., and Silva-Navarro, G. (2014). On-line algebraic identification of eccentricity parameters in active rotor-bearing systems. Int. J. Mech. Sci. 85, 152–159. doi:10.1016/j.ijmecsci.2014.05.027
Baltazar-Tadeo, L. A., Colín-Ocampo, J., Abúndez-Pliego, A., Mendoza-Larios, J. G., Martínez-Rayón, E., and García-Villalobos, A. (2024). Balancing of asymmetric rotor-bearing systems using modal masses array calculated by algebraic identification of modal unbalance. J. Vib. Eng. Technol. 12, 4765–4788. doi:10.1007/s42417-023-01151-9
Baltazar-Tadeo, L. A., Colín-Ocampo, J., Mendoza-Larios, J. G., Abúndez-Pliego, A., Nango-Blanco, M., Blanco-Ortega, A., et al. (2023). An integrated balancing method for asymmetric rotor-bearing systems: algebraic identification, modal balancing, and active balancing disks. J. Vib. Eng. Technol. 11, 619–645. doi:10.1007/s42417-022-00598-6
Barrerdo, E., Mendoza-Larios, J. G., Baltazar-Tadeo, L. A., and Landa-Damas, S. J. (2024). Algebraic identification of the physical parameters of a simplified two-degrees-of-freedom rotor-bearing system (in Spanish). CULCYT Cult. Científica Tecnológica 21, 4–12. doi:10.20983/culcyt.2024.1.2.1
Beltrán-Carbajal, F., Silva-Navarro, G., and Arias-Montiel, M. (2013). Active unbalance control of rotor systems using on-line algebraic identification methods. Asian J. Control 15, 1–11. doi:10.1002/asjc.744
Beltrán-Carbajal, F., Silva-Navarro, G., and Arias-Montiel, M. (2014). Active vibration control in a jeffcott-like rotor with variable speed using an electromechanical suspension (in Spanish). Rev. Iberoam. Automática Inform. Ind. 11, 295–303. doi:10.1016/j.riai.2014.05.002
Bently, D., and Hatch, C. (2002). Fundamentals of rotating machinery diagnostics. Minden, NV, USA: Bently Pressurized Bearing Press.
Bera, B., Huang, S.-C., Najibullah, M., and Lin, C.-L. (2023). An adaptive model-based approach to the diagnosis and prognosis of rotor-bearing unbalance. Machines 11, 976–1018. doi:10.3390/machines11100976
Ewins, D. J. (2000). Modal testing: theory, practice and application. Hertfordshire, England: Research Studies Press LTD.
Fliess, M., and Sira-Ramírez, H. (2003). An algebraic framework for linear identification. ESAIM Control, Optimisation Calc. Var. 1, 151–168. doi:10.1051/cocv:2003008
Friswell, M. I., Penny, J. E. T., Garvey, S. D., and Lees, A. W. (2010). Dynamics of rotating machines. Cambridge, UK: Cambridge University Press.
Lalanne, M., and Ferraris, G. (1998). Rotordynamics prediction in engineering. New York, USA: Wiley.
Li, L., Cao, S., Li, J., Nie, R., and Nou, L. (2021). Review of rotor balancing methods. Machines 9, 89–16. doi:10.3390/machines9050089
Mao, W., Liu, G., Li, J., and Liu, J. (2016). An identification method for the unbalance parameters of a rotor-bearing system. Shock Vib. 2016, 1–9. doi:10.1155/2016/8284625
Mendoza-Larios, J. G., Barredo, E., Arias-Montiel, M., Baltazar-Tadeo, L. A., Landa-Damas, S. J., Tapia-Herrera, R., et al. (2021). An algebraic approach for identification of rotordynamic parameters in bearings with linearized force coefficients. Mathematics 9, 2747–2821. doi:10.3390/math9212747
Mendoza-Larios, J. G., Colín-Ocampo, J., Blanco-Ortega, A., Abúndez-Pliego, A., and Gutiérrez-Wing, E. S. (2016). Automatic balancing of a rotor-bearing system: on-line algebraic identifier for a rotordynamic balancing system (in Spanish). Rev. Iberoam. Automática Inform. Ind. 13, 281–292. doi:10.1016/j.riai.2016.03.004
Novillo, E. (2022). “Vibration control engineering,” in Passive and feedback systems (Boca Raton, FL, USA: CRC Press).
Rajagopalan, S., Purohit, A., and Singh, J. (2023). “A systematic review of rotor unbalance diagnosis in rotating machinery based on machine learning algorithms,” in Vibration engineering and technology of machinery. Editors R. Tiwari, Y. S. R. Mohan, A. K. Darpe, V. A. Kumar, and M. Tiwari (Singapore: Springer), 281–300.
Schneider, H. (2023). “Rotor balancing,” in Fundamentals for systematic processes. Berlin, Germany: Springer Vieweg.
Sheng, Y., Wang, Z., Zhou, P., Wang, Z., Niu, Q. W. S., and Niu, S. (2024). Unbalanced feature identification of rotor system based on fused cross-correlation fast fourier transform. Int. J. Aerosp. Eng. 2024, 1–12. doi:10.1155/2024/3095976
Shrivastava, A., and Mohanty, A. R. (2019). Identification of unbalance in a rotor system using a joint input-state estimation technique. J. Sound Vib. 442, 414–427. doi:10.1016/j.jsv.2018.11.019
Shrivastava, A., and Mohanty, A. R. (2020). Identification of unbalance in a rotor-bearing system using kalman filter–based input estimation technique. J. Vib. Control 26, 1081–1091. doi:10.1177/1077546319891642
Sira-Ramírez, H., García-Rodríguez, C., Cortés-Romero, J., and Luviano-Juárez, A. (2014). Algebraic identification and estimation methods in feedback control systems. Chichester, United Kingdom: Wiley.
Subbiah, R., and Littleton, J. E. (2018). Rotor and structural dynamics of turbomachinery. A practical guide for engineers and scientists. Cham, Switzerland: Springer.
Trapero, J. R., Sira-Ramírez, H., and Batlle, F. (2008). On the algebraic identification of the frequencies, amplitudes and phases of two sinusoidal signals from their noisy sum. Int. J. Control 81, 507–518. doi:10.1080/00207170701561419
Vance, J., Zeidan, F., and Murphy, B. (2010). Machinery vibration and rotordynamics. New Jersey, USA: Wiley.
Wisal, M., and Oh, K.-Y. (2023). A new deep learning framework for imbalance detection of a rotating shaft. Sensors 23, 7141–7219. doi:10.3390/s23167141
Keywords: rotor-bearing system, experimental algebraic identification, unbalance, rotating machinery, vibration
Citation: Quiroz-Bautista JU, Arias-Montiel M, Mendoza-Larios JG and Vázquez-Sánchez L (2025) Experimental implementation of algebraic identifier for unbalance parameters in a rotor-bearing system. Front. Mech. Eng. 11:1553759. doi: 10.3389/fmech.2025.1553759
Received: 31 December 2024; Accepted: 18 March 2025;
Published: 31 March 2025.
Edited by:
Kuldeep Mahajan, Mes Wadia College of Engineering, IndiaReviewed by:
Athanasios Chasalevris, National Technical University of Athens, GreeceCopyright © 2025 Quiroz-Bautista, Arias-Montiel, Mendoza-Larios and Vázquez-Sánchez. This is an open-access article distributed under the terms of the Creative Commons Attribution License (CC BY). The use, distribution or reproduction in other forums is permitted, provided the original author(s) and the copyright owner(s) are credited and that the original publication in this journal is cited, in accordance with accepted academic practice. No use, distribution or reproduction is permitted which does not comply with these terms.
*Correspondence: Manuel Arias-Montiel, bWFtQG1peHRlY28udXRtLm14
Disclaimer: All claims expressed in this article are solely those of the authors and do not necessarily represent those of their affiliated organizations, or those of the publisher, the editors and the reviewers. Any product that may be evaluated in this article or claim that may be made by its manufacturer is not guaranteed or endorsed by the publisher.
Research integrity at Frontiers
Learn more about the work of our research integrity team to safeguard the quality of each article we publish.