- 1Intelligent Agricultural Machinery Equipment Engineering Laboratory, Harbin Cambridge University, Harbin, China
- 2College of Mechanical and Electrical Engineering, Northeast Forestry University, Harbin, China
- 3South Subtropical Crop Research Institute, Chinese Academy of Tropical Agricultural Sciences, Key Laboratory of Tropical Fruit Biology, Ministry of Agriculture & Rural Affairs, Key Laboratory of Hainan Province for Postharvest Physiology and Technology of Tropical Horticultural Products, Zhanjiang, China
- 4School of Mechanical Engineering, Guangdong Ocean University, Zhanjiang, China
Introduction: In order to improve the fertilizer-discharging uniformity of the traditional spiral fertilizer distributor and achieve precise and controllable fertilization, based on the agronomic characteristics of fertilization in pineapple orchards, a notched-blade spiral fertilizer discharger with the mechanism of discontinuous-blade sliding-cutting and pushing-pore fertilization is innovatively designed.
Methods: Based on parametric modelling and determining the volume of fertilizer accommodation of the spiral, the theoretical fertilizer-discharging amount of the fertilizer discharger is determined in combination with theoretical analysis. The main factors influencing the fertilization performance of the spiral fertilizer discharger are analyzed using theoretical calculation formulas. The discrete element method is used to simulate the fertilizer-discharging process. By comparing simulation experiments, it is determined that the notched-blade spiral fertilizer discharger has better uniformity than the traditional one. The effects of the number and shape of periodic notched blades on the fertilizer-discharging uniformity are analyzed through single-factor experiments. The L9 (3⁴) orthogonal table is adopted for conducting orthogonal simulation tests.
Results: The test results show that the primary and secondary order of the influence of test factors on test indexes is blade notch shape and periodic blade notch number. When the blade notch is a sector, and the periodic blade has three notches, the fluctuation coefficient of fertilizer discharge uniformity is 27.01%. The results of the bench test show that the uniformity fluctuation coefficient of the notched blade spiral fertilizer discharger is 27.42% when the rotating speed is 60r/min. The experimental and simulation values are consistent. Moreover, the fluctuation coefficient of the spiral fertilizer discharger is reduced by 64.86 percentage points compared with that of the spiral fertilizer discharger under the same conditions. Moreover, the fluctuation coefficient of the notched blade spiral is 64.86% lower than that of the spiral fertilizer discharger under the same conditions. Based on different rotational speeds, the fitting curve of fertilizer discharge is y = 2.02x + 23.02.
Conclusion: The fertilizer discharge can be controlled by adjusting the rotating speed. It improves the controlled accuracy and uniformity of fertilizer application and achieves the goal of green and sustainable development of the pineapple industry in the tropics. The research results can provide a reference for designing and optimizing spiral fertilizer dischargers.
1 Introduction
Pineapple is one of the five tropical fruits in the world and belongs to the perennial herb of the Pineapple family. It has a beautiful appearance and unique taste contains many nutrients such as vitamins, minerals, organic acids and fibrous needed by the human body (Liu et al., 2024; Ni et al., 2024). In the domestic market, pineapple is mainly sold as fresh fruit to some large and medium-sized cities in Northeast China, North China and Central China, and its sales volume gradually increases in the domestic market share year by year. The main forms of foreign trade for pineapple products in the international market are fresh or dried pineapple juice and canned pineapple. According to statistics, with the improvement of yield level brought by science and technology, the pineapple output in China has increased steadily year by year since 2012 (Zhang R. et al., 2022).
The complexity of agricultural production, the terrain, the complexity of working conditions, and the need for high productivity have led to the need for continuous improvement in the functioning of agricultural machinery. Studies such as those on cardan shafts and tractor oil checks evidence this (Aleksandar et al., 2013a; Aleksandar et al., 2013b). However, fertilization operations in agricultural production are critical to pineapple plantation management and play a key role in pineapple quality and yield. There are some things that could be improved with pineapple fertilization in China. Farmers carry out excessive fertilization in pineapple planting for market demand. The amount of nitrogen fertilizer in Chinese pineapple orchards alone exceeds 800 kg/hm2. Unreasonable chemical fertilizer application will cause excessive crop leaves and root growth, excessive consumption of nutrients and energy, and a decline in crop yield and quality (Liang et al., 2022). It easily leads to soil hardening, low utilization rate of fertilizer and pollution. Mechanical fertilization can improve fruit farmers’ labor intensity, fertilization efficiency, and agricultural production cost. Among them, the fertilizer discharger is the core component in fertilization operation. The excellent performance of fertilizer discharger directly affects the effect of fertilization. Currently, the market’s mainstream fertilizer dischargers include three categories: outer grooved wheel, spiral type and centrifugal type. Although the fertilizer mentioned above discharger is commonly used, it still needs better flow uniformity. Due to the structural design defects, it is difficult to realize precise fertilization because of the uneven flow of fertilizer discharge. Therefore, it is necessary to optimize and test the fertilizer discharging device to apply fertilizer scientifically and properly and improve the utilization rate of fertilizer. To achieve the goal of a green and sustainable pineapple industry in tropical areas.
Cundall and Strack first proposed the discrete Element Method (DEM) in the 1970s for the numerical simulation of discontinuous media problems (Wei and Gao, 2021). It can simulate and interact with agricultural particulate materials and mechanical equipment. It provides a new way to design modern agricultural equipment digitally, greatly improves the efficiency of research and development of agricultural equipment, and has a good application prospect in agricultural engineering. The Discrete Element Method (DEM) has significant advantages over simulation techniques such as Computational Fluid Dynamics (CFD), which focuses on the behavior of individual discrete particles and accurately resolves inter-particle contacts, collisions and trajectories. CFD, on the other hand, focuses on continuous fluids. In the study of complex physical processes involving particle-fluid coupling or dominated by particle systems, DEM is the preferred method for this study because it can provide detailed information at the microscopic level, which lays the foundation for an in-depth understanding and optimization of the relevant processes.
In order to improve the uniformity of fertilizer discharge and the utilization rate of fertilizer. The discrete element method (DEM) has been used to study the fertilization performance of the fertilizer discharger on fruits and crops. For example, Song et al. (2023a) studied the influence of a spiral grooved wheel fertilizer discharger on fertilizer discharger performance by the discrete element method. They obtained the optimal parameter of the spiral angle of sheave speed and shovel cross-section. Wang et al. (2023a) used the discrete element method to study qualitatively and numerically fertilizer particles. The effects of the rotational speed, working length and forward speed of the sheave on the morphology, stress and dynamic performance of fertilizing granules were investigated. Ma et al. (2024) developed a concave (BNS) spiral blade conveying device. EDEM software was used to simulate the influence of various factors on fertilization performance, and the parameters of pit diameter, axial distance and radial distance were determined. Bangura et al. (2020) designed a spiral-grooved wheel fertilization device. Through DEM experiment and simulation, by measuring fertilizer rate, uniformity of fertilizer discharge and falling velocity of fertilizer particles, it is proved that its fertilization performance is better than that of the straight grooved wheel. Zhao et al. (2023) designed a small spiral fertilizer discharger based on the agronomic characteristics of mango orchard fertilization. Determination of the optimal parameter combination of fertilizer discharge device by genetic algorithm. The fertilization performance of the device was tested using DEM simulation and bench test. By using the discrete element method, Zhang et al. (2024) explored the causes of flow fluctuation in the process of spiral fertilizer discharger, the influence of force chain evolution on particle flow fluctuation and the influence of rotational speed. Finally, the axial distribution of the force chain is the main influencing factor of the flow fluctuation. Peng et al. (2023) developed a new bidirectional screw fertilizer applicator to promote the green and healthy growth of sugarcane. EDEM is used for the simulation test, and the response surface method and artificial neural network are used to determine the optimal parameter combination. Sugirbay et al. (2020) developed a new needle roller design as a fertilizer discharge metering device for variable fertilizer. By optimizing the parameters of a pin, the uniformity of fertilizer discharge and the amount of fertilizer application were improved. Wang et al. (2023b) improved the design of the spiral grooved wheel fertilizer discharger. The spiral angle and mounting angle of the spiral grooved wheel are optimized. Finally, the uniformity and accuracy of fertilizer discharge are enhanced. Duan et al. (2024) established a granular fertilizer model with fragmentation characteristics using the discrete element method and explored the fragmentation law of fertilizer granules in lateral deep fertilization devices. The key parameters of screw pitch, screw speed and Y-shaped mouth angle are optimized. Sun et al. (2023) developed a spiral staggered furrow wheel fertilization device. Phenomenological and numerical studies of particle motion under the influence of structural characteristic parameters are carried out using the discrete element method. Results in the uniformity of fertilizer discharge were increased by 60.06%. Zha et al. (2021) designed a blocking wheel spiral fertilizer discharger. EDEM software is used to carry out simulation tests and bench performance tests. The range of parameters, such as the blocking wheel’s opening width and the device’s rotational speed, are determined. Dun et al. (2024) designed an oblique spiral fertilizer discharger. The inclination angle of the device and the range of parameters of the distance from the end spiral blade to the fertilizer discharge port were determined by DEM simulation and bench test, and the fertilization performance was verified. Song et al. (2020) designed a rotary variable fertilizer according to the distribution of banana roots. The parameters of the fertilizer were optimized by discrete element simulation. The optimum parameter combination of the periodic central angle of the forward speed turntable and the opening size of the curved groove is determined. The performance of the fertilizer was verified by field experiment. Jia et al. (2022) designed a pneumatic centralized and discharged precision mixed fertilization device according to the top-dressing requirements in corn’s middle and late growth period. Through the coupling simulation of fluid mechanics and discrete element method, the optimal parameters of gas velocity and bellows length at the inclined angle of the fertilizer discharge port were determined, and the fertilization performance was verified by field experiment.
Although many studies have been carried out on the fertilization performance of fruits and crops at home and abroad, there are few reports on the fertilization performance of pineapple orchards by fertilization machinery. The discrete element simulation was applied to the fertilization machinery of mango, banana, sugarcane, corn and other crops, which provided a basis for studying the design and fertilization performance of fertilization machinery in pineapple orchards. According to the agronomic characters of fermentation in pineapple orchards, a notched-blade spiral fertilizer discharger was designed in this study. Aiming to solve the problem of uniform fluctuation of spiral fertilizer discharger, the design was improved to improve fertilization performance. DEM simulation and bench test carried out the fertilization performance test and parameter optimization of the notched vane spiral fertilizer discharger. Firstly, the main factors influencing the fluctuation of spiral fertilizer dischargers are theoretically analyzed. At the same time, the discrete element model is established. Taking the fluctuation coefficient of fertilizer discharge uniformity as the evaluation index, the single factor and orthogonal test were used to simulate the fertilizer discharge performance and determine the experimental factors that have a significant influence. Then, the regression equation of test factors and test indexes is established, and the regression model is optimized by multi-objective optimization to get the optimal parameter combination. Finally, the bench test is carried out. Verify the accuracy and adaptability of simulation test results of notched blade spiral fertilizer discharger by commonly using different fertilizer particles. Improve fertilizer utilization and fertilization to promote fruit availability in tropical areas. This study provides a reference for studying fertilization machinery and related experiments in the pineapple planting industry.
2 Working principle and parameter determination of the whole machine
2.1 Structural design and working principle
The notched blade spiral is improved based on a continuous spiral blade. Using three-dimensional software to generate spiral blades: taking three sector notches in the circumferential direction as an example. The spiral discharge wheel is divided into three equal parts in the circumferential direction, and the cut area is equally divided with the reserved area. After the improvement, the blades with each pitch can have fertilizer discharge space to ensure the feasibility of fertilizer discharge.
According to the agronomic requirements of pineapple orchard and related theoretical formulas, a notched blade spiral fertilizer discharger was innovatively designed, which adopted the mechanism of intermittent leaf sliding cutting and moving pore fertilization. As shown in Figure 1, the three-dimensional model structure comprises a fertilizer box, fertilizer shell, notch, spiral blade, fertilizer discharge shaft, end cover and fertilizer discharge port. According to NY/T 1442–2007 (NY/T 1442–2007, 2007), the maximum amount of fertilizer discharged is 900 kg/hm2, and the spiral parameters are determined. In this study, the specific fixed size of the fertilizer discharger is known. The spiral outer diameter is 90mm, the spiral inner diameter is 30 mm, the screw pitch is 35 mm, the average thickness of the spiral blade is 4 mm, and the fertilizer outlet diameter is 62 mm. The motor drives the notched spiral blade to rotate the fertilizer discharge shaft. Under gravity, the fertilizer falls on the upper part of the fertilizer discharge shaft from the fertilizer box. When the rotated notched spiral blade pushes the fertilizer to move axially to the fertilizer discharge port, the notch of the spiral blade at the fertilizer discharge port can compensate for the periodic fluctuation of the spiral fertilizer discharge when rotating at different phase angles. The uniformity of fertilizer discharge of the notched vane spiral fertilizer discharger is improved. The fertilizer falls into the fertilizer discharge pipe and the soil by gravity to complete the fertilization operation.
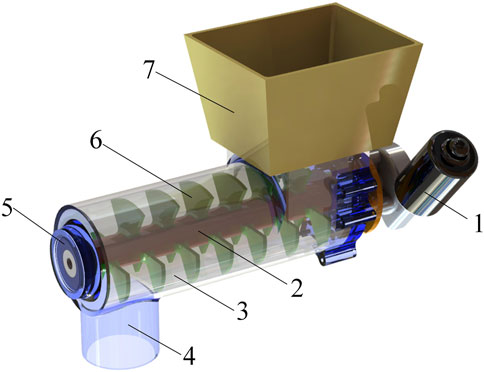
Figure 1. Schematic diagram of the structure of notched blade spiral fertilizer discharger. 1. Motor. 2. Fertilizer discharge shaft. 3. Shell. 4. Fertilizer outlet. 5. Bearings. 6. Notched spiral blade. 7. Fertilizer box.
2.2 Theoretical analysis of fertilizer discharger
2.2.1 Fertilizer discharge and application efficiency
Fertilizer discharge is a key indicator for evaluating the fertilizer discharge performance of the fertilizer discharger, while the structure and parameters of the fertilizer discharger affect the fertilizer discharge. In order to clarify the influencing factors of the notched blade spiral fertilizer discharger’s fertilizer discharge, the notched blade spiral fertilizer discharger’s fertilizer discharge performance, as well as the fertilizer discharge, were theoretically analyzed.
During the fertilizer application process, the theoretical volume of the fertilizer discharger is mainly determined by the difference between the volume of the housing cavity and the volume of the discharging wheel during a single rotation cycle. According to the working principle of the spiral conveying mechanism (Chen et al., 2015), the relationship between the amount of fertilizer discharged from the spiral discharger can be calculated according to Equation 1.
Where q is the fertilizer discharge volume of the fertilizer discharger, g/s; D is the outer diameter of the spiral blade, mm; d is the inner diameter of the spiral blade, mm; S is the pitch, mm; b is the thickness of the spiral blade, mm; h is the depth of the spiral, mm; ρ is the density of fertilizer, g/mm3; μ is the fertilizer discharging spiral filling coefficient, %; n is the number of notches; A is the surface area of a single notched blade, mm2; r is the drive motor speed, r/min.
From Equation 1, it can be seen that the fertilizer discharge device, in addition to the basic parameters that have been determined, the notched blade spiral fertilizer discharger is related to r, n, A, r, μ and so on. Since the dynamic influence parameters are variable factors, this paper ignores here and only studies and analyses the fixed parameters. When the fertilizer discharge is determined, the relevant blade notch parameters can be adjusted appropriately. To meet the demand for the amount of fertilizer to be applied to the pineapple crop in the agronomic model of starter planting. At the same time, research the planting pattern of the pineapple garden at the South Subtropical Research Institute in Zhanjiang City, Guangdong Province, to understand the real planting situation, as shown in Figure 2. The amount of fertilizer to be applied per acre by the notched blade spiral fertilizer discharger can be calculated by Equation 2 when the fertilizer discharger is moved forward a continuous distance.
where Q is the amount of fertilizer discharged, g; L is pineapple plant ridge spacing, mm; v is the machine operating speed, m/s.
The travelling speed of the fertilizer application equipment in the pineapple orchard is about 0–4 km/h (Xue et al., 2022), and the maximum operating speed is used to calculate Equation 3 to know the maximum fertilizer application efficiency of the fertilizer discharger.
where Pmax is the maximum fertilizer application efficiency of the fertilizer discharger, acre/h, 1 acre = 667 m2; L1 is the distance between the pineapple fertilizer ridges, taken as L1 = 1.1 m; v1 is the operating speed of the machine, taken as v1 = 4,000 m/h.
From Equation 3, Pmax = 6.6 acre/h.
2.2.2 Characterization of notched spiral blades for fertilizer discharge
The spiral fertilizer discharge wheel of the traditional screw-type fertilizer discharger adopts solid-type blades, and when the blades of the fertilizer discharge wheel rotate, the fertilizer is pushed to the fertilizer discharge outlet one by one through the blades. However, during the circumferential rotation of the continuous blades, a pulsation phenomenon is presented at the outlet, causing interruptions in the fertilizer discharge process. The notched blade auger is able to ensure the continuous discharge of fertilizer at different rotation angles by breaking through the blockage of the blades. Fertilizer can be applied to the aperture by the action of intermittent blade slip-cut nudging, as shown in the schematic diagram of Figure 3.
According to the material flow characteristics, the fertilizer flow space size should be at least 3 to 6 times the size of the fertilizer particles to avoid poor flow and fertilizer blockage (Wen, 2021). That is, the area of the screw conveyor notch is at least the sum of the homogeneous planes of 3 and more fertilizers, satisfying Equation 4.
where DP is the equivalent diameter of fertilizer particles, mm.
To further understand the fertilizer conveying process, force analysis of fertilizer particles was carried out under the action of notched spiral blades. The fertilizer particles conveyed on the notched blades are simplified to be mass points because of the relatively complex forces on the fertilizer during conveyance. Taking the center of mass as the origin O, the tangential direction of the rotating circle where the fertilizer particles are located as the Z-axis, and the direction of the notched spiral blade transversely conveying the fertilizer as the Y-axis, the coordinate system shown in Figure 4 is established. The combined fertilizer particle force Fe is subdivided into axial and circumferential forces as in Equations 5, 6.
where Fr is the axial component force, N; Fq is the circumferential component force, N; Fe is the combined force of the fertilizer particles, N. γ is the friction angle between the fertilizer and the blades (°); β is the helical lift angle (°).
where Fn is the notched helical blade normal thrust, N; Fp is the particle normal squeeze force at the notch, N; Ff is the rotational tangential friction, N; f is the surface friction, N.
The fertilizer combined force Fe is synthesized by the normal thrust force Fn of the spiral blades, the normal squeezing force Fp of the fertilizer particles at the notch, the tangential friction force Ff and the surface friction f against it. Where Fn is speed-dependent with respect to the dynamic parameters of the fertilizer discharger. Fp is related to the sparsity of fertilizer build-up at the spiral blade notch. Ff and f are related to the material properties of the spiral blades and fertilizer particles. Therefore, removing the influence of material properties and subsequent dynamic parameters, the key factor for the overall material transport movement is the normal squeezing force at the blade notch. The squeezing force of fertilizer build-up at the blade notches during the operation of the device is closely related to the number of notches and the shape of the notches. When the number of circumferential uniform notches is too many, and the shape is too narrow, or the number is too few, and the shape passes well, the effect of fertilizer discharge is very different. Therefore, the number of cycle blade notches and blade notch shape of notched blade spiral fertilizer discharger will be considered important research factors in this paper.
3 Discrete element simulation
The discrete Element Method (DEM) analyzes the forces between models by transferring the forces between particles based on the forces of motion between particles and collisions between particles. It has been widely used in agricultural engineering (Shi and Sakai, 2022). The spiral discharge wheel is the core component of the fertilizer application operation, and its structural parameters directly impact the amount and uniformity of fertilizer discharge (Fang et al., 2024). In order to clarify the fertilizer discharge characteristics of the notched blade spiral fertilizer discharger, a numerical simulation model of the discharger was established using a discrete element simulation platform to analyze the influence of the structural parameters of the discharging wheel on the fertilizer discharge volume and uniformity of the discharged fertilizer.
3.1 Discrete element model of fertilizer particles
In pineapple orchard applications, it is important to select organic fertilizer as the material for DEM (Discrete Element Method). Research has shown that organic fertilizer can release nitrogen, phosphorus, potassium, and other nutrients slowly and continuously to meet the needs of pineapples at different growth stages. At the same time, it can increase soil porosity by more than 30%, improve soil aeration and water retention, and create excellent conditions for pineapple root growth and nutrient absorption. In order to make the fertilizer particle discrete element model closer to the actual fertilizers, so in this paper, the organic fertilizers from Shandong Microtillage Agricultural Science and Technology Co. Ltd. Were selected as the test materials for the fertilizer particle discrete element modeling. Referring to the method of 3D modeling of fertilizer particles (Yu et al., 2022; Song et al., 2023b; Ferreira et al., 2020), 100 random samples were taken from the fertilizer pile, and the 3D dimensions of the fertilizer particles were measured using vernier calipers (Qingdao et al., ARZ-1332 digital calipers). Its average length was 3.76 mm, width was 3.47 mm, and height was 3.31 mm. The equivalent diameter DP and sphericity SP of fertilizer particles were calculated according to Equations 7, 8.
where DP is the equivalent diameter of fertilizer particles, mm; SP is the sphericity of fertilizer particles, %; L is the length of fertilizer particles, mm; B is the width of fertilizer particles, mm; H is the height of fertilizer particles, mm.
The equivalent diameter of fertilizer particles DP = 3.51 mm and sphericity SP = 93.35% were calculated, and since SP > 90%, a sphere with a diameter of 3.51 mm was chosen as a more appropriate model for the simulated particles. The simplification of the spherical model ignores the particles’ real shape diversity, resulting in distortion of the simulation of key parameters such as contact area and friction. This distortion will cause small deviations in the analysis of the particle dynamics behavior in the practical application, with a negligible effect.
Origin 2022 software was applied to statistically analyze the population distribution pattern of the sample fertilizer particles by plotting histograms, as shown in Figure 5. The normal distribution function shown in Equation 9 was used to fit the sample distribution pattern data.
where y is the dependent variable, and x table is the independent variable. a, b, c0, and ε denote the coefficients of the normal distribution function. The fit was a = 1.05, b = 37.33, c0 = 3.41, and ε = 1.32, where the goodness of fit R2 = 0.92. It can be argued that the equivalent diameters of the fertilizer particles follow a typical distribution pattern. Hence, the generation pattern of fertilizer particles in the setup of a pellet plant follows a normal distribution.
3.2 Theoretical model of discrete element method and parameter setting
The discrete element method describes the collision process as the creation of contact and the occurrence of action. Different contact models have different application scenarios. Based on the physical characteristics of fertilizer particles and their low surface adhesion. The changes in force, velocity, and displacement of the fertilizer particles during the fertilizer process when the discharger is in operation are determined by small elastic deformations between the fertilizer particles or between the granular fertilizer and the geometry. Multiple fertilizer particles collide with each other by friction, which is suitable for the theory of soft sphere particle analysis in the discrete element method. Therefore, the soft particle contact model is used in this study. Considering that common fertilizer particles do not adhere, the Hertz-Mindlin no-slip contact mechanics model was used as a contact model between fertilizer particles and the fertilizer dischargers (fertilizer box, discharging box, spiral discharging wheels, and housing). The model accurately represents the physical situation and is precise and efficient in calculating forces (Gao et al., 2024; Sun et al., 2024). The discrete element method simulates the contact between soft particles by setting springs, dampers, sliders, and couplers between particles i and j (or contact walls) (Dun et al., 2020), as shown in Figure 6.
In the present study, the properties of PLA material were used for the fertilizer discharge apparatus fertilizer box, fertilizer discharge box, spiral fertilizer discharge wheel, and casing. As shown in Table 1, the material and contact mechanics parameters associated with the fertilizer particles and the discharger were determined using a combination of experimental measurements and a review of relevant literature (Yang et al., 2018; Yu and HenrikSaxe, 2010).
3.3 Simulation model building
SolidWorks 3D software was used to 3D model the 1:1 scale notched blade type spiral fertilizer discharger, and the output STL format was imported into EDEM software for simulation. Establishment of a pellet plant inside the fertilizer tank to generate spherical fertilizer pellets at a rate of 80,000 pellets per second. When the number of fertilizer particles reaches a certain level and is stationary, the fertilizer discharge wheel is set to rotate, and the fertilizer collection plate is set to move, respectively, to carry out simulation tests. A fertilizer plate consisting of a single square slot with an overall length of 3,000 mm and a width of 300 mm is provided below the discharger’s fertilizer outlet. This plate is sufficient to collect all the discharged fertilizer, observe the fertilizer distribution, and reduce the impact of the bouncing of the discharged fertilizer particles. The rotational speed of the fertilizer discharge wheel was set at 60 rpm, the movement speed along the x-axis was 0.5 m/s, the total simulation time was 8 s, and the data recording interval was 0.01 s. The simulation time was 8 s, and the data logging interval was 0.01 s. EDEM simulation of fertilizer discharge process for notched blade spiral fertilizer discharger shown in Figure 7.
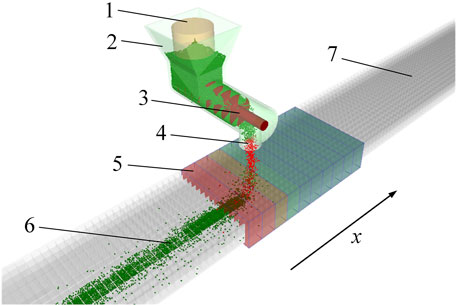
Figure 7. Schematic diagram of simulation test. 1. Particle plant. 2. Shell. 3. Notched blade spiral fertilizer discharging wheel. 4. Fertilizer discharge opening. 5. Uniformity monitoring area. 6. Fertilizers. 7. Fertilizer collection plate. Note: x is the forward direction of the fertilizer discharger.
3.4 Methods for evaluating the performance of fertilizer drainage
3.4.1 Grid division method
In order to accurately determine the effect of different rotational speeds of spiral fertilizer discharging wheels on the uniformity of fertilizer discharge in the discrete element simulation test, reference is made to NY/T 1003–2006 Technical Specification for Quality Evaluation of Fertilizer Applying Machines (NY/T 1003–2006, 2015). The object of study is the change rule of the amount of fertilizer discharged by the notched blade-type spiral discharging apparatus in a rotational cycle. The coefficient of fluctuation of the uniformity of fertilizer discharging is the evaluation index for the study. The unit is driven at near-average operating speed to discharge fertilizer and passes through a monitoring area where the fertilizer falling in each compartment is collected and weighed separately. Fertilizer discharge uniformity was calculated by dividing the distance of a single cycle of rotation of the fertilizer discharge wheel into 10 equal parts of 500 mm in length using grid dissection, and the direction of placement of the length was the direction of advancement. Labelled sequentially with numbers from 1 to 10 in the positive direction of the x-axis, Figure 8 shows the setup of the statistical grid.
3.4.2 Calculation of the coefficient of fluctuation of fertilizer discharge uniformity
Using the above approach, the uniformity monitoring area was changed to a different location and repeated three times. Equations 10, 11 calculated the mean, standard deviation, and coefficient of uniformity fluctuation of fertilizer quality of each mean grid to investigate the effect of fertilizer discharge in a notched blade spiral fertilizer discharger.
where m is the average mass of fertilizer in the mean grid, g; mi is the mass of fertilizer in the ith mean grid, g; N is the number of statistical grids for fertilizer quality in the monitoring area, N = 10; σ is the coefficient of fluctuation of homogeneity in a single cyclic cycle, %.
The coefficient of fertilizer discharge uniformity fluctuation was calculated for each grid, with lower values representing better discharge uniformity and vice versa.
3.5 Comparative analysis of fertilizer discharge characteristics
Based on the traditional spiral fertilizer discharger, set the same working length, blade inner and outer diameters of the spiral fertilizer discharging wheel, and the same shell sleeve inner diameter parameters to make a comparative analysis of the simulation test. One of the notched blade fertilizer dischargers is exemplified by 4 fan-shaped notches. The fertilizer drainer was modeled 3D using SolidWorks software, and the 3D model was imported into EDEM 2022 software. Fill in the parameters in Table 1 and set the plant to generate 100,000 fertilizers at 50,000 pcs/s. Fill in the parameters according to Table 1 and set the plant to generate 100,000 fertilizers at a rate of 50,000 particles/s. Once the fertilizer granules have been formed into a pile, the auger discharge wheel is rotated. Setting the rotational speed of the spiral fertilizer discharging wheel at 60rpm and the data recording interval at 0.01s, the angular changes of its three different phase angles are shown in Figure 9.
The instantaneous discharge of fertilizer from the outlet was analyzed separately for the 0°–90° intervals where there was a significant difference in contrasts during cyclic fertilizer discharge (Yang et al., 2020). Instantaneous fertilizer discharges of notched vane dischargers did not very much at different phase angles. In contrast, the conventional spiral fertilizer discharger has a variable instantaneous fertilizer discharge during the same phase angle change as the former. This is because the continuous spiral blades have a significant blocking effect on fertilizer delivery, opening and closing the fertilizer outlet at regular intervals as the phase angle of the fertilizer discharge wheel rotation continues to change. The fertilizer clogs the delivery path when the spiral blades rotate in a particular position. Whereas notched spiral blades are not affected by different phase angles, fertilizer can be extruded and discharged at any notch.
To further verify its accuracy, fertilizer quantity monitoring zones of the same size were established at the fertilizer outlet based on the discrete element simulation model to collect fertilizer particle data. Figure 10 shows a preliminary comparison and analysis of the trend of the fluctuation coefficient of the two types of fertilizer dischargers at different times.
As shown in Figure 10, the fluctuation of the number of fertilizer particles in the traditional spiral fertilizer discharger is much more significant than the fluctuation of the notched blade spiral fertilizer discharger, and the overall amplitude of the number of fertilizers varies greatly. Whereas the number of notched blade fertilizer discharges varied, the overall volatility was balanced and stable. Among the traditional curves, the pre-flow extremes are small, probably because the fertilizer fluctuation stability has not been reached at the beginning of the fertilizer discharge, and the flow rate reaches a stable fluctuation by 6s later.
Therefore, such a conclusion had been drawn. The continuous blade structure of the spiral discharge wheel results in a periodic variation of the instantaneous fertilizer discharge from the outlet. This leads to problems such as fluctuations in the amount of fertilizer discharged and poor uniformity of fertilizer application by the traditional spiral fertilizer discharger. The notched blade spiral can reduce the fertilizer slow plugging situation and, to a certain extent, improve the uniformity of fertilizer discharge. Therefore, the importance of notched blade spiral al fertilizer discharger on uniformity is informative.
3.6 Single-factor test
The preliminary theoretical analysis determined that the key factors for the overall material transport movement were the number of notches at the blade notch and the notch pattern. To determine the effect of the number of period blade notches and blade notch shapes of the spiral fertilizer discharging wheel on the uniformity of fertilizer discharging, a one-factor experimental study was carried out using a discrete element simulation technique under different numbers of period blade notches and blade notch shapes.
3.6.1 Calculation of the coefficient of fluctuation of fertilizer discharge uniformity
Too many notches in the blades of the spiral fertilizer discharging wheel will lead to fine crushing of the blades, dispersion of the force on the blade surface, and a reduction in the fertilizer delivery capacity. Moreover, the fertilizer tends to get stuck and clogged at the tiny notches. A one-way test was conducted using the number of cycle blade notches of 2, 3, 4, 5, and 6 to study the effect of fertilizer discharger on the coefficient of fluctuation of uniformity of fertilizer discharge at different numbers of cycle blade notches. The relationship between the fluctuation coefficient of fertilizer discharge uniformity and the number of blade notches in the fertilizer discharger cycle was obtained, as shown in Figure 11A.
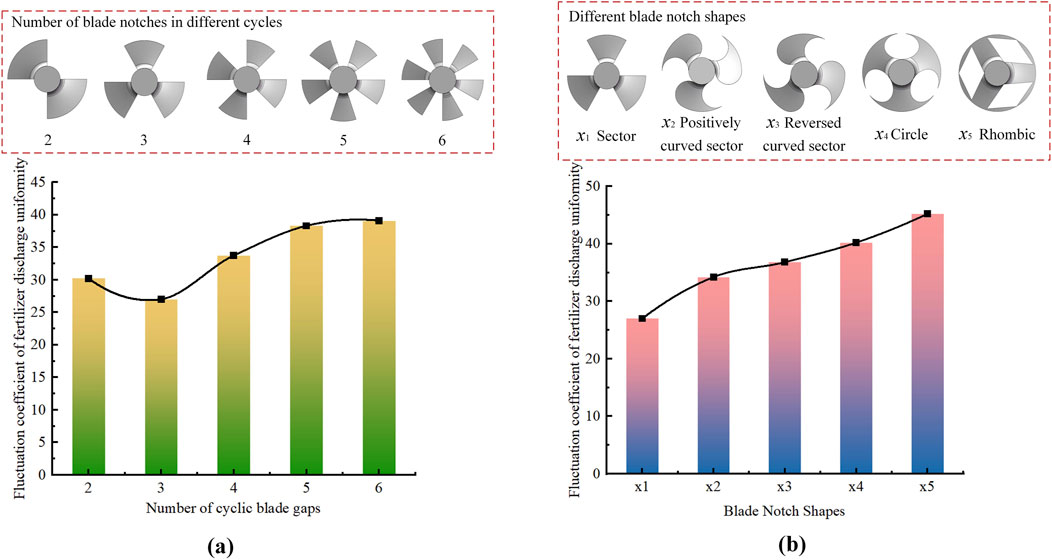
Figure 11. Impact curve of the single-factor test. (A) Relationship between periodic blade notch and uniformity. (B) Relationship between blade notch shape and uniformity.
The coefficient of fluctuation of fertilizer discharge uniformity decreases and then increases as the number of cycle blade notches gradually increases. The coefficient of fluctuation of fertilizer discharge uniformity was minimal when the number of cycle blade notches was about 3. Therefore, 2 to 4 were selected to carry out further studies in conjunction with the effect of other factors on homogeneity.
3.6.2 Blade notched shape
Spiral fertilizer dischargers apply fertilizer by gradually pushing it through the spiral blades. During the rotation of the spiral blades, stress changes occur at the notch between the fertilizer and the spiral blades. This is to confirm that variations in blade notch shape have different effects on fertilizer delivery. Therefore, the test determined that the fertilizer discharger cycle blades are based on 3 notches and the area of the notches is equally divided by the area of the blades. For single-factor tests, different notch shapes, sector, positively curved sector, reversed curved sector, circle, and rhombic were used, respectively. The effect of different blade notch shapes on the fluctuation of fertilizer discharge uniformity coefficient was investigated.
The variation of uniformity fluctuation coefficient for different blade notch shapes is shown in Figure 11B. Where x1∼ x3 fluctuation coefficients are the smallest. The fluctuation coefficients are more significant for x4 and x5, and the larger the coefficient of fluctuation, the worse the homogeneity. Adhering to the guideline of selecting the smaller uniformity coefficient as the better, it was determined that the blade notch shape was selected as sector x1, positively curved sector x2, and reversed curved sector x3 as the test factors for further testing.
4 Orthogonal test
4.1 Experimental design
Orthogonal tests can consider the effects of multiple discrete quantities of factors on the results of an experiment to determine the interactions between the factors and the optimal combination of factors. According to the above theoretical analysis of the notched blade spiral fertilizer discharger discharging process, the number of cycle blade notches of the spiral fertilizer discharging wheel and the change of the shape of the notches will affect the effect of fertilizer discharging. The number of blade notches is too tiny for the spiral blades to remain at a particular phase angle to prevent the fertilizer particles from being discharged. At the same time, too many will affect the fertilizer delivery capacity. Moreover, the spiral blade notch shape was changed based on the fan shape to study the effect of fertilizer discharge. The number of cycle blade notches was used as the test factor, and the setting range was from 3 to 5. The shape of the blade notch was used as a test factor to determine the shapes as a sector, positively curved sector, and reversed curved sector, denoted by x1, x2, and x3, respectively. The factor levels are shown in Table 2.
4.2 Experimental program and analysis of results
L9 Orthogonal table design dramatically reduces cost and time by its efficiency in capturing the effects of key factors in fewer trials. However, it may miss some of the higher-order interaction information compared to full factorial analysis. Although complete factor analysis is comprehensive and accurate, it requires many trials and is costly. Both have advantages and disadvantages, which must be weighed when applying them. To be consistent with the present study, the orthogonal test conducted with the L9 (34) orthogonal table was selected (Mo et al., 2022). The test factors were the number of cyclical blade gaps A and the blade notch shape B, and the test index was the coefficient of fluctuation of fertilizer discharge uniformity σ. The results of the tests were analyzed in terms of extreme variance (Wang et al., 2022), and the analysis of variance (ANOVA) was carried out by Design-Expert 13 (Lai et al., 2021), and the results are shown in Tables 3, 4.
Analysis of the primary and secondary relationship between the number of cyclical blade gaps and blade notch shape on the effect of uniformity fluctuation coefficient and determination of the preferred solution. The results of the polar analysis in Table 3 show that the primary and secondary relationships affecting the fluctuation coefficients are the blade notch shape and the number of cyclical blade gaps. A2B1 is the best parameter combination scheme, where the number of periodic blade notches is 3, and the shape of blade notches is sector.
Table 4 shows that the significance test result of the simulated fertilizer exclusion model was F = 16.91 (P = 0.009 < 0.01), and the model was highly significant. The number of periodic blade notches significantly affected the coefficient of uniformity fluctuation (0.01 < P = 0.0288 < 0.05). The Fertilizer discharge wheel blade notch shape significantly affected the coefficient of fluctuation of fertilizer discharge uniformity (P = 0.0059 < 0.01).
4.3 Impact and optimization
The orthogonal test shows that the notched blade spiral fertilizer discharger has the best structural parameters for uniformity and efficiency when the number of blade notches in the structural setting period is 3 and the shape of blade notches is sector. The simulation verification revealed that the coefficient of fluctuation of fertilizer discharge uniformity obtained at the optimum combination level is 26.54%, better than the values obtained at other levels. The reason may be that in the notched screw conveying situation, the fan-shaped groove shape can effectively reduce the friction between the material and the inner wall of the cavity by its unique geometrical characteristics, reduce mechanical wear, optimize the material fluidity, and enhance the conveying efficiency, so its research shape is the best. Figure 12 shows the effect of the number and shape of cycle blade notches on the uniformity of fertilizer discharge in a 3D bar view. Along with the increase in cycle blade gaps, the volatility coefficients show a process of change that first decreases and then increases. Moreover, the fluctuation coefficient shows an increasing trend as the shapes of sector x1, positively curved sector x2, and reversed curved sector x3 change sequentially. When the blades were 3-notched and sector, this condition had the shortest column and the smallest coefficient of uniformity fluctuation, which agrees with the results of the previous extreme variance analyses.
5 Bench test
Referring to NY/T 1003–2006 Fertilizer Applying Machinery Quality Evaluation Technical Specification, data was collected using a collection box in accordance with the simulation analysis criteria. Bench tests were conducted on the notched blade spiral fertilizer discharger to verify its reliability and feasibility.
5.1 Test materials and instruments
The test was conducted in September 2024 at the Intelligent Agricultural Machinery and Equipment Engineering Laboratory, Harbin Cambridge College, Harbin City, Heilongjiang Province. Organic fertilizer from Shandong Microploughing Agricultural Technology Co. Ltd. was selected as the test fertilizer. The number of periodic blade notches is 3, and the shape of the blade notches is sector. I am machining the notched blade spiral fertilizer discharger using a 3D printer and constructing a test bench. The motor speed is adjusted through the controller, and the fertilizer discharger is driven. The fertilizer collection box is placed on the test plate to collect the discharged fertilizer. At the end of the fertilizer discharge, the fertilizer collected by the collection box was statistically analyzed, and the test rig is shown in Figure 13.
5.2 Comparative validation tests
To verify the effect of the fertilizer discharger’s improvement in fertilizer uniformity and the accuracy of the simulation optimization results, a comparative verification test of fertilizer uniformity was carried out between the notched blade spiral fertilizer discharger and the traditional spiral fertilizer discharger with an external fluted wheel. The operating speed was 60 r/min, and the test time was 10 s. Each test group was repeated five times to take the average value, the statistical test fertilizer discharge, and the test uniformity fluctuation coefficient.
The results show that the notched blade spiral fertilizer discharger simulation test discharged 1,230.89 g of fertilizer with a fluctuation coefficient of 26.54%. In contrast, the bench test discharged 1,194.00 g of fertilizer, corresponding to a fluctuation factor of 27.42%. The bench test of the conventional spiral discharger discharged 701.72 g of fertilizer with a coefficient of fluctuation of 92.28%. Using the optimized structural parameters of the notched blade spiral fertilizer discharger, the relative error between the experimental and simulated fertilizer discharges was 3.09%. Through analysis, it was determined that the leading cause was the presence of clumps of fertilizer in the bench test, which were not entirely crushed, resulting in a slight discharge. However, the relative errors are all within 5 percent, an acceptable range that meets the practical requirements. The relative error between the experimental fluctuation coefficient and the simulated value is 3.21%. The analysis determined that the deviation was mainly due to the idealization of the particles as spherical in the simulation. The analysis determined that the deviation was mainly due to the idealization of the particles as spherical in the simulation. However, the deviation is insignificant, and the two match, indicating that the simulation optimization results are accurate. The average value of the conventional spiral manure discharger’s coefficient of fluctuation under the same conditions was 92.28 percent. The notched blade spiral fertilizer discharger reduced the coefficient of fluctuation by 64.86 percentage points over the conventional spiral fertilizer discharger. The new optimized fertilizer discharger discharges fertilizer better, effectively improves the uniformity of granular fertilizer application, and meets the design requirements. Precision fertilizer discharger reduces costs, increases crop yields for economic benefits, reduces fertilizer pollution, and produces significant ecological benefits.
5.3 Experimental programme and results
The fertilizer discharger designed in this paper does not have a fertilizer-regulating spacer. However, it can be controlled by controlling the rotational speed and, thus, the amount of fertilizer discharged. The single-factor test method was adopted. The test factors were the speed of the fertilizer discharge wheel, which was taken as 20, 30, 40, 50, and 60 r/min at five levels. The test index was the amount of fertilizer discharged. The test time for each level was 10 s. Data were collected every 2 s during the test, and each group of tests was repeated 5 times to take the average value. The variation curve of fertilizer discharge with working time is shown in Figure 14. Adjusting the rotational speed of the fertilizer discharge wheel can significantly change the amount of fertilizer discharged, and the amount of fertilizer discharged with the working time is a linear trend.
Origin 2024 was applied to fit the data to the experimental results, and the fit plot is shown in Figure 15. The fitted curve shows that the fertilizer discharge flow rate increases with the increase of the rotational speed of the fertilizer discharge wheel. The fitted curve equation is y = 2.02x + 23.02, R2 = 0.99. Under different operating conditions, the precise control of the fertilizer discharge volume is affected very little by the differences in fertilizer particle characteristics, the degree of clogging of the fertilizer discharge port, etc. The equation can accurately reflect the relationship between the fertilizer discharge volume and the related control variables. After a systematic and comprehensive investigation, the equation can accurately reflect the relationship between the fertilizer discharge volume and the related control variables, which thoroughly verifies its high reliability under different operating conditions, and provides a solid theoretical basis and practical guidance for the precise control of the fertilizer discharger. Therefore, the fertilizer discharger can regulate the discharge flow rate by changing the speed of the discharging wheel. Moreover, when the rotational speed of the fertilizer discharge wheel is 60 r/min and the machine speed is 4 km/h, the fertilizer discharge can reach 1,179.45 kg/hm2, which meets the design requirement of the maximum fertilizer discharge of 900 km/hm2.
6 Conclusion
1. Based on the agronomic characteristics of pineapple orchard fertilizer application, a notched blade spiral fertilizer discharger was innovatively designed using the intermittent blade sliding and cutting mechanism to nudge the aperture for fertilizer application. Through theoretical analysis, the main factors affecting the uniformity of its fertilizer discharge were identified as the number and shape of periodic blade notches.
2. Through theoretical analysis, the main factors affecting the uniformity of its fertilizer discharge were identified as the number and shape of periodic blade notches. Improved uniformity compared to conventional continuous blades.
3. The results of the single-factor simulation test showed that the uniformity of fertilizer discharge was better when the number of blade notches in the cycle was between 2 and 4 and when the shape of blade notches was sector, positively curved sector, and reversed curved sector. The optimal combination of structural parameters from the orthogonal test is 3 cycles of blade notch, blade notch shape of sector shape. At this time the coefficient of fluctuation of fertilizer discharge uniformity was minimum 27.01%.
4. The results of the bench validation test showed that the discharged fertilizer volumes in the simulation and the bench test were the same. The fluctuation coefficient of fertilizer discharge uniformity was 27.42% in the bench test, which was 64.86 percentage points less than that of the traditional spiral fertilizer discharger under the same conditions. Effectively improves the uniformity of granular fertilizer application. Moreover, the fitted curve for the discharge flow rate of the notched blade spiral fertilizer discharger was obtained as y = 2.02x + 23.02. It was demonstrated that regulation of fertilizer discharge could be achieved by varying the speed of the notched blade spiral fertilizer discharging wheel. The present study, through the precise optimization of agricultural machinery, not only strengthens the foundation of scientific theory but also meets society’s urgent need for efficient agriculture. In future research, it is possible to focus on fertilizer controllers that emit different fertilizers so that the emission of different fertilizers can be controlled precisely.
Data availability statement
The raw data supporting the conclusions of this article will be made available by the authors, without undue reservation.
Author contributions
GD: Conceptualization, Funding acquisition, Methodology, Project administration, Resources, Supervision, Writing–review and editing. QS: Conceptualization, Formal Analysis, Methodology, Software, Visualization, Writing–original draft, Writing–review and editing. XJ: Conceptualization, Investigation, Methodology, Software, Writing–review and editing. HL: Funding acquisition, Investigation, Project administration, Resources, Supervision, Writing–review and editing. CYM: Investigation, Methodology, Software, Writing–review and editing. XL: Investigation, Methodology, Software, Writing–review and editing. HS: Methodology, Software, Writing–review and editing. LW: Formal Analysis, Resources, Validation, Writing–original draft, Writing–review and editing. CM: Validation, Visualization, Writing–original draft, Writing–review and editing. ZY: Methodology, Validation, Writing–review and editing. HW: Data curation, Writing–review and editing.
Funding
The author(s) declare that financial support was received for the research, authorship, and/or publication of this article. This research was funded by Chinese Academy of Tropical Agricultural Sciences for Science and Technology Innovation Team of National Tropical Agricultural Science Center, grant number CATASCXTD202409, Heilongjiang Province Natural Science Foundation of China, grant number LH2023E025, and Harbin Cambridge University Key Scientific Research Application Research Project, grant number JQZKY2022021.
Conflict of interest
The authors declare that the research was conducted in the absence of any commercial or financial relationships that could be construed as a potential conflict of interest.
Generative AI statement
The author(s) declare that no Generative AI was used in the creation of this manuscript.
Publisher’s note
All claims expressed in this article are solely those of the authors and do not necessarily represent those of their affiliated organizations, or those of the publisher, the editors and the reviewers. Any product that may be evaluated in this article, or claim that may be made by its manufacturer, is not guaranteed or endorsed by the publisher.
References
Ašonja, A., Adamović, Ž., and Jevtić, N. (2013a). Analysis of reliability of cardan shafts based on condition diagnostics of bearing assembly in cardan joints. Metal. Int. 18, 216–221. Available at: https://www.researchgate.net/publication/297430787.
Ašonja, A., Mikić, D., Stojanović, B., Gligorić, R., Savin, L., and Tomić, M. (2013b). Examination of motor-oils in exploitation at agricultural tractors in process of basic treatment of plot. J. Balk. Tribol. Assoc. 19, 314–322. Available at: https://www.researchgate.net/publication/261070796.
Bangura, K., Gong, H., Deng, R., Tao, M., Liu, C., Cai, Y., et al. (2020). Simulation analysis of fertilizer discharge process using the Discrete Element Method (DEM). PLoS ONE 15, e0235872. doi:10.1371/journal.pone.0235872
Chen, X. F., Luo, X. W., Wang, Z. M., Zhang, M. H., Hu, L., Yang, W. W., et al. (2015). Design and experiment of fertilizer distribution apparatus with double-level screws. Trans. Chin. Soc. Agric. Eng. 31, 10–16. doi:10.3969/j.issn.1002-6819.2015.03.002
Duan, J. P., Liu, D. W., Xie, F. P., Zhang, Y. R., and Zheng, P. (2024). Breakage simulations and experiments of granular fertilisers for optimizing a device of side-deep fertilisation by using the discrete element method. Biosyst. Eng. 238, 105–114. doi:10.1016/j.biosystemseng.2024.01.003
Dun, G. Q., Gao, Z. Y., Guo, Y. L., Liu, Y. X., Mao, N., and Ji, W. Y. (2020). Simulation test and optimization for structural parameters of circular arc gear discharging fertilizer apparatus. Jour. Zhejiang Univ. Agric. Life Sci. 46, 625–636. doi:10.3785/j.issn.1008-9209.2019.11.101
Dun, G. Q., Sheng, Q. B., Ji, X. X., Zhang, C. X., Gao, S., Wei, Y. H., et al. (2024). Optimal design and experiment of electronically controlled inclined spiral precision fertilizer discharger. Agriculture 14, 1131. doi:10.3390/agriculture14071131
Fang, L., Yang, W., Luo, X., Guo, H., Song, S., Liu, Q., et al. (2024). Development and optimization of an offset spiral tooth fertilizer discharge device. Agriculture 14, 329. doi:10.3390/agriculture14020329
Ferreira, I., Peruchi, R. S., Fernandes, N. J., and Junior, P. R. (2020). Measurement system analysis in angle of repose of fertilizers with distinct granulometries. Measurement 170, 108681. doi:10.1016/j.measurement.2020.108681
Gao, K., Lin, L., Zhang, W., Xu, W., and Sun, L. (2024). Using vibration to attenuate the adhesive friction behavior between screw conveyor blades and wet coal particles. Powder Technol. 438, 119592. doi:10.1016/j.powtec.2024.119592
Jia, H. L., Tan, H. W., Wen, X. Y., Wang, G., Yuan, H. F., and Huang, D. Y. (2022). Design and experiment of pneumatic aggregate and discharge precision fertilizer mixing device. Trans. Chin. Soc. Agric. Mach. 53, 109–119+203. doi:10.6041/j.issn.1000-1298.2022.S2.013
Lai, X., He, G. Q., Li, S. P., Zeng, B., Mo, H. N., Teng, X., et al. (2021). Experimental research on the axial vibration of the cutting system for sugarcane harvesters. Trans. Chin. Soc. Agric. Eng. 37, 12–20. doi:10.11975/j.issn.1002-6819.2021.14.002
Liang, Z. H., Zhang, H. Y., Jin, X., Zhai, P. F., Zhao, Y., Li, C. J., et al. (2022). Effect of different fertilizer models on the growth, development, yield and quality of pineapple in tropics. Chin. Jour. Trop. Crop. 43, 2294–2303. doi:10.3969/j.issn.1000-2561.2022.11.014
Liu, T. H., Chen, S. Y., Yang, G. Z., Zhang, J. D., Zeng, Y. F., Sun, W. L., et al. (2024). Design and experiment of the double row alternating toothed sieve pineapple conveying mechanism. Trans. Chin. Soc. Agric. Eng. 40, 11–21. doi:10.11975/j.issn.1002-6819.202402005
Ma, Z., Wu, Z., Li, Y., Song, Z., Yu, J., Li, Y., et al. (2024). Study of the grain particle-conveying performance of a bionic non-smooth-structure screw conveyor. Bios. Eng. 238, 94–104. doi:10.1016/j.biosystemseng.2024.01.005
Mo, H. N., Li, S. P., Qiu, C., Ma, S. C., Huang, Z. M., and Zhou, J. H. (2022). Effects of the blade disk vibration in axial and cutting parameters on the cutting quality of sugarcane harvesters. Trans. Chin. Soc. Agric. Eng. 38, 62–71. doi:10.11975/j.issn.1002-6819.2022.18.007
Ni, Y. M., Dai, Y., Deng, G. R., Qin, J. Z., Li, L., and Zheng, S. (2024). Overview of the development of mechanized technology for pineapple production in China. Mod. Agric. Equip. 45, 17–23.
NY/T1003—2006 (2015). Technical specification for quality price of fertilizer machinery. Beijing, China: China Standards Press.
NY/T 1442—2007 (2007). Ministry of agriculture and rural affairs of the people’s Republic of China. Tech. Code Cultiv. Pineapple.
Peng, M., Zhang, Z., Zhang, W., Huang, H., Zhang, G., Liu, W., et al. (2023). Design and optimization of sugarcane spiral fertilizer applicator based on response surface methodology and artificial neural networks. Processes 11, 2881. doi:10.3390/pr11102881
Shi, Q., and Sakai, M. (2022). Recent progress on the discrete element method simulations for powder transport systems: a review. Adv. Powder Technol. 33, 103664. doi:10.1016/j.apt.2022.103664
Song, S. S., Duan, J. L., Zou, X. J., Yang, Z., Ou, Z. W., and Wang, B. (2020). Parameter optimization and test of variable fertilizer apparatus based on root distribution pattern of bananas. Trans. Chin. Soc. Agric. Eng. 36, 11–18. doi:10.11975/j.issn.1002-6819.2020.06.002
Song, X., Dai, F., Zhang, F. W., Wang, D., and Liu, Y. (2023a). Calibration of DEM models for fertilizer particles based on numerical simulations and granular experiments. Comput. Electron. Agric. 204, 107507. doi:10.1016/j.compag.2022.107507
Song, X., Dai, F., Zhang, X., Gao, W., Li, X., Zhang, F., et al. (2023b). Simulation and experiment of fertilizer discharge characteristics of spiral grooved wheel with different working parameters. Sustainability 15, 11309. doi:10.3390/su151411309
Sugirbay, A., Zhao, J., Nukeshev, S. O., and Chen, J. (2020). Determination of pin-roller parameters and evaluation of the uniformity of granular fertilizer application metering devices in precision farming. Comput. Electron. Agric. 179, 105835. doi:10.1016/j.compag.2020.105835
Sun, X., Niu, L., Cai, M., Liu, Z., Wang, Z., and Wang, J. (2023). Particle motion analysis and performance investigation of a fertilizer discharge device with helical staggered groove wheel. Comput. Electron. Agric. 213, 108241. doi:10.1016/j.compag.2023.108241
Sun, X., Niu, L., Zhang, H., Wang, Q., Zhou, W. B., Tang, H., et al. (2024). Exploring sustainable agriculture: investigating the impact of controlled release fertilizer damage through bonded particle modeling. J. Clean. Prod. 468, 143095. doi:10.1016/j.jclepro.2024.143095
Wang, J., Wang, R., Ju, J., Song, Y., Fu, Z., Lin, T., et al. (2023a). Study on the influence of grooved-wheel working parameters on fertilizer emission performance and parameter optimization. Agronomy 13, 2779. doi:10.3390/agronomy13112779
Wang, X., Jia, Z. X., Liu, L. J., Li, J. Q., Zhang, C. C., and Wang, S. F. (2022). Optimization of molding process parameters for sheet molding compound composites based on range analysis. China Plast. 36, 77–83. doi:10.19491/j.issn.1001-9278.2022.10.012
Wang, Y., Tan, Y. P., Wei, S. L., Liao, M. M., Zang, Y., and Zeng, S. (2023b). Design and experimental study of the fertilizer applicator with vertical spiral fluted rollers. Int J Agric and Biol Eng 16, 80–87. doi:10.25165/j.ijabe.20231605.7555
Wei, Z. Y., and Gao, A. P. (2021). Current status and outlook of the application of discrete element method in agricultural engineering research. J. Agric. Mach. 52 (04), 1–20. doi:10.13268/j.cnki.fbsic.2021.02.040
Wen, Y. S. (2021). Research on key technology of automatic transplanting for vegetable plug seedlings. Beijing (BJ): China Agricultural University.
Xue, Z., Zhang, X. M., Chen, R. Y., Wang, S., and Pan, R. (2022). Design and experiment of 2ZBL-90 double row pineapple planter. Jour. Chin. Agri. Mech. 43, 9–14. doi:10.13733/j.jcam.issn.2095-5553.2022.06.002
Yang, W. W., Fang, L. Y., Luo, X. W., Li, H., Ye, Y. Q., and Liang, Z. H. (2020). Experimental study on the effect of the parameters of the spiral fertilizer feeder on the performance of the fertilizer. Trans. Chin. Soc. Agric. Eng. 36, 1–8. doi:10.11975/j.issn.1002-6819.2020.17.001
Yang, Z., Zhu, Q. C., Sun, J. F., Chen, Z. C., and Zhang, Z. W. (2018). Study on the performance of fluted roller fertilizer distributor based on EDEM and 3D printing. Jour. Agric. Mech. Res. 40, 175–180. doi:10.3969/j.issn.1003-188X.2018.05.032
Yu, S., Bu, H., Dong, W., Jiang, Z., Zhang, L., and Xia, Y. (2022). Calibration of physical characteristic parameters of granular fungal fertilizer based on discrete element method. Processes 10, 1564. doi:10.3390/pr10081564
Yu, Y. W., and HenrikSaxe, N. (2010). Experimental and DEM study of segregation of ternary size particles in a blast furnace top bunker model. Chem. Eng. Sci. 65, 5237–5250. doi:10.1016/j.ces.2010.06.025
Zha, X., Zhang, G., Han, Y., Salem, A. E., Fu, J., and Zhou, Y. (2021). Structural optimization and performance evaluation of blocking wheel-type screw fertilizer distributor. Agriculture 11, 248. doi:10.3390/agriculture11030248
Zhang, M., Niu, H., Han, Y., Zhi, Y., Yuan, T., Zhang, H., et al. (2024). A simulation and experiment of the flow fluctuation characteristics of a fertilizer distribution apparatus with a screw from the perspective of the force chain. Appl. Sci. 14, 1122. doi:10.3390/app14031122
Zhang, R. H., Zhang, Q., Ou, J. S., He, K. J., Wang, Z. W., and Lu, D. X. (2022). Design and control of self-propelled pineapple flower induction machine with high gap. Mech. Elec. Eng. Tech. 51, 18–21. doi:10.3969/j.issn.1009-9492.2022.06.005
Keywords: agricultural machinery, DEM, fertilizer discharger, uniformity of fertilizer discharge, notched blade
Citation: Dun G, Sheng Q, Ji X, Li H, Ma C, Li X, Sun H, Wang L, Ma C, Yu Z and Wang H (2025) Parameter optimization of the notched blade spiral fertilizer discharger for pineapple orchards based on DEM. Front. Mech. Eng. 11:1535013. doi: 10.3389/fmech.2025.1535013
Received: 01 December 2024; Accepted: 22 January 2025;
Published: 17 February 2025.
Edited by:
Alessandro Ruggiero, University of Salerno, ItalyReviewed by:
Md Irfanul Haque Siddiqui, King Saud University, Saudi ArabiaAleksandar Ašonja, Business Academy University (Novi Sad), Serbia
Copyright © 2025 Dun, Sheng, Ji, Li, Ma, Li, Sun, Wang, Ma, Yu and Wang. This is an open-access article distributed under the terms of the Creative Commons Attribution License (CC BY). The use, distribution or reproduction in other forums is permitted, provided the original author(s) and the copyright owner(s) are credited and that the original publication in this journal is cited, in accordance with accepted academic practice. No use, distribution or reproduction is permitted which does not comply with these terms.
*Correspondence: Guoqiang Dun, ZHVuZ3VvcWlhbmdwYXBlckAxNjMuY29t; Hailiang Li, bGloYWlsaWFuZ0AxMjYuY29t