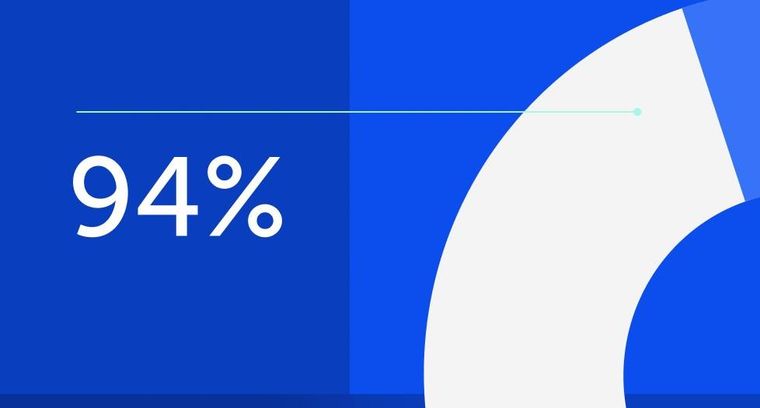
94% of researchers rate our articles as excellent or good
Learn more about the work of our research integrity team to safeguard the quality of each article we publish.
Find out more
EDITORIAL article
Front. Mech. Eng., 26 July 2024
Sec. Solid and Structural Mechanics
Volume 10 - 2024 | https://doi.org/10.3389/fmech.2024.1459814
This article is part of the Research TopicLightweight Mechanical and Aerospace Structures and MaterialsView all 5 articles
Editorial on the Research Topic
Lightweight mechanical and aerospace structures and materials
Innovative manufacturing technologies, such as additive manufacturing and auto fiber placement, have made it possible to fabricate high performance lightweight structures for mechanical and aerospace applications. Lightweight structures avoid excessive waste of raw materials and subsequently result in a reduced emission of greenhouse gases and increase energy efficiency. To enable wide applications of lightweight structures fabricated using these innovative manufacturing technologies, it is necessary to understand their structural performance under various operational environments. For example, static and vibration responses of thin-walled structures for wing skins and fuselage panels under aerodynamic loads, the crash behavior of helmet under impact load, stress and buckling response of the pipe vessel structures under hydrodynamic loadings, stress shielding of latticed hip arthroplasty stem structures, energy absorption of sandwich structures, etc. Composite/honeycomb/lattice structures, stiffened thin-walled metal structures, etc., have been widely used for these lightweight structure designs. Therefore, for a better lightweight structural design and subsequent efficient optimization studies, there is a need to develop high fidelity and efficient structural analysis approaches for studying linear and nonlinear responses of these innovative lightweight structures in practical applications.
The four research articles related to this Research Topic focus on obtaining novel insights into the mechanical performance of lightweight structures. Various analysis approaches in solid and structural mechanics, including analytical, semi-analytical, and numerical methods, are adopted in these articles.
The review article by An et al. highlights the critical need for protecting penetration fuzes from extreme g-forces experienced during operation. These devices can be subjected to tens of thousands or even hundreds of thousands of g-forces, necessitating robust protection. The study introduces various internal sealing reinforcements and external energy-absorbing materials, such as foam metals and composite sandwich structures, to safeguard the internal circuitry of the fuze. These materials demonstrate excellent energy absorption and mechanical properties, enhancing the fuze’s reliability. Additionally, the research calls for further exploration of factors like viscoelasticity, porosity, surface coating, and printing processes to optimize these materials’ performance. Advancing buffer materials for penetration fuzes is crucial for improving the safety and efficacy of these weapons.
Amin et al. examine the buckling response of functionally graded multilayer graphene platelet-reinforced composite (FG-GPL RC) rectangular plates with cutouts under various loads. This research is vital for applications demanding high strength-to-weight ratios and resilience, such as in aerospace and civil engineering. Using third-order shear deformation plate theory and finite element analysis, the study evaluates numerous factors, including plate aspect ratios, slenderness ratios, and the effects of different loading conditions. The comprehensive analysis of graphene platelet distributions offers valuable insights for optimizing composite structures, aiding the development of more efficient and resilient materials for critical applications.
Cheng et al. focus on optimizing integrally stiffened shells used in sealed cabins for aerospace purposes. These shells, known for their high stiffness, strength, and fatigue resistance, are essential for enhancing deep space payload detection capabilities. The proposed design framework employs topology optimization and mesh-mapping techniques, achieving up to 17.1% weight reduction compared to traditional designs while maintaining structural integrity. Experimental validation through hydrostatic and airtight tests confirms the framework’s effectiveness. Such advancements in lightweight design are pivotal for improving aerospace structures’ efficiency and performance, supporting more ambitious and cost-effective space missions.
Wael et al. investigate the design and analysis of lightweight gear transmission systems utilizing composite materials. The study addresses the complexities of designing composite gear pairs through a robust numerical approach using the flexible multibody method and MSC MARC solver. This method accurately estimates static transmission error (STE) in lightweight gears, considering nonlinear contact behavior. The research highlights the advantages of hybrid metal-composite gears in reducing vibrations and noise compared to traditional holed gears. Additionally, the study explores the effects of ply arrangements and fiber orientation on composite gears’ performance, paving the way for more efficient and quieter transmission systems essential for various industrial applications.
Collectively, these studies demonstrate the transformative potential of advanced materials and engineering designs. From enhancing military fuze safety and optimizing aerospace structures to improving mechanical gear systems, these innovations drive progress across multiple fields. Ongoing research and development promise even greater advancements, contributing to safer, more efficient, and sustainable technological solutions.
SD: Writing–original draft, Writing–review and editing. WZ: Writing–original draft, Writing–review and editing. ZY: Writing–original draft, Writing–review and editing.
The author(s) declare that no financial support was received for the research, authorship, and/or publication of this article.
The authors declare that the research was conducted in the absence of any commercial or financial relationships that could be construed as a potential conflict of interest.
All claims expressed in this article are solely those of the authors and do not necessarily represent those of their affiliated organizations, or those of the publisher, the editors and the reviewers. Any product that may be evaluated in this article, or claim that may be made by its manufacturer, is not guaranteed or endorsed by the publisher.
Keywords: lightweight, finite e1ement method, composite structures and heterogeneous materials, structural optimization, advanced material and structure
Citation: De S, Zhao W and Yuan Z (2024) Editorial: Lightweight mechanical and aerospace structures and materials. Front. Mech. Eng 10:1459814. doi: 10.3389/fmech.2024.1459814
Received: 04 July 2024; Accepted: 15 July 2024;
Published: 26 July 2024.
Edited and reviewed by:
Guoqiang Li, Louisiana State University, United StatesCopyright © 2024 De, Zhao and Yuan. This is an open-access article distributed under the terms of the Creative Commons Attribution License (CC BY). The use, distribution or reproduction in other forums is permitted, provided the original author(s) and the copyright owner(s) are credited and that the original publication in this journal is cited, in accordance with accepted academic practice. No use, distribution or reproduction is permitted which does not comply with these terms.
*Correspondence: Shuvodeep De, c2h1dm9kZUB2dC5lZHU=
Disclaimer: All claims expressed in this article are solely those of the authors and do not necessarily represent those of their affiliated organizations, or those of the publisher, the editors and the reviewers. Any product that may be evaluated in this article or claim that may be made by its manufacturer is not guaranteed or endorsed by the publisher.
Research integrity at Frontiers
Learn more about the work of our research integrity team to safeguard the quality of each article we publish.