- 1Department of Industrial and Systems Engineering, The Hong Kong Polytechnic University, Hong Kong, Hong Kong SAR, China
- 2Mechanical Engineering Department, Politecnico Di Milano, Milano, Italy
- 3Department of Mechanical Engineering, King Fahd University of Petroleum and Minerals, Dhahran, Saudi Arabia
- 4Interdisciplinary Research Center for Advanced Materials, King Fahd University of Petroleum and Minerals, Dhahran, Saudi Arabia
Each year, a significant amount of waste is produced from carbon fiber polymer composites at the end of its lifecycle due to extensive use across various applications. Utilizing regenerative carbon fiber as a feedstock material offers a promising and sustainable approach to additive manufacturing based on materials. This study proposes the additive manufacturing of recycled carbon fiber with a polyamide-12 polymer composite. Filaments of recycled carbon fiber-reinforced polyamide-12 (rCF-PA12) with different recycled carbon fiber contents (0%, 10%, and 15% by weight) in the polyamide-12 matrix are developed. These filaments are utilized for 3D printing of specimens by using various infill density parameters (80% and 100%) on a fused deposition modeling 3D printer. The study examined how the fiber content and infill densities influenced the flexural performance of the printed specimens. Notably, the part containing 15 wt% recycled carbon fiber (rCF) composites showed a significant improvement in flexural performance due to enhanced interface bonding and effective fiber alignment. The results indicated that reinforcing the printed part with 10% and 15 wt% recycled carbon fiber (rCF) improved the flexural properties by 49.86% and 91.75%, respectively, compared to the unreinforced printed part under the same infill density and printing parameters. The investigation demonstrates that the additive manufacturing-based technique presents a potential approach to use carbon fiber-reinforced polymers waste and manufacture high-performance engineering, economic, and environmentally friendly industrial applications with the complicated design using different polymer matrices.
1 Introduction
Carbon fiber-reinforced polymers (CFRP) have excellent engineering properties such as outstanding strength, strong modulus, lightweight, and abrasion resistance, making them suitable for use in a wide range of industrial applications. Due to the excellent performance and low maintenance costs of CFRP composites, along with light weight, they are growing in popularity as substitutes for metals in a variety of manufacturing, sporting, and transportation uses (Yang et al., 2012; Stewart, 2011). The widespread utilization of CFRP has additionally resulted in an accumulation of CFRP waste during the recent years. Estimates of CFRP in-use supplies revealed that approximately 97,000 tons of CFRP trash will be accumulated in China’s landfills by the year 2044 from the wind turbine and aviation sectors, which can be recycled to recover carbon fibers (Akbar and Liew, 2020). The aerospace industry generates the highest global CFRP demand (36% of the total need), after which comes the automobile industry (24% of total need), which mainly consists of excellent-quality polyacrylonitrile (PAN)-based carbon fibers and polymer (Sauer et al., 2018). Despite the significant increase in their manufacturing and applications, one of the major unresolved challenges is their disposal, both at the end of life and as waste trash, regardless of the matrix type, thermoset, or thermoplastic (Bledzki et al., 2021; Sommer and Walther, 2021).
Though CFRP manufacturing has been streamlined to meet the rising needs, there is still a problem of end-of-life CFRP and trash scraps resulting from manufacturing operations. At present, a significant proportion of CFRP trash is disposed of in landfills or burnt (Akbar and Liew, 2020). Their dumping results in the depletion of high-value carbon fiber and the emissions of greenhouse gases, both of which are environmentally hazardous. Some governments have implemented landfill taxes to minimize the quantity of trash disposed of in landfills and increase material recycling, particularly for CFRP garbage (Li et al., 2016). In accordance with the Japan carbon fiber manufacturers association (JCMA), the amount of energy used for creating virgin carbon fiber is approximately 290 MJ/kg, resulting in a significant virgin carbon fiber (vCF) price (J. The Society Of Fiber Science and Te, 2016). The minimum manufacturing cost of vCF is approximately 30–40€/kg (Holmes, 2018), whereas the significantly lower production cost of recycled carbon fiber (rCF) using the recycling process is approximately $5/lb (McConnell, 2010). It is worth noting that the utilization of the rCF in the manufacturing of the different parts with the polymer matrix composites provides dual benefits such as decreasing the emission of hazardous gases in the atmosphere and decreasing the manufacturing cost of the different products in comparison to manufacturing of the products using the vCF.
In sustainable manufacturing of the different parts, various researchers used rCF as a reinforcement in the different polymer matrix composites for manufacturing the different parts using the fused deposition technique (Huang et al., 2020; Liu et al., 2021; Su et al., 2022a). Tian et al. (2017a) developed and extensively examined the unique recycling and remanufacturing technique based on the 3D manufacturing of carbon fiber-reinforced thermoplastic composites (CFRTPCs). Continuous carbon fiber and polylactic acid (PLA) matrix were recovered from 3D-printed composite parts as the PLA-impregnated carbon fiber filament and employed as the raw material for subsequent 3D printing procedures, in which significant material recovery percentages were obtained for both carbon fiber (100%) and PLA matrix (73%). They observed that the tensile and flexural properties of the parts were 256 MPa and 263 MPa much higher than those of the pure PLA matrix manufactured using the 3D printer, respectively.
Liu et al. (2021) proposed a novel additive manufacturing-based technique that can be employed to recover the carbon fiber-reinforced polymer composite (CFRPC) trash and again utilized the rCF for the fabrications of different products. For obtaining the rCF, they decomposed the epoxy resin of the carbon fiber/epoxy resin (CF/EP) prepreg trash by increasing the temperature of the reactor at approximately 330°C for 60 min, and the n-butanol mixture achieved a supercritical state (330°C, 6.5 MPa). Following this, the reactor was cooled down by using an inner cooling pipe. The rCF was removed, cleaned with acetone, dried, and subsequently measured. They examined the mechanical properties of the reclaimed carbon fiber by producing components using a 3D printer with 10 wt% of rCF in the polyether-ether-ketone (PEEK) polymer matrix composites. The results demonstrated that adding 10 wt% of rCF content enhanced the tensile properties by 17.23%, improved the flexural strength of the parts by 10.18%, and increased the electrical conductivity by 96.69% compared to the samples fabricated using the pure PEEK polymer in the fused deposition modeling (FDM) technique.
Su et al. (2022a) fabricated the specimens using a 3D printer and rCF reinforcement with varying fiber fraction loadings of 10, 20, 30, and 40 wt% in a polyamide (PA) matrix composite. It was found that the samples with 20 wt% and 30 wt% of rCF exhibited superior mechanical characteristics, with the latter showing more variations attributed to fiber fracture. The tensile strength and modulus showed the most significant improvement in the 20–30 wt% samples, increasing by 175%–243% (up to 187.12 MPa) and 329%–562% (up to 12.04 GPa), respectively. Hengstermann et al. (2021) assessed the influence of yarn characteristics, fiber length, and fiber quantity on the tensile strength of rCF/PA composite web structures. The superior tensile strength of unidirectional (UD) composites having the 50% volume fraction was 80 MPa. Giani et al. (2022) manufactured specimens with 5 wt% and 10 wt% of rCF in the PLA polymer matrix using a 3D printer. They created dog bone specimens at different deposition angles of approximately 0° and 90°. In comparison to the 90° orientation, the composite containing 10 wt% rCF 3D printed at 0° shows a doubling of both the elastic modulus and peak stress concerning the applied stress orientation.
The utilization of carbon fiber composites in the 3D printing process with FDM printers is not a new topic of research, and various thermoplastic polymer matrices such as PLA (Banjo et al., 2022; Rimašauskas et al., 2022; Li et al., 2021; Saleh et al., 2024), acrylonitrile–butadiene–styrene (ABS) (Ning et al., 2015; Tekinalp et al., 2014), and nylon (Rodríguez-Reyna et al., 2022a; Ramachandran et al., 2024) have already been manufactured using carbon fiber as the reinforcement. Presently, most of the research studies in this field have focused on the manufacturing of various products using the vCF with the different polymer matrix in the 3D printer (Maqsood and Rimašauskas, 2022; Dong et al., 2023; Wang et al., 2023; Nasirov et al., 2020; Rodríguez-Reyna et al., 2022b; Belei and Amancio-Filho, 2023). Love et al. (2014) investigated the influence of short carbon fiber insertion on the strength, stiffness, thermal conductivity, and deformation of FDM-fabricated components. Ning et al. (2015) studied the impact of chopped carbon fibers on the mechanical characteristics of ABS, finding that varied concentrations of chopped fibers boosted both tensile and flexural qualities but may decrease toughness. Rodríguez-Reyna et al. (2022a) used vCF as a reinforcement in the nylon, PLA, and ABS matrix materials for analyzing the printing parameters of the 3D printer. It was found that nylon with the carbon fiber produced the ultimate tensile strength of approximately 31.5 MPa, which has a tridimensional pattern and infill density of approximately 100%. The fundamental challenge with CFRP recovery is the variability of supply materials because wastes and end-of-life items have uneven forms, leading to rCF of different lengths. This difficulty necessitates the reuse of rCF in a kind of short fiber to offer a reinforcing agent of uniform shape. Su et al. (2024) observed the tensile properties of the reclaimed carbon fiber-reinforced polyamide-6 composites manufactured using the FDM technique with the various percentages of the densities such as 10%, 30%, 50%, 70%, and 90%. The coupons manufactured using the 90% infill densities provide excellent performance. The samples had the tensile strength and modulus of 76.5 MPa ±3.5 MPa and 4.8 GPa ±0.1 GPa, respectively. Shah et al. (2019) examined the impacts of hybridizing hemp fiber with the rCF to identify trends in the mechanical performance qualities arising from the different weight fractions. This study demonstrated a 10%–15% improvement in tensile strength following the addition of hemp fiber to recycled carbon fiber reinforced. Flexural strength increased by 30%–35% when hemp fiber was added to recycled carbon fiber reinforcement. Cheng et al. (2021) examined the microtopography and monofilament tensile force of the rCF and mechanical characteristics of the rCF composites reinforced with polylactic acid. The findings indicate that when the ideal process parameters were followed, the monofilament tensile strength of rCF was 8% greater than that of the original carbon fiber (OCF). OCF-reinforced PLA composites (OCF/PLA) and rCF/PLA composites had tensile strengths that were 25% and 12.5% lower, respectively, than those of PLA.
Extensive research has been carried out on the effectiveness and mechanical performance of virgin carbon fiber-reinforced polymer composites in 3D printing. Carbon fibers have the ability to greatly enhance the manufactured part’s mechanical qualities and decrease distortion and shrinking. Due to the extensive application in different sectors, a large amount of waste is generated after the life cycle of the carbon fiber polymer composites, which is obtained from different industry sectors (such as airplane industry and automobile industry), and recycling of the carbon fiber is the only solution to decrease the energy impact over the life cycle. While research toward the use of the fibers as a reinforcement has been reported (Ghabezi et al., 2024; Shirasu et al., 2024; Sam-Daliri et al., 2022; Almeshari et al., 2023; Yang et al., 2022; Ghabezi et al., 2022), studies on the samples printed using the reinforcing with the recycled carbon fiber in the polymer are currently lacking. Some research studies that focus on the utilization of the rCF as a reinforcement with the different polymer composites have been reported (Tian et al., 2017b; Su et al., 2022b), but, to the best of our knowledge, we cannot find any published research in which samples are manufactured using the embedded recycled carbon fiber with polyamide-12 in the FDM printer. To address this knowledge gap, the part is printed by employing the rCF as reinforcement at varying percentages (10% and 15%) in polyamide 12 matrix materials using the FDM printer. The effect of the part printed using the FDM printer at different rCF contents as a reinforcement in the PA12 composites is presented.
The aim of this study is to examine the mechanical properties of parts manufactured using recycled carbon fiber-reinforced PA12 and unreinforced PA12 matrix materials in the FDM printer. This investigation additionally intended to explore the impact of additives (e.g., recycled carbon fibers) by comparing the performance of unreinforced and reinforced nylon printed specimens obtained using the produced filament using the filament extruder. The paper seeks to investigate the production of filaments by utilizing rCF/PA12 powder with a filament extruder, which is subsequently used in FDM printers to create specimens under various printing parameters. Moreover, this study demonstrates that rCF can serve as a substitute for virgin carbon fibers as long as the initial shorter fiber dimensions do not compromise performance. Consequently, filaments are produced using unreinforced PA12 matrix materials as a baseline, along with filaments containing 10 and 15 wt% of rCF as a reinforcement in the PA12 polymer matrix composite materials, without any additional processing steps following the recycling procedure. The influence of the rCF content weight on the mechanical performance of the fabricated parts was assessed through three-point bending testing. The potential of utilizing rCF as a reinforcing material in polyamide 12 matrix materials was showcased by producing filaments (with a diameter of 1.75 ± 0.05 mm) using a filament extruder. The manufacturing process of the 3D-printed PA12 and its rCF-PA12 composites by the fabrication of the filament using the filament extruder can benefit from the broad conclusion derived from the results, and comparable patterns are anticipated for the other composite materials using the rCF as a reinforcement in the fused deposition technology. This study adopts a strategy that encourages waste reduction of carbon fiber polymer composites while simultaneously investigating novel advantages for improving the qualities, printability, and potentials of use of recycled carbon fiber materials with the different polymers.
2 Materials and methods
2.1 Materials
Polyamide-12, which is supplied by the Foshan Glink intelligent technology Co., Ltd., Guangdong, China, is made from granules and antioxidants. The properties of the PA12 powder, which is supplied by the supplier, are illustrated in Table 1. The recycled carbon fiber, which is embedded as a reinforcement, is supplied by the ELG United Kingdom-based recycling company. After the airplane has reached the end of its useful life, the rCF is retrieved using a thermal recovery procedure known as pyrolysis. Pyrolysis is a technique that includes warming carbon fiber-epoxy composites at elevated temperatures (between 350 and 700°C) in inert environments (such as nitrogen) without the presence of oxygen (to avoid charring) to break down the composite into gas, oil, and fiber parts (Naqvi et al., 2018). The results of scanning electron microscopy (SEM) of the rCF are illustrated in Figure 1. Based on Figure 1, the average length of the rCF measured using the fiber was 98.125 μm. Additionally, the mean diameter of the fibers was calculated by measuring the diameter of the fiber, yielding an average diameter of about 7.92 μm, as shown in Figures 2A, B. The properties of rCF is shown in Table 1.
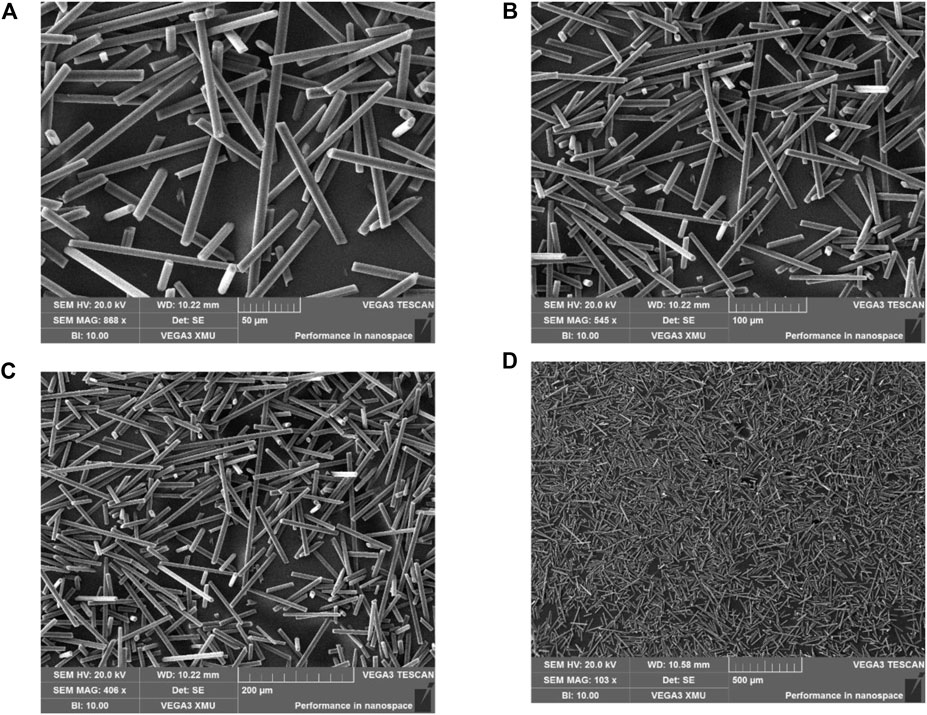
Figure 1. SEM showing rCF with the different resolutions of (A) 50 μm, (B) 100 μm, (C) 200 μm, and (D) 500 μm.
2.2 Filament fabrications
Starting materials (neat PA12 and rCF) were first dried in a vacuum oven at the temperature of 80°C for approximately 10 h. The complete manufacturing process of the filaments is shown in Figure 3. The fiber and PA12 were blended in different percentages of the weight of fiber (10% and 15%), as listed in Table 2. The ball milling machine is used for equal dispersion of the carbon fiber in the polyamide 12 matrix materials in which the ball milling was operated at the speed of approximately 120 rpm for approximately 1 h. After that, the composite materials were embedded into the hopper Noztek twin extruder, and the three-temperature zone and screw speed of the filament extruder were set for achieving the desired diameter of approximately 1.75 ± 0.05 mm. Equally dispersed rCF as the reinforcement in the PA12 powder composite materials were put into an extruder at carbon fiber contents of 10 and 15 wt% to extrude the PA12–rCF10 and PA12–rCF15 composite filaments with a diameter of approximately 1.75 mm ± 0.05 mm.
At the start of the experiment, a three-phase temperature zone from 170°C to 200°C and the extruder motor speed of approximately 19 rpm were used, but the produced filaments of the composites were higher than 1.75 ± 0.05 mm. Various trials of the experiments were performed for achieving the exact diameters by changing the phase temperature and screw speed of the filament’s extruder. After increasing the three-phase zone temperature to approximately 200–240 and the speed of the filament’s extruder to 21 rpm, the filaments obtained had the diameter of approximately 1.75 ± 0.05 mm, which was observed by the diameter gage and a Vernier caliper. Composite filaments produced homogeneously from the tip were sequentially transferred via the air-cooling fan and diameter gage before being placed on the traction device for rolling on the spool. A Vernier caliper was also employed to verify the diameter homogeneity while extruding. The whole process was performed again to create the remaining filaments of the composite’s materials and pure PA12. The fabricated composite filament was dried in an oven for 24 h at 80°C to remove the moisture content. The parameters used for achieving the desired diameter of the filaments are illustrated in Table 3.
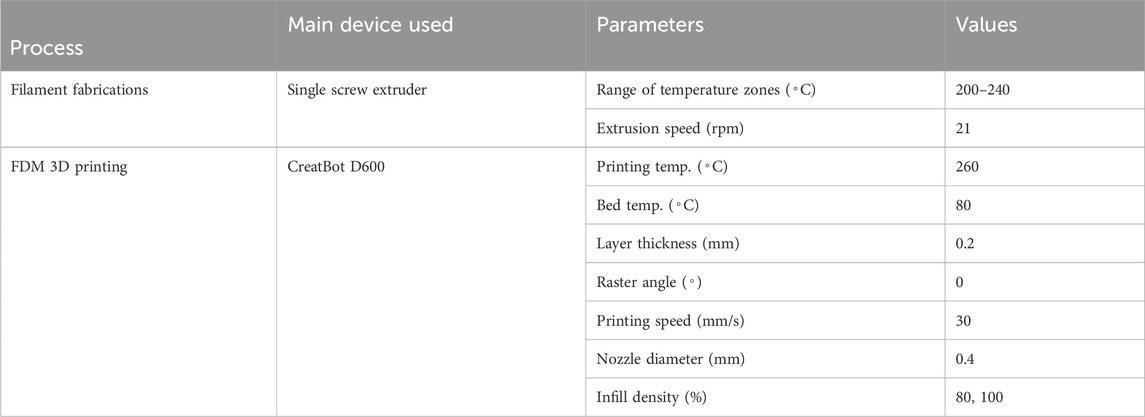
Table 3. Process parameters for making filaments of the composite’s materials and manufactured parts.
2.3 Mix percentage and preparation of the samples
The complete fabrication process of the composite’s materials having different contents of rCF (0%, 10%, and 15%) as a reinforcement in polyamide 12 is shown in Figure 3, and the more detailed parameters of the printing are illustrated in Table 3. The flexural specimens were manufactured by utilizing the filaments with a diameter of 1.75 ± 0.05 mm having 10 wt% and 15 wt% rCF in the polyamide-12 matrix material composites using the CreatBot D600 FDM 3D printer, and the dimensions of the flexural specimens are shown in Figure 5A. The composition of the produced filament using the rCF as a reinforcement is illustrated in Table 2. The samples were designed using the CAD program SolidWorks, which is able to be sliced into STL files. The samples’ virtual models were sliced, and the pattern route was altered with 3D slicer software to produce a G-code that could be recognized by the 3D printer. The FDM 3D printer is used for manufacturing flexural specimens, as illustrated in Figure 3. The quality of the produced samples is substantially influenced by the printing parameters of the FDM printer (Nguyen et al., 2024). Some printing parameters are considered secondary, which are kept constant during printing of all the samples: these are layer thickness 0.2 mm, printing speed 30 mm/s, nozzle diameter 0.4 mm, and raster angle 0°. For analyzing the printing effect of the infill density, two different infill densities are used for manufacturing the specimens using the FDM printer in each reinforcement percentage. The manufactured specimens with dimensions of approximately (80 mm × 10 mm × 4 mm) were selected according to the GB/T9341-2008 standard for flexural test (Huang et al., 2020). The printing parameters of the printing specimens are shown in Table 3.
2.4 Material characterization method and equipment
The impregnation performance of the fabricated filaments that are produced using rCF-reinforced PA12 composites is investigated by observing in a Tescan VEGA3 scanning electron microscope (SEM). The measurements are accompanied at 5 kV using secondary electrons after being sputtered with gold coating for 100 s at 20 mA. The operating conditions of the acceleration voltage and current were 30 KV and 80 μA during the scanning, respectively. Filaments of the rCF-PA12 polymer composite and pure polyamide 12 are observed to analyze the carbon fiber orientation and the presence of voids inside the filament.
2.5 Testing equipment
Flexural tests of the 3D-printed specimens were conducted according to the ASTM D790 standards on the universal testing machine. The three-point bending test was performed in an ambient atmosphere to analyze the performance of the samples. The specimens were tested under a 2 mm/min constant rate, and the distance between two supports was set at 64 mm. Each test included two different infill density percentage specimens (80% and 100%) and two different contents of the recycled carbon fiber used. The flexural stress of the printed specimens was calculated using the following equation:
where
3 Result and discussion
3.1 Surface morphology and physical properties of the filament
The fracture surface of the extruded filaments was examined using SEM to examine rCF-dispersion and adherence to the PA12 matrix. SEM was used to detect and validate the fabricated filament’s internal structure quality and investigate the sample’s fracture mechanism after the testing. The samples of the filament were coated with gold palladium target and taped with conductive carbon. Figure 4 illustrates the images at different magnifications of the three prepared filaments’ composition of pure polyamide, PA12–rCF10, and PA12–rCF15 composite materials. Voids and gaps were observed in the filaments manufactured using pure PA12 materials. Porosity is present between the filaments, as illustrated in Figures 4A, D, G. The gaps were randomly dispersed across the filaments and were mostly circular, implying that they formed due to the formation of bubbles throughout the extrusion. Figures 4B, E, H show the surface of the filament fabricated using the PA12–rCF10 composite materials at different magnifications for analyzing the internal structural quality of the filament. The microscopic image shows that voids are present in the filaments’ breakage section, which negatively impacts the performance of the printed parts using this filament. Several holes were present in the filaments of the PA12–rCF10 composites, which led the fiber to be pulled out from the PA12 matrix materials, which lead to enhancement of the flexural strength of the printed part, as shown in Figure 4E. The spaces in the composite filaments are most probably caused by air bubbles produced during the carbon fibers’ insertion into the PA12 matrix material.
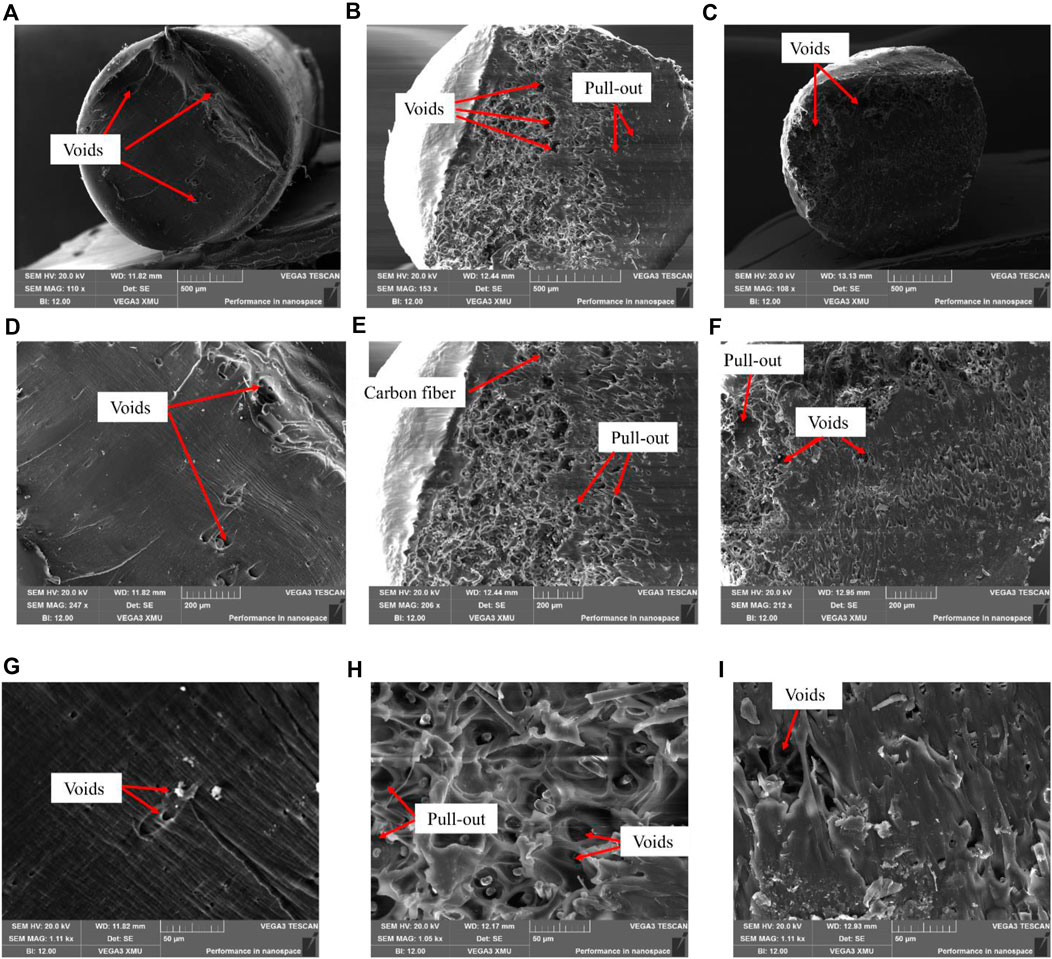
Figure 4. The fracture surface of the filament has (A) PA12 with a magnification of 500 μm, (B) PA12–rCF10 with a magnification of 500 μm, (C) PA12–rCF15 with a magnification of 500 μm, (D) PA12 with a magnification of 200 μm, (E) PA12–rCF10 with a magnification of 200 μm, (F) PA12–rCF15 with a magnification of 200 μm, (G) PA12 with a magnification of 50 μm, (H) PA12–rCF10 with a magnification of 50 μm, and (I) PA12–rCF15 with a magnification of 50 μm.
The composite material filaments that are fabricated using PA12–rCF15 have lower voids and gaps on the surface of the filaments as compared to the pure PA12 filament, as shown in Figures 4C, F, I. A homogenous filler distribution and an excellent connection between the fibers and the matrix were required for optimal mechanical performance, printability, and thermal conductivity (Spoerk et al., 2019; Kada et al., 2016). The inter-bead voids were reduced in the filament of PA12-rCF15 due to the homogeneous dispersion of the fiber, which led to the strong interfacial bond between the matrix materials and rCF.
3.2 Flexural strength of the 3D-printed specimen
3.2.1 Effect of rCF content on the flexural strength
Flexural tests were performed to determine the flexible characteristics of the manufactured samples for each composite’s material with different contents of rCF (polyamide-12, PA12–rCF10 composite, and PA12–rCF15 composite). The flexural specimens before and after the fracture are illustrated in Figure 5, and the results of the flexural strength are plotted in Figures 6A, B, while all important values of the flexural strength are summarized in Table 4. The SEM image of the fracture surface after the testing of flexural specimens is illustrated in Figure 7. From Table 4, it is found that the flexural strength is increased by increasing the percentage of the rCF from 0%, 10%, to 15% in the polyamide-12 matrix, which might be due to the strong adhesion bond between the fiber and polyamide-12 matrix materials, as illustrated in Figures 7A–C. Due to the strong adhesion bonding between the filler and matrix materials, the porosity in the printed specimens is decreased by increasing the content of the rCF in the PA12 composites. Highest flexural strength of the printed specimens was observed in specimens with 15 percent of rCF.
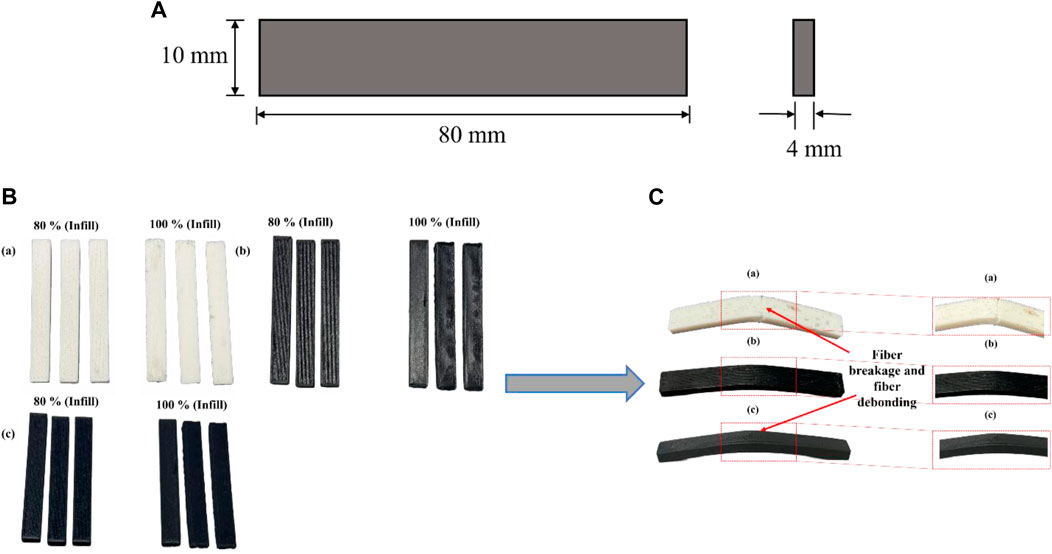
Figure 5. Flexural test of the 3D printed specimens of rCFRP specimens: (A) Dimension of the flexural specimen; (B) Printed specimens using the different composite materials of (a) PA12 specimen with the 80% and 100% infill density, (b) PA12-rCF10 specimen with the 80% and 100% infill density, (c) PA12-rCF15 specimen with the 80% and 100% infill density; (C) Fracture specimen using the different composites materials of, (a) Post-tested specimens of PA12 showing failure modes, (b) Post-tested specimens of PA12/rCF10 showing failure modes, (c) Post-tested specimens of PA12-rCF15 showing failure modes.
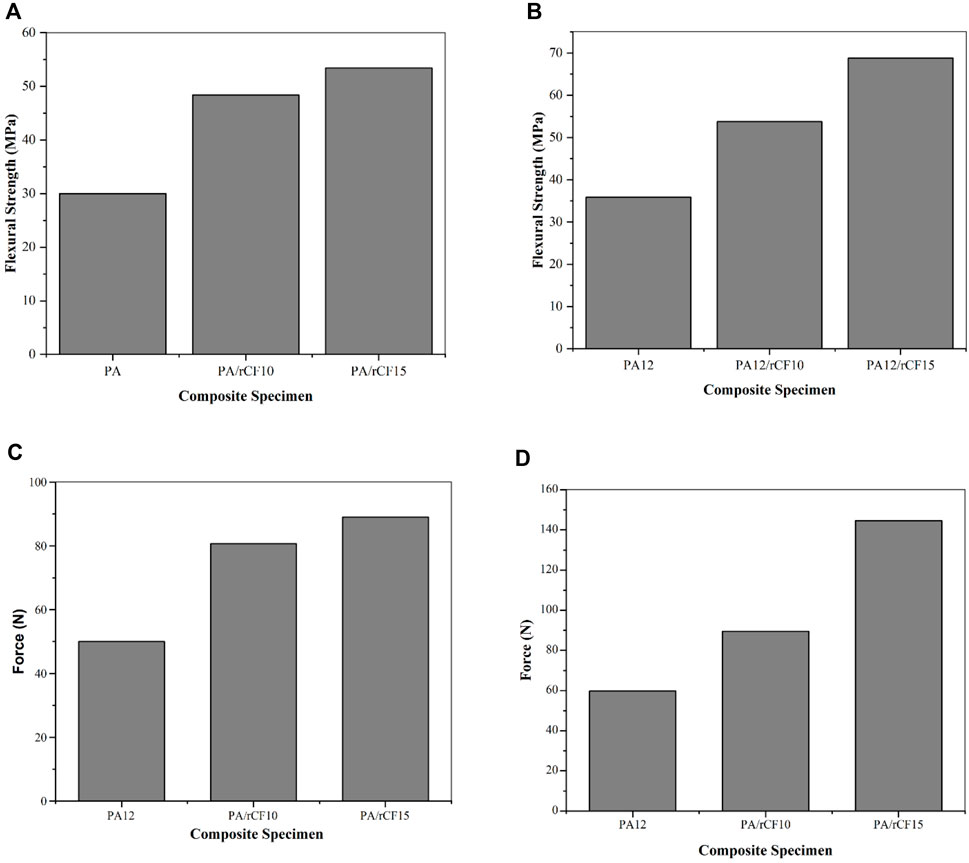
Figure 6. Properties of the printed specimen using the PA12 matrix materials PA12–rCF10 and PA12–rCF15 using the (A) flexural strength of specimens having 80% of infill density, (B) flexural strength of specimens having 100% of infill density, (C) force of specimens having 80% of infill density, (D) force of specimens having 100% of infill density.
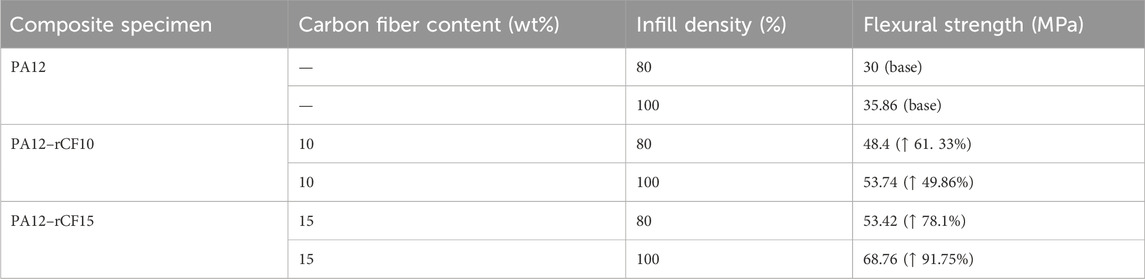
Table 4. Flexural strength of the composite’s material with the different contents of reinforcement of rCF.
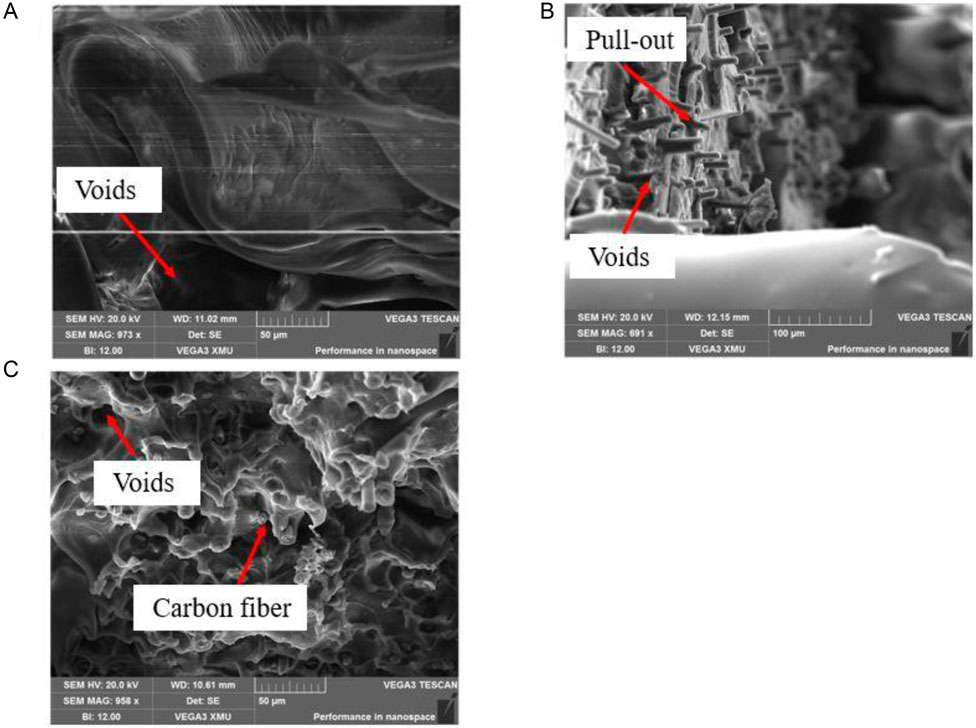
Figure 7. The fracture surface of the flexural-tested specimen has the composites of (A) PA12, (B) PA12–rCF10, and (C) PA12-rCF15.
After adding 15 wt% of rCF to the PA12 composite materials, the three-point bending test showed an increase in flexural strength from 30 to 68.78 MPa. Likewise, incorporating 10 wt% of rCF in the PA12 composites resulted in an improvement from 30 to 53.74 MPa. The specimens fabricated using PA12–rCF15, with a 15 wt% of rCF, showed the highest improvement of 91.75%, while PA12–rCF10 with 10 wt% of rCF exhibited a significant 49.86% enhancement in flexural strength compared to specimens made with unreinforced composite materials at 100% infill density. This is because a high force is required to fracture the reinforced composite specimen as compared to the unreinforced counterpart, as shown in Figures 6C, D. The low strength observed in PA12–rCF10 specimens is because of the poor load transfer observed in the low content of the carbon fiber, as observed in the literature (Sanjeevi et al., 2021; Su et al., 2022c). The flexural strength achieved in PA12–rCF15 specimens comparable the strength achieved when using milled carbon fiber-reinforced recycled PA12 produced through selective laser sintering (Wang et al., 2018). This improvement is more effective than the flexural strength examined by Banjo et al. (2022) using the nylon-6 copolymer reinforced with milled vCF fabricated in the Markforged FDM printer.
Finally, 3D printing rCF not only enables CFRP composite fabrication but also represents a step toward advancing the circular economy of these composites. Consequently, the circular economy model could yield economic benefits by reducing the raw material cost of 3D-printed CFRP parts. The cost of rCF is anticipated to range at $13–19/kg, while vCF incurs a substantial cost ($33–66/kg) due to the high power consumption needed for its production (Lefeuvre et al., 2017). Overall, the integration of 3D printing offers a promising avenue for the circular manufacturing of CFRP by utilizing CFRP waste as the raw material for producing rCFRP components. This process contributes to closing the loop and promoting sustainable CFRP production.
3.2.2 Effect of the infill densities on strength
The effect of the infill densities on the printed specimens using rCF as a reinforcement with the different percentages is shown in Figure 6. The inclusion of the carbon fiber increased the elasticity of the filament in nature. The improvement in the infill density results in a higher amount of the materials being used to fill the interior of the specimens, which leads to the uniform distribution of the carbon fiber throughout the PA12 matrix material. Rodríguez-Reyna et al. (2022a) studied and worked with the nylon–carbon fiber at the different infill densities and observed the performance of the printed parts. They investigated that an increase in the infill density has a positive effect on the performance of the specimen. The specimens manufactured using the PA12 materials increased the flexural strength of the printed part from 30 to 35.86 MPa by increasing the infill densities of the part from 80% to 100%, as illustrated in Figure 6. The same was also observed in the specimens printed using the reinforcement with rCF in the PA12 composite materials. The part printed using 100% of the infill density improved the flexural strength by approximately 28.72% as compared to the part printed using 80% infill density with the same parameters observed for the PA12–rCF15 composite material. This is evidence that the strong interfacial bond between the rCF and PA12 matrix materials is observed at 100% infill density due to the uniform distribution of the rCF in the PA12 matrix materials. Therefore, it is found that the infill densities have a significant impact on the performance of the part printed using the FDM printers. By increasing the infill density of the materials, the greater quantity of material utilized, more uniform distribution of the material, a decrease in gaps or spaces, and stronger bonds among the layers, raising the infill density can improve the performance of 3D-printed specimens. Overall, the results presented in this study encourage the usability of rCF in various applications by employing it as a reinforcement fiber material in polymer composite materials substituting virgin carbon fiber.
4 Conclusion
The impact of the parts manufactured using the rCF-reinforced PA12 composites on the flexural strength was investigated at different percentages of the rCF content (0, 10, and 15%). 3D printing filaments using rCF-reinforced polymer composites having a diameter of approximately 1.75 ± 0.05 mm were made and used for flexural specimen fabrication. The morphology of specimens was also studied using SEM to examine the fracture and voids of the composite specimens. The following conclusion can be drawn based on the research result:
⁃ It was found that the flexural strength of the part fabricated using the rCF-PA12 composite improves compared to that of the parts made by unreinforced PA12 materials.
⁃ The flexural strength of specimens having PA12–rCF15 (15% of the rCF) is 68.76 MPa at 100% infill density. Thus, flexural strength of the part having 15% rCF was improved by 91.75% when compared to the part printed using pure PA12.
⁃ It is revealed that specimens printed by employing 10% of rCF in the FDM printer was improved by 49.86% as compared to the part printed using the unreinforced PA12 materials.
⁃ It is found that infill densities 80% and 100% have a significant impact on the performance of the printed parts. Specimens fabricated using the 100% infill density improved the flexural strength owing to a decrease in the voids and gaps between the carbon fiber and polymer as compared to the parts fabricated using 80% of infill densities.
Future research will focus on the optimization of the recycling technique of the CFRP; thus, it will be able to achieve higher performance of rCF, which leads to providing better performance of the parts printed using the rCF. Additional aspects, including surface treatment (i.e., coupling agent, oxidation, and alkalization) for enhancing interfacial shear strength and the utilization of recovered polyamide, will be considered further. The AM of the rCF-reinforced polymer composites with varying contents of reinforcement in the different polymers to observe other mechanical properties needs further work. Furthermore, this study adds to our understanding of how to turn waste materials into high-quality, mechanically superior 3D-printed goods. The main factor propelling continued expansion is the industrial adoption of 3D printing technology and manufactured components. By employing CFRP trash as the raw material to create the complicated 3D CFRP parts, 3D printing stimulates the CFRP circular manufacturing process and closes the loop to enable the manufacture of CFRP in a sustainable manner.
Data availability statement
The raw data supporting the conclusions of this article will be made available by the authors, without undue reservation.
Author contributions
MA: data curation, formal analysis, investigation, resources, visualization, and writing–original draft. AN: conceptualization, methodology, project administration, supervision, validation, and writing–review and editing.
Funding
The author(s) declare that no financial support was received for the research, authorship, and/or publication of this article.
Conflict of interest
The authors declare that the research was conducted in the absence of any commercial or financial relationships that could be construed as a potential conflict of interest.
The reviewer ZA declared a shared affiliation, with no collaboration, with one of the authors, MA, to the handling editor at the time of the review.
Publisher’s note
All claims expressed in this article are solely those of the authors and do not necessarily represent those of their affiliated organizations, or those of the publisher, the editors, and the reviewers. Any product that may be evaluated in this article, or claim that may be made by its manufacturer, is not guaranteed or endorsed by the publisher.
References
Akbar, A., and Liew, K. M. (2020). Assessing recycling potential of carbon fiber reinforced plastic waste in production of eco-efficient cement-based materials. J. Clean. Prod. 274, 123001. doi:10.1016/j.jclepro.2020.123001
Almeshari, B., Junaedi, H., Baig, M., and Almajid, A. (2023). Development of 3D printing short carbon fiber reinforced polypropylene composite filaments. J. Mater. Res. Technol. 24, 16–26. doi:10.1016/j.jmrt.2023.02.198
Banjo, A. D., Agrawal, V., Auad, M. L., and Celestine, A.-D. N. (2022). Moisture-induced changes in the mechanical behavior of 3D printed polymers. Compos. Part C. Open Access 7, 100243. doi:10.1016/j.jcomc.2022.100243
Belei, C., and Amancio-Filho, S. T. (2023). Influence of raster orientation and feeding rate on the mechanical properties of short carbon fiber-reinforced polyamide printed by fused-filament fabrication. 3D Print. Addit. Manuf. doi:10.1089/3dp.2023.0173
Bledzki, A. K., Seidlitz, H., Goracy, K., Urbaniak, M., and Rösch, J. J. (2021). Recycling of carbon fiber reinforced composite polymers-review-Part 1: volume of production, recycling technologies, legislative aspects. Polym. (Basel) 13, 300. doi:10.3390/polym13020300
Cheng, H., Guo, L., Qian, Z., Sun, R., and Zhang, J. (2021). Remanufacturing of recycled carbon fiber-reinforced composites based on fused deposition modeling processes. Int. J. Adv. Manuf. Technol. 116, 1609–1619. doi:10.1007/s00170-021-07473-w
Dong, W., Bao, C., Lu, W., Liu, R., Ma, H., Li, S., et al. (2023). Fabrication of a continuous carbon fiber-reinforced phenolic resin composites via in situ-curing 3D printing technology. Compos. Commun. 38, 101497. doi:10.1016/j.coco.2023.101497
Ghabezi, P., Flanagan, T., and Harrison, N. (2022). Short basalt fibre reinforced recycled polypropylene filaments for 3D printing. Mater. Lett. 326, 132942. doi:10.1016/j.matlet.2022.132942
Ghabezi, P., Sam-Daliri, O., Flanagan, T., Walls, M., and Harrison, N. M. (2024). Circular economy innovation: a deep investigation on 3D printing of industrial waste polypropylene and carbon fibre composites. Resour. Conservation Recycl. 206, 107667. doi:10.1016/j.resconrec.2024.107667
Giani, N., Mazzocchetti, L., Benelli, T., Picchioni, F., and Giorgini, L. (2022). Towards sustainability in 3D printing of thermoplastic composites: evaluation of recycled carbon fibers as reinforcing agent for FDM filament production and 3D printing. Compos. Part A Appl. Sci. Manuf. 159, 107002. doi:10.1016/j.compositesa.2022.107002
Hengstermann, M., Hasan, M. M. B., Scheffler, C., Abdkader, A., and Cherif, C. (2021). Development of a new hybrid yarn construction from recycled carbon fibres for high-performance composites. Part III: influence of sizing on textile processing and composite properties. J. Thermoplast. Compos. Mater. 34, 409–430. doi:10.1177/0892705719847240
Holmes, M. (2018). Recycled carbon fiber composites become a reality. Reinf. Plast. 62, 148–153. doi:10.1016/j.repl.2017.11.012
Huang, H., Liu, W., and Liu, Z. (2020). An additive manufacturing-based approach for carbon fiber reinforced polymer recycling. CIRP Ann. 69, 33–36. doi:10.1016/j.cirp.2020.04.085
J. The Society Of Fiber Science And Te (2016). in High-performance and specialty fibers: concepts, technology and modern applications of man-made fibers for the future (Tokyo: Springer Japan). doi:10.1007/978-4-431-55203-1
Kada, D., Koubaa, A., Tabak, G., Migneault, S., Garnier, B., and Boudenne, A. (2016). Tensile properties, thermal conductivity, and thermal stability of short carbon fiber reinforced polypropylene composites. Polym. Compos. 39. doi:10.1002/pc.24093
Lefeuvre, A., Garnier, S., Jacquemin, L., Pillain, B., and Sonnemann, G. (2017). Anticipating in-use stocks of carbon fiber reinforced polymers and related waste flows generated by the commercial aeronautical sector until 2050. Resour. Conservation Recycl. 125, 264–272. doi:10.1016/j.resconrec.2017.06.023
Li, H., Liu, B., Ge, L., Chen, Y., Zheng, H., and Fang, D. (2021). Mechanical performances of continuous carbon fiber reinforced PLA composites printed in vacuum. Compos. Part B Eng. 225, 109277. doi:10.1016/j.compositesb.2021.109277
Li, X., Bai, R., and McKechnie, J. (2016). Environmental and financial performance of mechanical recycling of carbon fibre reinforced polymers and comparison with conventional disposal routes. J. Clean. Prod. 127, 451–460. doi:10.1016/j.jclepro.2016.03.139
Liu, W., Huang, H., Zhu, L., and Liu, Z. (2021). Integrating carbon fiber reclamation and additive manufacturing for recycling CFRP waste. Compos. Part B Eng. 215, 108808. doi:10.1016/j.compositesb.2021.108808
Love, L. J., Kunc, V., Rios, O., Duty, C. E., Elliott, A. M., Post, B. K., et al. (2014). The importance of carbon fiber to polymer additive manufacturing. J. Mater. Res. 29, 1893–1898. doi:10.1557/jmr.2014.212
Maqsood, N., and Rimašauskas, M. (2022). Influence of printing process parameters and controlled cooling effect on the quality and mechanical properties of additively manufactured CCFRPC. Compos. Commun. 35, 101338. doi:10.1016/j.coco.2022.101338
McConnell, V. P. (2010). Launching the carbon fibre recycling industry. Reinf. Plast. 54, 33–37. doi:10.1016/S0034-3617(10)70063-1
Naqvi, S. R., Prabhakara, H. M., Bramer, E. A., Dierkes, W., Akkerman, R., and Brem, G. (2018). A critical review on recycling of end-of-life carbon fibre/glass fibre reinforced composites waste using pyrolysis towards a circular economy. Resour. Conservation Recycl. 136, 118–129. doi:10.1016/j.resconrec.2018.04.013
Nasirov, A., Gupta, A., Hasanov, S., and Fidan, I. (2020). Three-scale asymptotic homogenization of short fiber reinforced additively manufactured polymer composites. Compos. Part B Eng. 202, 108269. doi:10.1016/j.compositesb.2020.108269
Nguyen, P. Q. K., Panta, J., Famakinwa, T., (Chunhui) Yang, R., Ahmed, A., Stapleton, M., et al. (2024). Influences of printing parameters on mechanical properties of recycled PET and PETG using fused granular fabrication technique. Polym. Test. 132, 108390. doi:10.1016/j.polymertesting.2024.108390
Ning, F., Cong, W., Qiu, J., Wei, J., and Wang, S. (2015). Additive manufacturing of carbon fiber reinforced thermoplastic composites using fused deposition modeling. Compos. Part B Eng. 80, 369–378. doi:10.1016/j.compositesb.2015.06.013
Ramachandran, K., Nasr Azadani, M., Ravichandran, P., Shivaprakash, N. B., Obi, M., and Gnanasagaran, C. L. (2024). Failure mechanics of fused filament fabricated nylon/carbon-reinforced composites. Prog. Addit. Manuf. doi:10.1007/s40964-024-00565-5
Rimašauskas, M., Jasiūnienė, E., Kuncius, T., Rimašauskienė, R., and Cicėnas, V. (2022). Investigation of influence of printing parameters on the quality of 3D printed composite structures. Compos. Struct. 281, 115061. doi:10.1016/j.compstruct.2021.115061
Rodríguez-Reyna, S. L., Mata, C., Díaz-Aguilera, J. H., Acevedo-Parra, H. R., and Tapia, F. (2022a). Mechanical properties optimization for PLA, ABS and Nylon + CF manufactured by 3D FDM printing. Mater. Today Commun. 33, 104774. doi:10.1016/j.mtcomm.2022.104774
Rodríguez-Reyna, S. L., Mata, C., Díaz-Aguilera, J. H., Acevedo-Parra, H. R., and Tapia, F. (2022b). Mechanical properties optimization for PLA, ABS and Nylon + CF manufactured by 3D FDM printing. Mater. Today Commun. 33, 104774. doi:10.1016/j.mtcomm.2022.104774
Saleh, M., Anwar, S., AlFaify, A. Y., Al-Ahmari, A. M., and Abd Elgawad, A. E. E. (2024). Development of PLA/recycled-desized carbon fiber composites for 3D printing: thermal, mechanical, and morphological analyses. J. Mater. Res. Technol. 29, 2768–2780. doi:10.1016/j.jmrt.2024.01.267
Sam-Daliri, O., Ghabezi, P., Flanagan, T., Finnegan, W., Mitchell, S., and Harrison, N. (2022). Recovery of particle reinforced composite 3D printing filament from recycled industrial polypropylene and glass fibre waste. doi:10.11159/icmie22.143
Sanjeevi, S., Shanmugam, V., Kumar, S., Ganesan, V., Sas, G., Johnson, D. J., et al. (2021). Effects of water absorption on the mechanical properties of hybrid natural fibre/phenol formaldehyde composites. Sci. Rep. 11, 13385. doi:10.1038/s41598-021-92457-9
Sauer, M., Kühnel, M., and Elma, W. (2018) “Report - composites market report 2018 - market developments, trends, outlook and challenges,” in Carbon composite. Available at: https://www.carbon-connected.de.
Shah, N., Fehrenbach, J., and Ulven, C. A. (2019). Hybridization of hemp fiber and recycled-carbon fiber in polypropylene composites. Sustainability 11, 3163. doi:10.3390/su11113163
Shirasu, K., Yamaguchi, Y., Hoshikawa, Y., Kikugawa, G., Tohmyoh, H., and Okabe, T. (2024). Micromechanics study of short carbon fiber-reinforced thermoplastics fabricated via 3D printing using design of experiments. Mater. Sci. Eng. A 891, 145971. doi:10.1016/j.msea.2023.145971
Sommer, V., and Walther, G. (2021). Recycling and recovery infrastructures for glass and carbon fiber reinforced plastic waste from wind energy industry: a European case study. Waste Manag. 121, 265–275. doi:10.1016/j.wasman.2020.12.021
Spoerk, M., Savandaiah, C., Arbeiter, F., Sapkota, J., and Holzer, C. (2019). Optimization of mechanical properties of glass-spheres-filled polypropylene composites for extrusion-based additive manufacturing. Polym. Compos. 40, 638–651. doi:10.1002/pc.24701
Stewart, R. (2011). Thermoplastic composites — recyclable and fast to process. Reinf. Plast. 55, 22–28. doi:10.1016/S0034-3617(11)70073-X
Su, N., Pierce, R. S., Rudd, C., and Liu, X. (2022a). Comprehensive investigation of reclaimed carbon fibre reinforced polyamide (rCF/PA) filaments and FDM printed composites. Compos. Part B Eng. 233, 109646. doi:10.1016/j.compositesb.2022.109646
Su, N., Pierce, R. S., Rudd, C., and Liu, X. (2022b). Comprehensive investigation of reclaimed carbon fibre reinforced polyamide (rCF/PA) filaments and FDM printed composites. Compos. Part B Eng. 233, 109646. doi:10.1016/j.compositesb.2022.109646
Su, N., Pierce, R. S., Rudd, C., and Liu, X. (2022c). Comprehensive investigation of reclaimed carbon fibre reinforced polyamide (rCF/PA) filaments and FDM printed composites. Compos. Part B Eng. 233, 109646. doi:10.1016/j.compositesb.2022.109646
Su, N., Zhu, C., and Chen, X. (2024). Investigation of tensile properties of FDM-printed reclaimed carbon fiber reinforced reclaimed polyamide-6 composites (rCF/rPA) via various densities of infill patterns. J. Phys. Conf. Ser. 2679, 012033. doi:10.1088/1742-6596/2679/1/012033
Tekinalp, H. L., Kunc, V., Velez-Garcia, G. M., Duty, C. E., Love, L. J., Naskar, A. K., et al. (2014). Highly oriented carbon fiber–polymer composites via additive manufacturing. Compos. Sci. Technol. 105, 144–150. doi:10.1016/j.compscitech.2014.10.009
Tian, X., Liu, T., Wang, Q., Dilmurat, A., Li, D., and Ziegmann, G. (2017a). Recycling and remanufacturing of 3D printed continuous carbon fiber reinforced PLA composites. J. Clean. Prod. 142, 1609–1618. doi:10.1016/j.jclepro.2016.11.139
Tian, X., Liu, T., Wang, Q., Dilmurat, A., Li, D., and Ziegmann, G. (2017b). Recycling and remanufacturing of 3D printed continuous carbon fiber reinforced PLA composites. J. Clean. Prod. 142, 1609–1618. doi:10.1016/j.jclepro.2016.11.139
Wang, L., Kiziltas, A., Mielewski, D. F., Lee, E. C., and Gardner, D. J. (2018). Closed-loop recycling of polyamide12 powder from selective laser sintering into sustainable composites. J. Clean. Prod. 195, 765–772. doi:10.1016/j.jclepro.2018.05.235
Wang, Q., Zhang, Q., Kang, Y., Wang, Y., and Liu, J. (2023). An investigation of preparation of continuous carbon fiber reinforced PLA prepreg filament. Compos. Commun. 39, 101530. doi:10.1016/j.coco.2023.101530
Yang, Y., Boom, R., Irion, B., van Heerden, D.-J., Kuiper, P., and de Wit, H. (2012). Recycling of composite materials. Chem. Eng. Process. Process Intensif. 51, 53–68. doi:10.1016/j.cep.2011.09.007
Keywords: recycled carbon fiber, recycled carbon fiber-reinforced polyamide-12 composite, additive manufacturing, flexural properties, fused deposition modeling, Sustainability
Citation: Ateeq M and Nazir A (2024) Upcycling end-of-life carbon fiber in high-performance CFRP composites by the material extrusion additive manufacturing process. Front. Mech. Eng. 10:1452778. doi: 10.3389/fmech.2024.1452778
Received: 21 June 2024; Accepted: 13 September 2024;
Published: 08 October 2024.
Edited by:
Kanak Kalita, Vel Tech Dr. RR and Dr. SR Technical University, IndiaReviewed by:
Kamran A. Khan, Khalifa University, United Arab EmiratesPouyan Ghabezi, University of Galway, Ireland
Zulfiqar Ali, The University of Hong Kong, Hong Kong SAR, China
Riad Ramadani, University of Pristina, Albania
Copyright © 2024 Ateeq and Nazir. This is an open-access article distributed under the terms of the Creative Commons Attribution License (CC BY). The use, distribution or reproduction in other forums is permitted, provided the original author(s) and the copyright owner(s) are credited and that the original publication in this journal is cited, in accordance with accepted academic practice. No use, distribution or reproduction is permitted which does not comply with these terms.
*Correspondence: Aamer Nazir, YWFtZXIubmF6aXJAa2Z1cG0uZWR1LnNh