- 1Department of Mechanical Engineering, Amity School of Engineering and Technology, Amity University Uttar Pradesh, Noida, India
- 2Federation University Australia, Ballarat, VIC, Australia
- 3Sat Kabir Institute of Technology and Management, Bahadurgarh, Haryana, India
- 4Department of Mechanical Engineering, School of Engineering and Technology, JECRC University, Jaipur, India
- 5Department of Mechanical Engineering, Yeshwantrao Chavan College of Engineering, Nagpur, India
- 6Department of VLSI Microelectronics, Saveetha School of Engineering, Saveetha Institute of Medical and Technical Sciences (SIMATS), Saveetha University, Chennai, TN, India
- 7Department of Mechanical and Industrial Engineering, Manipal Institute of Technology, Manipal Academy of Higher Education, Manipal, Udupi, India
The adoption of Lean Six Sigma has become increasingly widespread in manufacturing industries worldwide. It is a powerful methodology for optimizing operational efficiency and quality, leading to increased productivity, reduced costs, and higher customer satisfaction. However, implementing LSS effectively, especially in Indian manufacturing sectors striving for sustainability, presents significant challenges. In this paper, the authors have presented the critical factors that impede the successful integration of sustainable Lean Six Sigma practices within the Indian manufacturing landscape. Through a systematic review of existing literature and empirical studies, authors have identified the eighteen failure factors. To prioritize these factors, authors have employed the Best Worst Method (BWM), a decision-making tool that aids in ranking factors based on their importance and impact. It is a multi-criterion decision-making (MCDM) methodology to solve different types of fact-based decision–making problems. This method involves initially identifying the best (most important) and worst (least important) factors, followed by pairwise comparisons to determine their relative significance. Results depict that “Failure of leadership to inspire and motivate”, “Lack of well-defined framework for executing initiatives”, and “High implementation cost and poor estimation of cost” are three top-level critical failure factors.
1 Introduction
The landscape of international business has changed dramatically in recent years, with a greater focus being placed on efficiency, sustainability, and environmental responsibility (Ansari et al., 2024). Indian manufacturing sector is struggling with delayed deliveries, long manufacturing cycle, operational and technology issues. Sustainable continuous improvement of organizational processes can help in overcoming these issues (Kumar et al., 2023). Lean Six Sigma stands out as a potent methodology of sustainable continuous improvement in manufacturing organizations. It combines the ideas of Six Sigma with Lean manufacturing to optimize operations, improve quality, and cut costs (Antony et al., 2024; Lal Bhaskar, 2020). However, there are obstacles that prevent the full realization of Sustainable Lean Six Sigma in the Indian industry (Maware and Parsley, 2022; Utama and Abirfatin, 2023). These can be overcome by identification and prioritizing the challenges.
Cultural change and organization’s leadership can help to overcome these obstacles. This study aims to explore the essential factors contributing to the ineffective utilization of Lean Six Sigma and sustainability in the Indian manufacturing sector. The unique socio-economic and cultural landscape of India introduces complexities that demand a nuanced understanding of barriers to adopting sustainable practices (Zhen et al., 2021). By identifying and analyzing these critical failure factors, this study seeks to provide insights for overcoming challenges and facilitating successful implementation (Albliwi et al., 2014). The potential benefits of adopting Sustainable Lean Six Sigma in Indian manufacturing, beyond process optimization and cost reduction, are significant. They align with global trends towards environmental responsibility and social accountability, and successful implementation of sustainable practices not only enhances competitiveness but also improve the repute of the organization in global market, by quantifying operation efficiency and effectiveness. (Swarnakar et al., 2020; Meena et al., 2021; Utama and Abirfatin, 2023). This helps to generate long tern economic-benefits, ensures job security, and reduces negative environmental impacts. This study helps to identify CFF’s and develop sustainable manufacturing process.
Authors of the current study have identified the critical failure factors (CFF) through a systematic review of the literature and experts’ opinions. For collection and identification of CFF’s a detailed survey at digital platform (survey-monkey) used. The participants in the survey selected through vide range of industrial profile, i.e., Quality head, production head, Total quality management head at corporate level, etc., and panel of experts. The panel of experts consists of individuals with extensive experience in various domains, including automobile parts manufacturing having sheet metal, tyres, plastic injection moulding. Glass manufacturing, and academics with Six Sigma Black Belt certification. This study also included research associates and scholars involved in Lean Six Sigma implementation at various organizations. The identified CFFs have been analyzed using BWM techniques. The aim is to propose actionable recommendations to guide organizations in navigating challenges and realizing the full potential of Sustainable Lean Six Sigma. Through this research, the authors aim to contribute to sustainable business practices and foster the growth of the manufacturing sector in India.
1.1 Critical failure factor
The implementation of any strategic initiative within an organization presents challenges, and Lean Six Sigma, particularly in sustainability, is no exception. While Lean Six Sigma enhances efficiency and quality, the journey toward sustainability in manufacturing faces critical failure factors (Kumar et al., 2015). This study focuses on identifying these factors, which are essential for embedding sustainability seamlessly into Lean Six Sigma practices. Integrating sustainability principles into Lean Six Sigma becomes imperative as organizations strive to align with environmental responsibilities. Yadav et al. (2018) studied the prioritization of the barriers to Lean Six Sigma adoption. Utama and Abirfatin (2023) developed a framework of Sustainable Lean Six Sigma for improving sustainable manufacturing performance. Swarnakar et al. (2020) evaluated the critical failure factors for implementing a sustainable lean Six Sigma framework in manufacturing organizations. Sunder and Prashar (2020) examined the critical failure factors of continuous improvement deployments by stage-wise results and a contingency theory perspective. Anthony and Banuelas (2002) Analyzed management commitment and involvement, linking six sigma to business strategy and linking six sigma to customer are major failures factors. Hussain et al. (2019) considered barriers to deploy a green LSS framework in the industrial construction process. The findings included lack of customer awareness, the unstable environment, lack of management policies, lack of resources, and lack of top management direction are the top five barriers. Sodhi (2023) investigated and analyzed the failure factors for the implementation of scrap reduction techniques in Indian SMEs. However, complexities in integration and contextual factors can lead to setbacks (Huang et al., 2023). This study seeks to investigate the key factors that influence the integration of Lean Six Sigma with sustainable practices, examining the obstacles that organizations encounter in this endeavor. By pinpointing and examining these factors, this research aims to provide valuable insights that can help organizations navigate challenges and enhance the effectiveness of their implementation efforts. Swarankar et al. (2020) developed a 13 level interrelationship based on hierarchical model of CFF’s that helpd in systematic implementation of sustainable LSS framework in manufacturing industries. Recognizing distinct challenges in the Indian manufacturing landscape, the study tailors its focus to socio-economic and cultural nuances (Javaid et al., 2022). Albliwi et al. (2014) studied the critical failure factors of Lean Six Sigma. Antony et al. (2024) observed the global prospect on operational excellence by unveiling the critical failure factors. Bader et al. (2024) studied the process improvement in organizations. Gaikwad et al. (2020) analyzed the barriers and strategies for implementing Lean Six Sigma in the context of Indian SMEs. Antony and Desai (2009) concluded internal resistance against cultural change, Inappropriate training programs, project selection methodology inappropriate and analyzing through wrong tools selection are CFF’s. Hariyani et al. (2022) statistically analyzed the barriers to the adoption of the integrated sustainable green-lean-six sigma-agile manufacturing systems in Indian manufacturing industries. Huang et al. (2023) studied the role of Lean Six Sigma in driving sustainable manufacturing practices. The authors analyzed the relationship between Lean Six Sigma principles, data-driven decision-making, and environmental performance. Rathi et al. (2021) identified the barriers to Lean Six Sigma in the automobile part manufacturing industry. Understanding critical failure factors can mitigate risks and foster proactive sustainability approaches. Learning from both successes and failures contributes to enhancing Lean Six Sigma practices and sustainability efforts.
Lean and Six Sigma methodologies have demonstrated effectiveness, yet literature reveals instances of implementation failures. This study explores documented failures, seeking common themes, root causes, and lessons learned. For example, Pederson et al. (2024) highlight the challenges faced by businesses attempting Lean implementation, with a significant failure rate reported. Glasgow et al. (2010) and Gaikwad et al. (2020) identified the lack of stakeholder involvement as a key reason for LSS failures. These studies underscore the importance of addressing barriers and stakeholder engagement in Lean and Six Sigma implementations.
2 Research design
A systematic review of the literature was undertaken to identify and document critical failure factors that hinder the effective application of Lean Six Sigma in manufacturing settings. Using Exploratory Factor Analysis, these factors were grouped into categories, providing insight into the underlying challenges and obstacles that must be addressed to ensure successful implementation and sustainment of Lean Six Sigma initiatives in the manufacturing sector. The identified critical failure factors are further examined to assess the survey’s reliability. Techniques such as Importance Index analysis and the Corrected Item Minus Total Correlation (CIMTC) method are employed to analyze these classified factors. Cardinal grouping and group formation based on explorative factor analysis used to eliminate the irrelevant factors collected through the survey and group interviews. Cronbach’s alpha test is most commonly used to estimate internal consistency of items in a scale (Vaske et al., 2017). The alpha value shows the extent to which survey answers correlate with each other. Significant critical failure factors are identified through these statistical techniques using Statistical Package for Social Sciences (SPSS) software. After checking the consistency of CFF’s, prioritization of the selected factors done. Using appropriate multi-criteria decision-making techniques, we rank and prioritize the validated critical failure factors; in this instance, the authors employed the Best-Worst Method (BWM). The detailed methodology of the present work shows (in Figure 1) a literature review for the identification of CFF, followed by group formation and classification of LSS CFFs. Further, the CFF setting is followed by a consistency check and application of BWM on finalized factors. Finally, the ranking of CFFs, discussion, and implications are discussed.
2.1 Categorization of LSS critical failure factors
In this study, the authors identified eighteen critical failure factors for Lean Six Sigma implementation from a literature review and experts’ opinions. The authors have searched the literature from the Google Scholar database. Keywords used for the literature search were “Sustainable,” “Lean Six Sigma,” “India”, “Manufacturing,” and “Critical failure factors.” All articles that were searched were studied and shortlisted based on relevance to the subject, the language of publication, and the context of Indian manufacturing industries. The authors conducted a questionnaire-based survey among industry experts in the manufacturing sector. The authors examined papers by title and then abstracts when required, and by this means included all the papers that meet the inclusion criteria; however, the use of this method meant that it was not possible to exclude all unrelated papers for factors affecting LSS implementation. In total, 250 experts from the manufacturing sector were approached for the questionnaire based survey. Participants in the survey based questionnaire are from manufacturing organizations, industrial experts and consultants having vast knowledge of manufacturing processes. One hundred twenty complete responses were received. To further analyze the survey-based identified factors, the authors employed a statistical technique of exploratory factor analysis (EFA). This method reduces a huge number of variables to a smaller set of elements. Authors focused on factors with Eigenvalues greater than 1, as they explain significant variance in the data. The authors gathered data from a sample of 120 cases (n = 120) and ran Principal Component Analysis with Varimax rotation. Before diving into the analysis, we checked if our data was suitable for factor analysis using two tests: Kaiser-Meyer-Olkin (KMO) and Bartlett’s test of sphericity. In the present work, KMO values range from 0 to 1, with higher scores indicating greater appropriateness for factor analysis. We aimed for a KMO value of at least 0.6. Bartlett’s test assesses if correlations between variables are sufficiently large for factor analysis. Lower values indicate stronger correlations, which are ideal for this analysis. Table 1 presents the extracted critical failure factors.
With a threshold of 1.5 for Eigenvalues, factors that contribute significantly to the variation in our data were extracted. The authors established a minimum factor loading value of 0.40 to determine a variable’s significance in contributing to a factor. To facilitate a clear and concise visualization of our results, Scree plots, which graphically display the Eigenvalues on the x-axis and the categorized Lean Six Sigma critical failure factors on the y-axis, providing a visual representation of the underlying structure and relationships between these factors, were employed. This helped to understand the factors that are most important for successful implementation. Figure 2 presents the comparison of component numbers and eigenvalues.
2.2 Analysis of extracted critical failure factor
To identify the most significant Lean Six Sigma critical failure factors, we employed two methods: Correlation of Item and Total Correlation (CIMTC) and Importance Index. CIMTC helps uncover the connections between each item and the overall score derived from the questionnaire, allowing for a more detailed understanding of the item-score relationships. In a reliable scale, items measuring the same construct should correlate well. Therefore, if a critical failure factor CIMTC value is less than 0.500, it's considered for exclusion. Our statistical analysis revealed that six critical failure factors had CIMTC values below 0.500, indicating they were less correlated with the overall score and, thus, not suitable for further study. The remaining twelve critical failure factors had CIMTC values ranging from 0.500 to 0.748, affirming their importance in the context of our study. Additionally, these finalized critical failure factors exhibited a maximum standard deviation of 1.273, underscoring their significance in Indian manufacturing sectors. To bolster the insights gathered from the questionnaire survey, we also employed Importance Index analysis. This additional step enhances the confidence of experts engaged in the survey process. The following equation determines the Importance Index value.
Here pi = constant presenting weight given to i.
Xi = variable presenting frequency of response for I and I = 1,2,3,4,5.
The Importance Index, ranging from 0 to 1, helps us gauge the significance of critical failure factors. For ease of understanding, we categorized the Importance Index into five clusters. The results of the importance-index analysis for the critical failure factors are presented below, with further details available in Table 2.
The experts consulted in this study possessed diverse backgrounds and expertise. The panel consists of individuals with extensive experience in various domains, including industry executives, production managers, quality control specialists, production engineers, total quality management experts, academics with Six Sigma Black Belt certification, and research associates and scholars in Lean Six Sigma. Specifically, the experts have accumulated a range of experience, from 3 to 30 years, with an average of 14.5 years. This collective expertise spans executive leadership (25 years), production management (15 years), quality control (9 years), production engineering (10 years), total quality management (4 years), academia (30 and 20 years), and LSS research (10 and 3 years). This diverse panel brings a wealth of knowledge and practical experience to inform the study’s findings and recommendations. Table 3 shows the reliability statistics, and Table 4 shows the KMO and Bartlett’s Test values.
2.2.1 Reliability assessment of finalized critical failure factors
Before proceeding further, it is crucial to validate the sorted data to ensure accuracy. Validation prevents potential false results. The factors collected through the survey questionnaire mentioned in table 1 tested for statistical validation. The authors conducted a reliability test in SPSS software to authenticate the finalized critical failure factors. This test assesses the internal consistency of our survey. To measure internal consistency, we used Cronbach’s alpha, which evaluates the correlation between two-halves of the questionnaire designed to measure the same thing. It is the most common estimate of internal consistency of items in a scale (Vaske et al., 2017). It should be accompanied by a Confidence Interval (CI) for its population value (Bonett and Wright, 2015). The factors collected through survey questionnaire analysed using reliability statistics to find out the Cronbach’s alpha value. This index is used to assess the reliability of sum or average of measurements, calculated values greater than 0.70 signify respectable reliability. With a computed Cronbach’s alpha value of 0.884, it confirmed a strong internal consistency among the finalized CSF’s. This result supports the reliability and accuracy of our data, enabling us to proceed with confidence in our subsequent analyses. Table 5 presents the rotated component matrix, and Table 6 shows the critical failure factors with CIMTC, Mean, SD, and Important Index values.
2.3 Application of best-worst method
The Best-Worst Method, crafted by Jafar Rezaei (Rezaei, J. 2015), is a multi-criteria decision-making approach aimed at prioritizing and selecting the most and least important criteria from a set of alternatives. Firstly, we identify the best (most important) and worst (least important) criteria. Then, we conduct pairwise comparisons, ranking each criterion in terms of its superiority to others (best to others) and inferiority to others (worst to others). Next, we formulate a maximin problem to calculate the weights, which ultimately determines the ranking of the criteria. This method helps streamline decision-making processes by highlighting key factors for consideration.
Here, aij = 1 indicates that both criteria are of equal importance, and similarly, aij >1 implies that i is more significant than j. a11 to ann considers aij, which represents the relative importance of criteria I to criteria j.
The pairwise comparison method provides a structured approach to creating decision matrices, which are integral to all multiple-criteria decision-making techniques. Multi-criteria methods that use pairwise comparisons (like the Analytic Hierarchy Process) require to compare all pairs of elements above (or below) the main diagonal of the matrix. However, inconsistencies often arise in these matrices due to the unstructured nature of comparisons in pairwise methods. To address this, the Best-Worst Method (BWM) offers a solution. It necessitates a smaller comparison matrix, resulting in a more consistent relationship among alternatives. Moreover, it simplifies the comparison process by requiring only numerical values.
In the Best-Worst Method, pairwise comparisons are categorized into two main types.
Definition 1. A comparison is termed as a reference comparison if one criterion is deemed the best and the other the worst, or vice versa.
Definition 2. A comparison is considered a secondary comparison if neither criterion is classified as the best or the worst.
This classification helps streamline the comparison process and enhances the reliability of the decision-making framework.
To determine the relative importance of the critical failure factors, the Best-Worst Method (BWM) used, soliciting input from a panel of experts comprising industrial professionals from Indian manufacturing sectors and academic scholars with specialized knowledge in the field. The process involved the following steps.
Step 1: Determining a Set of Decisions for Critical Failure Factors
From our earlier analysis, through Exploratory Factor Analysis and reliability analysis, we established a set of three primary criteria and thirteen sub-criteria.
Step 2: Identifying the Best and Worst Critical Failure Factors
Nine experts from both industry and academia were interviewed to identify the most significant and least significant Critical Failure Factors among the thirteen finalized factors.
Step 3: Assessing the Preference of the Best Critical Failure Factors
During separate interviews, survey respondents provided their preferences for the best Critical Failure Factors compared to all others on a scale of 1 to 9. Here, aBj represents the preference for the best Critical Failure Factor over the jth Critical Failure Factor, with aBB having a value of 1.
This structured approach enabled us to rank the Critical Failure Factors effectively, incorporating insights from both industry professionals and academic experts.
Step 4: Evaluating the Inclination of Other Critical Failure Factors over the Worst Ones
Following the same structured approach, we interviewed survey respondents separately to gather their inputs. They provided their preferences for each Critical Failure Factor compared to the worst ones on a scale from 1 to 9. Here, ajW represents the preference of the jth Critical Failure Factor over the worst critical failure factors, with aWW having a value of 1.
This step completes our assessment, providing a comprehensive understanding of how each Critical Failure Factor ranks relative to the worst ones.
A thorough pairwise comparison of all criteria and sub-criteria was performed, considering the relationships and interdependencies among the critical failure factors. This method allowed for a detailed assessment of each factor’s significance in relation to others, revealing a more complete picture of their relative priorities. The attached tables show the pairwise comparison matrix, using data from one of the survey respondents.
Step 5: Assessing the Preference of Other Critical Failure Factors Compared to the Worst Ones
Continuing with our systematic approach, authors individually interviewed survey participants to collect their insights. They shared their preferences for each critical failure factor in comparison to the worst ones, rating them on a scale from 1 to 9. Here, ajW denotes the preference of the jth critical failure factor over the worst ones, where aWW remains at a value of 1.
By completing this step, we’ve gained a holistic view of how each critical failure factor performs compared to the worst ones, enriching our assessment process.
We can transform the maximin problem described above into the following:
min ξ, s.t.
To address the problem at hand, we derived the optimal weights (w1*, w2*, w3*, wn*) and ξ* for each criterion and sub-criteria. As shown in Table 7, we determined the high values of the Consistency Index based on the best-worst (aBw) method. By combining the Consistency Index with the ξ* value, we computed the Consistency Ratio, providing a measure of the consistency of the expert judgments in our analysis. A Consistency Ratio approaching zero indicates strong consistency, signifying a dependable decision-making process. Conversely, a ratio closer to one suggests less consistency, highlighting potential inconsistencies in our analysis. Table 8 shows the consistency Index. Table 9 shows the Global Weightage and Ranking of critical failure factors.
3 Discussion on findings
The current study aims to raise awareness and facilitate the adoption of Lean Six Sigma in manufacturing sectors for process improvement. At the initial stage, eighteen critical failure factors were identified through an extensive literature review and experts’ opinions. Based on their nature and implementation area, these critical failure factors were further categorized into three main groups: Top-level, Front-line, and others. To ensure the validity of the classified critical failure factors, it was required that their eigenvalues exceed 1.5 and factor loading values surpass 0.3.
The Importance Index analysis and CIMTC approaches were employed in order to identify highly important and critical failure factors. Six critical failure factors were shown to have little effect on the application of Lean Six Sigma in Indian manufacturing sectors, based on statistical analysis, as evidenced by their Corrected Item minus the Total Correlation values being less than 0.500. In order to improve the consistency and dependability of the outcomes, these critical failure factors were removed. A Cronbach’s alpha score of 0.884, which indicates extremely consistent Lean Six Sigma critical failure factors, was used to validate the consistency of the finished critical failure factors. Prioritization through ranking was required once the critical failure factors were grouped and analyzed to comprehend the significance and efficacy of particular factors. Therefore, the best-worst method technique was used in this situation. The best-worst method results demonstrated (refer to Tables 10–13) the critical significance that the lack of clear alignment between CI initiatives and organizational goals (O1) plays in implementing Lean Six Sigma. It was found to be the top-ranking factor in the prioritization process. The necessity of appropriate tool selection is highlighted by the second place ranking of suboptimal selection of project management tools and prioritization techniques (O2). Third place was the limited knowledge and expertise in applying LSS principles and techniques to project implementation (O3), suggesting that this is a crucial implementation factor. Top management’s absence of enthusiasm, responsibility, and participation (T4) was rated fourth among the top-level critical failure factors, highlighting the importance of top management support. Failure of leadership to inspire and motivate (T5) secured the fifth position. In contrast, limited insight into the varying customer profiles and preferences (T2) secured the sixth rank, underscoring their significance in the intermediate phase of implementation. In addition, (T3), the lack of a well-defined framework for executing initiatives is ranked 10th, demonstrating its critical importance to the success of implementation. Communication breakdowns (F2) were ranked seventh among the frontline critical failure factors, demonstrating the relevance of this factor. Reluctance to adapt to changing cultural values (F1) was ranked ninth, highlighting how important it is. Last but not least, the rankings of 11th and 12th, respectively, for limited access to continuing education and training programs (F4) and poor project management methodology (F3), emphasize their respective responsibilities in guaranteeing worker involvement and successful implementation. These rankings offer insightful information on the issues and difficulties surrounding the application of Lean Six Sigma in manufacturing.
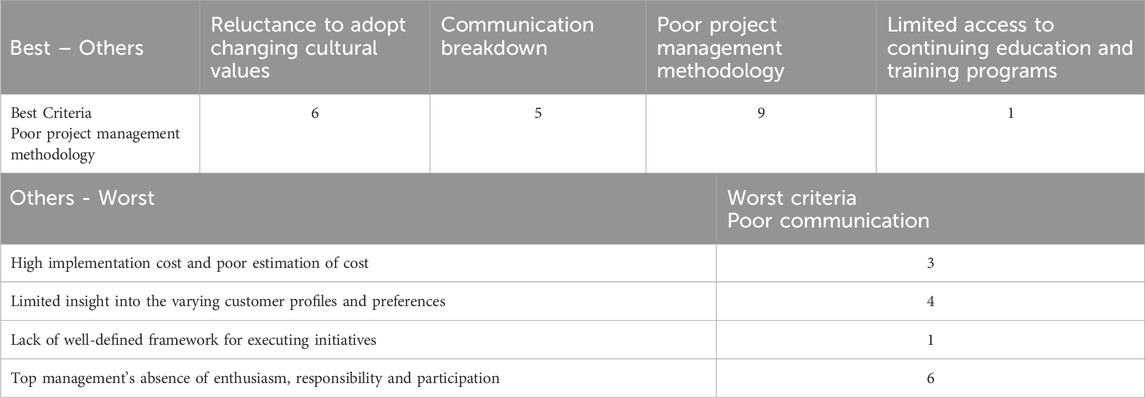
Table 12. Best to others (BO) and others-to-worst (OW) pairwise comparisons for Bottom-line based CFFs.
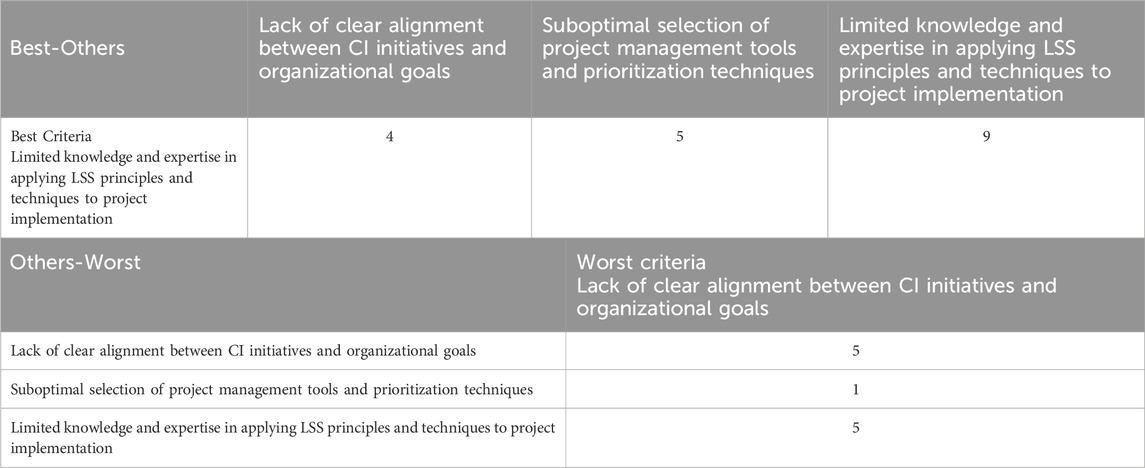
Table 13. Best-others (BO) others-to-worst (OW) pairwise comparisons for suppliers and others-based CSFs.
4 Conclusion
The analysis of critical failure factors in implementing Sustainable Lean Six Sigma within the Indian manufacturing sector unveils a multifaceted landscape influenced by socio-economic, cultural, and operational factors. Insights gleaned from literature and analysis shed light on the challenges organizations may face as they endeavour to embed sustainability into Lean Six Sigma practices. Understanding and addressing these critical failure factors are crucial for fostering successful implementations. Indian manufacturing industries grapple with unique challenges, including regulatory intricacies, resource limitations, varying levels of awareness, and the delicate balance between economic growth and sustainable practices. Addressing these challenges necessitates tailored strategies and proactive measures to mitigate risks and enhance the likelihood of success. Leadership commitment emerges as pivotal, highlighting the need for sustained support from top management. Effective change management strategies are essential for overcoming resistance to new practices and fostering a culture of continuous improvement intertwined with sustainability. Clear communication, well-defined metrics, and continuous training are vital failure factors.
Integrating sustainability into organizational culture requires a holistic approach that transcends process optimization to embrace environmental and social responsibility. This analysis offers a roadmap for Indian manufacturing industries to navigate the complexities of Sustainable Lean Six Sigma. By learning from failures and leveraging best practices, these industries can position themselves for operational excellence and responsible global citizenship.
5 Future research directions
The successful implementation of Sustainable Lean Six Sigma in Indian manufacturing requires a strategic fusion of methodologies, cultural adaptation, and forward-looking approaches. This research contributes to the discourse on sustainable business practices by spotlighting challenges specific to India and offering actionable recommendations for organizations aspiring to excel in efficiency and environmental stewardship. As the sector evolves, the lessons learned pave the way for a more sustainable and resilient future and research in other areas, too.
6 Implications of the study
Practical identification of CFF’s and their usefulness in Indian manufacturing industries are guidelines for managers and decision-makers. These helps to reduce the timeline of the project and avoids failure in conceptualization of the project. Results may varies in healthcare and service industries as this study concentrated on Indian manufacturing industry.
Data availability statement
The raw data supporting the conclusions of this article will be made available by the authors, without undue reservation.
Author contributions
SK: Conceptualization, Methodology, Writing–original draft. RK: Investigation, Writing–review and editing. RP: Conceptualization, Methodology, Writing–review and editing. AK: Conceptualization, Investigation, Methodology, Writing–review and editing. JB: Conceptualization, Investigation, Writing–review and editing. SB: Methodology, Writing–review and editing. JG: Methodology, Supervision, Writing–review and editing. SR: Investigation, Supervision, Writing–review and editing. AA: Investigation, Supervision, Writing–review and editing. VH: Investigation, Supervision, Writing–review and editing.
Funding
The author(s) declare that no financial support was received for the research, authorship, and/or publication of this article.
Acknowledgments
Authors acknowledge the efforts of anonymous participants in responding to the survey questions. During the preparation of this work, the author(s) used GPT-3.5 (2022) for Language Assistance, Error Checking, and Consistency in Style and Terminology. After using this tool, the author(s) reviewed and edited the content as needed and take(s) full responsibility for the content of the publication.
Conflict of interest
The authors declare that the research was conducted in the absence of any commercial or financial relationships that could be construed as a potential conflict of interest.
Publisher’s note
All claims expressed in this article are solely those of the authors and do not necessarily represent those of their affiliated organizations, or those of the publisher, the editors and the reviewers. Any product that may be evaluated in this article, or claim that may be made by its manufacturer, is not guaranteed or endorsed by the publisher.
References
Albliwi, S., Antony, J., Abdul Halim Lim, S., and van der Wiele, T. (2014). Critical failure factors of Lean Six Sigma: a systematic literature review. Int. J. Qual. and Reliab. Manag. 31 (9), 1012–1030. doi:10.1108/IJQRM-09-2013-0147
Ansari, M. S. A., Abouraia, M., El Morsy, R., and Thumiki, V. R. R. (2024). Influence of transformational and transactional leadership on agile project success: an empirical validation. Proj. Leadersh. Soc. 5, 100136. doi:10.1016/j.plas.2024.100136
Anthony, J., and Banuelas, R. (2002). Critial success factor for the successful implementing of Six Sigma projects. TQM Mag. 41 (2), 92–99. doi:10.1108/09544780210416702
Antony, J., and Desai, D. A. (2009). Assessing the status of Six Sigma implementation in the Indian industry: results from an exploratory empirical study. Manag. Res. News 32 (5), 413–423. doi:10.1108/01409170910952921
Antony, J., Sony, M., Jayaraman, R., Swarnakar, V., Tortorella, G. d.L., Garza-Reyes, J. A., et al. (2024). Global perspectives on operational excellence: unveiling critical failure factors and sustainable pathways. Int. J. Qual. and Reliab. Manag. ahead-of-print No. ahead-of-print. doi:10.1108/IJQRM-01-2024-0013
Bader, M., Antony, J., Jayaraman, R., Swarnakar, V., Goonetilleke, R. S., Maalouf, M., et al. (2024). Why do process improvement projects fail in organizations? A review and future research agenda. Int. J. Lean Six Sigma 15 (3), 664–690. doi:10.1108/IJLSS-07-2023-0126
Bonett, D. G., and Wright, T. A. (2015). Cronbach's alpha reliability: Interval estimation, hypothesis testing, and sample size planning. J. Organ. Behav. 36 (1), 3–15. doi:10.1002/job.1960
Fallah Shayan, N., Mohabbati-Kalejahi, N., Alavi, S., and Zahed, M. A. (2022). Sustainable development goals (SDGs) as a framework for corporate social responsibility (CSR). Sustainability 14 (3), 1222. doi:10.3390/su14031222
Gaikwad, S. K., Paul, A., Moktadir, M. A., Paul, S. K., and Chowdhury, P. (2020). Analyzing barriers and strategies for implementing lean six sigma in the context of Indian SMEs. Benchmark Int. J. 27 (8), 2365–2399. doi:10.1108/BIJ-11-2019-0484
Glasgow, J. M., Scott-Caziewell, J. R., and Kaboli, P. J. (2010). Guiding inpatient quality improvement: a systematic review of Lean and Six Sigma. Jt. Comm. J. Qual. Patient Saf. 36 (12), 533–AP5. doi:10.1016/s1553-7250(10)36081-8
Hariyani, D., Mishra, S., and Sharma, M. K. (2022). A descriptive statistical analysis of barriers to the adoption of integrated sustainable green-lean-six sigma-agile manufacturing system (ISGLSAMS) in Indian manufacturing industries. Benchmark Int. J. 30, 2705–2733. doi:10.1108/bij-11-2021-0701
Huang, J., Irfan, M., Fatima, S. S., and Shahid, R. M. (2023). The role of lean six sigma in driving sustainable manufacturing practices: an analysis of the relationship between lean six sigma principles, data-driven decision making, and environmental performance. Front. Environ. Sci. 11. doi:10.3389/fenvs.2023.1184488
Hussain, M., Al-Aomar, R., and Melhem, H. (2019). Assessment of lean-green practices on the sustainable performance of hotel supply chains. Int. J. Contemp. Hosp. Manag. 31 (6), 2448–2467. doi:10.1108/ijchm-05-2018-0380
Javaid, M., Haleem, A., Singh, R. P., Rab, S., Suman, R., and Khan, S. (2022). Exploring relationships between Lean 4.0 and manufacturing industry. Industrial Robot Int. J. robotics Res. Appl. 49 (3), 402–414. doi:10.1108/ir-08-2021-0184
Kaswan, M. S., Rathi, R., Reyes, J. A. G., and Antony, J. (2021). Exploration and investigation of green lean six sigma adoption barriers for manufacturing sustainability. IEEE Trans. Eng. Manag. 70, 4079–4093. doi:10.1109/TEM.2021.3108171
Kumar, R., Singh, K., and Jain, S. K. (2020). An empirical investigation and prioritization of barriers toward implementation of agile manufacturing in the manufacturing industry. TQM J. 33 (1), 183–203. doi:10.1108/TQM-04-2020-0073
Kumar, S., Kumar, N., and Haleem, A. (2015). Conceptualisation of sustainable green lean six sigma: an empirical analysis. Int. J. Bus. Excell. 8 (2), 210. doi:10.1504/IJBEX.2015.068211
Kumar, S., Swarnakar, V., Phanden, R. K., Antony, J., Jayaraman, R., and Khanduja, D. (2023). Analyzing critical success factors of Lean Six Sigma for implementation in Indian manufacturing MSMEs using best-worst method. Benchmarking Int. J. (In Press). doi:10.1108/BIJ-08-2022-0540
Lal Bhaskar, H. (2020). “Lean six sigma in manufacturing: a comprehensive review,” in Lean manufacturing and six sigma - behind the mask (London: IntechOpen). doi:10.5772/intechopen.89859
Maware, C., and Parsley, D. M. (2022). The challenges of lean transformation and implementation in the manufacturing sector. Sustainability 14 (10), 6287. doi:10.3390/su14106287
Meena, M. L., Yadav, V., Sharma, M. K., Mishra, Y., and Dangayach, G. S. (2021). Lean Six Sigma implementation in Indian manufacturing organisation: a case study. Int. J. Six Sigma Compet. Advant. 13 (1), 1. doi:10.1504/IJSSCA.2021.10038264
Mundra, N., and Mishra, R. P. (2023). Development of a model of critical failure factors for integrated LSS–AM practices in Indian manufacturing industries: a fuzzy TISM approach. Int. J. Syst. Assur Eng. Manag. 14, 1479–1491. doi:10.1007/s13198-023-01954-9
Pederson, M. D., Abildgaard, A. S., Caplan, S. M., Krings, G. H., Krosch, T. C., Linder, L. E., et al. (2024). Managing the OR: tools, resources and guidelines to effectively manage operative suites. Manag. Healthc. 8 (2), 182–194. doi:10.69554/edrv9615
Rathi, R., Singh, M., Verma, A. K., Gurjar, R. S., Singh, A., and Samantha, B. (2021). Identifcation of lean six sigma barriers in automobile part manufacturing industry. Mater Today Proc. 50, 728–735. doi:10.1016/j.matpr.2021.05.221
Rezaei, J. (2015). Best-worst multi-criteria decision-making method. Omega 53, 49–57. doi:10.1016/j.omega.2014.11.009
Shokri, A., Antony, J., and Garza-Reyes, J. A. (2022). A new way of environmentally sustainable manufacturing with assessing transformation through the green deployment of Lean Six Sigma projects. J. Clean. Prod. 351, 131510. doi:10.1016/j.jclepro.2022.131510
Sodhi, H. S. (2023). An investigation towards identifying and analysing the failure factors for the implementation of scrap reduction techniques in Indian SMEs. Int. J. Process Manag. Benchmarking 14 (2), 139–154. doi:10.1504/ijpmb.2023.130961
Sreedharan, V., Nair, R., Chakraborty, S., and Antony, J. (2018). Assessment of critical failure factors (CFFs) of lean six sigma in real life scenario: evidence from manufacturing and service industries. Benchmark Int. J. 25 (8), 3320–3336. doi:10.1108/BIJ-10-2017-0281
Sunder, M. V., and Prashar, A. (2020). Empirical examination of critical failure factors of continuous improvement deployments: stage-wise results and a contingency theory perspective. Int. J. Prod. Res. 58 (16), 4894–4915. doi:10.1080/00207543.2020.1727044
Swarnakar, V., Tiwari, A. K., and Singh, A. R. (2020). Evaluating critical failure factors for implementing sustainable lean six sigma framework in manufacturing organization: a case experience. Int. J. Lean Six Sigma 11 (6), 1069–1104. doi:10.1108/IJLSS-05-2019-0050
Swarnakar, V., Vaidya, S., Tiwari, A. K., and Singh, A. R. (2019). “Assessing critical failure factors for implementing Lean Six Sigma framework in Indian manufacturing organizations,” in 3rd IEOM European conference on industrial engineering and operations management, 2161–2172.
Utama, D. M., and Abirfatin, M. (2023). Sustainable Lean Six-sigma: a new framework for improve sustainable manufacturing performance. Clean. Eng. Technol. 17, 100700. doi:10.1016/j.clet.2023.100700
Vaske, J. J., Beaman, J., and Sponarski, C. C. (2017). Rethinking internal consistency in Cronbach's alpha. Leis. Sci. 39 (2), 163–173. doi:10.1080/01490400.2015.1127189
Yadav, G., Seth, D., and Desai, T. N. (2018). Prioritising solutions for Lean Six Sigma adoption barriers through fuzzy AHP-modified TOPSIS framework. Int. J. Lean Six. Sigma 9 (3), 270–300. doi:10.1108/ijlss-06-2016-0023
Keywords: sustainable Lean Six Sigma, Indian manufacturing industries, best worst method, critical failure factors, BWM technique
Citation: Kumar S, Kumar R, Phanden RK, Kumar A, Bala J, Bharath Kumar S, Giri J, Sathish RU, Agrawal A and Vishwanatha HM (2024) A study on critical failure factors for implementation of sustainable Lean Six Sigma from Indian manufacturing industries perspective using BWM technique. Front. Mech. Eng. 10:1451568. doi: 10.3389/fmech.2024.1451568
Received: 19 June 2024; Accepted: 06 August 2024;
Published: 21 August 2024.
Edited by:
Kanak Kalita, Vel Tech Dr. RR and Dr. SR Technical University, IndiaReviewed by:
Elio Padoano, University of Trieste, ItalyPraveen Barmavatu, Universidad Tecnológica Metropolitana, Chile
Mohinder Pal Garg, PEC University of Technology, India
Copyright © 2024 Kumar, Kumar, Phanden, Kumar, Bala, Bharath Kumar, Giri, Sathish, Agrawal and Vishwanatha. This is an open-access article distributed under the terms of the Creative Commons Attribution License (CC BY). The use, distribution or reproduction in other forums is permitted, provided the original author(s) and the copyright owner(s) are credited and that the original publication in this journal is cited, in accordance with accepted academic practice. No use, distribution or reproduction is permitted which does not comply with these terms.
*Correspondence: Ajay Kumar, YWpheS5rdW1hcjMwODg2QGdtYWlsLmNvbQ==; Jayant Giri, amF5YW50cGdpcmlAZ21haWwuY29t; Rao U. Sathish, c2F0aGlzaC5yYW91QG1hbmlwYWwuZWR1; Ashish Agrawal, YXNoaXNoLmFncmF3YWxAbWFuaXBhbC5lZHU=; H. M. Vishwanatha, dmlzaHdhbmF0aGEuaG1AbWFuaXBhbC5lZHU=