- School of Mechanics and Engineering, Liaoning Technical University, Fuxin, China
This research is based on the modeling, internal structure analysis, and automation of a cassava grinding machine. For the design, the single-cylinder grinder was chosen due to its advantages, notably simplicity and versatility. The grinding method used in this type of grinder is compression. The mechanical design and simulation software first allowed for the design of the grinder and then for performing static analyses under three loads (P1 = 10000N, P2 = 15000N, and P3 = 20000N). The results of these tests led to the selection of P3 = 20000N as the straightening load, with a maximum stress value in the static analysis of 88,18 MPa and a maximum deformation of 0,000358 under the force of load P3. Additionally, the frequency analysis distinguished five resonance modes. The results for each mode concluded that no resonance would affect the machine, thus ensuring stable operation. Furthermore, fatigue, frequency, and safety factor studies showed that the machine could withstand a load of m3 = 2000 kg without damage, with a service life of 1e+09 cycles. Considering the total number of life cycles, which is 1e+09 cycles, this means that the machine will have a service life of 347000 years, with a total grinding output of 2e+12 kg of cassava and 5840000 kg per year. The factor of safety is FoS = 1,78, indicating a sufficient margin for safe operating conditions. The automation of the grinder was carried out using a GRAFCET model and a sophisticated human-machine interface (HMI), providing an additional safety point for the machine and allowing the operator to monitor the operation via a simple graphical interface. This automation enables continuous operation with minimal human intervention, thereby improving the efficiency and safety of the cassava grinding process.
1 Introduction
Cassava (Manihot esculenta Crantz) is a vital crop with a rich history that is deeply intertwined with the culture and livelihoods of many communities around the world (Igwe, 2023). Originating in South America, cassava has spread to tropical and subtropical regions and has become a staple food for millions of people. Its versatility, resilience, and adaptability to diverse agroecological conditions have earned it the title of “insurance crop” or “famine crop” in many regions (Anwar et al., 2022; Raufu et al., 2023). In many areas, cassava starch plays a critical role in ensuring food security and economic stability. It serves as a primary source of dietary energy for millions of people, particularly in regions where other staple crops are scarce or unreliable due to factors such as climate variability, soil conditions, or economic constraints (Salazar, 2022; Sobowale et al., 2022; Wulandari et al., 2023). In addition, cassava starch contributes significantly to the livelihoods of smallholder farmers and rural communities engaged in cassava cultivation and processing.
Despite its importance, cassava processing faces numerous challenges that affect both producers and consumers. Traditional methods of cassava processing include manual grating, which involves rubbing peeled cassava against the rough surface of a grater to produce a coarse pulp. Another method is pounding with a mortar and pestle, which involves placing peeled cassava in a mortar and pounding it into a paste or pulp. Additionally, there is stone mill grinding, which involves passing cassava roots between two large stones to crush and grind them (Nasirembe et al., 2023a; Nasirembe et al., 2023b). These traditional cassava grinding methods are often labor-intensive and time-consuming, requiring considerable physical effort to process cassava roots into a useable form (Peter et al., 2021).
In light of these challenges, several advances in milling technology have led to the development of more efficient, productive, and versatile milling systems for cassava processing. First, researchers and engineers have focused on optimizing the mechanical design of milling systems to improve efficiency and reduce energy consumption (Sumit, 2023; Zheng and Jie, 2023). This includes the development of innovative grinding chamber geometries, rotor configurations, and grinding mechanisms to improve particle size reduction and starch extraction efficiency. In addition, advances in materials science have led to the use of high-performance materials for mill components, such as hardened steel, ceramics, and composites (Deng et al., 2021; Irgashev and Irgashev, 2022). Moreover, university researchers, engineers, and nonprofit organizations have worked to develop low-cost cassava grinders suitable for small farms in developing regions (Arifin et al., 2023). For example, research teams from Makerere University in Uganda and the University of Nairobi in Kenya have worked with local farmers to design low-cost grinders using locally available materials (Amick and Roy, 2022). However, this research sometimes lacks scientific rigor in the design and validation of prototypes, which can affect the reliability and efficiency of the final device. In addition, researchers are conducting energy performance analyses to evaluate and improve the energy efficiency of cassava mills (Nasirembe et al., 2023a). They are using energy analysis techniques to identify inefficiencies and propose design changes to reduce energy consumption. However, some of this research may focus solely on the theoretical aspect of energy efficiency without sufficient consideration of actual field conditions, which may limit the applicability of the results. Finally, some researchers are focusing on improving the durability and robustness of cassava grinders to extend their useful life and reduce maintenance costs (Samwel and Anwar, 2023). They conduct reliability analyses and durability tests to assess the strength of materials and components. Despite these efforts, this research can sometimes underestimate the impact of certain environmental and operational conditions on equipment durability, resulting in designs that do not effectively withstand these constraints.
In summary, although significant progress has been made in the field of mechanics to improve cassava grinders, certain shortcomings remain in terms of design, energy efficiency, adaptability to real-life conditions, and durability of the equipment (Abdulkadir and Ajagba, 2022). These limitations suggest that the studies have not been conducted thoroughly and that there are still areas that require further investigation. A comprehensive review of the literature on cassava grinder improvements reveals a lack of finite element analysis (FEA) studies. In addition, the study of grinder design remains superficial.
This research stands out from previous studies with its innovative and comprehensive approach to improving the mechanical design of milling systems. It incorporates the use of Finite Element Analysis (FEA), allowing for a thorough analysis of the internal structure of the grinder to precisely identify areas of potential stress and weaknesses. Furthermore, it innovates by integrating grinder automation, thereby enhancing operational efficiency and reducing labor costs. This automation enables better management of the grinding processes, thereby increasing productivity and ensuring consistency in the final product. Another distinctive feature is the in-depth analysis of Alloy steel material in grinder construction, offering a more robust and durable solution compared to previous studies that did not consider this material. Additionally, this research integrates frequency analysis into grinder design, ensuring its durability and resistance to real-world usage conditions. Thus, it proposes a design more suited to practical needs by considering environmental and operational factors. Unlike fragmented previous studies, this research offers a comprehensive and in-depth investigation of the cassava grinder. It includes detailed static, frequency, fatigue, and safety index analyses, evaluating the proposed design under real conditions to ensure its efficiency, durability, and ability to grind large quantities of cassava without significant damage. The result will be an improved, high-performance grinder design that meets user requirements.
2 Method and materials
This work is divided into three main parts: a general study of cassava grinders, the design and finite element analysis of the cassava grinder, and finally the automation of the grinding system. First, an in-depth study was conducted on the fragmentation methods and the different types of cassava grinders currently in use. This study made it possible to evaluate the advantages of each type of grinder. Considering criteria such as efficiency, simplicity, reduced cost and compactness, the roller mill was chosen. Then, each component of the grinder was modeled using mechanical design and simulation software. The complete assembly of the machine followed this. Finite Element Analysis (FEA) was used to perform a comparative study based on three static force analyses to observe the behavior of the grinder under different loads. In addition, a frequency analysis was performed to study potential vibrations and a fatigue analysis was performed to evaluate the durability and resistance of the components under repetitive stress conditions. Finally, the automation of the grinder was developed using specialized software. A simulation was started to validate the efficiency of the automated system. To improve the interaction between the operator and the machine, a human-machine interface (HMI) was created, making the grinder more optimal and easier to use.
2.1 General study of grinder
2.1.1 Fragmentation processes
Fragmentation mode refers to the process by which a material is broken down into smaller particles or fragments during grinding or comminution (Ashley et al., 2022). In the context of cassava processing, fragmentation mode is particularly relevant to the grinding of cassava roots into finer particles or pulp, a crucial step in starch extraction and other processing applications. The fragmentation mode in cassava grinding depends on several factors, including the type of grinder used, the operating parameters, and the physical properties of the cassava roots (Pierre et al., 2007). Common fragmentation modes in cassava grinding include impact, shear, compression, and abrasion.
Impact fragmentation occurs when cassava roots are subjected to high velocity impacts with grinding elements such as hammers, blades, or pins. This results in rapid fracture and disintegration of the roots into smaller particles due to the transfer of kinetic energy (Dhakate et al., 2023). Unlike impact fragmentation, shear fragmentation involves sliding or rubbing motion between adjacent particles or between particles and grinding surfaces. In cassava grinding, the shear forces generated by the interaction between the rotating grinding elements and the cassava roots contribute to the comminution of the roots into finer particles.
Compression fragmentation occurs when the cassava roots are subjected to compressive forces between two solid surfaces. In some grinding systems, such as roller mills or crushers, cassava roots are compressed between rollers or grinding plates, resulting in fragmentation by crushing and squeezing (Qiang et al., 2021). Attrition fragmentation involves the gradual wear or abrasion of cassava roots through repeated collisions and rubbing against grinding surfaces. This mode is prevalent in grinding systems where cassava roots are subjected to frictional forces in a confined space, resulting in gradual size reduction over time.
The choice of fragmentation mode in cassava grinding depends on various factors, including the desired particle size distribution, processing efficiency, and product quality requirements (Robert, 2018). Different grinding systems may use a combination of fragmentation modes to achieve the desired results. Understanding the fragmentation mode is essential for optimizing cassava grinding processes to maximize starch extraction yield, minimize energy consumption, and ensure consistent product quality. For this study, the selected fragmentation mode is compression. The use of compression for cassava milling offers several advantages that make it particularly effective and appropriate. Unlike impact methods, which use repeated impacts and consume more energy, compression uses continuous pressure to break down materials, resulting in greater energy efficiency. This is especially important in regions where energy is limited or costly (Ahmed et al., 2020). In addition, compression allows for precise control of particle size, which is critical in processes such as starch production, where consistency of particle size ensures the quality of the final product. Compared to impact or hammer mills, compression mills experience less wear, which reduces maintenance costs and extends equipment life, providing a significant economic benefit (Edun et al., 2022). Moreover, compression mills can be adjusted to process cassava tubers of different sizes and hardness, including tougher or fibrous tubers. These machines are simpler and more robust than machine using more complex methods, making them particularly suitable for harsh environments where machine reliability is paramount (Charles et al., 2021).
In summary, compression stands out as the preferred method for cassava crushing due to its remarkable mechanical characteristics. Its energy efficiency is noteworthy, as it applies continuous pressure to break down materials, as opposed to impact methods that rely on repeated shocks, thus conserving energy. The primary objective of cassava comminution is to break the tubers into smaller particles, typically between 0.5 mm and 1 mm, to facilitate subsequent processing steps such as starch extraction. In this context, compression fragmentation emerges as the ideal method due to its ability to achieve the desired particle size range with precision and efficiency, ensuring optimal performance throughout the processing chain (Oluleye and Ekun, 2022).
2.1.2 Grinding material characteristics
Grinding material characteristics include the physical and mechanical properties of the material being processed during the grinding process. In the context of manioc processing, these characteristics primarily relate to manioc roots, which are ground into finer particles or pulp to extract starch or produce other manioc-based products. Some of the key characteristics of cassava roots relevant to milling are moisture content, texture, hardness, particle size distribution, fiber content, and starch content. Moisture content significantly affects the grindability of cassava roots; texture and hardness influence the grinding process and equipment selection (Awoyale et al., 2023). Particle size distribution affects both the grinding process and the resulting particle size distribution of the ground product, while varying amounts of fibrous material in the fiber content can affect grinding efficiency and equipment wear. Starch content is critical in determining the yield and quality of starch extraction, and other constituents such as protein, lipids, and sugars can also influence grinding behavior and product properties. Cassava roots are typically long and tapered, with a firm and uniform flesh surrounded by a detachable 1 mm thick rough and brown rind, with a diameter of 5–10 cm at the top and a length of 15–30 cm, often containing a woody vascular bundle along its axis (Emmanuel et al., 2019). In order to optimize the compression milling process of cassava, it is essential to understand the mechanical properties of the material as well as the environmental parameters that influence its behavior during milling. The mechanical properties of cassava, such as its compressive strength and hardness, are essential for the proper operation of the mill. Research has shown that the compressive strength of cassava tubers varies based on factors such as loading rate, tuber age, and loading orientation, with values ranging from 1 619.61 to 3 636.19 N in the transverse direction and 136.08–384.52 N in the longitudinal direction (Marwa et al., 2022). This variation depends on several factors, including cassava variety, growing conditions, and tuber maturity. The hardness of cassava tubers, generally measured by penetration resistance, is another important characteristic. In addition to mechanical properties, the water content of cassava is an important parameter for efficient milling. Fresh cassava tubers generally have a high moisture content, around 60%–70%. At this moisture level, the tubers are softer and therefore easier to grind due to their lower resistance to fragmentation. However, in milling processes that require more controlled fragmentation, the moisture content is reduced to around 40%–50% (Ozi and Novison, 2022). This reduction allows for more precise grinding without making the material too hard for the mill. This manioc mill is designed to grind manioc tubers with a moisture content between 40% and 70%.
2.1.3 Types of grinders considered for grinding cassava
Several types of mills can be considered for grinding cassava, each with its own characteristics and suitability for specific processing requirements.
Hammer mills use high-speed rotating hammers to impact and pulverize cassava roots against a perforated screen (Olowonubi et al., 2022). They are versatile and can process a wide range of materials and particle sizes. However, they can produce a wide particle size distribution and require frequent screen changes to achieve the desired fineness.
Ball mills use rotating cylinders filled with grinding media such as balls or rods to grind cassava roots into finer particles. They are versatile and can be used for both wet and dry grinding. Ball mills are efficient at reducing particle size, but may require longer processing times and consume more energy than other methods (Mohsen, 2021).
Roller mills consist of one or more pairs of rollers that crush and grind cassava roots between them. They provide precise control over particle size and are suitable for producing uniform, finely ground particles. Roller mills are efficient and can handle high-capacity grinding operations. The Table 1 outlines some of the critical criteria for cassava mill design and shows how different types of mills perform with respect to each criterion.
According to Table 1, the hammer mill is very efficient in terms of speed, but consumes a lot of energy. Roller mills are more energy efficient but slightly slower. Burr mills offer a good compromise between speed and energy consumption. Roller mills are the most energy efficient, followed by burr mills, with hammer mills consuming the most energy due to their impact grinding mechanism. In contrast, hammer mills require frequent replacement of parts and offer moderate durability. Hammer mills generally have a lower initial cost but higher maintenance costs, while roller mills have a higher initial cost but lower long-term maintenance costs. Burr mills have moderate initial and maintenance costs. In addition, roller mills require the least maintenance, while hammer mills require frequent replacement of parts and burr mills require periodic adjustments. Roller and burr mills can produce finer and more uniform grinds than hammer mills. Hammer mills can handle a wider range of moisture levels, making them versatile for different cassava conditions, while roller and burr mills are better suited for lower moisture levels. In addition, hammer mills are the noisiest due to their impact mechanism, while roller mills are the quietest and burr mills produce moderate noise. In terms of throughput, hammer mills offer the highest throughput, making them suitable for larger operations, while roller and burr mills offer moderate throughput. Roller and burr mills are more versatile because they can process a variety of grains and tubers, while hammer mills are primarily used for grinding. Finally, roller and burr mills provide more uniform grinding than hammer mills. Hammer and roller mills are generally easy to operate, while burr mills require more skill to accurately adjust settings. To determine the most ideal mill for cassava grinding, several key criteria must be considered: energy efficiency, durability, initial and maintenance costs, moisture handling capacity, grinding fineness and uniformity, and versatility. The roller mill is particularly advantageous due to its energy efficiency, durability, and ability to produce a fine and uniform grind with low maintenance. Although it has a higher initial cost, its lower maintenance costs and quieter operation make it a cost-effective choice in the long run.
2.1.4 Some formulas related to the roller mill
Compressive force
Compressive force is the force applied to crush or deform a material, in this case, manioc. This force is directly related to the mechanical properties of manioc, specifically its compressive strength and hardness. Compressive strength represents the ability of manioc to withstand an axial load without breaking or permanently deforming. Thus, compressive strength is determined by the stresses applied to the manioc and its ability to withstand these stresses before failure (Céline et al., 2023). For a cylinder of manioc subjected to a compressive force, this force is calculated using Equation 1.
With: Fc is compressive force (N).
σ is the compressive stress (Pa).
A is the cross-sectional area to which force is applied (m2).
The gravitational force or weight of manioc.
The force P represents the gravitational force exerted on an object by the Earth’s gravity; in other words, it is the weight of the object. The gravitational force depends only on the mass of the cassava and the gravitational acceleration (Julian, 2017). Shows Equation 2.
With: P is the Gravitational force or weight (N).
m is Cassava mass (kg).
g: Acceleration due to gravity (m/s2).
The compressive force (Fc) applied by the toothed roller to grind the cassava is derived from the mechanical pressure (σ) exerted by the roller on the particle. This force plays a crucial role in the cassava grinding process. Various factors influence the pressure force, including the materials and dimensions of the roller, as well as the rotation speed and grinding surface. This force directly compresses the particle, crushing it. Its direction is perpendicular to the roller’s surface. The intensity of this force determines the degree of fragmentation of the cassava particle, thus influencing the size of the resulting particles and their granulometric distribution. Moreover, the specific pressure force σ, normalized by the contact surface area between the roller and the cassava particle, plays a crucial role. This force determines the intensity of the pressing action per unit surface, thus affecting the uniformity of the particle’s grinding. A high specific pressure force can lead to better homogeneity in particle size. Furthermore, the gravitational force (P), acting vertically on the particle, influences its positioning and movement in the grinder. It also affects the friction force between the particle and the roller’s surface, which plays a crucial role in stabilizing the particle during grinding, thus preventing undesirable lateral movements that could reduce the efficiency of the grinding process.
These forces are illustrated in the Figure 1.
The operating frequency of the grinder
The operating frequency of the grinder is a crucial element in modal analyses as it dictates the recurrence of operating cycles over a given period. With a rotation speed of 1200 revolutions per minute (rpm) for its drive motor, this frequency directly influences the grinder’s operation. During modal analyses, this frequency is critical for assessing the machine’s natural vibration modes and identifying potential issues with resonance or structural imbalance (Amine et al., 2023). Shows Equation 3.
Where:
Cylinder Rotation Speed: Shows Equation 4:
With:
Small Pulley Revolution Calculation: Show Equations 5, 6:
With: d1 = Diameter of the large pulley in (mm).
d2 = Small Pulley Diameter (mm).
N1 = Revolution of the large pulley (rpm).
N2 = Small Pulley Revolution (rpm).
According to Equation 5, Small Pulley Revolution will be calculate by Equation 6.
Belt Length Calculation: Shows Equation 7.
2.2 Design and analysis
2.2.1 Design
Using mechanical design and simulation software, each component was designed and integrated into a 3D model. The assembly tool within the software facilitated the integration of each part while adjusting degrees of freedom as needed. Figure 2 shows the components of the machine integrated into a 3D model, each of which performs a specific function. The notched roller is used to compressively grind the material. The pulley-belt arrangement was chosen for its low initial manufacturing cost and minimal maintenance requirements, other than periodic voltage checks and belt replacement due to wear. The rotational movement of the drive pulley is transmitted to the driven pulley via the belt, with V-belts being the preferred choice due to their reduced risk of slippage and misalignment, and their ability to transmit higher power than flat belts. They provide an optimal balance of traction, speed, load capacity, and durability. Deep groove ball bearings were selected for their simplicity, ease of maintenance, and local availability. Asynchronous motors, commonly used in many industrial applications, were selected for their simplicity, ease of maintenance, and affordability, with the added advantage of being powered directly from the distribution network. The mechanical software was used for system design and operational simulation. Figure 2 shows each individually designed part of the machine, while Figure 3 shows various projections of the assembled machine. Shows Figures 2, 3.
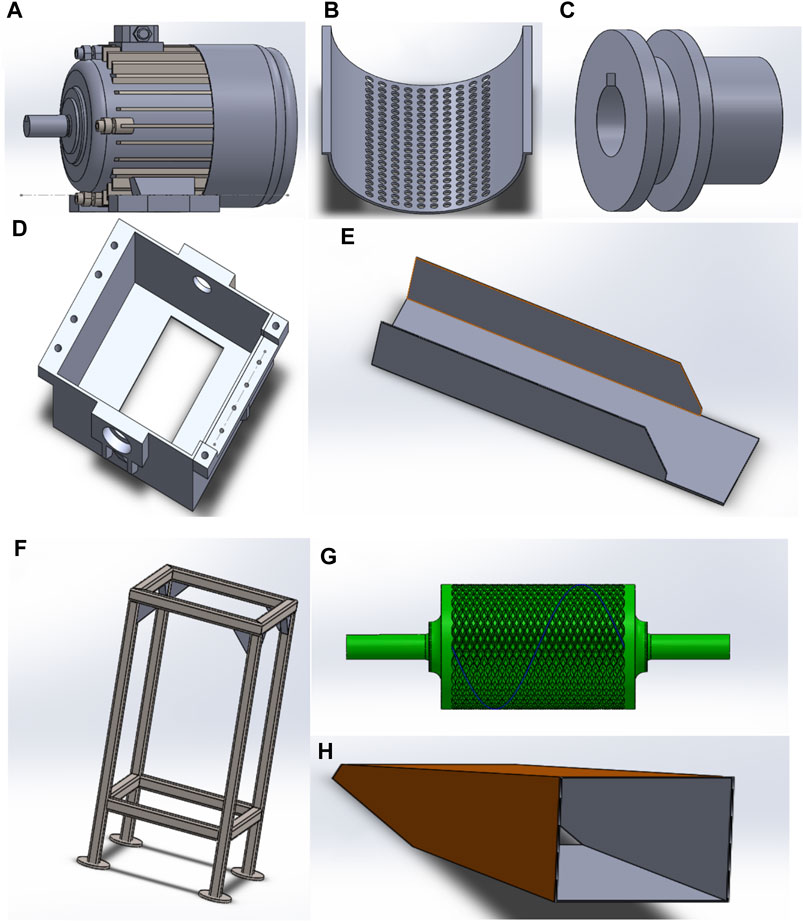
Figure 2. Grinding machine components. (A) Asynchronous motor. (B) Sieve. (C) Pulley. (D) Grinding chamber. (E) Overflow tray. (F) Grinder Frame. (G) Toothed grinding roller. (H) Grinder feed hopper.
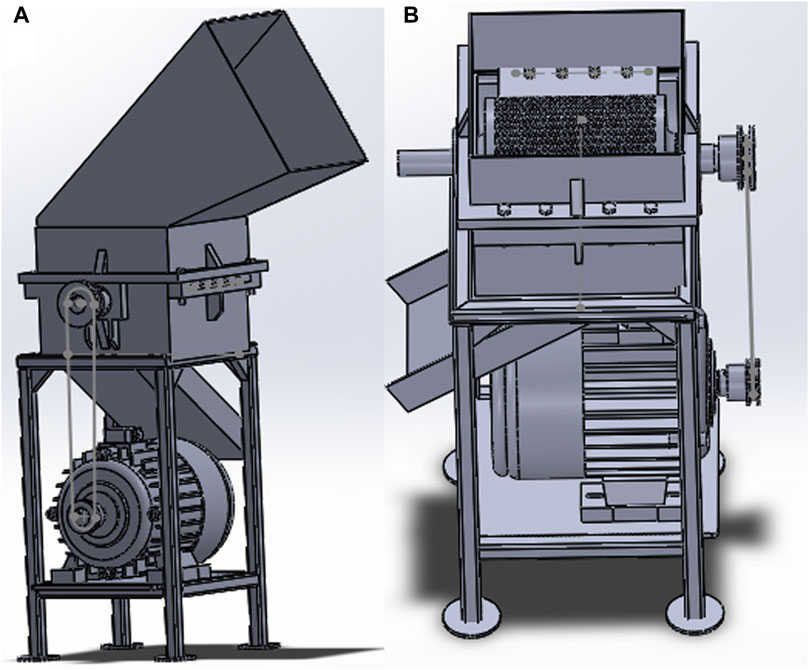
Figure 3. Grinder assembly illustrations. (A) Grinder front plane, (B) Grinder front plane without hopper.
For the continuation of the study, model (B) of the grinder will be used to provide more results and details on the crucial element of the grinder, which is the grinding roller.
2.2.2 Analysis by FEA
Finite Element Analysis (FEA) is a numerical method used to predict the behavior of a product or structure subjected to loading, stress, or temperature conditions. It relies on discretizing the model into finite elements, which are smaller sub-domains where equilibrium equations are approximated. These elements are assembled to form a mesh, and the equilibrium equations are solved numerically to obtain the system’s responses. FEA allows for the evaluation of the structural behavior of a product or component under different loads, such as forces, pressures, or moments. This helps predict deformations, stresses, and strains resulting from these loads, aiding in designing more robust and reliable products. By virtually analyzing different design configurations, FEA enables the optimization of geometry and materials to meet performance requirements while minimizing weight, manufacturing costs, and development time (Liang et al., 2023). FEA helps identify stress concentration areas or weak points in a design, enabling engineers to take corrective measures to reinforce these areas and improve product reliability. By performing virtual analyses, FEA reduces reliance on costly and time-consuming physical tests, leading to time and cost savings while speeding up the development process. FEA allows for the exploration of a variety of loading scenarios and boundary conditions, enabling quick assessment of the impact of different operational conditions on product performance. FEA helps validate the design and ensure it meets performance and safety requirements. In summary, Finite Element Analysis offers a powerful and efficient method for virtually evaluating product and structure performance, improving design quality, reliability, and efficiency while reducing costs and development timelines (Zhiqiang, 2023).
Using mechanical design and simulation software, a comprehensive approach was taken to manufacture the individual components of the manioc grinder, which are meticulously detailed in Figure 2, as well as the overall assembly shown in Figure 3. With a weight of 36 kg, the manioc grinder has compact dimensions of 1,40 m long and 0,90 m wide, allowing for easy integration into various production environments without compromising space efficiency. The grinding chamber, characterized by its cubic structure, has dimensions of 0,33 m in side length and 0,294 m in height, resulting in a volumetric capacity of 32 L, facilitating the processing of large quantities of manioc in a single operation. Central to its operation is a three-phase asynchronous motor operating at 1200 revolutions per minute (rpm), carefully calibrated to achieve optimum grinding speeds. This 7,5 kW motor provides the necessary power to ensure unrelenting and effective manioc grinding, even in the face of demanding workloads. Careful attention has been paid to the mechanical components, using robust materials and precision engineering to enhance efficiency and durability, ensuring consistent and reliable performance over extended periods of use.
The grinding machine is crafted from alloy steel, a remarkable metallic compound achieved by purposefully introducing alloying elements to the base steel (Huang et al., 2015). These elements, including chromium, nickel, manganese, vanadium, molybdenum, among others, are meticulously chosen to augment distinct properties of the steel based on the desired application criteria. Apart from these attributes, alloy steel boasts superb machinability and weldability, rendering it a favored material across various manufacturing methodologies like forging, rolling, casting, and welding. Its malleability, cutting, and shaping capabilities render it highly adaptable to diverse application needs. Table 2 furnishes insights into the material’s mechanical characteristics.
Mechanical conception and simulation software was used to perform detailed finite element analyses (FEA), including static, modal, and fatigue studies, to thoroughly evaluate the mechanical behavior of the manioc grinder. Once the grinder is assembled and imported, a series of in-depth analyses, listed below, are performed to evaluate its performance and safety under real-world operating conditions. The first step is the static analysis, a critical procedure aimed at meticulously evaluating the distribution of stresses and deformations in the grinder under specific loads such as grinding force and potential vibrations. This analysis involves accurate modeling of the grinder components, including the mechanical properties of the construction material, such as alloy steel. In addition, boundary conditions and circular supports for the grinder frame are precisely defined to reflect real-world usage conditions. Load forces are then methodically applied to all grinder components, from the grinding roller to the grinding chamber, bolts, ball bearings, and screen, to faithfully simulate cassava feeding and ensure even load distribution. Once these steps are completed, the model is meshed with great attention to detail, and the simulation software numerically solves the equilibrium equations to obtain the resulting stresses and deformations. These stress and deformation analysis results are then carefully compared to the yield strength of the material, which is 620,422 MPa for the alloy steel used. It is imperative that the maximum stresses remain below this yield strength limit to ensure the structural integrity of the grinder and prevent premature failure under applied loads. This analysis is a fundamental step in the process of evaluating the mechanical performance of the grinder and provides a solid foundation for subsequent modal and fatigue analyses.
Continuing the evaluation of the grinder’s performance and safety, a modal or frequency analysis is performed to delve deep into the machine’s inherent vibration modes and evaluate their impact on its stability and optimal operation. After importing the grinder simulation model, each component is subjected to specific boundary conditions and precise meshing is performed to ensure an accurate representation of the system. Once this process is complete, detailed stress and deformation results are displayed, revealing sensitive areas and potential points of mechanical failure. Performing this analysis is a rigorous process that involves meticulously solving the system’s equations of motion to accurately determine the natural frequencies and associated modes of vibration. This thorough investigation helps to identify potential resonant frequencies, which aids in the design of appropriate mitigation solutions to avoid any risk of structural failure. Although the grinder may exhibit a number of vibration modes, focusing on the five most significant modes is critical for accurate analysis. Ensuring that the operating frequency of the grinder is lower than the natural frequencies of the system can ensure stable and safe operation. To ensure effective protection against resonance damage, it is crucial that the operating frequency of the grinder is lower than the natural frequencies of the system. Using Equation 3, the working frequency of the grinder is determined to be 20 Hz. By carefully analyzing the first five vibration modes of the grinder, we ensure that the fundamental frequency, which is the lowest natural frequency of the system, is higher than the operating frequency of the grinder. By carefully examining each mode and comparing it to the operating frequency, we can confidently determine that the grinder is designed to withstand the mechanical stresses that will occur during operation.
Following these steps, a detailed analysis of the safety factor is carried out, based on the results of the previous analyses, to ensure the proper functioning of the grinder even in extreme conditions. This factor is calculated by comparing the stresses and loads carried by the grinder with its maximum resistance capacity in order to determine an appropriate safety factor. This process is essential to ensure that the grinder meets established safety standards and regulatory requirements. The value of the safety factor is then evaluated by comparing it to unity. If the coefficient is less than one (01), it indicates a potential risk of failure and corrective action must be taken to improve the safety of the grinder. Conversely, if the coefficient is greater than one (01), it confirms that the grinder is capable of operating safely under all intended operating conditions.
Finally, a comprehensive fatigue analysis is undertaken to evaluate the grinder’s resistance to repetitive cyclic loads, faithfully reproducing real-world usage conditions. This analysis aims to identify critical areas susceptible to fatigue damage due to the repetitive stresses incurred during grinder operation. The execution process of this analysis involves modeling the cyclic loading applied to the grinder, followed by using numerical fatigue calculation methods to estimate the grinder’s expected lifespan and the percentage of damage accumulated over time. This information allows for proposing appropriate modifications to reinforce fatigue-prone areas, ensuring a prolonged lifespan and optimal performance of the grinder under real operational conditions.
In conclusion, for these analyses, the complete grinder assembly was imported in the simulation tool of the software where the material “alloy steel” was assigned to all components. Boundary conditions were carefully defined: the grinder’s circular supports were considered fixed geometries, and loads were distributed uniformly throughout the model to simulate real-world usage conditions. The applied loads included forces on the hopper, grinding chamber walls, grinding roller shaft, and grinder frame. To simulate the load variation due to the progressive feeding of cassava, we initially modeled three load scenarios, each corresponding to a different mass of cassava: m1 = 1000 kg, m2 = 1500 kg, and m3 = 2000 kg. The corresponding loading forces for these scenarios were calculated using a specific equation (Equation 2) that accounts for the mass variation during feeding. This equation takes into consideration the kinematic parameters of the system and the dynamics of the feeding progression to estimate the forces applied on the grinder. In the absence of experimental data on the compression value used for cassava milling, we opted for an arbitrary value of 20 MPa, considering the mechanical characteristics of cassava as well as the tolerable constraints by the materials constituting the grinder. However, it is important to note that excessive compression force may lead to overheating of the grinder’s constituent materials, potentially resulting in premature degradation of these materials. Following the application of these loads, a static analysis was conducted to evaluate the deformations and stresses on the grinder under each load scenario. This analysis helps identify areas of the grinder susceptible to failure or excessive wear due to the imposed mechanical constraints. Subsequently, a modal analysis was performed to determine the natural frequencies of the system and the associated modal shapes. This analysis is essential for detecting potential dangerous resonances that could compromise the stability and structural integrity of the grinder. Finally, a fatigue analysis was undertaken to estimate the grinder’s lifespan, considering the cyclic constraints induced by the variable and repetitive loads applied during the milling process.
The applied loading forces in each scenario are as follows:
Once the previous steps are completed, it is necessary to proceed with meshing. Meshing, a critical step in finite element analysis (FEA) is used to simulate the behavior of structures and materials under physical loads. In this process, a complex structure is broken down into simpler elements, facilitating accurate numerical analysis. High-quality meshing is essential for accurate results: too coarse a mesh can result in loss of detail and underestimation of stresses, while too fine a mesh can significantly increase computation time. For the manioc grinder, meshing was performed taking into account its geometry and operation to accurately capture the structure and components of the grinder. The complex geometry of the grinder, including elements such as the grinding roller, grinding chamber, frame, motor, and hopper, requires detailed meshing to simulate applied forces, predict stresses, and identify areas prone to wear or fatigue. A mixed meshing approach was applied to the grinder. The use of a mixed mesh on the cassava grinder is essential due to the complexity of its structure, which includes areas of varied geometries and components subjected to different loads. A mixed mesh allows for fine meshes to be applied to critical areas where stresses are high and increased precision is needed, while coarser meshes are used in less stressed regions. This optimizes the accuracy of structural and fatigue analyses, ensuring efficient and precise modeling of the grinder.
Prior to meshing, the CAD model of the grinder was cleaned to eliminate redundant points or surfaces that could degrade mesh quality. The meshing adhered to several key principles: full expression of geometric features, geometric and physical continuity, good geometric shape, and smooth transition between meshes to avoid stress concentrations. These precautions ensured that the meshed model faithfully represented the structural reality and optimized the reliability of the analysis results. Figure 4 shows the diagram of force application on the grinder and mesh on the cassava grinder.
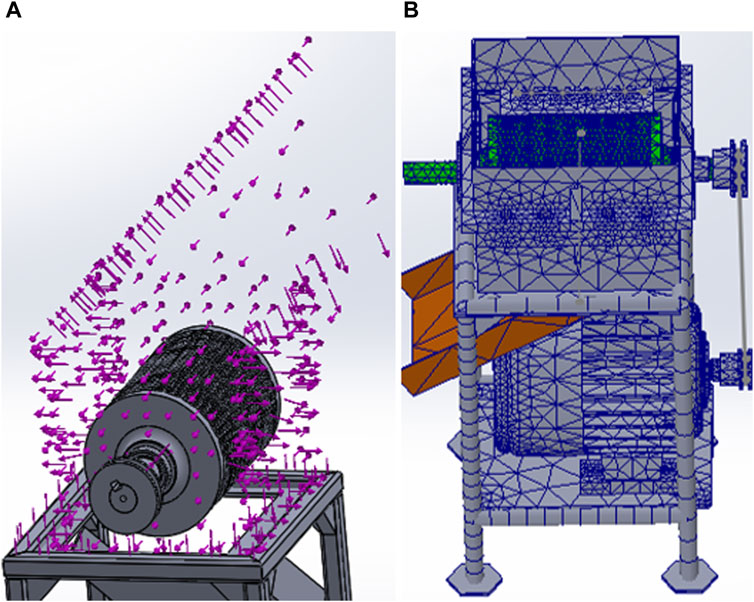
Figure 4. (A) Diagram of force application and distribution on the grinder; (B) Cassava grinding Mesh.
Figure 4 depicts a finite element mesh model comprising shell elements, beam elements, and rigid elements for 185261 nodes and 102650 elements. The mesh type utilized is neither entirely fine nor entirely coarse; it is a mixed mesh. This is attributed to the intricate structure of the grinding machine. Indeed, in a complex apparatus like a grinder, the mesh density may fluctuate due to various factors. Geometrically intricate components, such as those with curves or intricate details, necessitate a finer mesh to capture their mechanical behavior accurately. Additionally, highly stressed regions, such as the grinding blades, also demand finer resolution to precisely evaluate stresses. To conserve computational resources, a coarser mesh is often employed in less stressed regions.
2.3 Automation
As part of making the machine, more efficient and automated, automation of the grinding system of the machine was conceived. The study also focused on machine automation using a programmable logic controller (PLC). Programmable logic controllers (PLCs) are semiconductor members of the computer family that use integrated circuits instead of electromechanical devices to implement control of automation functions, to provide control of pre-actuators and actuators based on logic, analogic or digital information (Mao et al., 2021). The PLC is employed in various applications such as controlling the movement of step motor drives for milling work pieces (Cheypoca et al., 2023). It is a modular mini-controller for low power applications. Automating the cassava grinder offers several significant benefits. First and foremost, it increases the overall productivity of the grinder by optimizing the grinding processes. Repetitive and time-consuming tasks can be performed more quickly and consistently by automated systems, reducing downtime and increasing production capacity. In addition, automating the grinding process can help maintain consistent quality in finished products. Automated machines can follow precise parameters and repeat actions consistently, reducing variation and defects in finished products. In turn, automation reduces the reliance on human labor for routine tasks, which can result in significant long-term labor cost savings. As a result, it helps improve workplace safety by reducing workers’ exposure to hazardous environments. Replacing manual tasks with automated processes reduces the risk of accidents and injuries. It also enables operators to monitor machine performance in real time and take immediate action to correct problems.
Once the machine has been built and the analyses have been carried out to ensure its safety and correct operation, automation software is used to program the machine’s operating system. The automation of the cassava grinder aims to make the grinding machine more autonomous, resulting in faster and more efficient production, thereby increasing the overall yield of the cassava grinder. Hazardous tasks can be performed by automation, thus reducing the risks of accidents for workers, such as manually checking the cassava fill level, which is now solved thanks to level sensors. Advanced monitoring technologies like the HMI interface enable real-time performance monitoring and detection of potential issues, facilitating quick intervention to minimize downtime.
2.3.1 Grinding system to be automated
The latest innovation in agricultural machinery, a machine designed to crush manioc tubers, promises to revolutionize the process. The feed hopper of the crusher channels the cassava tubers into the machine, ensuring efficient processing. An electric vibrator (M2) attached to the hopper prevents cassava residues from sticking and keeps the hopper from emptying completely, alleviating the operator’s concerns. The machine features a high-level sensor (p1) that activates when the hopper is full, sending a signal to the motor feed system (dcy) to start the crusher motor (M1). An indicator light (Hr) and a siren (S) notify the operator that the system is operational. A low-level sensor (p2) triggers the vibrator to shake the hopper walls when tuber levels are low, and an empty-level sensor (p3) halts the vibrator when the hopper is empty. Table 3 provides a detailed overview of all sensors and actuators integrated into this advanced system.
2.3.2 Transcription of the system to be automate in SFC or GRAFCET
The programming language for the PLC is Ladder logic. To automate the system, it is essential to first transcribe it into GRAFCET (Graphical Representation of the Evolution of Control Systems) or SFC (Sequential Function Chart) (Schnakenbeck et al., 2023). GRAFCET or SFC is a graphical tool that outlines the various behaviors and transitions within an automated system. This method is particularly advantageous for systems characterized by sequential operations, allowing the process to be divided into distinct stages. Each stage can then be analyzed to derive equations compatible with Ladder logic. To illustrate, consider the mechanical components involved in the automation of the cassava grinder. The system includes several sensors and actuators, each playing a critical role in the automation process. The feed hopper, equipped with a high-level sensor (p1), detects when the hopper is full and sends a signal to the motor feed system (dcy). This activates the crusher motor (M1), starting the crushing process. An indicator light (Hr) turns on, and a siren (S) sounds to indicate the system is operational. As the cassava tubers are processed, the level sensor (p2) at a lower position in the hopper monitors the tuber levels. When tubers reach this sensor, it signals the electric vibrator (M2) to start, ensuring any remaining tubers are fed into the crusher. The vibrator, a small motor with disk weights, induces vibrations in the hopper, preventing blockages and ensuring continuous flow. A crucial aspect of the mechanical design is the integration of these sensors and actuators into the GRAFCET or SFC model. Each transition between states, such as from the hopper being full to the crusher motor starting, is defined by specific conditions and actions. For example, the high-level sensor (p1) triggers a transition that starts the crusher motor (M1) and activates the indicator light (Hr) and siren (S). The low-level sensor (p2) triggers the vibrator (M2) to ensure smooth material flow. Figure 8 illustrates the transcription of the system to be automated into an SFC diagram, detailing the step-by-step progression and the corresponding transitions required for the automation process. This diagram not only provides a clear visual representation of the sequence of operations but also helps in identifying potential points of failure and ensuring that all mechanical components work in harmony. By breaking down the process into manageable stages, the SFC allows for precise control and efficient automation of the cassava grinder. Shows Figure 5.
The equations derived from SFC are based on some SFC advancement rules (Yufeng et al., 1996). According to those rules Equations 8, 9 have been established.
Input Equations: shows Equation 8
Output Equations: Shows Equation 9
3 Results and discussions
3.1 Static analysis
By applying a force of P1 = 10000 N to the grinder, the statics analysis results are shown in the Figures 6A, B. By applying a force of P2 = 15000 N to the mill, the statics analysis results are shown in the Figures 6C, D. By applying a force of P3 = 20000 N to the grinder, the statics analysis results are shown in the Figures 6E, F and Figure 7 shows static analysis results of grinding roller.
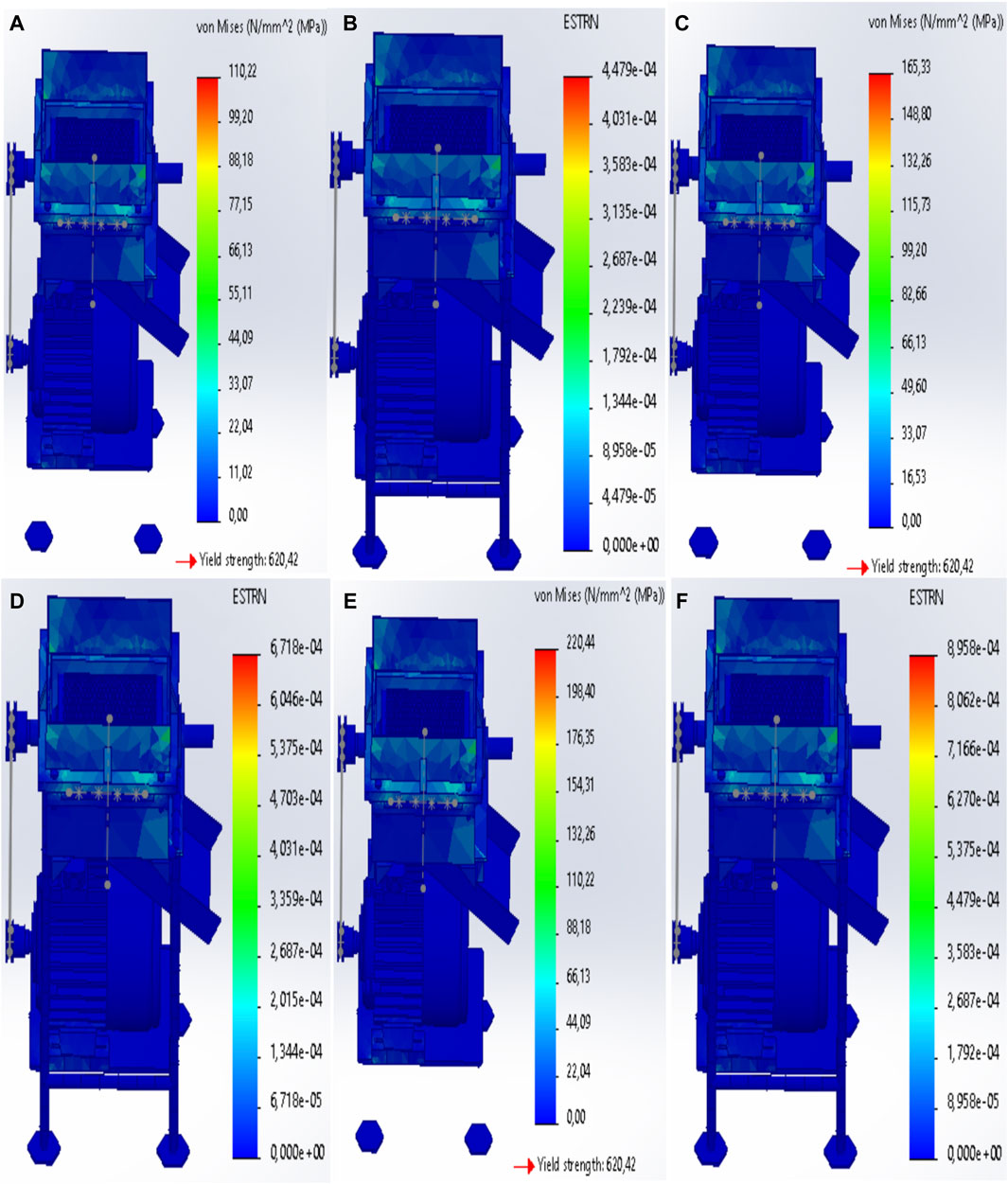
Figure 6. Static analysis test results. (A) Stress result P1. (B) Displacement result P1. (C) Stress result test P2. (D) Displacement result test P2. (E) Stress result test P3. (F) Displacement result test P3.
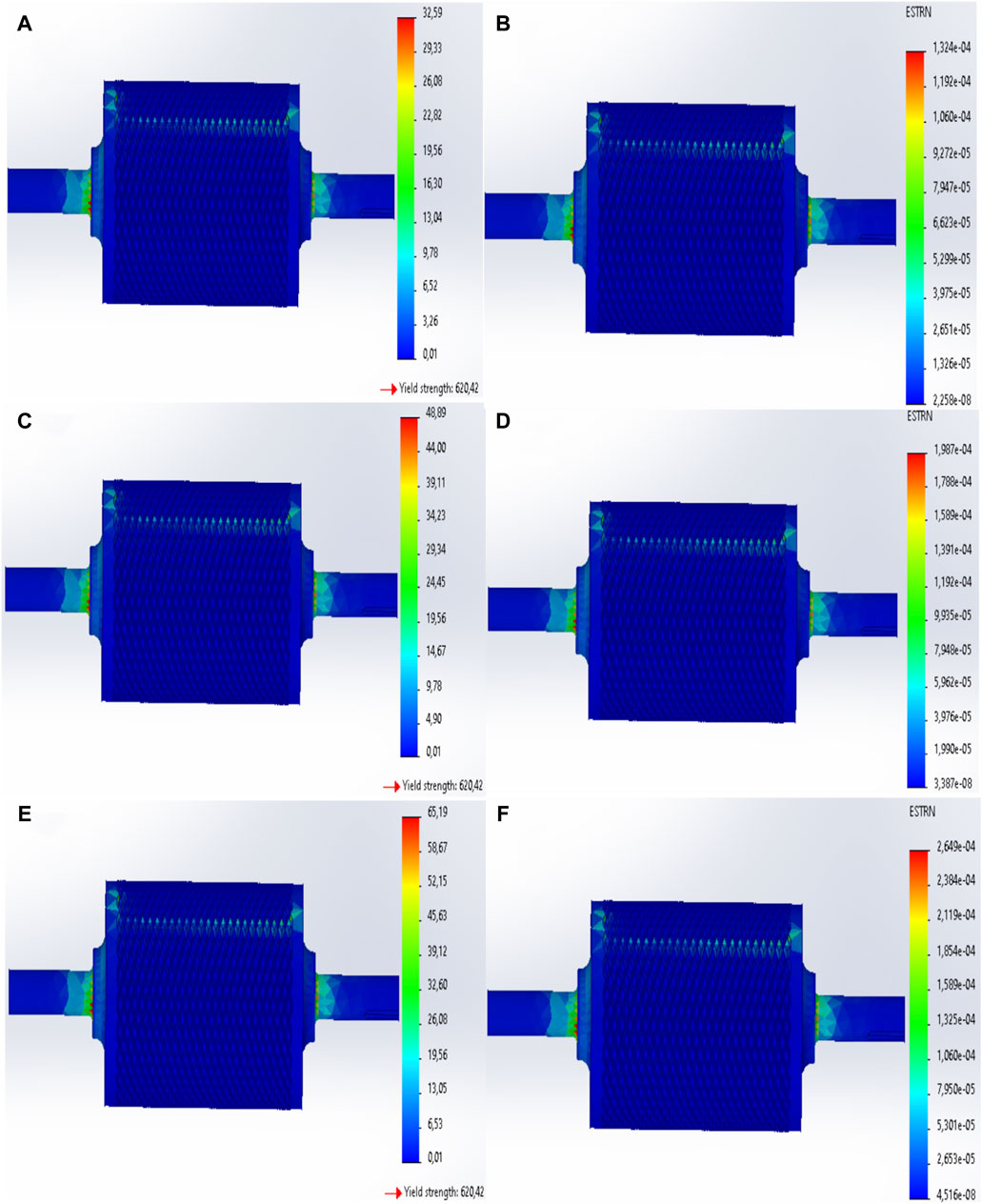
Figure 7. Static analysis test results of the grinding roller. (A) Stress result P1. (B) Displacement result P1. (C) Stress result test P2. (D) Displacement result test P2. (E) Stress result test P3. (F) Displacement result test P3.
From all the analysis results in Figure 7, it is observed that regardless of the applied force, the grinding roller is affected by stresses in the same areas. When applying a force of P1 = 10000 N, the grinding roller is subjected to a maximum stress of 29,33 MPa with a maximum deformation of 0,0001324, located mainly at the roller’s axes and, to a lesser extent, on the grinding surface of the roller. Next, when applying a load force of P2 = 15000 N, the grinding roller experiences a maximum stress of 44 MPa with a maximum deformation of 0,0001987 at both axes. Finally, when applying a load force of P3 = 20000 N, the grinding roller is subjected to a maximum stress of 58,67 MPa with a deformation of 0,0002649 at both axes. These values indicate that the maximum stress of 58,67 MPa and the deformation of 0,0002649 are well below the yield strength of the roller’s construction material. This confirms that the grinding roller is well-designed and that the chosen material is suitable for bearing the loads without deterioration. Thus, the simulation results indicate that the grinding roller can withstand the applied loads in scenarios P1, P2, and P3 without experiencing permanent deformation or structural failure. The identified critical areas, mainly at the axes and the surface of the roller, show a stress distribution that remains within the tolerance limits of the material used, thereby ensuring the robustness and durability of the roller under real operating conditions.
Table4 summarize static analyses results of cassava grinder.
According to the data presented in Table 2, the manioc grinder was subjected to load forces P1, P2, and P3 progressively. The results indicate that the grinder is not by these loads. The result graphs, located to the right of each analysis, illustrate the effect of the load forces on each component of the grinder. These graphs are divided into three color zones: blue for the safe level, green for the moderate risk level, and red for the high risk level.
Firstly, Figures 6A, B show the results of the grinder analysis under a load force of P1 = 10000N. The maximum stress recorded at the walls of the grinding chamber is 44,09 MPa, which is represented by the green color corresponding to the moderate risk zone. The maximum deformation measured at this point is 0,0001792. In parallel, the other components of the mill experience a maximum stress of 11,02 MPa, shown in blue, corresponding to the safe zone, with a maximum deformation of 0,0000447.
Secondly, Figures 6C, D show that under a load force of P2 = 15000N, the maximum stress on the walls of the grinding chamber reaches 66.13 MPa, shown in green, indicating a moderate risk. The maximum observed deformation is 0,0002687. In parallel, the other components experience a maximum stress of 16,53 MPa, indicated in blue, with a maximum deformation of 0,00006718.
Finally, Figures 6E, F show that when the cassava grinder is subjected to a load force of P3 = 20000N, the grinding chamber is subjected to a maximum stress of 88,18 MPa, represented by green zones on the walls. The measured maximum deformation is 0,0003583. In parallel, the other components experience a maximum stress of 22,04 MPa, indicated in blue, with a maximum deformation of 0,00008951.
In accordance with the methodology previously studied, these stresses are compared to the yield strength of the alloy steel material used to manufacture the grinder. It should be noted that according to Table 2, the yield strength of this alloy steel is 620,422 MPa. The observed maximum stress of 88,18 MPa is well below this yield strength, indicating that the selected material is ideal for the loads applied to the grinder. Thus, these results show that even under increasing load forces, the manioc grinder maintains stresses well below the yield strength of the alloy steel. The maximum deformations observed are also small, indicating that the grinder components will not deform under the expected loading conditions. The design and material selection ensure that the grinder can withstand the load forces without risk of structural failure. The identified stress zones (blue for safe, green for moderate risk) are consistent with safety and performance. Therefore, the grinder model is well designed to withstand the mechanical stresses imposed by operating conditions, ensuring its durability and efficiency.
3.2 Frequency analysis
The results of frequency analysis is shown of Figure 8.
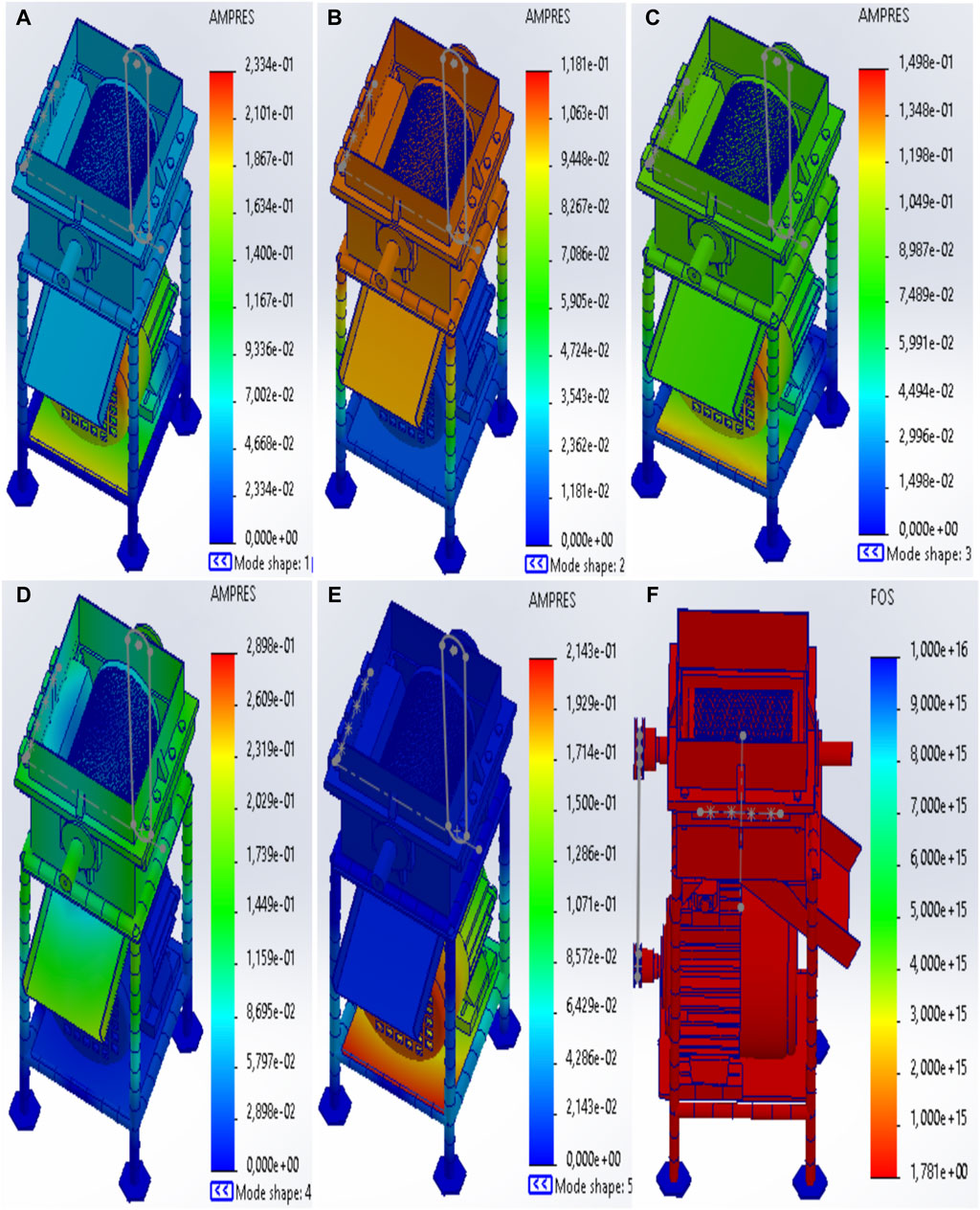
Figure 8. (A) Mode shape1. (B) Mode shape2. (C) Mode shape3. (D) Mode shape4. (E) Mode shape5. (F) Factor of Safety result.
The Table 5 summarizes natural frequencies of the machine studied according to each mode shape.
After a detailed modal analysis of the cassava grinder, and in accordance with the methodology studied, the first five modes of the cassava grinder have specific natural frequencies: f1 = 23,087 Hz, f2 = 27,516 Hz, f3 = 29,507 Hz, f4 = 51,339 Hz, and f5 = 106,31 Hz. These results are illustrated in Figures 8A–E. The first mode, also called the fundamental mode, has a natural frequency of 23,087 Hz. The entire grinder is subjected to a vibration with a maximum amplitude of 0,04668, shown in blue. However, the drive motor housing and the motor support plate experience vibrations with a maximum amplitude of 0,2101, indicating a greater susceptibility to vibration in these areas.
The second resonance mode characterized by a natural frequency of 27,516 Hz, shows that the lower part of the manioc grinder is subjected to a vibration with a maximum amplitude of 0,1181, while the upper part of the grinder is affected by a vibration with a maximum amplitude of 0,1063. This suggests an uneven distribution of vibrations across the grinder, with higher amplitudes in the upper sections.
The third resonant mode, with a natural frequency of 29,507 Hz, results in a vibration with a maximum amplitude of 0,07489 on all components of the grinder except the fan-side flange of the motor and the motor support plate, where the maximum vibration amplitude is 0,1348. These parts of the grinder are more sensitive to vibration.
The fourth resonance mode, with a natural frequency of 51,339 Hz, subjects the entire grinder to vibration with a maximum amplitude of 0,1449 at the top of the grinder and 0,02898 at the bottom. This mode indicates a greater intensity of vibration in the upper parts of the grinder compared to the lower parts.
The fifth and final resonance mode, with a natural frequency of 106,31 Hz, is characterized by a vibration with a maximum amplitude of 0,2143 on the entire grinder, except for the motor fan flange and the motor support plate, where the maximum amplitude is 0,1929. These values indicate critical points where vibrations are particularly significant.
According to the methodology studied, for a grinder to be reliable, robust and protected from resonance, it is imperative that the operating frequency of the grinder, which is 20 Hz, be lower than the natural frequencies of the grinder. When all of the natural frequencies of the grinder are compared to the 20 Hz operating frequency, it is apparent that all of the natural frequencies are higher than the operating frequency of the grinder. Thus, the grinder is protected from resonance phenomena caused by the vibrations of each resonance mode, ensuring stable and durable operation.
3.3 Factor of safety
According to Figure 8F, the safety factor (FoS) of the manioc grinder has a value of 1,781. Referring again to the methodology studied regarding the safety factor, it is noted that this factor is greater than 1. This means that this model of grinder and the chosen construction material are ideal and safe for manioc grinding. The safety factor (FoS) of 1,781 indicates that the mill can withstand an additional 78,1% of the expected operational loads before reaching the point of failure. This coefficient is critical in the context of mechanical design because it provides a margin of safety against uncertainties associated with real-world operating conditions, material variations, and manufacturing inaccuracies. Thus, with an FoS of 1,781, the material of the grinder (alloy steel) has been correctly chosen to guarantee not only safety, but also the durability and reliability of the cassava grinder under the various load conditions it may encounter during use. This confirms that the design and choice of materials are appropriate and ensure the safe and efficient operation of the grinder.
3.4 Fatigue analysis
Fatigue analysis result is shown on Figure 9.
Based on the findings presented in Figure 9, the analysis indicates that the machine will experience minimal damage, estimated at only 10%. This suggests that the machine operates within a safe operational range. Moreover, the assessment of total life expectancy, represented by the total number of cycles, demonstrates that the grinding machine is expected to endure an extensive lifecycle of 1e+09 cycles. The machine’s design specifications include an intended usage of 8 h per day with a grinding capacity of 2000 kg per hour, allowing for intermittent rest periods. With a total cycle count of 1e+09 cycles, this translates to an impressive service life of approximately 347000 years. Over this period, the machine is projected to process a total of 2e+12 kg of cassava, equating to an annual output of 5840000 kg. These results underscore the robustness and reliability of the chosen design and materials. They affirm that the machine satisfies crucial criteria such as safety, design integrity, structural durability, crushing capacity, and operational reliability. Consequently, users can have confidence in the machine’s performance, meeting their needs and expectations effectively.
3.5 Automation of the grinding system result
Automation of the grinding system result is shown in Figure 10.
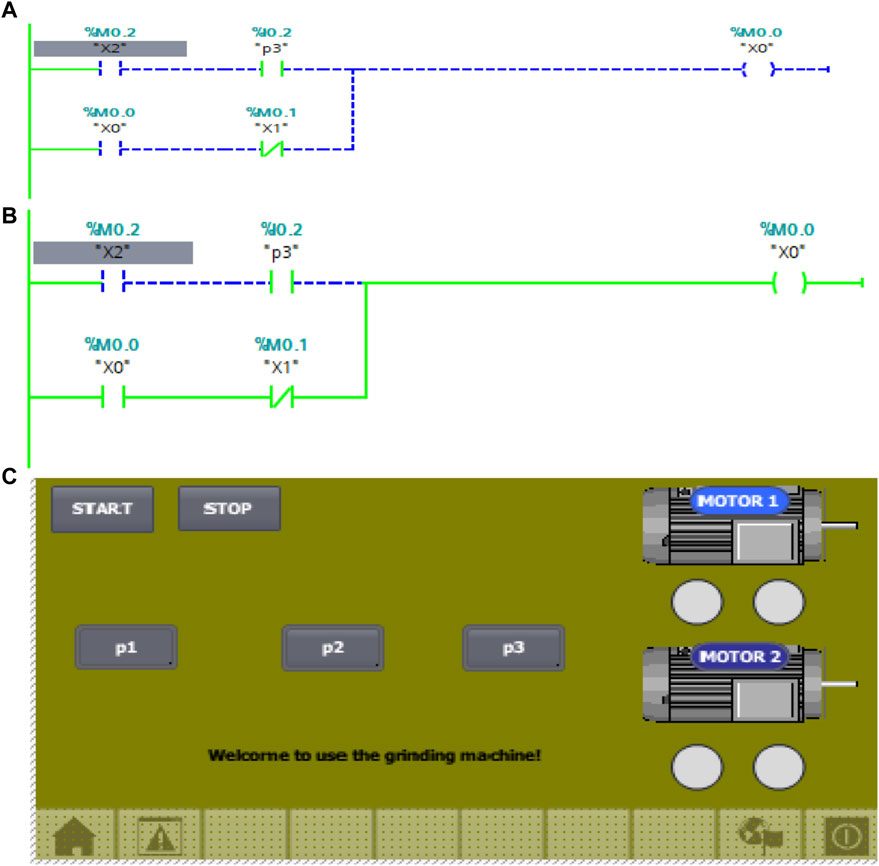
Figure 10. Automated Cassava Grinder Results: (A) System Simulation at stop; (B) System Simulation at Run; (C) Cassava Grinder HMI Interface.
The cassava grinder automation system features several innovative aspects. Unlike conventional systems, this approach integrates advanced sensor technology to monitor the consistency of the ground cassava in real time, allowing for automatic adjustments to the grinding parameters. Sensors, strategically placed along the grinder, measure the particle size of the ground cassava and send this data to a centralized control unit. This unit uses data processing algorithms to instantly adjust the rollers’ rotation speed and the applied pressure. Although the system has not yet been physically implemented, simulations show that this innovation improves efficiency and significantly reduces material and time losses. This is illustrated by Figures 10A, B, where a programmed system can be observed at rest. Once the simulation of the grinder’s operating conditions is activated, the sensors detect consistency variations and adjust the grinding parameters accordingly. This closed-loop feedback process allows for continuous optimization. In case of a problem, the sensors and integrated diagnostic systems can quickly identify the fault and facilitate its correction, saving time and preventing the loss of raw materials. For instance, if a sensor detects overheating due to excessive pressure, the system can immediately reduce the applied pressure or stop the grinder to prevent material damage.
Moreover, the system uses automatic algorithms to optimize the grinding process based on variations in the raw material. These algorithms analyze data in real-time to adjust parameters such as roller speed, pressure, and feed rate. This ensures consistent quality of the final product while minimizing energy consumption. Compared to the study mentioned in the introduction that relied on energy analysis theories for optimization, this solution provides a technical and practical response through automation. In terms of energy consumption, this solution reduces the average power of the automated grinder to 5 kW, compared to traditional systems that typically require between 6 and 8 kW for similar performance. This represents a nearly 20% reduction in energy consumption. Real-time optimization of grinding parameters reduces unnecessary processing cycles, resulting in 10% lower energy consumption per ton of cassava processed compared to classical systems.
Compared to traditional grinders, this simulated automation system shows significant improvements in energy consumption, grinding efficiency, and process stability. These simulated results clearly demonstrate the potential benefits of this cassava grinder automation system and confirm the improvements that this innovation could bring if implemented. Through programming and simulation, It was able to meticulously validate the functionality and sequencing of the Sequential Function Chart (SFC), ensuring precise automation of the grinder. Moreover, with the aid of the Human-Machine Interface (HMI) on Figure 10C, we successfully simulated the display screen interface of the system process, as elucidate (Junchen and Lin, 2019). This sophisticated interface not only enables meticulous monitoring of the machine’s operations but also streamlines system management tasks. Consequently, it provides a comprehensive means to closely oversee the grinder’s automation process, ensuring its seamless operation and performance.
The static analysis reveals that the maximum observed stress (88,18 MPa) is well below the yield strength of the alloy steel used (620,422 MPa), confirming the suitability of the material and design for the applied loads. With low maximum deformations, the grinder will not deform under expected loading conditions, ensuring durability and efficiency. In terms of modal analysis, all natural frequencies of the grinder are higher than the operating frequency of 20 Hz, protecting the device from resonance phenomena and ensuring stable and durable operation. The safety factor (FoS) of 1,781 indicates that the grinder can withstand an additional 78,1% of operational loads before reaching failure, ensuring an adequate margin of safety against operational and manufacturing uncertainties. Finally, fatigue analysis demonstrates that the grinder will only experience 10% damage, with an estimated lifetime of 1e+09 cycles, confirming that the grinder is well-designed to withstand long-term cyclic loads. The proposed grinder model is robust, reliable, resistant, durable, and safe. The results show a significant improvement in the automation of cassava grinders, directly impacting efficiency and safety. By integrating advanced sensors and actuators, the system ensures continuous operation with minimal human intervention, thereby resolving issues of manual monitoring and safety risks. This advancement represents a substantial progress compared to traditional methods, which are often prone to inconsistencies and operational interruptions. A significant contribution of this research is the implementation of a GRAFCET model to design and automate the grinding process. This model offers a structured method to develop and analyze the automation sequence, enhancing system reliability and maintainability. Additionally, an advanced monitoring system, utilizing level sensors in the feed hopper coupled with an electric vibrator, ensures a continuous flow of cassava tubers, reducing the risk of blockages and improving overall efficiency. Real-time performance indicators, such as warning lights and sirens, provide immediate feedback to operators, enhancing responsiveness and safety. Transcribing the automation process into an SFC diagram simplifies design and implementation phases, aiding in quick maintenance resolution and automation sequence optimization. Integration of automatic safety mechanisms reduces the need for manual intervention and associated risks, improving worker safety and operational reliability.
Furthermore, this research includes a comprehensive structural and modal analysis of the grinder, ensuring its ability to withstand operational stresses and maintain performance over time. Static analysis reveals that the maximum stress remains well below the material’s yield strength, indicating a high safety factor. Frequency analysis shows that natural frequencies of components are well separated from operational frequencies, minimizing the risk of resonant vibrations. Fatigue analysis confirms the system’s ability to endure cyclic loads without significant degradation, and the calculated safety coefficient exceeds industry standards, ensuring robust and reliable design. The innovations presented pave the way for more sophisticated and efficient cassava processing systems. Future research could integrate machine learning and artificial intelligence to further enhance performance and adaptability. The principles and methodologies demonstrated can also be applied to other agricultural processing systems, expanding the impact of research contributions.
4 Conclusion
In conclusion, this study represents a major advancement in the automation of manioc grinders, with particular emphasis on the importance of Finite Element Analysis (FEA) and its critical role in this research. A rigorous approach allowed for a detailed mechanical design of the grinder, incorporating static, frequency and fatigue analysis through FEA. This method verified the structural robustness and operational reliability of the grinder under various load conditions, ensuring the durability and efficiency of the system. Specifically, the static analysis showed that the maximum stresses observed were well below the yield strength of the alloy steel used, confirming that the material and design were appropriate for the applied loads. In addition, the frequency analysis showed that the natural frequencies of the grinder were higher than the operating frequency, protecting the device from resonance phenomena. Finally, the fatigue analysis confirmed that the grinder could withstand cyclic loads without degradation, ensuring a long service life.
Another major innovation is the automation of the grinding process, based on a GRAFCET model and a sophisticated human-machine interface (HMI). This allows continuous operation with minimal human intervention, improving the efficiency and safety of manioc processing. The integration of advanced sensors and actuators in the system ensures precise monitoring and easy handling, reducing the risk of blockages and improving operational responsiveness and safety. The results obtained demonstrate the technical viability and optimal performance of the system, paving the way for future research and applications in agricultural automation and food processing. By integrating cutting-edge technologies and advanced methodologies, this study contributes to addressing the current challenges of the agro-food industry and meeting the growing demands for process sustainability, efficiency and safety.
To further improve the quality of this grinder, a discrete element method (DEM) analysis would be ideal. DEM would allow for a detailed understanding of the interactions between the cassava particles and the grinder components, providing precise insights into the grinding phenomena at the microscopic scale. The integration of DEM would provide critical information on the distribution of forces and stresses within the mill during the grinding process. Combining the results of FEA with those of DEM would provide a holistic view of the mechanical behavior of the grinder. In conclusion, adding a DEM analysis to this study would provide a more comprehensive and accurate understanding of the operation of the manioc grinder. This would strengthen the robustness of the design and ensure that every aspect of the grinding process is optimized for superior performance, thereby continuously improving the efficiency, durability, and safety of the system.
Data availability statement
The raw data supporting the conclusions of this article will be made available by the authors, without undue reservation.
Author contributions
IO’sG: Conceptualization, Data curation, Formal Analysis, Investigation, Methodology, Resources, Software, Writing–original draft, Writing–review and editing. CG: Funding acquisition, Methodology, Supervision, Validation, Writing–review and editing.
Funding
The author(s) declare that no financial support was received for the research, authorship, and/or publication of this article.
Conflict of interest
The authors declare that the research was conducted in the absence of any commercial or financial relationships that could be construed as a potential conflict of interest.
Publisher’s note
All claims expressed in this article are solely those of the authors and do not necessarily represent those of their affiliated organizations, or those of the publisher, the editors and the reviewers. Any product that may be evaluated in this article, or claim that may be made by its manufacturer, is not guaranteed or endorsed by the publisher.
References
Abdulkadir, B., and Ajagba, G. C. (2022). Cassava grating machines, designs and fabrication: a review of related literature. AJMRA 3 (1), 1–11. doi:10.58314/908876
Ahmed, A. S., Seifelnassr, A. M., Abouzeid, G., and Zainelabdein, A. (2020). Grindability of quartz under compressive and impact forces. J. Petroleum Min. Eng. 22, 51–57. doi:10.21608/JPME.2020.28947.1032
Amick, J., and Roy, W. M. (2022). “The importance of local institutions: bottomup innovation in Uganda,” in Handbook of innovation and appropriate technologies for international development (Cheltenham: Edward Elgar Publishing), 240–258. doi:10.4337/9781800887824.00024
Amine, J. D., Adinife, P. A., and Sampson, C. O. (2023). Vibro-acoustic assessment of grain grinding machine for health risk factors analysis. Bitlis Eren Univ. J. Sci. Technol. 13 (1), 17–37. doi:10.17678/beuscitech.1217010
Anwar, A. F., Mary, S., Leena, T., and Samwel, M. (2022). Cassava (Manihot esculenta) dual use for food and bioenergy: a review. Hoboken, NJ, Unites States: Food and Energy Security. doi:10.1002/fes3.380
Arifin, F., Muhammad, S. A., and Angger, B. P. (2023). Desain dan analisis cassava chopper machine. Angkasa J. Ilm. Bid. Teknol. 15 (1), 85. doi:10.28989/angkasa.v15i1.1638
Ashley, D., Lalith, K., and Rohit, R. (2022). Understanding the effects of process parameters and material properties on the breakage mechanisms and regimes of a milling process. Chem. Eng. Res. and Des. 188, 607–619. doi:10.1016/j.cherd.2022.10.015
Awoyale, W., Olatoye, K., and Maziya-Dixon, B. (2023). Cassava pectin and textural attributes of cooked gari (eba) and fufu dough. doi:10.5772/intechopen.109580
Céline, S., Mickaël, D., and Julie, G. (2023). Transducing compressive forces into cellular outputs in cancer and beyond. Life Sci. alliance 6 (9), e202201862. doi:10.26508/lsa.202201862
Charles, O., Dare, O., Aderibigbe, A., Morakinyo, T. A., Olusola, F., and Olusunmade, B. O. (2021). A study on the influence of the loading rate and orientation on some mechanical properties of cassava tubers of different ages. Res. Agric. Eng. 67 (1), 34–44. doi:10.17221/57/2020-RAE
Cheypoca, T., Amata, L., and Virot, W. (2023). “Circular interpolation using siemens S7-1200,” in International conference on engineering, applied sciences, and technology (ICEAST) (IEEE), 1–4. doi:10.1109/ICEAST58324.2023.10157875
Deng, X., Chen, G., He, C., Zheng, R., Cai, Z., Wang, Z., et al. (2021). Properties of grinding tool material for double-disc straight-groove grinding method based on friction and wear experiment. Int. J. Adv. Manuf. Technol. 114, 2243–2259. doi:10.1007/S00170-021-07016-3
Dhakate, M. M., Aditya, V., and Devang, V. K. (2023). Breakage of a single particle in an air jet mill. ACS Eng. Au 3 (4), 257–264. doi:10.1021/acsengineeringau.3c00004
Edun, B. M., Oluseyi, O., Ajayi, P., and Babalola, O. (2022). Failure mode and cost effect analysis of a model bone crushing hammer. Key Eng. Mater. 917, pp63–69. doi:10.4028/p-z01ver
Emmanuel, D., Paul, D., Funkenbusch, E., and Effah, K. (2019). Characterization of cassava fiber of different genotypes as a potential reinforcement biomaterial for possible tissue engineering composite scaffold application. Fibers Polym. 20 (2019), 217–228. doi:10.1007/S12221-019-8702-9
Huang, D., Sun, G., Zhang, S., Han, L., Tian, J., Meng, J., et al. (2015). Alloy steel and manufacturing method thereof.
Igwe, D. O. (2023). Diseases of Cassava. Handbook of plant disease management, 1–37. doi:10.1007/978-3-030-35512-8_31-1
Irgashev, B., and Irgashev, A. (2022). Selection of gear tooth material based on the wear resistance. J. Sci. innovative Dev. 5, 24–35. doi:10.36522/2181-9637-2022-3-3
Julian, S. (2017). A vector field approach to calculating gravitational forces. New J. Phys. 19, no7–pp73032. doi:10.1088/1367-2630/AA7C80
Junchen, O., and Lin, S. (2019). “Design of automotive brakejoint size detection system based on TIA Portal,” in International conference on electronic information technology and computer engineering (EITCE) (IEEE), 317–322. doi:10.1109/EITCE47263.2019.9094820
Liang, L., Minliang, L., John, A. E., and Wei, S. (2023). PyTorch-FEA: autograd-enabled finite element analysis methods with applications for biomechanical analysis of human aorta. Comput. Methods Programs Biomed. 238, pp107616. doi:10.1016/j.cmpb.2023.107616
Mao, X., Xin, L., Yanhong, H., Jianqi, S., and Yueling, Z. (2021). Programmable logic controllers past linear temporal logic for monitoring applications in industrial control systems. IEEE Trans. Industrial Inf. 18 (7), 4393–4405. doi:10.1109/tii.2021.3123194
Marwa, G., Omer, A., David, O., Koteng, J., Ng'ang'a, T., and Mohammed, M. (2022). Analysing the effect of cassava flour as a mixture on the physical, mechanical, and durability properties of high-strength concrete. Civ. Eng. J. 8 (12), 3866–3882. doi:10.28991/cej-2022-08-12-015
Mohsen, M. (2021). Modelling of the high-energy ball milling process. Adv. Mater. Phys. Chem. 11 (1), 31–44. doi:10.4236/AMPC.2021.111004
Nasirembe, W., Rotich, E., Ruttoh, R., Nyakach, S., Maingi, S., Cheboswony, R., et al. (2023a). Evaluation of a modified multipurpose cassava processing machine for size reduction. Innovative Syst. Des. Eng. 13 (01). doi:10.7176/isde/13-1-06
Nasirembe, W., Rotich, E., Ruttoh, R., Nyakach, S., Maingi, S., Cheboswony, R., et al. (2023b). Evaluation of a modified multipurpose cassava processing machine for size reduction. J. Biol. Agric. Healthc. 13 (08). doi:10.7176/jbah/13-8-03
Olowonubi, J. A., Adejugbe, I. T., Fatounde, S. A., Aigbovbiosa, J. O., Oyegunwa, O. A., Komolafe, O., et al. (2022). Design and development of a petrol-powered hammer mill machine. Phys. Sci. Int. J. 26 (7), 33–41. doi:10.9734/psij/2022/v26i7754
Oluleye, A. E., and Ekun, K. R. (2022). Development of a predictive maintenance model for a cassava pulveriser. J. Eng. Agric. and Environ. 8, 14. doi:10.37017/jeae.v8i2.82
Ozi, A., and Novison, R. (2022). Studi analisis pengaruh temperatur terhadap ketebalan pada proses pengeringan ubi gaplek. J. Tek. Mesin 15 (2), 133–139. doi:10.30630/jtm.15.2.847
Peter, O. K., Leo, A. S., Agbetoye, S., and Agboola, O. (2021). Cassava mash process handling. International Review of Chemical Engineering (IRECHE) 13, 27. doi:10.15866/IRECHE.V13I1.20641
Pierre, B., El-Aïd, J., and Jacques, Y. (2007). Fragmentation appliquée aux minerais métalliques. doi:10.51257/A-V1-J3052
Qiang, Z., Qing, G., Yongtai, P., Changyong, Z., and Yinghua, W. (2021). Experimental research on the strength distribution of brittle spheres under compression. Physicochem. Problems Mineral Process. 57, 58–69. doi:10.37190/PPMP/132479
Raufu, S. O., Deola-Tayo, L., Azeez O, I., Mohammad B, A., and Oluwole O, O. (2023). Cassava production enterprise in the tropics, 284. doi:10.5772/intechopen.104677
Robert, N. (2018). Cassava in central and western Africa: postharvest constraints and prospects for research and market development. London, United Kingdom: IntechOpen, 199–217. doi:10.5772/INTECHOPEN.71507
Salazar, A. J. R. (2022). Sustainable technology for the production of artisanal cassava starch. Rev. Verde de Agroecologia e Desenvolv. Sustentável 17 (3), 178–185. doi:10.18378/rvads.v17i3.9269
Samwel, M. K., and Anwar, A. F. (2023). Advances in cassava trait improvement and processing technologies for food and feed. doi:10.5772/intechopen.110104
Schnakenbeck, A., Robin, M., Marcus, V., Stefan, K., and Alexaner, F. (2023). Transformation of GRAFCET into GAL for verification purposes based on a detailed meta-model. AT-AUTOMATISIERUNGSTECHNIK 71 (1), 56–67. doi:10.1515/auto-2022-0094
Sobowale, S. S., Olawale, P. O., Idowu, A., and Okonkwo, C. E. (2022). Effect of heat-moisture treatment on the functional and rheological characteristics of cassava (Manihot esculenta) starch. Trans. R. Soc. S. Afr. 77 (1), 89–99. doi:10.1080/0035919X.2022.2036265
Sumit, K. (2023). Optimization for truss design using Bayesian optimization. arXiv.org. doi:10.48550/arXiv.2306.01763
Wulandari, S., Ericha, N. A., Aniswatul, K., Afrizal, M. R., Titiek, P., and Ita, Y. (2023). Cassava as a local material source for some types of food products. E3S Web of Conf 373. 04025. doi:10.1051/e3sconf/202337304025
Yufeng, S., Hongxin, H., and Liangmo, Z. (1996). Retention in SFC at high density. Hrc-journal High Resolut. Chromatogr. 19 (3), 169–175. doi:10.1002/JHRC.1240190310
Zheng, M., and Jie, Y. (2023). A probabilistic multi-objective optimization mechanical design. J. Umm Al-Qura Univ. Eng. Archit. 14 (2), 115–121. doi:10.1007/s43995-023-00023-3
Keywords: mill, machine, load, value, grinding
Citation: Oroun’Gobi I and Guo CG (2024) Finite element analysis and automation of a medium scale grinder applied to the manufacture of cassava starch. Front. Mech. Eng. 10:1427388. doi: 10.3389/fmech.2024.1427388
Received: 03 May 2024; Accepted: 29 July 2024;
Published: 08 August 2024.
Edited by:
Dawood Desai, Tshwane University of Technology, South AfricaReviewed by:
Innocent Nnanna, Akanu Ibiam Federal Polytechnic, NigeriaEmmanuel Olatunji Olutomilola, Federal University of Technology, Nigeria
Sheriff Babatunde Lamidi, Lagos State University of Science and Technology, Nigeria
Copyright © 2024 Oroun’Gobi and Guo. This is an open-access article distributed under the terms of the Creative Commons Attribution License (CC BY). The use, distribution or reproduction in other forums is permitted, provided the original author(s) and the copyright owner(s) are credited and that the original publication in this journal is cited, in accordance with accepted academic practice. No use, distribution or reproduction is permitted which does not comply with these terms.
*Correspondence: Chen Guang Guo, Z3VvY2hlbmd1YW5nQGxudHUuZWR1LmNu