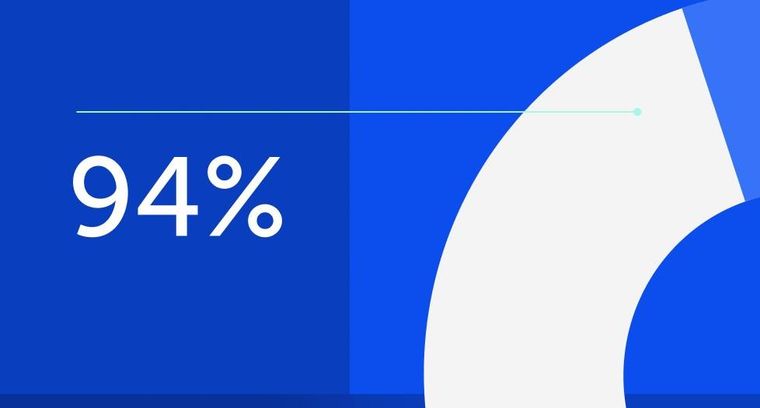
94% of researchers rate our articles as excellent or good
Learn more about the work of our research integrity team to safeguard the quality of each article we publish.
Find out more
ORIGINAL RESEARCH article
Front. Mech. Eng., 25 July 2024
Sec. Solid and Structural Mechanics
Volume 10 - 2024 | https://doi.org/10.3389/fmech.2024.1419210
This article is part of the Research TopicTechnical Briefs in Mechanical Engineering: Advances and InnovationsView all 8 articles
The layered configuration of different material plates is one of the ways of achieving protection against different kinds of kinetic energy ammunitions. The thickness of each plate is one of the most important influencing parameters to prevent the penetration of the projectile. In the present study, a layered configuration of the Al2O3 and Al 7075-T651 is analysed, to prevent the perforation of 7.62 mm Lead core projectile, under normal impact conditions, by using LS-DYNA numerical simulations. Experiments were conducted on Al 7075-T651 plate and Numerical model was validated with experiment results. To achieve the objective, the validated numerical model was used to investigate influence on various Al2O3 and Al 7075-T651 combinations. Three factors led to the selection of Al 7075-T561 and Al2O3 as the target materials. First, the literature review revealed that these materials have already been employed in the construction of armour. Second, Al2O3 is a brittle material whereas Al 7075-T651 is ductile. Consequently, when combined in a layered arrangement, these materials offer the ideal destroyer-absorber arrangement. Thirdly, these materials have lower densities than steel. As a result, these materials offer a lightweight alternative for lead core 7.62 mm bullet defense. From the analysis, it is observed that two layered configurations were found to be effective in the prevention of bullet perforation: a front plate of Al2O3 that was 10 mm thick and had a rear plate of Al 7075-T651 that was 06 mm thick, and a front plate of Al2O3 that was 04 mm thick and had a 12 mm thick layer of Al 7075-T651.
Various materials are being developed and researched for the application of ballistic protection against different attacks. Some of the ways of protection against kinetic energy ammunition is to use high-strength materials, configuration of different materials in layered formats such as double layered, triple layered configurations, spaced armour, etc. The design of armouring is generally based on the type of threat. Various research has been conducted on different parameters related to impact studies. J. Venkatesan et al. (Venkatesan et al., 2017) evaluated ballistic performance of layered armor made of SiC and aluminum against layered armor made of Al2O3 and aluminum against ogive nose projectiles. Results showed that performance of SiC-Al armour is better and it causes more damage of the bullet. Turhan et al. (2008) studied layered configuration of Al 2024-T351 and Al2O3 against 7.62 mm AP bullet. In this study, new material constants were obtained that better described the deformation of steel core and aluminium. Mazaheri et al. (2017) investigated the influence of wrapping aluminium foil on the impact face of Al2O3 tile on energy absorption as well as ballistic limit velocity using numerical and experimental methods. According to the results, there was an increase in energy absorption and ballistic limit velocity due to the fracture conoid angle, which delayed the crack’s propagation to the backplate. The ballistic limit velocity of laminated panels made of high-strength steel and Al 7075-T6 was investigated by Rahman et al. (2016) against 7.62 mm AP bullets at 900–950 m/s. The triple-layered mixture proved to be a good alternative for losing weight without compromising effectiveness, according to the results. Flores-Johnson et al. (2011) examined the ballistic performance of monolithic, double, and triple layer aluminum and steel plates against 7.62-mm APM2. Results predicted that improved ballistic performance and weight reduction can be achieved by layered configurations having different metals. Morghode et al. (Morghode and Thakur, 2023; Morghode et al., 2024) found that the layered arrangement of an Al2O3 front plate that was 18 mm thick and Al 7075-T651 back plate that was 10 mm thick, could stop 7.62 mm APM2 bullet with maximum impact velocity of 830 m/s from penetrating. Najihah Abdul Rahman et al. (2018) studied high speed impact on layered Al 7075-T651 and steel panel by 7.62 mm lead core bullet. Results showed that laminated panel with Al 7075-T651 back plate can be considered for designing protective structures for vehicle while maintaining performance and achieving weight reduction. Impact of material’s primary properties on modified Johnson-Cook material model was examined by Zuzov and Shash (2016).7.62 × 63 mm NATO Ball as well as 7.62 × 63 mm APM2 ammo were employed in this investigation along with an AA7075-T651 plate. Praveen et al. (2022) investigated influence of solution treatment and thickness of target on ballistic performance of Al 7075 T651 against 7.62 × 51 mm ball ammunition. Results showed that Al 7075-T651 experienced brittle fracture with splinter formation, whereas solution-treated plates experienced petaling. Vignjevic et al. (2012) conducted study on the modelling of dynamic failure in Al alloys. De Vuyst et al. (2017) studied orientation for cubical fragments. Using ANSYS Explicit dynamics/Autodyn software, Naik et al. (2024) conducted study on 3D printed Aluminium alloy for ballistic applications, Gálvez et al. (2005), V. Pranay (Pranay V. and Panigrahi S. K., 2022; Pranay V. and Panigrahi, S. 2022; Pranay and Panigrahi, 2022c; Pranay and Panigrahi, 2023; Pranay and Panigrahi, 2024) tried an effective penetration of the target and carried out numerical research for the creation of projectiles. Numerical finite element analysis is an effective method for solving problems of engineering field. It is very beneficial for problems where analytical solutions cannot be obtained. This approach is very useful when design geometry is complex and the accuracy requirement is high. FE analysis is recommended for problems involving understanding strength of materials under pressure loading (Pany, 2022a), structural design and testing (Vamsi et al., 2021), to predict the performance and behavior of the design (Pany, 2021b), to calculate the safety margin and to identify the weakness of the design accurately (Pany, 2021a) and to identify the optimal design (Pany and Rao, 2004; Pany, 2022b; Pany and Li, 2023). Lead-cored 7.62 mm ball bullet is a widely used ammunition that has resulted in numerous civilian casualties worldwide. Hence, there is an unavoidable need for security forces to protect from 7.62 mm ball bullets. Commercial vehicles used by the security forces are not capable of providing protection against 7.62 mm ball ammunition. Thus, fixing of add on armour on such vehicles is the most economical and effective method. However, adding more armor adds weight, which could reduce the vehicle’s efficiency. As per the literature of Morghode et al. (2024), the layered configuration of Al2O3 front plate and Al 7075-T651 back plate is studied against 7.62 mm APM2 projectile, which is made of hard steel core. In the present study, the same combination of materials, with different thicknesses, is used to study impact against 7.62 mm ball ammunition, which is made of lead core. The aim of this study is to minimise the penetration of 7.62 mm lead cored bullets with impact velocity of 720 m/s by carefully choosing and optimising the thickness of the materials that can be utilized as armour. As a result, the criteria to maximize the strength to weight ratio and provide defence against 7.62 mm ball rounds were met at the same time. Experiments were conducted on Al 7075-T651 plate and Numerical model is validated with experiment results. To achieve the objective, the validated numerical model is used to investigate influence on various Al2O3 and Al 7075-T651 combinations. Three factors led to the selection of Al 7075-T561 and Al2O3 as the target materials. First, the literature review revealed that these materials have already been employed in the construction of armour. Second, Al2O3 is a brittle material whereas Al 7075-T651 is ductile. Consequently, when combined in a layered arrangement, these materials offer the ideal destroyer-absorber arrangement. Thirdly, these materials have lower densities than steel. As a result, these materials offer a lightweight alternative for lead core 7.62 mm bullet defense. The Research methodology used for the study is explained in depth in the sections that follow.
Initially, an experiment is conducted on an Al 7075-T651 plate of 15 mm thickness, impacted by 7.62 mm Lead core ammunition, at normal impact conditions. A numerical model is developed using LSDYNA finite element analysis. The model is validated using the experiment results. The validated model conditions are used for the analysis of layered configuration. A detailed research methodology flow chart is shown in Figure 1.
Ballistic impact experiments on Al 7075-T651 plate were impacted by 7.62 mm lead core bullet. These bullets have an outer jacket for protection and an inside lead core. This jacket, which is often composed of brass, is intended to interact with barrel’s lands to give the bullet spin as it passes through the barrel. The target used for the experiment is Al 7075-T651 bar having diameter of 130 mm of 100 mm thickness. Target holders held the target plates in place, while the weapon was secured to the universal Ballistic Test Equipment. The schematic of the experiment setup is shown in Figure 2. The target was maintained 10 m away from the rifle’s barrel. A Doppler Velocity Measurement System is used to record the muzzle velocity and impact velocities. Doppler velocity analysis of impact of bullets is shown in Figure 3. This is a velocity versus time graph that represents velocity variation of the projectile with time, after it leaves the barrel of the weapon. In Figure 3, V0 represents the muzzle velocity and Vx1 represents the impact velocity of the projectile. The impact surface of Al 7075-T651 post impact of bullets is shown in Figure 4. Table 1 represents the muzzle velocities, impact velocities and depth of penetrations measured post impact experiments using two bullets.
In this study, impact analyses are performed using 7.62 mm lead cored bullets. The bullet’s contact with the target substance is unaffected by the brass jacket. In order to shorten computing time needed for simulations, jacket is not taken into account. The bullet was designed in Solid Works and then imported into LS DYNA for simulations. The schematic of projectile with dimensions is shown in Figure 5.
The target model was created using the LS-DYNA program. The target was intended to be a 152 mm-diameter circular plate. Three sections were further divided into this circular plate. The impact area at circular target’s centre was created as square with 10 mm edge. The circular-shaped second and third regions were intended to have respective diameters of 30 and 50 mm. The circular target’s dimensions are shown in Figure 6.
Hexahedron elements are used for meshing in order to cover maximal volume as well as curvature of bullet and the target (Pranay V. and Panigrahi S., 2022). LS DYNA (LS-DYNA, 2018) was used for target plate meshing, while ABAQUS was used for bullet meshing. A thorough analysis of mesh convergence was carried out in order to save computing time and choose ideal element size for projectile and target. The outcomes of trials were compared with those obtained by varying size of elements. The size of elements in square area at the target plate’s center was determined to be 0.25 mm. In a similar vein, the parts in the circular portion with the 50 mm and 30 mm diameters will have 1 mm and 0.5 mm in diameter, respectively. The element size will be 2 mm after reaching a diameter of 50 mm. The detailed mesh convergence study is presented in the literature (Morghode et al., 2024). The meshed models of the projectile and the target are shown in Figure 7.
Lead is considered for projectile, and Al 7075-T651 and Al2O3 are considered for target. The Johnson-Cook (JC) Strength and Failure Model (Johnson and Cook, 1983; Johnson and Cook, 1985) are used to define material for Lead (Seidl et al., 2018) and Aluminum 7075-T651 (Jørgensen and Swan, 2014) and the material properties are given in Table 2. Johnson Holmquist model (Johnson and Holmquist, 1994) is used to define the Al2O3 (Zochowski et al., 2021) and properties are given Table 3.
Table 2. Material characteristics of bullet (Seidl et al., 2018) and Al 7075-T651 (Jørgensen and Swan, 2014).
Table 3. Material properties for Al2O3 (Zochowski et al., 2021).
Since LS-DYNA is one of the best programs for conducting high-velocity impact simulations, it was utilized in this investigation. Prior to conducting layered configuration analysis, projectile and target model created for this study had to be validated. Therefore, the current model was validated using experimental results listed in Table 1. Rotational and translational degrees of freedom along the boundary of the target were constrained so that there was no motion. Figure 8 depicts the assembly of different parts and boundary conditions. The adhesive bond between the Al2O3 plate and the Al 7075-T651 plate was modeled by defining a contact model ‘Tie-Break Surface to Surface Contact’ that will break when the stress limits are exceeded. After standardizing the experimental data, it was discovered that the depth of penetration attained was 10.33 mm at impact velocity of 720 m/s. Depth of penetration obtained from numerical simulation was 11.05 mm (simulation is shown in Figure 9). On comparing both the results, it is observed that the present model resulted in 6.97% error in over estimation. It was fair to believe that model was validated and that it could be further expanded to examine layered setup because the error was extremely small and in the overestimation range.
For additional investigation, the verified model conditions were employed. The target materials for the monolithic plates were initially Al 7075-T651 and Al2O3. The majority of studies employ Al2O3 materials in layer configurations, meaning that Al2O3 layer is used to absorb impact and the other ductile layer is used to absorb leftover energy. This study examines both monolithic and layered armor systems to optimize weight without compromising functionality.
Initially, 7.62 mm lead core projectile having velocity 720 m/s, was impacted on 15 mm thick plate of Al 7075-T651. Bullet was successfully stopped by the plate, and measurement of depth of penetration revealed that it was 11.03 mm. The target underwent elastic deformation, and the rear face of the target seemed undamaged. Figure 9 displays impact simulations on independent monolithic Al 7075-T651 plate.
Furthermore, a 15 mm thick Al2O3 target was struck by a 7.62 mm lead cored bullet at the same velocity, i.e. 720 m/s. It was observed that Al2O3 plate was unable to restrict the bullet completely. Target had experienced failure having brittle fracture and the plate was completely damaged. Figure 10 displays impact simulations on an independent Al2O3 plate.
Al 7075-T651 and Al2O3 were combined and applied in layers to provide improved defense against 7.62 mm lead cored rounds. Al 7075-T651 was thought to be the back plate and Al2O3 to be the front plate.
First, the impact simulation was carried out and each plate in the stacked combination was taken to be 10 mm thick. It was noted that stacked plates effectively stopped the projectile, while the Al 7075-T651 plate only suffered minor pressures. The projectile had undergone significant distortion as well. Figure 11 shows some simulation images.
Figure 11. Effect on the Layered arrangement of 10 mm Al 7075-T651 rear plate and 10 mm Al2O3 front plate.
In order to optimize the weight of target further, different layered configurations were required to be tested. Therefore, an impact analysis was carried out and thickness of the Al 7075-T651 rear plate was lowered in stages of 2 mm during the first phase. It is discussed in earlier section that the projectile shatters the Al2O3 front plate. Therefore, the thickness of the Al 7075-T651 back plate is gradually decreased to ensure that protection against projectiles is maintained and that there is no plastic deformation at back plate’s rear surface. Then in second phase, thickness of Al2O3 front plate was reduced, in steps of 2 mm and the impact analysis was conducted to achieve optimum protection against the projectile. The impact analysis of various layered configurations is shown in succeeding sections.
The 7.62 mm Lead core bullet had an impact on the layered configuration of 10 mm thick front plate of Al2O3 and 08 mm thick back plate of Al 7075-T651. It was observed that this combination was able to arrest bullet but damage on front plate increased. The projectile was completely damaged. Simulation images are shown in Figure 12. Subsequently, the Al 7075-T651 back plate’s thickness was further decreased by 2 mm.
Figure 12. Effect on the Layered arrangement of 08 mm Al 7075-T651 rear plate and 10 mm Al2O3 front plate.
The 7.62 mm Lead core bullet had an impact on the layered configuration of 10 mm thick front plate of Al2O3 and 06 mm thick back plate of Al 7075-T651. It was observed that this combination was able to arrest bullet but excessive damage was observed on the front plate. The projectile was completely damaged. Deformation was also observed in Al 7075-T651 back plate but it was within elastic limit. No plastic deformation was observed in back plate. Simulation images is given in Figure 13. Subsequently, the Al 7075-T651 back plate’s thickness was further decreased by 2 mm.
Figure 13. Effect on the Layered arrangement of 06 mm Al 7075-T651 rear plate and 10 mm Al2O3 front plate.
The 7.62 mm Lead core bullet had an impact on the layered configuration of 10 mm thick front plate of Al2O3 and 04 mm thick back plate of Al 7075-T651. It was observed that this combination was able to arrest bullet but excessive damage was observed on the front plate. The projectile was completely damaged. Plastic deformation was observed in the Al 7075-T651 back plate, which is not desirable. Figure 14 shows some simulation images.
Figure 14. Effect on the Layered arrangement of 04 mm Al 7075-T651 rear plate and 10 mm Al2O3 front plate.
It was found that while projectile penetration was limited as rear plate thickness decreased, cone fracture formation boosted front plate damage on Al2O3. The intensification of the reflected stress waves was the cause of this. Following this simulation, it was determined that the best configuration for stopping the bullet without causing plastic deformation to the backplate was a layered arrangement with a 10 mm thick Al2O3 front plate and a 06 mm thick Al 7075-T651 rear plate. Al2O3 is known to have higher density than Al 7075-T651. Therefore, lowering Al2O3’s thickness will lower the configuration’s total weight. Hence, in order to achieve optimized weight, the Al2O3 front plate thickness was reduced in steps of 2 mm and thickness of Al 7075-T651 back plate was kept constant as 10 mm. The impact analysis of various layered configurations, while reducing the thickness of Al2O3 front plate, is shown in succeeding sections.
The 7.62 mm Lead core bullet had an impact on layered configuration of 08 mm thick front plate of Al2O3 and the 10 mm thick back plate of Al 7075-T651. It was observed that this combination was able to arrest bullet but excessive damage was observed on the front plate. The projectile was completely damaged. Deformation in the Al 7075-T651 back plate was very less and within plastic limit. Figure 15 shows some simulation images.
Figure 15. Effect on the Layered arrangement of 10 mm Al 7075-T651 rear plate and 06 mm Al2O3 front plate.
The 7.62 mm Lead core bullet had an impact on layered configuration of 06 mm thick front plate of Al2O3 and the 10 mm thick back plate of Al 7075-T651. Front plate was totally broken, yet it was noted that this combination was able to stop bullet. Projectile was completely damaged. Deformation in Al 7075-T651 back plate was less and within elastic limit. Figure 16 shows some simulation images.
Figure 16. Effect on the Layered arrangement of 10 mm Al 7075-T651 rear plate and 04 mm Al2O3 front plate.
The 7.62 mm Lead core bullet had an impact on layered configuration of 04 mm thick front plate of Al2O3 and the 10 mm thick back plate of Al 7075-T651. Front plate was totally broken, yet it was noted that this combination was able to stop bullet. Projectile was completely damaged. Deformation in Al 7075-T651 back plate increased but was within elastic limit. Figure 17 shows some simulation images.
Figure 17. Effect on the Layered arrangement of 10 mm Al 7075-T651 rear plate and 02 mm Al2O3 front plate.
The 7.62 mm Lead core bullet had an impact on layered configuration of 02 mm thick front plate of Al2O3 and the 10 mm thick back plate of Al 7075-T651. Front plate was totally broken, yet it was noted that this combination was able to stop bullet. Projectile was completely damaged. Deformation in Al 7075-T651 back plate increased significantly. Plastic deformation was observed in the back plate which was not desirable. Figure 18 shows some simulation images.
Figure 18. Effect on the Layered arrangement of 10 mm Al 7075-T651 rear plate and 02 mm Al2O3 front plate.
From this simulation it was observed that even 02 mm thick Al2O3 front plate can stop perforation of the bullet. But, plastic deformation in the Al 7075-T651 back plate is required to be controlled. Furthermore, as was already established, Al2O3 is denser than Al 7075-T651. Thus, the configuration’s total weight can be decreased by maintaining a thinner Al2O3 front plate. Therefore, it was decided that thickness of Al 7075-T651 back plate will be increased to 12 mm and impact analysis will be carried out by varying the thickness of Al2O3 front plate. The impact analysis of various layered configurations, while varying the thickness of Al2O3 front plate, is shown in succeeding sections.
The 7.62 mm Lead core bullet had an impact on layered configuration of 02 mm thick front plate of Al2O3 and the 12 mm thick back plate of Al 7075-T651. Front plate was totally broken, yet it was noted that this combination was able to stop bullet. Projectile was completely damaged. Deformation in Al 7075-T651 back plate was less as compared to 10 mm back plate. But plastic deformation was observed in the back plate which was not desirable. Figure 19 shows some simulation images.
The 7.62 mm Lead core bullet had an impact on layered configuration of 04 mm thick front plate of Al2O3 and the 12 mm thick back plate of Al 7075-T651. Front plate was totally broken, yet it was noted that this combination was able to stop bullet. Projectile was completely damaged. Deformation in Al 7075-T651 back plate was reduced. No plastic deformation was observed in back plate. Figure 20 shows some simulation images.
Following this simulation, it was determined that the optimal configuration for stopping bullets without causing plastic deformation to the rear plate was a layered configuration with an Al2O3 front plate that was 4 mm thick and Al 7075-T651 back plate that was 12 mm thick.
A projectile with impact velocity of 720 m/s was used in impact analysis on a target plate of Al 7075-T651, which was 15 mm thick. The bullet was observed to have penetrated target to depth of 11.05 mm. Ductile Hole Enlargement was Al 7075-T651 plate’s mode of failure. Tensile stresses in bullet travel direction causes delamination in rolling plane, because of layered and inhomogeneous micro structure of material. Delamination is also due to intergranular and intra granular disintegration caused by the tensile stresses. Additionally, it is discovered that due of significant mesh distortion, Lagrangian formulation in LS-DYNA was unable to adequately handle problem of ball bullet impacting on stiff plate. Bullet behaves like fluid during such strikes, and momentum becomes more important than strength. Severely distorted parts degraded continually even if the lead core’s adaptive refinement time interval was set extremely low. Additionally, during simulations, it is seen that instead of pushing target material out laterally during ductile hole expansion, the bullet erodes as it travels through the material during perforation. Monolithic Al2O3 was examined at 720 m/s with target thickness of 15 mm. When the projectile impacted Al2O3, primary resistance to penetration is due to compressive strength of Al2O3. As compressive strength is high, the projectile is deformed and eroded. The projectile’s low aspect ratio causes it to be defeated since Al2O3’s strength is greater than the projectile’s. Al2O3 will be ground up in a tiny area directly in front of the projectile’s leading edge by the stresses the projectile will be subjected to. Al2O3 has a tiny specific fracture surface energy when under tension, but a significant amount of energy may be needed to produce small fracture surface area when compressive and dynamic shear pressures are high. Therefore, the amount of energy required to create powdered surface area could be much greater. Damage cone that forms at penetrator’s leading edge is another important component that provides resistance to Al2O3 penetration. Cone formation is indicative of quasi-static indentation in Al2O3, following direction of the material’s highest tensile stress. Because of interaction between stress waves and reflections from the free surface, cone broadens at its base. Cone formation distributes the projectile’s load over a wide surface area. Consequently, the projectile’s kinetic energy density is decreased. Simulations revealed that the projectile underwent substantial deformation. Beyond the cone forms, radial fissures have formed in the Al2O3 plate. High-velocity fragments that develop within cone at free surface break material completely and may cause damage behind the Al2O3 target’s free surface. To retain the cone and bullet fragments, a stronger and more flexible layer is needed behind the Al2O3. Additionally, monolithic targets require greater thickness in order to stop perforation, which results in a noticeable increase in target weight. To achieve the best strength to weight ratio and maximum protection against 7.62 mm lead core ball bullet, a layered combination of front plate made of Al2O3 and back plate made of Al 7075-T651 was therefore taken into consideration.
First, a front plate of Al2O3 with a thickness of 10 mm and a back plate of Al 7075-T651 with thickness of 10 mm are taken into consideration. During initial stage of penetration, projectile tip is damaged and Al 7075-T651 yields at Al2O3 interface. The crack began at the Al2O3 rear surface and is oriented to follow motion of rear plate. Impact grows in both direction and magnitude. Fracture cone then expands in the direction of the penetrator’s movement from contact between projectile and target. Projectile erosion occurs similarly as in Krishnan et al. and Venkatesan et al. (Krishnan et al., 2010; Venkatesan et al., 2017), while Al2O3 fractures, consolidating, and intersecting to form debris. Yielding and plastic flow in the direction of the projectile’s normal path cause projectile erosion. When a projectile experience forces greater than its strength, erosion results. Rear plate absorbs any remaining energy in the projectile target system when projectile erosion stops. The similar results were seen in Morka et al. (Morka et al., 2009) in which the ceramic front plate was fractured post impact and the residual velocity of the bullet was absorbed by the Al 7,017 back plate. Only when target material is pushed forward or towards sides, can the projectile advance. Crushed Al2O3 cannot be pushed ahead due to rear confinement. One of the most important characteristics of the back plate is ductility, which enables the material to absorb stress waves created by impact on Al2O3 material. Stress waves are absorbed by the ductile material, which reduces the intensity of stress waves that Al2O3 reflects. This reduces damage to Al2O3 and increases the effectiveness of the armour. It was noted that the pieces had been effectively contained, and the back plate’s rear surface was undamaged. In addition, due to Al 7075-T651 target, Al2O3 target experience less damage than the monolithic plate. A multilayer structure effectively restricts the plate perforation.
From present study, following deductions are drawn:
• It is observed that for Al 7075-T651 monolithic plate, depth of penetration of projectile was
• 11.5 mm and ductile hole growth was observed. Al2O3 can deform the projectile, but it experienced brittle fracture in the form of a cone. Fragments are formed due to the shattering of Al2O3 plate.
• First, the layered arrangement of an Al2O3 front plate that is 10 mm thick and a back plate made of Al 7075-T651 that is 10 mm thick is examined. The perforation is successfully restricted with a layered configuration. The weight of armour has been increased significantly and areal density increased to 66.65 kg/m2.
• Various thicknesses of Al2O3 and Al 7075-T651 plates were examined for additional weight optimization. Two layered configurations— 10 mm thick front plate of Al2O3 and 06 mm thick rear plate of Al 7075-T651 and a 04 mm thick front plate of Al2O3 and 12 mm thick back plate of Al 7075-T651—were shown to be effective in preventing bullet perforation. However, when comparing the weight of these two arrangements, it was found that the configuration with a front plate of Al2O3 with a thickness of 04 mm and a back plate of Al 7075-T651 with thickness of 12 mm is the most optimal configuration for effectively limiting bullet perforation. The areal density of this configuration is 48.26 kg/m2. But these results are required to be validated with the experimental results. The experimental tests will be carried out in future study to validate the results obtained from the present study.
The original contributions presented in the study are included in the article/Supplementary Material, further inquiries can be directed to the corresponding author.
DM: Conceptualization, Data curation, Formal Analysis, Funding acquisition, Investigation, Methodology, Project administration, Resources, Software, Supervision, Validation, Visualization, Writing–original draft, Writing–review and editing. DT: Conceptualization, Data curation, Formal Analysis, Funding acquisition, Investigation, Methodology, Project administration, Resources, Software, Supervision, Validation, Visualization, Writing–original draft, Writing–review and editing. SS: Conceptualization, Data curation, Formal Analysis, Funding acquisition, Investigation, Methodology, Project administration, Resources, Software, Supervision, Validation, Visualization, Writing–original draft, Writing–review and editing. LC: Conceptualization, Data curation, Formal Analysis, Funding acquisition, Investigation, Methodology, Project administration, Resources, Software, Supervision, Validation, Visualization, Writing–original draft, Writing–review and editing. EA: Conceptualization, Data curation, Formal Analysis, Funding acquisition, Investigation, Methodology, Project administration, Resources, Software, Supervision, Validation, Visualization, Writing–original draft, Writing–review and editing.
The author(s) declare that financial support was received for the research, authorship, and/or publication of this article. The authors extend their appreciation to King Saud University for funding this work through Researchers Supporting Project number (RSP2024R164), King Saud University, Riyadh, Saudi Arabia. This article was co-funded by the European Union under the REFRESH—Research Excellence For REgion Sustainability and High-tech Industries project number CZ.10.03.01/00/22_003/0000048 via the Operational Programme Just Transition and has been done in connection with project Students Grant Competition SP2024/087 “Specific Research of Sustainable Manufacturing Technologies” financed by the Ministry of Education, Youth and Sports and Faculty of Mechanical Engineering VŠB-TUO. Article has been done in connection with project Students Grant Competition SP2024/087 “Specific Research of Sustainable Manufacturing Technologies” financed by the Ministry of Education, Youth and Sports and Faculty of Mechanical Engineering VŠB-TUO.
The authors declare that the research was conducted in the absence of any commercial or financial relationships that could be construed as a potential conflict of interest.
All claims expressed in this article are solely those of the authors and do not necessarily represent those of their affiliated organizations, or those of the publisher, the editors and the reviewers. Any product that may be evaluated in this article, or claim that may be made by its manufacturer, is not guaranteed or endorsed by the publisher.
De vuyst, T., Vignjevic, R., Albero, A. A., Hughes, K., Campbell, J. C., and Djordjevic, N. (2017). The effect of the orientation of cubical projectiles on the ballistic limit and failure mode of AA2024-T351 sheets. Int. J. Impact Eng. 104, 21–37. doi:10.1016/j.ijimpeng.2017.01.026
Flores-Johnson, E. A., Saleh, M., and Edwards, L. (2011). Ballistic performance of multi-layered metallic plates impacted by a 7.62-mm APM2 projectile. Int. J. Impact Eng. 38, 1022–1032. doi:10.1016/j.ijimpeng.2011.08.005
Gálvez, F., Chocron, S., Cendón, D., and Sánchez-Gálvez, V. (2005). “Numerical simulation of the tumbling of kinetic energy projectiles after impact on ceramic/metal armours,” in Computational ballistics II (Southampton, United Kingdom: WIT Press).
Johnson, G. R., and Cook, W. H. (1983). “A constitutive model and data for metals subjected to large strains, high strain rates, and high temperatures,” in Proceedings 7th international symposium on ballistics (The Hague), 541–547. 19-27 April.
Johnson, G. R., and Cook, W. H. (1985). Fracture characteristics of three metals subjected to various strains, strain rates, temperatures and pressures. Eng. Fract. Mech. 21, 31–48. doi:10.1016/0013-7944(85)90052-9
Johnson, G. R., and Holmquist, T. J. (1994). “An improved computational constitutive model for brittle materials,” in AIP conference proceedings, 981–984. doi:10.1063/1.46199
Jørgensen, K. C., and Swan, V. (2014). “Modeling of armour-piercing projectile perforation of thick aluminium plates,” in In proceedings of the 13th international LS-DYNA users conference (Dearborn, MI, USA), 8–10 June.
Krishnan, K., Sockalingam, S., Bansal, S., and Rajan, S. D. (2010). Numerical simulation of ceramic composite armor subjected to ballistic impact. Compos B Eng. 41, 583–593. doi:10.1016/j.compositesb.2010.10.001
LS-DYNA (2018). LS-DYNA R11.0.0 (R11.129956; 2018/09) released. Southampton, United Kingdom: ANSYS, Inc.
Mazaheri, H., Naghdabadi, R., and Arghavani, J. (2017). Experimental and numerical study on the effect of aluminum foil wrapping on penetration resistance of ceramic tiles. Sci. Iran. 24, 1126–1135. doi:10.24200/sci.2017.4094
Morghode, D. S., and Thakur, D. G. (2023). “Analysis of impact of high velocity projectile on layered configuration of armour materials,” in 2nd international conference on recent advances in materials, manufacturing and machine learning. (Nagpur).
Morghode, D. S., Thakur, D. G., salunkhe, S., Cepova, L., and Nasr, E. A. (2024). Numerical study on the optimized thickness of layer configuration against the 7.62 APM2 projectile. Front. Mech. Eng. 10. doi:10.3389/fmech.2024.1322640
Morka, A., Jackowska, B., and Niezgoda, T. (2009). Numerical study of the shape effect in the ceramic based ballistic panels. J. KONES 16, 539–548.
Naik, M., Pranay, V., Thakur, D. G., Chandel, S., Salunkhe, S., Pagac, M., et al. (2024). Numerical investigation on effect of different projectile nose shapes on ballistic impact of additively manufactured AlSi10Mg alloy. Front. Mater 11. doi:10.3389/fmats.2024.1330597
Pany, C. (2021a). Cylindrical shell pressure vessel profile variation footprint in strain comparison of test data with numerical analysis. Liq. Gaseous Energy Resour. 1, 91–101. doi:10.21595/lger.2021.22163
Pany, C. (2021b). Estimation of correct long-seam mismatch using FEA to compare the measured strain in a non-destructive testing of a pressurant tank. Int. J. Smart Veh. Smart Transp. 4, 16–28. doi:10.4018/IJSVST.2021010102
Pany, C. (2022a). An insight on the estimation of wave propagation constants in an orthogonal grid of a simple line-supported periodic plate using a finite element mathematical model. Front. Mech. Eng. 8. doi:10.3389/fmech.2022.926559
Pany, C. (2022b). Investigation of circular, elliptical and obround shaped vessels by finite element method(FEM) analysis under internal pressure loading. J. Sci. Technol. Eng. Res. doi:10.53525/jster.1079858
Pany, C., and Li, G. (2023). Editorial: application of periodic structure theory with finite element approach. Front. Mech. Eng. 9. doi:10.3389/fmech.2023.1192657
Pany, C., and Rao, G. V. (2004). Large amplitude free vibrations of a uniform spring-hinged beam. J. Sound. Vib. 271, 1163–1169. doi:10.1016/S0022-460X(03)00572-8
Pranay, V., and Panigrahi, S. (2022a). Effects of spinning on residual velocity of ogive-nosed projectile undergoing ordnance velocity impact. Proc. Inst. Mech. Eng. C J. Mech. Eng. Sci. 236, 1685–1697. doi:10.1177/09544062211020030
Pranay, V., and Panigrahi, S. (2023). Parametric study in analysing the effect of spinning on the deformable projectiles undergoing impact. Proc. Inst. Mech. Eng. C J. Mech. Eng. Sci. 238, 5227–5240. doi:10.1177/09544062231216844
Pranay, V., and Panigrahi, S. K. (2022c). “Effects of spinning on residual velocity of projectile for normal and oblique impact,” in 13th international high energy materials conference and exhibits, TBRL (Chandigarh: TBRL).
Pranay, V., and Panigrahi, S. K. (2022b). Design and development of new spiral head projectiles undergoing ballistics impact. Int. J. Struct. Integr. 13, 490–510. doi:10.1108/IJSI-01-2022-0008
Pranay, V., and Panigrahi, S. K. (2024). Numerical study on the effect of spinning for 7.62 APM2 projectile impacting on Al 7075-t651 target. MATEC Web Conf. 393, 02001. doi:10.1051/matecconf/202439302001
Praveen, R., Koteswara Rao, S., Damodaram, R., and Suresh Kumar, S. (2022). Numerical and experimental investigations on the effect of target thickness and solution treatment on the ballistic behaviour of AA7075 thick plates. Proc. Inst. Mech. Eng. C J. Mech. Eng. Sci. 236, 3530–3545. doi:10.1177/09544062211038981
Rahman, N., Abdullah, S., Abdullah, M., Zamri, W., Omar, M., and Sajuri, Z. (2018). Experimental and numerical investigation on the layering configuration effect to the laminated aluminium/steel panel subjected to high speed impact test. Met. (Basel) 8, 732. doi:10.3390/met8090732
Rahman, N. A., Abdullah, S., Zamri, W. F. H., Abdullah, M. F., Omar, M. Z., and Sajuri, Z. (2016). Ballistic limit of high-strength steel and Al7075-T6 multi-layered plates under 7.62-mm armour piercing projectile impact. Lat. Am. J. Solids Struct. 13, 1658–1676. doi:10.1590/1679-78252657
Seidl, M., Legendre, J. F., Mehl, M., and Souli, M. (2018). “Numerical Ricochet model of a 7.62 mm projectile penetrating an armor steel plate,” in In proceedings of the 15th international LS-DYNA users conference.
Turhan, L., Eksik, Ö., Yalçın, E. B., Demirural, A., Baykara, T., and Günay, V. (2008). “Computational simulations and ballistic verification tests for 7.62mm AP and 12.7mm AP bullet impact against ceramic metal composite armours,” in Structures under shock and impact X (Southampton, UK: WIT Press), 379–388. doi:10.2495/SU080371
Vamsi, A., Ansari, J., Mk, S., Pany, C., John, B., Samridh, A., et al. (2021). Structural design and testing of pouch cells. J. Energy Syst. 5, 80–91. doi:10.30521/jes.815160
Venkatesan, J., Iqbal, M. A., and Madhu, V. (2017). Ballistic performance of bilayer alumina/aluminium and silicon carbide/aluminium armours. Procedia Eng. 173, 671–678. doi:10.1016/j.proeng.2016.12.141
Vignjevic, R., Djordjevic, N., Campbell, J., and Panov, V. (2012). Modelling of dynamic damage and failure in aluminium alloys. Int. J. Impact Eng. 49, 61–76. doi:10.1016/j.ijimpeng.2012.03.009
Zochowski, P., Bajkowski, M., Grygoruk, R., Magier, M., Burian, W., Pyka, D., et al. (2021). Comparison of numerical simulation techniques of ballistic ceramics under projectile impact conditions. Materials 15, 18. doi:10.3390/ma15010018
Zuzov, V., and Shash, N. (2016). Impact of aluminum alloy parameters on penetration resistance of the bullets 7.62 «ball NATO» and «ARM2». Sci. Educ. Bauman MSTU 16. doi:10.7463/1116.0850281
Keywords: FEA, impact, Al2O3, Al 7075-T651, 7.62 mm ball projectile
Citation: Morghode DS, Thakur DG, Salunkhe S, Cepova L and Abouel Nasr E (2024) Analysis of the thickness of layered armor to provide protection against 7.62 mm ball projectiles using experimental and numerical methods. Front. Mech. Eng 10:1419210. doi: 10.3389/fmech.2024.1419210
Received: 17 April 2024; Accepted: 19 June 2024;
Published: 25 July 2024.
Edited by:
X. J. Jing, City University of Hong Kong, Hong Kong SAR, ChinaReviewed by:
Chitaranjan Pany, Vikram Sarabhai Space Centre, IndiaCopyright © 2024 Morghode, Thakur, Salunkhe, Cepova and Abouel Nasr. This is an open-access article distributed under the terms of the Creative Commons Attribution License (CC BY). The use, distribution or reproduction in other forums is permitted, provided the original author(s) and the copyright owner(s) are credited and that the original publication in this journal is cited, in accordance with accepted academic practice. No use, distribution or reproduction is permitted which does not comply with these terms.
*Correspondence: D. G. Thakur, dGhha3VyQGRpYXQuYWMuaW4=
Disclaimer: All claims expressed in this article are solely those of the authors and do not necessarily represent those of their affiliated organizations, or those of the publisher, the editors and the reviewers. Any product that may be evaluated in this article or claim that may be made by its manufacturer is not guaranteed or endorsed by the publisher.
Research integrity at Frontiers
Learn more about the work of our research integrity team to safeguard the quality of each article we publish.