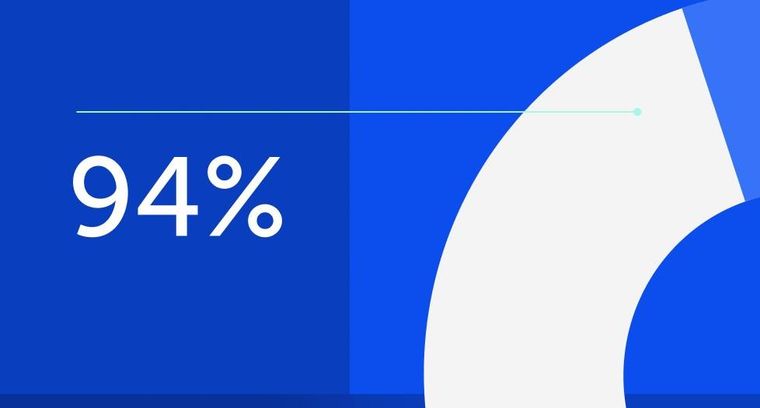
94% of researchers rate our articles as excellent or good
Learn more about the work of our research integrity team to safeguard the quality of each article we publish.
Find out more
ORIGINAL RESEARCH article
Front. Mech. Eng., 01 July 2024
Sec. Engine and Automotive Engineering
Volume 10 - 2024 | https://doi.org/10.3389/fmech.2024.1411456
Introduction: With the development of the new energy vehicle industry, the research aims to improve the energy utilization efficiency of electric vehicles by optimizing their composite power supply parameters.
Methods: An optimization model based on non-dominated sorting genetic algorithm II was designed to optimize the parameters of liquid cooling structure of vehicle energy storage battery. The objective function and constraint conditions in the optimization process were defined to maximize the heat dissipation performance of the battery by establishing the heat transfer and hydrodynamic model of the electrolyzer.
Results: The results showed that the optimization method had excellent performance on multiple evaluation indicators, the material degradation rate after optimization was reduced by 42%, the corrosion rate was reduced by 36%, and the battery life was increased by 17%. The optimization method ensured the maximum temperature control for the safe operation of the lithium-ion battery pack. The temperature of the battery pack was effectively controlled. The temperature difference was kept within 5°C, preventing the battery from overheating and extending its service life.
Discussion: The proposed liquid cooling structure design can effectively manage and disperse the heat generated by the battery. This method provides a new idea for the optimization of the energy efficiency of the hybrid power system. This paper provides a new way for the efficient thermal management of the automotive power battery.
The demand for in vehicle energy storage batteries is showing significant growth. However, these batteries emit numerous thermal energy during operation, which not only shortens batteries’ life, but may also pose safety hazards (Luo et al., 2022). Therefore, efficient battery thermal management becomes a key issue currently faced. Liquid cooling technology, as a widely used thermal management method, is crucial for maintaining temperature stability and uniformity during battery operation (Karimi et al., 2021). However, the design of liquid cooling and heat dissipation structures is quite complex and requires in-depth research and optimization to achieve optimal performance. The battery liquid cooling heat dissipation structure uses liquid, which carries away the heat generated by the battery through circulating flow, thereby achieving heat dissipation effect (Yi et al., 2022). The Non-dominated Sorting Genetic Algorithm II (NSGA-II) can find multiple optimal solutions in one run, achieving a good balance between multiple objective functions (Xiao et al., 2021; Wang et al., 2024). NSGA-II was studied and utilized to analyze the structure, working principle, heat generation characteristics, and heat transfer characteristics to optimize the heat dissipation effect, laying a theoretical foundation for the thermal analysis of battery stacks. Finally, the structure of the liquid cooling system for in vehicle energy storage batteries was optimized based on NSGA-II. The efficiency of NSGA-II enables the optimization design process to be completed in a relatively short time, reducing research, development, and time costs. Meanwhile, the global search capability of the algorithm also avoids the problem of getting stuck in local optima, improving the quality and reliability of optimization results. This study provides practical guidance for the optimization design of liquid cooled heat dissipation structures in vehicle mounted energy storage batteries. Meanwhile, this paper provides theoretical support for the application of multi-objective optimization algorithms in the design of the heat dissipation structure. The article is divided into four parts. The first part discusses and analyzes the optimization of the liquid cooling and heat dissipation structure of vehicle mounted energy storage batteries. The current research status of NSGA-II both domestically and internationally is analyzed. The second part proposes the optimization of battery model parameters and the optimization design of battery liquid cooling and heat dissipation structure based on NSGA-II. The third part verifies the effectiveness and performance of the algorithm through experiments. The fourth part summarizes the research findings.
The liquid cooling and heat dissipation of in vehicle energy storage batteries gradually become a research hotspot under the rapid industrial growth. Fayaz et al. addressed the poor thermal performance, risk of thermal runaway, and fire hazards in automotive energy storage batteries. A single-objective optimization technology was adopted to optimize the thermal parameters and structural design of lithium-ion batteries, effectively improving their thermal performance and lifespan (Fayaz et al., 2022). Karthik et al. learned and put forward a novel plate liquid battery thermal managing solution to address the abnormal temperature in automotive energy storage batteries under extreme working conditions. Research comparison showed that the mass flow, maximum pressure, and power consumption of the system were reduced by 66.33%, 38.10%, and 43.56% compared with the case of equal mass flow, respectively. The temperature rise and temperature distribution of the battery system were kept within the normal range (Karthik et al., 2021). Bulut et al. conducted predictive research on the effect of battery liquid cooling structure on battery module temperature using an artificial neural network model. The research results indicated that the power consumption reduced by 22.4% through optimization. The relative error of the prediction results was less than 1% (Bulut et al., 2022). Kalaf et al. learned and put forward a review for liquid cooling heat dissipation structure of in vehicle energy storage batteries. By reviewing recent research results on battery liquid cooling systems, they pointed out that an effective cooling system was crucial for extending battery life. This system effectively effected the temperature in terms of difference and peak between batteries (Kalaf et al., 2021). Chen et al. learned and put forward a microchannel thermal managing solution supported by neural network regression to address the enormous heat generated by lithium-ion batteries at high current charging rates. The research results showed that the charging state value increased by 0.5 after 15 min of charging. The energy consumption was less than 0.02 J. The maximum temperature was controlled within 33.35°C, with a temperature standard deviation controlled within 0.8°C (Chen et al., 2021). Park et al. focused on optimizing the cooling systems and designed the controller as an optimal control problem. They successfully significantly reduced energy consumption without increasing computational load by representing the terminal cost of the predicted horizon to infinity and using the calculated optimal expected cost to approximate the target operating cost (Park and Ahn, 2021).
In recent years, researchers are dedicated to studying the application of NSGA-II in liquid cooling and heat dissipation of batteries. He et al. adopted an innovative evolutionary NSGA-II in the multi-objective planning and operational collaborative optimization of vehicle mounted energy storage hybrid power systems. Through comparative research, the implementation of this collaborative operation strategy showed higher economic and reliability of in vehicle energy storage systems compared to single energy storage systems in different experimental scenarios, providing strong support for practical applications (He et al., 2022). Li et al. learned and put forward a multi-objective quantitative optimization for photovoltaic solar cells based on NSGA-II to address the uncertainty of charging requirements for in vehicle energy storage batteries. Research found that this method achieved cost reduction of retired batteries, with a reduction of 29.4%, providing a new way to reduce battery operating costs (Li et al., 2022). Tang et al. designed a target mode switching strategy for maximizing power system efficiency based on the dynamic programming nested decomposition NSGA-II algorithm to further explore the new hybrid power system. The experiment outcomes confirmed that this strategy was superior to the traditional NSGA-II algorithm in computational efficiency, providing new ideas for performance optimization of hybrid power systems (Tang et al., 2021). In response to the need to enhance electric vehicle battery systems, Wei et al. combined multi-objective solution to optimize the operating parameters. The research results indicated that the optimized operating parameters evolved batteries thermal performance and reduced power consumption, providing important theoretical guidance for the operation strategy (Wei et al., 2022).
In summary, the pipeline design of the liquid cooling method for batteries in the past is relatively complex, requiring high sealing requirements for the cooling circuit. The thermal balance of the liquid cooling method is poor. Therefore, in response to these defects, the optimization design of the liquid cooling heat dissipation structure of vehicle mounted energy storage batteries is studied. An optimized design of the liquid cooling structure of vehicle mounted energy storage batteries based on NSGA-II is proposed. Therefore, thermal balance can be improved, manufacturing costs and maintenance difficulties can be reduced, and the safety and service life of the batteries can be ensured. This algorithm has the advantages of strong global search ability and high computational efficiency. This paper can provide more efficient and comprehensive optimization methods for the design of heat dissipation structures of vehicle mounted energy storage batteries.
The study first analyzes the structure, working principle, heat generation characteristics, and heat transfer characteristics of the battery, laying a theoretical foundation for the thermal analysis of the stack. Finally, the structure of the liquid cooling system for in vehicle energy storage batteries is optimized based on NSGA-II.
The construction of mobile storage battery packs in vehicles can provide sufficient energy reserves and supply for the power system, improving the stability and reliability of the power system. The current in car energy storage batteries are mainly lithium-ion batteries, which have a high voltage platform, with an average voltage of 3.7 V or 3.2 V. Its energy storage density is 6-7 times higher than traditional lead-acid batteries. However, currently lithium-ion batteries generally have safety hazards and are prone to explosions (Xu and Shen, 2021; Serat et al., 2023). It is necessary to protect lithium-ion batteries to avoid overcharging and over discharging. According to the network data, the battery parameters related to the 18,650 lithium-ion battery are shown in Table 1.
In Table 1, there is a significant risk of heat accumulation. The charging and discharging current is very low, which cannot meet the requirements of high rate charging and discharging. The models are 18650E and 18650P, with high magnification and small capacity, mainly used in the relevant fields of power batteries. Although 18650D is slightly smaller than 18650B, both can meet the requirements of discharge rate and high-power discharge in extreme environments. However, due to the low charging and discharging rate and lower capacity of 18650D, its volume utilization rate is low. Therefore, the study chooses 18650B as the follow-up experimental battery. The single cell battery used is 3400mAh, with a rated voltage of 3.7V. It is assumed that
In Eq. 1,
In Figure 1, a single battery consisting of 8 in parallel and 7 in series is the module. Finally, the battery module is 16 in series and the remaining 30 in parallel. The heat generation is a common problem in power batteries, and their internal structure is very complex. Electrochemical reactions occur, which not only generate too much thermal energy but also release a large amount of chemical energy. It can more accurately reflect the temperature rise and heat generation rate changes, as shown in Eq. 2.
In Eq. 2,
In Eq. 3,
In Eq. 4,
In Eq. 5,
In Eq. 6,
In Figure 2,
The behavior of different batteries can be simulated by adjusting the parameters in the Thevenin model. In summary, the purpose of lithium-ion battery model parameter optimization is to improve the performance and safety of the battery, while considering the cost effectiveness of the battery. The goals of optimization focus on increasing the battery’s energy storage density, reducing internal resistance to reduce the risk of heat accumulation. Meanwhile, it should ensure that the battery can adapt to the requirements of high rate charging and discharging. Limitations include the physical specifications of the battery, the charge and discharge rate, and the cost, which together determine the practical feasibility of the battery design.
The heat dissipation problem of energy storage battery systems is a key challenge in the current development of battery technology. If heat dissipation cannot be effectively carried out, it can lead to thermal runaway due to the large amount of heat generated by batteries during operation. This problem may affect the performance and lifespan batteries, even potentially causing safety issues. Therefore, designing a reasonable heat dissipation scheme is crucial for the stable operation of energy storage battery systems (Zuo et al., 2023). The lithium-ion battery monomers and battery modules used are described, as shown in Figure 3.
Figure 3. Lithium-ion battery unit and battery module. (A) Ternary lithium-ion battery unit. (B) Ternary lithium-ion battery module.
In Figure 3, individual batteries are usually combined in series and parallel to meet the storage and performance requirements when designing battery packs. This design method can effectively evolve the energy density and output power, but it also brings the problem of heat dissipation. Because when a large number of batteries are tightly arranged together, heat transfer and dissipation between them become very difficult (Jilte et al., 2021). A common approach to solve this problem is to add a heat dissipation device inside. The liquid cooling plate is a heat dissipation device that takes away heat through liquid circulation. It can effectively reduce the temperature and improve the lifespan. Meanwhile, the liquid cooled plate can achieve a more uniform temperature distribution due to the good thermal conductivity of the liquid, thereby reducing the inconsistency between batteries. Based on the above analysis, a liquid cooled heat dissipation structure for energy storage batteries is designed, as shown in Figure 4.
Figure 4. Battery liquid cooling cooling structure. (A) Cooling pipe structure three-dimensional diagram. (B) Module assembly 3D diagram.
In Figure 4, a plate with a spacing of 6 mm is used to address the safety issues caused by direct contact between the plate and the individual battery. A liquid cooling plate is set between the battery and the liquid cooling plate. The thermal conductive silicone is filled. The size of the liquid cooling tube is 4 × 65 mm. The cross-sectional area of the flow channel is 2 × 63 mm. The liquid flow flows through the entire plate. The Reynolds number
In Eq. 8,
The cross-section of the liquid cooled pipeline flow channel designed for research is rectangular. The Reynolds coefficient is obtained through the above formula, which is
NSGA-II is a new genetic algorithm developed on the basis of genetic algorithm. When solving multi-objective optimization tasks, many traditional algorithms first decompose them into single ones, and then use the remaining objectives as constraints to solve these tasks. The fitness function or simulation results can be used to evaluate individuals in a population and provide reference for the survival of the fittest in offspring. It is assumed that there are
In Eq. 10,
In Eq. 11,
In Figure 5, the population is first initialized and then evaluated for fitness. If the termination condition is met, the process ends. Otherwise, a new population is selected. The NSGA-II has advantages in stability, reliability, efficiency, flexibility, interpretability, which is an excellent solution. In the structural design for vehicle mounted energy storage batteries, NSGA-II is used to optimize multiple performance indicators simultaneously. In the optimization software, the population size is set to 12 and the genetic algebra is set to 20. The proposed optimization method of liquid cooling structure of vehicle energy storage battery based on NSGA-Ⅱ algorithm takes into account the universality and adaptability of the algorithm during design. Therefore, this method is not only suitable for the battery module size and configuration used in the current study, but also has the potential to expand to different battery sizes and configurations. The optimization method adopts the modular design idea, which allows the parameter adjustment and optimization of different battery cells. Whether it is a standard-sized battery or a custom-sized battery, the optimization method is able to adapt the design parameters to its unique heat dissipation needs. The optimization method takes into account the thermal behavior of the battery in different operating modes and the influence of different ambient temperatures on the heat dissipation performance. This comprehensive consideration makes the optimization results not only perform well under specific operating conditions, but also adapt to variable operating conditions. In summary, the optimization of the battery liquid cooling system based on NSGA-Ⅱ algorithm solves the heat dissipation inside the battery pack and improves the performance and life of the battery. The goals of optimization include improving heat dissipation efficiency, achieving uniformity of fluid flow, and ensuring thermal balance to avoid inconsistencies between cells. The constraints relate to the spatial compatibility of the liquid cooling plate design, material characteristics, and flow path design, which are all key factors affecting the performance of the liquid cooling system.
Simulation experiments were conducted on battery modules to analyze their temperature and discharge conditions. Then, the surface temperature and pressure drop cloud maps of the battery were evaluated. Finally, a comparative analysis was conducted on the parameters of NSGA-II before and after optimizing the battery.
ICEMCFD software was used to divide the battery pack units into hexahedral sections, with the interface between the units and modules set as coupling walls. The simulation outcomes of the battery module are described in Table 2.
In Table 2, initial temperature, discharge time, and maximum temperature are the initial conditions of simulation, while discharge rate and maximum temperature difference are the results of simulation. “Temperature difference” refers to the maximum temperature difference between any two points inside the battery module. This index is used to measure the uniformity of the internal temperature distribution of the battery module during discharge. A large temperature difference can mean that some areas are overheating while others are relatively cold, which can affect the performance and life of the battery. In the cooling simulation, ICEMCFD software was used to split the battery pack unit. The unit was divided into hexahedron. The interface of the unit and module were set as coupling walls. This showed that the geometric structure of the battery module was considered in the simulation, which was divided into several small computing units to simulate the heat transfer and distribution. By comparing the results of experiments and numerical simulations, the temperature rise comparison chart experiment and simulation was obtained, as shown in Figure 6.
Figure 6. Comparison of temperature rise between experimental and simulated battery modules. (A) Comparison of battery surface temperature experiment and simulation at 26°C. (B) Comparison of battery surface temperature experiment and simulation at 40°C.
In Figure 6, there was a slight difference between the temperature rise values and simulations of batteries at the same temperature. In Figure 6A, the simulated temperature rise under different discharge currents did not exceed 1.5°C under the condition of 26°C. In Figure 6B, the difference between the experimental temperature rose and the simulated temperature rise did not exceed 1.8°C under the condition of 40°C. These data indicated that the temperature difference at the same ambient temperature was relatively small in lithium-ion batteries with different discharge rates. This proved the accuracy and reliability, accurately reflecting the heating degree. To verify the effectiveness of the cooling function of the liquid cooled heat dissipation structure designed for vehicle energy storage batteries, it was applied to battery modules to analyze their heat dissipation efficiency. The optimization of the parameters includes the design of the liquid cooling plate to better adapt to the shape and size of the battery module and improve the heat transfer efficiency. The cross-section size and shape of the runner were optimized to improve fluid flow characteristics and increase heat dissipation efficiency. For the optimization of heat transfer materials, thermal silicone materials were used between the battery and the liquid cooling plate. Under 0.1 m/s cooling medium flow rate, the surface temperature cloud map and pressure drop cloud map of the battery are shown in Figure 7.
Figure 7. Battery surface temperature cloud image and pressure drop cloud image. (A) Temperature cloud map. (B) Pressure drop cloud image.
In Figure 7, the structure of the vehicle mounted energy storage battery effectively adjusted the temperature. In terms of maximum temperature, the packs’ temperature was not high. The difference gave no information that indicating significant, ensuring that the temperature difference of the entire battery module was controlled within 5°C. Although there was still some room for optimization in the pressure drop of this structure, its effect in controlling the temperature was already quite significant.
The study simulated the parameters before and after optimization to analyze the performance differences of NSGA-II before and after optimizing the battery. The simulation cloud map is shown in Figure 8.
Figure 8. Simulation cloud image before and after optimization. (A) Before optimization. (B) After optimization.
In Figure 8, the temperature difference of the energy storage battery before and after NSGA-II optimization was 4.5°C. Compared with the predicted value after optimization, the difference was only 0.15°C, and the error was controlled within 3.2%. The liquid cooling performance was significantly improved. To analyze the performance of NSGA-II, its fitness curve and polarization characteristic curve before and after optimization were tested, as shown in Figure 9.
Figure 9. Fitness curve and polarization characteristic curve. (A) Fitness curve. (B) Polarization characteristic curve.
In Figure 9, as the population continued to evolve, the optimization process of NSGA-II gradually approached a stable value. When the population size was 30 and underwent 100 generations of evolution, the average optimal output voltage of the model started at 0.742 V. During the 1st to 10th generations, the output voltage rapidly increased. Subsequently, from the 10th generation to the 40th generation, the output voltage showed a stepwise upward trend. Finally, after the 50th generation, the output voltage stabilized at approximately 0.76 V, indicating that the NSGA-II optimization program successfully found the maximum average output voltage. This convergence process reflected the effectiveness and reliability of NSGA-II in solving optimization problems. The study compared and analyzed the optimization method of liquid structure for vehicle energy storage batteries based on NSGA-II (Method 1) with other methods. The comparison methods included genetic algorithm-based optimization of battery (Method 2), particle swarm optimization algorithm-based optimization of battery (Method 3), and simulated annealing algorithm-based optimization of battery liquid cooling heat dissipation structure (Method 4). The comparison indicators include heat dissipation efficiency, energy consumption, temperature uniformity, reliability, and optimization speed. Heat dissipation efficiency refers to the ratio of heat that the heat dissipation system can remove per unit time to the heat generated by the battery. Energy consumption means the energy consumed during the cooling system, usually calculated in electrical energy. Temperature uniformity describes the consistency of the temperature distribution between the individual cells in a battery pack. Reliability refers to the ability of the cooling system to maintain its performance over a long period. The optimization speed refers to the time required for the optimization algorithm to find the optimal or satisfactory solutions. When designing the heat dissipation structure, the optimization speed is related to the research and development cycle and cost. The comparison indicators are normalized, as shown in Table 3.
Table 3. Comparison of optimization methods and indicators of liquid cooling structure of different batteries.
In Table 3, the heat dissipation efficiency, energy consumption, temperature uniformity, reliability, and optimization speed of Method 1 were 0.78, 0.76, 0.82, 0.86, and 0.79, respectively, which were higher than the other three methods. This indicated that Method 1, based on NSGA-II, had the best performance in optimizing the liquid cooled heat dissipation structure of vehicle energy storage batteries. The paper further studied the long-term reliability considerations and compared the material degradation rate, corrosion rate, and battery life before and after optimization, as shown in Figure 10.
In Figure 10, the material degradation rate after optimization was reduced by 42%, the corrosion rate was reduced by 36%, and the battery life was improved by 17% compared to the pre-optimization. It showed that the optimized material structure had a significant improvement in performance, durability, and reliability. The experimental data were compared with the predicted results of the model to confirm whether the established heat transfer and fluid dynamics model can truly reflect the thermal behavior and heat dissipation performance of the battery under actual working conditions. The experimental data include the temperature distribution of the battery surface, the maximum temperature, temperature difference, fluid flow rate, pressure drop and average temperature difference. The details are shown in Table 4.
In Table 4, the average temperature difference predicted by the model was 4.5°C, the average temperature difference measured by the experiment was 4.3°C, the average absolute error was 0.2, and the average relative error was 4.4%. The average absolute error between the predicted value and the actual measured value was 0.25, and the relative error was less than 0.2, indicating that the model could predict the thermal behavior of the battery and the performance of the heat dissipation system well. Sensitivity analysis was performed to evaluate the influence of input parameter changes on optimization results. In the sensitivity analysis of the liquid cooling heat dissipation structure of the vehicle energy storage battery, the influence of several key parameters on the optimization results was investigated, as shown in Table 5.
In Table 5, when the battery capacity was increased to 3200 mAh to 3600 mAh, the heat dissipation efficiency was reduced and the heat dissipation difficulty was increased. When the internal resistance of the battery increased to 40 mΩ, the energy consumption increased, highlighting the importance of low internal resistance. The charge-discharge ratio varied from 1.0°C to 3.0°C, which had little effect on temperature uniformity. When the liquid cooling flow rate increased to 0.3 m/s, the heat dissipation efficiency was improved, but the pressure drop increased. When the physical parameters of the fluid changed by ±10%, they had a moderate effect on the energy consumption. This indicated that the physical characteristics of the fluid had a significant effect on the overall energy consumption of the system. The manufacturability, cost impact, and potential environmental impact of the optimized structure were discussed at the end of the study, as shown in Table 6.
In Table 6, in terms of production cost, the optimized cooling structure reduced the cost from 500,000 yuan to 430,000 yuan, and the processing time was also reduced from 40 min to 20 min. From the overall cost point of view, the optimization reduced the total cost of the cooling structure from 600,000 yuan to 540,000 yuan. At the same time, maintenance costs were reduced from 80,000 yuan to 50,000 yuan. In terms of energy consumption, the optimized cooling structure reduced monthly energy consumption from 100 kWh to 80 kWh, and the percentage of recycled materials used increased from 50% to 80%. In summary, the optimized thermal structure showed positive progress in terms of manufacturability, cost-effectiveness, and environmental impact. This structure not only improved the market competitiveness of the thermal structure, but also promoted sustainable development and environmental protection.
Under the fast growth of electric and hybrid vehicles, the heat dissipation problem of in vehicle energy storage batteries becomes more prominent. The optimization of the liquid cooling heat dissipation structure of the vehicle mounted energy storage battery based on NSGA-II was studied to reduce the temperature. The study established a multi-objective optimization model, comprehensively considering key indicators such as heat dissipation efficiency, energy consumption, and temperature uniformity. NSGA-II was used for optimization solution. The research outcomes indicated that the heat dissipation efficiency, reliability, and optimization speed of the liquid cooled heat dissipation structure optimization method for vehicle mounted energy storage batteries based on NSGA-II were 0.78, 0.76, 0.82, 0.86, and 0.79, respectively, which were higher than those of other methods. The temperature difference of the energy storage battery before and after NSGA-II optimization was 4.5°C, which was only 0.15°C different from the predicted value after optimization, and the error was controlled within 3.2%. The liquid cooling performance was significantly improved. The proposed liquid cooling heat dissipation structure significantly improved heat dissipation efficiency, reduced energy consumption, and improved temperature uniformity under the conditions of balancing heat dissipation efficiency, energy consumption, and temperature uniformity. The study does not fully consider the impact of changes in ambient temperature, battery usage patterns, and cooling fluid characteristics on the performance of the optimization design. Current design optimization is mainly based on existing material characteristics. The development of advanced materials may bring new performance improvement opportunities for cooling structures. This research focuses on liquid cooling technologies. However, other alternative cooling technologies such as phase change materials and air cooling may also have potential. Future studies need to analyze the uncertainties of these parameters in more depth and explore their long-term effects on thermal performance. Meanwhile, the integration and application of novel materials can be considered, and the application of advanced optimization algorithms in battery thermal design can be explored.
The original contributions presented in the study are included in the article/Supplementary material, further inquiries can be directed to the corresponding author.
GS: Conceptualization, Methodology, Project administration, Visualization, Writing–original draft. JP: Data curation, Formal Analysis, Software, Supervision, Writing–review and editing.
The author(s) declare that no financial support was received for the research, authorship, and/or publication of this article.
The authors declare that the research was conducted in the absence of any commercial or financial relationships that could be construed as a potential conflict of interest.
All claims expressed in this article are solely those of the authors and do not necessarily represent those of their affiliated organizations, or those of the publisher, the editors and the reviewers. Any product that may be evaluated in this article, or claim that may be made by its manufacturer, is not guaranteed or endorsed by the publisher.
Bulut, E., Albak, E. İ., Sevilgen, G., and Öztürk, F. (2022). Prediction and optimization of the design decisions of liquid cooling systems of battery modules using artificial neural networks. Int. J. Energy Res. 46 (6), 7293–7308. doi:10.1002/er.7637
Chen, S., Bao, N., Garg, A., Peng, X., and Gao, L. (2021). A fast charging-cooling coupled scheduling method for a liquid cooling-based thermal management system for lithium-ion batteries. Engineering 7 (8), 1165–1176. doi:10.1016/j.eng.2020.06.016
Duan, J., Zhao, J., Li, X., Panchal, S., Yuan, J., Fraser, R., et al. (2021). Modeling and analysis of heat dissipation for liquid cooling lithium-ion batteries. Energies 14 (14), 4187. doi:10.3390/en14144187
Fayaz, H., Afzal, A., Samee, A. D. M., Soudagar, M. E. M., Akram, N., Mujtaba, M. A., et al. (2022). Optimization of thermal and structural design in lithium-ion batteries to obtain energy efficient battery thermal management system (BTMS): a critical review. Archives Comput. Methods Eng. 29 (1), 129–194. doi:10.1007/s11831-021-09571-0
He, Y., Guo, S., Zhou, J., Ye, J., Huang, J., Zheng, K., et al. (2022). Multi-objective planning-operation co-optimization of renewable energy system with hybrid energy storages. Renew. Energy 184 (1), 776–790. doi:10.1016/j.renene.2021.11.116
Jilte, R., Afzal, A., Islam, M. T., and Manokar, A. M. (2021). Hybrid cooling of cylindrical battery with liquid channels in phase change material. Int. J. Energy Res. 45 (7), 11065–11083. doi:10.1002/er.6590
Kalaf, O., Solyali, D., Asmael, M., Zeeshan, Q., Safaei, B., and Askir, A. (2021). Experimental and simulation study of liquid coolant battery thermal management system for electric vehicles: a review. Int. J. Energy Res. 45 (5), 6495–6517. doi:10.1002/er.6268
Karimi, D., Behi, H., Akbarzadeh, M., Khaleghi, S., Van Mierlo, J., and Berecibar, M. (2021). Optimization of 1D/3D electro-thermal model for liquid-cooled lithium-ion capacitor module in high power applications. Electricity 2 (4), 503–523. doi:10.3390/electricity2040030
Karthik, A., Kalita, P., Garg, A., Gao, L., Chen, S., and Peng, X. (2021). A Novel MOGA approach for power saving strategy and optimization of maximum temperature and maximum pressure for liquid cooling type battery thermal management system. Int. J. Green Energy 18 (1), 80–89. doi:10.1080/15435075.2020.1831507
Li, J., He, S., Yang, Q., Ma, T., and Wei, Z. (2022). Optimal design of the EV charging station with retired battery systems against charging demand uncertainty. IEEE Trans. Industrial Inf. 19 (3), 3262–3273. doi:10.1109/tii.2022.3175718
Luo, H., Xiao, J., Benard, P., Chahine, R., and Yang, T. (2022). Multi-objective optimization of cascade storage system in hydrogen refuelling station for minimum cooling energy and maximum state of charge. Int. J. Hydrogen Energy 47 (20), 10963–10975. doi:10.1016/j.ijhydene.2022.01.059
Park, S., and Ahn, C. (2021). Model predictive control with stochastically approximated cost-to-go for battery cooling system of electric vehicles. IEEE Trans. Veh. Technol. 70 (5), 4312–4323. doi:10.1109/tvt.2021.3073126
Serat, Z., Fatemi, S. A. Z., and Shirzad, S. (2023). Design and economic analysis of on-grid solar rooftop PV system using PVsyst software. Archives Adv. Eng. Sci. 1 (1), 63–76. doi:10.47852/bonviewaaes32021177
Tang, X., Zhang, J., Cui, X., Lin, X., Grzesiak, L. M., and Hu, X. (2021). Multi-Objective design optimization of a novel dual-mode power-split hybrid powertrain. IEEE Trans. Veh. Technol. 71 (1), 282–296. doi:10.1109/tvt.2021.3130580
Wang, L., Luo, X., Zhang, J., and Fan, Y. (2024). Numerical study and multi-optimization of heat transfer performance in counter flow minichannel heat sink with slots on ribs using NSGA-Ⅱ. Therm. Sci. Eng. Prog. 48 (2), 102413. doi:10.1016/j.tsep.2024.102413
Wei, L., Zou, Y., Cao, F., Ma, Z., Lu, Z., and Jin, L. (2022). An optimization study on the operating parameters of liquid cold plate for battery thermal management of electric vehicles. Energies 15 (23), 9180–9196. doi:10.3390/en15239180
Xiao, W., Cheng, A., Li, S., Jiang, X., Ruan, X., and He, G. (2021). A multi-objective optimization strategy of steam power system to achieve standard emission and optimal economic by NSGA-Ⅱ. Energy 232 (1), 120953. doi:10.1016/j.energy.2021.120953
Xu, H., and Shen, M. (2021). The control of lithium-ion batteries and supercapacitors in hybrid energy storage systems for electric vehicles: a review. Int. J. Energy Res. 45 (15), 20524–20544. doi:10.1002/er.7150
Yi, F., Jiaqiang, E., Zhang, B., Zuo, H., Wei, K., Chen, J., et al. (2022). Effects analysis on heat dissipation characteristics of lithium-ion battery thermal management system under the synergism of phase change material and liquid cooling method. Renew. Energy 181 (1), 472–489. doi:10.1016/j.renene.2021.09.073
Zuo, W., Li, D., Li, Q., Cheng, Q., Zhou, K., and Jiaqiang, E. (2023). Multi-objective optimization of multi-channel cold plate under intermittent pulsating flow by RSM and NSGA-Ⅱ for thermal management of electric vehicle lithium-ion battery pack. Energy 283 (1), 129085. doi:10.1016/j.energy.2023.129085
Keywords: NSGA-II, vehicle mounted energy storage battery, liquid cooled heat dissipation structure, lithium ion batteries, optimal design
Citation: Sun G and Peng J (2024) Optimization of liquid cooled heat dissipation structure for vehicle energy storage batteries based on NSGA-II. Front. Mech. Eng 10:1411456. doi: 10.3389/fmech.2024.1411456
Received: 03 April 2024; Accepted: 30 May 2024;
Published: 01 July 2024.
Edited by:
Thanikodi Sathish, Saveetha University, IndiaCopyright © 2024 Sun and Peng. This is an open-access article distributed under the terms of the Creative Commons Attribution License (CC BY). The use, distribution or reproduction in other forums is permitted, provided the original author(s) and the copyright owner(s) are credited and that the original publication in this journal is cited, in accordance with accepted academic practice. No use, distribution or reproduction is permitted which does not comply with these terms.
*Correspondence: Guanhua Sun, YTE2ODEwMjMyOEAxNjMuY29t
Disclaimer: All claims expressed in this article are solely those of the authors and do not necessarily represent those of their affiliated organizations, or those of the publisher, the editors and the reviewers. Any product that may be evaluated in this article or claim that may be made by its manufacturer is not guaranteed or endorsed by the publisher.
Research integrity at Frontiers
Learn more about the work of our research integrity team to safeguard the quality of each article we publish.