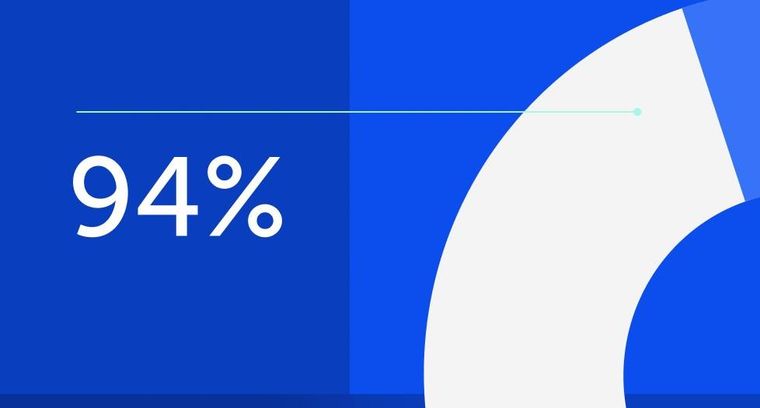
94% of researchers rate our articles as excellent or good
Learn more about the work of our research integrity team to safeguard the quality of each article we publish.
Find out more
ORIGINAL RESEARCH article
Front. Mech. Eng., 14 June 2024
Sec. Digital Manufacturing
Volume 10 - 2024 | https://doi.org/10.3389/fmech.2024.1393959
Aluminum metal–matrix composites (AMMCs) were prepared by dispersing TiO2 dispersoids of different volume fractions into an AA6063 matrix via stir casting and subjected to process–structure correlation studies. Four different samples based on weight ratio were considered herein: 99Al-1TiO2, 97Al-3TiO2, 95Al-5TiO2, and the as-received AA6063. Their mechanical properties namely, microhardness, tensile strength, and tribological behavior, were determined. In addition, the microstructure of the samples was also analysed. It was observed that the addition of 5% TiO2 particles enabled the AA6063 matrix to accommodate a higher strain energy while providing the required driving force to generate dislocations and substructures. Therefore, considering the plastic deformation, the ultimate tensile strength
Aluminum metal–matrix composite (AMMC) is a form of metal–matrix composite (MMC) in which aluminum is used as the matrix (Dey et al., 2021; Reddy et al., 2022). An MMC is a composite made up of at least two constituent materials, one of which must be a metal (Reddy et al., 2022). AMMCs have attracted substantial attention in recent years owing to their excellent mechanical and thermal properties, which have enabled their use in various industrial applications (Mavhungu et al., 2017; Srivyas and Charoo, 2019). AMMCs contain an aluminum matrix reinforced with other carbide and oxide alloys that offer a unique blend of high strength, low density, and enhanced wear resistance (Pramanik, 2016). Among the various types of reinforcements, boron carbide (B4C) and titanium dioxide (TiO2) have exhibited remarkable potential for enhancing the mechanical, tribological, and microstructural properties of AMMCs (Veeresh Kumar et al., 2017). On the other hand, aluminum and its alloys, which are renowned for their lightweight characteristics and corrosion resistance, are extensively used as the matrix in MMCs for aerospace, automotive, and other high-performance engineering applications (Dutt et al., 2021; Kumar, 2022; Kumar and Verma, 2022). Among the aluminum alloys, AA6063 has been widely used owing to its excellent extrudability and formability. Scientists and researchers have explored the integration of ceramic reinforcements to attain further enhancement of the mechanical and tribological characteristics. The combination of B4C and TiO2 particles is a compelling method of creating hybrid MMCs with synergistically improved attributes. B4C is known for its high hardness and enhanced wear resistance, whereas TiO2 offers unique chemical and mechanical properties.
Subramanian et al. reported the use of Si3N4 and BN reinforcements to improve the hardness and tribological characteristics of Al7068-based AMMCs (Subramanian et al., 2021); increasing the Si3N4 content in this AMMC improved the wear resistance while decreasing the wear rate (WR) and coefficient of friction (COF). In addition to the tribological characteristics, Yunus et al. reported the microstructural properties by considering B4C and graphite reinforcements, which impeded the dislocation movements and enhanced the material hardness, wear resistance, and microstructural as well as compressive properties (Yunus and Alfattani, 2023). In another work, Manoj Kumar et al. observed improved wear resistance of the Al6063-based AMMC upon reinforcement with fly ash and graphite (Manojkumar and Shanmuga Prakash, 2016). Minimized porosity showing wear resistance as well as predominantly abrasive and oxidative wear mechanisms at lower applied loads are also reported in other works (Chelladurai et al., 2021; Nandyala et al., 2023). In the context of mechanical properties, Ramesh et al. studied hybrid AMMCs and reported that the load transfer between the matrix and reinforcement as well as strain hardening effects were owed to the increased hardness (Ramesh et al., 2015). Shuvho et al. studied Al6063-based MMCs reinforced with Al2O3/SiC/TiO2 and reported higher hardness, tensile strength, and yield strength compared to the pure Al6063 with increasing reinforcement (Shuvho et al., 2020). Shin et al. reported the interface reactions and their influences on the mechanical properties using TiO2 nanoparticles as reinforcement; they noted that the higher chemical potential energy of the reinforcement induced dissolute formation of the interface layer and higher yield strength (Shin et al., 2014). Similarly, another study showed that aluminum oxide and TiO2 reinforcement improved the impact strength of the AMMC with simultaneous amalgamation of the reinforcements (Ahamad et al., 2020). In the context of microstructural properties, the AMMC wear surface showed abrasion, oxidation, and delamination as the dominant wear mechanisms (Joshua et al., 2018). However, diminished mechanical and wear properties were obtained for TiO2-based AMMCs at higher reinforcement weight% values owing to agglomeration of the reinforcement material (Alagarsamy and Ravichandran, 2019). A severely damaged machined subsurface with numerous geometrical defects and plastically deformed aluminum matrix was reported in another work (Kannan and Kishawy, 2006). The effects of particulate volume fraction and average size on alteration of the microhardness of the matrix were also investigated. Other types of composites and laminates prepared using different fabrication techniques have also been investigated by other researchers (Tyagi et al., 2021; Goyat et al., 2022; Singh et al., 2023; Kumar et al., 2024; Wagih et al., 2024). Bhoi et al. studied the mutual effects of ZnO nanorods and Y2O3 nanoparticles on the microstructural and mechanical responses of aluminum (Bhoi et al., 2022a); they reported that the enhanced material responses could be attributed to the uniform distribution of ZnO and Y2O3 in the hybrid composite material. In another similar work, they studied an aluminum-yttrium-oxide MMC synthesized by microwave hybrid sintering and reported enhanced nano hardness and elastic modulus (Bhoi et al., 2022b); the authors also synthesized a zinc-oxide-reinforced AMMC and noted a similar trend in the nanohardness, with marginal decrease of the elastic modulus (Kumar Bhoi et al., 2020).
Based on the above works, it is noted that the correlations between the microstructures and properties require further insights upon consideration of the combined tribological and mechanical behaviors of AA6063-TiO2. Therefore, in the present work, AA6063-TiO2 AMMCs with varying reinforcement weight% values were fabricated via stir casting. There are various fabrication methods for AMMCs, such as powder metallurgy, diffusion bonding, infiltration, and squeeze casting; however, stir casting is the most common commercial method of producing Al-matrix composites out of these techniques, where the melt is actively stirred during solidification and mixing with the reinforcing phase (Hang, 2022). This method is simpler and more flexible than other fabrication methods; it is also suitable for near-net shape components and is relevant to large-volume production. The stirring process has some important advantages, including a wider selection of materials, better matrix–particle bonding, easier control of the matrix structure, and simpler and inexpensive processing (Arsha et al., 2022). The mechanical, tribological, and microstructural properties such as ultimate tensile strength, yield strength, percentage reduction in area at fracture, microhardness, WR, effect of wear force, grain refinement, and precipitation strengthening were studied using adequate characterization techniques. The results were finally compared, and the process parameters were optimized.
The material investigated in this study was AA6063 AMMC reinforced with TiO2. Four different samples were prepared in accordance with the weight ratio as 99Al-1TiO2, 97Al-3TiO2, 95Al-5TiO2, and as-received AA6063 and evaluated thereafter. The weight% values of the matrix and reinforcement are presented in Table 1.
The flow diagram for the experimental procedures and characterizations is shown in Figure 1. The samples were prepared by a stir-casting process. Stir casting is a liquid-state method of fabricating composite materials, in which a dispersed phase is mixed with a molten matrix metal via mechanical stirring (Nandyala et al., 2023); the liquid composite material is then cast using various casting methods. However, uniform distribution of the TiO2 particles in the aluminum matrix was challenging owing to the wettability, porosity, and chemical reactions between the reinforcement material and matrix alloy (Alagarsamy and Ravichandran, 2019; Ahamad et al., 2020). Hence, a stirrer was used to disperse the TiO2 particles in the alloy matrix. AA6063 was used as the matrix material and TiO2 was used as the reinforcement. A zirconia crucible was used for melting as it possesses high resistance to thermal shock and wetting by molten metals, has low thermal expansion, and avoids carbon pickup. The crucible and reinforcements (in powder form) were preheated to a temperature of 400°C using an induction furnace to remove any moisture content as moisture affects the charge (matrix and reinforcement) reading and testing; the preheating of the reinforcement also enables better adhesion with the matrix, improves the heat insulation of the molten metal, and prevents temperature reduction.
The AA6063 ingots were heated to a temperature of 800°C, and the preheated reinforcement material was mechanically mixed with AA6063 simultaneously. The charge was melted using an induction furnace at a temperature of 830°C. The charge homogenization was achieved by the melt stirring at the rate of 550 rpm for 10 min. For the stirring process, three propeller blades were fixed on a shaft connected to the output shaft of an electric motor, and the height of the stirrer was adjustable through the lead screw power. The microhardness values of the samples were obtained using the FMV-1 Vickers microhardness testing apparatus at a load of 2 kg and dwell time of 15 s. The 136° pyramidal diamond indenter was used for the microhardness tests. The samples for this test were prepared by cutting them semiaxially using a waterjet cutting apparatus. The yield strength (σys), ultimate tensile strength (σut), fitted strain, and percentage reduction in area at fracture were calculated using a servohydraulic universal testing apparatus (INSTRON 8800). The tensile test specimens were prepared in accordance with the ASTM E8 standard (Kardak and Sinclair, 2020). The cylindrical samples with diameters of 10 mm and gauge lengths of 50 mm each were used to generate flow curves at room temperature; the test samples and sample dimensions are shown in Figures 2, 3, respectively. The samples were subjected to large-scale plastic deformations under a tensile load. The microstructural characterizations were performed via optical microscopy (OM), energy-dispersive X-ray spectroscopy (EDX, ESEM Quanta 200, FEI) attachment fitted to a scanning electron microscopy (SEM) device operated at a voltage of 20 kV in the high-current mode. The EDX samples were prepared by cutting the samples with a grinding machine and a diamond cutter. The mounted samples were then mechanically polished using emery papers with grit levels ranging from 100 to 500 µm, followed by cloth polishing using a TEGRAPOL polishing apparatus. The polishing grit were used in the size sequence of 9µ, 3µ, and 1µ for mechanical polishing.
The tribological studies were conducted in accordance with the Taguchi technique. The dry sliding wear tests were conducted using a pin-on-disc test setup as per ASTM G99-19 standards; the pin-on-disc test apparatus (NTS-V01) is shown in Figure 4A. The sliding direction in the circumferential plane and load in the axial direction are shown in Figure 4B. The sample pin was pressed against the steel disc, which was rotated at speeds of 1, 2, and 3 m/s. The hardness of the steel disc was 62 HRC, with a surface roughness of 0.5 µm. The sliding wear tests were conducted at room temperature. Before each test, the disc and samples were cleaned using acetone to eliminate possible experimental errors. The mass losses were determined using a mass balance (LF-225DR semimicro balance). All experimental trials were planned as per Taguchi’s L9 orthogonal array, where variations in the TiO2 weight%, normal load, and sliding speed were considered as the independent parameters. The influences of these parameters on the WR were determined through the analysis of variance (ANOVA) approach. After the wear tests, the sample surfaces were examined via OM.
Figure 4. Pin-on-disc wear test (A) apparatus (model NTS-V01) along with (B) load and sliding directions.
The mechanical, tribological, and microstructural characterizations of all the samples were performed, and the results were compared.
The flow curves for the AA6063, 99Al-1TiO2, 97Al-3TiO2, and 95Al-5TiO2 samples are shown in Figure 5. The region of the flow curve up to the yield strength was considered as the linear elastic region, while the region after the yield strength and up to complete fracture was considered as the plastic region. Both regions are important for engineering design considerations. However, most designs are often developed by considering the linear elastic region as the limit. There were three samples each for the AA6063, 99Al-1TiO2, 97Al-3TiO2, and 95Al-5TiO2 types that were subjected to uniaxial deformations. Hence, a total of 12 samples were tested to determine the
Table 2. Standard deviations of the
The ultimate tensile strengths of all samples are shown in Figure 6. Considering plastic deformation, 95Al-5TiO2 showed the highest ultimate tensile strength
When considering linear elastic deformations, AA6063 showed the lowest yield strength (σys) compared to the AMMC samples for all TiO2 weight% values, as shown in Figure 7. The variations in σys among the AMMC samples were minimal; in other words, the variations in weight% of TiO2 significantly enhanced the ultimate tensile strengths but not the yield strengths. The minimal variations in
According to the above observations, it is suggested that the addition of TiO2 affected the plastic deformation characteristics significantly while the linear elastic characteristics remained almost similar. Therefore, the AMMC samples in the present work are more suitable for optimum designs based on their
Figure 9. Percentage reductions in the areas at the fractures of the AA6063, 99Al-1TiO2, 97Al-3TiO2, and 95Al-5TiO2 samples.
Table 3. Percentage increases in the ultimate tensile strengths, yield strengths, microhardness, and percentage reductions in the areas at fractures for the AMMC samples.
The design of experiments (DOE) approach employing the Taguchi method of orthogonal arrays (L9, 3³), was adopted to predict the WRs considering three different process parameters (Hendronursito et al., 2020), namely, TiO2 weight%, normal load, and sliding speed. Accordingly, three levels were chosen for each of these three process parameters. The variance for WR is presented in Table 4; each row of the table represents the combination of parameters considered for the respective trial, and the last two rows indicate the residual errors and totals. The experimental data were analyzed using ANOVA to determine the effect of each parameter by considering the WR as the response. The ANOVA technique separated the observed variance data into different components for additional tests. An observed aggregate variability was grouped under two parts: systematic factors and random factors. The systematic factors had a statistical influence on the given dataset, whereas the random factors did not.
The F-statistic represents the ratio of mean-squares treatment to mean-squares error, while the p-value determines if the difference between the group means is statistically significant. The p-values of the individual parameters were significant at <0.05, indicating their statistical agreement. The contribution of the normal load was the highest, i.e., 53.72%, followed by those of the weight% of TiO2 and sliding speed. The sliding speed had the least contribution among all parameters, i.e., 14.61%. The percentage contribution of the interaction effects between the normal load and weight% of TiO2 was negligible.
Increasing values of the normal load on the pin increased the magnitude of contact stresses developed at the pin–disc interaction zone and dissipated the energy generated. The energy was dissipated in the form of heat via the force of contact friction and showed the surface damage. This suggests that the contact stresses affect the asperities on the disc surfaces, leading to ploughing. Subsequently, delamination along with severe plastic deformations were observed on the pin surfaces.
The current study examines the effects of TiO2 addition to the AA6063 matrix; therefore, the wear surface was characterized using a load of 20 N and speed of 2 m/s. The wear surface of the as-received AA6063 sample is shown in Figure 10; this sample exhibited voids owing to particle pull-out during the wear test. Crack voids as microstructural features were also reported in a similar work by Bhoi and Singh (2023). The mechanically mixed layer was also observed in the microstructure. The wear surfaces of the 95Al-5TiO2, 97Al-3TiO2, and 99Al-1TiO2 samples are shown in Figure 11, where microstructural features like voids, delamination, and microcracks are observed in the 95Al-5TiO2 sample shown in Figure 11A. This suggests that the higher TiO2 weight% causes matrix cracking and shearing of the cracks up to a certain extent. However, when the weight% of TiO2 is decreased, the samples show wear debris in addition to voids and microcracks, as seen in Figures 11B,C. This suggests that the wear debris are caused by the abrasion and adhesion induced by sliding. Similar microstructural features like minor delamination and wear debris have also been reported in other works (Bhoi and Singh, 2023). The 95Al-5TiO2 samples exhibited the least wear, while the AA6063 samples showed the most wear. It was observed that the WRs reduced with increasing weight% addition of TiO2. Here, TiO2 is a hard ceramic material; therefore, the addition of higher weight% of TiO2 resists delamination and adhesive wear attributed to the ploughing effect caused by the pull-out particles. Hence, a significant decrease in the WR was observed for 95Al-5TiO2. A higher percentage of reinforcement also improved the wear resistance of the aluminum matrix, suggesting that when the TiO2 weight% was lower (1 and 3), the surface energy was also lower; this lower surface energy showed higher susceptibility to the wear force.
Figure 10. Optical microscopy image of the wear surface of AA6063, where the red arrow indicates voids caused by particle pull out.
Figure 11. Optical microscopy images of the wear surfaces of the samples: (A) 95Al-5TiO2, (B) 97Al-3TiO2, and (C) 99Al-1TiO2. The red arrow indicates voids caused by particle pull out, while the yellow and green arrows indicate delamination and microcracks, respectively.
The experimental trials for the wear tests were conducted in accordance with Taguchi’s L9 orthogonal array, and the effects of the parameters on the WR were determined through ANOVA. The parameter levels considered in the trials are presented in Table 5. Furthermore, response surface plots (RSPs) were used to analyze the interaction effects of the parameters. The RSPs for different combinations of parameters are illustrated in Figure 12. Thus, reinforcing AA6063 with TiO2 improves the wear resistances of the AMMCs.
The microstructure of the as-received AA6063 used as the matrix for all TiO2 reinforcements is shown in Figure 13; the blue and green arrows indicate the grain boundaries (GBs) and dislocations/substructures at the grain interior, respectively. The grains were not equiaxed, meaning that they retained their thermal/mechanical strains during the thermal processing; furthermore, the presence of substructures was visible. This suggests that grain refinement may be achieved by the addition of TiO2 as reinforcement; however, the extent of microstructural changes remains to be confirmed for the AMMC samples.
Figure 13. Optical microscopy image of AA6063 at a magnification of 500×. The blue and green arrows indicate the grain boundaries and dislocations/substructures in the grain interior, respectively.
The OM-based microstructures of 99Al-1TiO2, 97Al-3TiO2, and 95Al-5TiO2 are shown in Figure 14; the GBs and grain sizes are observed to decrease with the addition of TiO2. The grain size was largest when the TiO2 weight% was lowest, that is 1; this suggests that during melt solidification (cooling cycle), the grain growth was surpassed/pinned by the TiO2 particles; in other words, the TiO2 was an obstacle to grain growth, hence causing grain-size refinement. The strength of a material is evidenced by its microstructure, and a finer grain size indicates higher ultimate tensile strength. Therefore, it is suggested that the higher ultimate tensile strength (discussed in section 3.1) is achieved by the higher weight% of TiO2. However, the presence of TiO2 is yet to be confirmed from EDX characterizations.
Figure 14. Optical microscopy images at a magnification of 500× for (A) 99Al-1TiO2, (B) 97Al-3TiO2, and (C) 95Al-5TiO2. The blue arrows (in all figures) represent the grain boundaries.
The EDX images enable qualitative analyses of the 99Al-1TiO2, 97Al-3TiO2, and 95Al-5TiO2 samples with different compositions, as given in Figure 15. Elemental mapping was carried out at chosen areas of size ∼400 µm × 400 μm in all samples; these areas are shown in the electron images given in Figures 15A–C. The elemental mappings of the samples confirm the presence of titanium (Ti) and oxygen (O) traces in the AA6063 matrix. The elemental maps of Ti originate from the K-shells (Ka1) of the samples, as shown in Figures 15D–F. Similarly, the elemental maps of O are shown in Figures 15G–I. From the elemental mapping, it was confirmed that TiO2 was present in the AA6063 matrix. The dispersions of Ti observed in Figures 15D–F are in good agreement with the weight percentages of Ti added to the AA6063 matrix. The presence (violet-colored dots) of Ti is minimum in Figure 15D, corresponding with the lower Ti quantity of 1%, while the Ti presence is more prominent in Figure 15F, in which the Ti quantity was higher (5%). Furthermore, from Figures 15G–I, it is seen that O was not uniformly distributed, suggesting that most of the O atoms were bonded with Ti rather than Al. The corresponding quantitative EDX elemental weight% of the 99Al-1TiO2, 97Al-3TiO2, and 95Al-5TiO2 samples are presented in Table 6. It is suggested that in addition to TiO2, other reinforcements like boron carbide (B4C) and silicon carbide (SiC) in the AMMCs can further influence the mechanical, tribological, and microstructural properties, which will be an investigation for a future work.
Figure 15. Scanning electron microscopy images showing the chosen areas for elemental mapping in the (A) 99Al-1TiO2, (B) 97Al-3TiO2, and (C) 95Al-5TiO2 samples. Energy-dispersive X-ray spectroscopy images showing Ti distribution in the (D) 99Al-1TiO2, (E) 97Al-3TiO2, and (F) 95Al-5TiO2 samples, as well as O distribution in the (G) 99Al-1TiO2, (H) 97Al-3TiO2, and (I) 95Al-5TiO2 samples.
The correlations between the microstructures and properties were analyzed by considering the influences of the grain sizes, microstructural features, and extent of inclusion of TiO2 in the AA6063 matrix on the mechanical properties (ultimate tensile strength, yield strength, and microhardness). The Hall–Petch relationship depicts the relationship between the theoretical yield strength and grain size of a material (Reed-Hill et al., 1973; Dieter and Bacon, 1976; Armstrong, 2014):
where
The above equation supports the hypothesis of a higher yield strength for a finer grain size as compared to coarse grains. In the present work, a similar trend was observed when the AMMC samples showed higher
Furthermore, the lower surface energy provides higher susceptibility against wear force. The addition of higher weight% of TiO2 resisted matrix-reinforcement delamination and was attributed to the ploughing effect caused by the pull-out particles. Therefore, a substantial reduction in the WR was observed for 95Al-5TiO2, as discussed in section 3.2. In addition to qualitative analysis of the microstructure, a quantitative analysis can be performed; this study establishes a more generalized relation between the grain sizes and yield strengths of the AMMC samples and AA6063. The Hall–Petch constants specific for a given TiO2 weight% are also calculated. However, similar studies can be conducted for hybrid AMMCs by considering boron carbide as an additional reinforcement with TiO2. The characterization techniques adopted in the present work can also be further improved by calculating the different microstructural phase percentages using electron backscattered diffraction (EBSD).
The principal premises of the current research yield significant results as follows:
1. The
2. When linear elastic deformation is considered, AA6063 shows the lowest yield strength (σys) compared to the AMMC samples for all TiO2 weight% values; however, the variations in σys among the AMMC samples are minimal.
3. The microhardness of the samples increases gradually with the addition of TiO2, and the percentage reduction in the area at the fracture is largest for 95Al-5TiO2. The addition of TiO2 as reinforcement enables the materials to accommodate higher strain energies. This higher strain energy provides the required driving force for the generation of dislocations and substructures, thereby increasing the microhardness with the addition of TiO2.
4. The percentage contribution of normal load to the material wear is highest (53.72), followed by those of weight% of TiO2 and sliding speed. The sliding speed has the least contribution among all parameters (14.61%). The percentage contribution of the interaction effects between normal load and weight% of TiO2 are negligible.
5. Wear surface characteristics, such as microvoids, delamination, microcracks, and wear debris, are qualitatively observed for most of the samples to varying extents.
6. During melt solidification (cooling cycle), the grain growth is surpassed/pinned by the TiO2 particles in the AMMCs; that is, TiO2 hinders the grain growth, thereby providing grain-size refinement, which in turn provides a higher ultimate tensile strength.
The original contributions presented in the study are included in the article/Supplementary Material; further inquiries can be directed to the corresponding authors.
JP: data curation, investigation, and writing–original draft. DR: conceptualization, methodology, supervision, and writing–review and editing. RM: formal analysis, software, and writing–review and editing. AK: formal analysis, investigation, and writing–review and editing. PK: formal analysis, investigation, and writing–review and editing. VHM: conceptualization, formal analysis, and writing–review and editing.
The author(s) declare that no financial support was received for the research, authorship, and/or publication of this article.
The authors declare that the research was conducted in the absence of any commercial or financial relationships that could be construed as a potential conflict of interest.
All claims expressed in this article are solely those of the authors and do not necessarily represent those of their affiliated organizations, or those of the publisher, the editors, and the reviewers. Any product that may be evaluated in this article, or claim that may be made by its manufacturer, is not guaranteed or endorsed by the publisher.
AMMC, aluminum metal–matrix composite; ANOVA, analysis of variance; EDX, energy-dispersive X-ray spectroscopy; GB, grain boundary; MMC, metal–matrix composite; OM, optical microscopy; SEM, scanning electron microscopy.
Ahamad, N., Mohammad, A., Sadasivuni, K. K., and Gupta, P. (2020). Structural and mechanical characterization of stir cast Al–Al2O3–TiO2 hybrid metal matrix composites. J. Compos. Mater. 54 (21), 2985–2997. doi:10.1177/0021998320906207
Alagarsamy, S. V., and Ravichandran, M. (2019). Synthesis, microstructure and properties of TiO2 reinforced AA7075 matrix composites via stir casting route. Mater. Res. Express 6 (8), 086519. doi:10.1088/2053-1591/ab1d3b
Anderson, T. L. (2017). Fracture mechanics: fundamentals and applications. Boca Raton, FL: CRC Press.
Armstrong, R. W. (2014). Engineering science aspects of the Hall–Petch relation. Acta Mech. 225, 1013–1028. doi:10.1007/s00707-013-1048-2
Arsha, A. G., Manoj, V., Raag, L. A., Akhil, M. G., and Rajan, T. P. D. (2022). “Metallic nanocomposites for automotive applications,” in Nanotechnology in the automotive industry (Elsevier), 163–198.
Bhoi, N. K., and Singh, H. (2023). Evaluation of susceptor-assisted microwave-sintering-produced Al-Y2O3 composite material’s compression and reciprocating wear performance. Phys. Scr. 98 (10), 105938. doi:10.1088/1402-4896/acf744
Bhoi, N. K., Singh, H., Pratap, S., Gupta, M., and Jain, P. K. (2022a). Investigation on the combined effect of ZnO nanorods and Y2O3 nanoparticles on the microstructural and mechanical response of aluminium. Adv. Compos. Mater. 31 (3), 289–310. doi:10.1080/09243046.2021.1993555
Bhoi, N. K., Singh, H., Pratap, S., and Jain, P. K. (2022b). Aluminum yttrium oxide metal matrix composite synthesized by microwave hybrid sintering: processing, microstructure and mechanical response. J. Inorg. Organomet. Polym. Mater. 32, 1319–1333. doi:10.1007/s10904-021-02195-8
Chelladurai, S. J. S., Kumar, S. S., Venugopal, N., Ray, A. P., Manjunath, T., and Gnanasekaran, S. (2021). A review on mechanical properties and wear behaviour of aluminium based metal matrix composites. Mater. Today Proc. 37 (9), 908–916. doi:10.1016/j.matpr.2020.06.053
Dey, A., Shrivastav, M., and Kumar, P. (2021). Optimum performance evaluation during machining of Al6061/cenosphere AMCs using TOPSIS and VIKOR based multi-criteria approach. Proc. Institution Mech. Eng. Part B J. Eng. Manuf. 235 (13), 2174–2188. doi:10.1177/0954405420958770
Dutt, A. K., Sindhuja, K., Reddy, S. V. N., and Kumar, P. (2021). “Application of artificial neural network to friction stir welding process of AA7050 aluminum alloy,” in Advances in industrial automation and smart manufacturing: select proceedings of ICAIASM 2019 (Singapore: Springer), 407–414.
Goyat, V., Ghangas, G., Sirohi, S., Kumar, A., and Nain, J. (2022). A review on mechanical properties of coir based composites. Mater. Today Proc. 62 (Part 4), 1738–1745. ISSN 2214-7853. doi:10.1016/j.matpr.2021.12.252
Hendronursito, Y., Rajagukguk, T. O., Safii, R. N., Sofii, A., Isnugroho, K., Birawidha, D. C., et al. (2020). Analysis of aluminium basalt particulate composite using stirring casting method through taguchi method approach. IOP Conf. Ser. Mater. Sci. Eng. 807 (1), 012003. doi:10.1088/1757-899x/807/1/012003
Joshua, K. J., Vijay, S. J., and Selvaraj, D. P. (2018). Effect of nano TiO2 particles on microhardness and microstructural behavior of AA7068 metal matrix composites. Ceram. Int. 44 (17), 20774–20781. doi:10.1016/j.ceramint.2018.08.077
Kannan, S., and Kishawy, H. A. (2006). Surface characteristics of machined aluminium metal matrix composites. Int. J. Mach. Tools Manuf. 46 (15), 2017–2025. doi:10.1016/j.ijmachtools.2006.01.003
Kardak, A. A., and Sinclair, G. B. (2020). Stress concentration factors for ASTM E8/E8M-16a standard round specimens for tension testing. J. Test. Eval. 48 (1), 711–719. doi:10.1520/jte20190549
Kumar, P. (2022). Fatigue life estimation of 7020 aluminum alloy subjected to aqueous sodium chloride solution. Key Eng. Mater. 928, 17–23. doi:10.4028/p-oi3mxu
Kumar, P., Hussain, S. S., Kumar, A., Srivastava, A. K., Hussain, M., and Singh, P. K. (2024). “10 Finite element method investigation on delamination of 3D printed hybrid composites during the drilling operation,” in 3D printing technologies: digital manufacturing, artificial intelligence, industry 4.0. Editors A. Kumar, P. Kumar, N. Sharma, and A. Kumar Srivastava (Berlin, Boston: De Gruyter), 223–234. doi:10.1515/9783111215112-010
Kumar, P., and Verma, B. B. (2022). Propagation of corrosion induced fatigue crack in aluminum alloy. AIMS Mater. Sci. 9 (3), 512–521. doi:10.3934/matersci.2022030
Kumar Bhoi, N., Singh, H., and Pratap, S. (2020). Synthesis and characterization of zinc oxide reinforced aluminum metal matrix composite produced by microwave sintering. J. Compos. Mater. 54 (24), 3625–3636. doi:10.1177/0021998320918646
Manojkumar, M., and Shanmuga Prakash, R. (2016). Wear characteristics of hybrid Al 6063 matrix composites reinforced with graphite and fly ash particulates. Appl. Mech. Mater. 854 (January), 1–9. doi:10.4028/www.scientific.net/amm.854.1
Mavhungu, S. T., Akinlabi, E. T., Onitiri, M. A., and Varachia, F. M. (2017). Aluminum matrix composites for industrial use: advances and trends. Procedia Manuf. 7, 178–182. doi:10.1016/j.promfg.2016.12.045
Nandyala, K., Kumar, B. S., and Durga Bhavani, G. I. K. (2023). Developing of hybrid composite of Al-6068 and Al-7075 by reinforcing TiO2/BN by stir casting process and finding mechanical and wear behavior of the hybrid composition. Chem. Bull. 2023 (6), 1036–1044. doi:10.31838/ecb/2023.12.6.95
Pramanik, A. (2016). Effects of reinforcement on wear resistance of aluminum matrix composites’, Transactions of Nonferrous Metals Society of China (English Edition). Nonferrous Metals Soc. China 26 (2), 348–358. doi:10.1016/S1003-6326(16)64125-0
Ramesh, B. T., Kumar, B. A. M., and Swamy, R. P. (2015). Dry sliding wear test conducted on pin-on-disk testing setup for Al6061-sic metal matrix composites fabricated by powder metallurgy. Int. J. Innovative Sci. Eng. Technol. 2 (6).
Reddy, D. A. K., Rajesh, G., Anbuchezhiyan, G., Ponshanmugakumar, A., Ganesan, R., Latha, A., et al. (2023). Investigating the mechanical properties of titanium dioxide reinforced magnesium composites. Mater. Today Proc. doi:10.1016/j.matpr.2023.05.193
Reddy, K. S. K., Lekha, B. C., Sakshi, K. U., Chouhan, M. S., Karthikeyan, R., and Aparna, S. (2022). Effect of different reinforcements on aluminium composite properties–a review. Mater. Today Proc. 62, 3963–3967. doi:10.1016/j.matpr.2022.04.572
Reed-Hill, R. E., Abbaschian, R., and Abbaschian, R. (1973). Physical metallurgy principles, 17. New York: Van Nostrand.
Shin, J. H., Choi, H. J., Cho, M. K., and Bae, D. H. (2014). Effect of the interface layer on the mechanical behavior of TiO2 nanoparticle reinforced aluminum matrix composites. J. Compos. Mater. 48 (1), 99–106. doi:10.1177/0021998312469238
Shuvho, M. B. A., Chowdhury, M. A., Kchaou, M., Roy, B. K., Rahman, A., and Islam, M. A. (2020). Surface characterization and mechanical behavior of aluminum based metal matrix composite reinforced with nano Al2O3, SiC, TiO2 particles. Chem. Data Collect. 28, 100442. doi:10.1016/j.cdc.2020.100442
Singh, A., Srivastava, A. K., Singh, G., Singh, A. D., Singh, H. K., Kumar, A., et al. (2023). Utilization of plastic waste for developing composite bricks and enhancing mechanical properties: a review on challenges and opportunities. Adv. Polym. Technol. 2023, 1–24. Article ID 6867755, 24 pages. doi:10.1155/2023/6867755
Srivallirani, K., and Rao, M. V. (2021). Fabrication and mechanical characterization of Al 7050/TiO2/BN hybrid metal matrix composites. Mater. Today Proc. 39, 1750–1753. doi:10.1016/j.matpr.2020.06.386
Srivyas, P. D., and Charoo, M. S. (2019). Application of hybrid aluminum matrix composite in automotive industry. Mater. Today Proc. 18, 3189–3200. doi:10.1016/j.matpr.2019.07.195
Subramanian, K., Murugesan, S., Mohan, D. G., and Tomków, J. (2021). Study on dry sliding wear and friction behaviour of al7068/si3n4/bn hybrid composites. Materials 14 (21), 6560. doi:10.3390/ma14216560
Tyagi, A., Pandey, S. M., Walia, R. S., Murtaza, Q., and Kumar, A. (2021). “Effect of temperature on the sliding wear behavior of HVOF sprayed Al2O3 composite coating,” in Advances in materials and mechanical engineering. Lecture notes in mechanical engineering. Editors C. Pandey, V. Goyat, and S. Goel (Singapore: Springer). doi:10.1007/978-981-16-0673-1_3
Veeresh Kumar, G. B., Gouda, P. S. S., Pramod, R., and Rao, C. S. P. (2017). Synthesis and characterization of TiO2 reinforced Al6061 composites. Adv. Compos. Lett. 26 (1), 096369351702600–096369351702623. doi:10.1177/096369351702600104
Wagih, A., Junaedi, H., Mahmoud, H. A., Lubineau, G., Kumar, A., and Sebaey, T. A. (2024). Enhanced damage tolerance and fracture toughness of lightweight carbon-Kevlar fiber hybrid laminate. J. Compos. Mater. 0 (0), 1109–1121. doi:10.1177/00219983241235853
Keywords: aluminum metal–matrix composite, ultimate tensile strength, microhardness, yield strength, wear rate, precipitation, grain refinement
Citation: Pattar J, Ramesh D, Malghan RL, Kumar A, Kumar P and H. M. V (2024) Investigation of AA6063-based metal–matrix composites reinforced with TiO2 dispersoids through digitally assisted techniques for mechanical, tribological, and microstructural characterizations. Front. Mech. Eng 10:1393959. doi: 10.3389/fmech.2024.1393959
Received: 29 February 2024; Accepted: 13 May 2024;
Published: 14 June 2024.
Edited by:
Kanak Kalita, Vel Tech Dr. RR & Dr. SR Technical University, IndiaReviewed by:
Satyanarayan, Kumamoto University, JapanCopyright © 2024 Pattar, Ramesh, Malghan, Kumar, Kumar and H. M.. This is an open-access article distributed under the terms of the Creative Commons Attribution License (CC BY). The use, distribution or reproduction in other forums is permitted, provided the original author(s) and the copyright owner(s) are credited and that the original publication in this journal is cited, in accordance with accepted academic practice. No use, distribution or reproduction is permitted which does not comply with these terms.
*Correspondence: Dasappa Ramesh, cmFtZXNoZEBzc2l0LmVkdS5pbg==; Vishwanatha H. M., dmlzaHdhbmF0aGEuaG1AbWFuaXBhbC5lZHU=
Disclaimer: All claims expressed in this article are solely those of the authors and do not necessarily represent those of their affiliated organizations, or those of the publisher, the editors and the reviewers. Any product that may be evaluated in this article or claim that may be made by its manufacturer is not guaranteed or endorsed by the publisher.
Research integrity at Frontiers
Learn more about the work of our research integrity team to safeguard the quality of each article we publish.