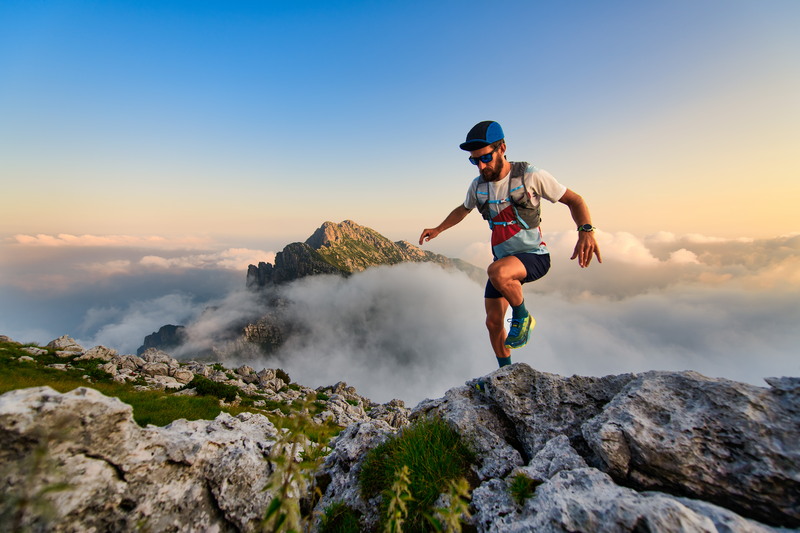
95% of researchers rate our articles as excellent or good
Learn more about the work of our research integrity team to safeguard the quality of each article we publish.
Find out more
ORIGINAL RESEARCH article
Front. Mech. Eng. , 04 April 2024
Sec. Digital Manufacturing
Volume 10 - 2024 | https://doi.org/10.3389/fmech.2024.1391315
This study compares conventional turning (CT) and ultrasonic vibration-assisted turning (UVAT) in machining hardened AISI 52100 steel (62 HRC) with a PVD-coated TiAlSiN carbide tool. UVAT experiments, utilizing an ultrasonic frequency of 20 kHz and vibration amplitude of 20 µm, varied the cutting speed, feed, and depth of cut. Remarkably, UVAT reduced tool wear, extending tool longevity. Surprisingly, power consumption showed no significant differences between CT and UVAT. Mathematical models based on experimental data highlight the substantial impact of the cutting speed on tool wear, followed closely by the depth of cut. For power consumption, the depth of cut took precedence, with the cutting speed and feed rate playing pronounced roles in UVAT. This emphasizes the potential for further research on machinability, particularly exploring different vibration directions on the tool in feed, tangential, and radial aspects.
The use of a novel technology for producing the components of lightweight materials and reducing the requirements of power utilized during manufacturing processes can be a great way to decrease pollution and save resources.
Because of its superior mechanical qualities, hardened AISI 52100 steel has found widespread application in industries, such as aviation bearings, aerospace components, and fuel injector nozzles. However, it is a pure case of a typical difficult-to-cut material that results in a huge built-up edge (BUE), poor surface quality, early tool failure, high cutting temperature, and severe work hardening in conventional turning (CT) (Ezugwu and Wang, 1997). However, considerable efforts were made on the machining of hardened steel by superimposing high-frequency, small-amplitude ultrasonic vibrations on the cutting tool for improved performance. The manufacturing of components from hard materials and alloys with reduced and optimized resources is one of the major areas of interests for researchers and scientists (Kumar et al., 2024a; Kumar et al., 2024b; Kumar Ajay et al., 2024). Three-dimensional (3-D) components can be fabricated successfully using novel manufacturing techniques for the aircraft and automobile sectors (Srivastava et al., 2023).
Ultrasonic vibration-assisted turning (UVAT) provides periodic separation between the cutting tool and the workpiece (Mitrofanov et al., 2003; Zhou et al., 2003). Ultrasonic vibration-assisted grinding, drilling, milling, and turning have been the subject of extensive research since the 1970s, particularly in the last 10 years. Koshimizu (2009) performed the machining of Ti-6Al-4V using an ultrasonic vibration with a frequency of 19 kHz and an amplitude of 0.03 mm. Their study found a lower cutting force, almost half to one-third of the cutting force using ultrasonic vibrations, than that of conventional machining. In addition, their computational simulation study showed lower cutting temperatures up to 100°C than in CT.
Maurotto et al. (2010) observed a decrease in the average tangential force, from 89.9 N to 48 N and from 51.8 N to 11.2 N for depths of cut of 100 and 200 μm, respectively, using ultrasonic vibrations during the machining of advanced alloys. Jiao et al. (2011) found that the 2D and 3D geometrical properties of ultrasonic machined surfaces outperformed those of conventionally machined surfaces during machining quenched steel at 50 HRC using a PCBN tool at an ultrasonic frequency of 20 kHz and amplitude of 16 µm. In addition, the influence of feed in UVAT was significantly lower than that for CT under the same cutting conditions.
Vivekananda et al. (2014) also observed a decrease in the cutting forces and surface roughness by 8%–54% and 12.5%–54.5%, respectively, in UVAT compared to CT. Habtamu et al. (2017) observed lower flank wear of about 20% and better surface quality with UVAT against CT during machining Inconel 718. The effects of ultrasonic vibration on coated carbide tool wear when cutting were investigated by Airao et al. (2021), who observed abrasion, chipping, notch wear, and built-up edge adhesion during the machining of Nimonic 90 under dry and wet conditions. However, this effect was less prominent with UVAT. In addition, their study found a 20% reduction in the flank wear width and a decrease in the cutting and feed force by 6%–20% and 13%–27%, respectively, with UVAT compared to the CT. Moreover, smoother, thinner, and shorter-length chips were obtained under UVAT against CT.
However, Dodla (2022) observed a higher tool wear rate in UVAT against CT during machining Inconel 718. A group of researchers evaluated the power consumption and surface roughness considering the effect of the process parameters (Valera and Bhavsar, 2014). The power consumption increased with the speed, feed, and depth of cut. Patel et al., (2020) observed a 43% reduction in surface roughness and a 3.13% reduction in power consumption with UVAT compared to CT during turning AISI 420 stainless steel. Ultrasonic vibrations superimposed on the tool produced discontinuous and segmented chips against continuous chips with CT. Florez Garcia et al. (2020) observed improved machinability of S235 carbon steel up to 18% with UVAT.
Razavi et al. (2012) investigated whether applying ultrasonic vibrations to the typical motion of the tool and workpiece in the turning process induces compression of the lateral machined surface of the workpiece, resulting in an increase in the surface hardness of the workpiece compared to CT. The experiments were performed on an aluminum rod with a carbide insert, VBMT-160404, at a frequency of f = 20 kHz and an amplitude of a = 10 m. Furthermore, the Vickers micro-hardness test demonstrated that the tool reciprocating motion impacts the hardness of the lateral machined surface. Additionally, Xu et al. (2020) emphasized on the theory of UAT tests with and without ultrasonic vibration on Inconel 718. The surface roughness, surface topography, and chip shape of the machined workpiece were studied and evaluated. When Inconel 718 was treated with UAT, the results revealed that it had a better machining effect than CT. The best parameter ranges for processing Inconel 718 utilizing the UAT machining technique developed in this study were ap = 0.1–0.15 mm and = 0.08–0.15 mm/rev, as appropriate technical parameters were applied. Inconel 718 UAT improved surface roughness, surface topography, and chip shape to varying degrees compared to CT. Researchers determined that with the right technical parameters, UAT can outperform CT in terms of machining performance. Zou et al. (2017) highlighted extensive theoretical and experimental research on ultrasonic vibration-aided turning of die steels utilizing single-crystal diamond tools. They reported that diamond tool wear was shown to depend highly on the feed rate and cutting speed while being insensitive to the depth of cut and tool relief angle. The technology of ultrasonic vibration-aided turning has the potential to drastically minimize tool wear. Moreover, Patil et al. (2014) explored the experimental characterization of UAT and the 2D FE transient simulation of UAT in the DEFORM framework. With the exception of the penetration stage, where both tools are subjected to the same stress levels, the simulation shows that UAT decreases the stress level on the cutting tool during machining compared to CT. Compared to CT, UAT has cutting pressures that are 40%–45% lower and a cutting temperature that is 48% lower. The UAT process experimental investigation showed that UAT surfaces are smoother than CT surfaces and have a matte finish compared to the glossy finish of CT surfaces. Kumar et al. (2023) proposed an exploration of additive manufacturing (AM) technologies, encompassing materials like polymers, ceramics, metals, composites, biomaterials, and smart materials. This aligns with the innovative advancements in UVAT, where a diverse range of materials is machined. The parallel lies in the adaptability and transformative potential of both AM and UVAT, contributing to advanced manufacturing processes that cater to specific needs, whether in the fabrication of biocomponents or the precision machining of various materials. Alper Sofuoglu et al. (2021) used DEFORM-2D software to investigate the numerical performance of Ti6Al4V alloy during hot ultrasonic-assisted turning (HUAT). For the simulation investigation, cutting parameters comprised cutting speed, feed rate, vibrational parameters, and preheating temperatures. Cutting forces, maximum effective stresses, and cutting temperatures were calculated using these values. The environmental effect and energy usage of this process have also been investigated. Cutting speed, feed rate, and preheating temperatures have a greater influence on machining characteristics than vibrational parameters. Reduced cutting and feed rates result in lower energy use. Furthermore, as the heating temperature and vibration frequency/amplitude increase, so does the power consumption. The results show that reduced cutting and feed rates result in less electricity being utilized. In addition, when the heating temperature, frequency, and amplitude increase, so does the power consumption. Kumar and Gulati (2019) proposed an optimization framework using the Taguchi method (TM) and analysis of variance (ANOVA) in single point incremental forming (SPIF). Investigating surface roughness in SPIF, they identified key parameters like tool diameter, shape, and forming oil viscosity as pivotal factors influencing the process. This optimization approach echoes the significance of parameter selection in enhancing the surface quality. Such methodologies find applicability in UVAT, highlighting the universal importance of optimization in diverse manufacturing processes, as reviewed in the existing literature. Moreover, it is observed that according to most of the researchers, turning with ultrasonic vibrations enhances machining efficiency. On the other hand, the impact of ultrasonic vibrations on the machinability of hardened steel is not well studied. The amount of power used when turning hardened steel while using ultrasonic vibrations has also received little attention from researchers. To bridge these knowledge gaps, this research study compares hardened AISI 52100 steel (62 HRC) using CT and UVAT techniques. A PVD-coated TiAlSiN carbide tool is used in the experimentation, and UVAT trials are carried out at an ultrasonic frequency of 20 kHz and a vibration amplitude of 20 µm. To thoroughly evaluate the performance, variations in the cutting speed, feed, and depth of cut during UVAT experiments are methodically investigated. The study aims to create mathematical models based on experiments in addition to these empirical investigations. The purpose of these models is to offer a detailed understanding of the ways in which the machinability of hardened steel is impacted by ultrasonic vibrations. Finally, by identifying the strengths and limitations of UVAT in machining hardened steel, the study aims to outline areas for future research and potential enhancements in the machining process. Ultimately, this work offers a fresh perspective on reducing tool wear and surprising results about power usage by focusing only on the machining of hardened AISI 52100 steels. Comparing UVAT with CT, with differences in the cutting speed, feed, and depth of cut, highlights the importance of UVAT in prolonging tool life and offers important insights into the dynamics of power usage. The machinability of hardened AISI 52100 steels using UVAT is a specific knowledge gap that this work fills by providing insightful empirical data and mathematical models. Table 1 below represents the summary of the contribution of this work.
Superimposing the ultrasonic vibrations on the workpiece was a challenging task because of its varying shape, size, and weight. On the other hand, it is easier to superimpose the ultrasonic vibration on top of a cutting tool, in addition to having a relatively set shape and lower weight. In this study, the designed UVAT machining system superimposes ultrasonic vibration on the cutting tool. UVAT can be divided into three categories based on the direction of the ultrasonic vibration: transverse vibration turning, longitudinal vibration turning, and feed vibration turning (Ghule and Sanap, 2021; Ghule et al., 2022).
In this study, longitudinal vibration turning is chosen so that the cutting tool can access the ultrasonic frequency mechanical vibration of a specific magnitude and carry out UVAT. A key element of an ultrasonic vibration-aided system is the ultrasonic horn. The vibrational energy created by the ultrasound generator in the ultrasonic horn is kept constant in the first instance. As the energy density is higher in the relatively small region, it results in increasing the ultrasonic amplitude to the required amplitude at the output end.
The entire setup of the ultrasonic vibratory tool (UVT) consists of a piezoelectric transducer, booster, and a horn, which acts like a tool holder. The UVT is mounted in place of the tool post on the lathe. Before the experiment, one end of the workpiece was held appropriately in a lathe chuck, while the other end was in a tailstock. The fixture was developed and engineered to install an UVT on a cross-slide of a lathe machine. Table 2 shows the factors considered with their actual values for the design of the ultrasonic horn. The selection of specific parameters for designing the ultrasonic horn in UVAT) is crucial for optimizing machining performance. Choosing a titanium alloy (Grade 5) ensures both structural integrity and durability in the demanding machining environment. A longitudinal velocity of sound at 4,400 m/s aligns with material properties, facilitating the efficient transmission of ultrasonic waves. A resonant frequency of 20 kHz is carefully chosen to match the machining requirements for enhanced tool performance. A larger diameter (40 mm) provides stability, while the resonant length (110 mm) maximizes resonance, collectively ensuring an effective and reliable UVAT process for machining hardened AISI 52100 steels.
Table 2. Factors considered for the designing of the ultrasonic horn (Kandi et al., 2020).
The UVT was secured to a fixture utilizing a collar and disc arrangement and bolted from the bottom side of the collar. The fixture has a provision for moving the entire UVT assembly along the feed direction. Figure 1 shows the schematic of the UVAT fixture used in the present study.
Figure 1. Schematic diagram of ultrasonic vibration-assisted turning (UVAT) fixture (Ghule and Sanap, 2021; Ghule et al., 2022).
During machining, the cutting tool and workpiece are intermittently separated and contacted. This intermittent cutting process prevents BUE formation. There are four stages of UVAT operation, namely, tool approach, tool contact, tool immersion, and tool back-off. In the tool approach stage, the tool moves toward the workpiece from its initial position. The tool–workpiece contact is established in the contact stage. The actual machining occurs in the tool immersion stage, and the tool returns to its original position during the back-off stage. These four stages of UVAT are shown in Figure 2. Figure 3 illustrates the different components of UVAT, such as the lathe, workpiece, fixture, ultrasonic frequency generator, and transducer–booster unit.
Figure 2. Stages of UVAT (Ghule and Sanap, 2021; Ghule et al., 2022).
The ultrasonic frequency generator generates a signal at a specific frequency that might be sinusoidal or pulsed. It is the specific frequency at which the transducer works. A piezoelectric transducer modifies the electrical energy pulses into mechanical vibratory waves. The height of the tool nose is maintained at the center of the workpiece during UVAT. The cutting insert is fastened to the ultrasonic horn. It becomes a resonant system with the entire vibration device, and the vibrational frequency remains constant (Duman et al., 2024). In this work, ultrasonic vibrations are delivered in the tangential direction to the cutting insert during the hard turning of AISI 52100 steel, as depicted in Figure 4.
Figure 4. Position of the stepped horn in UVAT (Ghule and Sanap, 2021; Ghule et al., 2022).
The actual photograph for the above setup is shown in Figure 5.
The workpiece material chosen for the investigation is high-carbon AISI 52100 alloy steel. AISI 52100 steel has high hardness and excellent wear resistance. Tables 3 and 4 summarize the chemical and mechanical parameters of AISI 52100 steel, respectively. It finds wide applications in ball and roller bearings, automotive chain parts, etc.
Table 3. Chemical and mechanical properties of AISI 52100 steel (Guo and Liu, 2002).
Table 4. Chemical and mechanical properties of AISI 52100 steel (Guo and Liu, 2002).
Extreme precision in the selection of cutting tool materials, tool geometry, and cutting conditions is crucial to meet the considerable challenges presented by large cutting forces, extensive work hardening, quick tool wear, and chip breakage when turning hardened AISI 52100 steel. The exceptional hot hardness and abrasion resistance of the cutting tool material are key factors in machinability. Table 5 describes the TiAlSiN nano-laminate cutting insert used in this investigation, which is PVD-coated. Table 6 shows how the response surface methodology, which is a central composite rotatable design, was used to strategically choose the ultrasonic frequency (20 kHz), vibrational amplitude (20 µm), cutting speed, feed, and depth of cut after pilot testing.
Tool wear and power consumption were the primary foci of the current study. Tool wear was measured using a Dino-Lite digital microscope with a magnification of up to ×240. A clothespin-shaped gadget, a clamp meter, was used to determine the current carried by a live wire. The magnetic field formed by a flowing current in a wire was detected by a clamp meter. The product of voltage and measured current provides the power consumption during machining. The actual photograph of the experimental setup is shown Figure 6.
This section presents the experimental findings and discussions on the comparative evaluation of the tool wear and power consumption during CT and UVAT of hardened AISI 52100 steel (62 HRC) using a PVD-coated TiAlSiN carbide tool. UVAT experiments were performed with an ultrasonic frequency of 20 kHz and vibration amplitude of 20 µm by varying the cutting speed, feed, and depth of cut. The effect of ultrasonic vibrations on the tool wear and power consumption during UVAT against CT is discussed by developing experiment-based mathematical models. Finally, this section lists the scope for further work to improve the machinability of hardened steel using a coated carbide tool.
Tool wear is the steady degradation of the tool material, which leads the tool to deviate from its initial geometry during cutting. The tool wear affects the machining effectiveness, precision, and cutting power. Additionally, tool wear has a significant influence on the surface quality of the machined component. In this study, the tool wear was measured using a digital microscope. Experiments were performed varying the cutting speed, feed, and depth of cut. The ultrasonic vibrations with a frequency of 20 kHz and vibrational amplitude of 20 microns were superimposed on the tool in the tangential direction during UVAT. The tool wear with CT and UVAT under different cutting conditions was measured after turning for a fixed length. The tool wear and power consumptions measured under different cutting conditions under CT and UVAT are given in Table 7.
The power consumption (Pm) models for CT and UVAT are shown in Eqs 3, 4, respectively:
ANOVA supports the researchers by grading the significance of process variables by the P-test (Kumar and Gulati, 2018; Kumar and Gulati, 2021). To ascertain the validity and consistency of the results, the data obtained from the experimental trials were subjected to a thorough statistical analysis. For every statistical test, the significance level (α) was established at 0.05, signifying a 95% confidence level.
ANOVA was used to determine the important variables affecting tool wear in both CT and UVAT scenarios.
To determine how much the cutting speed, feed, and depth of cut affected the tool wear statistically, the F-test was used. A larger F-value for cutting speed was found in ANOVA for tool wear under CT, suggesting that this parameter had a significant impact on tool wear. As an illustration of its significant impact on tool wear, ANOVA for tool wear under UVAT showed a higher F-value for the depth of cut. Similarly, power consumption data were subjected to ANOVA to identify the key variables influencing power consumption during CT and UVAT. The statistical influence of the cutting depth of cut, feed, and speed on power consumption was evaluated using the F-test. Cutting speed had a significant impact on power consumption under both machining conditions, with a more pronounced effect under UVAT, according to the results of ANOVA. Figure 7 shows the power consumption and tool wear varying with the process parameters under CT and UVAT. Figure 7A depicts varying power consumption and tool wear with the cutting speed and at a feed and depth of cut of 0.085 mm/rev and 0.4 mm, respectively. Both the power consumption and tool wear increased with the cutting speed. However, higher flank wear can be observed under CT than UVAT. On the other hand, no significant difference can be observed in the power consumption varying with the cutting speed under CT and UVAT.
Figure 7. Power consumption (Pm) and tool wear (Vb) vary with the (A) cutting speed, (B) feed, and (C) depth of cut.
Figures 7B,C depict varying power consumption and tool wear with the feed and depth of cut, respectively. Figure 7B is plotted using a cutting speed and depth of cut of 100 m/min and 0.4 mm, respectively. Figure 7C is plotted using a cutting speed and feed of 100 m/min and 0.085 mm/rev, respectively. The power consumption and tool wear increased with the feed and depth of cut. However, a higher flank wear under CT and no significant difference in the power consumption under CT and UVAT varying with the feed and depth of cut can be observed.
In CT, increased cutting speeds substantially boost tool wear because of an increase in the cutting temperature in the contact region. However, a lower tool wear observed with the cutting speed under UVAT could be attributed to intermittent contact between the tool and the workpiece, leading to lower contact region and, hence, the cutting temperature. Lower tool wear was observed under UVAT than that under CT. Figure 8 shows the images of the tool captured at the end of cutting during the turning of AISI 52100 steel (62 HRC) using a PVD-coated TiAlSiN carbide tool under CT and UVAT.
Figure 8. Tool images at the end of cutting for (A) conventional turning (CT) (V: 100 m/min, f = 0.085 mm/rev, and d = 0.5 mm), (B) UVAT (V: 100 m/min, f = 0.085 mm/rev, and d = 0.5 mm), (C) CT (V: 145 m/min, f = 0.085 mm/rev, and d = 0.4 mm), and (D) UVAT (V: 145 m/min, f = 0.085 mm/rev, and d = 0.4 mm).
In summary, lower flank wear under UVAT conditions suggests a promising reduction in tool wear compared to CT. This observation is consistent with the tool and workpiece coming into intermittent contact during UVAT, which reduces the contact region and, as a result, the cutting temperature, and hence, it demonstrates lower flank wear under UVAT than under CT. Comparably, the study findings regarding power consumption show that, although it increased with cutting parameters for both UVAT and CT, there was no discernible difference between the two techniques. This shows that when compared to conventional turning, the application of ultrasonic vibrations did not significantly change the trends in power consumption.
The promising outcomes of UVAT in terms of decreasing tool wear demonstrate the potential of the method to increase tool life and, as a result, machining efficiency and precision. Although ultrasonic vibrations did not significantly change the observed trends in power consumption, they do highlight the need for more research on the precise energy components that are impacted by the ultrasonic-assisted turning process. Future research could examine differences in the frequency and amplitude of vibrations, especially when applied simultaneously and independently in the tangential, feed, and radial directions, to further improve our understanding of ultrasonic vibration effects. Furthermore, given the growing interest in environmentally friendly machining methods, more research on the use of nanofluids under minimum quantity lubrication (NFMQL) during UVAT could lead to more effective and ecologically friendly machining procedures. In short, this study not only offers insightful information about how UVAT performs on hardened AISI 52100 steels but also presents opportunities for further research that can further the field of hard turning, especially regarding tool wear, power consumption, and environmentally friendly machining techniques.
This investigation delved into the machinability of hardened AISI 52100 steel (62–63 HRC) using a PVD-coated TiAlSiN carbide tool under CT and UVAT), incorporating a thorough exploration of varying cutting parameters. The study draws the following key conclusions, each offering valuable insights into the practical applications of the findings in real-world machining scenarios and their broader implications for the manufacturing field:
1) Promising results with UVAT: The application of ultrasonic vibration during hard turning demonstrated encouraging results, showcasing the potential of UVAT to enhance the machining of AISI 52100 steel (62 HRC) using a PVD-coated TiAlSiN carbide tool. These findings hold significant promise for improving the efficiency and effectiveness of machining processes.
2) Influence of cutting parameters on wear and power consumption: Notably, the investigation revealed a direct correlation between tool wear, power consumption, and the cutting parameters. While both tool wear and power consumption increased with cutting parameters, the pivotal influence of specific factors emerged. The cutting speed prominently affected tool wear, while power consumption was notably influenced by the depth of cut, followed by the cutting speed and feed. This nuanced understanding allows for informed decision-making under optimizing machining conditions for obtaining desired outcomes.
3) Comparison of flank wear under CT and UVAT: The substantial reduction in flank wear observed under UVAT compared to CT underscores the practical advantage of incorporating ultrasonic vibrations. This suggests an improved tool life and enhanced machining precision under UVAT conditions, providing tangible benefits in real-world manufacturing scenarios.
4) Reliability of mathematical models and predictive capabilities: To validate the encouraging results obtained using UVAT) in the hard turning of AISI 52100 steel (62 HRC) using a PVD-coated TiAlSiN carbide tool, rigorous comparison and analysis were conducted. The robust correlation coefficients (R-squared values exceeding 0.9) for the developed mathematical models attest to their reliability in predicting both power consumption and tool wear under CT and UVAT conditions. This reliability enhances the practical utility of the models, offering manufacturers a valuable tool for optimizing machining processes and resource utilization.
5) Scope for further research and technological advancements: The identification of potential areas for further research, specifically exploring the simultaneous and indigenous application of ultrasonic vibrations in various directions and investigating NFMQL, opens avenues for technological advancements. These avenues, when explored, can contribute to refining existing machining techniques and developing environmentally sustainable practices in manufacturing.
In conclusion, the findings of this study extend beyond the laboratory setting, carrying implications for real-world manufacturing scenarios. By emphasizing the practical benefits of UVAT, recognizing the influence of cutting parameters, and providing a reliable predictive framework, this research contributes to the ongoing evolution of machining practices, aligning with the dynamic needs of the manufacturing industry.
The original contributions presented in the study are included in the article/Supplementary Material; further inquiries can be directed to the corresponding author.
GG: conceptualization and writing–original draft. SS: resources, supervision, validation, and writing–review and editing. SC: formal analysis, investigation, methodology, and writing–review and editing. RC: supervision, validation, and writing–review and editing. AK: investigation, supervision, and writing–review and editing. SB: supervision and writing–review and editing. RK: validation and writing–review and editing. FA: writing–review and editing, formal analysis, visualization.
The author(s) declare that no financial support was received for the research, authorship, and/or publication of this article.
The authors declare that the research was conducted in the absence of any commercial or financial relationships that could be construed as a potential conflict of interest.
All claims expressed in this article are solely those of the authors and do not necessarily represent those of their affiliated organizations, or those of the publisher, the editors, and the reviewers. Any product that may be evaluated in this article, or claim that may be made by its manufacturer, is not guaranteed or endorsed by the publisher.
Airao, J., Nirala, C. K., Noberto Lopez de Lacalle, L., and Khanna, N. (2021). Tool wear analysis during ultrasonic assisted turning of nimonic-90 under dry and wet conditions. Metals 11 (8), 1253. doi:10.3390/met11081253
Alper Sofuoglu, M., Cemal Kushan, M., and Orak, S. (2021). Hot ultrasonic assisted machining modelling of Ti6Al4V in terms of power consumption. J. Adv. Manuf. Eng. 2 (2), 33–41. doi:10.14744/ytu.jame.2021.00006
Dodla, S. (2022). Experimental investigations of tool wear in vibration-assisted turning of Inconel 718. Archives Metallurgy Mater. 3, 949–953. doi:10.24425/amm.2022.139687
Duman, E., Furkan Yapan, Y., Salvi, H., Alper Sofuoglu, M., Khanna, N., and Uysal, A. (2024). Investigation of ultrasonic vibration assisted orthogonal turning under dry and minimum quantity lubrication conditions and performing sustainability analyses. J. Clean. Prod. 434, 140187. doi:10.1016/j.jclepro.2023.140187
Ezugwu, E. O., and Wang, Z. M. (1997). Titanium alloys and their machinability - a review. J. Mater. Process. Technol. 68 (3), 262–274. doi:10.1016/S0924-0136(96)00030-1
Florez Garcia, L. C., HernanRojas, A. G., and AntonioSanchez Egea, J. (2020). Estimation of specific cutting energy in an S235 alloy for multi-directional ultrasonic vibration-assisted machining using the finite element method. Materials 13 (3), Article no. 567. doi:10.3390/ma13030567
Ghule, G. S., and Sanap, S. (2021). Ultrasonic vibrations assisted turning (UAT): a review. Adv. Eng. Des. Lect. Notes Mech. Eng., 275–285. doi:10.1007/978-981-33-4684-0_28
Ghule, G. S., Sanap, S., Adsul, S., Chinchanikar, S., and Gadge, M. (2022). Experimental investigations on the ultrasonic vibration-assisted hard turning of AISI 52100 Steel using coated carbide tool. Mater. Proc. 68, 2093–2098. doi:10.1016/j.matpr.2022.08.368
Guo, Y. B., and Liu, C. R. (2002). Mechanical properties of hardened AISI 52100 steel in hard machining processes. J. Manuf. Sci. Eng. 124 (1), 1–9. doi:10.1115/1.1413775
Habtamu, A., Ghosh, S., and Rao, P. V. (2017). Experimental study on machinability of Inconel 718 using ultrasonic vibration assisted turning. Proc. 10th Int. Conf. Precis. Meso, Micro Nano Eng. COPEN 10, 583–586.
Jiao, F., Liu, X., Zhao, C. Y., and Zhang, X. (2011). Experimental study on the surface micro-geometrical characteristics of quenched steel in ultrasonic assisted turning. Adv. Mater. Res. 189-193, 4059–4063. doi:10.4028/www.scientific.net/AMR.189-193.4059
Kandi, R., Sahoo, S. K., and Sahoo, A. K. (2020). Ultrasonic vibration-assisted turning of Titanium alloy Ti–6Al–4V: numerical and experimental investigations. J. Braz. Soc. Mech. Sci. Eng. 42, 399. doi:10.1007/s40430-020-02481-5
Koshimizu, S. (2009). Ultrasonic vibration-assisted cutting of titanium alloy. Key Eng. Mater. 389-390, 277–282. doi:10.4028/www.scientific.net/KEM.389-390.277
Kumar, A., and Gulati, V. (2018). Experimental investigations and optimization of forming force in incremental sheet forming. Sādhanā 43, 159. doi:10.1007/s12046-018-0926-7
Kumar, A., and Gulati, V. (2019). Experimental investigation and optimization of surface roughness in negative incremental forming. Measurement 131, 419–430. doi:10.1016/j.measurement.2018.08.078
Kumar, A., and Gulati, V. (2021). Optimization and investigation of process parameters in single point incremental forming. Indian J. Eng. Mater. Sci. (IJEMS) 27 (2), 246–255. doi:10.56042/ijems.v27i2.45925
Kumar, A., Jee Mishra, G., Gulati, V., Srivastava, A. K., Kumar, P., Kumar, V., et al. (2024b). Correction to: a comprehensive review on heat-assisted incremental sheet forming. Int. J. Interact. Des. Manuf. doi:10.1007/s12008-024-01734-0
Kumar, A., Kumar, P., Mittal, R. K., and Gambhir, V. (2023). Materials processed by additive manufacturing techniques. Adv. Addit. Manuf., 217–233. doi:10.1016/B978-0-323-91834-3.00014-4
Kumar, A., Kumar, P., Sharma, N., and Srivastava, A. K. (2024c). 3D printing technologies: digital manufacturing, artificial intelligence, Industry 4.0. Berlin, Boston: De Gruyter. doi:10.1515/9783111215112
Kumar, A., Shrivastava, V. K., Kumar, P., Kumar, A., and Gulati, V. (2024a). Predictive and experimental analysis of forces in die-less forming using artificial intelligence techniques. Proc. Institution Mech. Eng. Part E J. Process Mech. Eng. 0 (0). doi:10.1177/09544089241235473
Maurotto, A., Roy, A., Babitsky, V. I., and Silberschmidt, V. V., “Recent developments in ultrasonically assisted machining of advanced alloys”, Proceedings of 4th CIRP International Conference on High Performance Cutting, 2010.
Mitrofanov, A. V., Babitsky, V. I., and Silberschmidt, V. V. (2003). Finite element simulations of ultrasonically assisted turning. Comput. Mater. Sci. 28, 645–653. doi:10.1016/j.commatsci.2003.08.020
Patel, T., Yadav, S., Raj, Z., Shah, P., and Khanna, N. (2020). Analysis of machining performance of AISI 420 stainless steel using conventional and ultrasonic assisted turning. Mater. Today Proc. 26, 2200–2207. doi:10.1016/j.matpr.2020.02.478
Patil, S., Joshi, S., Tewari, A., and SuhasJoshi, S. (2014). Modelling and simulation of effect of ultrasonic vibrations on machining of Ti6Al4V. Ultrasonics 54 (2), 694–705. doi:10.1016/j.ultras.2013.09.010
Razavi, H., Nategh, M. J., and Abdullah, A. (2012). Analytical modeling and experimental investigation of ultrasonic vibration-assisted oblique turning, part III: experimental investigation. Int. J. Mech. Sci. 63, 26–36. doi:10.1016/j.ijmecsci.2012.06.007
Srivastava, A. K., Kumar, A., Kumar, P., Gautam, P., and Dogra, N. (2023). Research progress in metal additive manufacturing: challenges and opportunities. Int. J. Interact. Des. Manuf. doi:10.1007/s12008-023-01661-6
Valera, H. Y., and Bhavsar, S. N. (2014). Experimental investigation of surface roughness and power consumption in turning operation of EN 31 alloy steel. Procedia Technol. 14, 528–534. doi:10.1016/j.protcy.2014.08.067
Vivekananda, K., Arka, G. N., and Sahoo, S. K. (2014). Design and analysis of ultrasonic vibratory tool (UVT) using FEM, and experimental study on ultrasonic vibration-assisted turning (UAT). Procedia Eng. 97, 1178–1186. doi:10.1016/j.proeng.2014.12.396
Xu, Y., Gao, F., Zou, P., Zhang, Q., and Fan, F. (2020). Theoretical and experimental investigations of surface roughness, surface topography, and chip shape in ultrasonic vibration-assisted turning of Inconel 718. J. Mech. Sci. Technol. 34 (9), 3791–3806. doi:10.1007/s12206-020-0830-x
Zhou, M., Eow, Y. T., Ngoi, B. K. A., and Lim, E. N. (2003). Vibration-assisted precision machining of steel with PCD tools. Mater. Manuf. Process. 18 (5), 825–834. doi:10.1081/AMP-120024978
Keywords: turning, manufacturing process, ultrasonic vibrations, AISI 52100, tool wear, power consumption, materials
Citation: Ghule GS, Sanap S, Chinchanikar S, Cep R, Kumar A, Bhave SY, Kumar R and Altarazi F (2024) Investigation of conventional and ultrasonic vibration-assisted turning of hardened steel using a coated carbide tool. Front. Mech. Eng 10:1391315. doi: 10.3389/fmech.2024.1391315
Received: 25 February 2024; Accepted: 12 March 2024;
Published: 04 April 2024.
Edited by:
Kanak Kalita, Vel Tech Dr. RR and Dr. SR Technical University, IndiaReviewed by:
Ashwini Kumar, Manav Rachna International Institute of Research and Studies (MRIIRS), IndiaCopyright © 2024 Ghule, Sanap, Chinchanikar, Cep, Kumar, Bhave, Kumar and Altarazi. This is an open-access article distributed under the terms of the Creative Commons Attribution License (CC BY). The use, distribution or reproduction in other forums is permitted, provided the original author(s) and the copyright owner(s) are credited and that the original publication in this journal is cited, in accordance with accepted academic practice. No use, distribution or reproduction is permitted which does not comply with these terms.
*Correspondence: Ajay Kumar, YWpheS5rdW1hcjMwODg2QGdtYWlsLmNvbQ==
†ORCID: Ajay Kumar, orcid.org/0000-0001-7306-1902
Disclaimer: All claims expressed in this article are solely those of the authors and do not necessarily represent those of their affiliated organizations, or those of the publisher, the editors and the reviewers. Any product that may be evaluated in this article or claim that may be made by its manufacturer is not guaranteed or endorsed by the publisher.
Research integrity at Frontiers
Learn more about the work of our research integrity team to safeguard the quality of each article we publish.