- 1Department of Mechanical Engineering, Sikkim Manipal Institute of Technology, Sikkim Manipal University, Gangtok, India
- 2Department of Mechanical and Industrial Engineering, Manipal Institute of Technology, Manipal Academy of Higher Education, Manipal, India
- 3Department of Machining, Assembly and Engineering Metrology, Faculty of Mechanical Engineering, VSB-Technical University of Ostrava, Ostrava, Czechia
- 4Department of Mechanical Engineering, Sri Sairam Institute of Technology, Chennai, India
- 5Department of Mechanical Engineering and University Centre for Research and Development, Chandigarh University, Mohali, India
- 6Department of Mechanical Engineering, Vel Tech Rangarajan Dr. Sagunthala R&D Institute of Science and Technology, Avadi, India
Non-Traditional Machining (NTM) outperforms traditional processes by offering superior geometric and dimensional accuracy, along with a better surface finish. Photo Chemical Machining (PCM) represents one such NTM process, using chemical etching for material removal. PCM finds substantial application in the creation of microchannels in pharmaceutical, chemical and energy industries. Several input parameters—such as etchant concentration, etching time and etchant temperature—profoundly influence the machining’s quality and efficiency. Therefore, the optimization of these parameters is crucial. This study presents a comparative analysis of five Multiple Criteria Decision Making (MCDM) techniques—Technique for Order of Preference by Similarity to Ideal Solution (TOPSIS), Multi-Objective Optimization on the basis of Ratio Analysis (MOORA), Additive Ratio Assessment (ARAS), Weighted aggregated sum product assessment method (WASPAS) and Multi-Attributive Border Approximation Area Comparison Method (MABAC)—for the optimization of the PCM process. Key performance metrics considered are Material Removal Rate (
1 Introduction
As the demand for superior dimensional and geometric accuracy rises, various non-traditional machining processes are gaining industrial prominence. The manufacturing of microfluidic devices in pharmaceutical and biotechnological industries necessitates exceptional dimensional accuracies, achievable only through a select few non-traditional machining processes (Wangikar et al., 2019). One such process is Photo-Chemical Machining (PCM), which employs photochemical etching for material removal, enabling the machining of intricate shapes with high dimensional accuracy. PCM leverages highly accelerated yet controlled corrosion to remove material from the bulk (Wangikar et al., 2017).
Recently, PCM has garnered significant interest from the scientific community due to its advantages, such as high dimensional accuracy, negligible residual stress and improved surface finish. Agrawal et al. (Agrawal et al., 2021) utilized PCM to machine SS-430 and conducted parametric optimization using Taguchi-Grey Relation Analysis to identify optimum process parameters. Their findings indicated that a lower concentration of etchant combined with high temperature and etching time yielded optimum results. Misal et al. (Misal et al., 2017) employed ferric chloride as an etchant to machine Inconel 718 using the PCM process, observing that the etchant’s temperature and etching time significantly influenced surface roughness.
Given PCM’s diverse applications, it is crucial to select optimum process parameters directly impacting machining quality. Multi-Criteria Decision Making (MCDM) techniques are widely used in various fields of study for process parameter optimization. Das and Chakraborty (Das and Chakraborty, 2022) applied a Grey Correlation-based EDAS technique for PCM, Laser-Assisted Jet Electro-Chemical Machining and Abrasive Water Jet Drilling process optimization. They accurately predicted optimum process parameters and confirmed these using regression equations. Chakraborty et al. (Chakraborty et al., 2020) used the Multi-Attributive Border Approximation Area Comparison Method (MABAC) approach to select the best non-traditional machining process. They successfully tested the method’s validity through two different scenarios, concluding that rough numbers could be effectively used with the MABAC technique for MCDM problems. Deosant et al. (Deosant et al., 2021) integrated the AHP with the Technique for Order of Preference by Similarity to Ideal Solution (TOPSIS) method to select suitable non-traditional micro-machining processes. Their study highlighted electrical discharge machining as the most effective technique among the various techniques considered.
Kalita et al. (Kalita et al., 2022) conducted a comparative study of various MCDM techniques for milling process optimization. They used entropy weight calculation with six MCDM techniques and compared the ranks obtained, suggesting that objective weight calculation performs better with robust data. Shanmugasundar et al. (Shanmugasundar et al., 2022) utilized Method Based on the Removal Effects of Criteria (MEREC) weight calculation with various MCDM techniques for industrial robot selection, presenting a comparative study among various MCDM techniques to identify the drawbacks and advantages of the techniques used. Kumari and Acherjee (Kumari and Acherjee, 2022) applied a Criterion-Induced Aggregation Technique (CRITIC)—COmbinative Distance-based ASsessment (CODAS)-based technique to select the best non-conventional machining process among eight processes based on six different criteria. Their method’s comparison with established methods demonstrated good performance. Pathapalli et al. (Pathapalli et al., 2020) developed an aluminium composite using the stir casting process and optimized turning process parameters using Multi-Objective Optimization on the basis of Ratio Analysis (MOORA) and weighted aggregated sum product assessment method (WASPAS) techniques. A comparative study revealed that both techniques work well for turning parameter optimization. Goswami et al. (Goswami et al., 2021) used an Additive Ratio Assessment (ARAS)-TOPSIS hybrid MCDM technique for robot selection among twelve industrial robots based on five contrasting criteria, suggesting that objective weight determination techniques are free from decision-maker biases and, thus, superior to subjective methods.
From the aforementioned literature, it is clear that MCDM techniques are widely used for selecting optimum process parameters in multi-objective problems. Although these techniques have been extensively applied across various domains, the optimization of PCM process parameters using MCDM techniques remains underexplored. Moreover, a comparative study of various MCDM techniques in the PCM process using objective weight determination methods has yet to be conducted. The current study attempts to bridge this gap by comparing five MCDM techniques—TOPSIS, MOORA, ARAS, WASPAS, and MABAC—using four different objective weight determination techniques namely, CRITIC, MEREC, Entropy along with equal weights to optimize PCM process parameters. Additionally, a correlation analysis is presented to elucidate the similarities and differences between the techniques employed.
2 Materials and methods
2.1 Experimental procedure
The experimental data for this study were derived from Agarwal and Kamble (Agrawal and Kamble, 2019). Stainless Steel-304 (SS-304) was selected as the substrate material for the PCM process. The etchant was prepared by dissolving ferric chloride in water, with precise weighing of ferric chloride to ensure the desired concentration. Prior to the application of the photoresist coating, the specimen was thoroughly cleaned with acetone and water. The coated material and phototool were then exposed to UV light. The portions not covered by the phototool and exposed to UV light remained unetched post-machining.
Agarwal and Kamble (Agrawal and Kamble, 2019) identified three input variables that were of prime significance following an extensive literature survey. These three input parameters: concentration of etchant, etching time and temperature of the etchant were varied between three levels to conduct 27 experimental runs based on Taguchi orthogonal array experimental design. Concentration of etchant was measured in gm/ltrs and denotes the strength of etchant, etching time was measured in minutes and denotes the time for which the material was exposed to the etchant. Etchant was also used in an elevated temperature to expedite the process of chemical etching and the temperature was measured in °C. Three levels of all these factors are presented in Table A1. The Material Removal Rate (
2.2 Multi criteria decision making
Five MCDM techniques namely, TOPSIS, MOORA, ARAS, WASPAS, and MABAC methods were used to identify the compromise optimum values of responses variables. Weight of the response variables were calculated using CRITIC, MEREC and Entropy methods and a comparison was made with the case when equal weights are assigned to all criteria. All the MCDM techniques used in the current work are discussed in detail in the following sections. It should be noted here that for all the methods discussed, in an MCDM problem having
2.2.1 CRITIC weight calculation
CRITIC was proposed by Diakoulaki et al. (Diakoulaki et al., 1995) in 1995 as an objective weight determination method. The primary advantage of objective weighting method is that it omits any preferences that the decision maker might have with respect to any criteria. The internal contrasts within a criterion and conflict intensity between criteria are assessed to assign weights to them using CRITIC method. Steps involved in CRITIC method are as follows:
Step 1:. Formulation of the decision matrix.
Step 2:. Decision matrix is normalized using Eq. 1,
Step 3:. Pearson Correlation Coefficient is used to determine the degree of correlation. It is calculated using Eq. 2
Step 4:. Weights of the criteria is calculated using Eqs 3, 4,
2.2.2 MEREC weight calculation
MEREC is a weight evaluation method developed in 2019 by Ghorabaee et al. (Keshavarz-Ghorabaee et al., 2021) to assess weights based on deviation of performance ratings on removal of a criteria. The weights reflect the effect it has on performance rating if the criteria were omitted from the decision-making process. The procedural steps involved in this method are as follows.
Step 1:. A normalized decision matrix
Step 2:. An index
Step 3:. Similarly, an index
Step 4:. Absolute deviation D is calculated by subtracting one performance rating with other. Absolute value of the difference is taken as the deviation. It can be mathematically represented as in Eq. 8,
Step 5:. Weights of each alternative is calculated using Eq. 9,
2.2.3 Entropy weight calculation
Entropy weights was adopted into MCDM problems from the concept of Shannon entropy developed by Shannon in 1948 as a concept in probabilities. This method works on the premise that the higher weight should be assigned to the criteria that carries the maximum information in a decision-making process. The procedural steps involved in this method are as follows:
Step 1:. The decision matrix is normalized using Eq. 10,
Step 2:. Entropy is then calculated as in Eq. 11,
Step 3:. The weight from the Entropy value is calculated using Eq. 12,
where
2.2.4 Technique for order of preference by similarity to ideal solution (TOPSIS)
TOPSIS was initially presented by Yoon and Hwang (Yoon and Hwang, 1981) in 1981 and is among the most popular MCDM technique that has been applied in various areas of study. Distance from the ideal best and ideal worst solution in the Euclidean scale is used to identify the best alternative in this method. Steps involved in TOPSIS method are presented below:
Step 1:. Decision matrix is normalized using Eq. 13,
Step 2:. Weighted normalized matrix is calculated by multiplying the normalized decision matrix by their corresponding criteria weights using Eq. 14.
Step 3:. Euclidean distances from the ideal best and ideal worst solutions are calculated using Eqs 15, 16,
Step 4:. Closeness coefficient is calculated using Eq. 17 and the alternatives are ranked based on
2.2.5 Multi-objective optimization on the basis of ratio analysis method (MOORA)
MOORA was used by Chakraborty (Chakraborty, 2011) to solve decision making problem for various applications in different manufacturing environments. Brauers et al. (Brauers et al., 2008) compared various ratios and suggested that the best choice as denominator is the square root of sum of squares which is considered in MOORA. The steps involved in MOORA is same as TOPSIS until the weighted normalized decision matrix is obtained. The steps after that are as follows
Step 1:. After obtaining the weighted normalized decision matrix following Step 1 and Step 2 of TOPSIS, performance score is calculated as
where criteria 1 to criteria “g” are the beneficial criteria
Step 2:. Rank the criteria based on performance score in descending order. The highest performance score will be ranked first.
2.2.6 Additive ratio assessment (ARAS)
ARAS method was presented by Zavadskas and Turskis (Zavadskas and Turskis, 2010) in the year 2010 as an MCDM technique that is simple and effective. ARAS method assumes that the effectiveness of an alternative is directly proportional to performance value under a criteria and weight of the criteria. This is the underlying principle behind the working of this technique. The steps in the ARAS method are as follows-
Step 1:. Normalization of the decision matrix is done using one of the two equations depending on whether the criteria is beneficial or cost
Step 2:. Weighted normalized decision matrix is calculated using Eq. 21,
Step 3:. Optimality function is calculated as follows
Step 4:. Degree of utility is computed using Eq. 23 and alternatives are ranked in the descending order of the obtained value.
2.2.7 Weighted aggregated sum product assessment method
WASPAS method was suggested by Zavadskas et al. (Zavadskas et al., 2012) in 2012 as a hybrid MCDM technique that combined two pre-existing techniques. The accuracy of WASPAS was seen to be better than its parent techniques (Zavadskas and Turskis, 2010). Combined effect of weighted sum and product is calculated and the final index is used to rank the alternatives in this method. The steps involved in this method are discussed below:
Step 1:. Normalization of the decision matrix is done using Eqs 24, 25,
Step 2:. Relative importance of alternative using the sum approach is calculated as follows
Step 3:. Relative importance of alternative using the product approach is also calculated using the following equation
Step 4:. Combined importance of alternatives is calculated using the following Eq. 28,
α is the factor that decides the weightage of each index. It is chosen as 0.5 commonly.
2.2.8 Multi-attributive border approximation area comparison method
MABAC method was proposed by Pamucar and Cirovic (Pamučar and Ćirović, 2015) in 2015 to solve MCDM problems and the comparison with few other MCDM techniques was also presented to validate the accuracy and consistency of the method. It works by calculating the distance of normalized performance values from the border approximation area (BAA). The alternatives with greater value of BAA is the better alternative using this method. The steps involved in ranking of alternatives using MABAC method are presented as under
Step 1:. Elements of normalized decision matrix is computed from the decision matrix using the following Eq. 29,
Step 2:. Weighted normalized matrix is calculated from the normalized decision matrix using the formula presented below in Eq. 30
Step 3:. BAA matrix
Step 4:. Distance from this BAA is calculated for all the alternatives using Eq. 32,
Step 5:. Ranking of the alternatives is done using the overall score computed as
Ranking is done in the descending order of
3 Results and discussion
The response values for
3.1 MCDM results
3.1.1 Weight determination
In the current work, criteria weight determination for all the MCDM techniques considered is done using four objective weight allocation methods. The steps involved in all the weight determination strategies is elucidated in earlier section. The discussed process has been religiously followed to calculate weights of various criteria in the selected MCDM problem. Weights of all the criteria obtained is presented in Table 1. It is worth noting here that while MEREC is heavily skewed in favor of surface roughness, other methods allocate weights to all criteria in close proximity with each other.
3.1.2 TOPSIS
Weights of all criterion obtained using the four weight allocation methods was used to obtain weighted normalized matrix using Eq. 14 after the normalized matrix is obtained using Eq. 13 discussed in Section 2.2.2. The distances from positive ideal and negative ideal solutions are calculated using Eqs 15, 16 respectively. Figure 1 shows the Euclidean distance from the best and the worst ideal solution. Selection of best alternative is based on the fact that the best alternative is the one that is the closest to the positive ideal but the farthest from the negative ideal point. Closeness coefficient measures how far the solution is from the ideal worst and how near a solution is to the ideal best. Ranks obtained using TOPSIS is presented in Table 2. It can be observed from Table 2 that alternative 15 can reliable be considered to be the optimal solution to the current MCDM problem which is ranked best by two of the methods and second best by the remaining two. Similarly, experiment 18 and experiment 5 are among the worst performing alternatives by TOPSIS among the 27 experiments considered.
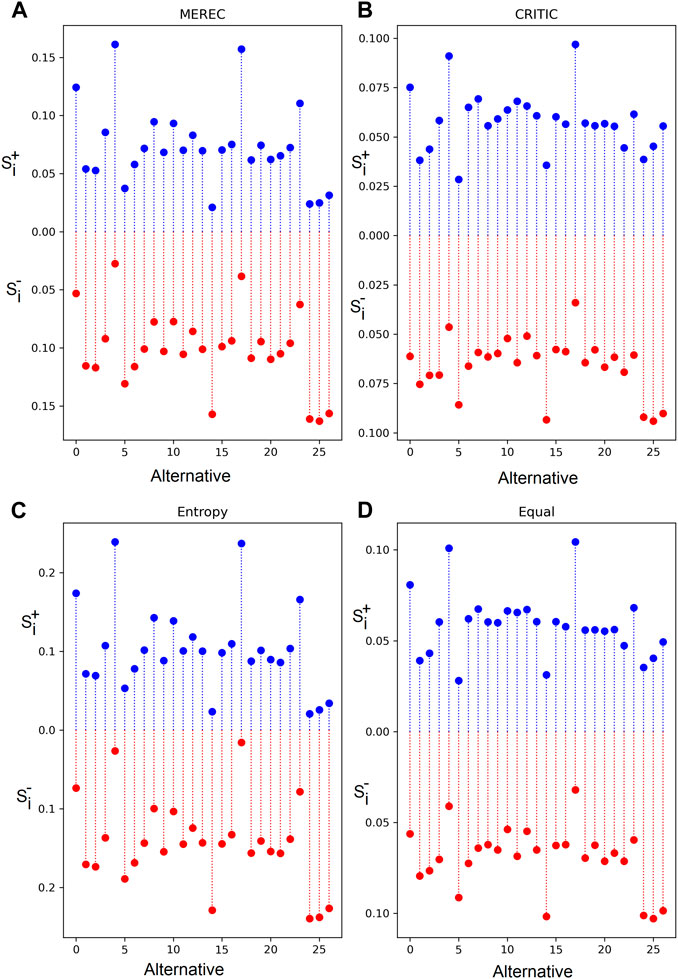
FIGURE 1. Plot of Euclidean distance versus alternatives for weights calculated by (A) MEREC, (B) CRITIC, (C) Entropy and (D) Equal weights.
3.1.3 MOORA
Decision matrix was normalized using Eq. 13 and weight obtained using all the methods considered were multiplied according to Eq. 14 to obtain weighted normalized decision matrix for MOORA method. Following Eq. 18, weighted normalized performance values under MRR and EF are added together and the sum of weighted normalized performance values for SR and Uc is subtracted from it to calculate the performance score. This score is used to rank the alternatives as shown in Table 3. Experiment 25 is ranked as the best alternative in two of the four weights considered. Experiment 3 and 4 and also among the better performing alternatives that are ranked first by the other two methods. Experiment 1 is again suggested to be the worst alternative among the 27 experiments.
3.1.4 ARAS
For ARAS method, a different normalization procedure is followed using Eq. 19 for MRR and EF and Eq. 20 for SR and Uc. Normalized decision matrix is multiplied with the weight of each criteria following Eqs 21, 22 based on the nature of criteria to obtain weighted normalized decision matrix. Sum of performance values under all the criteria is calculated following Eq. 23 to calculate the optimality function for an alternative. Degree of utility is calculated using Eq. 24 and the alternatives are ranked in the descending order of degree of utility as shown in Table 4. ARAS suggests that the experiment 25 is the best alternative followed by experiment 26. The worst alternative suggested by ARAS is experiment number 13.
3.1.5 WASPAS
WASPAS method is also used to identify the best alternative among the 27 experimental runs. Normalization of the decision matrix is done using Eqs 24, 25 depending on the type of criteria. Performance index for weighted aggregate sum and weighted aggregate product are calculated using Eqs 26, 27 respectively. The value of α is taken as 0.5 for the present work. The aggregate performance score is calculated using Eq. 28 and alternatives are ranked based on the score. Stepwise rank calculation is shown in Table 5 below. Experiments 25 and 26 are selected as the best and the second-best alternatives using WASPAS method. Experiment 18 is suggested to be the worst experiment by WASPAS method.
3.1.6 MABAC
In MABAC method, initial decision matrix is normalized using Eq. 21. It should be noted here that the best performance value for beneficial criteria is the maximum value while for the cost criteria it is the minimum value. Vice versa is true for worst value. For the weighted normalized matrix, Eq. 22 is used as mentioned in Section 2.2.6. BAA matrix G is then calculated using Eq. 23. Distance from this BAA matrix is calculated for all the alternatives under each criteria using Eq. 24. Eq. 25 is used to convert the Q matrix to a single performance score for each alternative. Ranks obtained using this score is tabulated in Table 6 below. It can be observed that MABAC chooses 6th experiment as the best alternative using CRITIC and equal weights are used while the 15th experiment is chosen as the best alternative when other two weights are used. 18th Experiment is chosen as the worst alternative by MABAC for most weights.
3.2 Comparative study
Figure 2 shows the plot of ranks obtained by different MCDM techniques. It can be clearly observed that the experiments no. 15 and 26 are ranked among the best four alternatives. Similarly experiment 10 and 13 are also ranked among the worst performing alternatives by all the techniques considered. It can be seen that ARAS and MOORA have significant overlap and TOPSIS, WASPAS and MABAC have significant overlap among each other for all the weights that were considered. Weights seem to play very little role as the overlap among the weights considered is significantly high for TOPSIS, WASPAS and MABAC. However, for ARAS and MOORA, the overlap among the weights considered and with other MCDM techniques considered seems very low.
Correlation analysis was also done to check the overlap between the ranks obtained by the MCDM techniques considered. Spearman rank correlation coefficient is selected as the measure for correlation between ranks in the current work (Figure 3). The most significant observation is that selection of appropriate weights is crucial to enhance the reliability of MCDM results as the correlation can be seen changing among MCDM techniques when weight allocation methods are different. While TOPSIS, WASPAS, and MABAC are quite similar, the differences in the approaches towards decision making might be the reason behind low correlation coefficient between ARAS and TOPSIS or ARAS and MOORA. Correlation coefficients also reflect that ARAS and MOORA are very closely related with each other.
4 Conclusion
This work compares TOPSIS, MOORA, ARAS, WASPAS, and MABAC using four different objectiive weight determination process, focusing on the widely used machining technique for crafting intricate shapes in microfluidic devices, specifically, the PCM process. A 27-alternative 4-criteria MCDM problem was constructed using an L27 Taguchi experimental design array and four response parameters: MRR, SR, Uc, and EF. The 15th, 25th, 26th, and 27th experimental runs emerged as better performing alternatives across all the MCDM techniques utilized in this study.
Correlation analysis between the techniques reveals that the ranks obtained using ARAS and MOORA closely correlate, while those obtained using TOPSIS, WASPAS and MABAC show close correlation among each other. There is a division between these two groups of MCDM techniques, which may be due to the normalization procedure followed in the processes. While TOPSIS, WASPAS and MABAC use the same approach to select the best alternative irrespective of the criteria’s nature post-normalization, ARAS and MOORA distinguish between the benefit and cost criteria in the process of selecting the best alternative. This study’s primary contribution is to elucidate this difference clearly using the example of PCM process parameters optimization.
The impact of the weight determination technique has also been studied. The most significant result in the comparison of weights is that the correlation among MCDM techniques is hugely dependent on the weight determination technique used. Therefore, weights play a significant role in reliability of MCDM tools and a careful selection of weight allocation technique is paramount in interpreting MCDM results. This work, however does not implement new age mathematical tools like fuzzy sets, soft sets and rough sets which can be integrated with the existing MCDM techniques to enhance their robustness in application.
Data availability statement
The raw data supporting the conclusion of this article will be made available by the authors, without undue reservation.
Author contributions
GS: Data curation, Formal Analysis, Investigation, Validation, Writing–original draft. RG: Writing–original draft, Writing–review and editing, Methodology. RČ: Conceptualization, Funding acquisition, Methodology, Supervision, Writing–review and editing. GS: Conceptualization, Formal Analysis, Methodology, Validation, Writing–review and editing. JSC: Formal Analysis, Investigation, Methodology, Writing–review and editing. KK: Conceptualization, Methodology, Software, Visualization, Writing–review and editing.
Funding
The author(s) declare that no financial support was received for the research, authorship, and/or publication of this article.
Conflict of interest
The authors declare that the research was conducted in the absence of any commercial or financial relationships that could be construed as a potential conflict of interest.
The author(s) declared that they were an editorial board member of Frontiers, at the time of submission. This had no impact on the peer review process and the final decision.
Publisher’s note
All claims expressed in this article are solely those of the authors and do not necessarily represent those of their affiliated organizations, or those of the publisher, the editors and the reviewers. Any product that may be evaluated in this article, or claim that may be made by its manufacturer, is not guaranteed or endorsed by the publisher.
References
Agrawal, D., and Kamble, D. (2019). Optimization of photochemical machining process parameters for manufacturing microfluidic channel. Mater. Manuf. process. 34, 1–7. doi:10.1080/10426914.2018.1512115
Agrawal, D., Kamble, D., and Ambhore, N. (2021). Parametric investigation of photochemical machining of SS- 430 for manufacturing of micromesh. Adv. Eng. Forum 43, 1–16. doi:10.4028/www.scientific.net/AEF.43.1
Brauers, W. K. M., Zavadskas, E. K., Peldschus, F., and Turskis, Z. (2008). “Multi-objective optimization of road design alternatives with an application of the MOORA method,” in The 25th International Symposium on Automation and Robotics in Construction ISARC-2008 , Vilnius, Lithuania, June 26–29, 2008. Editor E. K. Zavadskas, A. Kaklauskas, and M. J. Skibniewski (Vilnius: Technika Selected papers), 541–548 . doi:10.3846/isarc.20080626.541
Chakraborty, S. (2011). Applications of the MOORA method for decision making in manufacturing environment. Int. J. Adv. Manuf. Technol. 54, 1155–1166. doi:10.1007/s00170-010-2972-0
Chakraborty, S., Dandge, S. S., and Agarwal, S. (2020). Non-traditional machining processes selection and evaluation: a rough multi-attributive border approximation area comparison approach. Comput. Ind. Eng. 139, 106201. doi:10.1016/j.cie.2019.106201
Das, P. P., and Chakraborty, S. (2022). Application of Grey correlation-based EDAS method for parametric optimization of non-traditional machining processes. Sci. Iran. 29, 0–882. doi:10.24200/sci.2020.53943.3499
Deosant, P. V., Lande, A. R., Vishwakarma, A. G., and Jawale, H. P. (2021). “AHP integrated TOPSIS methodology for selection of non-conventional machining process for micro-drilling,” in Advances in industrial machines and mechanisms (Singapore: Springer), 489–499. doi:10.1007/978-981-16-1769-0_44
Diakoulaki, D., Mavrotas, G., and Papayannakis, L. (1995). Determining objective weights in Multiple criteria problems: the critic method. Comput. Oper. Res. 22, 763–770. doi:10.1016/0305-0548(94)00059-H
Goswami, S. S., Behera, D. K., Afzal, A., Razak Kaladgi, A., Khan, S. A., Rajendran, P., et al. (2021). Analysis of a robot selection problem using two newly developed hybrid MCDM models of TOPSIS-ARAS and COPRAS-ARAS. Symmetry 13, 1331. doi:10.3390/sym13081331
Kalita, K., Madhu, S., Ramachandran, M., Chakraborty, S., and Ghadai, R. K. (2022). Experimental investigation and parametric optimization of a milling process using multi-criteria decision making methods: a comparative analysis. Int. J. Interact. Des. Manuf. (IJIDeM) 17, 453–467. doi:10.1007/s12008-022-00973-3
Keshavarz-Ghorabaee, M., Amiri, M., Zavadskas, E. K., Turskis, Z., and Antucheviciene, J. (2021). Determination of objective weights using a new method based on the removal effects of criteria (MEREC). Symmetry 13 (4), 525. doi:10.3390/sym13040525
Kumari, A., and Acherjee, B. (2022). Selection of non-conventional machining process using CRITIC-CODAS method. Mater. Today Proc. 56, 66–71. doi:10.1016/j.matpr.2021.12.152
Misal, N. D., Saraf, A. R., and Sadaiah, M. (2017). Experimental investigation of surface topography in photochemical machining of Inconel 718. Mater. Manuf. process. 32, 1756–1763. doi:10.1080/10426914.2017.1317786
Pamučar, D., and Ćirović, G. (2015). The selection of transport and handling resources in logistics centers using multi-attributive border approximation area comparison (MABAC). Expert Syst. Appl. 42, 3016–3028. doi:10.1016/j.eswa.2014.11.057
Pathapalli, V. R., Basam, V. R., Gudimetta, S. K., and Koppula, M. R. (2020). Optimization of machining parameters using WASPAS and MOORA. World J. Eng. 17, 237–246. doi:10.1108/WJE-07-2019-0202
Shanmugasundar, G., Sapkota, G., Čep, R., and Kalita, K. (2022). Application of MEREC in multi-criteria selection of optimal spray-painting robot. Processes 10, 1172. doi:10.3390/pr10061172
Wangikar, S. S., Patowari, P. K., and Misra, R. D. (2017). Effect of process parameters and optimization for photochemical machining of brass and German silver. Mater. Manuf. process. 32, 1747–1755. doi:10.1080/10426914.2016.1244848
Wangikar, S. S., Patowari, P. K., Misra, R. D., and Misal, N. D. (2019). “Photochemical Machining: A Less Explored Non-conventional Machining Process,” in In Non-Conventional Machining in Modern Manufacturing Systems, Editor K. Kumar, N. Kumari, and J. Paulo Davim (Hershey, PA: IGI Global), 188–201. doi:10.4018/978-1-5225-6161-3.ch009
Yoon, K., and Hwang, C. L. (1981). “TOPSIS (technique for order preference by similarity to ideal solution)-a Multiple attribute decision making,” in Multiple attribute decision making-methods and applications, a state-of-the-at survey (Berlin: Springer), 128–140.
Zavadskas, E. K., and Turskis, Z. (2010). A NEW ADDITIVE RATIO ASSESSMENT (ARAS) METHOD IN MULTICRITERIA DECISION-MAKING/NAUJAS ADITYVINIS KRITERIJŲ SANTYKIŲ ĮVERTINIMO METODAS (ARAS) DAUGIAKRITERINIAMS UŽDAVINIAMS SPRĘSTI. Ukio Technol. Ir. Ekon. Vystym. 16, 159–172. doi:10.3846/tede.2010.10
Zavadskas, E. K., Turskis, Z., Antucheviciene, J., and Zakarevicius, A. (2012). Optimization of weighted aggregated sum product assessment. Elektron. Ir. Elektrotechnika 122, 3–6. doi:10.5755/j01.eee.122.6.1810
Appendix

TABLE A1. Input variables of experiment (Agrawal and Kamble, 2019).
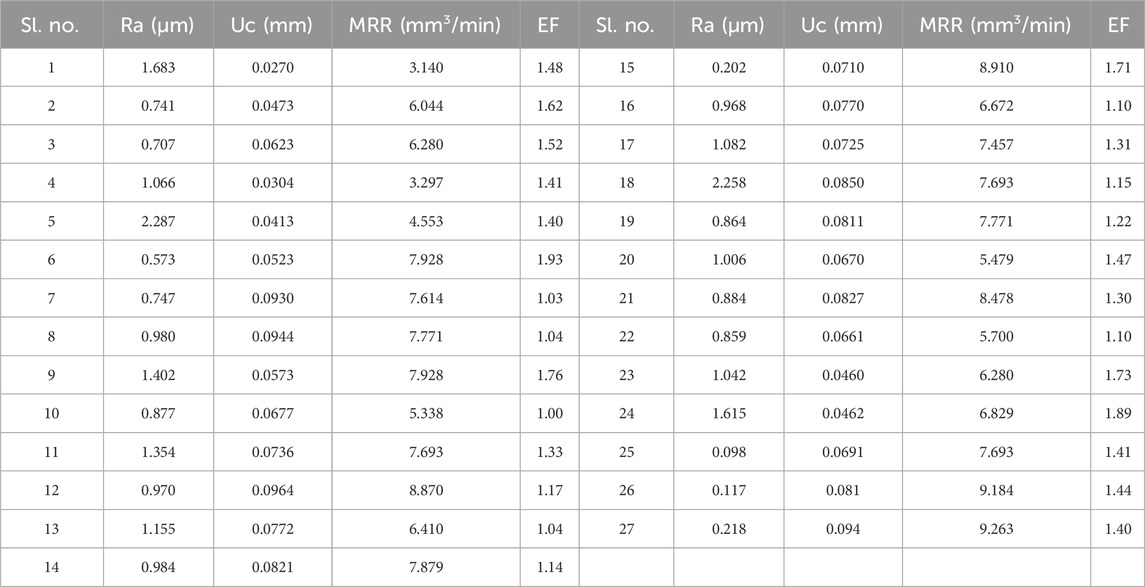
TABLE A2. Experimental data (Agrawal and Kamble, 2019).
Keywords: photochemical machining, MCDM, TOPSIS, MOORA, ARAS, non-traditional machining
Citation: Sapkota G, Ghadai RK, Čep R, Shanmugasundar G, Chohan JS and Kalita K (2024) Enhancing efficiency in photo chemical machining: a multivariate decision-making approach. Front. Mech. Eng 10:1325018. doi: 10.3389/fmech.2024.1325018
Received: 20 October 2023; Accepted: 31 January 2024;
Published: 13 February 2024.
Edited by:
Sabina Luisa Campanelli, Politecnico di Bari, ItalyReviewed by:
Krzysztof Żak, Opole University of Technology, PolandLeijie Fu, Xi’an Technological University, China
Copyright © 2024 Sapkota, Ghadai, Čep, Shanmugasundar, Chohan and Kalita. This is an open-access article distributed under the terms of the Creative Commons Attribution License (CC BY). The use, distribution or reproduction in other forums is permitted, provided the original author(s) and the copyright owner(s) are credited and that the original publication in this journal is cited, in accordance with accepted academic practice. No use, distribution or reproduction is permitted which does not comply with these terms.
*Correspondence: Ranjan Kumar Ghadai, cmFuamFuLmdoYWRhaUBtYW5pcGFsLmVkdQ==; Robert Čep, cm9iZXJ0LmNlcEB2c2IuY3o=; Kanak Kalita, ZHJrYW5ha2thbGl0YUB2ZWx0ZWNoLmVkdS5pbg==