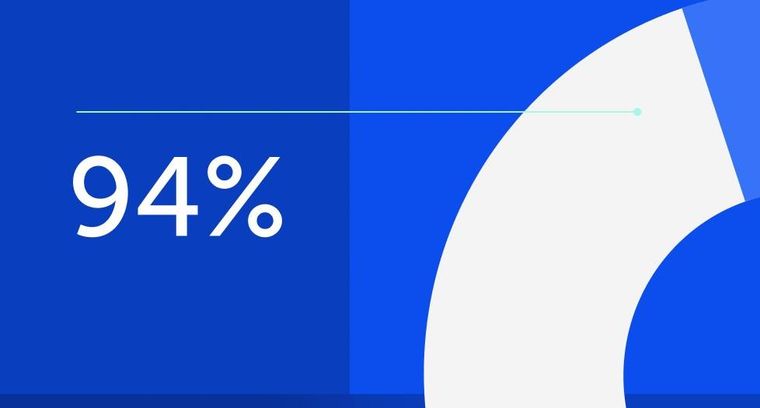
94% of researchers rate our articles as excellent or good
Learn more about the work of our research integrity team to safeguard the quality of each article we publish.
Find out more
EDITORIAL article
Front. Mech. Eng., 21 November 2023
Sec. Digital Manufacturing
Volume 9 - 2023 | https://doi.org/10.3389/fmech.2023.1334600
This article is part of the Research TopicGlobal Excellence in Digital Manufacturing: EuropeView all 5 articles
Editorial on the Research Topic
Global excellence in digital manufacturing: Europe
Global excellence in digital manufacturing sums up an era of success in the industry, where businesses and organizations use state-of-the-art digital technologies and strategies to improve overall operational efficiency, optimize production processes, and improve product quality globally.
The main concept of digital manufacturing (DM) is the blending of a wide range of cutting-edge technologies into conventional industrial processes, including additive manufacturing, automation, big data analytics, the Internet of Things (IoT), computer-aided manufacturing, robotics, process simulation, decision making, manufacturing resource planning, enterprise resource planning, logistics, supply chain management, e-commerce systems and artificial intelligence. Achieving global excellence in digital manufacturing entails harnessing the power of data-driven insights and real-time connectivity to streamline operations, reduce costs, and meet the demands of a rapidly evolving global marketplace. It is a crucial aspect of staying competitive in today’s highly dynamic and interconnected world of manufacturing.
Not by chance, digital manufacturing is one of the main plans of the European future vision and strategic goals towards knowledge-based production (Westkämper, 2007). It is fueled by the growing need for the effectiveness of operations in international networks as well as the deployment and standardization of information and communication technology. All technologies devised in this field share the common objective of using data-driven insights and real-time connection to optimize processes, cut costs, and satisfy the expectations of a continuously changing global market is necessary to achieve global excellence in digital manufacturing. Such important aspects are deemed essential for maintaining competitiveness in the extremely dynamic and linked manufacturing environment of today. In fact, digital manufacturing lowers operating expenses, improves product quality, and boosts manufacturing efficiency (Chen et al., 2017). Furthermore, technologies such as 3D printing enable customization and on-demand production, hence reducing the need for vast warehouses and overproduction. These developments lead to a considerable reduction in greenhouse gas emissions, material waste, and energy usage (Mahmood et al., 2022). In the last few years, DM has developed synergically with circular economy, sustainable process and product development. Redesigning goods and materials to be more robust, recyclable, and repairable is encouraged by the circular economy. Products and materials are reused as long as feasible rather than being thrown away after their intended usage. With this idea, a closed-loop system with ongoing material and product regeneration is created. It not only cuts waste but also lowers the need for raw materials and conserves resources (Furferi et al., 2022).
There is a significant overlap between digital manufacturing and the circular economy. Better product tracking and monitoring are made possible by digital technology throughout their lifecycle. In addition to improving product traceability, this gives producers insight into how their goods are being utilized and informs them when maintenance or repair might be necessary. Digital technologies also make it easier to develop items that are sustainable since they make it possible to create designs that are readily upgraded and adaptable (Bocken et al., 2016). Consequently, this increases the longevity of the items and lowers the requirement for disposal. Moreover, digital manufacturing facilitates the shared economy, in which goods are rented or shared as opposed to being owned individually (Cheng, 2016). This encourages resource efficiency and lowers the quantity of goods that are wasted. Additionally, smart technologies provide improved supply chain coordination, which lowers inefficiencies and lessens the environmental impact of logistics and transportation. This synergy has advantages for more than just individual companies. Reduced environmental deterioration, resource conservation, and the development of jobs in sustainable sectors benefit society at large. Communities become cleaner and healthier as a result of the decrease in waste and pollution. Governments and regulatory agencies are putting laws and incentives in place to promote the adoption of this partnership as they have begun to see its potential.
Based on the above considerations, Frontiers launched a Research Topic named “Global Excellence in Digital Manufacturing: Europe” with the goal of highlighting the latest advancements in Digital Manufacturing in Europe, showcasing the academic excellence and high-quality work of internationally recognized researchers. To take up this challenge fourteen authors proposed an overall number of 4 papers.
In (Psarommatis et al.) a model to address rescheduling caused by unexpected events, aiming to achieve the zero-defect manufacturing (ZDM) concept is proposed. The model’s objective is to combine conventional and ZDM-oriented events into a single technique to determine when the subsequent rescheduling will take place to respond to unforeseen occurrences efficiently. Event reaction time (RT) and event delay response time (DRT), two crucial time factors for every kind of event, are defined to support the technique. An event management algorithm is created to determine the best rescheduling option based on these characteristics. To represent the dynamics of production, the DRT parameter is computed using a multi-parametric dynamic formula. Additionally, the suggested approach’s degree of robustness is evaluated, and the behaviour of the generated technique is analysed using the ANOM and ANOVA methodologies. Ultimately, several simulation tests are carried out, a case study based on actual production circumstances is undertaken, and comparisons with other rescheduling plans are given. The outcomes show how well the suggested event management algorithm handles rescheduling. The authors conclude by mentioning a future project that will involve integrating predictive maintenance events with the scheduling tool and events management algorithm, as well as examining if the patterns discovered for the new control parameters are consistent with the findings of the research.
In (Mendaza-DeCal et al.) the concepts of digital excellence are developed in the biomedical field out by proposing exo-endoprosthesis as a suggested alternative to total limb amputation in small animals. An assessment is conducted on the internal 3D printing of exo-endoprostheses in polyether ether ketone (PEEK). This internal component was evaluated in two distinct shapes: one for the radius and the other for cylindrical medullary cavities. Appropriate PEEK temperature settings were achieved for fused filament fabrication (FFF) 3D printing of the interior component of exo-endoprostheses. To get the best results for bone anchoring and thread strength, printing trials were conducted for these components at various dimensions and printing orientations. Pull-off strength tests were conducted for the interior part’s various surfaces, with positive surfaces yielding the best results. For an ex vivo evaluation of thread strength characteristics and bone anchoring, all printed internal components were placed into the radii and tibiae of dogs. The optimal print temperatures were achieved at 410°C for the nozzle and 130°C for the bed, respectively. The printing code, quality, and take-off time were also shown to be positively correlated, but the take-off and the printing code, or quality, as well as the print-bed temperature and the printing code, were found to be negatively correlated. The results for pull-off strength were better on positive surfaces. For one version of each internal part form, excellent results were obtained for thread strength and bone anchoring. The designed devices demonstrated excellent threaded rod fitting into the PEEK plug and flawless PEEK plug bone anchoring for the radii and tibiae. Furthermore, the modest standard deviation of most PEEK tiny device manufacturing iterations using FFF technology have been demonstrated. This work demonstrates the wide range of possibilities offered by Additive Manufacturing and hints at future works dealing with the development of iterative, affordable, and reasonable options for producing small medical devices using high-performance plastic materials.
Authors of (Angelo et al.) leverage the concept of DM for ameliorating the design of electricity pylons. In detail, by using a methodical design approach for the morphological and structural optimization of artificial above-ground structures, such as pylons, masts, and towers of infrastructures and facilities, this work seeks to improve their visual quality. By using computer-aided tools, the technique accomplishes both functional and aesthetic aims. Specifically, three essential actions are followed to do this: morphological evolution of environment, culture, and social demands in relation to landscape symbolism, design of idea topology optimization, to lessen the visual effect and structural weight, and engineering of the optimal structure. As a case study, the method is used for designing electricity pylons for the coastal territory of a Mediterranean European country, such as Italy. Citizens were involved during the identification phase of a symbolic shape for the concept development and during the final assessment phase. To complete the engineering phase, conventional lattice components with welded connections were assembled. The designed construction uses an additional 15%–20% of trusses and sheet metal coverings, therefore even though using this truss-like structure should result in a minimal cost, the overall cost is more than a typical lattice pylon. Therefore, the structure has improved visual quality in accordance with international standards and completely satisfies all functional and required criteria, including those resulting from social and industrial feasibility as well as regulatory needs. Regarding the crucial circumstance under discussion, the approach demonstrates its potential in creating a unique design for lightweight structures with improved visual quality. The approach takes into account the topography in which the structures will be erected as well as the residents’ subjective perceptions and priorities. In the future, the method’s application to additional above-ground buildings and various scenarios where symbolic forms may be recognized as emblematic of the environment, the landscape, or the cultural background will be the main emphasis. Therefore, future work hinted at in this work, will focus on the particular economic analyses for manufacturing process optimization, defining the lowest cost and contrasting it with state-of-the-art methods.
In (Melani et al.) the main theme is the connection between excellence in DM and circular economy. As mentioned above, the impact of contemporary global Research Topic like environmental degradation and climate change must also be considered when designing or redesigning goods or services. During this process, it is necessary to implement established methods like the 3R recovery strategy and the Circular Economy approach, which are designed to decrease waste and enhance recycling, regeneration, and reusability. Within the framework of this article, research on the potential for reusing end-of-life mosquito nets—which are challenging to recycle—to lessen their environmental effect and provide new commercial prospects is presented. The study was carried out within a manufacturing firm. To this aim, several techniques for finding new product uses have been assessed from the literature, and the best option has been chosen. The process begins with determining the purposes of the product. Next, a series of patent searches are conducted to extract the Cooperative Patent Classifications (CPCs) of the resultant patents, which will be utilized as external stimuli in the design phase. The outcomes in terms of concepts produced are then displayed at the conclusion of the work, indicating the true efficacy of the employed methodology. Further research is required to examine some of the anticipated new uses, as some may be more challenging to implement than others. Specifically, it appears that the use of mosquito nets in the geogrid field presents the most challenges. If the product has the necessary mechanical attributes for these uses, it would be imperative to get waste parts with the most consistent form feasible. The fact that the fragments are never the same length makes this very important. Furthermore, an examination would be required to ascertain the best way to combine the separate components while maintaining the mechanical characteristics in the locations where they join.
The above-mentioned contributions highlight the importance of digital manufacturing as a game-changing strategy for fostering innovation, raising productivity, and boosting competitiveness in a variety of industries. Europe is positioned to uphold its status as a global manufacturing leader and make a positive impact on economic development, sustainability, and technical breakthroughs as long as it keeps investing in and embracing these digital innovations.
RF: Writing–original draft, Writing–review and editing. AR: Writing–original draft, Writing–review and editing.
The author(s) declare that no financial support was received for the research, authorship, and/or publication of this article.
The authors declare that the research was conducted in the absence of any commercial or financial relationships that could be construed as a potential conflict of interest.
All claims expressed in this article are solely those of the authors and do not necessarily represent those of their affiliated organizations, or those of the publisher, the editors and the reviewers. Any product that may be evaluated in this article, or claim that may be made by its manufacturer, is not guaranteed or endorsed by the publisher.
Bocken, N. M., De Pauw, I., Bakker, C., and Van Der Grinten, B. (2016). Product design and business model strategies for a circular economy. J. industrial Prod. Eng. 33 (5), 308–320. doi:10.1080/21681015.2016.1172124
Chen, B., Wan, J., Shu, L., Li, P., Mukherjee, M., and Yin, B. (2017). Smart factory of industry 4.0: key technologies, application case, and challenges. Ieee Access 6, 6505–6519. doi:10.1109/access.2017.2783682
Cheng, M. (2016). Sharing economy: a review and agenda for future research. Int. J. Hosp. Manag. 57, 60–70. doi:10.1016/j.ijhm.2016.06.003
Foivos, P., Giacomo, M., Xiaochen, Z., and Dimitris, K. (2021). A generic methodology for calculating rescheduling time for multiple unexpected events in the era of zero defect manufacturing. Front. Mech. Eng. 7, 2021. doi:10.3389/fmech.2021.646507
Furferi, R., Volpe, Y., and Franco, M. (2022). Circular economy guidelines for the textile industry. Sustainability 14, 11111. doi:10.3390/su141711111
Luca Di, A., Rocco, F., Francesco, G., and Emanuele, G. (2021). The integration of morphological design and topology optimization to enhance the visual quality of electricity pylons. Front. Mech. Eng. 8, 2021. doi:10.3389/fmech.2022.1061905
Mahmood, M. A., Rehman, A. U., Karakaş, B., Sever, A., Rehman, R. U., Salamci, M. U., et al. (2022). Printability for additive manufacturing with machine learning: hybrid intelligent Gaussian process surrogate-based neural network model for Co-Cr alloy. J. Mech. Behav. Biomed. Mater. 135, 105428. doi:10.1016/j.jmbbm.2022.105428
Marco, M., Rocco, F., Federico, R., and Luca, B. (2021). End of life of mosquito nets: searching for alternative uses through patent classification. Front. Manuf. Technol. 3, 2021. doi:10.3389/fmtec.2023.1172564
Rosa, M.-D. C., Salvador, P.-F., and Jesus, R.-Q. (2021). Test of designing and manufacturing a polyether ether ketone endoprosthesis for canine extremities by 3D printing. Front. Mech. Eng. 7, 2021. doi:10.3389/fmech.2021.693436
Keywords: digital manufacturing, additive manufacturing, IoT, design methodology, circular economy
Citation: Furferi R and Rehman AU (2023) Editorial: Global excellence in digital manufacturing: Europe. Front. Mech. Eng 9:1334600. doi: 10.3389/fmech.2023.1334600
Received: 07 November 2023; Accepted: 13 November 2023;
Published: 21 November 2023.
Edited and reviewed by:
Amit Bandyopadhyay, Washington State University, United StatesCopyright © 2023 Furferi and Rehman. This is an open-access article distributed under the terms of the Creative Commons Attribution License (CC BY). The use, distribution or reproduction in other forums is permitted, provided the original author(s) and the copyright owner(s) are credited and that the original publication in this journal is cited, in accordance with accepted academic practice. No use, distribution or reproduction is permitted which does not comply with these terms.
*Correspondence: Rocco Furferi, cm9jY28uZnVyZmVyaUB1bmlmaS5pdA==
Disclaimer: All claims expressed in this article are solely those of the authors and do not necessarily represent those of their affiliated organizations, or those of the publisher, the editors and the reviewers. Any product that may be evaluated in this article or claim that may be made by its manufacturer is not guaranteed or endorsed by the publisher.
Research integrity at Frontiers
Learn more about the work of our research integrity team to safeguard the quality of each article we publish.