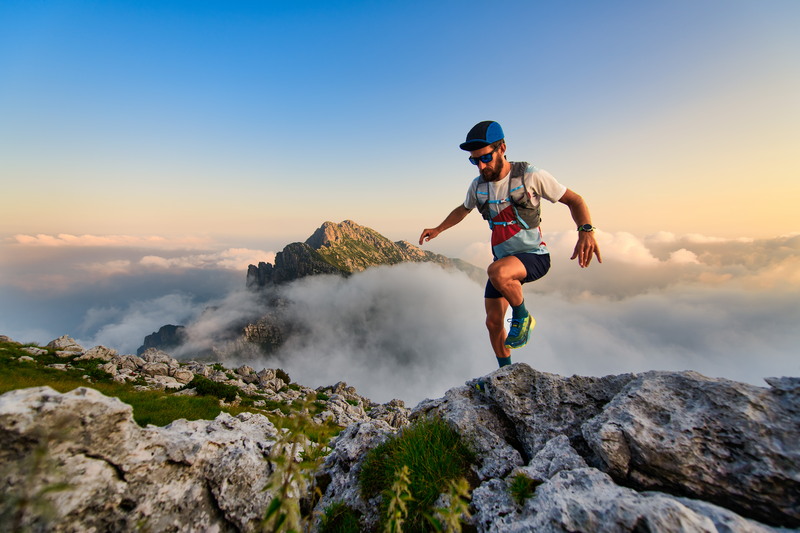
95% of researchers rate our articles as excellent or good
Learn more about the work of our research integrity team to safeguard the quality of each article we publish.
Find out more
ORIGINAL RESEARCH article
Front. Mech. Eng. , 01 December 2023
Sec. Tribology
Volume 9 - 2023 | https://doi.org/10.3389/fmech.2023.1325040
This article is part of the Research Topic Advancements in Thin Film Coating Technologies View all 4 articles
The present work deals with the study of various properties of aluminum (Al)-incorporated diamond-like carbon (DLC) thin films synthesized using the atmospheric pressure chemical vapor deposition (APCVD) technique by varying the deposition temperature (
Coatings play a crucial role in enhancing the performance and durability of various materials and surfaces. They offer a protective barrier against corrosion, wear, and other forms of degradation while also providing desirable properties, such as high hardness and low friction. Diamond-like carbon (DLC) thin films are a type of polycrystalline coating, which possess a very dense carbon crystalline network. These coatings have become popular due to their inherent properties such as higher hardness (
In recent years, metal-incorporated DLC coatings have been extensively studied by various research groups due to their higher chemical inertness, low residual stress (
Both physical vapor deposition (PVD) and chemical vapor deposition (CVD) methods have been used for the synthesis of Al-DLC thin films. Magnetron sputtering is a popular PVD technique used for the deposition of Al-DLC thin films due to its advantages in terms of high deposition rates, good film adhesion, and scalability (Kong et al., 2018). In magnetron sputtering, the target material is bombarded with high-energy ions, resulting in the sputtering of carbon and aluminum atoms, which are then deposited onto a substrate to form the Al-DLC film. The deposition temperature is controlled by adjusting the power applied to the target and substrate heating (Bouabibsa et al., 2018). Pulsed-laser deposition (PLD) is another popular PVD technique that has been employed for the synthesis of Al-DLC thin films (Ni et al., 2006). In the PLD method, a high-energy laser pulse ablates the target material, which generates a plasma plume that is deposited onto a substrate to form the film. PLD enables the precise control of the film composition and deposition temperature by adjusting the laser energy, pulse frequency, and substrate temperature. PLD produces highly crystalline and uniform films, which makes it a suitable method for synthesizing tailor-made Al-DLC thin films (Ding et al., 2021).
Plasma-enhanced chemical vapor deposition (PECVD) is a popular CVD technique used for depositing Al-DLC films since it produces high-quality films at relatively low temperatures (Huang et al., 2023b). In PECVD, a gaseous mixture of hydrocarbon and aluminum precursors in a reaction chamber is subjected to electrical discharges. This generates plasma, which causes film deposition onto the substrate. The deposition in PECVD can be controlled by adjusting the power input, precursor flow rates, and substrate heating (Huang et al., 2023b). Similarly, hot-filament chemical vapor deposition (HFCVD) is another CVD method used for the synthesis of Al-DLC films. In HFCVD, a hot filament is used to thermally decompose hydrocarbon and aluminum precursors in a gaseous mixture, which leads to the deposition of carbon and aluminum atoms onto the heated substrate (Pang et al., 2010). In HFCVD, the film properties can be the fine-tuned by adjusting the filament temperature and substrate heating.
Thus, it is noted that each technique offers certain advantages and drawbacks over the other. PVD techniques like magnetron sputtering and PLD generally have higher deposition rates, better film adhesion, and greater scalability (Ding et al., 2022). However, PVD techniques may suffer from issues related to film uniformity and stoichiometry control. On the other hand, CVD methods like PECVD and HFCVD can produce high-quality films at lower temperatures, making them more preferable for temperature-sensitive substrates (Huang et al., 2023b). CVD techniques also offer better control over film composition and uniformity but generally require longer deposition times (Pang et al., 2010).
Additionally, the literature review reveals that few researchers deposited the Al-DLC coating using physical vapor deposition techniques and obtained a reduction in the
In the present work, the synthesis of the Al-DLC coating has been carried out using the atmospheric pressure chemical vapor deposition (APCVD) technique. The objective of this study is to fill this knowledge gap by systematically investigating the influence of deposition temperature on the surface morphology, resistance to corrosion, nanohardness (
This paper is organized as follows: Section 1 presents a brief introduction to the need for Al incorporation into DLC films and reviews a few relevant literature works. Section 2 describes the experimental methods used in this study. The process of synthesis of Al-DLC films by the APCVD technique and the characterization techniques employed to investigate the surface morphology, resistance to corrosion, nanohardness, and Young’s modulus of the coatings are discussed in Section 2. Section 3 presents and discusses the results obtained from the analysis of the films, including the effects of the deposition temperature on the coating roughness, corrosion resistance, nanoindentation properties, and residual stresses. Section 4 presents a general discussion on the effect of the deposition temperature on AL-DLCs. Finally, Section 5 summarizes the main findings and conclusions of the study.
The methodology followed in this work is shown in Figure 1.
FIGURE 1. Flowchart depicting the methodology for the synthesis and characterization of Al-DLC coatings.
DLC coatings were deposited over Si (100) wafers. Before the synthesis of thin films, Si wafers were cleaned using the Radio Corporation of America (RCA) cleaning process, whose detailed explanation can be found in some other literature (Das et al., 2022). The substrates were kept in an APCVD chamber by placing them over an alumina ceramic boat. The synthesis of Al-DLCs was carried out using pure Al powder (99.9%). The Al-DLC samples were prepared by varying
The morphology and elemental composition of the coatings were analyzed using an SEM EVO MA18 instrument with an Oxford EDS (X-act) magnification range of ×1 to ×100,000. The AFM technique was used to evaluate the coating roughness (Ra) using Innova SPM (scanner 100 µm). The thin-film coating thickness was evaluated using a Dektak profilometer (Dektak 300 V). The corrosion behavior of DLC films was studied using CHI Software by plotting the curve between
The coating thickness of Al-DLC with respect to various deposition temperatures is listed in Table 1. From the table, it is observed that the coating thickness decreases with respect to the deposition temperature. The deposition rate depends on many parameters, like the deposition temperature, gas flow rate, deposition time, deposition pressure, and substrate position. With the increase in the deposition temperature, the particles in the deposition layer gradually become larger, leading to the gradual increase in thickness. The increase in the temperature leads to an increase in the growth rate of the nuclei, and the particles begin to fuse with each other to form cellular particles. Therefore, the porosity of the coating decreases, while its density increases (Bi et al., 2022). Furthermore, at a high temperature, the movement of gas molecules inside the chamber will be higher, which results in a rough surface and film thickness. The SEM images of the Al-DLC samples prepared at different
The EDS results, as shown in Figure 3, reveal that the concentration of Al in the Al-DLC film decreases with an increase in
The surface morphology of Al-DLC coatings characterized by the AFM technique is shown in Figure 4. The Al-DLC thin films prepared at 800
Figure 5 shows the polarization curve of different Al-DLC thin films through the Tafel plot using diluted water (50 mL) and KCl powder (1.5 g). The polarization curve indicates the corrosion potential (
The kinetic information and the interfacial properties of electrode materials were extracted using the EIS method—a non-destructive and easy method suitable for all coatings (Das et al., 2022). A Nyquist plot was constructed, which presents a plot of real impedance Z′ vs. negative imaginary impedance Z''. Figure 6 shows the Nyquist plots of all Al-DLC coatings prepared at different temperatures ranging from 800
The load–displacement curve of Al-DLC coatings prepared at different
The plasticity index (
Here,
The plasticity index measures the coating toughness, and plastic deformation resistance (
The detachment of films from the parent body leads to higher residual stress (
where
Thus, this study concludes that the deposition temperature has a significant impact on the morphology and structure of Al-DLC thin films. At lower deposition temperatures, Al-DLC films generally exhibit a more amorphous structure, which is associated with a random arrangement of carbon atoms and a mixture of
It has been reported in the literature that the deposition temperature also influences the grain size and surface roughness of Al-DLC films. As the deposition temperature increases, the grain size generally increases due to the enhanced atomic mobility, which leads to the growth of large crystalline domains (Zhou et al., 2019). The increase in the grain size often results in reduced film hardness and increased surface roughness. However, the exact relationship between deposition temperature, grain size, and surface roughness depend on the synthesis method and experimental conditions. This is why it is important to optimize these parameters for the desired film properties.
From the results of the experiments in the previous section, it is noted that the mechanical properties of Al-DLC films, such as hardness and elastic modulus, are strongly influenced by the deposition temperature. Higher deposition temperatures can lead to increased grain sizes and a more crystalline structure, which results in reduced film hardness (Kong et al., 2018). The DLC coating is basically a mixture of Sp2 and Sp3 bonds. The mechanical properties of the coating significantly affect the amount of Sp2 and Sp3 bonds present within the coating. The elastic modulus may also decrease with the increasing deposition temperature due to the transition from a more
Deposition temperature also plays a crucial role in determining the chemical composition of Al-DLC films, particularly the aluminum content and its distribution over the film. Because of enhanced surface mobility and diffusion of aluminum atoms, high deposition temperatures can lead to an increase in aluminum incorporation in the film (Ni et al., 2006). However, excessive aluminum content may also result in the formation of aluminum carbide phases, which can negatively impact the film’s mechanical and tribological properties (Voevodin et al., 1999). Therefore, careful control of the deposition temperature is needed to achieve the desired aluminum content and distribution in Al-DLC films. This further highlights the need for a carefully crafted design of experiments and optimization for obtaining the best DLC thin films. Due to its high hardness and low residual stress, the developed coating can be used in various automotive engine components, such as piston, piston ring camshaft, valve stem and head, and rocker arm (Voevodin et al., 1999; Zhang et al., 2002; Erdemir and Donnet, 2006; Ghadai et al., 2018). This type of coating can also be used for the development of a biological implant (Tay et al., 2001).
In the present research, Al-DLC coatings were synthesized using the APCVD technique by varying
The raw data supporting the conclusion of this article will be made available by the authors, without undue reservation.
RG: conceptualization, data curation, formal analysis, investigation, methodology, and writing–original draft. GS: conceptualization, methodology, and writing–original draft. LC: conceptualization, methodology, resources, and writing–review and editing. SD: data curation, formal analysis, investigation, and writing–original draft. PK: data curation, formal analysis, investigation, and writing–original draft. KK: resources, visualization, and writing–review and editing.
The authors declare that no financial support was received for the research, authorship, and/or publication of this article.
The authors declare that the research was conducted in the absence of any commercial or financial relationships that could be construed as a potential conflict of interest.
The author(s) declared that they were an editorial board member of Frontiers, at the time of submission. This had no impact on the peer review process and the final decision.
All claims expressed in this article are solely those of the authors and do not necessarily represent those of their affiliated organizations, or those of the publisher, the editors, and the reviewers. Any product that may be evaluated in this article, or claim that may be made by its manufacturer, is not guaranteed or endorsed by the publisher.
Ardigo, M. R., Ahmed, M., and Besnard, A. (2014). Stoney formula: Investigation of curvature measurements by optical profilometer. Adv. Mat. Res. 996, 361–366. doi:10.4028/www.scientific.net/amr.996.361
Bhushan, B., and Ko, P. L. (2003). Introduction to tribology. Appl. Mech. Rev. 56 (1), B6–B7. doi:10.1115/1.1523360
Bi, M., Zhu, J., Luo, Y., Cai, H., Li, X., Wang, X., et al. (2022). Effect of deposition temperature on the surface, structural, and mechanical properties of HfO2 using chemical vapor deposition (CVD). Coatings 12, 1731. doi:10.3390/coatings12111731
Bouabibsa, I., Lamri, S., and Sanchette, F. (2018). Structure, mechanical and tribological properties of Me-doped diamond-like carbon (DLC)(Me= Al, Ti, or Nb) hydrogenated amorphous carbon coatings. Coatings 8, 370. doi:10.3390/coatings8100370
Dai, W., and Wang, A. (2011). Deposition and properties of Al-containing diamond-like carbon films by a hybrid ion beam sources. J. Alloys Compd. 509, 4626–4631. doi:10.1016/j.jallcom.2011.01.132
Das, S., Guha, S., Ghadai, R., Sharma, A., and Chatterjee, S. (2022). Morphological, mechanical property analysis and comparative study over structural properties of CVD TiN film grown under different substrate temperature in nitrogen gas atmosphere. Silicon 14, 183–199. doi:10.1007/s12633-020-00807-5
Deng, B., Pei, J. F., and Tao, Y. (2014). Microstructure, mechanical and tribological properties of the TiAlN coatings after Nb and C dual ion implantation. Mat. Sci. For. 789, 455–460. doi:10.4028/www.scientific.net/msf.789.455
Ding, J. C., Chen, M., Mei, H., Jeong, S., Zheng, J., Yang, Y., et al. (2022). Microstructure, mechanical, and wettability properties of Al-doped diamond-like films deposited using a hybrid deposition technique: bias voltage effects. Diam. Relat. Mater. 123, 108861. doi:10.1016/j.diamond.2022.108861
Ding, J. C., Mei, H., Zheng, J., Wang, Q. M., Kang, M. C., Zhang, T. F., et al. (2021). Microstructure and wettability of novel Al-containing diamond-like carbon films deposited by a hybrid sputtering system. J. Alloys Compd. 868, 159130. doi:10.1016/j.jallcom.2021.159130
Domnich, V., Gogotsi, Y., and Dub, S. (2000). Effect of phase transformations on the shape of the unloading curve in the nanoindentation of silicon. Appl. Phys. Lett. 76, 2214–2216. doi:10.1063/1.126300
Erdemir, A., and Donnet, C. (2006). Tribology of diamond-like carbon films: recent progress and future prospects. J. Phys. D Appl. Phys. 39, R311–R327. doi:10.1088/0022-3727/39/18/r01
Fan, X., Wei, G., Lin, X., Wang, X., Si, Z., Zhang, X., et al. (2020). Reversible switching of interlayer exchange coupling through atomically thin VO2 via electronic state modulation. Matter 2, 1582–1593. doi:10.1016/j.matt.2020.04.001
Ghadai, R. K., Das, S., Kumar, D., Mondal, S. C., and Swain, B. P. (2018). Correlation between structural and mechanical properties of silicon doped DLC thin films. Diam. Relat. Mat. 82, 25–32. doi:10.1016/j.diamond.2017.12.012
Ghadai, R. K., Singh, K., Sharma, A., Roy, M. K., and Swain, B. P. (2021). Mechanical and Tribological properties of metal incorporated DLC thin film. Nanostructured Mater. their Appl., 229–263. doi:10.1007/978-981-15-8307-0_12
Guo, T., Kong, C., Li, X., Guo, P., Wang, Z., and Wang, A. (2017). Microstructure and mechanical properties of Ti/Al co-doped DLC films: dependence on sputtering current, source gas, and substrate bias. Appl. Surf. Sci. 410, 51–59. doi:10.1016/j.apsusc.2017.02.254
Han, C. X., Zhi, J. Q., Zeng, Z., Wang, Y. S., Zhou, B., Gao, J., et al. (2023). Synthesis and characterization of nano-polycrystal diamonds on refractory high entropy alloys by chemical vapour deposition. Appl. Surf. Sci. 623, 157108. doi:10.1016/j.apsusc.2023.157108
He, H. T., Fang, J. X., Wang, J. X., Sun, T., Yang, Z., Ma, B., et al. (2023). Carbide-reinforced Re0.1Hf0.25NbTaW0.4 refractory high-entropy alloy with excellent room and elevated temperature mechanical properties. Int. J. Refract. Hard Mater. 116, 106349. doi:10.1016/j.ijrmhm.2023.106349
He, Y., Wang, F., Du, G., Pan, L., Wang, K., Gerhard, R., et al. (2022). Revisiting the thermal ageing on the metallised polypropylene film capacitor: from device to dielectric film. High. Volt. 8, 305–314. doi:10.1049/hve2.12278
Huang, J., Peng, J., Qiu, X., and Li, X. (2023a). Evolution of the microstructure, hybridization, and internal stress of Al-doped Diamond-like carbon coatings: a molecular dynamics simulation. Langmuir 39, 3895–3904. doi:10.1021/acs.langmuir.2c03200
Huang, J., Peng, J., Qiu, X., and Li, X. (2023b). Evolution of the microstructure, hybridization, and internal stress of Al-doped diamond-like carbon coatings: a molecular dynamics simulation. Langmuir 39, 3895–3904. doi:10.1021/acs.langmuir.2c03200
Irudayaraj, A. A., Kuppusami, P., Thirumurugesan, R., Mohandas, E., Kalainathan, S., and Raghunathan, V. S. (2007). Influence of nitrogen flow rate on growth of TiAlN films prepared by DC magnetron sputtering. Surf. Eng. 23, 7–11. doi:10.1179/174329407x161627
Kong, C., Guo, P., Sun, L., Zhou, Y., Liang, Y., Li, X., et al. (2018). Tribological mechanism of diamond-like carbon films induced by Ti/Al co-doping. Surf. Coatings Technol. 342, 167–177. doi:10.1016/j.surfcoat.2018.02.098
Kong, D., and Fu, G. (2015). Nanoindentation analysis of TiN, TiAlN, and TiAlSiN coatings prepared by cathode ion plating. Sci. China Technol. Sci. 58, 1360–1368. doi:10.1007/s11431-015-5876-2
Lai, L., Gan, M., Wang, J., Chen, L., Liang, X., Feng, J., et al. (2023). New class of high-entropy rare-earth niobates with high thermal expansion and oxygen insulation. J. Am. Ceram. Soc. 106, 4343–4357. doi:10.1111/jace.19077
Liang, J. H., Chen, M. H., Tsai, W. F., Lee, S. C., and Ai, C. F. (2007). Characteristics of diamond-like carbon film synthesized on AISI 304 austenite stainless steel using plasma immersion ion implantation and deposition. Nucl. Instrum. Methods Phys. Res. B 257, 696–701. doi:10.1016/j.nimb.2007.01.143
Liu, E., Li, L., Blanpain, B., and Celis, J. P. (2005). Residual stresses of diamond and diamondlike carbon films. J. Appl. Phys. 98, 073515. doi:10.1063/1.2071451
Matei, A. A., Pencea, I., Branzei, M., Trancă, D. E., Ţepeş, G., Sfăt, C. E., et al. (2015). Corrosion resistance appraisal of TiN, TiCN and TiAlN coatings deposited by CAE-PVD method on WC–Co cutting tools exposed to artificial sea water. Appl. Surf. Sci. 358, 572–578. doi:10.1016/j.apsusc.2015.08.041
Ni, W., Cheng, Y.-T., Weiner, A. M., and Perry, T. A. (2006). Tribological behavior of diamond-like-carbon (DLC) coatings against aluminum alloys at elevated temperatures. Surf. Coatings Technol. 201, 3229–3234. doi:10.1016/j.surfcoat.2006.06.045
Pang, H., Wang, X., Zhang, G., Chen, H., Lv, G., and Yang, S. (2010). Characterization of diamond-like carbon films by SEM, XRD and Raman spectroscopy. Appl. Surf. Sci. 256 (21), 6403–6407. doi:10.1016/j.apsusc.2010.04.025
Patel, N. G., Sreeram, A., Venkatanarayanan, R. I., Krishnan, S., and Yuya, P. A. (2015). Elevated temperature nanoindentation characterization of poly(para-phenylene vinylene) conjugated polymer films. Polym. Test. 41, 17–25. doi:10.1016/j.polymertesting.2014.10.004
Peng, X. L., and Clyne, T. W. (1998). Residual stress and debonding of DLC films on metallic substrates. Diam. Relat. Mat. 7, 944–950. doi:10.1016/s0925-9635(97)00331-2
Pu, J., Zhang, G., Wan, S., and Zhang, R. (2015). Synthesis and characterization of low-friction Al-DLC films with high hardness and low stress. J. Compos. Mat. 49, 199–207. doi:10.1177/0021998313515291
Robertson, J. (2002). Diamond-like amorphous carbon. Mat. Sci. Eng. R. Rep. 37, 129–281. doi:10.1016/s0927-796x(02)00005-0
Singh, V., Jiang, J. C., and Meletis, E. I. (2005). Cr-diamondlike carbon nanocomposite films: synthesis, characterization and properties. Thin Solid Films 489, 150–158. doi:10.1016/j.tsf.2005.04.104
Tay, B. K., Cheng, Y. H., Ding, X. Z., Lau, S. P., Shi, X., You, G. F., et al. (2001). Hard carbon nanocomposite films with low stress. Diam. Relat. Mat. 10, 1082–1087. doi:10.1016/s0925-9635(00)00429-5
Voevodin, A. A., O'neill, J. P., and Zabinski, J. S. (1999). Nanocomposite tribological coatings for aerospace applications. Surf. Coatings Technol. 116, 36–45. doi:10.1016/s0257-8972(99)00228-5
Wang, J., Chong, X., Lv, L., Wang, Y., Ji, X., Yun, H., et al. (2023). High-entropy ferroelastic (10RE0.1)TaO4 ceramics with oxygen vacancies and improved thermophysical properties. J. Mat. Sci. Technol. 157, 98–106. doi:10.1016/j.jmst.2022.12.027
Wang, J., Pan, Z., Wang, Y., Wang, L., Su, L., Cuiuri, D., et al. (2020). Evolution of crystallographic orientation, precipitation, phase transformation and mechanical properties realized by enhancing deposition current for dual-wire arc additive manufactured Ni-rich NiTi alloy. Addit. Manuf. 34, 101240. doi:10.1016/j.addma.2020.101240
Wongpanya, P., Silawong, P., and Photongkam, P. (2022). Adhesion and corrosion of Al–N doped diamond-like carbon films synthesized by filtered cathodic vacuum arc deposition. Ceram. Int. 48, 20743–20759. doi:10.1016/j.ceramint.2022.04.055
Xie, J., Chen, Y., Yin, L., Zhang, T., Wang, S., and Wang, L. (2021). Microstructure and mechanical properties of ultrasonic spot welding TiNi/Ti6Al4V dissimilar materials using pure Al coating. J. Manuf. Process. 64, 473–480. doi:10.1016/j.jmapro.2021.02.009
Yang, Y. (2016). Sensitivity of nanoindentation strain rate in poly(ester-ester-ketone) using atomic force microscopy. Polym. Test. 53, 85–88. doi:10.1016/j.polymertesting.2016.05.013
Zhang, J., Wang, L., Zhong, A., Huang, G., Wu, F., Li, D., et al. (2019). Deep red PhOLED from dimeric salophen Platinum(II) complexes. Dyes Pigm 162, 590–598. doi:10.1016/j.dyepig.2018.10.053
Zhang, P., Tay, B. K., Sun, C. Q., and Lau, S. P. (2002). Microstructure and mechanical properties of nanocomposite amorphous carbon films. J. Vac. Sci. Technol. A 20, 1390–1394. doi:10.1116/1.1486227
Keywords: aluminum-incorporated diamond-like carbon, nanoindentation, residual stress, thin film, coatings
Citation: Ghadai RK, Shanmugasundar G, Cepova L, Das S, Kumar Mahto P and Kalita K (2023) A temperature-based synthesis and characterization study of aluminum-incorporated diamond-like carbon thin films. Front. Mech. Eng 9:1325040. doi: 10.3389/fmech.2023.1325040
Received: 20 October 2023; Accepted: 20 November 2023;
Published: 01 December 2023.
Edited by:
Vijay Raghunathan, King Mongkut’s University of Technology North Bangkok, ThailandReviewed by:
Jitendra Kumar Katiyar, SRM Institute of Science and Technology, IndiaCopyright © 2023 Ghadai, Shanmugasundar, Cepova, Das, Kumar Mahto and Kalita. This is an open-access article distributed under the terms of the Creative Commons Attribution License (CC BY). The use, distribution or reproduction in other forums is permitted, provided the original author(s) and the copyright owner(s) are credited and that the original publication in this journal is cited, in accordance with accepted academic practice. No use, distribution or reproduction is permitted which does not comply with these terms.
*Correspondence: Ranjan Kumar Ghadai, cmFuamFuLmdoYWRhaUBtYW5pcGFsLmVkdQ==; Kanak Kalita, ZHJrYW5ha2thbGl0YUB2ZWx0ZWNoLmVkdS5pbg==
Disclaimer: All claims expressed in this article are solely those of the authors and do not necessarily represent those of their affiliated organizations, or those of the publisher, the editors and the reviewers. Any product that may be evaluated in this article or claim that may be made by its manufacturer is not guaranteed or endorsed by the publisher.
Research integrity at Frontiers
Learn more about the work of our research integrity team to safeguard the quality of each article we publish.