- 1Department of Automotive and Marine Engineering Technology, Public Authority for Applied Education and Training, Adailiyah, Kuwait
- 2Department of Manufacturing Engineering Technology, The Public Authority for Applied Education and Training, Kuwait City, Kuwait
- 3Centre for Future Materials, School of Engineering, University Southern Queensland, Toowoomba, QLD, Australia
Bonding synthetic fibres to metals to improve strength, durability, and corrosion resistance is a prevalent practise in the automotive, marine, and aerospace industries. Lap shear adhesion, a measurement of the bonding strength between composites and metallic substrates, is essential for structural integrity. The emergence of natural fibre composites as sustainable alternatives to synthetic composites makes it essential to investigate their lap shear behaviour and the effect of fibre volume fraction on composite properties. This research investigates the adhesion behaviour of coir and glass fibre epoxy composites to mild steel. Coir fibres, which are known for their resilience and tenacity, were treated with an alkaline solution to improve their adhesion to the resin. Samples of lap shear adhesion were prepared in accordance with ASTM specifications, and tests were conducted using a tensile machine. Increasing the volume fraction of coir or glass fibres decreased the bond strength, as demonstrated by the results. Due to the fibres’ greater tensile strength and rigidity, glass fibre composites exhibited superior strength. However, under tensile loading conditions, coir fibres exhibited superior adhesion to mild steel surfaces. SEM micrographs confirmed that coir composites exhibit shear failure while glass composites exhibit fibre pull-out behaviour. This study concludes by highlighting the engineering potential of coir fibres, considering their natural properties and cost-effectiveness. It is necessary to further optimise the fiber-matrix interface and comprehend the mechanical behaviour of coir composites in order to maximise their effectiveness. To assure the long-term durability of composite-metal joints, surface preparation, adhesive type, application procedure, and environmental conditions must also be considered. At a content percentage of 10%, glass fibres exhibited 100% higher shear strength compared to coir fibres in epoxy composites. Conversely, coir fibres at 10% content demonstrated approximately 75% greater shear strength than the values obtained with 40% glass fibres. The failure mechanisms observed are delamination or fibre fracture in the bonding area under tensile and shear loading. Increasing the fibre volume fraction reduces bond strength. Factors such as limited space for the matrix, tension concentrations, and the mechanical properties of the fibres contribute to weakened bonds. Glass fibres have better strength and rigidity than coir fibres, affecting load transfer and adhesion. Interfacial bonding is crucial, and maintaining it becomes more difficult with higher fibre volume fractions, resulting in weakened bonds.
Introduction
In recent years, natural fibres have gained popularity as an alternative to synthetic fibres due to the negative environmental impact associated with the production of synthetic fibres (Ahmad and Zhou, 2022). Synthetic fibres are derived from petroleum-based chemicals that require significant quantities of energy to produce (Al-Maharma et al., 2022). In addition, they do not biodegrade and contribute to the increasing environmental problem of plastic pollution. Natural fibres, such as jute, coir, kenaf, and bamboo, are renewable and biodegradable resources that have been utilised for centuries in various industries, (Eid Alajmi et al., 2021). Compared to synthetic fibres, they require less energy to produce and have a smaller carbon footprint (Al-Maharma et al., 2022). Due to the sustainability and eco-friendliness of natural fibres, they are gaining traction as a substitute for synthetic fibres in a variety of engineering applications (Albdiry and Yousif, 2019). From a structural standpoint, bamboo, jute, and hemp can be used to generate lightweight, robust composites for use in the construction industry, (Hasan et al., 2023). In the automotive and aerospace industries, flax, hemp, coir and kenaf fibres are ideal for manufacturing lightweight components with superior mechanical properties, (Azwa et al., 2013).
Bonding synthetic fibres to metals is a prevalent practise in numerous industries, such as the automotive, marine, and aerospace sectors, (Adams, 2021). Synthetic fibres are frequently used to restore damaged metal body panels on automobiles. In the construction of yachts and other marine vessels, synthetic fibres are frequently employed. Frequently, synthetic fibres are bonded to metal components, such as the hull or superstructure, (Sarkar and Kandasubramanian, 2021). This provides the vessel with increased strength and durability, as well as protection against water damage. Synthetic fibres are also used in the construction of aircraft and spacecraft in the field of aerospace engineering. In certain instances, it may be bonded to metal components to increase their strength and rigidity. In many instances, synthetic fibres are adhered to metal components with an adhesive or resin. This can provide the equipment with increased strength and durability, as well as protection against corrosion and other forms of damage, (Altoubat et al., 2020; Hariharan et al., 2023; Xiang et al., 2023).
The lap shear adhesion of fibre composites to metal is an important topic of research for numerous reasons since, in many circumstances, composite materials must be bonded to metal substrates to form a structural junction, (Reis et al., 2020). The lap shear strength of the composite-metal bond is a significant aspect of the performance of such joints since it determines the overall strength and longevity of the structure. In the aerospace industry, lap shear adhesion testing is utilised to determine the bonding strength of composite materials to metallic substrates such as aluminium and titanium alloys, (Hu et al., 2022). These materials are frequently employed in the construction of aircraft structures and parts. In the automotive industry, lap shear adhesion testing is used to determine the bonding strength of composite materials to metal substrates used to construct vehicle bodies and components. For example, in the construction of automobile bodies and chassis, as well as interior and exterior components including doors, hoods, and spoilers, (Shanmugam et al., 2021). Therefore, it is essential to investigate the lap shear behaviour of natural fibre composites as they have emerged as a sustainable alternative to traditional synthetic composites in a variety of engineering applications. Besides, in determining the mechanical and physical properties of composites, the volume fraction of natural fibres plays an important function. Understanding the impact of volume fraction on composite material properties is essential for designing and optimising composite materials for specific applications, (Shalwan and Yousif, 2013).
The benefits and potential drawbacks of such an approach fall into different sectors. In the construction sector, coir-fiber-reinforced epoxy joints have many uses, including the bonding of structural components and the renovation and repair of buildings (Reddy, 2006). The reinforcement provided by the coir fibres increases the joint’s strength and ability to support more weight. The epoxy adhesive is a versatile option because it adheres well to a variety of materials, including concrete, steel, and wood. The strength and longevity of the joint are also enhanced by the natural qualities of coir fibres, which include high tensile strength and resistance to deterioration. For the automotive industry, automotive manufacturing and repairs can make use of coir-fibre-reinforced epoxy joints. Coir fibres’ light weight can contribute to a reduction in the overall weight of a vehicle’s parts while still providing an adequate level of strength and structural integrity. This may result in decreased emissions and better fuel efficiency. Additionally, the epoxy adhesive offers dependable bonding, which is necessary for a number of automotive applications, such as bonding trim pieces or joining composite panels. Further, applications in the marine industry can use coir-fibre-reinforced epoxy joining. Coir fibres are naturally water-resistant and able to withstand harsh marine environments. Because of this, they can be used for tasks like bonding fibreglass laminates, mending boat hulls, or strengthening marine structures. A strong and long-lasting bond that can withstand the challenges of moisture, saltwater, and UV exposure is ensured by the epoxy adhesive’s excellent adhesion to fibreglass and other common marine materials. The disadvantages of coir fibres include their limited availability and sourcing in some areas, the possibility of variability in their properties, which could affect the uniformity of the joint, and the need for consideration for moisture exposure because unprotected coir fibres can absorb water.
The present study is motivated by the aforementioned context to investigate the bonding behaviour of coir and glass fibre epoxy composites to mild steel. The primary objective of this study is to increase knowledge of the underlying mechanisms of adhesion between these materials and to investigate the feasibility of incorporating coir fibres into engineering applications.
Materials and experimental procedure
Material preparation
Coir fibres used in the current study due to their high strength, natural durability, biodegradability, excellent water retention, and low cost and play an essential role in various engineering applications. In the current study, coir fibres were supplied by Bunnings warehouse in Toowoomba, QLD, Australia. The fibres were cut into 10 mm in length, Figure 1. Micrographs of the fibres are shown in Figure 1B. The hydrophobic properties of coir fibres are attributed to the presence of lignin (Figure 1B), a natural wax on their surface. Lignin, a complex organic polymer, is a ubiquitous component of the cell walls of numerous plant species, including coconuts. This wax imparts water-repellent characteristics to coir fibres, providing them with protection against moisture-induced degradation. Furthermore, coir fibres contain other naturally occurring substances, such as cellulose, hemicellulose, and pectin (Figure 1B). The presence of the wax on the surface of the fibres acts as a protecting layer which would prevent the resin from penetrating inside the fibers or adhering properly into the surface of the fibres. To overcome this issue mercerization process implemented which could enhance the adhesion of the fibres with the resin, (Yousif et al., 2012; Khan et al., 2017). The procedure is first treating the fibers with a potent alkaline solution, usually sodium hydroxide (NaOH), and then thoroughly rinsing them with water. In the process, the cellulose fibers swell and alter shape because of being exposed to the alkali, which enhances strength, luster, and resin uptake. The NaOH specifically hydrolyzes the cellulose molecules in the fibers, releasing the hydroxyl groups by dissolving the hydrogen bonds that connect the glucose chains, (Alsufyani and M’sakni, 2023; Yousif and Chin, 2012). The sodium ions in the NaOH solution subsequently react with the exposed hydroxyl groups to generate sodium celluloseate.
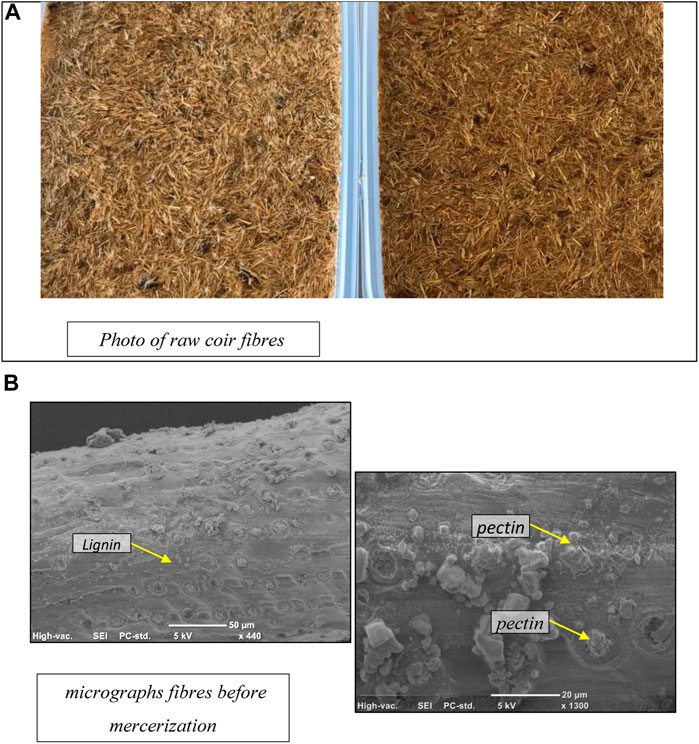
FIGURE 1. Photo and micrographs of coir fibres before mercerization. (A) photograph of cut fibres, (B) micrographs of the fibres before treatment.
For the current work, the prepared coir fibres were washed and then socked into a NaOH solution with a 6% concentration for 24 h, as recommended by many published articles, (Narish et al., 2011). The treated fibres were dried in an oven for 24 h at a temperature of 40°C. Figure 2 shows the surface of treated coir fibers, which clearly indicates the improvement of the treatment by removing the waxy layer and exposing the pectins of the fibres. This would roughen the surface and allow some of the resin to penetrate in the fibers, generating an interlock mechanism owing to improved interfacial adhesion of the fibres with the resin. For the synthetic fibres, glass fibres were used, and the micrographs of the fibres are shown in Figure 3.
When you prepared the coir fibre-reinforced epoxy joint with mild steel, the fibres were arranged inside the joint in a random orientation. The choice to use a random orientation for the fibres may have been influenced by particular requirements or considerations of the application or test being carried out. An isotropic distribution of mechanical properties may result from fibres being randomly oriented within a joint. This indicates that rather than being highly directional, the joint may exhibit similar strength and performance characteristics in a variety of directions. Random fibre orientation can help distribute stress more evenly throughout the joint and offer improved resistance to crack propagation. However, there may be speculative effects on the joint’s strength from using a random fibre orientation. In comparison to a joint with oriented fibres, the random distribution of fibres could lead to decreased overall strength. This is due to the possibility that the fibres’ capacity for bearing loads may not be maximised in a particular direction, potentially resulting in less overall strength and stiffness of the joint. Further affecting the joint’s strength is the possibility that the absence of fibre alignment will lead to a less effective transfer of load between the fibres and the epoxy matrix. It is crucial to keep in mind that the precise effects of using random fibre orientation in the joint will depend on a number of variables, including the type of applied load, the characteristics of the coir fibres, the epoxy matrix, and the joint configuration. Finding out the relative strengths and performance variations could be done by conducting a comparative analysis with joints that have oriented fibres.
For the Lap Shear Adhesion samples, the specimens were prepared according to ASTM D 5868–01 Standard, (D-01, 2014), Figure 4A. Mild steel strips were used and cut according to the given dimensions by the standard, Figure 4B. The adhesive composites were prepared with different volume fraction of either coir or glass fibres (0 Vol. %−40 Vol. %). In the preparation of the composite, the epoxy resin (Kinetix R246TX) were mixed with Hardness (Kinetix H160) with the ratio of ¼ and the required amount of fibres were added. The second step was to add the composite on one end of the milt steel stipe and maintaining the gap when the second stipe placed by using some edge retainers. The prepared samples were left for 24 h at temperature of 60°C for curing according to the specification of the resin.
The samples were placed in a tensile machine (MTS 810 Material Test System) and the force vs. deformation data were captured. The load rate was 1.27 mm/min. Tensile Stress (σ) were determined using Eq.1.
where: F is the applied tensile force and A is the cross-sectional area of the adhesive joint perpendicular to the applied force.
Shear Stress (τ) was calculated as the force per unit area applied tangentially to the joint, resulting in a sliding or shearing effect between the bonded surfaces.
where: As is the shear area of the adhesive joint parallel to the applied force.
A sample piece of composite material was placed into the smart coater after a tensile test. The coater applies a crisp gold finish with a spray gun to improve the quality of the picture captured by the scanning electronic microscope, the spraying procedure was extended for one full minute. The material sample was scanned using scanning electron microscopy (Joel desktop).
Results and discussion
The experimental results of the lap shear adhesion experiments are presented in Figures 5–7 showing the tensile strength, shear strength and deformation, respectively. Figure 5 shows the maximum tensile strength during the experiment of various samples containing different volume percentages of coir or glass fibres associated with the error bars. The figure shows that the increase in the volume fraction of either coir or glass fibres reduces the bond strength. Samples bonded with epoxy/glass fibres composites shows better strength than the ones with epoxy/coir composite at all the volume fractions. This is mainly due to the fact that the glass fibre strength is stronger than the coir fibre (Marimuthu et al., 2019). On the other hand, when the composites is subjected to shear stress the failure would be due to delamination or fibre fracture rather than fibre cut or breakage. During the tensile loading and the stress is great in the transverse direction, the failure would be due to shear stress in the bonding area rather than failure of the composite itself. Similar findings were reported by Grefe et al. (2020).
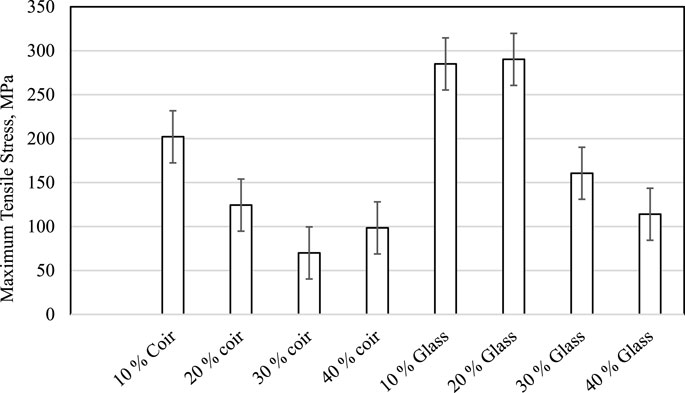
FIGURE 5. Maximum tensile strength of different bonding samples containing different epoxy composites.
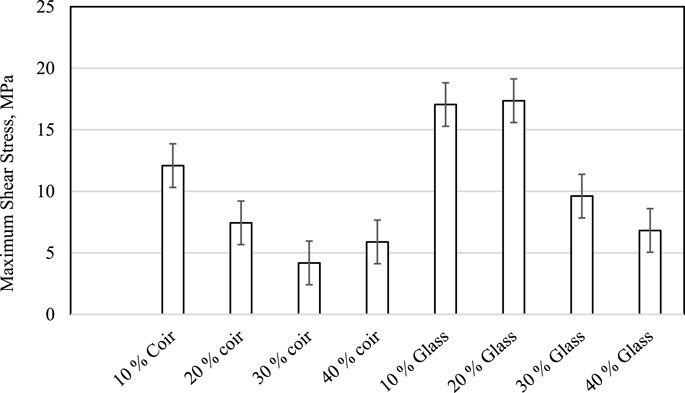
FIGURE 6. Maximum shear strength of different bonding samples containing different epoxy composites.
In the bonding area, the maximum shear stress of different samples is presented in Figure 6 for different composites used at different volume fraction percentages. The trend of the shear strength is similar to the one presented for the tensile strength in Figure 5. The increase in the volume fraction reduces the resistance to the shear in the bonded area of the samples. It should be mentioned here that the resistance to shea of 10% coir fibres/epoxy composites is very comparative to the ones of the 30% of glass fibres. In the bonding area seems to be that the glass fibres have poor interaction to the mild steel surface which coir fibres has better adhesion. In practical condition, fibre composites used on metal surfaces would be subjected to shear loading which would be the focus in the current study. In other words, it can say that coir fibres can replace glass fibres under this condition. With regarding of the deformation of the samples, Figure 7 show no remarkable different on the maximum deformation took place on the all the samples.
As the fibre volume fraction increases, the accessible space for the epoxy material decreases. The matrix is responsible for load transfer between the fibres and composite material cohesion, (Wang et al., 2020). When the volume fraction of either coir or glass fibres is high, there is insufficient space for the matrix to effectively distribute the load, resulting in a reduction in bond strength. The fibres themselves can also induce tension concentrations in composite materials. As the volume fraction of fibres increases, so does the fibre density within the bonding area. This can result in localised tension concentrations where the load is not distributed uniformly across the bonded region, (Zaghloul et al., 2022). These stress concentrations can initiate the propagation of cracks and weaken the overall bond strength. In addition, the characteristics of the fibres themselves are crucial. In the provided scenario, the mechanical properties of glass fibres are superior to those of coir fibres. Glass fibres have greater tensile strength and rigidity, which improves load transfer and adhesion strength. Conversely, coir fibres are comparatively weaker and less rigid, resulting in a decrease in overall bond strength when they comprise a greater volume fraction. In other words, the interaction between fibres and the matrix affects the bond strength. For load transfer, the bond between fibres and matrix material is crucial. The overall bond strength would be compromised if there is insufficient adhesion or bonding between the fibres and the matrix. Therefore, as the volume fraction of fibres increases, it becomes more difficult to maintain excellent interfacial bonding, which may result in weakened bonds. This can be further explained with the aid of the SEM micrographs in the coming discussion.
Figures 8, 9 are micrographs of the fractured surfaces of coir and glass/epoxy composites, respectively. Difficulties arose in analysing these surfaces due to the impact of the numerous sample preparation instruments on the surfaces. Therefore, only surfaces unaffected by the preparation procedure were selected for examination. Specifically, the surfaces of 20% fibre volume fraction epoxy composites were examined. The micrographs demonstrate two distinct failure modes. In the case of coir/epoxy composites, a distinct shear failure led to the sample’s ultimate fracture. This has been recently reported as well by (Sharma et al., 2023). In glass/epoxy composites, the fibres displayed a pull-out behaviour as opposed to fracturing. This observation lends credence to the notion that coir fibres are weaker than glass fibres. In addition, an increase in the fibre volume fraction is anticipated to reduce the interaction between the resin and fibres.
Conclusion
1. The experimental results indicate that the increase in the volume fraction of coir or glass fibers reduces the bond strength. Epoxy/glass fiber composites exhibit better strength compared to epoxy/coir composites at all volume fractions, primarily due to the stronger strength of glass fibers.
2. The shear strength of the samples follows a similar trend as the tensile strength, with an increase in volume fraction leading to reduced shear resistance in the bonded area. Interestingly, the resistance to shear of 10% coir fiber/epoxy composites is comparable to that of 30% glass fibers. This suggests that coir fibers could replace glass fibers in practical applications involving shear loading on metal surfaces.
3. The maximum deformation of the samples shows no remarkable differences among them.
4. As the volume fraction of fibers increases, the accessible space for the epoxy material decreases, affecting load transfer and composite cohesion. Insufficient space for the matrix to distribute the load effectively and localized tension concentrations due to increased fiber density can weaken the overall bond strength. Furthermore, surface preparation, adhesive type and application procedure, and environmental circumstances such as temperature and humidity can all affect the lap shear adhesion of fibre composites to metal. Understanding how these elements influence the bond’s lap shear strength can aid in the design of composite-metal joints and assure their long-term durability.
Data availability statement
The data analyzed in this study is subject to the following licenses/restrictions: No restrictions. Requests to access these datasets should be directed to YmVsYWwueW91c2lmQHVzcS5lZHUuYXU=.
Author contributions
All authors listed have made a substantial, direct, and intellectual contribution to the work and approved it for publication.
Conflict of interest
The authors declare that the research was conducted in the absence of any commercial or financial relationships that could be construed as a potential conflict of interest.
Publisher’s note
All claims expressed in this article are solely those of the authors and do not necessarily represent those of their affiliated organizations, or those of the publisher, the editors and the reviewers. Any product that may be evaluated in this article, or claim that may be made by its manufacturer, is not guaranteed or endorsed by the publisher.
References
Adams, R. D. (2021). Adhesive bonding: Science, technology and applications. Sawston, United Kingdom: Woodhead Publishing.
Ahmad, J., and Zhou, Z. (2022). Mechanical properties of natural as well as synthetic fiber reinforced concrete: A review. Constr. Build. Mater. 333, 127353. doi:10.1016/j.conbuildmat.2022.127353
Al-Maharma, A. Y., Patil, S. P., and Markert, B. (2022). “Environmental impact analysis of plant fibers and their composites relative to their synthetic counterparts based on life cycle assessment approach,” in Advances in bio-based fiber (Amsterdam, Netherlands: Elsevier), 741–781. doi:10.1016/b978-0-12-824543-9.00022-0
Albdiry, M. T., and Yousif, B. F. (2019). Toughening of brittle polyester with functionalized halloysite nanocomposites. Compos. Part B Eng. 160, 94–109. doi:10.1016/j.compositesb.2018.10.032
Alsufyani, T., and M’sakni, N. H. (2023). Part A: Biodegradable bio-composite film reinforced with cellulose nanocrystals from chaetomorpha linum into thermoplastic starch matrices. Polymers 15 (6), 1542. doi:10.3390/polym15061542
Altoubat, S., Karzad, A. S., Maalej, M., Barakat, S., and Junaid, T. (2020). “Experimental study of the steel/CFRP interaction in shear-strengthened RC beams incorporating macro-synthetic fibers,” in Structures. Amsterdam, Netherlands: Elsevier.
Azwa, Z., Yousif, B., Manalo, A., and Karunasena, W. (2013). A review on the degradability of polymeric composites based on natural fibres. Mater. Des. 47, 424–442. doi:10.1016/j.matdes.2012.11.025
D-01, A. (2014). Standard test method for lap shear adhesion for fiber reinforced plastic (FRP) bonding. West Conshohocken, PA, USA: American Society for Testing and Materials.
Eid Alajmi, A., Alotaibi, J. G., Yousif, B., and Nirmal, U. (2021). Tribological studies of bamboo fibre reinforced epoxy composites using a BOD technique. Polymers 13 (15), 2444. doi:10.3390/polym13152444
Grefe, H., Kandula, M. W., and Dilger, K. (2020). Influence of the fibre orientation on the lap shear strength and fracture behaviour of adhesively bonded composite metal joints at high strain rates. Int. J. Adhesion Adhesives 97, 102486. doi:10.1016/j.ijadhadh.2019.102486
Hariharan, M., Shamsudheen, S. P., Varghese, N., and Nair, A. B. (2023). “Application of UPR in pipeline corrosion: Protection and applications,” in Applications of unsaturated polyester resins. Amsterdam, Netherlands: Elsevier, 309–340.
Hasan, K. F., Al Hasan, K. N., Ahmed, T., György, S.-T., Pervez, M. N., Bejó, L., et al. (2023). Sustainable bamboo fiber reinforced polymeric composites for structural applications: A mini review of recent advances and future prospects. Case Stud. Chem. Environ. Eng. 8, 100362. doi:10.1016/j.cscee.2023.100362
Hu, Y., Zhang, J., Wang, L., Jiang, H., Cheng, F., and Hu, X. (2022). A simple and effective resin pre-coating treatment on grinded, acid pickled and anodised substrates for stronger adhesive bonding between Ti-6Al-4V titanium alloy and CFRP. Surf. Coatings Technol. 432, 128072. doi:10.1016/j.surfcoat.2021.128072
Khan, Z., Yousif, B., and Islam, M. (2017). Fracture behaviour of bamboo fiber reinforced epoxy composites. Compos. Part B Eng. 116, 186–199. doi:10.1016/j.compositesb.2017.02.015
Marimuthu, K. P., Kumar, S. M., Kumar, V. R., and Govindaraju, H. (2019). Characterization of mechanical properties of epoxy reinforced with glass fiber and coconut fiber. Mater. Today Proc. 16, 661–667. doi:10.1016/j.matpr.2019.05.143
Narish, S., Yousif, B., and Rilling, D. (2011). Adhesive wear of thermoplastic composite based on kenaf fibres. Proc. Institution Mech. Eng. Part J J. Eng. Tribol. 225 (2), 101–109. doi:10.1177/2041305x10394053
Reddy, J. (2006). Mechanics of advanced materials and structures. Mech. Adv. Mater Struct. 13, 443–455. doi:10.1080/15376490600862863
Reis, J. P., de Moura, M., and Samborski, S. (2020). Thermoplastic composites and their promising applications in joining and repair composites structures: A review. Materials 13 (24), 5832. doi:10.3390/ma13245832
Sarkar, P. K., and Kandasubramanian, B. (2021). Metals to polymer composites for submerged hull: A paradigm shift. Polymer-Plastics Technol. Mater. 60 (16), 1–35. doi:10.1080/25740881.2021.1930048
Shalwan, A., and Yousif, B. (2013). In state of art: Mechanical and tribological behaviour of polymeric composites based on natural fibres. Mater. Des. 48, 14–24. doi:10.1016/j.matdes.2012.07.014
Shanmugam, V., Karthikbabu, N., Rajendran, S., and Das, O. (2021). “Applications of various types of polymer-based composites,” in Polymer-based composites (Boca Raton, Florida, United States: CRC Press), 139–149.
Sharma, F., Kumar, R., and Bhowmik, S. (2023). “Response of coconut coir filler-reinforced epoxy composite toward cyclic loading: Fatigue property evaluation,” in Low cost manufacturing technologies: Proceedings of NERC 2022 (Berlin, Germany: Springer), 201–219.
Wang, Q., Li, T., Wang, B., Liu, C., Huang, Q., and Ren, M. (2020). Prediction of void growth and fiber volume fraction based on filament winding process mechanics. Compos. Struct. 246, 112432. doi:10.1016/j.compstruct.2020.112432
Xiang, W., Zhang, H., Chen, P., and Zhao, Q. (2023). Bonding performance of epoxy modified cement-based adhesive. J. Phys. Conf. Ser. IOP Publ. 2476, 012038. doi:10.1088/1742-6596/2476/1/012038
Yousif, B., and Chin, C. (2012). Epoxy composite based on kenaf fibers for tribological applications under wet contact conditions. Surf. Rev. Lett. 19 (05), 1250050. doi:10.1142/s0218625x12500503
Yousif, B., Shalwan, A., Chin, C. W., and Ming, K. (2012). Flexural properties of treated and untreated kenaf/epoxy composites. Mater. Des. 40, 378–385. doi:10.1016/j.matdes.2012.04.017
Keywords: natural fibres, lap shear adhesion, metals, glass fiber, engineering application
Citation: Alajmi AE, Alsaeed T, Alotaibi JG, Srelam JK and Yousif BF (2023) Investigating the lap shear adhesion of coir and glass-fibre reinforced epoxy bonding to mild steel with varying volume fractions. Front. Mech. Eng 9:1232643. doi: 10.3389/fmech.2023.1232643
Received: 31 May 2023; Accepted: 26 June 2023;
Published: 18 July 2023.
Edited by:
Alessandro Ruggiero, University of Salerno, ItalyReviewed by:
Petr Valasek, Czech University of Life Sciences Prague, CzechiaChenggao Li, Harbin Institute of Technology, China
Copyright © 2023 Alajmi, Alsaeed, Alotaibi, Srelam and Yousif. This is an open-access article distributed under the terms of the Creative Commons Attribution License (CC BY). The use, distribution or reproduction in other forums is permitted, provided the original author(s) and the copyright owner(s) are credited and that the original publication in this journal is cited, in accordance with accepted academic practice. No use, distribution or reproduction is permitted which does not comply with these terms.
*Correspondence: Belal F. Yousif, YmVsYWwueW91c2lmQHVzcS5lZHUuYXU=