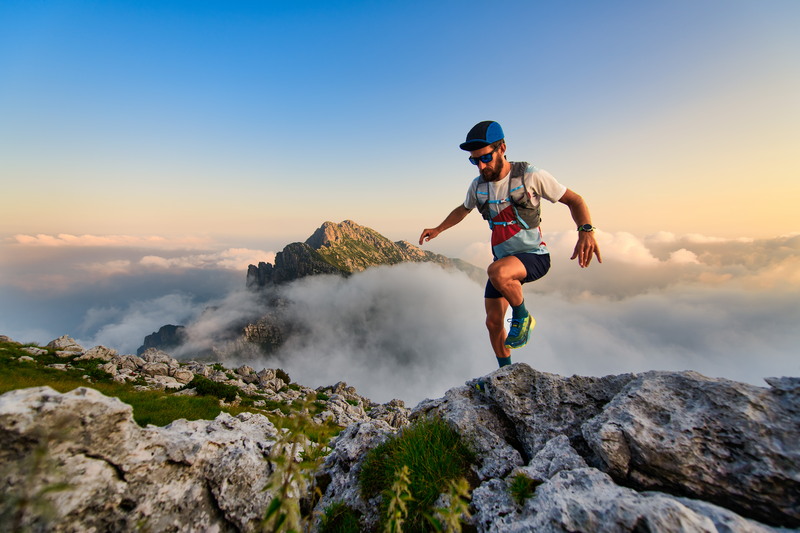
95% of researchers rate our articles as excellent or good
Learn more about the work of our research integrity team to safeguard the quality of each article we publish.
Find out more
MINI REVIEW article
Front. Mech. Eng. , 13 March 2023
Sec. Engine and Automotive Engineering
Volume 9 - 2023 | https://doi.org/10.3389/fmech.2023.1139385
This article is part of the Research Topic Fluids and Greases for Electrified Vehicles View all 6 articles
Hybrid electric and electric vehicles have represented a small portion of the automotive market for many years and mainly use current lubricants, typically automatic transmission fluids (ATFs). However, regulatory compliance to limit greenhouse gases and increased consumer demand have resulted in a rapid global transition to electrified vehicles. This has prompted the need for new advances in vehicle technology to improve efficiency and thereby increase range. Enabling and optimizing such advances requires a new generation of driveline lubricants. Incorporating an electric motor in a transmission or axle, where the motor is exposed to the gear box lubricant, creates new challenges that focus attention on lubricant characteristics that were previously not differentiating features, for example, electrical and thermal properties. Additionally, lubricants must now also be compatible with the constituents used in electric motors which include new polymeric materials and, in some cases, exposed copper. Compatibility tests of these polymers vary within the industry and the risk of copper corrosion in these applications is not always properly assessed by current specification tests. In this paper we will begin with a brief history of electric vehicles, highlight how driveline lubricants, specifically ATFs, have evolved over the years to meet new hardware requirements and then describe the performance requirements expected of lubricants specifically designed for vehicles with electric drive units (EDUs). Our primary goal, however, is to summarize the recent literature that illustrates the changing importance of various lubricant performance properties, new proposed test methods and offer some insight into future e-lubricant evolution.
The early development of self-powered vehicles saw all types of propulsion: steam, gasoline, kerosine, coal gas, hydrogen/oxygen mixtures and electric power (ThoughtCo, 2021a). At the turn of the 20th century gasoline internal combustion engines (ICEs) were dominant but electric vehicles (EVs) remained a viable option and even a hybrid electric vehicle (HEV) was available. During this time driving was primarily local due to poor road conditions between municipalities and EV range anxiety was not a concern. Electric cars had several advantages over gasoline powered vehicles as they were quiet, did not exude unpleasant exhaust and did not require manual changing of gears or a hand crank to start (United States Department of Energy, 2014). Electric cars could be recharged at public garages, though home chargers were also available (General Electric Company, 1913).
However, as the roads connecting cities improved, demand for longer range vehicles grew. The introduction of the conveyor belt-based assembly line, by Henry Ford in 1913, enabled the mass production of gasoline powered cars, and along with the production of inexpensive gasoline made abundant by the Texas oil boom, gasoline vehicles became the best economic choice (ThoughtCo, 2021b). At the start of 1913, there were 131 different gasoline powered vehicle choices compared with 25 EV choices. The least expensive electric cars cost ∼$2,000 (∼$56,000 in today’s currency) (von Kéler, 1913a) while gasoline cars started at ∼$600 (∼$16,000 in today’s currency) (von Kéler, 1913b). EVs were essentially gone by 1935, making only a minor resurgence in the 1970s as a response to the oil embargo (United States Department of Energy, 2014).
Driveline fluids have always evolved to meet new hardware needs. When automatic transmissions were first introduced into the market, they were originally lubricated with engine oil. However, it soon became apparent that this was not the best approach and specialized fluids began to emerge. In 1949, General Motors introduced the first specification, Type A, for mineral oils used in automatic transmissions (Newcomb et al., 2007). Since that time, transmission hardware continued to evolve, driving a stream of ever advancing fluid specifications. From the late 1950s through the mid-1970s, improvements were made to enhance ATF resistance to oxidation and to improve low temperature fluidity through the reduction of low temperature viscosity. The focus on reducing low temperature viscosity continued through to the 1990s, along with some further improvements in wear and oxidation resistance, and the optimization of friction characteristics (Newcomb et al., 2007). Starting in the mid-1990s, the desire to improve corporate average fuel economy (CAFÉ) led to the use of new hardware capable of using low viscosity fluids. These lower viscosity lubricants however were still required to protect hardware and maintain other performance attributes, and to accomplish this, the lubricant chemistry was further advanced. Today, most ATFs have a 100°C kinematic viscosity near 6.0 cSt, but some are as low as 4.5 cSt and 3.5 cSt. In general, the fluid specifications followed new hardware development, though recently there have been examples of hardware and fluids being developed simultaneously (Masuda et al., 2018; Tada et al., 2022; Tokozakura et al., 2022).
The requirement to reduce greenhouse gases has accelerated the incorporation of electric motors into the automobile drivetrain. When Toyota introduced the Prius HEV in 1997, the EDU had been developed with the ATF lubricant of the time, and many current EDUs use present day transmission fluids (Canter, 2022). Today, efforts are underway to understand how automotive lubricants in contact with an electric motor can enable more advanced performance.
A broad review of new lubricant performance needs for electric and hybrid vehicles was published recently (Chen et al., 2020) and includes both academic studies as well as industrial development. This paper focusses primarily on recent industry published work, but also complements the previous review by highlighting some less recent but relevant work.
The incorporation of an e-motor into the drivetrain introduces new safety concerns not applicable to ICE vehicles. One concern is whether the lubricant could provide a path for the electrical current powering the electric motor to leak through to the drivetrain housing, creating a shock hazard. This has focused attention on the lubricant’s electrical characteristics. Beyer et al. (2019), in addition to corrosion, heat transfer and material compatibility, also shared work measuring the impact of lubricant electrical conductivity on an HEV driveline unit. Three lubricants covering a wide range of electrical conductivities were used in the study and the leakage current was determined by measuring the case resistance from the energized motor to the unit housing following a modified ISO 6469-3 procedure (International Standard Organization, 2011). It was found that case resistance is linear with respect to lubricant resistivity (inverse conductivity). The HEV driveline unit cell constant was determined from the slope of this curve and could then be used to predict the lubricant conductivity that would result in a shock hazard. A more detailed presentation of this work, detailing the impact of lubricant conductivity on three different EDUs was presented at two SAE meetings (Hunt et al., 2019). Though the lubricants involved were not sufficiently conductive to create a shock hazard with these particular EDUs, the differences illustrated did establish that understanding the impact of lubricant electrical conductivity on specific hardware is crucial.
McFadden et al. (2016) published a comprehensive study on the factors that impact lubricant electrical conductivity of new and used ATFs. The electrical conductivity of new lubricants primarily depended on the amount and type of additive chemistry contained within the lubricant, and secondarily on the lubricant viscosity. The electrical conductivity of hydrocarbon base oils, typically used in ATFs, was so low as to be insignificant. However, used ATFs were found to possess higher conductivity than new, and it was determined that this was a consequence of oxidation. The study also established that the contribution from wear metals, whether as suspended particles or solubilized metal, was insignificant. Though this study did not include the impact of water, this was later measured and presented (Newcomb, 2018). The addition of 2000 ppm water to a new ATF resulted in increased conductivity, but once the water was thermally removed the conductivity returned to its nominal value.
Rodríguez et al. (2022) further investigated the effect of oxidation on lubricant conductivity using an 8-element full-factorial experimental design (23) with air flow, time, and temperature as the independent variables. These conditions were applied to three different lubricants and resulted in somewhat different models and through principal component analysis the authors were able to classify different oxidation/degradation states.
The Coordinating Research Council (CRC) (Coordinating Research Council, 2022) has recently released a report on thermal and electrical properties of 29 base oils, which includes a description of the base oil types. This provides data for a wider range of base oils than previously reported.
Several original equipment manufacturers (OEMs) now specify both new and aged lubricant electrical conductivity/resistivity as part of their specifications for EDU lubricants.
The automotive industry, like many others, has relied on the copper strip test, described in test procedures such as the ASTM D130, to anticipate copper corrosion problems and adjust lubricant chemistry to mitigate them. However, the test results are qualitative and subject to variation. Electric motor burn out, initiated by copper corrosion, has occurred even though the lubricant in use passed previously established copper strip test criteria (Hunt & Prengaman, 2020). This has prompted the industry to develop two new corrosion tests; a wire corrosion test (WCT) developed at the Lubrizol Corporation and introduced in 2016 (Gahagan & Hunt, 2016), and a conductive deposit test (CDT) developed at IFAS (Institute for Fluid Power Drives and Systems) at RWTH Aachen University. Both test methods have gained broad acceptance among groups developing future EDU lubricants (Canter, 2022; Hunt et al., 2023). In particular, much has been published on the WCT (Hunt, 2017; Hunt et al., 2017; Hunt, 2018), including its application to other metals (Bares et al., 2020). Both tests are recommended in the SAE J3200™ report on fluids for electrified drivetrains (SAE International, 2022), and are currently under review by ASTM and other standard organizations for adoption.
In addition to the copper windings, the electric motor introduces several different polymers in the form of magnetic wire insulation, flexible sheets and elastic bindings. Hard plastics are also becoming more common, replacing metal parts such as bearing cages, to reduce weight. There is currently no standard method agreed upon to test such parts, in particular the magnet wire insulation which can be quite complex (Hitachi Metals, 2019). Different approaches have been reported with some involving thermal shock tests with water contaminated lubricant (Canter, 2022), and others involving isothermal soak tests in pure lubricant (Gahagan, 2017). The current state of testing is discussed in SAE J3200 (SAE International, 2022).
ATFs have always acted as a cooling medium, a standard lubricant function. In conventional transmissions the cooling characteristics of all ATFs have been considered both adequate and equivalent. However, effective cooling of the electric motor can improve vehicle efficiency as resistance of the copper wires increases with temperature. Additionally, high temperatures can cause demagnetization of permanent magnets.
The four lubricant properties that affect heat transfer are density, ρ, viscosity, ν, thermal conductivity, Κ, and specific heat capacity, C. These properties are primarily related to the specific base oils and not the additive chemistry. The heat transfer ability can be quantified using a “Figure of Merit” or Mouromtseff number, θ, which is related to these properties by the expression:
where a, b, c, and d, are constants that are dependent on the nature of the lubricant flow regime (Le Pera & Oswald, 1974; Yu & Liu, 2013).
Mineral oils possess similar thermal conductivity (though the API group IV tend to have somewhat higher values), heat capacity and density. Additionally, the flow regimes expected and, in some cases determined (Newcomb et al., 2020), are primarily turbulent. In such situations, the heat transfer is mainly driven by viscosity, the lower the viscosity, the greater the heat transfer. However, to understand the possible impact base oils exert on heat transfer their thermal properties must be known. In 2019, both Kwak et al. (2019) and Narita & Takekawa, (2019) published lists of base oils with their respective thermal properties at a single temperature point. The base oils listed in these papers were also coded with limited information on their exact nature. In contrast, the CRC report, published in 2022, identifies the specific 29 base oils whose properties were measured and provides temperature dependent information on their thermal properties (Coordinating Research Council, 2022). These data are very useful to those studying the impact of base oil thermal properties on heat transfer. Work is also underway to measure the heat transfer using rigs (Richenderfer, 2021; Canter, 2022) created to mimic various flow regimes and in actual EDU hardware (Whitticar, 2022).
The higher rotational speeds possible with electric motors has raised concerns about air entrainment and high-speed wear. Though no new industrial standards have been proposed, there is ongoing work to explore if this is needed (Canter, 2022; Peerzada, 2022; Pellkofer, 2022; SAE International, 2022; Woydt, 2022).
Thermal spikes, due to the heat generated by the electric motor, have led to concerns that e-lubricants may require greater oxidation resistance and therefore new evaluation methods. Though under investigation, at this time current oxidation tests are considered adequate and there is no need to develop new oxidation tests (SAE International, 2022).
Gupta (2012), in his Master’s Thesis, investigated the impact of lubricant viscosity on the powertrain of a Toyota Prius modified to run in EV, HEV or Plugin Hybrid Electric Vehicle (PHEV) modes. In part, he found that the efficiency of the system was more sensitive to viscosity while in EV mode due to the lower unit operating temperature. He reasoned that since electric motors were generally three times more efficient than ICEs, any viscosity related efficiency gains would be three times greater. Lower viscosity lubricants would therefore have a greater efficiency impact on EVs than their corresponding ICE counterparts.
Lowering lubricant viscosity is also an assured method to improve heat transfer and thus reduce resistive losses in the electric motor, improving efficiency and therefore range.
Though lower viscosity fluids introduce potential problems with hardware protection, low temperature sealing and volatility, efforts are underway to address these challenges. For example, Tokozakura et al. (2022) has discussed countermeasures to these potential problems which include improved additive chemistry to counter wear and fatigue, and the redesign of seals for proper function at low temperatures. Shamszad et al. (2015) presented bench test and vehicle field test results that demonstrated properly formulated low viscosity ATFs were effective at protecting hardware designed for higher viscosity lubricants. Canter (2022), Lotfi (2021) has described work at ExxonMobil to manufacture low viscosity PAOs that are less volatile than today’s PAOs of similar viscosity.
EDU hardware continues to evolve rapidly to improve efficiency and thereby vehicle range. The time frame is such that optimizing the lubricant to the hardware or limiting the hardware design due to performance of the current lubricant is no longer a viable strategy. At the 2022 SAE International Powertrain Fuels & Lubricants meeting, Tokozakura et al. (2022) and Tada et al. (2022) described in two related papers how Toyota and ENEOS worked together to create Toyota’s newest e-transaxle lubricant. It is expected that this type of co-development will become more commonplace.
The field of lubricants for electrified vehicles is evolving at a rapid pace, and new learnings are frequently published. Though this review is not comprehensive, we hope that the material summarized here will aid in disseminating the latest e-lubricant developments.
TN conducted the literature search, evaluated the information, and wrote the paper.
Author TN was employed by the company The Lubrizol Corporation.
All claims expressed in this article are solely those of the authors and do not necessarily represent those of their affiliated organizations, or those of the publisher, the editors and the reviewers. Any product that may be evaluated in this article, or claim that may be made by its manufacturer, is not guaranteed or endorsed by the publisher.
Bares, J., Hunt, G., Prengaman, C., Wicks, J., and Nicholson, S. (2020). Establishing long-term corrosion protection of copper-based alloys in modern transmissions. SAE Int. J. Fuels Lubr. 13 (3), 251–264. doi:10.4271/04-13-03-0016
Beyer, M., Brown, G., Gahagan, M., Higuchi, T., Hunt, G., Huston, M., et al. (2019). Lubricant concepts for electrified vehicle transmissions and axles. Tribol. Online 14, 428–437. doi:10.2474/trol.14.428
Canter, N. (2022). Tribology and lubrication for E-mobility: Findings from the inaugural STLE conference on electric vehicles. STLE whitepaper. Available at: https://www.stle.org/files/Technical_Library/White_Papers/Tribology_and_Lubrication_for_E-Mobility/files/White_Papers/Tribology_and_Lubrication_for_E-Mobility.aspx.
Chen, Y., Jha, S., Raut, A., Zhang, W., and Liang, H. (2020). Performance characteristics of lubricants in electric and hybrid vehicles: A review of current and future needs. Front. Mech. Eng. 6, 571464. doi:10.3389/fmech.2020.571464
Coordinating Research Council (2022). “Thermal and electrical properties of lubricants for hev/ev applications,”. CRC Report No. AVFL-37.
Gahagan, M. P. (2017). Lubricant technology for hybrid electric automatic transmissions. Technical Paper 2017-01-2358. (Warrendale, PA: SAE International). doi:10.4271/2017-01-2358
Gahagan, M. P., and Hunt, G. J. (2016). New insights on the impact of automatic transmission fluid (ATF) additives on corrosion of copper -the application of a wire electrical resistance method. Int. J. Automot. Eng. 7 (4), 115–120. doi:10.20485/jsaeijae.7.4_115
General Electric Company (1913). Advertisement in “electricity’s part in the automobile”. Sci. Am. 108, 24.
Gupta, A. (2012). Characterization of engine and transmission lubricants for electric, hybrid, and plug-in hybrid vehicles (Columbus, OH: Ohio State University). [master’s thesis].
Hitachi Metals (2019). Magnet wire - selection and use directions for magnet wire, product brochure. CAT.NO.KVE200B. Available at: https://www.hca.hitachi-cable.com/products/hca/products/materials/pdf/MagnetWire_en.pdf (accessed February 5, 2019).
Hunt, G., Javaid, R., Simon, J., Peplow, M., and Prengaman, C. (2023). Understanding conductive layer deposits: Test method development for lubricant performance testing for hybrid and electric vehicle applications. SAE Int. J. Elec. Veh. 12, 2. doi:10.4271/14-12-02-0014
Hunt, G. J., Gahagan, M. P., and Peplow, M. A. (2017). Wire resistance method for measuring the corrosion of copper by lubricating fluids. Lubr. Sci. 29, 279–290. doi:10.1002/ls.1368
Hunt, G., McFadden, C., Saxton, C., Donnelly, K., and Newcomb, T. (2019). Establishing lubricant conductivity limits. Presented at SAE PFL Germany 2018 and SAE WCX 2019.
Hunt, G. (2018). New perspectives on lubricant additive corrosion: Comparison of methods and metallurgy. Technical Paper 2018-01-0656. (Warrendale, PA: SAE International). doi:10.4271/2018-01-0656
Hunt, G. (2017). New perspectives on the temperature dependence of lubricant additives on copper corrosion. SAE Int. J. Fuels Lubr. 10 (2), 521–527. doi:10.4271/2017-01-0891
Hunt, G., and Prengaman, C. (2020). Understanding vapor and solution phase corrosion of lubricants used in electrified transmissions. Technical Paper 2020-01-0561. (Warrendale, PA: SAE International). doi:10.4271/2020-01-0561
International Standards Organization (2011). Electrically propelled road vehicles – safety specifications - Part 3: Protection of persons against electric shock. ISO 6469-3:2011 (E).
Kwak, Y., Cleveland, C., Adhvaryu, A., Fang, X., Hurley, S., and Adachi, T. (2019). Understanding base oils and lubricants for electric drivetrain applications. Technical Paper 2019-01-2337. (Warrendale, PA: SAE International). doi:10.4271/2019-01-2337
Le Pera, M. E., and Oswald, G. E. (1974). Heat transfer characteristics of lubricants for internal-combustion engines. Industrial Eng. Chem. Prod. Res. Dev. 13 (3), 209–213. doi:10.1021/I360051A011
Lotfi, B. (2021). “Extending drive range and enhancing thermal management in EVs using next-generation PAOs,” in Presented at the Inaugural STLE Tribology & Lubrication for E-Mobility Conference.
Masuda, K., Nakao, H., Komatsubara, H., Kurosawa, O., Yamada, K., Ishikawa, K., et al. (2018). Super low viscosity ATF; AW-2. Technical Paper 2018-01-1756. (Warrendale, PA: SAE International). doi:10.4271/2018-01-1756
McFadden, C., Hughes, K., Raser, L., and Newcomb, T. (2016). Electrical conductivity of new and used automatic transmission fluids. SAE Int. J. Fuels Lubr. 9 (3), 519–526. doi:10.4271/2016-01-2205
Narita, K., and Takekawa, D. (2019). Lubricants technology applied to transmissions in hybrid electric vehicles and electric vehicles. Technical Paper 2019-01-2338. (Warrendale, PA: SAE International). doi:10.4271/2019-01-2338
Newcomb, T. (2018). Effect of hybrid & electric vehicles on lubricant evolution. Presented at STLE National Meeting.
Newcomb, T., Jayne, D., Richenderfer, A., Brown, G., Short, A., McFadden, C., et al. (2020). “Thermal properties and heat transfer performance of driveline lubricants,” in Presented at the SAE 2020 powertrains, fuels & lubricants digital summit (Warrendale, PA: SAE International).
Newcomb, T., Tipton, C., and Jao, T. (2007). Automatic transmission and driveline fluids. Technical Paper 2007-01-3988. (Warrendale, PA: SAE International). doi:10.4271/2007-01-3988
Peerzada, S. (2022). “A study of the effects of foam and air entrainment and defoamer performance in electric vehicle fluids,” in Presented at the 2nd STLE Tribology & Lubrication for E-Mobility Conference.
Pellkofer, J. (2022). “Method to assess the scuffing load capacity of lubricants for gears in E-vehicles using an FZG gear test rig,” in Presented at the 2nd STLE Tribology & Lubrication for E-Mobility Conference.
Richenderfer, A. (2021). “Heat transfer performance of fluids for EVs,” in Presented at the Inaugural STLE Tribology & Lubrication for E-Mobility Conference.
Rodríguez, E., Rivera, N., Fernandez-Gonzalez, A., Perez, T., Gonzalez, R., and Hernandez-Battez, A. (2022). Electrical compatibility of transmission fluids in electric vehicles. Tribol. Int. 171, 107544. doi:10.1016/j.triboint.2022.107544
SAE International (2022). Fluid for automotive electrified drivetrains. Report J3200_202210. doi:10.4271/J3200_202210
Shamszad, M., Abraham, W., Ishizaki, K., and Streck, K. (2015). Lowering ATF viscosity without compromising hardware durability. Presented at the SAE Transmission & Driveline Symposium.
Tada, A., Aizawa, K., Susukida, Y., Tokozakura, D., Nakamura, T., Sano, T., et al. (2022). Development of transaxle fluid for electrification vehicles: Design of novel additive formulation. Technical Paper 2022-01-1102. (Warrendale, PA: SAE International). doi:10.4271/2022-01-1102
ThoughtCo (2021a). A history of the automobile. Available at: https://www.thoughtco.com/who-invented-the-car-4059932 (accessed January 31, 2023).
ThoughtCo (2021b). The history of electric vehicles began in 1830. Available at: https://www.thoughtco.com/history-of-electric-vehicles-1991603 (accessed January 31, 2023).
Tokozakura, D., Sano, T., Nakamura, T., Tada, A., Susukida, Y., Moritani, H., et al. (2022). Development of transaxle fluid for electrified vehicles: Validating optimized viscosity through targeted hardware testing. Technical Paper 2022-01-1103. (Warrendale, PA: SAE International). doi:10.4271/2022-01-1103
United States Department of Energy (2014). Matulk, R. “The history of the electric car”. Available at: www.energy.gov/articles/history-electric-car (assessed February 3, 2023).
von Kéler, T. M. R. (1913b). What gasoline pleasure car can I buy? Sci. Am. 108, 44. doi:10.1038/scientificamerican01111913-44
Whitticar, D. (2022). Full-scale EDU and DHT testing capabilities used to develop next generation e-driveline fluids in Presented at the 2nd STLE Tribology & Lubrication for E-Mobility Conference.
Woydt, M. (2022). Measuring friction and wear and electrical properties of tribosystems – the basis for electrified powertrains? in Presented at the 2nd STLE Tribology & Lubrication for E-Mobility Conference.
Keywords: e-lubricant electrical properties, EV leakage current, e-lubricant corrosion tests, e-lubricant thermal properties, low viscosity e-lubricants, bespoke e-lubricants, SAE J3200
Citation: Newcomb T (2023) A brief review of the rapid transformation of driveline lubricants for hybrid electric and electric vehicles. Front. Mech. Eng 9:1139385. doi: 10.3389/fmech.2023.1139385
Received: 06 January 2023; Accepted: 24 February 2023;
Published: 13 March 2023.
Edited by:
Volker Null, Shell, GermanyReviewed by:
Michael Leighton, Anstalt für Verbrennungskraftmaschinen List, AustriaCopyright © 2023 Newcomb. This is an open-access article distributed under the terms of the Creative Commons Attribution License (CC BY). The use, distribution or reproduction in other forums is permitted, provided the original author(s) and the copyright owner(s) are credited and that the original publication in this journal is cited, in accordance with accepted academic practice. No use, distribution or reproduction is permitted which does not comply with these terms.
*Correspondence: Timothy Newcomb, dGltb3RoeS5uZXdjb21iQGx1YnJpem9sLmNvbQ==
Disclaimer: All claims expressed in this article are solely those of the authors and do not necessarily represent those of their affiliated organizations, or those of the publisher, the editors and the reviewers. Any product that may be evaluated in this article or claim that may be made by its manufacturer is not guaranteed or endorsed by the publisher.
Research integrity at Frontiers
Learn more about the work of our research integrity team to safeguard the quality of each article we publish.