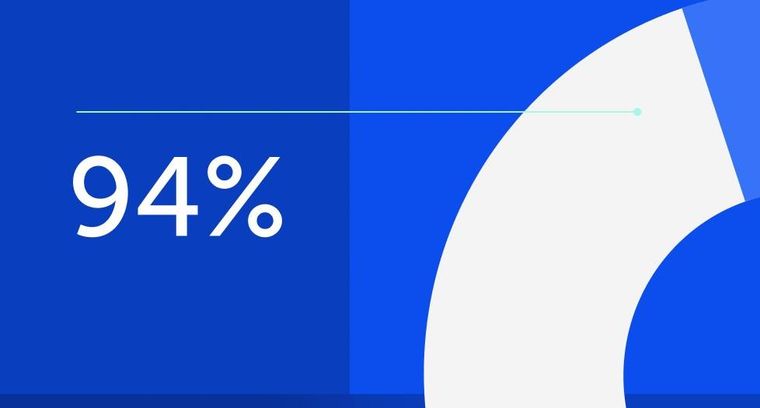
94% of researchers rate our articles as excellent or good
Learn more about the work of our research integrity team to safeguard the quality of each article we publish.
Find out more
ORIGINAL RESEARCH article
Front. Mech. Eng., 12 January 2023
Sec. Engine and Automotive Engineering
Volume 8 - 2022 | https://doi.org/10.3389/fmech.2022.1090152
This article is part of the Research TopicNew Developments in Vehicle Thermal ManagementView all 6 articles
On par with rapid motorization, excessive energy demand and air pollution have become major challenges in the global context. Fuel economy programs and emission reduction targets have proven to be among the most effective in mitigating these issues. In developing successful fuel economy programs and policies, understanding the factors affecting the fuel consumption of road vehicles is essential. Auxiliary engine loads are one of the commonest factors affecting a vehicle’s fuel economy performance. An auxiliary engine load is defined as the energy utilized to operate auxiliary equipment that draws its power from the vehicle’s engine. This study was limited to light duty vehicles, and an analytical method was adopted to assess the fuel economy impact of the auxiliary equipment in terms of air-conditioning load, alternator load, and water pump and steering pump load. As one of the main deliverables, the study developed a novel approach for estimating and modeling the air-conditioning load which is the major auxiliary energy consumer. For an average car of 100 brake horsepower (bhp) (74.7 kW), the engine auxiliary equipment consumes approximately 13.130 kW of power at an engine operating speed of 3,000 RPM, which amounts to 17.6% of the total bhp output. The major contributors to engine power demand are the air-conditioning unit and the alternator, which account for over 97% of the total auxiliary power requirement, while the water-pump and power steering-pump use relatively little power at 3% of the total auxiliary power demand. The novelty of the method adopted during this study is that it theoretically determines the major contributor of the auxiliary power demand, the air-conditioning load, whereas prior reports have used approaches involving empirical methods.
In order to align with sustainable development targets, regulations and goals for fuel economy and emissions have been imposed at both the national and international level. When developing policies related to sustainable road transportation and related energy consumption, it is important to identify the factors contributing to increased energy consumption and to develop a baseline model using both theoretical and empirical approaches. The major sources of power demand in a light duty vehicle (LDV) are the energy needed to overcome the aerodynamic drag resistance, rolling resistance, grade resistance, and inertial resistance. Auxiliary equipment is also assumed to be a major drain on power and its impact was measured and quantified in this study. The research scope encompassed the main auxiliary devices, the air-conditioning unit, the alternator, water pump, and power-steering pump. In the next section, we review the literature on this subject, discuss the findings, and identify the gaps in the previous work.
Several previous studies have been carried out by researchers to evaluate the impact of auxiliary engine loads on the overall power demand and fuel consumption of a given vehicle. The report by Welstand et al. (2003) revealed that belt-driven auxiliary units had a close, proportional relationship with engine speed, with higher power demand at higher engine speeds. The study found that during normal engine idling (800–1000 RPM), the auxiliary power demand was 1.75 kW with the air-conditioning (A/C) unit turned off and 3.25 kW with the A/C turned on. At a higher engine speed of around 3000 RPM, the auxiliary power demand increased to 9–9.5 kW with the A/C on. Also, the A/C system required a higher driving torque than any other auxiliary equipment. A common characteristic of engine belt-driven auxiliary units is that their input power for operation is proportional to the engine speed, while their output power may not be related to engine speed. The study conducted by Nadamoto and Kubota revealed that the compressor was the most significant component affecting the power demand because it was responsible for a 77–89% increase in energy consumption (Nadamoto and Kubota, 1999). The impact on energy demand of the subordinate components has been determined and is 6–12% from the blower, 4–10% from the cooling fan, and 0.7–2% from the clutch (Nadamoto and Kubota, 1999). The A/C system plays a crucial role when it comes to electric vehicles (EVs), including both hybrid electric vehicles (HEVs) and battery electric vehicles (BEVs). EVs have insufficient waste heat to warm up the cabin and the climate control system has a substantial effect on the energy consumption efficiency and operating range. The mobile climate control systems based on the magnetocaloric and thermoelectric effects could be utilized to optimize the range efficiency (Zhaogang, 2014). The vapor compression refrigeration-dedicated, combination heater-A/C systems, reversible vapor compression heat pump A/C systems, and non-vapor compression A/C systems have been critically appraised by Zhang et al. (2018) as the latest developments in air-conditioning and heat pump systems for EVs.
The vehicle’s water pump may be mechanical or electric. The major drawback of a mechanical pump is that it pumps in proportion to engine speed and not according to the heat rejection requirements (Tasuni et al., 2016). Hence, it is necessary to evaluate the operating characteristics of the water pump and its impact on fuel consumption. In general, 1–2 kW of power is transferred from the crankshaft to the water pump (Patel et al., 2013). The efficiency of a water pump is quite low due to its losses. According to the published data, the mechanical efficiency of a water pump typically lies between 37.5% and 55.0% within an RPM range of 2,000–5,000, respectively (Wang et al., 2015a). The lack of efficiency in the water pump operation can be attributed to three main causes: mechanical, hydraulic, and volumetric losses (Tasuni et al., 2016). The mechanical losses result from friction associated with the dynamic parts of the pump, hydraulic losses occur as internal losses in the impeller, while volumetric losses are due to the leakage of liquid from the discharge side to the suction side of the centrifugal pump (Tasuni et al., 2016).
There has been an increasing demand for electric power since automotive technological advancements have replaced many of the mechanical devices with electrical and electronic devices. Two major evolutions in automobile electrical systems can be stated: the change from 6V to 12V systems and the switch from DC generators to AC alternators (Cho et al., 2008). The AC alternator can be considered as the most important piece of equipment in the electrical system. The electrical power of a vehicle is generated as a direct result of the engine consuming fuel to drive the alternator (Bradfield, 2008). With a nominal efficiency level of 40% in the engine, 98% in the belt-train and 55% in the alternator, the electrical generation system has an overall efficiency of around 21% (Bradfield, 2008). With regard to the losses in the alternator, they can be stratified into three types: electrical, magnetic, and mechanical (Bradfield, 2008). The consensus in the literature, states that in general, the output power losses increase with increasing engine speed. Consequently, the increase in alternator losses can be said to be proportional to the increase in operating fuel consumption.
Nowadays, most of the previously belt-driven engine auxiliaries are driven by electricity. For example, the water/coolant pump and the power steering pump are more often electrically powered. Furthermore, with the increasing utilization of electric vehicles (EVs), including HEVs and BEVs, the necessity for electrically powering auxiliaries has increased. Estimating the power demand of the auxiliary loads is thus of greater importance than ever, since it directly affects an EV’s range and could enhance the range anxiety of users (Roskilly et al., 2015) (Weldon et al., 2016). The approach proposed by this study could eventually result in the development of a range prediction algorithm for EVs. Accurate range prediction is the key to minimizing range anxiety and helping drivers make the best use of their available energy (Wu et al., 2015) (Cuma and Koroglu, 2015). Thus, an accurate theoretical model is required to determine the major auxiliary load contributors, which is a major focus of this study.
In most of the previously published work, the auxiliary load determinations were performed using experimental evaluations, whereas in the proposed study, each sub-auxiliary system was analytically appraised using the governing equations, which can be considered a new contribution of this study. Against the empirical approach adopted in the literature, this study delves into a theoretical approach, especially pertaining to the determination of AC load. In the next sections, the power demands of the AC system, the alternator, the mechanical water pump, and the power-steering pump are characterized and analyzed.
The AC unit is an auxiliary device designed to ensure the comfort of the passengers by regulating the temperature and the relative humidity (RH) within the cabin. The AC system consists of the compressor, the belt, the blower, the cooling fan, the condenser, the receiver/drier, inline filter kit, expansion valve, hose assembly, and evaporator core. In this section, the AC load is theoretically modeled, and the total AC load is determined by the summation of the individual heat load contributors.
Eq. 1 gives the summation of the major contributors to automotive AC load. Each of these load types will be discussed under the following sections and the total AC load, (
Heat is dissipated from the human body as a result of metabolism, and this specific type of heat load also contributes to the total heat load of the AC. The metabolic load has two main components: the sensible heat load and the latent heat load. The sensible heat load refers to the heat given off from the human body by convection and radiation, whereas the latent heat load refers to the heat dissipated through evaporation.
In Eqs 6, 7,
In Eq. 9,
TABLE 1. Metabolic load calculation of a passenger car. Data taken from (Martinez et al., 2020).
The total sensible heat production rate of two passengers within a vehicle is determined by Eq. 6, whereas the total latent heat production rate is determined as in Eq. 7. When determining the metabolic rates of the occupants, the driver’s metabolic rate is considered with respect to moderate arm work since the driver is actively engaged in the task of driving, whereas the passenger is assumed to be just sitting.
Hence, total metabolic load can be determined using Eqs 8, 9.
In Eqs 8, 9,
Then, using the determined values for
Thus, the mean metabolic load of a car with two passengers in a local context can be modeled as portrayed in this section. The estimated mean metabolic heat load for an average car plus two occupants is calculated to be 447.26 W.
Figure 1 depicts a three-dimensional distribution of the metabolic heat load on par with the variation in body surface area using the Du Bois method for a two-occupant car cabin (a driver with medium arm work and one passenger at rest). The colored bar represents the intensity of the metabolic heat dissipation. It is conspicuous that the higher the weight and height of the occupants, the greater the metabolic heat dissipation.
Figure 2 portrays the surface plot of the metabolic heat load distribution against the body surface area and the number of passengers. It can clearly be seen that the greater the number of passengers, the higher the metabolic heat dissipation into the cabin. Moreover, the plot shows that a larger body surface area coincides with a higher metabolic heat load. The factors highlighted in Figure 1 and Figure 2 should be taken into account when designing automotive AC systems.
The ambient temperature affects the calculation of external and internal cooling loads of an automotive AC. The ambient load can be expressed as in Eq. 13.
In Eq. 13,
The term
The R value can be determined using the formula shown in Eq. 17.
In Eq. 17,
In Eq. 18, the terms can be elaborated as follows:
The ambient load varies with respect to the air velocity along the vehicular surface. The air velocity can be considered similar to the vehicular speed considering the relative motion between them. For the different driving cycles depicted in Table 2, the average speed varies among them, and therefore, the ambient load changes respectively. Assuming that the average speed estimated by the worldwide harmonized light vehicle test procedure (WLTP) is 12.91 m/s, the
When determining the ambient load, the surface areas of the vehicular exterior should be taken into account. In this study, the vehicular surface area was estimated using the mean vehicular surface area,
The ambient load of the A/C of an average passenger car can be estimated as 2,380 W as stated in Eq. 21, and it can be considered as a major contributor to the power demand of the A/C system.
The distribution of ambient heat load is clearly portrayed in the surface plot of Figure 3. The ambient heat load increases with increases in the temperature difference and the average speed of the vehicle. The ambient temperature difference signifies the temperature gap between the surface of the vehicular body and the cabin temperature.
FIGURE 3. Ambient heat load distribution vs. average speed (m/s) and ambient temperature difference (K).
Radiation load is another key element in determining the total A/C load. The radiation load is comprised of three major components: direct radiation load, diffuse radiation load, and reflected radiation load. The direct radiation load is caused by the radiation of direct sunlight whereas diffuse radiation is that part of the solar radiation, which results from indirect daylight radiation on a surface. The reflected load is caused by the reflected radiation from the surfaces (Abdulsalam et al., 2007). The total radiation load can be modeled using the formula shown in Eq. 22 (Fayazbakhsh and Bahrami, 2013).
In Eq. 22,
The direct radiation heat gain per unit area, i.e.,
In Eq. 25, the constant
The term
The surface absorptivity value,
Therefore, the total radiation load comprised of direct, diffuse, and reflected radiation is determined as stated in Eq. 29, and it can be claimed as one of the highest contributors to the automotive AC load with a power requirement of around 2.43 kW. Moreover, it accounts for 24% of the automotive AC power demand. The automotive AC energy efficiency can be improved by finding ways to mitigate the impact of the radiation heat load.
Since the study encompasses the scope of LDVs equipped with internal combustion engine (ICEs), exhaust emission is generated and transmitted from the exhaust manifold of the engine through the exhaust lines underneath the cabin to the tailpipe. The higher temperature of the exhaust gas can contribute to the thermal gain of the cabin through the cabin floor. The exhaust load can be modeled using the formula in Eq. 30.
In Eq. 30,
In determining the average surface area exposed to exhaust heat, the following assumptions and calculations have been made. The length of an average car is assumed to be 15 feet (4.50 m) (Automobiledimension, 2018). The length of an average exhaust-line (
The average cabin temperature,
Approximating the normal operating RPM of a 4-stroke ICE as 3000 RPM, the
Consequently, as shown in Eq. 33, the average exhaust load of an automotive AC is determined to be 2 kW under local conditions.
Engine load determines the amount of excess heat generated by the IC engine and the amount transferred into the cabin. The engine load can be modeled using the formula in Eq. 34.
In Eq. 34,
The estimation of the engine temperature can be performed using the formula in Eq. 36 (Khayyam et al., 2009).
The variation of engine load on par with engine RPM is depicted in Figure 4. It can be seen that the instantaneous engine heat load increases quadratically as a function of engine RPM.
Consequently, the engine load can be determined as stated in Eq. 37, using the aforementioned steps. The average engine load can be approximated as 2.6 kW under the given conditions.
Due to the leakage of air within the cabin to the atmosphere, ambient air is assumed to enter the cabin at the ambient temperature and with higher relative humidity. Typically, once steady-state operation is reached, the cabin air pressure is greater than the ambient air pressure. The thermal load can then be determined using the formula in Eq. 38 (Abdulsalam et al., 2007):
In Eq. 38,
In Eq. 39,
In Eq. 40,
The saturated vapor pressure and the relative humidity values should be substituted in (40) in reference to the values portrayed in Table 3.
After substituting the ambient values into Eq. 40, the value in Eq. 41 can be obtained. Similarly, for cabin parameters, Eq. 42 can be obtained.
According to the local context,
It is assumed that the mean RH of an air-conditioned car is around 50% [range, 30% to 65%, for temperatures from 20–25°C].
Similar to the method for obtaining (43), the result in Eq. 44 was achieved by assuming a mean mass air flow rate of 0.02 m3s-1, allowing the ventilation load to be determined as stated in Eq. 45.
Consequently, the average ventilation load of an automobile is estimated under the given local conditions as 120 W, which is comparatively lower than the other AC loads. Lastly, a summary of the determined values for each type of AC load under local conditions is provided in Table 4.
Alternators are the primary source of electric energy within a vehicle. The electric power demand of a contemporary automobile has rapidly increased along with the increase in use of electrical devices. The alternator provides the electric output as a consequence of an energy conversion chain. Taking the average efficiency values into account, the internal combustion engine has an efficiency of 40%, the belt-drive has an efficiency of 98%, and the alternator has an efficiency of 55%, which leads to an overall energy efficiency of around 21% (Allen and Lasecki, 2001).
Simply stated, an alternator is a synchronous alternating current (AC) electric generator with direct current (DC) diode rectification and pulse-width modulation voltage control (SAE International, 2011). It consists of a rotor, stator, diode rectifier, and voltage regulator. An automotive alternator has an efficiency of about 55% at an operating RPM of 1500. The power loss in an alternator is another important aspect to be analyzed since it can contribute to increased fuel consumption. The losses can be classified into three main types: electrical, magnetic, and mechanical. With this in mind, the overall energy conversion efficiency of an alternator can be stated as:
In Eq. 46,
It can be stated that the peak efficiency of an automotive alternator lies around 55% at an operating RPM of around 1500 (Liaw et al., 2006; Gajanayake et al., 2020). The term,
Assuming an alternator efficiency,
Therefore, the average input power demand of an automotive alternator is 2.8 kW, which is a significantly higher contributor.
In this study, the mechanical water pump and the power steering pump were identified and studied as auxiliary devices that run by engine power in addition to the AC and the alternator. When estimating the power demand of the water pump and the power steering pump, previous literature has been critically appraised. First, the power demand of the water pump is discussed and estimated. During driving cycle test schedules, which run from 1200 to 1800 s, the operation of the cooling system of an internal combustion engine (ICE) is critically important to ensure that the engine remains within the optimum operating temperature range. ICEs account for many types of heat losses, and the water pump is an essential device for circulating the coolant fluid within the engine block to maintain an optimum temperature. Every vehicle equipped with an ICE has a water pump that is operated either mechanically or electrically. In this study, the mechanical version of the water pump will be discussed. It operates as an engine auxiliary load that is coupled to the engine crankshaft by a serpentine belt. Single-stage radial centrifugal pumps are used in the vast majority of motor vehicle cooling circuits, and the speed of the pump and coolant flow rate are linked directly to the engine speed.
A typical mechanical water pump consists of an impeller located inside a spiral housing and sealed by an axial face seal. The spiral housing is mounted to the engine block with ports leading into and out of the coolant fluid channels within the engine block. The mechanical power arrives through the hub with a pulley. The channels on the pulley indicate the interface for the guides on the serpentine belt which transmits power from the crankshaft (Wang et al., 2015b). When referring to the relationship of the pressure generated within the water pump and the respective flow rate at different engine speeds, it can be seen that as the in the engine speed increases, the pump pressure also increases (Gota, 2018). Consequently, the amount of fluid horsepower generated will also be increased. The mechanical efficiency of a water pump typically lies between 35% and 55% for engine speeds ranging from 1000 RPM (idle) to 5000 RPM (Allen and Lasecki, 2001). The input power required by the water pump varies from 185 W to 220 W depending on the RPM range from 3000–5000 RPM. For an operating RPM of 3000, the power demand of the water pump can be estimated at 185 W.
The power steering pump is the other type of engine auxiliary for which the power demand was estimated and discussed in this study. During the driving cycle tests, the lateral motion of the vehicle steering was not considered; only the power demand of the power steering pump during the course of straight driving was discussed. When considering power steering mechanisms, there are two main technologies used: hydraulic power-assisted steering (HPAS) and electronic power-assisted steering (EPAS). The power consumption during a straight driving course shows significant discrepancies between these two technologies. The studies of Herkommer (Herkommer, 2002) have determined that fuel consumption was reduced up to 0.25 L per 100 km when EPAS systems were introduced in LDVs. In the conventional HPAS system, the power demand is dependent upon the delivery of oil and the system consumes approximately 0.3 L of fuel per 100 km (Herkommer, 2002) (Breitfeld et al., 2002).
Hydraulic pumps are usually fix-mounted to the engine and connected to the crankshaft by the serpentine belt. Since the engine RPM varies during driving, the flow delivered by the pump also varies proportionally, but the pumps are designed to deliver full flow at idle speed. This leads to the production of surplus oil when the engine runs at operating RPM, and this surplus oil is accountable for most of the power consumption associated with HPAS. Therefore, it is somewhat surprising that the overall energy efficiency of the HPAS system, 60%, is quite a lot higher than that of the EPAS system, at 22% (Wang et al., 2015b). The greater number of levels of power transmission in the EPAS system relative to the HPAS system is the cause of the lower efficiency values. Despite the lower efficiency, the overall power demand of the EPAS system is significantly lower than that of the HPAS system. The EPAS system is accountable for an overall power demand of approximately 38.5 W, whereas the HPAS system has an overall power demand of 175 W.
Auxiliary engine components play a significant role in contributing to the engine power demand. The percentage contributions of each auxiliary load toward the engine power demand are given as in Table 5.
Almost all the auxiliary equipment discussed in the study is belt-driven, and thus, there’s a significant dependency on engine speed and subsequently on the vehicular speed as well. Therefore, when tested on a driving cycle, the auxiliary equipment has a significant impact on the operating fuel economy of a light duty vehicle.
When analyzing the belt-driven mechanical auxiliary loads of the A/C unit, alternator, water pump, and steering pump, we found that the major users of engine power were the A/C system and the alternator, accounting for more than 97% of the total auxiliary power requirement. The power demands of the water pump and the power steering pump are quite low, around 3% of the total auxiliary power demand. When determining the auxiliary power requirements, an operating RPM of 3,000 was assumed, whereas the other physical factors were considered with respect to the local Sri Lankan context. For a standard LDV with a rated engine power of 100 bhp, equivalent to 74.7 kW, the engine auxiliaries required about 13.130 kW, which accounted for 17.6% of the engine’s total rated power. Therefore, it can be concluded that auxiliary engine loads must be taken into account when modeling the overall engine power demand since they claim a substantial portion of engine power and should be considered a main factor in modeling the engine loads on par with tractive loads and other inertial engine loads.
The original contributions presented in the study are included in the article/Supplementary Material; further inquiries can be directed to the corresponding author.
All authors listed have made a substantial, direct, and intellectual contribution to the work and approved it for publication.
The authors declare that the research was conducted in the absence of any commercial or financial relationships that could be construed as a potential conflict of interest.
All claims expressed in this article are solely those of the authors and do not necessarily represent those of their affiliated organizations, or those of the publisher, the editors, and the reviewers. Any product that may be evaluated in this article, or claim that may be made by its manufacturer, is not guaranteed or endorsed by the publisher.
Abdulsalam, O., Santoso, B., and Aries, D. (2007). Cooling load calculation and thermal modeling for vehicle by MATLAB. Int. J. Innovative Res. Sci. Eng. Technol. 3297 (5), 3052–3060. doi:10.15680/IJIRSET.2015.0405076
Allen, D. J., and Lasecki, M. P. (2001). Thermal management evolution and controlled coolant flow. Technical Paper Series 2001-01-1732. Society of Automobile Engineers.
ASHRAE (2017). Hvac system design software. 2nd. Ashrae. Available at: http://www.carrier.com/commercial/en/us/software/hvac-system-design/.
Automobiledimension (2018). Body dimensions. Available at: https://www.automobiledimension.com/ (Accessed June 20, 2021).
Bradfield, M. (2008). Improving alternator efficiency measurably reduces fuel costs 1–31. Indiana, United States: Remy International Inc.
Breitfeld, C., Foag, W., Guldner, J., M¨uller, S., Schmidt, W., and Vielwerth, G. (2002). “Actuator principles for integrated chassis control system - a comarison,” in 3rd International Fluid Power Conference, Aachen, Germany, March 2002, 399–418. ISBN 3–8265–9900–4. 42V.
Cho, G., Wi, H., Lee, J., Park, J., and Park, K. (2008). Effect of alternator control on vehicle fuel economy. Trans. KSAE 17 (2), 20–25.
Cuma, M. U., and Koroglu, T. (2015). A comprehensive review on estimation strategies used in hybrid and battery electric vehicles. Renew. Sustain Energy Rev. 42, 517–531. doi:10.1016/j.rser.2014.10.047
Department of Meteorology (2017). Department of Meteorology. Available at: https://www.meteo.gov.lk (Accessed July 25, 2021).
Fayazbakhsh, M. A., and Bahrami, M. (2013). Comprehensive modeling of vehicle air conditioning loads using heat balance method. SAE Tech. Pap. 2, 2688–3627. doi:10.4271/2013-01-1507
Gajanayake, S., Thilakshan, T., Sugathapala, T., and Bandara, S. (2020). “Study of the impact of electric vehicles on fuel consumption and carbon dioxide emission scenarios in Sri Lanka” in 2020 Moratuwa Engineering Research Conference (MERCon), 494–498. doi:10.1109/MERCon50084.2020.9185248
Gota, S. (2018). Two-and-Three-Wheelers: A policy guide to sustainable mobility solutions for motorcycles 40. Available at: https://www.sutp.org/files/contents/documents/resources/A_Sourcebook/SB4_Vehicles-and-Fuels/GIZ_SUTP_TUMI_SB4c_Two- and Three-Wheelers_EN.pdf.
Hara, D., and Özgen, G. O. (2016). Investigation of weight reduction of automotive body structures with the use of sandwich materials. Transp. Res. Procedia 14, 1013–1020. doi:10.1016/j.trpro.2016.05.081
Havenith, G., Holmér, I., and Parsons, K. (2002). Personal factors in thermal comfort assessment: Clothing properties and metabolic heat production. Energy Build. 34, 581–591. doi:10.1016/S0378-7788(02)00008-7
Herkommer, R. (2002). “Ways toward energy saving in hydraulic steering system,” in 3rd International Fluid Power Conference, Aachen, Germany, March 2002, 465–474. IFK02, ISBN 3–8265–9900–4.
ISO (1989). ISO 8996, ergonomics of thermal environments – determination of metabolic heat production. Geneva: ISO.
Khayyam, H., Kouzani, A. Z., and Hu, E. J. (2009). “Reducing energy consumption of vehicle air conditioning system by an energy management system,” in 2009 IEEE Intelligent Vehicles Symposium, Xi'an, China, 03-05 June 2009.
Liaw, C., Whaley, D., Soong, W., and Nesimi, E. (2006). Investigation of inverter less control of interior permanent-magnet alternators. IEEE Trans. Ind. Appl. 42 (2), 536–544. doi:10.1109/TIA.2005.863910
Martinez, R., Zhou, B., Sophiea, M. K., Bentham, J., Paciorek, C. J., Iurilli, M. L., et al. (2020). Height and body-mass index trajectories of school-aged children and adolescents from 1985 to 2019 in 200 countries and territories: A pooled analysis of 2181 population-based studies with 65 million participants. Lancet 396 (10261), 1511–1524. PMC 7658740. PMID 33160572. doi:10.1016/S0140-6736(20)31859-6
Nadamoto, H., and Kubota, A. (1999). Power saving with the use of variable displacement compressor. Technical Paper1999- 01-0875. Society of Automobile Engineers.
Patel, B. M., Modi, A. J., and Rathod, P. P. (2013). Analysis on engine cooling water pump of car and significance of its geometry. Intl. J. Mech. Eng. Technol. 4 (3), 100–107. ISSN 0976–6340.
Roskilly, A. P., Palacin, R., and Yan, J. (2015). Novel technologies and strategies for clean transport systems. Appl. Energy 157, 563–566. doi:10.1016/j.apenergy.2015.09.051
Secondskinaudio (2015). What's the square footage of my vehicle? Available at: https://www.secondskinaudio.com/square-footage-help/ (Accessed July 29, 2021).
Solar elevation angle Calculator (2014). Solar elevation angle (for a day) Calculator. Available at: https://keisan.casio.com/exec/system/1224682277 (Accessed October 2, 2021).
Surface Absoptivity (2016). Resources, tools and basic information for engineering and design of technical applications. Available at: https://www.engineeringtoolbox.com/radiation-surface-absorptivity-d_1805.html (Accessed August 2, 2021).
Tasuni, M. L. M., Latiff, Z. A., Nasution, H., Perang, M. R. M., Jamil, H. M., and Misseri, M. N. (2016). Performance of a water pump in an automotive engine cooling system. J. Teknol. 78 (10–2), 47–53.
Wang, X., Liang, X., Hao, Z., and Chen, R. (2015). Comparison of electrical and mechanical water pump performance in internal combustion engine. Int. J. Veh. Syst. Model. Test. 10 (3), 205–223. doi:10.1504/IJVSMT.2015.070155
Wang, X., Liang, X., Hao, Z., and Chen, R. (2015). Comparison of electrical and mechanical water pump performance in internal combustion engine. Int. J. Veh. Syst. Model. Test. 10 (3), 205–223. doi:10.1504/IJVSMT.2015.070155
Welstand, J., Haskew, H., Gunst, R., and Bevilacqua, O. (2003). Evaluation of the effects of air conditioning operation and associated environmental conditions on vehicle emissions and fuel economy. Technical Paper 2003-01-2247. Society of Automobile Engineers.
Weldon, P., Morrissey, P., and O'Mahony, M. (2016). Environmental impacts of varying electric vehicle user behaviours and comparisons to internal combustion engine vehicle usage–An Irish case study. J. Power Sources 319, 27–38. doi:10.1016/j.jpowsour.2016.04.051
WHO (2015). Non-communicable disease risk factor survey Sri Lanka. (PDF). Sri Lanka: World Health Organization, 81.
Wu, X. K., Freese, D., Cabrera, A., and Kitch, W. A. (2015). Electric vehicles’ energy consumption measurement and estimation. Transp. Res. D. Transp. Environ. 34, 52–67. doi:10.1016/j.trd.2014.10.007
Zhang, Z., Wang, J., Feng, X., Chang, L., Chen, Y., and Wang, X. (2018). The solutions to electric vehicle air conditioning systems: A review. Renew. Sustain. Energy Rev. 91, 443–463. doi:10.1016/J.RSER.2018.04.005
Zhaogang, Q. (2014). Advances on air conditioning and heat pump system in electric vehicles – a review. Renew. Sustain. Energy Rev. 38, 754–764. doi:10.1016/j.rser.2014.07.038
D the average diameter of the exhaust line
A/C air conditioning
AC alternating current
ASHRAE American Society of Heating Refrigerating and Air-conditioning Engineers
BEVs battery electric vehicles
DC direct current
EPAS electronic power-assisted steering
EVs electric vehicles
HEVs hybrid electric vehicles
HPAS hydraulic power-assisted steering
ICE internal combustion engine
ISO International Organization for Standardization
JC08 Japanese Chassis Dynamometer Test Cycle
NEDC New European Driving Cycle
RH relative humidity
US06 United States Supplemental Federal Test Procedure
WLTP World Harmonized Light Vehicle Test Procedure
Keywords: auxiliary engine loads, fuel economy, automotive air-conditioning, alternator, water pump, power steering pump, light duty vehicles
Citation: Gajanayake S, Bandara S and Sugathapala T (2023) A novel approach to estimate power demand of auxiliary engine loads of light duty vehicles. Front. Mech. Eng 8:1090152. doi: 10.3389/fmech.2022.1090152
Received: 05 November 2022; Accepted: 12 December 2022;
Published: 12 January 2023.
Edited by:
Fabio Fatigati, University of L'Aquila, ItalyReviewed by:
Amin Mahmoudzadeh Andwari, University of Oulu, FinlandCopyright © 2023 Gajanayake, Bandara and Sugathapala. This is an open-access article distributed under the terms of the Creative Commons Attribution License (CC BY). The use, distribution or reproduction in other forums is permitted, provided the original author(s) and the copyright owner(s) are credited and that the original publication in this journal is cited, in accordance with accepted academic practice. No use, distribution or reproduction is permitted which does not comply with these terms.
*Correspondence: Surath Gajanayake, Z2FqYW5heWFrZXNwQGtkdS5hYy5saw==
Disclaimer: All claims expressed in this article are solely those of the authors and do not necessarily represent those of their affiliated organizations, or those of the publisher, the editors and the reviewers. Any product that may be evaluated in this article or claim that may be made by its manufacturer is not guaranteed or endorsed by the publisher.
Research integrity at Frontiers
Learn more about the work of our research integrity team to safeguard the quality of each article we publish.