- State Key Laboratory of Tribology, Tsinghua University, Beijing, China
As a kind of self-lubricating material, diamond-like carbon (DLC) film is famous for its excellent tribological properties. Superlubricity state with nearly-vanishing friction achieved with DLC film has enormous potential applications in future mechanical systems. It is pointed out that its superlubricity state is highly related to both the inherent properties of the DLC film and external sliding conditions. Moreover, the underlying mechanisms of the superlubricity are complicated, posing uncertainties on their engineering application. This review provides an overview of the influence factors, including film composition, ambient, temperature, normal load, and sliding velocity and their correlations with the anti-friction behaviors of DLC films. These understandings will enable a more effective engineering application of self-lubricating carbon films with excellent tribological properties.
Introduction
Friction is one of the decisive factors affecting the efficiency and service life of a mechanical system. Statistically, 23% of global energy consumption is due to the friction-related activities, of which 40% can be prevented through application of advanced surface, material and lubrication technologies (Holmberg and Erdemir, 2017). With the increasing demand on higher efficiency, power and life of mechanical systems, studies on reducing friction and wear are becoming increasingly important both from the economic and environmental perspectives. The discovery of superlubricity provides a possibility to reduce tribological consumption to an extremely low level, and has triggered increasingly extensive attention from researchers around the world over the past three decades.
The concept of superlubricity was firstly brought out by Hirano in a theoretical prediction based on calculations that the friction force could reach zero level when two crystal surfaces sliding in an incommensurable condition (Hirano and Shinjo, 1990). And it was soon verified by nanoscale friction test on cleaved mica surfaces with different contact angles (Hirano et al., 1991). Now this ideal friction vanishing state is generally redefined as structural superlubricity, and the concept of superlubricity is generally accepted as a sliding state with a kinetic fiction coefficient bellow 0.01 (Erdemir and Eryilmaz, 2007). Around 2000s, with the rapid increase of research investment, more superlubricity phenomena have been revealed, which can be generally divided into solid and liquid superlubricity, respectively. In nanoscale or microscale, superlubricity is achievable via a variety of solid materials such as layered materials like graphite, graphene (Dienwiebel et al., 2004), BN (Song et al., 2018), and MoS2 (Martin et al., 1993), atomically smoothed crystals including covalent crystals like Si (001) (Hirano et al., 1997), ionic crystals (Socoliuc et al., 2004) like NaCl, metallic crystals like Ag (Goto and Honda, 2004). To date, various carbon-based materials have been found to be capable of achieving superlubricity (Chen and Li, 2020), for instance, C60 intercalated graphite films (Miura et al., 2005), carbon nanotubes (Zhang et al., 2013), graphite or graphene, ultra-nanocrystalline diamond (Kumar et al., 2011), onion-like/fullerene-like carbon (Gong et al., 2017), and diamond-like carbon (Erdemir and Eryilmaz, 2014). Nevertheless, most of these superlubricity behaviors are based on the incommensurable contact of the ultra-smooth crystalline surfaces, which is still far from being applicable for engineering due to the diversified interferences in macroscopic tribo-systems.
Diamond-like carbon (DLC) film is a class of carbon-based amorphous coating, which exists in the form of a disordered covalent network of sp1, sp2, and sp3 hybridized carbon atoms, and has the ability to introduce other elements such as hydrogen into the film. According to the differences in structure and doped materials, DLC can be generally divided into amorphous carbon (a-C), hydrogenated amorphous carbon (a-C:H), tetrahedral amorphous carbon (ta-C), and hydrogenated tetrahedral amorphous carbon (ta-C:H) (Robertson, 2002). The synthesis methods of DLC films can be divided into physical vapor deposition (PVD) and chemical vapor deposition (CVD). With the development of these technologies, DLC coatings can be deposited flexibly on a variety of materials such as silicon, ceramic, glass, metal, and rubber. Meanwhile, by changing the deposition conditions, their structure and composition are adjustable to obtain superior mechanical and tribological properties for different application conditions.
DLC was first synthesized around the 1950s. Systematic research on DLC started in the 1970s (Aisenberg and Chabot, 1971). Later in 1981, Enke reported the superlubricity behavior of DLC films with a friction coefficient of 0.005 in ultrahigh vacuum (Enke, 1981). In the 1990s, superlubricious capacity of a-C:H in vacuum was systematically studied by Donnet et al. (1994) and Donnet and Grill (1997). In 2000, an ultralow friction coefficient of 0.002 was achieved with self-mated a-C:H tested in nitrogen and argon atmosphere (Erdemir et al., 2000a), and an ultra-long superlubricity lifetime of 32 days was achieved (Erdemir et al., 2000b), as shown in Figure 1A. Recently, an extremely low friction coefficient of 0.0001 under heavy load was achieved with a-C:H in hydrogen atmosphere (Nosaka et al., 2017), as shown in Figure 1B. These results indicate that a-C:H films are capable of achieving stable superlubricity under dry inert atmosphere, vacuum and hydrogen, and the underling mechanism is closely related to friction-induced structural transformation of the contact area and tribo-chemical interaction between the sliding surfaces. Further researches have shown that introducing silicon (Chen et al., 2014, 2017) or sulfur (Freyman et al., 2006) into a-C:H films can significantly reduce its sensitivity to oxygen or water vapor, leading to superlubricity in humid air via novel pathways. Fullerene-like hydrogenated amorphous carbon (FL-C:H) films also exhibit superlubricious properties in both nitrogen and air (Wang et al., 2008). Kato et al. suggested that carbon nitride (CNx,) can achieve superlubricity in nitrogen atmosphere without the presence of hydrogen (Kato et al., 2003; Adachi and Kato, 2008). Table 1 shows the timeline of the research progress on solid superlubricity achieved with DLC films. As for liquid lubrication, researches showed that hydrogen-free ta-C can achieve superlubricity with the assistance of ester additive (Kano, 2006), glycerol (De Barros Bouchet et al., 2007), unsaturated fatty acids (Kuwahara et al., 2019). DLC lubricated with nano boron nitride particle dispersed in PAO is also available to achieve superlubricity (Zeng et al., 2013).
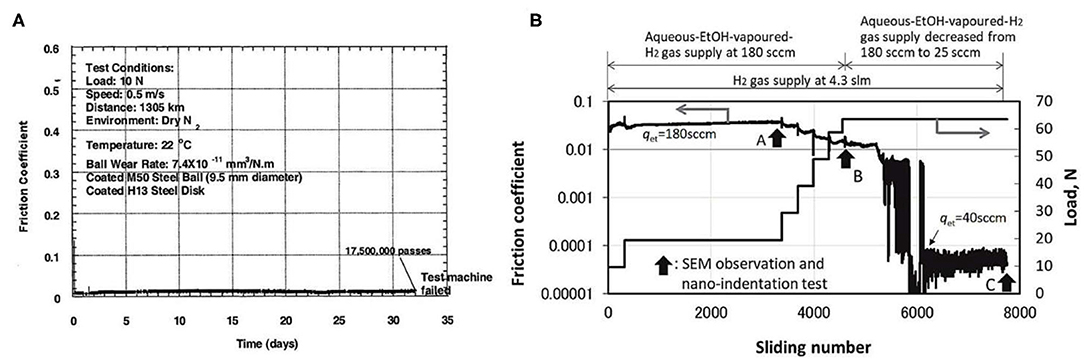
Figure 1. (A) Superlubricity with extremely long-lasting time of 32 days achieved with a-C:H films in N2 environment. Adapted with permission, Erdemir et al. (2000b) Copyright 2000, Elsevier Science B.V. (B) Extremely low friction coefficient below 0.0001 achieved with a-C:H films in H2 environment under heavy load. Adapted with permission from Nosaka et al. (2017) Copyright 2017, Japanese Society of Tribologists.

Table 1. Research progress on the solid superlubricity achieved with different types of DLC films under various environments.
To date, a growing interest in superlubricious DLC is aroused, and diversified superlubricity pathways have been discovered. Nevertheless, most of these superlubricity phenomena are achieved in strictly controlled lab conditions. The influencing mechanisms of environment and working conditions are complicated, and are still not fully comprehended, which poses uncertainties on the effective manipulation of superlubricious DLC films in mechanical engineering. In recent decades, numerous researches have been done, aiming at uncovering these mechanisms and optimizing the performance of DLC films in complicated environments. In the following sections, a review of superlubricity of DLC is provided in the perspective of influence factors as shown in Figure 2. Film composition is one of the key factors for the establishment of superlubricity. The influences of different elements, including hydrogen, fluorine, silicon, nitrogen, and metallic elements are discussed in section Influence of Film Elements. Stable superlubricity achieved with DLC films usually needs dry inert gaseous atmosphere or hydrogen environment. Though the friction of DLC films in vacuum is extremely low, their wear rate is very high. And it is still a challenge for DLC to achieve superlubricity in oxygen and water containing environments. The environmental sensitiveness and its mechanisms and controlling methods are discussed in section Influence of Environments. From the perspective of engineering applications, it is important to understand the influences of working conditions such as temperature, normal load and sliding velocity on the superlubricity of DLC films. The influence rules and their underlying mechanisms are introduced in section Influence of Testing Parameters. Finally, section Discussion and Conclusion presents the most prevailing theories for the mechanisms of superlubricity in the perspective of origin of friction. The fundamental restrictions of applying superlubricious DLC films in engineering and the approaches to combat these deficiencies are summarized.
Influence of Film Elements
The proper composition of DLC films is generally considered to be the precondition for achieving superlubricity state. Understanding the influencing mechanism of the film elements can enable a more effective manipulation of DLC with excellent tribological properties. In this section, the influence of film elements, for example, surface passivation induced by hydrogen and fluorine and low humidity sensitiveness enabled by silicon and sulfur, are presented. Superlubricity achieved via novel mechanisms in carbon nitride and metal-containing DLC films are also introduced.
Hydrogen is the most common element in DLC film, and its proportion can be controlled by changing deposition conditions such as the bias voltage (Chen and Kato, 2014) and the proportion of gas source (Erdemir et al., 2000c). Most of the hydrogen atoms exist in the form of bonded C-H, while some of hydrogen atoms are trapped in the interstice of carbon framework with the forms of unbonded atoms and not fully decomposed gas source molecules (Erdemir, 2004). During dry sliding contact, they are released in the forms of H2, CH4, and so on (Nevshupa et al., 2019). Studies have shown that the friction property of a-C:H is closely related with the proportion of hydrogen (Donnet et al., 1998, 1999; Erdemir, 2001; Fontaine et al., 2005). Generally, in vacuum or inert environments, hydrogen-rich a-C:H films, or polymer-like carbon (PLC) films (Casiraghi et al., 2005) with a hydrogen proportion higher than 40% are most favorable for achieving superlubricity (Donnet et al., 1994, 1999; Gao et al., 2003). Hydrogen-free DLC such as ta-C or a-C exhibits a very high friction coefficient up to 1 when tribo-tested in vacuum (Andersson et al., 2003). However, implanting hydrogen ion into the surface of hydrogen-free DLC can also lead to superlubricity (Eryilmaz and Erdemir, 2008). It is believed that introducing hydrogen into the film matrix will increase its void density and sp3 proportion, thereby reducing the residual stress in the film and softening the material (Chen and Li, 2020). Most importantly, hydrogen is speculated to passivate the carbon dangling bonds at the sliding interface, reducing tribochemical wear and friction caused by the formation of cross-interfacial carbon bonds and forming an none-adhesive sliding surface (Erdemir, 2001), as shown in Figure 3, which is proved by simulations (Pastewka et al., 2008, 2010; Schall et al., 2010). Meanwhile, simulations (Dag and Ciraci, 2004) also suggest that due to the low electronegativity of hydrogen, both hydrogenated surfaces are positively charged and generate repulsive force, thus reducing friction and wear (Eryilmaz and Erdemir, 2008). In addition to controlling the hydrogen proportion, introducing other elements is also an effective approach to improve the mechanical and tribological performance of DLC films. Fluorine is a case in point. Fluorine-doped a-C:H with lower hydrogen proportion (5 at.% H, 18 at.% F) could also achieve superlubricity with a friction coefficient of 0.005 in ultrahigh vacuum (Fontaine et al., 2004). They also exhibited higher thermal stability, even after annealing at a maximum temperature of 500°C (Nobili and Guglielmini, 2013). Fluorine, as another monovalent element like hydrogen, has the highest electronegativity and can effectively eliminate the dangling bond on the surfaces, providing negatively charged surfaces and repulsive force, leading to ultralow friction coefficients.
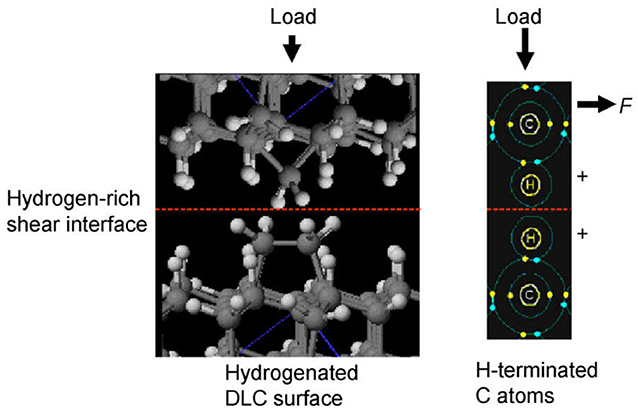
Figure 3. Schematic of hydrogen-passivated none-adhesive sliding surface. Adapted with permission from Erdemir (2001) Copyright 2001, Elsevier Science B.V.
Silicon is another common dopant for DLC films, which could reduce their humidity sensitiveness and improve the thermal stability. Similar with a-C:H, a-C:H:Si films also exhibit superlubricious properties in vacuum (Sugimoto and Miyake, 1990), nitrogen, and hydrogen environments (Chen et al., 2014). As shown in Figures 4A,B, the lowest friction coefficient in nitrogen could reach 0.001 for self-mated a-C:H:Si (31.9 at.% H, 9.3 at.% Si), similar with a-C:H (~40 at.% H) (Chen et al., 2017). Moreover, under certain conditions, it could also achieve superlubricity in humid air (Chen et al., 2013), as shown in Figure 4C, and even under liquid water (Zhao et al., 2009). The superlubricity behavior of a-C:H:Si films is closely related to the formation of a softer polymerlike tribo-film in the contact area (Chen et al., 2017). Silicon is capable of reducing sp2 proportion and stabilizing sp3 carbon network, improving thermal stability, and reducing residual stress. During dry sliding contact, silicon is expected to promote the phase transformation and the tribo-softening of the interface and involved in the evolution process of the tribofilm (Chen and Li, 2020). In humid conditions, the formation of a silica-like tribo-film and the hydroxyl groups attached to silicon atoms on the surface is supposed to be an important factor for their superlubricity behaviors, as they can directionally absorb water molecules and form layered-like structures under appropriate conditions.
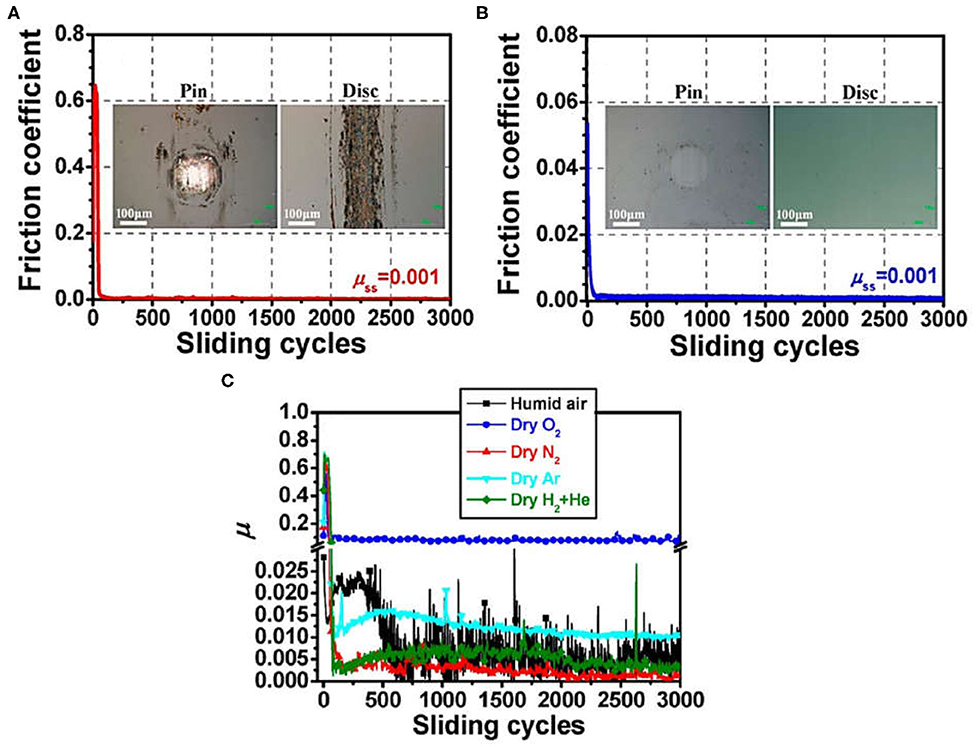
Figure 4. Contact area and extremely low friction coefficient of 0.001 achieved with a-C:H:Si (A) and (B) a-C:H. (C) Superlubricity achieved with a-C:H:Si in humid air, dry Ar, dry N2, and Dry H2+He. Adapted with permission from Chen et al. (2014) Copyright 2014, American Chemical Society.
To some extent, sulfur is similar to silicon in reducing humid sensitivity of DLC films. Experiments showed that a-C:H:S films (5.0 at. % S) are capable to realize superlubricity in humid environments with RH ranging from 0 to 50% (Freyman et al., 2006). Researchers suggested that sulfur can be involved in the formation of thiol-like (-C-S-H) groups on the sliding surfaces, leading to a weaker binding energy between water molecules and the sliding surface, and hence a low friction coefficient in humid environments.
Nitrogen doped DLC or CNx, could achieve superlubricity via a different pathway without the assistance of hydrogen. The friction coefficient between CNx (12 at.% N, 7 at.% O) and Si3N4 could reach a superlubricity state when tested in nitrogen environment, but lost this capacity in other inert ambient such as CO2, He and vacuum (Kato et al., 2003). The mechanism is still not fully comprehended, and the formation of a transfer layer on the counterpart material and the establishment of a chemical inert surface terminated by nitrogen are thought to be the key factors.
The incorporation of metal elements such as titanium, chromium, and tungsten in DLC films could improve their hardness and toughness (Voevodin and Zabinski, 2000). However, superlubricity is difficult to achieve in these cases, mainly due to the abrasive wear effect caused by the metallic carbide nanocrystals. Generally, in order to achieve superlubricity, metallic elements should be controlled within a low proportion to limit the formation of nanocrystals in the film. Titanium-doped DLC was reported to achieve superlubricity with a friction coefficient of 0.005 in humid air with a relative humidity of 40%, and the authors suggested it was attributed to the anti-oxidation effect of the TiC-rich surface and the formation of fullerene-like structure with TiO2 cores (Zhao et al., 2016). Titanium and silicon co-doped a-C:H films are also capable of achieving superlubricity in air with a friction coefficient of 0.007 (Jiang et al., 2010). Another study showed that aluminum and silicon co-doped a-C:H films could realize a superlow friction coefficient of 0.001 in high vacuum. Self-assembled nanostructure network and fullerene-like structures were observed to be the main factors for the superlubricity (Liu et al., 2012).
Influence of Environments
Previous researches have shown that a-C:H films can reach ultralow friction in clean, inert environments (such as nitrogen, carbon dioxide, noble gases, and vacuum) and hydrogen, but it is much challenging in oxygen or humid air (Erdemir et al., 2000c; Chen et al., 2014). Although DLC films are capable of achieving superlubricity in macroscale, their environmental sensitiveness is still a barrier to limit their engineering application. In this section, the experimental studies on superlubricious DLC films in dry inert gaseous atmosphere, vacuum, hydrogen, oxygen, or water containing environments are presented, respectively, and the influence mechanisms of these environments are discussed.
Dry Inert Gaseous Atmosphere
Dry nitrogen is the most frequently used environment for achieving superlubricity with DLC films. Generally, dry nitrogen is considered as a kind of inert gas that can exclude the interference of oxygen and water molecules in lab condition, which is beneficial for the self-lubrication effect of DLC films. The same is true with carbon dioxide and noble gases like argon. Simultaneously, the wear rate of a-C:H in dry inert gaseous environments is very low, sometimes even unmeasurable. Nevertheless, though superlubricity is available in nitrogen, carbon dioxide, and argon, the friction coefficient in argon is higher than that in nitrogen and carbon dioxide (Erdemir et al., 1991; Zhang et al., 2002; Ji et al., 2009), as shown in Figure 4C. The researchers suggest that at an appropriate sliding speed, due to the interaction between π orbital-lone pair electrons on the film and lone pair of electrons of the molecules, N2 and CO2 molecules are able to be absorbed on the surfaces to form a molecule layer with another lone pair of electrons pointing outside, generating coulomb repulsion forces and preventing the π-π* interactions between the two surfaces (Ji et al., 2009).
Vacuum
Vacuum is another important environment for superlubricious DLC films due to their superior properties for space applications (Vanhulsel et al., 2007). Researchers have shown that hydrogen-free DLC film exhibit a drastic friction and wear in vacuum with a fricion coefficient as high as 1 (Erdemir and Eryilmaz, 2014), while hydrogen-rich DLC films are able to achieve superlubicity of 0.006–0.008 in vacuum from 10−7 to 10−1 Pa (Donnet et al., 1994). However, compared with that in dry inert gaseous environment and hydrogen, the wear rate of a-C:H films is generally high in vacuum (Fontaine et al., 2001), which is still a barrier for their effective application in aerospace. Compared with the inert gas ambient, the vacuum environment mainly has three distinct characteristics theoretically (Xue and Wang, 2012). Firstly, the protective effects of absorbed gas molecules mentioned above do not exist, leading to a higher chance for π-π* interactions and hence tribochemical interactions between two surfaces. Secondly, convection heat transfer enabled by gas medium is not available, resulting in a higher flash temperature of the contact area, which facilitates their tribochemical reactions and hydrogen loss. Thirdly, the main free path of molecules in vacuum is significantly higher than that in gas ambient, which could increase the diffusion and loss speed of hydrogen on the contacting surfaces, and resulting in a higher wear rate. Improving the hydrogen proportion is an available approach to prolong the lasting time of superlubricity state in vacuum. For example, experiments showed that a-C:H films with a hydrogen proportion of 34% could only maintain the durability of about 40 cycles, while under the same circumstances a-C:H films with a higher hydrogen content up to 40% could maintain more than 500 cycles (Fontaine et al., 2001). In another experiment, the superlubricity state of DLC film with 50% of hydrogen lasted for about 34,000 cycles (Vanhulsel et al., 2007). In addition, another approach to prolong their lifetime in vacuum is introducing other elements into the film. For instance, sulfur-containing DLC films exhibit a higher sustainability but a relatively large friction coefficients in vacuum (Moolsradoo and Watanabe, 2010). Titanium and silver co-doping can also prolong the superlubricity lifetime of DLC films in vacuum. It has been observed that Ag was agglomerated on the sliding surface due to cold welding effect, and the anti-friction property of Ag contributed to the superlubricity behavior of the DLC film (Wang et al., 2012).
Hydrogen Ambient
As mentioned above, hydrogen contained in the film matrix or implanted at the surface is important for achieving superlubricity due to its passivation effect. Similarly, hydrogen gaseous ambient is also an advantageous environment for achieving superlubricity. The lasting time and friction coefficient of superlubricity state achieved with same DLC films in hydrogen is significantly superior than that in helium or vacuum (Fontaine et al., 2001), and the lasting time increased with the elevating pressure of hydrogen gas (Fontaine et al., 2005). Furthermore, hydrogen environment could significantly lower the friction coefficient of hydrogen-free ta-C films or a-C films, and even reach the superlubricity state (Erdemir and Eryilmaz, 2014; Okubo et al., 2015). In the hydrogen environment, an extremely low friction coefficient of 0.0001 was achieved with the tribo-couple of hydrogen-rich DLC films and ZrO2 counterpart under a heavy load of 2.6 GPa, as shown in Figure 1B (Nosaka et al., 2017). The researchers illustrated that hydrogen molecules in ambient are able to be involved in the tribochemical interactions at the surface with the assistance of shear force and flash temperature in the contact area, leading to the formation of a hydrogen passivated surface (Chen and Li, 2020). The researchers suggested that ZrO2 could act as a catalyzer to promote the disintegration of H2 into dissociative H, which facilitated the tribochemical process and contributed to the extremely low friction (Nosaka et al., 2017). It should be point out that during dry sliding contact, the film itself was observed to release gaseous molecules such as hydrogen, methane, carbonic oxide, as the molecules were squeezed out from the carbon framework or tribo-chemically generated during sliding contact (Nevshupa et al., 2019). The released gas molecules also took part in the tribochemical interaction in the contact area, and some researchers speculated that these released gaseous molecules were confined in the contact area, which was possible to act as gas bearing due to the elasto-hydrostatic effect and reduced the friction coefficient (Kato et al., 2018).
Oxygen and Water Containing Ambient
Although DLC films are capable to achieve ultralow friction and wear in dry inert environment, it is still a challenge to optimize their tribological properties in humid atmosphere. In ambient air, hydrogen-rich DLC films generally exhibit higher friction coefficients and it is much harder to achieve superlubricity, while hydrogen-free DLC films exhibit lower friction coefficient in humid environment (Ronkainen and Holmberg, 2008). This difference is mainly induced by the interruption of oxygen and water molecules in tribochemical-induced structural evolution on the surface. Experiments have shown that from ultra-high vacuum to several thousand Pa of dry oxygen, the superlubricity behaviors of a-C:H films are not significantly influenced (Donnet et al., 1998). However, when the pressure of oxygen reaches above this threshold, the friction coefficient increases with it obviously (Kim et al., 2006). Some researchers believed that an oxide layer with a depth of several nanometers would be formed on the top of films due to the exposure to oxygen, which was one of the factors explaining the high friction coefficient in the running-in process (Al-Azizi et al., 2015). According to classical molecular dynamics simulations, oxygen molecules can cause the breakdown of carbon chains step by step and finally convert them into carbon dioxide (Moras et al., 2011). Meanwhile, the formation of C-O-C bonds bridging two contact surfaces can also induce adhesive effect and result in higher friction coefficients (Zeng et al., 2018).
Compared to oxygen, water molecules have more significant impacts on the superlubricity of DLC films, and the corresponding mechanisms are more complicated. For hydrogen-free DLC films, humidity usually has a positive influence, which can reduce the friction coefficient from 0.7 to a relatively low value below 0.2 (Fontaine et al., 2008). Some researches even showed that cleaved (111) diamond could realize superlubricity at 85% relative humidity when sliding perpendicular to their cleaved lines (Liu et al., 2007). However, the impacts of water molecules on hydrogen-rich DLC films are quite otherwise. When humidity increases above a threshold, the superlubricity state will be interrupted, and their friction coefficient would increase above 0.05, approaching that of hydrogen-free DLC films (Fontaine et al., 2008). More detailed experiments showed that the threshold of water pressure was around 10 Pa, which was two orders of magnitude lower than that of oxygen, as shown in Kim et al. (2006). Several hypotheses have been proposed to explain this phenomenon. Firstly, water molecules are involved in the tribochemical interactions in the contact area. Calculations suggest that water molecules are energetically favorable to chemically absorb on the carbon chains (Moras et al., 2011). For hydrogen-free DLC films, this process can provide hydrogen and hydroxyl terminations, which could passivate the contact area. However, for hydrogen-rich DLC films, the oxygen-containing groups would cause hydrogen bond interactions, leading to higher adhesion force between the sliding surfaces. Energy dissipation during physical and chemical interactions between water molecules and the film also possibly contribute to the increase of friction. Secondly, higher humidity is also a barrier for the formation of a compact, robust carbonaceous transferfilm on the counterpart material (Donnet et al., 1998), which is considered to be a pivotal factor for DLC films to establish a non-adhesive sliding surface and realize their self-lubrication function. Thirdly, the physically absorbed water layer in humid ambient is also an influential factor. Experiments showed that about 1.5 layers of water molecules will be absorbed on a-C:H surface when the pressure of water was around 700 Pa (Shukla et al., 2003), and the adhesive force and friction force of a-C:H films would significantly increase when the thickness of absorbed water was higher than 1 monolayer (Tagawa et al., 2004). It is believed that the dipole-dipole interactions, the viscous drag effect, and the capillary effect of water layer absorbed on the film ultimately lead to a higher friction coefficient. As mentioned above, to combat the adverse impact of water molecules, introducing other elements such as silicon (Chen et al., 2013), sulfur (Freyman et al., 2006), or titanium (Zhao et al., 2016) is an effective approach. In these cases, water layers absorbed on the surfaces are utilized to establish the easy-shearing sliding surface. As shown in Figure 5, when sliding in moderate humid environment, silicon atoms were involved in the formation of a soft silica-like tribofilm and provided hydroxylated sliding interfaces with Si-OH termination and attracted water molecules directionally to arrange on the surface by hydrogen bond (Chen et al., 2013). Molecular dynamics simulations suggested that the layered water structure was robust in a wide range of normal loads and was capable of providing low shearing stress via boundary lubrication effect (Washizu et al., 2007).
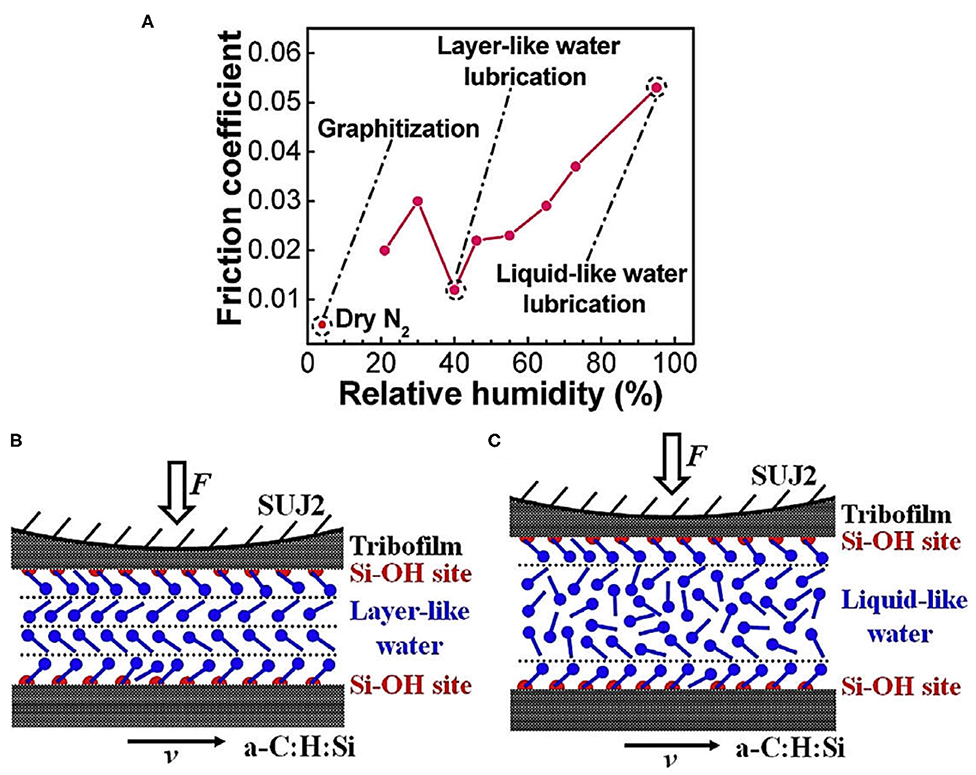
Figure 5. Friction coefficient of a-C:H:Si under different humidities (A) and its lubricating mechanism: (B) layer-like water absorption on the hydroxylated surfaces at moderate relative humidity and (C) liquid-like water absorption under high relative humidity. Adapted with permission from Chen et al. (2013) Copyright 2013, IOP Publishing Ltd.
In summary, the physical and chemical interactions between gas molecules and surfaces play an important role in the self-lubricating process of DLC films. The physical influences of environment are relative moderate, mainly through energy dissipation during the adsorption and desorption of gas molecules, heat transformation of contact area, elastic fluid dynamic pressure effect of gas in high-speed condition. The chemical reaction between surrounding molecules and surface material plays a most important role in the formation of tribolayers and passivation of dangling bonds, which governs the superlubricity properties of DLC films.
Influence of Testing Parameters
Understanding the performance of DLC films in different working conditions are important for the engineering application of these self-lubricating materials with superlubricity potential. In this section, the influence of temperature, normal load and sliding velocity are presented, respectively, and the most prevailing theories explaining their impacts on superlubricity are discussed.
Temperature
One of the advantages of solid lubricants is that they are applicable under both cryogenic and high temperature conditions where liquid lubrication cannot work. DLC is a case in point, which is capable of achieving ultralow friction coefficient in a wide range of temperatures. Temperature is also a core factor influencing physicochemical reaction, phase transformation and evolution of tribofilm, which fundamentally affects the superlubricity behavior of DLC films. DLC films exhibit superior tribological properties with a decreasing friction coefficient from cryogenic temperature to room temperature in ultrahigh vacuum (Aggleton et al., 2009). This trend continues in ambient air until reaching the lowest friction coefficient around 200–300°C, and then friction increases with elevated temperature (Lee and Wei, 2006; Zeng et al., 2015). Generally, in a moderate extent, the increase of temperature facilitates tribochemical reaction rate, which is conducive to friction-induced evolution of tribofilm and self-lubrication of DLC films. Specifically, more graphitization was observed (Zeng et al., 2015) and hydrogen emission rate was improved, promoting a more effective establishment of easy-shearing, highly passivated tribofilms. Meanwhile, the suppressed adsorption of gas or liquid layer at higher temperature may also be responsible for lower friction. Nevertheless, the heat resistance property of DLC films is confronted with a threshold. As the temperature is being higher, hydrogen spontaneous emission will become significant around 400–450°C (Liu et al., 1996), obvious thermal-induced graphitization will occur at around 500°C (Fink et al., 1983; Zeng et al., 2015), and thermal decomposition of C-H bond will start around 700°C (Su and Lin, 1998). These processes will result in an overquick hydrogen loss and more intensive π-π interactions, thus leading to higher friction coefficients. The deterioration caused by oxidation in ambient air also becomes a dominant factor, resulting in more extensive bond cleavage, and surface abrasion. As mentioned above, doping silicon or silicon-oxide into DLC films is an effective method to improve their thermal stability (Mangolini et al., 2018). Research shows that the friction coefficient of a-C:Si film is lower than 0.02 at a temperature ranging from 250 to 450°C (Jantschner et al., 2014). Adversely, in cryogenic condition, the tribochemical interaction and evolution of self-lubricated tribofilm are slowed down, and the flexibility of carbon network will be limited, leading to a higher friction coefficient. It should be pointed out that the friction coefficient of DLC films as well as other materials may have a peak around 100 K, which is considered to be a common character possessed by various materials. This phenomenon is governed by the competition process between thermally activated formation and rupturing of atomic contact (Barel et al., 2010).
Friction induced temperature rise, or flash temperature of the contact area should also be considered. In some cases, the temperature rise could reach above 200°C (Yamamoto et al., 2019). Theoretically, temperature rise is depending on the friction energy and the thermal conductivity of the tribo-pairs, and is interrelated with other factors, such as applied normal load, contact diameter, and sliding velocity, which can be estimated by the following formula (Rabinowicz, 2013):
where μ is the friction coefficient, Fn is the normal load, v is the sliding velocity, a is the radius of contact area, J is a constant, K1 and K2 are the thermal conductivities of ball and disk, respectively. Higher friction energy or sliding velocity could induce more significant temperature rises, while lager contact area would restrain temperature rise. Thus, it's possible for other working condition parameters (such as normal load, sliding velocity) to influence the friction properties via thermal effect.
Normal Load
Normal load is an important factor influencing the superlubricity behavior of DLC films. Researches have shown that a-C:H films generally exhibit lower friction properties under higher normal load both in air (Zhang et al., 2004; Liu Y. et al., 2019) and inert gaseous ambient such as argon and nitrogen (Kunze et al., 2014; Chen et al., 2017). As shown in Figure 6A, the friction coefficient of a-C:H films decreased from 0.008 to 0.001 as the normal load increased from 2 N to 10 N. In vacuum, higher normal load can significantly shorten the lifetime of DLC films (Kunze et al., 2014). The influencing mechanism of normal load is multi-faceted.

Figure 6. (A) Friction coefficients of self-mated a-C:H at different normal loads. (B) BF-STEM image of the scar center at 5 N (B) and 10 N (C). Bonding fraction of scar center at 5 N (D) and 10 N (E) calculated from EELS characterations. Adapted with permission from Chen et al. (2017) Copyright 2017, the authors.
Theoretically, the friction coefficient of dry sliding can be expressed as:
where Ff is friction force, Fn is normal load, Ar is real contact area, and τ is shear stress (Fontaine et al., 2008). Ar can be approximately replaced by Hertz contact area which is defended as:
where k is the ratio of the real contact area to the apparent contact area, A is the Hertz contact area, R and E are the effective radius and modulus of two surface materials, respectively. Then, the friction coefficient μ can be expressed as:
When the normal load increases, with the hypothesis that the DLC surface remains highly passivated (no structure change) and the shearing force τ generally stays constant, the correlation between normal load and friction coefficient is negative, which is believed to be one of the important factor for the lower friction under heavy load (Xue and Wang, 2012). However, as k increases with Fn, the negative influences of Fn on μ induced by contact area should be slighter than , which is lower than the tendency shown in experiments, indicating that the shearing force τ is negatively influenced by the increasing normal load.
As mentioned above, friction-induced thermal effect may be another possible reason for the negative correlation between normal load and friction coefficient. At the same circumstance, higher normal load would induce higher friction energy, which may result in a more significant temperature rise. However, according to Hertz contact theory, the contact diameter also increases with the normal load, which would partly restrain the temperature rise due to more effective thermal conduction. In formula (1), if we replace a with Hertz contact radius and replace μ with formula (4), the temperature rise can be expressed as:
Regarding that the shearing stress τ is also negatively affected by normal load for DLC films, the temperature rise induced by higher normal load should be lower. And it should be pointed out that temperature rising is more obvious during the high-friction state or running-in period. But for a typical superlubricity state, the friction energy dissipation is every low (for example, no more than 0.005 W in the experiment of Figure 6), and the temperature rise is supposed to be very small, which is not enough to individually induce significant structural change of DLC films. Normal load induced structural evolution of tribolayers should be the key factor for more superior properties under heavy load.
Experiments and simulations have indicated that friction induced structural evolution occurred during sliding contact, which could lead to a lower shearing force τ. During this process, normal load is a key factor. As shown in Figure 6, an extremely low friction of 0.001 was achieved with the highest normal load of 10 N. BF-STEM images and EELS results indicated that in this heavy-load condition, significant phase transformations of carbon bonds from sp2 to sp3 and local ordering appeared in the outer-most 3 nm region (Chen et al., 2017). These evidences suggest that higher normal load could facilitate the graphitization and hydrogen emission process in the contact area, leading to a nanostructured sliding surface with lower shearing forces. As shown in Figure 7, simulation with a-C films shows a similar trend that a higher normal load could induce more significant bond rehybridization, reorientation, and structural ordering within a localized shearing band, and friction state changes from stick-slip to continuous sliding with ultra-low friction (Ma et al., 2015).
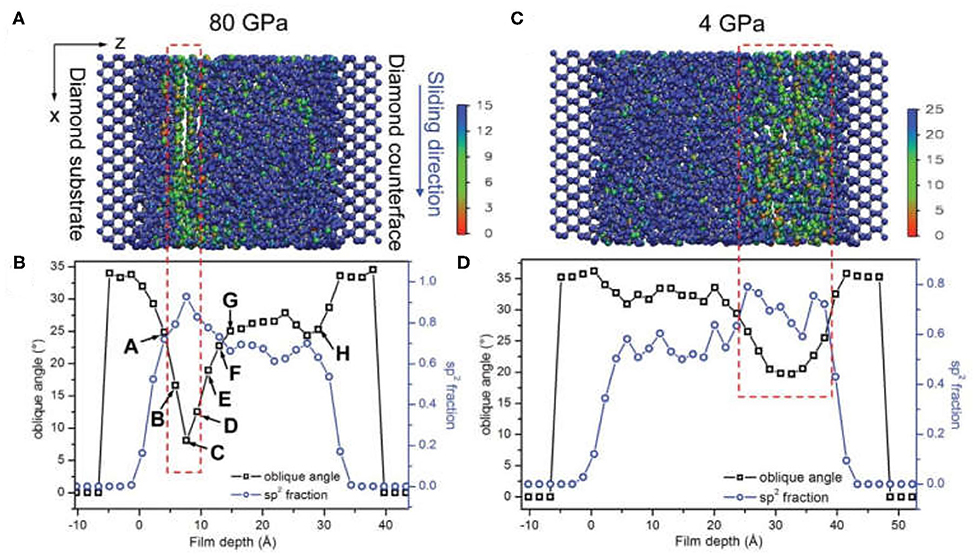
Figure 7. Shear localization and phase transformation of a-C films at different contact pressures. (A,C) System snapshots for 80 and 4 GPa. (B,D) Depth profiles of averaged C-C covalent bonding orientation angle and sp2 fraction. Adapted with permission from Ma et al. (2015) Copyright 2015, the authors.
When DLC films are coupled with other materials, the establishment of a robust carbonaceous transfer film on the counterpart material is a fundamental factor for superlubricity of DLC film, and this process is also influenced by the applied normal load, especially in the cases that the bonding strength between the counterpart material and carbon is relatively low (Xue and Wang, 2012). As shown in Figure 8, when Al2O3 ball was sliding against a-C:H films in vacuum at a normal load of 1 N, a stable ultralow friction coefficient of 0.002 was easily achieved and continuous carbonaceous transfer layers were formed on the ball. However, as the applied load increased to 3 N, the duration of superlubricity became shorter and ended up with a high friction state without transferfilm observed on the ball surface. Nevertheless, when these experiments were conducted in air, the stable state friction coefficient decreased from 0.15 to 0.06 with the normal load varied from 1 to 5 N, and an increasingly condensed transferfilm was developed on the ball scar (Liu Y. et al., 2019).
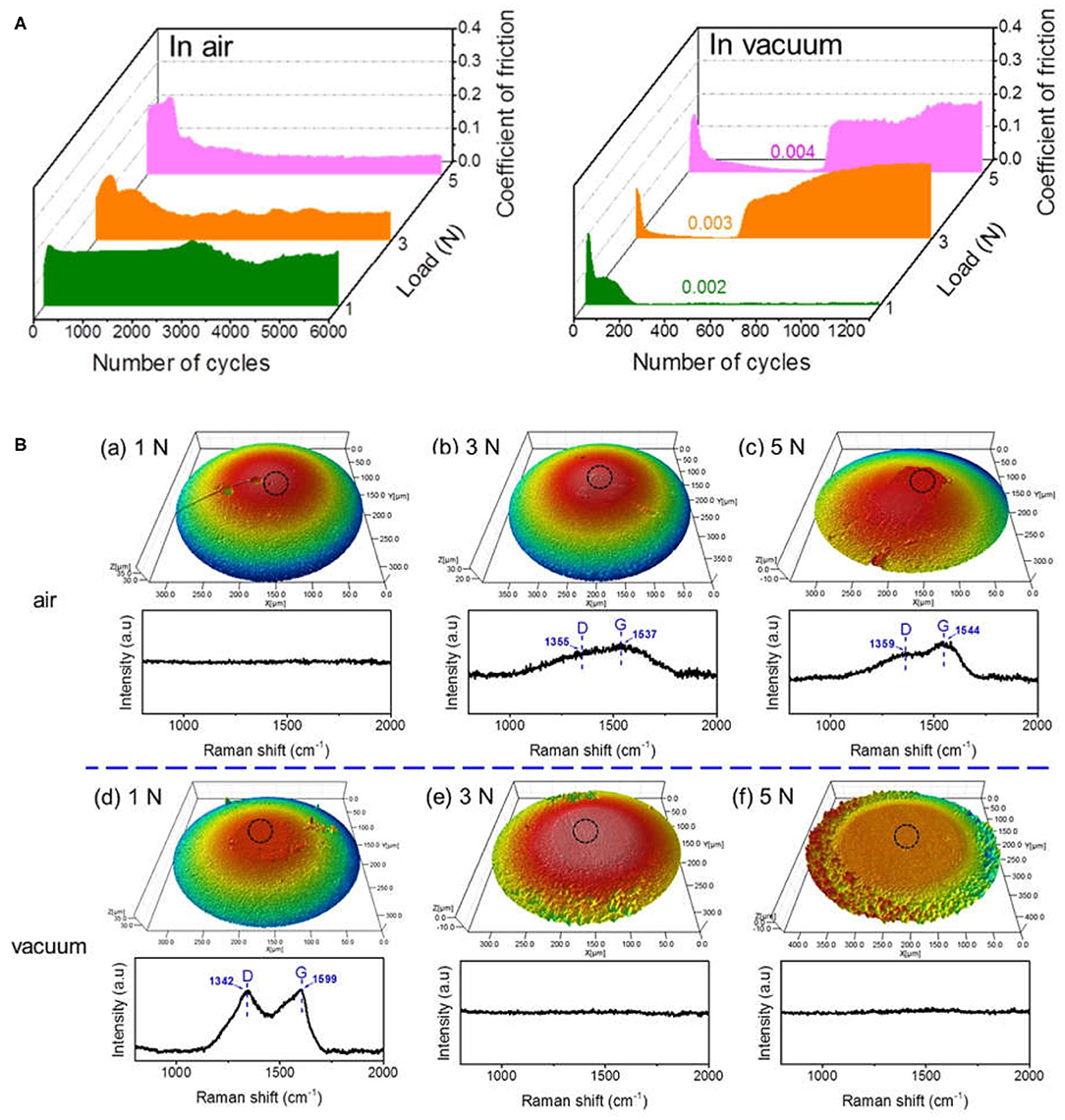
Figure 8. (A) Friction coefficient between a-C:H and Al2O3 in air and vacuum with different normal loads. (B) The wear scars of the ball surfaces after the tribo-testing and their Raman characterization. Adapted with permission from Liu Y. et al. (2019) Copyright 2019, the authors.
Sliding Velocity
Experiments have shown that sliding velocity also has a strong effect on superlubricity of DLC films. Generally, in ambient air or water vapor, higher sliding velocity will induce a decrease of friction coefficient (Kim et al., 2006; Xue and Wang, 2012). In inert gaseous ambient such as N2, similar trends were observed (Heimberg et al., 2001). To explain this phenomenon, multiple theories have been put forward. Friction induced thermal effect, gas absorption, and establishment of transfer-films are considered to be the influencing mechanisms for this trend.
As mentioned above, higher sliding speed will induce a more intense temperature rise due to higher friction energy, which is possible to promote the self-lubrication properties of DLC films. As shown in Formula (5), compared with normal load, sliding velocity has a more significant influence on temperature rise. Nevertheless, in most experiments, thermal effect is still not high enough to induce dramatic structural changes of tribofilm, as calculations suggest that for a high-friction running-in state (μ = 0.22, Fn= 1 N, v = 700 mm/s), the temperature rise ΔT is only 55.3°C (Liu et al., 2018), let alone the low energy dissipation of stable superlubricity state with friction coefficients lower than 0.01.
The most important factor for velocity dependence of superlubricious a-C:H is gas absorption. In gaseous environments, a chemical or physical absorbed layer exists on the surface of tribo-pairs, which will be removed during each sliding contact, causing energy dissipation, and occurrence of friction. According to the experiments coupled with the model based on kinetics of gas absorption (Borodich et al., 2007), higher sliding velocity will shorten the time interval between two slides of a single region, shortening the exposure time for gas absorption and reducing the energy cost for their remove. The influencing extent of sliding speed is closely related to the characteristics and density of ambient gases. For example, in ambient air (RH = 40%), when sliding speed increased from 262 to 2,093 mm/s, the friction coefficient was gradually reduced from 0.16 to 0.07. In contrast, their friction coefficients in nitrogen (RH = 5%) stayed constant around 0.02 for the same condition due to the relatively inert environment (Xue and Wang, 2012). Experiments under different pressures of water vapor showed that friction coefficient dropped faster with an increasing speed at relatively low pressure (Kim et al., 2006). Friction test with different reciprocating sliding distances at the same speed indicated that the exposure time dependence of superlubricity of DLC in nitrogen or carbon dioxide was significantly higher than that in argon. Moreover, with the increase of exposure time, their friction coefficient first decreased and then increased. Researchers suggested that there existed an optimized exposure time for nitrogen or carbon dioxide directionally absorbing with π bonds and leaving lone electron pair pointing outside, which could reduce friction due to repulsive force effect, inducing a minimum friction coefficient (Ji et al., 2009).
As mentioned above, when a-C:H coated planes slide against other materials, the establishment of a compact and continuous carbonaceous transfer layer on the ball side is an important factor for superlubricity. Likewise, researches have shown that when Al2O3 ball slides against a-C:H in vacuum, superlubricity state with friction coefficient of 0.003 can be achieved, as shown in Figure 9A. However, fluctuation of friction force increased with elevated sliding speed from 30 to 700 mm/s, and the proportion of superlubricity state decreased from 78.1 to 3.1%. According to SEM and Raman characteristics of the contact area, as shown in Figures 9B,C, the failure of superlubricity is always accompanied by the loss of transfer films. The authors believe that for this condition, excessive sliding speed will result in insufficient tribochemical interactions as well as intensified impact and vibration of friction interfaces, making it harder for transferlayers to be generated and tightly attached to the ball site, and resulting in the failure of superlubricity (Liu et al., 2018).
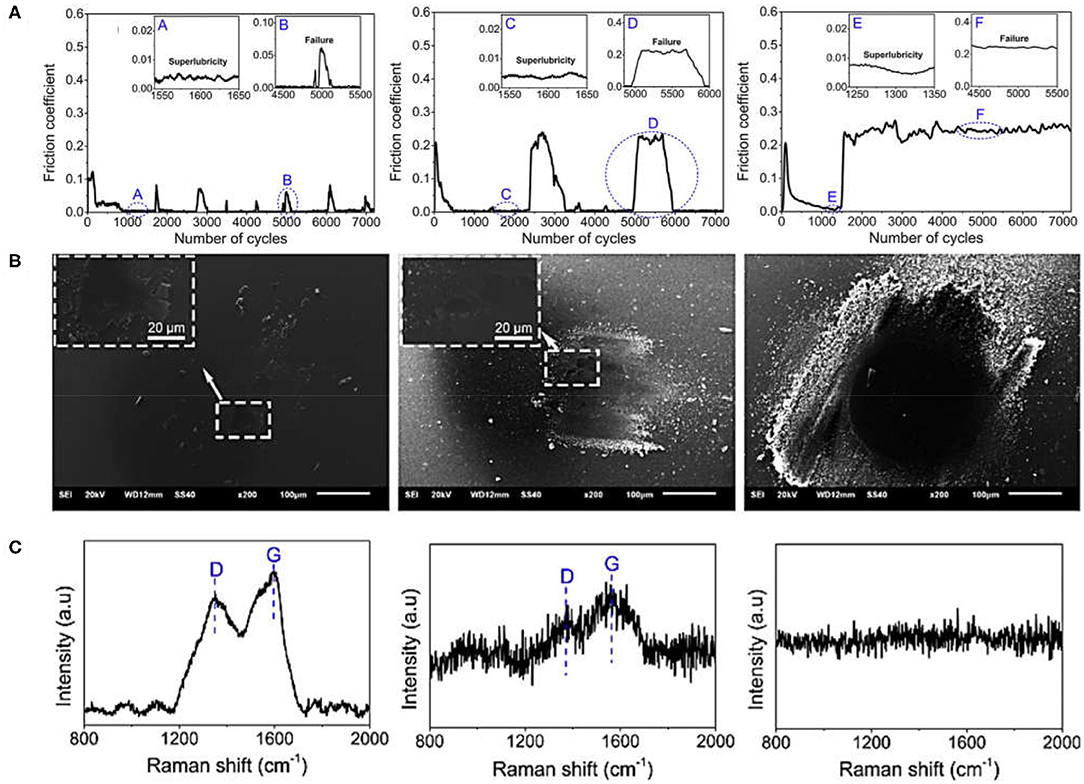
Figure 9. Velocity dependence of transfer layers in vacuum. (A) Friction coefficient curves for a-C:H against Al2O3 ball in vacuum at various sliding speeds. (B) SEM images and (C) Raman spectra of transfer layers generated in different sliding speeds. Adapted with permission from Liu et al. (2018) Copyright 2018, Elsevier B.V.
Discussion and Conclusion
The influencing factors and the mechanisms of superlubricity achieved with a-C:H films are multifaceted and interrelated. To date, diversified theories focusing on mechanical properties (Erdemir, 2004; Fontaine et al., 2004), establishment of transfer film (Chen et al., 2017; Liu et al., 2018; Liu Y. et al., 2019), surface passivation (Erdemir and Eryilmaz, 2014), and graphitization (Ma et al., 2015) have been brought up to explain the mechanism of solid superlubricity achieved with DLC films, and it seems that these factors are not working independently. Ultimately, the superlubricity state originates from the establishment of a sliding surface with low energy dissipation, meaning that the major interaction pathways between sliding surfaces are somehow sufficiently shielded. It is generally believed that the origin of friction force between solid surfaces can be qualitatively ascribed to three fundamental phenomena: abrasion, shearing, and adhesion (Fontaine et al., 2008), as shown in Figure 10. Abrasion is the plowing or scratching effect caused by micro-asperities or hard debris trapped between the sliding surfaces. Shearing is the energy consumption origins from the plastic or viscous flow of the material between the friction pairs. Adhesion is the resistance to break the micro-junctions bridging two sliding interfaces, mainly deriving from bonding force, electrostatic force, capillary force, and polarization forces. The realization of superlubricity needs all these friction contributors simultaneously to be limited at extremely low levels. DLC films exactly have the potential to accomplish this task owing to their numerous unique properties. Here, we can use superlubricious hydrogen-rich a-C:H film as an example for discussing.
From the mechanical perspective, DLC films exhibit special advantages in avoiding abrasion. Compared with other self-lubricating soft coatings, DLC films have higher hardness. For example, a hardness of 13.4 GPa for hydrogen-rich a-C:H film (Chen et al., 2017), is higher than that of common bearing steel or tool steel, which is generally around 10 GPa (Fontaine et al., 2008). Meanwhile, the surface roughness of DLC film is generally in accordance with their substrate, meaning that it can be controlled at an extremely low level, even atomically smooth. For example, the surface roughness of a-C:H film deposited on silicon wafer was 0.10 nm (Chen et al., 2017). The high hardness and ultrasmooth surface of DLC films can reduce the chance of abrasion in most cases. Moreover, due to the non-porous structure, hydrogen-rich DLC films also have unusual viscoelastic properties (Fontaine et al., 2004). As implied by the slow recovery of indents observed in nanoindentation experiments, a-C:H films may have some “healing” properties against scratches (Fontaine et al., 2008). These properties of DLC films can minimize the abrasive effect during sliding, paving the way for the establishment of stabilized, low-energy dissipation sliding interfaces.
When a-C:H film reaches a stable superlubricity state, the shearing behavior generally occurs inside an in-situ formed tribofilm or transferfilm with different mechanical properties, rather than in the film matrix (Fontaine et al., 2008). As shown in Figure 11, after friction against bare SUJ2 ball and Si3N4 ball, tribolayers of 27 and 5 nm thickness were generated on the balls, respectively. The establishment of these continuous, stably-attached carbonaceous tribofilms, together with the easy shearing nanostructure, will be a key factor for the superlubricity of DLC films (Liu et al., 2018; Liu Y. et al., 2019). High proportion of sp2 rehybridized carbon phase can be observed within the tribofilms, and obvious reorientation will be taking place under heavy normal loads, forming layer-like structure (Chen and Li, 2020). Simulations suggest that the significant drop of friction during running-in process is also accompanied with shearing localization, limiting the occurrence of sliding in a thin region (Ma et al., 2015). Meanwhile, near the sliding surface, the as-formed carbon rings with higher sp2 proportion are rotated parallel to the sliding direction, forming an interface with low proportion of out-of-plane sp3 bonds (Pastewka et al., 2010). The formation of easy-shearing sp2-C rich sliding interface (or called graphitization) and locally-ordered nanostructures, as well as the localization of shearing region, may be the key factors to keep the shearing resistance in a very low state, contributing to the stable superlubricious friction state.
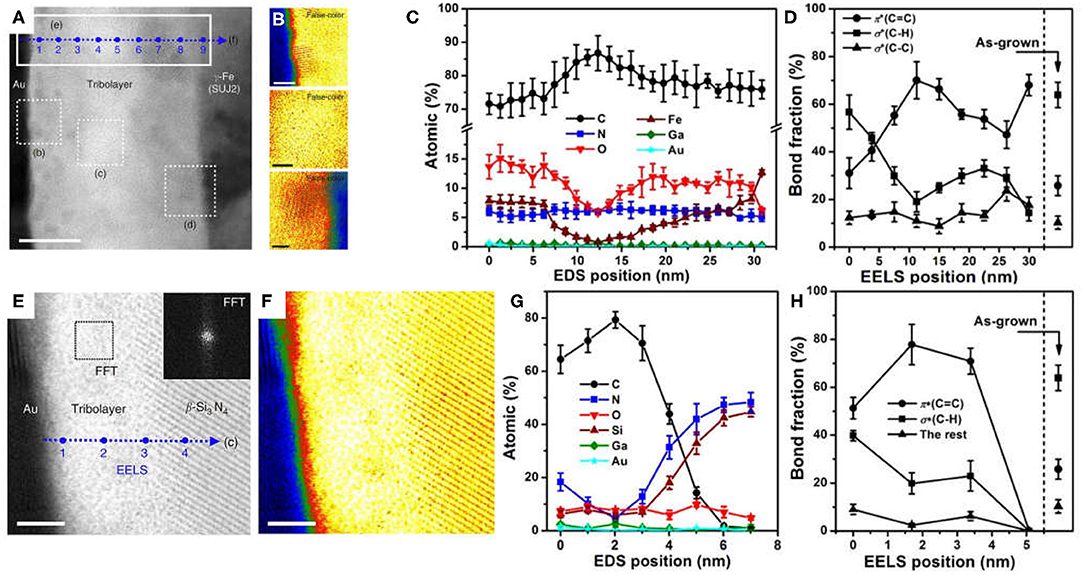
Figure 11. (A–D) Characterization of tribolayer generated on the ball surface for the friction pair of bare SUJ2 ball and a-C:H films. (A) BF-STEM image showing a tribolayer of ~27 nm generated on the SUJ2 ball. (B) False-color displayed BF-STEM images of three individual sublayers marked in (A). (C) The evolution of elemental composition across the tribolayer marked in (A). (D) Evolution of the calculated EELS C-bonds fractions across the tribolayer as marked in (A). (E–H) Characterization of tribolayer generated on ball surface for the friction pair of bare Si3N4 ball and a-C:H film. (E) BF-STEM image showing a tribolayer of ~5 nm generated on the Si3N4 ball. (F) False-color displayed BF-STEM images of (E). (G) The evolution of elemental composition across the tribolayer marked in (E). (H) Evolution of the calculated EELS C-bonds fractions across the tribolayer as marked in (E). Adapted with permission from Chen et al. (2017) Copyright 2017, the authors.
Tribological tests with DLC films in microscale have shown that the friction vs. normal load curve does not go through the origin, indicating that adhesion cannot be ignored (Shi et al., 2020). For a well-established carbon-based sliding interface, the adhesion phenomenon caused by the establishment and breaking of micro junctions across sliding surfaces is supposed to be the main contributor for the friction force (Fontaine et al., 2008). Firstly, σ dangling bonds generated during mechanical and tribochemical interactions have potential to form strong covalent bonds bridging the sliding surfaces, causing high adhesive friction and wear (Schall et al., 2010). This is the reason for the high friction of hydrogen-free DLC films in dry inert environment or vacuum and its prevention of friction via hydrogen gaseous environment or hydrogen contained in the film. The hydrogen species could react and passivate the dangling bonds generated at sliding surface timely, and hence eliminate the high friction caused by cross-linking of the interfacial bridging (Robertson, 2002). A self-terminated structure with carbon rings could be established during running-in process, leading to a continuous passivated interface with fewer dangling bonds exposed (Pastewka et al., 2010). Secondly, the interaction between out-of-plane π-orbitals of sp2 bonded carbon atoms, or π-π interaction, is another factor contributing to the friction force of DLC films. Likewise, this interaction can also be shielded by hydrogen, as they are reactive to carbon double bonds. Absorption of N2 and CO2 molecules can also restrain this phenomenon. Thirdly, for hydrogen-rich a-C:H films tested in humid environment, the hydrogen bond, and capillary force (mainly in micro-tribological experiments) induced by absorbed water layer are also contributors of friction force. Dry inert gaseous environments can prevent this phenomenon, thus superlubricity of a-C:H films can be achieved. Nevertheless, for hydrogen-free DLC, water can also act as a passivator preventing the strong π-π interactions and σ dangling bonds, leading to a relatively low friction, but has difficulty in achieving superlubricity. Fourthly, the van der Waals force is the weakest form for adhesion, and is the dominant factor for superlubricity state achieved with passivated DLC surfaces sliding in dry and inert environment. The repulsive coulombic force between two positively-charged C-H terminated interfaces can also account for the ultralow friction of DLC films.
To sum up, superlubricity of a-C:H films achieved in dry issnert environment mainly origins from three unique characteristics of the film: mechanical properties such as high hardness and viscoplastic properties and extremely low roughness, abilities in forming easy-shearing tribofilm or transferfilm through friction-induced phase transformation and bonding reorientation, abilities to passivate the sliding surface through self-contained hydrogen. All these factors work together to eliminate abrasion, shearing and adhesion effects to extremely low levels simultaneously, leading to superlubricity state. Basing on these understandings, involving other elements into the film is an effective approach to optimize their tribological properties since they could change the evolution process of tribofilms and state of sliding surface. As for gaseous ambient molecules, in addition to chemical involvement in the establishment of transfer film and passivation of sliding surface, they also influence friction force physically via thermal conduct and energy dissipation during desorption. Although the influence mechanisms of temperature, normal load, and sliding velocity are multifaceted, under the precondition that they are not crossing the threshold of the mechanical or thermal capacity of the film, their influencing trends mainly depend on whether they promote or deteriorate the evolution process of robust easy-shearing tribofilms and passivation of sliding surfaces.
Since the discovery of DLC films, their application as a self-lubricating and protective coating in mechanical engineering is increasingly broadened. For example, their applications in gearings (Michalczewski et al., 2019), bearings (Okamura et al., 2019), engine piston rings (Kumar et al., 2019), oil-well tubings (Liu L. et al., 2019), rubber seals (Liu J. Q. et al., 2019), and friction pairs in spacecraft (Donnet et al., 1999) have been testified to be effective and valuable. Superlubricity achieved with DLC coatings can provide a new concept to meet the increasing demand for lower energy consumption, longer life time, and higher power density of future mechanical systems, which has an enormous potential value from both economic and environmental perspectives. Nevertheless, it is still a challenge for engineering applications of superlubricious DLC films. More efforts should be concentrated on preventing their environmental sensitivity in humid condition and prolonging their service life in vacuum. Also, their performance still needs to be optimized in harsh working conditions such as extremely high or low temperature, extremely high pressure and velocity, and contaminated environment. Further researches on their superlubricity behaviors and mechanism can enable a more effective manipulation of DLC coatings with excellent self-lubrication properties.
Author Contributions
JL, CZ, and XC gave the guidance on the structure and content of this review. QY completed this review. All authors contributed to the article and approved the submitted version.
Funding
This work was funded by the National Natural Science Foundation of China (Grant Nos. 51975314, 51925506, and 51527901).
Conflict of Interest
The authors declare that the research was conducted in the absence of any commercial or financial relationships that could be construed as a potential conflict of interest.
References
Adachi, K., and Kato, K. (2008). “Tribology of carbon nitride coatings” in Tribology of Diamondlike Carbon Films: Fundamentals and Applications, eds C. Donnet and A. Erdemir (New York, NY: Springer), 339–361.
Aggleton, M., Burton, J. C., and Taborek, P. (2009). Cryogenic vacuum tribology of diamond and diamond-like carbon films. J. Appl. Phys. 106:013504. doi: 10.1063/1.3158339
Aisenberg, S., and Chabot, R. (1971). Ion-beam deposition of thin films of diamondlike carbon. J. Appl. Phys. 42, 2953–2958. doi: 10.1063/1.1660654
Al-Azizi, A. A., Eryilmaz, O., Erdemir, A., and Kim, S. H. (2015). Surface structure of hydrogenated diamond-like carbon: origin of run-in behavior prior to superlubricious interfacial shear. Langmuir 31, 1711–1721. doi: 10.1021/la504612c
Andersson, J., Erck, R. A., and Erdemir, A. (2003). Frictional behavior of diamondlike carbon films in vacuum and under varying water vapor pressure. Surface Coat. Technol. 163–164, 535–540. doi: 10.1016/S0257-8972(02)00617-5
Barel, I., Urbakh, M., Jansen, L., and Schirmeisen, A. (2010). Multibond dynamics of nanoscale friction: the role of temperature. Phys. Rev. Lett. 104:066104. doi: 10.1103/PhysRevLett.104.066104
Borodich, F. M., Korach, C. S., and Keer, L. M. (2007). Modeling the tribochemical aspects of friction and gradual wear of diamond-like carbon films. J. Appl. Mech. 74, 23–30. doi: 10.1115/1.2172267
Casiraghi, C., Ferrari, A. C., and Robertson, J. (2005). Raman spectroscopy of hydrogenated amorphous carbons. Phys. Rev. B 72:85401. doi: 10.1103/PhysRevB.72.085401
Chen, X., and Kato, T. (2014). Growth mechanism and composition of ultrasmooth a-C:H:Si films grown from energetic ions for superlubricity. J. Appl. Phys. 115, 2143–2201. doi: 10.1063/1.4863123
Chen, X., Kato, T., Kawaguchi, M., Nosaka, M., and Choi, J. (2013). Structural and environmental dependence of superlow friction in ion vapour-deposited a-C: H: Si films for solid lubrication application. J. Phys. D 46:255304. doi: 10.1088/0022-3727/46/25/255304
Chen, X., Kato, T., and Nosaka, M. (2014). Origin of superlubricity in a-C:H:Si films: a relation to film bonding structure and environmental molecular characteristic. ACS Appl. Mater. Inter. 6, 13389–13405. doi: 10.1021/am502416w
Chen, X., and Li, J. (2020). Superlubricity of carbon nanostructures. Carbon 158, 1–23. doi: 10.1016/j.carbon.2019.11.077
Chen, X., Zhang, C., Kato, T., Yang, X., Wu, S., Wang, R., et al. (2017). Evolution of tribo-induced interfacial nanostructures governing superlubricity in a-C:H and a-C:H:Si films. Nat. Commun. 8:1675. doi: 10.1038/s41467-017-01717-8
Dag, S., and Ciraci, S. (2004). Atomic scale study of superlow friction between hydrogenated diamond surfaces. Phys. Rev. B 70:241401. doi: 10.1103/PhysRevB.70.241401
De Barros Bouchet, M. I., Matta, C., Le-Mogne, T., Martin, J. M., Sagawa, T., Okuda, S., et al. (2007). Improved mixed and boundary lubrication with glycerol-diamond technology. Tribol. Mater. Surf. Interfaces 1, 28–32. doi: 10.1179/175158407x181507
Dienwiebel, M., Verhoeven, G. S., Pradeep, N., and Frenken, J. W. M. (2004). Superlubricity of graphite. Phys. Rev. Lett. 92:126101. doi: 10.1103/PhysRevLett.92.126101
Donnet, C., Belin, M., Augé, J. C., Martin, J. M., Grill, A., and Patel, V. (1994). Tribochemistry of diamond-like carbon coatings in various environments. Surf. Coat. Technol. 68–69, 626–631. doi: 10.1016/0257-8972(94)90228-3
Donnet, C., Fontaine, J., Le Mogne, T., Belin, M., Héau, C., Terrat, J. P., et al. (1999). Diamond-like carbon-based functionally gradient coatings for space tribology. Surf. Coat. Technol. 120–121, 548–554. doi: 10.1016/S0257-8972(99)00432-6
Donnet, C., and Grill, A. (1997). Friction control of diamond-like carbon coatings. Surf. Coat. Technol. 94–95, 456–462. doi: 10.1016/S0257-8972(97)00275-2
Donnet, C., Mogne, T. L., Ponsonnet, L., Belin, M., Grill, A., Patel, V., et al. (1998). The respective role of oxygen and water vapor on the tribology of hydrogenated diamond-like carbon coatings. Tribol. Lett. 4, 259–265. doi: 10.1023/A:1019140213257
Enke, K. (1981). Some new results on the fabrication of and the mechanical, electrical and optical properties of i-carbon layers. Thin Solid Films 80, 227–234. doi: 10.1016/0040-6090(81)90226-1
Erdemir, A. (2001). The role of hydrogen in tribological properties of diamond-like carbon films. Surf. Coat. Technol. 146–147, 292–297. doi: 10.1016/S0257-8972(01)01417-7
Erdemir, A. (2004). Genesis of superlow friction and wear in diamondlike carbon films. Tribol. Int. 37, 1005–1012. doi: 10.1016/j.triboint.2004.07.018
Erdemir, A., and Eryilmaz, O. (2014). Achieving superlubricity in DLC films by controlling bulk, surface, and tribochemistry. Friction 2, 140–155. doi: 10.1007/s40544-014-0055-1
Erdemir, A., and Eryilmaz, O. L. (2007). “Superlubricity in diamondlike carbon films” in Superlubricity, eds A. Erdemir and J. Martin (Amsterdam: Elsevier Science B.V.), 253–271.
Erdemir, A., Eryilmaz, O. L., and Fenske, G. (2000c). Synthesis of diamondlike carbon films with superlow friction and wear properties. J. Vacuum Sci. Technol. A 18, 1987–1992. doi: 10.1116/1.582459
Erdemir, A., Eryilmaz, O. L., Nilufer, I. B., and Fenske, G. R. (2000a). Effect of source gas chemistry on tribological performance of diamond-like carbon films. Diam. Relat. Mater. 9, 632–637. doi: 10.1016/S0925-9635(99)00361-1
Erdemir, A., Eryilmaz, O. L., Nilufer, I. B., and Fenske, G. R. (2000b). Synthesis of superlow-friction carbon films from highly hydrogenated methane plasmas. Surf. Coat. Technol. 133–134, 448–454. doi: 10.1016/S0257-8972(00)00968-3
Erdemir, A., Switala, M., Wei, R., and Wilbur, P. (1991). A tribological investigation of the graphite-to-diamond-like behavior of amorphous carbon films ion beam deposited on ceramic substrates. Surf. Coat. Technol. 50, 17–23. doi: 10.1016/0257-8972(91)90187-2
Eryilmaz, O. L., and Erdemir, A. (2008). On the hydrogen lubrication mechanism(s) of DLC films: an imaging TOF-SIMS study. Surf. Coat. Tech. 203, 750–755. doi: 10.1016/j.surfcoat.2008.06.156
Fink, J., Müller-Heinzerling, T., Pflüger, J., Bubenzer, A., Koidl, P., and Crecelius, G. (1983). Structure and bonding of hydrocarbon plasma generated carbon films: An electron energy loss study. Solid State Commun. 47, 687–691. doi: 10.1016/0038-1098(83)90635-X
Fontaine, J., Donnet, C., and Erdemir, A. (2008). “Fundamentals of the tribology of DLC coatings” in Tribology of Diamondlike Carbon Films: Fundamentals and Applications (New York, NY: Springer), 139–154.
Fontaine, J., Donnet, C., Grill, A., and LeMogne, T. (2001). Tribochemistry between hydrogen and diamond-like carbon films. Surf. Coat Technol. 146–147, 286–291. doi: 10.1016/S0257-8972(01)01398-6
Fontaine, J., Le Mogne, T., Loubet, J. L., and Belin, M. (2005). Achieving superlow friction with hydrogenated amorphous carbon: some key requirements. Thin Solid Films 482, 99–108. doi: 10.1016/j.tsf.2004.11.126
Fontaine, J., Loubet, J. L., Mogne, T. L., and Grill, A. (2004). Superlow friction of diamond-like carbon films: a relation to viscoplastic properties. Tribol. Lett. 17, 709–714. doi: 10.1007/s11249-004-8077-x
Freyman, C. A., Chen, Y., and Chung, Y. (2006). Synthesis of carbon films with ultra-low friction in dry and humid air. Surf. Coat. Technol. 201, 164–167. doi: 10.1016/j.surfcoat.2005.11.075
Gao, G. T., Mikulski, P. T., Chateauneuf, G. M., and Harrison, J. A. (2003). The effects of film structure and surface hydrogen on the properties of amorphous carbon films. J. Phys. Chem. B 107, 11082–11090. doi: 10.1021/jp034544+
Gong, Z., Shi, J., Zhang, B., and Zhang, J. (2017). Graphene nano scrolls responding to superlow friction of amorphous carbon. Carbon 116, 310–317. doi: 10.1016/j.carbon.2017.01.106
Goto, M., and Honda, F. (2004). Film-thickness effect of Ag lubricant layer in the nano-region. Wear 256, 1062–1071. doi: 10.1016/s0043-1648(03)00530-1
Heimberg, J. A., Wahl, K. J., Singer, I. L., and Erdemir, A. (2001). Superlow friction behavior of diamond-like carbon coatings: time and speed effects. Appl. Phys. Lett. 78, 2449–2451. doi: 10.1063/1.1366649
Hirano, M., and Shinjo, K. (1990). Atomistic locking and friction. Phys. Rev. B 41, 11837–11851. doi: 10.1103/PhysRevB.41.11837
Hirano, M., Shinjo, K., Kaneko, R., and Murata, Y. (1991). Anisotropy of frictional forces in muscovite mica. Phys. Rev. Lett. 67, 2642–2645. doi: 10.1103/PhysRevLett.67.2642
Hirano, M., Shinjo, K., Kaneko, R., and Murata, Y. (1997). Observation of superlubricity by scanning tunneling microscopy. Phys. Rev. Lett. 78, 1448–1451. doi: 10.1103/PhysRevLett.78.1448
Holmberg, K., and Erdemir, A. (2017). Influence of tribology on global energy consumption, costs and emissions. Friction 5, 263–284. doi: 10.1007/s40544-017-0183-5
Jantschner, O., Field, S. K., Music, D., Terziyska, V. L., Schneider, J. M., Munnik, F., et al. (2014). Sputtered Si-containing low-friction carbon coatings for elevated temperatures. Tribol. Int. 77, 15–23. doi: 10.1016/j.triboint.2014.04.006
Ji, L., Li, H., Zhao, F., Quan, W., Chen, J., and Zhou, H. (2009). Effects of environmental molecular characteristics and gas–surface interaction on friction behaviour of diamond-like carbon films. J. Phys. D 42:135301. doi: 10.1088/0022-3727/42/13/135301
Jiang, J., Hao, J., Wang, P., and Liu, W. (2010). Superlow friction of titanium/silicon codoped hydrogenated amorphous carbon film in the ambient air. J. Appl. Phys. 108:033510. doi: 10.1063/1.3462469
Kano, M. (2006). Super low friction of DLC applied to engine cam follower lubricated with ester-containing oil. Tribol. Int. 39, 1682–1685. doi: 10.1016/j.triboint.2006.02.068
Kato, K., Umehara, N., and Adachi, K. (2003). Friction, wear and N2-lubrication of carbon nitride coatings: a review. Wear 254, 1062–1069. doi: 10.1016/S0043-1648(03)00334-X
Kato, T., Matsuoka, H., Kawaguchi, M., and Nosaka, M. (2018). Possibility of elasto-hydrostatic evolved-gas bearing as one of the mechanisms of superlubricity. Proc. Instit. Mech. Eng. Part J 233, 532–540. doi: 10.1177/1350650117746025
Kim, H. I., Lince, J. R., Eryilmaz, O. L., and Erdemir, A. (2006). Environmental effects on the friction of hydrogenated DLC films. Tribol. Lett. 21, 51–56. doi: 10.1007/s11249-005-9008-1
Kumar, N., Sharma, N., Dash, S., Popov, C., Kulisch, W., Reithmaier, J. P., et al. (2011). Tribological properties of ultrananocrystalline diamond films in various test atmosphere. Tribol. Int. 44, 2042–2049. doi: 10.1016/j.triboint.2011.09.003
Kumar, V., Sinha, S. K., and Agarwal, A. K. (2019). Wear evaluation of engine piston rings coated with dual layer hard and soft coatings. J. Tribol. 141:031301. doi: 10.1115/1.4041762
Kunze, T., Posselt, M., Gemming, S., Seifert, G., Konicek, A. R., Carpick, R. W., et al. (2014). Wear, plasticity, and rehybridization in tetrahedral amorphous carbon. Tribol. Lett. 53, 119–126. doi: 10.1007/s11249-013-0250-7
Kuwahara, T., Romero, P. A., Makowski, S., Weihnacht, V., Moras, G., and Moseler, M. (2019). Mechano-chemical decomposition of organic friction modifiers with multiple reactive centres induces superlubricity of ta-C. Nat. Commun. 10:151. doi: 10.1038/s41467-018-08042-8
Lee, K. Y., and Wei, R. (2006). Tribological characteristics of DLC-coated alumina at high temperatures. J. Tribol. 128, 711–717. doi: 10.1115/1.2345395
Liu, E., Ding, Y. F., Li, L., Blanpain, B., and Celis, J. P. (2007). Influence of humidity on the friction of diamond and diamond-like carbon materials. Tribol. Int. 40, 216–219. doi: 10.1016/j.triboint.2005.09.012
Liu, J. Q., Wu, Z. Y., Cao, H. T., Wen, F., and Pei, Y. T. (2019). Effect of bias voltage on the tribological and sealing properties of rubber seals modified by DLC films. Surf. Coat. Technol. 360, 391–399. doi: 10.1016/j.surfcoat.2018.12.100
Liu, L., Wu, Z., Cui, S., An, X., Ma, Z., Shao, T., et al. (2019). Abrasion and erosion behavior of DLC-coated oil-well tubings in a heavy oil/sand environment. Surf. Coat. Technol. 357, 379–383. doi: 10.1016/j.surfcoat.2018.09.081
Liu, X., Yang, J., Hao, J., Zheng, J., Gong, Q., and Liu, W. (2012). A near-frictionless and extremely elastic hydrogenated amorphous carbon film with self-assembled dual nanostructure. Adv. Mater. 24, 4614–4617. doi: 10.1002/adma.201200085
Liu, Y., Chen, L., Zhang, B., Cao, Z., Shi, P., Peng, Y., et al. (2019). Key role of transfer layer in load dependence of friction on hydrogenated diamond-like carbon films in humid air and vacuum. Materials 12:1550. doi: 10.3390/ma12091550
Liu, Y., Erdemir, A., and Meletis, E. I. (1996). An investigation of the relationship between graphitization and frictional behavior of DLC coatings. Surf. Coat. Tech. 86–87, 564–568. doi: 10.1016/s0257-8972(96)03057-5
Liu, Y., Yu, B., Cao, Z., Shi, P., Zhou, N., Zhang, B., et al. (2018). Probing superlubricity stability of hydrogenated diamond-like carbon film by varying sliding velocity. Appl. Surf. Sci. 439, 976–982. doi: 10.1016/j.apsusc.2018.01.048
Ma, T., Wang, L., Hu, Y., Li, X., and Wang, H. (2015). A shear localization mechanism for lubricity of amorphous carbon materials. Sci. Rep. 4:3662. doi: 10.1038/srep03662
Mangolini, F., Krick, B. A., Jacobs, T. D. B., Khanal, S. R., Streller, F., McClimon, J. B., et al. (2018). Effect of silicon and oxygen dopants on the stability of hydrogenated amorphous carbon under harsh environmental conditions. Carbon 130, 127–136. doi: 10.1016/j.carbon.2017.12.096
Martin, J. M., Donnet, C., Mogne, T. L., and Epicier, T. (1993). Superlubricity of molybdenum disulphide. Phys. Rev. B Cond. Matter 48, 10583–10586. doi: 10.1103/PhysRevB.48.10583
Michalczewski, R., Kalbarczyk, M., Mankowska-Snopczynska, A., Osuch-Słomka, E., Piekoszewski, W., Snarski-Adamski, A., et al. (2019). The effect of a gear oil on abrasion, scuffing, and pitting of the DLC-coated 18CrNiMo7-6 steel. Coatings 9:2. doi: 10.3390/coatings9010002
Miura, K., Tsuda, D., and Sasaki, N. (2005). Superlubricity of C60 intercalated graphite films. E J. Surf. Sci. Nanotechnol. 3, 21–23. doi: 10.1380/ejssnt.2005.21
Moolsradoo, N., and Watanabe, S. (2010). Modification of tribological performance of DLC films by means of some elements addition. Diam. Relat. Mater. 19, 525–529. doi: 10.1016/j.diamond.2010.01.010
Moras, G., Pastewka, L., Gumbsch, P., and Moseler, M. (2011). Formation and oxidation of linear carbon chains and their role in the wear of carbon materials. Tribol. Lett. 44, 355–365. doi: 10.1007/s11249-011-9864-9
Nevshupa, R., Caro, J., Arratibel, A., Bonet, R., Rusanov, A., Ares, J. R., et al. (2019). Evolution of tribologically induced chemical and structural degradation in hydrogenated a-C coatings. Tribol. Int. 129, 177–190. doi: 10.1016/j.triboint.2018.08.023
Nobili, L., and Guglielmini, A. (2013). Thermal stability and mechanical properties of fluorinated diamond-like carbon coatings. Surf. Coat. Technol. 219, 144–150. doi: 10.1016/j.surfcoat.2013.01.018
Nosaka, M., Morisaki, Y., Fujiwara, T., Tokai, H., Kawaguchi, M., and Kato, T. (2017). The run-in process for stable friction fade-out and tribofilm analyses by SEM and nano-indenter. Tribol. Online 12, 274–280. doi: 10.2474/trol.12.274
Okamura, Y., Suzuki, D., Ikoma, K., Nagatomo, T., and Utsunomiya, H. (2019). Effects of segment-structured DLC film on the fretting wear of railway axle journal bearings. Mech. Eng. 6:18–00446. doi: 10.1299/mej.18-00446
Okubo, H., Tsuboi, R., and Sasaki, S. (2015). Frictional properties of DLC films in low-pressure hydrogen conditions. Wear 340–341, 2–8. doi: 10.1016/j.wear.2015.03.018
Pastewka, L., Moser, S., and Moseler, M. (2010). Atomistic insights into the running-in, lubrication, and failure of hydrogenated diamond-like carbon coatings. Tribol. Lett. 39, 49–61. doi: 10.1007/s11249-009-9566-8
Pastewka, L., Moser, S., Moseler, M., Blug, B., Meier, S., Hollstein, T., et al. (2008). The running-in of amorphous hydrocarbon tribocoatings: a comparison between experiment and molecular dynamics simulations. Int. J. Mater. Res. 99, 1136–1143. doi: 10.3139/146.101747
Robertson, J. (2002). Diamond-like amorphous carbon. Mater. Sci. Eng. R Rep. 37, 129–281. doi: 10.1016/S0927-796X(02)00005-0
Ronkainen, H., and Holmberg, K. (2008). “Environmental and thermal effects on the tribological performance of DLC coatings,” in Tribology of Diamond-Like Carbon: Fundamentals and Applications, eds C. Donnet and A. Erdemir (New York, NY: Springer), 155–200.
Schall, J. D., Gao, G., and Harrison, J. A. (2010). Effects of adhesion and transfer film formation on the tribology of self-mated DLC contacts. J. Phys. Chem. C 114, 5321–5330. doi: 10.1021/jp904871t
Shi, P., Sun, J., Yan, W., Zhou, N., Zhang, J., Zhang, J., et al. (2020). Roles of phase transition and surface property evolution in nanotribological behaviors of H-DLC: Effects of thermal and UV irradiation treatments. Appl. Surf. Sci. 514:145960. doi: 10.1016/j.apsusc.2020.145960
Shukla, N., Svedberg, E., van der Veerdonk, R. J. M., Ma, X., and Gellman, A. J. (2003). Water adsorption on lubricated aCH x in humid environments. Tribol. Lett. 15, 9–14. doi: 10.1023/A:1023503904927
Socoliuc, A., Bennewitz, R., Gnecco, E., and Meyer, E. (2004). Transition from stick-slip to continuous sliding in atomic friction: entering a new regime of ultralow friction. Phys. Rev. Lett. 92:134301. doi: 10.1103/PhysRevLett.92.134301
Song, Y., Davide, M., Oded, H., Michael, U., Ma, M., and Zheng, Q. (2018). Robust microscale superlubricity in graphite/hexagonal boron nitride layered heterojunctions. Nat. Mater. 17, 894–899. doi: 10.1038/s41563-018-0144-z
Su, C., and Lin, J. C. (1998). Thermal desorption of hydrogen from the diamond C(100) surface. Surf. Sci. 406, 0–166. doi: 10.1016/s0039-6028(98)00107-1
Sugimoto, I., and Miyake, S. (1990). Oriented hydrocarbons transferred from a high performance lubricative amorphous C:H:Si film during sliding in a vacuum. Appl. Phys. Lett. 56, 1868–1870. doi: 10.1063/1.103072
Tagawa, M., Ikemura, M., Nakayama, Y., and Ohmae, N. (2004). Effect of water adsorption on microtribological properties of hydrogenated diamond-like carbon films. Tribol. Lett. 17, 575–580. doi: 10.1023/B:TRIL.0000044507.44022.13
Vanhulsel, A., Velasco, F., Jacobs, R., Eersels, L., Havermans, D., Roberts, E. W., et al. (2007). DLC solid lubricant coatings on ball bearings for space applications. Tribol. Int. 40, 1186–1194. doi: 10.1016/j.triboint.2006.12.005
Voevodin, A. A., and Zabinski, S. J. (2000). Supertough wear-resistant coatings with ‘chameleon’ surface adaptation. Thin Solid Films 370, 223–231. doi: 10.1016/S0040-6090(00)00917-2
Wang, C., Yang, S., Wang, Q., Wang, Z., and Zhang, J. (2008). Super-low friction and super-elastic hydrogenated carbon films originated from a unique fullerene-like nanostructure. Nanotechnology 19:225709. doi: 10.1088/0957-4484/19/22/225709
Wang, Y., Wang, J., Zhang, G., Wang, L., and Yan, P. (2012). Microstructure and tribology of TiC(Ag)/a-C:H nanocomposite coatings deposited by unbalanced magnetron sputtering. Surf. Coat. Technol. 206, 3299–3308. doi: 10.1016/j.surfcoat.2012.01.036
Washizu, H., Sanda, S., Hyodo, S., Ohmori, T., Nishino, N., and Suzuki, A. (2007). Molecular dynamics simulations of elasto-hydrodynamic lubrication and boundary lubrication for automotive tribology. J. Phys. 89:012009. doi: 10.1088/1742-6596/89/1/012009
Xue, Q., and Wang, L. (2012). Nanoscience and Technology: Diamond-Like Carbon Film Materials. Beijing: Science Press (in Chinese).
Yamamoto, S., Liskiewicz, T., Fujimura, K., Tashiro, K., and Takai, O. (2019). Temperature rise of diamond-like carbon during sliding: consideration of the real contact area. Tribol. Int. 131, 496–507. doi: 10.1016/j.triboint.2018.09.022
Zeng, Q., Cao, Q., Erdemir, A., Li, S., and Zhu, J. (2018). Current development situation of superlow friction behavior of DLC films. China Surf. Eng. 31, 1–19. doi: 10.11933/j.issn.1007-9289.20180202002 (in Chinese).
Zeng, Q., Eryilmaz, O., and Erdemir, A. (2015). Superlubricity of the DLC films-related friction system at elevated temperature. RSC Adv. 5, 93147–93154. doi: 10.1039/C5RA16084G
Zeng, Q., Yu, F., and Dong, G. (2013). Superlubricity behaviors of Si3N4/DLC films under PAO oil with nano boron nitride additive lubrication. Surf. Interface Anal. 45, 1283–1290. doi: 10.1002/sia.5269
Zhang, R., Ning, Z., Zhang, Y., Zheng, Q., Chen, Q., Xie, H., et al. (2013). Superlubricity in centimetres-long double-walled carbon nanotubes under ambient conditions. Nat. Nanotechnol. 8, 912–916. doi: 10.1038/nnano.2013.217
Zhang, S., Wagner, G., Medyanik, S. N., Liu, W., Yu, Y., and Chung, Y. (2004). Experimental and molecular dynamics simulation studies of friction behavior of hydrogenated carbon films. Surf. Coat. Technol. 177–178, 818–823. doi: 10.1016/j.surfcoat.2003.06.022
Zhang, W., Tanaka, A., Wazumi, K., and Koga, Y. (2002). Effect of environment on friction and wear properties of diamond-like carbon film. Thin Solid Films 413, 104–109. doi: 10.1016/s0040-6090(02)00351-6
Zhao, F., Li, H., Ji, L., Wang, Y., Liu, X., Zhou, H., et al. (2016). Effect of microstructural evolution on mechanical and tribological properties of Ti-doped DLC films: how was an ultralow friction obtained? J. Vacuum Sci. Technol. 34:031504. doi: 10.1116/1.4944053
Keywords: diamond-like carbon, superlubricity, friction, influence factor, mechanism
Citation: Yu Q, Chen X, Zhang C and Luo J (2020) Influence Factors on Mechanisms of Superlubricity in DLC Films: A Review. Front. Mech. Eng. 6:65. doi: 10.3389/fmech.2020.00065
Received: 21 May 2020; Accepted: 06 July 2020;
Published: 11 August 2020.
Edited by:
Valentin L. Popov, Technical University of Berlin, GermanyReviewed by:
Lars Pastewka, University of Freiburg, GermanyWenling Zhang, University of Alberta, Canada
Copyright © 2020 Yu, Chen, Zhang and Luo. This is an open-access article distributed under the terms of the Creative Commons Attribution License (CC BY). The use, distribution or reproduction in other forums is permitted, provided the original author(s) and the copyright owner(s) are credited and that the original publication in this journal is cited, in accordance with accepted academic practice. No use, distribution or reproduction is permitted which does not comply with these terms.
*Correspondence: Chenhui Zhang, Y2h6aGFuZ0B0c2luZ2h1YS5lZHUuY24=