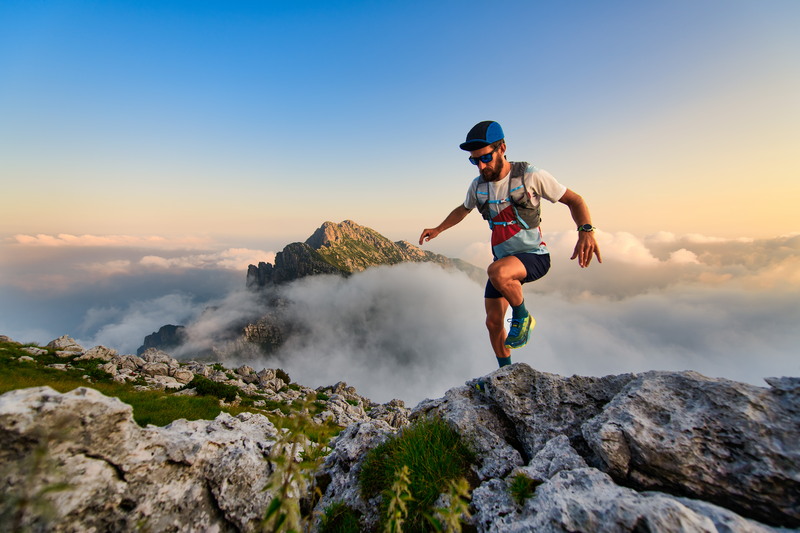
95% of researchers rate our articles as excellent or good
Learn more about the work of our research integrity team to safeguard the quality of each article we publish.
Find out more
ORIGINAL RESEARCH article
Front. Mech. Eng. , 29 July 2020
Sec. Tribology
Volume 6 - 2020 | https://doi.org/10.3389/fmech.2020.00056
This article is part of the Research Topic Contact mechanics perspective of tribology View all 37 articles
The production process significantly influences the surface properties of rolling element bearings raceways. Deep rolling can induce a depth dependent residual stress state. Previous numerical and experimental studies have shown that rolling bearings fatigue life can be positively influenced by high compressive residual stress to a depth of around 300 μm from the surface. By extending the components life, the resource efficiency of machine components can be increased. In order to determine the influence of the residual stress state in bearing fatigue life, a calculation method was developed for predicting the bearing fatigue life. This method was validated for hard-turning and subsequent deep rolling by experiments on a test rig in four-bearing configuration under radial load. An increase of the L10 bearing life by a factor of 2.5 has been achieved by inducing residual stresses on the bearing's inner ring. Due to similar process control, the manufacturing steps turning and deep rolling were combined. Bearings were manufactured combining the processes hard-turning and deep rolling (called turn-rolling). The heat from the hard machining has an effect on the residual stresses in the bearing subsurface, thus further altering the magnitude and maximum depth of the residual stress influencing the microstructure. With these bearings, the additional fatigue life was determined experimentally and compared to the results of the bearings produced by hard-turning and subsequent deep rolling. It could be shown, that the process of hard turning and subsequent deep rolling has highest potential to achieve improved bearing fatigue life. These findings were transferred to a “Tailored Forming” shaft with integrated raceway in a second step. In this case, a shaft made of mild steel is combined with a cladding layer of high strength bearing steel to be used as a bearing raceway.
A high reliability of machine elements under relative motion is of main importance. The dimensions of machine elements are calculated for reliability. Bearings properties as typical highly loaded machine elements are based on proven conventional production techniques. During operation bearings have to resist very high cyclic stresses. The fatigue life of rolling bearings is influenced in particular by the raceway properties. Böhmer provides an overview of the load conditions and material behavior of rolling contacts in Böhmer (1998). The author defines a large number of influencing variables on component fatigue life: surface micro topography, especially under mixed lubrication, lubricant and its contamination, residual stresses, and temperature effects as well as the material and the heat treatment processes. The cyclical rolling of the rolling elements over the raceways of inner and outer ring causes alternating stresses in the material volume of the contact partners. This can finally result in the nucleation of fatigue cracks in the very high cycle regime, which is known as rolling contact fatigue (RCF). If the alternating stress continues, crack growth processes occur on the boundary layer resulting in the separation of particles from the surface. Under ideal lubrication conditions the resulting chips, known as pittings, are one of the main causes of rolling bearing failure in practical applications (Glaeser and Shaffer, 1996).
Zwirlein and Schlicht (1989) describe the development of residual stresses due to the actual over-rolling process. They also describe the resulting equivalent stresses in the Hertzian contact zone as a function of existing residual stresses and friction occurring at the transition from full film lubrication to mixed lubrication. Under the influence of friction, the maximum of the equivalent stress of the multi-dimensional stress state below the running surface shifts increasingly in the rolling direction and toward the surface.
According to Voskamp, the material zone beneath the overrolled raceway goes through three phases over the period of the bearing's fatigue life in which a change of the microstructure takes place (Voskamp, 1985). In the first phase, named “shakedown phase,” which is occurring within the first 1,000 revolutions, plastic micro-deformations take place in the area below the raceway surfaces, leading to work hardening of the bearing material. It is characterized by the rapid reduction of residual austenite trapped in the martensitic structure of the bearing material and the build-up of residual compressive stresses. The extent of the changes depends on the load acting on the bearing. In the subsequent stationary second phase, also called steady-state phase, practically no plastic deformation and no structural change takes place. The duration of the stationary phase depends on the level of the load. For loads exceeding the “shakedown limit,” there is a direct transition from the first to the third phase. For small loads, the fatigue process remains in the second phase and no transition to the third phase takes place, and thus no component failure due to RCF occurs. In the third phase, the so called “instability phase,” the component subsurface can no longer absorb the acting loads in the form of elastic deformation. As a result of the cyclic contact conditions, a further change in the complex residual stress state of the microstructure occurs. The micro plastic deformations evolve to macro plastic deformations and result in component failure. Hollox et al. were able to detect the course and magnitude of the residual stresses below the raceways as a function of the running times for radially loaded deep groove ball bearings by X-ray diffraction (XRD) (Hollox et al., 1987). The alignment of the crystal structure as a result of the rolling stress and thus the formation of a texture in the subsurface of the rolling bearing was also determined and recognized as a characteristic feature of the third phase of the fatigue process. The development of residual stresses in near-subsurface areas of the raceways during cyclic over rolling was also proven by theoretical investigations by (Hills, 1983).
Voskamp later experimentally determined an increase in bearing fatigue life by subjecting the inner rings to a running-in process (Voskamp, 1996). During this running-in process, the bearings were subjected to high loads for a short time of over rolling. In the subsequent fatigue life experiments under normal load, the fatigue life was increased by a factor of three in comparison to standard bearing inner rings (which were not run-in) could be determined. Voskamp carried out these investigations under full film lubrication.
Poll and Hacke investigated the effect of a short time of overload during the running in on cylindrical roller bearings of the size NU206 and NJ206 (Poll and Hacke, 2010). The bearings were subjected to two different loads: a short phase of high load (C/P = 2.5 Hertzian pressure pm = 3,000 N/mm2) as an overloading and subsequent operation under normal load (C/P = 4, pm = 2,500 N/mm2). In the statistical evaluation of the tests, it was determined that the running times of the collective tests with run-in at increased load were higher than those of the pure single-stage tests. The increased bearing fatigue life is assumed to be the result of residual compressive stresses introduced in the running-in phase.
Besides a preloading of the bearings, there is also the possibility of applying pre-induced residual stresses by the manufacturing process. A relatively new method is laser shot peening (Montros et al., 2002). By usage of a high energy laser pulse, a plasma shock wave is generated on a metallic surface. When the shock wave is transmitted into the steel surface, a plastic deformation results, which leads to residual compressive stresses.
Altenberger emphasizes the positive influence of temperature on SAE 1045 and AISI 304 during deep rolling (Altenberger, 2005). In case of AISI 304 a much higher fatigue lifetime improvement compared to ultrasonic shot peened, deep rolled, and laser shock peened samples could be achieved. In similar investigations it could be shown that by means of mechanical surface treatments, especially deep rolling, also for non-steel materials such as aluminum-7075-T6 (Majzoobi et al., 2009) and titanium Ti-6Al-4V (Nalla et al., 2003) an increase in fatigue life could be achieved.
Pabst was also able to prove an increase in the bearing fatigue life of rolling bearings which had been modified by deep-rolling in order to induce compressive residual stresses (Pabst, 2018). Additional shot peening was investigated. Pabst assumed that the residual stress state did not increase the bearing fatigue life as much. Rather, the subsequent induction hardening process and its influence on material microstructure increased the fatigue life. He mentioned that the magnitude of the measured residual stresses can serve as an indirect assessment criterion. The machining processes results in a finer-grained microstructure with positive properties with regards to deformation and fracture.
The effect of an enhanced induced residual stress state by deep rolling of cylindrical roller bearings (CRB) was investigated by Neubauer (2016). The deep rolling process can be enhanced in the depth of the achieved residual stresses by using the effect of heat. In this case the heat from the turning process can be used if the rolling ball is placed directly behind the turning tool (Pape et al., 2017).
The aim of this study is to provide guidelines for optimized manufacturing processes for so called “Tailored Forming” machine elements such as multi-material shafts with integrated raceways for CRBs, as used in Coors et al. (2018). Thus, the here presented results based on a former project on the influence of production processes on the fatigue performance of machine elements are elaborated and transferred. The scheme of a Tailored Forming shaft is shown in Figure 1. In this case, a novel process chain for the production of load-adapted machine elements using steel-steel multi-material systems has been developed. A bearing steel with a high resistance to wear and fatigue like 100Cr6 (material number: 1.3505/SAE 52100) or better, is applied by plasma powder deposition welding on low-cost steel shafts, c.f. (Golovin et al., 2019). This allows for the local deposition of high strength steel, which serves as the raceway for a rolling element bearing and covers the fatigue life-determining material volume regarding rolling contact fatigue, c.f. (Behrens et al., 2019). The base material allows for basic requirements regarding structural load-bearing capacity, thus serving as a support structure and for the mechanical connection to other components. This hybrid workpiece is then formed by cross wedge rolling to achieve a fine grained microstructure, c.f. (Kruse et al., 2019). The finishing process is carried out by local induction hardening and hard-turning, and will be extended by deep rolling, c.f. (Denkena et al., 2019). In order to optimize the finishing process, the production steps and their effect on the bearing service life will be examined more closely.
For the investigations, CRB type NU206 were used as exemplary object of investigation for fatigue life effects of residual compressive stresses regarding RCF. Bearing inner rings were machined at the Institute of Production Engineering and Machine Tools, Leibniz University Hannover, Germany as shown in Denkena et al. (2016a). The bearings are made of 100Cr6 steel, and feature a hardness of 62 HRC. For the hard-turning process, carbide inserts with Al2O3 + Ti(C,N) coating were chosen. A hydrostatic rolling tool was used for the deep rolling process. In this case the bearings were prepared in a first step by hard-turning and subsequently the bearings were deep rolled. The combination of hard turning and deep rolling leads to an improved surface quality (Maiß et al., 2017). Due to the high hardness of the bearing material, the surface roughness from the turning process is not completely eliminated by the deep rolling process. Both processes influence each other and must be coordinated. In the deep rolling process, the roughness peaks are plastically deformed. This reduces the maximum profile height of the roughness, which in turn is advantageous for surfaces subject to tribological load. For the process, rolling pressure, ball diameter, and rolling feed are taken into account. The main process control variable is the degree of coverage, i.e., partial rolling over the same material area several times.
Additionally, a combination of the turning and deep rolling processes was developed, as shown by Denkena et al. (2016b) and Maiß et al. (2016). In this case, a deep rolling tool is combined with a cutting insert in one tool, merging the aforementioned sequential steps in one to increase efficiency (Maiß et al., 2016). The process was compared to hard turning and subsequent deep rolling by Denkena et al. illustrating the feasibility of the approach (Denkena et al., 2016b). The tool additionally allows a more precisely alignment of the deep rolling ball on the surface toward the cutting insert. The so called turn-rolling concept for machining of the inner rings is shown in Figure 2. The ball diameters (dk = 3.175 or 6.35 mm) and the insert corner radius (rβ = 1.6 mm) have been adjusted to achieve the positioning of the deep rolling ball in or on the turning grooves in the feed direction. The pressure on the rolling ball (rolling pressure pw) is supplied by oil. The rolling tool allows the induction of subsurface residual stresses. In combination with the heat generated by the cutting insert, the depth of the residual stresses can be increased.
To study the influence of the production processes on fatigue life, bearing inner rings of type NU206 were manufactured with the aforementioned turn-rolling process. These were mounted in a test rig for rolling bearings in four-bearing configuration and operated until failure, see Figure 3. The load is applied via disk springs, which act on a hollow shaft onto the both inner bearings. The symmetrical arranged outer bearings transfer the load toward the housing. The applied load is measured with a load cell during the tests. The radial load was chosen with C/P = 4, which is equivalent to a Hertzian pressure of pm = 2,500 MPa. The bearings are directly supplied with oil. The oil is tempered by a process thermostat to achieve permanently constant lubrication conditions. The tests were carried out under fully flooded lubrication conditions at 60°C. Synthetic oil of the viscosity ν40 = 68 mm2/s was used. The bearing ran with a rotational speed of n = 4,050 min−1. The lubrication parameter is calculated as λ = 3. Piezoelectric vibration transducers measure the vibrations and structure-borne sound in the load direction. By means of a self-developed condition monitoring system, an envelope curve analysis is carried out during the runtime of the experiment. If a fatigue damage in the rolling bearing develops to the point of surface chipping, the evaluation of the shock pulse repetition frequencies in the envelope curve spectrum allows conclusions to be drawn about bearing damage that has occurred. The test is aborted by a previously defined switch-off criterion of exceeding the steady state signal by 150%.
The bearings were investigated regarding the subsurface residual stress state. Doing so, X-ray diffraction measurements were performed at the Institute of Production Engineering and Machine Tools, Leibniz University Hannover, Germany. A two circle Bragg-Brentano-Diffractometer System (Type GE XRD 3003TT and Seifert XRD 3000P) with CrKa radiation was used for the measurement. For the depth profiling, the material on the surfaces was removed by electrolytical polishing.
Part of the current investigation is focused on how favorable boundary zone properties can be adjusted with respect to the residual stress state. For this purpose, the methods hard-turning, hard-turning with subsequent deep rolling, and turn-rolling were in the scope. To quantify changes of the boundary zone properties as a function of the test duration, the bearings were investigated in terms of XRD after defined running times.
In order to form a reference, standard bearings of the type NU206 C3 with increased internal clearance were examined. The raceways of the bearings were honed in the final machining process; the inner rings have a crowned profile. The maximum pressure in crowned roller contact between inner ring and rolling element is pm = 2,500 MPa. In new condition, residual compressive stresses of about σcircumference = −500 MPa are present on the surface, which are almost eliminated at a depth of about z = 20 μm as shown in Figure 4A. Within the first 3.9 million revolutions, the rolling bearings investigated show significant changes in the surface and subsurface properties during operation, the roughness peaks on the surfaces were plastically deformed and residual stresses were built up in the depth. Figure 4 also depicts the development of the residual stress state over the bearing test duration. The residual stresses have developed at the depth of the maximum shear stresses and then remain constant at this level after 106 to 108 revolutions (Pape et al., 2017).
Figure 4. Comparison of residual stress depth profiles at different running times depending on the respective production strategy for NU206 inner rings and a bearing load of C/P = 4. (A) Reference from conventional large series production, (B) Hard turning, (C) Hard turning with subsequent deep rolling, (D) Combined turn-rolling.
For the hard-turned bearings, the process had to be advanced to achieve bearings of a sufficient low surface roughness to allow for the bearing tests (Neubauer et al., 2013). It was shown that a low surface roughness is required in order to avoid surface-induced early bearing failures. With bearings manufactured with a sufficiently low roughness, results comparable to standard bearings could be achieved. It could be shown that in the running-in period the roughness has been reduced and residual stresses have increased. The changes of the residual stress over test duration are shown in Figure 4B. Due to hard turning process, the surfaces of the bearing inner rings do not have a crowned surface, so that a lower maximum Hertzian pressure of pmax = 2,300 MPa is present. As a result, slightly lower residual stresses were induced in the bearings (Denkena et al., 2016b; Pape et al., 2017).
In comparison, hard-turned and subsequent deep rolled bearing rings were examined; the residual stress depth curves after production and after varied running times were compared (Figure 4C). The manufacturing process induced a higher residual stress state than a running in phase would have. For the first 29 million revolutions, the residual stresses up to a depth of z = 120 μm are comparable to those directly after deep rolling. At greater depths, there is a slight increase in residual stresses. After 378 million revolutions, a reduction of the residual stresses can be observed in the near subsurface area (Denkena et al., 2016b; Pape et al., 2017).
The development of the residual stresses for the turn-rolled bearings are presented in Figure 4D. After manufacturing the residual stress state is shifted to a higher depth and, compared to the deep rolled bearings, the magnitude of the residual stresses could be increased. It can be seen that, within the first 18 million and 125 million revolutions, the residual stresses remain stable. After 328 million revolutions, a reduction of the residual stresses can be observed in the near-surface area.
The bearings underwent endurance tests. For the evaluation the slightly different contact pressure due to the hard-turning process has to be regarded. A bearing fatigue life of L10 = 274 h and a Weibull slope of 0.6 could be determined for the standard bearings. In this case the bearing inner rings feature a crowned profile and thus higher Hertzian pressure in the contact between inner ring and rollers. In case of the hard-turned bearings a lifetime of L10 = 771 h was determined. The hard-turned and subsequently deep rolled bearings exhibit a bearing fatigue life L10 = 1,924 h. Due to the deep rolling process, the service life could be increased by a factor of 2.5 (Neubauer, 2016). This increase can be explained by the induced residual stresses, which reach their maximum approximately at the depth of the highest load induced stresses. The turn-rolled bearing feature a L10 = 471 h which is even below the fatigue life of the hard-turned bearings. Although in a first view, the pre-induced residual stress state should allow an increased bearing fatigue life, so the process was not beneficial. The Weibull distribution at a load of C/P = 4 are shown for the hard-turned, deep rolled, and turn-rolled bearings in Figure 5.
Figure 5. Weibull plot for inner ring failure of CRB NU206 in dependence of the manufacturing strategy.
The results of the bearing fatigue tests show that the bearings can be significantly influenced by changes of the production step properties. The test results of the hard-turned bearings prove that this alternative machining process to the standard honing process allows the achievement of comparable fatigue lives. However, it should be noted that the hard-turned bearing rings have a different bearing clearance and profile than the reference bearings. A direct comparison can be done to the deep-rolled bearings as well as the turn-rolled bearings due to the comparable turning process with the same bearing clearance and the same profile. The steel rods of the hard-turned, deep-rolled, and turn-rolled bearings, in contrast to the reference bearing rings, come from the same material batch.
To obtain influences on the fatigue of the surface of the bearings, the development of the direction of the residual stresses before and after testing was inspected as shown in Figure 6. In case of the hard-turned bearing after production, only the first 10 μm experience a measurable residual stress condition. Due to RCF loading, after 18 million revolutions a residual stress state is induced to the material. For the first 25 μm, the circumferential and axial residual stress state differs, for higher depths both values deviate slightly. In comparison, the stress state for a deep rolled bearing in circumferential and axial direction remained equal even after 290 million revolutions. Even for very long running times (595 million revolutions) the circumferential and axial residual stress state remained equal.
Figure 6. Measured residual stresses in circumferential and axial directions for various manufacturing strategies after different phases, (A) hard turned bearing in new state, (B) hard turned bearing after test, (C) deep rolled bearing in new state, (D) deep rolled bearing after test, (E) turn rolled bearing in new state, (F) turn-rolled bearing after test.
For the turn-rolled bearing, the circumferential and the axial residual stress states before test are nearly equal. For a bearing inner ring removed at an early stage of 18 million revolutions, the circumferential and axial residual stress states differ significantly. Also the induced residual stress state in axial direction is increased up to magnitudes of more than −1,200 MPa. The distribution and difference between circumferential and axial residual stresses could also be proven for longer bearing running times. It could be shown that the material of the turn-rolled bearing inner ring exhibits anisotropic behavior regarding the orientation of the residual stress state. It is assumed that the heat influence causes an alignment of the surface structure which compensates the positive effect of the rotary rolling process. Additional a cross section for the turn rolled bearing was investigated (Figure 7). The cross section of a turn rolled bearing inner ring before test shows martensitic texture (Figure 7A). After test (125 million revolutions) the textures features darker spots due to carbon redistribution (Figure 7B).
To consider the influence of residual stresses on the fatigue life of bearings, a finite element model of a bearing inner ring segment was prepared and combined with a calculation routine. The external bearing load is added to the bearing ring as three-dimensional Hertzian pressure. The profile of the bearing inner ring is measured and taken into account in the modeling. It allows the three-dimensional stress state under the raceway surface to be determined. In doing so, the external loads are superimposed with an additional residual stress state. The procedure is described by Neubauer (2016). The determines the von Mises equivalent stresses, the orthogonal shear stresses, and the hydrostatic stresses as a result. The resulting stresses are used as input to the lifetime model based on Ioannides and Harris (1985). This approach regards a stress fatigue limit as well as a fatigue stress criterion. The probability of survival S can be obtained by the following equation (Ioannides et al., 1999):
The concept considers the magnitude and depth of the load induced stresses as well as the stressed volume V. In the formula S is the probability of survival: N stands for the number of load cycles, and z' is the stress-weighted depth from the surface. The exponents e, c, and h can be obtained from the literature (Ioannides et al., 1999): e = 9/8 (for line contact), c = 1/3 (exponents of Lundberg and Palmgren Lundberg and Palmgren, 1947 and h = 7/3. Tu represents the stress fatigue limit of the raceway material. For the stress related fatigue criterion, Ti, the Dang Van criterion Dang Van et al., 1989 is inserted: .This can be computed with the max. shear stress τOmax, khyd as a weighting factor for the hydrostatic stress , which includes compressive stresses. This model was evaluated with tests and allows the calculation of the bearing fatigue life with consideration of the residual stresses (Denkena et al., 2016b; Pape et al., 2018). The calculated bearing fatigue life L10, mod are nearly equal for the deep-rolled and turn-rolled bearing rings or the same rolling tool (dk = 6.35 mm). In both cases similar residual stress states are induced below the surface of the bearing inner ring. As in the Dang Van criterion, the orthogonal shear stresses are corrected by the residual stress state and, in both cases, an increase in the bearing fatigue life can be expected. The calculation does not regard any material anisotropy of the subsurface zone due to the turn-rolling process. Due to the modified process of turn-rolling involving a subsurface heat profile, it can be expected that the subsurface features anisotropic material behavior which should be regarded in future investigations.
Pre inducing a subsurface residual stress state in rolling bearings allows achieving an increased bearing fatigue life. This could be shown by experimental validation and in terms of a calculation approach based on Ioannides and Harris regarding the Dang Van fatigue criterion. By hard-turning and subsequent deep rolling a beneficial residual stress state in the depth of the highest load induced stresses was achieved. The residual stress state remains constant for very long bearing running times and the bearing fatigue life could be extended.
Despite this, a combined tool with the combination of hard-turning and deep rolling resulted in disadvantageous subsurface structure and slightly reduced bearing fatigue life compared to hard-turned bearings. It can be concluded that, due to the anisotropic heating during turn-rolling, the surface fine structure features anisotropic material behavior, resulting in an increased modification of the residual stresses. On the one hand, the residual stress state with a value higher than −1,200 MPa results in surface degradation. On the other hand, the differences in the residual stress direction can result in undesirable stress superposition in case of cyclic over rolling. There is demand to investigate this modification by ongoing studies and investigations on grain size.
All datasets generated for this study are included in the article/supplementary material.
FP and TC performed tests and researched on the influences of ESP on RCF and on the topic Tailored Forming. The contribution was written by FP and TC under supervision of GP. All authors contributed to the article and approved the submitted version.
Funding by the DFG (German research Foundation) within the research program Resource efficient Machine Elements (SPP1551) and the SFB 1153 Tailored Forming—Grant No. 252662854.
The authors declare that the research was conducted in the absence of any commercial or financial relationships that could be construed as a potential conflict of interest.
The authors thank the DFG (German Research Foundation) for supporting this project in the context of the research program the SFB Tailored Forming in the subproject C3. The authors would also like to thank apl. Prof. Breidenstein's team for carrying out the residual stress measurements using XRD.
Altenberger, I. (2005). “Deep rolling—the past, the present and the future,” in 9th International Conference on Shot Peening (ICSP9) (Paris), 144–155.
Behrens, B.-A., Chugreev, A., Matthias, T., Poll, G., Pape, F., Coors, T., et al. (2019). Manufacturing and evaluation of multi-material axial-bearing washers by tailored forming. Metals 9:232. doi: 10.3390/met9020232
Böhmer, H. J. (1998). Wälzverschleiß und –ermüdung von Bauteilen und Maßnahmen zu ihrer Einschränkung. Materialwiss. Werkstofftech. 29, 697–713. doi: 10.1002/mawe.19980291203
Coors, T., Pape, F., and Poll, G. (2018). Bearing fatigue life of a multi-material shaft with an integrated raceway. Bear. World J. 3, 23–30.
Dang Van, K., Griveau, B., and Message, O. (1989). On a New Multiaxial Fatigue Criterion: Theory and Application. London: Mechanical Engineering Publications, 479–496.
Denkena, B., Bergmann, B., Breidenstein, B., Prasanthan, V., and Witt, M. (2019). Analysis of potentials to improve the machining of hybrid workpieces. Prod. Eng. 13, 11–19. doi: 10.1007/s11740-018-00870-3
Denkena, B., Grove, T., and Maiß, O. (2016a). Influence of hard turned roller bearings surface on surface integrity after deep rolling. Proc. CIRP 45, 359–362. doi: 10.1016/j.procir.2016.02.047
Denkena, B., Poll, G., Maiß, O., Pape, F., and Neubauer, T. (2016b). Enhanced boundary zone rolling contact fatigue strength hrough hybrid machining by hard turn-rolling. Bear. World J. 1, 87–102.
Glaeser, W. A., and Shaffer, S. J. (1996). “Contact fatigue,” in ASM Handbook, Vol. 19 (Materials Park, OH: ASM Handbook Committee), 331–336.
Golovin, P. A., Mildebrath, M., and Zemlyakov, E. V. (2019). Effects of PTA deposition parameters on coating quality of 41Cr4, 50CrV4 and 100Cr6 steel. Key Eng. Mater. 822, 801–808. doi: 10.4028/www.scientific.net/KEM.822.801
Hills, D. A. (1983). Some aspects of post-yield contact problems. Wear 85, 107–119. doi: 10.1016/0043-1648(83)90339-3
Hollox, G. E., Voskamp, A. P., and Ioannides, E. (1987). Ermüdungssichere Auslegung von Wälzlagerkomponenten. Kugellagerzeitschrift 62, 20–27.
Ioannides, E., Bergling, G., and Gabelli, A. (1999). “An analytical formulation for the life of rolling bearings,” in Acta Polytechnica Scandinavica. Mechanical engineering series (Espoo; Stockholm: Finnish Acad. of Technology).
Ioannides, E., and Harris, T. A. (1985). A new fatigue life model for rolling bearings. ASME J. Tribol. 107, 367–337. doi: 10.1115/1.3261081
Kruse, J., Mildebrath, M., Behrens, B.-A., Stonis, M., and Hassel, T. (2019). Cross-wedge rolling of PTA-welded hybrid steel billets with rolling bearing steel and hard material coatings. AIP Conf. Proc. 2113:040019. doi: 10.1063/1.5112553
Lundberg, G., and Palmgren, A. (1947). “Dynamic capacity of roller bearings,” in Acta Polytechnica, Mechanical Engineering Series, Vol. 1, No. 3, Royal Swedish Academy of Engineering Sciences (Stockholm).
Maiß, O., Denkena, B., and Grove, T. (2016). Hybrid machining of roller bearing inner rings by hard turning and deep rolling. J. Mater. Process. Technol. 230, 211–216. doi: 10.1016/j.jmatprotec.2015.11.029
Maiß, O., Grove, T., and Denkena, B. (2017). Influence of asymmetric cutting edge roundings on surface topography. Prod. Eng. Res. Dev. 11, 383–388. doi: 10.1007/s11740-017-0742-7
Majzoobi, G. H., Azadikhah, K., and Nemati, J. (2009). The effects of deep rolling and shot peening on fretting fatigue resistance of aluminum-7075-T6. Mater. Sci. Eng. A 516, 235–247. doi: 10.1016/j.msea.2009.03.020
Montros, C. S., Wei, T., Ye, L., Clark, G., and Mai, Y.-W. (2002). Laser shock processing and its effects on microstructure and properties of metal alloys: a review. Int. J. Fatigue 24, 1021–1036. doi: 10.1016/S0142-1123(02)00022-1
Nalla, R. K., Altenberger, I., Noster, U., Liu, G. Y., Scholtes, B., and Ritchie, R. O. (2003). On the influence of mechanical surface treatments—deep rolling and laser shock peening—on the fatigue behavior of Ti−6Al−4V at ambient and elevated temperatures. Mater. Sci. Eng. A 355, 216–230. doi: 10.1016/S0921-5093(03)00069-8
Neubauer, T. (2016). Betriebs- und Lebensdauerverhalten hartgedrehter und festgewalzter Zylinderrollenlager (dissertation). Leibniz Universität Hannover, Hannover, Germany.
Neubauer, T., Poll, G., Denkena, B., and Maiß, O. (2013). “Fatigue life extension of rolling element bearings by residual stresses induced through surface machining,” in 5th World Tribology Congress (Turin).
Pabst, A. (2018). Steigerung der Ermüdungslebensdauer vonWälzlagern durch gezielt eingebrachte Druckeigenspannungen (dissertation). Friedrich-Alexander- Universität Erlangen-Nürnberg, Erlangen, Germany.
Pape, F., Maiß, O., Denkena, B., and Poll, G. (2018). Computational approach to improve bearings by residual stresses based on their required bearing fatigue, life. Int. J. Comput. Methods Exp. Meas. 6, 656–666. doi: 10.2495/CMEM-V6-N4-656-666
Pape, F., Neubauer, T., Maiß, O., Denkena, B., and Poll, G. (2017). Influence of residual stresses introduced by manufacturing processes on bearing endurance time. Tribol. Lett. 65:70. doi: 10.1007/s11249-017-0855-3
Poll, G., and Hacke, B. (2010). “Berücksichtigung von Betriebszuständen, Sonderereignissen und Überlasten bei der Berechnung der Wälzlager-Lebensdauer in Windenergieanlagen und Großgetrieben,” in Informationstagung 2010 der Forschungsvereinigung Antriebstechnik. Würzburg: FVA Forschungsreport.
Voskamp, A. (1996). Microstructural changes during rolling contact fatigue—metal fatigue in the subsurface region of deep groove ball bearing inner rings (dissertation). Technical University Delft, Delft, Netherlands.
Keywords: cylindrical roller bearing, fatigue life, residual stresses, deep rolling, turn-rolling
Citation: Pape F, Coors T and Poll G (2020) Studies on the Influence of Residual Stresses on the Fatigue Life of Rolling Bearings in Dependence on the Production Processes. Front. Mech. Eng. 6:56. doi: 10.3389/fmech.2020.00056
Received: 16 March 2020; Accepted: 16 June 2020;
Published: 29 July 2020.
Edited by:
Valentin L. Popov, Technical University of Berlin, GermanyReviewed by:
Jose Daniel Biasoli De Mello, Federal University of Uberlandia, BrazilCopyright © 2020 Pape, Coors and Poll. This is an open-access article distributed under the terms of the Creative Commons Attribution License (CC BY). The use, distribution or reproduction in other forums is permitted, provided the original author(s) and the copyright owner(s) are credited and that the original publication in this journal is cited, in accordance with accepted academic practice. No use, distribution or reproduction is permitted which does not comply with these terms.
*Correspondence: Florian Pape, cGFwZUBpbWt0LnVuaS1oYW5ub3Zlci5kZQ==
Disclaimer: All claims expressed in this article are solely those of the authors and do not necessarily represent those of their affiliated organizations, or those of the publisher, the editors and the reviewers. Any product that may be evaluated in this article or claim that may be made by its manufacturer is not guaranteed or endorsed by the publisher.
Research integrity at Frontiers
Learn more about the work of our research integrity team to safeguard the quality of each article we publish.