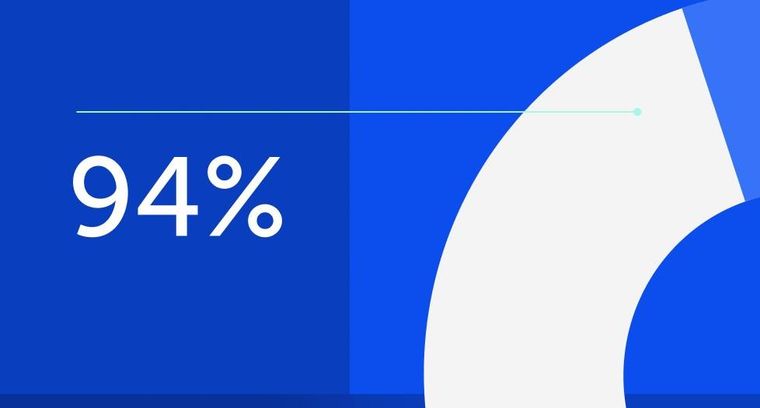
94% of researchers rate our articles as excellent or good
Learn more about the work of our research integrity team to safeguard the quality of each article we publish.
Find out more
ORIGINAL RESEARCH article
Front. Mater., 26 March 2025
Sec. Polymeric and Composite Materials
Volume 12 - 2025 | https://doi.org/10.3389/fmats.2025.1581900
This article is part of the Research TopicAdvanced Electronic Packaging Materials: Constitutive Model, Simulation, Design and ReliabilityView all 6 articles
In this paper, micro-sized Zn particles were added into Sn-58Bi solder flux to form Sn-58Bi-xZn composite solder. The evolution of microstructure, interfacial IMCs and shearing properties during long-term aging were investigated. The wettability of Sn-58Bi-xZn solder decreased with the increase in Zn content. Adding the Zn element refined the microstructure of Sn-58Bi solder and mitigated the aggregation of Bi phases during aging. The interfacial IMCs changed from Cu6Sn5 to Cu6(Sn,Zn)5 with 0.5 wt% Zn addition. Further increasing the Zn content, Cu5Zn8 instead of Cu6(Sn,Zn)5 generated at the Sn-58Bi-2.0Zn/Cu interface. After long-term aging, Bi diffused into Cu3Sn and formed an aggregation layer. With 0.5 wt% Zn addition the growth of interfacial Cu6Sn5 IMCs was suppressed. Shearing tests were conducted to evaluate the mechanical properties of Sn-58Bi-xZn joints before and after aging. Aging and excess Zn addition lead to a decrease in the shearing force of the joints. The fracture mode changed from solder fracture to interface fracture with excess Zn addition The Sn-58Bi-0.5Zn solder joints exhibited the optimal shearing properties during aging. The optimum amount of Zn addition to Sn-58Bi solder was 0.5 wt%.
Tin-lead solders have been widely used in the electronic packaging industry for decades. Due to the toxicity of lead and the increasing environmental concern, lead-containing solder has been banned since the ROSH Directive was enacted in 2006 (Zhang and Tu, 2014). Currently, several Pb-free solders such as Sn-Ag, Sn-Cu, Sn-Ag-Cu, Sn-Bi and Sn-Zn solder alloys have been extensively developed to replace the traditional Sn-Pb eutectic solder. Nevertheless, some application and reliability issues still need to be overcome (Abtew and Selvaduray, 2000). For example, the melting temperature of Sn-Ag, Sn-Cu and Sn-Ag-Cu solder alloys are too high to be compatible with printed circuit board (PCB) substrates during the soldering process. Moreover, the excessive growth of Cu6Sn5 and Ag3Sn intermetallic compounds (IMCs) in service will gradually reduce the reliability of solder joints (Berger et al., 2023; Mu et al., 2012; Zhang et al., 2024). The easy oxidation and poor wettability characteristics of Sn-Zn solder alloy hindered its application in the electronic industry (Liu et al., 2015; Xue et al., 2016).
Sn-Bi solder with its good solderability as the eutectic Sn-Pb solder, superior ultimate tensile strength and yield strength has drawn attention as an attractive candidate solder. However, the poor ductility and low reliability of Sn-Bi solder joints need to be improved (Zhang et al., 2022; Li et al., 2020). In recent years, reinforcement of solder alloys with micro or nanoparticles has been adopted to improve the performance of Sn-Bi alloy and is currently receiving great attention. The addition of micro Ni-particles significantly refined the microstructure of Sn-58Bi solder. Ni-Sn intermetallics obstructed the movement of Bi atom diffusion and improved the electromigration resistance of the Sn-58Bi composite solder joints (Xu et al., 2011). Li and Chan, (2015) have studied the mechanical properties and the growth of IMCs at the solder/Cu interface of Sn-58Bi solder with Ag nanoparticles addition. The results showed that the microhardness was increased by 12.2% and the shear strength was enhanced by 18.9% for the as-prepared solder. The dispersion strengthening theory was employed to elaborate the mechanical improvement mechanism. Some nanoparticles of non-metallic such as TiO2 (Tsao et al., 2012), CNT (Shen et al., 2013; Sun et al., 2016; Sun et al., 2022), POSS (Zhang et al., 2010; Rashid et al., 2009), graphene (Yang et al., 2013; Ma et al., 2017; Peng and Deng, 2015), Al2O3 (Hu et al., 2015) have been added into Sn-Bi alloy. These particles can accelerate β-Sn heterogeneous nucleation during reflow and reduce the size of β-Sn significantly. The growth of interfacial IMCs was depressed with nano non-metallic particle addition. However, these particles could not have metallurgical bonding with Sn solder. The excessive non-metallic particles will reduce the wettability due to the poor fluidity of composite solder (Yang et al., 2009).
Presently, most of the research is focused on the microstructure and mechanical properties of nanoparticle composite solder alloy itself, and few of them have studied the reliability of the micro joints using nanoparticle composite solder. Accordingly, this study aims to investigate the microstructure and mechanical properties of Sn-58Bi solder bearing micro-sized Zn-particles and prepare the ball grid array (BGA) solder joints using this composite solder alloy. The shearing test was conducted to evaluate the reliability of the solder joints. The effect of micro-sized Zn particles addition and solid-state aging on the reliability of Sn-58Bi micro-sized Zn particles composite solder joints was investigated.
Commercial Sn-58Bi solder paste with 11.5 wt% flux was used as the base material. The Sn-58Bi-xZn micro particles composite solder paste was prepared by mechanically dispersing the micro-sized Zn-particles into the Sn-58Bi solder paste. The spherical pure Zn particles with about 2.0 μm diameter were shown in Figure 1, and the content of Zn particles was set as 0, 0.5, 1.0, 1.5 and 2.0 wt% respectively. The mixed solder paste was stirred primarily under vacuum condition for at least 1 h to ensure the uniform distribution of Zn particles. Then, the composite solder paste was printed by a stainless steel stencil with a 1.2 mm diameter and 1 mm thickness. The printed circuit board (PCB) with a 0.8 mm diameter Cu pad was used as the substrate. Before soldering, Cu pads were cleaned by a 4.0 wt% HCl solution. The composite solder joints were heated on a heating platform at 180 °C for 40 s. After soldering, the joints were air-cooled and cleaned with alcohol as shown in Figure 2. The diameters of solder balls were about 1.0 mm.
The as-soldered joints were solid-state aged by oil bath at 120°C for 10, 20, 30, 40 and 50 days. The average thickness of interfacial IMCs was calculated by measuring the total area of the IMCs and dividing it by the total length of the images. The mechanical properties of Zn-particles composite solder joints were evaluated by a shearing tester. The shearing force was calculated as an average of 20 solder joints with a shearing speed of 0.01 mm/s.
The wettability of composite solder paste was evaluated according to the standard of JIS-Z3198-3. A certain quality of composite solder paste was printed on a polished Cu substrate as well as a stainless steel substrate by the stencil printing method. Then, the samples were heated at 180°C for 60 s. The height of solder balls wetted on stainless steel substrate and Cu substrate was measured by screw micrometer. The wettability of composite solder paste was evaluated by the spreading rate S, which can be expressed as Equation 1:
Where S is the spreading rate of composite solder paste, D is the height of composite solder paste wetted on a stainless steel substrate, and H is the height of composite solder paste wetted on a Cu substrate.
To characterize the microstructure, the solder joints were mounted in resin and ground using different grit sizes of emery papers. Finally, the samples were polished with 3.0, 0.5 μm diamond powder and 0.05 μm silica suspension. The specimens were etched with a solution of 4 vol% HNO3 + 96 vol% C2H5OH. The microstructure of composite solder matrix, interfacial IMCs and fracture surfaces after the shearing test was observed using a scanning electron microscope (SEM) equipped with an energy dispersive X-ray spectrometer (EDS).
The wettability is the primary condition for the usability of lead-free solder. Figure 3 presents the spreading rate of the Sn-58Bi-xZn composite solder paste on Cu substrates. The Sn-58Bi solder paste showed satisfactory wettability and the spreading rate was 81.9%. The spreading rate of the composite solder paste decreased slightly when 0.5 wt% Zn particles were added into the Sn-58Bi solder paste. Moreover, the spreading rate decreased seriously with more Zn particles addition. Residual Zn particles can be observed around the solder caps after soldering. It is worth noting that the molten solder and the Cu are assumed to be fully covered by flux. The wettability of solder on Cu is reactive wettability. The wettability was affected by the formation of interfacial IMCs. Different from Sn-Bi-Zn ternary alloy, the Sn-58Bi solder flux needs time to absorb the Zn particles. Due to the high cooling rate, excess Zn particles were not yet absorbed by the molten Sn-58Bi solder and existed at the edge of the solder cap. The aggregation of Zn particles hindered the spreading of molten solder on Cu. Therefore, the wettability deteriorated with the increase of Zn particles content.
Figure 4 shows the microstructure evolution of the as-soldered and aged composite solder bumps. The as-soldered Sn-58Bi solder bump shows a lamellar structure which mainly consists of Sn-rich phase and Bi-rich phase as shown in Figure 4a. With the addition of 0.5 wt% Zn particles, the microstructure of the composite Sn-58Bi-0.5Zn bump became finer with smaller Sn-rich phase and Bi-rich phase by comparing with the Sn-58Bi bump, as shown in Figure 4c. Fine Zn particles can be observed in the composite solder bump matrix.
Figure 4. Optical microstructure of the solder bumps aged for 0 days and 40 days. (a, b) Sn-58Bi, (c, d) Sn-58Bi-0.5Zn, (e, f) Sn-58Bi-2.0Zn.
Figure 5 shows the distribution of the Zn element in the as-soldered Sn-58Bi-0.5Zn composite solder bump. It can be found that Zn particles were uniformly distributed in the Sn-rich phase. According to previous studies (Ma and Wu, 2016; Shen et al., 2014), no binary or ternary compounds will form in the Sn-Bi-Zn ternary system. The existence of Zn particles played the role of refining the composite alloy by heterogeneous nucleation. The microstructure of the Sn-58Bi bump was not further refined with more Zn particles addition, as shown in Figure 4e. When the Zn content increased to 2.0 wt%, needle-like Zn phases can be found in the bump. It is reported that the ultimate tensile strength of Sn-Bi alloy was improved by the existence of needle-like Zn phases. However, the elongation of Sn-Bi-Zn alloy deteriorated seriously due to the high aspect ratio Zn phases (Shen et al., 2014). The tensile strength and shearing strength of Sn-58Bi alloy is much higher than that of Sn-37 Pb alloy (Abtew and Selvaduray, 2000). It is the poor ductility of the Sn-58Bi alloy that limits its utilization. Many efforts have been made on this problem, but it has not been solved until now (Zhang et al., 2022; Li et al., 2020; Xu et al., 2011).
Figure 5. Element mapping of the as-soldered Sn-58Bi-0.5Zn solder alloy. (a) Microstructure of the alloy (b) Sn element (c) Bi element and (d) Zn element.
The microstructure of the Sn-58Bi bump became coarse after aging for 40 days, as shown in Figure 4b. The bulk Bi phases were separately distributed in the Sn matrix. Some Bi phases with small size were observed as illustrated by the red circles in Figure 4b. The Bi phase in the bumps with Zn addition slightly grew after aging, as shown in Figures 4d, f. The microstructure of the Sn-Bi-Zn bumps kept a lamellar structure after aging for 40 days. The addition of Zn mitigated the aggregation and growth of Bi phases. The solute atoms migration is significant during thermal aging in the binary system, such as Sn-Pb, Sn-Bi and Sn-Cu, etc (Philippe and Voorhees, 2013). Based on the Ostwald ripening, the smaller second phases will dissolve and the larger ones will grow due to the diffusion of the solute atoms. The radius of the second phase can be expressed as Equation 2 (Kim and Voorhees, 2018; Lifshitz and Slyozov, 1961),
where r is the radius of the second phase, r0 is the initial radius of the second phase at the initial stage, K0 is the coarsening rate, t is the aging time, D is the diffusivity of solute atoms in the matrix, γ is the interface energy, Ce is the equilibrium concentration of solute atoms around the large second phase, Ω is the molar volume, R is the gas constant, T is the aging temperature.
According to the Sn-Zn binary alloy phase diagram, the solubility of Zn in Sn is approximately 0.7 at% at eutectic temperature (Wu et al., 2024). Due to the small volume and high undercooling of Sn-58Bi-xZn solder balls, zinc was not precipitated from Sn during the cooling process, resulting in the formation of supersaturated solid solutions. The solid solution atoms will hinder the intragranular diffusion of Bi in Sn leading to the decrease of diffusivity of solute atoms (Delhaise et al., 2019). Therefore, the radius of the Bi phase in the Sn matrix with Zn addition decreased after thermal aging.
The microstructure of the as-soldered solder/Cu interfaces is shown in Figure 6. The interfacial IMCs were observed from a cross-sectional view and top-view respectively. An extremely thin and scallop-shaped interfacial IMCs layer formed at the Sn-58Bi/Cu interface as shown in Figure 6a. According to the previous studies (Jeong et al., 2023; Chen et al., 2018; Hao et al., 2024), the composition of the IMCs was Cu6Sn5. The diameter of the IMCs was about 1.5 μm which can be observed from the top-view. Defects can be found in the IMCs as illustrated with the red circle in Figure 6b. The as-soldered Sn-58Bi-0.5Zn/Cu was shown in Figures 6c, d. A flat layer of IMCs can be observed with the addition of 0.5 wt% Zn particles. The thickness of the IMCs layer slightly increased by comparison with the as-soldered Sn-58Bi/Cu interface. The EDS result indicated that some Sn atoms have been replaced with Zn atoms in the Cu6Sn5 IMCs. The composition of the IMCs changed from Cu6Sn5 to Cu6(Sn,Zn)5 with 0.5 wt% Zn addition. The top-view morphology of Cu6(Sn,Zn)5 is shown in Figure 6d. It can be seen that the diameter and morphology of IMCs have not been changed by minor Zn addition. Significant changes in thickness and morphology occurred when the content of Zn increased to 2.0 wt% in the Sn-58Bi solder as shown in Figures 6e, f. The thickness of IMCs at the as-soldered Sn-58Bi-2.0Zn/Cu increased with more Zn addition. It has been reported that adding about 1.7 wt% of Zn to Sn makes the γ-brass (Cu5Zn8) to be the first phase to form at the soldering temperature (Laurila et al., 2010). Another study found that the addition of 1 wt% Zn results in the formation of Cu5Zn8 IMC layer at the Sn-Bi-Zn/Cu interface (Li et al., 2006). Therefore, the composition of the IMCs in Figure 6e can be identified as Cu5Zn8 IMCs. The diameter of the Cu5Zn8 IMCs was lower than 1.0 μm which is much smaller than that of Cu6Sn5 and Cu6(Sn,Zn)5 IMCs. The IMCs particles changed from dense to sparse at the solder/Cu interface and may ultimately affect the mechanical properties of the solder joints as shown in Figure 6f.
Figure 6. Cross-section and top-view microstructure of the initial IMCs at the interface. (a, b) Sn-58Bi/Cu, (c, e) Sn-58Bi-0.5Zn/Cu, (e, f) Sn-58Bi-2.0Zn/Cu.
Figure 7 shows the microstructure and composition of the interfacial IMCs at Sn-58Bi-xZn/Cu interface after aging at 120 °C for 40 days. Compared with the as-soldered IMCs shown in Figure 6, the thickness of the IMCs layer increased and IMCs became flattened after aging. A new interfacial IMCs layer formed at the Cu6Sn5/Cu interface as shown in Figure 7. According to the EDS results, the atomic percentage of Cu and Sn was approximately 3:1, indicating Cu3Sn has formed after aging. Some voids can be found in the Cu3Sn layer as shown in the magnified morphology in Figure 7. In the solid Sn/Cu diffusion couple, the dominant diffusion atoms are Sn and Cu in Cu6Sn5 and Cu3Sn respectively (Yuan et al., 2016). The formation of Cu3Sn can be contributed by two types of reaction. The interfacial Cu6Sn5 reacted with Cu to form Cu3Sn IMCs. Meanwhile, Sn atoms diffused through the interfacial Cu6Sn5 IMCs and reacted with Cu to form Cu3Sn IMCs. Due to the continuous diffusion of Cu in the Cu3Sn, Kirkendall voids formed at the Cu3Sn/Cu interface. Kirkendall voids are defects that will reduce the reliability of solder joints. Therefore, it is essential to inhibit the growth of Cu3Sn IMCs.
Figure 7. Microstructure and composition of the IMCs aged for 40 days. (a) Sn-58Bi/Cu interface, (b) Sn-58Bi-0.5Zn/Cu interface, (c) Sn-58Bi-2.0Zn/Cu interface, (d) element compositions at position P1 and (e) element compositions at position P2.
The microstructure of the aged Sn-58Bi-0.5Zn/Cu interface is shown in Figure 7. The thickness of the IMCs is slightly lower than that of Cu6Sn5 IMCs at the Sn-58Bi/Cu interface. The elemental compositions of the IMCs at position P1 are shown in Figure 7d. The main components of the IMCs are Cu, Sn and contain a certain amount of Zn element. Based on the atomic percentage of element content, the IMCs can be determined as Cu6(Sn,Zn)5 compounds. It is worth noting that no compounds were generated at the Cu6(Sn,Zn)5/Cu interface. This indicates that the addition of 0.5 wt% Zn in the Sn-58Bi solder delayed the growth of Cu6Sn5 IMCs and inhibited the generation of detrimental Cu3Sn IMCs. With the increase of Zn content in the Sn-58Bi solder, a thick and flat IMCs layer formed at the Sn-58Bi-2.0Zn/Cu interface after aging as shown in Figure 7c. The thickness of the IMCs at the Sn-58Bi-2.0Zn/Cu interface was the thickest among the three types of solders. The elemental compositions of the IMCs at position P2 are listed in Figure 7e. The main components of the IMCs are Cu and Zn elements indicating Cu5Zn8 IMCs had formed after aging. By comparing the compositions of IMCs before and after aging, adding different amounts of Zn element did not change the composition of IMCs at the solder/Cu interface.
Further increasing the aging time to 50 days, the microstructure of the Sn-58Bi/Cu interface and the element mapping are shown in Figure 8. According to the distribution of Bi elements, Bi diffused through Cu6Sn5 and distributed in the Cu3Sn layer. The physical properties of Bismuth are quite different from the Cu6Sn5 and Cu. The thermal expansion coefficient (CTE) of Bismuth decreases with the increase in temperature (Chen et al., 2024). However, the CTE of Cu6Sn5 and Cu increases with the increase in temperature. Therefore, the fatigue life of Sn-58Bi solder joints will reduce due to the Bi aggregation layer when bearing temperature cycling. The phenomenon occurred at the location where Cu6Sn5 came into contact with the Bi phase in the Sn-58Bi solder.
Figure 8. Layered Bi aggregation in the IMCs at the interface after aging for 50 days. (a) Microstructure of Bi-rich layer, (b) Sn element, (c) Cu element and (d) Bi element.
After aging for 50 days, the microstructure and elemental mapping of the IMCs at the Sn-58Bi-0.5Zn/Cu interface are shown in Figure 9. The IMCs near the Cu substrate showed a high content of Zn element, indicating Cu6(Sn,Zn)5 was first to generate. With the increase of aging time, the Zn near the solder/Cu interface has been consumed by the growth of IMCs. Therefore, the subsequently grown compounds at the interface were Cu6Sn5 IMCs. The Bi aggregation layer was not found at the interface. Meanwhile, Cu3(Sn,Zn) IMCs were hardly detected at the Cu6(Sn,Zn)5/Cu interface indicating the formation of Cu6(Sn,Zn)5 hindered the diffusion of Sn and Cu. Therefore, adding minor Zn is beneficial for the long-term reliability of Sn-58Bi solder joints.
Figure 9. Element mapping at the Sn-58Bi-0.5Zn/Cu interface aged for 50 days. (a) Microstructure, (b) Sn element, (c) Cu element and (d) Bi element.
The thickness of the interfacial IMCs at the Sn-58Bi-xZn/Cu interface was measured and plotted in Figure 10a. The thickness of the IMCs increased with the aging time. Adding 0.5 wt% and 1.0 wt% Zn into the Sn-58Bi solder decreased the growth rate of IMCs. However, further increasing the Zn content (over 1.0 wt%) will accelerate the growth of IMCs. The growth of IMCs was examined as a function of aging time. The correlation between IMCs thickness and aging time can be expressed by Arrhenius Equation 3:
Figure 10. Calculation of the IMCs thickness at the Sn-58Bi-xZn/Cu interface. (a) Thickness vs aging time, (b) thickness vs aging time in logarithmic form.
Where X is the average thickness of interfacial IMCs after aging, X0 is the initial average thickness of interfacial IMCs. D is the diffusion coefficient at the aging temperature, t is the aging time, n is the time exponent. Accordingly, Equation 3 can be rewritten into Equation 4:
The Previous studies indicated that the value of n was determined by the atomic diffusion mechanism (Zhang and Tu, 2014). When the time exponent n is close to 1, the growth of interfacial IMCs is controlled by interfacial reaction and follows the linear law, when n is close to 0.5, the growth of interfacial IMCs is controlled by volume diffusion and follows the parabolic law, when is close to 0.33, the growth of interfacial IMCs is controlled by grain boundary diffusion and follows the parabolic law.
Figure 10b shows the thickness of interfacial IMCs as a function of aging time in log-log format. The thickness was linearly related to aging time. According to the linear fitting results, the values of n were 0.45, 0.29, 0.35, 0.37 and 0.34, respectively. The values decrease with Zn addition. Moreover, the diffusion coefficient D was calculated in this study, as listed in Table 1. The time exponent n of the IMCs grown at Sn-58Bi/Cu interface is close to 0.5 indicating the growth of IMCs is controlled by volume diffusion. After Zn was added into Sn-58Bi solder, the time exponent n was close to 0.33. It indicated that the growth of the Cu6(Sn,Zn)5 and Cu5Zn8 were controlled by grain boundary diffusion. The addition of Zn into the Sn-58Bi changed the atomic diffusion mechanism at the solder/Cu interface. The diffusion coefficient of the IMCs at the aging temperature of 120°C was calculated by Arrhenius Equation 3. The diffusion coefficient of the IMCs at the Sn-58Bi/Cu interface was calculated to be 5.79 × 10−20 m2/s. The growth rate of the IMCs at the Sn-58Bi/Cu interface is much lower than that at the Sn-0.7Cu/Cu (Tian et al., 2017) and Sn-3.0Ag-0.5Cu/Cu (Tang et al., 2016) interface at 120 °C. The diffusion coefficient of Cu6(Sn,Zn)5 IMCs at the Sn-58Bi-0.5Zn/Cu interface decreased to 3.66 × 10−20 m2/s indicating the addition of Zn inhibited the growth of IMCs. Adding more Zn into the Sn-58Bi solder changed the phase generation in the interfacial IMCs. The diffusion coefficient of Cu5Zn8 was slightly higher than that of Cu-Sn IMCs.
Figure 11 shows the influence of Zn content and aging time on the maximum shearing force of the composite Sn-58Bi-xZn solder joints. The Sn-58Bi joints exhibited a maximum shearing force of approximately 25.2 N before aging. The addition of Zn did not improve the shearing strength of the Sn-58Bi joints. With the increase of the Zn content, the shearing force decreases to 19.5 N when the Zn content is 2.0 wt%. The fracture surfaces of the as-solder Sn-58Bi-xZn solder joints are shown in Figure 12. Residual Sn-58Bi solder can be found on the fracture surface as shown in Figure 12a. Sn-58Bi solder has relatively low plasticity compared with Sn-Pb or other lead-free solders. The brittle fracture morphology is observed as exhibited in Figure 12b. The fracture surface of the Sn-58Bi-0.5Zn joint is shown in Figure 12c. Residual solder was observed on the fracture surface and the Cu pad was not exposed after shearing. The magnified fracture morphology of the Sn-58Bi-0.5Zn joint is shown in Figure 12d. Similar to the Sn-58Bi joint, the fracture mode was also a brittle fracture. It has been reported that the addition of Zn improved the ultimate tensile strength but decreased the ductility (Ma and Wu, 2015). In this study, the addition of 0.5 wt% Zn has a minor influence on the mechanical properties of Sn-58Bi solder joints. The fracture surface of the Sn-58Bi-2.0Zn joint is shown in Figure 12e. The fracture surface was further analyzed by EDS, the Cu elemental mapping indicating that the Cu pad was exposed after the shearing test. The fracture mode of the Sn-58Bi-2.0Zn joint is interface fracture. A plethora of voids can be observed on the surface as shown in Figure 12f. The abovementioned studies in Figure 3 indicate that the spreading rate decreases seriously when the Zn content is over 0.5 wt%. Due to the poor wettability, the soldering defects of voids were generated at the solder/Cu interface. Therefore, the shearing force decreased significantly with the excessive addition of Zn.
Figure 12. Fracture surface of the as-soldered composite solder joints. (a, b) Sn-58Bi, (c, d) Sn-58Bi-0.5Zn, (e, f) Sn-58Bi-2.0Zn.
The shearing force of the solder joints decreased with the increase of aging time, as shown in Figure 11. After aging at 120 °C for 240 h, the shearing force of the Sn-58Bi joint decreased to 21.6 N. The shearing force of the Sn-58Bi joints ultimately stabilized at about 19.5 N after aging for 720 h. The fracture surface of the Sn-58Bi joint aged for 960 h is shown in Figures 13a, b. Interfacial IMCs of Cu6Sn5 and Cu3Sn were exposed on the surface indicating the fracture mode changed from solder fracture to solder/interface mixed fracture. The shearing force of the as-soldered Sn-58Bi-0.5Zn joint decreased from 24.3N to 22.0 N after aging for 240 h. With the increase of aging time, the shearing force of the joints with 0.5 wt% Zn addition was higher than that of Sn-58Bi joints as plotted in Figure 11. The fracture surface of the Sn-58Bi-0.5Zn joint after aging for 960 h is shown in Figures 13c, d. Hardly any IMCs can be detected indicating Cu pad was not exposed on the surface. The fracture mode of the aged Sn-58Bi-0.5Zn joint was solder fracture. The location with high Cu element concentration in Figure 13c is magnified in Figure 13d. Rare amounts of Cu6(Sn,Zn)5 and Cu3(Sn,Zn) IMCs were observed. The Sn-58Bi solder with 0.5 wt% Zn addition exhibited outstanding mechanical properties than that of pure Sn-58Bi solder. With the increase of Zn content from 1.0 wt% to 2.0 wt%, the shearing force was 21.2 N, 20.2 N and 19.4 N, respectively. Further adding Zn in the solder, the initial shearing force of joints was lower than that of Sn-58Bi. The shearing force decreased with the increase of aging time. The shearing strength of the joints with Zn content beyond 1.0 wt% was lower than the pure Sn-58Bi and Sn-58Bi-0.5Zn joints. The fracture surface of Sn-58Bi-2.0Zn aged for 960 h is shown in Figure 13e. From the uniform distribution of Cu element, it is considered that the fracture mode of the joint was interface fracture. The magnified fracture surface is shown in Figure 13f. The sparse distributed Cu5Zn8 IMCs particles can be observed on the surface indicating poor mechanical properties of Sn-58Bi-2.0Zn joints. The above research indicates that 0.5 wt% Zn addition into the Sn-58Bi solder is beneficial to the long-term mechanical properties. Additive more Zn is detrimental to the reliability of Sn-58Bi joints.
Figure 13. Fracture surface of the composite solder joints aged for 960 h (a, b) Sn-58Bi, (c, d) Sn-58Bi-0.5Zn and (e, f) Sn-58Bi-2.0Zn.
In this paper, micro-sized Zn particles were added into Sn-58Bi solder flux to form Sn-58Bi-xZn composite solder. The evolution of microstructure, interfacial IMCs and shearing properties during long-term aging were investigated. The conclusions are drawn as follows:
(1) Minor Zn addition had little effect on the wettability of Sn-58Bi solder. When added with the content of Zn over 0.5 wt%, the wettability significantly decreased.
(2) The addition of 0.5 wt% Zn refined the Sn-rich phase and Bi-rich phase in the Sn-58Bi solder. Neddle-like Zn phase occurred in the matrix of Sn-58Bi-2.0Zn. After aging at 120 °C for 40 days, Bi aggregated and formed bulk Bi phases due to the Ostwald ripening. The addition of Zn mitigated the aggregation and growth of Bi phases.
(3) The composition of the IMCs at the as-soldered Sn-58Bi/Cu interface was Cu6Sn5. With 0.5 wt% Zn addition, Cu6Sn5 changed to Cu6(Sn,Zn)5. Further increasing the Zn content, Cu5Zn8 instead of Cu6(Sn,Zn)5 generated at the Sn-58Bi-2.0Zn/Cu interface.
(4) After long-term aging, Cu3Sn generated at the Cu6Sn5/Cu interface, Bi diffused into Cu3Sn and form Bi aggregation layer. Minor Zn addition suppressed the growth of interfacial IMCs. When the Zn near the solder/Cu interface was consumed, the subsequently grown compounds at the interface were Cu6Sn5 IMCs. The Cu5Zn IMCs at Sn-58Bi-2.0Zn/Cu interface kept a high growth rate during aging.
(5) The Sn-58Bi-0.5Zn solder joints exhibited optimal shearing properties during aging. The cracks propagated along the solder before and after aging. The fracture mode of pure Sn-58Bi joints changed from solder fracture to solder/interface fracture after aging. When the content of Zn increased to 2.0 wt%, voids were found on the fracture surface due to the poor wettability. The fracture of Sn-58Bi-2.0Zn joints was interface fracture. The optimum amount of Zn addition to Sn-58Bi solder was 0.5 wt%.
The original contributions presented in the study are included in the article/supplementary material, further inquiries can be directed to the corresponding author.
XY: Data curation, Investigation, Methodology, Writing–original draft. ST: Funding acquisition, Resources, Supervision, Writing–review and editing. MZ: Conceptualization, Formal Analysis, Validation, Writing–original draft. HJ: Validation, Writing–review and editing. JW: Formal Analysis, Writing–review and editing. BW: Data curation, Writing–review and editing.
The author(s) declare that financial support was received for the research and/or publication of this article. The National Natural Science Foundation of China (62404212). The Basic Research Program of Jiangsu (BK20230191).
The authors would like to acknowledge the National Natural Science Foundation of China (62404212) and the financial support Funded by Basic Research Program of Jiangsu (BK20230191). The authors would like to thank the Reviewers for their suggestions.
Authors XY, ST, HJ, JW, and BW were employed by Wuxi Zhongwei High-tech Electronics Co., Ltd. Authors XY, ST, HJ, JW, and BW were employed by China Key System and Integrated Circuit Co., Ltd.
The remaining author declares that the research was conducted in the absence of any commercial or financial relationships that could be construed as a potential conflict of interest.
The author(s) declare that no Generative AI was used in the creation of this manuscript.
All claims expressed in this article are solely those of the authors and do not necessarily represent those of their affiliated organizations, or those of the publisher, the editors and the reviewers. Any product that may be evaluated in this article, or claim that may be made by its manufacturer, is not guaranteed or endorsed by the publisher.
Abtew, M., and Selvaduray, G. (2000). Lead-free solders in microelectronics. Mat. Sci. Eng. R. 27, 95–141. doi:10.1016/S0927-796X(00)00010-3
Berger, R., Schwerz, R., Rolling, M., and Heuer, H.(2023). Influence analysis of joint attributes on the fatigue progress of SnAgCu solder joints under thermomechanical loading. Microelectron. Reliab. 140, 114870. doi:10.1016/j.microrel.2022.114870
Chen, J., Mu, D., Liao, X., Huang, G., Huang, H., Xu, X., et al. (2018). Interfacial microstructure and mechanical properties of synthetic diamond brazed by Ni-Cr-P filler alloy. Int. J. Refract. Met. Hard Mat. 74, 52–60. doi:10.1016/j.ijrmhm.2018.03.005
Chen, W., Lin, P., Lin, T., and He, P. (2024). Microstructure evolution and properties of dissimilar YIG/MTC joint fabricated with bismuth-based glass ceramic. Ceram. Int. 50 (8), 13146–13154. doi:10.1016/j.ceramint.2024.01.226
Delhaise, A. M., Chen, Z., and Perovic, D. D. (2019). Solid-state diffusion of Bi in Sn: effects of anisotropy, temperature, and high diffusivity pathways. JOM 71, 133–142. doi:10.1007/s11837-018-3145-0
Hao, Q., Tan, X. F., McDonald, S. D., Sweatman, K., Akaiwa, T., and Nogita, K. (2024). Investigating the effects of rapid precipitation of Bi in Sn on the shear strength of BGA Sn-Bi alloys. J. Electron. Mat. 53, 1223–1238. doi:10.1007/s11664-023-10850-8
Hu, T., Li, Y., Chan, Y. C., and Wu, F. (2015). Effect of nano Al2O3 particles doping on electromigration and mechanical properties of Sn–58Bi solder joints. Microelectron. Reliab. 55, 1226–1233. doi:10.1016/j.microrel.2015.05.008
Jeong, M. S., Heo, M. H., Kim, J., and Yoon, J. W. (2023). A comparative study of laser soldering and reflow soldering using Sn–58Bi solder/Cu joints. J. Mat. Sci. Mat. Electron. 34, 1960. doi:10.1007/s10854-023-11419-1
Kim, K., and Voorhees, P. W. (2018). Ostwald ripening of spheroidal particles in multicomponent alloys. Acta Mater 152, 327–337. doi:10.1016/j.actamat.2018.04.041
Laurila, T., Vuorinen, V., and Paulasto-Krockel, M. (2010). Impurity and alloying effects on interfacial reaction layers in Pb-free soldering. Mat. Sci. Eng. R. 68, 1–38. doi:10.1016/j.mser.2009.12.001
Li, J. F., Mannan, S. H., Clode, M. P., Whalley, D. C., and Hutt, D. A. (2006). Interfacial reactions between molten Sn-Bi-X solders and Cu substrates for liquid solder interconnects. Acta Mater 54, 2907–2922. doi:10.1016/j.actamat.2006.02.030
Li, M., Tang, Y., Li, Z., Zhu, M., and Wang, W. (2020). Microstructure and mechanical properties of Sn–58Bi eutectic alloy with Cu/P addition. Mat. Res. Express 7, 116502. doi:10.1088/2053-1591/abc4f8
Li, Y., and Chan, Y. C. (2015). Effect of silver (Ag) nanoparticle size on the microstructure and mechanical properties of Sn58Bi–Ag composite solders. J. Alloys Compd. 645, 566–576. doi:10.1016/j.jallcom.2015.05.023
Lifshitz, I. M., and Slyozov, V. (1961). The kinetics of precipitation from supersaturated solid solutions. J. Phys. Chem. Solids 19, 35–50. doi:10.1016/0022-3697(61)90054-3
Liu, S., Xue, S. B., Xue, P., and Luo, D. x. (2015). Present status of Sn-Zn lead-free solders bearing alloying elements. J. Mat. Sci. Mat. Electron. 26, 4389–4411. doi:10.1007/s10854-014-2659-7
Ma, D., and Wu, P. (2016). Improved microstructure and mechanical properties for Sn58Bi0.7Zn solder joint by addition of graphene nanosheets. J. Alloys Compd. 671, 127–136. doi:10.1016/j.jallcom.2016.02.093
Ma, D. L., and Wu, P. (2015). Effects of Zn addition on mechanical properties of eutectic Sn-58Bi solder during liquid-state aging. Trans. Nonferrous Met. Soc. China 25, 1225–1233. doi:10.1016/S1003-6326(15)63719-0
Ma, Y., Li, X., Zhou, W., Yang, L., and Wu, P. (2017). Reinforcement of graphene nanosheets on the microstructure and properties of Sn58Bi lead-free solder. Mat. Des. 113, 264–272. doi:10.1016/j.matdes.2016.10.034
Mu, D., Yasuda, H., Huang, H., and Nogita, K. (2012). Growth orientation and mechanical properties of Cu6Sn5 and (Cu,Ni)6Sn5 on poly-crystalline Cu. J. Alloys Compd. 536, 38–46. doi:10.1016/j.jallcom.2012.04.110
Peng, Y. T., and Deng, K. (2015). Study on the mechanical properties of the novel Sn-Bi/graphene nanocomposite by finite element simulation. J. Alloys Compd. 625, 44–51. doi:10.1016/j.jallcom.2014.11.110
Philippe, T., and Voorhees, P. W. (2013). Ostwald ripening in multicomponent alloys. Acta Mater 61 (11), 4237–4244. doi:10.1016/j.actamat.2013.03.049
Rashid, E. S. A., Ariffin, K., Kooi, C. C., and Akil, H. M. (2009). Preparation and properties of POSS/epoxy composites for electronic packaging applications. Mat. Des. 30, 1–8. doi:10.1016/j.matdes.2008.04.065
Shen, J., Pu, Y., Yin, H., Luo, D., and Chen, J. (2014). Effects of minor Cu and Zn additions on the thermal, microstructure and tensile properties of Sn–Bi-based solder alloys. J. Alloys Compd. 614, 63–70. doi:10.1016/j.jallcom.2014.06.015
Shen, L., Tan, Z. Y., and Chen, Z. (2013). Nanoindentation study on the creep resistance of SnBi solder alloy with reactive nano-metallic fillers. Mat. Sci. Eng. A 561, 232–238. doi:10.1016/j.msea.2012.10.076
Sun, H. Y., Chan, Y. C., and Wu, F. S. (2016). Effect of CNTs and Ni coated CNTs on the mechanical performance of Sn57.6Bi0.4Ag BGA solder joints. Mat. Sci. Eng. A 656, 249–255. doi:10.1016/j.msea.2016.01.045
Sun, L., Zhang, L., Zhang, Y., Xu, Y. X., Zhang, P. X., Liu, Q. H., et al. (2022). Interfacial reaction and properties of Sn0.3Ag0.7Cu containing nano-TiN solder joints. J. Mat. Sci. Mat. Electron. 33, 3320–3330. doi:10.1007/s10854-021-07532-8
Tang, Y., Luo, S. M., Wang, K. Q., and Li, G. Y. (2016). Effect of Nano-TiO2 particles on growth of interfacial Cu6Sn5 and Cu3Sn layers in Sn-3.0Ag-0.5Cu-xTiO2 solder joints. J. Alloys Compd. 684, 299–309. doi:10.1016/j.jallcom.2016.05.148
Tian, S., Li, S., Zhou, J., Xue, F., Cao, R., and Wang, F. (2017). Effect of indium addition on interfacial IMC growth and bending properties of eutectic Sn-0.7Cu solder joints. J. Mat. Sci. Mat. Electron. 28, 16120–16132. doi:10.1007/s10854-017-7512-3
Tsao, L. C., Huang, C. H., Chung, C. H., and Chen, R. S. (2012). Influence of TiO2 nanoparticles addition on the microstructural and mechanical properties of Sn0.7Cu nano-composite solder. Mat. Sci. Eng. A 545, 194–200. doi:10.1016/j.msea.2012.03.025
Wu, H., Lai, H., Yang, L., Wang, X., and Zhang, Z. (2024). Microstructure, IMCs layer and shear property of Sn-9Zn solder joints reinforced by Cu nanoparticles during thermal cycling. J. Mat. Sci. Mat. Electron. 35, 2233. doi:10.1007/s10854-024-13958-7
Xu, G., Guo, F., Wang, X., Xia, Z., Lei, Y., Shi, Y., et al. (2011). Retarding the electromigration effects to the eutectic SnBi solder joints by micro-sized Ni-particles reinforcement approach. J. Alloys Compd. 509, 878–884. doi:10.1016/j.jallcom.2010.09.123
Xue, P., Wang, K. H., Qi, Z., Huang, J., Long, W. M., and Zhang, Q. K. (2016). Effect of Nd on tin whisker growth in Sn-Zn solder joint. J. Mat. Sci. Mat. Electron. 27, 3742–3747. doi:10.1007/s10854-015-4217-3
Yang, L., Du, C. C., Dai, J., Ning, Z., and Jing, Y. (2013). Effect of nanosized graphite on properties of Sn-Bi solder. J. Mat. Sci. Mat. Electron. 24, 4180–4185. doi:10.1007/s10854-013-1380-2
Yang, L., Jun, D., and Zhang, Y. C. (2009). Influence of BaTiO3 growth and shear strength of lead-free composite solder joints. J. Alloys Compd. 473, 100–106. doi:10.1016/j.jallcom.2008.05.070
Yuan, Y., Guan, Y., Li, D., and Moelans, N. (2016). Investigation of diffusion behavior in Cu-Sn solid state diffusion couples. J. Alloys Compd. 661, 282–293. doi:10.1016/j.jallcom.2015.11.214
Zhang, K., Li, W., Song, P., Zhao, C., and Zhang, K. (2022). Mechanical properties and constitutive model of Sn-58Bi alloy. Mat. Res. Express 9, 016505. doi:10.1088/2053-1591/ac4760
Zhang, L., and Tu, K. N. (2014). Structure and properties of lead-free solders bearing micro and nano particles. Mat. Sci. Eng. R. 82, 1–32. doi:10.1016/j.mser.2014.06.001
Zhang, R. H., Xu, G. C., Wang, X. T., Fu, G., Lee, A., and Subramanian, K. N. (2010). Electromigration in Sn-Bi modified with polyhedral oligomeric silsesquioxane. J. Mat. Sci. 39, 2513–2521. doi:10.1007/s11664-010-1377-z
Keywords: Sn-58Bi, Zn addition, interfacial IMCs, shearing properties, aging
Citation: Yao X, Tian S, Zhou M, Jiao H, Wang J and Wang B (2025) Microstructure, interfacial reaction and shearing property of Sn-58Bi solder joints reinforced by Zn particles during isothermal aging. Front. Mater. 12:1581900. doi: 10.3389/fmats.2025.1581900
Received: 23 February 2025; Accepted: 13 March 2025;
Published: 26 March 2025.
Edited by:
Yutai Su, Northwestern Polytechnical University, ChinaReviewed by:
Qianhao Zang, Jiangsu University of Science and Technology, ChinaCopyright © 2025 Yao, Tian, Zhou, Jiao, Wang and Wang. This is an open-access article distributed under the terms of the Creative Commons Attribution License (CC BY). The use, distribution or reproduction in other forums is permitted, provided the original author(s) and the copyright owner(s) are credited and that the original publication in this journal is cited, in accordance with accepted academic practice. No use, distribution or reproduction is permitted which does not comply with these terms.
*Correspondence: Shuang Tian, bW9sZW5raW5nQDE2My5jb20=
Disclaimer: All claims expressed in this article are solely those of the authors and do not necessarily represent those of their affiliated organizations, or those of the publisher, the editors and the reviewers. Any product that may be evaluated in this article or claim that may be made by its manufacturer is not guaranteed or endorsed by the publisher.
Research integrity at Frontiers
Learn more about the work of our research integrity team to safeguard the quality of each article we publish.