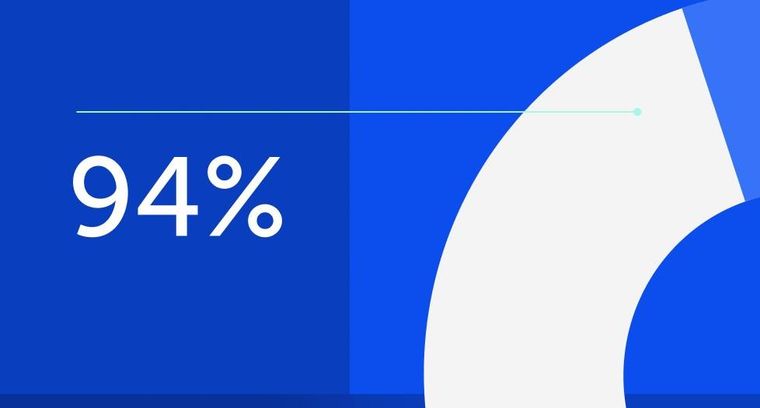
94% of researchers rate our articles as excellent or good
Learn more about the work of our research integrity team to safeguard the quality of each article we publish.
Find out more
ORIGINAL RESEARCH article
Front. Mater.
Sec. Environmental Degradation of Materials
Volume 12 - 2025 | doi: 10.3389/fmats.2025.1580067
This article is part of the Research TopicExploring Corrosion Resistance Mechanisms in Weathering SteelView all articles
The final, formatted version of the article will be published soon.
Select one of your emails
You have multiple emails registered with Frontiers:
Notify me on publication
Please enter your email address:
If you already have an account, please login
You don't have a Frontiers account ? You can register here
Cooling water heat exchangers are essential components in chemical production processes, requiring long-term stability under corrosive circulating cooling water conditions. Coating protection technology has become increasingly widespread for mitigating corrosion in these systems.However, prolonged immersion in cooling water during operation can result in coating degradation and detachment. This study examines the corrosion behavior associated with coating damage in cooling water heat exchangers under varying immersion times. Coated carbon steel specimens were coupled with artificially stripped specimens to simulate large cathode and small anode systems in a cooling water environment. The results reveal that the corrosion rate of the small exposed anode increases as the exposure area decreases. Simultaneously, the adhesion between the coating and the substrate of the large cathode weakens with immersion time, leading to the formation of voids regardless of the exposure area. The findings indicate that in practical applications, smaller areas of coating delamination drive localized corrosion at the exposed substrate, whereas larger areas promote internal corrosion beneath the coating, ultimately leading to complete coating failure.
Keywords: cooling water heat exchangers, Organic coatings, Chemical process safety, corrosion, Coating breakage
Received: 20 Feb 2025; Accepted: 21 Apr 2025.
Copyright: © 2025 Zuo, Yu, Hou, Ren, Zhang, Zhang, Zhang, Sand, Hu, Chen, Duan and Hou. This is an open-access article distributed under the terms of the Creative Commons Attribution License (CC BY). The use, distribution or reproduction in other forums is permitted, provided the original author(s) or licensor are credited and that the original publication in this journal is cited, in accordance with accepted academic practice. No use, distribution or reproduction is permitted which does not comply with these terms.
* Correspondence:
Jie Zhang, Institute of Oceanology, Chinese Academy of Sciences (CAS), Qingdao, 266071, Shandong Province, China
Ruiyong Zhang, Institute of Oceanology, Chinese Academy of Sciences (CAS), Qingdao, 266071, Shandong Province, China
Disclaimer: All claims expressed in this article are solely those of the authors and do not necessarily represent those of their affiliated organizations, or those of the publisher, the editors and the reviewers. Any product that may be evaluated in this article or claim that may be made by its manufacturer is not guaranteed or endorsed by the publisher.
Supplementary Material
Research integrity at Frontiers
Learn more about the work of our research integrity team to safeguard the quality of each article we publish.