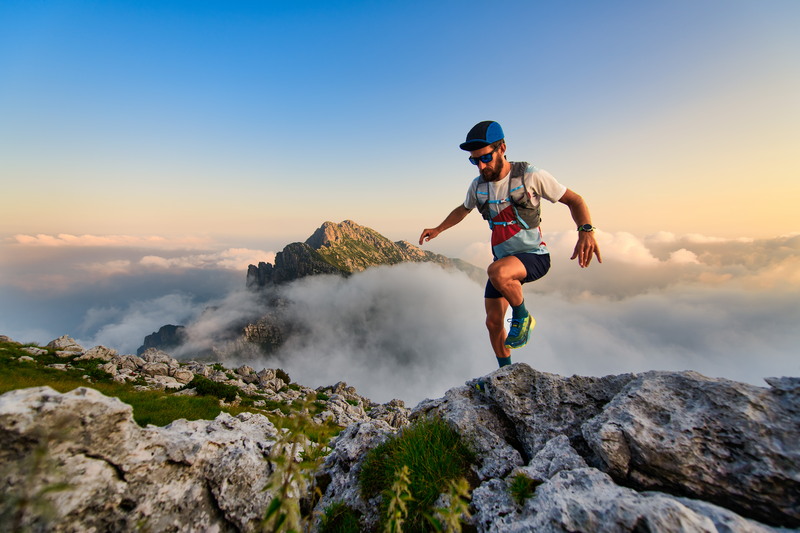
94% of researchers rate our articles as excellent or good
Learn more about the work of our research integrity team to safeguard the quality of each article we publish.
Find out more
ORIGINAL RESEARCH article
Front. Mater. , 26 March 2025
Sec. Energy Materials
Volume 12 - 2025 | https://doi.org/10.3389/fmats.2025.1567799
Coal gangue can be used for CO2 mineralization and then be backfilled into the goaf, which can simultaneously address the long-term management of coal gangue and CO2. Mechanical and composite activation methods were employed to enhance the activity and mineralization potential of coal gangue, and ion leaching experiments were conducted to leach active ions from mechanically-activated coal gangue (MACG) and composite-activated coal gangue (CACG) in this study. Additionally, the evolution of the mineralization potential of MACG and CACG samples under different conditions was explored by inductively coupled plasma-optical emission spectrometry (ICP-OES) tests. The results show that with the extension of milling time, the leaching rates of Ca2+, Mg2+, and K+ of MACG samples gradually increase, while the leaching rate of Ca2+ of CACG samples gradually decrease, and leaching rates of Mg2+ and K+ of CACG samples gradually increase. The activation mechanism of MACG samples was analyzed by the dry powder laser particle size analysis (DPLPSA) and Brunauer-Emmett-Teller (BET). The results show that when the milling time is less than 2 h, the average particle size of MACG samples decreases significantly and the specific surface area increases significantly with the extension of the milling time. However, when the milling time increases to 4 h, the changes in particle size and specific surface area become less significant, leading to an increase in the non-uniformity coefficient and a reduction in porosity. Thermogravimetry (TG) analysis was used to analyze the material components of MACG and CACG samples. It was found that due to the combustion of organic matter, thermal activation after mechanical activation can effectively improve the activity of coal gangue. After mechanical activation, the activity improvement of coal gangue is gradually reduced due to the advance of the transition temperature from metakaolinite to mullite. Finally, MACG and CACG samples before and after mineralization were analyzed by TG tests. The mineralization capacity of MACG samples with a 2-hour milling time was found to be 0.43%, whereas CACG samples achieved a higher mineralization rate of 0.53%.
In recent years, coal has constituted over half of China’s energy consumption, as shown in Figure 1A. Coal production has been on an upward trend, with a total output of 4.71 billion tons in 2023, an increase of 3.2% over the previous year. This growth is expected to persist in the coming years. During the coal mining and washing processes, a significant quantity of coal gangue is produced, resulting in water and soil contamination inevitably. Furthermore, the combustion of coal releases substantial amounts of CO2, contributing to environmental issues such as an enhanced greenhouse effect, soil acidification, and pollution of groundwater resources. According to statistics in Figure 1B, China’s annual carbon emissions account for more than 30% of the world’s total annual emissions.
Figure 1. Current status of gangue discharge and carbon emissions in China. (a) China’s gangue production and growth rate (b) Proportion of China’s carbon emissions.
In recent years, the burgeoning technology of carbon capture, utilization, and storage (CCUS) has emerged as a promising approach to addressing the issue of carbon dioxide (Jianfeng and Xiaofang, 2019; Fu et al., 2021). CCUS refers to the industrial process that separates CO2 from industrial emission sources or directly utilizes, or stores it to achieve CO2 emission reduction. As an important component of the CCUS, CO2 mineralization and storage refers to imitating the process of rock weathering. In this process, CO2 is captured and dissolved in water to form carbonic acid, which subsequently reacts with alkaline minerals to produce stable solid carbonate compounds. Compared with other storage methods, CO2 mineralization exhibits superior safety and stability, and has garnered growing attention. A large number of studies on the mineralization of steel slag, furnace slag and magnesium slag have been carried out (Weiji et al., 2024; Zuohui, 2021; Yu, 2018). Due to its tightly packed structure, gangue exhibits limited reactivity with other substances. As a result, research on gangue mineralization primarily concentrates on transforming it into porous adsorbent materials, while the chemical mineralization of gangue is rarely studied. To effectively improve the mineralization efficiency of gangue, the activation means are required to change the physical and chemical properties and boost its potential for mineralization.
Currently, commonly used mineralization methods include thermal activation, mechanical activation and chemical activation (Jin, 2022). Of these methods, chemical activation requires the addition of chemical activators, which increases the production cost and the difficulty of subsequent separation processes. In contrast, thermal activation and mechanical activation are more cost-effective options. Mechanical activation of coal gangue refers to the use of ball milling to refine the gangue particles and break the integrity of the gangue crystals (Zhang, 2014; Rees et al., 2007), thereby improving the activity of the gangue. Currently, researchers have proposed many theoretical models on the mechanism of mechanical force (Tian and Wang, 2021). During the thermal activation process, organic matters such as fixed carbon in the gangue are removed through calcination, the reactive substances in the gangue are exposed, and the kaolinite in the gangue is transformed into highly active products. This transformation is also referred to as calcination activation (Yao et al., 2021; Li, 2020). Numerous studies have investigated the impact of activation atmosphere, mineral composition, particle size, and carbon combustion on the thermal activation of coal gangue (Si, 2011; Zhang et al., 2019; Zhang et al., 2015). Among these factors, activation temperature remains one of the most critical elements. The pros and cons of the three activation methods are compared in Table 1. Furthermore, the integration of two or more activation methods is referred to as composite activation. This approach can compensate for the limitations of individual activation techniques, obtaining higher activation efficiency than the single activation method.
Regarding the research on the mineralization of coal-based solid waste, Zhu et al. (2024) reviewed the research advancements of CO2 mineralization and storage technology using coal-based solid waste as raw material. They discovered that this technology faces challenges such as stringent reaction conditions, significant expenses, and limited processing capacity, remaining largely confined to laboratory settings. By using the coal gangue below 200 mesh, Gao et al. (2015) prepared a new type of porous silicate material through calcination and alkali excitation. The adsorption capacity of porous silicate material (PSM) for CO2 within 90 min was 36.691 mg/g under a temperature of 293.15 K, normal pressure, and a pure CO2 flow rate of 1201 mL min. Wu et al. (2020) used coal gangue as the silicon source and prepared a series of adsorbents through the hydrothermal method. The results showed that Mg0.9-Cu0.1-SiO3 can adsorb 16.73 1 cm3/g CO2 at 298.15 K and 1 bar. Duo Zhang et al. (2016) designed the concrete with fly ash, water and cement in a ratio of 0.25:0.5:1. After pre-curing, the sample was cured for 12 h in a pure carbon dioxide atmosphere of 0.5 MPa. Finally, the compressive strength of mortar products mixed with 20% fly ash can reach 112 MPa. Huo et al. (2023), Huo et al. (2024) explored the relationship between the activity and specific surface area of acid- and alkali-modified coal gangue. It was found that when the acetic acid addition amount was 2 wt%, the CO2 capture capacity of the gangue reached 0.30 mmol/g. Researchers also developed cement-free high-calcium and low-calcium fly ash brick products and conducted comparative experiments (Wei et al., 2018). The results showed that high-calcium fly ash is more likely to produce dense cementing material, and the cemented solid strength reaches 35 MPa after 7 days of mineralization reaction at 75°C.
At present, the research on the activation properties of gangue with different activity techniques and parameters is mostly used to extract silicon and aluminum elements (Shao, 2023), while the mineralization potential dominated by calcium and magnesium elements is still lacking. In addition, researchers have studied the mineralization laws of highly active coal-based solid wastes such as fly ash under different conditions (Chujie et al., 2024; Ding et al., 2023). However, these studies on the mineralization performance of coal gangue focus on physical adsorption, and there is a lack of research on its chemical mineralization mechanism. To this end, the activity changes of MACG and CACG samples under different activation conditions were compared, the modification mechanism of gangue by mechanical activation time and composite activation was revealed, and the mineralization effect of coal gangue before and after composite activation was further verified.
Coal gangue from a certain coal mine was used as the raw material. The gangue samples were crushed and sieved to obtain the fine powder with a particle size of less than 1 mm for mechanical activation and composite activation. The mineralization potential of MACG and CACG samples was characterized by ion leaching experiments, and the influence mechanism of different milling time on MACG samples was revealed from the perspective of particle size gradation and pore distribution. TG analysis was used to explore the composite activation mechanism, and the mineralization effect of MACG and CACG samples was studied by pressurizing mineralization.
After grinding the gangue, the fine powder with a particle size of below 45 μm (using a 200-mesh sieve) was dried using a blast drying oven at a temperature of 60°C for 24 h. After that, an X-ray fluorescence spectrometer (XRF, Panalytical Axios, Netherlands) and X-ray diffractometer analysis (XRD, Rigaku Company, Japan) were used to analyze the chemical composition and mineral components of the gangue. The XRF analysis element range was 4Be-92U, and the element quantification range was ppm-100%. Table 2 shows the measured chemical composition and content of the coal gangue. XRD employed the copper target test, with a scanning range of 5°–90° and a scanning speed of 5°/min. Figure 2 shows the measured material components of coal gangue.
It can be found that the concentrations of CaO, MgO, and K2O that can be used for mineralization are 3.51%, 1.88%, and 2.21% respectively. Referring to Figure 1, it can be deduced that these compounds originate from anorthite, calcite, muscovite, dolomite, and carlosturanite. Due to the low content of mineralizable components and the dense arrangement of gangue crystal lattices, the original gangue demonstrates extremely low reactivity. Consequently, its utilization as a mineralization feedstock is particularly challenging, necessitating activation treatment.
Figure 3 shows the preparation process of MACG samples. The large gangue was crushed by a jaw crusher, and the gangue with a particle size of below 1 mm was obtained by vibration and put into a planetary ball mill (Beijing Gridman Company, BM6Pro). To study the activation mechanism of coal gangue by milling time, four groups of milling time (0 h, 1 h, 2 h, and 4 h) were selected to activate coal gangue. These samples are designated as M1, M2, M3, and M4, respectively. The specific parameters were as follows. A total of 150 g of coal gangue, and 135 g large-diameter milling balls (4 mm), 180 g medium-diameter milling balls (2 mm) and 135 g small-diameter milling balls (1 mm) were weighted, and the planetary ball mill was operated at a speed of 400 r/min, with a cooling interval of 20 min after every 30 min of milling. The ground samples were packaged for subsequent testing and characterization.
It should be noted that the excessively high activation temperature of coal gangue can result in the transformation of kaolinite into spinel and mullite phases, consequently leading to a reduction in material reactivity. Some scholars (Feng, 2021) reported that the optimal activation temperature of coal gangue is 650°C, 600°C. Therefore, the activation temperature in this study was designed to be 700°C. Figure 3 shows the CACG preparation process. Gangue samples (M1, M2, M3, and M4) were put into the muffle furnace. Once the furnace door was sealed, the samples were heated from room temperature to 700° Cat a heating rate of 10°C/min and kept for 2 h. After the temperature of the muffle furnace dropped to room temperature, the samples were taken out, classified as C1, C2, C3, and C4, and then sealed and stored for subsequent microscopic examination and characterization.
After characterizing the activities of MACG and CACG samples, the coal gangue before and after composite activation was put into the reaction kettle of the coal-based solid waste mineralization CO2 test platform (Figure 4), and mineralization experiments on MACG and CACG samples were conducted to explore the difference in their mineralization effects.
Before the mineralization, the CO2 cylinder, booster pump and inlet valve of the gas canister were first opened, and the pressure in the gas canister was increased to 15 MPa for standby use. Second, 268 g of water and 400 g of activated gangue powder were weighed by an electronic scale and poured into the reaction kettle. To prevent leakage, the hexagonal screws were tightened on the reaction kettle diagonally. Third, the CO2 flow rate was set as 1.5 L/min and the agitator speed to 600 r/min within the parameter setting and data acquisition system, and then the experiment was initiated with automatic data recording by clicking Experiment Start. Upon the initiation of the experiment, the inlet valve of the reaction kettle was opened to increase the pressure in the kettle to 6 MPa, Start Agitation within the parameter setting and data acquisition system was clicked and the duration was set for 30 min. After mineralization was completed, the outlet valve of the reaction kettle was opened to reduce the pressure in the kettle to 0.1 MPa, and then End Experiment was clicked in the parameter setting and data acquisition system. Finally, all pipeline connections were disconnected, the reactor was opened, and the mineralized slurry was excavated. To prevent excessive free water, the gangue after mineralization was dried at 60°C for 24 h, and the mineralized gangue powder with evaporated water was put into a sealed bag.
To explore the evolution law of the mineralization potential of MACG and CACG samples under various activation parameters, an ion leaching experiment was designed for their characterization. The activation mechanism of MACG samples was revealed by DPLPST and BET, the activation mechanism of CACG samples was revealed by TG analysis, and the mineralization effect of MACG and CACG samples were compared.
ICP-OES tests. Metal ion leaching experiment involves the process of extracting metal ions from mineral structures by dissolving the minerals in acidic or basic solutions, thereby forming soluble metal compounds. ICP-OES test can be used to obtain the concentration of each ion in the dilution solution based on the principle that different atoms and ions exhibit unique spectral characteristics. According to the measured data, the leaching rate of each element in ACG can be calculated using Equation 1 and Equation 2.
Where θ is the leaching rate of elements in ACG slag, %; C is the mass concentration of elements in the leaching solution, mg/L; V is the volume of filtrate after leaching, L; m is the mass of ACG, g; k is the mass fraction of the element in ACG, %; c is the mass concentration of elements in the leaching solution after dilution, mg/L; n is the dilution multiple of the leaching solution.
Figure 5 shows the experimental process (Song et al., 2024). (1) The ACG was placed in a forced air-drying oven and dried at 60°C for 24 h. To avoid moisture absorption from the air caused by high temperatures, the material was placed in a dryer for storage after it had naturally cooled in the oven; (2) A 30 mL HCl solution was weighed by a measuring cylinder and poured into a 150 mL conical flask. The leaching system was maintained at 30°C (water bath heating) by a constant temperature magnetic stirring, and then 1 g of ACG was weighed by the weighing paper and added to the conical flask. The magnetic stirring was initiated and the solution was mixed at a speed of 600 r/min for 8 min; (3) After centrifugation at 6,000 r/min for 3 min at a high-speed centrifuge, the slurry was filtered through a 0.22 μm organic filter (Labshark) to separate the residue from the leaching solution. (4) The concentration of alkali metal ions such as Ca2+, Mg2+, and K+ was analyzed by ICP-OES after 10 times dilution of 10 mL of the leaching solution.
The gangue powder was dried in a drying oven for 6 h, and then the gangue particle size was tested using DPLPST (Jinan Micro-Nano Particle Instrument Co., Ltd., Winner 3,009). Test method: Free distribution analysis mode. Based on the software test data and referring to the soil mechanics particle gradation (Li et al., 2021) evaluation method, the fine gangue particle size gradation Cu was further analyzed through the non-uniformity coefficient. The calculation function is as follows:
Among them, Cu reflects the concentration degree of particles. In general, as the value approaches 1, the particle concentration increases, resulting in reduced inter-particle meshing and decreased particle activity. D10 and D60 represent the particle sizes at which the cumulative distribution reaches 10% and 60% of the sample, respectively. These values are referred to as the effective particle size or limited particle size.
A fully automatic specific surface and porosity analyzer (American Micromeritics, ASAP2460) was used to detect and analyze the specific surface area, porosity and average pore size of MACG samples. The testing principle is as follows: the adsorption of gas or liquid molecules on the solid surface is the single-layer adsorption; as the pressure increases, multilayer adsorption occurs and this adsorption is reversible. At this time, the BET equation can be used to calculate the specific surface area, porosity and average pore size. The N2 was used as the adsorbent and the test was conducted at −195.850°C.
The carbonate loss on ignition after the mineralization of MACG and TACG samples was analyzed using TG (German Netzsch Company), and then compared with that before mineralization. Consequently, the impact of activation time on the mineralization efficiency was investigated.
After grinding the gangue, both its macroscopic and microscopic characteristics undergo alterations, resulting in modified reactivity. During mineralization, Ca2+ and Mg2+ ions primarily contribute to carbonate precipitation, serving as key raw materials for this process. In addition, soluble carbonates such as K2CO3 can also lead to the formation of certain carbonate crystals upon drying. Therefore, the leaching rates of Ca2+, Mg2+, and K+ can be used as characterization indicators of the mineralization potential of MACG samples. As shown in Figure 5, MACG was sampled for ion leaching experiments. The ICP-OES test was used to analyze the leaching concentrations of alkali metal ions such as Ca2+, Mg2+, and K+ in MACG samples with different milling time, and the ion leaching rates were calculated according to Equations 1, 2 as shown in Figure 6.
Figure 6 shows the effect of milling time on the activity of MACG. The results show that the milling time has different degrees of influence on the leaching rate of alkali metal ions such as Ca2+, Mg2+, and K+ in MACG samples. As the milling time increases, the leaching rates of Ca2+, Mg2+, and K+ exhibit an upward trend. For example, in samples M1, M2, M3, and M4: the leaching rates of Ca2+ are 16.98%, 24.32%, and 29.81%, and 31.29%respectively. Similarly, the leaching rates of Mg2+ are 8.27%, 14.26%, 18.68%, and 20.19%, while those for K+ are 0.53%, 1.93%, 3.20%, and 3.54%, respectively. However, the increase in the leaching rate of the sample slows down over time. Specifically, as the milling time increases from 0 h to 1 h, 2 h, and 4 h, the leaching rate of Ca2+ increases by 43%, 23%, and 5%, respectively; for Mg2+, the increments are 73%, 1%, and 8%; for K+, the increments are 268%, 65%, and 11%, respectively. It can be seen that the growth rate of MACG samples gradually decreases, especially after the milling time increases from 2 h to 4 h, and leaching rates of Ca2+ and Mg2+ increase slightly.
Through the above analysis, it can be found that when the milling time is less than 4 h, increasing the milling time can have a positive impact on MACG activity. However, when the time exceeds a certain threshold, the time consumed and economic cost will not be proportional to the improved performance. In addition, some researchers found that excessive milling time can lead to the agglomeration of gangue particles, thereby decreasing their activity.
The influence of mechanical activation time on MACG samples has been characterized. During the milling process of coal gangue, the particles are crushed due to mechanical force, and their particle size will inevitably change. In this experiment, DPLPST was used to explore the particle size gradation of samples M1, M2, M3, and M4, and the influence mechanism of gangue particle size on mineralization potential was elucidated. Figure 7 shows the particle size gradation of the MACG samples under different milling time.
Figure 7. Effect of milling time on particle size gradation of MACG samples. (a) M1 (b) M2 (c) M3 (d) M4.
As shown in Figure 7, the particles in sample M1 exhibit a larger size, all exceeding 100 μm, and follow an unimodal distribution. The particle size of sample M2 quickly shrinks to less than 200 μm, and converts to a bimodal distribution, with one located near 12 μm and the other near 120 μm. The particle size of sample M3 continues to shrink rapidly to below 20 μm, resulting in a return to a unimodal distribution. The particle size of sample M4 exhibits a continued reduction; however, this decrease is relatively minimal, and the distribution remains unimodal.
As shown in Figure 8, combined with Equation 3 the characteristic particle size and particle gradation of gangue are analyzed in detail. It can be found that as the milling time increases, both Dav and D90 of MACG samples decrease rapidly under the action of mechanical force. Compared with M1, the Dav of M2, M3, and M4 decreases from 718.547 μm to 41.909 μm, 9.927 μm, and 3.748 μm respectively, and D90 decreases from 1090.841 μm to 114.653 μm, 12.174 μm, and 5.174 μm, respectively. Compared with M1, the Dav of M2, M3, and M4 is reduced by 84.0%, 98.3%, and 99.5%, respectively, and D90 is reduced by 94.2%, 98.6%, and 99.3% respectively. This indicates that the mechanical milling effect is significant, and the D90 of samples under all milling time decreases by over 90%; however, the rate of reduction shows a gradual decline.
Figure 8. Effect of milling time on average particle size and particle size gradation of MACG samples.
The non-uniformity coefficient of MACG samples first decreases rapidly and then gradually stabilizes. Compared with M1, the non-uniformity coefficient of sample M2 drops from 2.39 to 1.80. As shown in Figure 7B, after 1 h milling, the particles of MACG samples undergo rapid refinement; however, their distribution remains broad. The non-uniformity coefficient of sample M3 drops to the lowest point of 1.39, and the particle size distribution is relatively concentrated, as shown in Figure 7C. The non-uniformity coefficient of sample M4 is slightly increased, reaching 1.42.
The particle size refinement rule of MACG samples is consistent with the ion leaching rule, and the mechanical activation mechanism of MACG samples can be explained from the perspective of particle size distribution. Researchers also found that as the milling time increases, the breakage of bonds leads to charging on the surface of the gangue particles, causing the fine particles to adsorb each other under the action of greater attraction and produce secondary agglomeration (Yu, 2006). Therefore, the increase in average particle size, D90 and non-uniformity coefficient after 4 h milling may be caused by the secondary agglomeration phenomenon. To avoid the adverse effects of secondary agglomeration on CG activity and ensure economic feasibility, the ball milling duration should not be prolonged, and 2–4 h is the optimal mechanical activation time.
During the gangue milling process, under the action of mechanical force, the original structure of the particles is broken, forming many micro-cracks. The existence of these micro-cracks increases the contact area between the gangue particles and other substances, thereby increasing the mineralization potential of the gangue. In this study, the BET test was used to explore the change patterns of specific surface area, porosity and average pore size of MACG samples in the four groups.
Figure 9 shows that milling time has varying degrees of impact on the specific surface area, porosity and average pore size of MACG samples. With the extension of milling time, the specific surface area of MACG samples shows an increasing trend. The specific surface areas for groups M1, M2, M3, and M4 are 6.6671 m2/g, 6.4621 m2/g, 16.7918 m2/g, and 17.4271 m2/g, respectively. This enhancement in specific surface area expands the interaction area with other materials, thereby positively influencing its reactivity. However, the average pore size of MACG samples shows a decreasing trend, such as the average pore size of M1, M2, M3, and M4 are 15.9898 nm, 15.1145 nm, 13.7046 nm, 11.4199 nm, respectively. The reduction of pore size has a negative effect on its activity. Porosity can be used to characterize the pore volume produced by the sample per unit weight. This parameter is proportional to the product of its specific surface area and average pore size. To a certain extent, porosity comprehensively represents the activation degree of MACG particles and can better reflect the activity of the sample. The porosity of the MACG sample first increases and then decreases. This indicates that before reaching the peak value, the increase in specific surface area has a more significant positive impact on its activity compared to reducing pore size. Conversely, after surpassing the peak value, the effect of decreasing pore size becomes more advantageous. For example, the porosities of samples M1, M2, M3, and M4 are 19.98 cm3/g, 24.42 cm3/g, 57.53 cm3/g, and 49.75 cm3/g, respectively. The porosity of MACG samples reaches a peak value at 2 h of ball milling, and the porosity of MACG samples increases by 288% compared with the unactivated group. However, it gradually decreases with the increase of milling time.
Figure 9. Effect of milling time on specific surface area, porosity and average pore size of MACG samples.
Figure 10A shows the volume adsorption pattern of MACG samples. The hysteresis loop type of MACG samples is type II isotherm. Compared with M1, M3 and M4 show a higher volume adsorption platform between 0–0.6 P/P0, indicating that the number of small pores in M1 is the least. This phenomenon proves that ball milling can quickly reduce the pore size of gangue, but after increasing the milling time from 2 h to 4 h, the number of small pores hardly changes. However, after the relative pressure is increased to 1, the gas adsorption amount of sample M2 exceeds that of sample M4, indicating that there are more macropores in MACG samples after 2 h mechanical grinding.
Figure 10. Volumetric adsorption pattern and pore size distribution of MACG samples. (a) Volumetric adsorption pattern (b) pore size distribution.
Figure 10B shows the influence of milling time on pore size distribution of MACG samples. It can be found that sample M1 exhibits pore sizes exceeding 2 nm, classifying them as mesoporous materials. In contrast, the other materials possess pores smaller than 2 nm, indicating a transition towards microporous materials. The pore size of sample M1 is concentrated at 2–8 nm, and the peak pore size of sample M2 near 4 nm is significantly reduced and a new peak is formed near 32 nm, indicating that pores of the sample have become larger after ball milling. The peak pore size of sample M3 at 4 nm and 32 nm are both increased, indicating that both large pores and small pores are newly generated. The sample M4 shows an increase in the peak at 4 nm, whereas the peak at 32 nm decreases. This suggests that prolonged milling results in larger pores being reduced to smaller ones.
Therefore, as the milling time increases, the pore size distribution evolves through three stages: (1) the enlarged pore size; (2) the generation of new large and small pores; (3) the transition from large pores into small pores. Based on the factor of porosity, this finding is consistent with the ion leaching law.
The leaching rates of Ca2+, Mg2+, and K+ are also used as indicators of MACG mineralization potential. As shown in Figure 5, CACG was sampled for ion leaching experiments. ICP-OES was used to test and analyze the leaching concentrations of alkali metal ions such as Ca2+, Mg2+, and K+ in CACG samples with different milling time, and the ion leaching rates were calculated according to Equations 1, 2 as shown in Figure 11.
Figure 11 shows the changes in the leaching rate of alkali metal ions such as Ca2+, Mg2+ and K+ after MACG samples was processed at 700°C for different milling time. The data shows that different activation parameters have varying degrees of impact on the leaching rate of alkali metal ions such as Ca2+, Mg2+ and K+ from the gangue. When calcined at 700°C, the leaching rate of Ca2+ in CACG samples shows a downward trend as the milling time increases. For example, in C1, C2, C3, and C4 groups, the leaching rates of Ca2+ are 34.28%, 33.48%, 31.66%, and 30.9%, respectively. In contrast, the leaching rates of Mg 2+ and K+ show an increasing trend. The leaching rates of Mg2+ in groups C1, C2, C3, and C4 are 13.18%, 13.87%, 18.85%, and 18.93% respectively. In addition, the decrease in the leaching rate of Ca2+ and the increase in the leaching rate of Mg2+ and K+ in groups C3 and C4 are not significant. The changes in Ca2+ and Mg2+, which serve as the main mineralization ions, are even less than 1%. However, these changes are more pronounced when compared to the C2 group.
As shown in Figure 6, the ion leaching rate in the composite activation group is generally higher than that in the mechanical activation group, which proves that thermal activation after mechanical activation can effectively improve the activity of coal gangue. However, this improvement gradually decreases with the prolongation of milling time, and even thermal activation after ball milling for 4 h reduces its ion leaching rate. The mechanism of this phenomenon will be explored in the next section.
To explore the changes in the material components of coal gangue caused by composite activation, TG analysis was used to detect and analyze MACG samples in M3 group and CACG in C3 group. Figure 12 shows the detailed results of TG analysis. The TG analysis results reveal four distinct peaks in the curve of MACG samples. The first peak, occurring below 100°C, corresponds to the evaporation of free water. The second peak, at approximately 446°C, is attributed to the combustion of volatiles and fixed carbon. The third peak, observed at around 631°C, signifies the decomposition of calcium carbonate. Finally, the fourth peak, at 900°C, indicates the transformation of metakaolinite into mullite. The overall weight loss rate of CACG samples is lower than that of MACG samples, and the peaks are not very obvious, indicating that calcination has burned out the free water and organic matter in the gangue.
Researchers have proposed a gas-solid phase reaction model of coal gangue to explain the fixed carbon combustion phenomenon during the calcination of the coal gangue, as shown in the shrinking core model in Figure 13 (Fu, 2003). As shown in Figure 13, when coal gangue is calcined, the thermal radiation from the muffle furnace causes the O2 in the air to react with the fixed carbon on the particle surfaces. As a result, an ash layer on the exterior of the gangue particles is formed, and CO2 is generated and diffuses toward the ash layer. Additionally, water vapor produced by the dehydroxylation reaction of kaolinite also moves outward through the pores between particles in the ash layer. The combustion of volatile components and fixed carbon not only removes these inert substances that do not participate in mineralization, but also creates many micropores on the surface of the gangue particles. Consequently, the contact area between the gangue particles and the solution is increased, thereby improving the mineralization potential of the MACG sample. However, as the reaction proceeds, the thickness of the ash layer gradually increases and the diffusion resistance increases. When the calcination temperature is lower than the combustion temperature of organic matter, the reaction of small particles and the generated gas are subject to less resistance. The more complete the calcination, the more conducive to the progress of the decomposition reaction. The temperature of 700°C significantly exceeds the combustion point of organic materials, ensuring that any organic matter within the gangue is thoroughly oxidized. As the particle size reduces, metakaolinite more readily undergoes transformation into the mullite phase. Under the melting effect, the particle size increases, the pores are gradually filled, and the activity of the gangue is reduced. Therefore, as the milling time increases, the leaching rate of Ca2+ from CACG sample decreases.
TG was used to detect and analyze the pyrolysis effect of gangue before and after mineralization of MACG and CACG samples. The results are shown in Figure 14.
Figure 14. TG analysis of MACG and CACG. (a) Pyrolysis curves of mineralized ACG (b) Pyrolysis curves of mineralized ACG.
As shown in Figure 14B, the peak in area A between 525°C and 700°C, the weight loss rate of the MACG smples after mineralization is significantly higher than that of the non-mineralized group. It can be speculated that this peak is the pyrolysis of carbonate. Combined with Figure 14A, during this period, the mass fraction of the mineralized group decreases from 93.67% to 90 0.94%, the loss on ignition is 2.73%; the mass fraction of the non-mineralized group decreases from 92.838% to 90.54%, the loss on ignition is 2.3%, then the difference between the two is the mineralization amount of the MACG, which is 0.43%. In other words, when CO2 is introduced into the MACG sample, 0.33% carbonate can be formed. In area A, the temperature range between 525°C and 650°C is the pyrolysis interval of calcium carbonate in CACG samples. As shown in Figure 14A, during this period, the mass fraction of the mineralized group decreases from 98.61% to 97.95%, and the loss on ignition is 0.66%; while the mass fraction of the non-mineralized group is reduced from 99.33% to 99.08%, and the loss on ignition is 0.12%. Then the difference between the two losses on ignition is the mineralization amount of MACG samples, which is 0.53%. In other words, when CO2 is introduced into the MACG sample, 0.53% carbonates are formed.
Therefore, the dense structure of coal gangue has been broken after mechanical activation, and then the chemical mineralization of CO2 can be carried out, but the consolidation amount is low. Composite mineralization can further increase the amount of CO2 mineralization based on mechanical activation.
Despite the understanding of the mechanisms of the mechanical and composite activations on gangue and the corresponding mineralization ability, there is much work yet to be performed to design a safe and cost-effective backfilling structure made with CO2-mineralized gangue. To shed light on this issue, more work is required as follows.
(i) Investigate the mechanical properties of the CO2-mineralized backfilling body, especially the long-term uniaxial compressive strength, which is the key to assessing the stability of the overlying strata in mines;
(ii) Analyze the cost investment of the negative-carbon backfilling technology and assess the environmental risks caused by the CO2-mineralized backfilling body.
In this study, ion leaching experiments and ICO-OES tests were used to characterize the mineralization potential of MACG and CACG samples at 0 h, 1 h, 2 h and 4 h, and DPLPST and BET tests on MACG samples were conducted. A TG analysis was performed on MACG and CACG samples before and after composite activation and before and after mineralization. The following conclusions are drawn as follows.
(1) When the milling time is 0 h, 1 h, 2 h and 4 h, the leaching rates of Ca2+ in MACG samples are 16.98%, 24.32%, 29.81% and 31.29%, respectively; the leaching rates of Ca2+ increases by 43%, 23%, and 5% respectively. The increase in milling time exhibits a positive impact on MACG activity. However, when the milling time exceeds 2 h, the activity of gangue increases slowly. When the milling time is less than 2 h, the average particle size of MACG samples decreases significantly and the specific surface area increases significantly with the extension of the milling time. However, when the milling time increases to 4 h, the changes in particle size and specific surface area become less significant, leading to an increase in the non-uniformity coefficient and a reduction in porosity.
(2) After composite activation of MACG samples for 0 h, 1 h, 2 h and 4 h, the leaching rates of Ca2+ are 34.28%, 33.48%, 31.66% and 30.9%, respectively; when the milling time is no more than 2 h, the ion leaching of the samples in the composite activation group is higher than those in the mechanical activation group. Owing to the combustion of organic matter, thermal activation after mechanical activation can effectively improve the activity of coal gangue. After mechanical activation, the activity improvement of coal gangue is gradually reduced due to the advance of the transition temperature from metakaolinite to mullite.
(3) The dense structure of coal gangue can be broken after mechanical activation, and then the chemical mineralization of CO2 can be carried out, while the consolidation amount is low. Composite mineralization can further increase the amount of CO2 mineralization based on mechanical activation. The mineralization amount of MACG samples with a milling time of 2 h is 0.43% and that of CACG samples is 0.53%.
The mineralization amount of the CACG sample is still insufficient, and further optimization research on the optimal composite activation parameters is needed. In addition, the influence of chemical activation on the mineralization effect of composite activation still needs to be explored.
The original contributions presented in the study are included in the article/supplementary material, further inquiries can be directed to the corresponding author.
LZ: Conceptualization, Funding acquisition, Resources, Writing – review and editing. CL: Conceptualization, Resources, Supervision, Writing – original draft. GD: Data curation, Formal Analysis, Visualization, Writing – original draft. ZL: Investigation, Software, Validation, Writing – original draft. LS: Methodology, Project administration, Writing – review and editing. YZ: Conceptualization, Methodology, Writing – review and editing. KF: Methodology, Project administration, Visualization, Writing – review and editing.
The author(s) declare that financial support was received for the research and/or publication of this article. This study was supported by the Jiangsu Province ‘Distinguished Professor 2023’ program (140923071) and the General Project of Fundamental Science (Natural Science) Research in Higher Education Institutions in Jiangsu Province (24KJB560002). The APC was funded by Science and Technology Project of China Coal Energy Research Instit,The project number is 2024210129.
Authors LZ, CL, and ZL were employed by China Coal Research Institute Co, Ltd.
The remaining authors declare that the research was conducted in the absence of any commercial or financial relationships that could be construed as a potential conflict of interest.
The author(s) declare that no Generative AI was used in the creation of this manuscript.
All claims expressed in this article are solely those of the authors and do not necessarily represent those of their affiliated organizations, or those of the publisher, the editors and the reviewers. Any product that may be evaluated in this article, or claim that may be made by its manufacturer, is not guaranteed or endorsed by the publisher.
MACG, mechanically-activated coal gangue; CACG, composite-activated coal gangue; ICP-OES, inductively coupled plasma-optical emission spectrometry; DPLPSA, dry powder laser particle size analysis; BET, Brunauer-Emmett-Teller; TG, thermogravimetric; CCUS, carbon capture, utilization, and storage; PSM, porous silicate material; XRF, X-ray fluorescence spectrometer; XRD, X-ray diffractometer; ACG, Activated coal gangue.
Chujie, Z., Yugao, W., Zhenzhao, Y., and Jiangfeng, Y. Research progress of coal fly ash for CO2 mineralization process Clean Coal Technology (2024). 30, 300–315. doi:10.13226/j.issn.1006-6772.YS23120101
Ding, Z., Zhang, X., Cheng, T., Shen, Y., Cai, W.-J., Chen, C.-T. A., et al. (2023). Unlocking high carbonation efficiency: direct CO2 mineralization with fly ash and seawater. Chem. Eng. Sci. 282, 119349. doi:10.1016/j.ces.2023.119349
Feng, T. (2021). Preparation of thermally activated copper tailings-gangue and alkali-excited cementitious materials. Master's degree. Kunming, China: Kunming University of Science and Technology.
Fu, C., Haochen, Y., Zhengfu, B., and Dengyu, Y. (2021). How to handle the crisis of coal industry in China under the vision of carbon neutrality. J. China Coal Soc. 46, 1808–1820. doi:10.13225/j.cnki.jccs.2021.0368
Fu, W. (2003). Theory of coal combustion and its macroscopic generic laws. Beijing: Tsinghua University Press.
Gao, Y., Huang, H., Tang, W., Liu, X., Yang, X., and Zhang, J. (2015). Preparation and characterization of a novel porous silicate material from coal gangue. MICROPOROUS MESOPOROUS Mater. 217, 210–218. doi:10.1016/j.micromeso.2015.06.033
Huo, B., Zhang, J., Li, M., Zhou, N., Qiu, X., Fang, K., et al. (2023). Effect of CO2 mineralization on the composition of alkali-activated backfill material with different coal-based solid wastes. SUSTAINABILITY 15, 4933. doi:10.3390/su15064933
Huo, B., Zhang, Q., Li, M., and Xing, S. (2024). Using recycled gangue to capture CO2 and prepare alkali-activated backfill paste: adsorption and microevolution mechanisms. FUEL 358, 130194. doi:10.1016/j.fuel.2023.130194
Jianfeng, M., and Xiaofang, M. (2019). Development trend analysis of carbon capture, utilization and storage technology in China. Proc. CSEE 39, 2537–2544. doi:10.13334/j.0258-8013.pcsee.190375
Jin, L. (2022). Experimental study on performance optimization of mechanically activated coal gangue-based grouting materials D. Xuzhou, China: China University of Mining and Technology.
Li, G., Sheng, Y., Song, Z., and Zhu, G. (2021). Study and optimization on rheological properties of high-concentration tailings slurry with different gradations in a mine. Min. Res. Dev. 41, 55–59. doi:10.13827/j.cnki.kyyk.2021.04.011
Li, Q. (2020). Effect of calcination temperature on the activity of coal gangue and mechanism study non-metallic mines, 43, 100–102+106.
Rees, C. A., Provis, J. L., Lukey, G. C., and van Deventer, J. S. J. (2007). Attenuated total reflectance Fourier transform infrared analysis of fly ash geopolymer gel aging. LANGMUIR 23, 8170–8179. doi:10.1021/la700713g
Shao, S. (2023). Basic research on thermal activation and HNO3 leaching of coal gangue to extract Al/Ga/Li university of science and technology beijing.
Si, P. (2011). Activation technology for aluminum recovery from coal spoil through acid leaching route. Ph.D. Shanghai, China East China University of Science and Technology.
Song, Q., Li, J., Wang, Y., Zhang, J., Peng, L., and Gao, A. (2024). Efficient leaching and indirect carbonation of Ca from AOD stainless steel slag Iron and Steel, 59, 200–209. doi:10.13228/j.boyuan.issn0449-749x.20230720
Tian, X., and Wang, X. (2021). Current status of mechanochemistry and its application prospects in wheat milling. Food Sci. 42, 275–282. doi:10.7506/spkx1002-6630-20200503-015
Wei, Z., Wang, B., Falzone, G., La Plante, E. C., Okoronkwo, M. U., She, Z., et al. (2018). Clinkering-free cementation by fly ash carbonation. J. CO2 Util. 23, 117–127. doi:10.1016/j.jcou.2017.11.005
Weiji, S., Lang, L., Zhiyu, F., Mengbo, Z., Geng, X., Wei, H., et al. (2024). Technique of wet carbonation of modified magnesium slag Chemical Industry and Engineering Progress, 43, 2161–2173. doi:10.16085/j.issn.1000-6613.2023-0660
Wu, Y., Wu, Z., Liu, K., Li, F., Pang, Y., Zhang, J., et al. (2020). Preparation of nano-sized Mg-doped copper silicate materials using coal gangue as the raw material and its characterization for CO2 adsorption. KOREAN J. Chem. Eng. 37, 1786–1794. doi:10.1007/s11814-020-0593-3
Yao, S., Cha, W., Liu, X., Ji, S., He, C., and Yu, Y. (2021). Physicochemical and thermal activation properties of waste coal gangue in pingxiang mining area. Bull. Chin. Ceram. Soc. 40, 2280–2287. doi:10.16552/j.cnki.issn1001-1625.20210510.001
Yu, L. (2018). “Fundamental research on mineralized GellingMechanism and regulation techniques of microbial carbonized steel slag BuildingMaterial products,” in master's degree. Nanjing, China: Southeast University.
Yu, Y. (2006). “Experiment research on mechano-chemistry ActivatingCoal gangue,” in Master's degree. Nanjing, China: Nanjing University of Technology.
Zhang, D., Cai, X., and Shao, Y. (2016). Carbonation curing of precast fly ash concrete. J. Mater. Civ. Eng. 28. doi:10.1061/(ASCE)MT.1943-5533.0001649
Zhang, J. (2014). Effect of mechanical grinding on the activity of gangue-based cementitious materials. J. Shandong Industrial Technol. 46. doi:10.16640/j.cnki.37-1222/t.2014.15.006
Zhang, Y., Xu, L., Seetharaman, S., Liu, L., Wang, X., and Zhang, Z. (2015). Effects of chemistry and mineral on structural evolution and chemical reactivity of coal gangue during calcination: towards efficient utilization. Mater. Struct. 48, 2779–2793. doi:10.1617/s11527-014-0353-0
Zhang, Y., Zhang, Z., Zhu, M., Cheng, F., and Zhang, D. (2019). Decomposition of key minerals in coal gangues during combustion in O2/N2 and O2/CO2 atmospheres. Appl. Therm. Eng. 148, 977–983. doi:10.1016/j.applthermaleng.2018.11.113
Zhu, L., Gu, W., Song, T., He, Z., and Liu, Z. (2024). Research progress of CO2 storage technology by mineralization of coal-based solid waste. Coal Sci. Technol. 52, 309–328.
Keywords: coal gangue, mechanical activation, composite activation, CO2 mineralization, ion leaching test
Citation: Zhu L, Liu C, Duan G, Liu Z, Shen L, Zhou Y and Fang K (2025) Investigation on the activation mechanisms of coal gangue and the corresponding CO2 mineralization potential. Front. Mater. 12:1567799. doi: 10.3389/fmats.2025.1567799
Received: 28 January 2025; Accepted: 17 March 2025;
Published: 26 March 2025.
Edited by:
Kunal Mondal, Oak Ridge National Laboratory (DOE), United StatesReviewed by:
Arnab Bose, Boehringer Ingelheim, United StatesCopyright © 2025 Zhu, Liu, Duan, Liu, Shen, Zhou and Fang. This is an open-access article distributed under the terms of the Creative Commons Attribution License (CC BY). The use, distribution or reproduction in other forums is permitted, provided the original author(s) and the copyright owner(s) are credited and that the original publication in this journal is cited, in accordance with accepted academic practice. No use, distribution or reproduction is permitted which does not comply with these terms.
*Correspondence: Kun Fang, fangkun0918@cumt.edu.cn
Disclaimer: All claims expressed in this article are solely those of the authors and do not necessarily represent those of their affiliated organizations, or those of the publisher, the editors and the reviewers. Any product that may be evaluated in this article or claim that may be made by its manufacturer is not guaranteed or endorsed by the publisher.
Research integrity at Frontiers
Learn more about the work of our research integrity team to safeguard the quality of each article we publish.