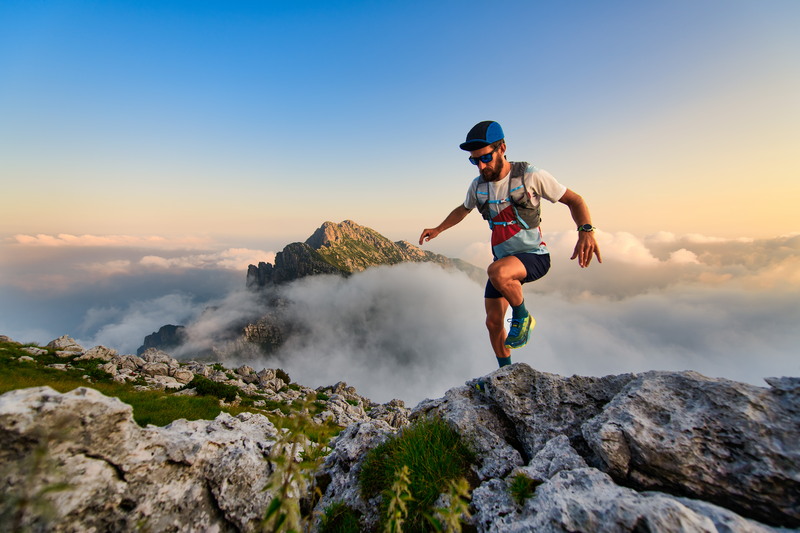
95% of researchers rate our articles as excellent or good
Learn more about the work of our research integrity team to safeguard the quality of each article we publish.
Find out more
ORIGINAL RESEARCH article
Front. Mater. , 24 March 2025
Sec. Energy Materials
Volume 12 - 2025 | https://doi.org/10.3389/fmats.2025.1559800
Elastocaloric systems, which leverage shape memory alloys (SMAs) to achieve efficient, eco-friendly thermal management, offer a promising alternative to conventional air conditioning technologies. This study presents a simulation-based approach to modeling the effects of moist air and condensation phenomena within these systems. Here, we examine key factors affecting SMA performance, including mechanical behavior and the material’s latent heat characteristics. Moist air, particularly under conditions where temperatures fall below the dew point, introduces condensation and latent heat release, which can influence thermal output in elastocaloric systems. This work develops a comprehensive model that couples the thermomechanical behavior of SMAs with the thermodynamics of moist air, incorporating condensation heat transfer, mass balance, and moisture transport. Through simulations, we quantify the impact of condensation on device level and assess how ambient moisture conditions affect overall heat exchange. The findings enhance our understanding of elastocaloric system performance under real-world conditions, contributing to the advancement of sustainable and modern technologies.
Elastocaloric (EC) materials have received considerable attention from researchers and industry recently for their potential utilization in air conditioning technologies. These materials, typically SMAs such as binary Nitinol (Ni-Ti), exhibit a significant temperature change when subjected to mechanical stress, a phenomenon known as the elastocaloric effect. This effect is characterized by the absorption or release of latent heat during the stress-induced phase transformation between austenitic and martensitic phases. The reversible nature of this solid-state transformation enables the repeated use of EC materials in cooling cycles, positioning them as viable candidates for next-generation technologies. The EC material’s key features are high material coefficient of performance (COP) and no global warming potential (GWP) in its use (Frenzel et al., 2015). Thus, the EU Commission and the US Department of Energy declared this technology as the most promising alternative to current vapor compression systems in 2016 (VHK and ARMINES, 2016; Goetzler et al., 2014). This unique material, originally developed for biomedical applications, already shows promising temperature differences of up to 40 K between hot and cold state, which corresponds to an adiabatic temperature change of around 20 K during loading or unloading (Frenzel et al., 2018). Elastocalorically optimized materials from early-stage research demonstrated a material COP of over 30 (Frenzel et al., 2015).
The development of elastocaloric devices has seen significant advancements since Takeuchi et al. introduced the first technological demonstrator in 2012 (Cui et al., 2012). Over the years, various system concepts and architectures have been realized in demonstration devices. In 2016, Qian et al. introduced a compression-based system using water as a heat transfer medium (Qian et al., 2016), while Tusek et al. presented the first regenerative tensile-loaded elastocaloric system (Tušek et al., 2016). Approaches utilizing thin metal foils for heat transfer via physical contact were proposed by Ossmer et al. (2016) and Bruederlin et al. (2018). That same year, Saarland University developed the first demonstrator capable of continuously cooling air directly without an additional heat exchange medium, as part of the German Research Foundation (DFG) Priority Program SPP 1599 “Ferroic Cooling” (Welsch et al., 2018a). In 2021, the Fraunhofer group led by Bartholomé introduced the “Active Elastocaloric Heatpipe” (AEH), combining compression-loaded elastocaloric materials with the heatpipe principle for efficient heat transfer (Bachmann et al., 2021; Ianniciello et al., 2022). More recently, in 2023, the University of Naples unveiled SUSSTAIN-EL, the first Italian rotary demonstrator for air conditioning (Borzacchiello et al., 2023; Cirillo et al., 2024). And CHECK TEMPERATURE, an electronic cooling device utilizing bending-loaded NiTi wires (Cirillo et al., 2023). Nonetheless, besides tension and compression loads, torsion load was investigated as well by Wang et al., in 2019 using twistocaloric cooling on material-level by applying torsional load on NiTi wires showing increased cooling efficiency compared to tension load (Wang et al., 2019). All these applications of EC system show that there is a high demand in international research in this topic and underlines the importance of further investigations.
The development of elastocaloric systems necessitates comprehensive modeling at both the material and system levels to optimize performance and efficiency. Material-level modeling focuses on understanding the thermomechanical behavior of SMAs including phase transformation kinetics, mechanical hysteresis and thermodynamics. Accurate models are essential for predicting the material’s response to cyclic loading and for designing materials with enhanced properties. In 1985 Achenbach and Müller presented a material model for SMAs including the thermodynamics on energy level and the kinetic theory with its microscopic properties (Achenbach and Müller, 1985). Further optimizations were done in years 1989 from Achenbach (1989) and 2001 from Müller and Seelecke (2001) resulting in the Müller, Achenbach and Seelecke (M-A-S) model, which serves until today as a baseline for material modeling of SMAs (Ballew and Seelecke, 2019).
System-level modeling, on the other hand, involves the integration of elastocaloric materials into practical cooling or heating devices. This includes the design of mechanical parts to apply and release stress, heat exchangers to manage heat transfer, and control systems to regulate the cooling or heating cycle. Numerical models simulate the performance of the entire system, accounting for factors such as heat transfer coefficients, system geometry, and operational parameters (Welsch et al., 2020; Welsch et al., 2018b).
Incorporating moisture considerations into EC system modeling is crucial for several reasons. The presence of moisture in the air can lead to condensation when the temperature in the system drops below the dew point. The latent heat released during condensation can impact the thermal dynamics of the system. Neglecting these effects may lead to inaccuracies in temperature predictions and, consequently, in the assessment of the system’s cooling capacity. Incorporating moisture-related latent heat effects into the energy balance equations ensures a more accurate representation of the system’s thermodynamics. Modeling moist air properties allows for the design of more efficient heat exchangers and the optimization of airflow rates to achieve desired cooling or heating performance. The significance of this topic plays a role in applications sensitive to environmental conditions such as in the automotive sector or in-house air conditioning.
This study presents a first approach to model condensation effects and implements EC system-level simulations. Current material and system models do not cover this phenomenon which motivates a first investigation.
In the first chapter the EC material model is explained. It covers the basic knowledge as well as in depth explanations on how to model the thermomechanical behavior of the EC material. This includes stress-strain relationship, latent heats, kinetics, and heat transfer mechanisms. In the following chapter the EC system-level model is explained followed by the Moist Air Model. This chapter is the focus of this study as it explains in detail which physics and mechanisms need to be covered in order to implement moist air effects into the model. Finally, the chapter Results and Discussion will show the simulations results, interpreting and discussing the presented figures. At the end The Summary and Outlook section will present an evaluation of the model, highlighting its strengths and limitations, along with recommendations for specific areas where further work is required.
This section describes the EC material model, which is characterized by its unique hysteretic mechanical response, considered quasi-elastic. The transformation between austenite and martensite phases occurs at different stress levels, with the gap between these stress levels defining the hysteresis width. The model also incorporates the material’s thermal response. During the austenite-to-martensite (A-M) transformation, latent heat is generated, causing the material to heat up, while the reverse martensite-to-austenite transformation (M-A) absorbs heat from the environment, leading to cooling. The model integrates these thermo-mechanical phenomena through a coupling mechanism.
For the EC material a constitutive equation is needed to provide the stress-strain relationship. Some assumptions are set. For a material that is a mixture of martensite and austenite, the total macroscopic strain
with the condition
with the elastic moduli
Equation 3 is the stress-strain relation for the used model which functions as a simple mixture-type constitutive equation.
Additionally, the effective elastic modulus
The effective elastic modulus will play a significant role modeling inner loops to account for an elastic unloading process in a mixed austenite/martensite phase state.
Experiments can be made to extract the parameters for the temperature dependency to feed the model. A standard isothermal tension load experiment can be repeated at different ambient temperatures. This way we can derive change in the transformation stress as a function of the temperature. Usually this is followed by a linearization since the working parameters are in the range of −20°C–80°C in extreme scenarios, in which the temperature dependency is almost linear (Schmidt et al., 2016). For common binary Nitinol alloys the temperature dependency of the transformation stress is around
There can be a disparity between the temperature dependency of the AM transformation and the MA transformation. In this model for simplicity, we set them to be equal. For a given temperature we can use Equation 6 to describe the transformation stress:
with the reference parameter of the transformation stress
with the hysteresis width
Here an assumption has been made to keep the temperature dependency of the austenite and martensite phase to be constant and equal.
The value of the latent heat released and absorbed by the material is commonly determined by either Differential Scanning Calometry (DSC) or Infrared Camera experiments (IR) (Louia et al., 2023). For simplicity we assume a constant latent heat of
The latent heat
The transformation probability for the transformation between the two phases austenite and martensite seeks a lot of attention.
In this study we consider the Helmholtz Free Energy (HFE)
Further the Gibbs Free Energy (GFE)
Applying stress to the material will change the energy minimum of the martensite phase and thus the relative energy difference of the minima. At a certain stress level, the transformation stress
where
To determine the kinetics or the transformation rate of a given transformation, we combine the thermally activated probability function with the actual volume fractions of the phases in Equations 13, 14:
The phase transformation between austenite and martensite causes the material to release or absorb latent heat. This process generates a temperature change in the material, which must be effectively transferred to the surrounding air or fluid medium. To model energy transfer mechanisms, we focus on the convective heat transfer. The rate of heat transfer by convection depends on the convective heat transfer coefficient
where
To calculate
The convective heat transfer coefficient is calculated by:
where
All thermal effects combined into one set of differential equations results in the following:
In Equation 18 the heat conduction with the thermal conductivity
The transition from modeling elastocaloric materials to simulating a complete elastocaloric system involves the integration of additional physical phenomena beyond the material’s intrinsic thermomechanical behavior. In particular, airflow dynamics play a crucial role in the overall system performance, as the air acts as a heat transfer medium between the elastocaloric material and its surroundings. To accurately capture this interaction, an additional set of governing equations is required to model the energy and mass transfer within the airflow. System-level simulations incorporate an air energy balance that accounts for heat conduction, advection and convection effects. The temperature evolution of the air
where
To numerically solve the coupled energy equations of the elastocaloric system, it is necessary to discretize the continuous partial differential equations (PDEs) in both space and time. Discretization transforms the continuous temperature, velocity, and moisture fields into values at discrete points (nodes) within a computational grid. Common techniques for spatial discretization include the finite difference method (FDM), finite element method (FEM), or finite volume method (FVM). Temporal discretization is achieved using explicit or implicit time-stepping schemes. For instance, the temperature gradient
Solving Equations 18, 19 simultaneously results in the overall EC system temperature distribution covering latent heats from the EC material and heat transfer interactions with the surrounding fluid. Figure 1 gives a schematic overview of the simulation results including discretization and energy balance of the air. It is a two-dimensional representation of the cross section of the EC system, however the calculations are based on the 1D model. With this EC system model, it is possible to perform parameter sweeps such as different fluid flow rates, varying rotation frequencies or changing the number of bundles in the system to optimize the output parameters of interest, namely, thermal powers or system COP. For example, if the fluid velocity or the rotation frequency is set too high, there is not enough time for the heat transfer to interchange temperatures resulting in a lower efficiency of the system. This optimization tool helps to find the best possible combinations of input parameters for given circumstances.
Figure 1. Schematic cross section of the temperature distribution on the fluid ducts (Welsch et al., 2018b).
This study will use the well-established EC system model to perform the simulations. A schematic machine design is shown in Figure 2. Nonetheless, another coexisting model will be implemented to cover the moist air effects and will be explained in the next section.
Figure 2. Schematic view of the mechanical framework for the elastocaloric device. For clarity, only eight SMA elements are shown and only one rotating disk without body is illustrated (Kirsch et al., 2017)
Moist air plays a significant role in the thermodynamic behavior of EC devices, particularly due to condensation phenomena and the release of latent heat. Understanding the fundamental properties of moist air is essential to accurately model the interaction between air, water vapor, and the EC material. This section provides an overview of key concepts such as the Mollier diagram, dew point temperature and latent heat of condensation, followed by a discussion on how these concepts can be incorporated into EC system-level simulations.
Moist air is a mixture of dry air and water vapor. The thermodynamic properties of this mixture are crucial for predicting condensation and latent heat release in elastocaloric systems.
The Mollier diagram (
• Enthalpy (
• Humidity ratio (
• Dew Point Temperature (
Figure 3. The Mollier diagram - specific enthalpy
The Mollier diagram allows users to visualize how the enthalpy and humidity of air change as it cools or heats. When the air cools at constant humidity, it eventually reaches its dew point, where water vapor begins to condense. This condensation releases latent heat into the system.
When air cools below the dew point, water vapor condenses, releasing latent heat of condensation (
where
The dew point temperature is directly related to the partial vapor pressure of water
with
To quantify the mass of water vapor that condenses when the air temperature drops below the dew point, a mass balance approach is used. The key objective is to compute the amount of water vapor
with V the given volume and
The moist air in the system can condense in different ways.
• in the air and thus fog formation
• at the chamber walls (inner and outer)
• directly on the EC material
Since the temperature must fall below the dew point, this phenomenon will only occur in the cold chamber of the EC system, which contains the cold EC material after unloading with a lower temperature than the surrounding air due to the heat transfer mechanism. This directly can lead to the assumption water droplets can form on the surface of the EC material. Model implementation wise, this means an effective heat transfer coefficient
Condensation as fog formation releases the latent heat directly into the air leading to a
It is less likely that the water vapor will condense at the chamber walls because it is usually built out of an isolating material to minimize the heat loss from the chamber to its surroundings.
In sum, fog formation and water droplet or water film formation are both dominant mechanisms occurring in the system, which are yet in need of an experimental investigation. Possible water droplet or water film formations on the surface of the EC material and their transport in system can be avoided by implementing a brush system or air pulse blow system in the transition zones between the hot and cold sections of the real-life device.
The condensation of water as fog formation is the main objective of interest in this study and will be implemented and further explained in the next section.
To integrate the effects of moist air into EC system-level simulations, the following thermodynamic principles are modified and applied in Equations 23-25.
1. Addition of
2. Condensation criteria; if
3. Moisture transport:
with the diffusion coefficient of water vapor
The addition of
This chapter presents the key results of this study and interprets their significance within the context of the research objectives. 5.1 outlines the simulation results obtained from the moist air model, while Section 5.2 provides a critical analysis of these results, highlighting their novelty and limitations.
While a whole parameter sweep was done, this study presents specific parameter combinations of interest. Given that a relative humidity (RH) of
In oceanic-continental climate regions relative humidities between 60% and 80% are common while temperatures may vary from around −10°C (winter) up to 30°C (summer). In this study we will cover condition combinations which seem most critical for condensation phenomena to occur as well as combinations to account for a certain critical winter case and summer case.
Table 1 shows the points of interest for a cold region including the dew point temperatures
As a reference EC system, we use the system-level framework presented in (Welsch et al., 2018b). It is the well-known rotatory system with equidistant bundles of EC wires aligned in the fluid chambers. For the material-level simulation a single crystal model was used, and the heat transfer medium is air. Specific material parameters can be read in (Welsch et al., 2020). Reported transformation stress values of ∼542 MPa and ∼423 MPa for
As a mid-sized EC device this set of parameters a capable of producing a temperature difference of
To directly match the localization of moist air simulation results with the EC system Figure 4 visualizes the EC system cross section of the parameters shown in Table 2:
In Figure 4 black arrows indicating air flow direction, big dots indicating bundle location and color scaling indicating temperature distribution (qualitative). The system rotates clockwise and thus operates in counter-flow mode. Top right is the outlet of the warm side, bottom right the inlet of the warm side, top left the inlet of the cold side and bottom left the outlet of the cold side. Between both top and bottom inlets and outlets is the transition zone between warm and cold side. In these transition zones the material is mechanically loaded and unloaded indicated by the black line. The model accounts for overflow/mixing between the warm and cold sides to better represent a real-life EC system in operation. The total incoming volume flow is divided, with 83.33% directed to the main chambers and 16.66% to the transition zones. Consequently, the volume flow rates in the transition zones equal 20% of the main chamber’s volume flow rates.
The moist air simulations follow the numerical calculations as described in the previous chapters. Figure 5 shows the moist air transport in this specific EC system at an environmental temperature of 15°C and a relative humidity of 80%:
The results show that the temperature drop in the cold chamber triggers the condensation as expected. Once the temperature drops below the dew point temperature, condensation criteria is met.
Transported mass of water vapor plays a significant role when it comes to quantifying the effect of condensation. Table 3 summarizes the results for the given parameter sweep in Table 1 regarding moist air stream
The moist air stream represents how much water vapor will be transported throughout the system over time. This value is highly sensitive to the volume flow rate of the EC system since it directly affects heat transfer, temperature difference and moist air transport velocity. The condensation generation rate
Not only is the moist air transport important, but the actual temperature distribution is also a parameter of interest as well. By comparing simulation results of the same parameter combinations with completely dry air vs moist air, we assess the importance of the consideration of moist air effects in EC system-level models. As an example, the same operating parameters were applied, but the temperature of the environment is set to 30°C to account for a warmer region. Increasing the temperature from 15°C to 30°C nets a higher saturation pressure of water vapor (following Equation 21) and thus a higher absolute humidity if the relative humidity remains constant. This means the air can hold more water vapor in the gas phase exponentially. Cooling down this warm air by the same amount of
Figure 6. Comparison dry air vs moist air: temperature distribution over time for the given EC system; RH = 90% and
Figure 6A follows the same operating parameters as Table 2 at higher temperature. The results show the expected heat transfer between EC material and fluid. However, comparing dry air vs. moist air temperature distribution, a certain difference can be observed, which implies that the condensation in that area occurred and released its latent heat to increase the temperature of the air. The temperature of the could output changes from
In Figure 7 path 1–2-3 shows how a temperature drop of
Figure 7. Simulation results shown in the Mollier diagram - connections 1-2-3 and 1–2′-3′ represent the two different scenarios.
Figure 8 provides a general overview of the impact of moist air under different ambient conditions, illustrating the expected energy loss with respect to the system’s temperature output in the cold chamber compared to dry air. Ambient temperatures of 15°C and 30°C were selected, with relative humidity levels ranging from 50% to 100%:
Figure 8. The effects of different ambient conditions on the thermal output of the system: 15°C (blue) and 30°C (red) at different relative humidity levels.
The key difference between the two selected ambient temperatures is the absolute humidity at a given relative humidity value. As expected, we see an increase in temperature loss for the 30°C ambient temperature due to a higher value of condensed mass of water, which leads to greater latent heat release from the condensation mechanism. For both scenarios we see the condensation phenomenon to have a considerable effect on the system starting between 70% and 80% relative humidity, reducing the efficiency by a factor of up to ∼0.89 and ∼0.79 at 100% RH (fully saturated moist air in the inlets) for 15°C and 30°C respectively. Since the system’s thermal power is directly correlated with the temperature difference between inlets and outlets of the system, those values are expected to show similar trends. The volume flow rate was set to
The simulations reveal significant insights into the moist air dynamics. This section discusses these results considering moist air transport and condensation in the EC system.
Both the inlet for the air in the warm chamber at an angle of 175° and the inlet for the air in the cold chamber at an angle of 355° have the input parameters of Table 1. Following the air flow of the warm chamber from an angle of 175°–5°, we see a steady decrease in relative humidity which is connected to the increasing temperature of air due to the heat transfer from the incoming loaded EC material releasing its latent heat. This means we see an increase in temperature along with a decrease of relative humidity. The absolute humidity
With the results shown condensation will likely occur for specific environmental conditions. Nonetheless Table 3 summarizes how much water vapor is transported over time. This includes the moist air stream solely from the air velocity and transportation of water vapor, and the condensation generation rate covering the condensed mass of water vapor over time. The sum of both values results in the overall moist air stream coming out of the EC system. Comparing these results with the moist air stream of around
The temperature analysis reveals important and interesting results. Looking specifically at the warm region case to exploit higher absolute humidity shows significant differences between dry air and moist air in the model. As the cold side is capable of cooling down the air below dew point, the latent heat of condensation is responsible for the change in temperature outputs of the cold outlet. The results show the significance of the moist air model pointing out that considering moist air effects will change EC system-level designs to account for condensation phenomena.
Moist air physics includes both condensation and evaporation mechanisms. While this study focused on the condensation part, evaporation was not included in the model.
This study presents a model to account for moist air dynamics for EC systems based on mass balance and condensation criteria. While the model has not yet been validated with experimental data, it helps to address discrepancies between experimental results and simulations from existing system-level models that neglect moist air effects. Every real-life system is exposed to environmental conditions even if they are less present in specific scenarios.
The primary goal of this work is to characterize and model moist air dynamics and condensation effects. A deeper optimization of both material-level and system-level models was not done. The results serve as a baseline for future EC device development, particularly for replacing less efficient and outdated technologies.
Applications sensitive to changing environmental conditions require a deeper understanding of how temperature or humidity affects the system. Future work should focus on validating the model using controlled experiments to refine parameters and ensure alignment with experimental data. These experiments should carefully control humidity and temperature and incorporate detailed observations of condensation phenomena, such as water droplets and layers, to capture localized heat transfer variations accurately. Further parameter studies will be done to account for the sensitivity of the system to fluid flow rate, relative humidities and temperature of incoming air. Furthermore, a deeper analysis of winter cases (−10°C–10°C) and summer cases (25°C–45°C) will be done to cover a broad spectrum of possible application scenarios.
The material used for this simulative study is currently the only EC material available in large quantities for building devices. With the high transformation stress levels in this tension case, it is not expected to show sufficient lifetime cycles. Partial loading, rather than full transformation, could help to extend the material’s lifetime. However, the drawback is a reduced latent heat output. Future studies should also focus on comparing new materials, particularly those optimized for EC applications. Additionally, experimental characterization should be performed to extract key parameters for the simulations.
The datasets presented in this article are not readily available because Confidential. Requests to access the datasets should be directed to DZ, ZGF2aWQuemltbWVybWFubkB1bmktc2FhcmxhbmQuZGU=.
DZ: Writing–original draft, Writing–review and editing. FL: Data curation, Resources, Writing–review and editing. FW: Data curation, Resources, Software, Writing–review and editing. PM: Project administration, Resources, Supervision, Writing–review and editing. SS: Conceptualization, Project administration, Resources, Supervision, Writing–review and editing.
The author(s) declare that no financial support was received for the research, authorship, and/or publication of this article.
The authors are grateful to Felix Welsch from the Intelligent Materials Systems Lab for their previous work on EC modeling and for continuous help and guidance. The authors acknowledge the use of OpenAI’s ChatGPT for language editing of this manuscript.
The authors declare that the research was conducted in the absence of any commercial or financial relationships that could be construed as a potential conflict of interest.
The authors declare that Gen AI was used in the creation of this manuscript. OpenAI’s GPT-4.
All claims expressed in this article are solely those of the authors and do not necessarily represent those of their affiliated organizations, or those of the publisher, the editors and the reviewers. Any product that may be evaluated in this article, or claim that may be made by its manufacturer, is not guaranteed or endorsed by the publisher.
Achenbach, M. (1989). A model for an alloy with shape memory. Int. J. Plasticity 5 (4), 371–395. doi:10.1016/0749-6419(89)90023-5
Achenbach, M., and Müller, I. (1985). Simulation of material behaviour of alloys with shape memory. Arch. Mech. Stosow. 37 (6), 573–585.
Alduchov, O. A., and Eskridge, R. E. (1996). Improved Magnus form approximation of saturation vapor pressure. J. Appl. Meteorology (1988-2005) 1, 601–609. doi:10.1175/1520-0450(1996)035<0601:imfaos>2.0.co;2
Bachmann, N., Fitger, A., Maier, L. M., Mahlke, A., Schäfer-Welsen, O., Koch, T., et al. (2021). Long-term stable compressive elastocaloric cooling system with latent heat transfer. Commun. Phys. 4 (1), 194. doi:10.1038/s42005-021-00697-y
Ballew, W., and Seelecke, S. (2019). Mesoscopic free energy as a framework for modeling shape memory alloys. J. Intelligent Material Syst. Struct. 30 (13), 1969–2012. doi:10.1177/1045389x19844330
Borzacchiello, A., Cirillo, L., Greco, A., and Masselli, C. (2023). A comparison between different materials with elastocaloric effect for a rotary cooling prototype. Appl. Therm. Eng. 235, 121344. doi:10.1016/j.applthermaleng.2023.121344
Bruederlin, F., Bumke, L., Chluba, C., Ossmer, H., Quandt, E., and Kohl, M. (2018). Elastocaloric cooling on the miniature scale: a review on materials and device engineering. Energy Technol. 6 (8), 1588–1604. doi:10.1002/ente.201800137
Cirillo, L., Greco, A., and Masselli, C. (2023). Development of an electronic circuit cooling system using elastocaloric effect: a FEM comparison among different configurations. Appl. Therm. Eng. 219, 119463. doi:10.1016/j.applthermaleng.2022.119463
Cirillo, L., Greco, A., and Masselli, C. (2024). The energy performances of an elastocaloric device for air conditioning through numerical investigation. Appl. Therm. Eng. 236, 121517. doi:10.1016/j.applthermaleng.2023.121517
Cui, J., Wu, Y., Muehlbauer, J., Hwang, Y., Radermacher, R., Fackler, S., et al. (2012). Demonstration of high efficiency elastocaloric cooling with large ΔT using NiTi wires. Appl. Phys. Lett. 101 (7), 073904. doi:10.1063/1.4746257
Frenzel, J., Eggeler, G., Quandt, E., Seelecke, S., and Kohl, M. (2018). High-performance elastocaloric materials for the engineering of bulk-and micro-cooling devices. MRS Bull. 43 (4), 280–284. doi:10.1557/mrs.2018.67
Frenzel, J., Wieczorek, A., Opahle, I., Maaß, B., Drautz, R., and Eggeler, G. (2015). On the effect of alloy composition on martensite start temperatures and latent heats in Ni–Ti-based shape memory alloys. Acta Mater. 90, 213–231. doi:10.1016/j.actamat.2015.02.029
Goetzler, W., Zogg, R., Young, J., and Johnson, C. (2014). Energy savings potential and RD&D opportunities for non-vapor-compression HVAC technologies. United States :Navigant Consulting Inc., prepared for US Department of Energy, 199.
Ianniciello, L., Bartholomé, K., Fitger, A., and Engelbrecht, K. (2022). Long life elastocaloric regenerator operating under compression. Appl. Therm. Eng. 202, 117838. doi:10.1016/j.applthermaleng.2021.117838
Kirsch, S. M., Schmidt, M., Welsch, F., Michaelis, N., Schütze, A., and Seelecke, S. (2017). Development of a shape memory based air conditioning system. Univ. Ilmenau.
Koutsoyiannis, D. (2012). Clausius–Clapeyron equation and saturation vapour pressure: simple theory reconciled with practice. Eur. J. Phys. 33 (2), 295–305. doi:10.1088/0143-0807/33/2/295
Louia, F., Michaelis, N., Schütze, A., Seelecke, S., and Motzki, P. (2023). A unified approach to thermo-mechano-caloric-characterization of elastocaloric materials. J. Phys. Energy 5 (4), 045014. doi:10.1088/2515-7655/acfb39
Müller, I., and Seelecke, S. (2001). Thermodynamic aspects of shape memory alloys. Math. Comput. Model. 34 (12-13), 1307–1355. doi:10.1016/s0895-7177(01)00134-0
Ossmer, H., Wendler, F., Gueltig, M., Lambrecht, F., Miyazaki, S., and Kohl, M. (2016). Energy-efficient miniature-scale heat pumping based on shape memory alloys. Smart Mater. Struct. 25 (8), 085037. doi:10.1088/0964-1726/25/8/085037
Qian, S., Geng, Y., Wang, Y., Muehlbauer, J., Ling, J., Hwang, Y., et al. (2016). Design of a hydraulically driven compressive elastocaloric cooling system. Sci. Technol. Built Environ. 22 (5), 500–506. doi:10.1080/23744731.2016.1171630
Schmidt, M., Ullrich, J., Wieczorek, A., Frenzel, J., Eggeler, G., Schütze, A., et al. (2016). Experimental methods for investigation of shape memory based elastocaloric cooling processes and model validation. JoVE J. Vis. Exp. 2 (111), e53626. doi:10.3791/53626-v
Tušek, J., Engelbrecht, K., Eriksen, D., Dall’Olio, S., Tušek, J., and Pryds, N. (2016). A regenerative elastocaloric heat pump. Nat. Energy 1 (10), 16134–16136. doi:10.1038/nenergy.2016.134
VHK and ARMINES (2016). Commision Regulation (EC) No. 643/2009 with regard to ecodesign requirements for household refrigeration appliances and Commission Delegated Regulation (EU) No. 1060/2010 with regard to energy labelling of household refrigeration appliances. Available online at: https://www.eup-network.de/fileadmin/user_upload/Household_Refrigeration_Review_TECHNOLOGY_ROADMAP_FINAL_20160304.pdf.
Wang, R., Fang, S., Xiao, Y., Gao, E., Jiang, N., Li, Y., et al. (2019). Torsional refrigeration by twisted, coiled, and supercoiled fibers. Science 366 (6462), 216–221. doi:10.1126/science.aax6182
Welsch, F., Kirsch, S. M., Michaelis, N., Mandolino, M., Schütze, A., Seelecke, S., et al. (2020). System simulation of an elastocaloric heating and cooling device based on SMA. InSmart Mater. Adapt. Struct. Intelligent Syst. 84027, V001T03A005. American Society of Mechanical Engineers. doi:10.1115/SMASIS2020-2262
Welsch, F., Kirsch, S. M., Michaelis, N., Motzki, P., Schmidt, M., Schütze, A., et al. (2018b). Elastocaloric cooling: system design, simulation, and realization. InSmart Mater. Adapt. Struct. Intelligent Syst. 51951, V002T08A005. American Society of Mechanical Engineers. doi:10.1115/SMASIS2018-7982
Keywords: elastocalorics, shape memory alloys, simulation, modeling, moist air dynamics, condensation, air conditioning
Citation: Zimmermann D, Louia F, Welsch F, Motzki P and Seelecke S (2025) Modeling moist air effects and shape memory alloys in elastocaloric devices. Front. Mater. 12:1559800. doi: 10.3389/fmats.2025.1559800
Received: 13 January 2025; Accepted: 04 March 2025;
Published: 24 March 2025.
Edited by:
Jaka Tušek, University Of Ljubljana, SloveniaReviewed by:
Žiga Ahčin, University of Ljubljana, SloveniaCopyright © 2025 Zimmermann, Louia, Welsch, Motzki and Seelecke. This is an open-access article distributed under the terms of the Creative Commons Attribution License (CC BY). The use, distribution or reproduction in other forums is permitted, provided the original author(s) and the copyright owner(s) are credited and that the original publication in this journal is cited, in accordance with accepted academic practice. No use, distribution or reproduction is permitted which does not comply with these terms.
*Correspondence: D. Zimmermann, ZGF2aWQuemltbWVybWFubkB1bmktc2FhcmxhbmQuZGU=
Disclaimer: All claims expressed in this article are solely those of the authors and do not necessarily represent those of their affiliated organizations, or those of the publisher, the editors and the reviewers. Any product that may be evaluated in this article or claim that may be made by its manufacturer is not guaranteed or endorsed by the publisher.
Research integrity at Frontiers
Learn more about the work of our research integrity team to safeguard the quality of each article we publish.