- 1School of Civil and Environmental Engineering, National University of Science and Technology, Islamabad, Pakistan
- 2Moscow Automobile and Road Construction State Technical University (MADI), Peter the Great St. Petersburg Polytechnic University, St. Petersburg, Russia
- 3Department of Buildings and Construction Techniques Engineering, College of Engineering, Al-Mustaqbal University, Hilla, Babylon, Iraq
- 4Department of Civil Engineering, College of Engineering, Qassim University, Buraydah, Saudi Arabia
- 5Department of Civil Engineering, National University of Sciences and Technology (NUST), Islamabad, Pakistan
- 6Civil Engineering Department, University of Engineering and Technology, Mardan, Pakistan
The construction industry consumes natural resources rapidly due to the increased population which requires the development of modern buildings. Therefore, several researchers pay attention to promoting sustainable construction. Among different types of waste, ceramic waste (CW) gained attention in concrete production which reduced the waste dumps from the ceramic industry and improved concrete sustainability. Although several researchers recommend the suitability of CW in concrete production. However, a detailed review is required which summarizes all the relevant information and provides compressive information on its impact on concrete performance. Recently, different researchers reviewed the suitability of CW in concrete. However, most researchers focus on strength properties while limited researchers focus on the durability and microstructure properties of CM concrete. Therefore, this review summarized the concrete durability and microstructure aspects with the substitution of CW. The durability performance of concrete was evaluated through percentages of voids, chloride penetration, water absorption, sulfuric acid resistance, shrinkage, freeze and thaw effect, corrosion resistance, and sulfate resistance. Furthermore, microstructure was reviewed through x ray diffraction, thermal stability, pozzolanic activity and scanning electronic microstructure. Also, the review evaluates the environmental and cost-benefits analysis of CW concrete through embodied energy (EE), carbon emissions (ECO2e), and costs. The findings indicate that CW can effectively replace 10%–15% of conventional materials in concrete, offering both environmental and economic advantages.
1 Introduction
The concept of sustainable building applies to a kind of management that assumes responsibility for creating an optimal atmosphere while taking into account ecological considerations and resource development (Du Plessis, 2007; Federico and Chidiac, 2009). Concrete is increasingly emerging as a fundamental construction material on a global scale, primarily due to its exceptional performance characteristics particularly high compressive strength (AL-Kharabsheh et al., 2022). However, the production of concrete has a detrimental influence on ecological systems due to its substantial use of natural resources (Althoey and Farnam, 2019; Smith et al., 2002; Islam et al., 2017; Scrivener et al., 2018). Therefore, researchers pay attention to searching for alternatives which easily accessible and promote sustainability (Liu et al., 2024a; Liu et al., 2024b; Zhao et al., 2024; Xi et al., 2024). In this regard, industrial waste materials are a valuable option (Jalal et al., 2013; Saikia and de Brito, 2009). Eco-friendly concretes, including geopolymer concrete, waste rubber concrete, recycled aggregate concrete, and those utilizing mineral and domestic waste, provide substantial benefits over traditional concretes in terms of energy reduction and environmental preservation (Wang et al., 2023). The industrial sector has seen substantial growth, leading to the generation of a considerable quantity of waste (Li et al., 2009; Lee et al., 2020; Ahmad and Zhou, 2023a; Ahmad and Zhou, 2023b). The dumping of these wastes has emerged as a critical concern due to their adverse effects on the environment (Lee et al., 2018; Fediuk and Yushin, 2015). The use of these industrial by-products within the construction sector, namely in the construction of concrete, can lower the environmental burden (Singh Shekhawat and Aggarwal, 2007; Vigneshwaran et al., 2019; Ahmad et al., 2022a; Golewski, 2023). In this research study, the focus is on CW utilization in concrete production. Ceramic waste (CW) from different sources is often disposed of in open landfills which imposes more pressure on available space and possibly releases pollutants throughout the degradation process (Jwaida et al., 2024). Reusing or recycling CW in construction (concrete) helps to save natural resources and lessen pollution to the environment. The environmental sustainability of utilizing ceramic waste (CW) powder as a cement replacement is supported by a life cycle assessment (LCA), which shows significant reductions in many adverse environmental categories (Dehghani et al., 2024) as cement is a major contributor of CO2 (Liu X. et al., 2024). The reduction of carbon emissions, energy usage, and raw material depletion is a noteworthy environmental aspect. Cement was replaced with CW powder to reduce the impact of concrete manufacturing on the environment and promote environmentally friendly building approaches. The Life Cycle Assessment (LCA) findings verify that the incorporation of CW powder into concrete not only facilitates waste management but also promotes environmental advantages. A significant quantity of CW is produced in the form of broken items (Siddique et al., 2019a). In the ceramic industries, waste products usually account for 15%–30% of the total throughout the production process (Vishnu and Singh, 2021). Ceramic waste disposal in open land (Figure 1) causes environmental pollution.
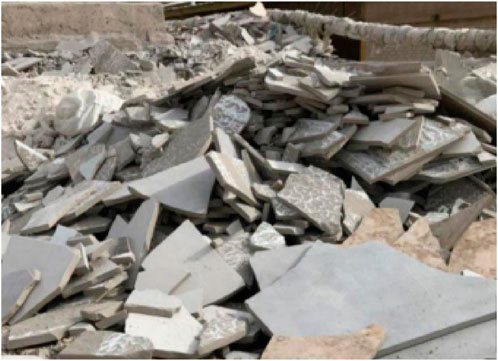
Figure 1. Ceramic waste (Shamsaei et al., 2020).
These waste materials contaminate the groundwater, the atmosphere, and the soil. Currently, there is a lack of recycling practices for the majority of CW. Consequently, the CW generated by industrial activities was disposed of by depositing it in designated pits or adjacent vacant spaces. The disposal causes significant hazards and necessitates the creation of substantial land space (Gautam et al., 2022). Therefore, CW has substantial environmental impacts (Hilal et al., 2022), necessitating the implementation of an alternate methodology to successfully address this issue. One option to solve this issue is the utilization of CW in concrete. The utilization of CW in concrete offers multiple benefits including waste dumps issues, preserving natural resources, and promoting sustainability. Furthermore, the utilization of CW in concrete also decreases the cost of concrete (Hilal and Hadzima-Nyarko, 2021) and protects the environment (Mansi et al., 2024). Therefore, the utilization of CW in concrete production attracts the attention of researchers. The researchers (Siddique et al., 2019b; Awoyera et al., 2018) indicate that the concrete compressive strength increased with the replacement of CW. Therefore, it is technically feasible and economically viable to use CW in the manufacturing of concrete. CW generally contains reactive constituents such as silica and alumina, which have the potential to undergo chemical reactions with cement, resulting in the formation of additional binding materials such as calcium silicate hydrates that enhance the strength properties of the concrete. The findings demonstrate a high level of performance, with satisfactory outcomes when substituting the ratio of CW as sand is up to 20% (Silva et al., 2010). The study conducted by researchers (Torkittikul and Chaipanich, 2010) revealed that the compressive strength of concrete containing 50% CW aggregate was comparable to the control specimens. A study (Zegardło et al., 2016) noted that the CW decreased the density of concrete due to lower porosity. A study (Ahmad et al., 2023) detected that the tensile strength of mortar improved with an increase in the proportion of crushed waste used as a substitute for natural aggregate. Additionally, it was found that when the control sample was combined with a 25% percentage of CW fine particles, the tensile strength exhibited an approximate 12% increase. The improved mechanical strength may be attributed to the greater surface area resulting from the rough surface texture of the CW aggregate. Moreover, this provides an adequate level of adhesion between the concrete ingredients (Medina et al., 2012).
The brief literature shows that CW has the potential to be utilized in concrete production. However, a detailed review is required which summarizes the relevant information and provides compressive information on its impact on concrete performance. Mostly the authors review (Ahmad et al., 2023) the strength properties of CW concrete and reported promising results in terms of strength. However, the durability aspect which is also important for the service life of the structure is missing.
Analyzing the correlation between mechanical characteristics and microstructure in heterogeneous materials and composites requires a comprehensive knowledge of these characteristics at macro-, meso, and micro levels (Stukhlyak et al., 2015). A study (Maruschak et al., 2023) also indicates that the fracture is generally studied through macro and micro levels. The macro level deals with the overall characteristics of concrete such as strength and durability. The meso level highlights the distribution and connection of pores or aggregates inside the concrete mix, which can significantly impact the concrete behavior under stress. Finally, the micro level examines the atomic or molecular structure, where certain bonding configurations and phases define the essential mechanical and durability characteristics of concrete. A study (Tang et al., 2022) also noted that knowing the interfacial bonding properties of repair materials and hydraulic concrete at macro, meso, and micro levels is important for improving concrete performance. This systematic method facilitates the organization of characteristics while simultaneously highlighting their physical and mechanical foundations. This method enables the finding of important relationships and helps in predicting how variations at one level (changes in microstructure) would affect characteristics at other levels (strength or durability).
Therefore, this review summarized the concrete durability aspects with the substitution of CW. The concrete’s durability performance was evaluated through several factors, including void percentages, chloride penetration, water absorption, shrinkage, freeze-thaw effect, corrosion resistance, and sulfate resistance. The study’s results indicate that the use of CW resulted in increased percentages of voids and chloride penetration. Additionally, it was observed that the replacement of CW led to a greater extent of shrinking. This may be linked to the ceramic aggregate’s tendency to absorb water, which is then released later, resulting in an enhanced shrinkage effect. The inclusion of CW strengthens the resistance of concrete against sulfate attack through its pozzolanic characteristics. This occurrence may be related to the generation of supplementary calcium silicate hydrate (CSH) gels, which enhance the construction of a compact microstructure and enhance the resistance against sulfate attack.
2 Methodology
The data search was done on academic databases such as Google Scholar, ResearchGate, and Scopus. To identify the related papers, relevant keywords such as ceramic waste-based concrete, sustainable concrete, durability of concrete, and other related terms such as chloride penetration, and microstructure analysis were used. The research article, thesis, books, conference paper, and review article focus on the suitability of ceramic waste-based concrete and study its impact on concrete durability performance were considered and reviewed. The exclusion criteria included papers that were not accessible in English and lacked adequate information on the durability of concrete. The authors searched the papers till the end and almost 90 papers were downloaded, and 77 relevant papers related to ceramic waste-based concrete were selected.
3 Durability methods
Table 1 highlights various methodologies used by researchers to predict the durability of concrete, including Ceramic Waste (CW). These methods examine key characteristics influencing durability under various environmental circumstances, The total void percentage of concrete was assessed according to the guidelines outlined in ASTM C 642 (Astm, 2006). A mortar specimen was used in the chloride test which was submerged in a 5% Na₂SO₄ solution. The evaluation of sulfate resistance included assessing changes in mass, size, and compressive strength of the specimens after exposure (Mohammadhosseini et al., 2020). A study (Heidari and Tavakoli, 2013) conducted the water absorption in accordance with ASTM C642. A study (Ghonaim and Morsy, 2023) conducted the acid resistance test using concrete cube specimens (150 mm) containing different proportions of ceramic dust which were first submerged in a 2% sulphuric acid solution after ordinary curing (28 days). Then specimens were tested in accordance with ASTM C267. Concrete shrinkage with different CW percentages was determined by a study (Jiménez et al., 2013) in accordance with the Spanish standard UNE 83831 which carefully recorded the dimensional variations of 40 mm × 40 mm × 160 mm specimens with time. A study (AlArab et al., 2022) tested the freeze-thaw resistance of concrete after 56 days, using a sample of 75 mm × 100 mm × 405 mm, in accordance with ASTM C666. Specimens sized 250 mm × 200 mm × 120 mm, each containing a ponding well on the upper surface, were casted for corrosion test (Siddique et al., 2019a). The vertical surfaces of the specimens were covered with epoxy paint. The anode and cathode terminals were connected with a 100 Ω resistor. The voltage between electrodes was recorded, and macro cell current was assessed in accordance with ASTM G109.
4 Results and discussions
4.1 Durability properties
4.1.1 Percentages of voids
The presence of voids or space impacts the concrete durability. The presence of voids provides routes for water, and deleterious chemicals to penetrate into the concrete structure, resulting in long-term deterioration. Research (Sun et al., 2022) indicates that most voids form around coarse aggregate. Voids, particularly those occurring around coarse aggregate particles due to inadequate compaction or incorrect water-to-binder ratios, affect the concrete density. The presence of air voids decreases the concrete resistance to external stress caused due to environmental influences, which increases the risk of chemical reactions such as carbonation or chloride ion infiltration, which results in corrosion of reinforcement and degradation of the concrete structure. Concrete loses strength due to the presence of air voids, with a 5% loss of strength for every 1% increase in air void volume. The proportion of voids in concrete samples with and without ceramic aggregate is shown in Figure 2. The proportion of voids increased as the percentage of CW aggregate increased. The production of voids in the concrete is marginally increased by the rough texture and angularity of raw ceramic aggregate. According to research, ceramic aggregate concrete bleeds more the conventional concrete (Siddique et al., 2019b). Bleeding in concrete indicates the movement of water to the concrete surface which results in the production of capillary voids after water evaporation, which further facilitates the creation of voids. According to research (Ben Nakhi and Alhumoud, 2019), the poorer connection between the recycled aggregate and the cement might lead to an increase in the number of voids. Capillary spaces develop in concrete when the bleed-out is higher. Additionally, when the water-to-binder ratio grew, the void increased. Concrete’s surplus water that was added after mixing eventually evaporates, leaving voids. The angular and rough surface texture of ceramic aggregates presents a problem for attaining sufficient workability and effective application of cement paste. A greater quantity of cement paste is necessary to completely cover the irregular surfaces of the ceramic particles. The angularity of the aggregate restricts the particles’ capacity for effective packing, resulting in air entrapment and increased void content. According to research (Zhang and Gao, 2019), porous concrete has a lower void content at a water-to-cement ratio of 0.25 compared to 0.3. The lower void content at a water-to-cement ratio is mainly due to the fact that a lower water-cement ratio produced less grout and cement coating on the surface of the coarse aggregate, leading to an increase in the void content of the concrete.
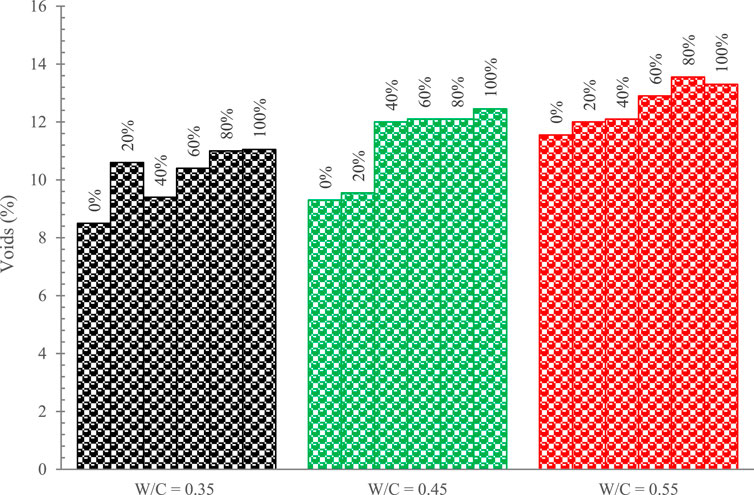
Figure 2. Voids of ceramic-based concrete (Siddique et al., 2019a).
4.1.2 Chloride penetration
The chloride penetration test findings provide important information into the degree of chloride infiltration and may be used to evaluate the potential risk for corrosion in steel reinforcement that is embedded inside a structure. The alterations in the mass of mortar samples subjected to NaCl solution after 18 months are shown in Figure 3. The findings demonstrate that the behavior of the cement and CW mortar samples, which increased the mass of the samples by absorbing chloride was identical. For cement and ceramic mortar mixes, the mass of the specimens raised by 3.8% and 2%, correspondingly, after the immersion time. Using waste ceramic in place of cement and sand significantly reduced the mass gain of the mortars when exposed to chloride. The pozzolanic character of the ceramic powder may be to blame for the decline in the mass loss of the CW mortar specimens. Ceramic waste (CW) generally includes active silica, during the hydration process it contributes to forming more CSH crystals (Lim et al., 2018). The CSH improved the binding ability of cement paste which led to more resistance to chloride penetration. Also, the micro-filling ability of CW particles which led to a more dense microstructure can contribute to improving the chloride ion penetration.
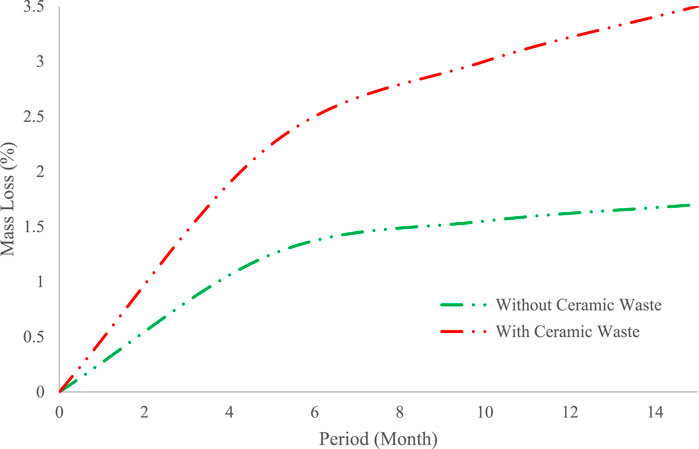
Figure 3. Mass loss of samples exposed 0.5% NaCl solution (Mohammadhosseini et al., 2020).
A study (Ma et al., 2019) concluded that the use of recycled concrete powder (RCP) in concrete leads to a reduction in chloride permeability. Notably, concrete specimens with a 30% RCP replacement ratio exhibit the lowest levels of chloride permeability. A study (Xu and Liu, 2019) also observed that the chloride ions permeability in recycled coarse aggregate concrete is seen to decrease by 13.6%. However, the recycled fine aggregate concrete shows slightly more reduction as compared to the recycled coarse aggregate concrete. The chloride ion permeability of recycled fine aggregate concrete shows a 15% reduction. The reduction in surface roughness of the aggregate, optimization of aggregate gradation, greater compactness of recycled concrete, and better chloride ion permeability are the reasons for the observed composite strengthening.
4.1.3 Water absorption
Figure 4 demonstrates the outcomes of the concrete water absorption with CW replacement after 90 days of curing. The water absorption dramatically decreased as the quantity of ceramic powder increased from 10% to 20%. However, with further addition of CW, the absorption rate gradually increased, eventually reaching 4.57% at a 40% concentration of CW. The findings indicate that 20% of CW exhibited the least amount of water absorption when compared to other combinations. The 90-day water absorption for concrete containing 10, 15, 20, 25, 30, and 40% CW decreased by 7.07, 9.09, 13.53, 12.72, 9.89, and 8.68%, respectively, as compared to the reference sample. This indicates that the pozzolanic action causes the concrete’s water absorption capacity to decrease. This behavior must be connected to the denser microstructure made possible by the pozzolanic activity of calcium hydroxide and powdered ceramic powder, which results in secondary CSH. Similar research suggested that enhanced microstructure in pozzolanic materials reduces water absorption (Ahmad et al., 2021; Ahmad et al., 2022b; Ullah et al., 2022). A study also reported that the substitution of ceramic dust at a 10% level resulted in the lowest water absorption percentage, which was 15% lower compared to the control mix. This reduction can be attributed to the combined effects of the pozzolanic reaction and the filling action of the ultrafine ceramic dust. However, when the percentage of ceramic dust exceeded 10%, the water absorption increased, leading to the rapid disappearance of its positive effect (Ghonaim and Morsy, 2023). The increase in water absorption at higher percentages of ceramic dust can be due to its higher porosity. The higher percentages of the porous particles (ceramic waste) in concrete can cause it to absorb more water which results in more water absorption. The higher water absorption of CW might be decreased by decreasing their particle size or adding more fine materials, but a detailed study is required.
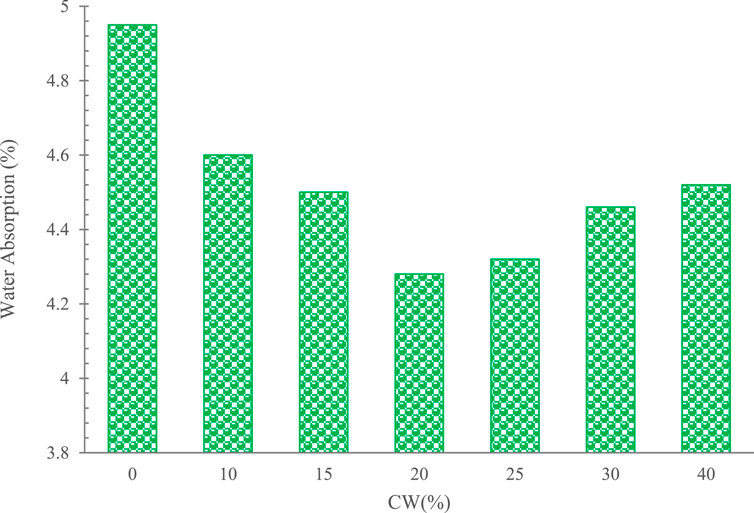
Figure 4. Water absorption of ceramic concrete (Heidari and Tavakoli, 2013).
4.1.4 Acid resistance
Figure 5 shows the compressive capacity of concrete with different substitution ratios of CW as cement replacement. The compressive test was carried out after 28 days of normal curing and the samples were subjected to a 2% sulfuric acid solution for 90 days. The purpose of this test was to evaluate the resistance of the concrete to acid attack and determine its strength under such conditions. The compressive strength of the control mixture decreased by 3.5% when compared to the cubes that were not subjected to an acidic environment. The experimental findings indicate that an increase in the proportion of ceramic dust as a substitute for concrete leads to a minor reduction in the compressive strength of cubes subjected to acidic environments, in comparison to the cubes without exposure to acidic conditions. The findings indicate that when concrete samples are subjected to acidic attacks, the compressive strength of cubes declined by 2% when 10% of the cement was replaced with ceramic dust. However, the control samples (without ceramic waste) show a 3.5% decrease in compressive strength which is more than the concrete samples made with a 10% substitution of CW as cement replacement. The use of CW as a filler has the potential to enhance the density of a material by filling voids and pores (Ahmad et al., 2023). The increase in density results in more resistance to acid attacks as the acid cannot easily penetrate into concrete.
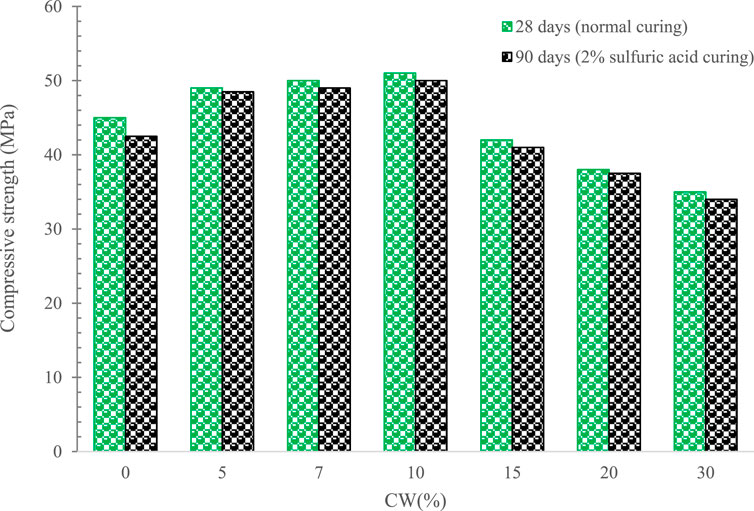
Figure 5. Sulfuric acid resistance (Ghonaim and Morsy, 2023).
Furthermore, scaling was more common in the reference concrete sample (Figure 6A). The more scaling in reference concrete causes a more significant deterioration of the top surface layers in reference samples indicating that reference samples show poor resistance to external environmental stressors. However, the CW concrete sample demonstrated markedly reduced scaling (Figure 6B), attributable to their superior durability performance and cohesive characteristics, which provide increased protection to the surface layers. A study (Mohit et al., 2021) also indicates that the compressive strength of mortar specimens declines when the internal spaces and pores inside the specimens expand. The mass loss rates of mortars consequently increase. Moreover, mortar specimens containing 5% and 10% ceramic powder have the lowest mass loss rates compared to others. Therefore, it suggests that ceramic powder effectively reduces the mass loss rate of mortar specimens during acid curing. The increased acid resistance of ceramic waste samples is due to pozzolanic reaction and filling voids among larger particles. Therefore, the improved internal structure of concrete with ceramic waste results in more resistance to acid.
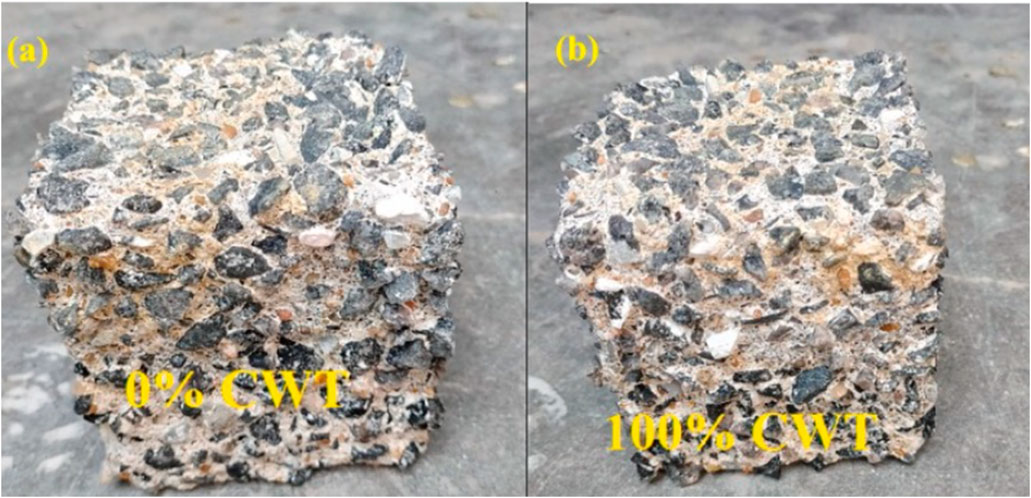
Figure 6. Acid resistance (HCL) (A) reference concrete and (B) 100% CW concrete sample (Meena et al., 2023).
Furthermore, the scanning electronic microscopy indicates that the specimen with 5% ceramic powder has a denser microstructure than the control specimen (Figure 7). The higher density of the sample with ceramic powder is due to the pozzolanic property which enhanced the mortar strength and durability. The ceramic powder interacts with calcium hydroxide to produce calcium silicate hydrate (C-S-H) and calcium aluminate hydrate (C-A-H) gels, which enhance acid resistance (Mohit et al., 2021). The reduced concentration of accessible calcium hydroxide (CH) decreases its reactivity with hydrochloric acid (HCl). Consequently, the use of ceramic powder alleviates the acidic and detrimental impacts of hydrochloric acid, resulting in enhanced durability under aggressive acidic conditions.
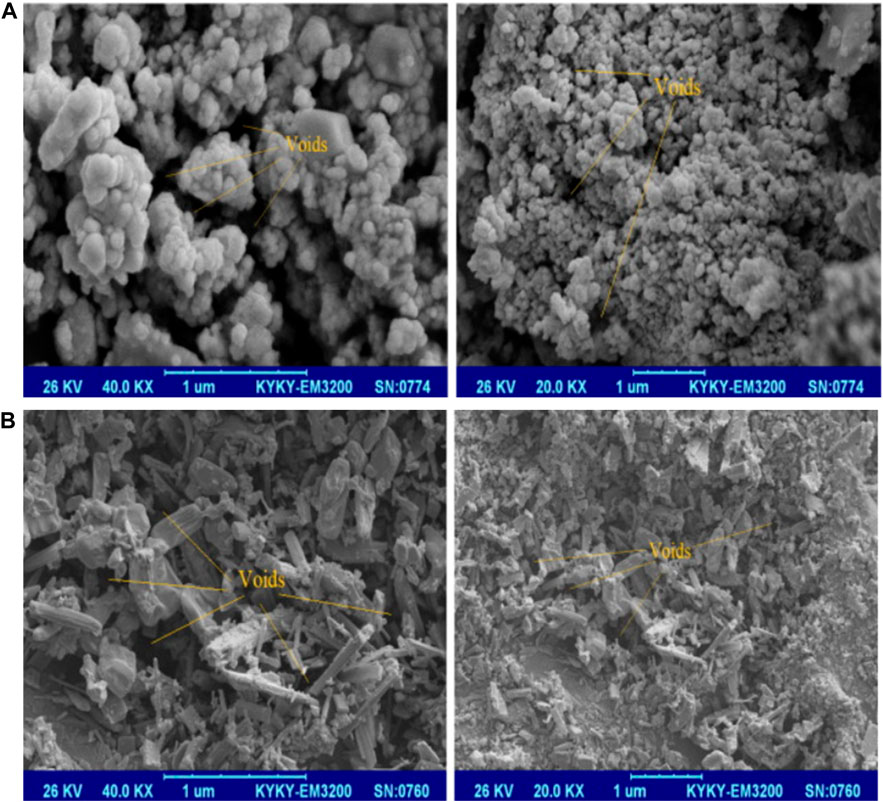
Figure 7. SEM of the sample exposed to HCL solution for 56 days (A) control and (B) 5% CW (Mohit et al., 2021).
4.1.5 Shrinkage
The shrinkage is shown in Figure 8 with various CW percentages. The findings indicate that the replacement ratios exceeding 10% often displayed mean values that were greater than the reference mortar. Concrete made with CW shows more shrinkage as compared to normal concrete. The CW particles significantly contribute to shrinkage and cracking because of their poorer bonding capacity with the cement paste as compared to the other types of aggregate. According to research (Miranda and Selmo, 2006), after 63 days of curing, shrinkage values for mortars with up to 25% fines content (i.e., finer than 75 microns) were greater than those for the reference mortar. Additionally, they noticed that mortars containing more ceramic blocks exhibited a little bit less shrinkage than the other mortars. Research (Silva et al., 2010) discovered a comparative rise in shrinkage after 80 days with the use of fine CW, although the variations were negligible at replacement ratios of 20%, 50%, and 100%.
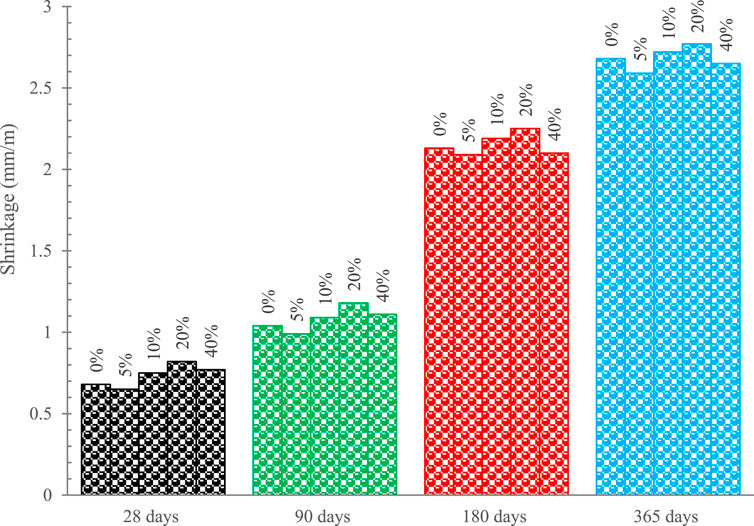
Figure 8. Shrinkage of ceramic mortar (Jiménez et al., 2013).
However, the exact impact of CW on concrete shrinkage will vary on numerous factors, involving the type and amount of CW used, the composition of the cement paste, and the curing conditions of the concrete. The use of CW may reduce shrinkage by providing more uniform particle packing and reducing the overall porosity of the concrete. Pozzolanic or cementitious materials such as fly ash improve the binding characteristics of the mixture due to the creation of secondary cementitious compounds (CSH) which leads to lower shrinkage. A study (Golewski, 2024) also indicates that fly ash improved strength. Furthermore, the addition of fibers is an effective method for mitigating the shrinking of ceramic waste concrete. The fibers bridge the possible development of cracks (Ahmad and Zhou, 2024) and distribute stresses within the concrete matrix which led more resistance to shrinkage induced cracking. Therefore, the durability and shrinkage characteristics of concrete made with ceramic waste improved.
4.1.6 Freeze and thaw effect
The combination of freezing and thawing temperatures is one of the primary causes of deterioration in the durability of concrete buildings in cold climates. This has a significant negative impact on the useful life of concrete structures in these areas (Baykal and Saygılı, 2012). The ceramic waste (CW) acts as filler material which leads to improved resistance to freezing and thawing. This is because CW particles can perform the function of filler material, thereby reducing the quantity of cement that is required in the mix. This can reduce the permeability of the concrete and improve its durability when subjected to conditions of freezing and thawing. Figure 9 shows an example of the relative dynamic elastic modulus for mixes of moderate strength after various freeze-thaw cycles. The relative dynamic elastic modulus significantly decreased with the addition of CW, dropping from 86 percent after 150 cycles. This could be connected to a dilution effect, which weakens concrete’s capacity to withstand degrading loads transported on by freeze-thaw cycles.
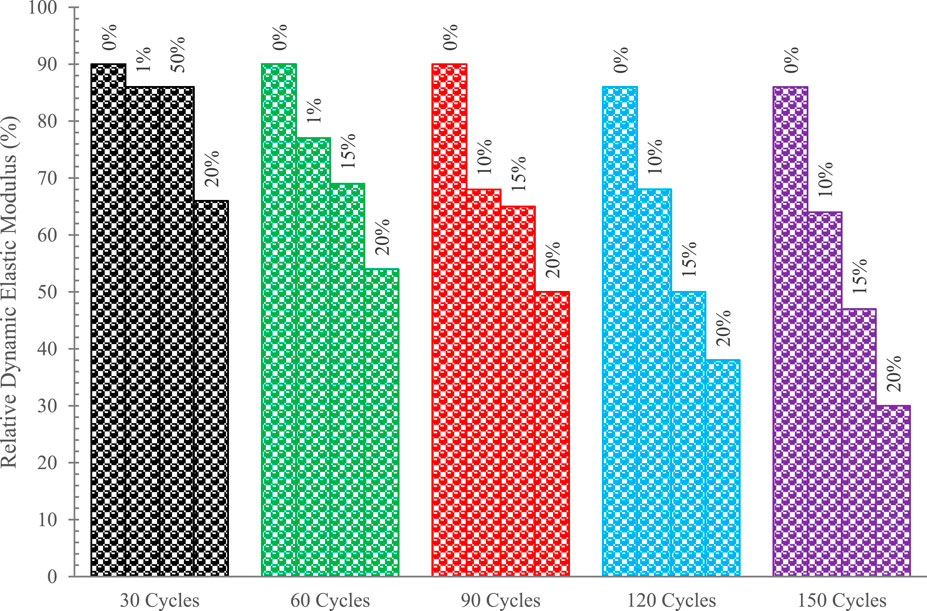
Figure 9. Freeze and thaw effect of ceramic-based concrete (AlArab et al., 2022).
The authors conclude that the impact of CW on freeze and thaw resistance is not clear, very limited study is available in literature and a more detailed study is required. Furthermore, freeze and thaw resistance can be improved with air entrained admixture. Therefore, incorporating air entrained admixture in ceramic waste-based concrete improves its freeze-thaw resistance in cold climates. The air-entraining agents provide pressure relief during expansion caused by freezing leading to more resistance, but a detailed study is required before practical use. The air entrained admixture in ceramic waste concrete will provide a more uniform and efficient use of ceramic waste in concrete exposed to freeze-thaw conditions particles in regions where the temperature is below freezing temperature. A study (El-Hawary et al., 2021) concluded that the use of varying quantities of recycled aggregates in concrete production results in different resistance to freezing-thawing cycles, with both low and high amounts exhibiting greater resistance compared to the average quantity of recycled aggregate. Furthermore, the study did not recommend the use of 50% recycled aggregates to get greater resistance in concrete. A study (Dehghani et al., 2024) also noted that the use of ceramic waste (CW) powder as a cement replacement in concrete mix leads to a denser matrix. This densification can result in a mix with fewer voids. Furthermore, even if not all the particles contribute to pozzolanic reactions, the finer particles of CW powder still enhance the packing density due to filling voids. This improved density can reduce permeability and increase durability. Therefore, a mix with a 30% replacement of cement by CW powder showed the best freeze-thaw resistance.
4.1.7 Corrosion resistance
Concrete constructions in coastal, urban, and industrial areas suffer significant damage from the corrosion of reinforcing steel. Steel corrodes, resulting in the highly expansive hydrated iron oxide, often known as rust. When the concrete breaks because of spalling, this expansion causes the internal pressure to build up. Numerous research have been conducted to stop the corrosion of reinforcing steel since this is one of the main causes of concrete degradation. The corrosion of steel rebars embedded in reinforced concrete components and buildings is a significant durability issue that may shorten their service life by allowing toxic chemicals and ions to enter a highly porous concrete matrix (Ji et al., 2015). In reality, throughout the last century, a large number of structural failures have been attributed to damage from the corrosion of steel rebars (Berrocal et al., 2016). A study recommends fiber-reinforced polymer to solve the corrosion problem of steel (Sun et al., 2023) but still not used commonly. Figure 10 shows the findings for microcell current measurements taken at various time intervals. Macrocell current levels greater than +10 A indicate the beginning of corrosion in the rebar. Throughout the whole testing period, mostly samples had values less than +10A. However, at 10 months of testing age, samples containing 0% and 20% CW had values of +11.15A and +10.32A, respectively. The ceramic concrete reveals less action for corrosion. According to research (Ghorbani et al., 2018), replacing cement at 10% and 20% with marble and granite waste showed very little degradation and a substantial increase in corrosion resistance, respectively. The greater concentration of CSH gel in the microstructure acts as an appropriate obstacle to prevent chloride ions from entering.
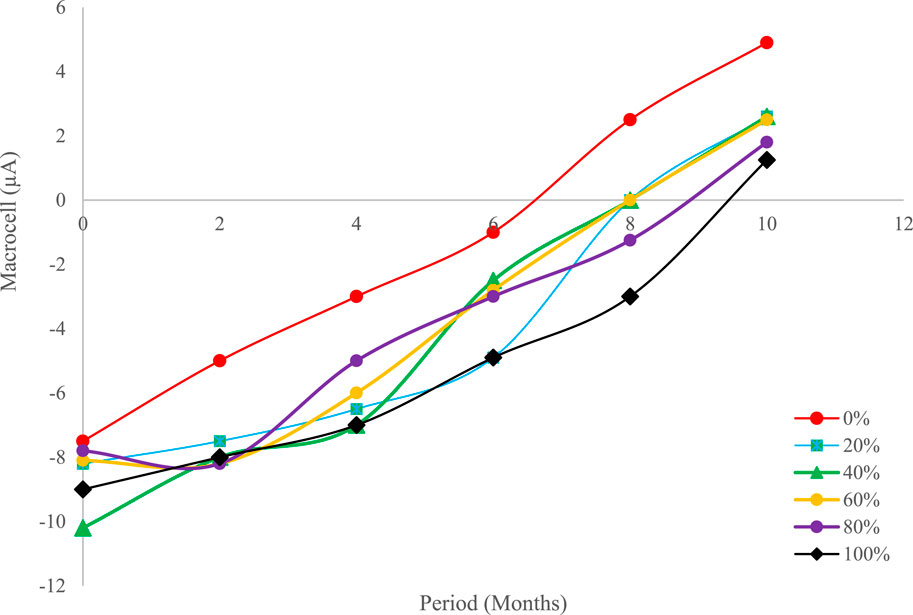
Figure 10. Macrocell of ceramic based concrete (Siddique et al., 2019a).
4.1.8 Sulfate resistance
Figure 11 shows the cement and ceramic mortar specimens in a 5 percent sodium sulfate (Na2SO4) solution after 540 days of immersion. The attack was seen as a white precipitate on the surface of both the cement and ceramic samples after the 540-day immersion period, however more slowly in the ceramic specimens. This was caused by the larger amount of lime that was leached and deposited in the cement specimens, which resulted in the formation of calcium sulfate (CaSO4). The surfaces of the ceramic mortar specimens have not changed, whereas considerable surface degradation was seen in the cement mortar specimen. Due to the sulfate attack, which occurs from the chemical interaction between the sulfate solution and Ca(OH)2 in the Portland cement, gypsum production was seen in the ceramic specimens. The surface of the specimen did not significantly alter in the ceramic mortar. This may be due to the ceramic powder’s pozzolanic properties, which produce additional CSH gels to create a thick microstructure and provide strong resistance to sulfate attacks.
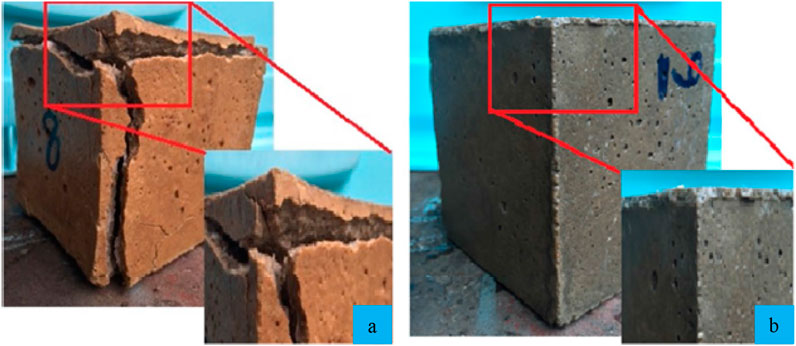
Figure 11. Specimens after exposure Na2SO4 (A) without CW and (B) with CW (Mohammadhosseini et al., 2020).
Figure 12 shows a strength comparison between specimens that were water-cured and those that were submerged in a Na2SO4 solution. All mix strength loss was thought to be a result of their extended immersion in the Na2SO4 solution. The strength loss was calculated as the variation in strength between the water-cured sample and those submerged in the solution. The compressive capacity of mortars is shown to decrease with increasing immersion time. The compressive capacity of the cement and ceramic mortars decreased by 41.1 and 16.8 percent, respectively, during the 18-month immersion period, relative to the strength of the samples before submersion. The breakdown of cement hydration products that results in the loss in strength might be linked to the interaction between sulfate and Ca(OH)2 that causes the drop in strength. A study (Bayraktar et al., 2024) noted that sulphate expansion was greatly decreased through the addition of waste polyester (WP) and substituting ceramic powder (CP) with cement. The findings indicate that a mix that included 20% CP, and 0.6% WP shows the least expansion (0.13%). This finding demonstrates the effective role of CP and WP acting in concrete to increase resistance to sulphates. Therefore, the durability of concrete in harsh conditions improved.
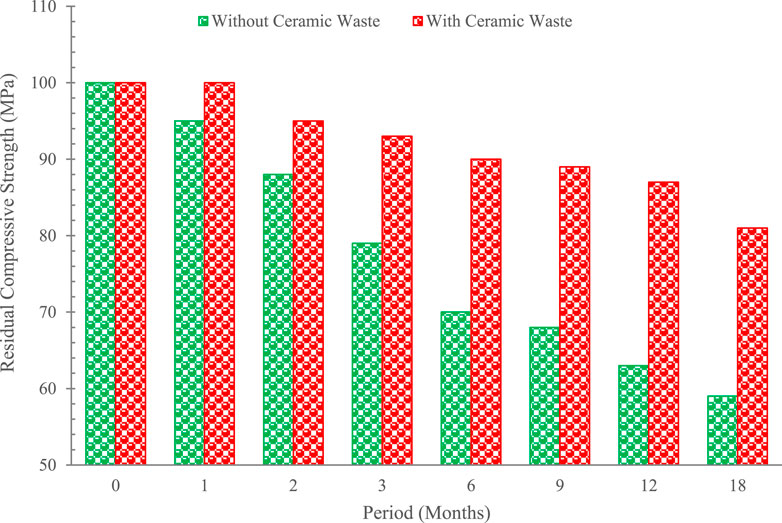
Figure 12. Residual compressive strength of sample exposed Na2SO4 (Mohammadhosseini et al., 2020).
Figure 13 shows the microstructure of the reference mixture (CP0WP0) when it was subjected to sulfate action. Different ettringite (Aft) structures were not detected, despite sulfate attacking the matrix. However, there was evidence of monosulfate (Afm). The deteriorating effects of the sulfate are apparently what led the matrix to display significantly larger cracks in comparison to normal hairline cracks.
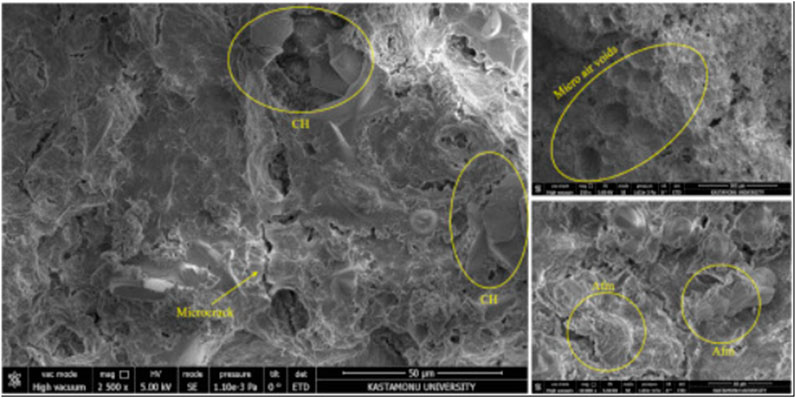
Figure 13. SEM of reference concrete exposed to sulfate attacks (Bayraktar et al., 2024).
The microstructure (scanning electronic microscopy) of the mix including 0.2% waste polyester (WP) and 10% ceramic powder (CP) is presented in Figure 14. The findings indicate that the mix (including 0.2% WP and 10% CP) when exposed to sulfate, had a 20% decrease in expansion compared to the reference mixture. This improvement shows that CP and WP increase the sulfate resistance of concrete.
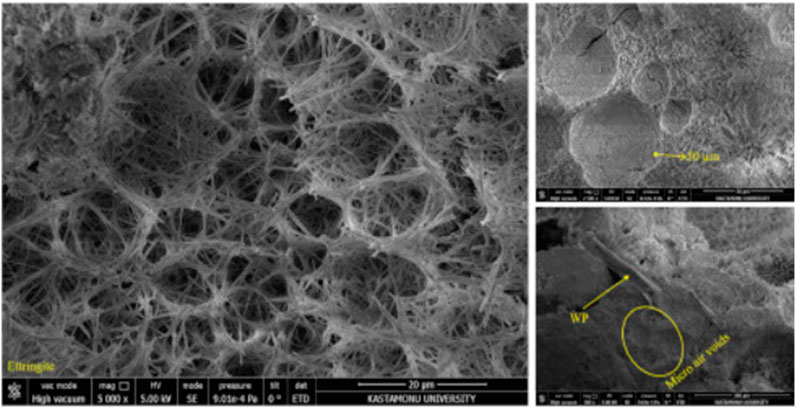
Figure 14. SEM of 10% CP and 0.2%WP concrete mix exposed to sulfate attacks (Bayraktar et al., 2024).
4.2 Microstructure analysis
4.2.1 Hydration heat test
Figure 15 shows heat release with various percentages of wall ceramic aggregate. The finding indicates that as the ceramic aggregate percentages increase, the total heat released during the exothermic process also rises. This indicates that more cement is reacting, and the cement hydration process has been prolonged. The finer or porous characteristics of the aggregate facilitate greater contact with water and cement particles, increasing the reaction in the initial stage. However, a longer hydration duration period was noted with ceramic waste aggregate particularly at higher aggregate percentages (20% and 30%).
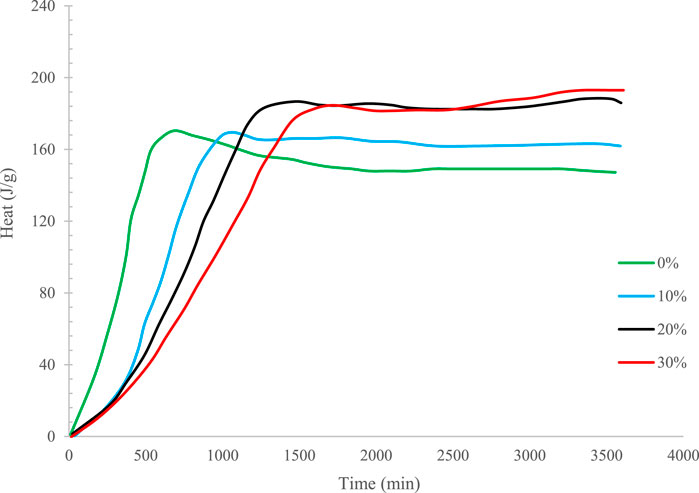
Figure 15. Heat release with various wall ceramic aggregates (Xu et al., 2023).
A study (Liu et al., 2024d) indicates that during the hydration process, the water supplied to the cement paste at the aggregate contact surface mostly comes from two sources: the adjacent cement paste and the aggregates themselves. The reduced water content in aggregates relative to the cement paste causes the cement paste in contact with the aggregates to undergo incomplete hydration during the hydration process, resulting in the creation of an interfacial transition zone (ITZ) on the aggregate surfaces. The ITZ typically presents greater porosity than the bulk cement pastes because of incomplete hydration. The ITZ is recognized as the most susceptible portion in the concrete cementitious materials, due to its reduced density and inadequate bonding, which decline strength. However, a longer hydration duration can improve durability due to the gradual formation of hydration products like calcium silicate hydrate (C-S-H). Furthermore, a longer hydration duration minimizes the possibility of micro-cracks resulting from fast early-stage reactions which enhances the long-term performance of the cement concrete. Therefore, the use of ceramic aggregates can extend the hydration period which imparts durability advantages and mitigates early thermal stress, making ceramic waste a viable material for environmentally friendly and resistant concrete applications.
4.2.2 X ray diffraction
Figure 16 illustrates the XRD patterns of hydration products for CW mixed cement paste on different days of curing. The findings indicate that the principal hydration products of the CW mixed cement paste are portlandite, ettringite, and calcite, in which portlandite is the predominant component. The Peaks of portlandite were detected at 2θ = 18.064°, 28.739°, 34.141°, and 47.172°, while ettringite phase peaks were noted at 2θ = 22.979° and 35.216° for all mixed made with different combination of CW and cement. A reduction in portlandite peak intensity corresponding to the increased percentages of CW was noted which suggests that the presence of CW consumes calcium hydroxide (CH). This decrease may be ascribed to the pozzolanic reaction which produced more cementitious compounds such as calcium silicate hydrates (Chen et al., 2022). Moreover, the XRD also reveals a higher silica (SiO₂) concentration in CW. Also, calcite peaks appear at different curing ages (7,28 and 56 days) due to the interaction of CO₂ with the paste to generate CaCO₃. The analysis also indicates calcium silicate peaks at 56 days, corresponding to unhydrated cement clinkers. Finally, the authors indicate that no more crystals were generated in the paste due to the presence of CW.
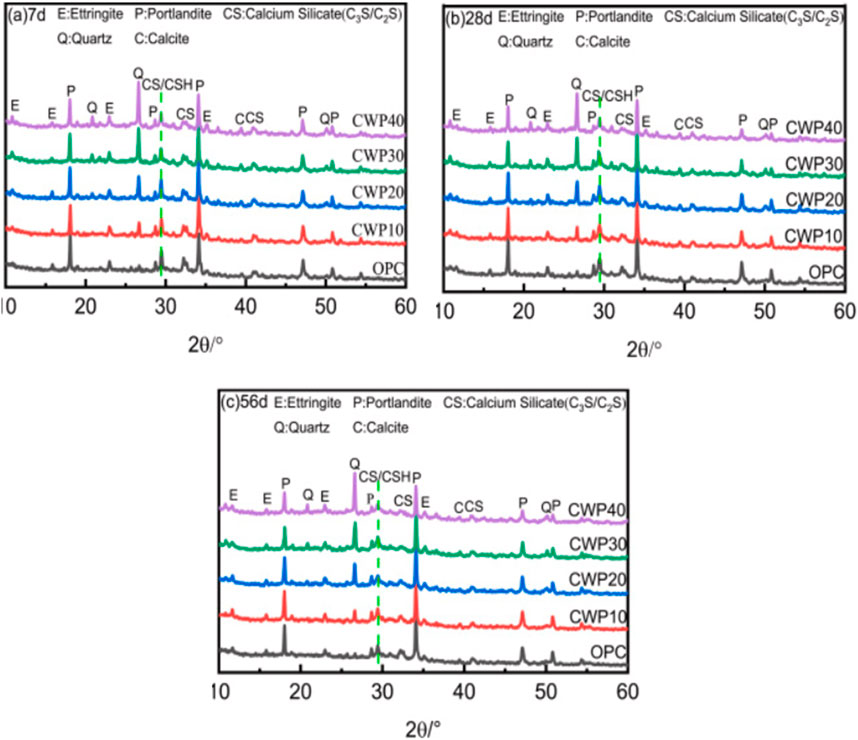
Figure 16. XRD of ceramic waste powder (Chen et al., 2022).
4.2.3 Thermal stability
The ability to understand the mechanism of cement paste deterioration at elevated temperatures is dependent upon the thermal stability of CSH (Rodriguez et al., 2017) which is the main strength contributing component of cement paste. Figure 17 shows the thermal stability of concrete with the substitution of red and white CW. It can be noted that the concrete with different percentages of CW exhibits several inconsistencies in the outcomes of the blended cement paste, specifically in the comparison between the red and white CW. Samples which include red ceramics have a noticeable dual pattern with peaks seen at temperatures ranging from 130°C to 220°C during a 28-day curing period. This range of temperature 130°C–220°C denotes the significant thermal stability of concrete as many important reactions take place at this temperature. This range of temperature (130°C–220°C) signifies the breakdown of calcium silicate hydrate (CSH). The CSH gel contains binding ability and considerable impact on the strength of concrete. The breakdown of CSH gel causes to release of water, as well as the decomposition of ettringite. The mechanical characteristics of cement pastes deteriorate due to an increase in porosity caused by changes in the morphology and nanostructure of CSH following exposure to high temperatures. Furthermore, it should be noted that this specific temperature range (130°C–220°C) is also associated with the breakdown of ettringite, which is a chemical generated during the hydration process of cement. The presence of ettringite plays a crucial role in the initial strength development of concrete. Nevertheless, when exposed to elevated temperatures, the concrete initiates a process of decomposition, potentially reducing its overall performance. The red ceramic exhibits a greater generation of ettringite as a result of its higher concentration of Al2O3 compared to the white ceramic (Lasseuguette et al., 2019).
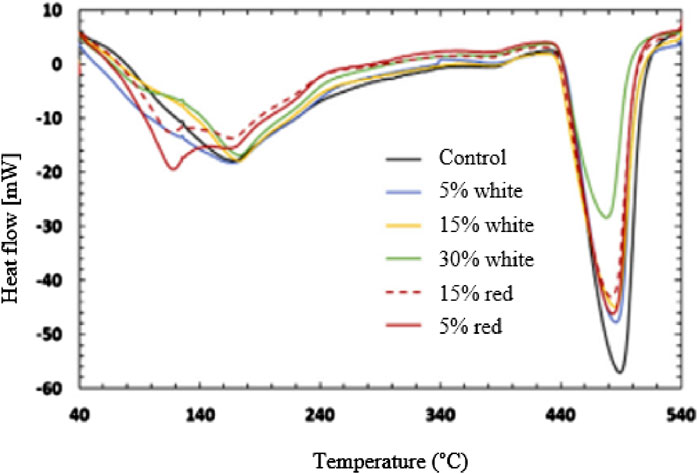
Figure 17. Thermal stability of CW concrete (Lasseuguette et al., 2019).
4.2.4 Pozzolanic reaction
A researcher (Chen et al., 2022) quantitatively determined the calcium hydroxide (CH) percentages from the TGA curve in OPC and CW mixed with cement pastes (Figure 18). The findings demonstrate that relative to OPC, the CH concentration in CW cement pastes declines at 7, 28, and 56 days when the percentages of CW increase. At 7 days, the CH content in OPC was 9.85%, but the CH content in CW powder with cement pastes decreased by 12.59%, 18.78%, 29.04%, and 34.01%, respectively, with increasing CW powder content from 10%, 20%, 30%, and 40% respectively. The CH concentration at 56 days in the cement pastes decreased significantly at 40% CW. The CH concentration in comparison to OPC at 56 days decreased by 13.37%, 33.99%, 49.72%, and 56.60% for 10%, 20%, 30% and 40% CW respectively. The decrease in CH percentages with time and with CW percentages is due to the pozzolanic reaction which consumes CH and produces calcium silicate hydrates.
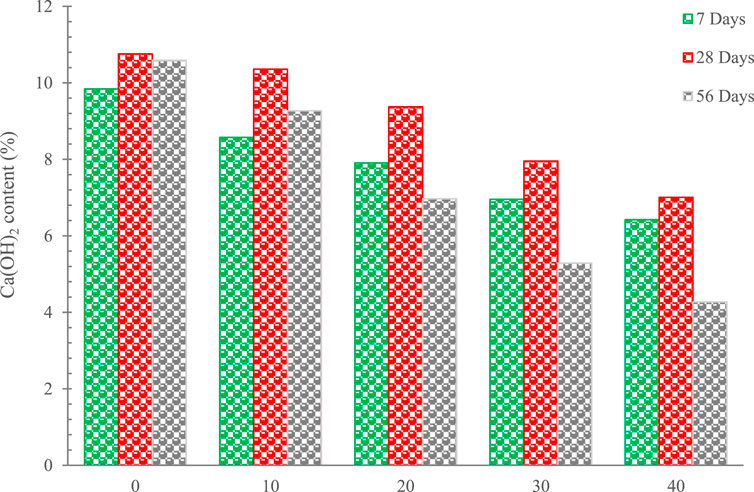
Figure 18. Ca(OH)2 percentages (Chen et al., 2022).
A study (Weng et al., 1997) noted that the pozzolanic reaction starts approximately within 3 days and becomes more significant with time (after 7 days). The combination of silica fume and fly ash accelerates early reactions, significantly decreasing calcium hydroxide (CH) levels within 12 h. Silica fume rapidly utilized calcium hydroxide due to its strong reactivity. However, fly ash has a slower reactivity as compared to the silica fume which enhanced long-term strength (after 7 days). The resultant mixture enhances the strength and durability of concrete by facilitating the production of calcium silicate hydrate (CSH).
4.2.5 Scanning electronic microscopy (SEM)
Figure 19A depicts a specimen without any ceramic dust and Figure 19B represents specimens with a 10% substitution of cement by ceramic dust. It can be noted that the samples without CW show the existence of pores. The presence of pores adversely impacts the concrete durability and strength. Harmful chemicals or water can easily enter the concrete through these pores which causes deterioration of concrete. However, according to the study (Ghonaim and Morsy, 2023), samples made with 10% substitution of CW exhibit an improvement in the pore structure in concrete (Figure 19B). The improvement in the pore structure might be due to micro-filling and pozzolanic activity. This finding provides evidence that the presence of 10% ceramic dust significantly influences the development of additional hydration products, leading to the strengthening of cement binder characteristics. Consequently, this contributes to the improvement of compressive strength and durability.
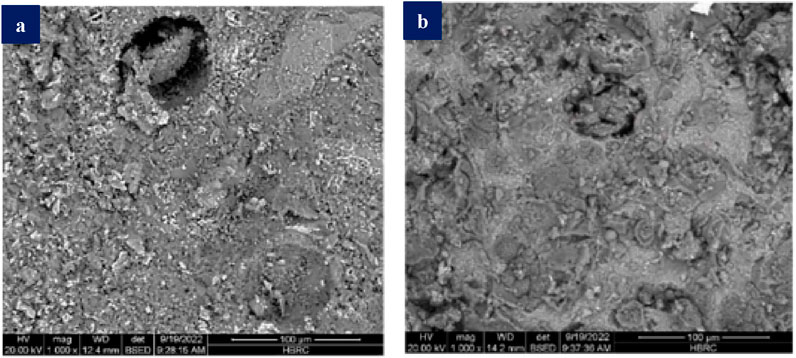
Figure 19. SEM of (A) without CW and (B) 10% CW substituted as cement replacement (Ghonaim and Morsy, 2023).
According to research (Siddique et al., 2019a), it has been shown that the angularity and rough surface texture of ceramic aggregate contribute to an increased need for cement paste to adequately cover the surface area. Consequently, this leads to the formation of additional voids within the concrete which decreases the service life of the concrete structure. However, the pozzolanic activity of the ceramic aggregate mitigates this tendency by facilitating the formation of hydration products that either maintain or enhance the strength capacity. However, a study noted that due to the pozzolanic properties of CW, the tensile strength of ceramic mortar after 7 days was lower compared to that of cement mortar (Ariffin et al., 2015). The decline in early strength was due to the fact that the pozzolanic materials gained strength at a slow rate as compared to the hydration of cement. A gradual reaction may result in denser and more durable concrete because the reaction products have more time to fill in the holes and cracks. Furthermore, it also decreases the heat which evolved during the hydration of cement. The decreased heat of hydration reduced the shrinkage cracks. The decrease in shrinkage cracks results in more durable concrete.
Furthermore, Figure 20 demonstrates scanning electron microscopic (SEM) images of concrete made with 10% and 50% ceramic tile aggregate respectively. The findings indicate that increasing the percentages of tile aggregate leads to the interfacial transition zone (ITZ) between the natural and tile aggregates becoming less pronounced. The 10% ceramic tile aggregate (Figure 20A) shows parallel cracks in the interfacial transition zone between the tile and natural aggregates suggesting a diminished connection at low percentages of tile which potentially results in worse mechanical performance, including lower strength and increased porosity.
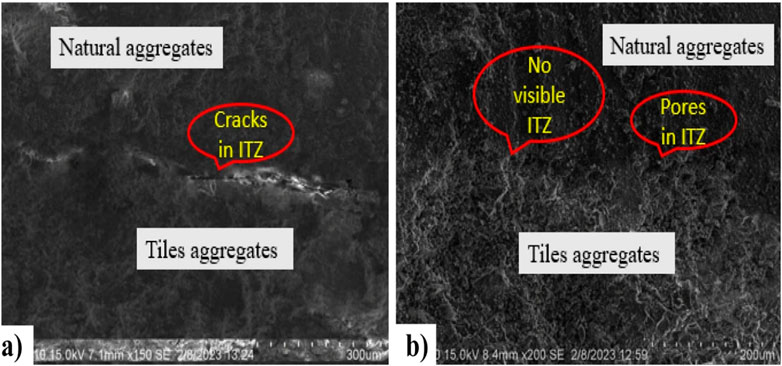
Figure 20. (A) 10% and (B) 50% ceramic waste aggregate (Paul et al., 2023).
However, the study (Paul et al., 2023) also suggests that the ITZ can be improved with pozzolanic materials such as fly ash and silica fume. Pozzolanic materials interact with calcium hydroxide (CH) in the cement hydration matrix, improving the interfacial transition zone by decreasing porosity and refining the microstructure, consequently strengthening the bond between aggregates and the adjacent cement paste. The enhancement of the ITZ may alleviate some negative effects linked to the tile aggregate content, including cracks seen in lower tile proportions but detailed experiments are required. Also, Figures 21, 22 illustrate the SEM and EDX of the control mix, 50% CW as fine aggregate, and 30% CW as cement and 50% CW as fine aggregate. The findings indicate that the control mixture consisted of unreacted and partly reacted particles, and its microstructure was comparatively loose, with many voids. Furthermore, the EDX analysis also demonstrates a higher Ca/Si ratio in the control mix indicating less efficient consumption of calcium hydroxide compared to the other mixtures.
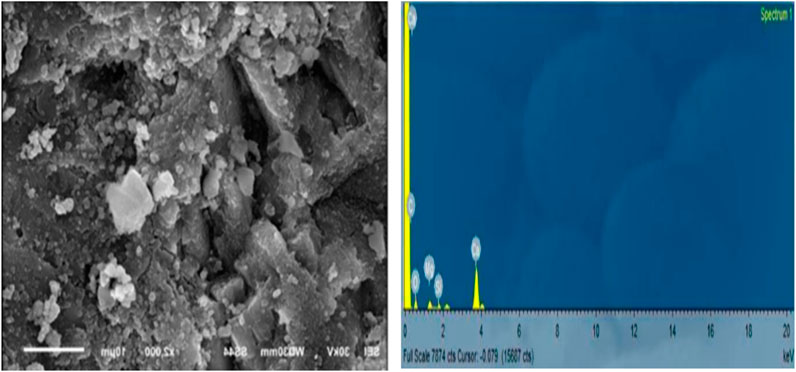
Figure 21. SEM and EDX of control mix (Elemam et al., 2023).
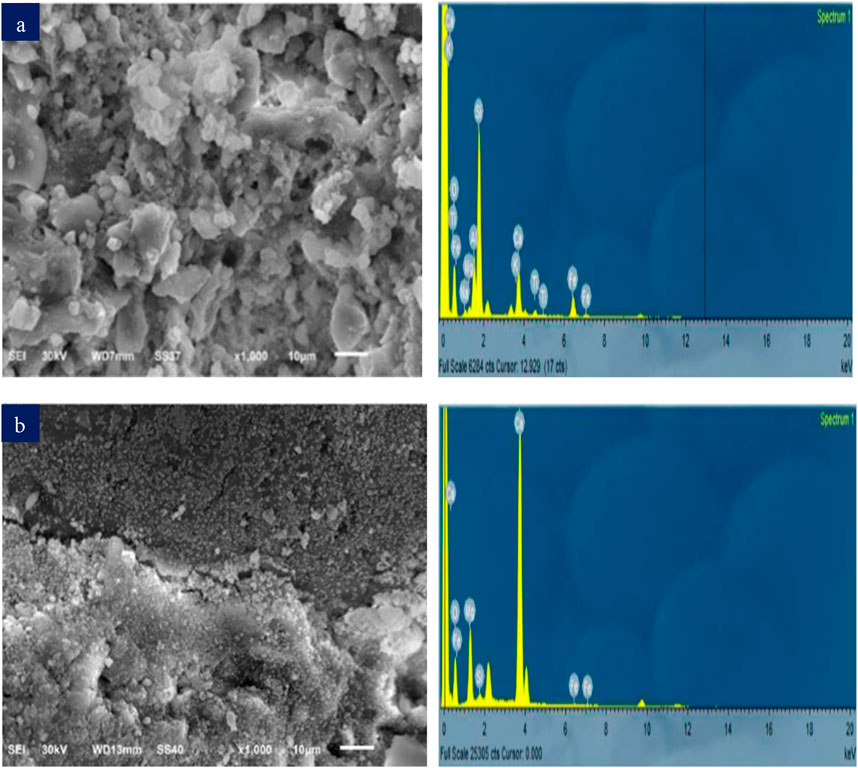
Figure 22. SEM and EDX (A) 50% CW as fine aggregate and (B) combine 30% CW as cement and 50% as fine aggregate (Elemam et al., 2023).
Figure 22A demonstrates that substituting sand with 50% CW produced a denser surface with reduced porosity. Nevertheless, the specimen including 30% CW and 50% CW (Figure 22B) exhibited a greater number of partly reacted and unreacted particles. Increasing the CW as cement percentages adversely affects the production of C-(A)-S-H gels, resulting in a higher quantity of unreacted particles, such as quartz, and partly reacted gels, such as mullite (Huseien et al., 2020). The EDX analysis also indicates that the mix of 50% CW as fine aggregate shows a lower Ca/Si ratio while the combined mix of 30% CW as cement and 50% CW as fine aggregate demonstrated a greater Ca/Si ratio. The analysis demonstrates that the utilization of calcium hydroxide lowers the Ca/Si ratio, hence improving the micromechanical characteristics of the hydrated calcium silicate phase. The reduced Ca/Si ratio in the case of 50% CW as fine aggregate indicates enhanced development of calcium silicate hydrate (C-S-H) gels, which enhances the mechanical strength and durability of the concrete.
5 Environmental and cost benefits
The two main parameters for assessing the sustainability of concrete are embodied carbon dioxide emissions (ECO2e) and embodied energy (EE). These measurements highlight the environmental aspects of concrete production, with ECO2e concentrating on the carbon footprint and EE evaluating the aggregate energy consumption related to material procurement, manufacture, and transportation. The concrete mix made with 40% ceramic waste (CW) as fine aggregate shows an EE value of 2,890.77 MJ/m³ as compared to other mixes (Figure 23). The decrease in EE is attributable to the replacement of fine aggregate with ceramic waste. The use of CW as a concrete ingredient considerably decreases EE. Conversely, increases in EE values of 2919 MJ/m³ and 2,922.38 MJ/m³ were observed for the reference concrete and concrete made with 100% CW as fine aggregate respectively.
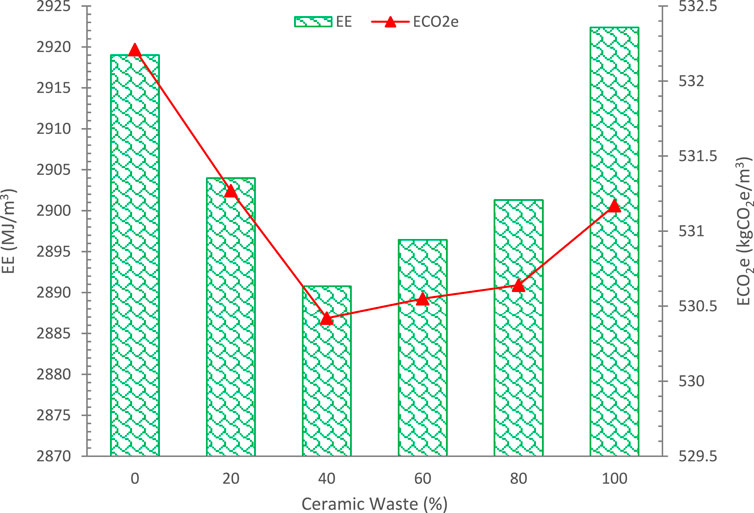
Figure 23. Environmental benefits analysis of ceramic waste concrete (Meena et al., 2023).
The increase in EE consumption in reference concrete and concrete made with 100% CW as fine aggregate is due to the increased ratio of natural fine aggregate and the increased dose of superplasticizer needed for the reference concrete and concrete made with 100% CW as fine aggregate mix. A similar trend is noted in the ECO2e emission with different ceramic waste concrete samples. Cement contributes significantly ECO2e emissions among all raw materials used in concrete production, followed by fine aggregate, coarse aggregate, and superplasticizer. However, CW does not contribute to ECO2e emissions. Therefore, the substitution of CW in concrete results in more sustainable and eco-friendly concrete alternatives. The cost analysis for the concrete made with different percentages of CW as fine and cost per MPa of compressive strength is shown in Figure 24. The findings indicate that the concrete made with 80% CW shows the most cost-effective option, providing an overall cost decrease which is 15% lower relative to the control mix. Furthermore, the mix made with 60% CW mix revealed the lowest cost per cubic meter for compressive strength (28 days), regardless of the increased expense of fine aggregate. Therefore, the use of ceramic waste CW as a fine aggregate significantly contributed to the reduction of cost, ECO2e, and EE.
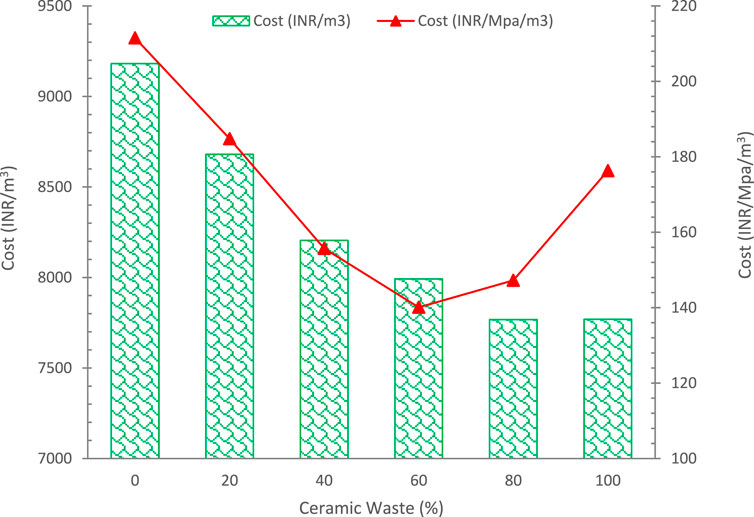
Figure 24. Cost analysis of ceramic waste concrete (Meena et al., 2023).
6 Conclusion and recommendation
This review summarized the durability aspects of concrete with the substitution of ceramic waste. The durability performance of concrete was evaluated through percentages of voids, chloride penetration, water absorption, sulfuric acid resistance, shrinkage, freeze and thaw effect, corrosion resistance, and sulfate resistance. Furthermore, the microstructure, environmental, and cost benefits of concrete made with the substitution of CW were also reviewed. Based analysis, the conclusions are:
• Different researchers reported different properties of concrete with substitution CW (some reported that CW increased concrete performance while some reported that CW decreased concrete performance). The different behaviors of CW in concrete may be due to variations in particle size, chemical composition, and color. However, no information is available that detects the exact parameter which causes variation. Therefore, the authors recommend future research to detect the exact factors that cause variation.
• Voids and chloride penetration increased with the substitution of CW. However, the decrease was minor, and concrete with CW can be suitable for normal strength structure.
• An increased shrinkage was observed with the substitution of CW due to the water absorption of ceramic aggregate which is released at a later age and causes more shrinkage. However, the use of supplementary materials like shrinkage-reducing admixtures and the implementation of enhanced curing techniques can improve the shrinkage resistance but a details study is required before practically used.
• Ceramic waste in concrete can improve freeze-thaw resistance by improving matrix density and reducing permeability, but limited studies exist in the present literature. Therefore, more detailed research is needed before practically used.
• Concrete sulfate and sulfuric acid resistance are enhanced with CW due to the pozzolanic nature of the CW, which creates more CSH gels to create a thick microstructure and provide strong resistance to sulfate and sulfuric acid attack.
• The XRD analysis reveals that including CW in cement paste promotes pozzolanic reactions, resulting in reduced portlandite content and the production of supplementary cementitious compounds with time.
• Thermal stability analysis indicates that the CW improved the thermal stability of CSH gel which is the main strength contributing factor. Therefore, concrete made with CW shows better performance as compared to the reference. However, non-linear behavior was observed which might be due to variations in chemical composition, color, and particle size. Therefore, the study recommends more detailed studies before applying practically.
• Scanning electronic microscopy depicts that the internal structure of concrete improved with the substitution of CW. The improvement might be due pozzolanic and micro-filling action of CW particles.
• The environmental and cost analysis indicates that CW as a fine aggregate in concrete significantly reduces embodied energy (EE), carbon emissions (ECO2e), and costs.
• The utilization of CW in concrete not only solves waste disposal issues but also promotes sustainability. Despite a detailed search, the authors did not find practical case studies or examples in the existing literature on CW concrete. Therefore, the review proposes a future study to investigate and record real-world uses of ceramic waste concrete to address this gap.
Author contributions
JA: Writing–original draft. MS: Conceptualization, Supervision, Writing–review and editing. AM: Conceptualization, Supervision, Writing–review and editing. WA: Supervision, Validation, Writing–review and editing. IK: Writing–review and editing. MA: Writing–review and editing.
Funding
The author(s) declare that financial support was received for the research, authorship, and/or publication of this article. This research was partially funded by Ministry of Science and Higher Education of Russian Federation (funding No FSFM-2024-0025).
Conflict of interest
The authors declare that the research was conducted in the absence of any commercial or financial relationships that could be construed as a potential conflict of interest.
Generative AI statement
The author(s) declare that no Generative AI was used in the creation of this manuscript.
Publisher’s note
All claims expressed in this article are solely those of the authors and do not necessarily represent those of their affiliated organizations, or those of the publisher, the editors and the reviewers. Any product that may be evaluated in this article, or claim that may be made by its manufacturer, is not guaranteed or endorsed by the publisher.
References
Ahmad, J., Abid, S. R., Arbili, M. M., Majdi, A., Hakamy, A., and Deifalla, A. F. (2022b). A review on sustainable concrete with the partially substitutions of silica fume as a cementitious material. Sustainability 14, 12075. doi:10.3390/su141912075
Ahmad, J., Alattyih, W., Jebur, Y. M., Alqurashi, M., and Garcia-Troncoso, N. (2023). A review on ceramic waste-based concrete: a step toward sustainable concrete. Rev. Adv. Mater. Sci. 62, 20230346. doi:10.1515/rams-2023-0346
Ahmad, J., Kontoleon, K. J., Majdi, A., Naqash, M. T., Deifalla, A. F., Ben Kahla, N., et al. (2022a). A comprehensive review on the ground granulated blast furnace slag (GGBS) in concrete production. Sustainability 14, 8783. doi:10.3390/su14148783
Ahmad, J., Zaid, O., Shahzaib, M., Abdullah, M. U., Ullah, A., and Ullah, R. (2021). Mechanical properties of sustainable concrete modified by adding marble slurry as cement substitution. AIMS Mater. Sci. 8, 343–358. doi:10.3934/matersci.2021022
Ahmad, J., and Zhou, Z. (2023a). Mechanical performance of waste marble based self compacting concrete reinforced with steel fiber (Part Ⅰ). J. Build. Eng. 78, 107574. doi:10.1016/j.jobe.2023.107574
Ahmad, J., and Zhou, Z. (2023b). Development of high strength self compacting concrete with waste glass and waste marble. Constr. Build. Mater. 408, 133760. doi:10.1016/j.conbuildmat.2023.133760
Ahmad, J., and Zhou, Z. (2024). Waste marble based self compacting concrete reinforced with steel fiber exposed to aggressive environment. J. Build. Eng. 81, 108142. doi:10.1016/j.jobe.2023.108142
AlArab, A., Hamad, B., and Assaad, J. J. (2022). Strength and durability of concrete containing ceramic waste powder and blast furnace slag. J. Mater. Civ. Eng. 34, 4021392. doi:10.1061/(asce)mt.1943-5533.0004031
Al-Kharabsheh, B. N., Arbili, M. M., Majdi, A., Alogla, S. M., Hakamy, A., Ahmad, J., et al. (2022). Basalt fibers reinforced concrete: strength and failure modes. Mater. (Basel) 15, 7350. doi:10.3390/ma15207350
Althoey, F., and Farnam, Y. (2019). The effect of using supplementary cementitious materials on damage development due to the formation of a chemical phase change in cementitious materials exposed to sodium chloride. Constr. Build. Mater. 210, 685–695. doi:10.1016/j.conbuildmat.2019.03.230
Ariffin, M. A., Hussin, M. W., Samadi, M., Abdul Shukor Lim, N. H., Mirza, J., Awalluddin, D., et al. (2015). Effect of ceramic aggregate on high strength multi blended ash geopolymer mortar. J. Teknol. 77, 33–36. doi:10.11113/jt.v77.6391
Awoyera, P. O., Ndambuki, J. M., Akinmusuru, J. O., and Omole, D. O. (2018). Characterization of ceramic waste aggregate concrete. HBRC J. 14, 282–287. doi:10.1016/j.hbrcj.2016.11.003
Baykal, G., and Saygılı, A. (2012). A new technique to improve freeze–thaw durability of fly ash. Fuel 102, 221–226. doi:10.1016/j.fuel.2012.06.041
Bayraktar, O. Y., Tunçtan, M., Benli, A., Türkel, İ., Kızılay, G., and Kaplan, G. (2024). A study on sustainable foam concrete with waste polyester and ceramic powder: properties and durability. J. Build. Eng. 95, 110253. doi:10.1016/j.jobe.2024.110253
Ben Nakhi, A., and Alhumoud, J. M. (2019). Effects of recycled aggregate on concrete mix and exposure to chloride. Adv. Mater. Sci. Eng. 2019, 1–7. doi:10.1155/2019/7605098
Berrocal, C. G., Lundgren, K., and Löfgren, I. (2016). Corrosion of steel bars embedded in fibre reinforced concrete under chloride attack: state of the art. Cem. Concr. Res. 80, 69–85. doi:10.1016/j.cemconres.2015.10.006
Chen, X., Zhang, D., Cheng, S., Xu, X., Zhao, C., Wang, X., et al. (2022). Sustainable reuse of ceramic waste powder as a supplementary cementitious material in recycled aggregate concrete: mechanical properties, durability and microstructure assessment. J. Build. Eng. 52, 104418. doi:10.1016/j.jobe.2022.104418
Dehghani, O., Eslami, A., Mahdavipour, M. A., Mostofinejad, D., Ghorbani Mooselu, M., and Pilakoutas, K. (2024). Ceramic waste powder as a cement replacement in concrete paving blocks: mechanical properties and environmental assessment. Int. J. Pavement Eng. 25, 2370563. doi:10.1080/10298436.2024.2370563
Du Plessis, C. (2007). A strategic framework for sustainable construction in developing countries. Constr. Manag. Econ. 25, 67–76. doi:10.1080/01446190600601313
Elemam, W. E., Agwa, I. S., and Tahwia, A. M. (2023). Reusing ceramic waste as a fine aggregate and supplemental cementitious material in the manufacture of sustainable concrete. Buildings 13, 2726. doi:10.3390/buildings13112726
El-Hawary, M., Al-Yaqout, A., and Elsayed, K. (2021). Freezing and thawing cycles: effect on recycled aggregate concrete including slag. Int. J. Sustain. Eng. 14, 800–808. doi:10.1080/19397038.2021.1886374
Federico, L. M., and Chidiac, S. E. (2009). Waste glass as a supplementary cementitious material in concrete – critical review of treatment methods. Cem. Concr. Compos. 31, 606–610. doi:10.1016/j.cemconcomp.2009.02.001
Fediuk, R. S., and Yushin, A. M. (2015). “The use of fly ash the thermal power plants in the construction,” in IOP conf. Ser. Mater. Sci. Eng. (IOP Publishing).12070. Available at: https://iopscience.iop.org/article/10.1088/1757-899X/93/1/012070/pdf#:∼:text=Thus%2C%20the%20fly%20ash%20consists,filler%20in%20the%20cement%20composition.
Gautam, L., Jain, J. K., Jain, A., and Kalla, P. (2022). “Recycling of bone China ceramic waste as cement replacement to produce sustainable self-compacting concrete,” in Structures (Elsevier), 364–378.
Ghonaim, S., and Morsy, R. (2023). Utilization of ceramic waste material as cement substitution in concrete. Buildings 13, 2067. doi:10.3390/buildings13082067
Ghorbani, S., Taji, I., Tavakkolizadeh, M., Davodi, A., and De Brito, J. (2018). Improving corrosion resistance of steel rebars in concrete with marble and granite waste dust as partial cement replacement. Constr. Build. Mater. 185, 110–119. doi:10.1016/j.conbuildmat.2018.07.066
Golewski, G. L. (2023). Examination of water absorption of low volume fly ash concrete (LVFAC) under water immersion conditions. Mater. Res. Express. 10, 085505. doi:10.1088/2053-1591/acedef
Golewski, G. L. (2024). Enhancement fracture behavior of sustainable cementitious composites using synergy between fly ash (FA) and nanosilica (NS) in the assessment based on digital image processing procedure. Theor. Appl. Fract. Mech. 131, 104442. doi:10.1016/j.tafmec.2024.104442
Heidari, A., and Tavakoli, D. (2013). A study of the mechanical properties of ground ceramic powder concrete incorporating nano-SiO2 particles. Constr. Build. Mater. 38, 255–264. doi:10.1016/j.conbuildmat.2012.07.110
Hilal, N., and Hadzima-Nyarko, M. (2021). Improvement of eco-efficient self-compacting concrete manufacture by recycling high quantity of waste materials. Environ. Sci. Pollut. Res. 28, 53282–53297. doi:10.1007/s11356-021-14222-9
Hilal, N., Tawfik, T. A., Edan, H. H., and Hamah Sor, N. (2022). The mechanical and durability behaviour of sustainable self-compacting concrete partially contained waste plastic as fine aggregate. Aust. J. Civ. Eng. 21, 151–166. doi:10.1080/14488353.2022.2083408
Huseien, G. F., Sam, A. R. M., Shah, K. W., and Mirza, J. (2020). Effects of ceramic tile powder waste on properties of self-compacted alkali-activated concrete. Constr. Build. Mater. 236, 117574. doi:10.1016/j.conbuildmat.2019.117574
Islam, G. M. S., Rahman, M. H., and Kazi, N. (2017). Waste glass powder as partial replacement of cement for sustainable concrete practice. Int. J. Sustain. Built Environ. 6, 37–44. doi:10.1016/j.ijsbe.2016.10.005
Jalal, M., Fathi, M., and Farzad, M. (2013). RETRACTED: effects of fly ash and TiO2 nanoparticles on rheological, mechanical, microstructural and thermal properties of high strength self compacting concrete. Mech. Mater. 61, 11–27. doi:10.1016/j.mechmat.2013.01.010
Ji, Y., Zhan, G., Tan, Z., Hu, Y., and Gao, F. (2015). Process control of reinforcement corrosion in concrete. Part 1: effect of corrosion products. Constr. Build. Mater. 79, 214–222. doi:10.1016/j.conbuildmat.2014.12.083
Jiménez, J. R., Ayuso, J., López, M., Fernández, J. M., and De Brito, J. (2013). Use of fine recycled aggregates from ceramic waste in masonry mortar manufacturing. Constr. Build. Mater. 40, 679–690. doi:10.1016/j.conbuildmat.2012.11.036
Jwaida, Z., Dulaimi, A., and Bernardo, L. F. A. (2024). The use of waste ceramic in concrete: a review. CivilEng. 5, 482–500. doi:10.3390/civileng5020024
Lasseuguette, E., Burns, S., Simmons, D., Francis, E., Chai, H. K., Koutsos, V., et al. (2019). Chemical, microstructural and mechanical properties of ceramic waste blended cementitious systems. J. Clean. Prod. 211, 1228–1238. doi:10.1016/j.jclepro.2018.11.240
Lee, H., Hanif, A., Usman, M., Sim, J., and Oh, H. (2018). Performance evaluation of concrete incorporating glass powder and glass sludge wastes as supplementary cementing material. J. Clean. Prod. 170, 683–693. doi:10.1016/j.jclepro.2017.09.133
Lee, W.-H., Lin, K.-L., Chang, T.-H., Ding, Y.-C., and Cheng, T.-W. (2020). Sustainable development and performance evaluation of marble-waste-based geopolymer concrete. Polym. (Basel) 12, 1924. doi:10.3390/polym12091924
Li, Y., Yao, Y., and Wang, L. (2009). Recycling of industrial waste and performance of steel slag green concrete. J. Cent. South Univ. Technol. 16, 768–773. doi:10.1007/s11771-009-0128-x
Lim, N. H. A. S., Mohammadhosseini, H., Tahir, M. M., Samadi, M., and Sam, A. R. M. (2018). Microstructure and strength properties of mortar containing waste ceramic nanoparticles. Arab. J. Sci. Eng. 43, 5305–5313. doi:10.1007/s13369-018-3154-x
Liu, X., Liu, X., and Zhang, Z. (2024c). Application of red mud in carbon capture, utilization and storage (CCUS) technology. Renew. Sustain. Energy Rev. 202, 114683. doi:10.1016/j.rser.2024.114683
Liu, Y., Deng, H., Jiang, Z., Tian, G., Wang, P., and Yu, S. (2024d). Research on influence laws of aggregate sizes on pore structures and mechanical characteristics of cement mortar. Constr. Build. Mater. 442, 137606. doi:10.1016/j.conbuildmat.2024.137606
Liu, Y., Wang, B., Fan, Y., Yu, J., Shi, T., Zhou, Y., et al. (2024a). Effects of reactive MgO on durability and microstructure of cement-based materials: considering carbonation and pH value. Constr. Build. Mater. 426, 136216. doi:10.1016/j.conbuildmat.2024.136216
Liu, Y., Wang, B., Qian, Z., Yu, J., Shi, T., Fan, Y., et al. (2024b). State-of-the art on preparation, performance, and ecological applications of planting concrete. Case Stud. Constr. Mater. 20, e03131. doi:10.1016/j.cscm.2024.e03131
Ma, Z., Li, W., Wu, H., and Cao, C. (2019). Chloride permeability of concrete mixed with activity recycled powder obtained from C&D waste. Constr. Build. Mater. 199, 652–663. doi:10.1016/j.conbuildmat.2018.12.065
Mansi, A. S., Aadi, A. S., Ali, T. K. M., Abdulhameed, H. A., and Hilal, N. N. (2024). The impact resistance of fire shooting for self-compacted concrete slabs containing ceramic powder and reinforced by novel waste nylon fiber. Ann. Chim. Sci. Des. Matériaux 48, 559–570. doi:10.18280/acsm.480413
Maruschak, P., Konovalenko, I., and Sorochak, A. (2023). Methods for evaluating fracture patterns of polycrystalline materials based on the parameter analysis of ductile separation dimples: a review. Eng. Fail. Anal. 153, 107587. doi:10.1016/j.engfailanal.2023.107587
Medina, C., De Rojas, M. I. S., and Frías, M. (2012). Reuse of sanitary ceramic wastes as coarse aggregate in eco-efficient concretes. Cem. Concr. Compos. 34, 48–54. doi:10.1016/j.cemconcomp.2011.08.015
Meena, R. V., Beniwal, A. S., Jain, A., Choudhary, R., and Mandolia, R. (2023). Evaluating resistance of ceramic waste tile self-compacting concrete to sulphuric acid attack. Constr. Build. Mater. 393, 132042. doi:10.1016/j.conbuildmat.2023.132042
Miranda, L. F. R., and Selmo, S. M. S. (2006). CDW recycled aggregate renderings: Part I–Analysis of the effect of materials finer than 75 μm on mortar properties. Constr. Build. Mater. 20, 615–624. doi:10.1016/j.conbuildmat.2005.02.025
Mohammadhosseini, H., Lim, N. H. A. S., Tahir, M. M., Alyousef, R., Samadi, M., Alabduljabbar, H., et al. (2020). Effects of waste ceramic as cement and fine aggregate on durability performance of sustainable mortar. Arab. J. Sci. Eng. 45, 3623–3634. doi:10.1007/s13369-019-04198-7
Mohit, M., Ranjbar, A., and Sharifi, Y. (2021). Mechanical and microstructural properties of mortars incorporating ceramic waste powder exposed to the hydrochloric acid solution. Constr. Build. Mater. 271, 121565. doi:10.1016/j.conbuildmat.2020.121565
Paul, S. C., Faruky, S. A. U., Babafemi, A. J., and Miah, M. J. (2023). Eco-friendly concrete with waste ceramic tile as coarse aggregate: mechanical strength, durability, and microstructural properties. Asian J. Civ. Eng. 24, 3363–3373. doi:10.1007/s42107-023-00718-x
Rodriguez, E. T., Garbev, K., Merz, D., Black, L., and Richardson, I. G. (2017). Thermal stability of CSH phases and applicability of Richardson and Groves’ and Richardson C-(A)-SH (I) models to synthetic CSH. Cem. Concr. Res. 93, 45–56. doi:10.1016/j.cemconres.2016.12.005
Saikia, N., and de Brito, J. (2009). Use of industrial waste and municipality solid waste as aggregate, filler or fiber in cement mortar and concrete. Adv. Mater. Sci. Res. 3, 65–116.
Scrivener, K. L., John, V. M., and Gartner, E. M. (2018). Eco-efficient cements: potential economically viable solutions for a low-CO2 cement-based materials industry. Cem. Concr. Res. 114, 2–26. doi:10.1016/j.cemconres.2018.03.015
Shamsaei, M., Khafajeh, R., Ghasemzadeh Tehrani, H., and Aghayan, I. (2020). Experimental evaluation of ceramic waste as filler in hot mix asphalt. Clean. Technol. Environ. Policy. 22, 535–543. doi:10.1007/s10098-019-01788-9
Siddique, S., Chaudhary, S., Shrivastava, S., and Gupta, T. (2019a). Sustainable utilisation of ceramic waste in concrete: exposure to adverse conditions. J. Clean. Prod. 210, 246–255. doi:10.1016/j.jclepro.2018.10.231
Siddique, S., Shrivastava, S., and Chaudhary, S. (2019b). Influence of ceramic waste on the fresh properties and compressive strength of concrete. Eur. J. Environ. Civ. Eng. 23, 212–225. doi:10.1080/19648189.2016.1275985
Silva, J., De Brito, J., and Veiga, R. (2010). Recycled red-clay ceramic construction and demolition waste for mortars production. J. Mater. Civ. Eng. 22, 236–244. doi:10.1061/(asce)0899-1561(2010)22:3(236)
Singh Shekhawat, B., and Aggarwal, V. (2007). Utilisation of waste glass powder in concrete-A literature review. Int. J. Innov. Res. Sci. Eng. Technol. An ISO. 3297, 2319–8753.
Smith, R. A., Kersey, J. R., and Griffiths, P. J. (2002). The Construction Industry Mass Balance: resource use, wastes and emissions. Construction 4, 680.
Stukhlyak, P. D., V Buketov, A., V Panin, S., Maruschak, P. O., Moroz, K. M., Poltaranin, M. A., et al. (2015). Structural fracture scales in shock-loaded epoxy composites. Phys. Mesomech. 18, 58–74. doi:10.1134/s1029959915010075
Sun, L., Wang, C., Zhang, C., Yang, Z., Li, C., and Qiao, P. (2023). Experimental investigation on the bond performance of sea sand coral concrete with FRP bar reinforcement for marine environments. Adv. Struct. Eng. 26, 533–546. doi:10.1177/13694332221131153
Sun, W., Wang, K., Taylor, P. C., and Wang, X. (2022). Air void clustering in concrete and its effect on concrete strength. Int. J. Pavement Eng. 23, 5127–5141. doi:10.1080/10298436.2021.2000986
Tang, J., Bai, Y., Chen, X., Cao, X., and Cui, D. (2022). Study on the macro-meso-and micro-interfacial bond characteristics between different repair materials and concrete in operation for 20 Years, meso-and micro-interfacial bond charact. between Differ. Repair Mater. Concr. Oper. 20. doi:10.2139/ssrn.4117120
Torkittikul, P., and Chaipanich, A. (2010). Utilization of ceramic waste as fine aggregate within Portland cement and fly ash concretes. Cem. Concr. Compos. 32, 440–449. doi:10.1016/j.cemconcomp.2010.02.004
Ullah, R., Qiang, Y., Ahmad, J., Vatin, N. I., and El-Shorbagy, M. A. (2022). Ultra-high-performance concrete (UHPC): a state-of-the-art review. Mater. (Basel) 15, 4131. doi:10.3390/ma15124131
Vigneshwaran, S., Uthayakumar, M., and Arumugaprabu, V. (2019). Development and sustainability of industrial waste-based red mud hybrid composites. J. Clean. Prod. 230, 862–868. doi:10.1016/j.jclepro.2019.05.131
Vishnu, T. B., and Singh, K. L. (2021). A study on the suitability of solid waste materials in pavement construction: a review. Technol. 14, 625–637. doi:10.1007/s42947-020-0273-z
Wang, L., Zhang, P., Golewski, G., and Guan, J. (2023). Editorial: fabrication and properties of concrete containing industrial waste. Front. Mater. 10, 1169715. doi:10.3389/fmats.2023.1169715
Weng, J. K., Langan, B. W., and Ward, M. A. (1997). Pozzolanic reaction in Portland cement, silica fume, and fly ash mixtures. Can. J. Civ. Eng. 24, 754–760. doi:10.1139/l97-025
Xi, X., Zheng, Y., Zhuo, J., Zhang, P., Golewski, G. L., and Du, C. (2024). Mechanical properties and hydration mechanism of nano-silica modified alkali-activated thermally activated recycled cement. J. Build. Eng. 98, 110998. doi:10.1016/j.jobe.2024.110998
Xu, F., Lin, X., and Zhou, A. (2023). Effect of recycled ceramic aggregate on hydration heat and permeability of high performance concrete. Cem. Concr. Compos. 137, 104930. doi:10.1016/j.cemconcomp.2023.104930
Xu, Q., and Liu, H.-M. (2019). “Research on chloride resisting properties of recycled concrete,” in IOP conf. Ser. Earth environ. Sci. (IOP Publishing).52051. Available at: https://iopscience.iop.org/article/10.1088/1755-1315/233/5/052051/pdf.
Zegardło, B., Szeląg, M., and Ogrodnik, P. (2016). Ultra-high strength concrete made with recycled aggregate from sanitary ceramic wastes–The method of production and the interfacial transition zone. Constr. Build. Mater. 122, 736–742. doi:10.1016/j.conbuildmat.2016.06.112
Zhang, W., and Gao, Y. (2019). “Experimental study of pervious concrete using recycled coarse aggregate,” in IOP conf. Ser. Earth environ. Sci. (IOP Publishing).12006. Available at: https://iopscience.iop.org/article/10.1088/1755-1315/283/1/012006.
Keywords: concrete, sustainability, ceramic waste, chloride penetration, water absorption and sulfate resistance
Citation: Ahmad J, Sabri MM, Majdi A, Alattyih W, Khan I and Alam M (2025) Durability and microstructure aspects of sustainable concrete made with ceramic waste: a review. Front. Mater. 11:1508989. doi: 10.3389/fmats.2024.1508989
Received: 10 October 2024; Accepted: 16 December 2024;
Published: 07 January 2025.
Edited by:
Neven Ukrainczyk, Darmstadt University of Technology, GermanyReviewed by:
Pavlo Maruschak, Ternopil Ivan Pului National Technical University, UkraineNahla Hilal, University of Fallujah, Iraq
Grzegorz Golewski, Lublin University of Technology, Poland
Copyright © 2025 Ahmad, Sabri, Majdi, Alattyih, Khan and Alam. This is an open-access article distributed under the terms of the Creative Commons Attribution License (CC BY). The use, distribution or reproduction in other forums is permitted, provided the original author(s) and the copyright owner(s) are credited and that the original publication in this journal is cited, in accordance with accepted academic practice. No use, distribution or reproduction is permitted which does not comply with these terms.
*Correspondence: Jawad Ahmad, amF3YWQuYWhtYWRAbmljZS5lZHUucGs=