- 1State Network Zhejiang Electric Power Co., Ltd., Integrated Services Branch, Hangzhou, China
- 2Hebei Key Laboratory of Distributed Energy Storage and Micro-grid, North China Electric Power University, Baoding, China
To explore sound-absorbing and flame-retardant materials that meet the requirements for double-shielded and double-insulated Faraday cages, polymethyl methacrylate (PMMA) microspheres were incorporated into epoxy resin-based syntactic foam materials for testing and analysis. The addition of PMMA microspheres was found to enhance the electrical, mechanical, sound-absorbing, and flame-retardant properties of the syntactic foam, providing a potential reference for applications in high-voltage hall shielding and sound absorption. Syntactic foams with four concentrations of PMMA microspheres (0%, 0.5%, 1%, and 2%) were prepared. High-voltage breakdown testing, impedance tube testing for sound absorption coefficient, cone calorimetry for flame-retardant performance, and tensile and bending tests were conducted. Results showed that as the concentration of PMMA microspheres increased, improvements were observed in the tensile, bending, flame-retardant, and sound absorption properties of the syntactic foams, while breakdown strength decreased. These findings provide valuable insights into the application of syntactic foam materials in double-insulation, double-shielded Faraday cages.
1 Introduction
Recently, several activities on foam materials have become more intense. Because epoxy resin syntactic foam (ERSF) (Zhu and Wu, 2009; Zixuan et al., 2021; Wen-lin, 2006; Author Anonymous, 2024) has the advantages of low density, high compressive strength, low water absorption and good insulation and breakdown performance, ERSF materials are widely used in ocean detection systems, deep-sea diving equipment, and offshore oil exploration equipment. As a kind of polymer particle, hollow microspheres (HMs) have a core-shell structure, which can combine materials having different structures or properties in a certain way and complement the excellent properties of different materials. Their special molecular composition gives them excellent characteristics, such as large surface area, low density, and excellent stability. Yu et al. used glass HMs and epoxy resin as raw materials to study the effect of microsphere particle size on the density and mechanical properties of composite materials. The research results show that the density of composite materials can reach 0.241–0.280 g/cm3, and the compression strength can reach 3.6–9.3 Mpa (Yu et al., 2018). However, glass HMs also have certain shortcomings, especially when used as fillers. The high density of glass HMs makes it difficult to obtain low-density composite materials. Lower-density polymer HMs (PHMs) should be used as the filler if a composite material with an even lower density is required. PHMs have low density and strength. Presently, few domestic studies exist on PHMs filled with ERSF materials. PHMs used in the literature mainly include phenolic resin and polystyrene microspheres (Liu et al., 2016). They are used in various products: polyester, epoxy, polyurethane, phenolic, and other composite materials. HMs made of epoxy resin are widely used to manufacture furniture, floating materials in the marine industry, and thermal insulation materials in the aerospace industry (Zhou et al., 2020). The HM-filled polymer can effectively reduce the density of the syntactic foam material without excessively affecting its strength. Liu et al. prepared lightweight composite materials with different microspheres content by using organic microspheres and silica-modified resins. It was found through experiments that with the increase of microspheres content, the water absorption rate of lightweight composite materials gradually increased, and the breakdown voltage gradually decreased (Liu et al., 2020). Therefore, the syntactic foam filled with the PHM is more widely used (Huang, 2020).
The Faraday cage principle can now be seen everywhere in production and life, with good results in high-voltage test hall applications, high-voltage live working protective clothing, and cage lightning protection nets for buildings. Among them, applying the Faraday cage in the high-voltage laboratory is essential because shielding is a key (Stonys et al., 2021). The insulation protection and shielding performance in a high-voltage test hall is critical. A double-insulation and double-shielding design (Liu et al., 2021) can be adopted to achieve a good insulation shielding effect. Thus, the structural requirements of the materials are as follows: shielding layer-insulating layer-shielding layer-insulating layer. The application of a double-shielded, double-insulated Faraday cage has the following advantages (Yue et al., 2013): (1) It improves the accuracy of high-voltage measurement and meets the requirement that the interference level of partial discharge measurement does not exceed a few pC; (2) It shields electromagnetic signals well and reduces the interference on broadcasting, TV, and industrial TV; (3) It uniforms electric field to avoid partial discharge (Cao et al., 2021). However, several problems still exist with the application of Faraday cages in the high-voltage laboratory, which mainly include: (1) Noise interference in the Faraday cage, mainly because the echo of human speech will generate reverberation in the cage; (2) Insulation, flame-retardant, shielding, and other performances will be affected by different application scenarios, such as humidity, temperature, and lightning (Li et al., 2020).
The composite foam is made by dispersing the HMs filler in a polymer resin matrix binder. The main advantages of syntactic foams are low density, high compressive strength, and low water absorption (Kim and Khamis, 2001; Kim and Plubrai, 2004; Gupta and Nagorny, 2006). Epoxy resins are one of the most widely used matrix resins for high voltage insulator and dielectric applications, and epoxy syntactic foams (ESFs) have good insulation and breakdown performance (Lee and Yee, 2000; Wouterson et al., 2005; Calahorra et al., 1987; Bilow and Paul, 1975). For the application of ESFs in Faraday cage research prospects have been clearer than in the past, many researchers have made positive attempts, but there are still many own limitations, has not been able to better balance the improvement of functional characteristics and mechanical strength reduction of the solution, it is still worth further exploration (Kinloch et al., 1985; Zotti et al., 2016; Wanshuang et al., 2017).
The study aims to explore the preparation process of polymer-filled epoxy resin-based syntactic foam materials, find the appropriate preparation process and pre-curing time through continuous experiments, and prepare effective epoxy resin-based syntactic foam materials with different organic microbead contents. Next, sound absorption, flame-retardant, breakdown, and mechanical performance tests are then performed respectively to obtain the corresponding test data and analyze the influence of the content of organic microbeads on the sound absorption, flame-retardant, mechanical properties, and other performance indicators of the ERSF materials. Finally, by analyzing the results of the tests, the choice of shielding and sound-absorbing materials for high-voltage halls based on sound-absorbing effect and test-working conditions is studied.
2 Experiment
2.1 Experimental materials
The main raw materials for this experiment include: bisphenol A epoxy resins (model E-51, Shanghai Resin Factory Co., Ltd.), whose molecular formula is shown in Figure 1A; methyl hexahydro Phthalic anhydride (MHHPA, 98% purity, Shanghai Resin Factory Co., Ltd.), which was used as the curing agent; and finally polymethyl methacrylate (PMMA) microspheres (model 920DET, Akzo Nobel).
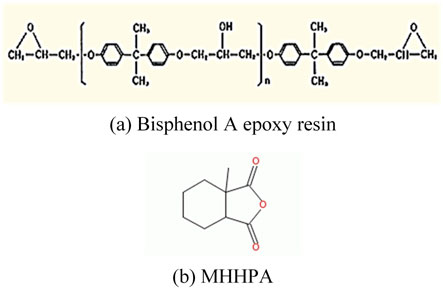
Figure 1. Molecular structure of bisphenol A epoxy resin and MHHPA. (A) Bisphenol A epoxy resin. (B) MHHPA.
Figure 1 shows the molecular structure of the main raw materials.
2.2 Sample preparation
First, E-51 and MHHPA were mixed in a mass ratio of 5:4, and then mixed with PMMA microspheres of different microcontents (0%, 0.5%, 1%, and 2%, respectively), and then 0.5 wt% of the catalyst DMP-30 (based on the total mass of curing agent and resin). The mixed matrix was put into the vacuum planetary agitator (MV300, China Maxi Technology) and stirred evenly at the speed of 600 r/min. Afterwards, the mixture is pre-cured in a thermostat (DZF-6020, Shanghai, China) at 85°C. The pre-curing conditions were denoted as M0-0 min, M0.5-57 min, M1-53 min, and M2-46 min. After pre-curing, the mixtures were stirred again. Finally, the mixtures were injected into a mold treated with a release agent and preheated (to 80°C). Next, the mixtures were transferred into the thermostat for high-temperature curing at 85°C for 6 h. In order to obtain a uniform sample in this curing stage, the method of multiple stirring in stages is used to reduce the stratification of the sample. During the cure of the blend, the blend is removed from the thermostat every 30 min and mixed with a planetary mixer. As the heating time gradually increases, the viscosity of the blend will gradually increase. A final stirring is performed when the viscosity of the blend has increased to the point where it will cure immediately. The blend is then quickly injected into a mold treated with release agent and preheated to 80°C for curing, resulting in a uniform composite foam sample. In addition, the defoaming method of vacuum defoaming with thermostat and stirring defoaming is used in the curing process. The ambient temperature was 25°C and the relative humidity was 40%.
2.3 Test characterization methods
2.3.1 AC breakdown test
The test method refers to the standard GB/T 1408.1-2006 for the electrical strength test of insulating materials at power frequency. The test process is as follows: a spherical-plate electrode was positioned in the center of the test material to ensure full contact between the electrode and the surface of the test material, and the two electrodes were aligned vertically. When the expected voltage value is unknown, a short-term (rapid) boost test method should be used so that most of the breakdown occurs between 10 and 20 s; thus, the test is considered successful. The test platform is shown in Figure 2.
2.3.2 Mechanical performance test
Two types of tests were conducted to investigate the mechanical performance: bending and compression. The bending test was performed on an ETM-104C universal mechanical testing machine following the ISO 178-2019 standard. The syntactic foam sample was 80.00
2.3.3 Sound absorption performance test
The sound absorption performance test of the sample adopts the impedance tube method (China Analysis Institute). The main application principle is the transfer function method, and the standard is GB/T 18696.2-2002. The samples were prepared in cylindrical shape, the diameter of the low-frequency sample was 40 mm, the high-frequency sample was 20 mm, and the thickness was 10 mm. Three samples of each composite foam sample were selected for the above performance test, and the measurement range of sound absorption frequency was 50 Hz–5,000 Hz.
2.3.4 Flame-retardant performance test
We can find an E test called a prototype calorimeter based on the principle of oxygen consumption, which determines the combustion characteristics of the selected materials, such as flame retardancy. Since the sample consumes a certain amount of oxygen in the instrument, combining the calorie value from the combustion, the flame retardancy test of the sample can be further analyzed based on the oxygen consumption and mass-loss rates of the materials.
3 Experimental results and analysis
3.1 Mechanical performance analysis
3.1.1 Bending performance analysis
The typical stress-strain curve of the SER-based syntactic foam material from the bending test is shown in Figure 3A. For syntactic foams (M0.5–M2), a nearly linear stress-strain relationship is observed before failure, indicating brittle-like mechanical behavior. With increasing external force, the stress and strain maintain a linear relationship until the fracture limit, showing no significant plastic deformation before failure.
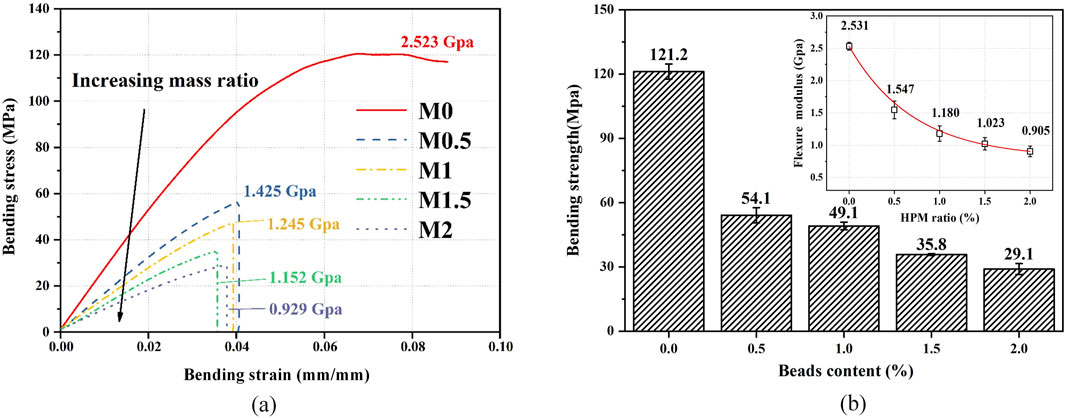
Figure 3. Typical bending stress-strain curve, tensile strength, and modulus of SER-based syntactic foams M0–M2. (A) Bending strain (mm/mm). (B) Beads content (%).
For the SER sample (M0) without hollow polymer microspheres, the bending behavior differs, displaying a plateau region after the initial linear trend in the stress-strain curve. The slope of each curve in Figure 3A represents the flexural modulus, which decreases with increasing PMMA microsphere content. This decrease in flexural modulus, which measures the material’s resistance to bending, indicates that the addition of PMMA microspheres reduces rigidity and increases susceptibility to bending deformation.
Figure 3B presents the average and standard deviation of the flexural strength and modulus of the syntactic foam. As PMMA content increases, a decrease in bending strength is evident. For instance, when the PMMA concentration rises from 0.5% to 2%, the flexural strength drops by about 64.7% (from 54.1 to 29.1 MPa), and the flexural modulus declines by about 41.5% (from 1.547 to 0.905 GPa). This demonstrates that incorporating PMMA microspheres significantly reduces the material’s flexural strength and rigidity.
The toughening mechanisms of epoxy resin through nanoparticles involve plastic deformation of the matrix, crack pinning, and crack deflection. During bending, as cracks encounter reinforcing particles, crack pinning and deflection occur, creating stress concentrations around the particles that cause localized plastic deformation, forming voids and limiting crack propagation.
However, effective toughening of the epoxy resin using PMMA particles is challenging due to two factors: achieving uniform dispersion of the nanoparticles and establishing a strong interface between the nanoparticles and the resin. PMMA particles do not significantly enhance the bending strength of the composite, likely due to suboptimal interface characteristics that result in easy debonding under stress, making effective crack pinning and deflection difficult to achieve.
3.1.2 Compression performance analysis
The typical compressive stress-strain curve of the composite material is shown in Figure 4A. In each curve, the initial compression stage is the linear elastic loading section, after which the maximum compressive strength is attained. This stage corresponds to the elastic yield stage of the matrix material. Since the maximum compressive strength represents the starting point of the fracture, the shape analysis of the curve shows that the PMMA microspheres of the syntactic foam will not be crushed before the peak stress and the PMMA microspheres have high structural stability and tolerance during initial compression. For the curve of the syntactic foams (M0.5–M2), approximate constant stress is observed after attaining the maximum compressive strength. This trend may be because the internal hollow volume of PMMA microspheres is compressed when they are crushed, and the SER matrix can occupy this hollow volume under compression, called the densification stage.
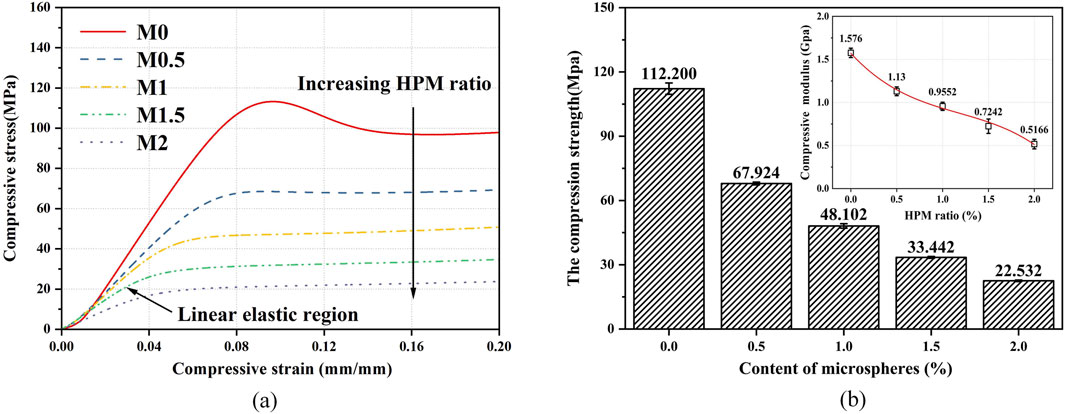
Figure 4. Typical compressive stress-strain curve, compressive strength, and modulus of SER-based syntactic foams M0–M2. (A) Compressive strain (mm/mm). (B) Content of microspheres (%).
Figure 4B summarizes the compressive strength and modulus values of samples M0–M2. As expected, when the content of PMMA microspheres increased from 0% to 2%, the compressive strength and modulus values decreased (from 112.2 MPa to 1.576 GPa to 22.532 MPa and 0.517 GPa). The addition of PMMA microspheres forms a hollow pore structure, which cannot share the stress, decreasing the compression performance of the composite material. However, compared with the compressive strength (1.1 MPa) of traditional internal insulation PUF material, even the M2 material with the highest PMMA content maintained a minimum compressive strength of 22.5 MPa, which still demonstrates the significant advantages of structural foams in terms of compression properties. In summary, the physical properties of composites can be changed to a certain extent by adjusting the content of PMMA microspheres, but it is necessary to weigh the impact of the compressive properties brought by the pore structure.
3.2 Electrical performance analysis
Enough polymer microspheres filled with epoxy resin-based syntactic foam were prepared according to the process described in section 1.2, where the filling amount of PMMA organic microspheres is an independent variable. Afterwards, they were made to undergo an AC breakdown test. The syntactic foam used in the test is shown in Figure 5.
In terms of mechanism, the syntactic foam has a hollow filling structure and the inside of the polymer filler is gas-insulated, which means it has a lower AC breakdown strength than the solid resin matrix. Figure 6 shows the two-parameter Weibull distribution of the breakdown strength of the composites with four PMMA microsphere filling contents. Taking the breakdown probability of 63.2% as an example, the breakdown strength of SER-based syntactic foam M0.5 is ∼29.15% < that of syntactic foam M0. Additionally, it was observed that when the filling mass of PMMA microspheres increased from 0.5% to 2.0%, the breakdown strength decreased from 23.38 to 19.02 kV/mm. Although a decrement occurred, the decreased value was insignificant.
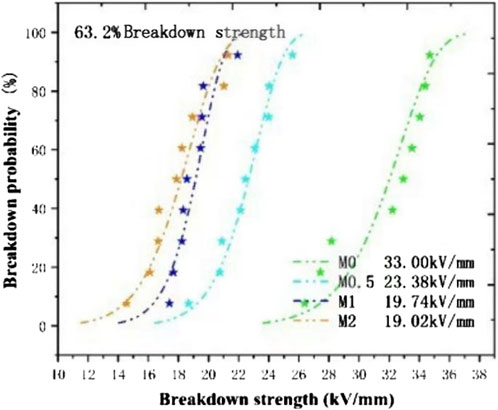
Figure 6. Breakdown field strength of epoxy resin-based syntactic foams with different organic microbead contents.
The reason for such a trend is analyzed as follows: The PMMA organic microspheres have good electrical conductivity (Sun et al., 2006), and the dielectric constant is < those of epoxy resin and air. The organic microspheres added to the epoxy resin-based syntactic foam fill the pores, making the filling place more prone to pore discharge (Zhang, 2019). The electrical breakdown process in composite foam materials may initially be triggered by the gas discharge inside the microsphere, which gradually causes the electric erosion of the microsphere with the development of the discharge, and finally leads to the breakdown of the composite material as a whole (Strauchs et al., 2012). Due to the addition of more HPM microsphere fillers, more defects will be generated, and more gas discharge will be introduced into the material volume, thus accelerating the formation of the breakdown channel, and reducing the breakdown strength of the composite material on a macro level. However, compared with the breakdown strength of traditional inpacked polyurethane (5.02 kV/mm), the lowest breakdown strength of the composite foam material is 19.02 kV/mm (M2), which still indicates that the composite foam material has good electrical insulation reliability and shows great potential in the application of composite insulated crossarm.
3.3 Flame-retardant performance analysis
The cone calorimeter (CONE) can analyze the combustion performance of materials under various preset conditions and obtain the time to ignition (TTI), peak heat release rate (PHRR), total smoke rate (TSR), total heat release rate (THRR), and other parameters (Pereira et al., 2021). The PMMA organic microspheres can improve the flame-retardant performance of epoxy resin-based syntactic foams (Wu et al., 2021). Its THRR, total oxygen consumption, average HRR, PHRR, and average mass-loss rate are shown in Figure 7A. The change in HRR with time is shown in Figure 7B. As the content of the organic microbeads increases, the above parameters all decrease to varying degrees. For example, when the content of organic microbeads increased from 0% to 2%, the THRR decreased by 33.38% (from 64.7 to 43.1 MJ/m2). The PHRR decreased by 23.73% (from 614.4 to 468.58 kW/m2), which indicates that the addition of organic microbeads improves the flame-retardant properties of epoxy resin and positively affects the flame-retardant properties of the composite materials. As the content of the organic microbeads increases, the syntactic foam samples are less likely to be burned (Figure 8), indicating that adding organic microbeads improves the flame retardancy of epoxy resin.
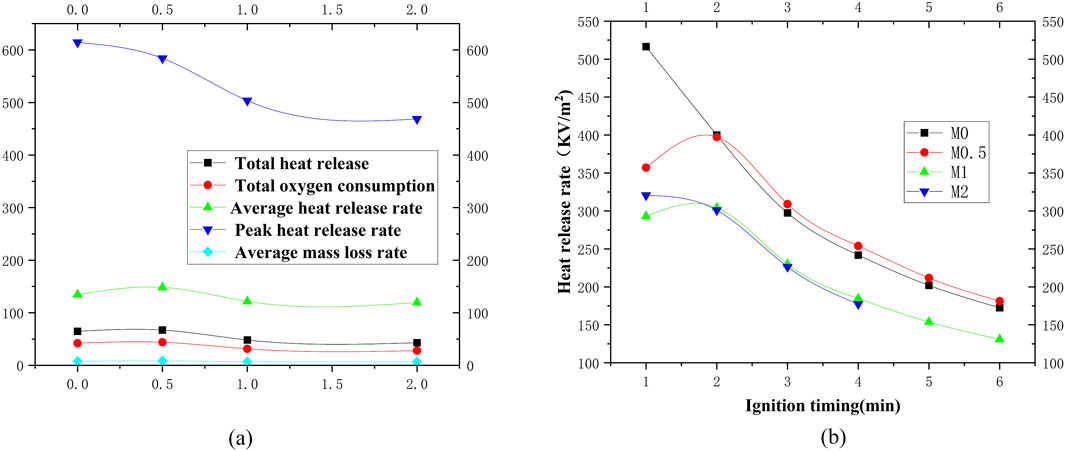
Figure 7. Flame-retardant data analysis of syntactic foam with different microbead content. (A) The change in THRR, total oxygen consumption, average HRR, PHRR, and average mass-loss rate with content of organic microbeads. (B) The change in HRR with time.
This outcome occurs because PMMA microspheres have good temperature resistance (Chen et al., 2020). The addition of PMMA microspheres increases the heat resistance time of the composite material. After adding the organic microspheres, the carbon residue mass of the composite material increases and covers the surface of the epoxy resin to insulate the heat and block oxygen, thereby slowing down the burning process of epoxy resin; thus, significantly improving the flame-retardant performance of the syntactic foam.
When the content of PMMA microspheres is low, it is difficult for the microspheres to be fully dispersed inside the epoxy resin, thereby causing unevenness of the epoxy resin material. The unevenness of the material causes uneven heating. In addition, the part with lower microsphere content has poor heat resistance, is easily heated, and has poor flame retardancy. Therefore, when the content of PMMA microspheres is low, the flame-retardant performance of the organic microsphere epoxy resin-based syntactic foam is less improved.
When the content of PMMA microspheres is high, the microspheres are fully distributed inside the epoxy resin, and the entire syntactic foam material is more uniform. Also, the microspheres fill the internal defects of the epoxy resin material, which improves the flame-retardant performance of the material. Therefore, when the content of PMMA microspheres is high, the flame-retardant performance of the organic microsphere epoxy resin-based syntactic foam is significantly improved.
3.4 Sound absorption performance analysis
Figure 9 shows the sound absorption data of the composite material tested by the reverberation chamber method. When the content of the organic microbeads increases from 0% to 0.5%, the sound absorption coefficient of the composite material ranging from 800 to 1,250 Hz increases significantly. The sound absorption coefficient at 1,250 Hz increases by 80% (from 0.1 to 0.18), whereas the sound absorption coefficient decreases considerably in the range of 1,600–5,000 Hz. The sound absorption coefficient of the composite materials at 1,600 Hz is reduced by 64.7% (from 0.17 to 0.06), the sound absorption coefficient at 2,000 Hz is reduced by 85.7%, the sound absorption coefficient at 2,500 Hz is reduced by 72.7% (from 0.11 to 0.03), the sound absorption coefficient at 3,150 Hz is reduced by 75% (from 0.08 to 0.02), the sound absorption coefficient at 4,000 Hz is reduced by 80% (from 0.05 to 0.01), and the sound absorption coefficient at 5,000 Hz is reduced by 75% (from 0.04 to 0.01).
When the content of organic microbeads increases from 0.5% to 2%, the sound absorption coefficient of the composite material in the range of 1,600–4,500 Hz gradually increases; however, it still decreases compared with the syntactic foam with 0% microbead content. The above data show that when there is a small increase in the content of organic microbeads, the sound absorption performance in the low-frequency range is improved. When the content of microbeads increases from 0.5% to 2%, the sound absorption performance in the frequency range of 1,600–4,500 Hz increases significantly; however, it is still < that of the 0% bead content of the foam material.
The possible reasons for such a trend are as follows. PMMA microspheres (Li, 2020; Peng et al., 2000) are hollow, low-density spheres (Shi, 2018; Tian, 2012) with low water absorption and heat insulation. Compared with hollow glass microspheres of inorganic silicates (He, 2018), their main component is polymethyl methacrylate, which has less impact (Li, 2020; Peng et al., 2000) on the compatibility of epoxy resin interfaces (Yang, 2013) and is theoretically an excellent filler for enhancing the sound insulation function of epoxy resins. The sound absorption performance of epoxy resin-based syntactic foams (Sun et al., 2006; Pereira et al., 2021) is determined by the density, thickness, open porosity, and cell size of the foam material (Huang, 2020). The increase in the content of PMMA microspheres makes the syntactic foam much more absorbent in the mid-to-high frequency range of 1,600–4,500 Hz. This trend occurs because the addition of PMMA microspheres improves the pore structure of the epoxy resin-based syntactic foam (Sun et al., 2006; Strauchs et al., 2012), and forms a better porous material.
Porous materials often contain a large number of ultra-small pores and gaps, or capillary structures, between which air is filled. When the sound wave is vertically incident on the surface of the porous material, part of the sound wave is reflected by the surface of the material, and the other part is transmitted to the inside of the material through the capillary tube that is transparent to the outside world. The vibration of sound waves entering the material causes the violent movement of air in the capillary tube, causing it to rub against the wall of the hole. Under the action of friction and viscous force, part of the sound energy is converted into heat energy, which attenuates the sound wave and weakens the reflected sound energy to achieve the sound absorption effect. In addition, the air in the capillary and the heat exchange between the hole wall and the material cause heat loss, and also cause sound energy attenuation. Therefore, the sound absorption effect of porous materials is the result of the combined action of the viscous force and friction force of the air, and the heat conduction between the air and the material between the capillary tubes.
The addition of PMMA microspheres in the composite foam material increases the pore content and porosity inside the composite foam, reduces the pore size, and thus increases the viscous resistance of sound waves inside the material. The internal viscous resistance converts sound energy into heat, which is consumed, thereby attenuating sound energy. The PMMA microspheres retain the complete structure after the syntactic foam is cured, and the epoxy resin does not fill the cavity of PMMA (He, 2018), which can improve the sound insulation performance of the syntactic foam. The hollow structure of PMMA can continuously diffract, scatter, and refract sound waves, which increases the propagation path of sound waves, increasing the sound energy loss during continuous propagation. Also, the addition of the polymethyl flexible chain (Yang, 2013) reduces the cohesion of the epoxy resin matrix, enhances the movement ability of the epoxy resin segment, and therefore, enhances the vibration absorption capacity of the syntactic foam (Hai-Shuo, 2019). Thus, the damping performance of the syntactic foam is enhanced, which indicates that the sound wave must overcome greater resistance when propagating inside the syntactic foam, thereby causing this part of the sound energy to be converted into heat energy and consumed. In summary, the addition of PMMA microspheres enhances the sound absorption performance of the epoxy resin-based syntactic foam.
However, the density difference between the epoxy resin and PMMA is relatively large, which may cause the macroscopic phase separation when the two materials are combined (Wen-bo, 2012), resulting in insufficient performance of the syntactic foam. Therefore, when the filling content of PMMA microspheres is increased from 0.5% to 1% and 2%, the sound absorption coefficient of the syntactic foam is not significantly improved compared with that of the syntactic foam of 0% microspheres.
4 Conclusion
This study focused on the preparation and analysis of PMMA organic microsphere-filled epoxy resin-based syntactic foam materials, exploring the effects of PMMA microsphere content on the various properties of these syntactic foams through tests such as AC breakdown, mechanical performance, sound absorption, and flame-retardant performance. The key conclusions are as follows:
Preparation and Optimization: Syntactic foam samples with different PMMA microsphere concentrations (0%, 0.5%, 1%, and 2%) were successfully prepared. The material ratio and pre-curing process were optimized based on experimental results, determining the appropriate pre-curing times to ensure uniformity and performance in the final test samples.
Performance Enhancement: Tests showed that the incorporation of PMMA microspheres enhances the mechanical, electrical, flame-retardant, and sound absorption properties of epoxy resin-based syntactic foams compared to unfilled foams. Specifically, the syntactic foams exhibited improved sound absorption and flame retardancy as PMMA content increased, though there was a trade-off with reduced breakdown strength.
Optimal Content and Application Insight: The results indicate that a 2% concentration of PMMA microspheres provides a balance between enhanced sound absorption and flame-retardant performance, while maintaining acceptable mechanical and electrical properties. This suggests that the 2% microsphere content is optimal for applications requiring sound absorption and insulation in high-voltage environments, such as double-shielded and double-insulated Faraday cages.
In summary, this research provides valuable insights and a reference for the preparation process and property enhancement of PMMA microsphere-filled epoxy resin syntactic foams, supporting their application in environments requiring high insulation, sound absorption, and flame resistance.
Data availability statement
The original contributions presented in the study are included in the article/supplementary material, further inquiries can be directed to the corresponding author.
Author contributions
WX: Conceptualization, Writing–review and editing. YF: Conceptualization, Writing–review and editing. JW: Methodology, Writing–review and editing. ZF: Methodology, Writing–review and editing. JS: Validation, Writing–review and editing. YM: Formal Analysis, Writing–original draft. YW: Resources, Writing–review and editing. HL: Investigation, Writing–review and editing. LL: Investigation, Writing–review and editing.
Funding
The author(s) declare that no financial support was received for the research, authorship, and/or publication of this article.
Conflict of interest
Authors WX, YF, JW, ZF and JS were employed by State Network Zhejiang Electric Power Co., Ltd. Integrated Services Branch.
The remaining authors declare that the research was conducted in the absence of any commercial or financial relationships that could be construed as a potential conflict of interest.
Publisher’s note
All claims expressed in this article are solely those of the authors and do not necessarily represent those of their affiliated organizations, or those of the publisher, the editors and the reviewers. Any product that may be evaluated in this article, or claim that may be made by its manufacturer, is not guaranteed or endorsed by the publisher.
References
Author Anonymous (2024). Research on electromagnetic shielding characteristics of national high voltage meter.
Bilow, N., and Paul, M. S. (1975). Coating processes for increasing the moisture resistance of polyurethane baffle material. J. Cell. Plastics 11 (4), 207–212. doi:10.1177/0021955x7501100404
Calahorra, A., Gara, O., and Kenig, S. (1987). Thin film parylene coating of three-phase syntactic foams. J. Cell. plastics 23 (4), 383–398. doi:10.1177/0021955x8702300402
Cao, Y., Pan, W. J., Zhu, Y. F., Yin, F., Yang, L., Yuan, Y., et al. (2021). Feasibility study on superconducting application of epoxy resin based PET composites. Low Temp. Supercond. 04, 26–30.
Chen, Y., Tan, X. M., Xiong, X. H., Gang, T., Zhang, J., Zhang, K., et al. (2020). Study on silver plating on polymethyl methacrylate microspheres. Precious Met. 01, 37–42.
Gupta, N., and Nagorny, R. (2006). Tensile properties of glass microballoon-epoxy resin syntactic foams. J. Appl. Polym. Sci. 102 (2), 1254–1261. doi:10.1002/app.23548
Hai-Shuo, C. (2019). Electromagnetic properties of fiber reinforcement epoxy resin absorbing composite. Nanjing: Nanjing University of Aeronautics and Astronautics, 78.
He, J. (2018). Preparation and application of polynucleic low density polymer microspheres. Kunming: Kunming University of Science and Technology, 143.
Huang, Z. (2020). Research on electromagnetic protection effect of Faraday cage in nuclear power plant under direct lightning based on Matlab. Mod. Build. Electr. 06, 34–37.
Kim, H. S., and Khamis, M. A. (2001). Fracture and impact behaviours of hollow micro-sphere/epoxy resin composites. Compos. Part A Appl. Sci. Manuf. 32 (9), 1311–1317. doi:10.1016/s1359-835x(01)00098-7
Kim, H. S., and Plubrai, P. (2004). Manufacturing and failure mechanisms of syntactic foam under compression. Compos. Part A Appl. Sci. Manuf. 35 (9), 1009–1015. doi:10.1016/j.compositesa.2004.03.013
Kinloch, A. J., Maxwell, D., and Young, R. J. (1985). Micromechanisms of crack propagation in hybrid particulate composites. J. Mater. Sci. Lett. 4, 1276–1279. doi:10.1007/bf00723480
Lee, J., and Yee, A. F. (2000). Fracture of glass bead/epoxy composites: on micro-mechanical deformations. Polymer 41 (23), 8363–8373. doi:10.1016/s0032-3861(00)00187-7
Li, L., Chen, M. Y., Sun, W., Wang, L., Bao, D., Wang, D., et al. (2020). Analysis of AC breakdown properties of SiO_2/epoxy resin composites for insulating tools. Contemp. Chem. Ind. 12, 2732–2735.
Li, W. (2020). Study on the preparation and properties of sound-absorbing flame retardant fiber composites. Shaanxi University of Science and Technology, 76.
Liu, G. H., Li, S. S., Dong, S. C., Zhang, X., Tian, S., Huang, Y., et al. (2016). Design and analysis of key structures in solid insulated ring net cabinet. High. Volt. Appliances 08, 136–140.
Liu, X., Xiong, X., Pang, J., Wu, L., and Zhang, H. (2021). Airflow resistivity measurement and sound absorption performance analysis of sound-absorb cotton. Appl. Acoust. 179, 108060. doi:10.1016/j.apacoust.2021.108060
Liu, Y., Li, L., Liu, H., Zhang, M., Liu, A., Liu, L., et al. (2020). Hollow polymeric microsphere-filled silicone-modified epoxy as an internally insulated material for composite cross-arm applications. Compos. Sci. Technol. 200, 108418. doi:10.1016/j.compscitech.2020.108418
Peng, L., Dean, L., and Yang, X. (2000). Research and application of microsphere composite foams. Fiber Reinf. Plastics. Composites 04, 21–24.
Pereira, M., Mareze, P. H., Godinho, L., Amado-Mendes, P., and Ramis, J. (2021). Proposal of numerical models to predict the diffuse field sound absorption of finite sized porous materials – BEM and FEM approaches. Appl. Acoust. 180, 108092. doi:10.1016/j.apacoust.2021.108092
Stonys, R., Jagniatinskis, A., Malaiskiene, J., Skamat, J., Antonovic, V., Koryakins, A., et al. (2021). Using the acoustic method of measuring the sound absorption coefficient to predict the durability (heat resistance) of heat-resistant concretes. Refract Ind Ceram. 61(6):709-714. doi:10.1007/s11148-021-00547-y
Shi, X. (2018). Mechanical and acoustic insulation properties of epoxy resin/hollow filler composites. Wuhan: Huazhong University of Science and Technology, 146.
Strauchs, A., Mashkin, A., and Schnettler, A. (2012). Effects of SiO2 nanofiller on the properties of epoxy resin based syntactic foam. IEEE Trans. Dielectr. Electr. Insulation 19(2): 400–407. doi:10.1109/tdei.2012.6180231
Sun, C., Xing, Y, and Wang, Q. (2006). High strength buoyancy material of deep sea was synthesized by hollow glass beads filled with polymer. J. Univ. Sci. Technol. 06, 554–558.
Tian, Z. M. (2012). Preparation and in vitro drug delivery of magnetic polymer nanoparticles with PMAA. Evanston: Northwestern University, 64.
Wanshuang, L., Wang, Y., Wang, P., Li, Y., Jiang, Q., Hu, X., et al. (2017). A biomimetic approach to improve the dispersibility, interfacial interactions and toughening effects of carbon nanofibers in epoxy composites. Compos. B Eng. 113, 197–205. doi:10.1016/j.compositesb.2017.01.040
Wen-bo, Z. (2012). Study on epoxy resin/polyvinyl chloride modified rigid polyurethane foam. Beijing: Beijing University of Chemical Technology, 78.
Wen-lin, H. (2006). Preparation and characterization of lightweight epoxy composites filled with polymer hollow microspheres. J. Zhejiang Univ. 91.
Wouterson, E. M., Boey, F. Y., Hu, X., and Wong, S. C. (2005). Specific properties and fracture toughness of syntactic foam: effect of foam microstructures. Compos. Sci. Technol. 65 (11-12), 1840–1850. doi:10.1016/j.compscitech.2005.03.012
Wu, H., Zhang, H., and Hao, C. (2021). Reconfigurable spiral underwater sound-absorbing metasurfaces Extreme Mech. Lett 101361.
Yang, Lu (2013). Synthesis of magnetic polymer microspheres containing epoxy groups and their immobilized enzyme properties. East China Univ. Sci. Technol. 68.
Yu, Q., Zhao, Y., Dong, A., and Li, Y. (2018). Mechanical properties of EPS filled syntactic foams prepared by VARTM. Compos. Part B Eng. 136, 126–134. doi:10.1016/j.compositesb.2017.07.053
Yue, L., Lu, Y., and Chen, K (2013). Research progress in application of sound-absorbing materials. Guangdong Chem. Ind. 10, 80–81.
Zhang, Y. (2019) Study on insulating properties of polyurethane composite foam with expanded organic microspheres 23.
Zhou, W., Xie, Y., and Zhang, W. (2020). Electric field analysis and optimization of key parts of double shielding insulating shell in PET. High. Volt. Appliances 10, 41–47.
Zhu, Z., and Wu, P. (2009). Research and development of high strength lightweight buoyancy materials for deep sea exploration. Mod. Technol. Ceram. 01, 15–20.
Zixuan, Li, Xinhai, Y, and Yu, X. (2021). Preparation and properties of epoxy resin packaging material for IGBT. New Mater. Chem. Industry, 1–16.
Keywords: PMMA beads, epoxy resin, sound absorption coefficient, breakdown voltage, flame-retardant coefficient
Citation: Xue W, Feng Y, Wang J, Fang Z, Shen J, Ma Y, Wang Y, Liu H and Li L (2024) Preparation of polymer hollow microsphere filled epoxy resin-based syntactic foam material and its performance analysis. Front. Mater. 11:1500015. doi: 10.3389/fmats.2024.1500015
Received: 22 September 2024; Accepted: 20 November 2024;
Published: 02 December 2024.
Edited by:
Junxin Wang, University of Cambridge, United KingdomReviewed by:
Xingzhe Wang, Lanzhou University, ChinaMauro Zarrelli, National Research Council (CNR), Italy
Copyright © 2024 Xue, Feng, Wang, Fang, Shen, Ma, Wang, Liu and Li. This is an open-access article distributed under the terms of the Creative Commons Attribution License (CC BY). The use, distribution or reproduction in other forums is permitted, provided the original author(s) and the copyright owner(s) are credited and that the original publication in this journal is cited, in accordance with accepted academic practice. No use, distribution or reproduction is permitted which does not comply with these terms.
*Correspondence: Yueru Wang, MTMxODQ1MTIxN0BxcS5jb20=