- Max Planck Institute for Chemical Physics of Solids, Dresden, Germany
This work comprises a generalization of a simple geometric model originally developed to describe coupled rotations of corner-sharing octahedra in the surface layer of
1 The 4-Octahedra model
1.1 Introduction
The presence and tuning of octahedral rotations and distortions in many forms of transition metal oxides (TMOs) built from corner-sharing octahedra, including bulk systems, thin films, layered compounds, and heterostructures, have a profound effect on their electronic properties (Morales et al., 2023; Liao et al., 2016; Paris et al., 2020; Aso et al., 2013; Ali et al., 2022; Angel et al., 2005; Lu et al., 2013; Herklotz et al., 2016; Thomas et al., 2017; Petrov et al., 2013; He et al., 2010). Describing, reproducing, and classifying the relevant octahedral geometry and its evolution are thus key aspects in explaining the observed responses, serving both as the input for theoretical calculations and in the design of novel experiments.
Models of corner-sharing octahedra are common in the literature on perovskites and TMOs (Glazer, 1972; Woodward, 1997; Howard and Stokes, 1998; Hammonds et al., 1998). Nevertheless, most of them consist of static visualizations and symmetry classifications derived from crystallographic solutions of particular structures—essentially, a series of coordinates defining the transition metal octahedra or the symmetry operations associated with a certain octahedral configuration. Some models are able to track the evolution in the octahedral configuration when a constraint is imposed on the system (Qian et al., 2020) but rely on classical elastic energy minimization to find an optimal geometry rather than explore all the possible outcomes compatible with the applied constraint. Moreover, the models are mostly focused on perovskites (Glazer, 1972; Woodward, 1997; Howard and Stokes, 1998; Qian et al., 2020), and the notation introduced for classifying the octahedra can be quite elaborate without a solid background in group theory (Howard and Stokes, 1998).
Instead, in this study, we develop a purely geometric two-dimensional model with a special focus on layered compounds such as Ruddlesden–Popper phases but also applicable to certain perovskites and other systems of corner-sharing octahedra. The individual octahedral configuration is rigorously parametrized and directly mapped to the global configuration of the lattice, including not only rigid rotations but also bond length and non-orthogonal distortions of the octahedra. This mapping has the advantage of tunability because octahedral manipulation is normally achieved by applying a macroscopic constraint to the lattice, such as doping, uniaxial or epitaxial strain, or interface engineering (Morales et al., 2023; Liao et al., 2016; Paris et al., 2020; Aso et al., 2013; Ali et al., 2022; Angel et al., 2005; Lu et al., 2013; Herklotz et al., 2016; Thomas et al., 2017; Petrov et al., 2013; He et al., 2010), which ultimately has an effect on the local octahedral configuration. Moreover, the model is easy to use and, in combination with theoretical methods such as density functional theory or tight-binding calculations, can serve as a benchmark for testing the effect that particular octahedral distortions have on the electronic structure derived from the underlying geometry (Morales et al., 2023).
The model construction is divided into three stages, each involving a different level of generality and applicability:
1.2 Single octahedron parametrization
We begin by defining a single octahedron as follows (see Figure 1):
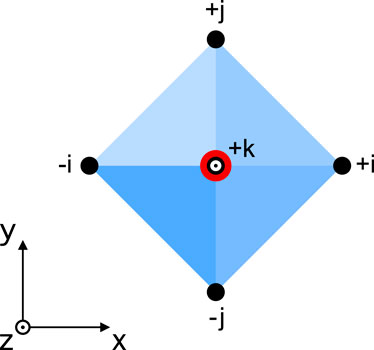
Figure 1. Basic single octahedron configuration and the labels employed for its corners (the
where
with
where
with
where we can recover the rotation angles from
The parameter
and
so that the octahedron can be written as
An example showing the effect of varying the different parameters of a single octahedron is shown in Figure 2. Next, we define the octahedron sub-site operators:
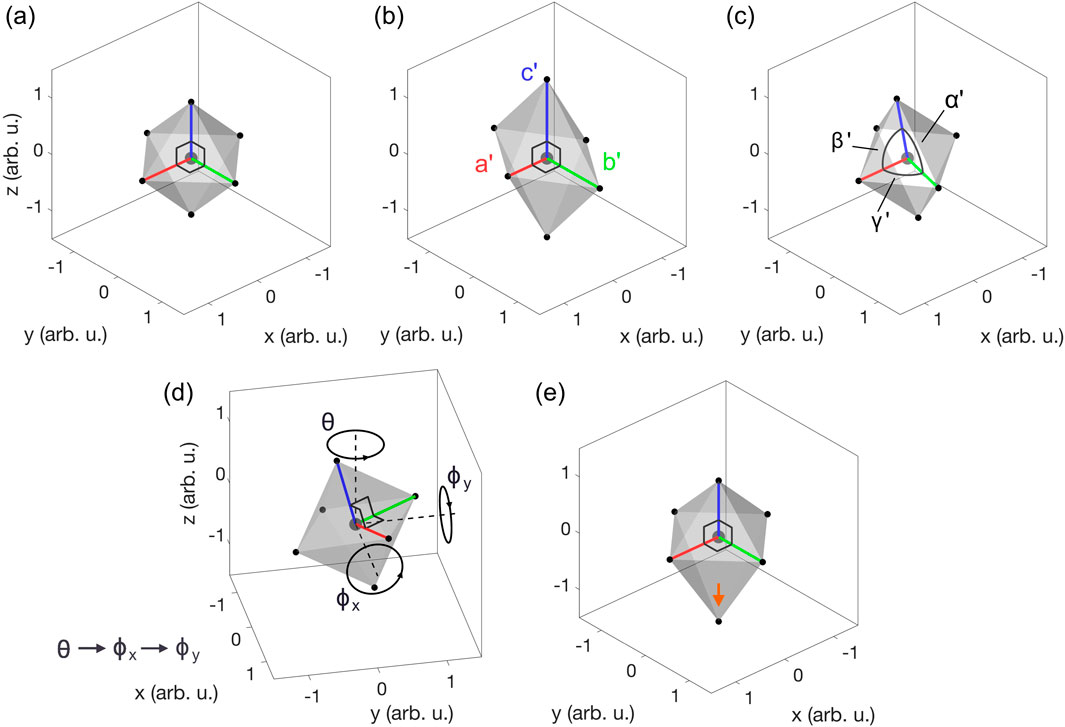
Figure 2. Parametrization of a single octahedron. (A) Regular, orthogonal octahedron of unitary arm length. (B) Non-regular, orthogonal octahedron with arm lengths
When these operators act on an octahedron
where
1.3 Extracting parameters from a single octahedron
To benefit from the parametrization given above in studying a particular system, we must first extract the octahedral information from its crystal structure. In other words, we want to build a set of relations that take the corners of an octahedron (
where
where
which is consistent with Equation 13. Thus,
where each row is an octahedron arm vector, with the last one multiplied by the unknown factor
and define
Thus,
Therefore, because the centroid
which is non-zero in ferroelectric materials, even for centrosymmetric octahedra, for example.
1.4 The 4-octahedra general case
We now create a system of four octahedra connected through their corners, as shown in Figure 3, such that the individual octahedra are free to rotate or distort but remain linked at all times. We call this system 4-octahedra, which we then use as a building block to form a lattice. In doing so, we determine all possible bond lengths, bond angles, and octahedral rotations within the 4-octahedra that are compatible with up to four inequivalent sites. According to Equation 10, we can express an individual octahedron as follows:
where
Now, the conditions for having the four octahedra connected through their corners, as shown in Figure 3, are as follows:
From these and Equation 11, we obtain the following set of equations:
which we rearrange to get the following relationships between the octahedral displacements:
and a displacement-independent structural equation, which provides a necessary and sufficient condition for the octahedra to be linkable (see Figures 4A, B):
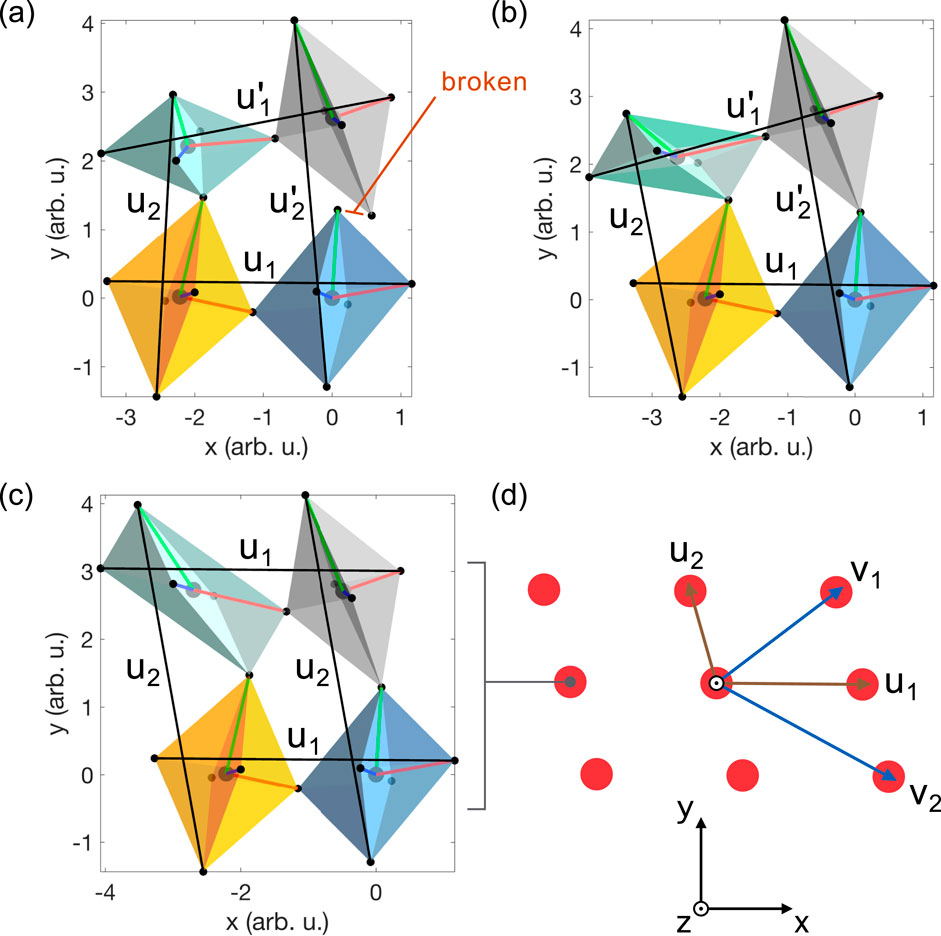
Figure 4. Formation of the 4-octahedral lattice. (A) 4-Octahedral model that does not satisfy Equation 26, showing a broken link and the impossibility to form a lattice. (B) 4-Octahedral model that does satisfy Equation 26, but not Equations 37, 38, showing octahedral linking incompatible with lattice formation. (C) 4-Octahedra satisfying Equations 37, 38 and exhibiting octahedral linking compatible with lattice formation. (D) The primitive and conventional lattice vectors of the 4-octahedral lattice formed by the 4-octahedra in (C), where each point represents a 4-octahedral unit. The lattice is monoclinic with
Furthermore, without loss of generality, we fix the translational freedom of the 4-octahedra such that
and we define a site-equivalency operator between two octahedra as follows:
Therefore, two sites are equivalent if
1.5 The 4-Octahedra lattice
In order for the 4-octahedra to form a two-dimensional lattice, we must impose periodic boundary conditions such that the bottom (left) corners in Figure 3 connect with the top (right) corners modulo two linearly independent vectors
which are clearly not satisfied in Figure 4B, where there is no unique
and eliminate
Moreover, combining Equations 20, 23 and Equations 21, 22 yields
Equations 33–36 imply that
which are displacement-independent structural conditions for the 4-octahedra to form a lattice. Moreover, the sum of the last two identities yields Equation 26. Thus, if satisfied, the lattice equations automatically imply octahedral linking. Furthermore, from Equation 32,
Therefore, using the condition in Equation 27, we obtain
Thus, we see that the octahedral displacements lie in the same plane. Equations 37, 38 hold immediately in monopartite
Substituting Equations 39, 40 into Equations 24, 25 yields
where we have defined the
Moreover, adding Equations 28, 29 and Equations 30, 31 and then using Equations 39, 40 and Equations 41, 42 yield
which define the primitive lattice vectors of the system as a function of the octahedral displacements or the
which run diagonally across the 4-octahedra lattice (see Figure 4D).
1.6 Relationship between the lattice and the 4-octahedra configuration
In this section, we establish a set of geometric relations that link the global properties of the lattice, such as the vector length and the projections between them, to the specific octahedral geometry and rotation angles encoded in the
and the projection between the primitive vectors:
Now, we evaluate the length difference between the conventional vectors:
and the length difference between the primitive vectors:
1.7 Main theorem of the 4-octahedra lattice
From Equations 48–51, we have shown that
where we define the geometric scalar fields:
Thus, we see that
which we refer to as conditions (1) and (2), respectively. It follows that
Therefore, we can map the octahedral configuration to the lattice geometry using only two parameters
1.8 Addressing the system rotational freedom
Just as we fixed the translational freedom of the 4-octahedra, we can (without loss of generality) choose the displacements of the octahedra to lie entirely within the
Furthermore, to fix the in-plane rotational freedom, we can set the displacements 1 and 2 to lie along the
Thus, rearranging Equations 54–56, we obtain
which means that we must choose
where
1.9 Toward three-dimensions and sites
A generalization that would allow the description of many more octahedral configurations implies extending the model to three dimensions and scaling it to support
The biggest drawback of this process is manipulating a large number of equations; however, the high level of symmetry displayed by the relationships suggests that there may be ways to automatize the algorithm, possibly using system matrices and other elements from linear algebra.
1.10 4-Octahedra two-site bipartite model
The model is chosen as a compromise between the generality afforded by multiple inequivalent sites while balancing the computational efficiency and analytical tractability; therefore, we now focus on the case where there are two inequivalent sites forming a bipartite lattice (checkerboard pattern), similar to the surface layer of
That is, sites 1 and 4 and sites 2 and 3 are equivalent, respectively, such that
where we used the relevant equations from Section 1.5 and considered
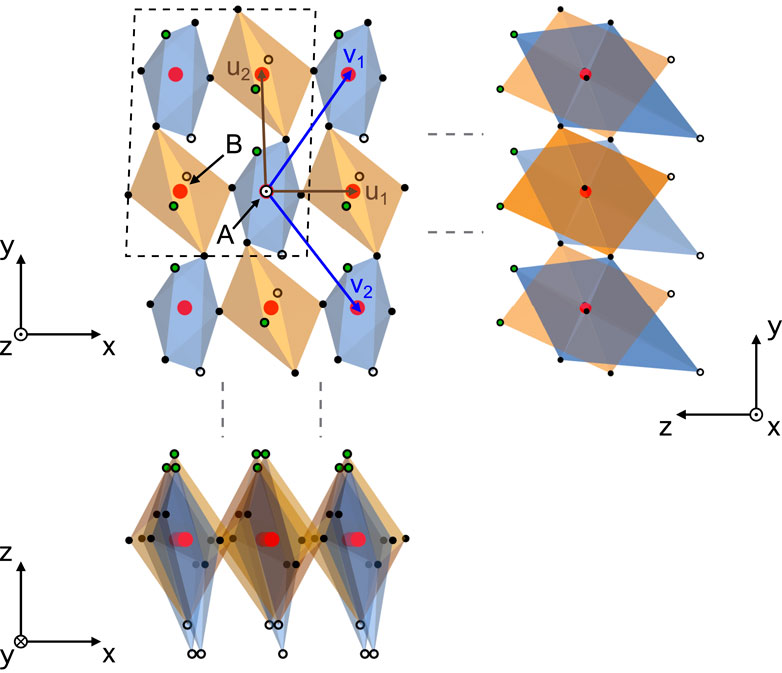
Figure 5. Bipartite model in a monoclinic configuration observed from different projections, where the 4-octahedra is enclosed by the dashed box. The arm lengths are
1.11 The 4-Octahedra model made accessible
The bipartite 4-octahedra model has been coded into MATLAB functions that facilitate its use and visualization (T. M. Inc, 2022). In this section, we review some examples that test the main function called Octahedron_algorithm.m, which is well commented and serves as a tutorial in combination with this text. The function takes as input the octahedral parameters at sites A and B and outputs the relevant system matrices and a three-dimensional visualization of the octahedral configuration. The simplest possible case is running the command:
Octahedron_algorithm([1 1 1 90 90 90 0 0 0 1],[1 1 1 90 90 90 0 0 0 1]);
in the MATLAB command window, which constructs a system of equivalent, undistorted, unrotated octahedra with arm lengths equal to unity. The first (second) array of numbers contains the octahedral parameters at site A (site B), with the following ordering:
[a’ b’ c’ alpha’ beta’ gamma’ theta phi_x phi_y f].
The function also accepts several optional arguments (documented in the code) that allow the manipulation of different visual elements of the system, such as colors, unit-cell drawings, and lattice extent. The basic example above is illustrated in Figure 6A, along with other octahedral configurations that the reader is encouraged to test. Figure 6B shows the formation of the stereotypical breathing mode by alternating the octahedral arm lengths between the sites. Figure 6C shows an example of in-plane bipartite rotation, encountered in the surface layer of Sr2RuO4 and the bulk of Sr3Ru2O7 (Morales et al., 2023). Figures 6D, E illustrate how octahedral non-orthogonality alone may lead to different types of lattices. Finally, Figure 6F shows combined octahedral distortions and rotations that lead to an intricate configuration.
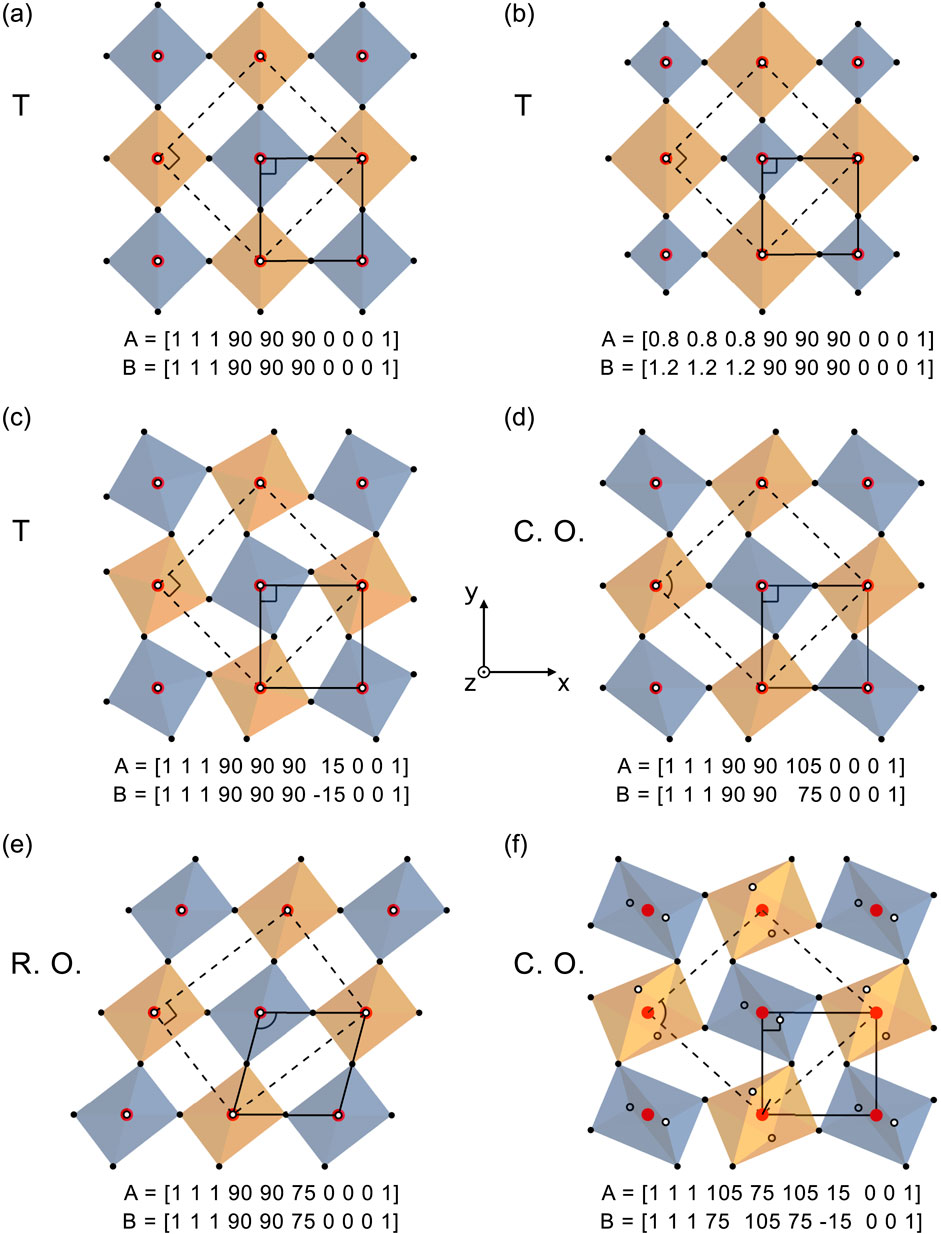
Figure 6. Examples of octahedral configurations built using the 4-octahedral parametrization. In each case, the arrays A and B are the input parameters of the Octahedron_algorithm.m function. The type of lattice is indicated, where the tetragonal cell is drawn using a black line and the primitive unit cell is shown with a dashed line. The top (bottom) apical corners are shown with white-filled (empty) open circles. (A) Basic 4-Octahedra configuration. (B) A simple octahedral breathing mode. (C) An example of in-plane bipartite rotation. (D,E) Octahedral non-orthogonality leading the formation of centered orthorhombic and rectangular orthorhombic lattices, respectively. (F) Complex octahedral configuration from combined in-plane rotation and non-orthogonal distortions.
1.12 A real example
The parametrization developed so far is quite general and can be employed to describe much more complicated geometries than the examples provided above (see Figure 5). More intuitively, we can test it on systems with a highly symmetric octahedral configuration, such as perovskites. Figure 7 shows contiguous planes of corner-sharing
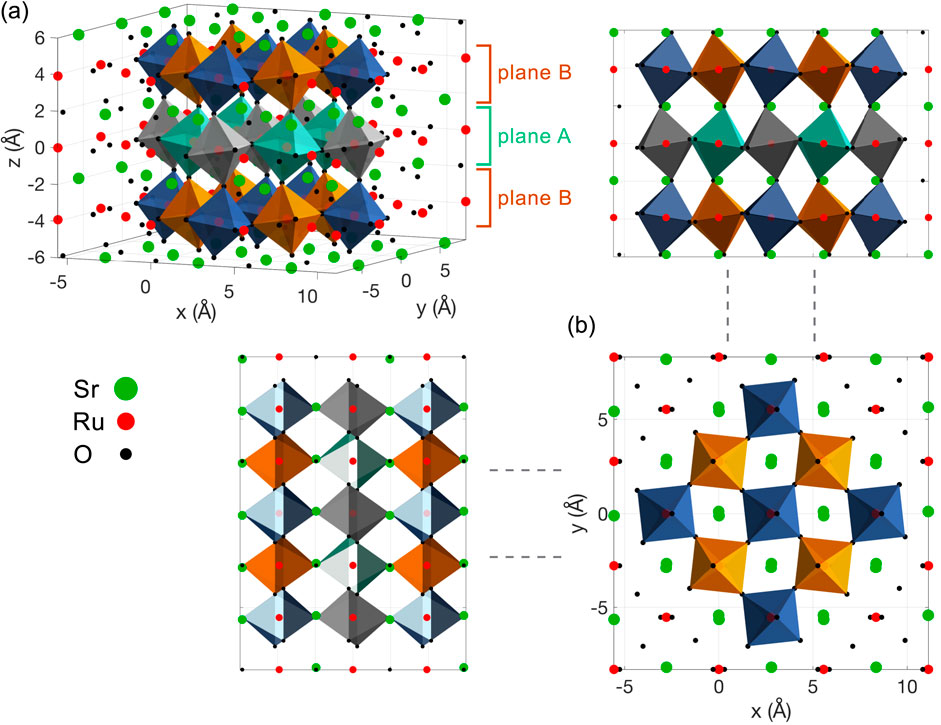
Figure 7. Parametrization of the octahedra in
The reader is encouraged to test this by running SrRuO3_lattice.m in the MATLAB command window. The first part of the routine builds the
2 The 4-Octahedra model under strain
2.1 Constitutive equations
The connection we have established between the global properties of the lattice and the local octahedral configuration allows us to tune the former to derive the possible outcomes of the latter. In experiments involving the epitaxial strain, for example, where an adequate substrate is chosen to vary the in-plane lattice parameters of a specimen layer or heterostructure (Paris et al., 2020), the control is always on the global properties of the lattice, more specifically the lattice vectors. There is no such method (yet) as to manipulate a single octahedron and study its effect on its surroundings. Instead, we tune octahedra indirectly by changing macroscopic parameters. In this context, we can apply the laws of continuum mechanics to the lattice and use the 4-octahedra parametrization to see how these adjustments affect the local octahedral configuration.
Away from strain gradients, such as in the central region of a crystal being compressed by a vice, the strain configuration of a system is characterized by a constant strain tensor. In two dimensions, this corresponds to the knowledge of three quantities
which represents the extent of the 4-octahedra along the out-of-plane direction, that is, we can think of the vectors
where
Evaluating Equation 65 at
where
which shows an elegant relationship between the global strain
Thus, expanding
and substituting into Equation 72 yields
where
The decomposition in Equation 77 states that the global strain configuration of the lattice
2.2 Final 4-octahedral configuration: limit cases
The ultimate goal of this work is to determine the final configuration of the 4-octahedra for a given applied strain. In principle, this is quite straightforward because we can calculate the
assuming that we know the original geometry of the system
Nevertheless, the
2.3 Final 4-octahedra configuration: longitudinal limit
If
In order to solve for
Because the
which must be diagonal by definition of the
and represented visually in Figure 8. In general, the scalar fields in the longitudinal limit are obtained from Equations 72 and 86 as follows:
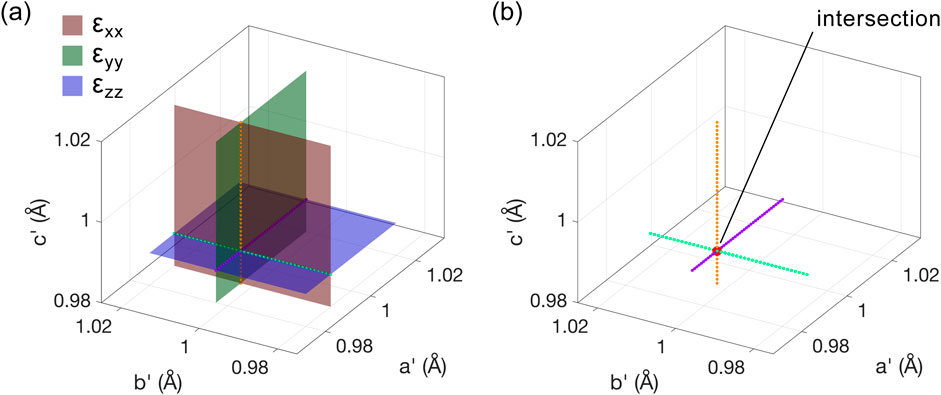
Figure 8. Example solution in the longitudinal limit for a system of equivalent, undistorted, unrotated octahedra with arm lengths equal to unity, subjected to the strain configuration given by
The MATLAB function called Octahedron_strain.m is designed to reproduce this (see Example 1 in the function header) and the following examples in an attempt to provide solutions for the octahedral configuration within the strain limits being discussed.
2.4 Final 4-octahedra configuration: distortional limit
If
which we want to solve for
such that
An example of the distortional limit is given in Figure 9. The starting configuration is the one in Figure 6C, with an in-plane bipartite rotation of 15°. We are interested in a solution with
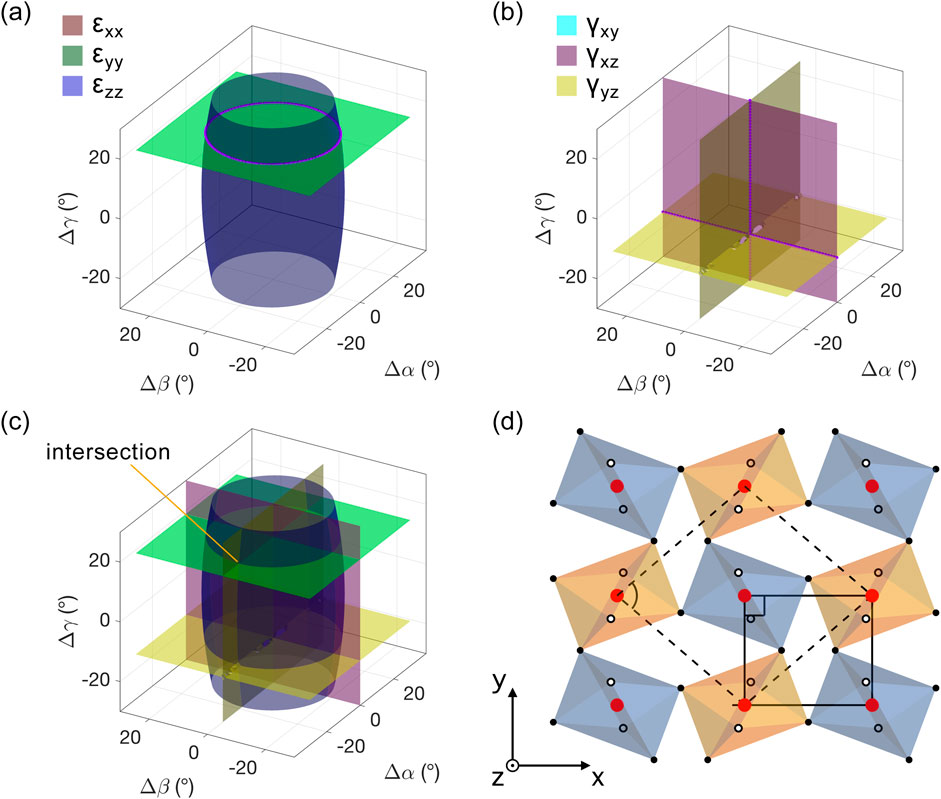
Figure 9. Example solution in the distortional limit for the system of octahedra with in-plane bipartite rotation shown in Figure 6C. (A) Longitudinal strain field isosurfaces for
2.5 Final 4-octahedra configuration: rotational limit
Finally, if
Because
where the matrix in parenthesis is simply
The rotational limit in the surface layer of
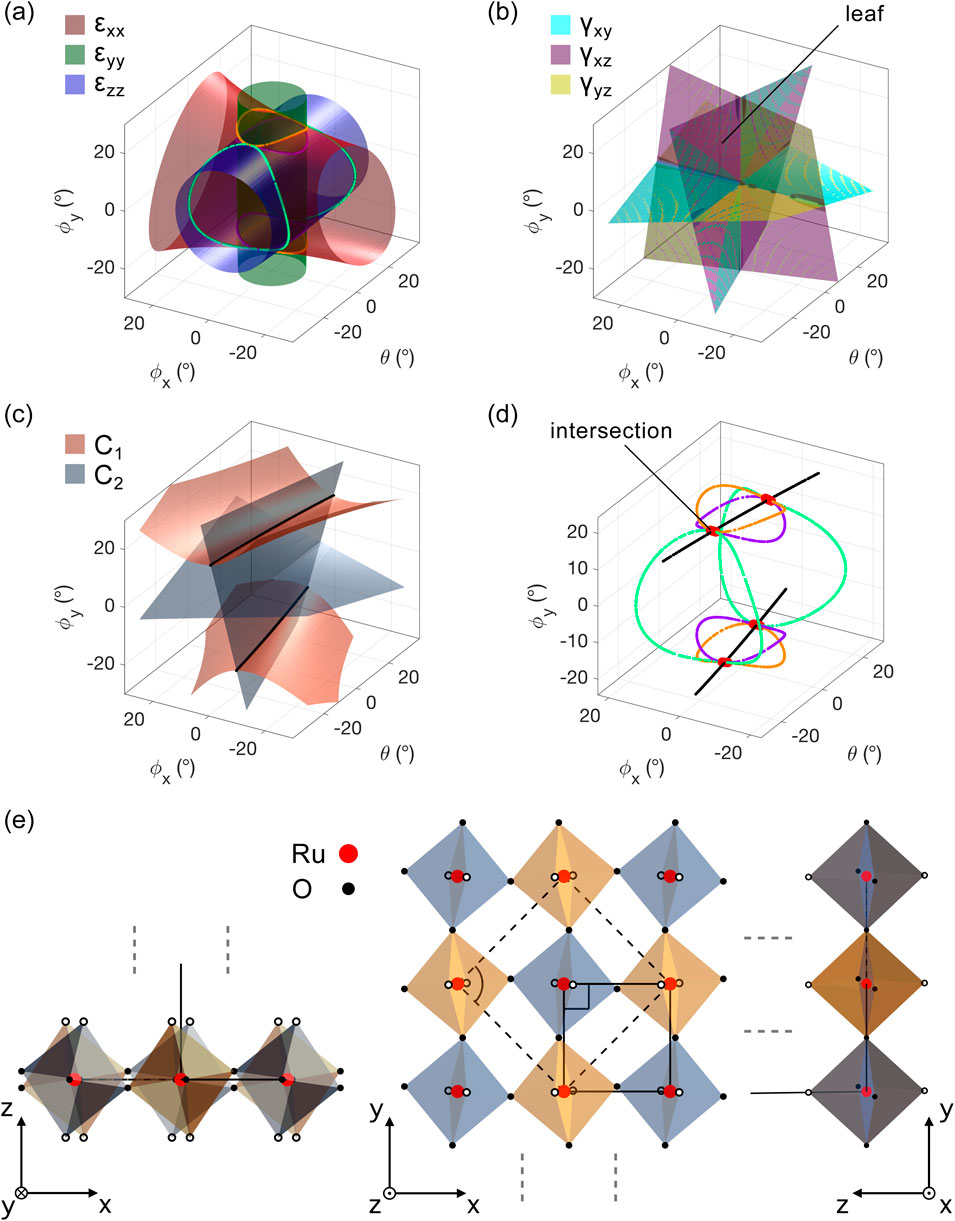
Figure 10. The surface layer of
Figures 10A, B show the longitudinal and shear strain field isosurfaces, respectively. The longitudinal isosurfaces intersect in four regions (see the color contours in Figure 10D). The value of
2.6 Final 4-octahedra configuration: general case
If a particular system is studied away from the limits above and the global strain is shared between the different microscopic mechanisms described in Equation 77, the procedure to find the solution space becomes quite elaborate. One must build the
3 Discussion
The value of the 4-octahedral model developed in this study can be regarded as technical, experimental, and theoretical. The single octahedron parametrization defined in Sections 1.2 and 1.3 can be readily used to extract the octahedral parameters from many crystal structures and could well be employed to define a standard to measure arm-lengths, orthogonality deviations, rigid rotations, and apical distortions. Furthermore, the general 4-octahedral model built in Sections 1.4–1.8 provides stringent conditions for systems of up to four inequivalent sites to link and form a two-dimensional lattice, while in Section 1.9, we provided a procedure to find such conditions in systems with three dimensions and
The particular case of a bipartite lattice was thoroughly studied and linked to real experimental situations, both for the description of perovskites in Section 1.9 and for the analysis of the surface electronic structure of
Future work that would considerably enrich this work involves the development of a mathematical framework to efficiently carry out such procedures and methods to find, classify, and study the structure of the large solution space described by Equations 77, 85. On the experimental front, the community already shows signs of interest toward the simulation of low-energy electron diffraction (LEED) patterns, benefiting from the rigorous and systematic control of the octahedral geometry provided in this study.
4 Conclusion
The 4-octahedral model provides a rigorous and tunable parametrization of systems of corner-sharing octahedra. The map between the global properties of the lattice and the local octahedral configuration allows for investigating the microscopic geometric response to applied strain and further classifying it into different mechanisms (see Equation 77). Although two-dimensional in nature, the model can be readily generalized to three dimensions by following a similar approach to the one presented in this study. Furthermore, when used as the geometric input in different types of calculations (ab initio tight binding models (Morales et al., 2023), for example), it provides a powerful and inexpensive benchmark to test the effects that octahedral distortions and rotations have on the electronic structure of many quantum materials.
Data availability statement
The original contributions presented in the study are included in the article/Supplementary Material; further inquiries can be directed to the corresponding author.
Author contributions
EM: writing–original draft and writing–review and editing.
Funding
The author declares that financial support was received for the research, authorship, and/or publication of this article. The author was directly funded by the Max Planck Society as part of their post-doctoral research position at the Max Planck Institute for Chemical Physics of Solids.
Acknowledgments
The author is grateful to Prof. Phil D. C. King for his support and valuable comments during the development of this model and his supervisor Berit H. Goodge for her useful remarks and suggestions during the writing of this manuscript.
Conflict of interest
The author declares that the research was conducted in the absence of any commercial or financial relationships that could be construed as a potential conflict of interest.
Publisher’s note
All claims expressed in this article are solely those of the authors and do not necessarily represent those of their affiliated organizations, or those of the publisher, the editors, and the reviewers. Any product that may be evaluated in this article, or claim that may be made by its manufacturer, is not guaranteed or endorsed by the publisher.
Footnotes
1The method decomposes a square matrix into a product of an element of
2Note that
3Naturally,
4These are lattice vectors only if sites A and B are equivalent (see Figure 5).
5Without loss of generality, this defines a fixed body point for the displacement field.
6In this section, the use of a zero index refers to the original configuration, and its absence refers to the strained system.
7That is, we address the global rotational freedom of the strained configuration to match the one of the unstrained system.
8Here,
References
Ali, Z., Saghayezhian, M., Wang, Z., O’Hara, A., Shin, D., Ge, W., et al. (2022). Emergent ferromagnetism and insulator-metal transition in delta-doped ultrathin ruthenates. npj Quantum Mater. 7 (1), 108. doi:10.1038/s41535-022-00518-7
Angel, R., Zhao, J., Ross, N., Jakeways, C., Redfern, S., and Berkowski, M. (2007). High-pressure structural evolution of a perovskite solid solution (La1-xNdx)GaO3. J. Solid State Chem. 180 (12), 3408–3424. doi:10.1016/j.jssc.2007.09.019
Angel, R. J., Zhao, J., and Ross, N. L. (2005). General rules for predicting phase transitions in perovskites due to octahedral tilting. Phys. Rev. Lett. 95 (2), 025503–503. doi:10.1103/physrevlett.95.025503
Aso, R., Kan, D., Shimakawa, Y., and Kurata, H. (2013). Atomic level observation of octahedral distortions at the perovskite oxide heterointerface. Sci. Rep. 3 (1), 2214. doi:10.1038/srep02214
Balachandran, P. V., and Rondinelli, J. M. (2013). Interplay of octahedral rotations and breathing distortions in charge-ordering perovskite oxides. Phys. Rev. B 88 (5), 054101–101. doi:10.1103/physrevb.88.054101
Berner, P. (2008). “Technical concepts: orientation, rotation, velocity and acceleration, and the SRM,” TENA (test & training enabling architecture) project by SEDRIS 21. Tech. Rep.
Gardner, J., Balakrishnan, G., and Paul, D. M. (1995). Neutron powder diffraction studies of Sr2RuO4 and SrRuO3. Phys. C. Supercond. 252 (3-4), 303–307. doi:10.1016/0921-4534(95)00495-5
Glazer, A. M. (1972). The classification of tilted octahedra in perovskites. Acta Crystallogr. B Struct. Cryst. Cryst. Chem. 28 (11), 3384–3392. doi:10.1107/s0567740872007976
Grosso, B. F., and Spaldin, N. A. (2021). Prediction of low-energy phases of BiFeO3 with large unit cells and complex tilts beyond Glazer notation. Phys. Rev. Mater. 5 (5), 054403–403. doi:10.1103/physrevmaterials.5.054403
Hammonds, K. D., Bosenick, A., Dove, M. T., and Heine, V. (1998). Rigid unit modes in crystal structures with octahedrally coordinated atoms. Am. Mineral. 83 (5-6), 476–479. doi:10.2138/am-1998-5-607
He, J., Borisevich, A., Kalinin, S. V., Pennycook, S. J., and Pantelides, S. T. (2010). Control of octahedral tilts and magnetic properties of perovskite oxide heterostructures by substrate symmetry. Phys. Rev. Lett. 105 (22), 227203–203. doi:10.1103/physrevlett.105.227203
Herklotz, A., Wong, A. T., Meyer, T., Biegalski, M. D., Lee, H. N., and Ward, T. Z. (2016). Controlling octahedral rotations in a perovskite via strain doping. Sci. Rep. 6 (1), 26491–26497. doi:10.1038/srep26491
Howard, C. J., and Stokes, H. T. (1998). Group-theoretical analysis of octahedral tilting in perovskites. Acta Cryst. B 54 (6), 782–789. doi:10.1107/s0108768198004200
Liao, Z., Huijben, M., Zhong, Z., Gauquelin, N., Macke, S., Green, R. J., et al. (2016). Controlled lateral anisotropy in correlated manganite heterostructures by interface-engineered oxygen octahedral coupling. Nat. Mater. 15 (4), 425–431. doi:10.1038/nmat4579
Lu, W., Dong Song, W., He, K., Chai, J., Sun, C. J., Chow, G. M., et al. (2013). The role of octahedral tilting in the structural phase transition and magnetic anisotropy in SrRuO3 thin film. J. Appl. Phys. 113 (6), 063–901. doi:10.1063/1.4790699
Morales, E. A., Siemann, G.-R., Zivanovic, A., Murgatroyd, P. A. E., Marković, I., Edwards, B., et al. (2023). Hierarchy of lifshitz transitions in the surface electronic structure of Sr2RuO4 under uniaxial compression. Phys. Rev. Lett. 130 (9), 096–401. doi:10.1103/PhysRevLett.130.096401
Paris, E., Tseng, Y., Pärschke, E. M., Zhang, W., Upton, M. H., Efimenko, A., et al. (2020). Strain engineering of the charge and spin-orbital interactions in Sr2IrO4. Proc. Natl. Acad. Sci. U.S.A. 117 (40), 24 764–824 770. doi:10.1073/pnas.2012043117
Petrov, A. Y., Torrelles, X., Verna, A., Xu, H., Cossaro, A., Pedio, M., et al. (2013). Surface octahedral distortions and atomic design of perovskite interfaces. Adv. Mater. 25 (29), 4043–4048. doi:10.1002/adma.201301841
Qian, H., Yu, Z., Lyu, C., Chen, F., Luo, Y., Liu, Y., et al. (2020). Easy-to-use model to reveal the nature of octahedral rotation transformations in perovskites. Ceram. Int. 46 (4), 4477–4483. doi:10.1016/j.ceramint.2019.10.174
Remani, C. (2013) Numerical methods for solving systems of nonlinear equations, 77. Ontario, Canada: Lakehead University Thunder Bay.
Roithmayr, C. M., and Hodges, D. H. (2016). Dynamics: theory and application of kane’s method. J. Comput. Nonlinear Dyn. 11. doi:10.1115/1.4034731
Thomas, S., Kuiper, B., Hu, J., Smit, J., Liao, Z., Zhong, Z., et al. (2017). Localized control of Curie temperature in perovskite oxide film by capping-layer-induced octahedral distortion. Phys. Rev. Lett. 119 (17), 177203–203. doi:10.1103/physrevlett.119.177203
T. M. Inc. (2022) MATLAB version: 9.13.0 (R2022b). Natick, Massachusetts, United States. Available at: https://www.mathworks.com.
Keywords: corner-sharing octahedra, octahedral tilting, octahedral distortion, perovskites, strain
Citation: Abarca Morales E (2024) The 4-Octahedra model. Front. Mater. 11:1461579. doi: 10.3389/fmats.2024.1461579
Received: 08 July 2024; Accepted: 27 August 2024;
Published: 22 October 2024.
Edited by:
Milan Radovic, Paul Scherrer Institute (PSI), SwitzerlandReviewed by:
Walber Hugo De Brito, Federal University of Minas Gerais, BrazilZhiming Wang, Chinese Academy of Sciences (CAS), China
Victor Rosendal, Technical University of Denmark, Denmark
Copyright © 2024 Abarca Morales. This is an open-access article distributed under the terms of the Creative Commons Attribution License (CC BY). The use, distribution or reproduction in other forums is permitted, provided the original author(s) and the copyright owner(s) are credited and that the original publication in this journal is cited, in accordance with accepted academic practice. No use, distribution or reproduction is permitted which does not comply with these terms.
*Correspondence: Edgar Abarca Morales, ZWRnYXIubW9yYWxlc0BjcGZzLm1wZy5kZQ==