- College of Transportation, Shandong University of Science and Technology, Qingdao, China
Sawdust, a solid waste generated during stone processing, poses a serious threat to the environment with its untreated accumulation. This paper first analyzes the chemical composition and physical properties of sawdust, and discusses its mechanism of action in cement mortar. By systematically optimizing the blending ratio and modification method of sawdust, the sawdust-modified cement mortar with excellent performance was prepared. This study evaluates the key performance indicators of sawdust-modified cement mortar, such as compressive strength, flexural strength, and durability, through a series of experiments. The experimental results indicate that the incorporation of an appropriate amount of sawdust significantly enhances the mechanical properties of cement mortar, while also improving its durability, particularly in terms of freeze-thaw resistance. Microstructural analysis reveals the mechanism by which sawdust improves the pore structure of cement mortar; the active components in the sawdust react with the hydration products of cement, resulting in the formation of crystalline structures with higher strength.Therefore, the use of sawdust as a modifier in cement mortar can improve its mechanical properties and durability, while simultaneously reducing the accumulation of solid waste and promoting the sustainable development of building materials.
1 Introduction
With the extensive exploitation of global stone resources, natural resources are also showing signs of depletion, and the ecological environment is continuously being damaged. At present, the production of waste slag from the global stone industry is huge. Conducting research on the modification of cement mortar with stone industry waste slag can help reduce waste emissions (Afonso et al., 2023). Reducing the generation of solid waste and strengthening its management can effectively decrease environmental pollution, including contamination of air, water bodies, and soil, thereby reducing environmental risks. In comparison, the preparation of traditional cement mortar involves high material costs and significant energy consumption. On the other hand, most of the waste from the stone industry is considered waste materials, which can reduce the cost of raw material procurement to a certain extent. This reduction can lower the production cost of modified cement mortar, enhance material performance, and meet the performance and environmental requirements of construction projects (Bai et al., 2015). Sawdust, as a type of solid waste, when utilized as a material for modifying cement mortar, can reduce the negative impact of waste on the environment. This approach not only mitigates environmental pollution but also achieves comprehensive utilization of resources, thereby improving the efficiency of resource utilization (Agwu et al., 2019). Sawdust, as a type of waste from the stone industry, is produced in large quantities and can improve the compressive strength, flexural strength, and durability of cement mortar (Wan et al., 2018; Gupta et al., 2019). The study analyzes the physical properties, mechanical properties, and durability of modified cement mortar, thereby enhancing the engineering performance and service life of the modified cement mortar. If properly utilized, it can help promote the transformation of the stone industry towards sustainable development, fostering the development of green production and a circular economy.
In recent years, scholars have conducted extensive and in-depth research on the preparation and properties of sawdust-modified cement mortar. The main chemical components of sawdust include SiO2, Fe2O3, CaO, MgO, K2O, Na2O, etc., which can meet the needs of most construction projects (Zhao et al., 2021). In terms of performance testing and evaluation, researchers have focused on the mechanical properties and durability indicators of cement mortar (Gupta et al., 2019). Through laboratory testing methods, the performance of sawdust-modified cement mortar has been evaluated. To address the accumulation of sawdust and achieve the resource utilization of solid waste, experimental studies on the mechanical properties of composite materials and their engineering applications have been conducted (Li et al., 2024; Liang et al., 2023). Cheng and colleagues used cement, lime, and fly ash as modifying materials to study the impact of the amount and mix ratio of composite materials on the strength of modified sawdust. Based on the physical and chemical properties of sawdust, it has been improved by incorporating sawdust into composite materials with different ratios. Unconfined compressive strength tests were conducted under both water-saturated and non-water-saturated curing conditions (Li et al., 2024). Liang and colleagues systematically studied the feasibility of using sawdust to replace fly ash in ready-mixed concrete and to form a mixed sand with manufactured sand for the preparation of C30 and C40 concrete. They also discussed the impact of the proportion of sawdust on the performance of concrete. The research results indicated that the physical properties of sawdust differ from those of granite powder. As the proportion of sawdust in concrete increases, the flowability of the fresh concrete decreases, the slump loss becomes greater, the cohesion and encasement performance deteriorate, and the setting time is prolonged. The incorporation of sawdust in concrete makes it more susceptible to cracking, that is, it is more prone to early cracking phenomena (Liang et al., 2023). Wan and colleagues used sawdust to replace river sand in the preparation of autoclaved aerated concrete (AAC), and the study results showed that AAC prepared with sawdust and river sand has good thermal insulation properties. As the amount of stone sawdust replacing river sand gradually increases, the bulk density and compressive strength of the aerated concrete gradually increase (Wan et al., 2018). Dang and colleagues studied the flexural strength of beams composed of two different binders, exploring factors such as pore size, crack location, viscosity, and interfacial surface roughness. The study results indicated that cement has strong bonding strength at the interface, and other factors are more important causes of weaknesses (Dang et al., 2011). Subramanian and colleagues found that cemented sand with lower cement content can achieve similar strength to cemented clay with higher cement content (Subramanian and Ku, 2023).
Researchers have investigated the impact of various mix designs on cement mortar performance, aiming to optimize the preparation process. Zhang using granite sawdust, fly ash, and desulfurized gypsum as basic raw materials and ordinary Portland cement as the main binding material, carried out mix design through orthogonal experiments and prepared concrete blocks with different compositions using two methods: static pressing and extrusion molding. The study focused on the impact of the incorporation of various solid waste amounts on the mechanical properties of concrete and the preparation process (Zhang et al., 2023).
Sawdust contains a high amount of impurities, mixed with a large amount of crushed stone and soil, and has a complex composition, with an average content of iron and calcium reaching 3%–4%. Traditional technological processes find it difficult to utilize it in large quantities (Zhong et al., 2021). In addition to China, research in other countries mainly includes the types and properties of sawdust modifiers, optimization of preparation processes, and performance testing and evaluation (Abdellahi and Hejazi, 2015). Scholars from various countries have made various attempts, focusing mainly on the comprehensive improvement and stabilization effects of composite materials on sawdust, comparing the physical and mechanical properties of modified sawdust, and achieving the synergistic utilization of solid waste (Abbasi et al., 2020).
This study primarily investigates the chemical composition, physical properties, and particle size distribution of sawdust, analyzing its potential and feasibility as a modifying material. The research examines the impact of different sawdust contents on the basic properties of cement mortar, such as flowability. Experimental data are utilized to analyze the improvement effects of sawdust on the mechanical properties (e.g., compressive strength, flexural strength) and durability (e.g., water resistance, freeze-thaw resistance) of cement mortar. The role of sawdust in cement mortar is explored through microscopic observation and chemical analysis to understand its mechanism of action. Laboratory tests are conducted to assess its adaptability and durability under various environmental conditions, providing theoretical basis and technical support for practical applications.
2 Materials and methods
2.1 Experimental materials
The experimental materials used for the preparation of sawdust-modified cement mortar in this study mainly include cement, ordinary river sand, and sawdust, etc.
2.1.1 Cement
The cement used in this experiment is PI42.5 Portland cement, whose properties all meet the specifications outlined in the “General Portland Cement” (GB175–2023) standard (National Standard of the People's Republic of China, 2024). The chemical composition and various performance indicators of the cement used are shown in Tables 1–4.
The performance test results of the benchmark mortar with mineral admixtures (additives) are shown in Table 5.
2.1.2 River sand
The apparent density of the river sand used in the experiment is 2.64 g/cm³, and the sieve residue greater than 80 μm is 11%. The main chemical composition is shown in Table 6.
2.1.3 Sawdust
The physical properties of the sawdust used in the experiment are presented in Table 7, and the particle size distribution is shown in Table 8.
2.1.4 Microstructure of sawdust
The micromorphology of the sawdust was characterized using scanning electron microscope (SEM).
As observed in Figure 1, the sawdust particles exhibit irregular shapes with varying sizes and a relatively uniform distribution. The particle sizes range from tens of micrometers to hundreds of micrometers, with some particles aggregated into clusters. The surface of the particles is generally rough, with sharp edges, likely due to mechanical cutting and grinding during the processing. Tiny cracks and pores can be observed on the particle surfaces, which may affect the physical and chemical properties of the particles. Curing conditions, such as temperature and humidity, as well as the uniformity of mixing and stirring, can all lead to the formation of pores and cracks. The interfaces between particles are relatively clear, with some particles having adhering fine particles or impurities on their surfaces. The particle size varies significantly, covering a range from tens to hundreds of micrometers, demonstrating the diversity of the particles.
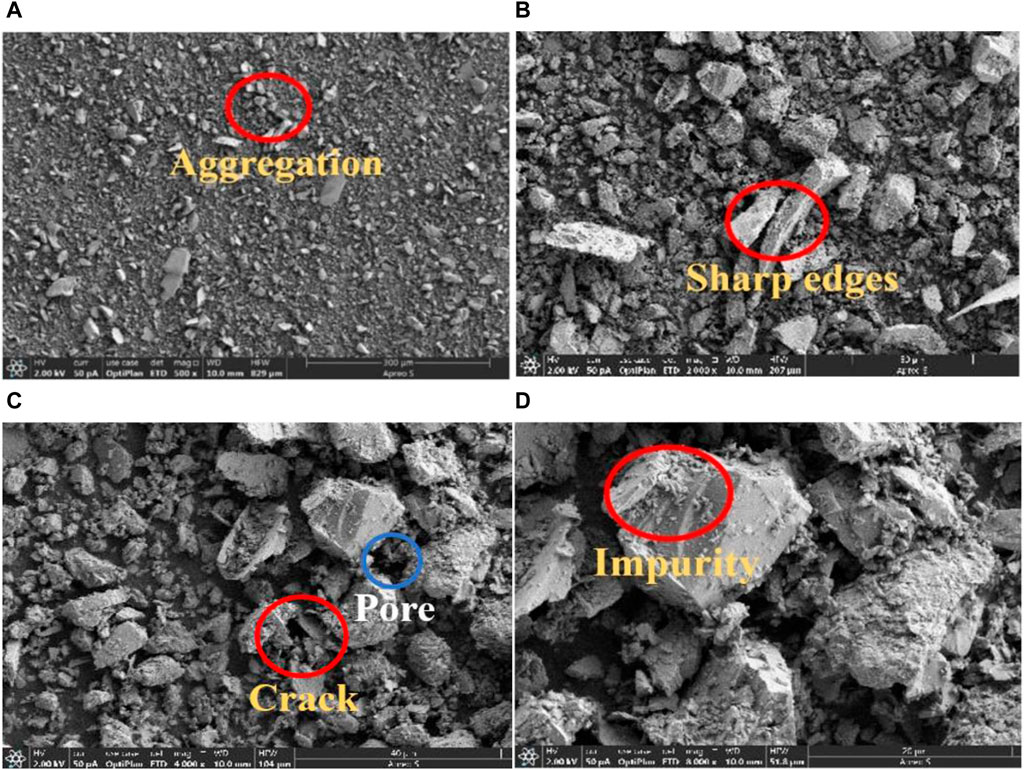
Figure 1. Scanning electron microscope (SEM) test results of sawdust. (A) 500×; (B) 2000×; (C) 4000×; (D) 8,000×.
Through SEM micro testing and analysis of sawdust, the following conclusions can be drawn: the irregular shape and rough surface of the sawdust particles endow them with good adhesion and filling capacity in certain applications (Wang et al., 2022). Sawdust can also be used as a filler for building materials, a soil conditioner, or for other industrial purposes, with specific applications requiring further testing of physical and chemical properties (Zhang et al., 2024). A thorough analysis of the microstructure and chemical composition of sawdust helps to develop its recycling value and reduce the environmental impact of waste.
2.2 Preparation of sawdust-modified cement mortar
2.2.1 Mix proportioning design
The experiment was conducted in accordance with the specifications of the ‘Standard for Test Method of Basic Properties of Construction Mortar’ (JGJ/T 70–2009) (Chinese Standard, 2009) and the ‘Method of Testing Cements—Determination of Strength of Cement Mortar (ISO Method)' (GB/T 17671–2021) (Standardization Administration of China, 2021), as well as the mix proportioning design from preliminary exploratory experiments and the experience of predecessors. The water-to-cement ratio was set to 0.5, and the cement-to-sand ratio was 1:3. The incorporation rate of sawdust was varied, with dried and finely ground sawdust powder mixed into the cement mortar at rates of 0%, 5%, 10%, 15%, 20%, and 25% by the mass of cement. The mix proportioning design for the cement mortar is shown in Table 9.
2.2.2 Specimen fabrication process and procedure
Figure 2 illustrates the fabrication process of sawdust-modified cement mortar.
During the experimental process, a forced mixer was used to ensure the quality and uniformity of the cement mortar. Before the experiment, the bottom and sides of the mold were coated with an oil-based release agent to facilitate demolding after curing the specimens to the specified age. The ambient temperature for the experiment was approximately 25°C. When preparing the sawdust-modified mortar, cement, sand, and sawdust (0%, 5%, 10%, 15%, 20%, 25%) were first mixed in a mixer at low speed for 30 s according to the ratio. Then, an appropriate amount of water was added, and high-speed mixing was initiated for another 30 s. After that, mixing was stopped for 90 s, and during the last 15 s of the pause, the mortar on the inner wall and blades of the mixer was quickly scraped off with a rubber spatula and incorporated into the mix. Finally, after an additional 60 s of high-speed mixing, the sawdust-modified mortar was obtained. The mortar was quickly tested for flow and other properties, or it was poured into molds, demolded after setting, and then cured to the specified age before undergoing strength, water absorption, and durability tests.
2.3 Experimental methods
2.3.1 Flowability test
The flowability test of the cement mortar is conducted according to the ‘Test method for flowability of cement mortar’ (GB/T 2419–2005) (Standardization Administration of China, 2005). The sawdust-modified mortar is prepared following the process flow described in the previous sections, and the freshly mixed mortar is filled into a conical mold in two portions for the flowability test.
2.3.2 Water absorption test
The fine pore water absorption test is conducted in accordance with the German standard ‘Determination of the Water Absorption Coefficient of Construction Materials’ (DIN 52617) (Deutsches Institut für Normung, 2020). After curing the specimens to the standard age, they are placed in an oven at 70°C for 48 h. Once the specimens have cooled to room temperature, their sides are sealed, and their upper surfaces are submerged in a constant temperature water bath for the water absorption test.
2.3.3 Flexural strength test
The determination of the flexural strength of the cement mortar is conducted according to the ‘Method of Testing Cements—Determination of Strength of Cement Mortar (ISO method)' (GB/T 17671–2021) (Standardization Administration of China, 2021). Specimens of size 40 mm × 40 mm × 160 mm are placed on the supporting cylinders of the testing machine with one of their sides facing down, to perform the flexural strength test.
2.3.4 Compressive strength test
The determination of the compressive strength of the cement mortar is conducted in accordance with the ‘Method of Testing Cements—Determination of Strength of Cement Mortar (ISO method)' (GB/T 17671–2021) (Standardization Administration of China, 2021). After the flexural strength test, the remaining half-prismatic specimens are placed on the testing machine to perform the compressive strength test.
2.3.5 Water resistance test
Modified mortar specimens with dimensions of 70 mm × 70 mm × 70 mm, prepared according to the procedures described in the previous sections, are placed in a constant temperature chamber at 20°C for a 24-h soak the day before the completion of the 7 d and 14 d curing periods for batches II0, II1, II2, II3, II4, and II5. Meanwhile, batches I0, I1, I2, I3, I4, and I5, serving as control groups, are returned to the curing box for continued curing for 24 h. The water level during the soak should be 20 mm above the upper surface of the specimens. After soaking, the specimens are removed, the surface moisture is wiped off, and their appearance is observed. The water resistance specimens and the control group specimens are then subjected to a compressive strength test simultaneously.
2.3.6 Freeze-thaw resistance test
The freeze-thaw resistance test of the modified mortar is conducted in accordance with the relevant provisions of the ‘Standard for Test Method of Basic Properties of Construction Mortar’ (GB/T 70–2009) (Chinese Standard, 2009).
After the curing period, the modified mortar specimens with dimensions of 70 mm × 70 mm × 70 mm, prepared according to the procedures described in the previous sections, are removed from the curing chamber and their original appearance is inspected and recorded. Subsequently, the specimens are immersed in water at a temperature of 15–20°C for 2°days of curing, then removed and the surface moisture is wiped off. The modified mortar specimens are grouped according to the incorporation rates (0%, 5%, 10%, 15%, 20%, 25%) and subjected to freeze-thaw resistance tests.
2.3.7 Microscopic mechanism analysis test
Analysis using Scanning Electron Microscope (SEM) was conducted to verify the mechanisms predicted by the aforementioned test results and to study the impact of sawdust powder on the microstructure of cement-based materials. To obtain SEM images, modified mortar specimens were divided into groups T1, T2, T3, and T4 according to the sawdust incorporation rates (5%, 10%, 15%, 20%), with a control group T0 without sawdust addition. Small samples of approximately 10 mm × 10 mm × 10 mm were taken from the center of the cement mortar specimens after 14 days of curing, and then dried in a constant temperature oven at 70°C for 2°days before being removed. After sample preparation, the microstructures were observed under a Scanning Electron Microscope.
3 Results and discussion
3.1 Flowability test
Good flowability endows building materials with excellent engineering properties.
Figure 3 reveals that the incorporation of sawdust causes the flowability of cement mortar to first increase and then decrease. The flowability of the modified cement mortar tends to gradually increase with sawdust content from 0% to 10%, and then gradually decreases as the sawdust content exceeds 10% of the cement. When the sawdust content is 5%, 10%, and 15%, the flowability of the sawdust-modified mortar increases by 7.40%, 9.04%, and 6.57% respectively compared to the control group. When the sawdust content is 20% and 25%, the flowability of the sawdust-modified mortar decreases by 1.40% and 4.38% respectively compared to the control group.
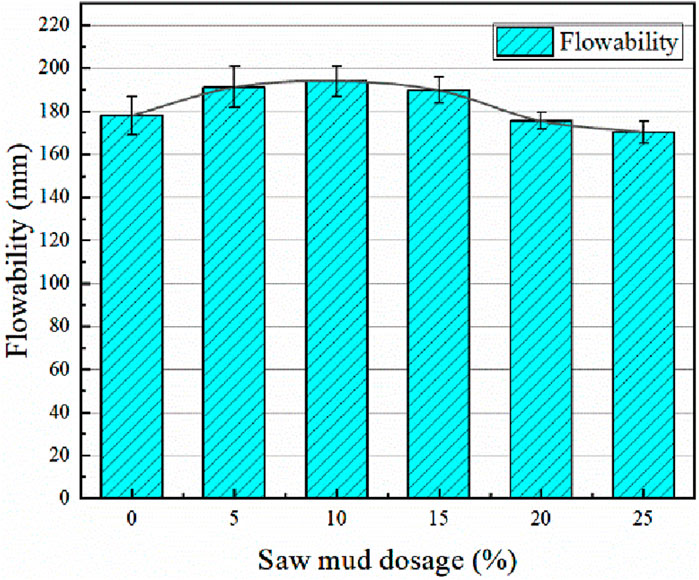
Figure 3. The influence of different sawdust incorporation rates on the flowability of cement mortar.
The reasons for the initial increase and subsequent decrease in the flowability of modified mortar with the increase of sawdust content are as follows: The initial increase is due to the fact that sawdust is essentially a high-quality stone powder with fine particle size, dense texture, and low water absorption rate. When the particle size of sawdust is finer than that of cement, the sawdust particles fill the gaps between cement particles, improving the particle gradation of the cementitious material, which favors the flow of the paste and thus increases the flowability of the mortar (Cannone Falchetto et al., 2018). The subsequent decrease may be attributed to the addition of sawdust, which increases the mass of solids in the mortar, leading to a relatively higher proportion of solids and a relatively lower proportion of free water in the system, thereby reducing the flowability of the mortar (Walther et al., 2019). The incorporation of sawdust can enhance the fluidity of cement mortar, facilitating more uniform spreading and filling during the construction process. However, the amount of sawdust added must be carefully controlled, as an excessive amount may reduce the compressive and flexural strengths of the cement mortar, as well as potentially affecting its bonding strength and water penetration resistance.
3.2 Water absorption test
Mortar with low water absorption can reduce the penetration of harmful ions from water into its interior, decreasing the damage to the mortar’s structure, thereby enhancing the durability of construction projects.
Figure 4 indicates that after the capillary water absorption rate of the modified mortar specimens reached stability at the 7 d curing age, the capillary water absorption rate of the sawdust-modified mortar specimens first decreased, then increased, and subsequently decreased again with the increase in sawdust content. Once the capillary water absorption rate stabilized, at sawdust contents of 5%, 20%, and 25%, it decreased by 7.82%, 17.39%, and 5.63% respectively compared to the control group. At sawdust contents of 10% and 15%, the capillary water absorption rate increased by 0.77% and 5.36% respectively compared to the control group. This suggests that in this study, the influence of sawdust on the capillary water absorption rate of the cement mortar specimens has a peak value, which is around 15%, and at this content, the capillary water absorption rate of the modified mortar specimens is higher than that of the control group. After the capillary water absorption rate of the modified mortar specimens reached stability at the 14 d curing age, the capillary water absorption rate first decreased and then increased with the increase in sawdust content. It is noteworthy that compared to the 7 d curing group, the final increase is not observed.
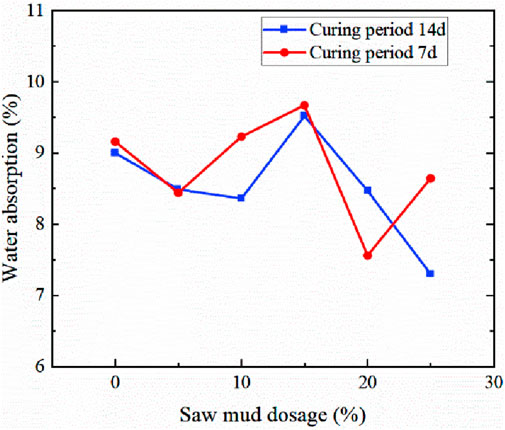
Figure 4. The influence of different sawdust incorporation levels on the water absorption of cement mortar.
The initial increase in water absorption may be attributed to the fact that an appropriate amount of sawdust can fill the pores within the mortar, increasing its compactness, which effectively reduces the infiltration of free water and thus lowers the water absorption rate of the mortar specimens (Sivrikaya et al., 2014). The subsequent decrease in water absorption may be due to the continued increase in sawdust content, leading to a significant increase in the content of harmless and slightly harmful pores, thereby increasing the capillary water absorption rate (Wang et al., 2022). The water absorption rate decreases again possibly because, with a further increase in sawdust content, the filling effect of the sawdust itself takes the leading role again, reducing the capillary water absorption rate (Pastor et al., 2023). Finally, the increase in water absorption may occur because, with further increases in the content, the sawdust itself introduces more pores and defects, which may offset the densification effect brought by the increased content, causing the water absorption rate to rise (Asadi Shamsabadi et al., 2018). Compared with the 7 d curing group, the 14 d curing group lacks the final increase because the different curing times lead to different degrees of hydration; the hydration reaction (Lu et al., 2020) at 14°days is nearly complete, and the pore structure has become stable, so the water absorption rate no longer increases significantly with the increase in sawdust content (Wang et al., 2022).
3.3 Flexural strength test
The mechanical strength of cement-based materials directly affects the safe use and reliability of building structures. Compressive and flexural strength tests were conducted on sawdust-modified cement mortar specimens.
Figure 5 reveals that the flexural strength of sawdust-modified mortar specimens exhibits an increasing and then decreasing trend with the increase of sawdust content under different curing ages. Upon closer examination, it can be observed that at the 7 d curing age, the flexural strength of the modified mortar specimens was the highest at a sawdust content of 20%. At the 14 d curing age, the flexural strength was the highest at a sawdust content of 15%, and both were higher than that of the control group at different curing ages. When the content of sawdust powder continued to increase, the flexural strength of the modified mortar specimens showed a declining trend but remained greater than the flexural strength of the control group’s mortar specimens.
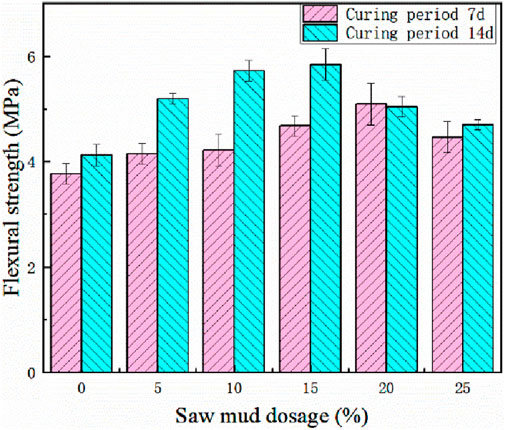
Figure 5. The influence of different sawdust incorporation levels on the flexural strength of cement mortar at various ages.
The reasons why sawdust powder can improve the flexural strength of cement mortar specimens are as follows: on one hand, the incorporation of sawdust powder can fill the pores within the mortar, slightly reducing the porosity of the specimens and increasing the compactness of the mortar, thereby enhancing the flexural strength of the mortar specimens; on the other hand, sawdust powder can act as a reinforcing material within the cement mortar, further improving the flexural strength of the mortar specimens. Moreover, the micro-aggregate effect of sawdust powder in the mortar also contributes to the enhanced flexural strength of the modified mortar specimens (Chen et al., 2021).
Additionally, it can be observed that, at the same incorporation rate, the flexural strength of the same type of sawdust-modified mortar specimens increases with the extension of the curing age, which is the result of the degree of cement hydration becoming more complete with time (Lu et al., 2020).
At a curing age of 7°days, the flexural strength of specimens with sawdust contents of 5%, 10%, 15%, 20%, and 25% increased by 10%, 11.84%, 23.95%, 35%, and 18.42% respectively. When the curing age was 14 days, the flexural strength of sawdust-modified mortar specimens with contents of 5%, 10%, 15%, 20%, and 25% increased by 25.91%, 38.84%, 41.65%, 22.28%, and 14.04% respectively; thus, the filling effect of sawdust is quite good, making the concrete structure more compact after the incorporation of sawdust.
3.4 Compressive strength test
The compressive strength of cement-based materials is closely related to their degree of compaction, and insufficient compressive strength can severely affect the quality and safety of construction projects.
Figure 6 indicates that the compressive strength of sawdust-modified mortar specimens exhibits an increasing and then decreasing trend with the increase of powder content at different curing ages. Upon closer examination, it is observed that at a 7 d curing age, the compressive strength of the modified mortar specimens is the highest at a sawdust content of 20%, and then gradually decreases with the further increase of sawdust powder content. At a 14 d curing age, the compressive strength is the highest at a sawdust content of 10%, after which the compressive strength of the modified mortar specimens gradually decreases with the increase of sawdust powder content. Moreover, at other contents, the compressive strength of the modified mortar specimens is higher than that of the control group’s mortar specimens. Therefore, the incorporation of an appropriate amount of sawdust can effectively improve the compressive strength of the specimens.
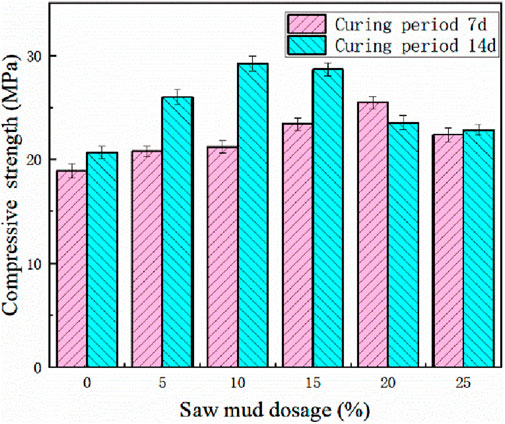
Figure 6. The influence of different sawdust incorporation levels on the compressive strength of cement mortar at various ages.
The reasons for this phenomenon are essentially the same as the influence of sawdust on the flexural strength of the mortar specimens, which is the filling effect of sawdust powder within the cement mortar (Chen et al., 2021). When the sawdust content exceeds the optimal content, the compressive strength of the modified mortar specimens begins to gradually decrease. This is because an excess of sawdust powder is prone to agglomeration. When the content exceeds the optimal value, sawdust can cause the sand to become loose and lead to an increase in the porosity of the mortar (Pastor et al., 2023), and at the same time, an excess of sawdust powder will hinder the degree of cement wrapping around the sand particles (Ma et al., 2023). These factors lead to a reduction in the compressive strength of the modified mortar specimens due to an excess of sawdust powder. Further observation of Figure 6 shows that the compressive strength of modified mortar specimens with sawdust contents of (5%, 10%, 15%, 20%, 25%) increased by 9.93%, 12.25%, 23.87%, 34.86%, 18.30% relative to the control group at a 7 d curing age, and increased by 25.88%, 41.41%, 38.70%, 13.98%, 10.06% at a 14 d curing age, respectively.
3.5 Water resistance test
Figure 7 demonstrates that with the increase of sawdust content, the compressive strength of cement mortar under both soaked and unsoaked conditions first increases and then decreases, yet remains higher than when the sawdust content is zero. Moreover, the softening coefficient is maximized at a sawdust content of 15%. For specimens with a curing age of 7°days, the calculated softening coefficient (Li et al., 2023) is 0.84 when the sawdust content is zero, and 0.93 when the sawdust content is 15%. For specimens with a curing age of 14°days, the calculated softening coefficient is 0.88 when the sawdust content is zero, and 0.95 when the sawdust content is 15%. Therefore, the incorporation of an appropriate amount of sawdust into cement mortar can improve its water resistance. The reason for this improvement is primarily due to the fine particles of sawdust, which fill the gaps between cement particles and contribute to compaction (Poulikakos et al., 2022). Additionally, some active metal oxides present in the sawdust participate in reactions that consume some unreacted soluble phosphates, thereby enhancing its water resistance (Le Rouzic et al., 2017).

Figure 7. The Effect of Water Resistance Tests on the Compressive Strength of Cement Mortar with Various Sawdust Incorporation Levels at Different Ages. (A) 7d curing; (B) 14d curing.
3.6 Freeze-thaw resistance test
The variation in strength loss ratio of sawdust-modified mortar specimens after 3, 6, and nine freeze-thaw cycles can be calculated using the strength loss ratio formula. Figure 8 indicates that after 3, 6, and nine freeze-thaw cycles, the specimens experienced minimal strength loss.
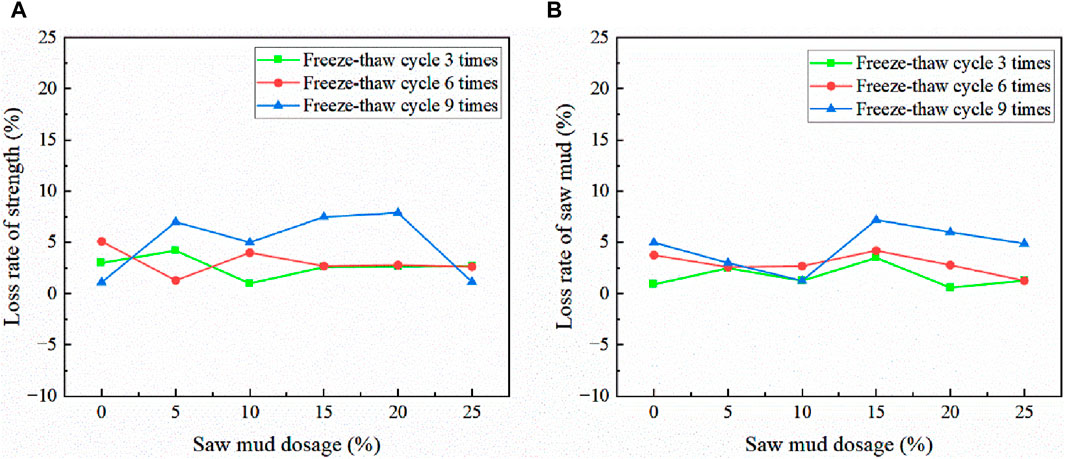
Figure 8. The Impact of Freeze-Thaw Resistance Tests at Different Ages on the Strength of Cement Mortar. (A) 7d curing; (B) 14d curing.
Figure 9 shows that after 3, 6, and nine freeze-thaw cycles, there is almost no mass loss in the specimens. Calculations using the mass loss formula indicate a mass loss rate below 5%, thus demonstrating that the freeze resistance of the mortar specimens is adequate for the number of cycles tested.

Figure 9. The mass change of sawdust-modified mortar specimens after being subjected to 3, 6, and nine freeze-thaw cycles with increasing amounts of sawdust incorporation. (A) 7d curing; (B) 14d curing.
The freeze-thaw resistance test reveals that sawdust-modified cement mortar exhibits good freeze-thaw performance, which may be due to the incorporation of sawdust improving the pore structure of the cement mortar, reducing the proportion of large pores, thereby decreasing the damage caused by the formation and expansion of ice crystals within the pores (Li et al., 2021; Pastor et al., 2023). During the freeze-thaw process, the migration of water in capillaries and the formation of ice crystals can damage the material structure (Sun et al., 2020). The optimized pore structure of sawdust-modified cement mortar may restrict the migration of water and reduce the formation of ice crystals, thereby lowering freeze-thaw damage (Zhang et al., 2022). The enhancement of freeze resistance in sawdust-modified cement mortar may be related to its chemical composition. Some active components in sawdust may react with cement hydration products to form more stable crystal structures, thus improving freeze-thaw resistance. The excellent freeze-thaw performance of sawdust-modified cement mortar makes it more suitable for use in cold regions or in environments subject to freeze-thaw cycles, providing a basis for its application in specific environments.
3.7 Microscopic mechanism analysis experiment
Specimens were observed under a Scanning Electron Microscope (SEM) to examine their microstructures.
Observing Figure 10, it can be seen that at 500 times magnification, the mortar in the control group exhibits noticeable cracks and pores. These are caused by factors such as autogenous shrinkage, hydration shrinkage, and drying shrinkage, and some are also due to the gaps between sand particles not being fully filled by cement particles, resulting in pores. These cracks and pores lead to a reduction in the strength and durability of the mortar (Luo et al., 2021). At 8,000 times magnification, a large amount of hydrated calcium silicate hydrate (C-S-H) appears in a fibrous and irregular pattern, which includes plate-like calcium hydroxide (Ca(OH)2) crystals.
Upon observing Figures 11–13, it can be seen that as the amount of sawdust incorporation gradually increases, at 500 times magnification, Group T1 has more pores than Group T3. This is due to the lower reactivity of sawdust, which can not fully consume the Ca(OH)2 crystals produced by cement hydration. With a lower content of sulfate ions in the system, a large amount of needle-shaped ettringite (AFt) crystals are not formed in the later stages of hydration. After the incorporation of sawdust, the amount of hydration products formed within the concrete decreases, leading to an increase in the content of gel pores (harmless pores) (Liu and Yan, 2008). However, in terms of overall pore structure, the incorporation of sawdust can optimize the pore structure of the concrete, thereby enhancing its durability. There is no significant difference in the morphology of hydration products between the control group and the sawdust-amended groups, indicating that the incorporation of sawdust has no significant impact on the hydration products.
Observing Figure 14, at 500 times magnification, it can be noted that Group T4 has more pores compared to Groups T3, T2, and T1. This indicates that with the continued increase in the incorporation of sawdust, the internal porosity also increases, but these are mostly harmless or slightly harmful pores (Liu and Yan, 2008), which do not significantly affect the stability of the mortar’s internal structure. At 8,000 times magnification, it is observed that with the increase in sawdust incorporation, the amount of C-S-H gel within the mortar of Group T4 increases, and the quantity of Ca(OH)2 crystals in the control group is significantly higher than in Group T4. This suggests that the addition of a large amount of sawdust leads to the production of more C-S-H gel, resulting in a denser internal structure of the mortar, reducing the occurrence of internal cracks, thereby enhancing the strength and durability of the mortar.
4 Conclusion
This study focuses on the preparation and research of sawdust-modified cement mortar. Through systematic experimental analysis and theoretical discussion, the following conclusions have been drawn:
(1) The filling effect of the fine particles in sawdust allows them to form a denser microstructure among cement particles, thereby enhancing the overall performance of the material. The proper incorporation of sawdust, especially at levels between 10% and 20%, can significantly improve the mechanical properties of cement mortar.
(2) Different types of modifiers have a markedly distinct impact on the properties of cement mortar. In this study, the chemical composition of sawdust, particularly the reactive silicon dioxide (SiO2) and calcium oxide (CaO), reacted with the hydration products of cement to form crystalline structures that enhance the performance of the material, thereby further improving the durability and freeze-thaw resistance of the modified cement mortar.
(3) Microscopic analysis indicates that the incorporation of sawdust has improved the pore structure of the cement mortar and promoted the formation of Calcium Silicate Hydrate (C-S-H) gel, thereby enhancing the material’s durability and crack resistance.
In summary, sawdust-modified cement mortar offers significant practical benefits and contributes to the reduction of environmental hazards caused by the accumulation of solid waste, as well as the advancement of sustainable green development in building materials.
Data availability statement
The original contributions presented in the study are included in the article/supplementary material, further inquiries can be directed to the corresponding author.
Author contributions
YC: Conceptualization, Funding acquisition, Resources, Visualization, Writing–original draft, Writing–review and editing. JL: Conceptualization, Data curation, Formal Analysis, Investigation, Methodology, Writing–original draft, Writing–review and editing. WW: Conceptualization, Investigation, Supervision, Validation, Writing–original draft, Writing–review and editing, Data curation. LJ: Project administration, Supervision, Writing–review and editing. SY: Validation, Visualization, Writing–review and editing.
Funding
The author(s) declare that financial support was received for the research, authorship, and/or publication of this article. This research was funded by the project on Green Low Carbon Design and High Resource Utilization of Concrete Materials (Funder: YC Funding number: SKDHKQ20240166) and the Research on Utilization Technology of Resourceful Highway Engineering of Stone Industry Waste Sludge (Sawdust) (Funder: YC Funding number: JS-22-1378).
Conflict of interest
The authors declare that the research was conducted in the absence of any commercial or financial relationships that could be construed as a potential conflict of interest.
Publisher’s note
All claims expressed in this article are solely those of the authors and do not necessarily represent those of their affiliated organizations, or those of the publisher, the editors and the reviewers. Any product that may be evaluated in this article, or claim that may be made by its manufacturer, is not guaranteed or endorsed by the publisher.
References
Abbasi, S., Jannaty, M. H., Faraj, R. H., Shahbazpanahi, S., and Mosavi, A. (2020). The effect of incorporating silica stone waste on the mechanical properties of sustainable concretes. Materials 13, 3832. doi:10.3390/ma13173832
Abdellahi, S. B., and Hejazi, S. M. (2015). Effect of glass and polypropylene fibers in cementitious composites containing waste stone powder. J. Industrial Text. 45, 152–168. doi:10.1177/1528083714567239
Afonso, P., Pires, V., Faria, P., Azzalini, A., Lopes, L., Mourão, P., et al. (2023). A novel approach for the reuse of waste from the extractive and processing industry of natural stone binders: development of stone composites. Sustainability 16, 64. doi:10.3390/su16010064
Agwu, O. E., Akpabio, J. U., and Archibong, G. W. (2019). Rice husk and saw dust as filter loss control agents for water-based muds. Heliyon 5, e02059. doi:10.1016/j.heliyon.2019.e02059
Asadi Shamsabadi, E., Ghalehnovi, M., De Brito, J., and Khodabakhshian, A. (2018) Performance of concrete with waste granite powder: the effect of superplasticizers. Appl. Sci. 8, 1808. doi:10.3390/app8101808
Bai, S., Zhang, J., and Wang, Z. (2015). A methodology for evaluating cleaner production in the stone processing industry: case study of a Shandong stone processing firm. J. Clean. Prod. 102, 461–476. doi:10.1016/j.jclepro.2015.04.139
Cannone Falchetto, A., Moon, K. H., Wang, D., and Riccardi, C. (2018). Investigation on the cooling medium effect in the characterization of asphalt binder with the bending beam rheometer (BBR). Can. J. Civ. Eng. 45, 594–604. doi:10.1139/cjce-2017-0586
Chen, Y., Liu, J., Feng, B., Tan, X., and Wang, B. (2021). Study on the influence of waste circuit board powder content on the performance of cement mortar. J. Wuhan Polytech. Univ. 40, 61–66. doi:10.3969/j.issn.2095-7386.2021.05.009
Chinese Standard (2009). Standard for test method of basic properties of construction mortar: jgj/t 70-2009. Beijing: Ministry of Housing and Urban-Rural Development of the People’s Republic of China.
Dang, K., Pelletier, M. H., and Walsh, W. R. (2011). Factors affecting flexural strength in cement within cement revisions. J. Arthroplasty 26, 1540–1548. doi:10.1016/jarth.2011.01.013
Deutsches Institut für Normung (2011). Determination of the water absorption coefficient of construction materials: din 52617. Berlin: Beuth Verlag GmbH.
Gupta, T., Kothari, S., Siddique, S., Sharma, R. K., and Chaudhary, S. (2019). Influence of stone processing dust on mechanical, durability and sustainability of concrete. Constr. Build. Mater. 223, 918–927. doi:10.1016/j.conbuildmat.2019.07.188
Le Rouzic, M., Chaussadent, T., Stefan, L., and Saillio, M. (2017). On the influence of Mg/P ratio on the properties and durability of magnesium potassium phosphate cement pastes. Cem. Concr. Res. 96, 27–41. doi:10.1016/j.cemconres.2017.02.033
Li, Q., Peng, X., Wang, J., Cheng, Y., Zhang, K., Dai, W., et al. (2023). Non-Sintered Wrap-Shell lightweight aggregates from dredged soils: study of softening coefficients and water Absorption-Desorption behavior. Constr. Build. Mater. 374, 130871. doi:10.1016/j.conbuildmat.2023.130871
Li, Y., Cheng, Y., Jin, L., and Cheng, G. (2024). Study on mechanical properties of solid-waste synergistic composites based on saw mud. Shandong Chem. Ind. 53, 30–33. doi:10.19319/j.cnki.issn.1008-021x.2024.03.018
Li, Y., He, X., Sun, H., and Tan, Y. (2021). Effect of freeze–thaw on fatigue damage characteristics of cement emulsified bitumen mastic. Road Mater. Pavement Des. 22, 1543–1558. doi:10.1080/14680629.2019.1702584
Liang, H., Hu, X., Hu, S., Zhu, F., and Wan, H. (2023). Study on the effect of granite saw-mud on the performance of ready-mixed concrete. J. Wuhan Univ. Technol. 45, 35–40. doi:10.39163/j.issn.1671-4431.2023.07.006
Liu, S., and Yan, P. (2008). Influence of limestone powder on filling effect of cement paste and pore structure of sand grout. J. Chin. Ceram. Soc. 36, 69–77. doi:10.14062/j.issn.0454-5648.2008.01.023
Lu, Z., Kong, X., Jansen, D., Zhang, C., Wang, J., Pang, X., et al. (2020). Towards a further understanding of cement hydration in the presence of triethanolamine. Cem. Concr. Res. 132, 106041. doi:10.1016/j.cemconres.2020.106041
Luo, X., Zhao, J., Zhuo, X., and Zhao, W. (2021). Analysis of causes of cracks in cast-in-place concrete and study on prevention and control Technology measures. Anhui Archit. (3), 166–176. doi:10.16330/j.cnki.1007-7359.2021.03.079
Ma, J., Nivitha, M. R., Hesp, S. A. M., and Murali Krishnan, J. (2023). Validation of empirical changes to asphalt specifications based on phase angle and relaxation properties using data from a northern Ontario, Canada pavement trial. Constr. Build. Mater. 363, 129776. doi:10.1016/j.conbuildmat.2022.129776
National Standard of the People's Republic of China (2024). General Portland cement' (GB 175-2023). released on November 27, 2023, and implemented on.
Pastor, J. L., Chai, J., and Sánchez, I. (2023). Strength and microstructure of a clayey soil stabilized with natural stone industry waste and lime or cement. Appl. Sci. 13, 2583. doi:10.3390/app13042583
Poulikakos, L. D., Pasquini, E., Tusar, M., Hernando, D., Wang, D., Mikhailenko, P., et al. (2022). RILEM interlaboratory study on the mechanical properties of asphalt mixtures modified with polyethylene waste. J. Clean. Prod. 375, 134124. doi:10.1016/j.jclepro.2022.134124
Sivrikaya, O., Kıyıldı, K. R., and Karaca, Z. (2014). Recycling waste from natural stone processing plants to stabilise clayey soil. Environ. Earth Sci. 71, 4397–4407. doi:10.1007/s12665-013-2833-x
Standardization Administration of China (2005). Test method for flowability of cement mortar: gb/t 2419-2005. Beijing: Standardization Administration of China.
Standardization Administration of China (2021). Method of testing cements—determination of strength (ISO method): gb/t 17671-2021. Beijing: Standardization Administration of China.
Subramanian, S., and Ku, T. (2023). A framework to investigate the effect of sand on strength of cement-admixed clay. J. Mater. Civ. Eng. 35 (7), 06023002. doi:10.1061/JMCEE7.MTENG-14465
Sun, G., Ma, J., Sun, D., Li, B., Ling, S., and Lu, T. (2020). Influence of thermal oxidative aging on temperature induced self-healing transition of polymer modified bitumens. Mater. Des. 192, 108717. doi:10.1016/j.matdes.2020.108717
Walther, A., Büchler, S., Cannone Falchetto, A., Wang, D., Riccardi, C., and Wistuba, M. P. (2019). Experimental investigation on asphalt mixtures prepared with reclaimed asphalt pavement and rejuvenators based on the BTSV method. Road Mater. Pavement Des. 20, 1695–1708. doi:10.1080/14680629.2019.1594053
Wan, H., Hu, Y., Liu, G., and Qu, Y. (2018) Study on the structure and properties of autoclaved aerated concrete produced with the stone-sawing mud. Constr. Build. Mater. 184, 20–26. doi:10.1016/j.conbuildmat.2018.06.214
Wang, T., Yang, W., and Zhang, J. (2022). Experimental studies on mechanical properties and microscopic mechanism of marble waste powder cement cementitious materials. Crystals 12, 868. doi:10.3390/cryst12060868
Zhang, C., Liu, T., Jiang, C., Chen, Z., Zhou, K., and Chen, L. (2022). The freeze-thaw strength evolution of fiber-reinforced cement mortar based on NMR and fractal theory: considering porosity and pore distribution. Materials 15, 7316. doi:10.3390/ma15207316
Zhang, X., Shao, Y., Wang, Y., Dong, Y., Sun, X., and Chen, G. (2024). Feasibility study on preparation of foamed ceramics lightweight wall materials from granite scrap. China Ceram. 60, 64–70. doi:10.16521/j.cnki.issn.1001-9642.2024.06.009
Zhang, Y., Zhou, L., and Liu, F. (2023). Study on the preparation of concrete with sawdust, fly ash, and other solid wastes. Shandong Chem. Ind. 52, 47–49. doi:10.19319/j.cnki.issn.1008-021x.2023.13.029
Zhao, H., Huang, Y., Bian, Y., and Dong, D. (2021). The impact of sawdust on the performance of PVA-modified calcium sulfoaluminate cement waterproof repair mortar. Create Living 45, 166–168. doi:10.3969/j.issn.2095-4085.2021.04.002
Keywords: sawdust, solid waste, modified cement mortar, mechanical properties, durability, microstructure
Citation: Cheng Y, Liu J, Wang W, Jin L and Yan S (2024) Preparation and property study of sawdust-modified cement mortar. Front. Mater. 11:1457167. doi: 10.3389/fmats.2024.1457167
Received: 30 June 2024; Accepted: 22 July 2024;
Published: 06 August 2024.
Edited by:
Di Wang, University of Ottawa, CanadaReviewed by:
Xinzhou Li, Chang’an University, ChinaJianmin Ma, Queen’s University, Canada
Xiaoning Zhang, Chongqing University, China
Copyright © 2024 Cheng, Liu, Wang, Jin and Yan. This is an open-access article distributed under the terms of the Creative Commons Attribution License (CC BY). The use, distribution or reproduction in other forums is permitted, provided the original author(s) and the copyright owner(s) are credited and that the original publication in this journal is cited, in accordance with accepted academic practice. No use, distribution or reproduction is permitted which does not comply with these terms.
*Correspondence: Wentong Wang, d3d0QHNkdXN0LmVkdS5jbg==