- 1Department of Metallurgy and Materials Engineering, Sakarya University, Sakarya, Türkiye
- 2Department of Mechanical Engineering, Istanbul Medeniyet University, Istanbul, Türkiye
- 3Department of Mechanical Engineering, Kocaeli University, Kocaeli, Türkiye
- 4The Environment and Resource Efficiency Cluster (EREC), Nazarbayev University, Nur-Sultan, Kazakhstan
- 5Department of Civil and Environmental Engineering, Nazarbayev University, Nur-Sultan, Kazakhstan
- 6School of Engineering, University of Southern Queensland, Toowoomba, QLD, Australia
- 7Department of Machine and Metal Technologies, Kocaeli University, Kocaeli, Türkiye
Titanium (Ti) alloys have been widely used in biomedical applications due to their superior mechanical, physical, and surface properties, while improving their tribological properties is critical to widening their biomedical applications in the current era. The present review examines the recent progress made in enhancing the tribological performance of titanium alloys and titanium matrix composites for biomedical purposes. It specifically focuses on the progress made in biomedical coatings, mechanical surface treatment, and developing titanium matrix composites in terms of their processing, tribological testing conditions, and characterization. Despite thorough investigations, the specific testing procedures for evaluating the friction and wear properties of the alloy and/or biomedical component are still uncertain. The majority of researchers have selected test methods and parameters based on previous studies or their own knowledge, but there is a scarcity of studies that incorporate limb-specific tribological tests that consider the distinct kinematic and biological structure of human limbs. Since advanced microscopy has great potential in this field, a variety of advanced characterization techniques have been used to reveal the relationship between microstructural and tribological properties. Many coating-based strategies have been developed using anodizing, PEO, VD, PVD, nitriding, thermal spray, sol-gel, and laser cladding, however; composition and processing parameters are crucial to improving tribological behaviour. Reinforcing component type, amount, and distribution has dominated Ti matrix composite research. Ti grade 2 and Ti6Al4V alloy has been the most widely used matrix, while various reinforcements, including TiC, Al2O3, TiB, hydroxyapatite, Si3N4, NbC, ZrO2 have been incorporated to enhance tribological performance of Ti matrix. Mechanical surface treatments improve biomedical Ti alloys’ tribological performance, which is advantageous due to their ease of application. The implementation of machine learning methods, such as artificial neural networks, regression, and fuzzy logic, is anticipated to make a substantial contribution to the field due to their ability to provide cost-effective and accurate results. The microstructural and surface features of biomedical Ti alloys directly affect their tribological properties, so image processing strategies using deep learning can help researchers optimize these properties for optimal performance.
1 Introduction
The selection of material and manufacturing methods for biomedical implants is crucial when considering the specific locations and movement conditions of structures like joints and bones in the human body. Increasing hardness and improving the wear properties of implants (Somasundaram Prasadh et al., 2021) could extend their service life (Kumar et al., 2021). This is especially pertinent when considering implants such as in knees and arms, as they experience high levels of stress and deterioration. Furthermore, the failure of an implant may result in a more extensive revision surgery and may potentially lead to complications such as bone loss and fractures. Regrettably, such cases lead to additional financial strain on both patients and the national healthcare systems due to the expenses associated with treatment (Sousa et al., 2022). The field of understanding tribological behaviour of biomaterials, particularly implants, aims to maintain friction and wear under the designed conditions by testing interacting surfaces in relative motion.
Titanium (Ti) and its alloys remain as preferred materials for implant production due to their superior properties. Despite their uses in a great variety of applications (briefly outlined in the following section), certain properties of Ti alloys such as low wear resistance, relatively low fatigue strength, and hardness may restrict their use, particularly if they are in contact with hard components under cycling loading (Kumar et al., 2018; Wang et al., 2019). Poor wear (Avila et al., 2021; Gonçalves et al., 2023) and corrosion behaviour of Ti alloys and their bioinert surfaces may slow down in vivo osseointegration (Avila et al., 2021; Sousa et al., 2021b). Moreover, inadequate tribocorrosion resistance (Sousa et al., 2021b; Gonçalves et al., 2023) of load-bearing Ti alloys is a major concern due to its impact on the interaction between the implant and the surrounding tissue (Sousa et al., 2022). In light of these limitations, researchers are exploring various methods for addressing the shortcomings of titanium alloys, which is the subject of the present review. It may be necessary to customize the surface properties of Ti alloys (such as roughness and surface topography) in order to enhance specific biological characteristics like osseointegration and antibacterial activity in biomedical applications, along with their tribological properties (Carreón et al., 2014). Thus, studies on improving tribological properties of titanium alloys have been an attractive field of research in the last decades. Consequently, a timely and thorough review is necessary to examine the progress made in enhancing the friction and wear properties of Ti alloys and Ti matrix composites for medical purposes.
This review provides an in-depth review of the tribological characteristics of titanium and titanium alloys. It accomplishes this by examining over 200 research articles published within the past 5 years. The paper provides a future perspective for researchers and industry by organising tribological testing, characterisation, and material production technologies in a systematic manner. The objective is to guarantee the progression of scientific knowledge in the field, the development of industrial applications, and the reproducibility of results. The present article is novel in its focus on the advancements in enhancing the tribological characteristics of Ti alloys, as outlined in Figure 1. It emphasizes the significant challenges and offers future directions in this field. A brief introduction of Ti alloys is presented by addressing their historical developments, applications, classifications, processing, and overall properties. Methods for testing and characterizing the tribological properties of titanium alloys are also briefly discussed. For each improvement strategy classified in Figure 1, final remarks and suggestions for future research are provided in the final section. Additionally, challenges and future research directions in investigating the tribological behavior of these materials are addressed.
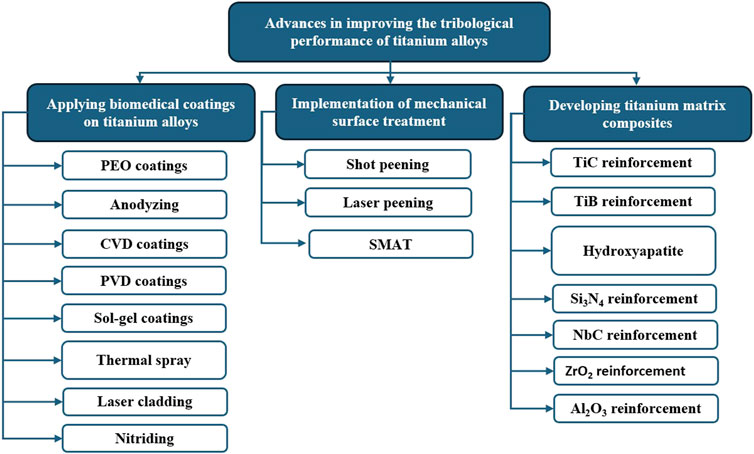
Figure 1. Most recent strategies for improving tribological properties of biomedical grade titanium alloys.
2 A brief introduction to Titanium (Ti) alloys
Titanium and its alloys find extensive applications in aerospace, medical, marine, energy, chemical, petrochemical, and nuclear industries owing to their exceptional properties including high strength-to-weight ratio, corrosion resistance, biocompatibility, and ability to maintain performance at elevated temperatures (Carreón et al., 2014; Gospodinov et al., 2016; Ranjith Kumar et al., 2019; Petronić et al., 2020; Chattopadhyay et al., 2021). The widespread use of Ti alloys in the biomedical field is mainly due to its exceptional biocompatibility, excellent strength-to-density ratio, antibacterial properties, and remarkable resistance to corrosion (Qin et al., 2021; Ju et al., 2023; Soltani-Kordshuli et al., 2023). Consequently, it has a broad range of applications, including the implantation of hard tissue (Li Y. et al., 2024), joint replacements (Soltani-Kordshuli et al., 2023), screw implants (Zhang Y. et al., 2024), endoprostheses (Ranusa et al., 2022) and dental implants (Madeira et al., 2022). Nevertheless, their relatively low wear resistance reduces their service life (Ju et al., 2023; Lei et al., 2024; Li Y. et al., 2024; Siahpour et al., 2024) and restricts their applications where tribological contact is inevitable. Today, it is possible to achieve combined performance gains such as strength, tribological, and hardness by applying additional methods such as coating and surface treatment to alloys. This section provides an overview of Ti alloys, focusing on their historical development, wide range of applications, systematic classification, and overall properties.
2.1 Historical development
Ti, formerly regards as a rare element (Liu et al., 2004), has now emerged as a highly important and widely used metal in a diverse range of applications from turbine blades (Ulutan and Ozel, 2011) to hip and knee replacements (Cui et al., 2011). It was discovered in England in 1791 by W. Gregor, a British clergyman and mineralogist (Liu et al., 2004; Nikiforov et al., 2014; Zhang et al., 2019), which was then named in 1795 by the German chemist Klaproth (Liu et al., 2004; Nikiforov et al., 2014). Ti is highly abundant in the earth’s crust, ranking ninth among all elements. The vast majority of Ti exists in the form of insoluble oxides (Nikiforov et al., 2014; Gospodinov et al., 2016; Quinn et al., 2020). Therefore, it is necessary to extract it from minerals such as ilmenite, rutile, and anatase (Prasad et al., 2015; Quinn et al., 2020). In 1910, M.A. Hunter developed the Hunter process, which enabled the extraction of Ti from minerals. However, this method was not suitable for large-scale extraction of Ti. W. Kroll subsequently pioneered the Kroll process, which facilitated the efficient extraction and utilization of Ti in diverse industries, beginning in 1936 (Bangera and D'Costa, 2015; Prasad et al., 2015). Subsequently, it has become one of the most appealing engineering materials, specifically to military applications, thus its usage has exponentially increased (Sonntag et al., 2015). In the early 1950s, Leventhal and Branemark introduced it as a promising material for biomedical applications because of its exceptional resistance to corrosion and compatibility with the human body. At present, Ti and its alloys are widely recognized as biomaterials because of their exceptional biological properties (e.g., strong corrosion resistance (Zhang and Chen, 2019), excellent biocompatibility (Liu et al., 2019), very good and fast osteointegration (Vasilescu et al., 2019)) and their high weight to strength ratio which also puts them among the most widely used biomaterials (Wang et al., 2014; Sonntag et al., 2015).
2.2 Applications
Ti is commonly alloyed with elements such as aluminum, vanadium, molybdenum, iron, niobium, and others to produce high-performance alloys with strong strength to weight ratio. For instance, titanium grades with comparable strength to high strength steel are approximately 45% lighter than steel (Ranjith Kumar et al., 2019). Due to its high chemical reactivity, it readily forms thin (5–6 nm) oxide layers on its surface when exposed to the atmosphere. This makes it highly resistant to corrosion in various environments, such as freshwater, seawater, aqua regia, chlorine, and many acids (Gospodinov et al., 2016; Chattopadhyay et al., 2021). It also has many outstanding properties including fatigue resistance (Chattopadhyay et al., 2021), low thermal conductivity (Wang et al., 2019), fracture toughness (Zhou et al., 2015), excellent high-temperature properties (Carreón et al., 2014; Wang et al., 2014; Kumar et al., 2018), and good biocompatibility (Petronić et al., 2020). Therefore, Ti and its alloys are highly demanded in aeronautics applications (e.g., spacecraft, missile, and aircraft components such as skeleton, skin, fasteners, engine elements, landing gears (Wang et al., 2019), and jet propulsion engines (Zhou et al., 2015)), biomedical applications (Wang et al., 2014) (e.g., cementless orthopedic prostheses, dental and trauma surgery implants such as plates, screws, and intramedullary nails), nuclear industry (Ranjith Kumar et al., 2019; Chattopadhyay et al., 2021), chemical industry (Gospodinov et al., 2016) (e.g., desalination units, heat exchanger systems, transuranic waste containers, seawater-cooled piping), energy industry (Petronić et al., 2020) (e.g., hydrogen storage devices, heat exchanger systems (Ranjith Kumar et al., 2019)), automotive industry (Gospodinov et al., 2016; Chattopadhyay et al., 2021), military industry (Gospodinov et al., 2016; Wang et al., 2019), marine industry (Ranjith Kumar et al., 2019; Petronić et al., 2020; Chattopadhyay et al., 2021) (Figure 2).
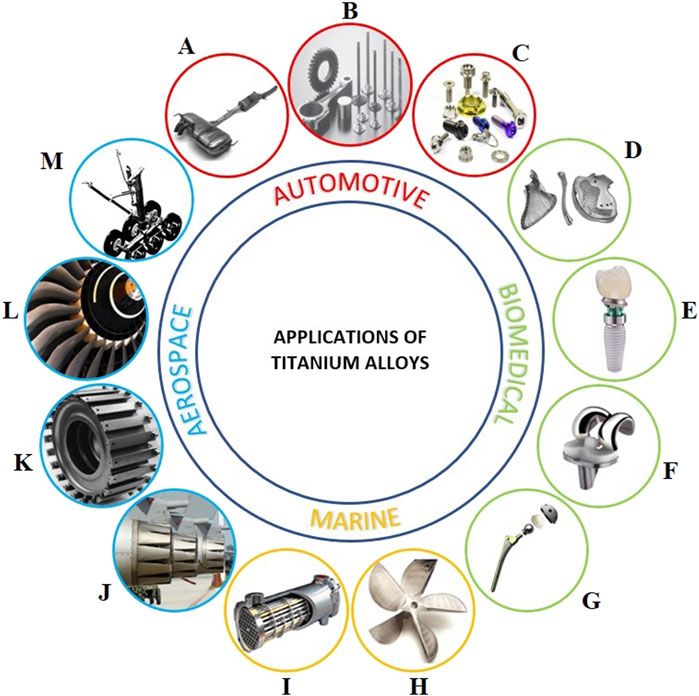
Figure 2. Example applications of Ti and its alloys in automotive: (A) exhaust system [adapted and modified from (Furuta, 2019)], (B) engine parts [adapted and modified from (Furuta, 2019)], and (C) fasteners [adapted and modified from (Gui et al., 2019)]; biomedical: (D) complex implants [adapted and modified from (Zhang et al., 2018)], (E) dental implant [adapted and modified from (Crosby, 2013)], (F) knee implant [adapted and modified from (Sáenz De Viteri and Fuentes, 2013)], (G) hip implant [adapted and modified from (Liu et al., 2004)]; marine: (H) propeller [adapted and modified from (Ranjith Kumar et al., 2019)], (I) heat exchanger [adapted and modified from (Ranjith Kumar et al., 2019)]; aerospace: (J) exhaust nozzle [adapted and modified from (Serra, 2008)], (K) fan disk [adapted and modified from (Tabie et al., 2020)], (L) fan blades [adapted and modified from (Lihui et al., 2014)], (M) main landing gear [adapted and modified from (Cotton et al., 2015)].
2.3 Classification and processing
Ti alloys can be classified as α, near α, metastable β, or stable β according to their position in the β isomorphous phase diagram depending on the room temperature microstructure (Liu et al., 2004; Barriobero-Vila, 2015). Alloys can be classified based on their various phase types, which are determined by the different metallurgical structures they possess (Table 1). However, in practice, the utilization of all types of titanium alloys is infrequent. As a result, manufacturers have started categorizing alloys based on their economic worth (Table 2). Thus far, Ti6Al4V alloy is the most commonly used titanium alloy in dental, orthopedic, and tissue engineering applications among the various types of titanium alloys employed in the biomedical field (Hezil et al., 2022). Ti6Al4V alloy is expected to remain popular in the coming period due to its wide commercial availability and economic viability (Pushp et al., 2022; 2024e).
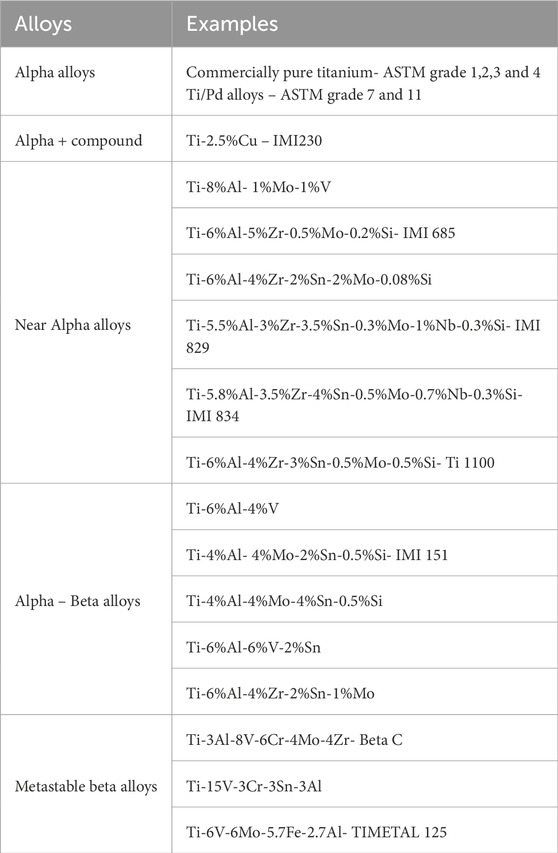
Table 1. Titanium alloys classified by metallurgical structure with examples (Pushp et al., 2022).
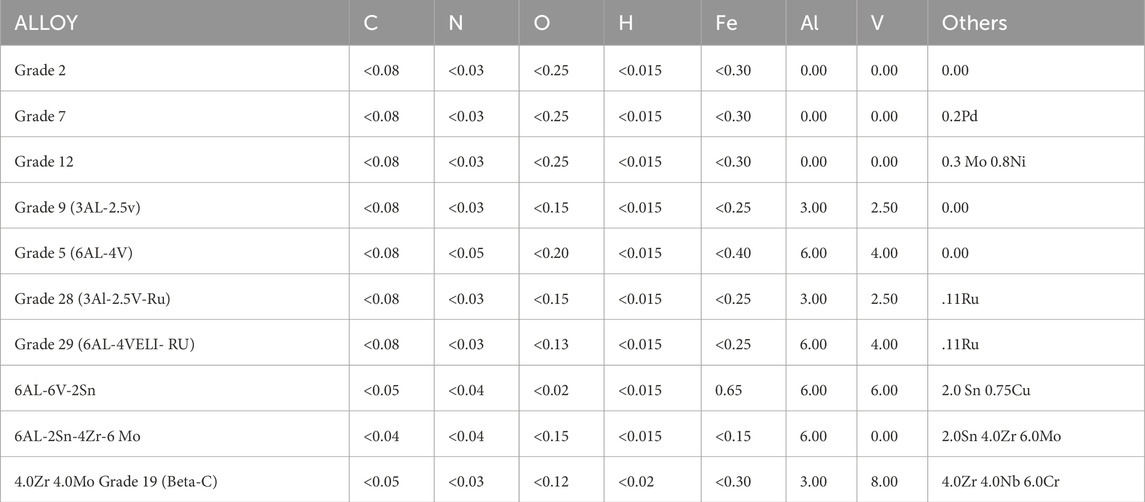
Table 2. Most commonly used titanium grades according to their economic worth (Titanium, 2024c).
2.4 Overall properties
The chemical composition and microstructural features of Ti alloys have a significant impact on their physical, mechanical, and technological properties. The ultimate properties of these alloys are determined by the processing history and alloying, which allows for control over the properties (Liu et al., 2004; Barriobero-Vila, 2015). Briefly, solid solution strengthening, precipitation strengthening, transformation hardening, work hardening, and grain boundary strengthening are the main deformation mechanisms contributing to the improvement of mechanical properties through alloying and processing (Barriobero-Vila, 2015). Ti components are produced in various forms such as sheets, billets, foils, bars, tubes, and wires via traditional metalworking processes such as casting, forging, and machining (Crosby, 2013; Sefer, 2014) as well as via advanced processing methods such as additive manufacturing (AM) (Hao et al., 2016; Trevisan et al., 2018; Kaur and Singh, 2019; Zhang L. C. et al., 2020) and sinter plasma sintering (SPS) (Cordeiro and Barão, 2017; Zhang and Chen, 2019). Table 3 presents the mechanical properties of the most commonly used biomedical titanium alloys, with conventional and advanced processing methods (Niinomi, 1998; Biesiekierski et al., 2016; 2024a; Abd-Elaziem et al., 2024).
3 Tribological testing and characterization methods used for Ti alloys
Friction-induced degradation of biomedical materials leads to material loss and a decrease in mechanical performance, thereby compromising the functionality of these materials in critical applications (Stachowiak and Batchelor, 1993; Soltani-Kordshuli et al., 2023). Particles and ions detached from the material may accumulate in the surrounding tissues, resulting in inflammation and toxic reactions (Kim et al., 2019). This may detrimentally affect human health and general wellbeing, while also leading to substantial economic losses (Stachowiak and Batchelor, 1993; Bian et al., 2023). Given the increasing utilization of Ti alloys in diverse applications that require enhanced tribological performance, it is imperative for these alloys to conform to the prevailing international standards. Therefore, tribological testing and characterization processes are crucial in guaranteeing the design, production, quality, and performance of Ti alloys. Moreover, it is crucial to utilize the most appropriate tribological testing and characterization techniques in order to develop novel strategies (such as the development of functional alloys (Majzoobi et al., 2023), application of wear-resistant biocompatible coatings (Wang et al., 2023a), surface texturing (Niu et al., 2023), etc.) to address the aforementioned undesirable tribological properties of Ti alloys employed in biomedical applications (Ranusa et al., 2022).
3.1 Tribological testing
The widespread use of titanium and titanium alloys in the biomedical industry has resulted in the adoption of tribological tests in various conditions and designs. The diversity of human limbs can be comprehended by considering the kinematic and biological distinctions among them. Table 4 presents a summary of the tribological testing methods and associated parameters utilized to study tribological behaviour of titanium alloys in the last 5 years. Ball or pin relative motion wear test methods on disc or plate, which are widely used in traditional tribology science, are still current and applicable. The simplicity and effectiveness of these testing methods, combined with their economic benefits have made them a central area of interest and research among scholars.
The terms “ball-on-disk” (Figure 3A) and “pin-on-disk” (Figure 3B) describe a wear test system that involves using wear-resistant materials in the form of pins or balls. These elements are subjected to circular motion relative to the part being tested, with parameters such as speed, load, frequency, etc. being controlled. The ball-on-plate (Figure 3C) and pin-on-plate (Figure 3D) mechanisms operate on a similar principle, although the relative motion is linear. The parameter, referred to as either friction distance or stroke length, is defined as the predetermined length of the wear track in the experiments. The parameter, commonly set at 5 mm, has emerged as a pragmatic choice for researchers. While there is no clearly better choice for sliding speed, it can be suggested that reciprocating frequencies of 1, 2, and 5 Hz are more preferred. Intermediate values ranging from 1 to 20 N were found to be more favored for the applied load, as listed in Table 4.
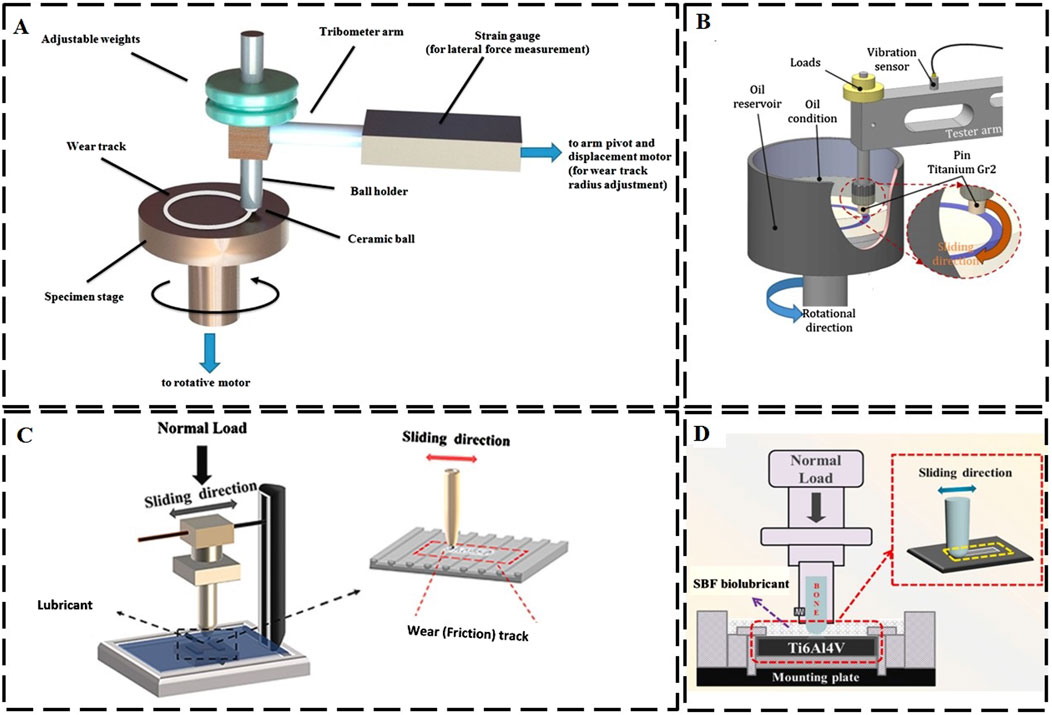
Figure 3. Tribological testing methods used for investigating tribological properties of Ti alloys in recent studies: (A) ball-on-disk, (B) pin-on-disk, (C) ball-on-plate, (D) pin-on-plate. (A) Reproduced with permission (Avcu, 2017a). Copyright 2017, Elsevier. (B) Reproduced under the terms of the CC-BY Creative Commons Attribution 4.0 International License (Şirin et al., 2023). Copyright 2023, The Authors, published by Elsevier. (C) Reproduced with permission (Zhang Y. et al., 2024). Copyright 2024, Elsevier. (D) Reproduced with permission (Wang et al., 2023b). Copyright 2023, Elsevier.
Most researchers indicated a preference for their own experiences and the load values ascribed in the literature. Limited research has been conducted to ascertain load preferences by simulating forces and interactions between limbs (Ranusa et al., 2022; Bian et al., 2023; Zhang Y. et al., 2024). The friction element acting on the surface to be tested is predominantly composed of wear-resistant Si3N4 (Qin et al., 2021; Chen et al., 2024; Li Y. et al., 2024; Yu et al., 2024) and Al2O3 (Madeira et al., 2022; Bouchareb et al., 2024; Lei et al., 2024; Woźniak et al., 2024) ceramic-based materials. The continued popularity of the Ti-6Al-4V alloy (Kaur et al., 2019; Costa et al., 2022; Hezil et al., 2022; Ju et al., 2023), as previously mentioned, is demonstrated by the sustained interest of researchers in its efficacy. Dry friction tests (Kumar Murmu et al., 2024; Saier et al., 2024; Xu Y. et al., 2024; Zhang Q. et al., 2024) have been commonly used in studies where surface treatments have been applied to the alloy. On the other hand, studies focused on enhancing the production and performance of the alloy have predominantly utilized lubricants that mimic the properties of the human body. This phenomenon is purpose-driven and encompasses the specific field of study that the researcher concentrates on. To summarize, the comprehensive analyses demonstrate that the utilization of conventional and knowledge-based test designs and equipment remains applicable in the current era.
3.2 Tribological characterization
The tribological properties of Ti alloys, which are extensively studied during and after wear testing, can be categorized into three groups: evaluation of the coefficient of friction, analysis of surface topography after wear, and analysis of surface morphology after wear. The initial techniques employed are those of force-time recording and topographic survey. These techniques yield measurable and visible data, such as the level of deterioration, friction coefficient, roughness, wear rate, and other similar parameters. Afterwards, precise morphological imaging techniques are primarily used to comprehend the underlying wear mechanisms that contribute to the tribological behavior of the tested alloy. Finally, the analysis of the microstructure and crystal structure of the alloy resulting from wear is accomplished by employing techniques rooted in principles such as X-ray and electron diffraction.
The primary focus of nearly all tribological studies is to determine the amount of wear and the frictional coefficient that contribute to the performance of the titanium alloy in real-world practical applications. Figure 4 illustrates examples of the force-time based friction coefficient behaviour observed in wear tests. Figure 4A illustrates the development and stability of the friction coefficient on the surface of the Ti6Al4V alloy subjected to laser texturing and simultaneous nitriding processes under simulated body fluid (SBF) lubrication conditions (Wang et al., 2023a). The time-friction coefficient graph (Figure 4B) was employed to determine the stable and improved wear performance of all three coatings, depending on the type of TiN, CrN, and TiB2 coatings applied to the same alloy by the RF magnetron sputter deposition method (Narayana and Saleem, 2024). Consequently, the graph formation allows for the interpretation of time- and distance-dependent behaviour.
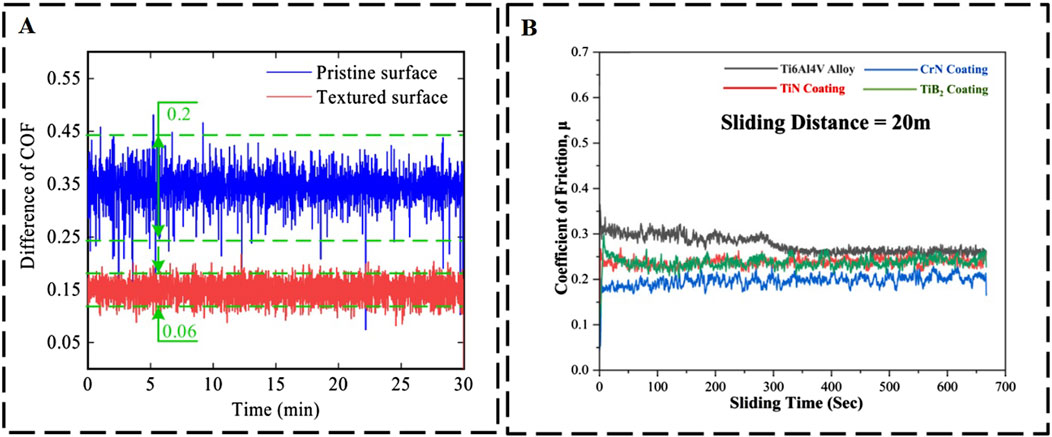
Figure 4. Force-time based friction graphs of Ti6Al4V alloy: (A) with laser texturing and simultaneous nitriding surface treatments, (B) with TiN, CrN and TiB2 coating by RF magnetron sputtering deposition. (A) Reproduced with permission (Wang et al., 2023a). Copyright 2023, Elsevier. (B) Reproduced with permission (Narayana and Saleem, 2024). Copyright 2024, Elsevier.
Figures 5A,B illustrate the 3D sample findings of the wear marks, which were visualized by a laser confocal microscope and an optical profilometer, respectively. The three-dimensional structure of the wear marks formed as a result of the tribological test of the surface obtained by laser surface texturing and double glow plasma surface chromising process on Ti6Al4V alloy is presented (Figure 5A). With imaging, it is possible to rapidly make predictions about the wear comparison from the topographic image difference that occurs when the related work is unprocessed or when using a single processing method (Lei et al., 2024). The 3D image and cross-sectional geometry of the worn surface of the TiN coating, as previously described, are presented here (Narayana and Saleem, 2024). Furthermore, quantitative data such as wear rate and amount can be obtained from the analysis of cross-sectional geometries extracted from 3D wear images using a suite of software (Figure 5B). The wear rates of the powder metallurgically produced Ti-5Cu-xNb alloy at different Nb ratios under different frictional loads are shown in Figure 5C (Pandey et al., 2023a). Using a different approach, gravimetric wear amounts on pin and disc were calculated (Figure 5D) for the effect of fiber laser nitriding on Ti grade 2 and 5 alloys (Chan et al., 2017).
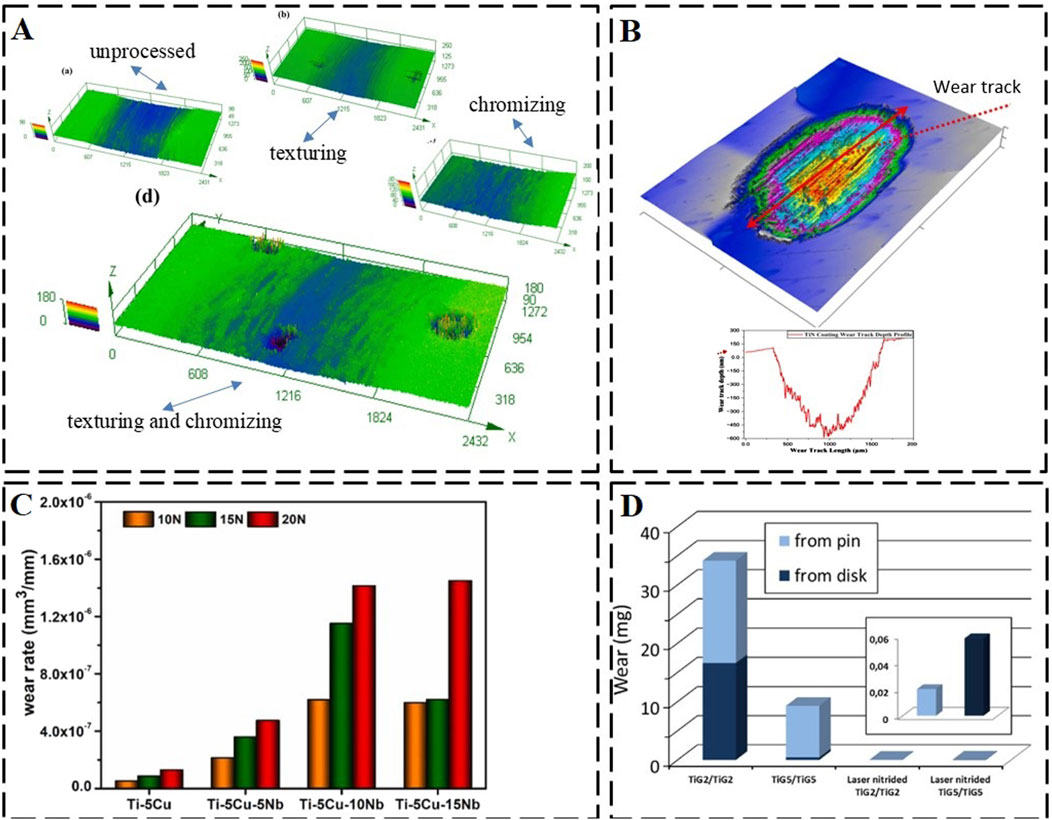
Figure 5. Wear: 3-D marks (A) laser confocal microscope, (B) optical profilometer analysis (C) wear rate, (D) wear amount. (A) Reproduced with permission (Lei et al., 2024). Copyright 2024, Elsevier. (B) Reproduced with permission (Narayana and Saleem, 2024). Copyright 2024, Elsevier. (C) Reproduced with permission (Pandey et al., 2023a). Copyright 2023, Elsevier. (D) Reproduced with permission (Chan et al., 2017). Copyright 2017, Elsevier.
The morphological structures formed by wear tests are frequently examined by scanning electron microscopy (SEM) in order to gain insight into the processing mechanisms that give rise to them. This characterization approach plays a pivotal role in determining the success of newly developed titanium alloys, surface treatments and test conditions. For instance, (Wang et al., 2023a) investigated the wear scars of the pristine Ti6Al4V alloy, whose parametric properties are presented in Table 4, under oil lubricant conditions using the ball-on-disc method. The SEM image in Figure 6A was instrumental in determining the morphological structures of plough and adhesion. Similarly, (Li Y. et al., 2024) conducted a ball-on-plate test to investigate the wear properties of a chitosan-MXene-based hydrogel coating of the same alloy. Thus, it was observed that micro-crack formation occurred in the wear scars under conditions of lubrication with simulated body fluid (Figure 6B). Consequently, the machining phenomena of such as adhesion, micro-cutting, and micro-cracks occurring on the alloy surface can be demonstrated with clarity. Furthermore, the EDS (energy dispersive spectroscopy) characterization technique incorporated into the method enables the determination of elemental composition, elemental exchange and elemental contaminants between the wear site and the base alloy. For instance, (Wang et al., 2023a) demonstrated the formation of the adhesion wear mechanism by revealing the presence of Si, C and O elements resulting from the transfer of Si3N4 ceramic balls and residual lubricant in the EDS examination of the wear scars (Figure 6C).
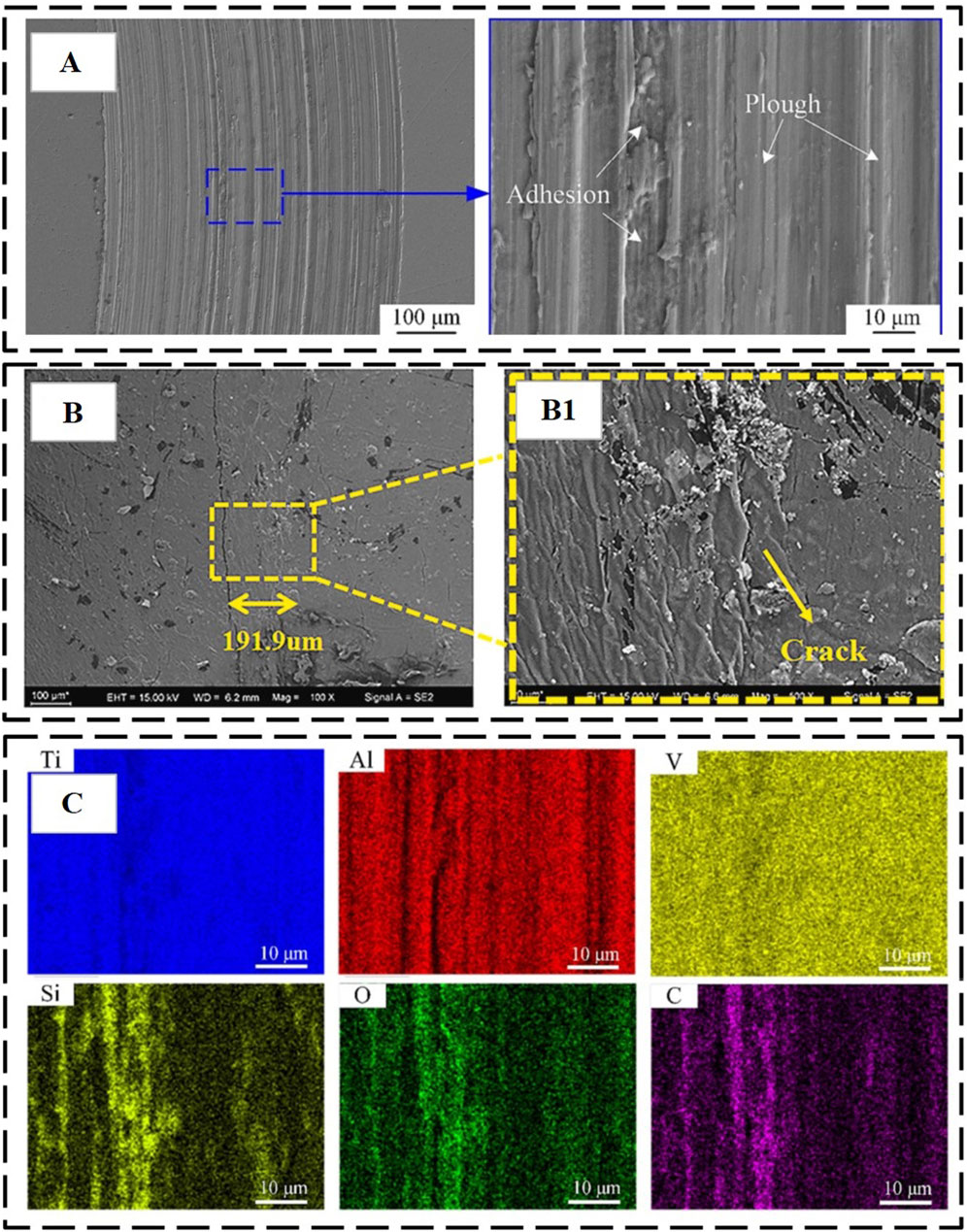
Figure 6. Determination of morphological structures in the wear scars by SEM: (A) adhesion and plough, (B) micro-cracks, (C) EDS elemental mapping. (A) and (C) Reproduced with permission (Wang et al., 2023a). Copyright 2023, Elsevier. (B) Reproduced with permission (Li Y. et al., 2024). Copyright 2024, Elsevier.
The microstructure and type of materials are the primary determinants of their wear performance in a relative moving contact. Therefore, researchers incorporate this factor into comprehensive wear mechanism studies. The characterization of materials, the determination of crystal structures and the measurement of residual stresses can be achieved through the utilization of X-ray data obtained from the machined surface. For instance, (Zhang et al., 2022) examined the tribological properties of a titanium nitride (TiN) coating on TA2 pure titanium using a multi-arc ion plating (MAIP) method. Figure 7A illustrates the XPS (X-ray photoelectron spectroscopy) spectrum of Ti2p on the wear tracks formed under oil lubricant conditions by the reciprocating sliding friction test. Furthermore, the behaviour of the material grains and residual stresses can be demonstrated by utilizing the electron backscattered diffraction (EBSD) data obtained from the cross-sectional regions of the Ta alloys. For, instance, (Yu et al., 2024) conducted a study investigating the tribological behaviour of Ti6Al4V alloy produced by the selected laser melting method in the presence of SBF lubricant. Figure 7B illustrates the microstructure observed in the cross-section of the sample following the tribological test, as determined using the EBSD inverse pole figure (IPF) technique. Lastly, the determination of material crystal structures and distribution of can be achieved by transmission electron microscopy (TEM). Yang et al. (2024) conducted a TEM investigation of the microstructure of the tribolayer formed on the surface of the ATP-TiB/Ti composite material subjected to wear testing in a ball-on-disc tribometer (Figure 7C). Similarly, (Weng et al., 2022) conducted a study in which they tested TA2 pure titanium with a pin-on-disc under dry sliding conditions at room and cryogenic temperatures. Figure 7D illustrates the grain morphology and dislocation distribution as observed under bright field images in a TEM.
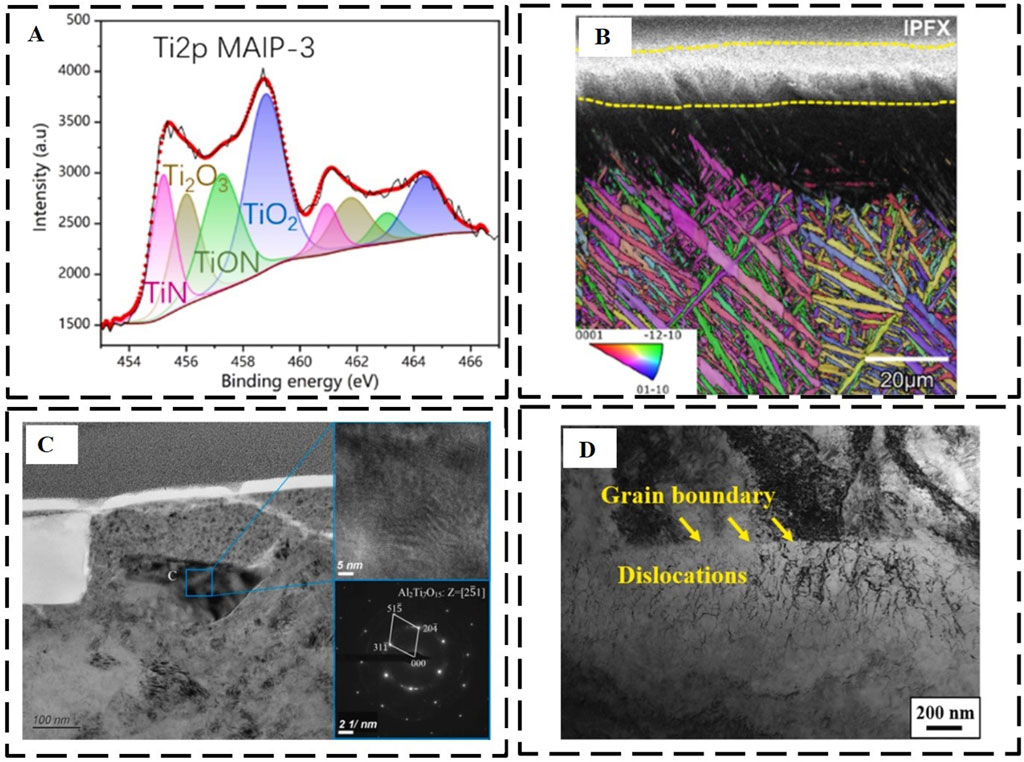
Figure 7. (A) XPS spectrum, (B) EBSD material grains, (C) TEM microstructure, (D) TEM dislocations and grain boundary. (A) Reproduced with permission (Zhang et al., 2022). Copyright 2022, Elsevier. (B) Reproduced with permission (Yu et al., 2024). Copyright 2024, Elsevier. (C) Reproduced with permission (Yang et al., 2024). Copyright 2024, Elsevier. (D) Reproduced with permission (Weng et al., 2022). Copyright 2022, Elsevier.
3.3 Shortcomings and future directions in tribological testing and characterization methods
Despite extensive research, tribological testing protocols applied to alloys and/or biomedical elements remain unclear. The majority of researchers have selected test methods and associated parameters based on the previous studies or their past experience. Furthermore, there are only few studies that include limb-specific tribological tests that take into account the different kinematic and biological structures of human limbs. The uncertainty in tribological test parameters in some literature is also noteworthy (refer to Table 4). All these factors point out to the need for the development of comprehensive protocols for tribological testing of titanium alloys.
To determine the wear mechanisms and corresponding cause-and-effect relationships, it is advisable to utilize a range of characterization techniques in tribological tests. A substantial body of research has shown that conventional load-cell-based wear testers remain crucial in the field (Maculotti et al., 2022). In the same manner, it is necessary to create suitable wear tests that accurately reflect the characteristics of limbs, kinematics, and biology. That being said, the use od advanced instruments have started in recent years (Davis et al., 2022; Liu et al., 2024c; Lypchanskyi et al., 2024; Qian et al., 2024; Srivastav et al., 2024) to study the various physical conditions that have emerged in titanium alloys through topographic, morphological, and microstructural examinations. The review showed that advanced characterization techniques can be used together with advanced detectors in scanning electron and transmission electron microscopes, such as EBSD and high-resolution transmission electron microscopy (HRTEM). Thus, it is recommended to incorporate advanced detectors and relevant data into future tribology studies on titanium.
Traditional studies on the tribological properties of titanium alloys lack certain elements that require further development and clarification. More specifically, the literature on tribological test parameters lacks studies that utilize statistical tools like design of experiments and analysis of variance (ANOVA) to assess the effects of these parameters. It is remarkable that these instruments have not been utilized in the study of friction, lubrication, and wear of biomedical titanium alloys despite their widespread application in the medical and health sectors. To determine and to optimize the tribological parameters and parameter levels of titanium alloys suitable for use in human limbs, future studies should focus on addressing the aforementioned shortcomings.
Finally, it is notable that machine learning methods such as artificial neural networks (Kumar et al., 2024), regression, and fuzzy logic, are yet to be employed in recent studies, where economic and efficiency considerations are of importance. There are almost no image processing studies employing deep learning for further characterization. The utilization of machine learning instruments for expeditious, cost-effective, and precise outcomes promises a significant potential for advancement. In the field of tribology, it is crucial to embrace a comprehensive approach that includes the design, implementation, and prediction stages.
4 Advances in developing biomedical coatings on titanium and alloys for tribological applications
Applying a coating to surfaces is an effective technique for enhancing the tribological characteristics of materials. These methods alter only the surface and subsurface characteristics of the material while leaving the properties of the bulk material unchanged. There are numerous coating methods that have been developed thus far, which can be categorized into two primary groups: modification methods and deposition methods. Plasma electrolytic oxidation (PEO), electron beam modification, anodization, chemical and physical vapor deposition (CVD and PVD), thermal spray, laser cladding, sol-gel, and nitriding are some of the topics that have been studied recently. Table 5 provides a concise overview of the coatings developed for biomedical titanium alloys in the field of tribological applications within the last 5 years.
4.1 Plasma electrolytic oxidation
Plasma electrolytic oxidation (PEO), also referred to as micro arc oxidation, is a technique employed to produce oxide-based coatings on valve metals’ surfaces. The coating layer produced using this technique exhibits uniformity, strong adhesion to the substrate, substantial thickness, density, and hardness. The process is rapid, straightforward, environmentally friendly, and more efficient than alternative methods (Mao et al., 2024). Numerous review articles provide comprehensive information about every aspect of the process developed for various applications (Simchen et al., 2020; Aliofkhazraei et al., 2021).
PEO coatings can be applied to Ti alloys because they are hard and wear resistant. In a study by Zhong et al. (Zhong et al., 2023), PEO coatings on Ti30Zr5Al3V alloy were deposited, and their tribological properties were examined. According to the results, process parameters had a significant effect on the friction coefficient and wear rate of the PEO layer (Zhong et al., 2023). Liu et al. (2024a) also produced PEO coatings on the surface of TC6 alloy and shown that the PEO coating improved the wear resistance of the TC6 alloy (Liu A. et al., 2024). Yang et al. (2023) were reported similar results, where the PEO coating formed on the surface of the TC4 alloy wore 10.4% less than the TC4 alloy. PEO coatings inherently contain porosity, cracks, diffusion channels, etc. This structure that it possesses adversely affects the tribological properties of the coatings. Upon examining recent studies, it can be observed that efforts have been made to enhance the properties of PEO coatings by incorporating various additives such as Al2O3, MoS2, TiC, and Y2O3 (Li and Wang, 2024; Liu A. et al., 2024; Shi et al., 2024; Tang et al., 2024).
4.2 Anodizing
Anodization is an electrochemical process employed to modify the surface of titanium and its alloys (Hang et al., 2020). In this method, a modification layer based on oxides is created, similar to the PEO method. Nevertheless, this approach involves a reduced applied voltage and an acidic electrolyte. The process offers several key advantages, including cost-effectiveness, suitability for complex geometries, uniform coating thickness, and straightforward process control. The properties of the oxide layer formed are significantly influenced by the applied voltage, time, and bath composition. The formation of TiO2 is dependent on these variables and can result in either rutile or anatase forms. Research has indicated that the rutile form exhibits exceptional wear resistance and hardness (Yetim, 2010; Izmir and Ercan, 2018).
Şenaslan et al. (2023) investigated the wear characteristics of Ti45Nb alloy by subjecting it to various voltage levels. The results indicate that the form of TiO2 and the thickness of the coating varied based on the different voltages used with an electrolyte containing H2SO4. The application of a voltage of 200 V resulted in the highest level of wear resistance. Asl et al. (2023) conducted a study where they utilized the anodization process on Cp-Ti, Ti6Al4V, and Ti45Nb alloys, applying the same process parameters. Based on the findings, the Ti45Nb alloy exhibited a more pronounced change in hardness compared to the other two alloys, with an increase of 94%. Ti45Nb alloy exhibited greater resistance to wear and higher hardness values, which were directly influenced by the amount of rutile present in its structure (Asl et al., 2023).
Upon reviewing the recent studies, it was observed that there is a scarcity of research on the tribological characteristics of anodized titanium and its alloys. The previous paragraph provides a summary of the existing literature on this topic. As stated earlier, TiO2 exists in two distinct forms: rutile and anatase. Among these, rutile possesses greater hardness and is necessary in applications that demand high wear resistance. Therefore, research focused on enhancing the plating bath and developing a rutile-based coating layer has demonstrated exceptional wear resistance.
4.3 Chemical vapor deposition
Chemical vapor deposition (CVD) refers to a group of techniques employed to produce usually hard coatings, typically a few microns thick, on the surfaces of metals and alloys. This technique involves the deposition of vaporized material onto a heated substrate material, either on its surface or within its interior. Coating properties can be influenced by factors such as the substrate material, process temperature, gas mixture, and gas flow pressure. The most commonly utilized types of chemical vapor deposition are traditional, minimal pressure chemical vapor deposition and plasma activated/assisted chemical vapor deposition (PACVD). Further information regarding the methodology can be located in other sources (Carlsson and Martin, 2010; Al-Asadi and Al-Tameemi, 2022).
Recent studies have shown that diamond-like-carbon (DLC) coatings are extensively studied for enhancing the tribological properties of titanium and its alloys. Ghio et al. (Ghio et al., 2023) conducted a study where they applied a DLC coating onto the surface of a Ti6Al4V alloy that was additively manufactured. They used the plasma-assisted CVD method for this process and then compared the properties of the DLC coating with those of PVD-AlCrN coatings. The DLC coating exhibited a lower coefficient of friction compared to the AlCrN coating (Ghio et al., 2023). Grabarczyk et al. (2020) investigated the impact of thermo-chemical treatments on the surface of Ti6Al4V alloy PVD and CVD coatings. According to the findings, carburization offers a low friction coefficient and wear rate (Grabarczyk et al., 2020). Zhang et al. (2020a) employed plasma-assisted CVD and plasma nitriding techniques to modify the surface of the Ti6Al4V alloy. The wear resistance was enhanced by this method, as indicated by the results (Zhang J. et al., 2020).
CVD is commonly employed to create thin film coatings that exhibit exceptional wear resistance and a low coefficient of friction. Due to the thin film characteristic of the coating layer, the parts used as biomaterials are susceptible to damages such as cracking and separation, which are dependent on the applied load. In light of this situation, researchers have conducted studies to enhance the coating characteristics of titanium and its alloys in CVD coating by implementing an additional technique, such as plasma nitriding. Nevertheless, there is a scarcity of research on the topic of biomedical titanium and its alloys, making it a crucial area in need of further investigation.
4.4 Physical vapor deposition
The formation of thin film coatings on the surface of materials is frequently achieved through physical vapor deposition (PVD). This method depends on the concept of transforming the target material into vapor through sputtering or evaporation, and then depositing it onto the surface of the material to be coated. Three of the most frequently employed PVD methods are sputter deposition, ion deposition, and vapor evaporation. The primary benefits of these coatings include high hardness, wear and corrosion resistance, high density, and good biocompatibility. Upon reviewing the recent literature, it is evident that a variety of coatings, including ZrN vr ta-C (Aslan et al., 2023), CrAlMoN (Bobzin et al., 2022), anodic alumina nanotubes (Sarraf et al., 2023), TiO2–SiO2 multilayer film (Çomaklı et al., 2023), and Ti3Au, are generally developed and applied to a variety of Ti alloys using PVD method (please see Table 5).
PVD, similar to CVD, is a technique used to produce thin film coatings that have excellent wear resistance and a low coefficient of friction, particularly on steel surfaces. Recent studies on PVD coating of titanium and its alloys have demonstrated the production of coatings with exceptional tribological performance. PVD coatings exhibit limited adhesion to the substrate material, and there is a potential for premature damage to occur as a result of the loading on the implants. To utilize PVD coatings in biomedical applications, it is necessary to enhance their properties while considering this circumstance.
4.5 Sol-gel coatings
Sol-gel coating technique allows for the obtaining of coatings on material surfaces that possess the desired biological properties and are resistant to wear and corrosion. The initial stage of the process involves the production of gel from the precursors through the use of appropriate reagents via the sol process. Subsequently, the gel is dehydrated and transformed into a solid state through the sintering procedure. It has been observed that this procedure is employed to enhance the tribological characteristics of titanium and its alloys. Al2O3/Gr/HAP (Shanmugapriya et al., 2021; Shanmugapriya et al., 2022), alumina/hydroxyapatite/graphene (Shanmugapriya et al., 2021), and graphene oxide (Li et al., 2020) coatings were obtained on the Ti6Al4V alloy surface using the sol-gel method.
Sol-gel is a coating technique that can effectively be used on titanium and its alloys. However, upon reviewing the studies conducted in recent years, it was observed that there were significant limitations in the research on the properties of these coatings, specifically in regards to corrosion, biocompatibility, and tribological properties. Hence, a thorough examination of the wear properties of these coatings is necessary for their application on implants.
4.6 Thermal spray coatings
Thermal spray coatings are a distinct category of coatings that are specifically applied to titanium and its alloys. This technique involves introducing feedstock, which can be in the form of powder, wire, rod, or suspension, into a spray torch. The feedstock is then sprayed onto the substrate material while it is in a molten or nearly molten state. Further information on thermal spray coatings can be found in other sources (Berger, 2015; Meghwal et al., 2020). Thermal spray methods are used to coat titanium and its alloys for biomedical applications. Upon careful examination of recent studies, hydroxyapatite coatings emerge as particularly notable (Singh G. et al., 2022; Hussain et al., 2023; Shankar et al., 2024). However, studies on the wear properties of these coatings are limited (Thirumalvalavan et al., 2022).
Thermal spray is extensively utilized in industrial applications to enhance wear resistance. Nevertheless, there is a scarcity of research investigating the tribological characteristics of biomedical titanium and its alloys. It is advantageous to incorporate research investigating the tribological characteristics of these coatings in the literature.
4.7 Laser cladding
Laser cladding has emerged as an extensively studied technique in recent years for enhancing the wear resistance of metals and alloys. This technique involves utilizing high-energy lasers to melt, solidify, and cool various materials such as powder, paste, or wire onto the surface of substrate materials. The resultant coating layers are of substantial thickness and exhibit exceptional adhesion properties to the substrate. Nevertheless, the expenses associated with investing in and maintaining this approach are substantial, and there is a risk of the substrate melting and experiencing segregation during the process. Comprehensive information regarding the method can be found in other sources (Wu Q. et al., 2024). The laser cladding method has been utilized in recent years to apply various coatings on the surface of titanium and its alloys, including but not limited to Ca/P (Liu B. et al., 2021), CaO-SiO2-MgO (Li et al., 2021), TiC/TiB (Chen et al., 2021), and TiNb (Zheng and Xu, 2023) enhancing their wear resistance.
Upon analyzing the recent studies, it is evident that laser cladding is a highly effective technique for enhancing the wear resistance of titanium and its alloys. Nevertheless, the cladding technique can result in chemical and microstructural irregularities within the coating layer. Additionally, there are challenges related to the inability to operate within tight tolerances. Addressing these issues has the potential to enhance the efficacy of the laser cladding technique for coating biomedical titanium and its alloys.
4.8 Nitriding
Nitriding of titanium and its alloys has been a subject that has been researched for a long time. Because the α-titanium phase can dissolve nitrogen at high rates and forms hard TiN and Ti2N compounds. In this way, layers or regions with a hardness of up to 3000 HV are formed on the surfaces. The nitriding process can be carried out by methods with different mechanisms, the most common of which are gas, plasma, ion and laser nitriding. Details of these methods can be found elsewhere (Selamat et al., 2001; Zhecheva et al., 2005; Zhecheva et al., 2006; Jiang et al., 2022).
The nitriding process not only increases the hardness Ti alloys, but also causes a decrease in the friction coefficient and wear rate. Das et al. (2024) applied laser surface treatment to Ti6Al4V alloy in nitrogen atmosphere. A lower friction coefficient was reported as a result of the process (Das et al., 2024). The decrease in wear rate was also reported in studies by Shen and Wang (2023), Kaewnisai et al. (2023), and Xu et al. (2023).
Nitriding is a highly effective technique for applying a coating to titanium and its alloys, due to their desirable characteristics of high hardness, wear resistance, and low coefficient of friction. Recent studies have shown that this efficient technique is utilized on conventional titanium and its alloys, including cpTi and Ti6Al4V. This subject has the potential to significantly impact the field of nitriding and the tribological properties of new generation titanium and its alloys.
4.9 Coating interface
Surface coatings applied to biomedical titanium and titanium alloys could significantly improve the tribological performance of the materials. One of the main factors affecting the material performance is the behaviour of the interfacial surface between the titanium substrate material and the coating material. Therefore, efforts to achieve superior tribological performance by improving the interfacial properties have been the focus of research.
Efforts to improve the interface could be achieved by mechanical, chemical, and physical bonding mechanisms. For mechanical bonding, the roughening of the surface is essential. Methods such as sandblasting (Wang et al., 2024) and shot peening (Yıldıran et al., 2015; Avcu, 2017b) are preferred. In the context of chemical bonding, coating methods such as CVD (Liu et al., 2024b), PVD (Noori et al., 2023), and sol-gel (Murari and Chauhan, 2024) could be purposefully chosen in order to achieve the desired formation of covalent, ionic, and metallic bonds. Finally, physical bonding includes Van der Waals forces (Grubova et al., 2020) and hydrogen bonding (as seen in biomolecular coatings) (Tan et al., 2022). The connection types as well as the bonding mechanism of the interface could directly affect the tribological properties. For this reason, direct connection, use of interlayer (Ali et al., 2024), functional gradient coating (Singh J. et al., 2021), and laminated coating (Wu L. et al., 2024) have been investigated and applied for substrate material, coating material, and tribological expectations.
A variety of testing and characterisation methods are available for the purpose of evaluating the targeted tribological performance of interfaces. The phenomenon of adhesion strength (Błoniarz et al., 2024) has been observed in almost all studies. Tensile (Jang et al., 2024) and scratch (Singh et al., 2024) tests have been employed for this purpose. Additionally, other mechanical tests such as nanoindentation (Valentim Gelamo et al., 2024), abrasion (Khan et al., 2024), and fracture-crack resistance (Fernandes et al., 2024) may be conducted. Thermal cycling (Xu M. et al., 2024) tests are utilized to ascertain the behavior of the interface under thermal stresses. Finally, corrosion tests (Alontseva et al., 2024) are employed to determine chemical resistance. To determine the morphological and topographical effects of these tests, advanced characterization methods including scanning electron microscopy (SEM), transmission electron microscopy (TEM), X-ray photoelectron spectroscopy (XPS), and energy dispersive spectroscopy (EDS) are employed.
Modelling and simulation studies which consider together the coating, the substrate, and the interface provide an important opportunity for researchers to investigate areas such as preventive design and optimisation. To achieve this, researchers employ a range of techniques including the finite element method (Liu W. et al., 2024), molecular dynamics (Mirzayev et al., 2024) and Monte Carlo (dos Santos-Junior et al., 2024) simulations, density functional theory (Kaseem et al., 2024), and multiscale modelling (Liu et al., 2023). The finite element method is employed to examine a range of mechanical properties, including stress, deformation analysis, and crack propagation; whereas molecular dynamics simulations are utilized to investigate the mechanisms of interaction and bonding at the interface as well as the thermal behaviour associated with thermal expansion and heat conduction. Monte Carlo simulations are capable of replicating a multitude of performance characteristics including wear, surface roughness, diffusion, and corrosion. Density functional theory employs quantum mechanical principles to analyse the electronic structure and chemical bonding at the interface, and can also calculate surface energy and adhesion forces. Lastly, macro-level behaviours can be determined by applying micro-mechanical and nano-mechanical models with multi-scale modelling. A selection of software is available to improve the time and cost-effectiveness of these simulations and models. Overall, the advanced research topics of the interface presented above have notable research potential for academia-industry collaboration.
4.10 Shortcomings and future directions in coatings methods
A number of techniques including plasma electrolytic oxidation (PEO), anodization, chemical and physical vapor deposition, sol-gel, thermal spray, laser cladding, and nitriding can be used to enhance the durability and to reduce the friction of titanium and its alloys. PEO, laser cladding, and nitriding methods have particularly gained prominence in recent years. The presence of defects, such as porosity, cracks, and diffusion channels in the structure of PEO coatings has a detrimental impact on their wear resistance. The strategies for eradicating these defects have become a prominent concern in recent years. Furthermore, the laser cladding technique has garnered significant attention recently, necessitating further research on the implementation of novel coatings and the assurance of chemical and microstructural homogeneity. In addition, nitriding is a crucial technique for enhancing tribological properties through the application of a protective coating. Nevertheless, the studies conducted in recent years have solely concentrated on conventional titanium and its alloys, thereby necessitating an investigation into new generation alloys as well.
5 Advances in implementing mechanical surface treatment methods on biomedical Ti alloys for tribological applications
Most industrial application failures are related to material surface properties and microstructural features, such as fretting fatigue, fatigue fracture, fracture toughness (Armağan and Arıcı, 2021; Saxena et al., 2024; Wagih et al., 2024), wear (Avcu Y. Y. et al., 2023), cracks, scratches, and corrosion (Avcu E. et al., 2023). Nanocrystalline and ultrafine-grained materials obtained with mechanical surface treatment methods have enhanced friction, wear properties, and superior corrosion resistance due to improved surface and microstructural properties (e.g., hardness, strength, ultra-fine grained microstructures, etc.) (Li et al., 2017; Maurel et al., 2019). Tribological properties are enhanced by the formation of ultra-fine grains (UFG) at the surface with the implementation of mechanical surface treatment on Ti alloys. Severe plastic deformation (SPD) is often used to transform coarse-grained microstructure into ultrafine sized or nano grained microstructure (Subham et al., 2024) since nanocrystalline and ultrafine-grained materials possess numerous properties such as high hardness (Yildiran Avcu et al., 2020; Ganesh and Kumar, 2021; Avcu Y. Y. et al., 2023) and strength (Ganesh et al., 2014; Rajabi et al., 2019), excellent friction, wear properties (Li et al., 2017; Zhou et al., 2019; Singh S. et al., 2021; Das et al., 2024) and superior corrosion resistance (Subham et al., 2024) without any change in the chemical composition of the alloy. Grain refinement and high compressive residual stress are responsible for these improved properties (Alikhani Chamgordani et al., 2018). Over the past 2 decades, severe plastic deformation (SPD) methods for nanostructured material manufacturing have garnered attention.
Therefore, mechanical surface treatment methods like laser peening (LP) (Yin et al., 2018; Tong et al., 2019; Zhou et al., 2019; Gu et al., 2023; Praveenkumar et al., 2023; Das et al., 2024; Li J. et al., 2024), surface mechanical attrition treatment (SMAT) (Wen et al., 2011; Anand Kumar et al., 2013; Wen et al., 2014; Li et al., 2017; Alikhani Chamgordani et al., 2018; Maurel et al., 2019; Rajabi et al., 2019; Acharya et al., 2020; Singh S. et al., 2021), shot peening (SP) (Fridrici et al., 2001; Ganesh et al., 2012; Ganesh et al., 2014; Wang et al., 2018; Yang et al., 2018; Yildiran Avcu et al., 2020; DiCecco et al., 2021; Avcu Y. Y. et al., 2023; Vella et al., 2023; Subham et al., 2024), ultrasonic shot peening (USP) (Ji et al., 2023; Subham et al., 2024), and ultrasonic impact treatment (UIT) (Ji et al., 2023) have been used in order to improve their performance in the tribological applications. Mechanical surface treatment of Ti and Ti alloys improves surface and subsurface properties, particularly wear properties (Wen et al., 2014). Table 6 summarises some recent studies related to the use of mechanical surface treatment methods on improving tribological properties of biomedical Ti alloys.

Table 6. Recent studies employing mechanical surface treatment methods on biomedical Ti alloys for improving their tribological properties.
5.1 Shot peening
The number of studies investigating the impact of shot peening (SP) on the tribological properties of engineering materials has recently increased (Ganesh et al., 2012; Wang et al., 2018; Yang et al., 2018; Yildiran Avcu et al., 2020; DiCecco et al., 2021; Moradi et al., 2022; Avcu Y. Y. et al., 2023; Ji et al., 2023; Vella et al., 2023; Subham et al., 2024). This is due to the fact that SP has the potential to enhance the tribological properties of Ti alloys, in addition to its well-known effect of enhancing the fatigue strength and service life of engineering materials. The repeated impact of high-velocity shots accelerated through a nozzle on the surfaces of materials via shot peening modifies their surface and subsurface properties (e.g., hardness (Yildiran Avcu et al., 2020; Avcu et al., 2021; Moradi et al., 2022; Vella et al., 2023), residual stress (Moradi et al., 2022), microstructural features (Yildiran Avcu et al., 2020; Moradi et al., 2022; Subham et al., 2024)), along with their tribological behaviour (Ganesh et al., 2014; Wang et al., 2018; Yang et al., 2018; Yildiran Avcu et al., 2020; Moradi et al., 2022; Vella et al., 2023). The tribological properties of the material are also significantly influenced by the surface work-hardening and changes in surface roughness that are caused by shot-peening. (Yildiran Avcu et al., 2020; Avcu Y. Y. et al., 2023; Subham et al., 2024). SP offers several advantages compared to SPD methods, such as minimal equipment requirements, the ability to adjust surface and subsurface properties through changes in process parameters, low energy consumption, short processing time, the ability to apply complex shapes to workpieces, and high production efficiency (Avcu et al., 2021).
There are reports available that discuss the tribological behavior of biomedical titanium alloys. The wear resistance of SPed Ti-6Al-4V was enhanced by 57% as a result of the formation of severe plastic deformation, nanostructure, compressive residual stress, micro-strains, and grain refinement on the surface (Moradi et al., 2022). The enhancement of surface hardness in the SPed Ti-6Al-4V has led to an improvement in the specimen’s wear resistance. Oxidative wear has been observed in specimens tested at lower sliding speeds, while delaminative wear has occurred at higher sliding velocities. (Ganesh et al., 2012). Several studies have shown that SP had minimal impact on the coefficient of friction (COF) and wear rates. The COF and wear rates were found to be similar when using a steel ball (DiCecco et al., 2021) and an alumina (Avcu Y. Y. et al., 2023) counterface, and the observations of debris were also comparable (DiCecco et al., 2021; Avcu Y. Y. et al., 2023). The study confirms that the influence of SP on the wear behavior of Ti–6Al–4V under fretting conditions is negligible. This is evident from the observation that experiments conducted with polished or shot peened specimens, with different displacement amplitudes, result in the same cumulated dissipated energy and wear measurements for both types of specimens (Fridrici et al., 2001). The main distinction observed between the wear testing results of the SPed and untreated samples was that wear in the SPed samples was primarily caused by oxidation (DiCecco et al., 2021).
5.2 Laser peening
Recently, enhancing of the wear resistance of metal alloys via laser surface modification methods, such as laser peening (LP) (Zhou et al., 2019) or laser shock peening (LSP) (Tong et al., 2019), and laser surface treatment (LST) (Das et al., 2024), have attracted great interest. Laser peening (LP) has the ability to create a plasma with high pressure, which can apply compressive residual stress to the surface (Yin et al., 2018; Praveenkumar et al., 2023), increase the surface micro-hardness (Zhou et al., 2019; Gu et al., 2023; Das et al., 2024; Li J. et al., 2024), and refine the grain of Ti alloys (Yin et al., 2018; Praveenkumar et al., 2023) to improve fatigue, wear (Das et al., 2024), tensile, and corrosion properties (Tong et al., 2019; Zhou et al., 2019).
LST technique offers several advantages compared to other surface treatment methods. These advantages include faster processing speed, minimal heat affected zone and structural deformation, higher precision, and environmental friendliness (Das et al., 2024). In the past, the technique has been effectively used to alter the microstructure and/or composition of titanium and its alloys in order to enhance their properties for biomedical purposes (Das et al., 2024). Laser surface treatments are sophisticated techniques used to create micro-scale structures on the surface of medical Ti6Al4V alloy. These structures are designed to improve the alloy’s ability to resist wear and tribo-corrosion under various process parameters (Yin et al., 2018; Zhou et al., 2019; Das et al., 2024).
The surface micro-hardness of the LPed Ti-6Al-4V was augmented by a substantial 25.7%, and the hardened layer extended to a depth exceeding 0.3 mm. The mean coefficient of friction (COF) and the amount of wear mass loss were both significantly decreased to 50% and 29.2%, respectively, due to the higher laser energy and increased number of impacts (Zhou et al., 2019). At higher temperatures, the wear performance of LPed samples was enhanced, with a reduction in wear volume loss of 30.3%, 19.58%, and 13.43% compared to the unpeened samples under different loads (10, 20, and 30 N) (Praveenkumar et al., 2023). The application of LSP treatment effectively decreases the depth, width, and volume of wear, while simultaneously improving the tribological characteristics of the Ti-6Al-4V alloy (Gu et al., 2023). An enhanced enhancement in wear resistance is observed as laser intensity increases (wear volume decreases by 27.2%) (Gu et al., 2023). The wear process of Ti-6Al-4V alloy primarily involves three mechanisms: abrasive wear, fatigue wear, and oxidation wear (Gu et al., 2023). The enhanced tribological characteristics of the LPed specimen can be attributed to work hardening, compressive residual stress, and refined grain. These factors effectively delay the initiation and propagation of cracks during the wear process (Tong et al., 2019).
5.3 Surface mechanical attrition treatment (SMAT)
Surface mechanical attrition treatment (SMAT) is a well-known method in the scientific community for producing a nanostructured layer on metal surfaces. It is one of several severe plastic deformation (SPD) methods that have gained significant attention (Singh S. et al., 2021). During the process of SMAT, spherical balls with a polished surface are placed inside a chamber that reflects light. The chamber is then vibrated using a device that generates vibrations. The samples that are being treated are attached to the top side of the chamber. Resonating the balls results in a rapid and intense bombardment of the sample surface by a multitude of flying balls. (Wen et al., 2011). Consequently, successive plastic deformations occur through repeated impacts from various directions, resulting in significant plastic deformation and the reduction of grain size to nano-scale dimensions (Rajabi et al., 2019). SMAT results in a nanostructured surface, enhanced mechanical properties (Acharya et al., 2020), high hardness (Anand Kumar et al., 2013; Alikhani Chamgordani et al., 2018; Acharya et al., 2020), good wear resistance while keeping the overall composition and/or phases unchanged and without changing chemical compositions (Li et al., 2017) and any contamination (Anand Kumar et al., 2013).
The improvement in wear resistance is due to the presence of a nanostructured surface that has a higher level of hardness. This increased hardness is primarily a result of grain refinement and strain hardening, which is achieved by mechanically applying a high amount of strain energy. Research on the tribological properties of nano/ultrafine grained surface materials has been restricted due to the challenges in creating samples that are suitable for friction and wear testing (Anand Kumar et al., 2013). For instance, certain studies have shown that the wear rates of samples treated with surface mechanical attrition treatment (SMAT) were greater than those of untreated samples. Put simply, there was a difference between the increase in hardness and the decrease in wear rate. Due to its inherent low toughness, the hardening treatment of titanium resulted in a degradation of its toughness. As a result, the samples eventually cracked and fractured during the wear process, indicating a reduction in wear resistance (Rajabi et al., 2019). However, the wear resistance was improved after SMAT, as evidenced by a 32% reduction in wear volume loss and a 21% decrease in friction coefficient. These improvements can be attributed to the enhanced ductility on the surface (Acharya et al., 2020). The wear resistance of CP-Ti was significantly enhanced. The friction coefficient of CP-Ti was decreased through the use of SMAT. As the treatment duration increased, the friction coefficient decreased even more, reaching a reduction of 66% by the end of the process. The increase in SMAT duration resulted in the elongation of the initial low friction coefficient stability, which can be attributed to the increase in the depth of the deformation layer (Alikhani Chamgordani et al., 2018). The samples treated with SMAT demonstrated reduced wear volume and specific wear rate in comparison to the untreated samples. When comparing samples fretted against alumina balls to samples fretted against steel balls at lower normal loads, the former showed higher wear volume and specific wear rate. The wear mechanism observed in this case is caused by three-body abrasion, which is induced by the generation of abrasive hard wear debris resulting from a tribochemical reaction between the Ti–6Al–4V sample and the alumina ball (Anand Kumar et al., 2013).
5.4 Shortcomings and future directions in mechanical surface treatments
Currently, shot peening, laser peening, and surface mechanical attrition are the most commonly employed mechanical surface treatment techniques for enhancing the tribological performance of biomedical Ti alloys. To achieve the optimal tribological properties for tailored applications, further research is required on the processing parameters of these methods such as shot size, pressure, laser power, contact pressure, cover rate, etc. The research area of hybrid and innovative water jet shot peening (Hou et al., 2022; Chakkravarthy et al., 2023; Wang G. et al., 2023; Wang Z. et al., 2023; Lu et al., 2024) which combines the techniques of shot peening (Yıldıran et al., 2015; Yildiran Avcu et al., 2020; Avcu et al., 2021) and abrasive water jet machining (Armağan and Arıcı, 2017; Armağan, 2021; Armağan and Arıcı, 2024b; Armağan and Arıcı, 2024a), is gaining increasing interest. Finite element modelling has already been utilized (Daoud et al., 2021; Zhou et al., 2022; Huang et al., 2023) to project the plastic strain and residual stress based on mechanical surface treatment parameters, demonstrating a good potential in the field. Nevertheless, there is a lack of research on modeling studies aimed at predicting tribological properties such as coefficient of friction and wear rate. Therefore, research in this area is anticipated to grow due to the time-consuming and expensive nature of investigating the relationship between processing parameters and tribological performance. Using these methods before the coating process has shown great potential (Cao et al., 2020; Dong et al., 2022; Xiao et al., 2022) in enhancing the adhesion, mechanical, and tribological properties of the coatings. Consequently, there is a projected increase in research focused on combining mechanical surface treatment techniques with coating technologies within the field.
6 Advances in developing biomedical grade Ti matrix composites for tribological applications
Titanium matrix composites (TMCs) consist of a titanium matrix and a reinforcing element, which can be a metal, ceramic, or organic compound (Somasundaram Prasadh et al., 2021). When considering composite material structures, it is advantageous to utilize the combined impact of the exceptional characteristics of both the matrix and reinforcing elements. Therefore, conducting research in the domain of composite design and production has the potential to improve the performance of implants. Moreover, the healthcare sector can verify the economic feasibility and reliability of implants to the degree that they are supported by scientific evidence. Titanium matrix composites have the potential to greatly enhance lifetime and reliability through their tribological behavior (Sousa et al., 2022). This chapter provides a review of the research conducted in the past 5 years on the tribological properties of titanium matrix composites, focusing on their design, manufacturing, testing, and performance characteristics.
6.1 Processing and composition of Ti matrix composites
The design and manufacturing conditions of titanium matrix composites exert a direct influence on their tribological behaviour. The matrix, reinforcement and operating conditions of composites attribute these behaviors to three main factors. The initial main factor concerns such as the type, shape, size, volume fraction and distribution of the reinforcing elements within the matrix phase. Phase structures affecting the hardness of titanium and operating conditions such as load, cycle, frequency, sliding distance and usage time constitute the other two main factors (Lal and Dey, 2024b). The choice of reinforcing elements for titanium matrix composites is influenced by various design objectives, such as ensuring biocompatibility (Kumar et al., 2021; Somasundaram Prasadh et al., 2021; Afrouzian and Bandyopadhyay, 2023), improved wear and corrosion resistance, and high hardness (Sousa et al., 2021a; Sousa et al., 2021b; Sousa et al., 2022). It is preferable for the reinforcing elements to exhibit isotropy and possess a high level of hardness (Gonçalves et al., 2023). In recent years, there has been a preference for the use of reinforcement materials such as TiC (Lal and Dey, 2024a; b), Al2O3 (Afrouzian and Bandyopadhyay, 2023; Sousa et al., 2023), TiB (Singh N. et al., 2022), hydroxyapatite (Somasundaram Prasadh et al., 2021; Afrouzian and Bandyopadhyay, 2023), Si3N4 (Afrouzian and Bandyopadhyay, 2023), NbC (Gonçalves et al., 2023), ZrO2, nitinol and Mg (Somasundaram Prasadh et al., 2021) in research.
The previously mentioned design outcomes, specifically biocompatibility, enhanced wear and corrosion resistance, are also applicable to biomedical titanium matrices. The alloy type and production conditions of the matrix have a direct impact on the phase structure, and it is therefore essential that they are compatible with the reinforcing element. In recent years, especially Ti grade 2 (Sousa et al., 2021a; Sousa et al., 2022; Sousa et al., 2023; Sousa et al., 2024), Ti6Al4V (Avila et al., 2021; Afrouzian and Bandyopadhyay, 2023; Lal and Dey, 2024a; b) and Ti-Nb (Somasundaram Prasadh et al., 2021; Gonçalves et al., 2022; Singh N. et al., 2022; Gonçalves et al., 2023) alloys are preferred as matrix materials. In addition, the principles of laser deposition (Singh N. et al., 2022; Afrouzian and Bandyopadhyay, 2023), sintering (Çaha et al., 2021; Sousa et al., 2023) and hot pressing (Sousa et al., 2021b; Gonçalves et al., 2022) are becoming more favored in the manufacture of Ti matrix composites.
6.2 Tribological testing of Ti matrix composites
Conventional tests, such as ball-on-disc tests (Lal and Dey, 2024a; b), along with advanced tribocorrosion tests (Sousa et al., 2021a; Sousa et al., 2021b; Gonçalves et al., 2022), accurately simulate the operating conditions of titanium matrix composites and comprehensively analyze the tribological behavior by considering all relevant factors. Table 7 presents a summary of the tribological tests applied to titanium matrix composites over the past 5 years. The studies showed that the ball-on-plate test method was used more often. Moreover, when the stroke length is 3 and 5 mm, the reciprocating frequency is 1 Hz, the load is 1 N, and the friction pair is alumina, these conditions are commonly preferred. An noteworthy trend in recent years has been the widespread increase in tribocorrosion tests. Consequently, tribological testing in corrosive environments, such as body fluids, is a more accurate representation of the performance of biomedical titanium matrix composites in humans than testing in dry or lubricating environments.
Sousa et al. (2021a) examined the design and production conditions of Ti grade 2 matrix and B4C reinforced composites by conventional sintering and hot-pressing techniques. The study has shown that the interaction between the matrix and reinforcement differs depending on the production conditions. Conventional sintering resulted in the formation of significantly thicker reaction zones, smaller B4C particles and a greater degree of porosity. Such factors can directly impact the performance characteristics of the material, including mechanical, tribological and biocompatibility properties.
Sousa et al. (2021a); Sousa et al. (2021b); Sousa et al. (2023) studied the effects of different manufacturing and reinforcement elements with the Ti grade 2 matrix in tribocorrosion tests that offer a number of benefits. The tribological formation differences of Ti grade 2, Ti-Al2O3 and Ti-B4C composites by conventional sintering (PM) and hot-pressing (HP), according to similar test conditions detailed in Table 1. A visual inspection reveals that the greatest wear is observed in Ti grade 2, while the least wear is observed in the composite with Al2O3 reinforcement. It can be further observed that samples produced by hot-pressing exhibit reduced wear. It can be posited that the observed changes in tribological performance are a consequence of the microstructural alterations to the production methods. Finally, scanning electron microscopy (SEM) and energy-dispersive X-ray spectroscopy (EDS) images of the test element, alumina ball, corroborate the aforementioned observations.
6.3 Shortcomings and future directions in titanium matrix composites
The previously explained limitations of titanium matrix biomedical composites also highlight several underexplored areas in the field of tribological studies. There are multiple types of titanium alloys, several reinforcement elements, and various manufacturing methods used. The predominant focus of research on tribological improvements in composites has been on the characteristics of the reinforcing component such as its type, amount, and distribution. However, only a few studies have examined the variations in production methodology. Furthermore, there are still notable shortcomings in the domain of advanced process causation, particularly in areas such as parametric optimization and machine learning. The choice of Ti grade 2 and Ti6Al4V alloy as matrix materials represents a departure from previous conventional practices in the manufacturing of composite materials. Researchers are advised to embrace a comprehensive approach when it comes to the design and production processes of composites. This will enhance the ability to precisely convey cause-and-effect relationships. In addition, the inclusion of statistical gains, such as variance analysis on all design, process, and performance outcomes, will guarantee the establishment of consistent, quantifiable, and similar conditions. The utilization of parametric optimization and machine learning is highly recommended since processing of Ti matrix composites is a challenging and costly task.
7 Conclusion
Titanium (Ti) alloys are extensively utilized in biomedical applications due to their exceptional mechanical, physical, and surface characteristics. However, enhancing their tribological properties is crucial for expanding their range and performance of biomedical applications. The present review analyzes the latest advancements in improving the tribological characteristics of titanium alloys and titanium matrix composites for biomedical applications. The advances in enhancing the performance of Ti alloys for tribological purposes has focused on these specific strategies: biomedical coatings, mechanical surface treatment, and the design strategies for alloys and titanium matrix composites. The current review has examined these strategies in terms of their formulation, manufacturing techniques, tribological testing parameters, and characterization methodologies. This final section provides future research directions and suggestions regarding the discussed strategies for improving tribological behaviour of Ti alloys used for biomedical applications.
The tribological testing protocols for alloys and biomedical elements are yet to be well established. The majority of researchers rely on prior studies and their own experience, often neglecting limb-specific tests that consider the unique human limb kinematics and biology. It is imperative that comprehensive protocols for titanium alloys are developed. While conventional load-cell-based wear testers are invaluable, advanced techniques such as EBSD and HRTEM should be integrated to facilitate detailed examinations. It is also concerning that many studies lack statistical tools (e.g., ANOVA) to evaluate parameter effects. Furthermore, machine learning methods are not utilised despite their large potential. It is therefore essential that future research addresses these gaps; optimising tribological parameters for human limb applications and incorporating comprehensive design, implementation, and prediction stages.
A variety of techniques including PEO, anodization, vapor deposition, sol-gel, thermal spray, laser cladding, and nitriding have been demonstrated to enhance the durability of titanium alloys and reduce friction. PEO, laser cladding, and nitriding are prominent techniques, but PEO coatings face issues with defects affecting wear resistance. Further research is required on novel coatings and uniformity for laser cladding. Nitriding improves tribological properties with protective coatings, but studies mostly focus on conventional titanium alloys, indicating a need to explore new-generation alloys.
The tribological performance of biomedical Ti alloys can be enhanced through the application of shot peening, laser peening, and surface mechanical attrition. However, further research is required to determine the optimal processing parameters for achieving the best results. In recent investigations, finite element modeling helps with strain and stress predictions but lacks tribological property forecasts. Combining these treatments with coatings shows promise, indicating increased future research in this area.
The limitations of titanium matrix biomedical composites highlight the need for further investigation in tribological studies, particularly with regard to the diverse types of titanium alloys, reinforcement elements, and manufacturing methods. The majority of research has concentrated on the characteristics of the reinforcement components, rather than on the production methodologies. Significant gaps exist in the understanding of advanced process causation, particularly in the areas of parametric optimisation and machine learning. The traditional Ti grade 2 and Ti6Al4V alloys have been the subject of extensive research. This highlights the necessity for a comprehensive innovative approach to the design and manufacture of titanium matrix composites.
Author contributions
EA: Conceptualization, Formal Analysis, Investigation, Methodology, Validation, Writing–original draft, Writing–review and editing. MA: Conceptualization, Formal Analysis, Investigation, Methodology, Validation, Visualization, Writing–original draft, Writing–review and editing. YY: Conceptualization, Formal Analysis, Investigation, Methodology, Validation, Writing–original draft, Writing–review and editing. MG: Formal Analysis, Methodology, Project administration, Supervision, Writing–original draft, Writing–review and editing. BY: Formal Analysis, Methodology, Project administration, Supervision, Writing–original draft, Writing–review and editing. EA: Conceptualization, Data curation, Formal Analysis, Funding acquisition, Investigation, Methodology, Project administration, Resources, Software, Supervision, Validation, Visualization, Writing–original draft, Writing–review and editing.
Funding
The author(s) declare that no financial support was received for the research, authorship, and/or publication of this article.
Conflict of interest
The authors declare that the research was conducted in the absence of any commercial or financial relationships that could be construed as a potential conflict of interest.
Publisher’s note
All claims expressed in this article are solely those of the authors and do not necessarily represent those of their affiliated organizations, or those of the publisher, the editors and the reviewers. Any product that may be evaluated in this article, or claim that may be made by its manufacturer, is not guaranteed or endorsed by the publisher.
References
Abd-Elaziem, W., Darwish, M. A., Hamada, A., and Daoush, W. M. (2024). Titanium-Based alloys and composites for orthopedic implants Applications: a comprehensive review. Mater. and Des. 241, 112850. doi:10.1016/j.matdes.2024.112850
Acharya, S., Panicker, A. G., Gopal, V., Dabas, S. S., Manivasagam, G., Suwas, S., et al. (2020). Surface mechanical attrition treatment of low modulus Ti-Nb-Ta-O alloy for orthopedic applications. Mater Sci. Eng. C Mater Biol. Appl. 110, 110729. doi:10.1016/j.msec.2020.110729
Afrouzian, A., and Bandyopadhyay, A. (2023). 3D printed silicon nitride, alumina, and hydroxyapatite ceramic reinforced Ti6Al4V composites - tailored microstructures to enhance bio-tribo-corrosion and antibacterial properties. J. Mech. Behav. Biomed. Mater 144, 105973. doi:10.1016/j.jmbbm.2023.105973
Al-Asadi, M. M., and Al-Tameemi, H. A. (2022). A review of tribological properties and deposition methods for selected hard protective coatings. Tribol. Int. 176, 107919. doi:10.1016/j.triboint.2022.107919
Ali, R., Faizi, T., Abbas, S. Z., and Khan, M. I. (2024). Effect of titanium interlayer configurations on residual stresses and performance of titanium/titanium nitride multilayer coatings. Surf. Eng. 0 (0), 370–383. doi:10.1177/02670844241246931
Alikhani Chamgordani, S., Miresmaeili, R., and Aliofkhazraei, M. (2018). Improvement in tribological behavior of commercial pure titanium (CP-Ti) by surface mechanical attrition treatment (SMAT). Tribol. Int. 119, 744–752. doi:10.1016/j.triboint.2017.11.044
Aliofkhazraei, M., Macdonald, D. D., Matykina, E., Parfenov, E. V., Egorkin, V. S., Curran, J. A., et al. (2021). Review of plasma electrolytic oxidation of titanium substrates: mechanism, properties, applications and limitations. Appl. Surf. Sci. Adv. 5, 100121. doi:10.1016/j.apsadv.2021.100121
Alontseva, D., Safarova, Y., Voinarovych, S., Obrosov, A., Yamanoglu, R., Khoshnaw, F., et al. (2024). Biocompatibility and corrosion of microplasma-sprayed titanium and tantalum coatings versus titanium alloy. Coatings 14 (2), 206. doi:10.3390/coatings14020206
Anand Kumar, S., Ganesh Sundara Raman, S., Sankara Narayanan, T. S. N., and Gnanamoorthy, R. (2013). Influence of counterbody material on fretting wear behaviour of surface mechanical attrition treated Ti–6Al–4V. Tribol. Int. 57, 107–114. doi:10.1016/j.triboint.2012.07.021
Armağan, M. (2021). Cutting of St37 steel plates in stacked form with abrasive water jet. Mater. Manuf. Process. 36 (11), 1305–1313. doi:10.1080/10426914.2021.1906895
Armağan, M., and Arıcı, A. A. (2017). Cutting performance of glass-vinyl ester composite by abrasive water jet. Mater. Manuf. Process. 32 (15), 1715–1722. doi:10.1080/10426914.2016.1269919
Armağan, M., and Arıcı, A. A. (2021). Investigation on fracture toughness of polytetrafluoroethylene with impact essential work of fracture method. Polym. Polym. Compos. 29 (9_Suppl. l), S335–S343. doi:10.1177/09673911211003392
Armağan, M., and Arıcı, A. A. (2024a). Analysis based on surface and kerf performance in multi-simultaneous cutting of S235JR structural steel with abrasive water jet. Mach. Sci. Technol., 1–23. doi:10.1080/10910344.2024.2332875
Armağan, M., and Arıcı, A. A. (2024b). Determination and prediction of surface and kerf properties in abrasive water jet machining of Fe-Cr-C based hardfacing wear plates. J. Manuf. Process. 117, 329–345. doi:10.1016/j.jmapro.2024.03.016
Asl, H. G., Sert, Y., Küçükömeroğlu, T., and Bayrak, Ö. (2023). The comparison of wear performances of CP-Ti, Ti6Al4V, Ti45Nb alloys oxidized by anodic oxidation under ambient air and vacuum conditions. Mater. Today Commun. 34, 105466. doi:10.1016/j.mtcomm.2023.105466
Aslan, N., Aksakal, B., Cihangir, S., Cetin, F., and Yilmazer, Y. (2023). ZrN and ta-C coatings on titanium for biomedical applications: improved adhesion, corrosion, antibacterial activity, and cytotoxicity properties. J. Mater. Res. 38 (16), 3923–3936. doi:10.1557/s43578-023-01109-3
Avcu, E. (2017a). The influences of ECAP on the dry sliding wear behaviour of AA7075 aluminium alloy. Tribol. Int. 110, 173–184. doi:10.1016/j.triboint.2017.02.023
Avcu, E. (2017b). Surface properties of AA7075 aluminium alloy shot peened. Acta Mater. Turc. 1, 3–10.
Avcu, E., Abakay, E., Yıldıran Avcu, Y., Çalım, E., Gökalp, İ., Iakovakis, E., et al. (2023a). Corrosion behavior of shot-peened Ti6Al4V alloy produced via pressure-assisted sintering. Coatings 13 (12), 2036. doi:10.3390/coatings13122036
Avcu, Y. Y., Gonul, B., Yetik, O., Sonmez, F., Cengiz, A., Guney, M., et al. (2021). Modification of surface and subsurface properties of AA1050 alloy by shot peening. Mater. (Basel) 14 (21), 6575. doi:10.3390/ma14216575
Avcu, Y. Y., Iakovakis, E., Guney, M., Çalım, E., Özkılınç, A., Abakay, E., et al. (2023b). Surface and tribological properties of powder metallurgical Cp-Ti titanium alloy modified by shot peening. Coatings 13 (1), 89. doi:10.3390/coatings13010089
Avila, J. D., Stenberg, K., Bose, S., and Bandyopadhyay, A. (2021). Hydroxyapatite reinforced Ti6Al4V composites for load-bearing implants. Acta Biomater. 123, 379–392. doi:10.1016/j.actbio.2020.12.060
Baldin, E. K., Santos, P. B., De Castro, V. V., Aguzzoli, C., Maurmann, N., Girón, J., et al. (2021). Plasma electrolytic oxidation (PEO) coated CP-Ti: wear performance on reciprocating mode and chondrogenic–osteogenic differentiation. J. Bio- Tribo-Corrosion 8 (1), 29. doi:10.1007/s40735-021-00627-z
Bangera, M., and D'costa, V. (2015). Titanium and its alloys: properties and applications for use as an oral biomaterial: a review. J. Res. Dent. 3, 592. doi:10.19177/jrd.v3e12015592-599
Barriobero-Vila, P. (2015). Phase transformation kinetics during continuous heating of α+β and metastable β titanium alloys.
Berger, L.-M. (2015). Application of hardmetals as thermal spray coatings. Int. J. Refract. Metals Hard Mater. 49, 350–364. doi:10.1016/j.ijrmhm.2014.09.029
Bian, Y., Cao, L., Zeng, D., Cui, J., Li, W., Yu, Z., et al. (2023). The tribological properties of two-phase hard and soft composite wear-resistant coatings on titanium alloys. Surf. Coatings Technol. 456, 129256. doi:10.1016/j.surfcoat.2023.129256
Biesiekierski, A., Lin, J., Li, Y., Ping, D., Yamabe-Mitarai, Y., and Wen, C. (2016). Investigations into Ti-(Nb,Ta)-Fe alloys for biomedical applications. Acta Biomater. 32, 336–347. doi:10.1016/j.actbio.2015.12.010
Błoniarz, A., Marchewka, J., Sitarz, M., Drożdż, K., Gosiewski, T., Brzychczy-Włoch, M., et al. (2024). Effect of adding selected carboxylic acids to the solution on electrophoretic deposition, adhesion strength, morphology and antibacterial properties of chitosan coatings on titanium. Prog. Org. Coatings 189, 108258. doi:10.1016/j.porgcoat.2024.108258
Bobzin, K., Kalscheuer, C., Carlet, M., Stachowski, N., Hintze, W., Möller, C., et al. (2022). Self-lubricating CrAlMoN high performance tool coatings for machining of TiAl6V4. Prod. Eng. 17 (3-4), 437–444. doi:10.1007/s11740-022-01161-8
Bohórquez, C. D., Pérez, S. P., Sarmiento, A., and Mendoza, M. E. (2020). Effect of temperature on morphology and wear of a Cu-Ti-TiC MMC sintered by abnormal glow discharge. Mater. Res. Express 7 (2), 026501. doi:10.1088/2053-1591/ab6e3b
Bouchareb, N., Hezil, N., Hamadi, F., and Fellah, M. (2024). Effect of milling time on structural, mechanical and tribological behavior of a newly developed Ti-Ni alloy for biomedical applications. Mater. Today Commun. 38, 108201. doi:10.1016/j.mtcomm.2024.108201
Budzyński, P., Kamiński, M., Surowiec, Z., Wiertel, M., Skuratov, V. A., and Korneeva, E. A. (2021). Effects of xenon-ion irradiation on the tribological properties and crystal structure of titanium and its alloy Ti6Al4V. Tribol. Int. 156, 106854. doi:10.1016/j.triboint.2021.106854
Çaha, I., Alves, A. C., Chirico, C., Pinto, A. M., Tsipas, S., Gordo, E., et al. (2021). Improved tribocorrosion behavior on bio-functionalized β-type titanium alloy by the pillar effect given by TiN reinforcements. Surf. Coatings Technol. 415, 127122. doi:10.1016/j.surfcoat.2021.127122
Cao, X., He, W., Liao, B., He, G., Jiao, Y., Huang, D., et al. (2020). Effect of TiN/Ti coating combined with laser shock peening pre-treatment on the fatigue strength of Ti-6Al-4V titanium alloy. Surf. Coatings Technol. 403, 126393. doi:10.1016/j.surfcoat.2020.126393
Carlsson, J.-O., and Martin, P. M. (2010). “Chapter 7 - chemical vapor deposition,” in Handbook of deposition technologies for films and coatings. 3rd Edn, Editors P. M. Martin (Boston: William Andrew Publishing), 314–363.
Carreón, H., Barriuso, S., Porro, J. A., González-Carrasco, J. L., and Ocaña, J. L. (2014). Characterization of laser peening-induced effects on a biomedical Ti6Al4V alloy by thermoelectric means. Opt. Eng. 53 (12), 122502. doi:10.1117/1.OE.53.12.122502
Chakkravarthy, V., Oliveira, J. P., Mahomed, A., Yu, N., Manojkumar, P., Lakshmanan, M., et al. (2023). Effect of abrasive water jet peening on NaCl-induced hot corrosion behavior of Ti–6Al–4V. Vacuum 210, 111872. doi:10.1016/j.vacuum.2023.111872
Chan, C.-W., Lee, S., Smith, G. C., and Donaghy, C. (2017). Fibre laser nitriding of titanium and its alloy in open atmosphere for orthopaedic implant applications: investigations on surface quality, microstructure and tribological properties. Surf. Coatings Technol. 309, 628–640. doi:10.1016/j.surfcoat.2016.12.036
Chattopadhyay, A., Muvvala, G., Sarkar, S., Racherla, V., and Nath, A. K. (2021). Effect of laser shock peening on microstructural, mechanical and corrosion properties of laser beam welded commercially pure titanium. Opt. and Laser Technol. 133, 106527. doi:10.1016/j.optlastec.2020.106527
Chen, T., Li, W., Liu, D., Xiong, Y., and Zhu, X. (2021). Effects of heat treatment on microstructure and mechanical properties of TiC/TiB composite bioinert ceramic coatings in-situ synthesized by laser cladding on Ti6Al4V. Ceram. Int. 47 (1), 755–768. doi:10.1016/j.ceramint.2020.08.186
Chen, Z., Wang, Z., Liu, J., Ye, Z., Hu, Y., Wu, J., et al. (2024). Enhancing the tribological properties of TA1 pure titanium by modulating the energy of pulsed laser nitriding. Opt. and Laser Technol. 169, 110118. doi:10.1016/j.optlastec.2023.110118
Çomaklı, O., Yazıcı, M., Demir, M., Yetim, A. F., and Çelik, A. (2023). Effect of bilayer numbers on structural, mechanical, tribological and corrosion properties of TiO2–SiO2 multilayer film-coated β-type Ti45Nb alloys. Ceram. Int. 49 (2), 3007–3015. doi:10.1016/j.ceramint.2022.09.285
Cordeiro, J. M., and Barão, V. a.R. (2017). Is there scientific evidence favoring the substitution of commercially pure titanium with titanium alloys for the manufacture of dental implants? Mater. Sci. Eng. C 71, 1201–1215. doi:10.1016/j.msec.2016.10.025
Costa, M. M., Lima, R., Alves, N., Silva, N. A., Gasik, M., Silva, F. S., et al. (2022). Multi-material cellular structured orthopedic implants design: in vitro and bio-tribological performance. J. Mech. Behav. Biomed. Mater 131, 105246. doi:10.1016/j.jmbbm.2022.105246
Cotton, J. D., Briggs, R. D., Boyer, R. R., Tamirisakandala, S., Russo, P., Shchetnikov, N., et al. (2015). State of the art in beta titanium alloys for airframe applications. JOM 67 (6), 1281–1303. doi:10.1007/s11837-015-1442-4
Crosby, K. (2013). Titanium-6Aluminum-4Vanadium for functionally graded orthopedic implant applications.
Cui, C., Hu, B., Zhao, L., and Liu, S. (2011). Titanium alloy production technology, market prospects and industry development. Mater. and Des. 32 (3), 1684–1691. doi:10.1016/j.matdes.2010.09.011
Daoud, M., Kubler, R., Bemou, A., Osmond, P., and Polette, A. (2021). Prediction of residual stress fields after shot-peening of TRIP780 steel with second-order and artificial neural network models based on multi-impact finite element simulations. J. Manuf. Process. 72, 529–543. doi:10.1016/j.jmapro.2021.10.034
Das, B., Srivastava, S. K., Manna, I., and Majumdar, J. D. (2024). Mechanically tailored surface of titanium based alloy (Ti6Al4V) by laser surface treatment. Surf. Coatings Technol. 479, 130560. doi:10.1016/j.surfcoat.2024.130560
Davis, A. E., Zeng, X., Thomas, R., Kennedy, J. R., Donoghue, J., Gholinia, A., et al. (2022). Optimising large-area crystal orientation mapping of nanoscale β phase in α + β titanium alloys using EBSD. Mater. Charact. 194, 112371. doi:10.1016/j.matchar.2022.112371
Dicecco, L.-A., Mehdi, M., and Edrisy, A. (2021). Dry-sliding wear mechanisms of shot-peened additive manufactured alpha titanium featuring TiB particles. Tribol. Lett. 69 (3), 90. doi:10.1007/s11249-021-01456-4
Dong, B., Guo, X., Zhang, K., Zhang, Y., Li, Z., Wang, W., et al. (2022). Combined effect of laser texturing and carburizing on the bonding strength of DLC coatings deposited on medical titanium alloy. Surf. Coatings Technol. 429, 127951. doi:10.1016/j.surfcoat.2021.127951
Dos Santos-Junior, J. A., Ferreira-Oliveira, J. R., Riffel, D. B., and Guimarães, G. (2024). Analysis of the effect of surface coating and texturizetion on the estimation of effective thermophysical properties. Therm. Sci. Eng. Prog. 50, 102558. doi:10.1016/j.tsep.2024.102558
Fellah, M., Hezil, N., Bouras, D., Bouchareb, N., Perez Larios, A., Obrosov, A., et al. (2024). Investigating the effect of Zr content on electrochemical and tribological properties of newly developed near β-type Ti-alloys (Ti–25Nb-xZr) for biomedical applications. J. Sci. Adv. Mater. Devices 9 (2), 100695. doi:10.1016/j.jsamd.2024.100695
Fernandes, M. F., Velloso, V. M. D. O., Callisaya, E. S., and Voorwald, H. J. C. (2024). Cr/CrN coating effect on the fatigue crack nucleation period of Ti-6Al-4V alloy. Mater. Today Commun. 38, 108049. doi:10.1016/j.mtcomm.2024.108049
Fridrici, V., Fouvry, S., and Kapsa, P. (2001). Effect of shot peening on the fretting wear of Ti–6Al–4V. Wear 250, 642–649. doi:10.1016/s0043-1648(01)00671-8
Furuta, T. (2019). “Chapter 4 - automobile applications of titanium,” in Titanium for consumer applications. Editors F. Froes, M. Qian, and M. Niinomi (London, United Kingdom: Elsevier), 77–90.
Ganesh, B. K. C., and Kumar, S. A. (2021). “Effect of peening based processes on tribological and mechanical behavior of bio-implant materials,” in Handbook of modern coating technologies, 355–379.
Ganesh, B. K. C., Ramanaiah, N., and Chandrasekhar Rao, P. V. (2012). Effect of surface treatment on tribological behavior of Ti-6Al-4V implant alloy. J. Minerals Mater. Charact. Eng. 11, 735–743. doi:10.4236/jmmce.2012.117061
Ganesh, B. K. C., Sha, W., Ramanaiah, N., and Krishnaiah, A. (2014). Effect of shotpeening on sliding wear and tensile behavior of titanium implant alloys. Mater. and Des. 56, 480–486. doi:10.1016/j.matdes.2013.11.052
Ghio, E., Bolelli, G., Bertè, A., and Cerri, E. (2023). Diamond-Like Carbon (DLC) and AlCrN films onto Ti-6Al-4V substrates by Laser-Powder Bed Fusion (L-PBF): effect of substrate heat treatment and surface finish. Surf. Coatings Technol. 475, 130128. doi:10.1016/j.surfcoat.2023.130128
Gonçalves, V. R. M., Çaha, I., Alves, A. C., Toptan, F., and Rocha, L. A. (2022). Improved tribocorrosion behavior obtained by in-situ precipitation of Ti2C in Ti-Nb alloy. Metals 12 (6), 908. doi:10.3390/met12060908
Gonçalves, V. R. M., Corrêa, D. R. N., Grandini, C. R., Pintão, C. a.F., Afonso, C. R. M., and Lisboa Filho, P. N. (2023). Assessment of improved tribocorrosion in novel in-situ Ti and β Ti–40Nb alloy matrix composites produced with NbC addition during arc-melting for biomedical applications. Mater. Chem. Phys. 301, 127597. doi:10.1016/j.matchemphys.2023.127597
Gospodinov, D., Ferdinandov, N., and Dimitrov, S. (2016). Classification, properties and application of titanium and its alloys.
Grabarczyk, J., Batory, D., Kaczorowski, W., Pazik, B., Januszewicz, B., Burnat, B., et al. (2020). Comparison of different thermo-chemical treatments methods of Ti-6Al-4V alloy in terms of tribological and corrosion properties. Mater. (Basel) 13 (22), 5192. doi:10.3390/ma13225192
Grenadyorov, A. S., Solovyev, A. A., Oskomov, K. V., Semenov, V. A., Zhulkov, M. O., Sirota, D. A., et al. (2023). Morphofunctional reaction of leukocytes and platelets in in vitro contact with a-C:H:x-coated Ti–6Al–4V substrate. J. Biomed. Mater Res. A 111 (3), 309–321. doi:10.1002/jbm.a.37470
Grubova, I. Y., Surmeneva, M. A., Surmenev, R. A., and Neyts, E. C. (2020). Effect of van der Waals interactions on the adhesion strength at the interface of the hydroxyapatite-titanium biocomposite: a first-principles study. RSC Adv. 10 (62), 37800–37805. doi:10.1039/d0ra06006b
Gu, C., Tian, Z., Zhao, J., and Wang, Y. (2023). Investigation of microstructure and tribological property of Ti-6Al-4V alloy by laser shock peening processing. Int. J. Adv. Manuf. Technol. 129 (1-2), 955–967. doi:10.1007/s00170-023-12354-5
Gui, N., Song, T., and Qian, M. (2019). “Chapter 16 - titanium springs and fasteners,” in Titanium for consumer applications. Editors F. Froes, M. Qian, and M. Niinomi (Futtsu City: Elsevier), 297–319.
Hamadi, F., Fellah, M., Hezil, N., Bouras, D., Laouini, S. E., Montagne, A., et al. (2024). Effect of milling time on structural, physical and tribological behavior of a newly developed Ti-Nb-Zr alloy for biomedical applications. Adv. Powder Technol. 35 (1), 104306. doi:10.1016/j.apt.2023.104306
Hang, R., Zhao, F., Yao, X., Tang, B., and Chu, P. K. (2020). Self-assembled anodization of NiTi alloys for biomedical applications. Appl. Surf. Sci. 517, 146118. doi:10.1016/j.apsusc.2020.146118
Hao, Y. L., Li, S. J., and Yang, R. (2016). Biomedical titanium alloys and their additive manufacturing. Rare Met. 35 (9), 661–671. doi:10.1007/s12598-016-0793-5
Hezil, N., Aissani, L., Fellah, M., Abdul Samad, M., Obrosov, A., Timofei, C., et al. (2022). Structural, and tribological properties of nanostructured α + β type titanium alloys for total hip. J. Mater. Res. Technol. 19, 3568–3578. doi:10.1016/j.jmrt.2022.06.042
Hou, R., Zhang, M., Wang, Y., and Lv, Z. (2022). Experimental study of abrasive water jet shot peening on TC4 titanium alloy of 3D printing. Res. Square. doi:10.21203/rs.3.rs-1578520/v1
Huang, H., Wang, S., Wang, C., Li, K., Zhou, Y., and Wang, X. (2023). Prediction of residual stress, surface roughness, and grain refinement of 42CrMo steel subjected to shot peening by combining finite element method and artificial neural network. Int. J. Adv. Manuf. Technol. 127 (7-8), 3441–3461. doi:10.1007/s00170-023-11716-3
Hussain, S., Shah, Z. A., Sabiruddin, K., and Keshri, A. K. (2023). Characterization and tribological behaviour of Indian clam seashell-derived hydroxyapatite coating applied on titanium alloy by plasma spray technique. J. Mech. Behav. Biomed. Mater 137, 105550. doi:10.1016/j.jmbbm.2022.105550
Hussein, M. A., Adesina, A. Y., Kumar, A. M., Sorour, A. A., Ankah, N., and Al-Aqeeli, N. (2020). Mechanical, in-vitro corrosion, and tribological characteristics of TiN coating produced by cathodic arc physical vapor deposition on Ti20Nb13Zr alloy for biomedical applications. Thin Solid Films 709, 138183. doi:10.1016/j.tsf.2020.138183
Izmir, M., and Ercan, B. (2018). Anodization of titanium alloys for orthopedic applications. Front. Chem. Sci. Eng. 13 (1), 28–45. doi:10.1007/s11705-018-1759-y
Jang, Y.-J., Jang, J. W., Kim, J.-I., Kim, W.-S., Kim, M. H., and Kim, J. (2024). Tensile testing as alternative evaluation method for enhanced adhesion of diamond-like carbon coatings with different titanium buffer layers. J. Mater. Res. Technol. 29, 1579–1589. doi:10.1016/j.jmrt.2024.01.105
Ji, X., Jin, J., Lai, Y., Wang, F., and Huang, X. (2023). Ultrasonic impact treatment of Ti-based amorphous alloy: improved tribological performance in air and 3.5 % NaCl solution. Surf. Coatings Technol. 469, 129798. doi:10.1016/j.surfcoat.2023.129798
Jiang, X. J., Wang, S. Z., Feng, Z. H., Qi, H. B., Fu, H., and Liu, R. P. (2022). Improving vacuum gas nitriding of a Ti-based alloy via surface solid phase transformation. Vacuum 197, 110860. doi:10.1016/j.vacuum.2021.110860
John, A., Showket, J., Joseph Babu, K., Edachery, V., and Suvin, P. S. (2023). Micro-tribological characteristics of Ti6Al4V alloy subjected to shot blasting surface treatment process. Trans. Indian Inst. Metals 76 (9), 2463–2471. doi:10.1007/s12666-023-02915-3
Ju, J., Zan, R., Shen, Z., Wang, C., Peng, P., Wang, J., et al. (2023). Remarkable bioactivity, bio-tribological, antibacterial, and anti-corrosion properties in a Ti-6Al-4V-xCu alloy by laser powder bed fusion for superior biomedical implant applications. Chem. Eng. J. 471, 144656. doi:10.1016/j.cej.2023.144656
Kaewnisai, S., Chingsungnoen, A., Poolcharounsin, P., Jongwannasiri, C., Manaspon, C., Udomsom, S., et al. (2023). Effect of pulse frequency on the surface properties and corrosion resistance of a plasma-nitrided Ti-6Al-4V alloy. Mater. Res. Express 10 (11), 116505. doi:10.1088/2053-1591/ad06ff
Kaseem, M., Safira, A. R., and Fattah-Alhosseini, A. (2024). Enhanced surface properties of TiO2-based coatings via stevia-assisted spark suppression: insights from density functional theory calculations. Inorganics 12 (5), 134. doi:10.3390/inorganics12050134
Kaur, G., and H. Oskouei, R. (2019). An overview on the tribological performance of titanium alloys with surface modifications for biomedical applications. Lubricants 7 (8), 65. doi:10.3390/lubricants7080065
Kaur, M., and Singh, K. (2019). Review on titanium and titanium based alloys as biomaterials for orthopaedic applications. Mater. Sci. Eng. C 102, 844–862. doi:10.1016/j.msec.2019.04.064
Khan, S. A., Ferreira, F., Oliveira, J., Emami, N., and Ramalho, A. (2024). A comparative study in the tribological behaviour of different DLC coatings sliding against titanium alloys. Wear 554-555, 205468–205555. doi:10.1016/j.wear.2024.205468
Kim, K. T., Eo, M. Y., Nguyen, T. T. H., and Kim, S. M. (2019). General review of titanium toxicity. Int. J. Implant Dent. 5 (1), 10. doi:10.1186/s40729-019-0162-x
Kumar, A., Kant, R., and Singh, H. (2021). Tribological behavior of cold-sprayed titanium/baghdadite composite coatings in dry and simulated body fluid environments. Surf. Coatings Technol. 425, 127727. doi:10.1016/j.surfcoat.2021.127727
Kumar, R., Singh, B. K., Kumar, A., Kumar, A., Kumar, A., and Kumar, P. (2024). Integrating selective flocculation techniques for enhanced efficiency in manufacturing processes: a novel approach through artificial neural network modeling. J. Alloys Metallurgical Syst. 7, 100088. doi:10.1016/j.jalmes.2024.100088
Kumar, R. G., Gopalakrishnan, A., Malav, A., Panjawani, H. S., and Rajyalakshmi, G. (2018). Comparative studies of simulation, artificial neural network and fuzzy logic for laser shock peening. UPB Sci. Bull. Ser. D. Mech. Eng. 80 (1), 229–242.
Kumar Murmu, S., Chattopadhayaya, S., Cep, R., Kumar, A., Kumar, A., Kumar Mahato, S., et al. (2024). Exploring tribological properties in the design and manufacturing of metal matrix composites: an investigation into the AL6061-SiC-fly ASH alloy fabricated via stir casting process. Front. Mater. 11. doi:10.3389/fmats.2024.1415907
Lal, B., and Dey, A. (2024a). Effect of TiC nano-particle on microstructure evolution and tribological behaviour of Ti6Al4V composites fabricated via spark plasma sintering. Tribol. Int. 197, 109775. doi:10.1016/j.triboint.2024.109775
Lal, B., and Dey, A. (2024b). Fretting wear characteristics of Ti6Al4V/TiC nano composites using response surface method. Tribol. Int. 193, 109412. doi:10.1016/j.triboint.2024.109412
Lei, X., Lin, N., Yuan, S., Lei, C., Nouri, M., Liu, Z., et al. (2024). Combining laser surface texturing and double glow plasma surface chromizing to improve tribological performance of Ti6Al4V alloy. Surf. Coatings Technol. 478, 130418. doi:10.1016/j.surfcoat.2024.130418
Li, H., Ma, L., Wen, P., Han, Y., Dong, R., and Fan, M. (2022). Molecular structure insight into the tribological behavior of sulfonate ionic liquids as lubricants for titanium alloys. J. Mol. Liq. 357, 119082. doi:10.1016/j.molliq.2022.119082
Li, H., and Wang, Z. (2024). Corrosion behavior and incorporation mechanism of Y2O3-TiO2 composite coatings fabricated on TC4 titanium alloy by plasma electrolytic oxidation. Chem. Phys. Lett. 841, 141170. doi:10.1016/j.cplett.2024.141170
Li, H., Xu, F., Cui, K., Tian, B., Dong, R., and Fan, M. (2023). Interfacial adsorption and tribological response of various functional groups on titanium surface: in-depth research conducted on the lubricating mechanism of liquid lubricants. Tribol. Int. 189, 108885. doi:10.1016/j.triboint.2023.108885
Li, H. C., Wang, D. G., Hu, C., Dou, J. H., Yu, H. J., Chen, C. Z., et al. (2021). Microstructure, mechanical and biological properties of laser cladding derived CaO-SiO2-MgO system ceramic coatings on titanium alloys. Appl. Surf. Sci. 548, 149296. doi:10.1016/j.apsusc.2021.149296
Li, J., Chen, S., Liu, L., Zhao, Y., Huang, S., Zhu, W., et al. (2024a). Microstructural evolution and tribological properties of TC6 titanium alloy strengthened by laser peening combined with nitrogen ion implantation. Vacuum 222, 112964. doi:10.1016/j.vacuum.2024.112964
Li, T., Li, L., Qi, J., and Chen, F. (2020). Corrosion protection of Ti6Al4V by a composite coating with a plasma electrolytic oxidation layer and sol-gel layer filled with graphene oxide. Prog. Org. Coatings 144, 105632. doi:10.1016/j.porgcoat.2020.105632
Li, Y., Tian, P., Cao, H., Wang, Y., Zhao, X., Han, S., et al. (2024b). Remarkable enhancement of corrosion resistance and tribological properties of chitosan-MXene based hydrogel coating on the surface of Ti6Al4V alloy. Tribol. Int. 192, 109229. doi:10.1016/j.triboint.2023.109229
Li, Y.-F., Chen, C., Ranabhat, J., and Shen, Y.-F. (2017). Formation mechanism and mechanical properties of surface nanocrystallized Ti–6Al–4V alloy processed by surface mechanical attrition treatment. Rare Met. 42 (4), 1343–1352. doi:10.1007/s12598-017-0988-4
Lihui, L., Kangning, L., Cai, G., Yang, X., Guo, C., and Bu, G. (2014). A critical review on special forming processes and associated research for lightweight components based on sheet and tube materials. Manuf. Rev. 1, 9. doi:10.1051/mfreview/2014007
Liu, A., Gao, S., Du, S., Lu, H., and Guo, J. (2024a). Enhancing PEO coating on TC6 alloy through in-situ synthesis of MoSe2—towards more efficient wear-reducing lubrication and wear resistance. Tribol. Int. 193, 109409. doi:10.1016/j.triboint.2024.109409
Liu, B., Deng, Z., and Liu, D. (2021a). Preparation and properties of multilayer Ca/P bio-ceramic coating by laser cladding. Coatings 11 (8), 891. doi:10.3390/coatings11080891
Liu, C., Wang, Q., Zhao, B., Liu, F., Zhu, S., Guan, S., et al. (2024b). A novel biofunctional TaCu coating on Ti6Al4V by CVD method. Mater. Lett. 366, 136586. doi:10.1016/j.matlet.2024.136586
Liu, C., Yu, Y., Sun, H., Yin, F., Xie, L., Qian, D., et al. (2024c). Local strain evolution near α/β interface in TC11 titanium alloy under electroshocking treatment. Mater. Charact. 209, 113689. doi:10.1016/j.matchar.2024.113689
Liu, Q., Liu, Y., Li, X., and Dong, G. (2021b). Pulse laser-induced cell-like texture on surface of titanium alloy for tribological properties improvement. Wear 477, 203784. doi:10.1016/j.wear.2021.203784
Liu, W., Liu, S., and Wang, L. (2019). Surface modification of biomedical titanium alloy: micromorphology, microstructure evolution and biomedical applications. Coatings 9, 249. doi:10.3390/coatings9040249
Liu, W., Shen, Q., Yang, M., Gao, T., Ji, B., Tu, R., et al. (2024d). High hardness and toughness potential TiN/TiSiN gradient nano-multilayer coating structure by finite element study. Ceram. Int. 50 (6), 9034–9046. doi:10.1016/j.ceramint.2023.12.217
Liu, X., Chu, P. K., and Ding, C. (2004). Surface modification of titanium, titanium alloys, and related materials for biomedical applications. Mater. Sci. Eng. R Rep. 47 (3), 49–121. doi:10.1016/j.mser.2004.11.001
Liu, Z. Y., Yang, L., and Zhou, Y. C. (2023). A multiscale model integrating artificial neural networks for failure prediction in turbine blade coatings. Surf. Coatings Technol. 457, 129218. doi:10.1016/j.surfcoat.2022.129218
Lu, S., Sun, J., Ma, Y., and Sun, N. (2024). Pre-mixed abrasive waterjet peening with post-low stress milling process and the effect of process parameters on the surface integrity of TC11 titanium alloy. Surf. Coatings Technol. 478, 130409. doi:10.1016/j.surfcoat.2024.130409
Lypchanskyi, O., Muszka, K., Wynne, B., Kawalko, J., and Śleboda, T. (2024). Microstructural analysis of titanium alloys based on high-temperature phase reconstruction. J. Mater. Sci. doi:10.1007/s10853-024-09963-0
Maculotti, G., Goti, E., Genta, G., Mazza, L., and Galetto, M. (2022). Uncertainty-based comparison of conventional and surface topography-based methods for wear volume evaluation in pin-on-disc tribological test. Tribol. Int. 165, 107260. doi:10.1016/j.triboint.2021.107260
Madeira, S., Buciumeanu, M., Nobre, D., Carvalho, O., and Silva, F. S. (2022). Development of a novel hybrid Ti6Al4V-ZrO(2) surface with high wear resistance by laser and hot pressing techniques for dental implants. J. Mech. Behav. Biomed. Mater 136, 105508. doi:10.1016/j.jmbbm.2022.105508
Majzoobi, G. H., Rahmani, K., Mohammadi, M., Bakhtiari, H., and Das, R. (2023). Tribological behaviour of Ti/HA and Ti/SiO2 functionally graded materials fabricated at different strain rates. Biotribology 35-36, 100233–100236. doi:10.1016/j.biotri.2022.100233
Mao, Y., Zhao, Q., Geng, J., Qian, W., Zou, H., Gong, T., et al. (2024). High-performance ceramic coatings for additive manufacturing biofunctional titanium alloy by regulating precipitation orientation. Chem. Eng. J. 489, 151325. doi:10.1016/j.cej.2024.151325
Maurel, P., Weiss, L., Bocher, P., Fleury, E., and Grosdidier, T. (2019). Oxide dependent wear mechanisms of titanium against a steel counterface: influence of SMAT nanostructured surface. Wear 430-431, 245–255. doi:10.1016/j.wear.2019.05.007
Mechanical Properties (2024a). Ti 12Mo 6Zr 2Fe mechanical properties. Available at: https://acnis-titanium.com/en/produit/ti-12mo-6zr-2fe/.
Mechanical Properties (2024b). Ti 15Mo mechanical properties. Available at: https://acnis-titanium.com/en/produit/ti-15mo/?application=medical.
Meghwal, A., Anupam, A., Murty, B. S., Berndt, C. C., Kottada, R. S., and Ang, A. S. M. (2020). Thermal spray high-entropy alloy coatings: a review. J. Therm. Spray Technol. 29 (5), 857–893. doi:10.1007/s11666-020-01047-0
Mirzayev, M. N., Imanova, G. T., Neov, D., Rasoul, M., Bekpulatov, I. R., Khallokov, F. K., et al. (2024). Surface evaluation of carbonitride coating materials at high temperature: an investigation of oxygen adsorption on crystal surfaces by molecular dynamics simulation. J. Porous Mater. 31 (4), 1531–1539. doi:10.1007/s10934-024-01627-3
Moradi, A., Heidari, A., Amini, K., Aghadavoudi, F., and Abedinzadeh, R. (2022). Taguchi analysis of shot peening parameters for surface hardness, wear resistance, roughness, and residual stress in Ti-6Al-4V alloy. Kov. Materialy-Metallic Mater. 60 (4). doi:10.31577/km.2022.4.267
Munir, K., Lin, J., Wright, P. F. A., Ozan, S., Li, Y., and Wen, C. (2022). Mechanical, corrosion, nanotribological, and biocompatibility properties of equal channel angular pressed Ti-28Nb-35.4Zr alloys for biomedical applications. Acta Biomater. 149, 387–398. doi:10.1016/j.actbio.2022.07.005
Muntean, R., Brindusoiu, M., Buzdugan, D., Nemes, N. S., Kellenberger, A., and Utu, I. D. (2023). Characteristics of hydroxyapatite-modified coatings based on TiO(2) obtained by plasma electrolytic oxidation and electrophoretic deposition. Mater. (Basel) 16 (4), 1410. doi:10.3390/ma16041410
Murari, B. M., and Chauhan, S. S. (2024). Characterisation of TEOS-based sol–gel-hydroxyapatite composite coating on titanium implants. Biomed. Mater. and Devices. doi:10.1007/s44174-024-00182-4
Narayana, T., and Saleem, S. S. (2024). Comparative investigation and characterization of the nano-mechanical and tribological behavior of RF magnetron sputtered TiN, CrN, and TiB2 coating on Ti6Al4V alloy. Tribol. Int. 193, 109348. doi:10.1016/j.triboint.2024.109348
Niinomi, M. (1998). Mechanical properties of biomedical titanium alloys. Mater. Sci. Eng. A243, 231–236. doi:10.1016/S0921-5093(97)00806-X
Nikiforov, G. B., Roesky, H. W., and Koley, D. (2014). A survey of titanium fluoride complexes, their preparation, reactivity, and applications. Coord. Chem. Rev. 258-259, 16–57. doi:10.1016/j.ccr.2013.09.002
Nikolova, M., Ormanova, M., Nikolova, V., and Apostolova, M. D. (2021). Electrochemical, tribological and biocompatible performance of electron beam modified and coated Ti6Al4V alloy. Int. J. Mol. Sci. 22 (12), 6369. doi:10.3390/ijms22126369
Niu, Y., Pang, X., Song, C., Shangguan, B., Zhang, Y., and Wang, S. (2023). Tailoring tribological properties of Ti-Zr alloys via process design of laser surface texturing and thermal oxidation. Surfaces Interfaces 37, 102743. doi:10.1016/j.surfin.2023.102743
Noori, M., Atapour, M., Ashrafizadeh, F., Elmkhah, H., Di Confiengo, G. G., Ferraris, S., et al. (2023). Nanostructured multilayer CAE-PVD coatings based on transition metal nitrides on Ti6Al4V alloy for biomedical applications. Ceram. Int. 49 (14), 23367–23382. doi:10.1016/j.ceramint.2023.04.169
Pandey, A. K., Gautam, R. K., and Behera, C. K. (2023a). Corrosion and wear behavior of Ti-5Cu-xNb biomedical alloy in simulated body fluid for dental implant applications. J. Mech. Behav. Biomed. Mater 137, 105533. doi:10.1016/j.jmbbm.2022.105533
Pandey, A. K., Kumar, A., Kumar, R., Gautam, R. K., and Behera, C. K. (2023b). Tribological performance of SS 316L, commercially pure Titanium, and Ti6Al4V in different solutions for biomedical applications. Mater. Today Proc. 78, A1–A8. doi:10.1016/j.matpr.2023.03.736
Petronić, S., Čolić, K., Đorđević, B., Milovanović, D., Burzić, M., and Vučetić, F. (2020). Effect of laser shock peening with and without protective coating on the microstructure and mechanical properties of Ti-alloy. Opt. Lasers Eng. 129, 106052. doi:10.1016/j.optlaseng.2020.106052
Prasad, S., Ehrensberger, M., Gibson, M. P., Kim, H., and Monaco, E. A. (2015). Biomaterial properties of titanium in dentistry. J. Oral Biosci. 57 (4), 192–199. doi:10.1016/j.job.2015.08.001
Praveenkumar, K., Swaroop, S., and Manivasagam, G. (2023). Effect of multiple laser shock peening without coating on residual stress distribution and high temperature dry sliding wear behaviour of Ti-6Al-4 V alloy. Opt. and Laser Technol. 164, 109398. doi:10.1016/j.optlastec.2023.109398
Pushp, P., Dasharath, S. M., and Arati, C. (2022). Classification and applications of titanium and its alloys. Mater. Today Proc. 54, 537–542. doi:10.1016/j.matpr.2022.01.008
Qian, B., Li, X., Wang, Y., Hou, J., Liu, J., Zou, S., et al. (2024). An ultra-low modulus of ductile TiZrHfTa biomedical high-entropy alloys through deformation induced martensitic transformation/twinning/amorphization. Adv. Mater 36 (24), e2310926. doi:10.1002/adma.202310926
Qin, W., Ma, J., Liang, Q., Li, J., and Tang, B. (2021). Tribological, cytotoxicity and antibacterial properties of graphene oxide/carbon fibers/polyetheretherketone composite coatings on Ti-6Al-4V alloy as orthopedic/dental implants. J. Mech. Behav. Biomed. Mater 122, 104659. doi:10.1016/j.jmbbm.2021.104659
Quinn, J., Mcfadden, R., Chan, C.-W., and Carson, L. (2020). Titanium for orthopedic applications: an overview of surface modification to improve biocompatibility and prevent bacterial biofilm formation. iScience 23 (11), 101745. doi:10.1016/j.isci.2020.101745
Rajabi, M., Miresmaeili, R., and Aliofkhazraei, M. (2019). Hardness and wear behavior of surface mechanical attrition treated titanium. Mater. Res. Express 6 (6), 065003. doi:10.1088/2053-1591/ab0673
Ranjith Kumar, G., Rajyalakshmi, G., and Swaroop, S. (2019). A critical appraisal of laser peening and its impact on hydrogen embrittlement of titanium alloys. Proc. Institution Mech. Eng. Part B J. Eng. Manuf. 233 (13), 2371–2398. doi:10.1177/0954405419838956
Ranusa, M., Cipek, P., Vrbka, M., Palousek, D., Krupka, I., and Hartl, M. (2022). Tribological behaviour of 3D printed materials for small joint implants: a pilot study. J. Mech. Behav. Biomed. Mater 132, 105274. doi:10.1016/j.jmbbm.2022.105274
Reger, N. C., K, B. D., P, T., Verma, S., and Balla, V. K. (2023). Electrochemical and tribological studies of in-situ grown ceramic layers on additively manufactured Ti–50Zr alloy for load-bearing implant applications. Results Surfaces Interfaces 13, 100168. doi:10.1016/j.rsurfi.2023.100168
Sáenz De Viteri, V., and Fuentes, E. (2013). Titanium and titanium alloys as biomaterials. Tribol. - Fundam. Adv., 154–181. doi:10.5772/55860
Saier, A., Esen, I., Ahlatci, H., and Keskin, E. (2024). Effect of oxidation process on mechanical and tribological behaviour of titanium grade 5 alloy. Mater. (Basel) 17 (4), 776. doi:10.3390/ma17040776
Santos, P. B., Baldin, E. K., Krieger, D. A., De Castro, V. V., Aguzzoli, C., Fonseca, J. C., et al. (2021). Wear performance and osteogenic differentiation behavior of plasma electrolytic oxidation coatings on Ti-6Al-4V alloys: potential application for bone tissue repairs. Surf. Coatings Technol. 417, 127179. doi:10.1016/j.surfcoat.2021.127179
Sarraf, M., Razak, B. A., Ghasemi, M., Zal Nezhad, E., Hashemi, R., and Bae, S. (2023). Systematic microstructure modification effect on nanomechanical, tribology, corrosion, and biomineralization behavior by optimized anodic alumina nanotubes coated Ti–6Al–4V alloy. Ceram. Int. 49 (14), 23437–23455. doi:10.1016/j.ceramint.2023.04.176
Saxena, A., Gupta, T. K., Srivastava, R., Srivastava, A. K., and Kumar, A. (2024). A comparison of different experimental approaches in the determination of dynamic fracture toughness (J1d) behavior for RHA steel cost sustainable MMAW weldments. J. Adhesion Sci. Technol., 1–22. doi:10.1080/01694243.2024.2334267
Sefer, B. (2014). Oxidation and alpha–case phenomena in titanium alloys used in aerospace industry: Ti–6Al–2Sn–4Zr–2Mo and Ti–6Al–4V.
Selamat, M. S., Baker, T. N., and Watson, L. M. (2001). Study of the surface layer formed by the laser processing of Ti–6Al–4V alloy in a dilute nitrogen environment. J. Mater. Process. Technol. 113 (1-3), 509–515. doi:10.1016/s0924-0136(01)00595-7
Şenaslan, F., Taşdemir, M., Çelik, A., and Bozkurt, Y. B. (2023). Enhanced wear resistance and surface properties of oxide film coating on biocompatible Ti45Nb alloy by anodization method. Surf. Coatings Technol. 469, 129797. doi:10.1016/j.surfcoat.2023.129797
Serra, D. (2008). “Superplastic forming applications on aero engines. a review of itp manufacturing processes,” in EuroSPF08. (Carcassonne, France).
Shankar, D., Jayaganesh, K., Gowda, N., Lakshmi, K. S., Jayanthi, K. J., and Jambagi, S. C. (2024). Thermal spray processes influencing surface chemistry and in-vitro hemocompatibility of hydroxyapatite-based orthopedic implants. Biomater. Adv. 158, 213791. doi:10.1016/j.bioadv.2024.213791
Shanmugapriya, P., Srinivasan, V., Karthikeyan, B., and Rajamurugan, T. V. (2021). Surface modification of nanocomposite Al2O3/Gr/HAP coating for improving wear and corrosion behaviour on Ti–6Al–4V alloy using sol–gel technique. Multiscale Multidiscip. Model. Exp. Des. 4 (3), 195–205. doi:10.1007/s41939-021-00089-3
Shanmugapriya, P., Sivamaran, V., Padma Rao, A., Senthil Kumar, P., Selvamani, S. T., and Mandal, T. K. (2022). Sol–gel derived Al2O3/Gr/HAP nanocomposite coatings on Ti–6Al–4V alloy for enhancing tribo-mech properties and antibacterial activity for bone implants. Appl. Phys. A 128 (8), 635. doi:10.1007/s00339-022-05784-7
Shen, H., and Wang, L. (2023). Tribological properties of Ti-N compound layer formed on Ti6Al4V by HCD assisted plasma nitriding. Mater. Today Commun. 36, 106652. doi:10.1016/j.mtcomm.2023.106652
Shi, L., Jiang, C., Zhao, R., Si, T., Li, Y., Qian, W., et al. (2024). Effect of Al2O3 nanoparticles additions on wear resistance of plasma electrolytic oxidation coatings on TC4 alloys. Ceram. Int. 50 (11), 18484–18496. doi:10.1016/j.ceramint.2024.02.332
Siahpour, P., Omar, S. M. T., Griffin, D., Amegadzie, M. Y., Tieu, A., Donaldson, I. W., et al. (2024). Evaluating surface mechanical properties and wear resistance of Ti-6Al-4V alloy subjected to ultrasonic pulsed waterjet peening. Wear 550-551, 205400. doi:10.1016/j.wear.2024.205400
Simchen, F., Sieber, M., Kopp, A., and Lampke, T. (2020). Introduction to plasma electrolytic oxidation—an overview of the process and applications. Coatings 10 (7), 628. doi:10.3390/coatings10070628
Singh, G., Mittal, M., Singh, J., Sharma, S., Singh Chohan, J., and Kumar, R. (2022a). Effect of post coating processing on the morphological and mechanical properties of plasma Spray-reinforced hydroxyapatite coating. Mater. Today Proc. 68, 1180–1186. doi:10.1016/j.matpr.2022.10.108
Singh, J., Chatha, S. S., and Singh, H. (2021a). Synthesis and characterization of plasma sprayed functional gradient bioceramic coating for medical implant applications. Ceram. Int. 47 (7), 9143–9155. doi:10.1016/j.ceramint.2020.12.039
Singh, N., Edachery, V., Rajput, M., Chatterjee, K., Kailas, S. V., and Prashanth, K. G. (2022b). Ti6Al7Nb–TiB nanocomposites for ortho-implant applications. J. Mater. Res. 37 (16), 2525–2535. doi:10.1557/s43578-022-00578-2
Singh, S., Pandey, K. K., Balla, V. K., Das, M., and Keshri, A. K. (2021b). Corrosion, wear and in-vitro biocompatibility property of surface mechanical attrition treatment processed Ti-6Al-4V alloy. Jom 73 (12), 4387–4396. doi:10.1007/s11837-021-04970-x
Singh, V., Sharma, R. K., and Sehgal, R. (2024). A comprehensive investigation on nanomechanical, scratch, and tribological characteristics of TaN-Ag nanocomposite coating on Ti6Al7Nb alloy. J. Mater. Eng. Perform. doi:10.1007/s11665-024-09408-4
Şirin, Ş., Akıncıoğlu, S., Gupta, M. K., Kıvak, T., and Khanna, N. (2023). A tribological performance of vegetable-based oil combined with GNPs and hBN nanoparticles on the friction-wear tests of titanium grade 2. Tribol. Int. 181, 108314. doi:10.1016/j.triboint.2023.108314
Soltani-Kordshuli, F., Choudhury, D., Goss, J. A., Campbell, M., Smith, E., Sonntag, S., et al. (2023). Cartilage-inspired surface textures for improved tribological performance of orthopedic implants. J. Mech. Behav. Biomed. Mater 138, 105572. doi:10.1016/j.jmbbm.2022.105572
Somasundaram Prasadh, S. S., Ratheesh, V., and Wong, R. (2021). Encyclopedia of materials: composites. Elsevier.
Sonntag, R., Reinders, J., Gibmeier, J., and Kretzer, J. P. (2015). Fatigue performance of medical Ti6Al4V alloy after mechanical surface treatments. PLoS ONE 10 (3), e0121963. doi:10.1371/journal.pone.0121963
Sousa, L., Alves, A. C., Costa, N. A., Gemini-Piperni, S., Rossi, A. L., Ribeiro, A. R., et al. (2022). Preliminary tribo-electrochemical and biological responses of the Ti-TiB-TiCx in-situ composites intended for load-bearing biomedical implants. J. Alloys Compd. 896, 162965. doi:10.1016/j.jallcom.2021.162965
Sousa, L., Alves, A. C., Guedes, A., and Toptan, F. (2021a). Corrosion and tribocorrosion behaviour of Ti-B4C composites processed by conventional sintering and hot-pressing technique. J. Alloys Compd. 885, 161109. doi:10.1016/j.jallcom.2021.161109
Sousa, L., Antunes, R. D. M., Fernandes, J. C. S., Alves, A. C., and Toptan, F. (2023). Influence of Al2O3 reinforcements and Ti-Al intermetallics on corrosion and tribocorrosion behavior of titanium. Surf. Coatings Technol. 470, 129835. doi:10.1016/j.surfcoat.2023.129835
Sousa, L., Basilio, L., Alves, A. C., and Toptan, F. (2021b). Tribocorrosion-resistant biofunctionalized Ti-Al2O3 composites. Surf. Coatings Technol. 420, 127329. doi:10.1016/j.surfcoat.2021.127329
Sousa, L., Costa, N. A., Rossi, A., Simões, S., Toptan, F., and Alves, A. C. (2024). Micro-arc and thermal oxidized titanium matrix composites for tribocorrosion-resistant biomedical implants. Surf. Coatings Technol. 485, 130854. doi:10.1016/j.surfcoat.2024.130854
Srivastav, C. K., Gangwar, M., Prasad, N. K., and Khan, D. (2024). Structural, mechanical and biocompatible evaluation of nanocrystalline Ti-Nb-Ta-Cr-Co0.2 HEA for implant applications. Mater. Today Commun. 39, 109355. doi:10.1016/j.mtcomm.2024.109355
Subham, K., Kumar, A., Kamboj, A., and Chaudhari, G. P. (2024). Effect of surface nano structuring on corrosion and tribocorrosion behavior of Ti6Al4V alloy in simulated body fluid. J. Mater. Eng. Perform. doi:10.1007/s11665-024-09458-8
Tabie, V., Li, C., Saifu, W., Li, J., and Xu, X. (2020). Mechanical properties of near alpha titanium alloys for high-temperature applications - a review. Aircr. Eng. Aerosp. Technol. ahead-of-print 92, 521–540. doi:10.1108/AEAT-04-2019-0086
Tan, C., Su, J., Liu, Y., Feng, Z., Song, X., Wang, X., et al. (2022). Enhanced interfacial bonding strength of laser bonded titanium alloy/CFRTP joint via hydrogen bonds interaction. Compos. Part B Eng. 239, 109966. doi:10.1016/j.compositesb.2022.109966
Tang, Y., Yang, C.-P., Sun, Q.-Q., Wu, L.-K., and Cao, F.-H. (2024). Effects of TiC particles on tribological and corrosion resistance of PEO coating on TC4 alloy. Corros. Commun. 14, 1–10. doi:10.1016/j.corcom.2023.10.002
Thirumalvalavan, S., Senthilkumar, N., Perumal, G., and Padmanaban, M. R. A. (2022). Ameliorating the wear defiance of HVOF thermal spray silicon carbide coated Ti-6Al-4V alloy using PCA-GRA technique. Silicon 14 (6), 3101–3117. doi:10.1007/s12633-022-01706-7
Titanium (2024a). Medical titanium products. Available at: https://acnis-titanium.com/en/produits/titanium/medical/.
Titanium (2024b). Titanium alloy guide. Available at: https://www.spacematdb.com/spacemat/manudatasheets/TITANIUM%20ALLOY%20GUIDE.pdf.
Titanium (2024c). Titanium grades. Available at: https://www.titaniumengineers.com/titanium-grades.html.
Tong, Z. P., Ren, X. D., Zhou, W. F., Adu-Gyamfi, S., Chen, L., Ye, Y. X., et al. (2019). Effect of laser shock peening on wear behaviors of TC11 alloy at elevated temperature. Opt. and Laser Technol. 109, 139–148. doi:10.1016/j.optlastec.2018.07.070
Toualbia, K., Fellah, M., Hezil, N., Milles, H., and Djafia, Z. (2024). Effect of milling time on structural, mechanical and tribological properties of nanostructured HIPed near type Ti-15Mo alloys. Tribol. Int. 197, 109731. doi:10.1016/j.triboint.2024.109731
Trevisan, F., Calignano, F., Aversa, A., Marchese, G., Lombardi, M., Biamino, S., et al. (2018). Additive manufacturing of titanium alloys in the biomedical field: processes, properties and applications. J. Appl. Biomaterials Funct. Mater. 16 (2), 57–67. doi:10.5301/jabfm.5000371
Ulutan, D., and Ozel, T. (2011). Machining induced surface integrity in titanium and nickel alloys: a review. Int. J. Mach. Tools Manuf. 51 (3), 250–280. doi:10.1016/j.ijmachtools.2010.11.003
Valentim Gelamo, R., Bueno Leite, N., Amadeu, N., Reis Pedreira Muniz Tavares, M., Oberschmidt, D., Klemm, S., et al. (2024). Exploring the Nb2O5 coating deposited on the Ti-6Al-4V alloy by a novel GE-XANES technique and nanoindentation load-depth. Mater. Lett. 355, 135584. doi:10.1016/j.matlet.2023.135584
Vasilescu, V. G., Gălbinașu, B., and Vasilescu, E. (2019). Aspects regarding the evolution and characteristics of some titanium alloys used in oral implantology. UPB Sci. Bull. Ser. B Chem. Mater. Sci. 81, 194–204.
Vella, K. A., Buhagiar, J., Cassar, G., Pizzuto, M. M., Bonnici, L., Chen, J., et al. (2023). The effect of a duplex surface treatment on the corrosion and tribocorrosion characteristics of additively manufactured Ti-6Al-4V. Mater. (Basel) 16 (5), 2098. doi:10.3390/ma16052098
Wagih, A., Junaedi, H., Mahmoud, H. A., Lubineau, G., Kumar, A., and Sebaey, T. A. (2024). Enhanced damage tolerance and fracture toughness of lightweight carbon-Kevlar fiber hybrid laminate. J. Compos. Mater. 58 (9), 1109–1121. doi:10.1177/00219983241235853
Wang, C., Huang, H., Wu, H., Hong, J., Zhang, L., and Yan, J. (2023a). Ultra-low wear of titanium alloy surface under lubricated conditions achieved by laser texturing and simultaneous nitriding. Surf. Coatings Technol. 474, 130083. doi:10.1016/j.surfcoat.2023.130083
Wang, C., Zhu, K., Gao, Y., Han, S., Ju, J., Ren, T., et al. (2023b). Multifunctional GO-based hydrogel coating on Ti-6Al-4 V Alloy with enhanced bioactivity, anticorrosion and tribological properties against cortical bone. Tribol. Int. 184, 108423. doi:10.1016/j.triboint.2023.108423
Wang, G., Yao, S., Chi, Y., Zhang, C., Wang, N., Chen, Y., et al. (2023c). Improvement of titanium alloy TA19 fatigue life by submerged abrasive waterjet peening: correlation of its process parameters with surface integrity and fatigue performance. Chin. J. Aeronautics 37, 377–390. doi:10.1016/j.cja.2023.03.033
Wang, H., Qi, L., Gao, H., Zhang, H., and Lan, Y. (2024). Optimizing microstructures and properties of PEO coatings on sandblasted pure titanium: the influence of jet angle. J. Adhesion Sci. Technol. 38 (14), 2533–2545. doi:10.1080/01694243.2024.2306065
Wang, W., Wang, Y., and Yu, X. (2018). Effect of shot-peening treatment on the bio-tribological properties of a Ni+ implantation layer formed on the surface of Ti6Al4V. Mater. Res. Express 5 (6), 066423. doi:10.1088/2053-1591/aacd3b
Wang, Y. M., Guo, J. W., Zhuang, J. P., Jing, Y. B., Shao, Z. K., Jin, M. S., et al. (2014). Development and characterization of MAO bioactive ceramic coating grown on micro-patterned Ti6Al4V alloy surface. Appl. Surf. Sci. 299, 58–65. doi:10.1016/j.apsusc.2014.01.185
Wang, Z., Ma, Z., Chen, T., Fan, C., Yu, T., and Zhao, J. (2023d). Experimental investigation into the effect of process parameters on the Inconel 718 surface integrity for abrasive waterjet peening. Surf. Coatings Technol. 454, 129186. doi:10.1016/j.surfcoat.2022.129186
Wang, Z.-M., Jia, Y.-F., Zhang, X.-C., Fu, Y., Zhang, C.-C., and Tu, S.-T. (2019). Effects of different mechanical surface enhancement techniques on surface integrity and fatigue properties of Ti-6Al-4V: a review. Crit. Rev. Solid State Mater. Sci. 44 (6), 445–469. doi:10.1080/10408436.2018.1492368
Wen, M., Wen, C., Hodgson, P., and Li, Y. (2014). Improvement of the biomedical properties of titanium using SMAT and thermal oxidation. Colloids Surf. B Biointerfaces 116, 658–665. doi:10.1016/j.colsurfb.2013.10.039
Wen, M., Wen, C., Hodgson, P. D., and Li, Y. C. (2011). Tribological behaviour of pure Ti with a nanocrystalline surface layer under different loads. Tribol. Lett. 45 (1), 59–66. doi:10.1007/s11249-011-9862-y
Weng, Z., Gu, K., Cui, C., Guo, J., and Wang, J. (2022). Cryogenic sliding induced subsurface deformation and tribological behavior of pure titanium. Cryogenics 124, 103489. doi:10.1016/j.cryogenics.2022.103489
Woźniak, A., Bialas, O., Adamiak, M., Hadzima, B., and Szewczenko, J. (2024). The influence of laser texturing on the tribological behavior of titanium alloy Ti6Al4V in medical applications. Archives Civ. Mech. Eng. 24 (3), 146. doi:10.1007/s43452-024-00960-3
Wu, L., Zhang, D., Jiang, Z., Zheng, B., and Yu, Z. (2024a). Effect of Cu content on the wear resistant behavior of arc-sprayed laminated-structured Cu–TiN/TiO2 composite coating. Ceram. Int. 50 (7), 11966–11979. doi:10.1016/j.ceramint.2024.01.100
Wu, Q., Long, W., Zhang, L., and Zhao, H. (2024b). A review on ceramic coatings prepared by laser cladding technology. Opt. and Laser Technol. 176, 110993. doi:10.1016/j.optlastec.2024.110993
Xiao, H., Liu, X., Lu, Q., Hu, T., Hong, Y., Li, C., et al. (2022). Promoted low-temperature plasma nitriding for improving wear performance of arc-deposited ceramic coatings on Ti6Al4V alloy via shot peening pretreatment. J. Mater. Res. Technol. 19, 2981–2990. doi:10.1016/j.jmrt.2022.06.067
Xu, M., Chen, W., Lu, X., Hu, Q., Huang, J., Deng, L., et al. (2024a). Effect of high-temperature infrared emissivity on thermal cycling performance of magnetoplumbite-type thermal barrier coatings under thermal gradient condition. J. Eur. Ceram. Soc. 44 (1), 448–459. doi:10.1016/j.jeurceramsoc.2023.09.012
Xu, S., Cao, Y., Duan, B., Liu, H., Wang, J., and Si, C. (2023). Enhanced strength and sliding wear properties of gas nitrided Ti-6Al-4V alloy by ultrasonic shot peening pretreatment. Surf. Coatings Technol. 458, 129325. doi:10.1016/j.surfcoat.2023.129325
Xu, Y., Ge, J., and Li, W. (2024b). Microstructure and tribological properties of cold sprayed WCp/Ti composite coatings on Ti6Al4V titanium alloy. Tribol. Int. 192, 109218. doi:10.1016/j.triboint.2023.109218
Yang, C.-P., Meng, X.-Z., Li, X.-R., Li, Z.-X., Yan, H.-J., Wu, L.-K., et al. (2023). Effect of electrolyte composition on corrosion behavior and tribological performance of plasma electrolytic oxidized TC4 alloy. Trans. Nonferrous Metals Soc. China 33 (1), 141–156. doi:10.1016/s1003-6326(22)66096-5
Yang, Q., Zhou, W., Zhong, Y., Zhang, X., Fu, X., Chen, G., et al. (2018). Effect of shot-peening on the fretting wear and crack initiation behavior of Ti-6Al-4V dovetail joint specimens. Int. J. Fatigue 107, 83–95. doi:10.1016/j.ijfatigue.2017.10.020
Yang, Z., Song, Z. Y., Yu, H. L., Yin, Y. L., Wang, H. M., Zhou, X. Y., et al. (2024). Effect of natural attapulgite mineral on microstructure, mechanical properties and tribological behaviors of in-situ TiB/Ti composite by SPS method. J. Alloys Compd. 976, 173185. doi:10.1016/j.jallcom.2023.173185
Yetim, A. F. (2010). Investigation of wear behavior of titanium oxide films, produced by anodic oxidation, on commercially pure titanium in vacuum conditions. Surf. Coatings Technol. 205 (6), 1757–1763. doi:10.1016/j.surfcoat.2010.08.079
Yıldıran, Y., Avcu, E., and Sınmazçelik, T. (2015). Optimization of surface properties of shot peened TI6AL4V alloy. Acta Phys. Pol. A 127 (4), 984–986. doi:10.12693/APhysPolA.127.984
Yildiran Avcu, Y., Yetik, O., Guney, M., Iakovakis, E., Sinmazcelik, T., and Avcu, E. (2020). Surface, subsurface and tribological properties of Ti6Al4V alloy shot peened under different parameters. Mater. (Basel) 13 (19), 4363. doi:10.3390/ma13194363
Yin, M., Wang, W., He, W., and Cai, Z. (2018). Impact-sliding tribology behavior of TC17 alloy treated by laser shock peening. Mater. (Basel) 11 (7), 1229. doi:10.3390/ma11071229
Yu, H., Ju, J., Yang, T., Wang, C., Zhang, T., Peng, P., et al. (2024). Experimental and finite element simulation studies of the bio-tribological behavior of L-PBF Ti-6Al-4V alloys with various surface roughness. Tribol. Int. 194, 109514. doi:10.1016/j.triboint.2024.109514
Zhang, J., Hu, H., Liu, X., and Li, D. S. (2019). Development of the applications of titanium nitride in fuel cells. Mater. Today Chem. 11, 42–59. doi:10.1016/j.mtchem.2018.10.005
Zhang, J., Li, K., and Hu, J. (2020a). Performances investigation of Ti6Al4V alloy modified by plasma nitriding + plasma enhanced chemical vapor deposition and laser remelting process in simulated body fluid. Metals Mater. Int. 27 (11), 4757–4767. doi:10.1007/s12540-020-00772-z
Zhang, L., Shao, M., Wang, Z., Zhang, Z., He, Y., Yan, J., et al. (2022). Comparison of tribological properties of nitrided Ti-N modified layer and deposited TiN coatings on TA2 pure titanium. Tribol. Int. 174, 107712. doi:10.1016/j.triboint.2022.107712
Zhang, L. C., and Chen, L. Y. (2019). A review on biomedical titanium alloys: recent progress and prospect. Adv. Eng. Mater. 21 (4). doi:10.1002/adem.201801215
Zhang, L. C., Chen, L. Y., and Wang, L. (2020b). Surface modification of titanium and titanium alloys: technologies, developments, and future interests. Adv. Eng. Mater. 22 (5). doi:10.1002/adem.201901258
Zhang, L. C., Liu, Y., Li, S., and Hao, Y. (2018). Additive manufacturing of titanium alloys by electron beam melting: a review. Adv. Eng. Mater. 20 (5). doi:10.1002/adem.201700842
Zhang, Q., Li, Y., Liang, F., Zhang, H., Wang, B., Li, X., et al. (2024a). Tailoring tribological characteristics in titanium alloys by laser surface texturing and 2D Ti3C2Tx MXene nanocoating. Adv. Funct. Mater. doi:10.1002/adfm.202401231
Zhang, Y., Du, X., Wang, C., and Zhang, G. (2024b). Tribological properties of titanium alloy with micro-nano multiscale texturing against bone under simulated implant contact conditions. Tribol. Int. 194, 109586. doi:10.1016/j.triboint.2024.109586
Zhang, Z., Liu, H., Sun, W., Si, C., and Wang, J. (2024c). Shot peening pre-treatment for nano-nitriding layer formation to enhance wear and corrosion resistance in medical titanium alloys. Mater. Lett. 368, 136669. doi:10.1016/j.matlet.2024.136669
Zhecheva, A., Malinov, S., and Sha, W. (2006). Titanium alloys after surface gas nitriding. Surf. Coatings Technol. 201 (6), 2467–2474. doi:10.1016/j.surfcoat.2006.04.019
Zhecheva, A., Sha, W., Malinov, S., and Long, A. (2005). Enhancing the microstructure and properties of titanium alloys through nitriding and other surface engineering methods. Surf. Coatings Technol. 200 (7), 2192–2207. doi:10.1016/j.surfcoat.2004.07.115
Zheng, Y., and Xu, P. (2023). Effect of Nb content on phase transformation and comprehensive properties of TiNb alloy coating. Coatings 13 (7), 1186. doi:10.3390/coatings13071186
Zhong, H., Liu, L., Yang, L. Q., Ma, M. Z., Hu, E. Z., and Hu, K. H. (2023). Preparation of oxide coating on Ti30Zr5Al3V alloy via plasma electrolytic oxidation and its tribological behavior. Surf. Coatings Technol. 474, 130095. doi:10.1016/j.surfcoat.2023.130095
Zhou, J., Cui, K., Xu, Z., Sun, Z., Guelorget, B., and Retraint, D. (2022). Modelling residual stress and residual work hardening induced by surface mechanical attrition treatment. Int. J. Mech. Sci. 233, 107688. doi:10.1016/j.ijmecsci.2022.107688
Zhou, J., Sun, Y., Huang, S., Sheng, J., Li, J., and Agyenim-Boateng, E. (2019). Effect of laser peening on friction and wear behavior of medical Ti6Al4V alloy. Opt. and Laser Technol. 109, 263–269. doi:10.1016/j.optlastec.2018.08.005
Keywords: mechanical surface treatment, coatings, Titanium alloy, biological properties, coefficient of friction, wear behavior, wear mechanisms, microstructural properties
Citation: Abakay E, Armağan M, Yıldıran Avcu Y, Guney M, Yousif BF and Avcu E (2024) Advances in improving tribological performance of titanium alloys and titanium matrix composites for biomedical applications: a critical review. Front. Mater. 11:1452288. doi: 10.3389/fmats.2024.1452288
Received: 20 June 2024; Accepted: 23 August 2024;
Published: 06 September 2024.
Edited by:
Chao Yang, South China University of Technology, ChinaCopyright © 2024 Abakay, Armağan, Yıldıran Avcu, Guney, Yousif and Avcu. This is an open-access article distributed under the terms of the Creative Commons Attribution License (CC BY). The use, distribution or reproduction in other forums is permitted, provided the original author(s) and the copyright owner(s) are credited and that the original publication in this journal is cited, in accordance with accepted academic practice. No use, distribution or reproduction is permitted which does not comply with these terms.
*Correspondence: Egemen Avcu, YXZjdWVnZW1lbkBnbWFpbC5jb20=; Mustafa Armağan, bXVzdGFmYWFybWFnYW5AaG90bWFpbC5jb20udHI=