- 1School of Physics, Engineering and Computer Science, Centre for Engineering Research, University of Hertfordshire, Hatfield, United Kingdom
- 2Department of Materials Science and Engineering, The University of Sheffield, Sheffield, United Kingdom
- 3Department of Geology and Geochemistry, Faculty of Sciences, Autonomous University of Madrid, Madrid, Spain
- 4Paul Scherrer Institute, Laboratory for Waste Management (LES), Villigen, Switzerland
Magnesium phosphate cement (MPC) is known as a high-performing rapid repair material for concretes in practice, and has also become a fast-moving research area for other applications, although its application has not yet reached its full potential. MPC has been utilized as a repair material in certain applications, although it is still less commonly used/recommended than the most popular and standardized repair materials. Therefore, it is important to systematically investigate the suitability of this material in the construction sector as a repair material. This review provides an in-depth summary of the engineering properties of magnesium potassium phosphate cements (MKPCs), as a particular example of MPCs that do not suffer from the undesirable release of ammonia which is observed in some other MPC formulations. Key properties relevant to the use of MKPCs as repair materials, from the fresh state to the hardened state are systematically examined. On this basis, the suitability of MKPC as a potential repair material is explored, highlighting the state-of-the-art practices, challenges and drawbacks in engineering applications, and future perspectives.
1 Introduction
With increasing focus internationally on the extension of the service life of structures, including retrofitting of buildings in preference to demolition and reconstruction (Scope et al., 2021), it is becoming increasingly important to have an effective and high-performing toolkit of available repair materials to enable any potential damage in old structures to be rehabilitated for extended service life (Pang et al., 2023; Czarnecki et al., 2020). A standard repair material that ensures its performance from casting to fulfilling structural/exposure/functional requirements is therefore highly desirable in the modern construction industry. A summary of the main performance characteristics, governing factors, and assessment criteria of an ideal concrete repair material is shown in Figure 1. A primary requirement of a good repair material is to ensure proper bonding with the old concrete, enhanced volume stability, and to be compatible with the existing surface, particularly matching the (usually low) thermal expansion values of the existing concrete (Yang et al., 2000a). Repair materials mainly fail due to stresses generated at the repair interface, either due to drying shrinkage or due to the mismatch between the coefficients of thermal expansion of both materials, or by debonding if the bond strength at the interface was inadequate (e.g., if the substrate was not well prepared prior to application).
In addition to structural stability and durability, repair materials are also expected to have functional requirements. Environmental performance indicators such as noise reduction, urban heat mitigation, de-icing and exhaust gas absorption are also considered in modern repair materials (Jiang et al., 2018). Therefore, it is ideal if the compatible repair materials also possess such added functionality.
A repair material should be able to withstand mechanical stresses on its own, in the bulk and at the interface, and also to protect the substrate from failure. In a typical concrete repair system, there are three main failure modes that need to be considered (Manawadu et al., 2023). First is the cohesive failure mode, where the failure can occur away from the interface, either in the substrate layer or in the newly cast repair layer. This failure mode occurs when the interface bond is stronger than the individual layers. Secondly, adhesive failure happens at the interface, indicating that the bond is not sufficient to withstand the stresses that arise. Thirdly, the failure can also occur in a mixed mode where the cracks appear both in the layers and interface as well. Therefore, it is vital to understand the inherent engineering properties of the repair materials considered for use, to evaluate the compatibility of any repair material with its substrate.
Over the past few decades, repairing deteriorated infrastructures including pavements, highways, bridges and airport runaways has been increasingly problematic to local and national governments around the globe. Such repair works often cause disruptions to public traffic or usage, resulting in increased costs that may even be much more expensive than the repair work itself. Therefore, a rapid repair material with improved performance is highly sought-after in the construction industry to effectively restore the quality of existing infrastructure within a given short timeframe. Magnesium phosphate cement (MPC) is known to have the potential to be an attractive repair material in practice, and has recently evolved as a fast-moving research area for this and other applications. MPC has been successfully utilized as a repair material, although it is still less commonly used/recommended than the most popular and standardized repair materials such as accelerated OPC and shrinkage compensating cements (Ley, 2022). Therefore, it is valuable to systematically investigate the suitability of this material in the construction industry as a repair material, and this is the main focus of the current paper.
1.1 The basis of MKPC as a cementitious material
Magnesium Phosphate Cements (MPCs) may also be classified as a type of chemically bonded ceramics (Wagh and Jeong, 2003). One particular formulation of phosphate-based cementitious materials was patented in 1939 for application as a dental cement (Prosen, 1939), although they have gained attraction from the construction industry over the past few decades due to their excellent properties as a rapid repair material (Walling and Provis, 2016). MPCs are primarily produced via a reaction between magnesia (periclase, MgO) and a soluble phosphate salt–most commonly either ammonium or potassium phosphate salts. At first, ammonium salts were widely used in the design of MPCs (Yang et al., 2000b; Abdelrazig et al., 1988; Sugama and Kukacka, 1983a; Abdelrazig et al., 1989; Sarkar, 1991; Jiang and Zhang, 2001; Paceagiu and Georgescu, 2008; Limes and Russell, 1977; Stierli et al., 1976; Brabston, 1984; Barde et al., 2006). Over time, the ammonium salts have become less utilized, mainly due to the release of gaseous ammonia during the setting and hardening process (Ding and Li, 2005; Li and Chen, 2013). In addition, as potassium-based phosphates show lower solubility in water than when using other amphoteric phosphate species, the reaction rates become somewhat slower, providing more opportunity to effectively control the heat release and setting time of the material (Le Rouzic et al., 2017a; Fan and Chen, 2014).
The magnesia used in this type of cement is produced mainly through the calcination of magnesite, although other non-carbonate MgO sources are increasingly under discussion as magnesia-based cements attract attention for potential CO2 emissions reduction purposes. Magnesium potassium phosphate cements (MKPCs) generally use dead-burned MgO, i.e., MgO that is calcined in a temperature range between 1500°C–2000°C, as documented in most of the literature (Walling and Provis, 2016). Higher calcination temperatures cause sintering of the MgO particles, which also brings reduced reaction rates and the ability to better control heat evolution and setting times compared to when more reactive (e.g., light-burned) magnesia are used.
Combinations of these constituents with water form as a principal reaction product potassium struvite (struvite-K) (Gardner et al., 2021), which is the main hydrated product in the hardening MKPC system and the main space-filling and strength-giving phase in the hardened MKPC. Struvite-K is a synthetic counterpart to the naturally occurring mineral struvite (MgNH4PO4.6H2O), which is also the binding phase that forms when using ammonium salts in MPC as the soluble phosphate (Xing et al., 2011). Struvite-K has also been recognized as a naturally occurring mineral (Graeser et al., 2008). Currently, MKPC is mainly used in two major practical applications: infrastructure rehabilitation (Yang et al., 2000a; Qiao, 2010; Qiao et al., 2010; Li Y. et al., 2014; Tan et al., 2016; Lu et al., 2016; Zheng et al., 2016; Lee et al., 2017; Li G. et al., 2017) and waste solidification (Wagh, 2004; Covill et al., 2011; Pyo et al., 2021; Gardner, 2016; Josephson et al., 2011). This material has also been identified as a candidate for the 3D printing of building structures due to its rapid setting, high early strength gain and low shrinkage (Zhao et al., 2021a; Zhao et al., 2021b; Khalil et al., 2020; Zhang et al., 2020). However, its cost is higher than the cements that are usually used in this type of higher-volume application, which is a barrier to its larger-scale application in bulk production (as opposed to repair material) scenarios. The printability of MKPC for repairing concrete structures in severe environmental conditions has also been assessed, due to its unique advantages as an excellent repair material (Fu et al., 2016).
MKPCs have been reported to have excellent performance characteristics as a rapid repair material (Figure 1), such as fast setting time (Li and Chen, 2013; Qiao et al., 2009; Seehra et al., 1993), high early strength (Qiao et al., 2010; Qiao et al., 2009), low shrinkage (Yang et al., 2000a; Li and Chen, 2013; Qiao et al., 2010; Li J. et al., 2014; Lei et al., 2018; Jiang et al., 2017), low permeability with improved durability characteristics (Yang et al., 2000a; Lei et al., 2018) and good bonding properties (Qiao et al., 2010; Lei et al., 2018; Li Y. et al., 2017). However, there is a lack of a systematic review to investigate its properties to evaluate the suitability of MKPCs as a rapid repair material. This review therefore provides an in-depth summary of the relevant properties of MKPCs. Key properties relevant to repair materials, from the fresh state to the hardened state, are systematically examined. The suitability of MKPC as a potential repair material is reviewed firstly, through a comparative analysis of the benefits and drawbacks of MKPC when compared with the other repair materials, particularly rapid-hardening cement-based repair materials. Secondly, the challenges and concerns of using MKPC in engineering applications are highlighted. Thirdly, the state-of-the-art practices and recommendations for optimizing the mix design are explored. Then, a commentary on standard specifications and the current status of MKPC with regard to the existing engineering guidelines is provided. On that basis, the suitability of MKPC as a repair material and future perspectives are explored.
2 A review on properties of MKPC
The suitability of MPC as a potential repair material has been summarised in some older review papers (Haque and Chen, 2019; Yang et al., 2014), and there have been detailed experimental studies on chemical and mechanical properties to understand the mechanisms of MKPC setting and hardening. In this section, an extensive review on the properties of MKPC is presented, covering aspects of the hydration process, microstructure analysis, volume stability, mechanical properties, durability aspects, and bonding performance when functioning as a repair material.
2.1 Early hydration and reaction mechanisms
MKPC is significantly different from Portland cement in terms of both the raw materials used and the reaction mechanisms that take place during the hydration process. It is a ternary system consisting of magnesia, KH2PO4, and water, that react to form struvite-K as the principal reaction product. The reaction sequence to reach struvite-K from these precursors can include various hydrous magnesium phosphates as intermediates; these have recently been reviewed and assessed by Lothenbach et al. (Lothenbach et al., 2019) and the discussion will not be repeated here, beyond noting that full struvite-K formation does require rather rigorous control of reaction stoichiometry. Because of the crystalline nature of struvite-K, the relationship between mix formulation and the exact identity of the hydrate products is more critical in MKPC than in most other cements.
Stoichiometrically, 1 mol of magnesium oxide reacts with 1 mol of potassium dihydrogen phosphate and 5 mol of water to form 1 mol of struvite-K. However, despite these theoretical molar ratios, it has been identified that an excess of magnesia over KH2PO4 is beneficial in practical applications, as enhanced chemical and mechanical stability can be achieved when increasing Mg/P molar ratio beyond the stoichiometric 1:1 (Qiao et al., 2010; Lee et al., 2017; Gardner et al., 2015a; Mácová and Viani, 2017), although very excessive addition of MgO does raise some risks around potential later-age expansion. The inclusion of retarders (see section 2.2) is also critical to control the rapid setting reaction which would otherwise occur in MKPCs. In addition to the basic constituents, MKPC formulations can also accept a number of fillers in their composition, which are used to replace some of the excess MgO that would otherwise remain unreacted, and can accommodate waste constituents if used as immobilization matrices.
The basic (overall) chemical reaction of MKPC hydration can be written as follows (Ma et al., 2014a; Xu et al., 2018a):
There are several proposed mechanisms for the precipitation of struvite-K in the literature:
1. Homogenous nucleation mechanism (Soudée and Péra, 2000) - the formation of struvite-K follows a topo-chemical reaction where the process initiates with the wetting of MgO, leading to the formation of Mg complexes on the surface of MgO grains. Then, the available aqueous phosphate ions react at the surface of the MgO grain to form struvite-K crystals.
2. Heterogeneous nucleation mechanism (Wagh, 2004) - A dense gel of struvite-K is formed and crystallizes around MgO grains that act as nucleation sites.
3. Multiple precipitation/dissolution reactions (Qiao, 2010; Wang et al., 2023) - An increase in the pH results from the dissolution of MgO. Intermediate products are formed and crystallise, then re-dissolve in the solution. Finally, saturation and crystallization of a struvite-K gel occur from this process.
Several studies have found that there are intermediate reaction products forming before transforming to struvite (Lahalle et al., 2016; Chau et al., 2012) and those can change material performance in terms of properties such as setting time, strength and volume stability (Qiao et al., 2010; Ma et al., 2014a; Wang et al., 2013a). However, in general, the intermediate hydration products tend to disappear within a very short time (Wang et al., 2023). The completion of the main reaction typically occurs within the first 3 h after casting. The Mg/P ratio, water availability, and pH values play an important role in determining the types of hydrates precipitated during the reaction of MKPCs (Lahalle et al., 2016; Chau et al., 2012; Le Rouzic et al., 2017b). Thermodynamic modelling performed in a MKPC system showed that the hydration reactions can be divided into six periods mainly depending on the pH value of the solution (Zhang et al., 2017).
The influence of magnesia reactivity is a leading factor in the hydration kinetics of MKPC systems. Typically, the reaction of magnesia is extremely fast, especially at higher Mg/P ratios and low water to binder ratios, even though dead-burned magnesia is generally used as was mentioned above. In this case, the maximum reaction takes place during the first day after casting, and not much reacts afterwards (Xu et al., 2022a). When the water to binder ratio is higher, more magnesia reacts and the reaction is prolonged (Xu et al., 2019). The reactivity of magnesia is a function of many factors including the calcination temperature, grinding of the material and the precursor used to produce magnesia (Qiao et al., 2009; Bocanegra-Bernal, 2008; Birchal et al., 2000). The reactivity is increased with an increase in the surface area of magnesia (Soudée and Péra, 2000; Soudée and Péra, 2002). However, the increase of surface area also produces higher viscosity and leads to shorter setting times. The calcination of magnesia at high temperatures (dead-burned is typically considered at temperatures in the range 1500ºC–2000°C) leads to a product with lower surface area, reducing the reactivity, which is typically preferred for MKPC.
2.2 Setting time
The quick setting of MKPCs is one main quality for it to be considered as an efficient rapid repair material. The rapid setting of MPC materials has been well-recognised for decades, and utilized in repairing damaged runways, pavements, and bridges since the 1980s (Brabston, 1984; Smith et al., 1984). One report, in particular, detailed the use of MPC for a rapid repair of bombing damage at Port Stanley Airport (Sinclair et al., 1984). The MPC used to repair this damage was set in about 30 min and the task force managed to patch over 1,000 scabs successfully within about 3 days enabling rapid re-commissioning of the airport. More importantly, this runaway repair demonstrated remarkable resilience, accommodating 77 landings of heavily loaded Hercules aircraft and hundreds of landings by Harriers with only minor maintenance needed afterwards.
However, the intense and exothermic reaction between acid phosphates and magnesia leads to a typical setting time of about 3 min without any retarders, and causes difficulties for many applications (Qiao et al., 2009). Therefore, retarders with soluble oxy-boron compounds such as borax or boric acid have been used to prolong the setting time, with minimal identified effects on the hydrated products (Qiao et al., 2009). As shown in Figure 2D, the addition of retarders such as borax results in a delay in the setting time; however, retarder addition in excessive amounts could adversely affect strength properties (Qiao et al., 2009). Therefore, it is important to use an optimum borax amount that provides a balance between a sufficiently long setting time and good strength development. Such retarders have been claimed to act only as pH-buffering agents, with less attention paid to their involvement in the reaction mechanisms (Ma and Xu, 2017; Dong et al., 2023), but their effects in forming surface-blocking films on reactant particles, and in complexation of aqueous reactant species, have more recently been identified (Gelli et al., 2022). The retardation mechanism is reported to occur due to: borax being hydrolyzed in the solution to produce a compound that precipitates as a film around MgO grains (Sugama and Kukacka, 1983b); production of lünebergite as a coating on MgO particles (Wagh and Jeong, 2003); or due to the formation of an amorphous mineral containing borate and orthophosphate with the stabilization of the Mg2+ and K+ ions in the solution (Lahalle et al., 2018). However, in the literature, yet there is no clear consensus regarding the retarding mechanism during the setting of MPCs. Besides, oxy-boron compounds are classified as substances with reproductive toxicity in the EU candidate list of substances of very high concern for authorization (Cau Dit Coumes et al., 2021). Alternative safer retarders to oxy-boron compounds such as sodium alginate and aluminum nitrate have been examined and have shown encouraging signs in terms of retarding MPCs while ensuring higher safety to the user (Cau Dit Coumes et al., 2021; Liu et al., 2022; Yang et al., 2022). Therefore, a fundamental understanding of the governing factors affecting setting time and further research on alternative retarders that alleviate the issues with oxy-boron compounds will be beneficial for the future use of this class of cements as a reliable repair material.
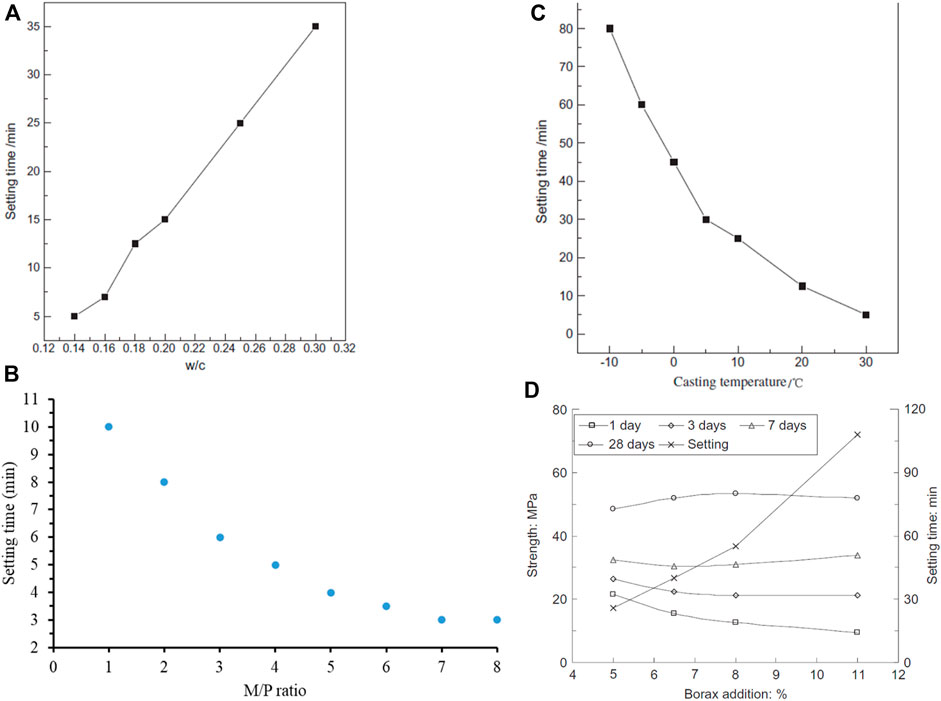
Figure 2. Relevant factors affecting the setting time of MKPC: (A) effect of w/b on the setting time (constant casting temperature of 20°C) (Li and Chen, 2013) Copyright 2013 Elsevier B. V.; (B) effect of Mg/P ratio on the setting time (Xing et al., 2011) Copyright 2011 Thomas Telford Ltd.; (C) effect of casting temperature on the setting time (Li and Chen, 2013) Copyright 2013 Elsevier B. V.; (D) effect of borax addition on the compressive strength (left Y-axis) and setting time (right Y-axis) (Qiao et al., 2009) Copyright 2009 Thomas Telford Ltd.
There are multiple other governing factors that affect the setting time of MKPCs, and that need to be understood both in isolation, and in terms of the interactions between them. One main factor is the water to binder (w/b) ratio of the cement paste (note that the term “binder” used in this paper refers to the total mass of MgO + KH2PO4). It is evident from Figure 2A that a higher w/b leads to a longer setting time (Li and Chen, 2013). This can be primarily due to the lower concentration of the reactants in the solution leading to a prolonged setting time at higher w/b ratios. Similar observations were reported for mortars tested at different w/b ratios (Lee et al., 2017).
The Mg/P ratio also plays an important role in governing the properties of MKPC materials. As shown in Figure 2B, the setting time was observed to be quicker when the MgO content was increased as the M:P ratio varied from one to 8 (Xing et al., 2011). This is because of the rapid chemical reaction of magnesia and phosphate, upon the addition of water. However, higher Mg/P ratios (between eight and 16) have been reported to yield almost similar setting times (Qiao et al., 2009; Xu et al., 2015). At higher Mg/P ratios, the setting time is insignificantly affected, possibly due to the formation of insufficient reaction products to bond the magnesia particles together beyond the optimum Mg/P ratio levels.
Another factor significantly affecting the setting time is the casting temperature. Figure 2C shows that the setting time of MKPC cement (with a w/b ratio of 0.18, including retarder) decreases with casting temperature. When the temperature was higher than 30 °C, too short a setting time was recorded. On the other hand, MKPCs have prolonged but not excessive setting times at lower casting temperature levels, at 0°C or even at −20°C, indicating that this type of cement can harden and gain strength in cold weather conditions. The MPCs can outperform other repair materials that have difficulties in application in negative temperature environments. However, it is important to control the Mg/P ratio, w/b ratio, and the admixtures used in MPCs for improved performance under such conditions (Huang et al., 2023). A higher Mg/P ratio leads to a release of more heat at early age and generates more hydration products, even at lower temperatures. In terms of the w/b ratio: too low a w/b ratio will lead to defects such as honeycombs, while too high a w/b ratio will lead to internal icing and freeze-thaw cracking. Controlling the admixtures will be also important in terms of the strength development in cold weather conditions.
For acid-base and alkali-activated cements, the Arrhenius equation (Equation 2) may be used to describe the dependence of the setting reaction on temperature:
where
The apparent
A kinetic study performed on MKPC in the temperature range 5ºC–25°C attributed an apparent
Among the other factors influencing setting time, the purity of the magnesia used may also be important (Qiao et al., 2009). An increase in the magnesia with relatively high purity and reactivity (
Recent studies have also focused on prolonging the setting time by using sustainable methods in mixing MKPC cements. A relevant study (Qiao et al., 2009) shows that MKPC mixes including seawater have shown prolonged setting time, delayed heat release and increased compressive strength. Such future industrial applications can be essentially useful in densely populated areas where freshwater availability is limited, to produce cement-based materials. The use of seawater in cementitious materials is generally restricted by the risk of corrosion of embedded steel, but MKPC is in any case not usually intended for use with steel reinforcement, so this is less problematic for these materials than for other types of cements.
2.3 Microstructure
Two main phases, struvite-K and unreacted MgO, are found as the dominant binder constituents after the acid-base chemical reaction between MgO and KH2PO4 that leads to hardening of an MKPC (Ding and Li, 2005; Xing et al., 2011; Qiao et al., 2009; Wang et al., 2013a; Ding et al., 2012; Qiao et al., 2012). The struvite-K is the main crystalline product formed in MKPC, and may be produced following the overall reaction formula mentioned in Equation 1, including potential pathways that involve transient Mg-phosphate intermediates of differing stoichiometry. The most intense XRD reflections for struvite-K are observed at 20.9°, 30.9°, 21.6°, and 34° 2θ when conducting XRD using Cu-Kα radiation; those of unreacted MgO (periclase) are detected at 42.9, 62.3, and 78.6° (Lee et al., 2017) (Figure 3).
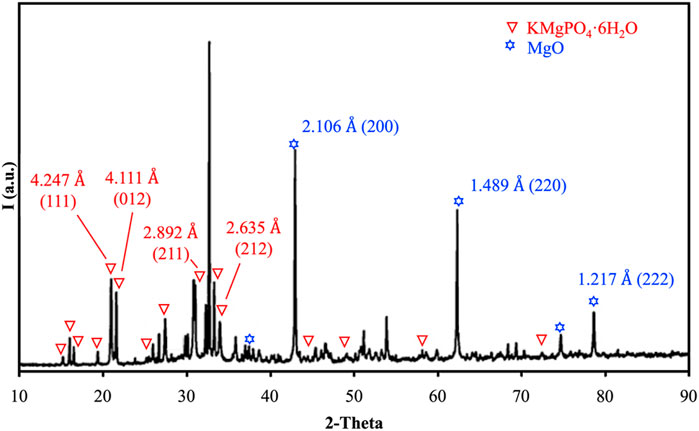
Figure 3. XRD showing the main reflections attributed to struvite-K (red) and periclase (blue). The figure was modified from (Formosa et al., 2012), and presents data for an MKPC formulation cured for 28 days, using a low-grade MgO and KH2PO4, and scanned using Cu
In addition, some solid non-crystalline phases may also form in the MKPC cement matrix (Xing et al., 2011), and/or some of the intermediate phases may persist if the mix stoichiometry does not exactly match the conditions required to produce pure struvite-K. In most MKPC formulations, potassium dihydrogen phosphate (KDP) is totally consumed in the chemical reaction to produce struvite-K, and therefore, no remaining KDP is observed by XRD, especially at higher Mg/P ratios (Hou et al., 2016). Conversely, in MKPC cement pastes with low water to solid ratios (
In contrast, MKPC pastes with Mg/P molar ratios <4 at a higher water to solid ratio (
When added to MKPC mixes, fly ash or blast furnace slag are considered as fillers because they do not participate in the main chemical reaction that leads to struvite-K formation. MKPC formulations including fillers did not show crystalline secondary products, but there was some evidence of reaction of the filler particles–particularly blast furnace slag–with the formation of disordered or amorphous reaction products, indicating that blast furnace slag is not wholly inert in MKPC blends (Gardner et al., 2015b). Another type of filler used is wollastonite, which also shows some reactivity when blended in MKPCs. Partial replacement by wollastonite slows down cement hydration kinetics and reduces the amount of heat release (Xu et al., 2020), but the reaction of wollastonite in MKPCs leads to the formation of amorphous hydroxyapatite and M-C-S-H hydrates that enhance the strength at later ages (Xu et al., 2020; Xu et al., 2021).
Typically, a tightly joined polycrystalline microstructure is observed in MKPC paste under SEM (Ding et al., 2012). The morphology of the formed struvite-K crystalline microstructure appears to be related to the Mg/P ratio (Le Rouzic et al., 2017a); 90-day old samples with a w/b of 0.20, at different Mg/P ratios, are shown in Figure 4. Figure 4A shows that needle-like crystals are formed when the Mg/P ratio is 1. At this low Mg/P ratio a condensed microstructure of struvite-K is produced and less unreacted MgO remains (Xu et al., 2015). With an increase in the Mg/P ratio from one to 5, a mix between platelet and prismatic morphologies is formed. When the Mg/P ratio is 5, a clear prismatic shape was observed (Figure 4B). At an Mg/P ratio of 10, the formed products did not have a regular defined morphology and showed poor crystallinity (Figure 4C); amorphous phases were present.
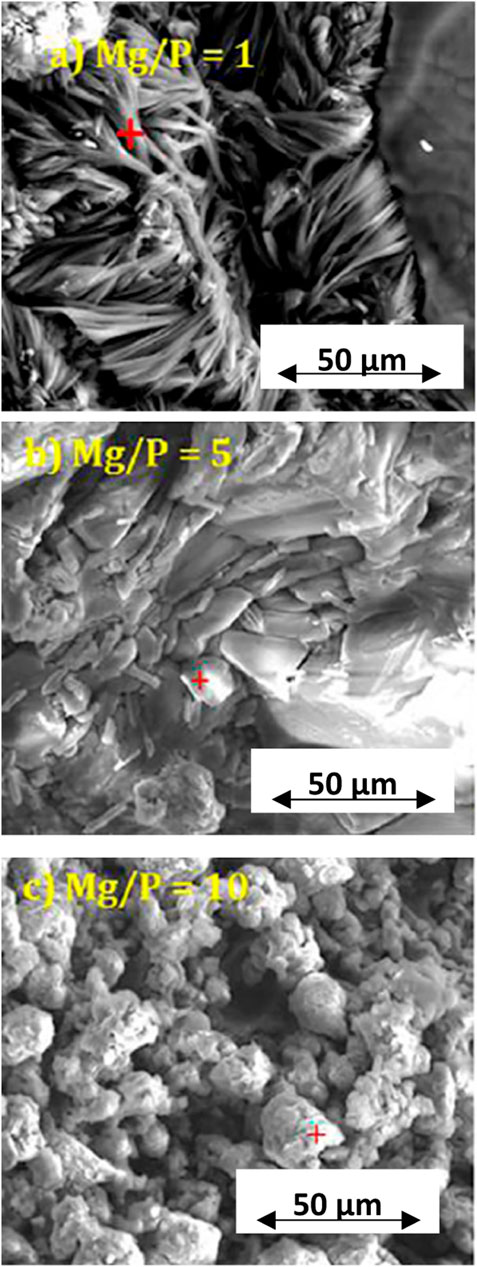
Figure 4. Morphology of struvite-K with varying Mg/P ratios (Le Rouzic et al., 2017a). Copyright 2017 Elsevier B. V.
It is also important to investigate the dehydration characteristics of MPCs; the phase changes that occur due to rising temperature can affect the properties of MPCs (Zhang et al., 2013). It is reported that both magnesia and KDP have extremely stable thermal behaviour up to 210 °C (Xu et al., 2015). Struvite-K has its dehydration temperature centered around 105°C–136°C (Lahalle et al., 2016; Zhang et al., 2013; Lahalle et al., 2019), and the weight loss observed below 105°C typically corresponds to the evaporation of free water. In the presence of fly ash, it is reported to have slightly lesser weight loss in this temperature range, due to the reduced formation of struvite-K (Xu et al., 2018b). Thereafter, the weight loss is attributed to the thermal decomposition of unreacted residual KDP.
Another important aspect of MKPC microstructure is its pore structure, which has a significant influence on both the mechanical and transport properties. Within the microstructure of MKPC systems, two main types of regions can be identified: a crystal region containing struvite-K crystals up to hundreds of microns in size, and a hybrid region where unreacted MgO and amorphous hydrates exist (Zhang G. et al., 2023). The hydration of the MKPC system is mainly governed by mass transport through the macropores (Lee et al., 2017; Li et al., 2015a); an increase of the w/b ratio in MKPC results in an increase in the number of capillary pores and macropores (Lee et al., 2017). Mercury intrusion porosimetry (MIP) tests conducted on MKPC cement paste with an Mg/P ratio of 4 (Ma et al., 2014a) indicated that as the age and hydration degree increases, the porosity decreases, while the pore size distribution mode does not change as much. Porosity measurements performed over a wide range of different Mg/P ratios showed that porosity in MKPCs may not be a monotonic function of the Mg/P ratio. An Mg/P ratio of six gave the lowest porosity at 3 days, while Mg/P ratios of 4 and 12 had higher porosity (Ma et al., 2014a). Similarly, in (Lee et al., 2017) it was reported that at a Mg/P ratio of about 8, a slight increase of the capillaries; however, a decrease of the capillaries was observed at lower Mg/P ratios.
The reaction kinetic effects leading to the existence of optimum Mg/P values remain unclear and should be further assessed in future, as all of these compositions are significantly above the 1:1 stoichiometric ratio required for struvite-K formation and so must be under kinetic control. Moreover, it is worth investigating pore size distribution curves of MKPC cement paste formulations with lower Mg/P ratios that tend to show a higher amount of larger pores due to expansion and subsequent cracking (Xu et al., 2019).
2.4 Strength development and elastic properties
The rapid development of compressive strength is one of the most favourable properties that leads MKPC to be used as a repair material. It is reported that at a very early age (∼3 h after casting) MPC cement pastes within a w/b ratio range of 0.14–0.20 reached approximately 30 MPa, which is much higher than Portland cement at the same age (Li and Chen, 2013). As was discussed above regarding setting time, probably the key factor affecting the rate of compressive strength development of MKPC paste is the w/b ratio. The strength of MKPC pastes indicated an inverse relationship with w/b ratios in the range from 0.14 to 0.20, at testing ages ranging from 3 h to 28 days (Li and Chen, 2013). As is conventional across cementitious materials, lower mechanical strength is observed with the increase of water content (Ding and Li, 2005; Li and Chen, 2013; Wang et al., 2013a; Wang et al., 2013b). This is attributed to the higher number of pores being formed at high w/b ratios. However, extremely low w/b ratios are not always beneficial. For example, in (Xing et al., 2011) it was shown that a very low Mg/P ratio resulted in very low strength development; samples with a Mg/P ratio of 1:1 cracked after being exposed to air curing at 3 days, without a measurable strength.
Another governing factor is the Mg/P ratio, which is closely linked to the rate of reaction, where an optimum value can result in better crystallization and growth of struvite-K, leading to a denser microstructure. Among the main constituents of MKPC pastes, magnesia evidently has the best mechanical properties in terms of hardness, elastic modulus, fracture toughness, compressive strength, and tensile strength (Le Rouzic et al., 2017a), but it is dispersed within the hydrate matrix so generally acts as an inclusion and micro-aggregate phase rather than imparting its high mechanical properties directly to the overall composite microstructure; it is bonded to the hydration products and thus contributes to mechanical properties development (Qiao et al., 2010). Different studies show different observed optimum values of Mg/P ratios that resulted in the highest mechanical properties, especially in mixes with low w/b ratios (Le Rouzic et al., 2017a; Qiao et al., 2009) where sample production is challenging and water availability for the reaction process may become a limitation. An excess of magnesia is generally required to ensure strength development, since only the outer rims of magnesia particles can react with KDP within a short period of reaction. At high Mg/P ratios (more than 8), there may be insufficient hydration products to bond the magnesia particles together, thus negatively affecting the strength properties. It is also observed that an excessive Mg/P ratio beyond an optimum value leads to a very fast reaction that can cause a lack of time to properly form a dense reaction product (Xu et al., 2015). An optimum Mg/P ratio leads to better cohesion in the microstructure of cement paste. Overall, the mechanical properties of the MKPCs are functions of the mechanical properties of each phase (including anhydrous grains, reaction products and porosity), and the cohesion between the different phases (Le Rouzic et al., 2017a).
One major limitation in the literature is the lack of available test data on the elastic properties of MKPC; in use as a repair material, the elastic properties of the substrate and patch materials must be compatible to avoid interfacial debonding under mechanical load. In terms of the elastic modulus value of individual compounds, struvite-K has a bulk modulus of about 27–29 GPa, which is comparable to the binding phases in other systems of similar density (Li et al., 2020; Pernal et al., 2023). MgO has a very high elastic modulus (270–330 GPa) (Le Rouzic et al., 2017a; Shand, 2006), while any residual KDP crystals that may be present at low KDP content have a value of 63 GPa (Wang et al., 2009). On this basis, it can be reasonably predicted that an increasing Mg/P ratio leads to an increase of the overall elastic modulus, as long as the formation of struvite-K is sufficient to fill the space between unreacted MgO particles and provide an effective matrix in which the stiff MgO inclusions are bound. A recent study has reported elastic modulus evolution for high-strength concretes (cube compressive strength
The optimization of the mix design using filler materials is proven to be useful in obtaining high-performance MPCs. A study showed an optimized formulation of MKPC containing fly ash in terms of both enhanced compressive strength and fluidity with a dense microstructure (Tan et al., 2023). This formulation contains 30% of fly ash and 10% of ultrafine fly ash. The addition of ultrafine fly ash resulted in a better filling effect in this mix design.
2.5 Volume stability
Another important factor in designing a repair material is the volume stability; investigation of shrinkage characteristics is important in assessing the cracking risk when the repaired material is subjected to restraint. Overall, the shrinkage of MKPCs is reported to be less than that of pastes made with Portland cement, which may be related to the lower water contents that are conventionally used in formulating MKPCs.
As the thickness of typical repair material layers is low, water can easily evaporate, or be absorbed by a porous concrete substrate, once the material is cast. So, low drying shrinkage evolution is essential; MKPC appears to offer advantages in this regard when compared to paste made with Portland cement, as several studies have reported lower drying shrinkage evolutions of MKPC repair materials when compared to that of Portland cements (Yang et al., 2000a; Li and Chen, 2013; Qiao et al., 2010; Li J. et al., 2014; Lei et al., 2018), with very low drying shrinkage evolution observed for MKPC mortars in (Li and Chen, 2013; Li J. et al., 2014). Mortars made with MPC had lower drying shrinkage values at all test ages ranging from 1 to 28 days after casting (Yang et al., 2000a; Qiao et al., 2010). For example, the drying shrinkage of mortar made with Portland cements increases significantly in the first week after casting, while that of MKPC mortar is about 40% of Portland cements mortar at the same age (Qiao et al., 2010). The drying shrinkage profile for MKPC can be divided into three main stages (Lei et al., 2018); (i) a swelling stage (before 1 day) (ii) a fast shrinkage stage (between 1 and 7 days) and (iii) a stable shrinkage stage (after 7 days). Nevertheless, such obtained drying shrinkage profiles were significantly lower than those obtained in paste with Portland cement.
Understanding the autogenous shrinkage evolution in MKPC repair materials is equally important, especially at early ages. The autogenous shrinkage is linked to chemical shrinkage where smaller values of the latter lead to lesser strains on the material, thus lowering the autogenous shrinkage. When the hydration progresses, water is consumed, and empty capillary porosity is created by self-desiccation. MKPC cement paste has shown much lower autogenous shrinkage values than cement pastes made with Portland cement (Le Rouzic et al., 2017a). One of the main reasons for lesser autogenous shrinkage is the reduced overall chemical shrinkage of MKPC materials when compared to Portland cement, leading to a lesser deformation of the microstructure. Besides, the porosity of these two systems plays a main role in the differences of the autogenous shrinkage values. The porosity of Portland cement is a very complex system ranging from nanometer scale to large capillary pores, whereas this diversity in pore sizes tends to be less in an MKPC system (Le Rouzic et al., 2017a; Ma et al., 2014b). Such differences in porosity are very important and can explain the low autogenous shrinkage observed in MKPC to a certain extent (Le Rouzic et al., 2017a). Furthermore, MKPC mortars with different types of fillers including metakaolin and pumice showed excellent dimensional stability (Dieguez et al., 2023).
2.6 Durability aspects
There is reported evidence of strong durability performance of MPC materials in practical applications, for example, in the use of MPC in the Dalton Highway project in Alaska in 1991 (Pioneering precast in Alaska, 1993; Burris et al., 2015; Mazari et al., 2020). In an extremely short construction season due to adverse weather conditions, the engineering team utilized MPC-based repair materials along with precast concrete deck panels to undertake rapid deck replacement in 18 bridges along this highway, which provides the only road access to large parts of northern Alaska and so is essential to maintain effectively. When examined after 20 years, the MPC bridge joints were observed to be in good service condition. Figure 5 shows an image of MPC-based grout on a bridge after 20 years of service. It is noteworthy that the cracking in the joints is mainly attributed to the torsional forces from bridge deck bending and not due to material defects (Burris et al., 2015).
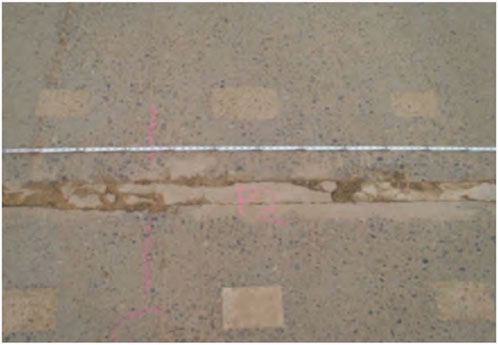
Figure 5. Bridge grout made from MPC in Dalton Highway in Alaska after 20 years of service (Burris et al., 2015).
There is an important lack of studies evaluating the durability aspects of MKPC under field or field-representative conditions, and a relatively small number of research studies are available to evidence the claimed improvements in the durability performance of MKPCs. Most of the studies conducted about 2 decades ago performed durability assessment of MPCs with ammonium phosphate as the soluble phosphate. It is reported that MPC mortar performs well against freeze-thaw and sulphate attack (Seehra et al., 1993). Considering the practical applications, a feasibility investigation of using MPC-based materials for repairing railway tracks indicated that MPC repair materials satisfy the operational requirements for the maintenance of the tracks. More importantly, MPC materials showed lower cracking resistance and good compatibility in terms of setting, elastic properties and thermal properties (Chen et al., 2017). The suitability of using MPC repair materials in negative temperature environments was assessed for road repair works (Huang et al., 2023). It is reported that the MPC materials successfully met the requirements for emergency road repair constructions in negative temperature environments. It was also noted that due to the unique advantages such as rapid strength gain, corrosion resistance, adhesive performance, and excellent volume stability, MPC materials outperform other cement-based repair materials under negative temperature levels.
A recent study reported that MKPC paste blended with limestone powder and silica fume was able to form a denser structure that can reduce the external deterioration of freezing and thawing in corrosive solutions (Chong et al., 2019). Similarly, MKPC mortar has good resistance against salt and frost spalling, owing mainly to its low water demand and uniformity of the closed pore distribution in microstructure (Ding et al., 2005). The sulfate freezing and thawing resistance of mortar can be improved by using limestone sand (Wu et al., 2022). The immersion of MKPC paste in different aqueous solutions for a longer period can lead to changes in the transport and mechanical properties of the material; the resistance of MKPC to basic media depends on the stability of the struvite-K (Lahalle et al., 2019).
As a repair material, the ability to demonstrate water resistance at early age is also important to applications in practice, especially when working in moist environments. It has been reported that when MKPC paste samples are immersed in water at early ages, some of the hydration products and unreacted phosphate can dissolve, leading to an increase in porosity which is detrimental in terms of strength (Shi et al., 2014). It was recommended to increase the natural curing time before water soaking, and also the addition of waterglass to improve the water stability of MKPC at early ages. The added waterglass (sodium silicate) was reported to form magnesium silicate hydrates that fill up the pores, thereby improving the pore structure (Shi et al., 2014). Another aspect in terms of the durability of a repair material is the ability to repair structures exposed to wet-dry cycles and sulfate. Degradation of MKPC under wet-dry cycles in 5 wt% Na2SO4 solution was investigated, and the mechanisms explored, in (Li et al., 2019). It was reported that when exposed to such an environment, the MKPC gradually degrades as (i) part of the struvite-K dissolves, leading to a partial loss of structural performance; (ii) fatigue crystallization pressure leads to microcrack formation, and (iii) Mg(OH)2 formation leads to expansion (Li et al., 2019). It was observed that fly ash improves the microstructure, thereby increasing the durability under wet-dry cycles.
In a repair material, it is crucial to minimize stresses at the repair interface, by having comparable (and, ideally, low) coefficients of thermal expansion in the old substrate surface and the repair material. Valuable test data on the coefficient of thermal expansion of mortar made with MPC compared to that made with Portland cement were put forward in (Yang et al., 2000a); the values obtained using MPCs were lower than those obtained using Portland cement. More importantly, it was observed that the coefficient of thermal expansion of MPC was comparable to the Portland cement concrete used in the same study, which indicated the compatibility of MPCs to use as a repair material on old concrete surfaces. Deicer-frost resistance is another quality a repair material should possess, especially because the combined action of frost and deicer in cold climates causes deterioration problems for many pavements, airport runways, bridges and roads. In (Yang et al., 2000a), was is shown that MPC mortar and concrete can show equal or better performance in terms of deicer-frost resistance compared to conventional Portland cement mortar or concrete.
Conversely, some studies have also observed drawbacks in terms of the durability properties of MKPCs. Efflorescence has been observed in MKPCs with Mg/P molar ratios <4 (Xu et al., 2019). Efflorescence can include several phases such as Mg2KH(PO4)2·15H2O, phosphorrösslerite (MgHPO4.7H2O), unreacted KH2PO4, and an unidentified phase. A main disadvantage reported is the swelling of MKPC samples (especially with low Mg/P molar ratios) that leads to cracking (Li Y. et al., 2014; Gardner, 2016; Josephson et al., 2011; Iyengar and Al-Tabbaa, 2007). MKPC pastes with low Mg/P ratios showed precipitation of an unidentified swelling product that led to cracking and disintegration of the samples (Le Rouzic et al., 2017a). However, for high Mg/P ratios (>5) in the same study, no swelling was observed. Xu et al. (Xu et al., 2019) reported that the swelling of MKPC paste disappears when the Mg/P molar ratio is higher than 3. A possible interpretation for the swelling is given in (De Campos et al., 2021), where the main cause is reported as the sedimentation of various particles. A schematic diagram of the swelling mechanism is shown in Figure 6 (adapted from (De Campos et al., 2021)). The swelling mechanism is briefly summarized as follows.
• Just after mixing, undissolved particles of KH2PO4 and MgO start to sediment while forming the intermediate phase phosphorrösslerite (MgHPO4⋅7H2O). Formation of this phase causes an increase of the sample volume than its initial stage (in the liquid state).
• KH2PO4 tend to settle faster than the MgO particles, leaving larger amounts of KH2PO4 at the bottom. This leads to two issues: (i) a pH gradient, where the bottom has a lower pH than the top, and (ii) a locally varying Mg/P ratio, with a lower ratio at the bottom.
• The swelling gradually occurs throughout the solidification process since the volume of MgHPO4⋅7H2O is much larger than that of MgO and KH2PO4. While the swelling continues, due to the pH gradient and local variation of the Mg/P ratio, a threshold allows the transformation of MgHPO4⋅7H2O to the second intermediate phase Mg2KH(PO4)2·15H2O, causing about 20% solid volume reduction. With a gradual increase of pH (mainly at the top part), struvite-K is formed from Mg2KH(PO4)2·15H2O, causing a further contraction of 6%. This volume reduction causes the sample to crack, mainly in the middle region.
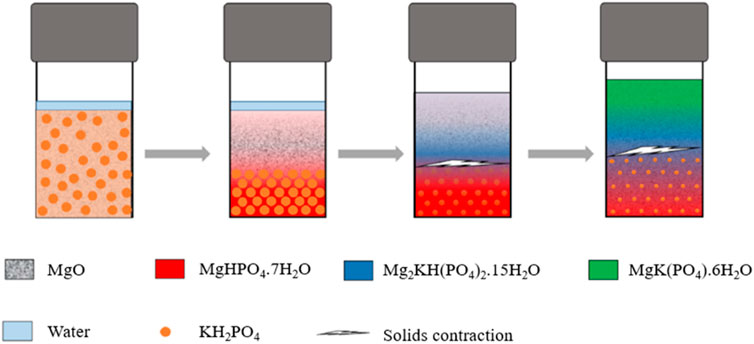
Figure 6. Schematic depiction of swelling mechanism in a stoichiometric MPC cement paste, adapted from De Campos et al. (2021). Copyright 2021 Elsevier B. V.
In some cases, poor water resistance of MPC-based materials has also been reported (Yang et al., 2000a; Li et al., 2009; Yang et al., 2013; Shao et al., 2013). The strength loss in magnesium phosphate materials that are stored in water for a very long time is a critical concern. The strength loss in mortar made with MPC increases with the soaking time in water, and can reach up to 20% strength loss within 90 days (Yang et al., 2000a). A possible cause of poor water resistance of low Mg/P pastes is the presence of grains of anhydrous KDP that are highly soluble, and can end up leaving voids when the sample is in contact with water (Le Rouzic et al., 2017a). The unreacted phosphates can be dissolved under long-term water immersion, causing a reduction of the reactant availability for ongoing struvite-K formation (Haque and Chen, 2019). It is also reported that the presence of residual soluble and non-binding KH2PO4 is somewhat problematic for the transport properties of the materials, for similar microstructural reasons, and provides further motivation for the use of higher Mg/P ratios in MKPC formulations (Le Rouzic et al., 2017a).
The performance of MKPC at elevated temperatures was investigated in (Li et al., 2015b), and it was observed that the strength significantly decreased when temperatures passed 130 °C. This is due to the evaporation and loss of crystal water from struvite-K. The strength of MKPC decreased gradually with the temperature continuing to increase beyond 200°C.
2.7 Bonding properties
Bonding performance is critical for any concrete repair and is highly dependent on the quality of the interface between the substrate concrete and the repair material. Studies have reported that MPC pastes and mortars are compatible in terms of the ability of bonding to PC concrete (Yang et al., 2000b; Yang et al., 2002; Zhang S. et al., 2023). There are a few studies that investigated the bonding performance of MKPC-based repair materials; however, this aspect is not yet rigorously assessed in the literature. In general, MPC-based repair materials appear to exhibit favourable bond properties mainly due to their bond strength, and low shrinkage characteristics.
MPC repair materials with lower Mg/P and w/b ratios have moderately higher bond strength than those with higher Mg/P and w/b ratios (Qin et al., 2018). This is mainly attributed to the production of cohesive struvite hydrates that can lead to well-developed interfaces in mixes with lower Mg/P and w/b ratios. A series of tests to investigate the bonding performance of damaged mortar and concrete repaired using MKPC was presented in (Li Y. et al., 2017). Splitting tensile tests performed on damaged concrete repaired by MKPCs indicated improved adhesive properties. High-strength MKPC showed excellent bonding performance with low-strength concrete by improving the interface bonding strength of the specimens. The tensile bond strength of MKPC mortar was measured through pull-off tests, and it was observed that MKPC-repaired samples had up to 120% higher bond strength properties compared to Portland cement-repaired samples at 28 days (Qiao et al., 2010). In (Qin et al., 2018), it is reported that MPC repair systems can achieve early high tensile bond strengths, surpassing 7 MPa at 28 days with a corresponding flexural bond strength of up to 12 MPa, ensuring adequate elastic compatibility with old concrete. In terms of improving the flexural strength and bonding strength of MKPC mortar as a repair material, nickel-iron slag and steel fibers have been utilized in the mix design in (Zhang et al., 2021). MKPC mortar showed good bonding strength to old substrate concrete slabs, and improved volume stability in a field application performed using MKPC mortar for crack repairs (Kim et al., 2020).
At present, there are few (if any) detailed investigations into the underlying causes of the alkali leaching effect of MKPC, releasing K, that could potentially cause alkali-silica reactions in repaired concretes. Conversely, the alkaline resistance of MKPC has been reported to be weak due to mass loss and brucite formation, although this is improved by the addition of silica-rich fillers into the formulation (Yue et al., 2015). A thermodynamic model based on alkali hydroxide (KOH and NaOH) and Ca(OH)2 addition to struvite-K, showed that this can lead to its partial destabilization and precipitation of brucite and hazenite (Mg2KNa(PO4)2·14H2O), associated with shrinkage (Xu et al., 2023). However, the addition of wollastonite to struvite-K led to the formation of M-S-H phases and hydroxyapatite and resulted in late precipitation of brucite at higher pH, preventing cracking.
3 Evaluating the suitability of MKPC as a repair material
Based on the review on properties, it is noted that MKPC repair materials possess unique advantages and also challenges when compared to other repair materials, particularly rapid-hardening cement-based repair materials. A comparative summary of these advantages and disadvantages of MKPC compared to other repair materials is provided in Table 1 below. In addition to the comparisons related to engineering properties, some of the other considerations such as materials availability and cost are also put forward in Table 1. While limited sources are available on detailed cost implications of using MKPC, it is recommended to conduct a comprehensive cost analysis to compare MKPC with other repair materials to identify the relevant applications where utilizing MKPC-based repair materials can be cost-effective.
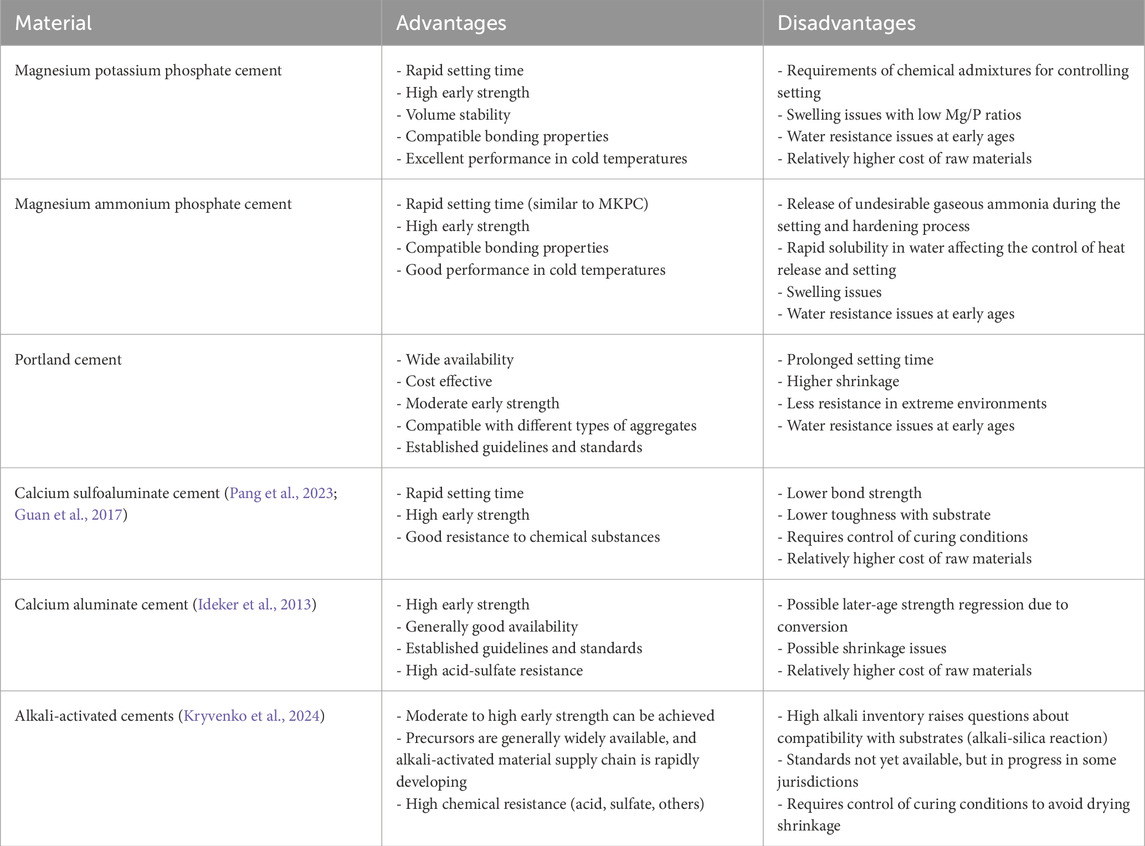
Table 1. Comparative analysis of advantages and disadvantages of MKPC rapid repair materials with other commonly used rapid hardening repair materials.
In engineering applications, the challenges of using MKPCs, state-of-the-art recommendations, and commentary on standard specifications are detailed in the below sections.
3.1 Challenges of MKPC in engineering applications
There are several concerns over the properties of MKPCs when it comes to practical applications, as listed below.
• Rapid setting time: the exothermic reaction between magnesia and acid phosphate is rapid and typically leads to setting times of less than 3 min at standard ambient temperatures if a retarder is not used. Such a rapid setting time is not feasible in field applications. The high cost and potentially hazardous classification of borate retarders may limit their use in MKPCs in construction applications. Conversely, the ability of the cement to set rapidly under very cold conditions may be advantageous.
• The strength loss: strength loss in magnesium phosphate-based materials that are stored in water for a very long time is another concern. Thus, it is recommended that the repair of structures that a frequently exposed to water should be done with proper care.
• Lack of available test data on elastic properties: in the design of repair materials, it is required to have extensive test data to evaluate the elastic properties, under both compression and tension; more research is needed in this area.
• Possible filler materials: filler materials need to be further assessed, to decrease cost and improve strength properties of MKPC systems.
• Swelling of MKPC samples: swelling has been observed in several studies, as described in Section 2.6, especially with MKPC pastes with low Mg/P molar ratios. This may cause cracking of the samples and, therefore, is a critical concern when it comes to large-scale implementation and utilization of this material at an industrial scale. The reasons for swelling and cracking are not yet well understood.
In addition to the existing challenges related to the engineering applications of MKPC, the practical implications of its usage when it comes to availability and its environmental impacts should be carefully considered. On one hand, the production of reactive magnesia (rMgO or light-burned MgO) is considered to emit less CO2 than PC, mainly due to lower thermal conversion and certain capacity to absorb atmospheric CO2 during its lifetime, although in a lower amount than that required for its manufacture (Onyekwena et al., 2023). The rMgO, is obtained by calcination of Mg-carbonates at low temperatures, in the range 700ºC–1000°C, saving energy associated with the lower temperatures, compared to the conversion of CaCO3 to PC (1450°C), and decreasing the overall environmental burdens associated with its production (16.4% lower than quicklime production and 41.6% lower than PC); although these calculations do not apply to hard-burned (1,000ºC–1,500°C) and dead-burned (1,500ºC–2000°C) MgO (Ruan et al., 2020). On the other hand, in some studies that mainly considered the life cycle assessment of MgO production, reported that MgO releases more CO2 than the same amount of cement (Barcelo et al., 2014; Ruan and Unluer, 2016). It is reported that the main environmental impact of MKPC comes from the production stage of MgO and phosphate. However, it is important to note that the MKPC based materials possess great advantages as rapid repair materials and coatings and can reduce the carbon emissions by 12%–98% compared to other repair materials (Shen et al., 2024).
Moreover, the resources utilized in producing MKPC are somewhat limited for its wider application in the construction industry. Firstly, Mg and P are critical elements worldwide (Hayes and McCullough, 2018). Secondly, MgO reserves are limited (most MgO comes from Russia and China), and deposits are distributed heterogeneously (e.g., not many deposits are found in Europe, except some in Greece and Spain) (Mineral commodity summaries 2022, 2022). In addition, KH2PO4 or other phosphates are produced and distributed as fertilizers and therefore have more value for other purposes. These environmental concerns and material limitations may cause MKPC to be restricted to use in certain niches when it comes to engineering applications. On the positive aspects, the contribution of MPCs to the global warming potential can be counteracted by continuing to utilize lower calcination temperatures, and the potential of MgO to carbonate thereby sequestering CO2 (Galvez-Martos et al., 2016; Mo and Panesar, 2013). In addition, the ability to incorporate industrial byproducts as aggregates or fillers further contributes reduced impact of MPCs on the global warming potential (Sinka et al., 2018). Therefore, it is vital to perform a comprehensive life cycle assessment as a possible future extension to this study, that compares MPCs with traditional repair materials integrating the aspects of raw material sourcing, carbon sequestration potential, and the incorporation of sustainable fillers.
3.2 State-of-the-art recommendations on MKPCs
There are some important experimental outcomes and recommendations in the available literature regarding optimizing the MKPC mix designs in practice. Such main outcomes and recommendations are listed below.
• Blending of different qualities of MgO may be a good idea to produce a more economical product with adequate characteristics (Qiao et al., 2009). Low reactive magnesia (dead-burned MgO with low surface area) is generally better. However, this requires achieving higher calcination temperatures, thus increasing costs and CO2 emissions.
• In terms of setting time, controlling water to binder ratio, Mg/P ratio, and casting temperature is vital for obtaining the required setting times depending on the applications and the environmental conditions.
• Increasing the borax dose remarkably retards the setting times of MKPCs; however, it negatively affects the strength at early ages. Therefore, an optimum borax amount must be utilised in a rapid repair material to achieve a balance between a practical setting time and reasonably high early strength (Qiao et al., 2009), considering also the likely application temperature and balancing the retarder dose accordingly. Alternative retarders should be more intensively investigated as there are concerns in research and society about the reproductive toxicity of borax (Ma et al., 2021).
• In terms of strength, having a relatively lower water to binder ratio that reduces porosity and an optimum Mg/P ratio that leads to better cohesion to the microstructure are important design considerations to have the desired strength development.
• The use of an optimum struvite-K/space ratio for designing the MKPC-based repair materials has been proposed in (Ma and Xu, 2017). The struvite-K/space ratio was defined similarly to the gel/space ratio in cement-based materials, considering the ratio between the volume of struvite-K and the sum of the volumes of the reacted magnesia and KDP and the original capillary pores. The struvite-K is used as the basis of this calculation since it is the final dominant reaction product in MKPCs. Compressive strength was observed to be approximately proportional to the third power of the struvite-K/space ratio (Ma and Xu, 2017).
• Typically Mg/P ratios higher than four are frequently used for MKPCs focusing on infrastructural applications. High-strength MKPC-based composites used as repair materials have Mg/P ratios ranging between four and 8 (Qiao et al., 2010; Lee et al., 2017; Ma and Xu, 2017; Xu et al., 2015).
• A majority of the applications of MKPC as repair materials use mineral admixtures such as fly ash, ground granulated blast furnace slags, metakaolin, wollastonite, and others (Le Rouzic et al., 2017a; Gardner et al., 2015b). However, more work in determining and defining interactions between MKPC and these fillers, which are potentially partly reactive, is needed. These fillers also reduce the expansion that is often seen in MKPCs (Tan et al., 2016; Zheng et al., 2016; Gardner et al., 2015a; Xu et al., 2021; Chen et al., 2011). More importantly, the inclusion of mineral admixtures is reported to effectively reduce the overall cost MKPC-based materials (Zhang et al., 2022).
• In terms of durability aspects, blending mineral admixtures such as limestone powder and silica fume can help form a denser structure that can reduce the external deterioration of the applications. For optimum performance in structural applications, it is recommended to have slightly prolonged curing processes at early ages to enhance the water resistance of the MPC-based materials.
• Efflorescence is a major concern in upscaling MKPCs as repair materials. This can be suppressed by the use of high Mg/P molar ratios and relatively low water to binder ratios (Le Rouzic et al., 2017a; Xu et al., 2019). Using mineral admixtures such as fly ash, wollastonite, or metakaolin can also be beneficial in terms of reducing efflorescence (Xu et al., 2021; De Campos et al., 2021; Xu et al., 2017) in optimized mix designs. A study also reported that the presence of aluminium sulfate can inhibit efflorescence due to the increased consumption of potassium and phosphate ions (Xu et al., 2022b).
3.3 Commentary on standard specifications of MKPC-based repair materials
Standard specifications for rapid hardening cement-based materials used in concrete repairs are well established by international standardization agencies such as ASTM (ASTM, 2020; ASTM, 2019) and CEN (BSI, 2005). The performance requirements have been set for such materials mainly considering the structural requirements, such as compressive strength and bond strength, and length change; casting requirements such as consistency of concrete or mortar; and durability requirements such as scaling resistance (ASTM, 2020). MKPC can meet the requirements of many of these performance-based specifications and thus be utilized. Although MKPC is not yet specifically standardized in its own right, its properties and performance characteristics have shown MKPC to be well within most of the guidelines to serve as a structural repair material. As implied by the discussion in section 2 of this paper, MKPC materials fulfil compressive strength, drying shrinkage, and final setting time requirements in the standard physical requirement criteria mentioned in ASTM standards (ASTM, 2019). However, there is limited data to indicate the performance of MKPC in terms of the optional requirements such as heat of hydration and expansion in water. Some other main types of performance requirements mentioned in the EN standard (BSI, 2005) that require proper evaluation for MKPC-based repair materials include elastic modulus and water permeability.
On a practical basis, it is important to note that guidelines should be developed for MKPC in the field addressing the best practices such as mixing, placement, and curing conditions to ensure successful implementation. Based on the review, during the mix design, it is crucial to utilize an optimized water to binder ratio and Mg/P ratio depending on the application. Retarders, such as borax, should be used cautiously to extend the working time, but their dosage must be optimized to avoid compromising early strength. Alternatively, more research is required to find chemical admixtures that are safer for the users. In terms of placement, typically the MKPC repair materials should be applied quickly to the prepared substrate, ensuring a clean and roughened surface to promote good bonding. Placement should be done quickly after mixing, especially in warm environments, to avoid premature setting. It is crucial to design guidelines for curing processes for MKPC, particularly in moist or humid environments, where early exposure to water may cause porosity or strength reduction. Natural curing in air can be a good recommendation before exposure to water. While these recommendations provide a strong basis for field applications, it is essential to perform more research and establish formal guidelines to ensure consistent and successful implementation of MKPC in practical construction projects.
4 Summary and future perspectives of MKPC-based repair materials
Rapid repair materials with improved performance are highly sought after in the construction industry to effectively restore the quality of existing infrastructure within a given (usually short) timeframe. As such, MKPC has great potential owing to its excellent mechanical properties and dimensional stability. It is important to overcome several issues related to its engineering applications, such as rapid setting time, strength loss under water, lack of test data on elastic properties, and swelling/cracking of specimens, if this type of material is to be used at an industrial scale. In addition to the existing challenges related to the engineering applications of MKPC, the practical implications of its usage when it comes to availability and its environmental impacts should be carefully considered. There are several methods for optimizing MKPC mixes with varied formulations that provide a dense microstructure, although they should be holistically understood in terms of in-depth studies on reaction kinetics and microstructure. Although there are encouraging test data and field observations in terms of the long-term durability aspects of MKPC, it is evident from this study that generating extensive field data is essentially important via collaborative studies and/or industry partnerships to enhance the robustness of the durability aspects.
MKPC-based repair materials have shown positive signs in their applications in the construction industry. As discussed in this paper, MKPC has been successfully utilized for repairing damaged runways, pavements, and bridges since the 1980s, showcasing the advantages this material possesses, especially in terms of quick setting time, rapid developments of mechanical properties, and durability aspects. Moreover, MKPC has been used as highway projects in regions where extremely cold temperatures persist and have shown benefits in workability and durable performances in such extreme weather conditions. Recently, this material has been increasingly used in infrastructure rehabilitation and waste solidification and has been showing advantageous performances in these applications.
MKPC has shown promising signs of future engineering applications as well. Mineral admixtures such as fly ash and ground granulated blast furnace slag have been used in MKPC mixes to promote performance and minimize the carbon footprint. MKPCs have also been evaluated for their ability to function as a 3D printing material. Therefore, in recent years, MKPCs have not only gained attraction due to improved performance, but also have been a driving factor in the future of eco-friendly cements.
Author contributions
AD: Conceptualization, Investigation, Methodology, Visualization, Writing–original draft, Writing–review and editing. RF: Investigation, Methodology, Writing–original draft, Writing–review and editing. JP: Methodology, Supervision, Writing–review and editing.
Funding
The author(s) declare that no financial support was received for the research, authorship, and/or publication of this article. Open access funding by PSI - Paul Scherrer Institute.
Acknowledgments
Raúl Fernández acknowledges the Spanish Ministry of Science, Innovation and Universities and the Autonomous University of Madrid for funding for his research stay at the University of Sheffield though the Recovery, Transformation and Resilience Plan with grant number CA2/RSUE/2021-00871.
Conflict of interest
The authors declare that the research was conducted in the absence of any commercial or financial relationships that could be construed as a potential conflict of interest.
The author(s) declared that they were an editorial board member of Frontiers, at the time of submission. This had no impact on the peer review process and the final decision.
Publisher’s note
All claims expressed in this article are solely those of the authors and do not necessarily represent those of their affiliated organizations, or those of the publisher, the editors and the reviewers. Any product that may be evaluated in this article, or claim that may be made by its manufacturer, is not guaranteed or endorsed by the publisher.
Abbreviations
struvite, MgNH4PO4·6H2O; struvite-K, MgKPO4·6H2O; magnesia/periclase, MgO; potassium dihydrogen phosphate/KDP, KH2PO4; phosphorrösslerite, MgHPO4⋅7H2O.
References
Abdelrazig, B. E. I., Sharp, J. H., and El-Jazairi, B. (1988). The chemical composition of mortars made from magnesia-phosphate cement. Cem. Concr. Res. 18, 415–425. doi:10.1016/0008-8846(88)90075-0
Abdelrazig, B. E. I., Sharp, J. H., and El-Jazairi, B. (1989). The microstructure and mechanical properties of mortars made from magnesia-phosphate cement. Cem. Concr. Res. 19, 247–258. doi:10.1016/0008-8846(89)90089-6
ASTM (2019). C1600/C1600M-19: standard specification for rapid hardening hydraulic cement. West Conshohocken, PA: ASTM International.
ASTM (2020). C928/C928M-20a: standard specification for packaged, dry, rapid-hardening cementitious materials for concrete repairs. ASTM International.
Barcelo, L., Kline, J., Walenta, G., and Gartner, E. (2014). Cement and carbon emissions. Mater. Struct. 47, 1055–1065. doi:10.1617/s11527-013-0114-5
Barde, A. D., Parameswaran, S., Chariton, T., Weiss, W. J., Cohen, M. D., and Newbolds, S. A. (2006). Evaluation of rapid setting cement-based materials for patching and repair. Indiana Department of Transportation and Purdue University.
Birchal, V. S. S., Rocha, S. D. F., and Ciminelli, V. S. T. (2000). The effect of magnesite calcination conditions on magnesia hydration. Miner. Eng. 13, 1629–1633. doi:10.1016/s0892-6875(00)00146-1
Bocanegra-Bernal, M. H. (2008). Microstructural evolution during sintering in MgO powders precipitated from sea water under induced agglomeration conditions. Powder Technol. 186, 267–272. doi:10.1016/j.powtec.2007.12.015
Brabston, W. N. (1984) “Bomb damage repair: precast slab design,” in Report ESL-TR-84-21, Air Force Engineering and Services Center: Tyndall Air Force Base. Florida.
BSI, EN 1504-1:2005 Products and systems for the protection and repair of concrete structures. Definitions, requirements, quality control and evaluation of conformity, British Standards Institution, 2005.
Burris, L., Kurtis, K., and Morton, T.(2015). Tom Morton, Novel alternative cementitious materials for development of the next generation of sustainable transportation infrastructure, TechBrief. Georgia Institute of Technology.
Cau Dit Coumes, C., Rousselet, A., Xu, B., Mercier, C. A., and Gauffinet, S. (2021). Investigation of aluminum nitrate as a set retarder of magnesium potassium phosphate cement: mechanisms involved in diluted suspension. Cem. Concr. Res. 150, 106608. doi:10.1016/j.cemconres.2021.106608
Chau, C. K., Qiao, F., and Li, Z. (2011). Microstructure of magnesium potassium phosphate cement. Constr. Build. Mater. 25, 2911–2917. doi:10.1016/j.conbuildmat.2010.12.035
Chau, C. K., Qiao, F., and Li, Z. (2012). Potentiometric study of the formation of magnesium potassium phosphate hexahydrate. J. Mater. Civ. Eng. 24, 586–591. doi:10.1061/(asce)mt.1943-5533.0000410
Chen, B., Oderji, S. Y., Chandan, S., and Fan, S. (2017). Feasibility of Magnesium Phosphate Cement (MPC) as a repair material for ballastless track slab. Constr. Build. Mater. 154, 270–274. doi:10.1016/j.conbuildmat.2017.07.207
Chen, B., Wu, Z., and Wu, X. P. (2011). Experimental research on the properties of modified MPC. J. Wuhan Univ. Technol. 33, 29–34.
Chong, L., Yang, J., Xu, Z. Z., and Xu, X. (2019). Freezing and thawing resistance of MKPC paste under different corrosion solutions. Constr. Build. Mater. 212, 663–674. doi:10.1016/j.conbuildmat.2019.03.269
Covill, A., Hyatt, N. C., Hill, J., and Collier, N. C. (2011). Development of magnesium phosphate cements for encapsulation of radioactive waste. Adv. Appl. Ceram. 110, 151–156. doi:10.1179/1743676110y.0000000008
Czarnecki, L., Geryło, R., and Kuczyński, K. (2020). Concrete repair durability. Materials 13, 4535. doi:10.3390/ma13204535
De Campos, M., Davy, C. A., Djelal, N., Rivenet, M., and Garcia, J. (2021). Development of a stoichiometric magnesium potassium phosphate cement (MKPC) for the immobilization of powdered minerals. Cem. Concr. Res. 142, 106346. doi:10.1016/j.cemconres.2020.106346
Dieguez, M., Ruiz, A. I., Cuevas, J., Alonso, M. C., García-Lodeiro, I., and Fernández, R. (2023). Evaluation of fillers for magnesium potassium phosphate cement (MKPC) for the encapsulation of low and intermediate level metallic radioactive wastes. Materials 16, 679. doi:10.3390/ma16020679
Ding, Z., Dong, B., Xing, F., Han, N., and Li, Z. (2012). Cementing mechanism of potassium phosphate based magnesium phosphate cement. Ceram. Int. 38, 6281–6288. doi:10.1016/j.ceramint.2012.04.083
Ding, Z., and Li, Z. (2005). Effect of aggregates and water contents on the properties of magnesium phospho-silicate cement. Cem. Concr. Compos. 27, 11–18. doi:10.1016/j.cemconcomp.2004.03.003
Ding, Z., Li, Z., and Xing, F. (2005). Chemical durability investigation of magnesium phosphosilicate cement. Key Eng. Mater. 302, 275–281. doi:10.4028/0-87849-983-0.275
Dong, J., Zheng, W., Chang, C., Wen, J., and Xiao, X. (2023). Function and effect of borax on magnesium phosphate cement prepared by magnesium slag after salt lake lithium extraction. Constr. Build. Mater. 366, 130280. doi:10.1016/j.conbuildmat.2022.130280
Fan, S., and Chen, B. (2014). Experimental study of phosphate salts influencing properties of magnesium phosphate cement. Constr. Build. Mater. 65, 480–486. doi:10.1016/j.conbuildmat.2014.05.021
Feldman, R. F., and Beaudoin, J. J. (1991). Pretreatment of hardened hydrated cement pastes for mercury intrusion measurements. Cem. Concr. Res. 21, 297–308. doi:10.1016/0008-8846(91)90011-6
Formosa, J., Chimenos, J. M., Lacasta, A. M., and Niubó, M. (2012). Interaction between low-grade magnesium oxide and boric acid in chemically bonded phosphate ceramics formulation. Ceram. Int. 38, 2483–2493. doi:10.1016/j.ceramint.2011.11.017
Fu, Y., Cao, X. A., and Li, Z. (2016). Printability of magnesium potassium phosphate cement with different mixing proportion for repairing concrete structures in severe environment. Key Eng. Mater. 711, 989–995. doi:10.4028/www.scientific.net/kem.711.989
Galvez-Martos, J. L., Morrison, J., Jauffret, G., Elsarrag, E., AlHorr, Y., Imbabi, M. S., et al. (2016). Environmental assessment of aqueous alkaline absorption of carbon dioxide and its use to produce a construction material. Resour. Conservation Recycl. 107, 129–141. doi:10.1016/j.resconrec.2015.12.008
Gardner, L. J. (2016). Assessment of magnesium potassium phosphate cements for radioactive waste encapsulation, Ph.D. thesis, Department of Materials Science and Engineering. University of Sheffield.
Gardner, L. J., Bernal, S. A., Walling, S. A., Corkhill, C. L., Provis, J. L., and Hyatt, N. C. (2015b). Characterisation of magnesium potassium phosphate cements blended with fly ash and ground granulated blast furnace slag. Cem. Concr. Res. 74, 78–87. doi:10.1016/j.cemconres.2015.01.015
Gardner, L. J., Lejeune, V., Corkhill, C. L., Bernal, S. A., Provis, J. L., Stennett, M. C., et al. (2015a). Evolution of phase assemblage of blended magnesium potassium phosphate cement binders at 200° and 1000°C. Adv. Appl. Ceram. 114, 386–392. doi:10.1179/1743676115y.0000000064
Gardner, L. J., Walling, S. A., Lawson, S. M., Sun, S., Bernal, S. A., Corkhill, C. L., et al. (2021). Characterization of and structural insight into struvite-K, MgKPO4·6H2O, an analogue of struvite. Inorg. Chem. 60, 195–205. doi:10.1021/acs.inorgchem.0c02802
Gelli, R., Tonelli, M., Martini, F., Calucci, L., Borsacchi, S., and Ridi, F. (2022). Effect of borax on the hydration and setting of magnesium phosphate cements. Constr. Build. Mater. 348, 128686. doi:10.1016/j.conbuildmat.2022.128686
Graeser, S., Postl, W., Bojar, H. P., Berlepsch, P., Armbruster, T., Raber, T., et al. (2008). Struvite-(K), KMgPO46H2O, the potassium equivalent of struvite a new mineral. Eur. J. Mineralogy 20, 629–633. doi:10.1127/0935-1221/2008/0020-1810
Guan, Y., Gao, Y., Sun, R., Won, M. C., and Ge, Z. (2017). Experimental study and field application of calcium sulfoaluminate cement for rapid repair of concrete pavements. Front. Struct. Civ. Eng. 11, 338–345. doi:10.1007/s11709-017-0411-0
Haque, M. A., and Chen, B. (2019). Research progresses on magnesium phosphate cement: a review. Constr. Build. Mater. 211, 885–898. doi:10.1016/j.conbuildmat.2019.03.304
Hayes, S. M., and McCullough, E. A. (2018). Critical minerals: a review of elemental trends in comprehensive criticality studies. Resour. Policy 59, 192–199. doi:10.1016/j.resourpol.2018.06.015
Hou, D., Yan, H., Zhang, J., Wang, P., and Li, Z. (2016). Experimental and computational investigation of magnesium phosphate cement mortar. Constr. Build. Mater. 112, 331–342. doi:10.1016/j.conbuildmat.2016.02.200
Huang, X., Liu, G., Zheng, Y., and Luo, H. (2023). The performance of magnesium phosphate cement in negative temperature environment: a state-of-the-art review. J. Build. Eng. 76, 107278. doi:10.1016/j.jobe.2023.107278
Ideker, J. H., Gosselin, C., and Barorak, R. (2013). An alternative repair material: basics and practical testing of calcium aluminate cement concrete. Concr. Int. 35, 33–37.
Iyengar, S. R., and Al-Tabbaa, A. (2007). Developmental study of a low-pH magnesium phosphate cement for environmental applications. Environ. Technol. 28, 1387–1401. doi:10.1080/09593332808618899
Jiang, H. Y., and Zhang, L. M. (2001) Investigation of phosphate cement-based binder with super high early strength for repair of concrete, 16. J. Wuhan U. Sci. Technol., Mater. Sci. Ed.: Journal Wuhan University of Technology, 46–48.
Jiang, W., Huang, Y., and Sha, A. (2018). A review of eco-friendly functional road materials. Constr. Build. Mater. 191, 1082–1092. doi:10.1016/j.conbuildmat.2018.10.082
Jiang, Z., Qian, C., and Chen, Q. (2017). Experimental investigation on the volume stability of magnesium phosphate cement with different types of mineral admixtures. Constr. Build. Mater. 157, 10–17. Report PNNL-20751, Pacific Northwest National Laboratory, Richland WA.doi:10.1016/j.conbuildmat.2017.09.037
Josephson, G. B., Westsik, J. H., Pires, R. P., Bickford, J., and Foote, M. W. (2011). Engineering-scale demonstration of DuraLith and Ceramicrete waste forms.
Khalil, A., Wang, X., and Celik, K. (2020). 3D printable magnesium oxide concrete: towards sustainable modern architecture. Addit. Manuf. 33, 101145. doi:10.1016/j.addma.2020.101145
Kim, H., Han, D., Kim, K., and Romero, P. (2020). Performance assessment of repair material for deteriorated concrete slabs using chemically bonded cement. Constr. Build. Mater. 237, 117468. doi:10.1016/j.conbuildmat.2019.117468
Kryvenko, P., Rudenko, I., Sikora, P., Sanytsky, M., Konstantynovskyi, O., and Kropyvnytska, T. (2024). Alkali-activated cements as sustainable materials for repairing building construction: a review. J. Build. Eng. 90, 109399. doi:10.1016/j.jobe.2024.109399
Lahalle, H., Cau Dit Coumes, C., Mercier, C., Lambertin, D., Cannes, C., Delpech, S., et al. (2018). Influence of the w/c ratio on the hydration process of a magnesium phosphate cement and on its retardation by boric acid. Cem. Concr. Res. 109, 159–174. doi:10.1016/j.cemconres.2018.04.010
Lahalle, H., Cau Dit Coumes, C., Mesbah, A., Lambertin, D., Cannes, C., Delpech, S., et al. (2016). Investigation of magnesium phosphate cement hydration in diluted suspension and its retardation by boric acid. Cem. Concr. Res. 87, 77–86. doi:10.1016/j.cemconres.2016.04.010
Lahalle, H., Patapy, C., Glid, M., Renaudin, G., and Cyr, M. (2019). Microstructural evolution/durability of magnesium phosphate cement paste over time in neutral and basic environments. Cem. Concr. Res. 122, 42–58. doi:10.1016/j.cemconres.2019.04.011
Lee, K.-H., Yoon, H.-S., and Yang, K.-H. (2017). Tests on magnesium potassium phosphate composite mortars with different water-to-binder ratios and molar ratios of magnesium-to-phosphate. Constr. Build. Mater. 146, 303–311. doi:10.1016/j.conbuildmat.2017.04.123
Lei, F., Zhen-ya, Z., Xiao-dong, W., Chao, X., and Dong-yuan, H. (2018). Long-term behaviors of phosphate-based rapid repairing material for concrete shafts in coal mines. J. Appl. Biomate. Funct. Mater. 16, 171–177. doi:10.1177/2280800018766998
Le Rouzic, M., Chaussadent, T., Platret, G., and Stefan, L. (2017b). Mechanisms of k-struvite formation in magnesium phosphate cements. Cem. Concr. Res. 91, 117–122. doi:10.1016/j.cemconres.2016.11.008
Le Rouzic, M., Chaussadent, T., Stefan, L., and Saillio, M. (2017a). On the influence of Mg/P ratio on the properties and durability of magnesium potassium phosphate cement pastes. Cem. Concr. Res. 96, 27–41. doi:10.1016/j.cemconres.2017.02.033
Ley, T. (2022). Synthesis of rapid setting repair materials, InTrans Project 15-532, Institute for Transportation. Iowa State University.
Li, D. X., Li, P. X., and Feng, C. H. (2009). Research on water resistance of magnesium phosphate cement. J. Build. Mater. 12, 505–510.
Li, G., Zhang, J., and Zhang, G. (2017a). Mechanical property and water stability of the novel CSA-MKPC blended system. Constr. Build. Mater. 136, 99–107. doi:10.1016/j.conbuildmat.2017.01.036
Li, J., Zhang, W., and Cao, Y. (2014b). Laboratory evaluation of magnesium phosphate cement paste and mortar for rapid repair of cement concrete pavement. Constr. Build. Mater. 58, 122–128. doi:10.1016/j.conbuildmat.2014.02.015
Li, J., Zhang, W., and Monteiro, P. J. M. (2020). Mechanical properties of struvite-K: a high-pressure X-ray diffraction study. Cem. Concr. Res. 136, 106171. doi:10.1016/j.cemconres.2020.106171
Li, Y., Bai, W., and Shi, T. (2017b). A study of the bonding performance of magnesium phosphate cement on mortar and concrete. Constr. Build. Mater. 142, 459–468. doi:10.1016/j.conbuildmat.2017.03.090
Li, Y., and Chen, B. (2013). Factors that affect the properties of magnesium phosphate cement. Constr. Build. Mater. 47, 977–983. doi:10.1016/j.conbuildmat.2013.05.103
Li, Y., Shi, T., Chen, B., and Li, Y. (2015b). Performance of magnesium phosphate cement at elevated temperatures. Constr. Build. Mater. 91, 126–132. doi:10.1016/j.conbuildmat.2015.05.055
Li, Y., Shi, T., Li, Y., Bai, W., and Lin, H. (2019). Damage of magnesium potassium phosphate cement under dry and wet cycles and sulfate attack. Constr. Build. Mater. 210, 111–117. doi:10.1016/j.conbuildmat.2019.03.213
Li, Y., Sun, J., and Chen, B. (2014a). Experimental study of magnesia and M/P ratio influencing properties of magnesium phosphate cement. Constr. Build. Mater. 65, 177–183. doi:10.1016/j.conbuildmat.2014.04.136
Li, Y., Sun, J., Li, J., and Shi, T. (2015a). Effects of fly ash, retarder and calcination of magnesia on properties of magnesia–phosphate cement. Adv. Cem. Res. 27, 373–380. doi:10.1680/adcr.14.00029
Limes, R. W., and Russell, R. O. (1977). Production of fast-setting bonded aggregate structures. U.S. Patent 4,059,455.
Liu, R., Fang, B., Zhang, G., Guo, J., and Yang, Y. (2022). Investigation of sodium alginate as a candidate retarder of magnesium phosphate cement: hydration properties and its retarding mechanism. Ceram. Int. 48, 30846–30852. doi:10.1016/j.ceramint.2022.07.038
Lothenbach, B., Xu, B., and Winnefeld, F. (2019). Thermodynamic data for magnesium (potassium) phosphates. Appl. Geochem. 111, 104450. doi:10.1016/j.apgeochem.2019.104450
Lu, Z., Hou, D., Ma, H., Fan, T., and Li, Z. (2016). Effects of graphene oxide on the properties and microstructures of the magnesium potassium phosphate cement paste. Constr. Build. Mater. 119, 107–112. doi:10.1016/j.conbuildmat.2016.05.060
Ma, C., Liu, Y., Zhou, H., He, F., Li, Y., Ren, W., et al. (2021). Influencing mechanism of sodium tripolyphosphate on the rheological properties of magnesium phosphate cement. Powder Technol. 387, 406–414. doi:10.1016/j.powtec.2021.04.052
Ma, H., and Xu, B. (2017). Potential to design magnesium potassium phosphate cement paste based on an optimal magnesia-to-phosphate ratio. Mater. and Des. 118, 81–88. doi:10.1016/j.matdes.2017.01.012
Ma, H., Xu, B., and Li, Z. (2014a). Magnesium potassium phosphate cement paste: degree of reaction, porosity and pore structure. Cem. Concr. Res. 65, 96–104. doi:10.1016/j.cemconres.2014.07.012
Ma, H., Xu, B., Liu, J., Pei, H., and Li, Z. (2014b). Effects of water content, magnesia-to-phosphate molar ratio and age on pore structure, strength and permeability of magnesium potassium phosphate cement paste. Mater. and Des. 64, 497–502. doi:10.1016/j.matdes.2014.07.073
Mácová, P., and Viani, A. (2017). Investigation of setting reaction in magnesium potassium phosphate ceramics with time resolved infrared spectroscopy. Mater. Lett. 205, 62–66. doi:10.1016/j.matlet.2017.06.063
Manawadu, A., Qiao, P., and Wen, H. (2023). Characterization of substrate-to-overlay interface bond in concrete repairs: a review. Constr. Build. Mater. 373, 130828. doi:10.1016/j.conbuildmat.2023.130828
Mazari, M., Aval, S. F., and Rodriguez-Nikl, T. (2020). Evaluating the use of recycled and sustainable materials in self-consolidating concrete for underground infrastructure applications (California State University, I. University Transportation Center for Underground Transportation).
Mo, L., and Panesar, D. K. (2013). Accelerated carbonation - a potential approach to sequester CO2 in cement paste containing slag and reactive MgO. Cem. Concr. Compos. 43, 69–77. doi:10.1016/j.cemconcomp.2013.07.001
Onyekwena, C. C., Xue, Q., Li, Q., Umeobi, H. I., Ghaffar, A., and Fasihnikoutalab, M. H. (2023). Advances in the carbonation of MgO-based binder and CO2 utilization in the construction industry. Clean Technol. Environ. Policy 25, 1763–1782. doi:10.1007/s10098-023-02482-7
Paceagiu, J., and Georgescu, M. (2008). The influence of curing conditions on the physical and mechanical properties of magnesia phosphate cements. Rev. Chim. 59, 135–139. doi:10.37358/rc.08.2.1720
Pang, B., Yang, C., Wang, P., Tian, L., Mei, B., and Song, X. (2023). Cement-based ductile rapid repair material modified with self-emulsifying waterborne epoxy. J. Build. Eng. 79, 107864. doi:10.1016/j.jobe.2023.107864
Pernal, K., Kołodziejczyk, Ł., Jiménez Riobóo, R. J., and Prywer, J. (2023). Experimental–computational approach to investigate elastic properties of struvite. J. Chem. Phys. 158, 244501. doi:10.1063/5.0155040
Pioneering precast in Alaska (1993). The 7-month replacement of 18 bridges on the storied Dalton Highway, Highways for LIFE. Washington, DC: Federal Highway Administration.
Prosen, E. M., Dental investment or refractory material, Patent number: US2152152A, United States, (1939).
Pyo, J.-Y., Um, W., and Heo, J. (2021). Magnesium potassium phosphate cements to immobilize radioactive concrete wastes generated by decommissioning of nuclear power plants. Nucl. Eng. Technol. 53, 2261–2267. doi:10.1016/j.net.2021.01.005
Qiao, F. (2010). Reaction mechanisms of magnesium potassium phosphate cement and its application. Hong Kong University of Science and Technology, 226.
Qiao, F., Chau, C. K., and Li, Z. (2009). Setting and strength development of magnesium phosphate cement paste. Adv. Cem. Res. 21, 175–180. doi:10.1680/adcr.9.00003
Qiao, F., Chau, C. K., and Li, Z. (2010). Property evaluation of magnesium phosphate cement mortar as patch repair material. Constr. Build. Mater. 24, 695–700. doi:10.1016/j.conbuildmat.2009.10.039
Qiao, F., Chau, C. K., and Li, Z. (2012). Calorimetric study of magnesium potassium phosphate cement. Mater. Struct. 45, 447–456. doi:10.1617/s11527-011-9776-z
Qin, J., Qian, J., You, C., Fan, Y., Li, Z., and Wang, H. (2018). Bond behavior and interfacial micro-characteristics of magnesium phosphate cement onto old concrete substrate. Constr. Build. Mater. 167, 166–176. doi:10.1016/j.conbuildmat.2018.02.018
Ruan, S., Liang, S., Kastiukas, G., Zhu, W., and Zhou, X. (2020). Solidification of waste excavation clay using reactive magnesia, quicklime, sodium carbonate and early-age oven curing. Constr. Build. Mater. 258, 120333. doi:10.1016/j.conbuildmat.2020.120333
Ruan, S., and Unluer, C. (2016). Comparative life cycle assessment of reactive MgO and Portland cement production. J. Clean. Prod. 137, 258–273. doi:10.1016/j.jclepro.2016.07.071
Saadoon, T., Gómez-Meijide, B., and Garcia, A. (2019). New predictive methodology for the apparent activation energy and strength of conventional and rapid hardening concretes. Cem. Concr. Res. 115, 264–273. doi:10.1016/j.cemconres.2018.10.020
Sarkar, A. K. (1991). Hydration/dehydration characteristics of struvite and dittmarite pertaining to magnesium ammonium phosphate cement systems. J. Mater. Sci. 26, 2514–2518. doi:10.1007/bf01130204
Scope, C., Vogel, M., and Guenther, E. (2021). Greener, cheaper, or more sustainable: reviewing sustainability assessments of maintenance strategies of concrete structures. Sustain. Prod. Consum. 26, 838–858. doi:10.1016/j.spc.2020.12.022
Seehra, S. S., Gupta, S., and Kumar, S. (1993). Rapid setting magnesium phosphate cement for quick repair of concrete pavements - characterisation and durability aspects. Cem. Concr. Res. 23, 254–266. doi:10.1016/0008-8846(93)90090-v
Shao, Y. X., Gu, Y. P., and Yang, J. M. (2013). Control technology study of early water stability of magnesium potassium phosphate cement. Bull. Chin. Ceram. Soc. 32, 1141–1145.
Shen, X., Wang, X., Li, K., Hu, X., and Shi, C. (2024). Life cycle assessment of magnesium phosphate cement production. J. Clean. Prod. 467, 142981. doi:10.1016/j.jclepro.2024.142981
Shi, C., Yang, J., Yang, N., and Chang, Y. (2014). Effect of waterglass on water stability of potassium magnesium phosphate cement paste. Cem. Concr. Compos. 53, 83–87. doi:10.1016/j.cemconcomp.2014.03.012
Sinclair, G. B., Barton, F. G., and Kennedy, L. J. (1984). Military engineering in the Falkland Islands 1982-83. Proc. Instn. Civ. Engrs. 76, 269–277. doi:10.1680/iicep.1984.1332
Sinka, M., Van den Heede, P., De Belie, N., Bajare, D., Sahmenko, G., and Korjakins, A. (2018). Comparative life cycle assessment of magnesium binders as an alternative for hemp concrete. Resour. Conservation Recycl. 133, 288–299. doi:10.1016/j.resconrec.2018.02.024
Smith, K. G., Fowler, D. W., and Meyer, A. H. (1984). Laboratory and field evaluation of rapid setting materials used for repair of concrete pavements. Austin, Texas: Texas State Department of Highways and Public Transportation. Report FHWA/TX-85/20+311-4.
Soudée, E., and Péra, J. (2000). Mechanism of setting reaction in magnesia-phosphate cements. Cem. Concr. Res. 30, 315–321. doi:10.1016/s0008-8846(99)00254-9
Soudée, E., and Péra, J. (2002). Influence of magnesia surface on the setting time of magnesia–phosphate cement. Cem. Concr. Res. 32, 153–157. doi:10.1016/s0008-8846(01)00647-0
Sugama, T., and Kukacka, L. E. (1983a). Magnesium monophosphate cements derived from diammonium phosphate solutions. Cem. Concr. Res. 13, 407–416. doi:10.1016/0008-8846(83)90041-8
Sugama, T., and Kukacka, L. E. (1983b). Characteristics of magnesium polyphosphate cements derived from ammonium polyphosphate solutions. Cem. Concr. Res. 13, 499–506. doi:10.1016/0008-8846(83)90008-x
Tan, Y., Gardner, L. J., Walkley, B., Hussein, O. H., Ding, H., Sun, S., et al. (2023). Optimization of magnesium potassium phosphate cements using ultrafine fly ash and fly ash. ACS Sustain. Chem. Eng. 11, 3194–3207. doi:10.1021/acssuschemeng.2c04987
Tan, Y., Yu, H., Li, Y., Bi, W., and Yao, X. (2016). The effect of slag on the properties of magnesium potassium phosphate cement. Constr. Build. Mater. 126, 313–320. doi:10.1016/j.conbuildmat.2016.09.041
Viani, A., and Mácová, P. (2018). Polyamorphism and frustrated crystallization in the acid-base reaction of magnesium potassium phosphate cements. CrystEngComm 20, 4600–4613. doi:10.1039/c8ce00670a
Wagh, A. S., Chemically bonded phosphate ceramics- Twenty-first century materials with diverse applications, 2004.
Wagh, A. S., and Jeong, S. Y. (2003). Chemically bonded phosphate ceramics: I, A dissolution model of formation. J. Am. Ceram. Soc. 86, 1838–1844. doi:10.1111/j.1151-2916.2003.tb03569.x
Walling, S. A., and Provis, J. L. (2016). Magnesia-based cements: a journey of 150 years, and cements for the future? Chem. Rev. 116, 4170–4204. doi:10.1021/acs.chemrev.5b00463
Wang, A.-j., Yuan, Z.-l., Zhang, J., Liu, L.-t., Li, J.-m., and Liu, Z. (2013b). Effect of raw material ratios on the compressive strength of magnesium potassium phosphate chemically bonded ceramics. Mater. Sci. Eng. C 33, 5058–5063. doi:10.1016/j.msec.2013.08.031
Wang, A.-j., Zhang, J., Li, J.-m., Ma, A.-b., and Liu, L.-t. (2013a). Effect of liquid-to-solid ratios on the properties of magnesium phosphate chemically bonded ceramics. Mater. Sci. Eng. C 33, 2508–2512. doi:10.1016/j.msec.2013.02.014
Wang, Q., Cong, W., Pei, Z. J., Gao, H., and Kang, R. (2009). Rotary ultrasonic machining of potassium dihydrogen phosphate (KDP) crystal: an experimental investigation on surface roughness. J. Manuf. Process. 11, 66–73. doi:10.1016/j.jmapro.2009.09.001
Wang, Y., Lin, B., He, F., Zhou, J., Chen, C., He, Z., et al. (2023). Understanding hydration process and paste viscosity evolution of magnesium potassium phosphate cement. Cem. Concr. Res. 169, 107177. doi:10.1016/j.cemconres.2023.107177
Wu, Q., Hou, Y., Mei, J., Yang, J., and Gan, T. (2022). Influence of synthetic limestone sand on the frost resistance of magnesium potassium phosphate cement mortar. Materials 15, 6517. doi:10.3390/ma15196517
Xing, F., Ding, Z., and Li, Z.-J. (2011). Study of potassium-based magnesium phosphate cement. Adv. Cem. Res. 23, 81–87. doi:10.1680/adcr.9.00030
Xu, B., Cau dit Coumes, C., Lambertin, D., and Lothenbach, B. (2023). Compressive strength and hydrate assemblages of wollastonite-blended magnesium potassium phosphate cements exposed to different pH conditions. Cem. Concr. Compos. 143, 105255. doi:10.1016/j.cemconcomp.2023.105255
Xu, B., Lothenbach, B., Leemann, A., and Winnefeld, F. (2018a). Reaction mechanism of magnesium potassium phosphate cement with high magnesium-to-phosphate ratio. Cem. Concr. Res. 108, 140–151. doi:10.1016/j.cemconres.2018.03.013
Xu, B., Lothenbach, B., and Li, Z. (2022a). Properties and hydrates of seawater-mixed magnesium potassium phosphate cements with high magnesium-to-phosphate ratio. Cem. Concr. Compos. 134, 104807. doi:10.1016/j.cemconcomp.2022.104807
Xu, B., Lothenbach, B., and Ma, H. (2018b). Properties of fly ash blended magnesium potassium phosphate mortars: effect of the ratio between fly ash and magnesia. Cem. Concr. Compos. 90, 169–177. doi:10.1016/j.cemconcomp.2018.04.002
Xu, B., Lothenbach, B., and Winnefeld, F. (2020). Influence of wollastonite on hydration and properties of magnesium potassium phosphate cements. Cem. Concr. Res. 131, 106012. doi:10.1016/j.cemconres.2020.106012
Xu, B., Ma, H., and Li, Z. (2015). Influence of magnesia-to-phosphate molar ratio on microstructures, mechanical properties and thermal conductivity of magnesium potassium phosphate cement paste with large water-to-solid ratio. Cem. Concr. Res. 68, 1–9. doi:10.1016/j.cemconres.2014.10.019
Xu, B., Ma, H., Shao, H., Li, Z., and Lothenbach, B. (2017). Influence of fly ash on compressive strength and micro-characteristics of magnesium potassium phosphate cement mortars. Cem. Concr. Res. 99, 86–94. doi:10.1016/j.cemconres.2017.05.008
Xu, B., Winnefeld, F., Kaufmann, J., and Lothenbach, B. (2019). Influence of magnesium-to-phosphate ratio and water-to-cement ratio on hydration and properties of magnesium potassium phosphate cements. Cem. Concr. Res. 123, 105781. doi:10.1016/j.cemconres.2019.105781
Xu, B., Winnefeld, F., and Lothenbach, B. (2021). Effect of temperature curing on properties and hydration of wollastonite blended magnesium potassium phosphate cements. Cem. Concr. Res. 142, 106370. doi:10.1016/j.cemconres.2021.106370
Xu, B., Winnefeld, F., Ma, B., Rentsch, D., and Lothenbach, B. (2022b). Influence of aluminum sulfate on properties and hydration of magnesium potassium phosphate cements. Cem. Concr. Res. 156, 106788. doi:10.1016/j.cemconres.2022.106788
Yang, J. M., Shao, Y. X., and Liu, H. (2013). Influences of ratio of acid to base on the properties of magnesium and potassium phosphate cement. J. Build. Mater. 16, 923–929.
Yang, N., Shi, C., Yang, J., and Chang, Y. (2014). Research progresses in magnesium phosphate cement-based materials. J. Mater. Civ. Eng. 26, 04014071. doi:10.1061/(asce)mt.1943-5533.0000971
Yang, Q., Zhang, S., and Wu, X. (2002). Deicer-scaling resistance of phosphate cement-based binder for rapid repair of concrete. Cem. Concr. Res. 32, 165–168. doi:10.1016/s0008-8846(01)00651-2
Yang, Q., Zhu, B., and Wu, X. (2000a). Characteristics and durability test of magnesium phosphate cement-based material for rapid repair of concrete. Mater. Struct. 33, 229–234. doi:10.1007/bf02479332
Yang, Q., Zhu, B., Zhang, S., and Wu, X. (2000b). Properties and applications of magnesia–phosphate cement mortar for rapid repair of concrete. Cem. Concr. Res. 30, 1807–1813. doi:10.1016/s0008-8846(00)00419-1
Yang, Y., Fang, B., Zhang, G., Guo, J., and Liu, R. (2022). Hydration performance of magnesium potassium phosphate cement using sodium alginate as a candidate retarder. Materials 15, 943. doi:10.3390/ma15030943
Yue, L., Tongfei, S., and Jia, S. (2015). Experimental study on the performance of magnesium phosphate cement in alkali. J. Build. Mater. 18.
Zhang, G., Wang, Q., Li, Y., and Zhang, M. (2023a). Microstructure and micromechanical properties of magnesium phosphate cement. Cem. Concr. Res. 172, 107227. doi:10.1016/j.cemconres.2023.107227
Zhang, J., Hu, X., Hong, W., Li, T., Shi, D., and Li, T. (2023b). Experimental research on mechanical properties and microstructure of magnesium phosphate cement-based high-strength concrete. J. Build. Eng. 65, 105784. doi:10.1016/j.jobe.2022.105784
Zhang, J., Hu, X., Shao, W., Lim, Y. M., Chen, Z., and Zhu, W. (2022). Experimental study on properties of magnesium phosphate cement–based self-compacting concrete with high-early strength. J. Mater. Civ. Eng. 34, 04021435. doi:10.1061/(asce)mt.1943-5533.0004075
Zhang, J., Ji, Y., Xu, Z., Xue, Q., Zhou, Y., and Jin, C. (2021). Study on improving interface bonding performance of magnesium potassium phosphate cement mortar. Mater. Construcción 71, e255. doi:10.3989/mc.2021.00421
Zhang, S., Shi, H.-S., Huang, S.-W., and Zhang, P. (2013). Dehydration characteristics of struvite-K pertaining to magnesium potassium phosphate cement system in non-isothermal condition. J. Therm. Analysis Calorim. 111, 35–40. doi:10.1007/s10973-011-2170-9
Zhang, S., Yuan, Q., Li, Q., Zhang, F., and Xie, Z. (2023c). Microstructural characteristics of bonding interfacial transition zone of concrete and magnesium ammonium phosphate cement. J. Build. Eng. 76, 107208. doi:10.1016/j.jobe.2023.107208
Zhang, T., Chen, H., Li, X., and Zhu, Z. (2017). Hydration behavior of magnesium potassium phosphate cement and stability analysis of its hydration products through thermodynamic modeling. Cem. Concr. Res. 98, 101–110. doi:10.1016/j.cemconres.2017.03.015
Zhang, Y., Wang, S., Zhang, B., Hou, D., Li, H., Li, L., et al. (2020). A preliminary investigation of the properties of potassium magnesium phosphate cement-based grouts mixed with fly ash, water glass and bentonite. Constr. Build. Mater. 237, 117501. doi:10.1016/j.conbuildmat.2019.117501
Zhao, Z., Chen, M., Xu, J., Li, L., Huang, Y., Yang, L., et al. (2021b). Mix design and rheological properties of magnesium potassium phosphate cement composites based on the 3D printing extrusion system. Constr. Build. Mater. 284, 122797. doi:10.1016/j.conbuildmat.2021.122797
Zhao, Z., Chen, M., Zhong, X., Huang, Y., Yang, L., Zhao, P., et al. (2021a). Effects of bentonite, diatomite and metakaolin on the rheological behavior of 3D printed magnesium potassium phosphate cement composites. Addit. Manuf. 46, 102184. doi:10.1016/j.addma.2021.102184
Keywords: magnesium potassium phosphate cement, repair material, fresh state properties, hardened state properties, microstructure
Citation: Dabarera A, Fernández R and Provis JL (2024) A systematic review of engineering properties of magnesium potassium phosphate cement as a repair material. Front. Mater. 11:1451079. doi: 10.3389/fmats.2024.1451079
Received: 18 June 2024; Accepted: 19 November 2024;
Published: 04 December 2024.
Edited by:
Baojian Zhan, Shenzhen University, ChinaReviewed by:
Mahmoud Ebrahimi, University of Maragheh, IranAmir Ali Shahmansouri, Washington State University, United States
Copyright © 2024 Dabarera, Fernández and Provis. This is an open-access article distributed under the terms of the Creative Commons Attribution License (CC BY). The use, distribution or reproduction in other forums is permitted, provided the original author(s) and the copyright owner(s) are credited and that the original publication in this journal is cited, in accordance with accepted academic practice. No use, distribution or reproduction is permitted which does not comply with these terms.
*Correspondence: Arosha Dabarera, YS5kYWJhcmVyYUBoZXJ0cy5hYy51aw==