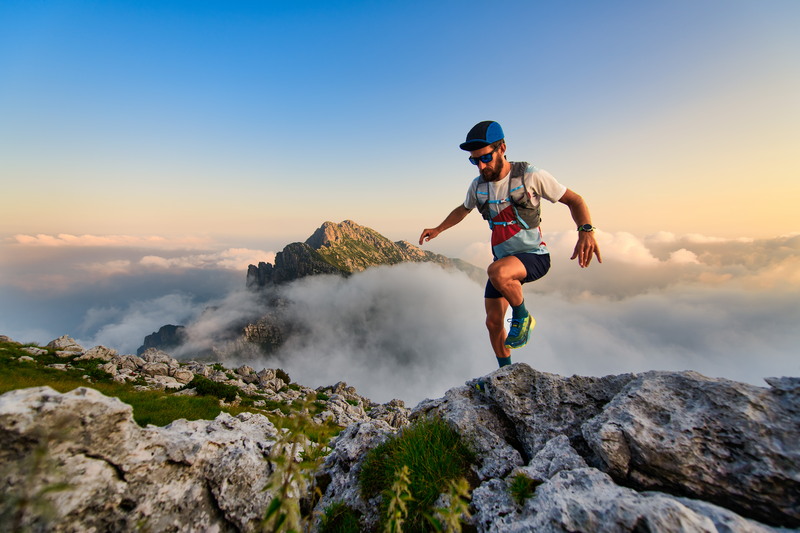
95% of researchers rate our articles as excellent or good
Learn more about the work of our research integrity team to safeguard the quality of each article we publish.
Find out more
ORIGINAL RESEARCH article
Front. Mater. , 25 July 2024
Sec. Polymeric and Composite Materials
Volume 11 - 2024 | https://doi.org/10.3389/fmats.2024.1443089
This article is part of the Research Topic Recent Advances in Flame Retardant Polymeric Materials and Composites View all articles
Vinyl ester/flax (VE/flax) bio-composites were made after incorporating hybrid concentrations (0, 3, and 6% by weight (wt)) of halloysite nanotubes (HNT), magnesium hydroxide (MHO) and chitosan infused ammonium polyphosphate (CAP) particles. The purpose of incorporation of these particles was to improve the fire-retardant (FR) properties of the VE/flax composite; however, its effect on mechanical properties was also evaluated. To reduce the number of experiments (from 27 to 9), Taguchi design of experiment was employed during composite fabrication phase. Initially, the burning time and burning rate of all the composites were calculated using a horizontal burning test while tensile properties were determined using a tensile test. To predict an optimum composition, a signal to noise (S/N) ratio analysis of the burning time and tensile strength was conducted as “larger is better” criteria. The combination of 6% MGO and 3% CAP was predicted to be an optimum hybrid filler for enhanced fire retardancy, while VE/flax composite with no filler proved to have the highest tensile strength. HNT was found to be the least effective filler for both tensile and fire-retardant properties. The predicted composition was then fabricated and validated through experimental characterizations. The fire-retardant properties of the optimized composite were additionally assessed using a limiting oxygen index (LOI) test and thermal stability was evaluated using a thermogravimetric analysis (TGA). The burning time of the optimized composite was found to be delayed by 46.5% of that of VE/flax composite, while its thermal degradation was 11.23% lower than VE/flax composite.
Impact of plastic pollution on the environment and the consistent depletion of petroleum-based resources have given rise to the need for bio-composite materials in various applications (Akter, Uddin, and Tania, 2022; Kane et al., 2022). Enough research is being conducted on the development of bio-composite materials and various applications of these materials can be seen in certain industries, e.g., packaging (Manu et al., 2022). Some other sectors have also recently adopted the use of bio-composites in manufacturing internal parts of automobiles, marines, and construction (Dittenber and GangaRao, 2012; Koronis, Silva, and Fontul, 2013). As the application of these materials is increasing in different sectors, different concerns regarding the limitations of such materials are also rising (Kovačević et al., 2021; Rashid et al., 2021; Shi et al., 2021; Zwawi, 2021; Andrew and Dhakal, 2022). One prominent shortcoming of bio-composites is their flammability and low thermal stability (Chee et al., 2020; Li, Guo, and Qian, 2021; Nguyen-Ha et al., 2023). Besides fire and thermal stability, mechanical properties of the bio-composites are also reported to be on the lower side as compared to synthetic composite materials (Bambach, 2020; Begum, Fawzia, and Hashmi, 2020; Shaker, Nawab, and Jabbar, 2021). Various natural fibers have been reported in the literature which have been used as a reinforcement in bio-composites (Malviya et al., 2020; Azman et al., 2021). Among plant-based fibers, flax fiber is considered to possess superior mechanical properties (Nayak et al., 2021; Amroune etal., 2022).
Various studies are available on enhancing the fire retardant and mechanical properties of bio-composites; however some relevant studies are being reported here. A study by Azad et al. (2022) has reported a delay of 56% in the ignition time and an increase of 23% in the tensile strength of jute/starch bio-composite after incorporation of an inorganic silica filler. Silica is chemically compatible with jute and starch while it produces a char layer around the composite when burnt. In another study conducted by (Prabhakar et al., 2021), the burning rate of bamboo/vinyl ester composites was decreased by 34% while the tensile strength was increased 19.5% after incorporation of an organic chitosan-based filler. The flame rate was reduced due to formation of carbonaceous silicate char layer during burning of the composites in the presence of Chitosan. A study by Ahmad et al. (2024) has used hybridization of resins and reinforcements to enhance the mechanical properties and thermal stability of epoxy and vinyl ester-based composites. Some studies have also reported the combined effect of multiple fillers on the mechanical and fire-retardant properties of composite materials (Shah et al., 2023; Yu et al., 2023). Another study by Ejaz et al. (2022) utilized the synergy of two inorganic fillers (aluminum trihydrate and zirconium hydroxide) on the mechanical and fire-retardant properties of polyester/jute bio-composite. They found encouraging effects of hybrid fillers on the fire-retardant properties due to char layer formation and water molecules liberation during combustion. However, they observed a decrease in the mechanical properties. These studies suggest that organic fillers contain compatible chemical structures with the natural fibers which enhance the mechanical properties of the bio-composites while inorganic fillers are comparatively efficient in enhancing the fire-retardant properties. The organic fillers derived from natural resources can easily make chemical bonds with the natural fibers which enhances the performance of the bio-composites. On the other hand, inorganics fillers are thermally more stable and produce thick char layers when burnt. Therefore, a combined effect of different organic and inorganic fillers on the fire retardant and mechanical properties of the bio-composites is required to be explored which has been conducted in the current study.
In this study, VE/flax composite material was fabricated using vacuum bagging method. The synergistic effect of HNT, MHO and CAP fillers was evaluated on the fire retardant and tensile properties of the VE/flax composite. The concentration of the three fillers was varied (as 0, 3, 6 wt%) to find an optimum combination for the desired properties. The total number of combinations in this case would be 27, which involves a significant amount of material consumption and time. To save the material cost and time, Taguchi design of experiment (DOE) method was utilized to initially reduce the number of combinations to nine only. The Taguchi method is a famous DOE technique to save experimental time and cost, which has been utilized by various researchers in similar studies as it is easy to use without requiring special expertise. The flame time/rate, and tensile properties of the nine composites were evaluated using a horizontal burning test and a tensile test respectively. The VE/flax composite with 3% CAP and 3% MHO displayed the largest burning time, while the VE/flax composite with no filler particles displayed the maximum tensile strength. The hybrid filler combinations caused poor interfacial bonding between the flax fiber and VE resin which resulted in reducing the tensile strength of the composites. The failure mechanism of the broken surfaces after tensile test was studied using field emission scanning electron microscopy (FESEM). The results of the burning time and tensile strength were then investigated using a S/N ratio analysis. Based on the S/N ratio analysis, it was predicted that VE/flax composite containing 3% CAP and 6% MHO would survive the flame for the longest time; while for tensile strength, the VE/flax composite with no filler was predicted to be the optimum composition. For validation of the S/N ratio analysis, a VE/flax composite with 3% CAP and 6% MHO was fabricated and its burning time was calculated which was found to be more than the previously fabricated nine composites. Additionally, a limiting oxygen index (LOI) test of the optimized composite was conducted and compared with the VE/flax composite, and the composition which displayed the largest burning time among the previous nine composites. Similarly, a thermogravimetric analysis (TGA) was also conducted. Both the LOI and TGA also validated the enhanced fire retardant and thermal properties of the proposed composition (3% CAP and 6% MHO filled VE/flax composite), as compared to all the composites.
Based on its utility and applications in different industries, this study involves enhancement of fire-retardant properties of bio-composites using innovative fillers, contributing to SDG 9 (Industry, Innovation, and Infrastructure), SDG 12 (Responsible Consumption and Production), SDG 13 (Climate Action), and SDG 17 (Partnerships for the Goals).
The VE resin (viscosity: 150 cps, and sp. density: 1.03) along with its hardener (Butanox M-60) and releasing agent (Frekote 700-NC) were purchased from CCP Composites (Korea). A balanced flax fabric was obtained from LINEO ITS Composites (China). HNT (MW: 29,419) and MHO nano filler (MW: 58.32) were procured from Sigma-Aldrich (United States). The CAP particles were synthesized in our laboratory by chemically modifying chitosan powder through ammonium polyphosphate (APP) using the method described by (Prabhakar et al., 2019). The APP (MW: 916.37) was also procured from Sigma Aldrich.
This study was conducted in five steps, as explained in the block diagram shown in Figure 1. At first the number of compositions to be fabricated were decided based on Taguchi DOE method. The composites were then fabricated and characterized to find their tensile and flammability properties. Only tensile and horizontal flame tests were conducted initially. A statistical tool (S/N ratio analysis) was used to find the effect of each filler on the flammability and tensile properties of the VE/flax composites. An optimized concentration of each filler was predicted based on S/N ratio analysis. At the last step, the optimized composition was manufactured and tested to validate the predictions of the statistical analysis. Details of experimental and statistical methods employed in this study are given below.
A commercially available statistical tool (Minitab 17) was used to design an L9 orthogonal array for Taguchi DOE. Three factors (HNT, MHO and CAP) each with three levels (0, 3, and 6%) were used to develop the L9 array which is shown in Table 1. The number of compositions was reduced from 27 to 9. Table 1 shows the variation in the concentration of filler particles only, while the VE resin concentration changes accordingly.
The VE/flax composites with and without the fillers were prepared using vacuum bagging method. The filler particles were dispersed between the layers of flax fabric using a hand layup method before the resin infusion. The fabric layers were stacked up on a metal surface which was earlier kept at 100°C in an oven. The VE resin was also kept in an oven at 30°C for 1 hour to obtain its viscosity at room temperature. The fabric layers were packed in a vacuum bag using a sealant tap on the surface of the metallic plate. The resin was infused in the fabric layers at a vacuum pressure of 40 kPa using a vacuum pump. The composite was initially cured at 100°C in an autoclave for 5 h and then allowed to cure at room temperature. The wt% of flax in all the composites is 40% as it has been reported in literature (Ejaz et al., 2020; Samant et al., 2023).
Initially, a horizontal flame test and a tensile test of all the composites mentioned in Table 1 were conducted according to ASTM D635 and ASTM D3039 standards respectively. The horizontal burning tests were conducted in a locally fabricated chamber while the tensile tests were carried out on an MTS 97 kN load cell. The fractured surfaces of the composite specimens after the tensile test were observed using a field emission scanning electron microscope (FESEM) [Zeiss Gemini (Germany)].
At the end, the flammability properties were validated by conducting a LOI test and a thermogravimetric analysis of the composites. The LOI test was conducted following the ASTM D2893 standard using an LOI equipment of FESTEC International Co. Ltd., Korea. TGA was carried out on SDT Q600 thermal analyser till 800°C at a heating rate of 10°C/min in an inert N2 environment.
S/N ratio analysis is a statistical tool used for a large set of data to reduce the variability (noise) and find an optimum configuration. This method plays a key role in identifying the key factors and their desired levels in the Taguchi DOE optimization technique as reported in the literature (Saghir et al., 2023; Achmad Jusuf Zulfikar, 2024). In this study, an S/N ratio analysis on the burning time and tensile strength data was carried out for the nine specimens defined in Table 1. Both burning time and tensile strength are desired to be maximum, so the S/N ratio analysis type was “larger is better”. The analysis was carried out using Minitab 17. An optimized set of composition of the three fillers was obtained because of this analysis, which was manufactured and validated experimentally.
Burning time and burning rate of all the nine composites are plotted in Figure 2. Each filler and the combination of all the fillers were observed to enhance the burning time of the VE/flax composite. The fire retardancy mechanism of both the organic and inorganics fillers is available in literature (Madyaratri et al., 2022). However, the synergistic effect of these fillers has been presented in the current study. On burning the HNT, a layer on the surface of the base material is deposited which acts as a thermal barrier to stop the flow of heat (Arora et al., 2014). The MHO dissolves into a char layer of magnesium oxide and water vapours at high temperatures (Wang et al., 2020). The char layer acts as a thermal barrier while the water vapours support fire extinguishing. The CAP is reported to liberate carbon dioxide on combustion which acts as a fire extinguisher; additionally, it produces phosphoric acid which acts as a blowing agent, and a char layer which acts as a thermal barrier (Prabhakar et al., 2019). The results showed that specimen D exhibited the highest burning time (289 s) and lowest burning rate (0.260 mm/s) compared to 230 s and 0.326 mm/s of specimen A. This specimen contains 3% CAP and 3% MHO in a VE/flax composite. The increase in burning time of specimen D is 25.65% of that of Specimen A. The combined effect of CAP and MHO verifies a synergy of the two fillers in enhancing the fire-retardant property. The two fillers contain free -OH groups which is also contained in flax fiber, this may be their possible interaction mechanism during combustion and the evaporation of water vapours. At this stage, composite specimen D is considered to display maximum burning time. S/N ratio analysis on this data was carried out to find an optimized composition for maximum burning time which may not be among these nine compositions. The analysis is presented in a later section.
The tensile strength and modulus of the nine composites have been plotted in Figure 3. Tensile strength of the fire-retardant fillers incorporated bio-composites has generally been reported to decrease compared to the unfilled composites (Bazan, Salasińska, and Kuciel, 2021; Thiyagu and NarendraKumar 2023). The same phenomenon was observed in the current study as well. VE/flax composite without any filler (specimen A) was found to have maximum tensile strength (105.65 MPa) among all the nine composites. The fillers in individual as well as hybrid combinations have caused a slight decrease in the tensile properties, especially the strength. The decrease in the tensile strength of fillers incorporated composites (specimens B to I) was found to vary between 3%–22%. This decrease in the tensile strength may be attributed to the high degree of inhomogeneity because of multiple fillers incorporation in the VE/flax composite.
FESEM images of specimen A and specimen D have been compared in Figures 4A, B, respectively. Failure in specimen A seems to occur due to a dominant fiber breakage pattern while specimen D, which contains fillers, also shows spots of fiber pull-outs. Flax fibers are the main load carriers in these composites under a tensile load, a fiber pull-out shows a weak interface between the VE resin and flax fiber in the presence of the fire-retardant fillers. However, in specimen A, in the absence of any filler a dominant fiber breakage phenomenon can be observed which shows that flax fibers have taken the maximum load before breakage rather than slipping out from the interfaces. The failure behavior in specimen D explains failure of all the fillers incorporated composites in this study.
A statistical analysis to determine the influence of each filler on the burning time and tensile strength was carried out using S/N ratios. This analysis was conducted on Minitab tool using “larger is better” criteria. The numerical values of tensile strength and burning time obtained above along with their S/N ratios are shown in Table 2. The mean S/N ratio of each factor against its levels has been plotted in Figure 5. The influence of each filler on the burning time and tensile strength was determined individually from Figures 5A, B, respectively. The horizontal dotted line in these figures shows the mean S/N ratio value. The analysis plotted in Figure 5 predicts that a hybrid composition of 6% MHO, 0% HNT and 3% CAP fillers will result in maximum burning time of VE/flax composite. While the VE/flax composite with no filler is a proposed composite with highest tensile strength.
The response of S/N ratios for burning time and tensile strength is shown in Table 3. The maximum value of S/N ratio for each filler corresponds to its optimum concentration. The results in Table 3 show that CAP has the maximum influence on enhancing the fire-retardant properties, as it ranks at one. Similarly, HNT showed maximum effect on causing a decrease in the tensile strength of the composites. As discussed earlier, CAP and MHO both contain free -OH groups which is compatible with the cellulose found in the flax fiber. However, HNT is chemically not compatible with any of the constituents of these composites. Therefore, HNT was found to have the least effect of enhancing any of the properties of the composites in this study.
To validate the proposed composition as evaluated by the S/N ratio analysis above, a new VE/flax composite with a hybrid incorporation of 3% CAP and 6% MHO was fabricated by the same method as explained earlier. This new composite material will be referred to as specimen J in this study onwards.
The newly fabricated specimen J was testing for horizontal burning, LOI and TGA. The LOI test and TGA of specimen A and specimen D were also carried out to compare with the optimized composite specimen J. The results of the burning test are shown in Figure 6. Specimen J was found to have enhanced burning time (337 s) and minimum burning rate (0.222 mm/s) as compared to that of specimens A (230 s and 0.326 mm/s) and D (289 s and 0.260 mm/s). The burning duration of specimen J is 46.5% and 16.6% more than that of specimens A and D respectively; while it is higher than those of all other composites fabricated for this study.
The LOI value of specimen J (27.2%) is also higher than those of specimen A (19.4%) and D (22.6%). The results of LOI test agree with the results of horizontal burning test. The results of LOI test are plotted in Figure 7. The thermal stability of specimens A, D and J was also evaluated and compared using TGA thermograms in Figure 8. All the composites went through two stages of thermal degradation. Initially, the thermal degradation of specimens D and J was slightly faster than specimen A, which may be due to the early loss of water of crystallization. The onset of degradation for all specimens started between 320°C–340°C, which is a close range. At the first stage, the loss of weight is also approximately the same (10%) for all the composites. However, at high temperatures, the fillers incorporation showed a prominent effect on the thermal stability of the VE/flax composite. In the final stage (between 450°C–800°C) specimen A lost around 93% of its weight while specimens D and J lost 87.4% and 81.77% of their weights, respectively. This was mainly due to the protection of the composite specimens under the char layers produced during the combustion process of CAP and MHO. The results of thermal degradation of the composites are also analogues to the results of flame and LOI tests. Specimen J was proved to possess the greatest thermal stability and fire-retardant properties which validates the predictions of the statistical analysis used in this study.
Three fillers (HNT, MHO and CAP) were incorporated in the VE/flax composite to enhance its fire-retardant properties. Taguchi DOE technique was employed to reduce the number of experiments (from 27 to 9) involved in optimizing the composition of VE/flax composites containing hybrid concentrations (0, 3, 6%) of the fillers. Synergistic effect of these fillers on the flammability and tensile properties was studied using a horizontal burning test and a tensile test, respectively. Among the nine composites, it was found that VE/flax composite with hybrid incorporation of 3% CAP and 3% MHO (specimen D) showed the maximum resistance to flame propagation; however, tensile strength of VE/flax composite without any filler (specimen A) was found maximum. A S/N ratio analysis was conducted on the burning time and tensile strength values of the nine composites, and it was predicted that hybrid incorporation of 3% CAP and 6% MHO in the VE/flax composite will result in delaying the burning time. For validation, a composite with the same composition (specimen J) was fabricated and tested. The specimen J was found to have a burning time of 46.5% higher than that of the original VE/flax composite. It was also verified through LOI test; the LOI of specimen J was found to be 40% higher than that of specimen A, which is analogous with the results of the burning test. Similarly, the wight loss of specimen J (81.77%) was found to be less than all other composites. The thermal stability and fire-retardant properties of specimen J were found to be greater than all other composites in this study. CAP and MHO were ranked as the top two contributors in enhancing the fire-retardant properties of the composites. The same two fillers had shown least effect on reducing the tensile properties of the composites. Their synergistic effect was also proven to be efficient. On the other hand, HNT was found to contribute least to enhancing the fire-retardant properties and had shown greater effect in deteriorating the tensile properties of the composites.
The raw data supporting the conclusions of this article will be made available by the authors, without undue reservation.
MF: Conceptualization, Funding acquisition, Investigation, Methodology, Writing–original draft, Writing–review and editing.
The author(s) declare that financial support was received for the research, authorship, and/or publication of this article. This work was supported by the Deanship of Scientific Research, Vice Presidency for Graduate Studies and Scientific Research, King Faisal University, Saudi Arabia (Grant no. KFU241309).
The author declares that the research was conducted in the absence of any commercial or financial relationships that could be construed as a potential conflict of interest.
All claims expressed in this article are solely those of the authors and do not necessarily represent those of their affiliated organizations, or those of the publisher, the editors and the reviewers. Any product that may be evaluated in this article, or claim that may be made by its manufacturer, is not guaranteed or endorsed by the publisher.
Achmad Jusuf Zulfikar, Z. (2024). Optimization of Flexural Strength in Jute and E-Glass Laminated Composite Materials Using the Taguchi Method. doi:10.5281/ZENODO.10570192
Ahmad, H., Shah, A. U. R., Kamran Afaq, S., Azad, M. M., Arif, S., Siddiqi, M. U. R., et al. (2024). Development and Characterization of Kevlar and Glass Fibers Reinforced Epoxy/Vinyl Ester Hybrid Resin Composites. Polym. Compos. 45 (9), 8133–8146. doi:10.1002/pc.28329
Akter, M., Uddin, Md H., and Tania, I. S. (2022). Biocomposites Based on Natural Fibers and Polymers: A Review on Properties and Potential Applications. J. Reinf. Plastics Compos. 41 (17–18), 705–742. doi:10.1177/07316844211070609
Amroune, S., Ahmed, B., Bourchak, M., Makhlouf, A., and Hamid, S. (2022). Statistical and Experimental Analysis of the Mechanical Properties of Flax Fibers. J. Nat. Fibers 19 (4), 1387–1401. doi:10.1080/15440478.2020.1775751
Andrew, J. J., and Dhakal, H. N. (2022). Sustainable Biobased Composites for Advanced Applications: Recent Trends and Future Opportunities – A Critical Review. Compos. Part C. Open Access 7 (9), 100220. doi:10.1016/j.jcomc.2021.100220
Arora, R., Mandal, U. K., Sharma, P., and Srivastav, A. (2014). Effect of Fabrication Technique on Microstructure and Electrical Conductivity of Polyaniline-TiO2-PVA Composite Material. Procedia Mater. Sci. 6 (2), 238–243. 3rd International Conference on Materials Processing and Characterisation (ICMPC 2014). doi:10.1016/j.mspro.2014.07.029
Azad, M. M., Ejaz, M., Shah, A. U. R., Kamran Afaq, S., and Jung-il, S. (2022). A Bio-Based Approach to Simultaneously Improve Flame Retardancy, Thermal Stability and Mechanical Properties of Nano-Silica Filled Jute/Thermoplastic Starch Composite. Mater. Chem. Phys. 289, 126485. doi:10.1016/j.matchemphys.2022.126485
Azman, M. A., Asyraf, M. R. M., Khalina, A., Petrů, M., Ruzaidi, C. M., Sapuan, S. M., et al. (2021). Natural Fiber Reinforced Composite Material for Product Design: A Short Review. Polymers 13 (12), 1917. doi:10.3390/polym13121917
Bambach, M. R. (2020). Direct Comparison of the Structural Compression Characteristics of Natural and Synthetic Fiber-Epoxy Composites: Flax, Jute, Hemp, Glass and Carbon Fibers. Fibers 8 (10), 62. doi:10.3390/fib8100062
Bazan, P., Salasińska, K., and Kuciel, S. (2021). Flame Retardant Polypropylene Reinforced with Natural Additives. Industrial Crops Prod. 164, 113356. doi:10.1016/j.indcrop.2021.113356
Begum, S., Fawzia, S., and Hashmi, M. S. J. (2020). Polymer Matrix Composite with Natural and Synthetic Fibres. Adv. Mater. Process. Technol. 6 (3), 547–564. doi:10.1080/2374068X.2020.1728645
Chee, S. S., Jawaid, M., Alothman, O. Y., and Yahaya, R. (2020). Thermo-Oxidative Stability and Flammability Properties of Bamboo/Kenaf/Nanoclay/Epoxy Hybrid Nanocomposites. RSC Adv. 10 (37), 21686–21697. doi:10.1039/D0RA02126A
Dittenber, D. B., and GangaRao, H. V. S. (2012). Critical Review of Recent Publications on Use of Natural Composites in Infrastructure. Compos. Part A Appl. Sci. Manuf. 43 (8), 1419–1429. doi:10.1016/j.compositesa.2011.11.019
Ejaz, M., Azad, M. M., Shah, A. U. R., Kamran Afaq, S., and Jung-il, S. (2020). Mechanical and Biodegradable Properties of Jute/Flax Reinforced PLA Composites. Fibers Polym. 21 (11), 2635–2641. doi:10.1007/s12221-020-1370-y
Ejaz, M., Azad, M. M., Shah, A. U. R., Kamran Afaq, S., and Jung-il, S. (2022). Synergistic Effect of Aluminum Trihydrate and Zirconium Hydroxide Nanoparticles on Mechanical Properties, Flammability, and Thermal Degradation of Polyester/Jute Fiber Composite. Cellulose 29 (3), 1775–1790. doi:10.1007/s10570-022-04417-9
Kane, S., Van Roijen, E., Ryan, C., and Miller, S. (2022). Reducing the Environmental Impacts of Plastics While Increasing Strength: Biochar Fillers in Biodegradable, Recycled, and Fossil-Fuel Derived Plastics. Compos. Part C. Open Access 8, 100253. doi:10.1016/j.jcomc.2022.100253
Koronis, G., Silva, A., and Fontul, M. (2013). Green Composites: A Review of Adequate Materials for Automotive Applications. Compos. Part B Eng. 44 (1), 120–127. doi:10.1016/j.compositesb.2012.07.004
Kovačević, Z., Grgac, S. F., and Bischof, S. (2021). Progress in Biodegradable Flame Retardant Nano-Biocomposites. Polymers 13 (5), 741. doi:10.3390/polym13050741
Li, X., Guo, R., and Qian, X. (2021). Study on Flame Retardancy and Mechanism of Talc Composite Foams. Front. Mater. 8, 661906. doi:10.3389/fmats.2021.661906
Madyaratri, E. W., Ridho, M. R., Arum Aristri, M., Lubis, M. A. R., Iswanto, A. H., Nawawi, D. S., et al. (2022). Recent Advances in the Development of Fire-Resistant Biocomposites—A Review. Polymers 14 (3), 362. doi:10.3390/polym14030362
Malviya, R. K., Singh, R. K., Purohit, R., and Sinha, R. (2020). Natural Fibre Reinforced Composite Materials: Environmentally Better Life Cycle Assessment – A Case Study. Mater. Today Proc. 26, 3157–3160. doi:10.1016/j.matpr.2020.02.651
Manu, T., Ali, R. N., Shahri, B., Emerson, N., and Huber, T. (2022). Biocomposites: A Review of Materials and Perception. Mater. Today Commun. 31, 103308. doi:10.1016/j.mtcomm.2022.103308
Nayak, S. Y., Shenoy Heckadka, S., Seth, A., Prabhu, S., Sharma, R., and Shenoy, K. R. (2021). Effect of Chemical Treatment on the Physical and Mechanical Properties of Flax Fibers: A Comparative Assessment. Mater. Today Proc. 38, 2406–2410. doi:10.1016/j.matpr.2020.07.380
Nguyen-Ha, , Minh, T., Nguyen, T. B., Nguyen, T.An, Pham, L. H., Nguyen, D. H., et al. (2023). Novel High-Performance Sustainable Polyurethane Nanocomposite Foams: Fire Resistance, Thermal Stability, Thermal Conductivity, and Mechanical Properties. Chem. Eng. J. 474, 145585. doi:10.1016/j.cej.2023.145585
Prabhakar, M. N., Raghavendra, G. M., Vijaykumar, B. V. D., Patil, K., Seo, J., and Jung-il, S. (2019). Synthesis of a Novel Compound Based on Chitosan and Ammonium Polyphosphate for Flame Retardancy Applications. Cellulose 26 (16), 8801–8812. doi:10.1007/s10570-019-02671-y
Prabhakar, M. N., Venakat Chalapathi, K., Rehman, S. A. U., and Jung-il, S. (2021). Effect of a Synthesized Chitosan Flame Retardant on the Flammability, Thermal Properties, and Mechanical Properties of Vinyl Ester/Bamboo Nonwoven Fiber Composites. Cellulose 28 (18), 11625–11643. doi:10.1007/s10570-021-04252-4
Rashid, M., Chetehouna, K., Cablé, A., and Gascoin, N. (2021). Analysing Flammability Characteristics of Green Biocomposites: An Overview. Fire Technol. 57 (1), 31–67. doi:10.1007/s10694-020-01001-0
Saghir, Q., Shah, A. U. R., Kamran Afaq, S., Ahmed, T., and Jung-il, S. (2023). Effect of Machining Parameters on Surface Quality and Delamination of Carbon/Glass/Epoxy Hybrid Composite Material During End Milling Operation. J. Mech. Sci. Technol. 37 (5), 2319–2324. doi:10.1007/s12206-023-0408-7
Samant, L., Goel, A., Mathew, J., Jose, S., and Thomas, S. (2023). Effect of Surface Treatment on Flax Fiber Reinforced Natural Rubber Green Composite. J. Appl. Polym. Sci. 140 (12), e53651. doi:10.1002/app.53651
Shah, A.Ur R., Jalil, A., Sadiq, A., Alzaid, M., Naseem, M. S., Alanazi, R., et al. (2023). Effect of Rice Husk and Wood Flour on the Structural, Mechanical, and Fire-Retardant Characteristics of Recycled High-Density Polyethylene. Polymers 15 (19), 4031. doi:10.3390/polym15194031
Shaker, K., Nawab, Y., and Jabbar, M. (2021). “Bio-Composites: Eco-Friendly Substitute of Glass Fiber Composites,” in Handbook of Nanomaterials and Nanocomposites for Energy and Environmental Applications. Editors O. V. Kharissova, L. M. Torres-Martínez, and B. I. Kharisov (Cham, Switzerland: Springer International Publishing), 151–175. doi:10.1007/978-3-030-36268-3_108
Shi, Y., Yu, B., Wang, X., and Yuen, A. C. Y. (2021). Editorial: Flame-Retardant Polymeric Materials and Polymer Composites. Front. Mater. 8. doi:10.3389/fmats.2021.703123
Thiyagu, C., and NarendraKumar, U. (2023). Effect of Ammonium Polyphosphate on Fire-Retardant, Mechanical, and Vibrational Analysis of Epoxy/Glass/Ramie Hybrid Composite. Polym. Compos. 44 (1), 621–631. doi:10.1002/pc.27123
Wang, C., Liu, J., Wang, Y., and Han, Z. (2020). Enhanced Flame Retardance in Polyethylene/Magnesium Hydroxide/Polycarbosilane Blends. Mater. Chem. Phys. 253, 123373. doi:10.1016/j.matchemphys.2020.123373
Yu, Y., Ma, C., Zhang, H., Zhang, Y., Fang, Z., Song, R., et al. (2023). Combination Effects of a Bio-Based Fire Retardant And Functionalized Graphene Oxide on a Fire Retardant and Mechanical Properties of Polylactide. Mater. Today Chem. 30, 101565. doi:10.1016/j.mtchem.2023.101565
Keywords: fire retardancy, mechanical properties, synergy, design of experiments, biocomposites
Citation: Faraz MI (2024) Optimizing the synergistic effect of organic and inorganic fillers on fire-retardant and mechanical properties of vinyl ester/flax bio-composites. Front. Mater. 11:1443089. doi: 10.3389/fmats.2024.1443089
Received: 03 June 2024; Accepted: 01 July 2024;
Published: 25 July 2024.
Edited by:
Jun Sun, Beijing University of Chemical Technology, ChinaReviewed by:
Prabhakar M. N., Changwon National University, Republic of KoreaCopyright © 2024 Faraz. This is an open-access article distributed under the terms of the Creative Commons Attribution License (CC BY). The use, distribution or reproduction in other forums is permitted, provided the original author(s) and the copyright owner(s) are credited and that the original publication in this journal is cited, in accordance with accepted academic practice. No use, distribution or reproduction is permitted which does not comply with these terms.
*Correspondence: Muhammad Iftikhar Faraz, bWZhcmF6QGtmdS5lZHUuc2E=
Disclaimer: All claims expressed in this article are solely those of the authors and do not necessarily represent those of their affiliated organizations, or those of the publisher, the editors and the reviewers. Any product that may be evaluated in this article or claim that may be made by its manufacturer is not guaranteed or endorsed by the publisher.
Research integrity at Frontiers
Learn more about the work of our research integrity team to safeguard the quality of each article we publish.