- 1School of Traffic and Transportation Engineering, Changsha University of Science and Technology, Changsha, China
- 2Guangxi Transportation Science and Technology Group Co. Ltd., Nanning, China
- 3Guangxi Key Lab of Road Structure and Materials, Nanning, China
- 4School of Materials Science and Engineering, Chang’an University, Xi’an, China
- 5College of Transportation, Jilin University, Changchun, China
Waste rubber modified bitumen has gained significant attention as a sustainable and innovative material in the field of pavement engineering. This study aims to evaluate the performance of rubber modified bitumen mastic by considering its rheological properties, specifically focusing on preparation parameters, i.e., rubber content, mesh number, and filler to bitumen ratio. From the experimental results, the rheological properties of rubber modified bitumen mastic were significantly influenced by preparation parameters. Increasing the rubber powder content in bitumen mastic results in higher viscosity. Increasing the rubber content improves high-temperature rutting resistance to a certain extent, however, excessive rubber powder content would result in weakened high-temperature performance improvement. The rutting factor decreases gradually with an increase in the rubber mesh number. A ratio of filler to bitumen of 0.95 exhibits the best resistance to rutting at high temperatures. Higher rubber content and larger mesh number correspond to stronger low-temperature crack resistance in bitumen mastic. As the ratio of filler to bitumen increases, the low-temperature deformation capacity gradually decreases, resulting in weaker low-temperature crack resistance. Based on the grey relation analysis, the ratio of filler to bitumen has the greatest impact on the high and low-temperature rheological properties of bitumen mastic, followed by the rubber content. The rubber mesh number has a relatively lower impact. It is crucial to control the ratio of filler to bitumen to avoid excessive values. When possible, a higher rubber powder content should be used while meeting process requirements. These findings provide valuable insights into the design and optimization of rubber modified bitumen mastic, which can contribute to the development of sustainable and high-performance bitumen mixtures, promoting the use of recycled rubber in pavement engineering.
1 Introduction
Reusing waste tires has been one key point to maximize the value of resources (Karakurt, 2015; Xu et al., 2022). With the swift expansion witnessed in the automotive sector, the tyre production is also growing rapidly, and the resulting environmental pressure cannot be underestimated (Noura et al., 2021; Zhang et al., 2023). It is a good way to reuse resources by crushing waste tires and producing rubber powder, which not only effectively solves the accumulation of waste tires and avoids the problem of black pollution, but also maximizes the value of waste tires (Ameli et al., 2020; Li et al., 2023). At the same time, waste tire rubber powder is a good modified material for road bitumen, rubber bitumen has better road performance, the pavement paved by rubber bitumen exhibits excellent performance in different temperature conditions, along with remarkable fatigue resistance as well as low noise environmental protection characteristics, so rubber powder has become a widely employed modifier (Sun et al., 2021; Kumar et al., 2022a). Bitumen mortar plays an important role in filling the aggregate gap and bonding aggregate in the bitumen mixture system, the composition structure and rheological properties of which will greatly affect the mixture’s performances at different temperatures (Yan et al., 2015; Kumar et al., 2022b). The added rubber powder will affect rheological characteristics for rubberized-bitumen mortar, whose rheological properties are the key to affecting the mixture performance (Wang et al., 2021; Li, 2023). Hence, conducting additional investigations into the rheological characteristics of rubberized-bitumen mixtures is imperative based on various preparation parameters, which will have great guiding significance to rubber bitumen pavement construction.
Generally, during interaction procedure with binder, the change process of rubber powder is divided into two stages: swelling and dissolution (Neto et al., 2006). Waste tire rubber powder is dispersed into filaments in bitumen and asphaltene micelles are evenly distributed in bitumen oil, forming a stable and physically compatible system without phase separation (Kim and Lee, 2013; Hosseinnezhad et al., 2019; Zhou et al., 2021). The oil wax group with similar solubility parameters to rubber will slowly diffuse into the space of rubber chain segment, making the rubber chain segment loose, disengage and dissolve (Gergó et al., 2017). At a lower temperature and in the early interaction stage, particle volume can expand to 2 to 3 times of the original, and the expansion of rubber particles experiences an escalation of viscosity for mixture system (Hemida and Abdelrahman, 2020; 2021).
The properties of rubber bitumen depend on different parameters including preparation process and raw material parameters (He et al., 2023). The former includes temperature, stirring rate and reaction time (Yu et al., 2017; Yucel and Ozturk, 2023). The latter depends on basic characteristics about rubber as well as matrix bitumen, i.e., rubber powder source, treatment method, particle size and content, grade, chemical composition as well as molecular weight distribution for matrix bitumen (Apeagyei, 2011; Xing et al., 2023). Previous studies have shown that the mixing intensity during the interaction period influences greatly the characteristics of bitumen as well as rubber powder blending system. The difference of mixing and shear strength may make the bitumen’s properties different owing to changing mixing rate (Xie et al., 2023). Low-speed stirring can keep rubber particles in suspension, while high-speed shearing can decompose rubber particles mechanically. Under low-speed stirring, rubber particles swell, and rubber polymers are basically not dissolved in matrix bitumen, but bitumen components are simply absorbed (Pei et al., 2023). In the process of high-intensity mixing, As a result of bitumen absorption, the expanded rubber particles soften, and high-speed mixing is easy to shear the softened rubber outer surface, and at this time, the rubber powder component takes the opportunity to dissolve into the bitumen phase (Duan et al., 2022). This is a pivotal factor impacting the overall performance of rubber bitumen materials. The behavior of rubber powder particles in different reaction stages has varying impacts on the characteristics of bitumen (Ding et al., 2023). On the one hand, the expanded rubber powder particles alter the physical properties of bitumen by absorbing its lighter components, on the other hand, they also serve as elastic fillers in bitumen, elevating the viscosity and complex modulus of bitumen (Huang, 2023). Meanwhile, some components of the dissolved rubber powder particles are released into the bitumen matrix, and on the one hand, they are combined with other swollen rubber powder particles, thus improving the viscoelastic properties of bitumen (Gulzar and Underwood, 2020; Hajikarimi et al., 2022). On the other hand, each component released from the particles can interact with the bitumen component independently, changing the bitumen composition, thus changing the properties of bitumen (Huang et al., 2017; Gao et al., 2022).
The modification process of rubber bitumen and the various factors affecting its properties have been thoroughly investigated both domestically and internationally. These findings provide a solid groundwork for our current project, focusing on the rheological characteristics of rubber bitumen mortar. In this study, diverse mastic samples containing granulated rubber modification were crafted, each with distinct rubber concentrations, mesh numbers, and filler-bitumen ratios. The rheological characteristics of the granulated rubber modified mastic, including viscosity, rutting factor, phase angle and stiffness modulus, were evaluated employing both a dynamic shear rheometer (DSR) and a bending beam rheometer (BBR). The rubber content was varied from 16% to 24%, the mesh number ranged from 20 to 60, and the filler-bitumen ratio was adjusted from 0, 0.65, 0.95 and 1.25.
2 Materials and methods
2.1 Raw materials
The 70# base bitumen supplied by Guangxi Dongyou was employed for the preparation of the modified bitumen. The basic physical characteristics of 70# base bitumen are displayed in Table 1, which could meet the requirements of Chinese specification JTG E20-2011.
The granulated rubber was kindly supplied by Guangxi Transportation Science and Technology New Material Technology Co., Ltd. (China), and the main technical characteristics are displayed in Table 2.
The limestone mineral powder was adopted as the filler in bitumen binder. The main technical properties are shown in Table 3.
2.2 Testing procedure
2.2.1 Sample preparation
In this study, granulated rubber modified bitumen and granulated rubber modified bitumen mastic would be made by using the former raw materials. In the process of preparing rubber modified bitumen, the base bitumen was firstly quickly heated to 180°C, and then granulated rubber powder was mixed in the base bitumen within 1 min and continuously stirred. After that, the mixture was manually stirred at (180 ± 5)°C for 30 min, then sheared at the shearing rate of 4,000 r/min for 30 min. Finally, the finished rubber modified bitumen was made by mixing as well as developing in an incubator at 180°C for 60 min. In the course of preparing rubber modified bitumen mastic, the processed rubber modified bitumen was heated to 180°C, then the weighed mineral powder was mixed in the molten rubber modified bitumen, which can be stirred evenly at 180°C.
2.2.2 Viscosity test
The bitumen’s rotary viscosity test can evaluate the apparent viscosity of bitumen, reflect the bitumen’s capability to withstand deformation when subjected to external force, and then characterize the high temperature performance and flow characteristics of bitumen. Generally, the larger the rotary viscosity of bitumen, the stronger its deformation resistance and the worse the fluidity. The Brookfield Rotary viscometer is globally recognized as a commonly utilized device for bitumen viscosity measurement, mostly employed to measure the high-temperature viscosity of bitumen and bitumen mastic. For the purpose of analysis, the viscosity variation of granulated rubber modified bitumen mastic with temperature under the conditions of different mesh number of granulated rubber powder, different content of granulated rubber powder and different ratio of filler to bitumen, the bitumen rotary viscosity test was conducted in accordance with T0625 method in the testing specification JTG E20-2011.
2.2.3 Rheological properties tests
The softening point and rutting factor are commonly used to evaluate the high temperature performance of granulated rubber modified bitumen mastic. The rutting factor (G*/sinδ) is the proportion of complex shear modulus (G*) to the sine value of phase angle (δ). The greater the G*/sinδ, the more significant the elastic behavior of bitumen as well as the stronger the resilience against rutting at high temperature. In this research, the dynamic shear rheometer (DSR) was employed to evaluate the characteristics of granulated rubber modified mastic according to T0628 in JTG E20-2011. The DSR test adopted the stress control mode, and the parameters were set as follows: the stress is 100 Pa, the frequency is 0.159∼15.9 Hz, the test temperature was 64°C∼82°C. In order to fully understand the high temperature characteristics of granulated rubber modified bitumen mastic, the ADS-COV rheometer was used in this test to conduct dynamic scanning. The parallel plates have a diameter of 25 mm and a height of 1 mm.
In general, the low temperature creep stiffness (S) and creep stiffness change rate (m) were employed to describe the bitumen’s resistance to low temperature cracking. The greater the creep stiffness (S), the more brittle the bitumen as well as the easier the pavement to crack at low temperature. The higher the creep stiffness change rate (m), the larger the stress relaxation of road materials, the superior the resilience of pavement to temperature stress caused by temperature drop, and the possibility of temperature shrinkage cracks will be reduced. Therefore, bitumen mastic with a smaller creep stiffness modulus (S) and a larger creep stiffness change rate (m) exhibits improved crack resistance at low temperatures. In this investigation, the bending beam rheometer (BBR) test at −12°C was conducted for granulated rubber modified bitumen mastic with various ratios of filler to bitumen and different granulated rubber contents. The low-temperature creep stiffness (S) and creep stiffness change rate (m) of the bitumen binder were determined utilizing a TE-BBR according to T0627 in JTG E20-2011, which is a widely recognized index for assessing the low temperature properties of bitumen in recent years.
3 Influence analysis of preparation factors on viscosity characteristics of granulated rubber modified bitumen mastic
Bitumen mixture exhibits a dispersed system featuring a complex spatial network structure, where the mastic serves to adhere aggregates together and fill gaps. The performance of the mastic has a considerable impact on the viscoelasticity of bitumen combination. The measurement of viscosity of bitumen binder is generally used to determine the construction temperature, and research has confirmed there is a strong correlation between viscosity and high-temperature performance metrics such as anti-rutting factor.
3.1 Impact of the proportion of granulated rubber
To investigate how the proportion of granulated rubber powder affects the viscosity of bitumen mastic, this paper adopts 20 mesh, 40 mesh and 60 mesh granulated rubber powder to alter the matrix bitumen, respectively. The impact of the granulated rubber powder content on the 170°C viscosity of bitumen mastic with different ratios of filler to bitumen is studied, as illustrated in Figure 1. The figure clearly illustrates that the viscosity of bitumen mastic at 170°C rises as the content of granulated rubber powder increases, irrespective of the powder’s mesh size. This increase can be attributed to the formation of a spatial network structure upon adding granulated rubber powder, which dampens the flow of free bitumen. The higher the content of granulated rubber powder, the denser the network structure, the stronger the damping effect, and then the higher the viscosity. Meanwhile, the added granulated rubber powder will take in part of the light components and increase the relative content of gum and asphaltene. Asphaltene is the most polar component and the group core of bitumen colloid, which significantly influences bitumen viscosity. Therefore, the higher the content of granulated rubber powder, the higher the consistency of bitumen modified with granulated rubber. At the same time, it is evident from Figure 1 that as the granulated rubber powder content rises from 20% to 24%, the corresponding viscosity increases greatly, which indicates that the proportion of granulated rubber powder will cause a dramatic rise in viscosity and is not conducive to construction.
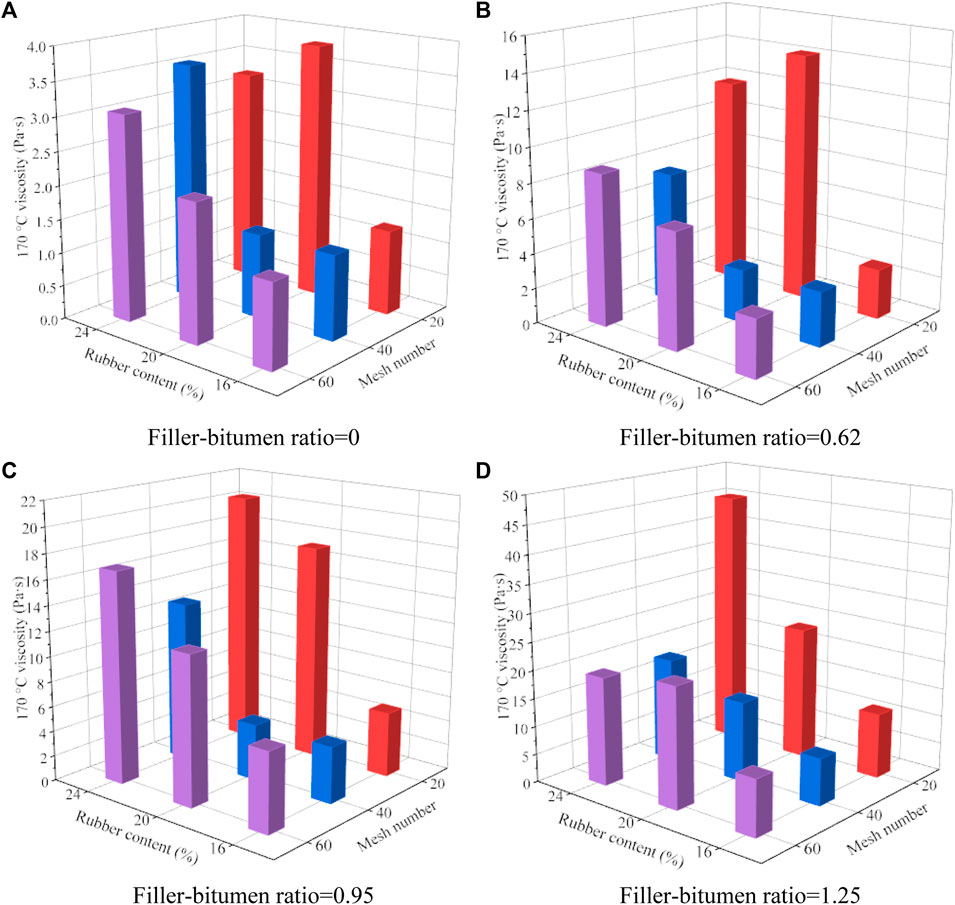
Figure 1. Effect of granulated rubber content on viscosity of bitumen mastic with varying filler-to-bitumen ratios. Effect of granulated rubber content on viscosity of bitumen mastic with varying filler-to-bitumen ratios: (A) Ratio = 0; (B) Ratio = 0.62; (C) Ratio = 0.95; (D) Ratio = 1.25.
3.2 Influence of granulated rubber mesh number
The mesh number of granulated rubber powder represents the dimension of granulated rubber particles, with a higher mesh number indicating smaller particles. The mesh size of granulated rubber powder influences the viscosity of granulated rubber modified bitumen mastic to a certain extent. When the mesh number of granulated rubber powder is appropriate, the distribution of granulated rubber particles within the bitumen is well-established, and the particle gaps are suitable, resulting in a lower viscosity and better flowability in the bitumen mastic modified with granulated rubber. When the mesh number of granulated rubber powder is too small or too large, the distribution of granulated rubber particles in the rubber modified bitumen mastic is poor, and the particle gaps are small, resulting in a higher viscosity and poorer flowability of the rubber modified bitumen mastic. Additionally, compared with Figure 2, it can be found that the granulated rubber modified bitumen mastic made by 40 mesh granulated rubber powder has a relatively lower viscosity at 170°C than that of the other two mesh number. This variety of granulated rubber-modified bitumen mastic exhibits enhanced penetration into bitumen mixture voids, thereby enhancing pavement adhesion and elasticity modulus, and increase the durability of the road surface. In addition, it can form a more uniform colloidal network structure, to some extent increase the viscosity and adhesion of the bitumen, and increase the shear resistance and anti-wrinkle properties of the road surface. Therefore, the mesh number of granulated rubber powder has a substantial impact on the viscosity of granulated rubber modified bitumen mastic. The viscosity of bitumen mastic is influenced differently by the yield of granulated rubber powder and the ratio of filler to bitumen, and selecting the appropriate mesh number of granulated rubber powder can regulate the rheological characteristics of the bitumen mastic to meet different engineering requirements.
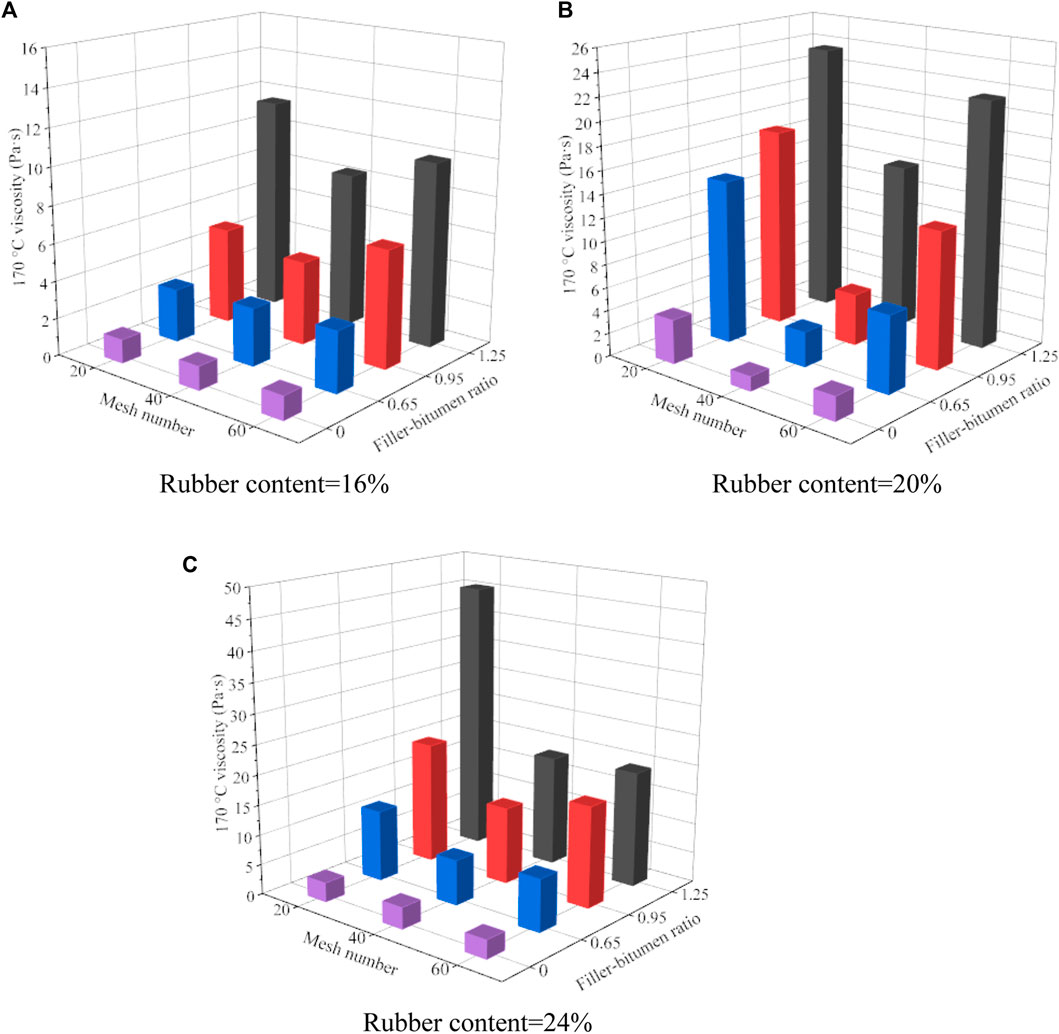
Figure 2. Effect of granulated rubber mesh number on viscosity of bitumen mastic at different rubber contents. Effect of granulated rubber mesh number on viscosity of bitumen mastic at different rubber contents: (A) Content = 16%; (B) Content = 20%; (C) Content = 24%.
3.3 Effect of filler-to-bitumen ratio
The ratio of filler to bitumen is one of the important factors affecting the viscosity of bitumen mastic modified with granulated rubber. Generally, when the ratio of granulated rubber powder increases, the density of granulated rubber modified bitumen mastic also increases. It is evident from Figure 3 that for granulated rubber modified bitumen mastic prepared with different mesh numbers and dosage of granulated rubber powder, the viscosity at 170°C shows an increasing trend as the filler-to-bitumen ratio increases. This is because granulated rubber powder has high molecular weight and viscosity, and its addition results in a rise in the viscosity of the bitumen system. The particles of granulated rubber powder form a three-dimensional network formation within the bitumen, thereby increasing the viscosity. In addition, the impact of the filler-to-bitumen ratio on the viscosity of granulated rubber-modified bitumen mastic is also associated with the mesh size of the granulated rubber powder. Generally, granulated rubber powder with greater particle dimension is easier to scatter in the bitumen, forming a more stable network structure, which results in a more pronounced rise in the viscosity of the bitumen mastic. Through comparison in Figure 3, it is also apparent that the viscosity of granulated rubber modified bitumen mastic prepared with 40 mesh granulated rubber powder increases or decreases with the change of filler to bitumen ratio less than that of 20 mesh and 60 mesh, indicating that, the properties of granulated rubber modified bitumen mastic readied from 40-mesh granulated rubber powder are relatively stable. It should be noted that changing the ratio of filler to bitumen will also affect other properties of granulated rubber modified bitumen mastic, attributes like flexibility and longevity. Therefore, when determining the proportion of filler to bitumen, the targeted viscosity of the bitumen mastic and other performance requirements need to be considered comprehensively.
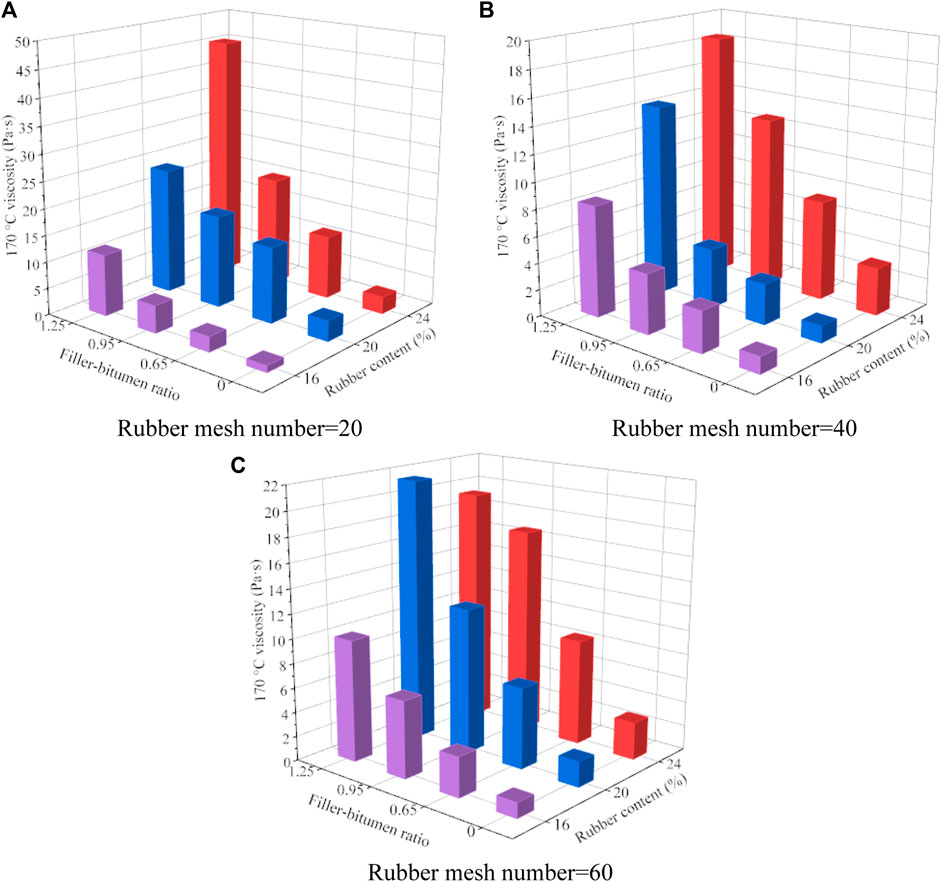
Figure 3. Effect of filler-to-bitumen ratio on viscosity of bitumen mastic at different rubber mesh number. Effect of filler-to-bitumen ratio on viscosity of bitumen mastic at different rubber mesh number: (A) Number = 20; (B) Number = 40; (C) Number = 60.
3.4 Effect of test temperature
In order to further explore the impact of the test temperature on the adhesion of granulated rubber modified bitumen mastic, this study extensively examined granulated rubber modified bitumen formulated with a 20% content of 40-mesh granulated rubber powder, and obtained the change trend of the viscosity of granulated rubber modified bitumen mastic with the proportion of filler to bitumen at various temperatures, as depicted in Figure 4. It is evident from the test that temperature is a crucial factor that influences viscosity of granulated rubber modified bitumen mastic. As illustrated in Figure 4A, with the increase of temperature, the density of granulated rubber modified bitumen mastic decreases exponentially or logarithmically. Upon reaching a designated temperature, the change of viscosity begins to stabilize. With the progressive elevation of temperature, the viscosity of bitumen mastic with different ratio of filler to bitumen tends to coincide, indicating that at a particular temperature level, the viscosity of granulated rubber modified bitumen mastic tends to align. The density of the bitumen mastic no longer varies with temperature. Therefore, in the bitumen mixture pavement construction process, special emphasis should be placed on the control of the construction temperature, the temperature is too small, the viscosity of the bitumen mastic is large, resulting in the construction of the bitumen mixture is difficult. The temperature is too large, the viscosity of the bitumen mastic is small, and part of the bitumen is easy to age, thus impacting the pavement performance of the bitumen mixture.
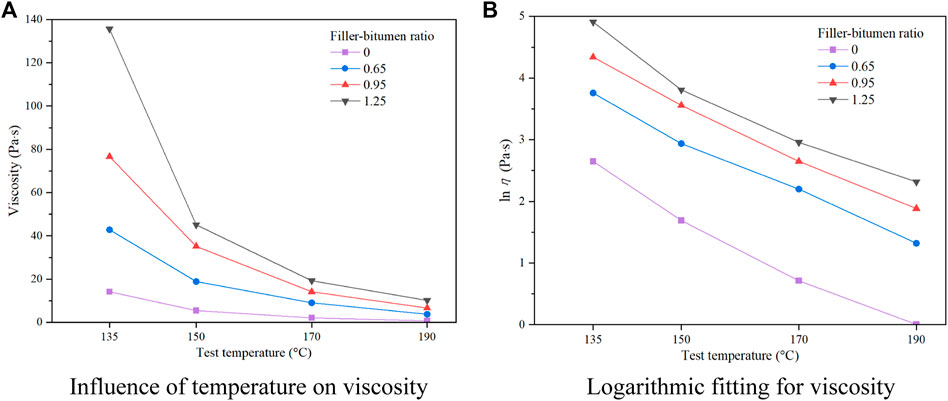
Figure 4. Viscosity results of granulated rubber modified bitumen mastic. Viscosity results of granulated rubber modified bitumen mastic: (A) Influence of temperature on viscosity; (B) Logarithmic fitting.
For the purpose of study, the variation law of the viscosity of granulated rubber modified bitumen mastic with temperature, the viscosity-temperature variation curves of granulated rubber modified bitumen mastic with 40 mesh and 20% ratio of filler to bitumen was fitted by semi-logarithmic coordinates:
where η represents density, T represents temperature, and a and b are curve fitting parameters. The value of b reflects the sensitivity of viscosity of granulated rubber modified bitumen mastic to temperature change. The greater b is, the more sensitive the density of bitumen mastic is to temperature change. The fitting curve for Eq. 1 is shown in Figure 4B.
The fitting equations and parameters of the above fitting curve are shown in Eqs 2–5. It is evident from the equations that the correlation values R2 of the fitted values hover around 0.99, indicating that the logarithmic function can well express the viscous-temperature variation characteristics of granulated rubber modified bitumen mastic at different temperatures. The b value corresponding to the fitting equation also escalates as the filler-to-bitumen ratio rises, showing that for the same granulated rubber modified bitumen mastic. As the ratio of filler to bitumen increases, the temperature sensitivity becomes more pronounced.
4 Influence analysis of preparation parameters on rheological property of granulated rubber modified bitumen mastic
Granulated rubber modified bitumen mastic plays a significant role in rubberized bitumen mixtures. Relative to ordinary bitumen mastic, granulated rubber modified bitumen mastic contains a large quantity of swelling granulated rubber powder. Mineral powder and granulated rubber powder adsorb free bitumen and increase the content of structural bitumen. The rheological property of bitumen mastic is the essential factor in affecting the performance of the bitumen mixture, so it is crucial to examine the rheological property of granulated rubber modified bitumen mastic.
4.1 Analysis of high-temperature rheological property based on DSR test
4.1.1 Impact of granulated rubber proportion
To study the effects of granulated rubber powder content on the high temperature capability of mastic, this paper conducted dynamic scanning of granulated rubber modified bitumen mastic with varying compositions, mesh numbers, and filler to bitumen ratios under test conditions of 70°C and 1.59 Hz. The changing trends of complex modulus, rutting factor as well as phase angle at 70°C with the granulated rubber content, mesh number, and ratio of filler to bitumen are illustrated in Figure 5.
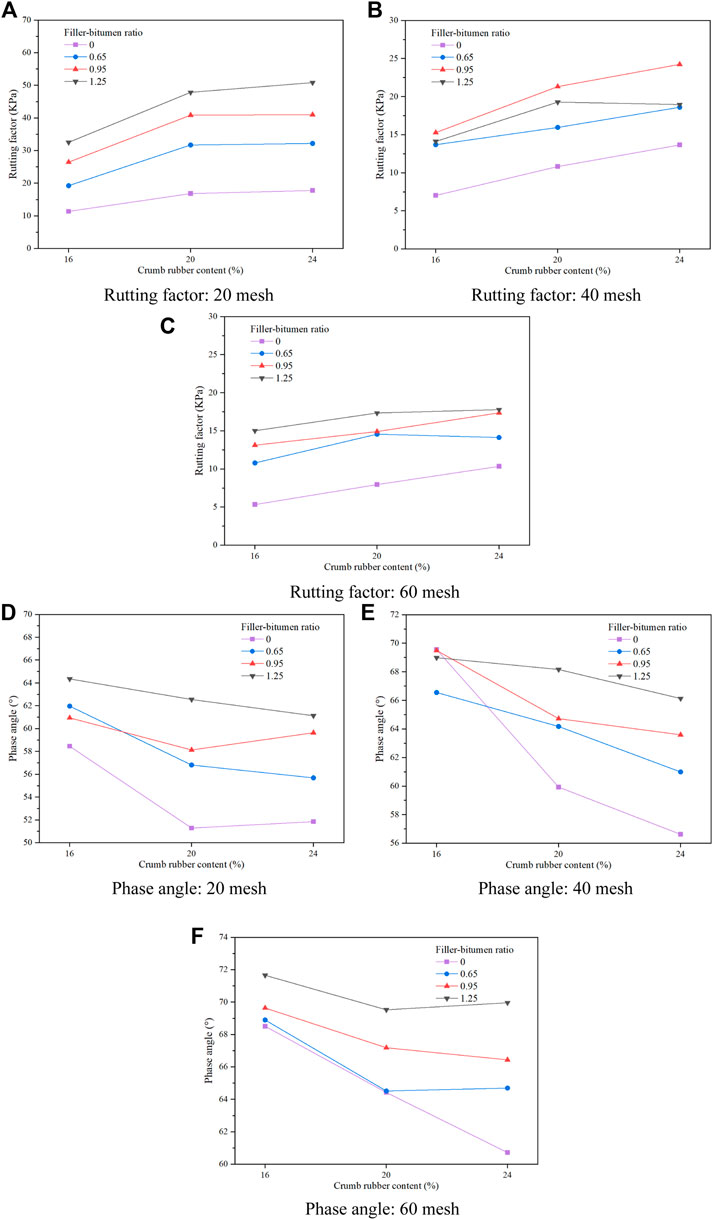
Figure 5. Influence of granulated rubber proportion concerning the rutting factor and phase angle of bitumen mastic. Influence of granulated rubber proportion concerning the rutting factor and phase angle of bitumen mastic: (A) Rutting factor: 20 mesh; (B) Rutting factor: 40 mesh; (C) Rutting factor: 60 mesh; (D) Phase angle: 20 mesh; (E) Phase angle: 40 mesh; (F) Phase angle: 60 mesh.
As can be observed from Figures 5A–C, the rutting factor (G*/sinδ) corresponding to the granulated rubber modified bitumen mastic with various mesh number and ratio of filler to bitumen basically showed an increasing trend with the content increases of granulated rubber powder. This is because rubber powder absorbs and swells in bitumen, which reduces the light components in bitumen and increases the gel film around rubber powder, thus improving the high temperature performance of cement (Wang et al., 2022). While only the rutting factor increased initially then decreased when the ratio of filler to bitumen of 40 mesh and 60 mesh granulated rubber modified bitumen mastic was 1.25. This suggests that rising the content of granulated rubber powder can improve its high-temperature rutting resistance to a certain extent, but along with the growth in content of granulated rubber powder, the growth range of G*/sinδ gradually decreases or even shows a trend of decline, which means that while the substance of granulated rubber powder is too large, it cannot further significantly enhance its high-temperature rutting resistance, because after the substance of granulated rubber powder exceeds the full swelling limit. Alongside the rise of the dosage, the swelling of granulated rubber powder is insufficient, and the desulfurization and degradation reactions are gradually weakened, leading to the improvement of high temperature capability is reduced or even weakened.
The phase angle serves as a relative indicator of viscosity and elastic deformation of bitumen, and the smaller the phase angle is, the nearer the bitumen approaches the elastomer. As is evident from Figures 5D–F, the phase angle of granulated rubber modified bitumen mastic gradually decreases concurrent with the growth of the content of granulated rubber powder, as well as the reduction rate gradually slows down as the content increases granulated rubber powder, suggesting that the addition of granulated rubber powder increases the elastic component of granulated rubber modified bitumen mastic. The elastic properties are gradually enhanced, and the increase in elastic properties is attenuated with the continual addition of granulated rubber powder.
4.1.2 Effect of granulated rubber mesh number
For the purpose of further study, the impact of mesh number of granulated rubber powder concerning rheological properties of granulated rubber modified bitumen mastic, dynamic shear rheological experiments were conducted on 20 mesh, 40 mesh and 60 mesh granulated rubber modified bitumen mastic with 20% content under the test conditions of 70°C and 1.59 Hz, and the experimental results were depicted in Figure 6. As illustrated in Figure 6 that the rutting factor progressively declines with the rise of mesh number of granulated rubber powder. This is mainly because when the size of the particles in granulated rubber powder is 20 mesh, the particle size is large, the swelling rate is slow, and it is not conducive to the dispersion in bitumen (Zheng et al., 2024). The overly high viscosity of granulated rubber modified bitumen mastic makes the rutting factor larger, but it is not conducive to the on-site construction. When the mesh number increases to 40 mesh, the granulated rubber powder is more prone to swelling reaction, and the density of granulated rubber particles in bitumen increase, which is conducive to forming a stable network structure and has a better rutting resistance. With the continuous rise in the mesh number of granulated rubber powder, that is, the granulated rubber particle size further decreases, although the granulated rubber particles are more likely to swell and disperse, but simultaneously, the desulfurization and cracking reaction of granulated rubber particles is intensified, destroying the stable network structure, and the resistance to high-temperature deformation is weakened.
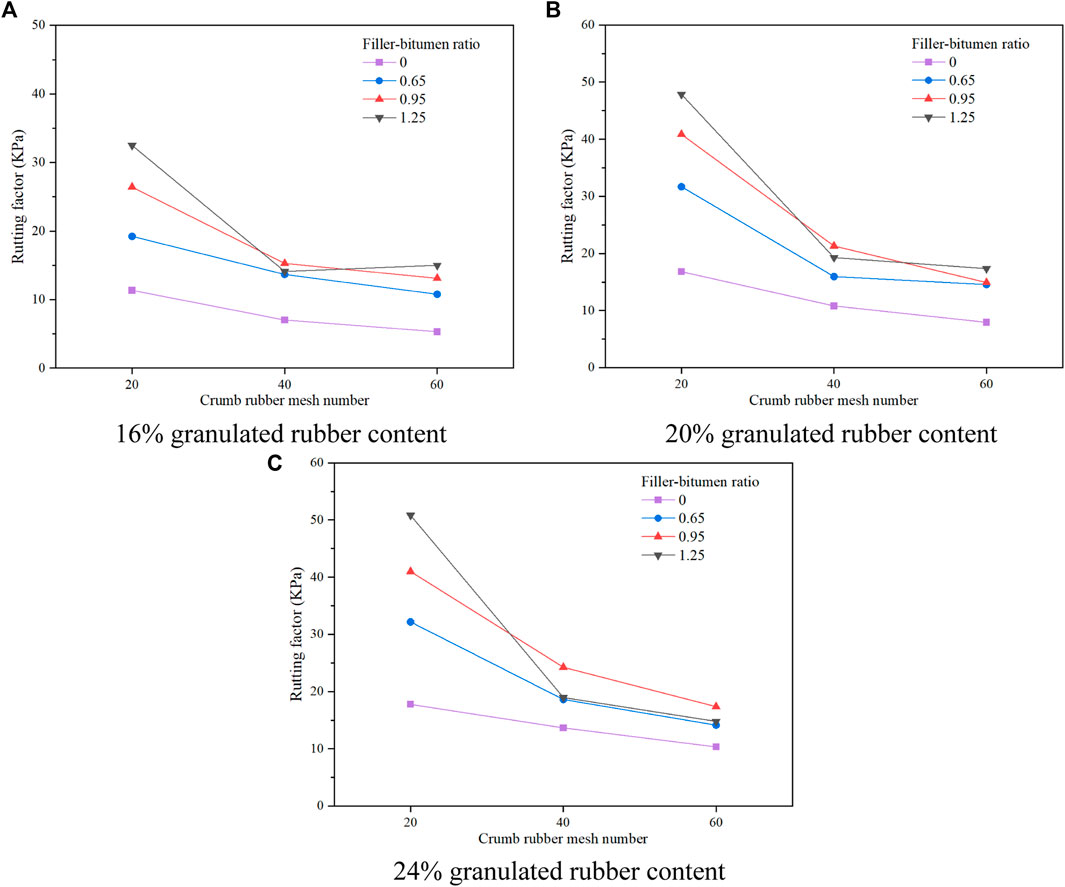
Figure 6. Influence of granulated rubber mesh number on the rutting factor of bitumen mastic. Influence of granulated rubber mesh number on the rutting factor of bitumen mastic: (A) Content = 16%; (B) Content = 20%; (C) Content = 24%.
4.1.3 Effect of filler to bitumen ratio
The impact of the proportion of filler to bitumen on the rutting factor of granulated rubber modified bitumen is complex, and it involves the interaction of multiple factors. The analysis focused on the effect of the filler-to-bitumen ratio on the rutting factor of granulated rubber modified bitumen. Through experimental research, this study measured the rutting performance of granulated rubber modified bitumen at different ratios of filler to bitumen and conducted data analysis. The study evidence suggests that the ratio of filler to bitumen profoundly affects the rutting factor of granulated rubber modified bitumen, as shown in Figure 7. The proportion of filler to bitumen can influence the deformation resistance of granulated rubber modified bitumen, thereby affecting the rutting factor. Increasing the mineral filler content may increase the rigidity of granulated rubber modified bitumen, making it more resistant to deformation. This reduces rutting as the highly rigid rubberized bitumen is better able to withstand traffic loads and reduces settlement. However, when the content of mineral filler is too high, the rutting factor starts to decrease. Generally, an appropriate addition of mineral filler can enhance the deformation resistance of granulated rubber modified bitumen, reducing the formation of rutting. This is because the addition of mineral powder can fill the voids in the bitumen, forming an interconnected skeleton form, increasing the material’s cohesion and stability, thus reducing deformation and settlement (Meng et al., 2023). Therefore, it is recommended to control the ratio of filler to bitumen as part of the planning for granulated rubber modified bitumen to achieve optimal rutting performance. This study provides scientific evidence for the planning and implementation of rubberized bitumen pavement.
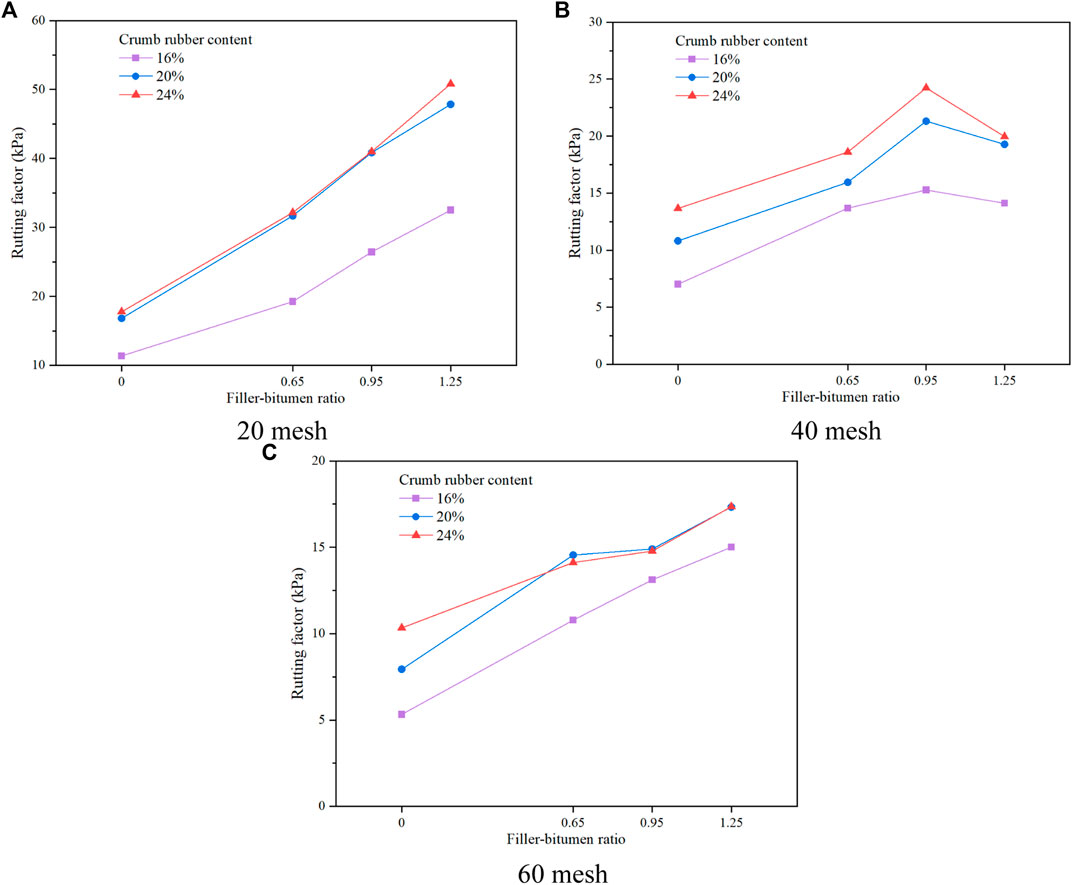
Figure 7. Influence of filler to bitumen ratio on the rutting factor of bitumen mastic. Influence of filler to bitumen ratio on the rutting factor of bitumen mastic: (A) 20 mesh; (B) 40 mesh; (C) 60 mesh.
4.1.4 Effect of test conditions
To fully understand the capability at elevated temperatures of granulated rubber modified bitumen mastic, temperature scanning at 64°C∼82°C and frequency scanning at 70°C were performed on the granulated rubber modified bitumen mastic with 20% composition of 40 mesh granulated rubber powder. The test results are illustrated in Figure 8.
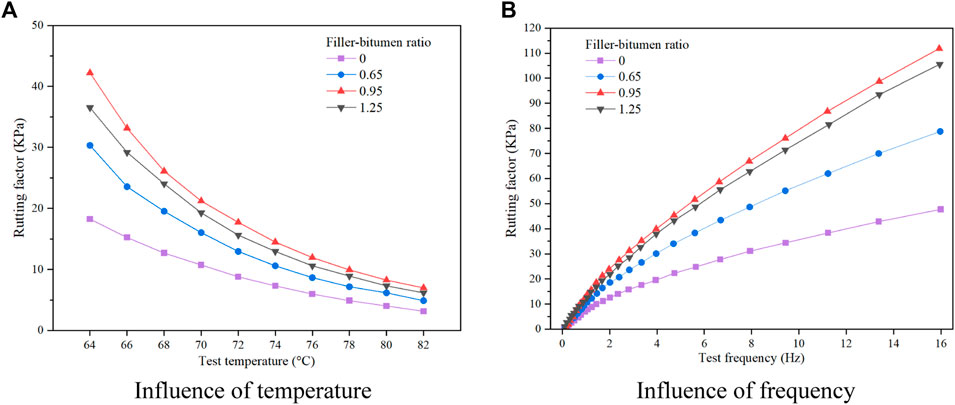
Figure 8. Influence of temperature and frequency on the rutting performance of bitumen mastic. Influence of temperature and frequency on the rutting performance of bitumen mastic: (A) Influence of temperature; (B) Influence of frequency.
G*/sinδ represents the permanent deformation resistance of bitumen material, which can be employed to judge the high temperature performance of bitumen mastic. The higher the G*/sinδ value, the better the elevated temperature performance. As depicted in Figure 8A, the rutting factor G*/sinδ of granulated rubber modified bitumen mastic with different ratio of filler to bitumen declines with the rise of temperature. The rutting factor of granulated rubber modified bitumen mastic at 0.95 filler concentration in bitumen is always in the maximum position, indicating granulated rubber modified bitumen mastic at 0.95 proportion of filler to bitumen exhibits superior rutting resistance in high temperatures than granulated rubber modified bitumen mastic. As shown in Figure 8B, the rutting factor of granulated rubber modified bitumen mastic rises with the increase of frequency. When the frequency is small, the rutting factor changes more sharply, and when the frequency increases to a certain value, the change is gradually gentle and presents a linear change. This view was also supported by the analysis in some studies (Sesay et al., 2023; Xue et al., 2023). Based on the above test result and analysis, the relationship between frequency and rutting resistance factor can be obtained by linear and polynomial fitting, as shown in Eqs 6–9.
The fitting results in Eqs 6–9 indicate that G*/sinδ and angular frequency satisfy a simple linear relationship, y = A + Bω + Cω2, where y represents G*/sinδ, ω represents angular frequency, and A and B denote fitting factors. The correlation coefficients are all above 0.99, and the more terms in the equation, the larger the R2 value, and the more accurate the fitting results. At any frequency, it is also evident from the figure, the ratio 0.95 of filler to bitumen has the largest rutting factor than granulated rubber modified bitumen mastic, which also indicates that its rutting resistance is the best.
4.2 Analysis of low-temperature rheological property based on BBR test
4.2.1 Effect of granulated rubber proportion
Using 20 mesh, 40 mesh and 60 mesh granulated rubber powder, granulated rubber modified bitumen was produced by blending granulated rubber powder in proportions of 16%, 20%, and 24%, and then mixed with mineral powder according to different ratio of filler to bitumen (0.65, 0.95 and 1.25) to make granulated rubber modified bitumen mastic beams. Then BBR was used to test granulated rubber modified bitumen with varying ratio of filler to bitumen at −12°C. The results are depicted in Figure 9. It is evident from Figure 9 that the stiffness modulus of the granulated rubber modified bitumen mastic decreases with the increase in granulated rubber powder content, while the slope of the creep curve increases slowly. This shows that with the increase in granulated rubber powder content, the brittleness of granulated rubber modified bitumen mastic decreases, the stress relaxation ability increases, as well as the low temperature cracking resistance increases. This is because the incorporation of granulated rubber powder can increase the elastic component in granulated rubber modified bitumen mastic, as a result enhancing the elasticity and shear resilience of the modified bitumen mastic. In low-temperature environments, granulated rubber powder can act as a filler in bitumen mastic, increasing the density of the granulated rubber modified bitumen mastic.
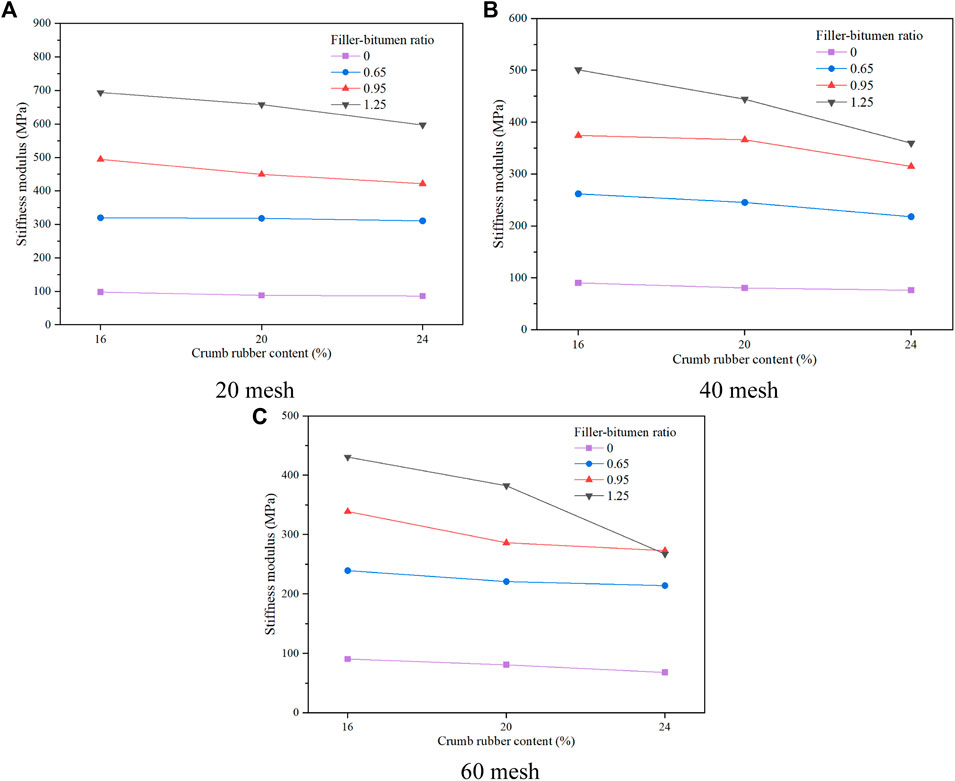
Figure 9. Influence of granulated rubber proportion on the inflexibility modulus of bitumen mastic. Influence of granulated rubber proportion on the inflexibility modulus of bitumen mastic: (A) 20 mesh; (B) 40 mesh; (C) 60 mesh.
4.2.2 Influence of granulated rubber mesh number
The granulated rubber mesh number leads to a considerable impact on the low-temperature rheological properties of granulated rubber modified bitumen mastic. Figure 10 illustrates that the stiffness modulus of granulated rubber modified bitumen mastic decreases. As the quantity of the mesh number of granulated rubber powder, that is, the larger-scale the mesh number of granulated rubber powder, the miniature the stiffness. This demonstrates that the added granulated rubber powder has small particle size and strong deformation ability at low temperature, which contributes to enhancing the resistance of bitumen mastic to low temperature cracking. A larger mesh number of granulated rubber powder implies smaller particles, which can better bond with the bitumen mastic. Additionally, smaller particles of granulated rubber powder form a more uniform dispersed state in granulated rubber modified bitumen mastic, thereby effectively improving its flowability and toughness. On the other hand, a smaller mesh number of granulated rubber powder means larger particles, which can cause particle aggregation and hinder uniform dispersion in the bitumen mastic. As a result, a larger particle size of granulated rubber powder decreases the flowability and toughness of granulated rubber modified bitumen mastic. A smaller mesh number of granulated rubber powder contributes to enhanced rheological properties at low temperatures of granulated rubber modified bitumen mastic, while a larger granulated rubber mesh number may reduce these properties. It can be seen that to enhance the low temperature crack resistance of granulated rubber modified bitumen mastic, The utilization of finer granulated rubber powder (i.e., larger mesh) is suitable to prepare granulated rubber modified bitumen.
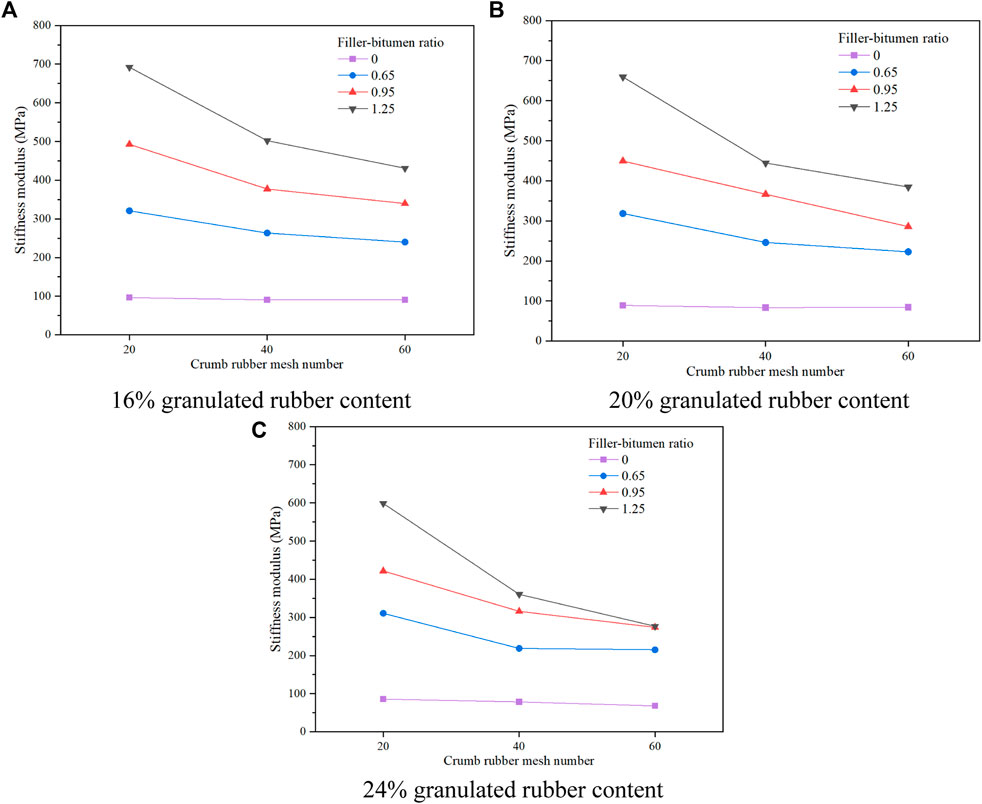
Figure 10. Influence of granulated rubber mesh number on the rigidity modulus of bitumen mastic. Influence of granulated rubber mesh number on the rigidity modulus of bitumen mastic: (A) Content = 16%; (B) Content = 20%; (C) Content = 24%.
4.2.3 Effect of ratio of filler to bitumen
From Figure 11, it is evident that the stiffness modulus of granulated rubber modified bitumen mastic progressively rises with the increase of ratio of filler to bitumen. The results show that the low temperature deformation ability and low temperature cracking resistance of granulated rubber modified bitumen mastic decrease gradually as the ratio of filler to bitumen increases. This is because, after mixing granulated rubber modified bitumen with mineral powder, the mineral powder adsorbs the bitumen, forming layered structural bitumen on the surface, the bitumen outside the structural layer is free bitumen, structural bitumen has a strong bonding force, promoting the mineral powder particles to contact each other, hindering free flow. Meanwhile, the addition of mineral powder can fill the voids in the granulated rubber modified bitumen mastic and increase the viscosity and rigidity of the bitumen mastic. The addition of mineral powder can also enhance the surface area and deformability of the bitumen mastic, thereby increasing the strength and stability of the bitumen mastic. Corresponding to the increase in mineral powder, the amount of structural bitumen increases, the amount of free bitumen decreases, the fluidity of mastic decreases, the flexibility becomes worse, the stiffness increases, and the deformation ability decreases. However, the ratio of filler to bitumen should not be too high. This is because an elevated levels of mineral powder can result in particle stacking and agglomeration in the bitumen mastic, reducing the strength and viscosity of the bitumen mastic. In summary, the proportion of filler to bitumen has a significantly affects the low-temperature rheological properties of granulated rubber modified bitumen mastic. Therefore, the appropriate ratio of filler to bitumen should be selected based on specific circumstances in practical applications.

Figure 11. Impact of filler-to-bitumen ratio on the rigidity modulus of bitumen mastic. Impact of filler-to-bitumen ratio on the rigidity modulus of bitumen mastic: (A) 20 mesh; (B) 40 mesh; (C) 60 mesh.
5 Grey relation analysis between preparation parameter and rheological properties of granulated rubber modified bitumen mastic
For the purpose of facilitating the study of the correlation between mesh number, content of granulated rubber powder and rheological properties and ratio of filler to bitumen of granulated rubber modified bitumen mastic, the 70°C rutting factor and −12°C stiffness modulus of different granulated rubber modified bitumen mastic specimens as well as the test data were summarized, the findings were displayed in Table 4.
5.1 Grey relation analysis of high temperature rheological properties
In this study, 70°C rutting factor was chosen as the reference sequence, and the granulated rubber powder mesh number (R1), content (R2), and filler to bitumen ratio (R3) were used as the comparison sequence. The dimensionless quantification on the data in Table 4 was performed, and then the grey relation coefficient could be calculated. The computation outcomes are displayed in Table 5.
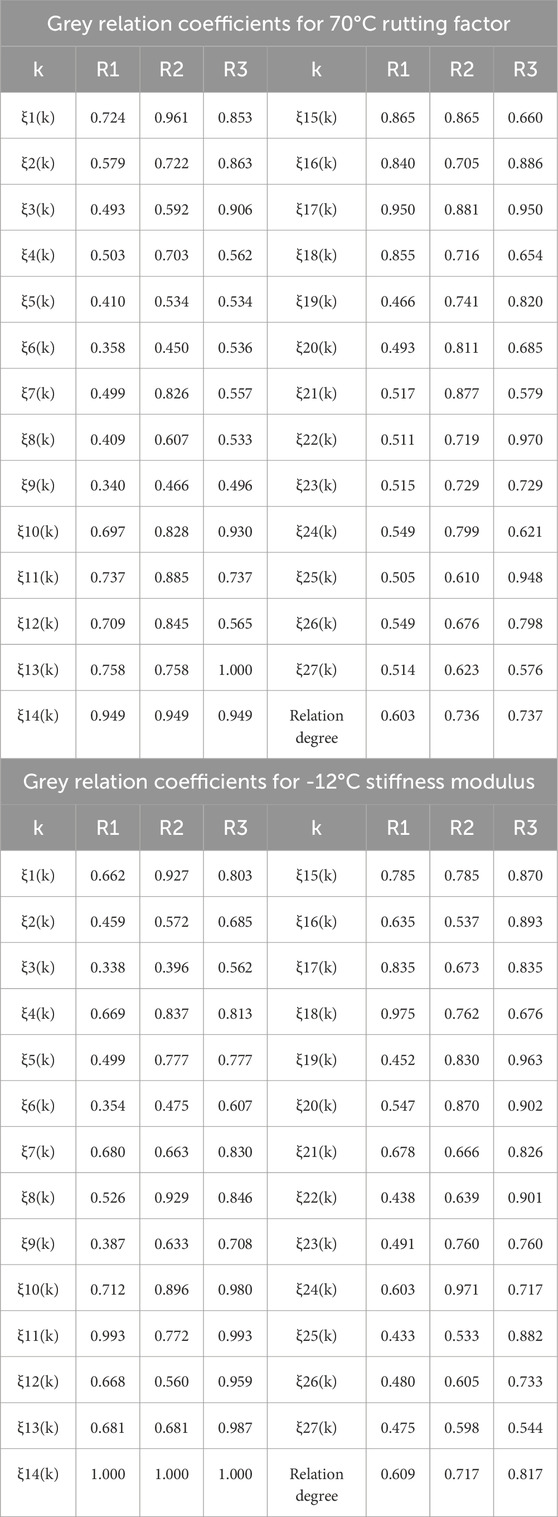
Table 5. Grey relation coefficients of various influencing factors for 70°C rutting factor and −12°C stiffness modulus.
From the grey relation between the factors in Table 5 and 70°C rutting factor, it is evident that the degree of impact of every parameter on the high-temperature capability of granulated rubber modified bitumen mastic is: ratio of filler to bitumen > granulated rubber content > granulated rubber mesh number. The comparative analysis of data shows that within the spectrum of different factors, the influence of ratio of filler to bitumen and granulated rubber powder content on the high-temperature capability of granulated rubber modified bitumen mastic is equivalent, while the influence of granulated rubber powder mesh number on the high-temperature capability of granulated rubber modified bitumen mastic is relatively low. Therefore, from the perspective of improving the high-temperature rheological characteristics of granulated rubber modified bitumen mastic, the first step is to control the ratio of filler to bitumen within a certain range. At the same time, under the premise of meeting the process requirements, increasing the amount of granulated rubber powder appropriately is beneficial for enhancing the high-temperature deformation resistance of granulated rubber modified bitumen mastic.
5.2 Grey relation analysis of high temperature rheological properties
The −12°C stiffness modulus was selected as the reference sequence, the granulated rubber powder mesh number (R1), content (R2), and ratio of filler to bitumen (R3) were respectively taken as the comparison series, and the data in Table 5 are subjected to dimensionless quantization, and then the grey relation coefficient is calculated. The findings are displayed in Table 5. It is evident from the gray correlation degree between each factor and the stiffness modulus of −12°C in Table 5 that the influence degree of each factor on the low temperature capability of granulated rubber modified bitumen mastic is as follows: ratio of filler to bitumen > granulated rubber content > granulated rubber mesh number. The comparative analysis of the data shows that the proportion of filler to bitumen has the greatest influence on the low temperature performance of granulated rubber modified bitumen mastic, followed by the substance of granulated rubber powder, and the mesh number of granulated rubber powder has a low influence. Therefore, in order to ensure that the granulated rubber modified bitumen mastic has outstanding low temperature capability, the proportion of filler to bitumen should not be too large. At the same time, under the premise of satisfying the process, as much granulated rubber powder is used as possible.
6 Conclusion
This study emphasized the assessment of performance of granulated rubber modified bitumen mastic in accordance with rheological properties, taking into consideration the rubber content, mesh number, and ratio of filler to bitumen. The findings of this research offer valuable perspectives on the advancement and enhancement of granulated rubber modified bitumen mixtures. The following key findings were observed.
(1) As the rubber content increases, the density of granulated rubber modified bitumen mastic also raise. When the rubber content exceeds 20%, the viscosity of the mastic shows a significant increase, which is unfavorable for construction.
(2) It is imperative to regulate the bitumen pavement construction temperature. If the temperature is too low, the mastic viscosity becomes high, leading to construction difficulties. On the contrary, if the temperature is too high, the mastic viscosity becomes low, and some of the bitumen may age, affecting the pavement performance. A higher filler-bitumen ratio increases its temperature sensitivity, making it more susceptible to changes in construction temperature.
(3) Raising the rubber content to a specific degree can improve the resistance to rutting at high temperatures. However, when the rubber content exceeds an optimal level, inadequate swelling of the rubber particles can lead to a decrease or even a weakening in the enhancement of high-temperature performance.
(4) The rutting factor gradually reduces with a raise in the rubber mesh number. Large particle volume results in slow swelling rates and poor dispersion in the bitumen, while small particle volume intensifies desulfurization and cracking reactions, disrupting the stable network structure and reducing the high-temperature deformation resistance. The bitumen mastic with a filler-to-bitumen ratio of 0.95 demonstrates the most robust resistance to rutting under high temperatures.
(5) A higher rubber content and larger mesh number correspond to stronger low-temperature crack resistance of bitumen mastic. As the filler-bitumen proportion increases, the low-temperature deformation capacity of the mastic gradually decreases, leading to diminished resistance to low-temperature cracking.
(6) The ratio of filler to bitumen exerts the most significant influence on the rheological properties of bitumen mastic at both high and low temperatures, followed by the rubber content, while the rubber mesh number has a relatively lower impact. It is important to control the filler-bitumen proportion to avoid excessive values. The 20% rubber content, 40 mesh, and filler-to-bitumen ratio of 0.95 were recommended. Whenever possible, a higher rubber content should be used while meeting the process requirements.
Overall, this study highlights the importance of optimizing the rubber content, mesh number, and ratio of filler to bitumen in granulated rubber modified bitumen mastic. The findings suggest that an appropriate combination of these factors can improve the rheological properties of the bitumen mastic, resulting in improved performance and endurance of the bitumen pavement. Future research should focus on further investigating the extended-term functionality and sustainability of granulated rubber modified bitumen mixtures to fully understand their potential benefits and limitations. In addition, the microscopic mechanism of rubber powder modified bitumen needs to be deeply analyzed.
Data availability statement
The original contributions presented in the study are included in the article/Supplementary material, further inquiries can be directed to the corresponding authors.
Author contributions
HZ: Conceptualization, Funding acquisition, Supervision, Writing–review and editing. YZ: Data curation, Formal Analysis, Methodology, Writing–original draft. JC: Data curation, Investigation, Writing–review and editing. WL: Data curation, Investigation, Writing–review and editing. WW: Data curation, Formal Analysis, Methodology, Writing–original draft.
Funding
The author(s) declare that financial support was received for the research, authorship, and/or publication of this article. This research was funded by the Scientific Research Project of the Department of Education of Jilin Province (grant number: JJKH20241300KJ).
Acknowledgments
The authors are grateful for the support.
Conflict of interest
Authors HZ, YZ, and JC were employed by Guangxi Transportation Science and Technology Group Co Ltd.
The remaining authors declare that the research was conducted in the absence of any commercial or financial relationships that could be construed as a potential conflict of interest.
Publisher’s note
All claims expressed in this article are solely those of the authors and do not necessarily represent those of their affiliated organizations, or those of the publisher, the editors and the reviewers. Any product that may be evaluated in this article, or claim that may be made by its manufacturer, is not guaranteed or endorsed by the publisher.
References
Ameli, A., Maher, J., Mosavi, A., Nabipour, N., Babagoli, R., and Norouzi, N. (2020). Performance evaluation of binders and stone matrix asphalt (SMA) mixtures modified by ground tire rubber (GTR), waste polyethylene terephthalate (PET) and anti stripping agents (ASAs). Constr. Build. Mater. 251, 118932. doi:10.1016/j.conbuildmat.2020.118932
Apeagyei, A. K. (2011). Laboratory evaluation of antioxidants for asphalt binders. Constr. Build. Mater. 25, 47–53. doi:10.1016/j.conbuildmat.2010.06.058
Ding, X. H., Huang, F. Y., Rath, P., Ye, Z. Y., Buttlar, W. G., and Ma, T. (2023). Comparative fracture resistance assessment of rubber-modified asphalt mortar based on meso-and macro-mechanical analysis. Int. J. Pavement Eng. 24. doi:10.1080/10298436.2023.2265032
Duan, K. X., Wang, C. H., Liu, J. K., Song, L., Chen, Q., and Chen, Y. Z. (2022). Research progress and performance evaluation of crumb-rubber-modified asphalts and their mixtures. Constr. Build. Mater. 361, 129687. doi:10.1016/j.conbuildmat.2022.129687
Gao, M. X., Chen, Y. L., Fan, C. H., and Li, M. J. (2022). Molecular dynamics study on the compatibility of asphalt and rubber powder with different component contents. Acs Omega 7, 36157–36164. doi:10.1021/acsomega.2c02813
Gergó, P., Holló, A., and Geiger, A. (2017). Rheological investigation of rubber bitumen containing various waxes as warm mix additive. Stud. Univ. Babes-Bolyai Chem. 62, 247–257. doi:10.24193/subbchem.2017.2.19
Gulzar, S., and Underwood, B. S. (2020). Nonlinear viscoelastic response of crumb rubber modified asphalt binder under large strains. Transp. Res. Rec. 2674, 139–149. doi:10.1177/0361198120907097
Hajikarimi, P., Hosseini, A. S., Tehrani, F. F., Rahi, M., Absi, J., and Moghadas Nejad, F. (2022). Heterogeneous visco-hyperelastic numerical modelling of crumb rubber-modified asphalt binders. Int. J. Pavement Eng. 23, 1500–1511. doi:10.1080/10298436.2020.1808652
He, Y. Z., Wang, Q. G., Zhang, J. P., Li, Y., He, H. Q., and Huang, G. J. (2023). Foamed crumb rubber asphalt binder: preparation, rheological properties and adhesion characteristics. J. Clean. Prod. 396, 136516. doi:10.1016/j.jclepro.2023.136516
Hemida, A., and Abdelrahman, M. (2020). Monitoring separation tendency of partial asphalt replacement by crumb rubber modifier and guayule resin. Constr. Build. Mater. 251, 118967. doi:10.1016/j.conbuildmat.2020.118967
Hemida, A., and Abdelrahman, M. (2021). Component analysis of bio-asphalt binder using crumb rubber modifier and guayule resin as an innovative asphalt replacer. Resour. Conservation Recycl. 169, 105486. doi:10.1016/j.resconrec.2021.105486
Hosseinnezhad, S., Kabir, S. F., Oldham, D., Mousavi, M., and Fini, E. H. (2019). Surface functionalization of rubber particles to reduce phase separation in rubberized asphalt for sustainable construction. J. Clean. Prod. 225, 82–89. doi:10.1016/j.jclepro.2019.03.219
Huang, S. H. (2023). Study on rheological properties of asphalt modified by different types of anti-stripping agents and rubber. J. China and Foreign Highw. 43, 254–258. doi:10.14048/j.issn.1671-2579.2023.05.043
Huang, W. D., Lin, P., Tang, N. P., Hu, J. Y., and Xiao, F. P. (2017). Effect of crumb rubber degradation on components distribution and rheological properties of Terminal Blend rubberized asphalt binder. Constr. Build. Mater. 151, 897–906. doi:10.1016/j.conbuildmat.2017.03.229
Karakurt, C. (2015). Microstructure properties of waste tire rubber composites: an overview. J. Material Cycles Waste Manag. 17, 422–433. doi:10.1007/s10163-014-0263-9
Kim, H., and Lee, S. J. (2013). Laboratory investigation of different standards of phase separation in crumb rubber modified asphalt binders. J. Mater. Civ. Eng. 25, 1975–1978. doi:10.1061/(asce)mt.1943-5533.0000751
Kumar, A., Choudhary, R., and Kumar, A. (2022a). Rheological, mechanical, and chemical characterization of asphalt binders and mixtures with waste tire and plastic pyrolytic chars. J. Mater. Civ. Eng. 34. doi:10.1061/(asce)mt.1943-5533.0004234
Kumar, A., Choudhary, R., and Kumar, A. (2022b). Storage stability of waste tire pyrolytic char-modified asphalt binders: rheological and chemical characterization. J. Mater. Civ. Eng. 34. doi:10.1061/(asce)mt.1943-5533.0004129
Li, J. Q. (2023). Effect of wax-based warm mix additives on rutting and fatigue performance of waste crumb rubber modified asphalt. J. China and Foreign Highw. 43, 230–235. doi:10.14048/j.issn.1671-2579.2023.05.039
Li, T. G., Qiao, W. Y., Wang, Y., and Wu, S. T. (2023). Research on the performance and application of solubilized adhesive power modified asphalt mixture. J. Munic. Technol. 41, 207–212. doi:10.19922/j.1009-7767.2023.11.207
Meng, Y. J., Lai, J., Ling, L. S., Zhang, C. Y., Chen, J., and Zhu, J. (2023). Preparation of an eco-friendly de-icing filler and its effects on the performance of different asphalt mastic. Constr. Build. Mater. 364, 129967. doi:10.1016/j.conbuildmat.2022.129967
Neto, S. a.D., Farias, M. M., Pais, J. C., Pereira, P. a.A., and Sousa, J. B. (2006). Influence of crumb rubber and digestion time on the asphalt rubber binders. Road Mater. Pavement Des. 7, 131–148. doi:10.3166/rmpd.7.131-148
Noura, S., Al-Sabaeei, A. M., Safaeldeen, G. I., Muniandy, R., and Carter, A. (2021). Evaluation of measured and predicted resilient modulus of rubberized Stone Mastic Asphalt (SMA) modified with truck tire rubber powder. Case Stud. Constr. Mater. 15, e00633. doi:10.1016/j.cscm.2021.e00633
Pei, Y., Jiang, S. Q., Ding, Z., Cheng, L. D., Li, P. L., and Jiang, X. M. (2023). Preparation and performance analysis of high-viscosity asphalt containing high-content SBS and crumb rubber by oxygen-free high-temperature treatment. Constr. Build. Mater. 402, 132763. doi:10.1016/j.conbuildmat.2023.132763
Sesay, T., You, Q. L., Chuan, J., Qiao, H. L., Zhang, H. L., and Tian, S. T. (2023). High and intermediate temperature performance of warm asphalt rubber containing conventional warm mix additives and novel chemical surfactant. Constr. Build. Mater. 394, 132214. doi:10.1016/j.conbuildmat.2023.132214
Sun, L. J., Wen, Y., Liu, Q., Li, D., Lyu, L., Pei, J. Z., et al. (2021). A laboratory investigation into the effect of waste non-tire rubber particles on the performance properties of terminal blend rubberized asphalt binders. Constr. Build. Mater. 313, 125409. doi:10.1016/j.conbuildmat.2021.125409
Wang, S., Huang, W. D., Liu, X. Y., and Lin, P. (2022). Influence of high content crumb rubber and different preparation methods on properties of asphalt under different aging conditions: chemical properties, rheological properties, and fatigue performance. Constr. Build. Mater. 327, 126937. doi:10.1016/j.conbuildmat.2022.126937
Wang, S. Q., Gao, Y., Yan, K. Z., You, L. Y., Jia, Y. S., Dai, X. W., et al. (2021). Effect of long-term aging on waste tire rubber and amorphous poly alpha olefin compound modified asphalt binder and its mixtures. Constr. Build. Mater. 272, 121667. doi:10.1016/j.conbuildmat.2020.121667
Xie, E. L., Xiao, X., Hou, J. N., Zhou, C. H., and Li, P. (2023). Effects of water-light coupling aging on performance of crumb rubber modified asphalt. Highw. Eng. J. 48, 154–160. doi:10.19782/j.cnki.1674-0610.2023.03.022
Xing, C. W., Li, M. C., Liu, L. Y., Lu, R., Liu, N., Wu, W. J., et al. (2023). A comprehensive review on the blending condition between virgin and RAP asphalt binders in hot recycled asphalt mixtures: mechanisms, evaluation methods, and influencing factors. J. Clean. Prod. 398, 136515. doi:10.1016/j.jclepro.2023.136515
Xu, G., Kong, P. P., Yu, Y. H., Yang, J. Y., Zhu, M. H., and Chen, X. H. (2022). Rheological properties of rubber modified asphalt as function of waste tire rubber reclaiming degree. J. Clean. Prod. 332, 130113. doi:10.1016/j.jclepro.2021.130113
Xue, Y. Y., Ge, D. D., Lv, S. T., Duan, D. F., and Deng, Y. J. (2023). Evaluation of asphalt modified with bio-oil and high rubber content: low temperature and short mixing time production condition. Constr. Build. Mater. 408, 133656. doi:10.1016/j.conbuildmat.2023.133656
Yan, K. Z., Xu, H. B., and You, L. Y. (2015). Rheological properties of asphalts modified by waste tire rubber and reclaimed low density polyethylene. Constr. Build. Mater. 83, 143–149. doi:10.1016/j.conbuildmat.2015.02.092
Yu, H. Y., Leng, Z., Zhou, Z. Y., Shih, K. M., Xiao, F. P., and Gao, Z. M. (2017). Optimization of preparation procedure of liquid warm mix additive modified asphalt rubber. J. Clean. Prod. 141, 336–345. doi:10.1016/j.jclepro.2016.09.043
Yucel, A. O., and Ozturk, H. I. (2023). Evaluation of mortar film thickness of dry process crumb rubber modified warm mix asphalt concrete utilizing 2-dimensional images. Constr. Build. Mater. 409, 133959. doi:10.1016/j.conbuildmat.2023.133959
Zhang, L., Wang, H. B., Zhang, C. P., and Wang, S. F. (2023). Laboratory testing and field application of devulcanized rubber/SBS composite modified asphalt. Case Stud. Constr. Mater. 19, e02285. doi:10.1016/j.cscm.2023.e02285
Zheng, Y. Y., Han, S., Zhang, C. C., Luo, Y. D., and Men, C. (2024). Preparation and application of rubber modified emulsified asphalt. Constr. Build. Mater. 411, 134540. doi:10.1016/j.conbuildmat.2023.134540
Keywords: waste rubber modified bitumen, rheological properties, rubber content, mesh number, filler-to-bitumen ratio, pavement engineering
Citation: Zhang H, Zhang Y, Chen J, Liu W and Wang W (2024) Influence of preparation parameters on rheological properties and relation analysis of waste rubber modified bitumen mastic. Front. Mater. 11:1435814. doi: 10.3389/fmats.2024.1435814
Received: 21 May 2024; Accepted: 20 June 2024;
Published: 09 July 2024.
Edited by:
Xiaolong Sun, Guangdong University of Technology, ChinaReviewed by:
Zepeng Fan, Harbin Institute of Technology, ChinaZongwu Chen, China University of Geosciences Wuhan, China
Copyright © 2024 Zhang, Zhang, Chen, Liu and Wang. This is an open-access article distributed under the terms of the Creative Commons Attribution License (CC BY). The use, distribution or reproduction in other forums is permitted, provided the original author(s) and the copyright owner(s) are credited and that the original publication in this journal is cited, in accordance with accepted academic practice. No use, distribution or reproduction is permitted which does not comply with these terms.
*Correspondence: Yangpeng Zhang, eWFuZ3Blbmd6MTZAbWFpbHMuamx1LmVkdS5jbg==; Wensheng Wang, d2FuZ3dzQGpsdS5lZHUuY24=