- 1University Lille, IMT Nord Europe University Artois, Yncrea Hauts de France, Laboratoire de Génie Civil et géo-Environnement, Lille, France
- 2IMT Nord Europe, Institut Mines-Télécom, University Lille, CERI Matériaux et Procédés, Lille, France
Introduction: Glass fibers with polyester resin structural composites are highly sought after in many sectors such as transportation industries, thanks to their low density and fairly good mechanical properties. However, their end-of-life management is not yet satisfactory. Composites mostly end in energy recovery in the best-case scenario or, worse, in landfills. Transformation into shreds and powders for reuse as a new source of raw material for the construction sector (concrete) is an economically and environmentally attractive recovery solution. The present study investigates the development of a concrete filled with glass/polyester composite shreds.
Methods: To this end, rheological (cone spread) and physico-mechanical (density and mechanical strength in flexion and compression) characterization tests were carried out. Several mix designs were tested in order to understand the impact of introducing composite shreds as a substitute for sand. Composite shreds were introduced in the following ratios by volume: 0, 1, 1.5, 2, 2.5, 3, and 7% with water and cement ratio equal to 0.5, 0.6, and 0.7.
Results and discussion: The results obtained indicate that workability decreases with the substitution of sand by shreds. For a substitution of sand by shreds of 2%, it is relatively small, and the pouring of the mortar is still feasible. The decrease can be attributed to the water absorption of the composite shreds. Concerning mechanical results, for formulations with a substitution percentage of composite shreds lower than 3%, the mechanical strength (both compression test and flexure test) is slightly higher than that of the reference sample. The increase in compressive strength that can be observed is at its maximum, equal to 10%, compared to that of the reference sample. These results are in line with density results, which are also slightly higher than that of the reference sample. This effect can be attributed to water absorption of composite shreds and the filling effect of the powders. For a percentage of substitution equal to 7%, the mechanical strength is lower than that of the reference sample (30% decrease), with a compressive strength equal to 33 MPa (47 MPa for the reference sample). For this percentage of substitution equal to 7%, a decrease in density is also observed (6% decrease) and can be explained by the porosity created by the incorporation of the composite shreds into the mortar.
1 Introduction
The amount of polymer composites produced was estimated to be more than 12 million tons in Europe in 2021 (Jec observer, 2022). They comprise 15 application sectors and are widely used in the field of transport. However, their end-of-life management is a real issue as landfill is no longer a solution since 1 July 2002 (Agence-rhone-alpes, 2003). One of the first recovery solutions was energy valorization. It presents a load-added value compared to material valorization. Recycling solutions, which are preferred to energy valorization, are more challenging for thermoset resin composites such as epoxy or polyester than for thermoplastic matrix composites. Techniques such as solvolysis, thermolysis, and pyrolysis have been used to separate fibers from the resin (Chayma Chaabani, 2017; Crepin, 2021). They are more commonly used for carbon fibers (mostly associated with epoxy resin) as they are less economical for glass fibers (polyester resin). For glass fiber (in polyester resin) composites, processing into shreds and powders for re-use as a new source of raw material seems to be a better solution for valorization (Agogue et al., 2022).
In addition to the problem of managing polymer composite waste, the construction sector consumes large quantities of non-renewable raw materials such as sand extracted from quarries. Four hundred million tons of granular materials are consumed in France every year (Nature-action, 2019; Kiema, 2023). In order to reduce the environmental impact of this sector, the use of composite shreds (glass fibers/polyester resin) as a substitute for sand could be an interesting solution. Several studies have investigated the technical feasibility of this solution for various civil engineering applications (Sebaibi, 2010; Ben Zaouche, 2020; Elmouden, 2021; Tao et al., 2023; Ganesan et al., 2014), (Correia et al., 2011; Rodin et al., 2018).
The reincorporation of composite shreds into a resin matrix for the manufacture of a fiberglass–polyester resin composite will be studied as part of this research. This solution would enable recycling within the framework of the circular economy. Blagojević et al. (2020) presents an overview of the various studies that have developed such a solution. The material developed enables the manufacture of reliable products that meet virtually all design criteria. The target applications are for indoor environments.
In the building industry, the use of fibers as reinforcement in concrete is a well-known but relatively recent approach. It offers economic, ecological, and technical advantages. The considered fibers are of different types, such as metal, flax, and even glass. They are generally characterized by the following properties: good adhesion to the matrix, controlled lengths, good resistance to moisture and corrosion, and relatively low thermal conductivity. Fiber-reinforced concrete continues to be studied in order to improve its properties and gain a better understanding of them (Sadoun et al., 2019; Ahmad et al., 2022). The results of these studies indicate the effects of incorporating composite shreds into concrete/mortar.
The use of recycled shred composites (glass fiber in polyester resin) in a mineral matrix can thus present a high potential for valorization. Nevertheless, due to the presence of the remaining cured polyester resin and the shredding process, heterogeneity in size and shape and reduced mechanical properties compared to virgin glass fibers are expected. The literature findings indicate that the powdery residue contains a high proportion of fillers and polymers. On the contrary, the coarse fractions tend to present high glass fiber content and particles having a high shape factor (Agogue et al., 2022).
At the fresh state of the mortar, the literature indicates that the use of fibers, independently of the fiber type (flax, glass, metal, etc.), in concrete/mortar reduces its workability; the placement and spreading of the concrete become slow and industrially unsatisfactory. The fibers’ volume fraction must be less than the percolation threshold; i.e., the fibers are likely to form a percolated network of interacting fibers (Yun et al., 2008). Increasing the fiber percentage from 5% to 20% and beyond significantly reduces the workability of the mixture, and the mortar becomes too stiff to be poured (Casanova, 1995).
According to the literature, the incorporation of composite shreds also reduces the workability of the mortar mixture. Composite shreds tend to agglomerate and significantly increase the mortar viscosity, showing a similar conclusion than for the metallic fibers, as presented above. Moreover, powders and fibers have a high specific surface area, which increases the apparent absorption of water, leading to a decrease in the workability of the concrete/mortar (Ganesan et al., 2014; Zhou et al., 2021). The decrease in the workability can also be attributed to the angular shape of glass particles (Tao et al., 2023). This means that, in the context of this study, limiting the grinding process will probably accentuate the effect (decrease) of the incorporation of glass fibers on the workability of the concrete/mortar. Xu et al. (2022) used a shredding machine to process waste wind turbine blades into macro fibers of various lengths less than 100 mm for being incorporated into the concrete. The incorporation of recycled macro fibers leads to a slump loss of 54% at a fiber volume ratio of 2.5%. Thus, a significant reduction in the workability of mortar incorporating composite shreds is observed in this study.
Mechanically, concrete and mortar are brittle. They have low tensile strength and low deformation capacity.
According to the literature, the incorporation of fibers helps concrete, increasing its durability, enhancing the capacity for deformation, and showing better fracture behavior, particularly in bending (Hambach and Volkmer, 2017; Bos, 2002; Dehghan et al., 2017; Xiong et al., 2021). More precisely, the presence of fibers does not reduce the stress at which the first crack appears, but it limits its progression (García et al., 2014). Thillo et al. 2021 highlighted that the incorporation of 0.2% of glass fibers (volumetric fraction) resulted in a decrease of 0.9%, 3.4%, and 4.6%, respectively, in compressive, tensile splitting, and flexural tensile strength. It has been found that this mixture is less compacted compared to a mixture without fiber reinforcement (Thillo et al., 2021). With the incorporation of composite shreds into concrete/mortar, the effects can be fairly nuanced (Tao et al., 2023). Regarding compressive behavior, some studies proposed that the incorporation of composite shreds into concrete/mortar reduces its strength (Dehghan et al., 2017) and also leads to a disruption in granular stacking, which increases the porosity and heterogeneity of the concrete (Baron and Ollivier, 1997; Sebaibi, 2007). Xu et al. (2022) incorporated recycled macro fiber composite (glass fiber-reinforced polymer) into concrete, which led to a reduction of 14.07% in compressive strength at a fiber volume ratio of 2.5%. Another study on the incorporation of polymer shreds and glass powder into cementitious materials (El-Seidy et al., 2023) indicated a decrease in the compressive strength and density. These decreases are attributed to the following reasons:
− Poorer adhesion between the cementitious matrix and the polymer.
− Significant water absorption by the glass powder.
Other studies have shown an increase in compressive strength with the incorporation of composite shreds. This increase is attributed to the filler effect of the powder part of the shreds, which helps reduce the voids between the particles in the concrete (Farinha et al., 2019; Ribeiro and Meixedo, 2015). Baturkin et al. (2021) concluded that these powders have a pozzolanic effect, which increases the compressive strength (Xu et al., 2022).
Given these disparate conclusions, the present study will shed light on the impact on mechanical properties due to incorporation of composite shreds into concrete/mortar and provide a better understanding of the potential for using composite shreds in concrete.
For flexural strength, the results in the literature are varied, as is the case for compressive strength. Ribeiro and Meixedo (2015) found an 18% increase in flexural strength for an incorporation of 8% (percentage by mass in relation to the total mass of mortar, which is equivalent to 3% by volume as a substitute for sand). Xu et al. (2022) incorporated recycled macro fiber composite (glass fiber-reinforced polymer) into concrete, which led to an improvement of 38% in flexural strength at a fiber volume ratio of 2.5%.
Rodin et al. (2018) highlighted that incorporating large composite shreds (glass fiber polymer resin) at 1, 3, and 5% replacement of sand (volumetric fraction) resulted in 5, 25, and 35% increases, respectively, in the 90-day modulus of rupture, with significant increases in the toughness index and minimal reductions in the compressive strength compared to the control mortar.
On the other hand, other studies have observed a reduction in the flexural strength with the incorporation of composite shreds (Tittarelli and Shah, 2013; Coppola et al., 2011). This reduction is attributed to the following reasons:
− An increase in the porosity due to the incorporation of shreds.
− Poorer mechanical strength of the shreds compared to the silica in the sand.
Based on the literature results, this paper establishes the technical feasibility of incorporating SMC (sheet molding compound) composite shreds resulting from production waste into mortar. The objective is to propose a new solution of valorization of the composite (glass fiber and polyester resin), which permits limiting the composite preparation stage and, therefore, limiting costs and the ecological impact (as shredding does). Regarding shredding, according to the literature, the more the composite is shredded, the better are its mechanical and rheological properties.
The use of composite shreds (polyester resin-coated glass fibers) in the formulation of concrete (mortar) has not been sufficiently researched in the literature. Studies into the use of similar alternative materials such as glass fibers in mortars are common. Although similarities can be observed, this is a completely different material that requires a more thorough characterization than currently exists in the literature. The approach of the study is first to verify the assumptions made in the literature, which can sometimes contradict each other (e.g., mechanical performance).
At first, the approach will be to understand the properties of the mortar according to the composite shreds’ percentage of incorporation. Afterward, results will be achieved by observations of the adhesion of composite shreds with the cementitious matrix. The study corresponds to the first part, i.e., the physical characterization (mechanical and workability) of different mix designs. The ratio of water/cement and composite shreds’ percentage of incorporation will be changed to optimize the mortar properties. The first section describes the scientific approach adopted to achieve these objectives. The various processes and procedures involved in the experiment are presented. The second section corresponds to the experimental results and their analysis.
2 Materials and methods
2.1 Cement
Cement CEM I 42.5 R has been used in the mortar mix.
2.2 Sand
Sand was extracted from the Boulonnais quarry. The particle size distribution of sand is presented in Figure 1. Particle size analysis was carried out on two samples to check the repeatability. The uniformity coefficient is 2, indicating that the sand is quite homogeneous. To optimize the granular skeleton of a mortar, it is preferable to use heterogeneous sand. This means that the incorporation of composite shreds can improve the granular arrangement.
2.3 Composite shreds
Composites are obtained from the plant Plastic Omnium located in Flers-en-Escrebieux (59128, France). They correspond to production scraps from SMC materials, which are composed of glass fibers with polyester resin. The composite waste used in this study was ground to obtain shreds.
Composite shred granulometry can be estimated with the naked eye as sized from 10 mm to very fine powder (Figure 2). Particle size distribution reveals heterogeneous composite shreds. Because of the shape of the shreds, particle size analysis by sieving was not used to characterize the shreds. They were classified into three groups after observation with the naked eye. Photographs were taken and processed using ImageJ software to assess the proportions of each group.
•Group n°1: coarse pieces (Figure 3A) These correspond to sizes from 1 mm to 1 cm. These are resin-coated fibers.
•Group n°2: fibers (Figure 3B). They have a slender shape with a length of 1 cm. They contain little resin.
•Group n°3: the others
Table 1 shows the proportions of shreds from each group. These results correspond to an average of four samples.
2.4 Physical characteristics of the materials
The absolute density of the sand was measured using a helium pycnometer (Micromeritics AccuPyc 1330) in accordance with standard NF EN 1097-7. It performed several measurements of mass and volume on the same sample, and the average of the measurements was recorded.
The water absorption (noted as Ab) of the sand was measured in accordance with standard EN 1097-6.
where Ms = the mass of dry sample after oven drying at 105°C and Ma = the mass of soaked sample, with the dry surface determined as explained in appendix 1 (Supplementary Material/Section 1).
Composite shreds were characterized by measuring the same parameters as the sand (absolute density and water absorption) and using the same protocols. The results are presented in Table 2. The absolute densities of sand and of composite shreds are quite similar. This result means that the difference in the density between the sand and the composite shred material will not be taken into account to assess the impact of replacement. The density of composite shreds should not have an impact on the developed mortar (compared with the reference sample).
2.5 Mix design method
The mix design method is based on the NF EN 196-1. The reference sample corresponds to the standardized mortar. The resulting composition of 1 m3 of mortar is presented in Table 3. The water/cement (W/C) ratio has been noted to be different for different percentages of composite shreds in order to study the potential effect of water on this substitution. W/C is equal to 0.5, 0.6, and 0.7. For each mix design with the W/C ratio fixed, sand is substituted by composite shreds with a percentage by volume that equals to 0, 1, 1.5, 2, 2.5, 3, and 7% (compared to the volume of sand).
It should be noted that not all combinations of values for these parameters have been tested. The mix designs to be tested were decided as the first results were obtained. The substitution percentages were chosen on the basis of the state of the art in the following way:
At first, 7% substitution had been tested (with W/C of 0.5). The 7% substitution was chosen in order to define a high substitution range for the study. This value was chosen by cross-referencing several studies in the literature (Rodin et al., 2018; Ribeiro and Meixedo, 2015; Casanova, 1995).
As the mechanical strength obtained was lower than that of the reference sample (0% substitution with composite shreds), it was decided to test lower substitution percentages. Some studies in the literature have shown an optimal substitution of approximately 2% (in terms of fiber volume fraction; Rodin et al., 2018; Xu et al., 2022; Ribeiro and Meixedo, 2015).
Following observations of the mixture at the fresh state (dry), higher values (higher than 0.5) of the W/C ratio were investigated for 2%. W/C ratios equal to 0.6 and 0.7 were not studied for 7% of substitution, given the lower mechanical strength with a ratio equal to 0.5.
In view of the interesting results for the mix with a W/C ratio of 0.5 and with a percentage of substitution lower than 7%, these formulations were particularly studied by testing additional substitution percentages (1%, 1.5%, 2.5%, and 3%).
The mix design tested with mixing proportions for 1 m3 is indicated in Table 4.
It should be noted that this mix design method has been established on the assumption that the volume of water added by varying the W/C ratio was negligible compared to the total volume. This variation is for 0.6 and 0.7, which equals to 5% and 11%, respectively.
2.6 Mortar mixing protocol
The mixing protocol of the mortar has been adapted from the preparation of standardized mortar (standard EN 196-1):
1- Add cement + sand + composite shreds and mix for 60 s at low speed equal to 140 rpm.
2- Introduce 80% of water and mix for 60 s at low speed.
3- Add the remaining 20% of water and mix for 60 s.
4- Increase the speed to 285 rpm, and mix for 180 s.
For the study, time “zero” is set when the cement is in contact with water.
The mixing machine used had a volume capacity equal to 5 L. It was an automatic mixing machine of the brand IGM (Figure 4).
2.7 Preparation and cure conditions of the test specimens (compressive and flexure strength)
The mortar is poured into this mold by introducing the mortar twice and applying 60 shocks to the mold by using the agitator. The mold is then flattened and stored in a damp room or cupboard to maintain relative humidity. Between 20 h and 24 h after the start of mixing, these specimens are removed from the mold and stored in water at 20 C° ± 1 C°.
2.8 Experimental test protocol
The workability of mortar at the fresh state is estimated by measuring the diameter of the slump spread with the cone in accordance with standard NF EN 1015-3. The description of the test is given in appendix 2 (Supplementary_Material/Section 2).
The diameter of the slump is measured in two directions, as shown in Figure 5. The cone is 60 mm in height, 70 mm in the top diameter, and 100 mm in bottom diameter.
The spreading results correspond to a percentage. It has been calculated with the following formula:
where S: the spreading in percentage;
D1: the lower mold diameter; D: the average diameter of the mortar after spreading.
The mortar bulk density of the mortar is measured in accordance with standard NF P18-459, 2010. It is measured twice:
• When specimens are removed from the mold after 24 h curing.
• Before the mechanical tests are carried out (after 7 days).
It is measured in relation to the specific weight of water using the following formula:
where
d: mortar bulk density (no unit: g/cm3/1 g/cm3).
m: the mass obtained by weighing the specimen* at the time in question. The specimen is a right prism with rectangular base dimensions height*width*length = 4 cm*4 cm*16 cm.
V: the volume of the specimen (256 cm3).
mvwater: the specific weight of water equal to 1 g/cm3.
Compressive and flexural strength are evaluated at 7 days using the press INSTRON 5500 R with a capacity of 150 kN. It is assessed on prismatic samples of dimensions height*width*length = 4 cm*4 cm*16 cm (NF EN 196-1). A three-point flexural test is set up to measure the flexural strength. The compression test is conducted with the two pieces retrieved after the flexural test (Figure 6). For each mix design, three samples are used for the flexural test, and six samples are used for the compressive test. During the test, the force ramp is controlled by a speed of pressing force (in accordance the standard), and the force is measured with a cell. The force velocity for the compression test and the flexural test are 2.4 kN/s and 0.05 kN/s, respectively.
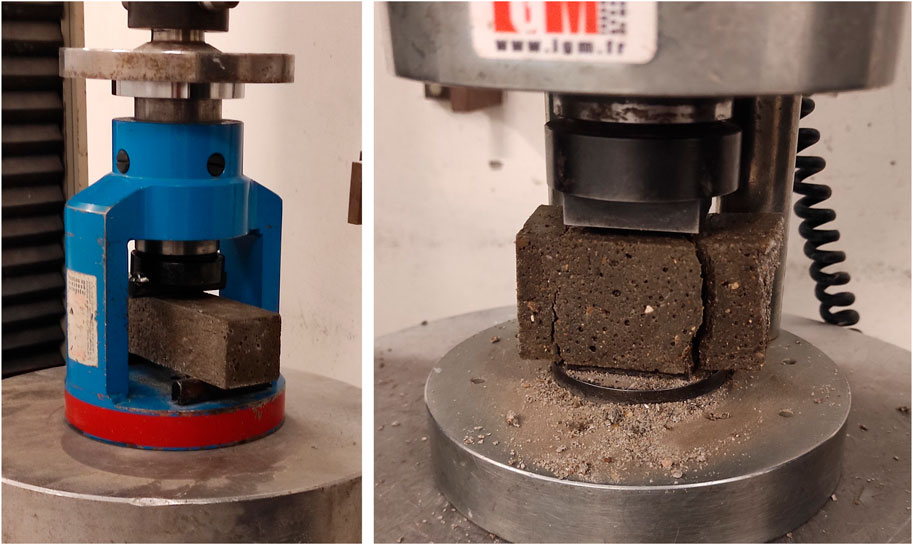
Figure 6. Pictures of compressive and three-point flexural tests using press INSTRON 5500 R (capacity of 150 kN) on the prismatic test samples 4*4*16 cm3 (NF EN 196-1).
The compressive strength is calculated with the following formula:
where
F: the maximum force during the test;
S: the cross-sectional area to the force.
The flexural strength is calculated with the following formula:
where
F: the maximum force during the test;
L: the distance between the two lower supports (mm);
b: the specimen width (mm);
h: the specimen height.
2.9 Calculation of the variability of results
Variability is indicated for all the results presented in the following section. This variability is calculated with the standard deviation using the following formula:
where
V: the standard deviation;
x: the data;
n: the number of data.
Standard deviations were calculated on two data types:
1. Calculation of the standard deviation of several measurements (from a test) carried out on the same mixture. The “data” is the measurement.
2. Calculation of the standard deviation of several results obtained from several mixtures of the same formulation. One result corresponded to the average of several measurements taken for one mixture. The “data” is the result of one mixture.
This second calculation of standard deviation is often greater than the first and enables assessing the repeatability of the making process.
These two standard deviations are indicated and interpreted in the results presented in the following section.
3 Results and discussion
3.1 Over time bulk density
Bulk densities of mortar after 24 h and after 7 days are presented in Figure 7. For each mix design, in Figure 7, one density value is indicated. This value corresponds to an average value for several mixtures (when they were repeated). The variability indicated in Figure 4 has been evaluated with the standard deviation for several measures of one mixture. This variability is negligible. The variability between two batches for one mix design is equal to 0.004 (average for all mix designs tested). This variability is also negligible.
For the ratio of composite shreds lower than 3%, the density seems to increase for each mix design. For the percentage ratio equal to 7%, the density is significantly lower than that of the reference mix design (with 0% percentage of composite shreds). It can be assumed that at 7% substitution, the incorporation of composite shreds disturbs the granular arrangement and creates porosity in the mortar. Mercury porosity tests will be performed at a later stage to verify this assumption.
The difference in the density between the composite shreds and the sand may also be responsible for this decrease in mortar density. However, given the small difference in the density between the two materials (sand and shreds), it cannot be the only cause.
At percentage ratio lower than 3%, it can be assumed that this decrease in density is caused by water absorption of composite shreds, which is higher than that of sand (more than five times higher). The mixing water no longer occupies the volume at the grain interfaces as it is absorbed by the composite shreds. It can also be assumed that at this percentage of substitution (lower than 3%), fine powder of the composite shreds complete and improve the granular arrangement. The granulometry analysis of composite shreds compared to the sand will help verify this assumption.
3.2 Workability
Spread at the fresh state according to the percentage of composite shreds for the mixture with different parameters W/C (equal to 0.5; 0.6, and 0.7) is presented in Figure 8.
The variability indicated in Figure 8 has been evaluated with standard deviation for several results from one mixture to another for the same mix design parameters. This variability is equal to 0.2 on average for all formulations. It can be considered negligible.
Spread variations according to the percentage of composite shreds, for formulations with different parameters W/C, have the same trend. It decreases with the composite shreds’ ratio.
Two effects may explain this variation:
• First, composite coarse shreds may mechanically slow down the flow of mortar at the fresh state.
• Second, composite fine shreds show a hydrophilic behavior. This water absorption dries the mortar at the fresh state, which reduces its fluidity. This decrease may seem linear. The slope coefficient of the lines is quite similar for mix designs with different W/C. EL-Seidy et al. (2023) also noted a decrease in the density with the incorporation of glass powder in cementitious materials. This decrease was attributed to the high water absorption of the glass powder.
3.3 Compressive and flexure strength
Compressive and flexural strength are presented in Figures 9, 10 respectively.
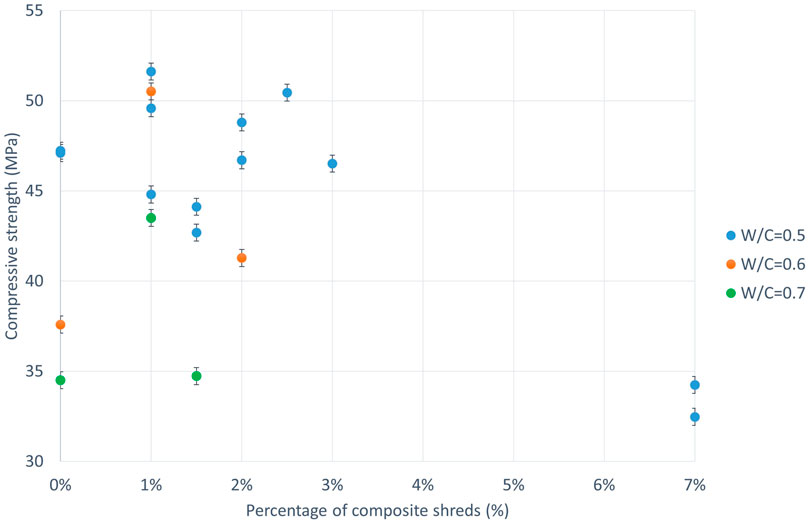
Figure 9. Compressive strength according to the percentage of composite shreds (variability calculated for several samples of one mixture).
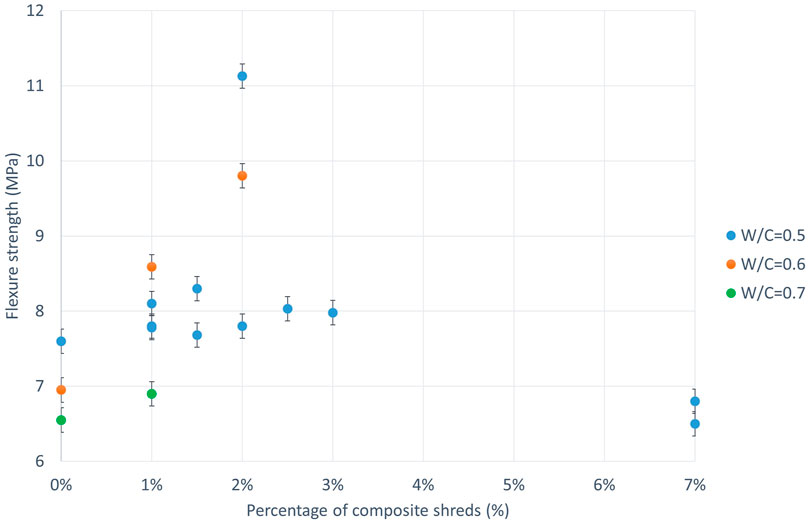
Figure 10. Flexural strength according to the percentage of composite shreds (variability calculated for several samples of one mixture).
Before commenting on the effect of substitution by composite shreds on these properties, it should be noted that tests on the mix design have been done twice or thrice. All the results are shown in the figures, and variability from one mixture to another for the same mix design is significant. It is equal for compressive and flexural strength of 1.021 and 0.534, respectively, (averages calculated on all mix designs tested). Figures indicated an error bar, which corresponds to the variability from one sample to another for the same mixture. It is equal for compressive and flexural strength of 0.47 and 0.16, respectively. These values correspond to averages calculated on all mix designs tested (for compressive and flexure strength, respectively). These variabilities are negligible and much smaller than variabilities from one mixture to another for the same mix design. The effect of the composite shreds cannot be assessed and may be apparently reduced by this variability.
Nevertheless, these results allow us to understand that the impact of the substitution of sand with composite shreds is less than the generated variability. The impact seems positive given that the mechanical strength (for compression and flexion) is higher than that of the reference mix (average of several mixtures for one mix design). The improvement in the mechanical performance with the incorporation of composite shreds is similar to the results of other studies (Farinha et al., 2019; Ribeiro and Meixedo, 2015). This increase is attributed to the filler effect of the powdered part of the shreds, which helps reduce the voids between the particles in the concrete/mortar. In this study, this explanation is in line with the density results (presented above), which show a certain increase for these formulations.
The 7% substitution mix design presents a lower mechanical strength than the reference mix design. This decrease in strength for mortar with incorporation of fiber shreds has been observed and attributed to a disturbance in the granular arrangement (Baron and Ollivier, 1997; Sebaibi, 2007). As presented above, a lower density has been observed for this mix design, which is in line with the decrease in strength and corroborates the results from literature. The high variability from one mixture to another for one mix design highlights a particular characteristic of the composite shreds to be taken into account in the manufacturing process. The protocol is not repeatable, as different results for the same mix design has been obtained. This is probably due to the sampling of the composite shreds.
4 Conclusions and perspectives
The present study investigated the development of a concrete filled with glass fiber and polyester resin composite shreds. In a preliminary approach, the technical feasibility of incorporating composite shreds as a substitute for sand in mortar was validated. This was validated for certain substitution percentages set at the beginning of the study based on the state of the art. To this end, the rheological (spread test) and physico-mechanical (density and mechanical strength in flexion and compression) characterization tests were carried out for mortar specimens. Several mix designs were tested in order to understand the impact of introducing composite shreds as a substitute for sand. Composite shreds were introduced in the following percentages by volume: 0, 1, 1.5, 2, 2.5, 3, and 7%, with water and cement ratio equal to 0.5, 0.6, and 0.7.
The results obtained, presented below, validated certain hypotheses made at the start of the study and invalidated others:
• Slump results show that rheology decreases with the substitution of sand by shreds. This result validates those of the literature. The decrease obtained in the study seems to follow a linear law with a coefficient approximately equal to 3 to 6. For a substitution of sand by shreds of 2%, it is relatively small, and the pouring of the mortar is still feasible. The decrease can be attributed to the water absorption of the composite shreds. Further tests will be carried out to confirm this hypothesis.
• Concerning mechanical results:
o For formulations with a substitution percentage of composite shreds lower than 3%, mechanical strength (both compression test and flexural test) is quite similar to that of the reference sample. It can be concluded that the introduction of composite shreds has no impact on the mechanical properties of the mortar at these substitution percentages.
o For a percentage of substitution equal to 7%, the mechanical strength is lower than that of the reference sample. Compressive strength is 30% lower than that of the reference sample. Despite this reduction, this still corresponds to an acceptable compressive strength of 33 MPa. For this percentage of substitution equal to 7%, a decrease in density is also observed, and it can be explained by the porosity created by the incorporation of the composite shreds into the mortar.
This result invalidates the hypothesis put forward at the start of the study. Some studies in the literature have also found a reduction in the mechanical performance. This impact is attributed to the poor adhesion between the cementitious matrix and the composite shreds. SEM observations will be carried out to investigate this adhesion.
Moreover, the rest of the project will carry out additional analyses to understand the results obtained.
o Is there an impact on cement hydration with substitution?
o Characterize the fracture faces qualitatively by SEM observation.
The applications targeted for the concrete developed in this study, in view of the mechanical strengths obtained on mortar (approximately 30 MPa for compressive strength), make it possible to envisage a concrete for slabs or floors.
A study of the economic and environmental aspects of the proposed solutions will be carried out as part of this project.
It should be noted that the standard deviation of mechanical properties from one mixture to another is highly significant. At first sight, it could be explained by the heterogeneous sampling of composite shreds and materials in the mortar. The composite shreds will be characterized more precisely to understand this variability. In addition, the making protocol will be modified to understand the reason of the variability observed from one batch to another.
At a later stage, mechanical tests with strain measurements will be carried out to study the mechanical behavior of the mortar incorporating composite shreds.
Data availability statement
The raw data supporting the conclusions of this article will be made available by the authors, without undue reservation.
Author contributions
AZ: writing–original draft and writing–review and editing. MD-L: writing–review and editing.
Funding
The author(s) declare that no financial support was received for the research, authorship, and/or publication of this article.
Acknowledgments
The author thanks Plastic Omnium in Flers-en-Escrebieux (59128) for the composite shreds provided for this study.
Conflict of interest
The authors declare that the research was conducted in the absence of any commercial or financial relationships that could be construed as a potential conflict of interest.
Publisher’s note
All claims expressed in this article are solely those of the authors and do not necessarily represent those of their affiliated organizations, or those of the publisher, the editors, and the reviewers. Any product that may be evaluated in this article, or claim that may be made by its manufacturer, is not guaranteed or endorsed by the publisher.
Supplementary material
The Supplementary Material for this article can be found online at: https://www.frontiersin.org/articles/10.3389/fmats.2024.1416647/full#supplementary-material
Abbreviations
CEM, characterizes a cement mix that complies with European standard EN 197-1; SMC, sheet molding compound.
References
Agence-Rhone-Alpes (2003). G. déchets: valorisation des déchets composites à matrice thermodurcissable. La maîtrise Des. matériaux, 1–60.
Agogue, M., Glais, A., Courtemanche, M., Ruch, Z., and Brun, L. (2022). Guide pour le recyclage et l’écoconception des composites. Rapport technique, 171.
Ahmad, G., Kahla, B., Majdi, A., Ben Kahla, N., and El-Shorbagy, M. A. (2022). Glass fibers reinforced concrete: overview on mechanical, durability and microstructure analysis. Materials 15, 5111. doi:10.3390/ma15155111
Baron, , and Ollivier, (1997). Matrice cimentaires renforcées de fibres de carbone, Association technique de l’industrie des liants hydrauliques. Les Bét. Bases données pour leur formulation, 507–512.
Baturkin, , Hisseine, , Masmoudi, , Masmoudi, R., Tagnit-Hamou, A., and Massicotte, L. (2021). Valorization of recycled FRP materials from wind turbine blades in concrete. Resour. Conservation Recycl. 174, 105807. doi:10.1016/j.resconrec.2021.105807
Ben Zaouche, N. (2020). Etude expérimentale d’un béton à base de déchets de verre non coloré confiné avec des matériaux composites.
Blagojević, J., Mijatović, B., Kočović, D., Stojanović, B., Ivanović, L., and Gajević, S. (2020). A review to cast polymer composite materials for interior environments. Applied Engineering Lett. 5 (No.1), 1–7. doi:10.18485/aeletters.2020.5.1.1
Casanova (1995). Bétons renforcés de fibres métalliques: du matériau à la structure. Etude expérimentale et analyse du comportement de poutres soumises à la flexion et à l’effort tranchant. Ecole Nationale des Ponts et Chaussées. Thèse.
Chayma Chaabani (2017). Composites à fibres de carbone: récupération des fibres par solvolyse hydrothermale. Impact sur la qualité des fibres et valorisation de la phase liquide, Ecole des Mines d'Albi-Carmaux. Génie Des. procédés.
Coppola, L., Cadoni, E., Forni, D., and Buoso, A. (2011). Mechanical characterization of cement composites reinforced with fiberglass, carbon nanotubes or glass reinforced plastic (GRP) at high strain rates. Appl. Mech. Mater. 82, 190–195.
Correia, J. R., Almeida, N. M., and Figueira, J. R. (2011). Recycling of FRP composites: reusing fine GFRP waste in concrete mixtures. J. Clean. Prod. 19 (115), 1745–1753. doi:10.1016/j.jclepro.2011.05.018
Crepin, B. (2021). Vers un recyclage plus vertueux des fibres de carbone de materiaux composites. [En ligne].
Dehghan, A., Peterson, K., and Shvarzman, A. (2017). Recycled glass fiber reinforced polymer additions to portland cement concrete. Constr. Build. Mater. 146, 238–250.
Elmouden, H. (2021). “Etude de l'influence de matériaux alternatifs sur les propriétés des mortiers mousse, en vue de leur valorisation,” in sédiments de dragage, mâchefers et fibre de verre, IMT-Nord-Europe, École-doctorale-Sciences-de-l’ingénierie-et-des-systèmes-Lille.
EL-Seidy, , Chougan, , Sambucci,, , AL-Kheetan, , Biblioteca, , Valente, , and Sghaffar, (2023). Lightweight alkali-activated materials and ordinary Portland cement composites using recycled polyvinyl chloride and waste glass aggregates to fully replace natural sand. Constr. Build. Mater. 368, 130399. doi:10.1016/j.conbuildmat.2023.130399
Farinha, D., de Brito, J., and Veiga, R. (2019). Assessment of glass fibre reinforced polymer waste reuse as filler in mortars. J. Clean. Prod. 210, 1579–1594. doi:10.1016/j.jclepro.2018.11.080
Ganesan, N, Indira, P.V., and Sabeena, M. (2014). Behaviour of hybrid fibre reinforced concrete beam–column joints under reverse cyclic loads. Mater. and Des. (1980-2015) 54, 686–693. doi:10.1016/j.matdes.2013.08.076
García, D., Vegas, I., and Cacho, I. (2014). Mechanical recycling of GFRP waste as short-fiber reinforcements in microconcrete. Constr. Build. Mater. 64, 293–300.
Hambach, M., and Volkmer, D. (2017). Properties of 3D-printed fiber-reinforced Portland cement paste. Cem. Concr. Compos. 79, 62–70. doi:10.1016/j.cemconcomp.2017.02.001
JEC Observer (2022). Aperçu du marché des composites au niveau mondial. Available at: https://www.jeccomposites.com/wp-content/uploads/2022/03/V3_14588_DP-Digital-JEC-2022_02_24-fr.pdf.
NATURE-ACTION (2019). L’augmentation de la demande de sable appelle à la gouvernance des ressources. [En ligne].
Ribeiro, M., and Meixedo, F. (2015). Re-use assessment of thermoset composite wastes as aggregate and filler replacement for concrete-polymer composite materials: a case study regarding GFRP pultrusion wastes. Resour. Conservation Recycl. 104, 417–426.
Rodin, H., Nassiri, S., Englund, K., Fakron, O., and Li, H. (2018). Recycled glass fiber reinforced polymer composites incorporated in mortar for improved mechanical performance. Constr. Build. Mater. 187, 738–751. doi:10.1016/j.conbuildmat.2018.07.169
Sadoun, F., and Djebri, L. (2019). Etude comparative entre les mortiers renforcés avec la fibre métalliques et verre, Mémoire de fin d’études - UNIVERSITE AKLI MOHAND OULHADJ de Bouira.
SEBAIBI (2010). “Valorisation des composites thermodurcissables issus du recyclage dans une matrice cimentaire: application aux betons a ultra-haute performance,” in Laboratoires d’accueil: Département Technologie des Polymères et Composites and Ingénierie Mécanique, Ecole des Mines de Douai Département Génie Civil et Environnemental, Ecole des Mines de Douai.
Tao, H., Hadigheh, S. A., and Wei, Y. (2023). Recycling of glass fibre reinforced polymer (GFRP) composite wastes in concrete: a critical review and cost benefit analysis. Structures 53, 1540–1556. doi:10.1016/j.istruc.2023.05.018
Thillo, L. V., Blom, J., Moreels, A., and Craeye, B. (2021). Influence of aggregates, glass fibre reinforcement and recycled aggregates on polyester mortar. Constr. Build. Mater.
Tittarelli, F., and Shah, S. P. (2013). Effect of low dosages of waste GRP dust on fresh and hardened properties of mortars: Part 1. Constr. Build. Mater. 47, 1532–1538.
Xiong, L. I., Lan, L. I., Lan, T., Li, H., Long, W., and Xing, F. (2021). Sustainable use of recycled carbon fiber reinforced polymer and crumb rubber in concrete: mechanical properties and ecological evaluation. J. Clean. Prod. 279, 123624. doi:10.1016/j.jclepro.2020.123624
Xu, L. I. U., Xiang, F. U., Xiang, Y., and Fu, B. (2022). Valorization of macro fibers recycled from decommissioned turbine blades as discrete reinforcement in concrete. J. Clean. Prod. 379, 134550. doi:10.1016/j.jclepro.2022.134550
Yun, K. I. M., Jeon, P., and et, L. E. E. (2008). Effects of fibre-reinforced cement composites ductility on the seismic performance of short coupling beams. Mag. Concr. Res. 60, 223–233.
Keywords: material valorization, glass fiber, polyester resin, composite, concrete, resource preservation, multi-physics characterization
Citation: Zambon A and Deleglise-Lagardere M (2024) Potential for material valorization of composites (glass fiber in polyester resin) in concrete: performance evaluation on mortar. Front. Mater. 11:1416647. doi: 10.3389/fmats.2024.1416647
Received: 12 April 2024; Accepted: 07 October 2024;
Published: 29 October 2024.
Edited by:
Giulia Masi, University of Bologna, ItalyReviewed by:
Ionut Ovidiu Toma, Gheorghe Asachi Technical University of Iași, RomaniaSaša Milojević, University of Kragujevac Faculty of Engineering, Serbia
Milan Bukvic, University of Kragujevac, Serbia
Copyright © 2024 Zambon and Deleglise-Lagardere. This is an open-access article distributed under the terms of the Creative Commons Attribution License (CC BY). The use, distribution or reproduction in other forums is permitted, provided the original author(s) and the copyright owner(s) are credited and that the original publication in this journal is cited, in accordance with accepted academic practice. No use, distribution or reproduction is permitted which does not comply with these terms.
*Correspondence: Agnès Zambon, YWduZXMuemFtYm9uQGltdC1ub3JkLWV1cm9wZS5mcg==