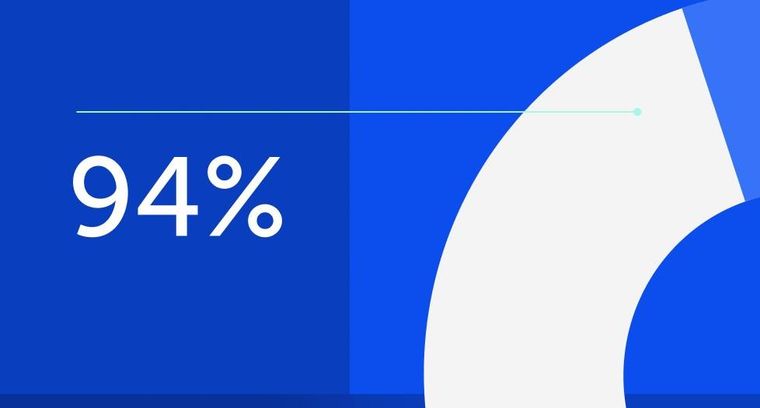
94% of researchers rate our articles as excellent or good
Learn more about the work of our research integrity team to safeguard the quality of each article we publish.
Find out more
ORIGINAL RESEARCH article
Front. Mater., 01 May 2024
Sec. Polymeric and Composite Materials
Volume 11 - 2024 | https://doi.org/10.3389/fmats.2024.1406583
This article is part of the Research TopicMultifunctional, Flexible, Polymeric Materials with Controlled NanostructuresView all 6 articles
In light of escalating global climate change concerns and the pressing need to address industries with high carbon emissions and pollution, enhancing the preparation of phenol-formaldehyde epoxy resins has emerged as a critical research focus. This study seeks to fabricate waterborne phenol-formaldehyde epoxy resins with superior performance by investigating pivotal factors influencing their properties and refining preparation methods. Utilizing tetrabutylammonium bromide as a phase transfer catalyst, the phenol-formaldehyde epoxy resins are synthesized via a two-step alkalization process. Subsequent etherification reactions involve modifying the phenol-formaldehyde epoxy resins using cationic modifier diethanolamine (DEA) and anionic modifier sodium p-amino benzenesulfonate, resulting in waterborne phenol-formaldehyde epoxy resins. Subsequently, in situ synthesis is employed to produce nanoscale silica (SiO2) modified waterborne phenol-formaldehyde epoxy resins. The findings reveal that when the ratio of n1 to n2 falls within the range of 1/3.25 to 1/3, the emulsion displays a moderate particle size and maintains stable storage. Furthermore, an increase in DEA dosage leads to a particle size of less than 324 nm when the ratio of n1 to n2 exceeds 1/3, indicating stability. Moreover, optimal stability and prolonged storage lifespan are achieved when the nano SiO2 content is approximately 1.5%. This study contributes by synthesizing high-quality waterborne phenol-formaldehyde epoxy resin emulsions through optimized methods. The research findings offer a theoretical foundation for this domain and support the practical application of low-carbon and environmentally friendly concepts in the coatings industry.
Amidst the escalating influence of global climate change, nations have implemented and progressively reinforced regulations and policies to constrain high-polluting and high-carbon industries, urging a shift towards low-carbon, eco-friendly, and sustainable practices (Sovacool et al., 2022). Among these, the coatings industry, recognized as a significant polluter, confronts pressures from both regulatory mandates and market competition, compelling the development of products aligned with low-carbon and environmental standards to meet market demands (Pathak et al., 2022; Pleshivtseva et al., 2023).
Waterborne coatings, prized for their eco-friendly attributes, stand as a pivotal strategy for the coatings industry’s pursuit of low-carbon transitions. Among these, waterborne epoxy resin emulsions, serving as pivotal constituents for various functional coatings, have garnered considerable scholarly and industrial focus in both production and application realms (Steinbrück et al., 2022). However, prevailing waterborne epoxy resin formulations often fall short of meeting demands for high-temperature conditions. Consequently, the development of waterborne epoxy resin emulsions capable of harmonizing low-carbon environmental performance with high-temperature resilience assumes critical importance, not only for advancing the low-carbon evolution of the coatings sector but also for presenting substantial industrial and market application opportunities in the realm of high-temperature-resistant materials utilizing waterborne epoxy resins. The significance of attaining a low-carbon footprint in the preparation process is twofold: it aligns with the global imperative to mitigate climate change and bolster environmental integrity, while also addressing the inherent need for sustainable growth within the coatings industry. Embracing low-carbon technologies and materials enables the industry to mitigate its environmental footprint, complying with stricter regulations and meeting evolving market expectations. Additionally, these technologies can bolster material performance and efficiency, fostering innovation in both materials and processes, thereby catalyzing the green transition and fostering high-quality development across the coatings industry worldwide.
This study begins by reviewing the current research landscape both domestically and internationally. It then outlines the main research methodologies employed, encompassing the preparation of waterborne phenol-formaldehyde epoxy resins, surface modification of nano silica (SiO2), investigation into SiO2-modified waterborne phenol-formaldehyde epoxy resin composites, and the in situ synthesis of nano SiO2-modified waterborne phenol-formaldehyde epoxy resins. Subsequently, the prepared samples undergo testing, and the resultant findings are discussed. Ultimately, the research concludes by presenting its key findings and implications.
The primary research objectives of this study are outlined as follows:
(1) Synthesis of waterborne phenol-formaldehyde epoxy resin employing a phase transfer catalyst and a two-step alkaline method.
(2) Surface modification of nano SiO2 utilizing γ-glycidoxypropyltriethoxysilane.
(3) Examination of the synthesis of SiO2-modified waterborne phenol-formaldehyde epoxy resin composites through in situ polymerization, alongside the investigation of emulsion stability and coating performance.
Numerous scholars have made significant progress in optimizing the preparation of waterborne phenol-formaldehyde epoxy resin. Wang H. et al. (2022) proposed a direct emulsification method using high-speed shearing and a large emulsifier to convert epoxy resin into emulsions. However, the resulting emulsion had a larger particle size and poor storage stability (Wang L. et al., 2022). In contrast, Aksoy (2022) highlighted the effectiveness of the phase inversion method in producing smaller and more stable emulsion products. This approach involves forming a water-soluble anionic intermediate by reacting epoxy resin with amine solvent, followed by adjusting the system’s water acidity/alkalinity to induce the inversion of the anionic intermediate. It is considered more suitable for industrial production (Aksoy, 2022). Clark et al. (2022) demonstrated that existing waterborne epoxy resin products were most suitable for room temperature conditions but exhibited reduced adhesion, decreased hardness, and expansion phenomena at high temperatures, limiting their application in high-temperature industrial fields (Clark et al., 2022). Tang et al. (2022) suggested enhancing the high-temperature resistance of epoxy resin by selecting high-performance curing agents and reinforcing fillers, and optimizing the curing process and mechanisms. For instance, curing agents like polyurethane and phenolic resins could achieve curing at temperatures ranging from 120°C to 180°C (Tang et al., 2022). Ajanovic et al. (2022) devised a method to prepare a high-temperature-resistant waterborne phenol-formaldehyde epoxy resin emulsion, demonstrating superior thermal stability and solvent resistance. Through adjustments in parameters such as the content of phenol-formaldehyde resin, epoxy resin, and surfactant, as well as the type and dosage of surfactant under varying conditions, they achieved optimal emulsion performance (Ajanovic et al., 2022). Wang H. et al. (2022) highlighted that by controlling parameters like pH value, temperature, and stirring speed, along with specific conditions of phenol-formaldehyde resin content, epoxy resin content, and surfactant dosage, a more stable emulsion with enhanced performance could be obtained (Wang L. et al., 2022). Basak et al. (2024) developed novel nitrogen oxide-based nanogels using controlled reversible addition-fragmentation chain transfer polymerization, resulting in an over 85% increase in shelf life compared to natural superoxide dismutase (Basak et al., 2024). Das et al. (2018) evaluated these nanoparticles using techniques such as X-ray diffraction and Fourier Transform Infrared Spectroscopy (FTIR). They observed UV-visible spectra supporting the production of AgNPs on the surface of polydopamine-coated hydrated silica (SiO2) (Das et al., 2018).
In conclusion, incorporating resins and curing agents with superior high-temperature adaptability into the curing system and optimizing synthesis and curing processes can synergistically enhance the high-temperature resistance and low-carbon performance of waterborne epoxy resin products.
Phenol-formaldehyde epoxy resin contains significant amounts of organic solvents, emitting large quantities of volatile organic compounds into the air after use. This fails to meet current environmental standards amidst low-carbon requirements, leading to increasingly restricted applications. Waterborne transformation of phenol-formaldehyde epoxy resin emerges as an effective solution. Given the higher epoxy value of phenol-formaldehyde epoxy resin compared to traditional epoxy resin, the introduction of hydrophilic groups can be achieved by reacting a portion of the epoxy groups, without compromising the comprehensive performance of the cured film. The specific research and preparation process are detailed below. The purities of the materials used in the experiment are as follows: phenol, 98%; formaldehyde, 34%; epichlorohydrin (ECH), 99%; tetrabutylammonium bromide, 98%; diethanolamine (DEA), 99%; and sodium p-toluenesulfonate, 98%.
The experiments involve various reagents. Table 1 presents the information for all reagents used in this experiment.
The instruments utilized in the experiments are outlined in Table 2.
The reagents and equipment utilized in this study are outlined previously. Next, the synthesis process of waterborne phenol-formaldehyde epoxy resin is elucidated. In a four-necked flask equipped with a condenser, 20.00 g of phenol, 3.00 g of deionized water, and 0.24 g of oxalic acid were added under an N2 atmosphere. The mixture is stirred magnetically at 60°C for 15 min, followed by the dropwise addition of 14.00 g of formaldehyde solution. After the completion of the addition, another 0.24 g of oxalic acid is added, and the temperature is raised to 75°C for a 2-h reaction. Subsequently, the temperature is further increased to 90°C, and the reaction continued for 2 h (Liu et al., 2022; Ma et al., 2022; Oyebanji et al., 2022). Following the reaction, the product is washed with water to neutrality and subjected to vacuum distillation to remove water, yielding the phenol-formaldehyde resin (I). The principle of this reaction is illustrated in Figure 1.
Under an N2 atmosphere, an excess of ECH and 0.48 g of tetra-n-butylammonium bromide (TBAB) is added to the previously obtained compound (I). The reaction temperature is set at 90°C for 3 h. Subsequently, the temperature is reduced to 70°C, and a sodium hydroxide (NaOH) solution is added dropwise, followed by an additional 2-h reaction period. Upon completion of the reaction, the product is washed with water to neutrality and subjected to vacuum distillation to remove the solvent. Finally, epoxy phenol novolac (EPN) (II) is obtained (Cohen et al., 2022; Wangari et al., 2022; Abdurahmonov et al., 2023). The principle of this reaction is illustrated in Figure 2.
A specified quantity of EPN (II) is dissolved in tetrahydrofuran (THF) at 65°C with stirring. DEA is then added according to the prescribed amount, and the reaction proceeded for a specific duration. Upon completion of the reaction, oxalic acid is introduced to neutralize the system for 0.5 h, followed by a temperature reduction to 55°C. Deionized water is subsequently slowly added while stirring for 1 h to yield the waterborne phenol-formaldehyde epoxy resin emulsion. This emulsion is labeled Diethanolamine Water Epoxy Phenol Novolac (D-WEPN) (Sun et al., 2022). The preparation principle of this emulsion is depicted in Figure 3.
EPN (II) is dissolved in THF at 65°C. Sodium p-amino benzenesulfonate is then added as per the specified amount, and the reaction proceeds at 100°C for 24 h (Wu et al., 2022). Subsequently, the temperature is reduced to 65°C, and the cosolvent sodium dodecyl sulfate (SDS) is introduced. Deionized water is slowly added dropwise while stirring for 2 h (Strassburger et al., 2023). Finally, high-shear emulsification is employed to form the emulsion, resulting in the waterborne phenol-formaldehyde epoxy resin emulsion denoted as S-WEPN.
The prepared emulsion is combined with a defoaming agent and then applied onto a polytetrafluoroethylene template. Triethylenetetramine (TETA) curing agent is uniformly added and stirred. Vacuum curing is conducted at 50°C for 4 h, followed by additional curing at 110°C for 10 h, yielding the WEPN film (Hanif et al., 2023).
Nano SiO2 undergoes surface modification using γ-aminopropyltriethoxysilane (APTES) to decrease surface hydroxyl (-OH) content and graft organic groups, thereby improving its hydrophobicity for enhanced dispersion in the resin (Gonçalves et al., 2022a; Kyei et al., 2022; Sonnendecker et al., 2022). More efficient surface modification is achieved by finely controlling the dosage of APTES and adjusting reaction conditions such as time and temperature. This results in a reduction of the hydroxyl content on the surface of nano SiO2, thereby enhancing its dispersibility and hydrophobicity in phenolic epoxy resin, consequently improving the resin’s high-temperature resistance. Subsequently, employing phenol-formaldehyde prepolymer, ECH, DEA, and acetic acid as primary constituents, the nanoscale SiO2-modified waterborne phenol-formaldehyde epoxy resin is synthesized via the prepolymer method (Sharmila et al., 2022; Romão et al., 2022).
The experiment utilizes reagents listed in Table 1 and instruments detailed in Table 2.
Initially, 4 g of nanoscale SiO2 are dispersed in 100 mL of ethanol and stirred for 20 min, then sonicated for 30 min (Grinins et al., 2022; Henn et al., 2022; Vázquez Loureiro et al., 2023). Subsequently, 1.6 g of 3-APTES are dissolved in a 10-mL ethanol-water solution and stirred for 30 min for adequate hydrolysis. The dispersed mixture is then magnetically stirred at 70°C under a nitrogen atmosphere for 1 h, followed by the slow addition of APTES hydrolysate and an 8-h reaction (Wang H. et al., 2022; Koch et al., 2022; Thakare et al., 2022). Upon completion, centrifugation, washing with deionized water and ethanol, and centrifugation are conducted three times. Finally, vacuum drying is performed at 60°C for 24 h, succeeded by grinding and pulverization (Pan et al., 2022).
Initially, under a nitrogen atmosphere, 20.00 g of phenol, 3.00 g of deionized water, and 0.24 g of oxalic acid are combined in a four-neck flask and magnetically stirred at 60°C for 15 min (Dagdag et al., 2022). Subsequently, 14 g of formaldehyde is added dropwise, followed by the introduction of 0.24 g of oxalic acid. The temperature is raised to 70°C, and the reaction proceeds for 2 h to yield the phenol-formaldehyde prepolymer. Then, N-SiO2 is introduced, and the temperature was raised to 80°C for 2 h, followed by an additional 1 h of reaction at 95°C (Fritz and Olivera, 2022). Following neutralization through water washing, the system undergoes constant pressure fractionation, with water evaporated to obtain the nanoscale SiO2-modified phenol-formaldehyde resin. Excess ECH and 0.48 g of TBAB are added, and the reaction is conducted at 90°C for 3 h. Then, the temperature is lowered to 70°C, and a sodium hydroxide (NaOH) solution is added dropwise for a further 2 h. Subsequently, excess ECH and 0.48 g of TBAB are added, and the reaction is carried out at 90°C for 3 h. The temperature is then lowered again to 70°C, and NaOH solution is added dropwise to continue the reaction for 2 h (Gonçalves et al., 2022b; Okamura et al., 2022; Liang et al., 2023). After washing to neutral pH, the mixture undergoes constant pressure filtration and rotary evaporation to remove the solvents, resulting in SiO2/EPN composite. The SiO2/EPN is mixed with THF and stirred at 65°C until fully dissolved. DEA is added according to the stoichiometric ratio and reacted at 65°C for 2 h (Khan et al., 2022). Then, oxalic acid is added for neutralization and stirred for 1 h. The temperature is lowered to 55°C, and deionized water is added with stirring until a milky white system is formed, resulting in the SiO2/WEPN emulsion.
The SiO2-modified phenolic epoxy resin water-based emulsion is mixed with a defoaming agent and uniformly dripped into a polytetrafluoroethylene mold. The curing agent is added and stirred until homogeneous, followed by vacuum drying at 50°C for 4 h (Shibata et al., 2022). Subsequently, it is heat-cured at 110°C for 8 h to obtain the final SiO2-modified phenolic epoxy resin composite coating.
To achieve uniform dispersion of nano SiO2 in the phenolic epoxy resin, this study employs an in situ polymerization method (Wen et al., 2022). The surface hydroxyl groups of nano SiO2 are copolymerized with monomeric phenolic compounds and formaldehyde to obtain SiO2-modified phenolic resin. Subsequently, it is further reacted with ECH, DEA, and acetic acid to produce a SiO2-modified phenolic epoxy resin water-based emulsion (Steinbrück et al., 2022).
The reagents utilized in this experiment are detailed in Table 1, while the instruments employed are delineated in Table 2.
Polyphenol is blended with nano SiO2 and sonicated for 0.5 h to ensure uniform dispersion. Under a nitrogen atmosphere, formaldehyde is gradually added while maintaining a pH of 1–3 using oxalic acid, and the reaction proceeds at 65°C for 1 h. Subsequently, the temperature is raised to 85°C over 2 h, followed by an additional 2-h reaction to obtain SiO2-modified phenolic resin (Mfune and Adams, 2022). Adequate epichlorohydrin is introduced, and at 85°C, the pH is adjusted to 8 using tetrabutylammonium bromide, with the reaction continuing for 2 h. The temperature is then reduced to 65°C, and the pH is stabilized using NaOH solution for an additional 2 h to yield SiO2-modified phenolic epoxy resin. After water washing, the rotary evaporation process removes solvents and unreacted materials, resulting in the production of SiO2-modified phenolic epoxy resin.
The prepared SiO2-EPN is blended with THF and stirred at 65°C until completely dissolved. DEA is then added according to the stoichiometric ratio and allows to react for 2 h. Subsequently, oxalic acid is introduced for neutralization and reacted for 0.5 h. The gradual addition of deionized water with stirring for 1 h leads to the formation of the SiO2/WEPN emulsion.
During the alkalization and etherification reactions, precise adjustments are made to the reaction conditions, optimizing the introduction of hydrophilic groups through the selection of appropriate phase transfer catalysts (TBAB) and modifiers (DEA and sodium p-aminobenzenesulfonate). This optimization results in waterborne phenolic epoxy resin emulsions with enhanced stability and high-temperature resistance. Furthermore, in the preparation of composite materials by incorporating modified nano SiO2, a more uniform dispersion of nano SiO2 is achieved through adjustments in the amount of SiO2 added, dispersion method, and reaction conditions of the prepolymers. This not only improves the mechanical properties and chemical stability of the materials but also significantly enhances their high-temperature resistance. Details of the characterization equipment used in the experimental process are provided in Table 3.
The prepared samples undergoes testing, including infrared analysis, emulsion stability assessment, and film performance evaluation. Following the removal of solvent from the samples, a FTIR test is conducted with a scanning range of 4000 to 500 cm⁻1, 32 scans per sample, and a resolution of 4.0 cm⁻1. Figure 4 depicts the analysis results of the waterborne novolak epoxy resin.
Figure 4. Results of the infrared test and analysis of conducted on the waterborne novolak epoxy resin.
In Figure 4, the phenolic resin reveals numerous phenolic hydroxyl groups, evident through a broad absorption peak near 3300 cm⁻1 and characteristic benzene ring peaks at 1500–1600 cm⁻1. Upon addition of epichlorohydrin, a distinctive epoxy peak emerges at 912 cm⁻1, and most hydroxyl peaks near 3300 cm⁻1 diminish, indicating the completion of the epoxy reaction and the substitution of most hydroxyl groups by epoxy groups. Subsequent addition of DEA leads to some epoxy groups undergoing addition reactions to form hydroxyl groups, resulting in a weakened epoxy peak at 912 cm⁻1 and a strengthened hydroxyl peak near 3300 cm⁻1. Neutralization with acetic acid yields a carboxyl carbonyl peak at 1734 cm⁻1. Infrared spectroscopic analysis confirms the successful synthesis of phenolic epoxy resin, with the obtained product exhibiting the expected structure. Figure 5 presents the infrared test analysis results of nano SiO2 modification before and after.
In Figure 5, the spectra reveal characteristic peaks of nano SiO2 at 3435 cm−1, 1105 cm−1, 808 cm−1, and 471 cm−1. The peak at 3435 cm−1 corresponds to the absorption of hydroxyl groups (-OH) on the surface of SiO2. The peak at 1105 cm−1 signifies the symmetric stretching vibration of Si-O-Si, while the peak at 808 cm−1 represents the antisymmetric stretching vibration of Si-O-Si. Additionally, the peak at 471 cm−1 corresponds to the bending vibration of Si-O-Si. Comparatively, the other two curves exhibit absorption peaks attributed to -CH2 and -CH3 groups near 2900 cm−1, with the third peak being more prominent, indicating the introduction of -CH2 and -CH3 groups from 3-APTES. The enhancement of peaks near 1100 cm−1, 800 cm−1, and 470 cm−1 suggests the formation of Si-O-Si bonds. The broadening of the peak around 3400 cm−1 is attributed to the overlap between the -NH2 groups introduced by 3-APTES and the -OH groups.
Figure 6 depicts a comprehensive analysis of the infrared test results for the nano SiO2-modified water-based phenolic epoxy resin.
Figure 6. Analysis results of the infrared test conducted on nano SiO2-modified waterborne novolac epoxy resin.
In Figure 6, the Simple A curve reveals the presence of abundant phenolic hydroxyl groups in the phenolic resin, evidenced by the prominent and broad hydroxyl peak at 3400 cm−1. Following the reaction with ECH, depicted in the Simple B curve, the hydroxyl groups undergo epoxidation, leading to a notable decrease in the hydroxyl peak at 3400 cm−1 and the emergence of an epoxy peak at 910 cm−1. These data affirm the successful reaction between ECH and hydroxyl groups, evidenced by the attenuation of the hydroxyl peak. Upon the addition of DEA, depicted in the Simple C curve, some epoxy groups react with DEA to form hydroxyl groups, resulting in a reduction of the epoxy peak at 910 cm−1 and an augmentation of the hydroxyl peak at 3400 cm−1. After neutralization with acetic acid, the Simple D curve reveals a carboxyl carbonyl peak at 1732 cm−1. Throughout the process, a faint Si-O-Si bending vibration peak at 471 cm−1 persists, indicating the formation of chemical bonds between SiO2 and the EPN molecular chain.
Emulsion stability testing encompasses the assessment of various aspects, including the influence of DEA on the stability of the water-based phenolic epoxy resin emulsion, the impact of nano SiO2 on the stability of SiO2/WEPN composite material emulsion, and the effect of nano SiO2 on the stability of modified water-based phenolic epoxy resin emulsion. The specific test results are outlined below, with detailed data on the impact of DEA dosage on the average particle size and zeta potential of the emulsion provided in Table 4.
When the ratio of n1/n2 exceeds 1/3, the absolute value of the system’s zeta potential surpasses 32 mV, indicating high emulsion stability. With increasing DEA dosage, the emulsion particle size gradually decreases. However, when the n1/n2 ratio falls below 1/3.5, the particle size exceeds 1265 nm, signifying instability, possibly leading to gel formation. Within the range of 1/3.25 to 1/3, the emulsion particle size ranges from 324 to 859 nm, indicating moderate particle size conducive to stable storage. A n1/n2 ratio exceeding 1/3 results in particle size below 324 nm, signifying stable emulsion. Table 5 provides detailed insights into the impact of DEA dosage on emulsion stability.
As DEA dosage increases, the emulsion transitions from a pale yellow hue to milky white, and precipitate particles diminish. When the n1/n2 is ratio is ≤1/3.5, precipitation occurs, rendering the emulsion unstable. Conversely, with a n1/n2 ratio ≥1/3.25, minimal precipitation is observed, ensuring stable storage.
In Table 6, when the nano SiO2 content exceeds 2%, the centrifugation time of the emulsion decreases rapidly due to nano SiO2 aggregation. Consequently, the emulsion color gradually shifts to pale yellow, and stability decreases, resulting in shortened storage life, rendering it impractical. Based on dispersion and emulsion stability analyses, a nano SiO2 content below 3% is optimal, with a recommendation of 2%.
In Table 7, when the nano SiO2 content is below 2%, the absolute value of the Zeta potential exceeds 30 mV, indicating good system stability. However, as the nano SiO2 content increases, the average particle size of the emulsion gradually increases. Once the nano SiO2 content surpasses 2%, the average particle size of the emulsion exceeds 1000 nm, resulting in instability and the formation of precipitate particles. Therefore, it is advisable to maintain the nano SiO2 content below 2%, ideally around 1.5%.
Table 7. Detailed impact of nano SiO2 on the stability of modified water-based phenolic epoxy resin emulsion.
Table 8 displays the impact of nano SiO2 content on various application properties of the coating films.
Table 8 displays the variation in coating properties with increasing nano SiO2 content. Initially, the acid and alkali resistance of the coatings rises before declining. Similarly, the impact resistance increases from 40 cm to 50 cm, then declines. Pencil hardness gradually elevates to 3H, while adhesion grade decreases from 0 to 1. Additionally, both surface and bulk drying times gradually decrease.
In Figure 6, the phenolic resin exhibits numerous phenolic hydroxyl groups, evident from the prominent and broad peak at 3400 cm−1 in the Simple A curve. Upon reaction with ECH, the hydroxyl groups undergo epoxidation, leading to a notable decrease in the hydroxyl peak at 3400 cm−1 and the emergence of an epoxy peak at 910 cm−1 in the Simple B curve. These data signify the effective reaction of ECH with hydroxyl groups and the attenuation of the hydroxyl peak. With the addition of DEA, some epoxy groups undergo an addition reaction with DEA, forming hydroxyl groups. This results in a reduction of the epoxy peak at 910 cm−1 and an amplification of the hydroxyl peak at 3400 cm−1 in the Simple C curve. Following neutralization with acetic acid, the Simple D curve displays a carboxyl carbonyl peak at 1732 cm−1. Notably, a weak Si-O-Si bending vibration peak at 471 cm−1 persists throughout the process, indicating chemical bonding between SiO2 and the EPN molecular chain.
The enhanced water-based phenolic epoxy resin emulsion, distinguished by its remarkable high-temperature resistance, chemical stability, environmental compatibility, and superior mechanical attributes, holds immense promise across various applications. It finds suitability in surface coatings within sectors such as automotive, aerospace, and industrial machinery, offering enduring corrosion protection. Moreover, serving as a matrix resin, it augments material high-temperature performance, making it ideal for high-performance composite materials fabrication. Additionally, it meets the requirements for high-strength bonding in elevated-temperature environments, applicable in industrial equipment and aerospace component bonding. In contrast to the research endeavors of others, exemplified by Pan and Yan (2023), focusing predominantly on enhancing high-temperature resistance through alterations in resin cross-linking density, this study fortifies high-temperature resistance via optimized preparation processes, nano SiO2 surface modification, and composite material techniques. This approach not only elevates high-temperature resistance but also ensures environmental compatibility and widens application horizons (Pan and Yan, 2023). Similarly, juxtaposed with the research conducted by Zhao et al. (2022), which concentrates on leveraging diverse chemical modification methods to bolster resin physical properties, this study, through comprehensive methodological optimization, not only achieves enhancements in physical attributes but also broadens material application realms by incorporating nano-fillers, particularly in demanding high-temperature and high-performance sectors (Zhao et al., 2022).
This study aims to enhance phenolic epoxy resin by incorporating nano SiO2 to produce water-based phenolic epoxy resin, thus achieving water-based properties and augmenting its high-temperature resistance. Furthermore, the adoption of water-based phenolic epoxy resin aids in reducing volatile emissions, aligning with the environmental requisites of a low-carbon context. The specific research conclusions are delineated as follows:
(1) The synthesis of phenolic epoxy resin proceeds smoothly, with the replacement of hydroxyl groups by epoxy groups. Some epoxy groups react with DEA to yield hydroxyl groups.
(2) The characteristic spectral peaks of nano SiO2 are attributed to the vibration of Si-O-Si bonds. Introduction of 3-APTES enhances the vibration peak of Si-O-Si bonds.
(3) Upon reaction with ECH, hydroxyl groups in the phenolic resin are epoxidized. Following DEA addition, some epoxy groups react with DEA to form hydroxyl groups. SiO2 is chemically bonded to the EPN molecular chain.
(4) When the ratio of n1/n2 exceeds 1/3, with an absolute Zeta potential value surpassing 32 mV, the emulsion maintains stability. However, as DEA dosage increases, instability occurs when the ratio of n1/n2 falls below 1/3.5. Within the range of 1/3.25 to 1/3, the emulsion exhibits a moderate particle size, facilitating stable storage. A ratio of n1/n2 exceeding 1/3 signifies emulsion stability, with particle size below 324 nm.
(5) The emulsion transitions from pale yellow to milky white with rising DEA dosage. Instability and precipitation occur when the ratio of n1/n2 is ≤1/3.5, while stability prevails when the ratio is ≥1/3.25.
(6) Beyond a nano SiO2 content of 2%, emulsion stability diminishes, leading to reduced storage life and an average particle size exceeding 1000 nm, resulting in precipitate particle formation. It is advisable to maintain nano SiO2 content below 2%, ideally around 1.5%.
While this study yields promising outcomes, there are certain limitations to consider. It exclusively addresses the preparation of a singular type of phenolic epoxy resin emulsion, neglecting exploration into alternative phenolic epoxy resin emulsions. Future research endeavors will involve conducting more extensive application studies to assess the emulsion’s performance in practical settings. Additionally, comparative analyses among various phenolic epoxy resin emulsions will be undertaken to ascertain the optimal choices.
The original contributions presented in the study are included in the article/Supplementary material, further inquiries can be directed to the corresponding author.
YL: Conceptualization, Investigation, Writing–original draft, Writing–review and editing. JG: Conceptualization, Investigation, Writing–original draft, Writing–review and editing. JY: Data curation, Methodology, Writing–original draft. LW: Project administration, Validation, Writing–review and editing. XW: Data curation, Project administration, Writing–original draft. XX: Conceptualization, Data curation, Investigation, Methodology, Writing–review and editing. FY: Software, Writing–review and editing. LH: Software, Writing–original draft, Writing–review and editing.
The author(s) declare that no financial support was received for the research, authorship, and/or publication of this article.
The authors would like to show sincere thanks to those techniques who have contributed to this research.
Authors YL, JY, LW, XW, XX, FY, and LH were employed by the Suzhou Paint-key Material Technology Co., Ltd.
The remaining author declares that the research was conducted in the absence of any commercial or financial relationships that could be construed as a potential conflict of interest.
All claims expressed in this article are solely those of the authors and do not necessarily represent those of their affiliated organizations, or those of the publisher, the editors and the reviewers. Any product that may be evaluated in this article, or claim that may be made by its manufacturer, is not guaranteed or endorsed by the publisher.
Abdurahmonov, A., Madamiovna, K. D., and Egamberdiyeva, T. (2023). High temperature resistant reinforced concrete made on the basis of industrial waste. Best J. Innovation Sci. Res. Dev. 2 (3), 26–33. doi:10.15407/scine16.02.051
Ajanovic, A., Sayer, M., and Haas, R. (2022). The economics and the environmental benignity of different colors of hydrogen. Int. J. Hydrogen Energy 47 (57), 24136–24154. doi:10.1016/j.ijhydene.2022.02.094
Aksoy, K. (2022). Water-based polyurethanes for antibacterial coatings: an overview. Eur. J. Res. Dev. 2 (4), 213–242. doi:10.56038/ejrnd.v2i4.124
Basak, S., Mukherjee, I., and Das, T. K. (2024). Injectable biocompatible raft mediated nitroxide nanogels: a robust ROS-reduction antioxidant approach. Colloids Surfaces B Biointerfaces 236, 113790. doi:10.1016/j.colsurfb.2024.113790
Clark, M., Springmann, M., Rayner, M., Scarborough, P., Hill, J., Tilman, D., et al. (2022). Estimating the environmental impacts of 57,000 food products. Proc. Natl. Acad. Sci. 119 (33), e2120584119. doi:10.1073/pnas.2120584119
Cohen, R., Eames, P. C., Hammond, G. P., Newborough, M., and Norton, B. (2022). Briefing: the 2021 Glasgow Climate Pact: steps on the transition pathway towards a low carbon world. Proc. Institution Civ. Engineers-Energy, Int. J. Hydrogen Energy 175 (3), 97–102. doi:10.1680/jener.22.00011
Dagdag, O., Hsissou, R., Safi, Z., Hamed, O., Jodeh, S., Haldhar, R., et al. (2022). Viscosity of epoxy resins based on aromatic diamines, glucose, bisphenolic and bio-based derivatives: a comprehensive review. J. Polym. Res. 29 (5), 200. doi:10.1007/s10965-022-03040-3
Das, T. K., Ganguly, S., Bhawal, P., Remanan, S., Ghosh, S., and Das, N. C. (2018). A facile green synthesis of silver nanoparticles decorated silica nanocomposites using mussel inspired polydopamine chemistry and assessment its catalytic activity. J. Environ. Chem. Eng. 6 (6), 6989–7001. doi:10.1016/j.jece.2018.10.067
Fritz, C., and Olivera, J. F. (2022). Nanocellulose in heterogeneous water-based polymerization for wood adhesives. Polysaccharides 3 (1), 219–235. doi:10.3390/polysaccharides3010012
Gonçalves, F. A., Santos, M., Cernadas, T., Alves, P., and Ferreira, P. (2022a). Influence of fillers on epoxy resins properties: a review. J. Mater. Sci. 57 (32), 15183–15212. doi:10.1007/s10853-022-07573-2
Gonçalves, F. A., Santos, M., Cernadas, T., Ferreira, P., and Alves, P. (2022b). Advances in the development of biobased epoxy resins: insight into more sustainable materials and future applications. Int. Mater. Rev. 67 (2), 119–149. doi:10.1080/09506608.2021.1915936
Grinins, J., Iesalnieks, M., Biziks, V., Gritane, I., and Sosins, G. (2022). Birch wood surface characterization after treatment with modified phenol-formaldehyde oligomers. Polymers 14 (4), 671. doi:10.3390/polym14040671
Hanif, Z., Choi, K. I., Jung, J. H., Pornea, A. G. M., Park, E., Cha, J., et al. (2023). Dispersion enhancement of boron nitride nanotubes in a wide range of solvents using plant polyphenol-based surface modification. Industrial Eng. Chem. Res. 62 (6), 2662–2670. doi:10.1021/acs.iecr.2c03897
Henn, K. A., Forssell, S., Pietiläinen, A., Forsman, N., Smal, I., Nousiainen, P., et al. (2022). Interfacial catalysis and lignin nanoparticles for strong fire-and water-resistant composite adhesives. Green Chem. 24 (17), 6487–6500. doi:10.1039/d2gc01637k
Khan, S. A. R., Godil, D. I., Yu, Z., Abbas, F., and Shamim, M. A. (2022). Adoption of renewable energy sources, low-carbon initiatives, and advanced logistical infrastructure-an step toward integrated global progress. Sustain. Dev. 30 (1), 275–288. doi:10.1002/sd.2243
Koch, S. M., Pillon, M., Keplinger, T., Dreimol, C. H., Weinkotz, S., and Burgert, I. (2022). Intercellular matrix infiltration improves the wet strength of delignified wood composites. ACS Appl. Mater. Interfaces 14 (27), 31216–31224. doi:10.1021/acsami.2c04014
Kyei, S. K., Eke, W. I., Darko, G., and Akaranta, O. (2022). Natural polyhydroxy resins in surface coatings: a review. J. Coatings Technol. Res. 19 (3), 775–794. doi:10.1007/s11998-021-00604-8
Liang, Y., Luo, Y., Wang, Y., Fei, T., Dai, L., Zhang, D., et al. (2023). Effects of lysine on the interfacial bonding of epoxy resin cross-linked soy-based wood adhesive. Molecules 28 (3), 1391. doi:10.3390/molecules28031391
Liu, X. J., Zheng, M. S., Chen, G., Dang, Z. M., and Zha, J. W. (2022). High-temperature polyimide dielectric materials for energy storage: theory, design, preparation and properties. Energy & Environ. Sci. 15 (1), 56–81. doi:10.1039/d1ee03186d
Ma, Y., Wan, J., Yang, Y., Ye, Y., Xiao, X., Boyle, D. T., et al. (2022). Scalable, ultrathin, and high-temperature-resistant solid polymer electrolytes for energy-dense lithium metal batteries. Adv. Energy Mater. 12 (15), 2103720. doi:10.1002/aenm.202103720
Mfune, P., and Adams, S. (2022). Spray-painters and occupational contact dermatitis. Curr. Allergy & Clin. Immunol. 35 (3), 164–168. doi:10.1016/j.ijhydene.2022.02.094
Okamura, N., Kimura, T., Harada, T., and Hashimoto, T. (2022). Water-based dispersions of luminescent metal complexes for wet-processed multilayer organic light-emitting diodes. Mol. Cryst. Liq. Cryst. 744 (1), 31–36. doi:10.1080/15421406.2022.2055257
Oyebanji, M. O., Castanho, R. A., Genc, S. Y., and Kirikkaleli, D. (2022). Patents on environmental technologies and environmental sustainability in Spain. Sustainability 14 (11), 6670. doi:10.3390/su14116670
Pan, P., and Yan, X. (2023). Preparation of antibacterial nanosilver solution microcapsules and their impact on the performance of Andoung wood surface coating. Polymers 15 (7), 1722. doi:10.3390/polym15071722
Pan, P., Yan, X., and Wang, L. (2022). Effects of thermochromic fluorane microcapsules and self-repairing waterborne acrylic microcapsules on the properties of water-based coatings on basswood surface. Polymers 14 (12), 2500. doi:10.3390/polym14122500
Pathak, T. K., Sharma, V., Jassal, P. S., Singh, R. P., and Johar, R. (2022). Bio-modified pyrotechnic composite materials for firefighting application. Fire Mater. 46 (8), 1168–1179. doi:10.1002/fam.3060
Pleshivtseva, Y., Derevyanov, M., Pimenov, A., and Rapoport, A. (2023). Comprehensive review of low carbon hydrogen projects towards the decarbonization pathway. Int. J. Hydrogen Energy 48 (10), 3703–3724. doi:10.1016/j.ijhydene.2022.10.209
Romão, E. G. M., Oliveira, M. P., and Guerrini, L. M. (2022). Evaluation of the oligomeric epoxy silane as coupling agent on thermal and mechanical properties of water-based acrylate adhesives. Polym. Eng. Sci. 62 (10), 3310–3322. doi:10.1002/pen.26105
Sharmila, V. G., Tamilarasan, K., Kumar, M. D., Kumar, G., Varjani, S., Kumar, S. A., et al. (2022). Trends in dark biohydrogen production strategy and linkages with transition towards low carbon economy: an outlook, cost-effectiveness, bottlenecks and future scope. Int. J. Hydrogen Energy 47 (34), 15309–15332. doi:10.1016/j.ijhydene.2021.12.139
Shibata, A., Takeda, Y., Kimura, Y., and Tsuji, N. (2022). Hydrogen-related fracture behavior under constant loading tensile test in as-quenched low-carbon martensitic steel. Metals 12 (3), 440. doi:10.3390/met12030440
Sonnendecker, C., Oeser, J., Richter, P. K., Hille, P., Zhao, Z., Fischer, C., et al. (2022). Low carbon footprint recycling of post-consumer PET plastic with a metagenomic polyester hydrolase. ChemSusChem 15 (9), e202101062. doi:10.1002/cssc.202101062
Sovacool, B. K., Newell, P., Carley, S., and Fanzo, J. (2022). Equity, technological innovation and sustainable behaviour in a low-carbon future. Nat. Hum. Behav. 6 (3), 326–337. doi:10.1038/s41562-021-01257-8
Steinbrück, M., Stegmaier, U., Große, M., Czerniak, L., Lahoda, E., Daum, R., et al. (2022). High-temperature oxidation and quenching of chromium-coated zirconium alloy ATF cladding tubes with and w/o pre-damage. J. Nucl. Mater. 559 (15), 153470. doi:10.1016/j.jnucmat.2021.153470
Strassburger, D., Silveira, M. R., Baldissera, A. F., and Ferreira, C. A. (2023). Performance of different water-based resins in the formulation of intumescent coatings for passive fire protection. J. Coatings Technol. Res. 20 (1), 201–221. doi:10.1007/s11998-021-00597-4
Sun, L., Yang, J., and Yan, J. (2022). The structure and properties of water-based silicone blended phenolic resin and its application in oil filter paper-based materials. Korean J. Chem. Eng. 39 (8), 2201–2210. doi:10.1007/s11814-022-1073-8
Tang, Y. M., Chau, K. Y., Fatima, A., and Waqas, M. (2022). Industry 4.0 technology and circular economy practices: business management strategies for environmental sustainability. Environ. Sci. Pollut. Res. 29 (33), 49752–49769. doi:10.1007/s11356-022-19081-6
Thakare, D. R., Xiong, T. M., Flueck, I. L., Morado, E. G., Zimmerman, S. C., and Sottos, N. R. (2022). Acid-responsive anticorrosion microcapsules for self-protecting coatings. Macromol. Chem. Phys. 223 (5), 2100382. doi:10.1002/macp.202100382
Vázquez Loureiro, P., Lestido-Cardama, A., Sendón, R., Bustos, J., Paseiro Losada, P., and Rodríguez Bernaldo de Quirós, A. (2023). Identification of potential migrants from epoxy and organosol coatings used in metal food cans. Food Addit. Contam. Part A 40 (4), 597–611. doi:10.1080/19440049.2023.2183051
Wang, H., Li, X., Zhao, X., Li, C., Song, X., Zhang, P., et al. (2022a). A review on heterogeneous photocatalysis for environmental remediation: from semiconductors to modification strategies. Chin. J. Catal. 43 (2), 178–214. doi:10.1016/s1872-2067(21)63910-4
Wang, L., Chen, L., and Li, Y. (2022b). Digital economy and urban low-carbon sustainable development: the role of innovation factor mobility in China. J. Nucl. Mater. 29 (32), 48539–48557. doi:10.1007/s11356-022-19182-2
Wangari, T. N., Mahajan, G., and Chauhan, B. S. (2022). Glyphosate resistance in junglerice (Echinochloa colona) and alternative herbicide options for its effective control. Weed Technol. 36 (1), 38–47. doi:10.1017/wet.2021.100
Wen, Z., Chen, S., Li, A., Sun, M., Zhang, Y., and Wang, W. (2022). Anticorrosive performance of polyaniline/aluminum tripolyphosphate/waterborne epoxy composite coatings. J. Adhesion Sci. Technol. 36 (23-24), 2527–2546. doi:10.1080/01694243.2022.2067434
Wu, C., Pan, X., Lin, F., Cui, Z., Li, X., Chen, G., et al. (2022). High-temperature electrical properties of polymer-derived ceramic SiBCN thin films fabricated by direct writing. Ceram. Int. 48 (11), 15293–15302. doi:10.1016/j.ceramint.2022.02.063
Keywords: waterborne phenolic-epoxy resin, emulsion preparation, nano SiO2, high temperature resistance, low carbon, environmental protection
Citation: Lu Y, Gu J, Yuan J, Wu L, Wang X, Xu X, Ye F and He L (2024) Optimization of preparation techniques for high-temperature resistant waterborne phenolic-epoxy resin emulsion under low carbon background. Front. Mater. 11:1406583. doi: 10.3389/fmats.2024.1406583
Received: 25 March 2024; Accepted: 16 April 2024;
Published: 01 May 2024.
Edited by:
Tushar Kanti Das, Silesian University of Technology, PolandReviewed by:
Suman Basak, Dyson, United KingdomCopyright © 2024 Lu, Gu, Yuan, Wu, Wang, Xu, Ye and He. This is an open-access article distributed under the terms of the Creative Commons Attribution License (CC BY). The use, distribution or reproduction in other forums is permitted, provided the original author(s) and the copyright owner(s) are credited and that the original publication in this journal is cited, in accordance with accepted academic practice. No use, distribution or reproduction is permitted which does not comply with these terms.
*Correspondence: Libin He, Y3VuZ3VpNUAxNjMuY29t
Disclaimer: All claims expressed in this article are solely those of the authors and do not necessarily represent those of their affiliated organizations, or those of the publisher, the editors and the reviewers. Any product that may be evaluated in this article or claim that may be made by its manufacturer is not guaranteed or endorsed by the publisher.
Research integrity at Frontiers
Learn more about the work of our research integrity team to safeguard the quality of each article we publish.