- 1Shandong Transportation Research Institute, Jinan, China
- 2School of Transportation Southeast University, Nanjing, China
A cold recycling asphalt mixture has significant economic and environmental benefits compared to other pavement material recycling technologies. The cold recycling mixture contains reclaimed asphalt pavement (RAP), new aggregate particles (NAPs), asphalt emulsion, cement, and fillers. The internal material composition is complex, and the interface form is changeable. Both have a significant impact on the mechanical properties. Therefore, this paper aims to study the influence of material composition and related content on the strength performance of a cold recycling mixture from the two aspects of macroscopic mechanical tests and microscopic characteristics analyses. In this paper, the strength evolution law of a cold recycling mixture under changed amounts of cement, emulsified asphalt, and RAP content is carried out. The test result shows that low cement content has little effect on the strength of a cold recycling mixture and is not the main factor affecting its strength composition. The asphalt mainly plays the role of a binder. Compared with the NAPs, the aged asphalt mortar and emulsified asphalt mortar have better interfacial bonding effects. The NAP surface needs more asphalt to form structural asphalt. From the microscopic characteristics of the interfacial transition zone, the cement hydration products and asphalt mortar are intertwined to form a network structure, and the pore structure is filled with asphalt. Compared with the aggregate–asphalt interface, the cement hydration product has poor adhesion with the aggregate. Some micro-cracks are visible in the interface transition zone, which is mainly used as an interface modifier and interface improver to enhance the interface bonding effect.
1 Introduction
Mixture waste, such as reclaimed asphalt pavement (RAP) and recycling stabilized base (RAI), is produced in highway maintenance engineering. Open-pit stacking, landfill, and other traditional treatment methods will cause a certain degree of environmental pollution and lead to waste of nonrenewable resources. Therefore, the reasonable reuse of waste asphalt pavement materials has become the focus of many scholars (Walther et al., 2019; Jia et al., 2023a; Ke et al., 2024; Salih, 2024). A cold recycling mixture is composed of emulsified/foamed asphalt, cement, new aggregate, and RAP material, and its strength composition is consistent with that of a hot mix asphalt mixture (HMA). Mixture strength is provided by the internal friction resistance between aggregates, embedded extrusion force, and the bonding effect between binder and aggregate. Different from HMA, emulsified asphalt must form a continuous asphalt film on the surface of the aggregate and perform as a binder after infiltration adhesion, flocculation demulsification, and water volatilization.
A cold recycling asphalt mixture has the characteristics of low initial strength, high porosity, and continuous strength growth. A certain proportion of cement is usually added to enhance the early strength of the cold recycling mixture and improve its long-term performance (Arimilli et al., 2016; Sabine et al., 2023); at the same time, cement can be regarded as a modifier to enhance the interfacial adhesion between aggregate and asphalt mortar. The asphalt emulsion and cement hydration products interact and penetrate each other, forming a spatial network structure and a composite binder (Wang et al., 2020; Husain et al., 2023) and reducing the gap between the interface transition zone. In addition, the relative content of cement and asphalt emulsion will significantly affect the mechanical properties of cold recycling asphalt mixture (Tangzhong et al., 2017). For RAP material, due to the existence of aging asphalt, the interfacial bonding effect between the RAP and the binder is significantly different from that of new aggregate (Renken et al., 2018; Yunliang et al., 2018; Ngoc et al., 2023; Sadaf and Amir, 2023). Pores in the RAP material will affect the strength performance of the cold recycling mixture. Therefore, there is a complex interaction between the material components of a cold recycling mixture that leads to its complex strength composition mechanism. It is necessary to comprehensively study the influence of various material components and relative content changes on the strength performance (Yan et al., 2011; Buczyński and Iwański, 2017; Zheng, 2017; Ayar, 2018; Min et al., 2018; Graziani et al., 2019; Mazurek et al., 2021; Chakravarthi et al., 2022).
For asphalt concrete materials, the interfacial transition zones between different materials have different microstructure characteristics (binder thickness, immersion depth, pore size, and number) (Büchner et al., 2019; Wang et al., 2023; Wu et al., 2024). Research shows that especially the difference in pore parameters of the interfacial transition zone will directly affect the mechanical strength and failure mode of the mixture (Guofeng et al., 2017). The crack initiation position of a cold recycling mixture under stress is usually located in the internal weak position, especially the micro pores in the interfacial transition zone and asphalt mortar. Therefore, it is helpful to reveal the strength and failure mechanism of a cold recycling mixture by studying the pore characteristics of the interface transition zone. At present, many scholars use scanning electron microscopy (SEM) (Luan et al., 2021; Jia et al., 2023b), nanoindentation and atomic force microscopy (AFM) (Kyu et al., 2017; Shan et al., 2020), and other technical means to study the microscopic physical characteristics and mechanical properties of asphalt mixture. Among them, SEM technology has been widely used in the study of the microstructure morphology and distribution of asphalt mixtures. Combined with image processing analysis methods such as BSE, the characteristic microstructure parameters can be quantitatively analyzed.
In this paper, mechanical strength tests were carried out on cold recycling mixtures with different contents of RAP, cement, and emulsified asphalt, and the strength evolution law of cold recycling materials under different factors was clarified. Based on this, the microscopic characteristics of cold recycling mixture in different aggregate–cement interface transition zones were tested. Compared with the macro performance test results, the strength composition mechanism of the cold recycling mixture is clarified.
2 Test design
2.1 Proportion design
The cold recycling mixture in this article adopts CR25 with medium grain gradation, and the raw materials include RAP material, new aggregate, cement, and emulsified asphalt (Kumar et al., 2024). Based on the screening results of RAP materials, due to the maximum grain limit of RAP and the design gradation requirements, the new aggregate is used in two grades of 16–19 mm and 19–26.5 mm. To maximize the utilization rate of RAP materials, RAP materials are used for aggregates less than 16 mm. The mixing ratio of cold recycling mixture to aggregate part is RAP:NAP: mineral filler = 86.8:10:3.2. The gradation curve is shown in Figure 1. The mineral filler is limestone mineral filler, and NAP is basalt. Shanghai Conch P.O 42.5 ordinary Portland cement is used, and the technical indicators are shown in Table 1. Cationic slow-cracking ordinary emulsified asphalt is used, and the test results and technical requirements are shown in Table 2 (Author Anynomus, 2024).
2.2 Test scheme
A test scheme of RAP material content, asphalt content, cement content, and other factors was designed to study the influence of different material compositions on the mechanical strength of a cold recycling mixture. The specific scheme is shown in Tables 3, 4.
2.3 Test methods
2.3.1 SEM test
An FEI Inspect F50 scanning electron microscope was used for the SEM and BSE analysis reported in this article. In cold recycling asphalt mixtures, cement, and emulsified bitumen work together to provide adhesion as a binder. In order to effectively compare and distinguish the microscopic characteristics of the two types of binders, three mortars were mixed: cement–filler mortar, emulsified asphalt–filler mortar, and cement–emulsified asphalt mortar. The mortars were poured onto a glass slide and placed in a 60°C oven for 3 d. The surface of the mortar was kept clean and tidy during maintenance. The molded specimen is shown in Figure 2.
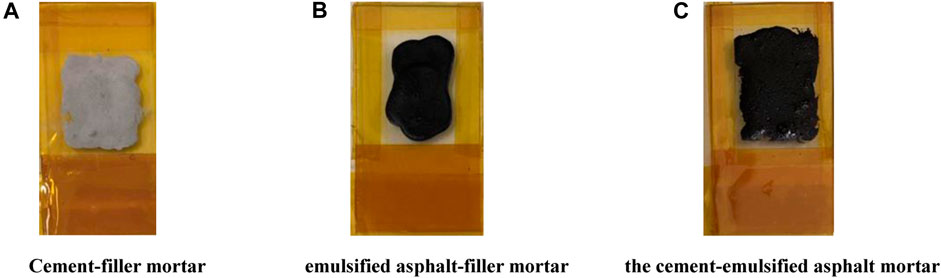
Figure 2. Cold recycling cement mortar molding diagram. (A) Cement-filler mortar. (B) emulsified asphalt-filler mortar. (C) the cement-emulsified asphalt mortar
To observe the interfacial transition zone of the cold recycling mixture, the Marshall compaction method was used to form the cold recycling mixture specimen. The 15 mm × 15 mm × 5 mm specimen was placed in a vacuum drying oven at room temperature for drying. Then, the sample was impregnated with low-viscosity epoxy resin, and the resin was fully solidified for 48 h to ensure that the sample had a high vacuum degree during observation and stabilize the pore structure inside the sample. After the epoxy resin was completely solidified, 400 mesh, 600 mesh, 800 mesh, 1,000 mesh, and 3,000 mesh silicon carbide sandpapers were successively selected by the polishing machine to polish the sample surface to fine smoothness. The surface smoothness of the sample was examined by an optical microscope before the SEM test until the surface was polished to have a clear light reflection. The test process is shown in Figure 3.
This paper adopts different mixing orders and forms cold recycling mixture specimens with different interfaces: NAP–asphalt mortar–cement slurry, old material–asphalt mortar–cement slurry, new material–cement slurry–asphalt mortar, and old material–cement slurry–asphalt mortar. First, the aggregate was mixed with added water for 150 s, and the first binder was added for 90 s. Then, the second binder was added for 90 s, and Marshall compaction was used. The specimens were kept in an oven at 60°C for 3 d, and the specimens of appropriate size were taken to form different small specimens in a 2 cm inner diameter mold, as shown in Figure 4. Then, the specimens were treated according to the test method in Section 2.3.1 and transferred to the scanning electron microscope for observation.
2.3.2 Split test
The splitting strength test is used to test the strength performance of the cold recycling mixture. The test temperature was set to 25°C, and the loading rate was 50 mm/min. The test size was height 100 mm × diameter 63.5 mm. The splitting tensile strength (x) of the cold recycling mixture specimen was calculated and obtained based on the maximum split load value and sample size.
RT: splitting tensile strength (MPa);
PT: maximum split load value (N);
h: specimen height (mm).
3 Analysis of performance test results
3.1 Analysis of different cement content
Four test schemes are adopted to study the performance of cold recycling mixtures with different binders, as shown in Figure 5. Taking cement (4.5% asphalt) as an example, Figure 5 indicates that under this condition, the cement content is changed from 1.0% to 2.5%, and the fixed asphalt content is unchanged at 4.5%. Asphalt (1.5% cement) indicates that the asphalt content changes from 4% to 5.5%, and the fixed cement content remains unchanged at 1.5%; 0% represents none of this type of binder. In order to clearly and conveniently display the diagram of the test results, the horizontal coordinates of Figure 5 are double labeled.
Figure 5 shows that when the asphalt contents of 0% and 4.5% are fixed, and the cement content is changed, the splitting strength of the cold recycling mixture increases linearly with the increase in cement content. When the cement content increases from 1.0% to 2.5%, the overall strength of the cold recycling mixture with 0% asphalt content is lower, the splitting strength increases from 0.24 MPa to 0.35 MPa, and the strength increasing range is 0.11 MPa. The splitting strength of the cold recycling mixture with 4.5% asphalt content increases from 1.31 MPa to 1.40 MPa, and the strength increasing range is 0.09 MPa. Therefore, the effect of cement on the strength increase of the cold recycling mixture is less affected by emulsified asphalt. Compared with the 0% and 4.5% asphalt content samples, the splitting strength of the cold recycling mixture increases by 300%–400% with different cement contents. Therefore, adding a small amount of cement has little effect on the strength of the cold recycling mixture and is not the main factor affecting its strength composition. Asphalt plays a major role as a binder.
When the cement content is fixed, and the emulsified asphalt content is changed, the splitting strength increases first and then decreases. The splitting strength corresponding to 5.0% asphalt content is the maximum. When the asphalt content exceeds the optimal asphalt content, the splitting strength decreases.
The influence of emulsified asphalt and cement on the strength performance of a cold recycling mixture is further clarified. Figure 6 shows the results of two schemes of fixing cement content at 1.5% and 0% and changing the asphalt content. The two schemes are treated differently. That is, to compare the influence of changing asphalt content on the strength of a cold recycling mixture without cement, the figure is expressed as “asphalt (1.5%–0% cement),” and the “cement (4.5%–0% asphalt)” scheme is obtained.
Figure 6 shows that two schemes of changing asphalt content were compared by using 0% cement and 1.5% cement. The splitting strength of the cold recycling mixture with 1.5% cement content is higher than that with 0% cement content, and the strength difference between the two increases with the cement content. Similarly, compared with the fixed 4.5% asphalt content and 0% asphalt content, the splitting strength of the cold recycling asphalt mixture under the former scheme is higher than that under the latter scheme, but the difference in strength between the two schemes is less affected by the change of cement content. When cement and asphalt are used together as binders, the overall strength of a cold recycling mixture can be improved. Cement develops hydration reactions with needle-like microstructures and forms a spatial network structure. The interaction between cement and asphalt enhances the overall cohesion of the binder. Cement can be regarded as an interface adhesion enhancer between the aggregate and the asphalt.
3.2 Analysis of different RAP content
Figure 7 shows that the splitting strength of cold recycling asphalt mixture with 100% RAP content is higher than that with 50% RAP content. This is mainly because the adhesion effect of aging asphalt mortar on the RAP surface is better than that of NAPs and asphalt. This phenomenon can be observed under SEM.
Second, whether RAP content is 50% or 100%, the splitting strength of a cold recycling mixture increases significantly with the increase of asphalt content. For the 50% RAP specimen, the splitting strength increases first and decreases later with the increase of asphalt content, and 5% emulsified asphalt is the optimum asphalt content. For 100% RAP content, the splitting strength increases rapidly with the increase of asphalt content. The 5.5% asphalt content is not the optimum asphalt content. Scheme II-II includes 50% RAP and 50% NAPs, and the NAP surface needs more asphalt to form structural asphalt.
The above analysis shows that the type and content of aggregate and binder will affect the overall strength performance of the cold recycling mixture. At the micro level, different types and contents of binder will form a cohesive state, thus affecting the cohesive performance of asphalt mortar. Second, different aggregate–cement interface forms will affect the pore structure and the distribution of microstructures in the interfacial transition zone, which greatly influences the adhesion performance of the mixture. The adhesion effect of aggregate and cement is particularly important to the mechanical properties of a cold recycling mixture mixed at room temperature. Therefore, SEM microscopic tests with different interface forms are carried out below to extract the key pore parameters and reveal the strength performance mechanism of the cold recycling mixture.
4 SEM result analysis
Because the cold recycling mixture has both cohesive and adhesive strength, SEM tests were carried out on the interface transition zones of the cold recycling binder and the aggregate cement, respectively.
4.1 The SEM binder test results
Figure 8 shows the microscopic scanning diagram of different mortar systems.
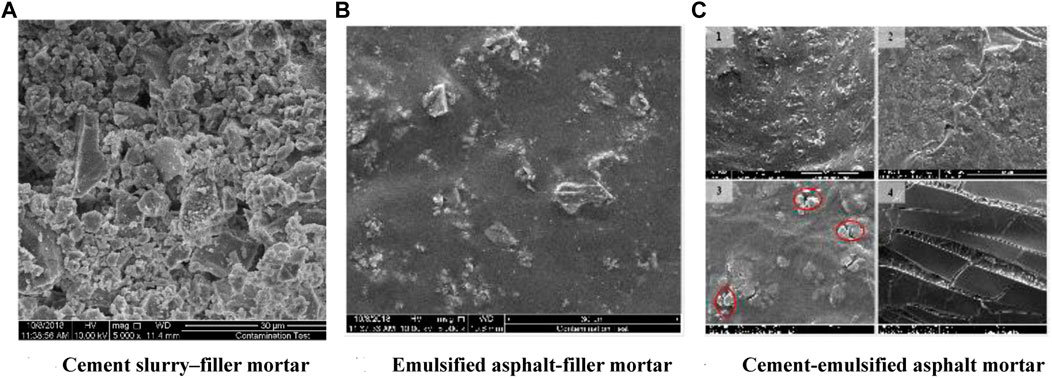
Figure 8. SEM images of different mortar systems of cold recycling mixture. (A) Cement slurry–filler mortar. (B) Emulsified asphalt-filler mortar. (C) Cement-emulsified asphalt mortar.
Figure 8A shows the scanning electron microscope image of the cement slurry–filler structure at 500× magnification. It can be seen that the hydration products of cement are branched and bifurcated, which is due to the bending and twisted band of C-S-H crystals. At the same time, the cement hydration products are mixed with a large number of filler particles. Due to the hindrance of filler particles, cement hydration products do not form continuous C-H crystals. At the same time, filler particles can better fill the pores of cement hydration products. The emulsified asphalt–filler mortar can be seen in Figure 8B. In addition to some larger particles, the filler is more evenly dispersed in the emulsified asphalt, and the surface of the emulsified asphalt is smoother. In Figure 8C showing the cement–emulsified asphalt mortar, Picture 1 shows that some cement particles did not experience a hydration reaction, which is more evenly dispersed in asphalt and plays the role of filler. Picture 2 shows the cement hydration products that have initially formed an interconnected structure. The growth of a single hydration product becomes larger, and the pore structure is gradually compacted. Picture 3 shows that the cement hydration products and asphalt mortar are intertwined to form a network structure. Compared with the complex pore structure in the cement paste shown in Figure 8A, the pore structure in Picture 3 is densely filled with asphalt to form a good overall structure. At the same time, compared with the emulsified asphalt mortar in Figure 8B, due to the hydration reaction of cement after adding cement, the hydration products have the characteristics of high porosity, which will lead to the increase of pores in the mortar system (in the red circle in the figure). The hydration products in Picture 4 show smooth strips.
4.2 SEM test result of aggregate–binder interface
The microstructure of cold recycling composite mortar and its interface with aggregate were studied in this section.
The observed morphology of NAP–cement slurry–asphalt mortar is shown in Figure 9. The vertical red line area is, from right to left, NAPs, cement slurry, and asphalt mortar. Area A is the cement hydration product area, and the local magnification map of area A shows that the cement slurry has the characteristics of multi-porosity, and the local hole phenomenon is obvious. Area B is the transition zone between cement slurry and asphalt mortar. The transition zone is smooth and flat, and the interface is dense. The immersion depth of the interface between asphalt mortar and cement hydration products is approximately 15 μm. Area C is the interface transition zone between the cement hydration products and the aggregate, and the width is approximately 90 μm. The microstructure of the area is loose, and the local cracks are obvious. The fracture characteristics suggest that the cement slurry is dry shrinking during maintenance, and the micro-cracks are interconnecting to form a more visible local crack.
The observation morphology of NAP–asphalt mortar–cement slurry is shown in Figure 10. The deep black area in the middle is the asphalt mortar belt with a thickness of approximately 100 μm. Area A is the interface between the NAPs and the asphalt mortar, and the interface transition is more natural. The immersion depth of asphalt is approximately 6 μm, and the NAPs present a block joint shape. Area B is the transition zone between the asphalt mortar and the cement slurry, and the cement hydration products are distributed in granular form. The immersion depth of asphalt is approximately 2.5 μm. Compared with the bond between cement hydration products and asphalt mortar, the immersion depth of asphalt mortar and NAPs is greater.
Figure 11 shows the observed morphology of RAP material–cement slurry–asphalt mortar, and the areas A, B, and C are RAP, cement slurry, and composite mortar, respectively. The surface of the RAP material in area A is wrapped with different thicknesses of old asphalt mortar. Area B1 is a strip of hydration products with a thickness of approximately 200 μm. The amplification map of the local area B1 shows that the C-S-H crystal is in the shape of a sheaf of wheat. The width of cement hydration products in area B2 is approximately 70 μm, and the particles are loose with more voids and micro-cracks. The immersion depth of the cement–asphalt interface transition zone is approximately 5.5 μm and is mainly composed of cement hydration products, and asphalt is wrapped on the surface of hydration products. Area C shows the transition zone between the cement slurry and the emulsified asphalt mortar.
The observed morphology of the RAP material–asphalt mortar–cement slurry is shown in Figure 12. Area I is RAP material, area II is asphalt mortar, and area III is cement hydration products. The left image in Figure 12 shows that the thickness of the asphalt mortar belt is approximately 40 μm, and the immersion depth with RAP material is approximately 7.5 μm. The right SEM image shows that there is a clear transition zone between the cement hydration products and the asphalt mortar, and the immersion depth of the cement hydration products and asphalt mortar is approximately 6 μm.
4.3 Summary
The SEM tests of the different interface forms indicate that the cement hydration products show porous characteristics and a certain degree of dry shrinkage micro-cracks. The apparent adhesion of cement hydration products and asphalt is good. Compared with the asphalt–aggregate interface, the adhesion effect of cement hydration products and aggregates is poor, and micro-cracks appear in the interface transition zone, which is consistent with the conclusion that cement has little effect on the growth of cold regeneration strength in the macroscopic mechanical properties test. Cement can be considered as an interface bonding performance improver that promotes the demulsification of emulsified asphalt and consumes water to improve the early strength of the cold recycling mixture.
5 Conclusion
In this paper, the mechanisms influencing the strength of cold recycling asphalt mixtures based on material composition were studied. The main conclusions are:
(1) The splitting strength of a cold recycling mixture increases linearly with the increase of cement content and increases first and decreases later with the increase of asphalt content.
(2) The effect of cement on the strength of a cold recycling mixture is less affected by emulsified asphalt, and the effect of low-dose cement on the strength of the cold recycling mixture is smaller. Low-dose cement is not the main factor affecting the strength composition of the mixture. Asphalt plays a major role in cementing material.
(3) The adhesion effect of aging asphalt mortar on the RAP surface is better than that of NAPs and asphalt; compared with RAP, the NAP surface needs more asphalt to form structural asphalt.
(4) For the cement–asphalt mortar system, the filler is uniformly dispersed in emulsified asphalt. The cement hydration products and asphalt mortar are intertwined to form a network structure, and the pore structure is densely filled with asphalt.
(5) The adhesion effect of cement hydration products and aggregate is poor, and asphalt as the main binder has a great influence on the strength performance of a cold recycling mixture.
Data availability statement
The raw data supporting the conclusion of this article will be made available by the authors, without undue reservation.
Author contributions
ZD: formal analysis, funding acquisition, resources, and writing–review and editing. GX: methodology, project administration, and writing–original draft. SX: investigation and writing–original draft. SM: writing–review and editing. TM: writing–review and editing. YL: writing–review and editing. JL: data curation and writing–review and editing.
Funding
The author(s) declare that financial support was received for the research, authorship, and/or publication of this article. This study was sponsored by the National Natural Science Foundation of China (51878164) and the Shandong Provincial Natural Science Foundation (ZR2020KE024). The authors are grateful for the financial support.
Conflict of interest
The authors declare that the research was conducted in the absence of any commercial or financial relationships that could be construed as a potential conflict of interest.
Publisher’s note
All claims expressed in this article are solely those of the authors and do not necessarily represent those of their affiliated organizations, or those of the publisher, the editors, and the reviewers. Any product that may be evaluated in this article, or claim that may be made by its manufacturer, is not guaranteed or endorsed by the publisher.
References
Arimilli, S., Jain, P. K., and Nagabhushana, M. N. (2016). Optimization of recycled asphalt pavement in cold emulsified mixtures by Mechanistic characterization. J. Mater. Civ. Eng. 28 (2). doi:10.1061/(asce)mt.1943-5533.0001412
Author Anynomus (2024). “JTG/T 5521-2019,” in Technical specification for highway asphalt pavement recycling.
Ayar, P. (2018). Effects of additives on the mechanical performance in recycled mixtures with bitumen emulsion: an overview. Constr. Build. Mater. 178, 178551–178561. doi:10.1016/j.conbuildmat.2018.05.174
Büchner, J., Wistuba, M. P., Remmler, T., and Wang, D. (2019). On low temperature binder testing using DSR 4 mm geometry. Mater. Struct. 52, 113–211. doi:10.1617/s11527-019-1412-3
Buczyński, P., and Iwański, M. (2017). Fatigue life Comparison of recycled cold mixes with foamed bitumen and with bitumen emulsion. Procedia Eng. 172, 172135–172142. doi:10.1016/j.proeng.2017.02.035
Chakravarthi, S., Rajkumar, G., and Shankar, S. (2022). A review on design, evaluation, and performance of emulsified asphalt-treated bases using recycled aggregates. Environ. Sci. Pollut. Res. Int. 29 (31), 46570–46586. doi:10.1007/s11356-022-20522-5
Graziani, A., Godenzoni, C., and Canestrari, F. (2019). Experimental characterization of the 3D linear viscoelastic behavior of cold recycled bitumen emulsion mixtures. J. Traffic Transp. Eng. Engl. ed. Online 6 (4), 324–336. doi:10.1016/j.jtte.2019.03.001
Guofeng, L., Peiwen, H., and Jiang, H. (2017). Impacts of freeze-thaw cycles on microscopic characteristics of recycled mixture with foamed asphalt. J. Beijing Univ. Technol. 43 (10), 1508–1513. doi:10.11936/bjutxb2017020008
Husain, F. S., Qamhia, A. I. I., Vyas, A., Maia, R. S., Tutumluer, E., and Hajj, R. (2023). Emulsion mixtures of Fractionated reclaimed asphalt pavement and Quarry by-products: a Laboratory evaluation. Sustainability 15 (13), 10735. doi:10.3390/su151310735
Jia, S., Sang, L., Yaozheng, W., et al. (2023a). Pre-treatment of steel slag and its applicability in asphalt mixtures for sustainable pavements. Chem. Eng. J., 476. doi:10.1016/j.cej.2023.146802
Jia, S., Wei, H., Guoyang, L., et al. (2023b). Investigation of the performance and micro-evolution mechanism of low-content thermosetting epoxy asphalt binder towards sustainable highway and bridge decks paving. J. Clean. Prod., 384. doi:10.1016/j.jclepro.2022.135588
Ke, S., Feng, M., Zhen, F., et al. (2024). Enhancing aged SBS-modified bitumen performance with unaged bitumen additives. Constr. Build. Mater., 412134768. doi:10.1016/J.CONBUILDMAT.2023.134768
Kumar, R., Goli, A., Gottumukkala, V. B., Shankar, S., and Kuna, K. K. (2024). Influence of curing process on the moisture loss, mechanical and performance characteristics of cold recycled asphalt mixes. Road Mater. Pavement Des. 25 (2), 259–275. doi:10.1080/14680629.2023.2199884
Kyu, C. P., Kyungsu, K., Jae, W. K., and Lee, H. J. (2017). Performance evaluation of cold recycled asphalt mixtures with asphalt emulsion and Inorganic additives. Int. J. Highw. Eng. 19 (2), 137–142. doi:10.7855/ijhe.2017.19.2.137
Luan, Y., Chen, T., and Ma, T. (2021). Fracture performance analysis of cold-recycled mixture based on DEM Precise Modeling. China J. Highw. Transp. 34 (10), 125–134. doi:10.19721/j.cnki.1001-7372.2021.10.010
Mazurek, G., Iwański, M., Buczyński, P., and Horodecka, R. (2021). Influence of innovative three-element binder on permanent deformations in recycled mixtures with emulsion and foamed bitumen. Archives Civ. Mech. Eng. 21 (2), 55–26. doi:10.1007/s43452-021-00192-9
Min, Y. K., Joon, H. C., and Yeol, J. R. (2018). Characterization of emulsified asphalt emulsifier for cold recycling asphalt mixture. Int. J. Highw. Eng. 20 (6), 151–161. doi:10.7855/ijhe.2018.20.6.151
Ngoc, L. N., Huu, M. N., Van, D. D., Nguyen, P. Q., Thi Nguyen, T. M., and Tran, T. D. (2023). Effect of curing regimes on the dynamic modulus of entirely RAP cold recycled asphalt mixture. Proc. Institution Mech. Eng. Part L J. Mater. Des. Appl. 237 (9), 1975–1989. doi:10.1177/14644207231167256
Renken, P., Büchler, S., Falchetto, A. C., et al. (2018). Warm mix asphalt-a German case study. Asph. Paving Technol. 87, 685–716.doi:10.12783/aapt2018/33821
Sabine, V., Marine, H., Didier, L., Van Rompu, J., Geisler, F., and Pouget, S. (2023). Development of a novel infrared methodology to assess the degree of blending in cold and warm recycled asphalt mixtures incorporating a bituminous or bio-based virgin binder. Constr. Build. Mater. 403, 133103. doi:10.1016/j.conbuildmat.2023.133103
Sadaf, S., and Amir, M. (2023). Optimization of asphalt cold recycling containing ordinary and waste additives based on life cycle assessment considering the road traffic level-case study: Coal preparation plant. Case Stud. Constr. Mater. 19, e02329. doi:10.1016/j.cscm.2023.e02329
Salih, K. (2024). Cost-effective Use of reclaimed asphalt mixtures with various Rubber Modification technologies for pavement maintenance Applications. J. Mater. Civ. Eng. 36 (4). doi:10.1061/jmcee7.mteng-17174
Shan, L., Zhang, E., and Liu, S. (2020). Etc. Analysis of microscopic Damage mechanism of asphalt binder through atomic force microscopy (AFM). China J. Highw. Transp. 33 (10), 171–177. doi:10.19721/j.cnki.1001-7372.2020.10.011
Tangzhong, W., Jinxiang, H., and Lin, J. (2017). Effect and action mechanism of cement and emulsified asphalt on the strength of cold regeneration. J. Build. Mater. 20 (02), 310–315. doi:10.3969/j.issn.1007-9629.2017.02.027
Walther, A., Büchler, S., Cannone Falchetto, A., Wang, D., Riccardi, C., and Wistuba, M. P. (2019). Experimental investigation on asphalt mixtures prepared with reclaimed asphalt pavement and rejuvenators based on the BTSV method. Road Mater. Pavement Des. 20 (7), 1695–1708. doi:10.1080/14680629.2019.1594053
Wang, D., Hao, P., and Le, J. (2020). Rheological properties of emulsified asphalt residues for cold recycling. Mater. Rep. 34 (06), 6081–6087.
Wang, H., Airey, G. D., Leng, Z., Lu, G., Jin, Y., Hu, H., et al. (2023). Controllable Synthesis, formation mechanism, and Photocatalytic Activity of Tellurium with various Nanostructures. ROAD Mater. PAVEMENT Des. 15, 1–12. doi:10.3390/mi15010001
Wu, W., Cavalli, M. C., Jiang, W., and Kringos, N. (2024). Differing perspectives on the use of high-content SBS polymer-modified bitumen. Constr. Build. Mater. 411, 134433. doi:10.1016/j.conbuildmat.2023.134433
Yan, J., Fujian, N., and Yang, M. (2011). Indirect tensile fatigue properties of asphalt emulsion cold recycled mixes. J. Build. Mater. 14 (01), 58–61. doi:10.3969/j.issn.1007-9629.2011.01.012
Yunliang, L., Liu, Y., and Ji, L. (2018). Effect of aging on dynamic mechanical properties of cement emulsified asphalt mastic. Acta Mater. Compos. Sin. 35 (07), 1975–1982. doi:10.13801/j.cnki.fhclxb.20170821.010
Keywords: cold recycling mixture, interface transition zone, SEM, mechanical properties, strength characteristics
Citation: Dong Z, Xu G, Xu S, Ma S, Ma T, Luan Y and Liu J (2024) Study on the strength composition mechanism and interface microscopic characteristics of cold recycling asphalt mixture. Front. Mater. 11:1397335. doi: 10.3389/fmats.2024.1397335
Received: 07 March 2024; Accepted: 04 April 2024;
Published: 13 June 2024.
Edited by:
Di Wang, University of Ottawa, CanadaReviewed by:
Dongdong Yuan, Chang’an University, ChinaWentong Wang, Shandong University of Science and Technology, China
Fan Zhang, Aalto University, Finland
Copyright © 2024 Dong, Xu, Xu, Ma, Ma, Luan and Liu. This is an open-access article distributed under the terms of the Creative Commons Attribution License (CC BY). The use, distribution or reproduction in other forums is permitted, provided the original author(s) and the copyright owner(s) are credited and that the original publication in this journal is cited, in accordance with accepted academic practice. No use, distribution or reproduction is permitted which does not comply with these terms.
*Correspondence: Shudong Xu, ODQyNjMxODQ5QHFxLmNvbQ==