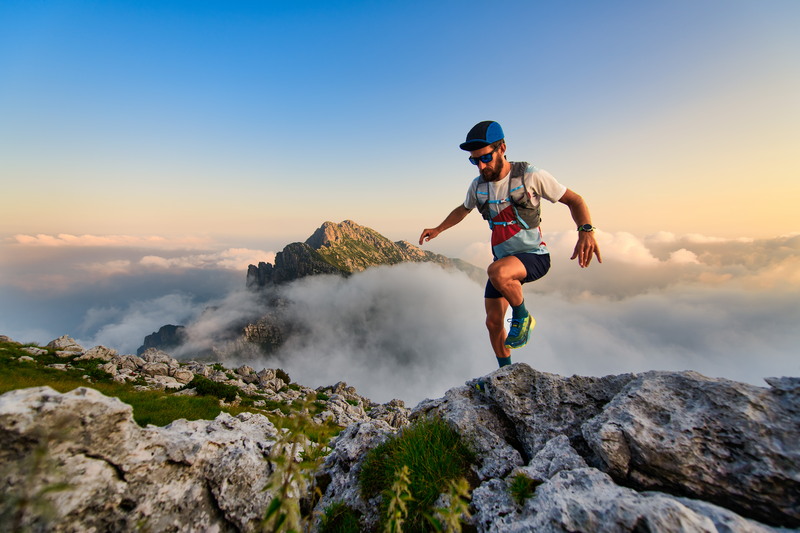
95% of researchers rate our articles as excellent or good
Learn more about the work of our research integrity team to safeguard the quality of each article we publish.
Find out more
EDITORIAL article
Front. Mater. , 12 March 2024
Sec. Mechanics of Materials
Volume 11 - 2024 | https://doi.org/10.3389/fmats.2024.1393286
This article is part of the Research Topic Recent Advances in the Identification of Stress-Strain States of Materials View all 5 articles
Editorial on the Research Topic
Recent advances in the identification of stress-strain states of materials
As materials science and technology progress, residual stress analysis is facing a new set of challenges. Together with microstructure and texture, the stress state is a characteristic parameter of the material state. Since all interaction with the material takes place at its surface, the condition of the component’s surface layers can have a decisive impact on its utility properties. In a material, residual stresses occur without external forces acting on it. The residual stresses are one of the parameters used to determine the overall condition of a material. During the manufacturing process, they arise and affect the strength, fatigue, and corrosion properties of the material. The residual stresses cause unevenness on machining surfaces. It is empirically known that, as the cutting conditions increase, residual stresses increase and surface roughness worsens.
Therefore, one of the bases for maximizing the machining process in terms of workpiece quality is to investigate the impact of the operating conditions on the type and amount of residual stresses in the surface layers of the workpiece. Compared to classical measuring methods, the proposed method (Šafář et al.) involves several improvements that can lead to a quicker understanding of the development of residual stresses. In principle, the solution is based on emphasizing the mechanical or stress-strain parameters of the cut material and on the mechanical balance of the system: material - tool - deformation. The properties of the elements of this system have a high informative value, which must be identified and interpreted in connection with their interactions. The quality of machining is characterized by the degree of accuracy of shape, dimensions, the condition of the surface layer after machining and the associated surface roughness. The use of the topographic function and its stress-strain relations accurately describes the state of the distribution of residual stresses on the cutting surface. The creation of new analytical relations for the prediction of surface roughness resulting from turning and hardening in terms of residual stresses is a unique aspect of this work. In the study reported by Šafář et al., surface topography is shown to be a useful tool for solving questions concerning stress relations during deformation.
As an innovative technique for surface coating preparation, plasma cladding technology provides an efficient solution for the preparation of Fe-based coatings. Plasma cladding has the disadvantage of producing high thermal gradients in the surface layers that cause residual stress to be generated as a result of high heating sources with a high energy density. The use of ultrasonic vibration is being studied by numerous researchers in order to regulate the microstructure and mechanical properties of the clad layers in metal additive manufacturing. Ultrasonic vibration has an important influence on the residual stresses in a substrate. Lai et al. used a one-way test to determine the plasma cladding process parameters by measuring ultrasonic vibration power and frequency. Two factors (ultrasonic frequency and power) were considered in analyzing the impact of ultrasonic vibration on the substrate’s residual stress. On the surface of the plasma substrate, residual stress can be successfully reduced by applying ultrasonic vibration.
Concrete is one of the most popular building materials due to its strength and durability. Adding additives and admixtures to concrete is an important aspect of advanced concrete design. Metakaolin (MK) with steel fibers (SF) has been found to possess unique properties as an additive for concrete, making it particularly suitable for a wide range of applications. There are still several unresolved issues that are discussed in the paper reported by Dou et al. These authors found that the coupling effects of MK and SF on the mechanical performance of high-fluidity concrete, such as strength, ductility, and deformation modulus, have not been adequately studied. They pointed out that there is a lack of quantitative prediction models for the strength and toughness development of MK-modified concrete at different curing ages. A detailed study of the crack developmentand microstructure of steel fiber reinforced concrete (SFRC) incorporating MK has not been conducted after long-term curing. To address this knowledge gap and to contribute to a better understanding of the long-term mechanical behavior and microstructure of MK-SF concretes in the presence of high fluidity, Dou et al. performed a study whose goal was to investigate the stress-strain behavior of MK-SF concretes. A series of changes in the compressive stress-strain curve occurred with increasing MK content over time, namely, an increase in the maximum compressive stress, a decrease in secant slope before failure, and an increase in residual stress after failure. A relative strength or toughness index and a new generalized hyperbola model were proposed to predict its long-term mechanical performance. There was an increase in both failure strain and residual stress after failure in the group with SF compared to the group without MK at both the long-term and early stages. This indicates that MK-SF concrete has improved ductility and resistance to cracking as a result of the addition of SF. Interestingly, MK and SF have demonstrated an impact on the mechanical behavior and performance of concrete, with MK affecting brittleness over a long period of time, while SF improves ductility and crack resistance.
In the context of residual stress and crack propagation, it is important to understand how residual stresses are redistributed. The manufacturing process and component lifetime are connected to the execution of stress analysis. In situ monitoring of crack propagation is particularly interesting. SLM (selective laser melting) is an important technology whose application has become increasingly popular throughout the world. In this Research Topic, Tan et al. presented a study on SLM 316L stainless steel. It was found that the stress concentration at the crack tip has a significant effect on the transformation of strain-induced α′- martensite in the samples.
In this Research Topic, we explore promising, recent, and novel research trends in the identification of stress-strain states of materials. We believe that this will help researchers better understand the mechanical behavior of different materials.
MH: Writing–original draft. JV: Writing–review and editing. VS: Writing–original draft, Writing–review and editing.
The author(s) declare that no financial support was received for the research, authorship, and/or publication of this article.
The authors declare that the research was conducted in the absence of any commercial or financial relationships that could be construed as a potential conflict of interest.
All claims expressed in this article are solely those of the authors and do not necessarily represent those of their affiliated organizations, or those of the publisher, the editors and the reviewers. Any product that may be evaluated in this article, or claim that may be made by its manufacturer, is not guaranteed or endorsed by the publisher.
Keywords: residual stress, mechanical behavior, surface texture, stress-strain states, surface layers
Citation: Harničárová M, Valíček J and Šepeľák V (2024) Editorial: Recent advances in the identification of stress-strain states of materials. Front. Mater. 11:1393286. doi: 10.3389/fmats.2024.1393286
Received: 28 February 2024; Accepted: 29 February 2024;
Published: 12 March 2024.
Edited and reviewed by:
Nicola Maria Pugno, University of Trento, ItalyCopyright © 2024 Harničárová, Valíček and Šepeľák. This is an open-access article distributed under the terms of the Creative Commons Attribution License (CC BY). The use, distribution or reproduction in other forums is permitted, provided the original author(s) and the copyright owner(s) are credited and that the original publication in this journal is cited, in accordance with accepted academic practice. No use, distribution or reproduction is permitted which does not comply with these terms.
*Correspondence: Marta Harničárová, bWFydGEuaGFybmljYXJvdmFAdW5pYWcuc2s=
Disclaimer: All claims expressed in this article are solely those of the authors and do not necessarily represent those of their affiliated organizations, or those of the publisher, the editors and the reviewers. Any product that may be evaluated in this article or claim that may be made by its manufacturer is not guaranteed or endorsed by the publisher.
Research integrity at Frontiers
Learn more about the work of our research integrity team to safeguard the quality of each article we publish.