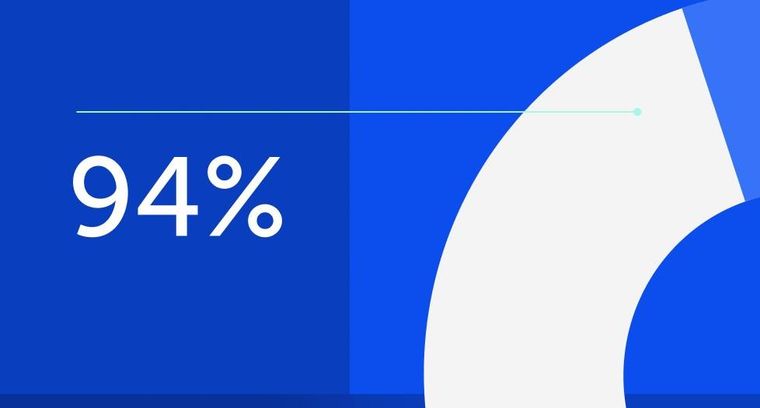
94% of researchers rate our articles as excellent or good
Learn more about the work of our research integrity team to safeguard the quality of each article we publish.
Find out more
ORIGINAL RESEARCH article
Front. Mater., 08 February 2024
Sec. Polymeric and Composite Materials
Volume 11 - 2024 | https://doi.org/10.3389/fmats.2024.1355976
Siloxanes are a group of substances characterized by Si-O-Si functional group. Siloxanes can react with alcohols to form Si-O-C bond. Siloxanes have been widely used as crossing linking agents and graft copolymers as well as additives for plastics. Lignin contains both phenolic and aliphatic hydroxy groups which have the potential to instigate bonding with siloxane compounds. However, there has not been any attempt to apply siloxanes as crosslinking agents for biobased composite formation. This manuscript presents the first study of applying siloxanes compounds to lignin and Cellulose nanofibers (CNF) with respective PLA, PETG, and HDPE to prepare biocomposites. Both Tetramethyl Tetraphenyl Trisiloxane (TTT) and Tetraethoxysilane (TEOS) were used as cross-linking agents. We have successfully incorporated 20 wt% lignin and 10 wt% CNF into the biocomposite filaments. The tensile properties of ensuing biocomposite were investigated. The objective of this work is to demonstrate the potential of lignin and CNF as a sustainable co-polymer to improve the properties of PLA/PETG/HDPE-based materials for 3D printing. This paper will also discuss the challenges and opportunities associated with the use of lignin in 3D printing, including the effect of lignin and CNF content on the mechanical and thermal properties, the compatibility of lignin and CNF with PLA/PETG/HDPE, and the potential for further optimization of the cross-linking chemistry using TTT and TEOS.
Additive manufacturing, commonly known as 3D printing, stands as a rapidly advancing technology that facilitates the efficient creation of intricate geometric structures with unparalleled freedom. Among the various techniques within additive manufacturing, fused deposition modeling (FDM) emerges as the foremost and versatile technique in which a solid thermoplastic filament is used as a feedstock (Nguyen et al., 2018a; Wasti and Adhikari, 2020). In FDM, a solid thermoplastic filament serves as the raw material, passing through an extruder where it undergoes melting. Layer by layer, the melted material is deposited on the build platform, gradually solidifying into the desired object. To give an example, Nguyen et al. (2018a) have extensively investigated the FDM-printability and rheological behavior of polymer and lignin composites. Their study found that the structural units of lignin correlate to the rheological properties to prepare renewable 3D-printable materials that exhibit outstanding printability and mechanical performances. This offers a quantitative measure of the material’s printability, which was determined based on viscosity change with temperature and shear rate. This illustrates that the lignin type plays a role in printability. Also, by applying melt rheology Nguyen et al. determined compositions for lignin-based, fiber-reinforced composites demonstrate extraordinary mechanical properties and superior 3D printability by FDM.
Commonly used thermoplastics employed in this process include polylactic acid (PLA), Polyethylene Terephthalate Glycol (PETG), High-Density Polyethylene (HDPE), and acrylonitrile butadiene styrene (ABS), the majority of which are derived from petroleum (Wasti and Adhikari, 2020). These petroleum-based polymers find widespread usage in industries such as packaging, automobiles, and construction (Mimini et al., 2019). However, the extensive reliance on these materials has given rise to environmental challenges, notably an increase in greenhouse gas emissions. In response to the environmental repercussions stemming from the overuse of petroleum-based plastics and the global shift towards a circular economy from a single-use paradigm, researchers are actively engaged in the development of bio-based sustainable materials. These materials are poised to serve as viable alternatives to their petroleum-based counterparts, aiming to mitigate environmental impact while meeting the evolving needs of society.
Lignin, a natural polymer found in plant cell walls, is a promising candidate for blending with PLA due to its abundance, low cost, and potential to improve mechanical properties. It is the second most abundant renewable bio-resource after cellulose and is considered as a waste product in several industrial processes (Tanase-Opedal et al., 2019; Wasti et al., 2021). Lignin is a renewable and biodegradable material that can be extracted from various sources such as wood, grasses, and agricultural residues (Liu et al., 2016;Kun and Pukánszky, 2017 Nguyen et al., 2018b). Incorporating lignin into 3D printing filaments improves the mechanical properties of the printed products, making them more environmentally friendly and biodegradable. Blending thermoplastics with lignin to produce composite filaments for 3D printing is a promising bio-based option that could increase lignin utilization rather than burning it for heating energy. The use of lignin as a feedstock in biopolymer manufacturing helps its valorization. Several studies were carried out regarding incorporating lignin with PLA, PETG, and HDPE to form composite filaments for 3D printing, making it evident that lignin’s addition often leads to decreased tensile strength and elongation Liu and Wang, 2010; Kun and Pukánszky, 2017; Szabó et al., 2017; Romhányi et al., 2018; Ajay Kumar et al., 2020; Amjadi and Fatemi, 2020; Zhang et al., 2022). Filaments with poor properties will be the death of successful commercialization efforts. There is still a lack of studies done regarding the enhancement of PLA/PETG/HDPE-lignin composite filaments’ properties. Various strategies were found in literature to enhance the properties of polymer-lignin composite filaments, such as modifying lignin, adding cross-linking agents, and carbon fibers.
Cellulose nanofibers (CNF) are an emerging class of nanomaterials derived from renewable sources such as wood pulp, cotton, and agricultural waste. CNF has received significant attention as a potential reinforcement agent for biodegradable polymers such as polylactic acid (PLA). The addition of CNF to thermoplastic polymers has been shown to significantly enhance the mechanical properties of the resulting biocomposite materials, including improved strength, stiffness, and toughness (Kun and Pukánszky, 2017; Nguyen et al., 2018b; Zhang et al., 2022). However, the combination of cellulose fiber and PLA exhibited poor interfacial compatibility due to the presence of hydrophilic groups in cellulose and hydrophobic groups in PLA. Therefore, the hydrophobic modification of cellulose using some adhesive such as lignin is often necessary to promote the interfacial compatibility of cellulose and the PLA matrix, which can improve the physical properties (Jonoobi et al., 2010; Fortunati et al., 2014; Zhang et al., 2021).
In this study, lignin and CNF were blended with PLA, PETG, and HDPE in varying amounts to obtain biocomposite filaments. We were successfully able to incorporate 20 wt% lignin and 10 wt% CNF in the biocomposite filaments. The tensile properties of produced biocomposite filaments were studied. The objective of this work is to explore the potential of lignin and CNF as a sustainable additive to improve the properties of PLA/PETG/HDPE-based materials for 3D printing. This paper will also discuss the challenges and opportunities associated with the use of lignin in 3D printing, including the effect of lignin and CNF content on the mechanical and thermal properties, the compatibility of lignin and CNF with PLA/PETG/HDPE, and the potential for further optimization of the cross-linking agents Tetramethyl Tetraphenyl Trisiloxane (TTT) and Tetraethoxysilane (TEOS).
The study encompasses three polymer matrices—PETG, HDPE, and PLA—chosen for their diverse properties. PETG (Polyethylene terephthalate glycol) is a thermoplastic polyester that has significant chemical resistance, durability, high impact resistance, and is better suited to higher temperatures. HDPE (High Density Polyethylene) is a thermoplastic polymer made from petroleum and is known for its outstanding tensile strength, high impact resistance, and melting point. PLA (Polylactic acid) is a thermoplastic polymer derived from renewable sources such as corn starch or sugar cane. PLA demonstrates high mechanical strength, good processing ability with low shrinkage, and is completely biodegradable. PETG and PLA pellets were purchased from 3DXTECH (Grand Rapids, MI, United States). HDPE pellets were purchased from Premier Plastic Resins (Lake Orion, MI, United States).
Lignin, a natural polymer commonly found in plant cell walls, is a renewable and biodegradable material that can be extracted from various sources such as wood, grasses, and agricultural residues. The lignin used in this study was extracted from pine wood by deep eutectic solvent (DES), the steps of which can be found in our previous work (Alvarez-Vasco et al., 2016; Lin et al., 2023). DES is a mixture of two or more chemicals acting as either hydrogen-bond donors (HBD) or hydrogen-bond acceptors (HBA). In this study, the DES was prepared using a 2:1 M ratio of lactic acid and choline chloride (La-ChCl). A 10:1 mass ratio of DES and pine wood (16–40 mesh) are then mixed and treated at
Two cross-linking agents are incorporated to enhance the three thermoplastic polymers properties. 7044B vacuum diffusion oil (Tetramethyl Tetraphenyl Trisiloxane (TTT)) is a commercial silocone oil that has a strong attraction to both lignin and the polymer matrix. Tetraethoxysilane (TEOS) is silane compound which forms bonds with hydroxyl groups found in both lignin and the polymer matrix. TTT and TEOS were provided by BSEL (Richland, WA, United States). Cellulose nanofibers (CNF) are made from wood-derived fiber (pulp) that has been micro-refined to the nano level. CNF retains most of the characteristics of cellulose with low density, biodegradability, and biocompatibility, but also possesses other excellent properties such as high specific surface area, large aspect ratio, high crystallinity, and high surface activity. A dried, powdered form of CNF was purchased from Sappi (Boston, MA, United States). Sappi has reported the length of the fibers to be between 70nm–5
PLA, PETG, and HDPE pellets were pre-dried in the Fisher Isotemp Vacuum Oven (Model 281) at
A 3D CAD model for dynamic mechanical analysis (DMA) were prepared using Solidworks. A dog bone sample following the ASTM D638 type V dimensions was prepared. The Solidworks files were converted into. STL files and imported into the Prusa software for 3D printing. Filament with a diameter in the range of 1.4–1.8 mm were selected and used for 3D printing using the Prusa MK3S+ (Prague, Hlavni mesto Praha, Czech Republic). The printer had a nozzle diameter of 0.4 mm and was set at a temperature of 200
Differential Scanning Calorimetry (DSC) was performed using a 214 Polyma (NETZSCH, Selb, Bayern, Germany), operated under a nitrogen atmosphere at the flow rate of 40 mL/min. The samples, weighting from 5–10 mg, were first heated to 300
As shown in Table 2, it can be seen that after incorporation of lignin, there was a slightly lower Tg for both PLA and PETG composites. However, this is contrary to HDPE composite, the Tg of which increased to around 160°C from about 133°C. Figure 2 illustrates the FT-IR spectra of three composites. The broad troughs between wavenumber 2900–3,000 cm-1 (carboxylic -O-H) and ranging around 3,300–3,500 cm-1 (alcoholic -O-H) are missing completely, which indicates they go to form ester linkage. As shown, the C=O double bond stretch in ester functional group is located at around 1745 cm-1. The peak seen ranging from 1,150–1,250 cm-1 is the asymmetric C-C-O stretch. The vibration shifts in the range of 1,050–1,100 cm-1 representing the asymmetric O-C-C stretch. For both pre- and post-addition of lignin, all the adsorption peaks fall into the same range of chemical shifts, which indicates that addition of lignin has slight effect on the cross-linking in forming PLA composites. The CNF is rich in hydroxyl groups, so CNF addition leads to an increased density of ester bonds, which can be proved by the sharper peaks appearing in FT-IR spectra.
The results of mechanical testing of PLA, PETG, and HDPE composites with the incorporation of lignin, CNF, and the cross-linking agents are presented in Figure 3, Figure 4, Figure 5. On the whole, according to the results, adding more than 10 wt% CNF in PLA showed poor mechanical properties even though we successfully produced filaments. Therefore, two different cross-linking agents, a 704BB vacuum diffusion pump oil Tetramethyl Tetraphenyl Trisiloxane (TTT) and Tetraethoxysilane (TEOS), were added in with the blending process of the three thermoplastics. TTT is a silicone-based substance that stands out for its strong attraction to both lignin and the polymer matrix (Ransom et al., 2019; AZoM.com, 2023). When added to the polymer blend, it forms networks through physical entanglement and weak chemical interactions. This process enhances the material’s toughness, impact resistance, and elongation properties. Also, the compatibility of this oil with lignin helps evenly disperse lignin particles within the polymer matrix, further improving mechanical properties and ensuring a uniform structure. TEOS is a silane compound which forms bonds with hydroxyl groups found in both lignin and the polymer matrix. This chemical bonding creates a strong network that improves thermal stability, chemical resistance, and dimensional stability of the material (Shweta and Jha, 2015; Shweta and Jha, 2016; Liu et al., 2022). Additionally, the silica-rich nature of TEOS cross-linking enhances the material’s fire resistance, making it a promising choice for applications where safety is a top priority.
The results in Figure 3; Figure 4; Figure 5 indicate that with the addition of lignin in PLA, PETG, and HDPE, the tensile strength of the composites decreases. There is an approximate 30% decrease in the tensile strength with a 20 wt% addition of lignin. With the addition of 10 wt% of CNF the tensile strength increases for all thermoplastics, averaging 44 MPa, which is stronger than both pure PLA and pure HDPE. The positive impact of the nanofibers, especially in the composite strength indicates that the used nanofibers have good mechanical properties and that there is an interaction between the PLA/PETG/HDPE and the CNF.
The baseline tensile strength of pure PLA was measured at 42.54 MPa. Introducing lignin into PLA significantly decreased tensile strength, with an average value of 25.89 MPa, representing a reduction of approximately 39%. This decrease can be attributed to the incompatibility of lignin with PLA, which disrupts the polymer matrix, creating weak points and reducing overall strength. Wasti et al. reported a 25% decrease in tensile strength with a 20 wt% addition of lignin (Wasti et al., 2021). This result was attributed to a decrease in the effective load-bearing cross-section of PLA in the presence of lignin (Kumar Singla et al., 2016). TTT as a coupling agent alongside lignin resulted in a notable increase in tensile strength, reaching an average of 49.50 MPa, representing an increase of approximately 92%. TTT acts as a coupling agent, improving the adhesion between lignin and the PLA matrix, which enhances the interfacial bonding and, subsequently, the tensile strength. The combination of lignin, cellulose nanofibers (CNF), and TTT within the PLA matrix exhibited the highest tensile strength at 56.39 MPa, showcasing the synergistic enhancement achieved by adding multiple reinforcing agents. When tetraethoxysilane (TEOS) was introduced in the PLA composite with lignin and CNF, the highest tensile strength was recorded, with an average value of 57.16 MPa. TEOS likely played a role in forming a silica-based network within the composite, strengthening the material, and further improving the tensile strength. Bang et al. observed the resulting PLA/SiO2 hybrids showed improved phase compatibility capable of creating covalent bonds between the organic and the inorganic phases. This strong bonding resulted in homogeneous microstructures with silica nanoparticles dispersed in the PLA matrix (Bang and Kim, 2012). Incorporating CNF with PLA, along with the cross-linking agents TTT and TEOS, enhances the tensile strength of the composite. This improvement can be attributed to the reinforcing effects of CNF, which bridges and strengthens the polymer matrix, ultimately enhancing load transfer and stress distribution within the material. In Jonoobi et al. (2010) PLA was mixed with 1,3, and 5 wt% of CNF and observed an increase in tensile strength and modulus of about 20% in all cases. Santos et al. and Suryanegara et al. reported similar improvements for PLA-CNF with 5 wt% fiber content (Suryanegara et al., 2009; dos Santos et al., 2016).
The baseline tensile strength of pure HDPE was established at 37.86 MPa. The introduction of lignin into HDPE decreased tensile strength, with an average of 28.04 MPa, representing a reduction of approximately 26%. In this case, lignin disrupts the HDPE matrix, creating weaknesses that result in decreased tensile strength. However, including TTT as a coupling agent alongside lignin increased tensile strength to 39.25 MPa, representing an increase of approximately 40%. TTT serves as a coupling agent, improving the adhesion between lignin and the HDPE matrix, strengthening the interfacial bonding, and improving tensile strength. The combination of lignin, CNF, and TTT within the HDPE matrix demonstrated the highest tensile strength at 50.84 MPa, highlighting the role of TTT in reinforcing interfacial interactions and representing an increase of approximately 81%. The enhancement in tensile strength can be attributed to the synergistic effects of CNF and TTT, where CNF strengthens the matrix, while TTT improves interfacial adhesion. Incorporating TEOS into HDPE with lignin led to an average tensile strength of 40.95 MPa, indicating an increase of approximately 7.4% compared to the composite without TEOS. TEOS likely formed a silica-based network, contributing to improved material strength, and the composite containing lignin, CNF, and TEOS which reached the highest tensile strength at 53.38 MPa, representing an increase of approximately 40% compared to the baseline. The addition of TEOS complemented the reinforcing effects of CNF and TTT, resulting in further improvement in tensile strength. In Ma et al. they observed that, when the TEOS dosage in their HDPE hybrid material was linearly increased, the tensile strength linearly increased as well, finding an approximate 31% increase in their tensile strength with the addition of TEOS (Ma et al., 2014).
The baseline tensile strength of pure PETG was measured at 50.52 MPa. The introduction of lignin into PETG reduced tensile strength, averaging 39.96 MPa, representing a reduction of approximately 21%. This reduction is often associated with the incompatibility of lignin with PETG, weakening interfacial interactions, and reducing the strength. However, when TTT was added as a coupling agent alongside lignin, the tensile strength increased to 49.81 MPa, indicating an increase of approximately 25%. TTT improved interfacial bonding between lignin and PETG, enhancing tensile strength. The combination of lignin, cellulose nanofibers (CNF), and TTT within the PETG matrix resulted in the highest tensile strength at 54.29 MPa, demonstrating the synergistic effect achieved by incorporating multiple reinforcing agents and representing an increase of approximately 7.6%. CNF’s reinforcing effect was crucial in this enhancement, while TTT improved adhesion, contributing to increased tensile strength. Additionally, incorporating TEOS into PETG with lignin led to an average tensile strength of 52.18 MPa, indicating an increase of approximately 30% compared to the composite without TEOS. TEOS likely strengthened the material further by forming a silica-based network. The composite containing lignin, CNF, and TEOS exhibited the highest tensile strength at 55.45 MPa, representing an increase of approximately 10.7% compared to the baseline. TEOS added to the synergistic effect of CNF and TTT, resulting in enhanced tensile strength.
Based on the characterizations, we proposed the cross linking diagram in PLA based composite. As depicted in Figure 6, the incorporated lignin and CNF connect with the carbonyl groups in PLA through hydrogen bonds. Similarly, the TEOS links to the hydroxyl groups of lignin and CNF by both hydrogen and covalent bonds. Whereas, neither the Si-O nor the Si-O-C adsorption peaks were observed in FT-IR spectra in Figure 2. This might be because of the small number of Si-O or Si-O-C bonds trapped in the fragment of composite that were not detectable. The aliphatic fractions of CNF and lignin incorporation may enable to increase the tensile strength of composite. However, the aromatic fractions in lignin may decrease the tensile strength of PLA composite.
In our study, we initially compared the controls, which were pure Polylactic Acid (PLA), Polyethylene Terephthalate Glycol (PETG), and High-Density Polyethylene (HDPE) to establish baseline tensile strengths. Among the controls, PLA exhibited a tensile strength of 42.54 MPa, HDPE had a tensile strength of 37.86 MPa, and PETG showed the highest tensile strength at 50.52 MPa. This initial comparison highlights the inherent differences in mechanical properties among these polymers, with PETG demonstrating superior tensile strength compared to PLA and HDPE. We then explored the impact of various additives on these polymer matrices. The introduction of lignin into the polymers initially led to decreased tensile strength, suggesting incompatibility and potential weakening of the matrix. However, adding cellulose nanofibers (CNF) alongside lignin positively affected tensile strength, indicating the potential for reinforcement through CNF addition. This observation suggests that CNF significantly enhances mechanical properties and could serve as a precursor for cross-linking. We incorporated Tetraethoxysilane (TEOS) and Tetramethyl Tetraphenyl Trisiloxane (TTT) into all three polymers to test the cross-linking hypothesis. The results supported our hypothesis, as adding TEOS and TTT significantly improved the tensile strength in all cases. This indicates that the cross-linking effect of TEOS and TTT successfully enhanced the mechanical properties of PLA, HDPE, and PETG.
To explore the potential replacement of PETG and HDPE with PLA-based composites, we compared the tensile strengths of PLA-Lignin and PLA-Lignin-CNF composites. The addition of lignin initially led to decreased tensile strength in PLA. However, the subsequent inclusion of CNF, known for its reinforcing properties, significantly improved tensile strength. This finding suggests that PLA-based composites, with the right combination of additives like CNF, can potentially replace PETG and HDPE while maintaining or enhancing tensile properties. This indicates a promising direction for sustainable and high-performance polymer composites in various applications.
The original contributions presented in the study are included in the article/Supplementary Material, further inquiries can be directed to the corresponding author.
SG: Investigation, Validation, Writing–original draft, Writing–review and editing. XZ: Writing–review and editing. C-HY: Conceptualization, Data curation, Formal Analysis, Funding acquisition, Investigation, Methodology, Project administration, Resources, Supervision, Validation, Writing–review and editing. IO: Writing–review and editing. CW: Writing–review and editing.
The author(s) declare that no financial support was received for the research, authorship, and/or publication of this article.
We would like to thank Washington State University office of commercialization for funding this work.
The authors declare that the research was conducted in the absence of any commercial or financial relationships that could be construed as a potential conflict of interest.
All claims expressed in this article are solely those of the authors and do not necessarily represent those of their affiliated organizations, or those of the publisher, the editors and the reviewers. Any product that may be evaluated in this article, or claim that may be made by its manufacturer, is not guaranteed or endorsed by the publisher.
Ajay Kumar, M., Khan, M. S., and Mishra, S. B. (2020). Effect of machine parameters on strength and hardness of FDM printed carbon fiber reinforced PETG thermoplastics. Mater. Today Proc. 27, 975–983. doi:10.1016/j.matpr.2020.01.291
Alvarez-Vasco, C., Ma, R., Quintero, M., Guo, M., Geleynse, S., Ramasamy, K. K., et al. (2016). Unique low-molecular-weight lignin with high purity extracted from wood by deep eutectic solvents (DES): a source of lignin for valorization. Green Chem. 18 (19), 5133–5141. doi:10.1039/C6GC01007E
Amjadi, M., and Fatemi, A. (2020). Creep and fatigue behaviors of High-Density Polyethylene (HDPE): effects of temperature, mean stress, frequency, and processing technique. Int. J. Fatigue 141, 105871. doi:10.1016/j.ijfatigue.2020.105871
AZoM.com (2023). The spectra of Dow704 diffusion pump oil. Availableat: https://www.azom.com/article.aspx?ArticleID=11531 (Accessed May 09, 2023).
Bang, G., and Kim, S. W. (2012). Biodegradable poly(lactic acid)-based hybrid coating materials for food packaging films with gas barrier properties. J. Ind. Eng. Chem. 18 (3), 1063–1068. doi:10.1016/j.jiec.2011.12.004
dos Santos, F. A., Iulianelli, G. C. V., and Tavares, M. I. B. (2016). The use of cellulose nanofillers in obtaining polymer nanocomposites: properties, processing, and applications. Mater. Sci. Appl. 7 (5), 257–294. doi:10.4236/msa.2016.75026
Fortunati, E., Luzi, F., Puglia, D., Dominici, F., Santulli, C., Kenny, J., et al. (2014). Investigation of thermo-mechanical, chemical and degradative properties of PLA-limonene films reinforced with cellulose nanocrystals extracted from Phormium tenax leaves. Eur. Polym. J. 56, 77–91. doi:10.1016/j.eurpolymj.2014.03.030
Jonoobi, M., Harun, J., Mathew, A. P., and Oksman, K. (2010). Mechanical properties of cellulose nanofiber (CNF) reinforced polylactic acid (PLA) prepared by twin screw extrusion. Compos. Sci. Technol. 70 (12), 1742–1747. doi:10.1016/j.compscitech.2010.07.005
Kumar Singla, R., Maiti, S. N., and Ghosh, A. K. (2016). Crystallization, morphological, and mechanical response of poly(lactic acid)/lignin-based biodegradable composites. Polym.-Plast. Technol. Eng. 55 (5), 475–485. doi:10.1080/03602559.2015.1098688
Kun, D., and Pukánszky, B. (2017). Polymer/lignin blends: interactions, properties, applications. Eur. Polym. J. 93, 618–641. doi:10.1016/j.eurpolymj.2017.04.035
Lin, K.-T., Wang, C., Guo, M. F., Aprà, E., Ma, R., Ragauskas, A. J., et al. (2023). Lignin with controlled structural properties by N-heterocycle-based deep eutectic solvent extraction. Proc. Natl. Acad. Sci. 120 (32), e2307323120. doi:10.1073/pnas.2307323120
Liu, L., Qian, M., Song, P., Huang, G., Yu, Y., and Fu, S. (2016). Fabrication of green lignin-based flame retardants for enhancing the thermal and fire retardancy properties of polypropylene/wood composites. ACS Sustain. Chem. Eng. 4 (4), 2422–2431. doi:10.1021/acssuschemeng.6b00112
Liu, T., and Wang, Q. W. (2010). Bio-ethanol lignin waste/HDPE composites: preparation and mechanical properties. Adv. Mater. Res. 113 (116), 606–609. doi:10.4028/www.scientific.net/AMR.113-116.606
Liu, W., Yi, S., Liu, Z., Mo, Q., Xian, X., Ma, L., et al. (2022). Sol-gel silica modified recovered lignin particles and its application as blend with HDPE. Ind. Crops Prod. 189, 115842. doi:10.1016/j.indcrop.2022.115842
Ma, W., Gong, F., Liu, C., Tao, G., Xu, J., and Jiang, B. (2014). SiO2 reinforced HDPE hybrid materials obtained by the sol–gel method. J. Appl. Polym. Sci. 131 (6). doi:10.1002/app.39891
Mimini, V., Sykacek, E., Syed Hashim, S. N. A., Holzweber, J., Hettegger, H., Fackler, K., et al. (2019). Compatibility of kraft lignin, organosolv lignin and lignosulfonate with PLA in 3D printing. J. Wood Chem. Technol. 39 (1), 14–30. doi:10.1080/02773813.2018.1488875
Nguyen, N. A., Barnes, S. H., Bowland, C. C., Meek, K. M., Littrell, K. C., Keum, J. K., et al. (2018a). A path for lignin valorization via additive manufacturing of high-performance sustainable composites with enhanced 3D printability. Sci. Adv. 4 (12), eaat4967. doi:10.1126/sciadv.aat4967
Nguyen, N. A., Bowland, C. C., and Naskar, A. K. (2018b). A general method to improve 3D-printability and inter-layer adhesion in lignin-based composites. Appl. Mater. Today 12, 138–152. doi:10.1016/j.apmt.2018.03.009
Pawale, S., Kalia, K., Alshammari, S., Cronin, D., Zhang, X., and Ameli, A. (2022). Deep eutectic solvent-extracted lignin as an efficient additive for entirely biobased polylactic acid composites. ACS Appl. Polym. Mater. 4 (8), 5861–5871. doi:10.1021/acsapm.2c00742
Ransom, T. C., Casalini, R., Fragiadakis, D., and Ronald, C. M. (2019). The complex behavior of the ‘simplest’ liquid: breakdown of density scaling in tetramethyl tetraphenyl trisiloxane. J. Chem. Phys. 151, 174501. doi:10.1063/1.5121021
Romhányi, V., Kun, D., and Pukánszky, B. (2018). Correlations among miscibility, structure, and properties in thermoplastic polymer/lignin blends. ACS Sustain. Chem. Eng. 6 (11), 14323–14331. doi:10.1021/acssuschemeng.8b02989
Sappi Global (2024). Valida nanocellulose. Available at: https://www.sappi.com/valida-nanocellulose (Accessed January 21, 2024).
Shweta, K., and Jha, H. (2016). Synthesis and characterization of crystalline carboxymethylated lignin–TEOS nanocomposites for metal adsorption and antibacterial activity. Bioresour. Bioprocess. 3, 31. doi:10.1186/s40643-016-0107-7
Shweta, K., and Jha, H. (2015). Rice husk extracted lignin–TEOS biocomposites: effects of acetylation and silane surface treatments for application in nickel removal. Biotechnol. Rep. 7, 95–106. doi:10.1016/j.btre.2015.05.003
Suryanegara, L., Nakagaito, A. N., and Yano, H. (2009). The effect of crystallization of PLA on the thermal and mechanical properties of microfibrillated cellulose-reinforced PLA composites. Compos. Sci. Technol. 69 (7), 1187–1192. doi:10.1016/j.compscitech.2009.02.022
Szabó, G., Romhányi, V., Kun, D., Renner, K., and Pukánszky, B. (2017). Competitive interactions in aromatic polymer/lignosulfonate blends. ACS Sustain. Chem. Eng. 5 (1), 410–419. doi:10.1021/acssuschemeng.6b01785
Tanase-Opedal, M., Espinosa, E., Rodríguez, A., and Chinga-Carrasco, G. (2019). Lignin: a biopolymer from forestry biomass for biocomposites and 3D printing. Materials 12, 3006. doi:10.3390/ma12183006
Wasti, S., and Adhikari, S. (2020). Use of biomaterials for 3D printing by fused deposition modeling technique: a review. Front. Chem. 8, 315. doi:10.3389/fchem.2020.00315
Wasti, S., Triggs, E., Farag, R., Auad, M., Adhikari, S., Bajwa, D., et al. (2021). Influence of plasticizers on thermal and mechanical properties of biocomposite filaments made from lignin and polylactic acid for 3D printing. Compos. Part B Eng. 205, 108483. doi:10.1016/j.compositesb.2020.108483
Zhang, K., Chen, Z., Smith, L. M., Hong, G., Song, W., and Zhang, S. (2021). Polypyrrole-modified bamboo fiber/polylactic acid with enhanced mechanical, the antistatic properties and thermal stability. Ind. Crops Prod. 162, 113227. doi:10.1016/j.indcrop.2020.113227
Keywords: lignin, cellulose nanofibers, 3D printing, tensile strength, biopolymers
Citation: Grade S, Zhang X, Yang C-H, Oduro I and Wang C (2024) Cross-linking lignin and cellulose with polymers using siloxane compounds. Front. Mater. 11:1355976. doi: 10.3389/fmats.2024.1355976
Received: 14 December 2023; Accepted: 25 January 2024;
Published: 08 February 2024.
Edited by:
Ping Wang, Jiangnan University, ChinaReviewed by:
Haibo Deng, Jiangnan University, ChinaCopyright © 2024 Grade, Zhang, Yang, Oduro and Wang. This is an open-access article distributed under the terms of the Creative Commons Attribution License (CC BY). The use, distribution or reproduction in other forums is permitted, provided the original author(s) and the copyright owner(s) are credited and that the original publication in this journal is cited, in accordance with accepted academic practice. No use, distribution or reproduction is permitted which does not comply with these terms.
*Correspondence: Che-Hao Yang, Y2hlLWhhby55YW5nQHdzdS5lZHU=
Disclaimer: All claims expressed in this article are solely those of the authors and do not necessarily represent those of their affiliated organizations, or those of the publisher, the editors and the reviewers. Any product that may be evaluated in this article or claim that may be made by its manufacturer is not guaranteed or endorsed by the publisher.
Research integrity at Frontiers
Learn more about the work of our research integrity team to safeguard the quality of each article we publish.