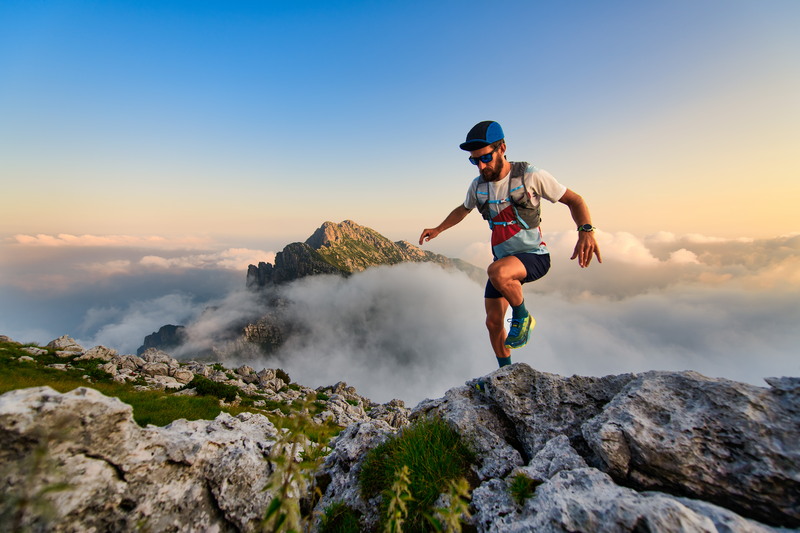
95% of researchers rate our articles as excellent or good
Learn more about the work of our research integrity team to safeguard the quality of each article we publish.
Find out more
ORIGINAL RESEARCH article
Front. Mater. , 18 March 2024
Sec. Polymeric and Composite Materials
Volume 11 - 2024 | https://doi.org/10.3389/fmats.2024.1344351
This article is part of the Research Topic Development of Novel Biodegradable Materials under Cryogenic Environment View all 6 articles
Linum usitatissimum commonly known as flax fibers, emerges as a promising reinforcement phase for artificial polymer resins, boasting ecological benefits, low density, and easy accessibility. However, the mechanical behavior of such composites hinges crucially on factors such as fiber mat thickness, nanoTiO2 filler content, and the application of cryogenic treatment. Addressing this complex interplay, this study employs a hand lay-up technique for composite construction, subjecting nanocomposite plates to the challenging liquid nitrogen conditions at 77 K post-manufacture. Recognizing the need for an optimized approach, Response Surface Methodology (RSM) based on Box-Benhken designs is employed to enhance the mixing features of linum usitatissimum polymer composites. The study calculates anticipated mechanical strength values through rigorous ANOVA inferential analysis, uncovering the pivotal roles played by fiber mat thickness, nanofiller content, and cryogenic treatment in the two feature interactions (2FI) model components. The methodology proves robust with high R2 values (0.9670 for tensile, 0.9845 for flexural, and 0.9670 for interlaminar shear strength) consistently aligning with experimental findings. The study culminates in identifying optimized parameters for maximal mechanical properties—300 gsm flax fiber thickness, 5 wt.% nano TiO2 concentration, and a 15-min cryogenic treatment—a result that advances our understanding of fundamental factors influencing composite performance and provides practical guidelines for applications in fields requiring superior mechanical strength in challenging environments.
Composites are a diverse set of materials with various qualities and uses. The matrices and reinforcements are made of two or more biologically different elements. The reinforcements are typically stiffer and stronger than the matrices. The matrix maintains the reinforcements in place and offers a uniform structure (Lefeuvre et al., 2015). Even though man-made fabrics are the most commonly used reinforcements in polymeric materials, rising ecological issues have freshly prompted the usage of biodegradable alternatives. Owing to their scientific and environmental benefits, disposable reinforcement substances like organic fabrics are the ideal replacement for artificial materials in the composites sector (Kamarudin et al., 2022). Natural fiber-reinforced composites are superior to synthetic fibers in several important ways for the aerospace and automotive sectors. First, their much-reduced density helps with light weighting, essential for improving performance and fuel economy. This weight decrease helps aircraft applications improve the fuel-to-payload ratio and the automobile industry fulfill stricter fuel efficiency criteria. Natural fibers are also renewable, biodegradable, and environmentally benign, which aligns with the increased emphasis on sustainability and lowering carbon emissions (Surakasi et al., 2023). Additionally, these composites have good vibration-dampening properties, which improve passenger comfort in cars and lessen structural fatigue in airplanes. Furthermore, natural fibers are usually less expensive than synthetic ones, making them a sensible option economically. Lastly, natural fibers are a desirable substitute for synthetic materials in various structural applications because of their intrinsic qualities, which include high specific strength and stiffness. These sectors are increasingly concerned with cost-effectiveness, environmental friendliness, and resource efficiency (Velmurugan and Babu, 2020). Mechanical and chemical characteristics of frequently exploited natural fabrics may be discovered in the bibliography. Natural fibres are useful in various industries, such as automotive, architecture, and the aviation sector, because of their relatively low cost, density, reduced carbon emissions, soft microfiber character, absence of skin annoyance, and minimal health hazard. Most organic fibre-based composites are low-cost, more durable, and ecologically benign. Flax (Linum usitatissimum) was among the earliest plants harvested, twisted, and woven into fabrics (Dhakal and Sain, 2020). Flax textiles have been discovered in Egyptian tombs going back to 6000 B.C. (Cerbu, 2015) Up to 32,000 decades previously, twisted natural flax fibres at Dzudzuana Caves suggested the primitive poacher was creating ropes for hafting primitive tools, spinning baskets, or stitching clothes (Ahmad et al., 2021). Longer flax fibres that are fine and uniform are frequently spun into flax threads. Flax fabric holds a strong historical position amongst high-quality domestic fabrics, like bed sheets, decorative textiles, and home décor items. Cooking cloths, sails, awnings, and canvases are made using thicker threads from smaller flax strands (Saidane et al., 2021). Lesser fiber quality could not meet the criteria for automotive applications (Koronis et al., 2013).
Natural fibres have a few drawbacks, such as incompatibility between fibres and matrix and hydrophilic natural fabrics, geometrical instabilities, and a predisposition to congregate throughout the preparation and their considerable positives (Prabhu et al., 2020). The poor interfacial interaction among liquid natural fabrics and water-repellent polymer chains reduces the polymeric composite’s characteristics, which is bad for the commercial and construction industries. Surface modification of reinforced fibre, recombination, and filler additions are just a few of the methods and procedures that may be used to solve such flaws (Coroller et al., 2013). Whenever natural materials are treated with different agents, their chemical properties, surface roughness, and topographical change, some of the available surface therapeutic approaches are Alkaline, siloxane, acetyl, benzoylation, peroxidase, ammonium nitrate, and potassium chlorite. One of the most extensively used and easiest procedures for increasing the adherence qualities of the fibre matrices is alkali treatment, often called mercerization. This approach uses sodium hydroxide (NaOH) to change the cellulose properties of natural fibres, resulting in rapid fibre breakage and dispersion (Fernández et al., 2016). Oils, waxes, lignin, and pectin are removed from the fibres during alkali, leaving a clear, homogeneous texture. Hybridization is another method for improving the mechanical performance of lightweight materials (Baley et al., 2020). Hybrid composites often comprise two or three dissimilar fibre varieties inside the same matrices and a mixture of two or more materials strengthened with similar fabrics (Duc et al., 2014). Hybridization’s main purpose is to circumvent a structure’s limits by supplementing it with another substance with equal or greater qualities (Campana et al., 2018). Mixing different types of nanoparticles or nano powder in the same matrices may create hybrid nanocomposite substances at the nanoscale. Hybrid nanostructure substances were employed in various applications and features at a cheaper cost than standard lightweight materials (Saadati et al., 2020).
Liquid nitrogen capabilities can increase the material characteristics of fiber-reinforced polymers. For instance, polymers used in aircraft construction must be gifted to endure temperatures up to −200°C. Cryogenically treated materials and polymers consume improved strength, resilience, inflexibility, and fatigue strength (Kureemun et al., 2018). Consequently, fluid nitrogen-treated materials could develop a vital fragment of modern investigation and technology to ensure the properties of natural composites (Rajeshkumar et al., 2021). Response Surface Methodology (RSM) is an assemblage of computational and scientific methodologies for emerging, ornamental, and optimizing processing limits (Setswalo et al., 2022). It is a multi-dimensional excitable tool for estimating and visualising the cause-and-effect relationship among replies and the control input elements that influence outcomes (Zeeshan et al., 2021). The Box-Behnken design (BBD) is observed as experimental by RSM. BBD offers the benefit of avoiding tests performed in severe settings and excluding combinations in which all components are simultaneously at their maximum and minimum levels. Moreover, because the BBD is a cost-effective structure that only needs 3 levels for every constituent, it is frequently used in industrial investigation (Vinod et al., 2021).
Some man-made fibres are poisonous, non-disposable, rough, and require a lengthy production process, whereas natural fabrics are durable, inexpensive, and environmentally benign (Daria et al., 2020). As environmental considerations have grown, researchers have shifted their focus from artificial to natural-fiber lightweight materials. Many earlier studies have used natural fibres; nevertheless, their findings show that they have worse characteristics and interoperability when associated with artificial materials, necessitating a change in the manufacturing process. To improve the total concert of natural fibre amalgams, nanoparticle inclusion and fibre surface augmentation might be considered useful strategies. Furthermore, there is a noteworthy dearth of studies on this subject. The combined impact of the cryogenic treatment and the inclusion of nanoparticles on the mechanical features of the hybrid nanocomposite was examined in this work. Utilizing the hand lay-up process, the polymeric composites were created utilizing alkali-treated flax and nano-TiO2 reinforced composites. For tensile, bending, and ILSS characteristics, the influence of cryogenic treatment and nanofiller addition was examined, and an SEM was used to analyze the fractured construction of the composites. The work is innovative since it completely improves hybrid composites’ mechanical behavior in harsh environments. This research introduces an innovative material synergy achieved through the combination of epoxy, natural flax fibers, and Nano TiO2 particles. Notably, the use of Response Surface Methodology (RSM) for systematic optimization sets this work apart, providing an organized and efficient approach to exploring the multidimensional design space. A demanding and unique dimension is added by investigating mechanical characteristics especially in a liquid nitrogen environment, which is essential for cryogenic engineering and aerospace applications. This comprehensive viewpoint advances our knowledge of composite behavior by considering both the environmental influences and the composition of the materials. The wide range of possible uses from cryogenic storage tanks to aircraft components, emphasizes the practical importance of research in creating cutting-edge materials for difficult real-world situations.
Flax fiber is stem fiber indigenous to South Asia and prevalent in countries like India, Malaysia, and Indonesia, undergoes the retting process for fiber extraction from the plant’s stem bark. The initial separation results in slender elements, each measuring up to a meter in length, which are subsequently skillfully woven into mats. The RKG natural sources in Mellor, Tamil Nadu, India, gathered flax fibres and matrices such as epoxy. The Nano TiO2 powders utilized in traditional pallets are sourced from the reputable Naga Chemical Factory in Chennai, Tamil Nadu, India.
The flax fibres has washed individually at 63°C–78°C for 60 min with 1–2 percent bathe resolutions, washed with purified waters, and dried in a microwave heating chamber at 75°C for 60 min, as per the developed process, to avoid any undesirable contaminants (Van de Weyenberg et al., 2003). After cleaning the filaments, they were soaked in a 5% NaOH solution for 4 h at 40°C. Purified water extensively cleansed and dehydrated the fibres in the open air to get alkali-treated fibres.
The matrix and substances were incorporated during the initial stage by mechanically spinning nano-TiO2 and resin for 15 minutes. The additive is subsequently distributed into the substrate by the ultrasonicate using acoustic oscillations. Different weight ratios of nano-silica filler load, including 2.5, 5, and 7.5 wt %, were employed to create a hybrid. After being physically stirred, the nano-sized silicon and resin solution was transferred to an acrylic pipette held in a heated ultrasonic bath and operated on the pulse setting for 45 min.
When the method was finished, the compression molding technique was implemented to create hybrid material made of flax and nano-TiO2. The concentrations and characteristics given were used to build a combined instance. The casting was subsequently filled with the epoxy/nano-TiO2 combination that was earlier created. Once the remaining adhesives were absorbed and the basic surface was attached. Then, additional layers were added until they became showery utilizing a different resin/Nano-TiO2 mixture. The fold was completed by applying the same technique again. The material was then severely crushed with a motorized rolling component to the extent of within 3 mm. The created hybrid polymeric specimens were allowed to dry at atmospheric temperatures for a full day by ASTM protocol before being broken into pieces with an appropriate diameter for mechanical evaluation. Table 1 shows the current study’s fiber, filler, and epoxy resin proportions. Table 2 shows the properties of the blends and their distinct stages.
In the introduction of this research, the selection of a nitrogen environment can be contextualized by addressing a research gap and justifying the choice compared to other conditions. One potential research gap could be the limited exploration of the mechanical behavior of flax/nano TiO2/epoxy hybrid composites under extreme environments. Using a nitrogen environment becomes pivotal as it represents a challenging condition characterized by low temperatures, specifically at 77 K. This condition holds relevance in industries like aerospace and cryogenic engineering, where materials must endure rigorous environmental challenges. Through exposure to a nitrogen environment, the study endeavours to fill a crucial gap in comprehending the performance of these materials under extreme conditions, delving into dimensions beyond the scope of conventional testing environments. This methodology offers valuable insights into the composite’s behaviour, revealing nuances that might escape notice under standard conditions. Such insights contribute to a more thorough understanding of its practical suitability in real-world scenarios, thereby addressing a distinct research gap in the existing body of literature. All freezing procedures were meticulously executed using pre-programmed conditions within an electronically controlled cylinder. By carefully cooling at a 3°C/min rate, the internal temperature was reduced to −196°C. The produced prototypes were subsequently immersed in liquid N2 at −196°C for freezing treatment for 15 min, 30 min, and 45 min by the experimental layout. Following the completion of the procedure, the plastic composites were brought to ambient temperatures at a continuous warmth rate of 45°C/h.
RSM is a technique for analyzing the relationships among several specified circumstances and obtained results. When creating a model for statistics, we need to comprehend what is involved. This strategy was extensively explored (Van de Weyenberg et al., 2003; Gupta et al., 2021). Performing technically prepared trials, forecasting variables using a method of science, foreseeing answers, and verifying that the model is applicable are the three primary phases in this optimization method. Accordingly, the numbers X1, X2, and X3 have been assigned to the key factors of fibre thickness, silicon particle ratios, and freezing processing. Table 3 displays each parameter’s low, moderate, and high criteria as a series of letters -, 0-, and +, correspondingly. Multiple regression examination and the least-squares method were used for the computation.
With the aforementioned formulas from Eq 1, Xi is a self-governing factor’s coding significance, Xi is a self-governing factor’s actual worth, Xo is a self-governing factor’s real value depending on the middle value, and X is a self-governing factor’s modifying level. In each Box-Behnken layout, a cluster of dots is located at the halfway point of each edge along the replicated middle within each volumetric block. The average of the results from a set of processing scenarios was utilized as a final result after the three rounds of each test. The quadratic expression (2) is commonly used to express the theoretical connection between what happens depending on the parameters in a configuration with three significant independent elements: X1, X2, and X3.
Where X is the predictable response, α0 is the prototypical coefficient, Z1, Z2 and Z3 are momentous influences,
The mechanical properties of the composite were assessed using a computerized universal testing machine (Model PNP-01) with a 10 kN load capacity, crafted by BISS Bangalore. The fabricated composites were precision-cut in accordance with the ASTM D 3039 standard for tensile testing, employing a cross-head speed of 0.5 mm/min. The sample has dimensions of 250 × 25 × 3 mm, ASTM D-790 models alongside measurements of 125 × 10 × 3 mm for bending evaluation, and ASTM D-2344 models alongside measurements of 3 mm by 45 mm and 3 mm for interlaminar shear strength (ILSS). The same universal testing machine was used to measure the flexural and ILSS behaviors with a cross-head speed of 1 mm/min.
For mechanical properties such as tension, bending, and ILSS with three-dimensional models (third order polynomial equations) were built utilizing expression (2) from data acquired according to the investigational matrix developed based on L17 orthogonal design as given in Table 3 based on Design expert 13 version. Normal probability plots were used to check for normality in the created model. Such graphs were discovered to follow a normal distribution as seen in Figure 1. The normal plot may also be used to check the correctness of an analysis of variance (ANOVA).
The anticipated vs. real charts for the attributes in Figure 2 show that the variance is homogeneous. The models were then tested for fit quality against real values from Table 4 using the coefficient of determination (R2). The numbers were extremely near to one, indicating that the models are well-fitting. High Adjusted R2 values near 1 indicate that the created models are accurate. All property models have appropriate accuracy values greater than 4, indicating they can be used to explore the strategy. Low coefficients of difference suggest that the experiments were extremely reliable (Kumar et al., 2023a).
The cubic models for tensile strength are significant, as indicated by the F-value (48.84) in Table 5 of ANOVA. There’s only a 0.01 percent chance that this strong F-value is attributable to mistakes. The tensile behavior of the composite is suggestively affected by the thickness of flax fibre, the weight percentages of filler particles, and the length of cryogenic treatment. The interactive RSM graphs in Figure 3 show that tensile behavior is greatest in the zone where the period of cryogenic processing is shortest and fibre thickness is greatest (Seghini, 2020). When the time of cryogenic treatment is maintained at a short time, tensile strength increases with increasing flax fibre thickness. When the cryogenic treatment was long, the composite’s tensile strength degraded due to crack development, as seen in the SEM pictures. The major cause of the fracture growth was the extrinsic damage generated in the fibres during treatment (Hemanth et al., 2017). The matrix’s crack nucleating locations were the exterior damaged spots. The resulting tensile strength mathematical model for coded factors is shown the expression (3). This equation might be used to make tensile strength estimates for the predetermined rates of the components. The nano TiO2 filler concentration raises the hybrid composite’s tensile strength. However, the following conclusions are only valid up to a filler percentage of 5%. The tensile strength of the composites deteriorated as the filler’s concentration was raised beyond these thresholds. As a result of the low adhesion and composite strength properties, aggregation may occur (Rajeshkumar et al., 2021). The coded tensile strength equations are represented by (3). The strong bonding of fibers to the matrix obtained by NaOH treatment greatly improves composite laminates’ overall strength and longevity. By promoting efficient interface connections, this procedure guarantees better load transmission between the matrix’s substance and the reinforcement component. Consequently, laminated materials exhibit improved mechanical qualities, such as tensile and flexural strength, and heightened resistance to fatigue and delamination, making them more durable in various challenging environments. Additionally, treated fibers are less vulnerable to outside elements like water absorption, increasing the blended material’s long-term endurance. Mechanical testing and microscopy methods such as SEM are among the evaluations that confirm the beneficial effects of NaOH treatment on the interface between fibers and matrix and its crucial role in strengthening the foundational strength and endurance of composite laminated materials.
FIGURE 3. Surface conspiracies for Tensile behaviour for collaborative consequence among (A) Cryogenic vs. flax fiber; (B) Cryogenic vs. Nano filler and (C) Nano Filler vs. flax fiber.
The ANOVA included only the components and associated two-way combinations with a considerable influence on mechanical features (p-values 0.05). The F-value (49.45) for flexural strength in Table 6 indicates that the quadratic model is statistically significant. There’s only a 0.01 percent chance that this strong F-value is attributable to mistakes. Some unimportant model variables were not taken into account. The flexural strength of the produced composite material is affected by the flax fibre thickness and the length of cryogenic treatment (p-values 0.05). Because flexural failures are caused by the shattering of cell walls in fibre bundles, the increased thickness of the flax fibre mat has improved the composite’s flexural strength. Because of the formation of fractures in isolated locations, the length of cryogenic treatment substantially impacted flexural strength as demonstrated in the micrograph. The resulting flexural mathematical model for coded components is shown in the expression (4). The formula above may be used to estimate the bending strength provided by the element’s measurements. It is possible to evaluate the elements’ respective influence by analyzing the correlation coefficient of each one (Rajeshkumar et al., 2021; Setswalo et al., 2022). The bending strength is maximum when the cryogenic procedure is lowest and the amount of nano filler concentration is mild, according to the interaction response-surface plots in Figure 4.
FIGURE 4. Surface conspiracies for Bending behaviour for collaborative consequence among (A) Cryogenic vs. flax fiber; (B) Cryogenic vs. Nano filler and (C) Nano filler vs. flax fiber.
In the Table 7, F-value (48.84) indicates that the cubic model for interlaminar shear strength is substantial, with only a 0.01 percent chance that this large F-value is attributable to mistakes. The ILSS of the produced composite is significantly affected by flax fibre thickness and cryogenic treatment (p-values 0.05). The interlaminar shear strength of the composite best when the quality of the woven flax fibre and the cryo processing are balanced, as shown by the response-surface plots in Figure 5. Interlaminar shear strength is stronger in sections with thick flax fibre and less cryo processing or in areas with a reasonable amount of nano filler (5 wt%) and a thicker flax fibre (Belaadi et al., 2020; Vinod et al., 2021). Regarding coded factors, the complete mathematical model for interlaminar shear is shown the Eq 5. This equation might be used to predict the future of ILSS intensity for the given values of the components. The mechanical and physical characteristics of nano composites reinforced with flax fiber undergo a significant transformation when subjected to cryogenic treatment. Extremely low temperatures, usually close to liquid nitrogen, improve mechanical strength overall by encouraging a more even dispersion of reinforcing materials, such as tiny TiO2 particles and flax fibers, throughout the epoxy matrix. Increased load-bearing capacity, tensile strength, and flexural characteristics are also included in this upgrade, which is very important for aerospace applications. Additionally, cryogenic treatment reduces brittleness by improving interfacial bonding and decreasing microcrack development, which leads to increased toughness—a crucial attribute for impact resistance in applications such as automotive components. Additionally, the procedure improves dimensional stability by lowering the possibility of warping or distortion in response to temperature fluctuations. Cryogenic treatment-induced microstructural changes that affect the microscopic arrangement of particles and fibers further enhance these composites’ overall optimization for particular engineering applications.
FIGURE 5. Surface conspiracies for ILSS behaviour for collaborative consequence among (A) Cryogenic vs. flax fiber; (B) Cryogenic vs. Nano filler and (C) Nano Filler vs. flax fiber.
Mechanical qualities were shown to be improved at 15 min of cryogenic treatment. Figure 6A–C show the composites’ shattered surface after cryogenic processing. The cryogenic healing hurt the composites, resulting in a reduction in strength. Figure 6A shows the nano TiO2 filler distribution in the epoxy matrix. During the cryogenic treatment, the composites were subjected to severe internal stresses. The fibre and matrix bonding were impacted by internal stress at the interface zone (Kumar et al., 2023b). Forming a coarse fiber surface can improve mechanical performance in composite materials in several ways. The rough or uneven surface roughness of coarse fibers helps to increase the interfacial adhesion between the fibers and the matrix material. Because of this improved bonding, there is greater load transmission between the reinforcement and the matrix, which increases the composite’s strength and stiffness. In addition to providing mechanical interlocking with the matrix, the rough surface of coarse fibers also lessens the possibility of fiber pullout and facilitates more effective stress transmission.
FIGURE 6. Microstructural analysis of flax fiber/Nano TiO2/Epoxy based hybrid composites under cryogenic treatment. (A) Nano TiO2 filler distribution, (B) Existence of a coarse fiber surface, (C) Longer cryo treatment period.
By looking at the abnormalities, protrusions, or rough textures on the fiber surfaces, one may visually validate the existence of a coarse fiber surface in SEM pictures in Figure 6B. Furthermore, the positioning of the matrix substance within fibers and the degree of bonding between them may be seen in SEM pictures. In SEM pictures, a rough and well-bonded fiber surface often indicates strong interphase among the fibers and matrix and good stress transmission, which indicate superior mechanical characteristics. SEM analysis offers a clear and straightforward way to confirm the beneficial effects of creating a coarse fiber exterior on the mechanical characteristics of composites.
The mechanical characteristics of the material were observed to deteriorate when the treatment period was extended due to the formation of fractures on the material due to high internal forces. Furthermore, when the cryo treatment period was extended, fissures appeared in solitary areas as the fibres, nano filler, and matrix contracted at various speeds (Longana et al., 2018; Natrayan et al., 2023). On the other hand, the composites with the alkaline-treated fibre demonstrated good adhesion in the Figure 6B. The greater stress caused by the longer cryo treatment period caused the fibres to rupture into fibrils shown in Figure 6C, reducing the load transfer under loading and lowering the performance. In contrast, the chemical and physical characteristics of the flax fibre in the composite may have altered following cryogenic healing, thereby affecting the composite’s durability (Sumesh and Kanthavel, 2022). SEM images demonstrated flexural strength increased progressively as filler addition (5 wt%) increased due to improved matrix-fiber bonding.
The present study focuses on improving the mechanical properties of TiO2-filled braided flax/epoxy hybrid materials. This enhancement is achieved by implementing Response Surface Methodology (RSM). By employing the multiple reaction interface technique, specific parameters for the controlled processing of nano TiO2 with flaxseed-based hybrid composites were identified as 5% nano TiO2, 300 gsm flaxseed fiber mats, and a freezing processing time of 15 min. The correlation ratios (R2) for tension, bending, and ILSS are 0.96, 0.98, and 0.95, respectively. According to RSM findings, the width of flax fibers and the freezing processing time are the most influential factors in determining the mechanical properties. The combination of different components results in hybrid materials with superior mechanical features. In particular, the hybrid material with 5-wt% TiO2 exhibits higher mechanical durability than those with 2.5 wt% and 7.5 wt%. This improvement is attributed to the counteraction of hole impacts through the controlled inclusion of filler additives, as supported by SEM images. The outcomes demonstrate enhanced mechanical properties as the flaxseed fiber content increases in grams per square meter. The interaction area between fibers and matrices expands with higher fiber concentration, requiring greater force to maintain cohesion among stressed fiber bundles. Notably, during the initial 15 min of the freezing treatment, stress levels at intersections are reduced. This reduction contributes to improved matrix-fiber adhesion, thereby enhancing the overall performance of the hybrid materials.
The positive results of this work open up new avenues for investigation in future TiO2 filled braided flax/epoxy hybrid materials. Prospective studies might focus on improving mechanical qualities by adjusting processing settings, experimenting with a wider range of TiO2 concentrations, and looking into extra fillers or reinforcements. Promising directions for additional research include long-term durability evaluations, multiscale modeling, sophisticated characterization methods, and applications in certain sectors. Furthermore, a focus on environmental impact assessment and cooperative efforts between industry stakeholders and researchers might hasten the transfer of these materials from laboratory-based research to real-world, sustainable uses. By providing high-performance materials with an emphasis on toughness, adaptability, and environmental sustainability for a range of industrial applications, these future directions hope to progress the area.
The recently created laminates, which include a hybrid composite made of cryogenic-treated TiO2 nanoparticles and flax fibers, show promise for use in the automotive and aerospace sectors. With their increased impact resistance, lightweight design, and possible cost savings over more conventional materials, these laminates might be successfully incorporated into dashboards, door panels, and seat constructions in the car industry. Furthermore, these laminates have potential applications in the aircraft industry for non-structural parts such as interior panels, cabin elements, and ornamental features. By using their improved mechanical qualities and less weight, these laminates can help improve overall fuel economy. The cryogenic treatment improves their suitability for aircraft applications through increased dimensional stability and decreased brittleness. Because flax fibers are environmentally benign, flax/TiO2 hybrid laminates provide a more sustainable choice than current materials like carbon fiber composites or ordinary fiberglass, all while maintaining competitive mechanical performance. Their application potential is in striking a balance in certain components between cost-effectiveness, sustainability, and performance; this makes them a strong option in these sectors’ search of innovative materials.
The raw data supporting the conclusion of this article will be made available by the authors, without undue reservation.
SM: Conceptualization, Data curation, Formal Analysis, Writing–review and editing. LN: Investigation, Software, Supervision, Writing–original draft. JG: Investigation, Methodology, Validation, Visualization, Writing–review and editing. SM: Conceptualization, Data curation, Funding acquisition, Project administration, Resources, Validation, Writing–review and editing.
The author(s) declare that no financial support was received for the research, authorship, and/or publication of this article.
The authors declare that the research was conducted in the absence of any commercial or financial relationships that could be construed as a potential conflict of interest.
The author(s) declared that they were an editorial board member of Frontiers, at the time of submission. This had no impact on the peer review process and the final decision.
All claims expressed in this article are solely those of the authors and do not necessarily represent those of their affiliated organizations, or those of the publisher, the editors and the reviewers. Any product that may be evaluated in this article, or claim that may be made by its manufacturer, is not guaranteed or endorsed by the publisher.
Ahmad, F., Yuvaraj, N., and Bajpai, P. K. (2021). Influence of reinforcement architecture on static and dynamic mechanical properties of flax/epoxy composites for structural applications. Compos. Struct. 255, 112955. doi:10.1016/j.compstruct.2020.112955
Baley, C., Gomina, M., Breard, J., Bourmaud, A., and Davies, P. (2020). Variability of mechanical properties of flax fibres for composite reinforcement. A review. Industrial crops Prod. 145, 111984. doi:10.1016/j.indcrop.2019.111984
Belaadi, A., Amroune, S., and Bourchak, M. (2020). Effect of eco-friendly chemical sodium bicarbonate treatment on the mechanical properties of flax fibres: weibull statistics. Int. J. Adv. Manuf. Technol. 106 (5-6), 1753–1774. doi:10.1007/s00170-019-04628-8
Campana, C., Leger, R., Sonnier, R., Ferry, L., and Ienny, P. (2018). Effect of post curing temperature on mechanical properties of a flax fiber reinforced epoxy composite. Compos. Part A Appl. Sci. Manuf. 107, 171–179. doi:10.1016/j.compositesa.2017.12.029
Cerbu, C. (2015). Practical solution for improving the mechanical behaviour of the composite materials reinforced with flax woven fabric. Adv. Mech. Eng. 7 (4), 168781401558208. doi:10.1177/1687814015582084
Coroller, G., Lefeuvre, A., Le Duigou, A., Bourmaud, A., Ausias, G., Gaudry, T., et al. (2013). Effect of flax fibres individualisation on tensile failure of flax/epoxy unidirectional composite. Compos. Part A Appl. Sci. Manuf. 51, 62–70. doi:10.1016/j.compositesa.2013.03.018
Daria, M., Krzysztof, L., and Jakub, M. (2020). Characteristics of biodegradable textiles used in environmental engineering: a comprehensive review. J. Clean. Prod. 268, 122129. doi:10.1016/j.jclepro.2020.122129
Dhakal, H. N., and Sain, M. (2020). Enhancement of mechanical properties of flax-epoxy composite with carbon fibre hybridisation for lightweight applications. Materials 13 (1), 109. doi:10.3390/ma13010109
Duc, F., Bourban, P. E., and Månson, J. A. E. (2014). Dynamic mechanical properties of epoxy/flax fibre composites. J. Reinf. plastics Compos. 33 (17), 1625–1633. doi:10.1177/0731684414539779
Fernández, J. A., Le Moigne, N., Caro-Bretelle, A. S., El Hage, R., Le Duc, A., Lozachmeur, M., et al. (2016). Role of flax cell wall components on the microstructure and transverse mechanical behaviour of flax fabrics reinforced epoxy biocomposites. Industrial Crops Prod. 85, 93–108. doi:10.1016/j.indcrop.2016.02.047
Gupta, U. S., Dharkar, A., Dhamarikar, M., Choudhary, A., Wasnik, D., Chouhan, P., et al. (2021). Study on the effects of fiber orientation on the mechanical properties of natural fiber reinforced epoxy composite by finite element method. Mater. Today Proc. 45, 7885–7893. doi:10.1016/j.matpr.2020.12.614
Hemanth, H., et al. (2017). Evaluation of mechanical properties of E-Glass and coconut fiber reinforced with polyester and epoxy resin matrices. Int. J. Mech. Prod. Eng. Res. Dev. 7 (5), 13–20. doi:10.24247/ijmperdoct20172
Kamarudin, S. H., Mohd Basri, M. S., Rayung, M., Abu, F., Ahmad, S. B., Norizan, M. N., et al. (2022). A review on natural fiber reinforced polymer composites (NFRPC) for sustainable industrial applications. Polymers 14 (17), 3698. doi:10.3390/polym14173698
Koronis, G., Silva, A., and Fontul, M. (2013). Green composites: a review of adequate materials for automotive applications. Compos. Part B Eng. 44 (1), 120–127. doi:10.1016/j.compositesb.2012.07.004
Kumar, S., Dang, R., Manna, A., Dhiman, N. K., Sharma, S., Dwivedi, S. P., et al. (2023b). Optimization of chemical treatment process parameters for enhancement of mechanical properties of Kenaf fiber-reinforced polylactic acid composites: a comparative study of mechanical, morphological and microstructural analysis. J. Mater. Res. Technol. 26, 8366–8387. doi:10.1016/j.jmrt.2023.09.157
Kumar, S. S., Vignesh, V., Prasad, V. V. S. H., Sunil, B. D. Y., Srinivas, R., Sanjay, M. R., et al. (2023a). Static and dynamic mechanical analysis of hybrid natural fibre composites for engineering applications. Biomass Convers. Biorefinery, 1–13. doi:10.1007/s13399-022-03689-2
Kureemun, U., Ravandi, M., Tran, L. Q. N., Teo, W. S., Tay, T. E., and Lee, H. P. (2018). Effects of hybridization and hybrid fibre dispersion on the mechanical properties of woven flax-carbon epoxy at low carbon fibre volume fractions. Compos. Part B Eng. 134, 28–38. doi:10.1016/j.compositesb.2017.09.035
Lefeuvre, A., Bourmaud, A., and Baley, C. (2015). Optimization of the mechanical performance of UD flax/epoxy composites by selection of fibres along the stem. Compos. Part A Appl. Sci. Manuf. 77, 204–208. doi:10.1016/j.compositesa.2015.07.009
Longana, M. L., Ondra, V., Yu, H., Potter, K. D., and Hamerton, I. (2018). Reclaimed carbon and flax fibre composites: manufacturing and mechanical properties. Recycling 3 (4), 52. doi:10.3390/recycling3040052
Makhlouf, A., Belaadi, A., Amroune, S., Bourchak, M., and Satha, H. (2022). Elaboration and characterization of flax fiber reinforced high density polyethylene biocomposite: effect of the heating rate on thermo-mechanical properties. J. Nat. Fibers 19 (10), 3928–3941. doi:10.1080/15440478.2020.1848737
Natrayan, L., Kaliappan, S., Saravanan, A., Vickram, A. S., Pravin, P., Abbas, M., et al. (2023). Recyclability and catalytic characteristics of copper oxide nanoparticles derived from bougainvillea plant flower extract for biomedical application. Green Process. Synthesis 12 (1), 20230030. doi:10.1515/gps-2023-0030
Prabhu, L., Krishnaraj, V., Sathish, S., Gokulkumar, S., Sanjay, M. R., and Siengchin, S. (2020). Mechanical and acoustic properties of alkali-treated sansevieria ehrenbergii/camellia sinensis fiber–reinforced hybrid epoxy composites: incorporation of glass fiber hybridization. Appl. Compos. Mater. 27, 915–933. doi:10.1007/s10443-020-09840-4
Rajeshkumar, G., Hariharan, V., Indran, S., Sanjay, M. R., Siengchin, S., Maran, J. P., et al. (2021). Influence of sodium hydroxide (NaOH) treatment on mechanical properties and morphological behaviour of Phoenix sp. fiber/epoxy composites. J. Polym. Environ. 29, 765–774. doi:10.1007/s10924-020-01921-6
Saadati, Y., Lebrun, G., Chatelain, J. F., and Beauchamp, Y. (2020). Experimental investigation of failure mechanisms and evaluation of physical/mechanical properties of unidirectional flax–epoxy composites. J. Compos. Mater. 54 (20), 2781–2801. doi:10.1177/0021998320902243
Saidane, E. H., Scida, D., and Ayad, R. (2021). Thermo-mechanical behaviour of flax/green epoxy composites: evaluation of thermal expansion coefficients and application to internal stress calculation. Industrial Crops Prod. 170, 113786. doi:10.1016/j.indcrop.2021.113786
Seghini, M. C. (2020). Investigation into the mechanical properties and fibre/matrix interface optimization for next generation of basalt-plant fibre hybrid composites.
Setswalo, K., Oladijo, O. P., Namoshe, M., Akinlabi, E. T., and Sanjay, M. R. (2022). The mechanical properties of alkali and laccase treated pterocarpus angolensis (mukwa)-polylactic acid (PLA) composites. Int. J. Biol. Macromol. 217, 398–406. doi:10.1016/j.ijbiomac.2022.07.075
Sumesh, K. R., and Kanthavel, K. (2022). Grey relational optimization for factors influencing tensile, flexural, and impact properties of hybrid sisal banana fiber epoxy composites. J. Industrial Text. 51 (3_Suppl. l), 4441S–4459S. doi:10.1177/1528083720928501
Surakasi, R., Paramasivam, P., Dhanasekaran, S., and Patil, P. P. (2023). Statistical experiment analysis of wear and mechanical behaviour of abaca/sisal fiber-based hybrid composites under liquid nitrogen environment. Front. Mater. 10, 1218047. doi:10.3389/fmats.2023.1218047
Van de Weyenberg, I., Ivens, J., De Coster, A., Kino, B., Baetens, E., and Verpoest, I. (2003). Influence of processing and chemical treatment of flax fibres on their composites. Compos. Sci. Technol. 63 (9), 1241–1246. doi:10.1016/s0266-3538(03)00093-9
Velmurugan, G., and Babu, K. (2020). Statistical analysis of mechanical properties of wood dust filled Jute fiber-based hybrid composites under cryogenic atmosphere using Grey-Taguchi method. Mater. Res. Express 7 (6), 065310. doi:10.1088/2053-1591/ab9ce9
Vinod, A., Sanjay, M. R., and Siengchin, S. (2021). Fatigue and thermo-mechanical properties of chemically treated Morinda citrifolia fiber-reinforced bio-epoxy composite: a sustainable green material for cleaner production. J. Clean. Prod. 326, 129411. doi:10.1016/j.jclepro.2021.129411
Keywords: flax fiber, nanocomposites, cryogenic treatment, tensile strength, optimization, TiO2 nano filler
Citation: Mohammed Ajmal SF, Natrayan L, Giri J, Makki E, Shah MA and Mallik S (2024) Utilization of response surface methodology to optimize the mechanical behaviour of flax/nano TiO2/Epoxy based hybrid composites under liquid nitrogen environment. Front. Mater. 11:1344351. doi: 10.3389/fmats.2024.1344351
Received: 25 November 2023; Accepted: 08 January 2024;
Published: 18 March 2024.
Edited by:
Vinod Ayyappan, King Mongkut’s University of Technology North Bangkok, ThailandReviewed by:
Yashas Gowda T. G., Malnad College of Engineering, IndiaCopyright © 2024 Mohammed Ajmal, Natrayan, Giri, Makki, Shah and Mallik. This is an open-access article distributed under the terms of the Creative Commons Attribution License (CC BY). The use, distribution or reproduction in other forums is permitted, provided the original author(s) and the copyright owner(s) are credited and that the original publication in this journal is cited, in accordance with accepted academic practice. No use, distribution or reproduction is permitted which does not comply with these terms.
*Correspondence: L. Natrayan, bmF0cmF5YW5waGRAZ21haWwuY29t; Mohd Asif Shah, ZHJtb2hkYXNpZnNoYWhAa2R1LmVkdS5ldA==; Saurav Mallik, c2F1cmF2bXRlY2gyQGdtYWlsLmNvbQ==
Disclaimer: All claims expressed in this article are solely those of the authors and do not necessarily represent those of their affiliated organizations, or those of the publisher, the editors and the reviewers. Any product that may be evaluated in this article or claim that may be made by its manufacturer is not guaranteed or endorsed by the publisher.
Research integrity at Frontiers
Learn more about the work of our research integrity team to safeguard the quality of each article we publish.