- 1School of Engineering and Architecture, Chengdu Vocational and Technical College of Industry, Chengdu, Sichuan, China
- 2Department of Civil and Construction Engineering, National Taiwan University of Science and Technology, Taipei, Taiwan
- 3The Third Engineering Co., Ltd., China Railway 19th Bureau Group, Shenyang, Liaoning, China
- 4Department of Mechanical Engineering, Islamic Azad University, North Tehran Branch, Tehran, Iran
In this research, free vibration characteristics of functionally graded metal foam doubly curved panels reinforced with graphene platelets and with porosities have been surveyed. Halpin Tsai's approach is utilized for extracting the effective Young modulus of porous metal foam nanocomposite and also the effective density of nanocomposite porous doubly curved shell panel is estimated by using an extended rule of mixture. The FSDT hypothesis is utilized for determining the displacement field and the Finite element and Hamilton principle are utilized for deriving the mass and stiffness matrices of the structure. Finally, the influences of several variables such as porosity distribution, porosity coefficient, GPL dispersion pattern, the weight fraction of Nanofillers, and span angles on the free vibrations characteristics of doubly curved shell panels with FG porosities and reinforced by graphene platelet have been reported in detail.
1 Introduction
Composite materials, including functionally graded materials (FGMs), play a pivotal role in various industries due to their unique combination of properties, such as high strength-to-weight ratio and corrosion resistance (Hucke, 1971; Shen and Bever, 1972; Mahamood et al., 2017). The importance of composites lies in their ability to provide enhanced performance compared to traditional materials. To ensure their effectiveness, researchers employ rigorous evaluation methods to assess material properties. These methods include mechanical testing, non-destructive testing, and advanced analytical techniques (Voigt, 1889; Hill, 1965; Halpin and Tsai, 1969; Mori and Tanaka, 1973; Wakashima and Tsukamoto, 1991). Understanding and optimizing these properties are crucial for developing lightweight and durable structures in the aerospace, automotive, and construction industries. Researchers study composite structures (Wattanasakulpong and Chaikittiratana, 2015; Sobhani et al., 2021; Civalek et al., 2022) even in nanoscience (Saffari et al., 2017; Penna et al., 2021; Penna et al., 2022; Lovisi, 2023; Penna, 2023) to push the boundaries of material science, aiming for innovations that improve efficiency, sustainability, and overall performance in diverse applications (Dastjerdi et al., 2020a; Dastjerdi et al., 2020b).
Nowadays, scholars are evaluating the performance of structures that are made of polymeric and metallic nanocomposite in practical applications subjected to various loadings. Also, some of these structures have been employed in various industries like aerospace, marine, automobile, etc. One of the most important characteristics of these structures is their low weight in connection with high stiffness. On the other hand, adding the nanoparticles to the matrix (polymer or metal) does not change the weight of the structure considerably but it can more significantly increase its stiffness. It is mentioned that these nanoparticles may decrease the stiffness of structures. Since, the nanoparticles have a high level of energy and if their weight fraction is more than a certain amount in the matrix, the nanoparticles stick together and agglomeration will occur. There are many investigations about determining the maximum weight fraction of various nanofillers. Two famous examples of nanoparticle reinforcement which recently attracted the attention of researchers are carbon nanotubes (CNTs) and graphene platelets (GPLs). Since many studies have been conducted into structures that are reinforced with these nanoparticles, studies are considered which are related to the free vibration characteristics of shell-type structures reinforced by GPLs. Babaei et al. (Mollaei et al., 2023) presented free vibrations of functionally graded graphene reinforced composite (FG-GPL RC) cylindrical shell panels employing three-dimensional FEM. Hamilton principle was applied to obtain the governing equations. Amirabadi et al. (Amirabadi et al., 2022) employed third-order shear deformation theory (TSDT) combined with generalized differential quadrature (GDQ) procedure to predict the free vibration behavior of rotating FG- GPL conical shells for various boundary conditions. Dynamic characteristics of FG-GPL shells with piezoelectric patches assuming nonlinear behavior for electro-elastic coupling were presented by Rao et al. (Rao et al., 2018). Nguyen Van Do and Hyung Lee (Van Do and Lee, 2020a) evaluated static bending and natural frequencies of FG-GPL RC cylindrical shell panels employing FSDT and utilizing the isogeometric method. Applying classical shell theory and the Rayleigh-Ritz technique, the free vibration response of sandwich FG-GPL cylindrical shells was studied by Permoon, Farsadi, and Askarian (Permoon et al., 2023). Dynamic characteristics of an FG-GPL conical structure applying Jacobi-Ritz solution were presented by Zhao et al. (Zhao et al., 2023). Free vibration characteristics of rotating 2D FG-GPL conical shells supporting an elastic medium employing FSDT were presented by Amirabadi et al. (Amirabadi et al., 2021). Mohammadi et al. (Mohammadi, 2023) applied isogeometric procedure and higher order shear deformation theory (HSDT) to evaluate free vibrations of trapezoidally corrugated FG-GPL RC laminated cylindrical panels. Mohammadi, Shojaei, and Kiani (Mohammadi et al., 2023) presented an isogeometric method for free vibrations of FG-GPL panel-type structures based on the Kirchhoff–Love shell hypothesis. Liu et al. employing an analytical model (Amirabadi et al., 2023) presented 3D buckling and free vibration behavior of pre-stressed FG-GPL RC cylinders. Dong et al. (Dong et al., 2022) combined GDQM and trigonometric expansion analysis to evaluate the vibration behavior of FG-GPL RC conical shells assuming the ring as a frequency controller based on FSDT. Dong et al. (Dong et al., 2018a) performed an investigation about the influences of rotation and axial force simultaneously on the geometrically nonlinear free vibrations of FG-GPL RC cylinders applying Donnell's theory and an analytical solution. Based on HSDT, the natural frequency characteristics of FG-GPL cylindrical and spherical shell-type panels by employing isogeometric solution were presented by Nguyen Van Do and Hyung Lee (Van Do and Lee, 2020b). Liu et al. (Liu et al., 2021) used three-dimensional elasticity assumptions and an analytical layer-wise solution for the investigation of free vibration characteristics of FG GPL spherical shells. Traveling wave evaluation of a rotating FG-GPL RC cylinder for several boundary conditions according to Donnell shell theory was conducted by Qin et al. (Qin et al., 2019). Utilizing FSDT as a theory and using GDQM as a solution, natural frequencies of FG-GPL cylinders resting on various types of elastic foundations for different BCs were presented by Sobhani et al. (Sobhani et al., 2023a). Sobhani and Avcar (Sobhani and Avcar, 2022) examined various nanofiller materials' effects on the free vibration of cylindrical shells employing FSDT and using GDQM as a numerical solution.
Free vibrations characteristic of FG-GPL doubly curved shell structures have been studied in few articles. The differences between these works are usually in methodology. In detail, Wang et al. (Wang et al., 2018) introduced an analytical model for obtaining natural frequencies of FG doubly curved panels reinforced by GPLs based on HSDT. Free vibration responses of FG GPLs doubly curved shells based on HSDT were presented by Adamian (Adamian et al., 2020). Employing FSDT and Ritz solution, free vibrations of FG-GPL doubly curved panels were presented by Esmaili et al. (Esmaeili et al., 2022). In another investigation by considering the same hypothesis and solution, they (Esmaeili and Kiani, 2022) studied thermal induced vibration responses of GPL RC doubly curved panels. Free vibrations of FG-GPL RC doubly curved shell-type structures in thermal conditions employing Reddy’s HSDT and using an analytical model were developed by Shen et al. (Shen et al., 2019). Sobhi, Ashraf, and Zenkour (Sobhy and Zenkour, 2019) proposed an analytical model for free vibration analysis of FG-GPL RC doubly-curved panels supported on elastic foundations based on an HSDT.
The weight of the structure is too prominent in the aerospace industry and the low weight of the structure can be useful for other applications where saving energy is important. One of the ways to decrease the weight of a structure is BY creating pores in it; the stiffness of the structure also will decrease. To compensate for the decrease in stiffness of the structures, these structures can be reinforced with nanoparticles. Hence, scholars have examined the various types of structures which were fabricated by FG porous material reinforced by nanoparticles. Due to there being many investigations in this field, we review the articles which are related to the vibration behavior of shell structures made of FG porous material reinforced by GPLs. In detail, Bahaadini et al. (Bahaadini et al., 2019) proposed an analytical model for obtaining natural frequencies of FG-GPL RC conical shells with FG porosities employing Love’s first approximation assumptions. Ye and Wang (Ye and Wang, 2021) employed the Galerkin method to study the resonance phenomenon in an FG- GPL cylinder with FG porosities based on Donnell’s nonlinear assumptions. Wang et al. (Wang et al., 2019) conducted an investigation into the nonlinear vibrations of a porous cylinder reinforced with GPLs nanofillers by employing the Galerkin approach and Donnell nonlinear hypothesis. Moradi Dastjerdi and Behdinan (Moradi-Dastjerdi and Behdinan, 2021) presented an axisymmetric meshless model according to moving least squares approximations for obtaining the stress waves in porous cylindrical shells reinforced by GPL nanofillers exposed to thermal conditions. Nonlinear free vibrations of FG-GPL imperfect cylinders with FG porosities employing FSDT were performed by means of an analytical model by Salehi et al. (Salehi et al., 2023). Nejadi et al. (Nejadi et al., 2021) presented a GDQM numerical model as a semi-analytical formulation for free vibrations of sandwich cylinders based on FSDT and by assuming porosity and GPL sense on transfering fluid flow. Zhou et al. (Zhou et al., 2021) employ Reddy theory and the standard Lagrange model to illustrate free vibrations of FG GPL cylinders with FG porosities under supersonic load. Ton-That et al. (Ton-That et al., 2021) reported the nonlinear forced vibrations of FG-GPL cylinders with FG porosity effects by applying nonlinear Donnell assumptions and the Galerkin solution. Ebrahimi et al. (Ebrahimi et al., 2019) presented an analytical model for free vibration analysis of FG –GPL cylinders with FG porosities employing the FSDT as a theory. Pourjabari et al. (Pourjabari et al., 2019) analytically reported the free and forced vibrations characteristic of the FG-GPL cylinders in a micro sense employing modified strain gradient theory. Free vibrations of FG-GPL cylinders considering various FG porosity patterns were presented by Barati and Zenkour (Barati and Zenkour, 2019). Kiarasi et al. (Kiarasi et al., 2021) utilized FEM as a numerical solution and two-dimensional axisymmetric elasticity as an accurate theory to study the free vibrations of FG-GPL RC joined conical–cylindrical structure considering FG porosities. Zhang et al. (Zhang et al., 2023) examined free vibrations characteristic of FG-GPL joined hemispherical–cylindrical–hemispherical structure with FG porosities by using 3D elasticity based on FEM. Cho (Cho, 2023) applied FSDT and two-dimensional FE solution to present free vibration characteristics of FG –GPL cylindrical panels with FG porosities. Twinkle and Pitchaimani (Twinkle and Pitchaimani, 2021) examined the influence of FG-GPL reinforcement and FG porosities on the free vibrations and stability of porous GPL-reinforced cylindrical shell panels according to HSDT and utilizing Galerkin solution. Salehi et al. (Salehi et al., 2023) proposed a novel analytical model for geometrically nonlinear vibrations of FG-GPL RC imperfect cylinders with FG porosities employing FSDT. A novel analytical model for investigating the traveling wave vibrations of rotating FG GPL joined conical-cylindrical structures considering FG porosities applying Donnell’s assumptions was reported by Chai and Wang (Chai and Wang, 2022).
The above literature review shows that in the most of investigations, structures with simple shapes and governing equations like cylindrical and conical shells have been considered, and free vibrations of porous metal foam FG-GPL doubly curved panels have not been investigated so far. In this investigation, FSDT as a theory and FEM as a numerical solution are applied to investigate the natural frequency characteristics of porous FG-GPL metal foam doubly curved panels. Four distinct porosity distributions combined with five different GPL dispersion functions are assumed through the thickness of the structures. The porosity distributions are assumed with symmetric, asymmetric, and uniform patterns through the thickness of the structure. Two distributions of porosity are employed for a symmetric pattern. In one of them, the pores are mainly concentrated at the upper and lower surfaces of the doubly curved shell panel and in the other, the concentration of pores at the upper and lower surfaces of the structure is too low. In asymmetric porosity distribution, the number of pores at the structure’s thickest point is low and the number of pores gradually increases from the structure’s least to most thick points. Five distinct GPL dispersion functions are supposed via the thickness of the shell panel: GPLX, GPLO, GPLA, GPLV, and GPLUD. The effect of various variables including porosity distribution, porosity coefficient, GPL dispersion pattern, weight fraction of GPLs, and span angles on the free vibration characteristics of FG porous nanocomposite structure have been studied. In Section 2, the effective mechanical properties of the structure are presented by proposing the Halpin-Tsai model and extension rule of mixture. Then, in Section 3, the finite element procedure and Rayleigh-Ritz method are utilized for extracting the stiffness and mass matrix of FG porous doubly curved panel reinforced with GPLs.Finally, in Section 4 the numerical results of the natural frequencies of the structures are presented and discussed in detail. The most prominent finding results are presented in the conclusion section.
2 Governing equations of porous FG-GPL RC doubly curved shell panel
2.1 Description of the Geometry
Figure 1 denotes the geometrical parameters of the FG porous metal foam doubly-curved panel reinforced by GPLs, where h is the thickness of the shell structure, R1 and R2 are the radiuses of curvature,
2.2 Obtaining the equal mechanical properties of FG porous doubly curved panel reinforced with graphene platelet:
Four different porosity functions are supposed via the thickness of the doubly curved panel. (See Figure 1) and their relation to changing mechanical properties including Young modulus and density along the structure thickness is shown in Eqs 1–4. Besides, five GPL dispersion functions through the thickness of a doubly curved panel are shown in Figure 1; Eq. 16 (Anirudh et al., 2019; Li and Zheng, 2020; Moradi-Dastjerdi and Behdinan, 2020; Zhao et al., 2020).
Nonlinear symmetric porosity function 1:
where
Nonlinear symmetric porosity function 2:
Nonlinear asymmetric porosity function 3:
Uniform porosity pattern 4:
΄Where
Mass density and modules of elasticity for open-cell metal foam such as used in this research are dependent as presented in the below Eq. (Gibson and Ashby, 1982; Ashby et al., 2000; Asgari et al., 2022).
Eq. 4 is utilized to denote the dependency between the mass density and porosity coefficients for each porosity function as following relations:
For comparing the stiffness of different distributions, the analyses should be implemented for the shells with identical masses. Hence, it is supposed that the mass of doubly curved shell panels with different porosity functions and nanofiller dispersion functions are similar:
Based on Eq. 7, the amounts of
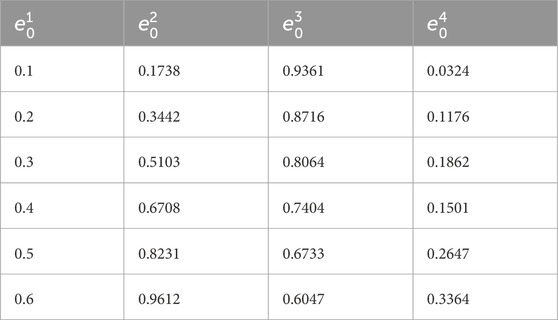
TABLE 1. Porosity coefficients for various patterns (Dong et al., 2018b; Yang et al., 2018).
The Young’s modulus of the doubly curved panel fabricated by metallic nanocomposite without porosity based on the Halpin-Tsai micromechanics model (Choi and Lakes, 1995; Liu, 1997; Arshid et al., 2020; Arshid et al., 2021; Ebrahimi et al., 2021) is calculated as the following:
in which
The mechanical properties of GPLs are shown with subscripts of GPL. Additionally, the subscripts of m are utilized for showing the corresponding mechanical properties of matrix material. The volume amount of nanofillers is indicated with
According to the rule of mixture, mass density and Poisson's ratio of the shell are obtained as below Eqs (Guo et al., 2021; Babaei, 2022):
Accordingly, the shear modulus of the shell is expressed below:
Also, the
Where
2.3 FSDT shell theory equations
FSDT shell theory is hired to present the displacements of doubly curved shell panels as follows:
In Eq. 2, u, v, and w, are displacements along the x, y, and z axes, respectively, while
where
Therefore, the matrix form of Eq. 21 will be as:
where
where
The constitutive relations of a porous FG-GPL doubly curved shell panel are:
By integrating the stress field along the thickness direction, resultant moment and force will be:
In Eq. 24, K is the shear correction factor and equals 5/6.
Simplified form of Eq. 24 is as follows:
where:
The strain and kinetic energies of the doubly curved panel may be presented as the below Eqs.
where:
Replacing Eqs 27, 28 Hamilton’s principle, we have:
2.4 FEM solution of governing equations:
In this section, for solving the governing motion equations of the shell, the graded FE method is used. In conventional FEM, the material property is constant through the element. In GFEM, to treat the material heterogeneity, in addition to the displacement field, the material properties of the FG-GPL porous doubly curved structure could also be determined from their nodal values. This approach leads to a smooth change of the properties along the structure and also obtains more precise results than discretizing the structure into elements with constant properties. By using the interpolation functions of cubic ten nodded triangular element, the displacement field, and material properties of individual element
where
Substituting Eqs 30, 31 in Eq. 29 can be rewritten as
where
Rearranging Eq. 33, the FE model of porous FG-GPL RC doubly curved panel element will be as follows:
Where in Eq. 34 and mass matrix of element, [I] may be evaluated as:
where
By assembly of mass, stiffness, and force matrices of each element, the FE motion equations of the FG-GPL RC doubly curved panel are as
The natural frequency problem of the structure may be derived by the solution of the eigenvalue model as follows:
where
The shell is fully clamped at its all edges as:
3 Numerical results and discussion
In this part, natural frequencies of FG-GPL porous doubly curved shell panels examined by changing the volume weight fraction of nanofillers, nanofiller dispersion pattern, porosity distribution, and porosity coefficient are investigated in detail. The shell is fully clamped on its four edges.
3.1 Validation
To validate the obtained results of the present research, the first six natural frequencies of isotropic homogenous doubly curved shell panels with clamped edges are extracted employing commercial FEM software ANSYS-WORKBENCH, and the results are compared with the results of the present research. Therefore, one may consider e0=0 and
A comparison of the results of the present research with natural frequencies of ANSYS WORKBENCH is presented in Table 2, and it indicates excellent concordance between the results.
3.2 Natural frequencies of FG porous doubly curved shell panel reinforced by GPLs
The influence of coefficients of porosity and distributions of porosity, GPL pattern, and weight fraction of nanofillers and span angles on the natural frequency characteristics of an FG-GPL porous doubly curved shell panel is investigated in this section. Therefore, the below material properties and dimensions are employed:
Geometry: R1=0.225 m, R2=0.4 m, h=0.025m,
Material property:
Table 3 describes the influences of nanofiller patterns on the free vibrations of the porous FG-GPL doubly curved shell panel (
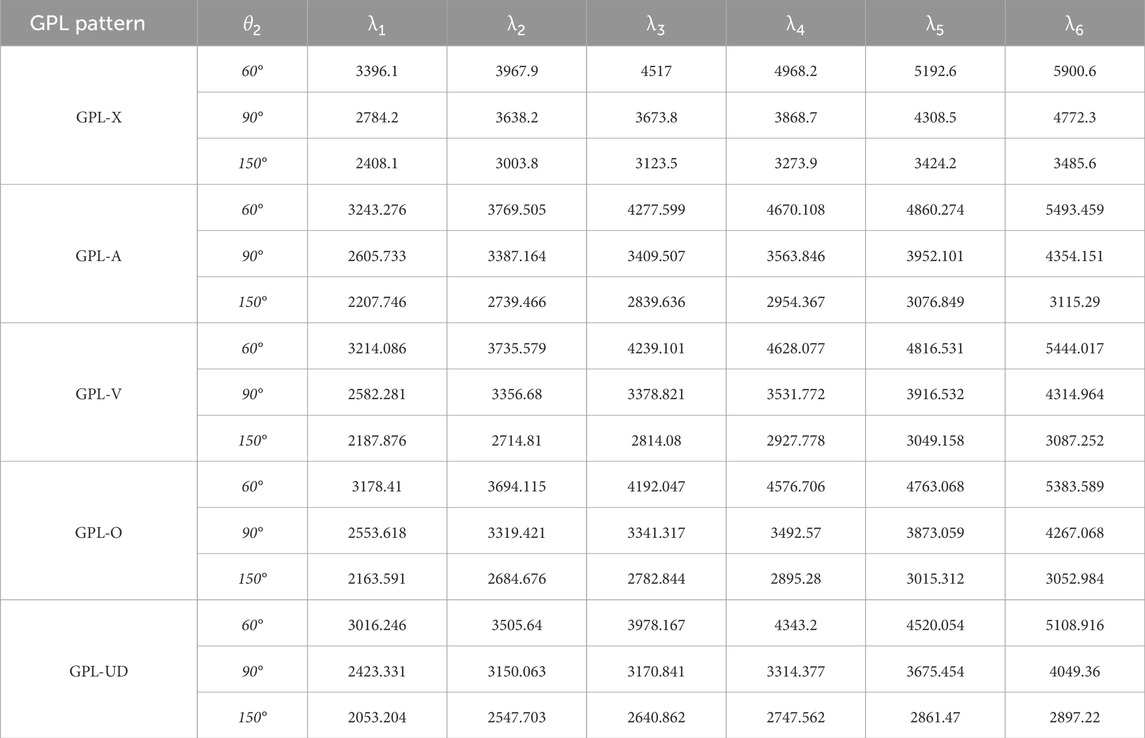
TABLE 3. Natural frequencies of FG- porous doubly curved panel reinforced by graphene nanoparticles for various span angles and GPL pattern (
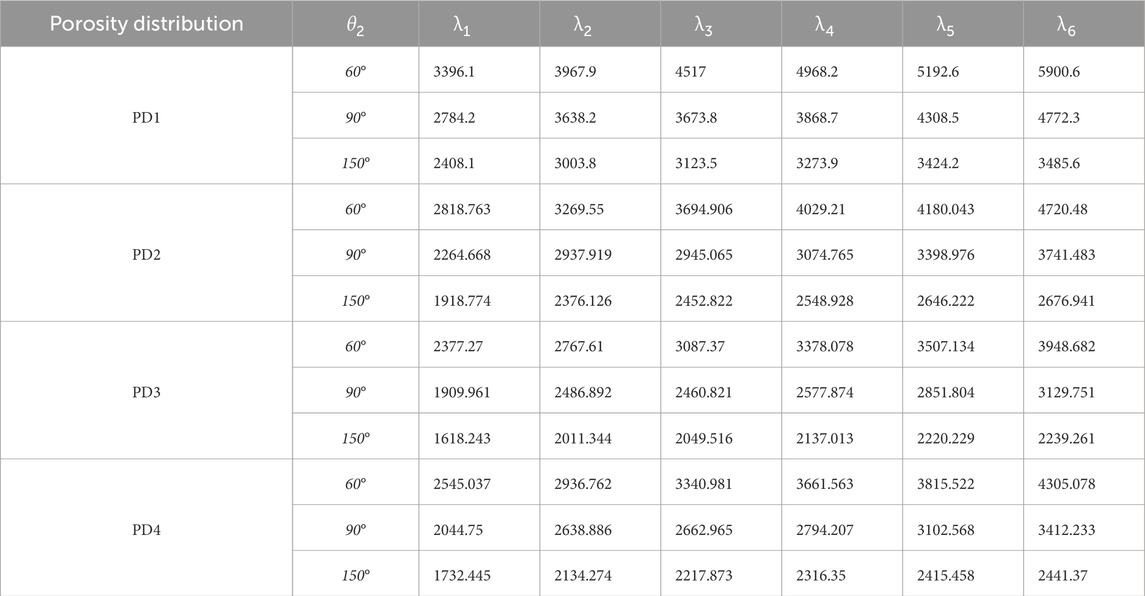
TABLE 4. Natural frequencies of FG- porous doubly curved panel reinforced by graphene nanoparticles for various span angles and porosity distribution (
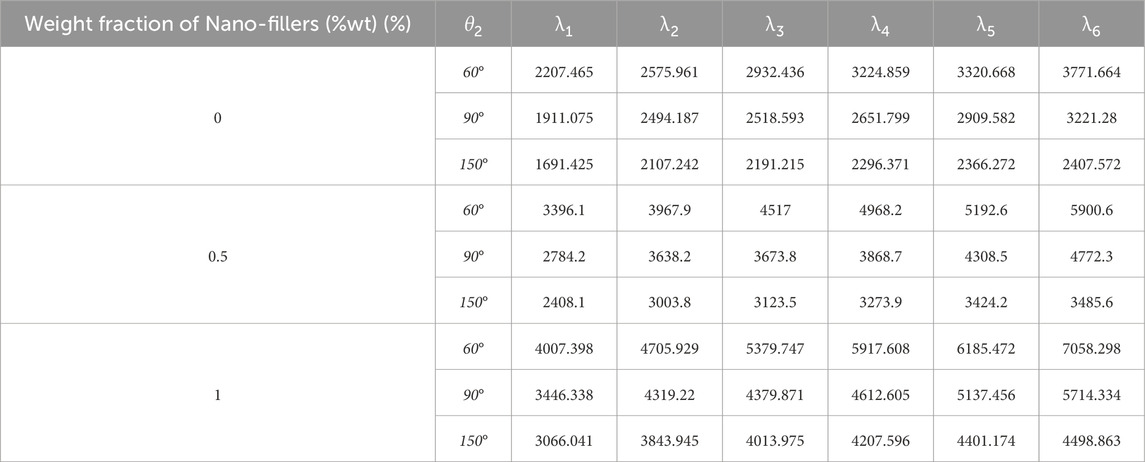
TABLE 5. Natural frequencies of FG- porous doubly curved panel reinforced by graphene nanoparticles for various span angles and weight fraction of nanofiller (
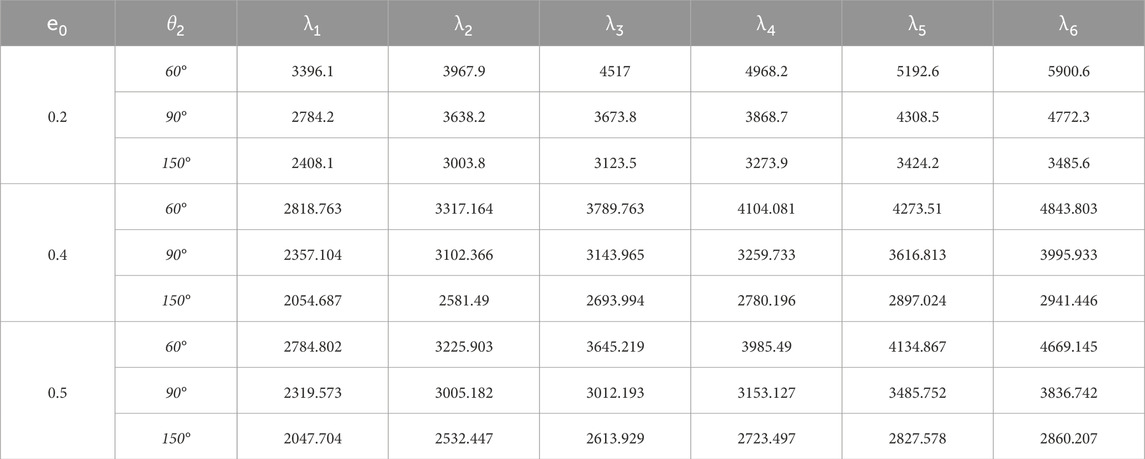
TABLE 6. Natural frequencies of FG- porous doubly curved panel reinforced by graphene nanoparticles for various span angles and porosity coefficients (
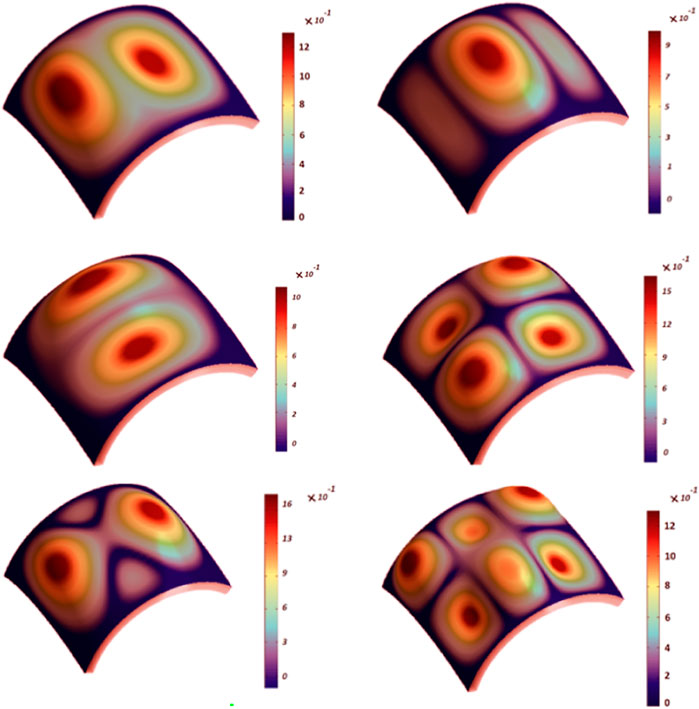
FIGURE 2. The first six mode shapes of FG-GPL porous doubly curved panel (GPLX,
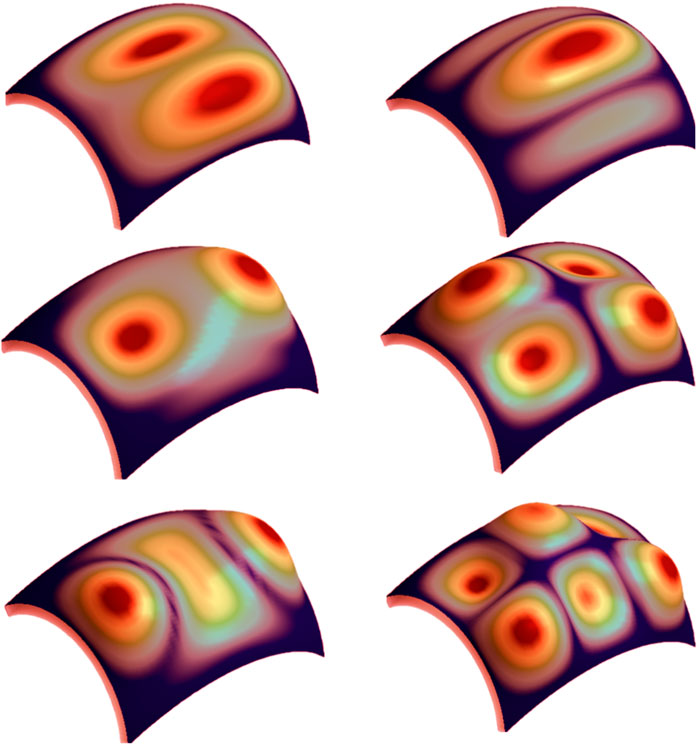
FIGURE 3. The first six mode shapes of FG-GPL porous doubly curved panel (GPLX,
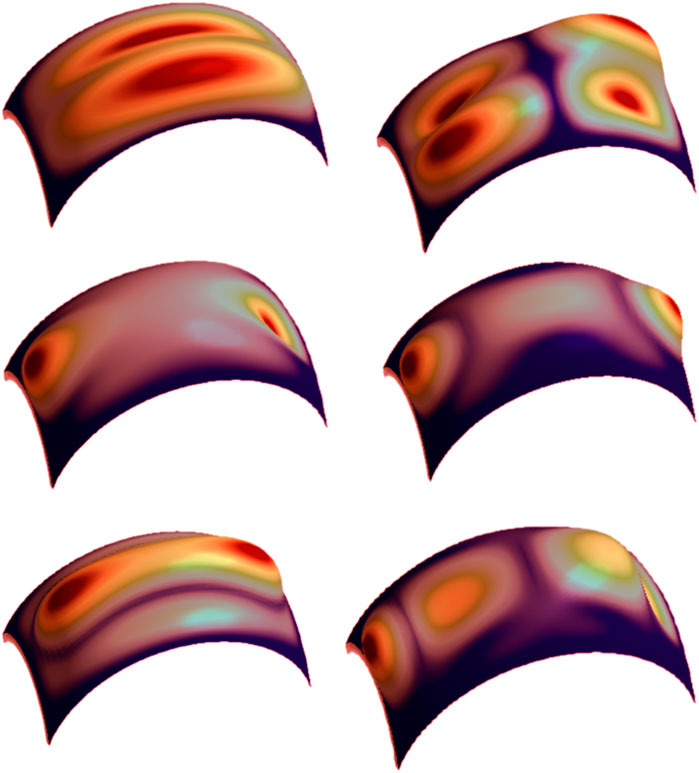
FIGURE 4. The first six buckling mode shapes of FG-GPL porous doubly curved panel (GPLX,
4 Conclusion
Free vibration characteristics of FG porous metal foam doubly curved shell panel reinforced by GPLs nanofillers have been surveyed in this research. Four distinct porosity functions and five GPL distributions are considered across the shell thickness. Applying FSDT and employing FEM based on the Hamilton principle, the governing motion equations of the shell are derived. The effects of GPL patterns, the weight fraction of nanofillers, porosity coefficient, and pattern and span angles on the free vibration responses of FG-GPL doubly curved panels with FG porosities have been examined. The main results are as:
a) Maximum and minimum fundamental frequencies are obtained for GPL-X and GPL-UD, respectively.
b) The fundamental frequencies of GPL-A and GPL-V are approximately identical.
c) The maximum and minimum fundamental frequencies of the shell have been obtained for PD1 and PD3.
d) By changing
e) By growing the size of the porosity of the structure, the fundamental frequencies of the shell decrease by 22%.
f) The natural frequencies are less influenced by GPL distribution than other parameters (about 13%).
g) By increasing the span angle
Data availability statement
The raw data supporting the conclusion of this article will be made available by the authors, without undue reservation.
Author contributions
Li-Li Zhang: Conceptualization, Data curation, Formal Analysis, Investigation, Methodology, Software, Validation, Writing original draft, Writing–review & editing. Li-Cai Zhao: Conceptualization, Data curation, Formal Analysis, Investigation, Methodology, Software, Validation, Writing–original draft, Writing–review & editing. Song-Jun Lang: Conceptualization, Data curation, Formal Analysis, Investigation, Methodology, Software, Writing–original draft, Writing–review & editing. Kamran Asemi: Conceptualization, Investigation, Methodology, Supervision, Validation, Writing–review & editing.
Funding
The author(s) declare that no financial support was received for the research, authorship, and/or publication of this article.
Conflict of interest
Author L-CZ was employed by Co., Ltd. The remaining authors declare that the research was conducted in the absence of any commercial or financial relationships that could be construed as a potential conflict of interest.
Publisher’s note
All claims expressed in this article are solely those of the authors and do not necessarily represent those of their affiliated organizations, or those of the publisher, the editors and the reviewers. Any product that may be evaluated in this article, or claim that may be made by its manufacturer, is not guaranteed or endorsed by the publisher.
References
Adamian, A., Hosseini Safari, K., Sheikholeslami, M., Habibi, M., Al-Furjan, M. S. H., and Chen, G. (2020). Critical temperature and frequency characteristics of GPLs-reinforced composite doubly curved panel. Appl. Sci. 10 (9), 3251. doi:10.3390/app10093251
Amirabadi, H., Farhatnia, F., and Civalek, Ӧ. (2021). Frequency response of rotating two-directional functionally graded GPL-reinforced conical shells on elastic foundation. J. Braz. Soc. Mech. Sci. Eng. 43 (7), 349. doi:10.1007/s40430-021-03058-6
Amirabadi, H., Farhatnia, F., Eftekhari, S. A., and Hosseini-Ara, R. (2022). Free vibration analysis of rotating functionally graded GPL-reinforced truncated thick conical shells under different boundary conditions. Mech. Based Des. Struct. Mach. 50 (11), 3821–3852. doi:10.1080/15397734.2020.1822183
Amirabadi, H., Farhatnia, F., Eftekhari, S. A., and Hosseini-Ara, R. (2023). Wave propagation in rotating functionally graded GPL-reinforced cylindrical shells based on the third-order shear deformation theory. Waves Random Complex Media 33 (2), 345–371. doi:10.1080/17455030.2021.1880031
Anirudh, B., Ganapathi, M., Anant, C., and Polit, O. (2019). A comprehensive analysis of porous graphene-reinforced curved beams by finite element approach using higher-order structural theory: bending, vibration and buckling. Compos. Struct. 222, 110899. doi:10.1016/j.compstruct.2019.110899
Arshid, E., Amir, S., and Loghman, A. (2020). Static and dynamic analyses of FG-GNPs reinforced porous nanocomposite annular micro-plates based on MSGT. Int. J. Mech. Sci. 180, 105656. doi:10.1016/j.ijmecsci.2020.105656
Arshid, E., Amir, S., and Loghman, A. (2021). Thermal buckling analysis of FG graphene nanoplatelets reinforced porous nanocomposite MCST-based annular/circular microplates. Aerosp. Sci. Technol. 111, 106561. doi:10.1016/j.ast.2021.106561
Asgari, G. R., Arabali, A., Babaei, M., and Asemi, K. (2022). Dynamic instability of sandwich beams made of isotropic core and functionally graded graphene platelets-reinforced composite face sheets. Int. J. Struct. Stab. Dyn. 22 (08), 2250092. doi:10.1142/s0219455422500924
Ashby, M. F., Evans, T., Fleck, N. A., Hutchinson, J., Wadley, H., and Gibson, L. (2000). Metal foams: a design guide. Oxford, United Kingdom: Butterworth-Heinemann.
Babaei, H. (2022). Thermomechanical analysis of snap-buckling phenomenon in long FG-CNTRC cylindrical panels resting on nonlinear elastic foundation. Compos. Struct. 286, 115199. doi:10.1016/j.compstruct.2022.115199
Bahaadini, R., Saidi, A. R., Arabjamaloei, Z., and Ghanbari-Nejad-Parizi, A. (2019). Vibration analysis of functionally graded graphene reinforced porous nanocomposite shells. Int. J. Appl. Mech. 11 (07), 1950068. doi:10.1142/s1758825119500686
Barati, M. R., and Zenkour, A. M. (2019). Vibration analysis of functionally graded graphene platelet reinforced cylindrical shells with different porosity distributions. Mech. Adv. Mater. Struct. 26 (18), 1580–1588. doi:10.1080/15376494.2018.1444235
Chai, Q., and Wang, Y. Q. (2022). Traveling wave vibration of graphene platelet reinforced porous joined conical-cylindrical shells in a spinning motion. Eng. Struct. 252, 113718. doi:10.1016/j.engstruct.2021.113718
Cho, J. R. (2023). Free vibration analysis of functionally graded porous cylindrical panels reinforced with graphene platelets. Nanomaterials 13 (9), 1441. doi:10.3390/nano13091441
Choi, J., and Lakes, R. (1995). Analysis of elastic modulus of conventional foams and of re-entrant foam materials with a negative Poisson's ratio. Int. J. Mech. Sci. 37, 51–59. doi:10.1016/0020-7403(94)00047-n
Civalek, Ö., Dastjerdi, S., and Akgöz, B. (2022). Buckling and free vibrations of CNT-reinforced cross-ply laminated composite plates. Mech. Based Des. Struct. Mach. 50 (6), 1914–1931. doi:10.1080/15397734.2020.1766494
Dastjerdi, S., Akgöz, B., and Civalek, Ö. (2020a). On the effect of viscoelasticity on behavior of gyroscopes. Int. J. Eng. Sci. 149, 103236. doi:10.1016/j.ijengsci.2020.103236
Dastjerdi, S., Akgöz, B., Civalek, Ö., Malikan, M., and Eremeyev, V. A. (2020b). On the non-linear dynamics of torus-shaped and cylindrical shell structures. Int. J. Eng. Sci. 156, 103371. doi:10.1016/j.ijengsci.2020.103371
Dong, Y., Gao, Y., Zhu, Q., Moradi, Z., and Safa, M. (2022). TE-GDQE implementation to investigate the vibration of FG composite conical shells considering a frequency controller solid ring. Eng. Analysis Bound. Elem. 138, 95–107. doi:10.1016/j.enganabound.2022.01.017
Dong, Y. H., He, L. W., Wang, L., Li, Y. H., and Yang, J. (2018b). Buckling of spinning functionally graded graphene reinforced porous nanocomposite cylindrical shells: an analytical study. Aerosp. Sci. Technol. 82, 466–478. doi:10.1016/j.ast.2018.09.037
Dong, Y. H., Zhu, B., Wang, Y., Li, Y. H., and Yang, J. (2018a). Nonlinear free vibration of graded graphene reinforced cylindrical shells: effects of spinning motion and axial load. J. Sound Vib. 437, 79–96. doi:10.1016/j.jsv.2018.08.036
Ebrahimi, F., Mohammadi, K., Barouti, M. M., and Habibi, M. (2021). Wave propagation analysis of a spinning porous graphene nanoplatelet-reinforced nanoshell. Waves random complex media 31 (6), 1655–1681. doi:10.1080/17455030.2019.1694729
Ebrahimi, F., Seyfi, A., Dabbagh, A., and Tornabene, F. (2019). Wave dispersion characteristics of porous graphene platelet-reinforced composite shells. Struct. Eng. Mech. Int'l J. 71 (1), 99–107. doi:10.12989/sem.2019.71.1.099
Esmaeili, H. R., and Kiani, Y. (2022). Vibrations of graphene platelet reinforced composite doubly curved shells subjected to thermal shock. Mech. Based Des. Struct. Mach. 52, 650–679. doi:10.1080/15397734.2022.2120499
Esmaeili, H. R., Kiani, Y., and Beni, Y. T. (2022). Vibration characteristics of composite doubly curved shells reinforced with graphene platelets with arbitrary edge supports. Acta Mech. 233 (2), 665–683. doi:10.1007/s00707-021-03140-z
Gibson, I. J., and Ashby, M. F. (1982). The mechanics of three-dimensional cellular materials. Proc. R. Soc. Lond. A. Math. Phys. Sci. 382 (1782), 43–59. doi:10.1098/rspa.1982.0088
Guo, H., Yang, T., Żur, K. K., Reddy, J. N., and Ferreira, A. J. M. (2021). “Effect of thermal environment on nonlinear flutter of laminated composite plates reinforced with graphene nanoplatelets,” in Modeling and computation in vibration problems, volume 1: numerical and semi-analytical methods (Bristol, United Kingdom: IOP Publishing).
Hill, R. (1965). A self-consistent mechanics of composite materials. J. Mech. Phys. Solids 13 (4), 213–222. doi:10.1016/0022-5096(65)90010-4
Hucke, E. E. (1971). “Preliminary reports,” in Memoranda and Technical Notes of the ARPA Materials Summer Conference Held at Woods Hole Volume 1, Massachusetts, July 1971. & MICHIGAN UNIV ANN ARBOR DEPT OF MATERIALS AND METALLURGICAL ENGINEERING.
Kiarasi, F., Babaei, M., Mollaei, S., Mohammadi, M., and Asemi, K. (2021). Free vibration analysis of FG porous joined truncated conical-cylindrical shell reinforced by graphene platelets. Adv. nano Res. 11 (4), 361–380. doi:10.12989/anr.2021.11.4.361
Li, Z., and Zheng, J. (2020). Nonlinear stability of the encased functionally graded porous cylinders reinforced by graphene nanofillers subjected to pressure loading under thermal effect. Compos. Struct. 233, 111584. doi:10.1016/j.compstruct.2019.111584
Liu, D., Zhou, Y., and Zhu, J. (2021). On the free vibration and bending analysis of functionally graded nanocomposite spherical shells reinforced with graphene nanoplatelets: three-dimensional elasticity solutions. Eng. Struct. 226, 111376. doi:10.1016/j.engstruct.2020.111376
Liu, G. R. (1997). A step-by-step method of rule-of-mixture of fiber-and particle-reinforced composite materials. Compos. Struct. 40 (3-4), 313–322. doi:10.1016/s0263-8223(98)00033-6
Lovisi, G. (2023). Application of the surface stress-driven nonlocal theory of elasticity for the study of the bending response of FG cracked nanobeams. Compos. Struct. 324, 117549. doi:10.1016/j.compstruct.2023.117549
Mahamood, R. M., Akinlabi, E. T., Mahamood, R. M., and Akinlabi, E. T. (2017). Types of functionally graded materials and their areas of application. Funct. graded Mater., 9–21. doi:10.1007/978-3-319-53756-6_2
Mohammadi, H. (2023). “Isogeometric free vibration analysis of trapezoidally corrugated FG-GRC laminated panels using higher-order shear deformation theory,” in Structures (vol. 48) (Amsterdam, Netherlands: Elsevier), 642–656.
Mohammadi, H., Shojaee, M., and Kiani, Y. (2023). A simplified isogeometric approach for vibrational analysis of nanocomposite panels with a free-form curve. Thin-Walled Struct. 183, 110426. doi:10.1016/j.tws.2022.110426
Mollaei, S., Babaei, M., and Asemi, K. (2023). Torsional buckling of functionally graded graphene reinforced composite laminated cylindrical panel. Archive Appl. Mech. 93 (2), 427–435. doi:10.1007/s00419-022-02132-2
Moradi-Dastjerdi, R., and Behdinan, K. (2020). Stability analysis of multifunctional smart sandwich plates with graphene nanocomposite and porous layers. Int. J. Mech. Sci. 167, 105283. doi:10.1016/j.ijmecsci.2019.105283
Moradi-Dastjerdi, R., and Behdinan, K. (2021). Stress waves in thick porous graphene-reinforced cylinders under thermal gradient environments. Aerosp. Sci. Technol. 110, 106476. doi:10.1016/j.ast.2020.106476
Mori, T., and Tanaka, K. (1973). Average stress in matrix and average elastic energy of materials with misfitting inclusions. Acta metall. 21 (5), 571–574. doi:10.1016/0001-6160(73)90064-3
Nejadi, M. M., Mohammadimehr, M., and Mehrabi, M. (2021). Free vibration and stability analysis of sandwich pipe by considering porosity and graphene platelet effects on conveying fluid flow. Alexandria Eng. J. 60 (1), 1945–1954. doi:10.1016/j.aej.2020.11.042
Penna, R. (2023). Bending analysis of functionally graded nanobeams based on stress-driven nonlocal model incorporating surface energy effects. Int. J. Eng. Sci. 189, 103887. doi:10.1016/j.ijengsci.2023.103887
Penna, R., Feo, L., and Lovisi, G. (2021). Hygro-thermal bending behavior of porous FG nano-beams via local/nonlocal strain and stress gradient theories of elasticity. Compos. Struct. 263, 113627. doi:10.1016/j.compstruct.2021.113627
Penna, R., Feo, L., Lovisi, G., and Fabbrocino, F. (2022). Application of the higher-order Hamilton approach to the nonlinear free vibrations analysis of porous FG nano-beams in a hygrothermal environment based on a local/nonlocal stress gradient model of elasticity. Nanomaterials 12 (12), 2098. doi:10.3390/nano12122098
Permoon, M. R., Farsadi, T., and Askarian, A. R. (2023). Vibration analysis of sandwich cylindrical shells made of graphene platelet polymer–viscoelastic–ceramic/metal FG layers. Funct. Compos. Struct. 5 (1), 015004. doi:10.1088/2631-6331/acbd28
Pourjabari, A., Hajilak, Z. E., Mohammadi, A., Habibi, M., and Safarpour, H. (2019). Effect of porosity on free and forced vibration characteristics of the GPL reinforcement composite nanostructures. Comput. Math. Appl. 77 (10), 2608–2626. doi:10.1016/j.camwa.2018.12.041
Qin, Z., Safaei, B., Pang, X., and Chu, F. (2019). Traveling wave analysis of rotating functionally graded graphene platelet reinforced nanocomposite cylindrical shells with general boundary conditions. Results Phys. 15, 102752. doi:10.1016/j.rinp.2019.102752
Rao, M. N., Schmidt, R., and Schröder, K. U. (2018). “Forced vibration analysis of FG-graphene platelet reinforced polymer composite shells bonded with piezoelectric layers considering electroelastic nonlinearities,” in Smart materials, adaptive structures and intelligent systems (vol. 51944, p. V001T03A006) (American Society of Mechanical Engineers).
Saffari, S., Hashemian, M., and Toghraie, D. (2017). Dynamic stability of functionally graded nanobeam based on nonlocal Timoshenko theory considering surface effects. Phys. B Condens. Matter 520, 97–105. doi:10.1016/j.physb.2017.06.029
Salehi, M., Gholami, R., and Ansari, R. (2023). Analytical solution approach for nonlinear vibration of shear deformable imperfect FG-GPLR porous nanocomposite cylindrical shells. Mech. Based Des. Struct. Mach. 51 (4), 2177–2199. doi:10.1080/15397734.2021.1891096
Shen, H. S., Xiang, Y., and Fan, Y. (2019). Large amplitude vibration of doubly curved FG-GRC laminated panels in thermal environments. Nanotechnol. Rev. 8 (1), 467–483. doi:10.1515/ntrev-2019-0042
Shen, M., and Bever, M. B. (1972). Gradients in polymeric materials. J. Mater. Sci. 7, 741–746. doi:10.1007/bf00549902
Sobhani, E., Arbabian, A., Civalek, Ö., and Avcar, M. (2021). The free vibration analysis of hybrid porous nanocomposite joined hemispherical–cylindrical–conical shells. Eng. Comput. 38, 3125–3152. doi:10.1007/s00366-021-01453-0
Sobhani, E., and Avcar, M. (2022). The influence of various nanofiller materials (CNTs, GNPs, and GOPs) on the natural frequencies of Nanocomposite Cylindrical Shells: a comparative study. Mater. Today Commun. 33, 104547. doi:10.1016/j.mtcomm.2022.104547
Sobhani, E., Koohestani, M., Civalek, Ö., and Avcar, M. (2023a). Natural frequency investigation of graphene oxide powder nanocomposite cylindrical shells surrounded by Winkler/Pasternak/Kerr elastic foundations with a focus on various boundary conditions. Eng. Analysis Bound. Elem. 149, 38–51. doi:10.1016/j.enganabound.2023.01.012
Sobhani, E., Masoodi, A. R., and Civalek, Ö. (2023b). On vibrational-based numerical simulation of a jet engine cowl shell-like structure. Mech. Adv. Mater. Struct. 30 (19), 4016–4027. doi:10.1080/15376494.2022.2087241
Sobhy, M., and Zenkour, A. M. (2019). Vibration analysis of functionally graded graphene platelet-reinforced composite doubly-curved shallow shells on elastic foundations. Steel compos. Struct. 33 (2), 195–208. doi:10.12989/scs.2019.33.2.195
Ton-That, H. L., Nguyen-Van, H., and Chau-Dinh, T. (2021). A novel quadrilateral element for analysis of functionally graded porous plates/shells reinforced by graphene platelets. Archive Appl. Mech. 91, 2435–2466. doi:10.1007/s00419-021-01893-6
Twinkle, C. M., and Pitchaimani, J. (2021). Free vibration and stability of graphene platelet reinforced porous nano-composite cylindrical panel: influence of grading, porosity and non-uniform edge loads. Eng. Struct. 230, 111670. doi:10.1016/j.engstruct.2020.111670
Van Do, V. N., and Lee, C. H. (2020a). Bézier extraction based isogeometric analysis for bending and free vibration behavior of multilayered functionally graded composite cylindrical panels reinforced with graphene platelets. Int. J. Mech. Sci. 183, 105744. doi:10.1016/j.ijmecsci.2020.105744
Van Do, V. N., and Lee, C. H. (2020b). Static bending and free vibration analysis of multilayered composite cylindrical and spherical panels reinforced with graphene platelets by using isogeometric analysis method. Eng. Struct. 215, 110682. doi:10.1016/j.engstruct.2020.110682
Voigt, W. (1889). Ueber die Beziehung zwischen den beiden Elasticitätsconstanten isotroper Körper. Ann. Phys. 274 (12), 573–587. doi:10.1002/andp.18892741206
Wakashima, K., and Tsukamoto, H. (1991). Mean-field micromechanics model and its application to the analysis of thermomechanical behaviour of composite materials. Mater. Sci. Eng. A 146 (1-2), 291–316. doi:10.1016/0921-5093(91)90284-t
Wang, A., Chen, H., Hao, Y., and Zhang, W. (2018). Vibration and bending behavior of functionally graded nanocomposite doubly-curved shallow shells reinforced by graphene nanoplatelets. Results Phys. 9, 550–559. doi:10.1016/j.rinp.2018.02.062
Wang, Y. Q., Ye, C., and Zu, J. W. (2019). Nonlinear vibration of metal foam cylindrical shells reinforced with graphene platelets. Aerosp. Sci. Technol. 85, 359–370. doi:10.1016/j.ast.2018.12.022
Wattanasakulpong, N., and Chaikittiratana, A. (2015). Flexural vibration of imperfect functionally graded beams based on Timoshenko beam theory: Chebyshev collocation method. Meccanica 50, 1331–1342. doi:10.1007/s11012-014-0094-8
Yang, J., Chen, D., and Kitipornchai, S. (2018). Buckling and free vibration analyses of functionally graded graphene reinforced porous nanocomposite plates based on Chebyshev-Ritz method. Compos. Struct. 193, 281–294. doi:10.1016/j.compstruct.2018.03.090
Ye, C., and Wang, Y. Q. (2021). Nonlinear forced vibration of functionally graded graphene platelet-reinforced metal foam cylindrical shells: internal resonances. Nonlinear Dyn. 104 (3), 2051–2069. doi:10.1007/s11071-021-06401-7
Zhang, D., Wang, Y., and Li, L. (2023). Free vibration response of FG porous joined hemispherical–cylindrical–hemispherical shell vessels reinforced by graphene platelet. Int. J. Struct. Stab. Dyn. 23 (03), 2350025. doi:10.1142/s0219455423500256
Zhao, J., Fan, G., Guan, J., Li, H., Liu, J., Xie, Z., et al. (2023). Free vibration and dynamic analysis on free-constrained layer of graphene based on composite conical shell via Jacobi-Ritz method. Int. J. Struct. Stab. Dyn. doi:10.1142/s0219455424500238
Zhao, S., Yang, Z., Kitipornchai, S., and Yang, J. (2020). Dynamic instability of functionally graded porous arches reinforced by graphene platelets. Thin-Walled Struct. 147, 106491. doi:10.1016/j.tws.2019.106491
Zhou, X., Wang, Y., and Zhang, W. (2021). Vibration and flutter characteristics of GPL-reinforced functionally graded porous cylindrical panels subjected to supersonic flow. Acta Astronaut. 183, 89–100. doi:10.1016/j.actaastro.2021.03.003
Appendix A
Keywords: Doubly curved panel, FG porous, GPLS, Free vibration, FSDT, FEM
Citation: Zhang L-L, Zhao L-C, Lang S-J and Asemi K (2024) Free vibration analysis of functionally graded graphene platelet-reinforced metal foam doubly curved panel. Front. Mater. 11:1339865. doi: 10.3389/fmats.2024.1339865
Received: 16 November 2023; Accepted: 07 February 2024;
Published: 01 March 2024.
Edited by:
Luciano Feo, University of Salerno, ItalyReviewed by:
Ömer Civalek, Akdeniz University, TürkiyeRaffaele Barretta, University of Naples Federico II, Italy
Giuseppe Lovisi, University of Salerno, Italy
Copyright © 2024 Zhang, Zhao, Lang and Asemi. This is an open-access article distributed under the terms of the Creative Commons Attribution License (CC BY). The use, distribution or reproduction in other forums is permitted, provided the original author(s) and the copyright owner(s) are credited and that the original publication in this journal is cited, in accordance with accepted academic practice. No use, distribution or reproduction is permitted which does not comply with these terms.
*Correspondence: Li-Cai Zhao, emhhb2xpY2FpQHRqdS5lZHUuY24=; Kamran Asemi, ay5hc2VtaUBpYXUtdG5iLmFjLmly