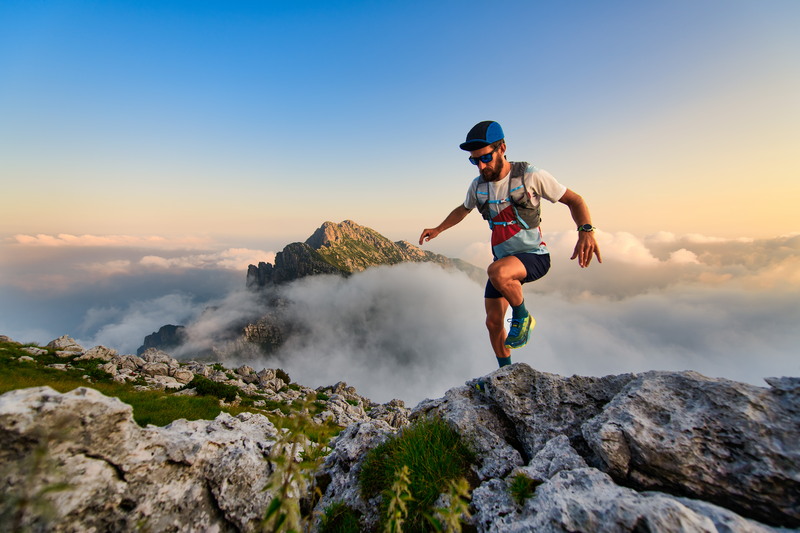
95% of researchers rate our articles as excellent or good
Learn more about the work of our research integrity team to safeguard the quality of each article we publish.
Find out more
ORIGINAL RESEARCH article
Front. Mater. , 22 February 2024
Sec. Structural Materials
Volume 11 - 2024 | https://doi.org/10.3389/fmats.2024.1308884
This article is part of the Research Topic Recent advances in eco-friendly construction materials: waste upcycling in building materials View all 3 articles
Construction and demolition waste (CDW) was fully exploited to prepare high-strength and low-cost unfired bricks. A compound additive consisting of sodium silicate, microsilica powder, an early-strength water reducer, and wood fiber was incorporated into the bricks. Tests (compressive tests, freeze–thaw cycle tests, and scanning electron microscopy (SEM)) were carried out to determine the effect of the contents of the additive components on the properties (the strength, softening coefficient, freezing resistance, hydration products, and microscopic morphology) of unfired bricks of different curing ages. The experimental results were used to determine the optimum ratio of the components and the hydration mechanism. The optimized compound additive considerably improved the mechanical properties and crack resistance of the bricks, where the optimum content was found to be only 3.15% of the CDW dry mass. Compared with unfired bricks with no additives, unfired bricks with the optimized compound additive exhibited increases in the 1- and 28-day compressive strengths and softening coefficient of up to 66.8%, 65.9%, and 8.46%, respectively (corresponding to values of 8.46 MPa, 29.36 MPa, and 0.934, respectively) and a decrease in the freeze–thaw strength loss rate of 61.38%. Incorporating the compound additive into the unfired bricks considerably reduced the environmental impact. The SEM micrographs showed that the compound additive increased the silicon-to-calcium ratio and workability of the preparation mixture, increased the hydration rate, promoted the conversion of calcium hydroxide in the product to a C–S–H gel, and enhanced the density and strength of the hydration product.
Construction and demolition waste (CDW) is solid waste generated by activities such as the construction, demolition, and renovation of buildings (Islam et al., 2019). Studies have shown that construction waste accounts for 30%–40% of the total solid waste generated worldwide (Islam et al., 2019; Pallewatta et al., 2023). Construction and demolition waste has environmental and economic repercussions in many countries (Aslam et al., 2020). As a result of accelerating urbanization, the estimated total quantity of construction waste in China in 2014 was over 1.1 billion tons (Menegaki and Damigos, 2018; Duan et al., 2019; Gupta et al., 2020). This quantity exceeded 20 billion tons in 2020 and has since been increasing at a rapid rate of 3 billion tons per year (Liu et al., 2022). More than 50% of CDW is not directly used and is stored in outdoor open spaces, which takes up a large proportion of arable land, affects the urban landscape, and causes severe environmental pollution (Wu et al., 2022). Reuse is the most effective management and disposal scheme for reducing the quantity and toxicity of CDW.
At present, CDW is commonly used to prepare recycled aggregates. After crushing and sieving of CDW, coarse particles with a particle size greater than 4.75 mm are used as recycled aggregates for concrete (Mi et al., 2022; Raza et al., 2022; Zhang et al., 2022), but the fine particles are directly discarded and dumped because of a high impurity content. Discarding these fine particles reduces the waste utilization rate and may cause severe secondary air and water pollution (Jannat et al., 2020; Limami et al., 2020; Limami et al., 2021). Unfired bricks are not picky about raw materials, and CDW fine particles contain a lot of active substances (Borrachero et al., 2022; Sanqiang et al., 2022). With the activation of additives (Villaquirán-Caicedo and Mejía de Gutiérrez, 2021), they can promote the strength of unfired bricks and save costs. Therefore, using fine CDW particles to fabricate unfired bricks has been proven to be both environmentally friendly and technically feasible (Menegaki and Damigos, 2018; Aslam et al., 2020; Kurmus and Mohajerani, 2020).
Unfired bricks are building blocks fabricated from binder, natural sand, clay, and a portion of solid waste materials. The brick preparation mixture is homogenized by vibration, subjected to static pressure, and manually molded (Fragnoli et al., 2023; Othmane et al., 2023). Waste materials can replace some of the raw materials used for unfired bricks, and a binder can be used instead of firing to produce strength. The prepared bricks are a low-carbon, economical, and sustainable building material (Chen et al., 2023).
Many researchers have substituted natural materials in unfired bricks by stabilizing various waste materials, such as tunnel musk, mud, sand, clay, CDW, stone dust, and paper-mill residue. Hu et al., 2022b attempted to use cement and additives to bond tunnel sludge to prepare unburned bricks to improve the utilization rate of tunnel sludge. The research results showed that the addition of cement, soil ionic agents, and red brick powder can significantly improve the compressive strength of unburned bricks. Hu and Hongye, 2021 prepared unfired bricks using sulfoaluminate cement stabilized slurry and investigated the effects of changes in slurry content on the fluidity, setting time, porosity, and compressive strength of the slurry. Tao et al., 2018 tested the physical and mechanical properties and microstructure of unfired brick specimens using sand as the substrate, and pointed out that compared to only adding cement, the addition of GGBS can adjust the particle size distribution morphology, promote volcanic ash reaction, and fill the pores, thereby improving the compactness and strength of the specimens. Some scholars also use natural clay and river silt, excavation silt, stone mud, etc. to prepare unfired bricks, but soil with high viscosity has the characteristic of poor water stability, requiring the addition of a large number of stable materials for blending (Oti et al., 2014; Dove et al., 2016; El Fgaier et al., 2016; Muheise-Araalia and Pavia, 2021; Sharma et al., 2022). To reduce the weight of unfired bricks. Raut et al., 2013 used paper mill residue (RPMR) and rice husk ash (RHA) to improve the performance of unfired bricks. When the compressive strength reached 15 MPa, the density could be reduced to 0.55 g/cm3. However, this type of unfired brick has lower fire resistance. It has been proven feasible to replace some natural clay with crushed construction waste and use cement, blast furnace slag, lime, and fly ash as cementitious materials to prepare unfired bricks. However, the utilization rate of construction waste is relatively low (Xu et al., 2012; Contreras et al., 2016; Seco et al., 2018). Chen et al., 2023 exploited the similarity between the characteristics of natural clay and red mud by using a dealkalized calcium silicate residue made of red mud, cement, and sand as raw materials in the preparation of unfired lightweight bricks. Increasing the content of the dealkalized calcium silicate slag was found to reduce the compressive strength and softening coefficient of the unfired bricks. The strength of the lightweight bricks was maximized (at 15 MPa) by using a preparation mixture of 20%, 50%, and 30% of added cement, dealkalized calcium silicate, and sand, respectively. Shi et al., 2020 evaluated the performance of bricks prepared from pulverized coal ash slag, phosphogypsum slag, and silt. The fluidity of the preparation mixture decreased as the silt content increased. Using a cementitious material dosage of 40% of the silt mass produced bricks with a compressive strength of only 11.6 MPa. Zhu et al., 2020 used a cement–lime dual gel to stabilize silt for preparing unfired bricks. The effect of the cement-to-lime ratio on the properties of unfired bricks was studied. Using equal contents (20%) of R. SAC42.5 cement and lime produced unfired bricks with a strength of up to 18 MPa. Yu et al., 2021 studied how the silt content affected the strength, density, shrinkage rate, and water absorption of unfired bricks. The brick strength was found to decrease as the silt content increased. Using a 63:37 silt-to-cement ratio resulted in a brick strength of only 8.6 MPa. The application of a low-performing waste, such as silt, for fabricating unfired bricks is limited by the need to use large quantities of binder as well as by the low strength and durability of the produced bricks (Zhao and Gou, 2021; Hu et al., 2022b; Mojapelo and Nkosinomusa Nomfundo, 2022).
Some researchers have used CDW to improve the physical and mechanical properties of unfired bricks. J.E. Oti et al., 2014 assessed the feasibility of using brick powder waste to replace clay in unfired bricks. For unfired bricks with 5%–20% waste brick powder, the compressive strength increased with the powder replacement rate. Aguilar-Penagos et al., 2017 used cactus mucilage and four different building waste powders to replace clay in unfired bricks. Although CDW can be used with natural binders to reduce environmental impact and costs, CDW has a replacement rate of only 17% and produces bricks with a maximum strength of only 6 MPa. Khitab et al., 2021 used brick powder and ceramic powder to replace a portion of the clay used in clay bricks. The results showed that as the replacement rate of brick powder and ceramic powder increases, the properties of the brick such as frost resistance, compressive strength, and elastic modulus also increase. The best performance is achieved at a replacement rate of 9%. At this time, the brick showed the highest resistance against freeze and thaw (only 0.87% weight loss), with the highest compressive strength and elastic modulus being 11 MPa and 3.32 MPa, respectively. When the powder substitution rate exceeds the optimal value, various properties decrease accordingly. However, when the powder content reaches 27%, the various properties of the brick are consistent with those of 100% clay brick. A. Seco et al., 2018 used recycled concrete and ceramic fine particles to replace clay in unfired bricks. The performance of the unfired bricks deteriorated as the waste replacement rate was increased. The maximum replacement rate of concrete and ceramic particles that did not affect the brick performance was found to be 50% and 30%, respectively. Lei et al., 2022 studied the influence of sisal fiber on compressive strength, flexural strength, porosity, microstructure, and saturation coefficient of waste ceramic tile recycled brick. The research results showed that the addition of sisal fiber increases the maximum flexural strength of recycled bricks by 36.83%, but reduces the maximum compressive strength by 19.12%. When the dosage is 3.0 kg/m3, the 28 days flexural strength is 4.5 MPa, and the compressive strength is 16 MPa, respectively, at this time, the overall performance of the compressive strength and flexural strength of recycled bricks reached the optimal balance. In previous studies, replacing less than 50% of natural materials with construction waste and using over 30% of cementitious material was found to produce unfired bricks with strengths below 20 MPa (Contreras et al., 2016; Menegaki and Damigos, 2018). This result shows that the production of unfired bricks requires considerable consumption of natural materials, such as sand, clay, and cementitious materials. In addition, high production costs and the poor mechanical properties of the produced bricks pose considerable challenges to the industrial preparation of unfired bricks.
To promote the large-scale production of unfired bricks prepared from CDW, this study was performed to investigate the feasibility of using CDW (as a complete replacement for natural materials) in conjunction with a small quantity of cement and a compound additive to prepare high-performance and low-cost fired bricks. The compound additive consisted of sodium silicate, microsilica powder, an early-strength water reducer, and wood fiber. Compressive strength tests, freeze–thaw cycle tests, and scanning electron microscopy (SEM) were carried out to determine how the contents of the additive components affected the properties (the strength, softening coefficient, frost resistance, hydration products, and microstructure) of bricks of different ages. The optimal ratio of the components of the compound additive was determined, and the hydration mechanism was elucidated. The environmental impact of the compound additive was evaluated.
Fine particles were prepared from CDW and mixed with P.O42.5 ordinary Portland cement (as the base cementitious material) and a compound additive to fabricate unfired bricks. The fine particles had a particle size of <4.75 mm and was obtained from a CDW crushing plant in Zhengzhou, Henan province, China. The P.O42.5 ordinary Portland cement was produced by the Tianrui Cement Factory. The compound additive used in the unfired bricks had four components. Water glass (liquid sodium silicate with a Baume degree of 37.3) was used as an activator for the fine particles and cement. Microsilica powder with a purity of 96% was used as a reinforcing agent. A water reducer was used to increase the content of free water in the preparation mixture and enhance the early strength of the unfired bricks. Wood fiber was used to enhance the frost- and crack-resistance of the unfired bricks. Table 1 shows the contents of the main oxides in the CDW, cement, and microsilica powder.
TABLE 1. Chemical and environmental characterization of construction and demolition wastes (CDW), cement, and microsilica powder.
Figure 1 shows the test scheme used in this study. The fine particles produced from CDW and the components of the compound additive were weighed, mixed manually, moistened, and homogenized. A two-step mixing procedure was used. First, the dry materials were placed in a blender and stirred for 120 s. Water was added to the mixture, which was then stirred for a further 480 s to ensure that the mixture had been homogenized and had fully absorbed the water. The mixture was placed in a special mold for preparing standard brick specimens with dimensions of 240 mm × 115 mm × 53 mm, and a pressure of 20 MPa was exerted on the mold for 2 s. The samples were stored indoors for 1 day (d) to obtain early strength, then sprayed with water, and cured to the desired age.
The compressive strength and softening coefficient of unfired bricks of various curing ages were measured following the JC/T422-2007 (2007) and GB/T 2542-2012 (2012) standards, respectively (Figure 2). Freeze–thaw cycle tests were also conducted on the bricks.
(1) Compressive strength test: The dried unfired bricks were broken by bending and arranged in stacks ≥100 mm long. The bricks were then placed in a TYA-2000 pressure testing machine and loaded in increments of 1 kN/s until the brick body was damaged. The average of the measured compressive strengths of five brick samples of a particular curing age was reported. The strengths of brick samples with curing ages of 1, 7, and 28 days were determined.
(2) Softening coefficient test: Unfired bricks were soaked in water for 24 h, wiping off surface moisture with a damp towel, and the compressive strength was measured.
(3) Freeze–thaw cycle test: The brick temperature was controlled from −15°C to 20°C. One freeze–thaw cycle consisted of freezing a brick specimen at −15°C for 5 h (h) and then placing the brick in warm water at 20°C for 3 h. The compressive strength of the brick sample after freezing and thawing was measured.
FIGURE 2. Tests performed on unfired bricks in the laboratory (A) Compressive strength test (B) Softening coefficient test (C) Freeze–thaw cycle test.
The components of the compound additive were added to the unfired bricks in separate stages to optimize the component contents. On the basis of the results of previous tests, cement was used as the base cementitious material. The cement content was 10% of the dry mass of the fine particles, and the water content was 17% of the total mass of the fine particles and cement. The test scheme consisted of four stages, and 19 different combinations of cementitious materials were added to the preparation mixture (Table 2). The prepared unfired bricks were then cured to the desired ages. The physical and mechanical indices (the compressive strength, softening coefficient, and frost resistance) of the cured bricks were then measured.
Water glass was added as an activator to the fine particles produced from CDW and cement. During the first test stage, the optimal dosage of water glass was determined to be 1% (A1) based on comparing the values of the compressive strength, softening coefficient, and frost resistance of the unfired bricks with various contents of water glass. This optimal dosage was then used in the initial control group tested in the second stage. During the second stage, microsilica powder was added as a reinforcing agent in various proportions to improve the long-term strength of the unfired bricks. The optimal proportion of microsilica powder was determined by assessing the three aforementioned indices and used for the initial control group (B4) tested in the third stage. The third stage consisted of adding a water reducer at various contents to the unfired brick to improve the early strength and facilitate hydration of the cement and microsilica powder. The optimal water reducer content (C2) was determined by evaluating the early strength of the bricks. As the thus-prepared unfired bricks were prone to cracking and had poor frost resistance, wood fiber was added during the fourth test stage. The optimal content of wood fiber was determined by analyzing the frost resistance of the bricks. The optimal ratio of the components of the compound additive was thereby determined.
The effect of the water-glass content on the properties of the unfired bricks was investigated. Bricks containing 1%–5% of water glass (in 1% increments) were prepared and cured for 1, 7, and 28 days Figure 3 shows the compressive strength versus the water-glass dosage for bricks of various ages.
FIGURE 3. Influence of the water-glass dosage on the compressive strength of bricks of various ages.
As the water-glass content increased, the compressive strength increased up to a water-glass content of 1%–2% and then decreased. The early strength of the unfired bricks cured for 1 day ranged between 5 and 6 MPa. For unfired bricks with 1% water glass, the compressive strength was increased by 4.2% and 7.9% by curing for 1 and 28 days, respectively.
Many studies (Robayo-Salazar et al., 2017; Riyap et al., 2020) have shown that the material strength increases with the water-glass content. However, the optimal water-glass content was found to be 1%–2% in this study, mainly because of the characteristics of the water glass and preparation technology used. A fast reaction between water glass and cement occurred as the preparation mixture was stirred. Thus, as the water-glass content increased, the rate of generation of the hydration products of the reaction increased, and the number and diameter of granular flocculants in the mixture increased. During pressing of the mixture, the largest particles were crushed first, whereas the small particles were not affected and adhesion between particles was lost after the gel product was destroyed. Therefore, as the dosage of the water glass increased, the strength of the unfired brick increased up to the optimal dosage and then decreased considerably.
Figure 4 shows the effect of the water-glass dosage on the softening coefficient and frost resistance of the unfired bricks. The softening coefficient varied considerably with the curing age. Regardless of the water-glass content, the maximum softening coefficient (almost >1.0) was obtained for bricks cured for 1 day. This result could be attributed to the softening effect of water being weaker than the strength enhancement from hydration of the cement and water glass during soaking. The softening coefficient of the bricks cured for 28 days varied between 0.82 and 0.88. The minimum softening coefficient was obtained by curing the bricks for 7 days, the age at which water had the strongest softening effect on the unfired bricks. For the unfired bricks cured for 7 and 28 days, the softening coefficient first increased and then decreased with increasing water-glass content. The softening coefficient reached a maximum for the bricks with a water glass content of ca. 1%. Thus, as the curing age increased, the strength first increased substantially but then decreased. For the unfired bricks that were cured for 7 days, insufficient hydration resulted in the formation of a large number of internal pores and softening. As the water-glass content increased, the strength loss of the unfired bricks (as measured in the freeze–thaw cycle tests) initially decreased and then increased nonlinearly. For bricks with a water-glass content of 1%, the minimum loss rate was 13.58%, corresponding to a decrease in the compressive strength from 18.93 MPa to 16.36 MPa.
FIGURE 4. Effect of the water-glass content on the softening coefficient and frost resistance of the unfired bricks.
By comprehensively considering the effect of the water-glass content on the compressive strength, softening coefficient, and frost resistance of the unfired bricks, the optimal water-glass content was determined to be 1% (Group A1). The compressive strength, softening coefficient, and frost resistance of the unfired bricks with 1% water glass after 28 days of curing were 7.9%, 2%, and 5.5% higher, respectively, than those of the control group.
As mentioned in Section 3.1, the unfired bricks with the optimal water-glass content had a 28-day compressive strength of 18.93 MPa, which meets the minimum MU15 level specified in the standards (2007). Therefore, the strength of the unfired bricks urgently needed to be improved. At this test stage, Group A1 was used as the initial group B0 to determine the optimal content of microsilica powder by comparing the values of the compressive strength, softening coefficient, and frost resistance of unfired bricks with various contents of microsilica powder. Microsilica powder particles are small and uniform, with large specific surface area and active properties, which can effectively fill the small pores in the sample and improve the compactness. At the same time, it reacts with the strong calcium oxide in the cement hydration product to generate the hydrated calcium silicate gel with high stability and strength. Therefore, the addition of micro silica powder can effectively improve the strength of unburned bricks (Biao et al., 2022).
Figure 5 shows the compressive strength of unfired bricks versus the content of microsilica powder. As the content of microsilica powder increased, the growth rate of the 7- and 28-day compressive strength first increased slowly, then increased rapidly, and finally decreased slightly. Increasing the content of microsilica powder from 0% to 1% resulted in a slow increase in the growth rate of the 7- and 28-day compressive strength to 0.5% and 6%, respectively. By contrast, as the content of microsilica powder was increased to 2%, the 7- and 28-day compressive strength increased rapidly to 19.64 and 25.47 MPa, respectively (corresponding to growth rates of 26.6% and 34.5%, respectively). Further increasing the content of microsilica powder to 2.5% caused the growth rates for the 7- and 28-day compressive strength to decrease to 23.9% and 27.3%, respectively. The early strength of the unfired bricks that were cured for 1 day exhibited an overall increasing trend in the content of microsilica powder. A maximum growth rate of the early strength of 10.4% was obtained for bricks with 2.5% microsilica powder.
FIGURE 5. Effect of the content of microsilica powder on the compressive strength of the unfired bricks.
Figure 6 shows the variation in the softening coefficient and frost resistance of the unfired bricks with the content of microsilica powder. The softening coefficient of the bricks with curing ages of 7 and 28 days increased overall as the content of the microsilica powder increased, reaching a maximum at contents of microsilica powder of 2.5% and 2%, respectively. For the unfired bricks with added microsilica powder, the compressive strength was clearly strongly correlated with the frost resistance (Figures 5, 6). That is, an increase in the compressive strength generally corresponded to an increase in the frost resistance. A minimum freeze–thaw strength loss rate of ca. 8.5% was obtained for bricks with 2% microsilica powder.
FIGURE 6. Effect of the content of microsilica powder on the softening coefficient and frost resistance of the unfired bricks.
In Group B4, the unfired bricks that were cured for 28 days had a maximum compressive strength of 25.47 MPa, which meets the high MU25 level in the standards (2007). However, the unfired bricks that were cured for 1 day had a low early strength, which does not facilitate brick transport and storage. Therefore, a water reducer was added during the third test stage to improve the early strength of the unfired bricks by fully using the internal moisture of the bricks to accelerate hydration. During this stage, Group B4 was used as the initial group C0, and the effect of the water-reducer content on the early compressive strength of the unfired bricks was determined. The water-reducer content was calculated based on the cement quality.
Figure 7 shows the compressive strength of the unfired bricks of various curing ages versus the water-reducer content. The increase in the compressive strength for the unfired bricks cured for 1 day was larger than those of bricks cured for 7 and 28 days. As the water-reducer content was increased from 0% to 0.5%, the early strength of the bricks with a curing age of 1 day increased rapidly by 40.5% to a maximum of 8.46 MPa. As the water-reducer content was further increased from 0.5% to 1%, the early strength decreased slowly and the rate of increase of the strength compared with that of Group C0 decreased to 33.7%. As the water-reducer content increased, the growth rate of the compressive strength of bricks that were cured for 7 and 28 days first increased slowly to a maximum at a water-reducer content of 0.5% and then decreased rapidly.
Figure 8 shows the softening coefficient and frost resistance of the unfired bricks with water-reducer contents ranging from 0% to 1%. For the unfired bricks with a curing age of 1 day, the softening coefficient gradually decreased as the water-reducer content increased. The softening coefficients for all the considered bricks were >1.0 because hydration was accelerated under the combined effects of the water reducer and water softening. As the water-reducer content increased, the softening coefficient of the unfired bricks cured for 28 days ranged from 0.9 to 0.92, indicating that the water reducer had an insubstantial effect on the strength. Figure 8 shows that the freeze–thaw strength loss rate fluctuated around ca. 10% for bricks with <1% water reducer but increased sharply to 13% for bricks with 1% water reducer.
FIGURE 8. Effect of the water-reducer content on the softening coefficient and frost resistance of the unfired bricks.
Although the strength of the unfired bricks was improved during the first three test stages, the bricks remained prone to microcracking during curing. Microcracks can provide channels for water transfer, and subsequent crack expansion and block loss during a freeze–thaw cycle can reduce the frost resistance of bricks. Therefore, to improve the crack resistance, frost resistance, and water retention of the unfired bricks, wood fiber was added at various contents during the fourth test stage. The optimal wood-fiber content was determined from the test results. Figures 7, 8 show the effect of the wood-fiber content on the compressive strength, water resistance, and frost resistance of the unfired bricks.
Figure 9 shows small-amplitude fluctuations in the compressive strength of the unfired bricks with various contents of added wood fiber and a curing age of 1 day. As the wood-fiber content increased, the strength of bricks with curing ages of 7 and 28 days first increased and then decreased. The bricks with 0.1% wood fiber and curing ages of 7 and 28 days had peak strengths of 22.61 and 29.36 MPa, respectively. Figure 10 indicates that as the wood-fiber content increased, the freeze–thaw strength loss rate of the unfired bricks first decreased rapidly and then increased rapidly. The bricks with 0.1% wood fiber exhibited the minimum strength loss of 5.6%, which was 39% lower than that of the control group (Group D0). Thus, the addition of wood fiber at an appropriate content can improve the frost resistance of unfired bricks. The softening coefficient of the unfired bricks varied with increasing fiber content. The softening coefficient of bricks cured for 28 days was slightly larger than those cured for 7 days.
FIGURE 10. Effect of the wood-fiber content on the softening coefficient and frost resistance of the unfired bricks.
The aforementioned changes mainly result from interweaving of the wood fiber and cementitious products into a network structure in the unfired bricks. These dispersed network structures both improve the compressive strength of unfired bricks and limit the formation and expansion of cracks, thereby improving the anticrack performance of the unfired bricks. However, an excessive content of wood fiber resulted in inadequate dispersion of wood fibers in the bricks, creating a weak interface and deteriorating the compressive strength. The flocculated wood fiber strongly absorbed water, making the brick prone to microcracking upon freezing (Can Mark and Vincent, 2022). Therefore, the reasonable additional amount of wood fibers has become a key issue in research. If the addition amount is too small, the wood fibers are independent of each other, making it difficult to form an effective tensile effect in unburned bricks, and the improvement of the physical and mechanical properties of the sample is limited. However, if the addition amount is too much, it can cause the fibers to form clumps, which actually reduces the compressive strength and crack resistance of unburned bricks. Based on the experimental results in Figure 10, the addition of 0.1% wood fiber reached the maximum value without forming clumps in unburned bricks, which is the optimal value. However, if specific fibers or special spraying processes are used to reduce fiber aggregation, the fiber content can be further increased.
Figure 11 shows the cracks and surface damage for the unfired bricks with 0%, 0.1%, and 0.2% wood fiber after 15 freeze–thaw cycles. After freeze–thawing, prominent cracks appeared on the side of the bricks without added wood fiber, whereas the surface of the bricks with 0.1% wood fiber was intact and smooth, without visible cracks or other damages. Freeze–thawing of the brick body containing 0.2% wood fiber resulted in various types of damage (such as corner shedding, surface detachment, and crack development). Thus, the freeze–thaw resistance of unfired bricks can be improved by adding 0.1% wood fiber.
On the basis of the results of the four test stages, the optimal group of compound additives is D2 in Table 2, and the optimal ratio of water glass: microsilica powder: water reducing agent: wood fiber was found to be 1:2:0.05:0.1, and the optimal content was 3.15% of CDW dry mass. Figure 12 shows the environmental impact of the compound additive based on the carbon dioxide (CO2) emissions and embodied energy. In the figure below, CA denotes the compound additive.
FIGURE 12. Environmental impact of the compound additive based on (A) the absolute and relative CO2 emissions and (B) the absolute and relative embodied energy.
For purposes of comparison (Seco et al., 2018), the absolute and relative CO2 emissions and embodied energy were calculated for unfired bricks made of clay with 10% cement, CDW with 10% cement, and CDW with 10% cement and 3.15% of the compound additive (Damineli et al., 2010; Grist et al., 2015; Seco et al., 2018).
The bricks based on CDW have lower CO2 emissions and embodied energy than the bricks based on clay because CDW has a zero environmental impact. As the compound additive has a lower environmental impact than cement, there is no discernible difference between the absolute environmental impact of bricks with small quantities of the additive and bricks without the additive. However, the incorporation of the compound additive into the unfired brick considerably improves the compressive strength, reducing the relative CO2 emissions from 5.31 kg/MPa to 2.80 kg/MPa (a 47.1% decrease) and the relative embodied energy from 21.71 MJ/MPa to 11.45 MJ/MPa (a 47.3% decrease). This result shows that the incorporation of the compound additive can considerably reduce the environmental impact of unfired bricks based on the relative CO2 emissions and embodied energy.
To elucidate the action mechanism of the compound additive, SEM was used to analyze the brick samples in Groups A0–D0 that were cured for 28 days.
Figure 13 shows that the microstructure and mineral composition of the unfired bricks containing various additives were substantially different (Figure 13). In Group A0 (Figure 13A), the addition of cement to the fine particles generated few hydration products. By comparison, the addition of cement and water glass to the fine particles (Group B0) generated more hydration products in the form of clusters in the unfired bricks (Figure 13B), indicating that the addition of sodium silicate facilitated the formation of a silicic acid gel. It can be seen that the addition of water glass increases the hydration rate of cement, resulting in the production of a large amount of poorly crystallized hydrated calcium silicate in the sample in a short period of time (Zhong and Neohiko, 1994; Wang et al., 2023). This phenomenon becomes more apparent as the production of glass increases. And with the rapid consumption of water, there will also be a lot of calcium hydroxide precipitation. So, adding an excessive content of sodium silicate to the preparation mixture caused the fast reaction between the water glass and cement slurry to generate a large number of hard product particles. Breakage of these hard particles during brick preparation deteriorated the strength of the unfired bricks. Thus, the strength of the unfired bricks is optimized by the addition of water glass at an appropriate content but is deteriorated by the addition of excess water glass. Group C0 consisted of the fine particles with added cement, the water glass, and the microsilica powder (Figure 13C), resulting in the generation of many fibrous and tufted silica gels and only a few calcium hydroxide flakes. Thus, incorporating the microsilica powder into the bricks reduced the ratio of calcium ions to silicate ions and facilitated the formation of a strong fibrous silica gel. The cross-linked fibrous gels bridged the coarse particles, enhancing the overall strength of the unfired brick. A fast reaction between the silicate ions and cement readily produced clusters of C–S–H silicate gel particles (Figure 13B). The main hydration products were a large number of uniform, dense, fibrous, and clustered siliceous gel particles (Figure 13C) because of the slow hydration rate of the active microsilica powder and cement. Adding a water reducer to the fine particles (Group D0) generated similar hydration products to those generated in Group C0, albeit with a higher content of the fibrous silicate gel (Figure 13D). This difference may have resulted from the water reducer inhibiting the formation of ettringite and enhancing the release of free water molecules during the early stage of hydration, facilitating the formation of fibrous silicate gel particles during the late stage (Hu et al., 2022a). The strength analysis presented in Section 3 shows that the polycarboxylic water reducer improves the early compressive strength of the unfired bricks and substantially increases the long-term strength. The incorporation of wood fiber enhanced the performance of the unfired bricks because a network structure formed instead of the hydration reaction occurring. Thus, there was no need to analyze the microstructure and mineral composition of the bricks with added wood fiber.
FIGURE 13. Scanning electron microscopy images of the hydration products generated in the unfired bricks in Groups (A) A0, (B) B0, (C) C0, and (D) D0.
This study was performed to evaluate the feasibility of fabricating high-strength and low-cost unfired bricks by using a CDW fine particles, no added natural material, a small quantity of cement, and a compound additive. Experiments were carried out to determine the optimum ratio of the components of the compound additive and the action mechanism of this additive. The compound additive stimulates the activity of volcanic ash, affects water retention, and enhances the performance of the preparation mixture. The strength and compactness of the cement hydration products are thereby enhanced, reducing the required quantity of cementitious material and comprehensively improving the strength, water resistance, and frost resistance of the unfired bricks. The main conclusions of this article are as follows:
1) Sodium silicate can activate the fine particles and cement ash to accelerate cement hydration. However, the addition of more than 1% sodium silicate can result in the generation of flocculation particles that deteriorate the mechanical properties of unfired bricks.
2) The incorporation of microsilica powder into unfired bricks containing water glass promotes the conversion of calcium hydroxide to hydrated calcium silicate, improves the compactness of hydrated calcium silicate, and considerably improves the mechanical properties and water resistance of the bricks.
3) The addition of a water reducer at an appropriate content can improve the workability of the preparation mixture and increase the hydration rate of the binder. However, excessive addition of the water reducer causes water to be released from the preparation mixture during pressing and forming, and this water outflow inhibits hydration.
4) Wood fiber incorporated at an appropriate content into the preparation mixture can interweave with gel products into a network structure, which improves the compressive strength of the brick, inhibits the formation and expansion of cracks, and improves the crack resistance of the brick. However, added wood fiber at contents above 0.1% cannot be dispersed in the preparation mixture, resulting in the formation of a weak surface on the brick body that deteriorates the mechanical properties of the unfired bricks.
5) The optimal ratio of the water glass: microsilica powder: water reducer: wood fiber was 1:2:0.05:0.1, and the optimal content of the compound additive was 3.15% of the dry mass of CDW in the bricks. Compared with the bricks without the compound additive, the unfired bricks with the optimal content of the compound additive exhibited increases in the 1-day and 28-day compressive strengths and a softening coefficient of 66.8%, 65.9%, and 8.46%, respectively (corresponding to values of 8.46 MPa, 29.36 MPa, and 0.934, respectively), and a 61.38% decrease in the freeze–thaw strength loss rate.
6) An environmental impact analysis showed that incorporation of the compound additive can considerably reduce the relative CO2 emissions and embodied energy of the unfired bricks.
The original contributions presented in the study are included in the article/Supplementary material, further inquiries can be directed to the corresponding author.
H-DL: Data curation, Formal Analysis, Funding acquisition, Methodology, Project administration, Resources, Supervision, Visualization, Writing–review and editing. LF: Conceptualization, Data curation, Investigation, Methodology, Writing–original draft.
The author(s) declare financial support was received for the research, authorship, and/or publication of this article. This study was supported by the National Natural Science Foundation of China (No. U1704243); Henan Provincial Science and Technology Research Project (No. 222102320404); Key Scientific Research Project of Higher Education Institutions of the Education Department of Henan Province (No. 22B560018); and Research Project of Zhengzhou University of Science and Technology (No. 23010121006). The sponsors played no role in the study design, collection, analysis, and interpretation of data; writing of the report; and the decision to submit the article for publication.
We thank Michel Scott Long, PhD, and Jacqueline Goveas, PhD, from Liwen Bianji (Edanz) (www.liwenbianji.cn) for editing the English text of a draft of this manuscript.
The authors declare that the research was conducted in the absence of any commercial or financial relationships that could be construed as a potential conflict of interest.
All claims expressed in this article are solely those of the authors and do not necessarily represent those of their affiliated organizations, or those of the publisher, the editors and the reviewers. Any product that may be evaluated in this article, or claim that may be made by its manufacturer, is not guaranteed or endorsed by the publisher.
Aguilar-Penagos, A., Gómez-Soberón, J., and Rojas-Valencia, M. (2017). Physicochemical, mineralogical and microscopic evaluation of sustainable bricks manufactured with construction wastes. Appl. Sci. 7, 1012. doi:10.3390/app7101012
Aslam, M. S., Huang, B., and Cui, L. (2020). Review of construction and demolition waste management in China and USA. J. Environ. Manage 264, 110445. doi:10.1016/j.jenvman.2020.110445
Biao, L., Qinyong, M., and Fa, Z. (2022). Mechanism analysis of the influence of ultrafine slag powder and silica fume on the performance of cement-based grouting materials. Bull. Chin. Ceram. Soc. 41 (12), 11.
Borrachero, M. V., Payá, J., Brito, S., Segura, Y. P., Soriano, L., Tashima, M. M., et al. (2022). Reusing construction and demolition waste to prepare alkali-activated cement. Materials 15, 3437. doi:10.3390/ma15103437
Can Mark, B., and Vincent, O. (2022). Fiber reinforced concrete with natural plant fibers—investigations on the application of bamboo fibers in ultra-high performance concrete. Sustainability. doi:10.3390/su141912011
Chen, W., Xiao-lin, P., Jian-nan, P., Zhong-yang, L., and Hai-yan, Y. (2023). Preparation and characterization of unfired lightweight bricks using dealkalized calcium silicate residue from low-calcium sintering red mud. J. Central South Univ. doi:10.1007/s11771-023-5352-2
Contreras, M., Teixeira, S. R., Lucas, M. C., Lima, L. C. N., Cardoso, D. S. L., da Silva, G. A. C., et al. (2016). Recycling of construction and demolition waste for producing new construction material (Brazil case-study). Constr. Build. Mater. 123, 594–600. Brazil case-study). doi:10.1016/j.conbuildmat.2016.07.044
Damineli, B. L., Kemeid, F. M., Aguiar, P. S., and John, V. M. (2010). Measuring the eco-efficiency of cement use. Cem. Concr. Compos. 32 (8), 555–562. doi:10.1016/j.cemconcomp.2010.07.009
Dove, C. A., Bradley, F. F., and Patwardhan, S. V. (2016). Seaweed biopolymers as additives for unfired clay bricks. Mater. Struct. 49 (11), 4463–4482. doi:10.1617/s11527-016-0801-0
Duan, H., Miller, T. R., Liu, G., and Tam, V. W. Y. (2019). Construction debris becomes growing concern of growing cities. Waste Manag. 83, 1–5. doi:10.1016/j.wasman.2018.10.044
El Fgaier, F., Lafhaj, Z., Chapiseau, C., and Antczak, E. (2016). Effect of sorption capacity on thermo-mechanical properties of unfired clay bricks. J. Build. Eng. 6, 86–92. doi:10.1016/j.jobe.2016.02.011
Fragnoli, P., Boccalon, E., and Liberotti, G. (2023). Designing a ‘yellow brick road’ for the archaeometric analyses of fired and unfired bricks. J. Cult. Herit. 59, 231–246. doi:10.1016/j.culher.2022.12.007
Grist, E. R., Paine, K. A., Heath, A., Norman, J., and Pinder, H. (2015). The environmental credentials of hydraulic lime-pozzolan concretes. J. Clean. Prod. 93, 26–37. doi:10.1016/j.jclepro.2015.01.047
Gupta, V., Chai, H. K., Lu, Y., and Chaudhary, S. (2020). A state of the art review to enhance the industrial scale waste utilization in sustainable unfired bricks. Constr. Build. Mater. 254, 119220. doi:10.1016/j.conbuildmat.2020.119220
Hu, C., Li, C., Yan, B., and Chen, G. (2022a). Effect of water reducing agents on the rheological properties of fine-grained tailings paste. Chin. J. Nonferrous Metals 32 (8), 2458–2468.
Hu, Y., Yang, D., Li, S., Li, H., Zhang, S., Hou, Y., et al. (2022b). Preliminary study on preparation of unfired bricks using filter cake from tunnel muck. J. Build. Eng. 60, 105175. doi:10.1016/j.jobe.2022.105175
Hu, Z., and Hongye, G. (2021). Unfired bricks prepared with red mud and calcium sulfoaluminate cement: properties and environmental impact. J. Build. Eng. 38, 102238. doi:10.1016/j.jobe.2021.102238
Islam, R., Nazifa, T. H., Yuniarto, A., Shanawaz Uddin, A. S. M., Salmiati, S., and Shahid, S. (2019). An empirical study of construction and demolition waste generation and implication of recycling. Waste Manag. 95, 10–21. doi:10.1016/j.wasman.2019.05.049
Jannat, N., Hussien, A., Abdullah, B., and Cotgrave, A. (2020). Application of agro and non-agro waste materials for unfired earth blocks construction: a review. Constr. Build. Mater. 254, 119346. doi:10.1016/j.conbuildmat.2020.119346
Khitab, A., Riaz, M. S., Jalil, A., Khan, R. B. N., Anwar, W., Khan, R. A., et al. (2021). Manufacturing of clayey bricks by synergistic use of waste brick and ceramic powders as partial replacement of clay. Sustainability 13, 10214. doi:10.3390/su131810214
Kurmus, H., and Mohajerani, A. (2020). Leachate analysis of heavy metals in cigarette butts and bricks incorporated with cigarette butts. Materials 13 (12), 2843. doi:10.3390/ma13122843
Lei, T., Tianle, L., Pengliang, S., Yuanhao, W., and Guangyan, L. (2022). Sisal fiber modified construction waste recycled brick as building material: properties, performance and applications. Structures 46, 927–935. doi:10.1016/j.istruc.2022.10.126
Limami, H., Manssouri, I., Cherkaoui, K., and Khaldoun, A. (2021). Mechanical and physicochemical performances of reinforced unfired clay bricks with recycled Typha-fibers waste as a construction material additive. Clean. Eng. Technol. 2, 100037. doi:10.1016/j.clet.2020.100037
Limami, H., Manssouri, I., Cherkaoui, K., Saadaoui, M., and Khaldoun, A. (2020). Thermal performance of unfired lightweight clay bricks with HDPE & PET waste plastics additives. J. Build. Eng. 30, 101251. doi:10.1016/j.jobe.2020.101251
Liu, J., Chen, Y., and Wang, X. (2022). Factors driving waste sorting in construction projects in China. J. Clean. Prod. 336, 130397. doi:10.1016/j.jclepro.2022.130397
Menegaki, M., and Damigos, D. (2018). A review on current situation and challenges of construction and demolition waste management. Curr. Opin. Green Sustain. Chem. 13, 8–15. doi:10.1016/j.cogsc.2018.02.010
Mi, R., Liew, K. M., and Pan, G. (2022). New insights into diffusion and reaction of CO2 gas in recycled aggregate concrete. Cem. Concr. Compos. 129, 104486. doi:10.1016/j.cemconcomp.2022.104486
Mojapelo, L., and Nkosinomusa Nomfundo, B.-D. (2022). Impact of topsoil mining for unfired mudbricks on soil quality in eastern KwaZulu-Natal, South Africa. Land Degrad. Dev. 34, 1051–1066. doi:10.1002/ldr.4515
Muheise-Araalia, D., and Pavia, S. (2021). Properties of unfired, illitic-clay bricks for sustainable construction. Constr. Build. Mater. 268, 121118. doi:10.1016/j.conbuildmat.2020.121118
Othmane, N., Imad, M., Hassane, S., Houssame, L., and Asmae, K. (2023). Rheological and physico-mechanical investigations on the destabilization of unfired clay bricks with almond husk additive by salt. Constr. Build. Mater. 375, 130971. doi:10.1016/j.conbuildmat.2023.130971
Oti, J. E., Kinuthia, J. M., and Robinson, R. B. (2014). The development of unfired clay building material using Brick Dust Waste and Mercia mudstone clay. Appl. Clay Sci. 102 (dec), 148–154. doi:10.1016/j.clay.2014.09.031
Pallewatta, S., Weerasooriyagedara, M., Bordoloi, S., Sarmah, A. K., and Vithanage, M. (2023). Reprocessed construction and demolition waste as an adsorbent: an appraisal. Sci. Total Environ. 882, 163340. doi:10.1016/j.scitotenv.2023.163340
Raut, S., Ralegaonkar, R., and Mandavgane, S. (2013). Utilization of recycle paper mill residue and rice husk ash in production of light weight bricks. Archives Civ. Mech. Eng. 13 (2), 269–275. doi:10.1016/j.acme.2012.12.006
Raza, A., Hechmi El Ouni, M., Ali, L., Awais, M., Ali, B., Ahmad, Z., et al. (2022). Structural evaluation of recycled aggregate concrete circular columns having FRP rebars and synthetic fibers. Eng. Struct. 250, 113392. doi:10.1016/j.engstruct.2021.113392
Riyap, H. I., Banenzoué, C., Tchakouté, H. K., Nanseu, C. N. P., and Rüscher, C. H. (2020). A comparative study of the compressive strengths and microstructural properties of geopolymer cements from metakaolin and waste fired brick as aluminosilicate sources. J. Korean Ceram. Soc. 58, 236–247. doi:10.1007/s43207-020-00097-y
Robayo-Salazar, R. A., Rivera, J. F., and Mejía de Gutiérrez, R. (2017). Alkali-activated building materials made with recycled construction and demolition wastes. Constr. Build. Mater. 149, 130–138. doi:10.1016/j.conbuildmat.2017.05.122
Sanqiang, Y., Zhenyu, Y., and Jie, L. (2022). Study on the construction waste composition and strength mechanism of recycled mixture. Adv. Mater. Sci. Eng. 2022, 1–13. doi:10.1155/2022/6898455
Seco, A., Omer, J., Marcelino, S., Espuelas, S., and Prieto, E. (2018). Sustainable unfired bricks manufacturing from construction and demolition wastes. Constr. Build. Mater. 167, 154–165. doi:10.1016/j.conbuildmat.2018.02.026
Sharma, T., Singh, S., Sharma, S., Sharma, P., Gehlot, A., Shukla, A. K., et al. (2022). The use of marble dust, bagasse ash, and paddy straw to improve the water absorption and linear shrinkage of unfired soil block for structure applications. Materials 15 (21), 7786. doi:10.3390/ma15217786
Shi, P. Y., Zhang, Y., and Chen, Z. (2020). Study on the properties of non-calcination brick with different silt content in alkali-activated fly ash-slag system. New Build. Mater. 47 (9), 40–44.
Tao, G., Pan, Y., Qiao, Z., and Jiang, C. (2018). Utilization of sandy soil as the primary raw material in production of unfired bricks. Adv. Mater. Sci. Eng. 2018, 1–11. doi:10.1155/2018/7320298
Villaquirán-Caicedo, M. A., and Mejía de Gutiérrez, R. (2021). Comparison of different activators for alkaline activation of construction and demolition wastes. Constr. Build. Mater. 281, 122599. doi:10.1016/j.conbuildmat.2021.122599
Wang, Y., Chen, P., Zhang, L., Tan, W., and Fang, J. (2023). Effect of MgO/sodium silicate composite on the hydration and mechanical properties of alkali slag. J. Build. Mater. 26 (2), 186–192.
Wu, G., Wang, L., Yang, R., Hou, W., Zhang, S., Guo, X., et al. (2022). Pollution characteristics and risk assessment of heavy metals in the soil of a construction waste landfill site. Ecol. Inf. 70, 101700. doi:10.1016/j.ecoinf.2022.101700
Xu, Y., Jiang, L., Xu, J., and Li, Y. (2012). Mechanical properties of expanded polystyrene lightweight aggregate concrete and brick. Constr. Build. Mater. 27 (1), 32–38. doi:10.1016/j.conbuildmat.2011.08.030
Yu, Y. F., Zhang, K., Ying, X., and Zhu, Z. (2021). Experimental study on preparation of baking-free bricks from river silt. New Build. Mater. 48 (02), 150–153.
Zhang, K., Xiao, J., Hou, Y., and Zhang, Q. (2022). Experimental study on carbonation behavior of seawater sea sand recycled aggregate concrete. Adv. Struct. Eng. 25 (5), 927–938. doi:10.1177/13694332211026221
Zhao, H., and Gou, H. (2021). Unfired bricks prepared with red mud and calcium sulfoaluminate cement: properties and environmental impact. J. Build. Eng. 38, 102238. doi:10.1016/j.jobe.2021.102238
Zhong, B., and Neohiko, O. (1994). The effect of water glass on the hydration of portland cement. J. Build. Mater. 7 (2), 7.
Keywords: construction waste, demolition waste, unfired bricks, compound additive, environmental impact
Citation: Liu H-D and Fan L (2024) Optimization and mechanism analysis of a compound additive for unfired bricks made of construction and demolition wastes. Front. Mater. 11:1308884. doi: 10.3389/fmats.2024.1308884
Received: 07 October 2023; Accepted: 07 February 2024;
Published: 22 February 2024.
Edited by:
Muhammad Junaid Munir, RMIT University, AustraliaReviewed by:
Soon Poh Yap, University of Malaya, MalaysiaCopyright © 2024 Liu and Fan. This is an open-access article distributed under the terms of the Creative Commons Attribution License (CC BY). The use, distribution or reproduction in other forums is permitted, provided the original author(s) and the copyright owner(s) are credited and that the original publication in this journal is cited, in accordance with accepted academic practice. No use, distribution or reproduction is permitted which does not comply with these terms.
*Correspondence: Liujun Fan, bGl1anVuZmFuQHppdC5lZHUuY24=
Disclaimer: All claims expressed in this article are solely those of the authors and do not necessarily represent those of their affiliated organizations, or those of the publisher, the editors and the reviewers. Any product that may be evaluated in this article or claim that may be made by its manufacturer is not guaranteed or endorsed by the publisher.
Research integrity at Frontiers
Learn more about the work of our research integrity team to safeguard the quality of each article we publish.