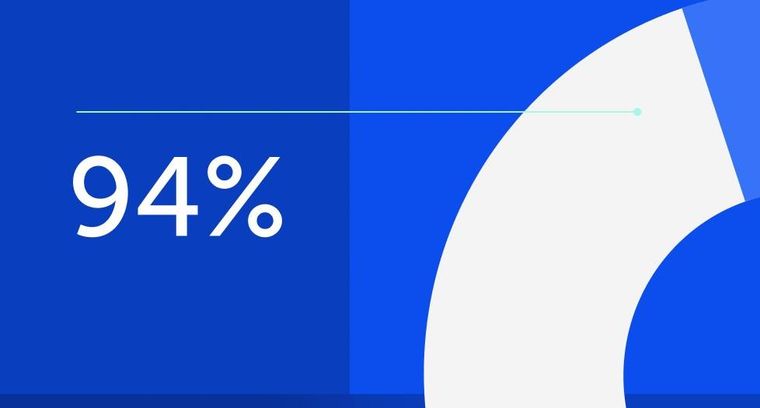
94% of researchers rate our articles as excellent or good
Learn more about the work of our research integrity team to safeguard the quality of each article we publish.
Find out more
ORIGINAL RESEARCH article
Front. Mater., 14 December 2023
Sec. Mechanics of Materials
Volume 10 - 2023 | https://doi.org/10.3389/fmats.2023.1330354
This article is part of the Research TopicResponse and Catastrophe Mechanisms of Geotechnical Underground Exploration: Theories and Numerical ModelingView all 14 articles
Deep-hole bench blasting is the primary method for aggregate extraction in mines. However, factors such as complex geological conditions and suboptimal blasting parameters often result in uneven rock fragmentation and high fines content. This not only increases the cost and energy consumption of subsequent aggregate processing but also has adverse environmental implications. In this study, based on the Changjiu Shenshan limestone aggregate mining project in China, large-scale blasting experiments were conducted to investigate the influence of rock properties and blasting parameters on the size distribution of post-blast fragments and fines content. The results of the blasting experiments indicate that by controlling the size of the crushing zone and adjusting explosive performance, it is possible to significantly reduce fines content while improving mining efficiency. Recommended values for drilling and blasting parameters have been proposed based on geological conditions to more effectively control the generation of fines. The results highlight the importance of optimizing blasting parameters and charge structure for large-scale mining operations to achieve uniform rock fragmentation and low fines content. By adopting explosive performance adjustment methods based on reasonable control of the crushing zone, improving explosive performance can improve the economic benefits of mining operations, reduce energy consumption, and contribute to environmental protection.
Deep-hole bench blasting is currently the primary method for aggregate extraction in mines. However, during the process of aggregate extraction, issues such as uneven rock fragmentation and high fines content often arise due to the complex geological conditions and suboptimal blasting process parameters (Roy et al., 2016). The elevated fines content not only increases the energy consumption and costs for subsequent processing of the aggregate but also results in significant ore wastage, which is detrimental to environmental preservation (Bhandari, 2012). Consequently, improving the distribution of rock fragmentation and controlling fines content has become a pressing concern in the field of mining aggregate extraction.
In recent decades, numerous scholars have conducted extensive research on the causes, influencing factors, and control measures of fines generation during mining blasting processes (Esen et al., 2003; Onederra et al., 2004; Park and Kim, 2020). From a mechanistic perspective, the generation of fines is inevitable. This is because the peak pressure of the shockwave produced by explosives after detonation far exceeds the compressive strength of the rock, leading to extreme fragmentation of the surrounding rock and the formation of fines. Although fines generation is an unavoidable consequence, it can be minimized to a significant extent by optimizing blasting parameters and process control, thus achieving the goals of uniform rock fragmentation and low fines content. To achieve this objective, researchers have explored the effects of blasting parameters on blast fragmentation size distribution through experimental and simulation studies. For instance, Yi et al. (2017) utilized the finite element software LS-DYNA to investigate the influence of delay time and initiation location on blast fragmentation, with results indicating that longer delay times contribute to improved rock fragmentation. Liu et al. (2015) studied the distribution characteristics of blast energy for different initiation locations, revealing that central initiation is favorable for reducing the occurrence of large boulders. Chi et al. (2022) investigated the effects of decoupling coefficients, free faces, and boundary conditions on blast fragmentation distribution through small-scale blasting experiments on rock cylinders. Zhang et al. (2021) examined the impact of stemming conditions on rock fragmentation results, suggesting that complete stemming leads to superior fragmentation compared to partial stemming. Singh et al. (2016), in the context of an Indian coal mine, studied the influence of 91 sets of different blasting design parameters and charge structures on rock fragmentation. Their findings indicated that rock fragmentation size increases with an increasing burden, decreases with a lower stemming-to-burden ratio, and shows an inverse relationship with hole spacing ratio. A moderate increase in specific explosive consumption can reduce rock fragmentation size. Leng et al. (2020) concluded that reducing the burden and increasing the spacing between blast holes enhance the tensile action of the stress wave within the rock mass, leading to the propagation of inherent cracks until they intersect with the free face, thus achieving a more uniform distribution of rock fragmentation and improved blasting performance.
The aforementioned studies indicate that, when designing blasting schemes, achieving the desired fragmentation size distribution can be attained by selecting appropriate blasting parameters, thereby reducing fines content. For instance, the adjustment of explosive quantity, spacing to burden ratio, and stemming column length can influence the degree of rock fragmentation and the size distribution of fragments. Alternatively, optimizing the charge structure and initiation sequence, as well as modifying the propagation path and energy release of the shockwave, can be used to control the fragmentation size distribution. It is essential to note that controlling fragmentation size distribution is a complex issue influenced by multiple factors. Factors such as the physical properties of rocks and geological structures can all impact fragmentation size distribution (Tao et al., 2020; Azizi and Moomivand, 2021; Njock et al., 2021; Sanchidrián et al., 2022). Therefore, in practical applications, it is essential to consider these factors comprehensively and determine the optimal blasting parameters and construction measures through experimental research to achieve effective control over the fragmentation size distribution and fines content.
Although there is a relative abundance of research on the fragmentation size distribution in blasting, it has predominantly focused on numerical simulations and small-scale field experiments. However, in large-scale mining operations, the control of blast-induced fragmentation size distribution and fines content holds significant importance for economic efficiency and environmental preservation. Therefore, for mining aggregate production, it is imperative to propose large-scale, applicable, and feasible control measures from various perspectives, such as explosive performance and construction measures, based on geological and lithological conditions. This research, based on the Changjiu Shenshan limestone aggregate mining project in China, conducted four sets of blasting experiments in two different lithological zones. It investigated the factors affecting the fragmentation size distribution and fines content of artificial aggregate mining, unveiled the mechanism of fines generation in limestone mines, and proposed methods for adjusting explosive performance based on rational control of the crushing zone to control fines content.
The Changjiu Shenshan Limestone Mine is located in Chizhou City, Anhui Province, and is currently the largest limestone mine in China. The mine utilizes open-pit blasting for excavation, with an annual production capacity of up to 70 million tons. The mining operation is designed to produce ore with a block size not exceeding 1,000 mm. The mining site represents an isolated ore body with significant relative elevation differences, typically featuring slope angles ranging from 15° to 34°. The predominant rock type in the mining area is limestone, with minor interbedded shale. Structural features are limited, although localized karst phenomena are well-developed. The rock mass exhibits good integrity, with a Platts coefficient of 8–12, a density of 2.68 g/cm3, and compressive strength values ranging from 36.3 to 93.4 MPa, with an average of 64.9 MPa. With the exception of the Permian Longtan Formation shales, the stability of the rock mass is generally favorable. The geological structure in the mining area is complex, characterized by the presence of prominent folds and faults. Folding predominantly forms anticlines, while the dominant faults include northwesterly-oriented (F1, F2, F3) faults, followed by nearly east-westerly-oriented (F4, F5) faults. These faults can influence the integrity and stability of the slope. Localized deep-seated karst features are observed in the mining area, primarily characterized by small caves, though a few large caverns are present as well. In sections with developed karst features, the load-bearing capacity of the rock layers may decrease, potentially leading to the collapse or detachment of overlying rock layers.
Based on the development of rock joints, the Changjiu Shenshan limestone mine is divided into two mining areas: 1# and 2#. In the 1# mining area, the dominant rock type comprises thin-bedded limestone, with some areas containing extremely thin-bedded limestone layers, influenced significantly by geological structures. On the other hand, the 2# mining area consists mainly of thin-bedded limestone, with some areas featuring medium-thickness limestone layers. It experiences less influence from geological structures, and the rock type is relatively intact. The typical rock mass structures in the field are illustrated in Figure 1.
Considering the geological conditions and rock characteristics of the Changjiu Shenshan limestone mining area, a total of four sets of blasting tests were conducted in the 1# and 2# mining areas. Specifically, three sets of blasting tests were carried out in the 1# mining area, while one set of blasting test was conducted in the 2# mining area. The location of each test set is illustrated in Figure 2.
The distribution of rock fragmentation and fines content in blasting is significantly influenced by geological conditions and blasting parameters. In order to investigate the effects of rock properties and blasting parameters, including hole spacing, burden, explosive quantity, and stemming length, on the post-blasting fragmentation and fines content of ore, a series of blasting experiments were conducted. For these experiments, we utilized on-site mixed porous prilled ammonium nitrate explosive with a density of 850 kg/m3 and a detonation velocity of 2,900 m/s. In each test, we arranged a total of 12 blastholes in three rows on the bench near the free face. The blasthole layout followed a pattern resembling a “plum blossom,” with hole angles not less than 85°. As depicted in Figure 3, every test consisted of two comparative test areas, resulting in a total of four sets of tests encompassing eight different blasting scenarios. The specific blasting parameters are shown in Table 1. It is noteworthy that in the fourth set of tests, we introduced a 1.0-m air deck segment below the 3.2-m stemming column, whereas conventional stemming methods were employed in the other tests.
In bench blasting, the distribution of fragmentation plays a crucial role in assessing the efficiency of explosive energy utilization, optimizing blasting parameters, and controlling the fines content. Typical fragmentation distributions after blasting are presented in Figure 4. The evaluation of fragmentation distributions in blasting experiments is performed using on-site sieving techniques. Specifically, following each blasting test, samples are collected from six locations: the upper, middle, and lower parts in front of the blastholes and the upper, middle, and lower parts between two adjacent blastholes on the same row. During sampling, the surface layer of blast debris, typically 2–3 m thick, is removed to access the interior rock samples. The collected raw materials are subjected to initial sieving using a mobile screening machine on a flat surface to obtain coarse stones (>120 mm), medium stones (60–120 mm), and small stones (<60 mm), as illustrated in Figure 5. Subsequently, a portion of the medium and small stone samples is further refined through laboratory sieving, enabling the determination of the overall fragmentation distribution and fines content of the raw materials.
FIGURE 4. Typical blast fragmentation size distribution diagram from the blasting experiments (A) Blasting condition 1#, (B) Blasting condition 2#, (C) Blasting condition 3#, (D) Blasting condition 4#, (E) Blasting condition 5#, (F) Blasting condition 6#, (G) Blasting condition 7#, (H) Blasting condition 8#.
FIGURE 5. Blasting fragmentation sieving test (A) Preliminary screening of limestone, (B) Fine screening of limestone.
Based on the on-site sieving experiments, fragmentation distribution curves are obtained after each blasting test, as shown in Figure 6. From the graph, it can be observed that in the same area and for the same group of tests, curves with higher specific explosive consumption are positioned higher, indicating that with the same block size conditions, a higher specific explosive consumption results in a lower distribution of large rock fragments in the muckpile. Therefore, during the blasting process, reducing the specific explosive consumption in the blast design can increase the proportion of large rock fragments in the muckpile. Furthermore, Figure 6 also illustrates that as the burden-to-spacing ratio decreases and specific consumption increases, the gradation curves of the tests become steeper. This suggests that reducing the burden-to-spacing ratio contributes to increased rock fragmentation during the blasting process, making the size distribution of rock fragments in the muckpile more uniform.
Based on previous research (Bohloli, 1997) and the sieving results after each experiment, a threshold of 4.75 mm diameter was used, considering rock fragments with a diameter less than 4.75 mm as fine materials. Figure 7 presents the rock powder content for each blasting test. Given that geological conditions vary between each blasting test, two tests were selected for comparison within the same group. For example, in the case of blasting tests 5# and 6#, with the burden-to-spacing ratio held constant, test 6# exhibited a slightly higher rock powder content than test 5#, with an increase of approximately 10%. This suggests that higher specific explosive consumption leads to increased rock powder content. Comparing tests 1# and 5#, with other parameters held constant, as borehole depth increased, the post-blast powder content significantly increased from 0.69% to 3.19%. This indicates that the post-blast rock powder content is significantly affected by the amount of explosives per borehole. In comparison to the second group and the fourth group of blasting tests, although tests 3# and 7# had higher specific explosive consumption compared to tests 4# and 8#, the former exhibited more uniform gradation of muckpile materials with fewer large chunks and fine particles, resulting in a notable reduction in rock powder content. Comparing tests 5# and 8#, for the same borehole spacing, air-decked blasting resulted in significantly lower rock powder content, approximately 40% less than the coupled-charging method. The field test results demonstrate that in engineering applications, it is possible to effectively control rock powder content by appropriately reducing the specific consumption, employing a wider borehole spacing with a shorter burden-to-spacing ratio, and utilizing air-decked charging structures.
When explosives interact with rock mass, transmission and reflection will occur at the interface due to different wave impedances. The selection of an appropriate explosive type based on rock properties significantly influences the effective control of the crushing zone and the optimal utilization of explosive energy. Assuming the wave impedances of the explosive and the rock are
where,
However, in practical blasting operations, explosives typically have a density ranging from 0.8 to 1.3 g/cm3 and detonation velocities between 2,000 and 5,000 m/s. Rocks generally have densities ranging from 2.3 to 2.8 g/cm3, and longitudinal wave velocities typically fall within the range of 2,500–5,500 m/s. It is evident that achieving equal wave impedance between explosives and rocks is quite challenging under normal circumstances, with the wave impedance of explosives often being around 50% of that of rocks.
Observations in the field and laboratory experiments have demonstrated the presence of a crushing zone around blast holes (Esen et al., 2003; Yilmaz and Unlu, 2013; Liu et al., 2022; Pan et al., 2022). The formation of the crushing zone consumes a significant amount of energy, hindering the further diffusion of explosive gases into cracks and affecting the “gas wedge” effect. Additionally, particles with a high surface area within the crushing zone absorb a substantial amount of thermal energy generated by the explosion, reducing the effective utilization of explosive energy. According to the principle of energy conservation, the energy Ec expended on the crushing zone can be divided into fracture surface energy
According to Leng et al. (2014), the quantities
where,
Then the energy consumed in the crushing zone can be calculated using Eq. 5:
In Eq. 5, it can be observed that reducing the size of the crushing zone decreases the energy expended for breaking the rock near the blast hole, thereby optimizing the distribution of explosive energy. According to relevant engineering experience, the energy consumed in the crushing zone should not exceed 5% of the total energy. Otherwise, excessive energy consumption in the crushing zone will inevitably reduce the energy available for fracturing rock outside the crushing zone, thereby affecting the fragmentation efficiency. Therefore, the rock-explosive energy matching method based on the reasonable control of the crushing zone can both achieve efficient fragmentation and control the fines content effectively.
Based on the analysis in Section 4.1, it can be concluded that the size of the crushing zone impacts the efficiency of energy utilization. If the crushing zone is too large, it will consume a significant amount of explosive energy, which is not conducive to fracturing the rock mass outside the crushing zone. Additionally, the fracturing characteristics of the rock within the crushing zone determine whether it can serve as a primary source of fine particles. Therefore, it is necessary to comprehensively consider engineering requirements and actual geological conditions to determine the reasonable distribution range of the crushing zone. Taking into account that the rock is hard limestone in the Changjiu Shenshan project, it is essential to minimize the production of rock fines in the engineering blasting. Thus, the primary goal in this project is to control the size of the crushing zone to ensure that the fracturing area meets the requirements for rock crushing. Specifically, the following conditions need to be met: a. It is essential to ensure that the size of the crushing zone is appropriate, which means
The upper limit of the crushing zone range ζ1 is determined by Eq. 5:
In the Eq. 6, the value of rock-specific surface energy Gf is determined by the rock’s elastic modulus and dynamic fracture toughness. It is calculated using Eq. 7:
where, KID is the dynamic fracture toughness of rock, Pa·m1/2; E is the elastic modulus of rock mass, Pa. The dynamic fracture toughness of the rock, KID, is typically calculated based on its static fracture toughness, KIC, and an amplification factor λ. In this work, the amplification factor λ is taken as 1.5. The relationship between static fracture toughness, KIC, and the rock’s compressive strength,
Table 2 lists the unit surface energy Gf of rocks under different conditions, and further the upper limit of the crushing zone range
The upper limit of the crushing zone range determined by the fine particle size material content requirements
where, KS represents the ratio of blasthole spacing to the burden, typically ranging from 1.2 to 1.5. For this specific engineering project, a value of 1.5 has been adopted based on the actual drilling and blasting parameters. KB denotes the ratio of the burden to blasthole diameter, usually falling within the range of 25–35. ηC represents the contribution rate of fine particles generated in the crushing zone to the total amount of fine particles, which depends on the rock type and blastability and is generally around 10%. ηB signifies the percentage of fine particles with a particle size smaller than
By comparing Table 2 and Table 3, it can be observed that the energy-based crushing zone limit
From the analysis in Section 4.2, it can be seen that based on the existing on-site drilling and blasting parameters, combined with the requirements for pulverization rate control in the project, a reasonable distribution range of the crushing zone can be determined. In addition to altering drilling and blasting parameters to control the blasting effect on-site, adjusting explosive performance using the explosive self-loading vehicle can also achieve control crushing rates. The key parameters that signify explosive performance are explosive density and detonation velocity. These two factors directly determine the peak value of the blasting load. Previous studies (Esen et al., 2003; Far and Wang, 2016) have shown that the intensity of the blast load directly affects the size of the crushing zone. Consequently, the adjustment of explosive performance parameters provides a means to control the range of the crushing zone.
In engineering practice, the performance of explosives is enhanced mainly by adjusting the proportion of explosive components, increasing the density of explosives, and increasing the detonation velocity of explosives. Extensive experiments have shown that within a certain range, detonation velocity is linearly related to explosive density. Here, D represents the actual detonation velocity at an in-situ explosive loading density of
where, M is a coefficient related to explosive performance, representing the increase in detonation velocity for every 1.0 g/cm3 increase in loading density. M can be determined through experimental measurements, and its typical value ranges from 3,000 to 4,300 (m∙s⁻1)/(g∙cm⁻3). For this study, we use a value of 3,000 (m∙s⁻1)/(g∙cm⁻3).
Based on the recommended values for the controlled range of the crushing zone under different geological conditions in the project, controlling the crushing zone within the suggested range can theoretically achieve control over the fines content by adjusting the explosive performance. To achieve this objective, the calculation of the destructive range of the crushing zone under different explosive performances was conducted using Eqs 6–10. Subsequently, recommended values for the drilling and blasting parameters and explosive matching parameters suitable for this project’s geological conditions were proposed, and these values are listed in Table 4.
The calculations from Table 4 demonstrate that the explosive parameters for rock matching vary based on different geological conditions and fines content control requirements. For the ore zone with rock fragmentation, the corresponding explosive detonation velocity is 2,890 m/s when controlling for a 1% fines content. When controlling for a 2% fines content, the corresponding explosive detonation velocity is 2,970 m/s, and for controlling a 3% fines content, the corresponding explosive detonation velocity is 3,120 m/s. Therefore, if the properties of the rock remain consistent, we can optimize the spacing between blast holes and utilize higher-performance explosives with larger spacing parameters, all while maintaining control over fines generation rates. This approach can enhance mining efficiency.
This study conducted a large-scale blasting experiment at the Changjiu Shenshan limestone mine in China to deeply explore the impact of geological conditions and blasting parameters on the control of fragment size distribution and fine particle content in aggregate mining, and the following main conclusions were drawn:
(1) The blasting experiments conducted in the limestone mine demonstrate that reducing the specific consumption of explosives can effectively decrease the production of fines. Simultaneously, adopting a blasting method with wider hole spacing and smaller burden contributes to a more uniform distribution of fragment sizes, playing a noticeable role in controlling the generation of fines.
(2) Effective reduction of fines content in aggregate extraction can be achieved by appropriately controlling the size of the crushing zone and adjusting explosive performance. Following the principles of rational crushing zone control, performance parameters for explosives matching the geological conditions and various fines requirements are calculated. The use of explosives with suitable characteristics allows for control over the fines content in the rock.
(3) The explosive performance adjustment method based on reasonable control of the crushing zone can provide practical operation guidance for large-scale mining of aggregates. By controlling the size distribution of fragments and the content of fine particles, economic benefits can be improved, resource waste reduced, and environmental protection requirements met.
The original contributions presented in the study are included in the article/Supplementary Material, further inquiries can be directed to the corresponding author.
PG: Resources, Writing–original draft. CP: Funding acquisition, Writing–review and editing. QZ: Supervision, Writing–review and editing. CD: Funding acquisition, Writing–review and editing.
The author(s) declare financial support was received for the research, authorship, and/or publication of this article. This work was financially supported by the Scientific Research Foundation for High-level Talents of Anhui University of Science and Technology (No. 2022yjrc80), the National Natural Science Foundation of China (No. 52074006), Natural Science Research Project of Anhui Educational Committee (No. 2023AH051227).
The authors declare that the research was conducted in the absence of any commercial or financial relationships that could be construed as a potential conflict of interest.
All claims expressed in this article are solely those of the authors and do not necessarily represent those of their affiliated organizations, or those of the publisher, the editors and the reviewers. Any product that may be evaluated in this article, or claim that may be made by its manufacturer, is not guaranteed or endorsed by the publisher.
Azizi, A., and Moomivand, H. (2021). A new approach to represent impact of discontinuity spacing and rock mass description on the median fragment size of blasted rocks using image analysis of rock mass. Rock Mech. Rock Eng. 54, 2013–2038. doi:10.1007/s00603-020-02360-4
Bhandari, S. (2012). “Fines and dust generation and control in rock fragmentation by blasting,” in 10th international symposium on rock fragmentation by blasting (Boca Raton, FL: CRC Press), 511–520.
Bohloli, B. (1997). Effects of the geological parameters on rock blasting using the Hopkinson split bar. Int. J. Rock Mech. Min. Sci. 34 (3-4), 32.e1–32.e9. doi:10.1016/S1365-1609(97)00228-1
Chi, L. Y., Wang, C., Zhang, Z. X., Xu, X., and Yang, J. (2022). Experimental investigation of decoupled charge effect on rock fragmentation by blasting. Rock Mech. Rock Eng. 55, 3791–3806. doi:10.1007/s00603-022-02823-w
Esen, S., Onederra, I., and Bilgin, H. A. (2003). Modelling the size of the crushed zone around a blasthole. Int. J. Rock Mech. Min. Sci. 40 (4), 485–495. doi:10.1016/S1365-1609(03)00018-2
Far, M. S., and Wang, Y. (2016). Probabilistic analysis of crushed zone for rock blasting. Comput. Geotech. 80, 290–300. doi:10.1016/j.compgeo.2016.08.025
Leng, Z., Fan, Y., Gao, Q., and Hu, Y. (2020). Evaluation and optimization of blasting approaches to reducing oversize boulders and toes in open-pit mine. Int. J. Min. Sci. Technol. 30 (3), 373–380. doi:10.1016/j.ijmst.2020.03.010
Leng, Z., Lu, W., Yan, P., Chen, M., and Hu, Y. (2014). A new method of rock-explosive matching in drilling and blasting based on reasonable control of the crushed zone. Strategic Study CAE 16 (11), 28–35+47.
Li, J. T., Gu, D. S., Cao, P., and Wu, C. (2009). Interrelated law between mode-I fracture toughness and compression strength of rock. J. Cent. South Univ. Sci. Technol. 40 (6), 1695–1699.
Liu, D., Lu, W., Yang, J., Gao, J., Yan, P., Hu, S., et al. (2022). Relationship between cracked-zone radius and dominant frequency of vibration in tunnel blasting. Int. J. Rock Mech. Min. Sci. 160, 105249. doi:10.1016/j.ijrmms.2022.105249
Liu, L., Chen, M., Lu, W., Hu, Y., and Leng, Z. (2015). Effect of the location of the detonation initiation point for bench blasting. Shock Vib. 2015, 1–11. doi:10.1155/2015/907310
Miao, Y., Zhang, Y., Wu, D., Li, K., Yan, X., and Lin, J. (2021). Rock fragmentation size distribution prediction and blasting parameter optimization based on the muck-pile model. Min. Metallurgy Explor. 38, 1071–1080. doi:10.1007/s42461-021-00384-0
Njock, M. C., Meli’i, J. L., Poufonne, Y. K., Mbouombouo, I. N., Well, T. H. L., Arétouyap, Z., et al. (2021). Influence of natural discontinuities and mechanical properties on the fragmentation of marble by blasting in Central Africa. Environ. Earth Sci. 80, 616. doi:10.1007/s12665-021-09916-9
Onederra, I., Esen, S., and Jankovic, A. (2004). Estimation of fines generated by blasting–applications for the mining and quarrying industries. Min. Technol. 113 (4), 237–247. doi:10.1179/037178404225006191
Ouchterlony, F., Nyberg, U., Olsson, M., Bergqvist, I., Granlund, L., and Grind, H. (2004). Where does the explosive energy in rock blasting rounds go? Sci. Technol. Energ Mater 65 (2), 54–63.
Pan, C., Xie, L. X., Li, X., Liu, K., Gao, P. F., and Tian, L. G. (2022). Numerical investigation of effect of eccentric decoupled charge structure on blasting-induced rock damage. J. Cent. South Univ. 29 (2), 663–679. doi:10.1007/s11771-022-4947-3
Park, J., and Kim, K. (2020). Estimation of fines generation in blasting using dynamic rock properties and a near-field PPV damage model. Min. Metallurgy Explor. 37 (4), 1169–1183. doi:10.1007/s42461-020-00245-2
Roy, M. P., Paswan, R. K., Sarim, M. D., Kumar, S., Jha, R., and Singh, P. K. (2016). Rock fragmentation by blasting-A review. J. Mines Met. Fuels 64 (9), 424–431.
Sanchidrián, J. A., Segarra, P., and López, L. M. (2007). Energy components in rock blasting. Int. J. Rock Mech. Min. Sci. 44 (1), 130–147. doi:10.1016/j.ijrmms.2006.05.002
Sanchidrián, J. A., Segarra, P., Ouchterlony, F., and Gómez, S. (2022). The influential role of powder factor vs. delay in full-scale blasting: a perspective through the fragment size-energy fan. Rock Mech. Rock Eng. 55, 4209–4236. doi:10.1007/s00603-022-02856-1
Singh, P. K., Roy, M. P., Paswan, R. K., Sarim, M. D., Kumar, S., and Jha, R. R. (2016). Rock fragmentation control in opencast blasting. J. Rock Mech. Geotech. Eng. 8 (2), 225–237. doi:10.1016/j.jrmge.2015.10.005
Tao, J., Yang, X. G., Li, H. T., Zhou, J. W., Qi, S. C., and Lu, G. D. (2020). Numerical investigation of blast-induced rock fragmentation. Comput. Geotech. 128, 103846. doi:10.1016/j.compgeo.2020.103846
Yi, C., Sjöberg, J., Johansson, D., and Petropoulos, N. (2017). A numerical study of the impact of short delays on rock fragmentation. Int. J. Rock Mech. Min. Sci. 100, 250–254. doi:10.1016/j.ijrmms.2017.10.026
Yilmaz, O., and Unlu, T. (2013). Three dimensional numerical rock damage analysis under blasting load. Tunn. Undergr. Space Technol. 38, 266–278. doi:10.1016/j.tust.2013.07.007
Keywords: deep-hole bench blasting, aggregate extraction, fragmentation size distribution, fines content, explosive performance
Citation: Gao P, Pan C, Zong Q and Dong C (2023) Rock fragmentation size distribution control in blasting: a case study of blasting mining in Changjiu Shenshan limestone mine. Front. Mater. 10:1330354. doi: 10.3389/fmats.2023.1330354
Received: 30 October 2023; Accepted: 30 November 2023;
Published: 14 December 2023.
Edited by:
Yongqiang Zhou, Chinese Academy of Sciences (CAS), ChinaCopyright © 2023 Gao, Pan, Zong and Dong. This is an open-access article distributed under the terms of the Creative Commons Attribution License (CC BY). The use, distribution or reproduction in other forums is permitted, provided the original author(s) and the copyright owner(s) are credited and that the original publication in this journal is cited, in accordance with accepted academic practice. No use, distribution or reproduction is permitted which does not comply with these terms.
*Correspondence: Cheng Pan, Y3BhbjE5ODlAMTYzLmNvbQ==
Disclaimer: All claims expressed in this article are solely those of the authors and do not necessarily represent those of their affiliated organizations, or those of the publisher, the editors and the reviewers. Any product that may be evaluated in this article or claim that may be made by its manufacturer is not guaranteed or endorsed by the publisher.
Research integrity at Frontiers
Learn more about the work of our research integrity team to safeguard the quality of each article we publish.