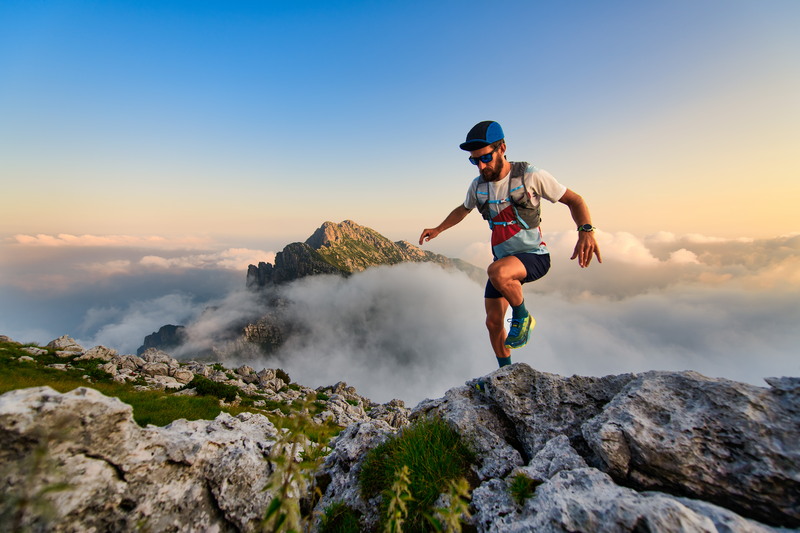
95% of researchers rate our articles as excellent or good
Learn more about the work of our research integrity team to safeguard the quality of each article we publish.
Find out more
EDITORIAL article
Front. Mater. , 29 September 2023
Sec. Mechanics of Materials
Volume 10 - 2023 | https://doi.org/10.3389/fmats.2023.1292283
This article is part of the Research Topic Design and Mechanical Failure of Deep-Sea Pressure Structures View all 6 articles
Editorial on the Research Topic
Design and mechanical failure of deep-sea pressure structures
Deep-sea pressure structures, including submersibles, deep-sea space stations and delivery platforms, underwater gliders, subsea pipelines, ocean platforms, electronic cabins, etc., play an important role in resource exploration, deep-sea monitoring and information network construction. The performance of deep-sea pressure structures is affected by a variety of factors, including material properties, structural forms, loads and environment. Under deep-sea conditions, the service conditions and functional requirements of equipment have many new features. For example, the superposition of extremely high seawater external pressure and equipment structural stresses leads to harsh stressing conditions of the pressure structures, which may suffer mechanical failures, including corrosion fatigue, creep, buckling, erosion, and fracture. Therefore, understanding the mechanism of the mechanical failure of deep-sea pressure structures and designing safe and reliable deep-sea pressure equipment are essential to ensure the safety and reliability of deep-sea pressure structures.
In this Research Topic, five papers are published focusing on the novel shell buckling, titanium alloy fracture mechanism, fully transparent pressure hull strength, fibre pipe mechanical characteristics and aluminium alloy cutting mechanism. These papers are the latest research in the “Design and mechanical failure of deep-sea pressure structures.”
The article by Cao et al. investigated an analytical method of global buckling of ring stiffened sandwich cylindrical shells by using the layerwise theory. The strain energy of the inner shell and ribs as well as the work done by the external force were derived based on the classical lamination theory, and the formulae for the critical buckling load of the ribbed sandwiched cylindrical shell were obtained using the Rayleigh-Ritz method. The results, which have been supported by numerical simulations, demonstrate that the suggested technique has good accuracy in forecasting the overall buckling behaviour of this type of cylindrical shell.
Compared with steel, the elasticity modulus, manufacturing process and failure form of titanium alloys are different, and there are still some common basic problems to be solved. The article by Zhang and Wan studied the failure strain and fracture mechanism of a TA31 titanium alloy of a pressure shell based on continuum damage mechanics. Triaxial tests of four different stresses were carried out by combining experimental and numerical approaches. Additionally, the predicted results of finite element simulations and the results of experiments were compared. The results demonstrate that the Bonora model with constant parameters is insufficient to forecast the evolution of failure strain and damage. Lower plastic deformation is produced by higher stress triaxiality and shear mechanisms, which also prevent void growth during damage evolution.
Due to their light weight, high strength, corrosion resistance, and ease of processing, non-metallic materials have demonstrated increasing potential for underwater pressure structural applications. Currently, the commonly used materials for aerospace and deep sea exploration are resin-based carbon fibres and glass fibres. The article by Sun et al. studied the mechanical properties of fibre-reinforced flexible pipes under radial compression loads. The radial stiffness of the circular pipe was then determined analytically using a formula based on the fundamentals of elastic theory. Radial compression tests and numerical simulations were carried out on the specimens. The radial stiffness of the pipe was obtained by comparing the results of the analytical, test and finite element model. The experimental results are very close to those of the numerical analyses. Therefore, the analytical and numerical models can be used to estimate the radial stiffness of fibre-reinforced pipes.
The article by Wu et al. explored the failure analysis of fully transparent deep-sea pressure hulls used at 2,500 m depth. Quasistatic compression tests were conducted on PMMA samples with different loading rates, and the relevant parameters were fitted to the test data to establish a finite element model. An equation for predicting the unstable type of failure was described. In addition, the ultimate load and failure mode of a fully transparent deep-sea pressure hull were also determined using finite elements. It is shown that, in contrast, the failure analysis of fully transparent pressure hulls can be accomplished using the provided simulation procedure.
The article by Yu et al. investigated the cutting mechanism of 5,052 aluminium alloy by means of numerical simulations, experiments and underwater sensors. The effects of certain parameters such as the cutting current, voltage and water depth on the formation of underwater incisions were investigated. The cutting arc trajectory and the combustion process during cutting were monitored using visual sensing. The aluminium alloy notch formation and temperature distribution were analysed by combining numerical analysis with observations. The numerical results match the experimental data and reveal the cutting mechanism.
As guest editors, we are deeply grateful to all the authors who submitted their papers on time. We also thank the reviewers, who carefully reviewed the manuscript and made constructive suggestions, for their excellent work that enhanced the papers’ calibre and readability. Finally, we would like to express our sincere gratitude to the Frontiers in Materials editorial staff for their hard work in ensuring that this Research Topic of all the reviewed manuscripts was published on time and in a stunning format.
We hope that the results of this Research Topic will provide support for early damage prediction and pressure assessment of deep-sea pressure structures. Furthermore, we hope that this contribution will drive innovative developments in deep-sea pressure structural design and mechanical failure.
YoZ: Writing–original draft. JZ: Writing–review and editing. YuZ: Writing–review and editing. XL: Writing–review and editing. N-AN: Writing–review and editing.
The authors declare that the research was conducted in the absence of any commercial or financial relationships that could be construed as a potential conflict of interest.
All claims expressed in this article are solely those of the authors and do not necessarily represent those of their affiliated organizations, or those of the publisher, the editors and the reviewers. Any product that may be evaluated in this article, or claim that may be made by its manufacturer, is not guaranteed or endorsed by the publisher.
Keywords: pressure structure, strength, buckling, mechanical failure, metal degradation
Citation: Zhu Y, Zhang J, Zhang Y, Liang X and Noda N-A (2023) Editorial: Design and mechanical failure of deep-sea pressure structures. Front. Mater. 10:1292283. doi: 10.3389/fmats.2023.1292283
Received: 11 September 2023; Accepted: 25 September 2023;
Published: 29 September 2023.
Edited and reviewed by:
Nicola Maria Pugno, University of Trento, ItalyCopyright © 2023 Zhu, Zhang, Zhang, Liang and Noda. This is an open-access article distributed under the terms of the Creative Commons Attribution License (CC BY). The use, distribution or reproduction in other forums is permitted, provided the original author(s) and the copyright owner(s) are credited and that the original publication in this journal is cited, in accordance with accepted academic practice. No use, distribution or reproduction is permitted which does not comply with these terms.
*Correspondence: Jian Zhang, emhqaWFuMTI3QGp1c3QuZWR1LmNu; Yu Zhang, emhhbmd5dUBjdXAuZWR1LmNu
Disclaimer: All claims expressed in this article are solely those of the authors and do not necessarily represent those of their affiliated organizations, or those of the publisher, the editors and the reviewers. Any product that may be evaluated in this article or claim that may be made by its manufacturer is not guaranteed or endorsed by the publisher.
Research integrity at Frontiers
Learn more about the work of our research integrity team to safeguard the quality of each article we publish.