- 1Changchun Institute of Technology, School of Architecture, Changchun Jilin, China
- 2Department of Civil Engineering, College of Engineering, Najran University, Najran, Saudi Arabia
- 3Architectural Engineering Department, College of Engineering, Najran University, Najran, Saudi Arabia
- 4Department of Civil, Environmental and Natural Resources Engineering, Luleå University of Technology, Luleå, Sweden
- 5Department of Civil Engineering, School of Engineering, Monash University Malaysia, Selangor, Malaysia
- 6Department of Civil Engineering, COMSATS University Islamabad, Abbottabad, Pakistan
3D printing, also known as additive manufacturing, has recently gained significant attention and popularity as a transformative technology across various industries. One area where 3D printing is making remarkable strides is in the construction field, particularly with the emergence of 3D printing concrete (3DPC). While 3DPC holds immense promise, there are still challenges to overcome, such as incorporating reinforcement. This study reviews the potential of using fibre reinforcement to overcome the challenge of making ductile concrete for 3D printing that can withstand substantial tensile stresses. Effects of various types of fibre addition on widespread aspects of 3DPC are systematically reviewed. This review study considers various aspects of 3DPC: rheological characteristics, buildability, anisotropic mechanical behavior, and ductility. These characteristics of fibre-reinforced 3DPC are discussed in light of the published literature. This research’s graphical and statistical visualizations offer valuable insights for academic scholars. This review summarizes recent advancements in fibre-reinforced 3DPC while highlighting the persisting challenges in developing fibre-reinforced 3DPC with desired properties for real-world applications.
1 Introduction
Concrete is a widely utilized building material, following water as the most extensively employed substance worldwide (Gagg, 2014). On an annual basis, around 10 billion tons of concrete are manufactured globally (Meyer, 2004). The substantial demand for concrete necessitates materials possessing specific attributes and exceptional durability. Consequently, the domain of material science dedicated to concrete has witnessed substantial progress over time. The strength of construction-grade concrete has experienced significant enhancements in the last 5 decades. In the 1960s, the prevailing concrete compositions exhibited compressive strengths ranging from 15 to 20 MPa. However, modern skyscrapers are frequently built employing ultra-high-strength concrete, capable of withstanding compressive strengths of up to 120 MPa. This progression has occurred gradually, accompanying the advancement of specialized concrete variants such as fibre-reinforced concrete, self-compacting concrete, and low-density structural concrete (Cao et al., 2018a; Cao et al., 2018b; Cao and Khan, 2021; Chang et al., 2023; Li et al., 2023). Nonetheless, constructing concrete structures involving placement and shaping has remained relatively unaltered over the years, even with advancements in the science of concrete materials. Typically, this procedure relies on manual labor to batch, blend, and pour the concrete into molds. In contrast to industries like automotive and aerospace, which have experienced rapid technological advancements, the construction sector has primarily adhered to traditional methodologies (Khan and Ali, 2016; Cao et al., 2019; Khan and Ali, 2019; 2020).
Over the last 2 decades, 3D printing concrete (3DPC) has become a prominent digital fabrication technology within the concrete industry (Buswell et al., 2020). The adoption of this technology has witnessed a swift expansion, encompassing a wide range of applications, including off-site production of prefabricated panels and on-site construcion (Khan and Ali, 2019; Khan et al., 2022b; Ma et al., 2022). 3DPC is extensively utilized and is experiencing swift evolution and acceptance across various industries, including the construction sector. Among these approaches, Inkjet 3DP stands out as the method that presents the most favorable and immediate prospects for seamlessly incorporating the advantages of additive manufacturing techniques into the construction domain (Shakor et al., 2019a). This particular iteration of additive manufacturing utilizes concrete as the primary material for the printing process, enabling the creation of three-dimensional structures. It involves the utilization of a 3D printer, a device designed to deposit sequential layers of material to construct three-dimensional objects (Gibson et al., 2015; Khan et al., 2021; Khan et al., 2022a). Within the domain of 3D printing of concrete, cement-based mortars are frequently employed through an extrusion method (Zou et al., 2021). This technique involves the controlled deposition of a continuous material flow by robotic arms or gantry systems guided by computer numerical control technology (Paul et al., 2018). Izadgoshasb et al. (2021) also utilized various machine learning algorithms to compute and predict the compressive strength in the context of extrusion-based 3D printed mortar. Moreover, Shakor et al. (2021) conducted finite element analysis to investigate the resilient and ideal mechanical attributes of 3D-printed cementitious mortar derived from laboratory experiments, simulating structural elements via ABAQUS software. Their findings revealed that the 3D-printed cementitious materials exhibit orthotropic characteristics, and the experimental outcomes closely aligned with both analytical predictions and the proposed model for various geometric configurations. This discovery holds significant importance in defining the optimal characteristics of 3D-printed structures. The merits of 3DPC encompass rapid construction facilitated by digitally crafted designs, which allow for the utilization of exceptionally sturdy cement-based materials (Tay et al., 2017; Hou et al., 2021; Mechtcherine et al., 2021).
Incorporating cellulose fibre into cement mortar and establishing interlayer connections represents a valuable approach to improving bonding in the 3D printing concrete (3DPC). Additionally, the interface structure assumes a pivotal role in achieving robust bonding. The interface structure between pre-existing and freshly applied concrete comprises three distinct layers, organized as follows: a penetrating layer, a layer with significant influence, and a layer with comparatively lesser influence (Hui-cai et al., 2002). It has been emphasized that roughness is a critical parameter for achieving interlocking between layers in 3DPC (Santos et al., 2012). In the literature, several methods have been investigated to create varying degrees of interface roughness, including steel brushing, sandblasting, and chiselling. The results of these studies revealed that, among the examined techniques, sandblasting consistently yielded the highest levels of bonding, both in terms of shear and tension strength (Julio et al., 2004). In the context of the reviewed literature, an evaluation of an interlocking structure was conducted during the 3D printing process. The outcomes of the splitting tests revealed a significant improvement in the average bond strength (Zareiyan and Khoshnevis, 2017). In the literature under consideration, the application of polymer-modified mortars, including epoxy resin and chloroprene latex, has proven to be an effective means of enhancing the typically weak interlayer bonding performance. The central focus of the study was to investigate the relationship between bond strength and the impact of setting time and variations in interlayer moisture levels within printed concrete (Wang et al., 2020).
This comprehensive review entails a systematic analysis to categorize and consolidate research findings. The objective is to provide a reliable and comprehensive reference for experts in this field. While researching the incorporation of fibres in 3DPC, researchers often face limitations caused by a lack of information, which hampers innovative research and collaborative efforts. Consequently, it is imperative to establish and implement a plan that supports researchers in accessing essential materials from reliable and valuable sources. The current study focuses on conducting a bibliographic analysis of the fibre-reinforced 3DPC. The findings derived from this study offer valuable insights into the diverse systems employed in 3D printing construction, the significance of standardized material testing, and the viability of integrating fibres. Including fibres can significantly enhance the rheology, sustainability, and constructability of 3DPC, thereby facilitating its extensive adoption. This review actively contributes to advancing and practically applying fibre-reinforced 3DPC technology within the construction industry by providing these insights and suggestions for future research.
2 Research significance
This comprehensive review extensively explores various aspects of 3D printing concrete (3DPC), specifically focusing on integrating fibre reinforcement. The review encompasses various topics, including technological advancements, material innovations, extrusion properties, sustainability considerations, and mechanical characteristics. By examining system utilization, standardized material testing, incorporating recycled materials, and optimizing printing ink, this study makes a substantial contribution to advancing the practical application of fibre-reinforced 3DPC technology within the construction industry. The significance of this review lies in its thorough exploration and analysis of essential aspects pertaining to fibre-reinforced 3DPC. This research enhances our collective comprehension of this technology by scrutinizing various pivotal factors. It delves into recent technological advancements, including the latest developments in fibre-reinforced 3DPC, innovative material formulations, extrusion process attributes, and the sustainability implications of 3DPC technology. This comprehensive examination provides a holistic view of the current state of fibre reinforcement in 3DPC technology. Additionally, the study extends valuable recommendations for potential research and development endeavors in this field, offering guidance for future advancements. This literature review is significant as it spotlights recent progress and practical applications of fibre-reinforced 3DPCs in the construction sector. It underscores the importance of optimizing printing ink to achieve more favorable economic and environmental outcomes across various applications. Through the presentation of these insights and recommendations, this review actively contributes to the advancement and widespread integration of fibre-reinforced 3DPC technology within the construction industry.
3 Material innovation in 3DPC
One of the main tasks in 3DPC is the incorporation of reinforcement. Concrete can crack or fail when subjected to tension or bending forces. Steel reinforcement or dispersed fibres reinforcement is added to the mix in traditional concrete to provide additional tensile strength and prevent these failures (Khan et al., 2022a; Farooqi and Ali, 2023; Li et al., 2023). However, in 3D printing, the concrete is extruded layer by layer, which makes it challenging to place steel reinforcement in the appropriate locations (Liu et al., 2023a). In addition, the use of steel reinforcement can interfere with the 3D printing process, leading to clogs or other errors. Using steel reinforcement also incurs high labor costs and material consumption during construction, as the steel must be manually positioned and secured within the molds. Researchers are investigating alternative reinforcement materials that can be seamlessly integrated into the 3D printing process to surmount these obstacles. One potential solution to this issue is employing high or ultra-high-strength concrete (Gosselin et al., 2016). The attainment of greater strengths is contingent upon significant material parameters, including a decreased water-to-cement ratio, integration of micro-fillers like silica fume, and appropriate aggregates (Baduge et al., 2018; Kristombu Baduge et al., 2020; Kristombu Baduge et al., 2023). Nevertheless, heightening the compressive strength does not necessarily result in a substantial increase in ductility and tensile/flexural strength. Consequently, enhancing the flexural and tensile strength of the printing material is imperative for bolstering the tensile and flexural capacity. In the erection of large 3D-printed concrete structures, reinforcement methods such as pre- and post-installed are frequently employed. Given the existing technological constraints, simultaneous printing or installation of reinforcement alongside concrete printing is impractical. As a result, reinforcement is often positioned before or after the structure is printed. HuaShang Tengda Ltd., which specializes in producing large 3D printed structures, employed pre-installed reinforcement in horizontal and vertical directions before printing the concrete (Scott, 2016), as depicted in Figure 1 (Marchment and Sanjayan, 2020). Nonetheless, this approach requires further enhancement to accommodate vertical components with numerous deposits of reinforcement and horizontal members.
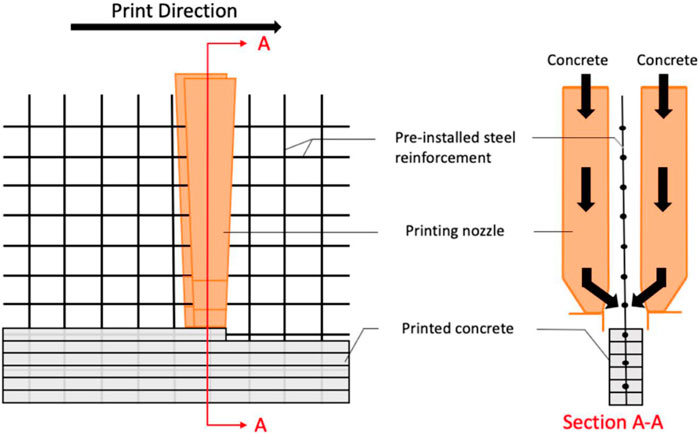
FIGURE 1. Pre-installment setup employed by HuaShang Tengda Ltd. (Wu et al., 2022).
Several studies have proposed the utilization of fibre-reinforced printable concrete as a solution to overcome this issue, as it can provide sufficient ductility, tensile, and flexural strength (Farooq and Banthia, 2022; Chen et al., 2023). The scientific literature introduced cementitious composites that comprise highly efficient synthetic fibres such as carbon or glass fibres in the 1960s. Since the late 1990s, attempts have been made to extrude cement pastes reinforced with fibres through a straightforward extrusion process. The goal of this endeavor was twofold: first, to enhance the density of the cement paste, and second, to exert some control over the alignment of fibres within the cementitious medium (Qian et al., 2003; Takashima et al., 2003; Shen et al., 2008). Comprehending the behavior of the fibre, cement matrix, and fibre-matrix boundary is imperative to grasp the behavior of composite materials like fibre-reinforced cement-based mixtures. In this regard, fibre orientation is crucial in enhancing fibre-reinforced composites’ performance (Almeida Jr et al., 2023). The orientation angle exerts a notable influence on the mechanical performance of printed samples. There exists variation in mechanical strength along different directions within each plane, rendering it a material with anisotropic properties (Shakor et al., 2023a). It has been established that when the average length of reinforcing fibres exceeds the diameter of the nozzle, they line up along the direction of movement through the nozzle, as depicted in Figure 2, as presented by Zhang et al. (2021). Research has shown that aligning the fibres in parallel with the printing direction improves printed samples’ bending resistance compared to traditionally cast counterparts (Arunothayan et al., 2020; Ziaee et al., 2022; Zhou et al., 2023). This effect can be explained by the fact that the maximum bridging effect will take place when fibres are oriented perpendicular to the crack.
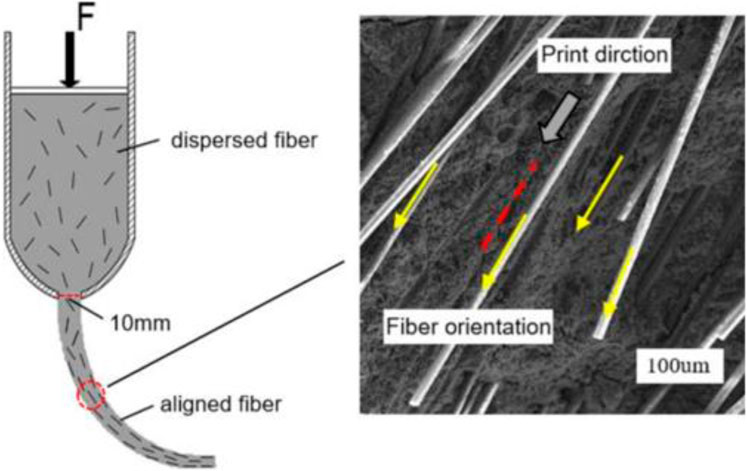
FIGURE 2. Fibres’ orientation in 3D printing concrete (Zhang et al., 2021).
In recent investigations focusing on the application of extrusion-based 3D printing for fibre-reinforced cement composites, it has been observed that the fibres exhibit a propensity to align with the direction of the printing flow (Nematollahi et al., 2018a; Ogura et al., 2018; Ji et al., 2019a; Bos et al., 2019). Zhu et al. (2019) conducted a study and concluded that incorporating polyethylene fibres in cementitious composites substantially improved the tensile properties of 3d printed specimens compared to traditionally produced specimens. This improvement was likely because of fibres alignment in the direction of printing. Conversely, a study by Chaves Figueiredo et al. (2020) discovered that in SHCC, the PVA fibres exhibited a predominant inclination relative to the printing direction. Ma et al. proposed a cementitious composite that can be used in 3D printing based on the extrusion method and contains copper tailings. (Ma et al., 2018a). In their study, Le et al. report the findings from an experiment focused on the combination formulation and freshly mixed characteristics of superior-quality, fibre-reinforced concrete made with fine aggregates. This concrete can be used to construct 3D-printed concrete structures (Le et al., 2012a). Perrot et al. proposed a theoretical framework and a method for optimizing the building rate, which greatly improves the design of 3DPC (Perrot et al., 2016). The application of the 3D printing technique and manufacturing of printable cementitious materials on a large scale presents a promising path toward producing construction projects, and significant progress has been made in the automation of construction (Kazemian et al., 2017; Ma et al., 2018b; Ma and Wang, 2018). 3D printing of cementitious composites has been widely adopted as it allows the creation of complex, multi-scale structures (Gosselin et al., 2016; Kazemian et al., 2017). In an experimental study, steel reinforcement has been integrated as horizontal ties to construct concrete walls by 3DPC (Khoshnevis et al., 2006; Jianchao et al., 2023). Employing the Concrete Printing method to construct a framework with designated gaps for installing post-tensioning rebar represents a distinctive approach to integrating reinforcement in 3DPC (Lim et al., 2011; Lim et al., 2023). Alternatively, Liu et al. used 3D printing to create reinforced concrete members with steel reinforcement in the form of wire mesh, which is placed during the printing process on top of the concrete (Liu et al., 2018). Extrusion-based 3DPC is the prevailing additive manufacturing technique utilized for constructing structures among the various available methods. This technique involves depositing cement-based material layer by layer using a nozzle, which creates a continuous filament (Buswell et al., 2018a).
Compared to 3D printed concrete reinforced with fibres, the technology of concrete contour crafting is still in the early stages of exploration. This method is characterized by using a gantry robot to automatically build the contour of a structure by layering concrete material. Nonetheless, research has demonstrated that the mechanical characteristics of 3DPC using this method are inferior to traditional concrete construction (Reiter et al., 2018; Ma et al., 2019; Wolfs et al., 2019). Addressing the incorporation of reinforcement into 3D-printed concrete structures represents a primary challenge that necessitates attention (Marchment and Sanjayan, 2020). One solution to this issue is to use short fibres as an alternative to steel bars. It is essential to develop fibre-reinforced cement-based materials to expand the use of 3D-printed concrete for high-performance structures (Melenka et al., 2016; Al Abadi et al., 2018; Kabir et al., 2020). In the literature, printable concretes have been characterized by diverse combinations of properties, encompassing normal strength concrete, geo-polymer concrete, foam concrete, and highly efficient fibre-reinforced concrete (Le et al., 2012a; Perrot et al., 2018; Sanjayan et al., 2018; Zhang et al., 2018; Bong et al., 2019; Markin et al., 2019). Several investigators have incorporated fibres into concrete to resolve the difficulty of utilizing traditional steel reinforcement with 3D printing. An example of this approach is the utilization of polypropylene fibres, which reduces plastic shrinkage in 3D-printed fibre-reinforced concrete (Le et al., 2012a). An investigation revealed that 3d printing of fibre-reinforced geo-polymers containing more than 0.75% vol. Polypropylene fibres displayed a failure response characterized by increased strength or resistance to deformation under load (Nematollahi et al., 2018a). Panda et al. (2017c) conducted a study examining the mechanical characteristics of 3D-printed geo-polymers with the integration of short glass fibres. Another study involved the utilization of small, linear steel fibres to enhance the ductility of 3D-printed concrete of standard strength (Panda et al., 2017c; Bos et al., 2019). The fibres also help maintain the concrete’s shape during printing, leading to more accurate and precise prints. Fibre’s addition may affect concrete flowability, directly influencing pump-ability during 3D printing. That is why the impacts of various kinds of fibres on concrete properties, in general, and flowability in particular, must be considered. A comprehensive study conducted by Jiang et al. (2022) aimed to evaluate the effects of nano silica and polypropylene fibre on the printability and anisotropy of 3D-printed concrete. The pictorial description of dispersed fibres reinforcement in 3D printed concrete compiste is shown in Figure 3 (presented by Cao et al. (2022a)). The impact of Nano Silica and Polypropylene fibres on fresh properties, including printability and flowability and strength characteristics, has been observed. Both fresh properties significantly impact the mechanical properties of 3D printed models or structures. The printability of mortar can be greatly improved, and the anisotropy of printed samples can be reduced by utilizing NS and PP fibres, due to the low cost of PP fibres and the small amount of NS required. This improves shape stability and buildability, making the 3DPC useful for printing civil structures and art pieces to enhance their appearance and uniformity. Additionally, the rock-like characteristics of these fibres make them useful for rock physical model testing (Jiang et al., 2022). The copper tailings were used to improve the extrudability of concrete by substituting sand. However, it was observed that the rise in copper concentration decreased the workability of the cementitious blend.
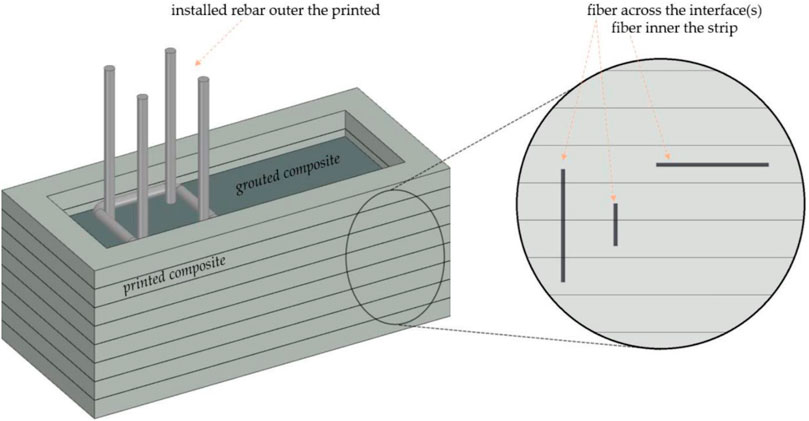
FIGURE 3. Pictorial description of fibres reinforcement in cement-based 3D Printing (Cao et al., 2022a).
4 Fibre utilization in 3DPC
In the past few years, 3D printing has experienced rapid growth. As a result, the building construction sector has embraced this technology to transform intricate building designs into tangible structures and create environmentally sustainable buildings on a large scale. Over the last 10 years, significant progress has been made in developing large-scale concrete printing, with more than thirty international research groups actively engaged in this study area (Buswell et al., 2018b). Reinforcement is a critical component in concrete construction, where steel bars or mesh are placed in the concrete to provide tensile strength and to resist structural forces. Reinforcement in either embedded steel bars in structural components or short-length fibres is mixed with concrete to improve mechanical properties. However, effectively integrating these materials within a 3D-printed structure can be difficult. This is because the concrete mixture must be precisely controlled during the printing process to guarantee even distribution of the reinforcement and to evade any premature setting or cracking. Additionally, the reinforcement must be correctly positioned and aligned to provide optimal support to the structure. These challenges require a combination of advanced printing techniques, material science, and engineering to overcome. The limitations of 3D printing technology present a significant challenge for including reinforcement in concrete printing, making it difficult to achieve. The procedure of 3DPC includes the deposition of concrete in layers, which can lead to discontinuities and weak bonding between the layers, particularly at the concrete and reinforcement interface. Moreover, traditional reinforcement may also obstruct the deposition of concrete and the movement of the printer’s nozzle, which limits the flexibility and design freedom that 3D concrete printing offers. Therefore, finding alternative reinforcement methods compatible with 3D printing that can provide sufficient strength and durability remains a significant research area. Researchers have developed fibre-reinforced 3D concrete printing as a viable substitute that eliminates traditional reinforcement’s necessity. Different varieties of fibres, such as glass, plastic, steel, and even carbon, glass, basalt and PET fibres, have been utilized to fabricate printable concretes (Panda et al., 2017c; Nematollahi et al., 2018a; Bos et al., 2019; Hambach et al., 2019; Ma et al., 2019; Nematollahi et al., 2019; Pham et al., 2020; Nematollahi et al., 2023). Shakor et al. (2020b) performed horizontal and vertical line printing assessments to evaluate the mixture’s workability, constructability, and consistency and to track the alignment of the fibre flow in the 3D printed samples. The findings indicate that including glass fibre in 3D printed specimens increased compressive strength compared to specimens lacking glass fibre. A strain-hardening concrete ink was formulated by incorporating a substantial amount of polyvinyl alcohol fibres, specifically at a dosage of 2% relative to the weight of the binder (Soltan and Li, 2018). Subsequently, other researchers have developed comparable printable mixtures that demonstrate strain-hardening behavior by applying high levels of polyvinyl alcohol or polyethylene fibres (Ogura et al., 2018; Figueiredo et al., 2019; Zhu et al., 2019). Pham et al. (2020) conducted a research study examining the mechanical characteristics of high-efficiency printable concrete. The study focused on incorporating steel fibres with varying lengths and fibre volume contents, ranging from 0.25% to 1%. According to the experimental outcomes, the crucial factors in enhancing flexural performance through the fibre bridging mechanism are the fibre alignment and the critical length and volume fraction of fibres (Pham et al., 2020). A separate investigation was carried out to examine the influence of polypropylene fibre length and quantity on the buildability and mechanical properties of 3DPC (Zhao et al., 2021). The findings from the research suggest that as the quantity of polypropylene fibre in 3DPC increases, both the static and dynamic yield stress exhibit a corresponding elevation. However, this increase in fibre content leads to a decrease in extrudability. Buildability displays an initial increase followed by a decrease. Additionally, an increase in the length of the polypropylene fibre causes a rise in static and dynamic yield stress while extrudability decreases. Buildability follows a similar pattern of initial increase and subsequent decrease. Shakor et al. (2019a) conducted an empirical investigation to assess the buildability, flow characteristics, extrusion performance, and mold-shaping potential of 3D-printed concrete mixtures. The horizontal test was employed to evaluate flowability and consistency, while vertical and squeeze-flow tests were utilized to gauge the layer-building capabilities. The manipulation of concrete extrusion and mold-shaping was achieved through precise control of robot and extruder speeds. Furthermore, it was observed that 3DPC with 9 mm length fibres exhibits better printability compared to those with 6 mm and 12 mm fibres. Finally, upon conducting compressive and flexural strength tests, it was discovered that 3DPC has a significant anisotropy in both compressive and flexural strengths. S. S. Mousavi and M. Dehestani attempted to use fibres produced from recycled latex and disposable vinyl gloves and nanomaterial based on graphene oxide to enhance the working performance of 3DPC. The research findings demonstrate that incorporating both recycled fibres and graphene oxide has a beneficial synergistic effect on the 3D printing properties of mortar. It indicates that a significant concentration of recycled fibres can potentially diminish the concrete’s compressive strength. Nevertheless, including graphene oxide compensates significantly for this reduction (Mousavi and Dehestani, 2022). A summary of investigative studies conducted to assess the impact of fibres on 3DPC characteristics is given in Table 1. One noteworthy constraint of fibre-reinforced 3D concrete printing is that the enhancement in tensile strength is predominantly evident when the testing is conducted parallel to the printing path. This effect is likely due to the fibres becoming more oriented toward printing during the deposition (Soltan and Li, 2018; Hambach et al., 2019; Li et al., 2020; Nematollahi et al., 2023).
5 Influence of fibres on the anisotropic characteristics of 3DPC
The force direction can cause variations in the strength of 3DPC. This is because when concrete is printed in layers, the strength of each layer can be affected by several factors, such as printing parameters, concrete mixture quality, and the curing process. In general, the strength of 3DPC in the vertical direction (i.e., the direction in which the layers are stacked) is typically higher than in the horizontal direction. This is because the layers provide some reinforcement in the vertical direction, whereas in the horizontal direction, the layers are more likely to separate or delaminate under stress. However, several techniques can be used to improve the strength and durability of 3D-printed concrete in all directions. For example, adding fibres or other reinforcements to the concrete mixture can improve its tensile strength and toughness, while optimizing the printing parameters and curing process can help to reduce defects and ensure consistent quality throughout the printed structure. When fibres are added to the concrete mix, they become distributed throughout the material and help to reinforce it in all directions. This can help prevent cracking and delamination in the horizontal direction, improving the overall durability and resistance to wear and tear. In addition, fibres can help reduce the risk of shrinkage and thermal cracking during curing. In 3D printing, various types of fibre-reinforced concrete can be employed, such as short, long, and continuous fibres. Each type possesses its own set of advantages and limitations. Selecting the appropriate fibre type depends on factors such as the intended application, desired structural properties, and the cost and availability of materials.
Another approach is to use additives or fibres in the concrete mixture to improve its strength and durability in different directions. Murcia et al. (2020) studied the influence of printing orientation on the varying properties of 3D-printed concrete. The findings revealed that all samples displayed directional dependence, where the compressive strength and elastic modulus were lower in the Z-direction when compared to the X- and Y-directions. Nevertheless, no significant difference was observed in the elastic modulus between the X and Y directions, indicating their comparability (Murcia et al., 2020). A research investigation was carried out by Panda et al. to examine the properties of geo-polymer concrete fabricated using fly ash via 3D printing technology. The study findings revealed that the mechanical properties of 3D-printed geo-polymers were notably impacted by the load path, which was attributable to the anisotropic nature of the printing process. Additionally, incorporating fibres in the concrete mix improved the performance of 3DPC (Panda et al., 2017b). Ding et al. (2020) examined the mechanical characteristics of 3DPC with polyethylene fibres and reported considerable anisotropic performance by the samples. The researchers identified that the uniform and well-aligned distribution of fibres played a crucial role in improving the concrete’s final strength (Ding et al., 2020). The reason behind this is that, during bending tests, the maximum normal stress at the specimen’s middle point usually determines the sample’s ultimate strength. When subjecting the specimen to loading in the X direction, the tensile stress at the middle point acted perpendicular to the layer interface, where the bond strength was the weakest. The fibres, as they did not traverse the printed filaments, had minimal impact on enhancing the weak bond strength at the interface. Consequently, the flexural strength in the X direction remained the least robust (Ding et al., 2020). Similarly, the direction of load with respect to 3D-printed layers is demonstrated in Figure 4, as reported by Abualsaud et al. (2022). Results revealed significant anisotropy in compressive strength, as can be interpolated from Figure 5.
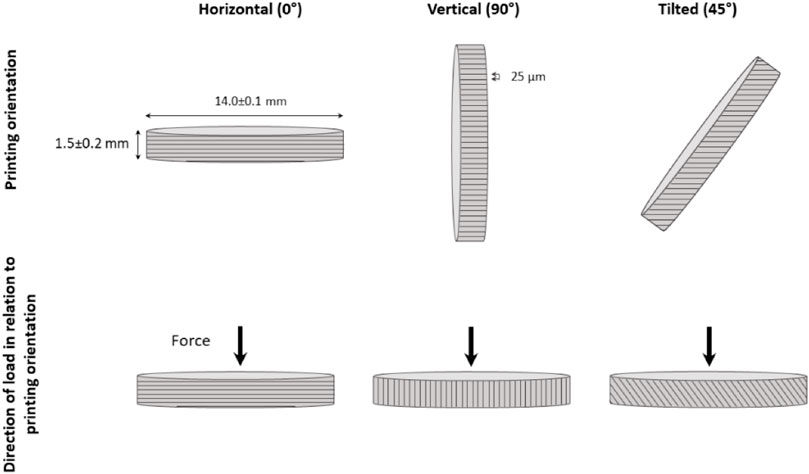
FIGURE 4. The direction of load with respect to 3D-printed layers (Abualsaud et al., 2022).
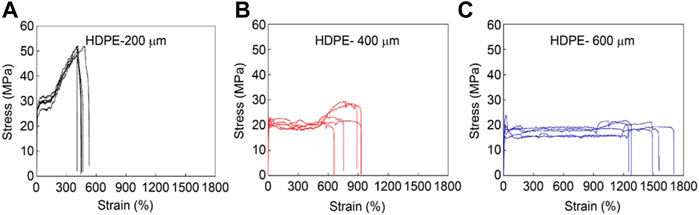
FIGURE 5. Effect of polyethylene fibres on the anisotropic performance of 3DPC reported by (Xiao et al., 2023) (A) 200 μm fibres, (B) 400 μm fibres, and (C) 600 μm fibres.
A study was conducted on the mechanical properties of sustainable building materials produced through 3D printing, which contained short glass fibres of varying lengths and ratios. The results indicated that these properties showed significant directional dependence (Yu et al., 2014). Shakor et al. (2020b) explored the impact of heat-curing and the incorporation of E6-glass fibres as a reinforcement strategy for the printed samples. The findings revealed that subjecting the cement mortar to a heat-curing process led to enhanced mechanical properties. Furthermore, introducing fibre reinforcement improved consistency in powder flowability and surface roughness across the specimens. Ultra-High-Performance Concrete (UHPC) with fibre reinforcement is a more suitable material for 3D printing when compared to normal-strength and high-strength concrete. This is due to its strength and ductility (Habel et al., 2006; Yu et al., 2014; Yang et al., 2019). Prior studies have examined the anisotropic properties of UHPC incorporating fibre reinforcement made for 3d printing (Yang et al., 2022). The study examined how the testing direction affected the compressive strength and rupture modulus of 3D-printed ultra-high-performance fibre-reinforced concrete. Furthermore, it investigated the relationship between fibre orientation and the mechanical properties of the printed samples (Arunothayan et al., 2020; Arunothayan et al., 2021). Given the increasing need for higher safety standards in civil engineering worldwide, it has become essential to comprehend the dynamic mechanical properties. As a result, extensive investigation has been conducted on the dynamic performance of conventional concrete (Hao and Hao, 2013; Su and Xu, 2013; Su et al., 2016b; a; Guo et al., 2017). SHPB impact tests were conducted by Wang et al. (2008) on concrete reinforced with steel fibres, specifically ultra-short steel fibres. Using stress-strain curves obtained at varying loading rates, a dynamic design model for SFRC composites was explicitly formulated for compression. Fu et al. (2018) examined the dynamic mechanical characteristics of concrete reinforced with basalt polypropylene fibres in their research. The researchers observed that incorporating basalt and polypropylene fibres into the concrete improved its impact resistance. Based on their results, the researchers developed a technique to precisely describe basalt polypropylene fibre-reinforced concrete’s dynamic stress-strain correlation (Fu et al., 2018).
6 Rheology and buildability of fibre-reinforced 3DPC
The challenges hinder the widespread adoption of 3DPC in understanding and characterizing fibre-reinforced printable materials in their fresh state. For a material to be suitable for 3DPC, it must exhibit a combination of low viscosity to enable continuous extrusion and high yield stress to maintain its shape when subjected to the weight of subsequent layers printed on top. These two properties are essential for an ideal 3DPC material. The extrusion-based method utilizes a nozzle to extrude materials and ensure the concrete is buildable, resulting in the creation of multiple layers that are structurally sound. To achieve pumpability and extrudability, concrete mixtures must display sufficient thixotropic properties that cater to static buildability and dynamic fluidity (De Schutter et al., 2018; Zareiyan and Khoshnevis, 2018; Liu et al., 2019). The 3DPC technology system’s primary focal point is the printing head/extruder, serving as the convergence point for data, mechanical processes, and material flow (Cao et al., 2022b). Within this component, material is deposited quantitatively in three dimensions through precise movements, enabling the realization of 3D printing. A complete nozzle unit encompasses both the extrusion mechanism and the nozzle tip. Previous research has identified three distinct extrusion mechanisms: ram extrusion, screw-based pumping, and direct screw-based extrusion, as illustrated in Figure 6, as presented by Cao et al. (2022b). Ram Extrusion (RE), depicted in Figure 6A, involves the direct expulsion of material from the nozzle tip through the action of a piston without introducing any twisting or screwing motion. This method is often employed for straightforward printing assessments, with less emphasis on pump-ability considerations. Various tools have been adapted as printing nozzles, including syringes (Nair et al., 2020) (typically with a volume less than 300 mL), dispensing tubes (Vergara and Colorado, 2020), or customized pistons (Figueiredo et al., 2019). Additionally, larger piston-based devices, such as glue tubes, have been utilized as printing nozzles, and more robust piston systems (Bong et al., 2019) serve as the pumping source. Screw Pump (SP), illustrated in Figure 6B, operates with a rotor encased within a tightly fitted rubber stator (Borisova et al., 2017), characterized as a closed screw mechanism in contrast to the direct screw approach. Material is propelled from the nozzle tip using a robust motor. SP requires the material to possess high fluidity to facilitate the pumping process, resulting in a significant slump after printing and making it challenging to maintain the desired geometry during printing. In Direct Screw (DS), as depicted in Figure 6C, material extrusion occurs through an open screw mechanism (as opposed to the closed screw configuration in the previous SP), moving the material from the reservoir to the nozzle tip. DS extruders offer simplicity in terms of utilization, control, and maintenance. They can be integrated into desktop gantry systems, facilitating manual feeding and operation (Ma et al., 2020). In order to enhance the pumpability of fibre-reinforced concrete, scientists have utilized 3D printing techniques with fibre-reinforced concrete having a restricted fibre content. By employing this approach, they could assess the material’s plastic viscosity, thixotropy, and dynamic static yield stress. While the available literature on the fresh properties of fibre-reinforced cementitious materials is limited, previous studies have indicated a decrease in the material’s workability with the introduction of fibres. This effect becomes more pronounced with increasing aspect ratio and fibre volume fraction (Weng et al., 2018). By creating a more compact fibre network, the fibres improved cohesion and Led to a decrease in the slump flow. The increase in fibre percentage led to higher yield stress while decreasing workability (Dedenis et al., 2020). According to Swamy (1974), even in the instance of highly liquid concretes such as Self-Compacting Concretes, there exists a critical concentration of fibres where the concrete becomes unworkable, emphasizing the presence of a limit. Beyond this threshold concentration, it has been noted that fibres tend to agglomerate and form clusters. The fibre factor, which combines the numerical values of aspect ratio and fibre volume fraction, is typically recommended to fall within the range of 0.2–2, according to existing literature (Kooiman, 2000; Grünewald, 2004; Banfill et al., 2006; Marković, 2006). Concrete comprises a range of components, from Sub-micron-sized cement particles to Aggregate particles of centimeter scale. To explore the relationship between mix design and rheological properties, a multi-scale approach appears to be a very promising avenue of study (Flatt, 2004; Toutou and Roussel, 2006; Yammine et al., 2008). Earlier research has highlighted the irregular flow characteristics of fibre-reinforced cementitious composites. This is primarily attributed to the diverse material selection, which greatly influences the composites’ performance (Arora et al., 2018). Incorporating fibres into printable concrete mixtures is crucial for achieving the necessary ductility. Nevertheless, employing a high fibre content can lead to obstructions and impediments during the extrusion process, especially when smaller nozzles are utilized (Arunothayan et al., 2021; Arunothayan et al., 2023). To reinforce cementitious materials, the industry employs various types of fibres. In civil engineering, a combination of flexible fibres, such as polypropylene and organic fibres, is utilized alongside rigid fibres, with steel fibres being the most commonly used option. The inclusion of rigid sphere-shaped additions in composite cementitious materials results in a notable decrease in the fluidity of the fresh mixture. This decrease is primarily attributed to forming a through-interaction link between fibres at a critical volume fraction. This system can increase the material’s yield stress only if it comprises direct interactions between stiff forms and withstands external loads. Hence, it is crucial to differentiate between rigid and flexible fibres. Martinie et al. (2010) proposed a method to differentiate between rigid and flexible fibres by considering them as beams loaded by fluid (fresh concrete) and measuring the ratio of deflection to fibre length. They classify rigid fibres as having a ratio of less than 1%. In addition, fibres also greatly affect aggregates’ packing and, ultimately, the rheology of printable concrete (Krieger and Dougherty, 1959; Grünewald, 2012). It has been reported that the decrease in packing density due to the incorporation of fibres is somewhat greater in the case of coarse aggregate than sand. This is because the presence of fibres causes coarse aggregates to be separate, while sand can compact closely around the fibres (Bartos and Hoy, 2004). It is impossible to quantitatively predict the complex phenomenon depicted in Figure 7 without conducting several experimental measurements to fit empirical coefficients (Wiemer et al., 2020). It can be seen that fibre restricts the packing of coarse aggregates. Previous studies have examined three packing regimes to investigate the impact of fibre packing: semi-dilute packing, dense packing, and random loose packing (Martinie et al., 2010). In order to predict the flow characteristics of concentrated suspensions such as cementitious materials, it is crucial to consider the ratio between the volume of the suspended phase and the filling density (Sedran, 1999).
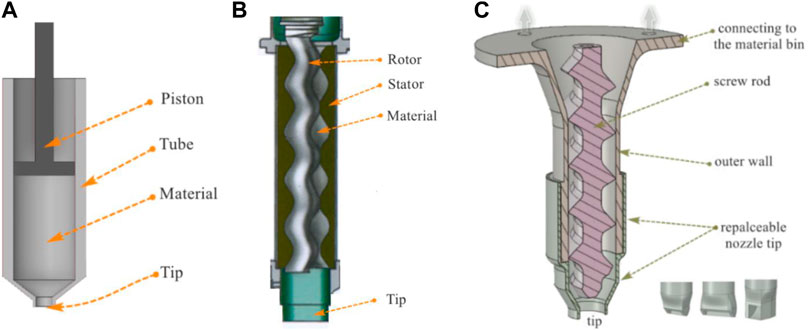
FIGURE 6. Nozzle types (A) piston extruder (B) screw pump (C) direct screw with replaceable nozzle tips (Cao et al., 2022b).
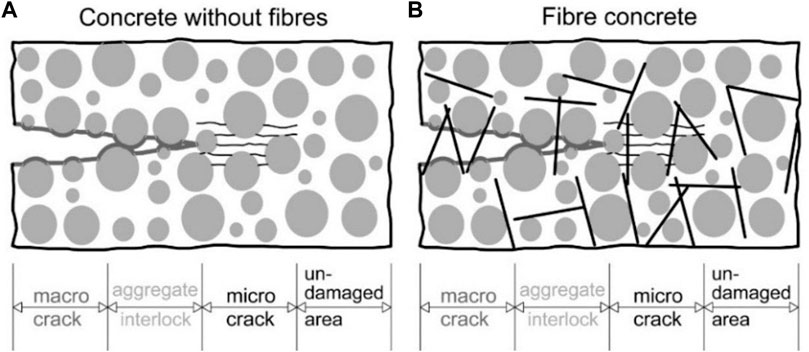
FIGURE 7. Effect of fibre on packing of coarse and fine particles (A) without fibre (B) with fibre (Wiemer et al., 2020).
Other research has utilized viscosity modifiers to enhance the fibre dispersion, viscosity, and thixotropic characteristics of mixtures intended for 3D printing (Arunothayan et al., 2023). Zhang et al. (2018) increased the buildability of 3DPC up to 150% by using small amounts of nano clay. A recent study proposed a high-efficiency, lightweight concrete reinforced with fibres for extrusion-based 3DPC. The study systematically investigated the printability, lightweight properties, and mechanical characteristics (flexural strength and compressive strength) of well-proportioned lightweight concrete containing PVA fibres. After making minor adjustments, the chosen lightweight concrete mix design was printed and compared to conventionally cast counterparts. Furthermore, a detailed microstructural analysis was carried out to examine how the performance of PVA fibres reinforced the printed structures. In order to compensate for the negative effects of fibres on rheology, a viscosity-modifying admixture (VMA) was used. The printability of the resulting printed concrete was measured by extrudability and shape retention tests. By utilizing a VMA ratio of 0.20%, the concrete achieved an optimal shape-retaining characteristic and exceptional printability without encountering bleeding or blockage. The shape-retaining property was validated by a slump loss of less than 3%. Furthermore, the printability parameter remained within the desired threshold of 2, indicating an optimal capability for printing. As a result, the calibration methodology determined that the preferable combination consisted of a water-to-cement (w/c) ratio of 0.65 and a VMA ratio of 0.02% (Sun et al., 2021).
The buildability of 3D printed concrete refers to how well the concrete material can be used in a 3D printing process to create a desired structure. It encompasses a range of factors, including the flow properties of the concrete, its setting time, its ability to bond with other layers or materials, and the overall structural integrity of the printed object. An established method for evaluating the constructability of fresh concrete involves determining the maximum number of layers or the height of the printed object that can be successfully achieved while still maintaining structural integrity without any significant deformation (Le et al., 2012b; Zhu et al., 2019). The relationship between the buildability of printable concrete and its rheological behavior and early-age mechanical properties is widely recognized (Roussel, 2018). Buildability tests on steel fibre-reinforced 3D-printed concrete vases having square cross sections and twisted geometry were performed by Pham et al. (2020). The vase has a buildup height of 790 mm with a deviation of 1% from the designed digital model. The vase with 0.5% steel fibres and has a height of 805 mm, corresponding to the designed height of 810 mm, with a deviation of only 0.62%. In the similar manner, the buildability comparison of fibre-reinforced 3D printed concrete specimens is done by Liu et al. (2023b), as illustrated in Figure 8.
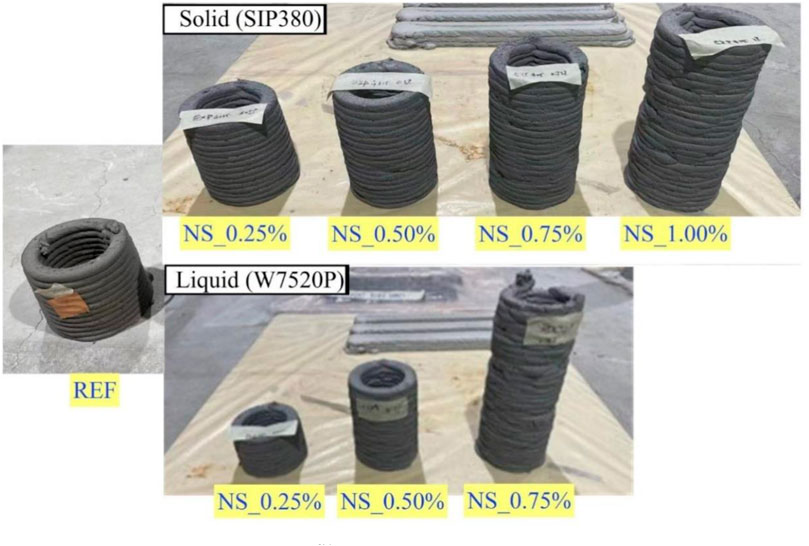
FIGURE 8. Buildability comparison of fibre-reinforced 3D printed concrete specimens (Liu et al., 2023b).
The mix design of ultra-high-performance steel fibre-reinforced concrete initially formulated for traditional casting purposes, is adapted and modified to suit the requirements of 3D printing (Wu et al., 2017). Assessing the constructability of a fresh concrete mixture typically involves quantifying the number of layers or the height of the printed object, ensuring no noticeable deformation (Le et al., 2012a; Ma et al., 2018a; Zhu et al., 2019). A study was conducted using a piston-type extruder to evaluate the extrudability of Ultra-High-Performance Fibre-Reinforced Concrete (UHPFRC). The study used a qualitative methodology, which involved observing and describing the behavior of the concrete as it was extruded. To ascertain successful extrudability, the fresh mixtures must be extruded through the nozzle without encountering any hindrance, such as blockage, bleeding, segregation, or tearing. This was tested by extruding five unstacked layers of the mixture. Other studies have used similar methodologies to evaluate extrudability (Le et al., 2012a; Bong et al., 2019). It is worth mentioning that prior research has used a comparable technique to examine the ability of fresh printing materials to retain their shape (Nematollahi et al., 2018a; Arunothayan et al., 2020). A pictorial depiction for buildability of 3D specimens is shown in Figure 9, as presented by Robayo-Salazar et al. (2023).
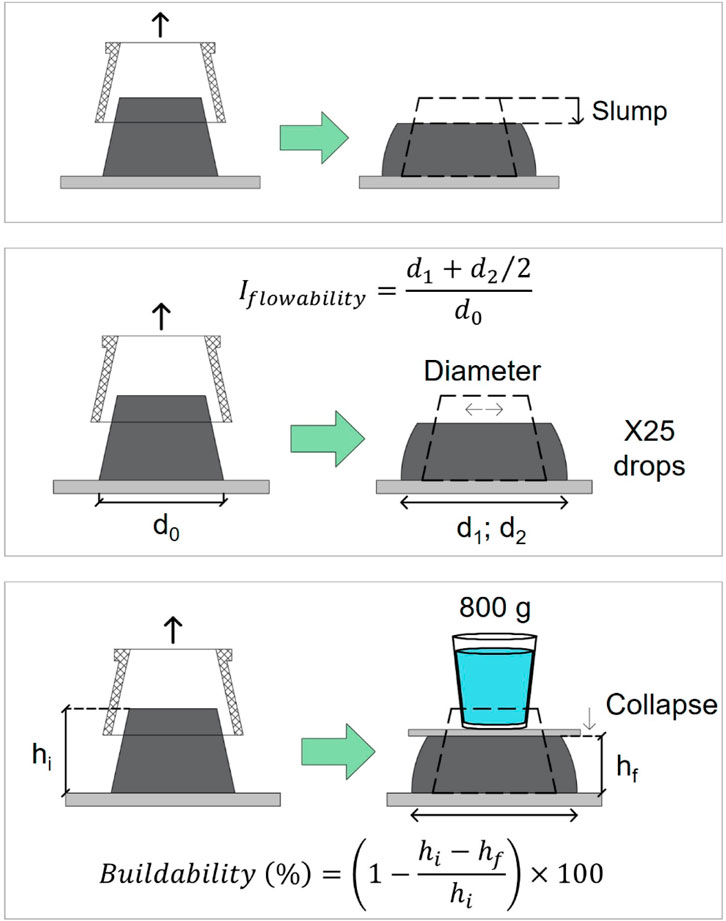
FIGURE 9. A pictorial description of shape retention by 3DPC samples (Robayo-Salazar et al., 2023).
7 Mechanical properties of fibre-reinforced 3DPC
The literature frequently proposes using fibres to reinforce concrete printed structures or materials based on cement. To illustrate, several researchers have suggested incorporating fibres into the concrete mix to enhance the mechanical characteristics of the cementitious materials for 3DPC application. The results of a previous study indicated that 3D printed fibre-reinforced concrete (FRC) samples exhibited improved flexural performance in the direction of printing than their counterparts cast in molds. The researchers postulated that this was attributed to the alignment of short steel fibres in the printing direction, which differed from the random fibre orientation observed in molded FRC. The inefficiency of the randomly oriented fibres in the molded FRC was attributed to the fact that the flexural and tensile stresses act primarily in a specific direction. In contrast, the fibres are dispersed in three degrees of freedom (Yoo et al., 2016). Sonebi et al. (2023) evaluated the compressive strength of cubical 3d printed specimens containing natural fibres and silica fume. Achieving this objective involves printing and cutting five to six layers of material while still wet in cubic molds, then extracting them 1 minute later. Size of cubical specimens was kept 45 mm. Yoo et al. (2016) found that incorporating longer, straight steel fibres having a greater aspect ratio in concrete can significantly improve its bending behavior, such as flexural strength, deflection behavior, and energy fascination. This is because longer fibres have a larger attachment area with the concrete matrix and are more likely to be situated at the crack surfaces, effectively resisting crack propagation and enhancing overall performance. In contrast, short fibres are less effective due to their smaller bonding area and lower chance of being positioned at crack surfaces (Yoo et al., 2016). Ding et al. (2020) observed that incorporating polyethylene fibres into the 3D printed specimens significantly improved bending strength compared to plain concrete specimens. This improvement was observed in all three directions. Remarkably, the strength of the fibre-reinforced 3D printed specimens surpassed that of the conventionally cast specimens by nearly twice the amount. Furthermore, Austin et al. compared the anisotropic characteristics of a cement-based material containing polypropylene micro fibres fabricated through extrusion-based 3D printing and samples produced through casting using the same mix design. Samples were tested under compressive loads applied in three different directions, i.e., a) load parallel to layers and print direction, b) perpendicular to layers and c) parallel to layers but perpendicular to printing direction. The compressive strength of the printed samples varied between 91 and 102 MPa. The case where the load was applied parallel to the layers showed the lowest resistance. However, in the other two directions, the compressive behavior and strength of the printed concrete were comparable to those of the cast samples. Based on their observations, the researchers deduced that the anisotropy in compressive strength was caused by defects at the layer interface (Le et al., 2012c). Researchers are developing fibre-reinforced cementitious composites (FRCC) that have high tensile ductility and can undergo large tensile strain. These concretes are required for 3D printing concrete structures, as conventional reinforcement is difficult to install during digital fabrication. Ribeiro et al. (2023) manufactured an FRC that exhibited as high as 11% tensile strain capacity in one similar effort, as demonstrated in Figure 10. Pseudo strain-hardening behavior was observed in all specimens. Increasing the fibre content did not have a significant impact on the ultimate tensile strength of the specimens. The ultimate tensile strength remained relatively constant at around 5 MPa throughout all the fibre volume fractions tested. However, there was a significant increase in the ability to sustain tensile strain as the fibre content was raised. This can be attributed to more fibres intersecting each crack, leading to an amplified bridging effect.
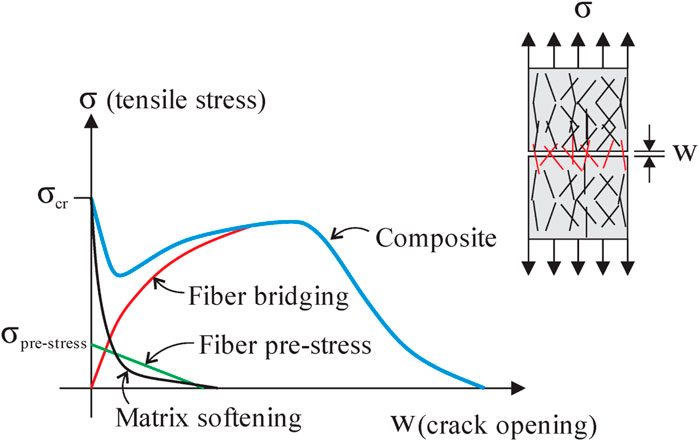
FIGURE 10. Tensile strain hardening behavior of 3D printed FRCC (Ribeiro et al., 2023).
Yu et al. (2018) investigated the feasibility of this type of FRCC for the 3D printing of concrete structures without conventional reinforcement. The seismic performance of double-story conventionally reinforced and polyethylene fibres reinforced concrete structures was evaluated. At minor 7.5 earthquakes, no visible damage was detected in the frame of fibre-reinforced concrete during excitations. However, tiny cracks, less than 0.1 mm, were observed to initiate and propagate at the joints during moderate 7.5 earthquakes. Furthermore, when the ground motion input exceeded the significant 8.0 threshold, multiple cracks became evident at the ends of the columns on the first story. Inter-story drift was also observed to be within the Chinese code requirements. Ultra-high strain capacity highly ductile concrete can be used to construct most buildings globally across various zones, even without steel reinforcement (Yu et al., 2018). Ji et al. (2019b) introduces a columnar mechanical structure for the 3D printer, where a four-column frame is established to facilitate 3D printing within it, as depicted in Figure 11.
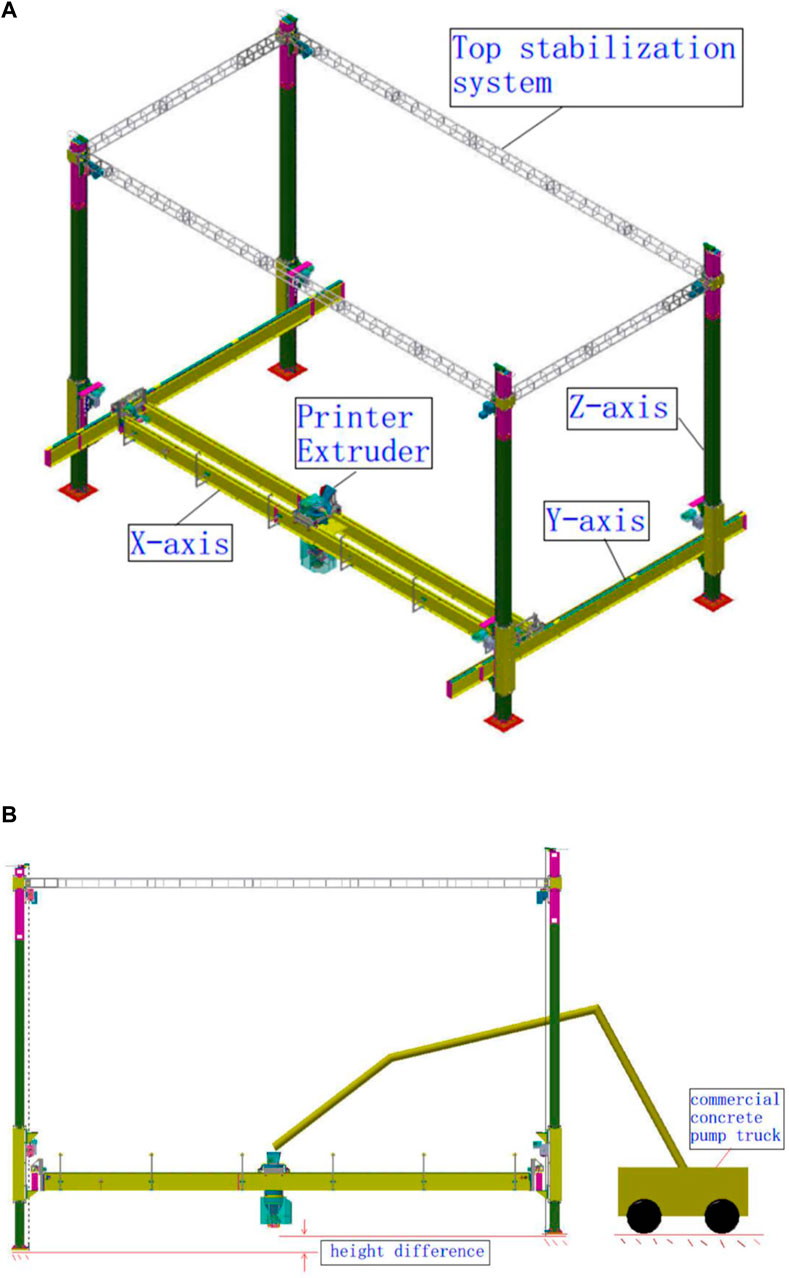
FIGURE 11. Large-scale framed 3D printed concrete (A) Axonometric view (B) Elevation view (Ji et al., 2019b).
In another study, strain-hardening cement-based composites were developed to be 3D-printed, incorporating different amounts of high-density polyethylene fibre. These composites were then employed to manufacture small-scale walls for further examination digitally. The extracted samples from these walls demonstrated a maximum tensile strength of 5.7 MPa and a maximum tensile strain capacity of 3.2% (Ogura et al., 2018). Panda et al. (2017a) researched to investigate the anisotropic property of the printing process for large-scale concrete structures by adding glass fibre (GF) to the geopolymer matrix. Custom-made geopolymer mortar was used to print specimens with varying fibre content and length, which were later evaluated for mechanical strength in different directions. Different testing directions with respect to layers adopted for study are shown in Figure 12, as presented by Rehman and Kim (2021). T1 direction represents the load applied perpendicular to layers and print direction; T2 represents load applied parallel to layers but perpendicular to print direction and in T3 direction, load was applied parallel to both layers and print direction. The study revealed that the inclusion of GF up to 1% resulted in an increasing trend in flexural strength. In contrast to casted specimens, the properties showed a directional dependency as an intrinsic characteristic of the layered manufacturing process. Maximum flexural strength was observed in the loading direction perpendicular to layers. Other researchers also observed similar results (Le et al., 2012c). The orientation of fibres along the layers and print direction is assumed to be the reason for this.
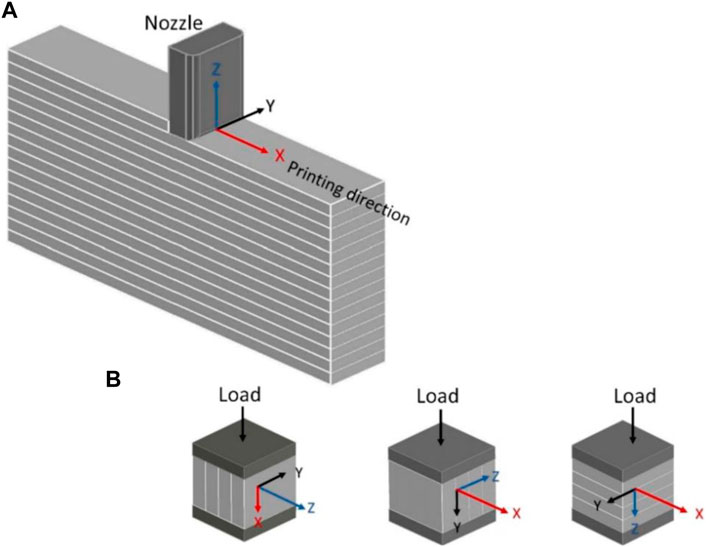
FIGURE 12. Description of test direction (A) identification of the X, Y, and Z axes to assess anisotropic mechanical properties; (B) evaluation of compressive strength anisotropy (Rehman and Kim, 2021).
Fibre-reinforced 3DPC has a significant drawback, whereby the enhancement of tensile strength is mainly noticeable in tests conducted parallel to the printing direction. This can be attributed to the greater orientation of fibres along the printing direction, resulting from the pumping and extrusion process. The fibres in the composite material cannot form bridges through the weak layer interfaces when positioned perpendicular to the print direction. As a result, these composites may only be suitable for applications where tensile stresses predominantly develop in a single direction, such as one-way slabs. Additionally, there may be challenges in pumping and extruding composite mixtures with high fibre content (Nematollahi et al., 2018a; Hambach et al., 2019; Li et al., 2020). According to Chu et al. (2021), including steel fibres was more advantageous in enhancing strength but comparatively less effective in improving the interlayer bond when compared to carbon or glass fibres. On the other hand, incorporating an appropriate quantity of nanoparticles generally favored strength and interlayer bond improvements. In conclusion, fibre reinforcement in 3D-printed concrete has been shown to affect mechanical strength positively. Adding fibres, such as steel, carbon, or glass, can enhance the printed concrete’s tensile strength, flexural strength, and impact resistance. Fibre reinforcement helps distribute and absorb stress within the material, improving structural integrity and durability. Fibres can also improve crack resistance and control crack propagation, increasing the mechanical performance of 3D-printed concrete structures.
8 Discussion and future prospects
While 3D printing of concrete offers numerous advantages and promising applications, this technology must address certain limitations. The incorporation of conventional reinforcement during printing is one of them. Although some breakthroughs have been made recently, such as printing reinforcement and installing reinforcement post-printing, these methods are complicated and costly. Utilization of fibre reinforcement is seen as a potential solution to this problem. However, several factors affect fiber-reinforced concrete performance and need extensive research before application in large-scale 3D printing. Furthermore, traditional research studies that rely on literature reviews are inadequate in establishing accurate associations among different aspects of the literature. Therefore, the systematic review conducted in this current study enables the correlation between bibliographic data and statistical analysis of research centered on 3DPC incorporating fibres. Hence, the objective of this study is to thoroughly identify commonly used keywords, the countries with the highest level of contribution to relevant articles, the primary sources responsible for producing influential articles, and the most respected authors based on their published articles and citation records in the specific research area of 3DPC incorporating fibres. The evaluation of keywords highlights a significant focus on exploring the incorporation of fibres into 3DPC to enhance mechanical properties and promote sustainable development. Furthermore, by examining the literature, the countries that have made noteworthy contributions to research in this particular domain are identified, showcasing the interconnectedness through citations. This extensive analysis has the potential to foster collaboration among researchers, thus driving advancements in research within this field. By employing scientometric analysis to assess keywords and interconnected literature, the present study emphasizes delineating opportunities in research on fibre-reinforced 3DPC. As the field of 3D printing technology progresses, its potential to transform the construction industry also expands. The capacity to effortlessly create intricate forms and structures, the freedom to customize designs, and the reduced wastage of materials are among the numerous advantages of 3D printing. Nevertheless, hurdles remain to overcome before its widespread integration into the construction field. Consequently, various recommendations have been put forth to enhance the process and fully capitalize on its advantages in the future.
• A comprehensive investigation should be conducted into the performance characteristics of diverse fibre types, including steel, glass, carbon, and polymeric fibres, as well as their combinations, within the context of fibre-reinforced 3DPC. The impacts of fibre length, aspect ratio, and distribution should also be evaluated on crucial factors such as mechanical properties, printability, and structural performance.
• A scholarly investigation should examine the impact of printing parameters’ impact on the dispersion and orientation of fibres embedded within the 3D-printed concrete, including printing speed, layer height, and extrusion pressure. Develop novel techniques to improve Fibers’ uniformity and alignment to enhance mechanical properties and structural integrity.
• Rigorous research should be undertaken to explore the complex bonding mechanisms and interactions between fibres and the cementitious matrix within 3D-printed concrete. Methodologies should be explored, including surface treatments, fibre coatings, and additive modifications, to augment the interfacial adhesion and optimize the load transfer efficiency between the fibres and the matrix.
• The structural behavior, load-carrying capacity, and long-term durability of structures made from fibre-reinforced 3D printed concrete should be evaluated thoroughly. Experimental testing and computational simulations should be employed to assess the influence of fibre content, geometry, and printing parameters on crucial factors such as mechanical response, crack propagation, and resistance to environmental degradation.
• The viability of integrating sustainable and recycled fibres, such as cellulose, textile waste, and industrial byproducts, into 3D-printed concrete should also be explored. The mechanical properties, impact on printability, and environmental advantages should be evaluated by considering availability, cost-effectiveness, and long-term durability.
• The obstacles associated with scaling up fibre-reinforced 3D concrete printing should be tackled for extensive application in large-scale construction projects. Methodologies should be devised to optimize printing speed, material delivery systems, and structural design considerations, aiming to facilitate this technology’s cost-effective and efficient implementation in real-world construction endeavors.
• In the future, it is recommended to broaden the scope of life cycle assessment (LCA) studies in the fibre-reinforced 3D concrete printing field. These studies should go beyond the Global Warming Potential metric and consider a wider range of environmental impacts. It is important to expand the scope and scale of these assessments to encompass factors beyond just the material level, considering the interconnections between material composition, construction processes, and environmental impact. Furthermore, particular attention should be directed toward assessing the impact of formworks in LCA modeling. To ensure the accuracy of these assessments, it is crucial to develop methodological guidelines that can enhance the precision and reliability of future LCA studies in the context of fibre-reinforced 3DPC.
9 Conclusion
This research focuses on analyzing existing reviews, with the primary goal of identifying recurring themes and trends within the literature related to fibre-reinforced 3D printing concrete (3DPC). This exploration holds significant potential benefits for emerging scholars and researchers seeking a deeper understanding of this domain. This study’s primary objective is to comprehensively review the relevant literature concerning fibre-reinforced 3DPC, delving into its multifaceted aspects. In pursuit of this objective, this research adopts a systematic approach to investigate the impact of incorporating various types of fibres on the diverse facets of 3DPC. Through this methodical examination, the study endeavors to extract insights and derive the following conclusions.
• Within the fibre-reinforced 3DPC, an array of fibre types finds application, encompassing steel fibres, polymer variants (such as polypropylene and polyethylene), glass fibres, carbon fibres, and natural fibres. The selection among these diverse fibre types entails careful consideration of their distinct merits and attributes, affording the capacity for tailoring the material composition to align with the intended printed structure’s specific structural requirements and performance criteria.
• The incorporation of fibre reinforcement partially improves the structural integrity and form retention of the printed construction. Nevertheless, when employed in substantial volumetric proportions, fibre reinforcement can impede the fluidity of 3DPC, leading to the obstruction and blockage of the printing nozzle. To mitigate these challenges, observing a recommended upper threshold of 2 for the fibre factor is advisable. Additionally, incorporating viscosity modifiers is an effective strategy for preserving the requisite flow characteristics of 3DPC during the printing process.
• Fibrous reinforcement yields a substantial augmentation in the mechanical properties of 3DPC, particularly concerning its flexural and tensile strength. Additionally, fibres contribute to an increased capacity for tensile strain in 3DPC. Nevertheless, it is noteworthy that the efficacy of fibres in enhancing the inter-layer adhesion within 3DPC remains limited, primarily due to their predominant alignment in the direction of printing.
• Achieving superior flexural strength and post-peak behavior hinges upon a delicate equilibrium between the content and alignment of fibres. The optimal fibre content can be meticulously fine-tuned to attain the desired printing attributes and mechanical performance to accommodate the specific demands of the extrusion-based printing process.
• Fibre inclusion did not induce a perceptible change in the inherent anisotropy commonly associated with layered materials manufactured using 3D printing techniques. Notably, the utilization of highly ductile fibre-reinforced concrete obviates the necessity for conventional steel reinforcing bars in construction applications while still exhibiting commendable performance, particularly under seismic conditions.
• The efficacious execution of fibre-reinforced 3DPC necessitates meticulous attention to a constellation of factors, encompassing the dispersion of fibres, the calibration of printing parameters, the interface dynamics between fibres and the matrix, and the materials’ congruence. Attaining the coveted mechanical attributes and printing proficiency mandates the discernment of the optimal fibre dosage, even distribution of fibres, and judicious selection of printing methodologies.
Author contributions
YZ: Conceptualization, Funding acquisition, Methodology, Visualization, Writing–original draft. FA: Conceptualization, Funding acquisition, Investigation, Project administration, Validation, Writing–review and editing. BA: Investigation, Resources, Software, Supervision, Validation, Writing–review and editing. YG: Data curation, Methodology, Visualization, Writing–review and editing. BI: Data curation, Methodology, Visualization, Writing–review and editing.
Funding
This work was financially supported by the Applied Research Project of The Education Department of Jilin Province (JJKH20210699KJ). The authors are also thankful to the Deanship of Scientific Research at Najran University for funding this work, under the Research Groups Funding program grant code (NU/RG/SERC/12/1).
Conflict of interest
The authors declare that the research was conducted in the absence of any commercial or financial relationships that could be construed as a potential conflict of interest.
Publisher’s note
All claims expressed in this article are solely those of the authors and do not necessarily represent those of their affiliated organizations, or those of the publisher, the editors and the reviewers. Any product that may be evaluated in this article, or claim that may be made by its manufacturer, is not guaranteed or endorsed by the publisher.
References
Abualsaud, R., Abussaud, M., Assudmi, Y., Aljoaib, G., Khaled, A., Alalawi, H., et al. (2022). Physiomechanical and surface characteristics of 3D-printed zirconia: an in vitro study. Materials 15 (19), 6988. doi:10.3390/ma15196988
Al Abadi, H., Thai, H.-T., Paton-Cole, V., and Patel, V. (2018). Elastic properties of 3D printed fibre-reinforced structures. Compos. Struct. 193, 8–18. doi:10.1016/j.compstruct.2018.03.051
Alchaar, A. S., and Al-Tamimi, A. K. (2021). Mechanical properties of 3D printed concrete in hot temperatures. Constr. Build. Mater. 266, 120991. doi:10.1016/j.conbuildmat.2020.120991
Almeida, J. H. S., Christoff, B. G., Tita, V., and St-Pierre, L. (2023). A concurrent fibre orientation and topology optimisation framework for 3D-printed fibre-reinforced composites. Compos. Sci. Technol. 232, 109872. doi:10.1016/j.compscitech.2022.109872
Arora, A., Aguayo, M., Hansen, H., Castro, C., Federspiel, E., Mobasher, B., et al. (2018). Microstructural packing- and rheology-based binder selection and characterization for Ultra-high Performance Concrete (UHPC). Cem. Concr. Res. 103, 179–190. doi:10.1016/j.cemconres.2017.10.013
Arunothayan, A. R., Nematollahi, B., Khayat, K. H., Ramesh, A., and Sanjayan, J. G. (2023). Rheological characterization of ultra-high performance concrete for 3D printing. Cem. Concr. Compos. 136, 104854. doi:10.1016/j.cemconcomp.2022.104854
Arunothayan, A. R., Nematollahi, B., Ranade, R., Bong, S. H., and Sanjayan, J. (2020). Development of 3D-printable ultra-high performance fiber-reinforced concrete for digital construction. Constr. Build. Mater. 257, 119546. doi:10.1016/j.conbuildmat.2020.119546
Arunothayan, A. R., Nematollahi, B., Ranade, R., Bong, S. H., Sanjayan, J. G., and Khayat, K. H. (2021). Fiber orientation effects on ultra-high performance concrete formed by 3D printing. Cem. Concr. Res. 143, 106384. doi:10.1016/j.cemconres.2021.106384
Baduge, S. K., Mendis, P., Ngo, T., Portella, J., and Nguyen, K. (2018). Understanding failure and stress-strain behavior of very-high strength concrete (>100 MPa) confined by lateral reinforcement. Constr. Build. Mater. 189, 62–77. doi:10.1016/j.conbuildmat.2018.08.192
Banfill, P., Starrs, G., Derruau, G., McCarter, W., and Chrisp, T. (2006). Rheology of low carbon fibre content reinforced cement mortar. Cem. Concr. Compos. 28 (9), 773–780. doi:10.1016/j.cemconcomp.2006.06.004
Bartos, P. M., and Hoy, C. (2004). “Interaction of particles in fibre reinforced concrete,” in Production methods and workability of concrete (Boca Raton, Florida, United States: CRC Press), 463–474.
Bong, S. H., Nematollahi, B., Nazari, A., Xia, M., and Sanjayan, J. (2019). Method of optimisation for ambient temperature cured sustainable geopolymers for 3D printing construction applications. Materials 12 (6), 902. doi:10.3390/ma12060902
Borisova, K., Ivanova, T., and Latypov, R. (2017). Study of screw pump stator and rotor working capacity to increase the output. Procedia Eng. 206, 688–691. doi:10.1016/j.proeng.2017.10.538
Bos, F., Bosco, E., and Salet, T. (2019). Ductility of 3D printed concrete reinforced with short straight steel fibers. Virtual Phys. Prototyp. 14 (2), 160–174. doi:10.1080/17452759.2018.1548069
Buswell, R. A., da Silva, W. L., Bos, F. P., Schipper, H., Lowke, D., Hack, N., et al. (2020). A process classification framework for defining and describing Digital Fabrication with Concrete. Cem. Concr. Res. 134, 106068. doi:10.1016/j.cemconres.2020.106068
Buswell, R. A., De Silva, W. L., Jones, S. Z., and Dirrenberger, J. (2018a). 3D printing using concrete extrusion: a roadmap for research. Cem. Concr. Res. 112, 37–49. doi:10.1016/j.cemconres.2018.05.006
Buswell, R. A., Leal de Silva, W. R., Jones, S. Z., and Dirrenberger, J. (2018b). 3D printing using concrete extrusion: a roadmap for research. Cem. Concr. Res. 112, 37–49. doi:10.1016/j.cemconres.2018.05.006
Cao, M., and Khan, M. (2021). Effectiveness of multiscale hybrid fiber reinforced cementitious composites under single degree of freedom hydraulic shaking table. Struct. Concr. 22 (1), 535–549. doi:10.1002/suco.201900228
Cao, M., Mao, Y., Khan, M., Si, W., and Shen, S. (2018a). Different testing methods for assessing the synthetic fiber distribution in cement-based composites. Constr. Build. Mater. 184, 128–142. doi:10.1016/j.conbuildmat.2018.06.207
Cao, M., Xie, C., Li, L., and Khan, M. (2019). Effect of different PVA and steel fiber length and content on mechanical properties of CaCO<sub>3</sub> whisker reinforced cementitious composites. Mater. Construcción 69 (336), e200. doi:10.3989/mc.2019.12918
Cao, M., Xie, C., Li, L., and Khan, M. (2018b). The relationship between reinforcing index and flexural parameters of new hybrid fiber reinforced slab. Comput. Concr. Int. J. 22 (5), 481–492. doi:10.12989/cac.2018.22.5.481
Cao, X., Yu, S., and Cui, H. (2022a). Experimental investigation on inner- and inter-strip reinforcements for 3D printed concrete via automatic staple inserting technique. Appl. Sci. 12 (4), 2099. doi:10.3390/app12042099
Cao, X., Yu, S., Cui, H., and Li, Z. (2022b). 3D printing devices and reinforcing techniques for extruded cement-based materials: a review. Build. [Online] 12 (4), 453. doi:10.3390/buildings12040453
Chang, Q., Liu, L., Farooqi, M. U., Thomas, B., and Özkılıç, Y. O. (2023). Data-driven based estimation of waste-derived ceramic concrete from experimental results with its environmental assessment. J. Mater. Res. Technol. 24, 6348–6368. doi:10.1016/j.jmrt.2023.04.223
Chaves Figueiredo, S., Romero Rodríguez, C., Y Ahmed, Z., Bos, D. H., Xu, Y., Salet, T. M., et al. (2020). Mechanical behavior of printed strain hardening cementitious composites. Materials 13 (10), 2253. doi:10.3390/ma13102253
Chen, W., Pan, J., Zhu, B., Ma, X., Zhang, Y., Chen, Y., et al. (2023). Improving mechanical properties of 3D printable ‘one-part’geopolymer concrete with steel fiber reinforcement. J. Build. Eng. 75, 107077. doi:10.1016/j.jobe.2023.107077
Chu, S. H., Li, L. G., and Kwan, A. K. H. (2021). Development of extrudable high strength fiber reinforced concrete incorporating nano calcium carbonate. Addit. Manuf. 37, 101617. doi:10.1016/j.addma.2020.101617
De Schutter, G., Lesage, K., Mechtcherine, V., Nerella, V. N., Habert, G., and Agusti-Juan, I. (2018). Vision of 3D printing with concrete — technical, economic and environmental potentials. Cem. Concr. Res. 112, 25–36. doi:10.1016/j.cemconres.2018.06.001
Dedenis, M., Sonebi, M., Amziane, S., Perrot, A., and Amato, G. (July 2020). "Effect of metakaolin, fly ash and polypropylene fibres on fresh and rheological properties of 3d printing based cement materials", in: Proceedings of the second RILEM international conference on concrete and digital fabrication: digital concrete 2020, Digital Concrete, 206–215.
Ding, T., Xiao, J., Zou, S., and Zhou, X. (2020). Anisotropic behavior in bending of 3D printed concrete reinforced with fibers. Compos. Struct. 254, 112808. doi:10.1016/j.compstruct.2020.112808
Farooq, M., and Banthia, N. (2022). Strain-hardening fiber reinforced polymer concrete with a low carbon footprint. Constr. Build. Mater. 314, 125705. doi:10.1016/j.conbuildmat.2021.125705
Farooqi, M. U., and Ali, M. (2023). A study on natural fibre reinforced concrete from materials to structural applications. Arabian J. Sci. Eng. 48 (4), 4471–4491. doi:10.1007/s13369-022-06977-1
Figueiredo, S. C., Rodríguez, C. R., Ahmed, Z. Y., Bos, D. H., Xu, Y., Salet, T. M., et al. (2019). An approach to develop printable strain hardening cementitious composites. Mater. Des. 169, 107651. doi:10.1016/j.matdes.2019.107651
Flatt, R. (2004). Towards a prediction of superplasticized concrete rheology. Mater. Struct. 37, 289–300. doi:10.1617/14088
Fu, Q., Niu, D., Zhang, J., Huang, D., Wang, Y., Hong, M., et al. (2018). Dynamic compressive mechanical behaviour and modelling of basalt–polypropylene fibre-reinforced concrete. Archives Civ. Mech. Eng. 18 (3), 914–927. doi:10.1016/j.acme.2018.01.016
Gagg, C. R. (2014). Cement and concrete as an engineering material: an historic appraisal and case study analysis. Eng. Fail. Anal. 40, 114–140. doi:10.1016/j.engfailanal.2014.02.004
Gibson, I., Rosen, D., and Stucker, B. (2015). “Additive manufacturing technologies: 3D printing,” in Additive manufacturing technologies: 3D printing, rapid prototyping, and direct digital manufacturing (Berlin, Germany: Springer).
Gosselin, C., Duballet, R., Roux, P., Gaudillière, N., Dirrenberger, J., and Morel, P. (2016). Large-scale 3D printing of ultra-high performance concrete–a new processing route for architects and builders. Mater. Des. 100, 102–109. doi:10.1016/j.matdes.2016.03.097
Grünewald, S. (2012). “9 - fibre reinforcement and the rheology of concrete,” in Understanding the rheology of concrete. Editor N. Roussel (Sawston, United Kingdom: Woodhead Publishing), 229–256.
Grünewald, S. (2004). Performance-based design of self-compacting fibre reinforced concrete. Delft, Netherlands: Delft University Press.
Guo, Y., Gao, G., Jing, L., and Shim, V. (2017). Response of high-strength concrete to dynamic compressive loading. Int. J. Impact Eng. 108, 114–135. doi:10.1016/j.ijimpeng.2017.04.015
Habel, K., Viviani, M., Denarié, E., and Brühwiler, E. (2006). Development of the mechanical properties of an ultra-high performance fiber reinforced concrete (UHPFRC). Cem. Concr. Res. 36 (7), 1362–1370. doi:10.1016/j.cemconres.2006.03.009
Hambach, M., Rutzen, M., and Volkmer, D. (2019). “Properties of 3D-printed fiber-reinforced Portland cement paste,” in 3D concrete printing technology (Amsterdam, Netherlands: Elsevier), 73–113.
Hao, Y., and Hao, H. (2013). Dynamic compressive behaviour of spiral steel fibre reinforced concrete in split Hopkinson pressure bar tests. Constr. Build. Mater. 48, 521–532. doi:10.1016/j.conbuildmat.2013.07.022
Hou, S., Duan, Z., Xiao, J., and Ye, J. (2021). A review of 3D printed concrete: performance requirements, testing measurements and mix design. Constr. Build. Mater. 273, 121745. doi:10.1016/j.conbuildmat.2020.121745
Hui-cai, X., Geng-ying, L., and Guang-jing, X. (2002). Microstructure model of the interfacial zone between fresh and old concrete. J. Wuhan Univ. Technology-Mater. Sci. Ed. 17 (4), 64–68. doi:10.1007/bf02838421
Izadgoshasb, H., Kandiri, A., Shakor, P., Laghi, V., and Gasparini, G. (2021). Predicting compressive strength of 3D printed mortar in structural members using machine learning. Appl. Sci. 11 (22), 10826. doi:10.3390/app112210826
Ji, G., Ding, T., Xiao, J., Du, S., Li, J., and Duan, Z. (2019a). A 3D printed ready-mixed concrete power distribution substation: materials and construction technology. Materials 12 (9), 1540. doi:10.3390/ma12091540
Ji, G., Ding, T., Xiao, J., Du, S., Li, J., and Duan, Z. (2019b). A 3D printed ready-mixed concrete power distribution substation: materials and construction technology. Mater. [Online] 12 (9), 1540. doi:10.3390/ma12091540
Jianchao, Z., Zhang, T., Faried, M., and Wengang, C. (2023). “3D printing cement based ink, and it’s application within the construction industry,” in Proceedings of the MATEC Web of conferences: EDP sciences.02003
Jiang, Q., Liu, Q., Wu, S., Zheng, H., and Sun, W. (2022). Modification effect of nanosilica and polypropylene fiber for extrusion-based 3D printing concrete: printability and mechanical anisotropy. Addit. Manuf. 56, 102944. doi:10.1016/j.addma.2022.102944
Julio, E. N., Branco, F. A., and Silva, V. t.D. (2004). Concrete-to-concrete bond strength. Influence of the roughness of the substrate surface. Constr. Build. Mater. 18 (9), 675–681. doi:10.1016/j.conbuildmat.2004.04.023
Kabir, S. F., Mathur, K., and Seyam, A.-F. M. (2020). A critical review on 3D printed continuous fiber-reinforced composites: history, mechanism, materials and properties. Compos. Struct. 232, 111476. doi:10.1016/j.compstruct.2019.111476
Kazemian, A., Yuan, X., Cochran, E., and Khoshnevis, B. (2017). Cementitious materials for construction-scale 3D printing: laboratory testing of fresh printing mixture. Constr. Build. Mater. 145, 639–647. doi:10.1016/j.conbuildmat.2017.04.015
Khan, M., and Ali, M. (2019). Improvement in concrete behavior with fly ash, silica-fume and coconut fibres. Constr. Build. Mater. 203, 174–187. doi:10.1016/j.conbuildmat.2019.01.103
Khan, M., and Ali, M. (2020). Optimization of concrete stiffeners for confined brick masonry structures. J. Build. Eng. 32, 101689. doi:10.1016/j.jobe.2020.101689
Khan, M., and Ali, M. (2016). Use of glass and nylon fibers in concrete for controlling early age micro cracking in bridge decks. Constr. Build. Mater. 125, 800–808. doi:10.1016/j.conbuildmat.2016.08.111
Khan, M., Cao, M., Ai, H., and Hussain, A. (2022a). Basalt fibers in modified whisker reinforced cementitious composites. Period. Polytech. Civ. Eng. 66 (2), 344–354. doi:10.3311/ppci.18965
Khan, M., Cao, M., and Ali, M. (July 2023). "Influence of CaCO3 whiskers, steel fibers and basalt fibers hybridization on flexural toughness of concrete", in: Proceedings of the fifth international conference on sustainable construction materials and technologies, London, UK), 14–17.
Khan, M., Cao, M., Chaopeng, X., and Ali, M. (2022b). Experimental and analytical study of hybrid fiber reinforced concrete prepared with basalt fiber under high temperature. Fire Mater. 46 (1), 205–226. doi:10.1002/fam.2968
Khan, M., Cao, M., Hussain, A., and Chu, S. (2021). Effect of silica-fume content on performance of CaCO3 whisker and basalt fiber at matrix interface in cement-based composites. Constr. Build. Mater. 300, 124046. doi:10.1016/j.conbuildmat.2021.124046
Khoshnevis, B., Hwang, D., Yao, K.-T., and Yeh, Z. (2006). Mega-scale fabrication by contour crafting. Int. J. Industrial Syst. Eng. 1 (3), 301–320. doi:10.1504/ijise.2006.009791
Kooiman, A. G. (2000). Modelling steel fibre reinforced concrete for structural design. Berlin, Germany: Springer.
Krieger, I. M., and Dougherty, T. J. (1959). A mechanism for non-Newtonian flow in suspensions of rigid spheres. Trans. Soc. Rheology 3 (1), 137–152. doi:10.1122/1.548848
Kristombu Baduge, S., Mendis, P., Lee, L., Vanissorn, V., and Thilakaratne, P. (2023). “Importance of selecting suitable coarse aggregate to produce very-high-strength concrete (>100 MPa),” in Proceedings of the Australasian conference on the mechanics of structures and materials
Kristombu Baduge, S., Mendis, P., San Nicolas, R., Rupasinghe, M., and Portella, J. (2020). Aggregate-dependent approach to formulate and predict properties of high-strength and very-high-strength concrete. J. Mater. Civ. Eng. 32 (4), 04020053. doi:10.1061/(asce)mt.1943-5533.0003055
Le, T. T., Austin, S. A., Lim, S., Buswell, R. A., Gibb, A. G. F., and Thorpe, T. (2012b). Mix design and fresh properties for high-performance printing concrete. Mater. Struct. 45 (8), 1221–1232. doi:10.1617/s11527-012-9828-z
Le, T. T., Austin, S. A., Lim, S., Buswell, R. A., Gibb, A. G., and Thorpe, T. (2012a). Mix design and fresh properties for high-performance printing concrete. Mater. Struct. 45 (8), 1221–1232. doi:10.1617/s11527-012-9828-z
Le, T. T., Austin, S. A., Lim, S., Buswell, R. A., Law, R., Gibb, A. G. F., et al. (2012c). Hardened properties of high-performance printing concrete. Cem. Concr. Res. 42 (3), 558–566. doi:10.1016/j.cemconres.2011.12.003
Li, L., Yan, C., Zhang, N., Farooqi, M. U., Xu, S., and Deifalla, A. F. (2023). Flexural fracture parameters of polypropylene fiber reinforced geopolymer. J. Mater. Res. Technol. 24, 1839–1855. doi:10.1016/j.jmrt.2023.03.035
Li, V. C., Bos, F. P., Yu, K., McGee, W., Ng, T. Y., Figueiredo, S. C., et al. (2020). On the emergence of 3D printable engineered, strain hardening cementitious composites (ECC/SHCC). Cem. Concr. Res. 132, 106038. doi:10.1016/j.cemconres.2020.106038
Lim, S., Buswell, R., Le, T., Wackrow, R., Austin, S. A., Gibb, A., et al. (2011). Development of a viable concrete printing process. https://www.iaarc.org/publications/fulltext/S20-3.pdf.
Lim, S., Le, T., Webster, J., Buswell, R., Austin, A., Gibb, A., et al. (2023). “Fabricating construction components using layered manufacturing technology,” in Global innovation in construction conference (Loughborough, England: Loughborough University Leicestershire), 512–520.
Liu, D., Zhang, Z., Zhang, X., and Chen, Z. (2023a). 3D printing concrete structures: state of the art, challenges, and opportunities. Constr. Build. Mater. 405, 133364. doi:10.1016/j.conbuildmat.2023.133364
Liu, M., Wang, L., Li, Z., Sun, J., and Ma, G. (2023b). “Strength and toughness enhancement of 3D printed structures through steel wire mesh reinforcement,” in 1st international conference on 3D construction printing (Melbourne, Australia: Swinburne University of Technology).
Liu, Z., Li, M., Moo, G. S., Kobayashi, H., Wong, T. N., and Tan, M. J. (2023c). Effect of nanostructured silica additives on the extrusion-based 3D concrete printing application. J. Compos. Sci. 7 (5), 191. doi:10.3390/jcs7050191
Liu, Z., Li, M., Weng, Y., Wong, T. N., and Tan, M. J. (2019). Mixture Design Approach to optimize the rheological properties of the material used in 3D cementitious material printing. Constr. Build. Mater. 198, 245–255. doi:10.1016/j.conbuildmat.2018.11.252
Ma, G., Buswell, R., da Silva, W. R. L., Wang, L., Xu, J., and Jones, S. Z. (2022). Technology readiness: a global snapshot of 3D concrete printing and the frontiers for development. Cem. Concr. Res. 156, 106774. doi:10.1016/j.cemconres.2022.106774
Ma, G., Li, Y., Wang, L., Zhang, J., and Li, Z. (2020). Real-time quantification of fresh and hardened mechanical property for 3D printing material by intellectualization with piezoelectric transducers. Constr. Build. Mater. 241, 117982. doi:10.1016/j.conbuildmat.2019.117982
Ma, G., Li, Z., and Wang, L. (2018a). Printable properties of cementitious material containing copper tailings for extrusion based 3D printing. Constr. Build. Mater. 162, 613–627. doi:10.1016/j.conbuildmat.2017.12.051
Ma, G., Li, Z., Wang, L., Wang, F., and Sanjayan, J. (2019). Mechanical anisotropy of aligned fiber reinforced composite for extrusion-based 3D printing. Constr. Build. Mater. 202, 770–783. doi:10.1016/j.conbuildmat.2019.01.008
Ma, G., and Wang, L. (2018). A critical review of preparation design and workability measurement of concrete material for largescale 3D printing. Front. Struct. Civ. Eng. 12 (3), 382–400. doi:10.1007/s11709-017-0430-x
Ma, G., Wang, L., and Ju, Y. (2018b). State-of-the-art of 3D printing technology of cementitious material—an emerging technique for construction. Sci. China Technol. Sci. 61 (4), 475–495. doi:10.1007/s11431-016-9077-7
Marchment, T., and Sanjayan, J. (2020). Mesh reinforcing method for 3D concrete printing. Automation Constr. 109, 102992. doi:10.1016/j.autcon.2019.102992
Markin, V., Nerella, V. N., Schröfl, C., Guseynova, G., and Mechtcherine, V. (2019). Material design and performance evaluation of foam concrete for digital fabrication. Materials 12 (15), 2433. doi:10.3390/ma12152433
Marković, I. (2006). High-performance hybrid-fibre concrete: development and utilisation. Amsterdam, Netherlands: IOS Press.
Martinie, L., Rossi, P., and Roussel, N. (2010). Rheology of fiber reinforced cementitious materials: classification and prediction. Cem. Concr. Res. 40 (2), 226–234. doi:10.1016/j.cemconres.2009.08.032
Mechtcherine, V., Buswell, R., Kloft, H., Bos, F. P., Hack, N., Wolfs, R., et al. (2021). Integrating reinforcement in digital fabrication with concrete: a review and classification framework. Cem. Concr. Compos. 119, 103964. doi:10.1016/j.cemconcomp.2021.103964
Melenka, G. W., Cheung, B. K., Schofield, J. S., Dawson, M. R., and Carey, J. P. (2016). Evaluation and prediction of the tensile properties of continuous fiber-reinforced 3D printed structures. Compos. Struct. 153, 866–875. doi:10.1016/j.compstruct.2016.07.018
Meyer, C. (2004). Concrete materials and sustainable development in the USA. Struct. Eng. Int. 14 (3), 203–207. doi:10.2749/101686604777963757
Mousavi, S. S., and Dehestani, M. (2022). Influence of latex and vinyl disposable gloves as recycled fibers in 3D printing sustainable mortars. Sustainability 14 (16), 9908. doi:10.3390/su14169908
Murcia, D. H., Genedy, M., and Taha, M. R. (2020). Examining the significance of infill printing pattern on the anisotropy of 3D printed concrete. Constr. Build. Mater. 262, 120559. doi:10.1016/j.conbuildmat.2020.120559
Nair, S. A., Panda, S., Santhanam, M., Sant, G., and Neithalath, N. (2020). A critical examination of the influence of material characteristics and extruder geometry on 3D printing of cementitious binders. Cem. Concr. Compos. 112, 103671. doi:10.1016/j.cemconcomp.2020.103671
Nematollahi, B., Vijay, P., Sanjayan, J., Nazari, A., Xia, M., Naidu Nerella, V., et al. (2018a). Effect of polypropylene fibre addition on properties of geopolymers made by 3D printing for digital construction. Materials 11 (12), 2352. doi:10.3390/ma11122352
Nematollahi, B., Xia, M., Sanjayan, J., and Vijay, P. (2023). “Effect of type of fiber on inter-layer bond and flexural strengths of extrusion-based 3D printed geopolymer,” in Materials science forum (Wollerau, Switzerland: Trans Tech Publications), 155–162.
Nematollahi, B., Xia, M., Vijay, P., and Sanjayan, J. G. (2019). “Properties of extrusion-based 3D printable geopolymers for digital construction applications,” in 3D concrete printing technology (Amsterdam, Netherlands: Elsevier), 371–388.
Ogura, H., Nerella, V. N., and Mechtcherine, V. (2018). Developing and testing of strain-hardening cement-based composites (SHCC) in the context of 3D-printing. Materials 11 (8), 1375. doi:10.3390/ma11081375
Panda, B., Chandra Paul, S., and Jen Tan, M. (2017a). Anisotropic mechanical performance of 3D printed fiber reinforced sustainable construction material. Mater. Lett. 209, 146–149. doi:10.1016/j.matlet.2017.07.123
Panda, B., Paul, S. C., Hui, L. J., Tay, Y. W. D., and Tan, M. J. (2017b). Additive manufacturing of geopolymer for sustainable built environment. J. Clean. Prod. 167, 281–288. doi:10.1016/j.jclepro.2017.08.165
Panda, B., Paul, S. C., and Tan, M. J. (2017c). Anisotropic mechanical performance of 3D printed fiber reinforced sustainable construction material. Mater. Lett. 209, 146–149. doi:10.1016/j.matlet.2017.07.123
Paul, S. C., Van Zijl, G. P., Tan, M. J., and Gibson, I. (2018). A review of 3D concrete printing systems and materials properties: current status and future research prospects. Rapid Prototyp. J. 24 (4), 784–798. doi:10.1108/rpj-09-2016-0154
Perrot, A., Rangeard, D., and Courteille, E. (2018). 3D printing of earth-based materials: processing aspects. Constr. Build. Mater. 172, 670–676. doi:10.1016/j.conbuildmat.2018.04.017
Perrot, A., Rangeard, D., and Pierre, A. (2016). Structural built-up of cement-based materials used for 3D-printing extrusion techniques. Mater. Struct. 49 (4), 1213–1220. doi:10.1617/s11527-015-0571-0
Pham, L., Tran, P., and Sanjayan, J. (2020). Steel fibres reinforced 3D printed concrete: influence of fibre sizes on mechanical performance. Constr. Build. Mater. 250, 118785. doi:10.1016/j.conbuildmat.2020.118785
Qian, X., Zhou, X., Mu, B., and Li, Z. (2003). Fiber alignment and property direction dependency of FRC extrudate. Cem. Concr. Res. 33 (10), 1575–1581. doi:10.1016/s0008-8846(03)00108-x
Rehman, A. U., and Kim, J.-H. (2021). 3D concrete printing: a systematic review of rheology, mix designs, mechanical, microstructural, and durability characteristics. Materials 14 (14), 3800. doi:10.3390/ma14143800
Reiter, L., Wangler, T., Roussel, N., and Flatt, R. J. (2018). The role of early age structural build-up in digital fabrication with concrete. Cem. Concr. Res. 112, 86–95. doi:10.1016/j.cemconres.2018.05.011
Ribeiro, P. D., Krahl, P. A., Carrazedo, R., and Bernardo, L. F. (2023). Modeling the tensile behavior of fiber-reinforced strain-hardening cement-based composites: a review. Materials 16 (9), 3365. doi:10.3390/ma16093365
Robayo-Salazar, R., Martínez, F., Vargas, A., and Mejía de Gutiérrez, R. (2023). 3D printing of hybrid cements based on high contents of powders from concrete, ceramic and brick waste chemically activated with sodium sulphate (Na2SO4). Sustainability 15 (13), 9900. doi:10.3390/su15139900
Roussel, N. (2018). Rheological requirements for printable concretes. Cem. Concr. Res. 112, 76–85. doi:10.1016/j.cemconres.2018.04.005
Shakor, P., Renneberg, J., Nejadi, S., and Paul, G. (2023c). "Optimisation of different concrete mix designs for 3D Printing by utilising 6DOF industrial robot", in: Proceedings of the ISARC 2017-proceedings of the 34th international symposium on automation and robotics in construction), Taipei, Taiwan
Sanjayan, J. G., Nematollahi, B., Xia, M., and Marchment, T. (2018). Effect of surface moisture on inter-layer strength of 3D printed concrete. Constr. Build. Mater. 172, 468–475. doi:10.1016/j.conbuildmat.2018.03.232
Santos, D. S., Santos, P. M., and Dias-da-Costa, D. (2012). Effect of surface preparation and bonding agent on the concrete-to-concrete interface strength. Constr. Build. Mater. 37, 102–110. doi:10.1016/j.conbuildmat.2012.07.028
Scott, C. (2016). Chinese construction company 3D prints an entire two-story house on-site in 45 days. https://3dprint.com/138664/huashang-tengda-3d-print-house/.
Sedran, T. (1999) Rheologie et rhéométrie des bétons. Application aux bétons autonivelants.(Rheology and Rheometry of concrete. Application to SCC) Dotcoral Thesis. France: Ecole Nationale des Ponts et Chaussées.
Shakor, P., Gowripalan, N., and Rasouli, H. (2021). Experimental and numerical analysis of 3D printed cement mortar specimens using inkjet 3DP. Archives Civ. Mech. Eng. 21 (2), 58. doi:10.1007/s43452-021-00209-3
Shakor, P., Nejadi, S., and Gowripalan, N. (July 2023a). "Effect of heat curing and E6-glass fibre reinforcement addition on powder-based 3DP cement mortar", in: Proceedings of the second RILEM international conference on concrete and digital fabrication: digital concrete 2020, Digital Concrete, 508–515.
Shakor, P., Nejadi, S., and Paul, G. (2019b). A study into the effect of different nozzles shapes and fibre-reinforcement in 3D printed mortar. Materials 12 (10), 1708. doi:10.3390/ma12101708
Shakor, P., Nejadi, S., and Paul, G. (2019a). "An investigation into the effects of deposition orientation of material on the mechanical behaviours of the cementitious powder and gypsum powder in Inkjet 3D printing", in: Proceedings of the 36th international symposium on automation and robotics in construction, ISARC 2019), Banff, Canada
Shakor, P., Nejadi, S., Paul, G., and Gowripalan, N. (2023b). Effects of different orientation angle, size, surface roughness, and heat curing on mechanical behavior of 3D printed cement mortar with/without glass fiber in powder-based 3DP. 3D Print. Addit. Manuf. 10 (2), 330–355. doi:10.1089/3dp.2021.0067
Shakor, P., Nejadi, S., Sutjipto, S., Paul, G., and Gowripalan, N. (2020b). Effects of deposition velocity in the presence/absence of E6-glass fibre on extrusion-based 3D printed mortar. Addit. Manuf. 32, 101069. doi:10.1016/j.addma.2020.101069
Shen, B., Hubler, M., Paulino, G. H., and Struble, L. J. (2008). Functionally-graded fiber-reinforced cement composite: processing, microstructure, and properties. Cem. Concr. Compos. 30 (8), 663–673. doi:10.1016/j.cemconcomp.2008.02.002
Soltan, D. G., and Li, V. C. (2018). A self-reinforced cementitious composite for building-scale 3D printing. Cem. Concr. Compos. 90, 1–13. doi:10.1016/j.cemconcomp.2018.03.017
Sonebi, M., Rubio, M., Amziane, S., and Perrot, A. (September 2023). "Mechanical properties of 3d printing bio-based fiber cement-based materials", in: Proceedings of the RILEM 1st international conference on digital fabrication with concrete, Zurich), 50–51.
Su, H., and Xu, J. (2013). Dynamic compressive behavior of ceramic fiber reinforced concrete under impact load. Constr. Build. Mater. 45, 306–313. doi:10.1016/j.conbuildmat.2013.04.008
Su, Y., Li, J., Wu, C., Wu, P., and Li, Z.-X. (2016a). Effects of steel fibres on dynamic strength of UHPC. Constr. Build. Mater. 114, 708–718. doi:10.1016/j.conbuildmat.2016.04.007
Su, Y., Li, J., Wu, C., Wu, P., and Li, Z.-X. (2016b). Influences of nano-particles on dynamic strength of ultra-high performance concrete. Compos. Part B Eng. 91, 595–609. doi:10.1016/j.compositesb.2016.01.044
Sun, J., Aslani, F., Lu, J., Wang, L., Huang, Y., and Ma, G. (2021). Fibre-reinforced lightweight engineered cementitious composites for 3D concrete printing. Ceram. Int. 47 (19), 27107–27121. doi:10.1016/j.ceramint.2021.06.124
Swamy, R., and Mangat, P. S. (1974). Influence of fibre-aggregate interaction on some properties of steel fibre reinforced concrete. Materiaux Constructions/Materials Struct. 7 (41), 307–314. doi:10.1007/bf02473840
Takashima, H., Miyagai, K., Hashida, T., and Li, V. C. (2003). A design approach for the mechanical properties of polypropylene discontinuous fiber reinforced cementitious composites by extrusion molding. Eng. Fract. Mech. 70 (7-8), 853–870. doi:10.1016/s0013-7944(02)00154-6
Tay, Y. W. D., Panda, B., Paul, S. C., Noor Mohamed, N. A., Tan, M. J., and Leong, K. F. (2017). 3D printing trends in building and construction industry: a review. Virtual Phys. Prototyp. 12 (3), 261–276. doi:10.1080/17452759.2017.1326724
Toutou, Z., and Roussel, N. (2006). Multi scale experimental study of concrete rheology: from water scale to gravel scale. Mater. Struct. 39, 189–199. doi:10.1617/s11527-005-9047-y
Vergara, L. A., and Colorado, H. A. (2020). Additive manufacturing of Portland cement pastes with additions of kaolin, superplastificant and calcium carbonate. Constr. Build. Mater. 248, 118669. doi:10.1016/j.conbuildmat.2020.118669
Wang, L., Tian, Z., Ma, G., and Zhang, M. (2020). Interlayer bonding improvement of 3D printed concrete with polymer modified mortar: experiments and molecular dynamics studies. Cem. Concr. Compos. 110, 103571. doi:10.1016/j.cemconcomp.2020.103571
Wang, Z.-L., Liu, Y.-S., and Shen, R. (2008). Stress–strain relationship of steel fiber-reinforced concrete under dynamic compression. Constr. Build. Mater. 22 (5), 811–819. doi:10.1016/j.conbuildmat.2007.01.005
Weng, Y., Lu, B., Li, M., Liu, Z., Tan, M. J., and Qian, S. (2018). Empirical models to predict rheological properties of fiber reinforced cementitious composites for 3D printing. Constr. Build. Mater. 189, 676–685. doi:10.1016/j.conbuildmat.2018.09.039
Wiemer, N., Wetzel, A., Schleiting, M., Krooß, P., Vollmer, M., Niendorf, T., et al. (2020). Effect of fibre material and fibre roughness on the pullout behaviour of metallic micro fibres embedded in UHPC. Mater 13 (14), 3128. doi:10.3390/ma13143128
Wolfs, R., Bos, F., and Salet, T. (2019). Hardened properties of 3D printed concrete: the influence of process parameters on interlayer adhesion. Cem. Concr. Res. 119, 132–140. doi:10.1016/j.cemconres.2019.02.017
Wu, Z., Memari, A. M., and Duarte, J. P. (2022). State of the art review of reinforcement strategies and technologies for 3D printing of concrete. Energies 15 (1), 360. doi:10.3390/en15010360
Wu, Z., Shi, C., He, W., and Wang, D. (2017). Static and dynamic compressive properties of ultra-high performance concrete (UHPC) with hybrid steel fiber reinforcements. Cem. Concr. Compos. 79, 148–157. doi:10.1016/j.cemconcomp.2017.02.010
Xiao, Y., Zhang, S., Chen, J., Guo, B., and Chen, D. (2023). Mechanical performance of 3D-printed polyethylene fibers and their durability against degradation. Mater 16 (14), 5182. doi:10.3390/ma16145182
Yammine, J., Chaouche, M., Guerinet, M., Moranville, M., and Roussel, N. (2008). From ordinary rhelogy concrete to self compacting concrete: a transition between frictional and hydrodynamic interactions. Cem. Concr. Res. 38 (7), 890–896. doi:10.1016/j.cemconres.2008.03.011
Yang, Y., Wu, C., Liu, Z., Liang, X., and Xu, S. (2019). Experimental investigation on the dynamic behaviors of UHPFRC after exposure to high temperature. Constr. Build. Mater. 227, 116679. doi:10.1016/j.conbuildmat.2019.116679
Yang, Y., Wu, C., Liu, Z., Wang, H., and Ren, Q. (2022). Mechanical anisotropy of ultra-high performance fibre-reinforced concrete for 3D printing. Cem. Concr. Compos. 125, 104310. doi:10.1016/j.cemconcomp.2021.104310
Ye, J., Cui, C., Yu, J., Yu, K., and Dong, F. (2021). Effect of polyethylene fiber content on workability and mechanical-anisotropic properties of 3D printed ultra-high ductile concrete. Constr. Build. Mater. 281, 122586. doi:10.1016/j.conbuildmat.2021.122586
Yoo, D.-Y., Banthia, N., and Yoon, Y.-S. (2016). Predicting the flexural behavior of ultra-high-performance fiber-reinforced concrete. Cem. Concr. Compos. 74, 71–87. doi:10.1016/j.cemconcomp.2016.09.005
Yu, K., Li, L., Yu, J., Xiao, J., Ye, J., and Wang, Y. (2018). Feasibility of using ultra-high ductility cementitious composites for concrete structures without steel rebar. Eng. Struct. 170, 11–20. doi:10.1016/j.engstruct.2018.05.037
Yu, R., Spiesz, P., and Brouwers, H. (2014). Mix design and properties assessment of ultra-high performance fibre reinforced concrete (UHPFRC). Cem. Concr. Res. 56, 29–39. doi:10.1016/j.cemconres.2013.11.002
Zareiyan, B., and Khoshnevis, B. (2018). Effects of mixture ingredients on extrudability of concrete in Contour Crafting. Rapid Prototyp. J. 24 (4), 722–730. doi:10.1108/RPJ-01-2017-0006
Zareiyan, B., and Khoshnevis, B. (2017). Effects of interlocking on interlayer adhesion and strength of structures in 3D printing of concrete. Automation Constr. 83, 212–221. doi:10.1016/j.autcon.2017.08.019
Zhang, H., Zhu, L., Zhang, F., and Yang, M. (2021). Effect of fiber content and alignment on the mechanical properties of 3D printing cementitious composites. Materials 14 (9), 2223. doi:10.3390/ma14092223
Zhang, Y., Zhang, Y., Liu, G., Yang, Y., Wu, M., and Pang, B. (2018). Fresh properties of a novel 3D printing concrete ink. Constr. Build. Mater. 174, 263–271. doi:10.1016/j.conbuildmat.2018.04.115
Zhao, Y., Wu, X., Zhu, L., Yang, Z., Wang, Y., and Xi, X. (2021). The influence of polypropylene fiber on the working performance and mechanical anisotropy of 3D printing concrete. J. Adv. Concr. Technol. 19 (12), 1264–1274. doi:10.3151/jact.19.1264
Zhou, W., McGee, W., Gökçe, H. S., and Li, V. C. (2023). A bio-inspired solution to alleviate anisotropy of 3D printed engineered cementitious composites (3DP-ECC): knitting/tilting filaments. Automation Constr. 155, 105051. doi:10.1016/j.autcon.2023.105051
Zhu, B., Pan, J., Nematollahi, B., Zhou, Z., Zhang, Y., and Sanjayan, J. (2019). Development of 3D printable engineered cementitious composites with ultra-high tensile ductility for digital construction. Mater. Des. 181, 108088. doi:10.1016/j.matdes.2019.108088
Ziaee, M., Johnson, J. W., and Yourdkhani, M. (2022). 3D printing of short-carbon-fiber-reinforced thermoset polymer composites via frontal polymerization. ACS Appl. Mater. Interfaces 14 (14), 16694–16702. doi:10.1021/acsami.2c02076
Keywords: additive manufacturing, 3D printing, 3D printing concrete (3DPC), fibre reinforcement, sustainable construction materials
Citation: Zhou Y, Althoey F, Alotaibi BS, Gamil Y and Iftikhar B (2023) An overview of recent advancements in fibre-reinforced 3D printing concrete. Front. Mater. 10:1289340. doi: 10.3389/fmats.2023.1289340
Received: 05 September 2023; Accepted: 28 September 2023;
Published: 24 October 2023.
Edited by:
Mehran Khan, University College Dublin, IrelandReviewed by:
Arslan Akbar, City University of Hong Kong, Hong Kong SAR, ChinaPshtiwan Shakor, Sulaimani Polytechnic University, Iraq
Copyright © 2023 Zhou, Althoey, Alotaibi, Gamil and Iftikhar. This is an open-access article distributed under the terms of the Creative Commons Attribution License (CC BY). The use, distribution or reproduction in other forums is permitted, provided the original author(s) and the copyright owner(s) are credited and that the original publication in this journal is cited, in accordance with accepted academic practice. No use, distribution or reproduction is permitted which does not comply with these terms.
*Correspondence: Yi Zhou, emhvdXlpMTc2NUBzaW5hLmNvbQ==; Yaser Gamil, eWFzZXIuZ2FtaWxAbHR1LnNl