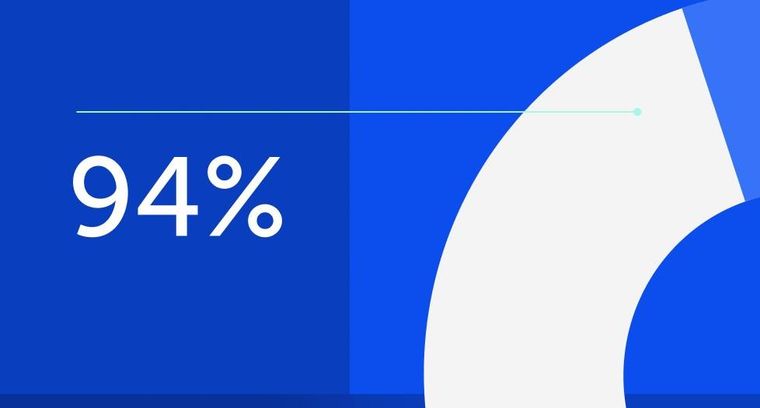
94% of researchers rate our articles as excellent or good
Learn more about the work of our research integrity team to safeguard the quality of each article we publish.
Find out more
ORIGINAL RESEARCH article
Front. Mater., 27 November 2023
Sec. Smart Materials
Volume 10 - 2023 | https://doi.org/10.3389/fmats.2023.1268975
This article is part of the Research TopicSmart Textiles for Fluid-Driven Soft Wearable RoboticsView all 5 articles
Linkage fabric structures show potential as assistive technology that can provide support and assistance for individuals with specific mobility and disability needs. The core functionality of these fabrics is the ability to passively and actively control the mechanics of each link producing a structure with variable and adjustable stiffness. Current actuators have shown limited ability to produce active stiffening within a fabric structure without the addition of a continuous energy supply to the structure, therefore, limiting its use as wearable assistive technology. Here, we address the energy supply problem and show the novel use of sodium acetate trihydrate (SAT) in the linkage structures to induce mechanical stiffening through a phase change induced by an electric impulse. We find that a SAT aqueous concentration of 55 wt% is optimum to achieve a stable supercooled liquid (to ambient temperature) and effective electrical nucleation from liquid to solid, which provides robust locking mechanism of individual linkages able to withstand mechanical torsion up to 200 mNm. We demonstrate proof of principle through the integration of SAT into one- and two-dimensional linkage structures and their nearly instantaneous stiffening within each link by enabling electrically controlled actuation.
Assistive technology plays an important role in improving the quality of life for individuals with disabilities, the elderly and infirm. Traditionally, these have been mechanical devices to aid mobility and activity such as wheelchairs, prosthetics, and orthotics. The drawbacks of some of these technologies include limited functionality, discomfort, and aesthetic concerns (Shinohara and Wobbrock, 2011; Doughty and Appleby, 2016; Marti and Recupero, 2022). With the advancements in material innovation and soft robotics in recent years, new types of wearable technologies are emerging that address the user requirements of higher adaptability, while reducing bulkiness and weight (Walsh et al., 2006; Thalman and Artemiadis, 2020; Martinez-Hernandez et al., 2021). At the heart of these new materials is their bespoke mechanics and ability to adapt to their user’s needs. One approach has been to develop linkage fabric structures (Ransley et al., 2017; Ploszajski et al., 2019; Wang et al., 2021b). The ability to design linkage fabrics to actively modulate stiffness on demand is envisioned to support joints and facilitate limb movement, as illustrated in Figure 1.
FIGURE 1. Schematic of wearable assistive linkage fabric: (A) a demonstration of how wearable assistive devices can actively modulate stiffness on demand is envisioned to support joints and facilitate limb movement; (B) showing the details of the linkage fabric consisting of block-shaped links that are connected through flexible joints that can be locked and unlocked on demand changing the stiffness of.
Progress in designing and 3D printing of bespoke linkage fabrics has been possible through the development of additive manufacturing technologies, such as selective laser sintering (SLS). These additive manufacturing techniques allow for the design of the linkage fabric with tailored geometries so that these wearable technologies can answer individual needs. Designed to be worn like clothes, these linkage fabrics could allow wearers to overcome barriers and participate actively in various aspects of life.
The tunability of these fabrics can be achieved through passive means like granular jamming (Wang et al., 2021b; Hu et al., 2023; Tian et al., 2023; Xu et al., 2023), where the geometry of the links is modified throughout the stiffening process, or through active means (Ransley et al., 2017). The latter allows for the stiffness of the fabric to be changed locally through the actuation of each link in contrast to the former, where the whole fabric is manipulated at once. However, to maintain the desired stiffness and actuation of the fabric, both approaches require constant energy input such as a vacuum compressor or electric power, limiting their applications. There is a need for a method that can create a change in fabric stiffness without needing constant energy input to maintain it, the so-called locking of the structure.
Sodium acetate trihydrate (SAT) is an inorganic substance known for its high exothermic enthalpy of solidification, which is typically utilised for thermal energy storage (Sandnes and Rekstad, 2006; Jin et al., 2014; Wang et al., 2021a). When heating SAT crystals in water above 77.6°C, the crystals fully dissolve. When cooling these SAT solutions, an unusual property occurs. They can undergo a high degree of supercooling before solidification. According to Sandes and Rekstad (2006), the SAT solution can, once it reaches equilibrium with its surroundings, remain a supercooled liquid for an indefinite period. Remarkably, solidification of the supercooled liquid can be initiated within seconds by a low-voltage electric field (Wang et al., 2021a), making SAT a promising actuator for the active stiffening of linkage fabrics.
However, its mechanical properties and application to stiffness modulation have not yet been investigated which is the aim of this paper. Here we investigate SAT as a stiffening actuator for adaptable linkage fabrics. This paper discusses the novel use of SAT to create a linkage structure with variable stiffness that can maintain its shape without an external energy supply. We characterise the mechanical properties of the material and showcase an example of a one-dimensional fabric linkage structure with variable stiffness using SAT.
Sodium acetate solutions with concentrations of 40 wt% to 56 wt%, in 2 wt% intervals, were prepared using sodium acetate trihydrate crystals (99% purity, Fisher Scientific) and distilled water. The salt hydrate was diluted to obtain the desired concentration and then heated above its phase transition temperature (around 58°C) until all crystals were fully dissolved. These solutions were sealed in 50 mL polypropylene (PP) test tubes to reduce evaporation of the water. The preparation of the electrodes for electric nucleation was followed as described by Dong et al. (2022). In short, two Ag-electrodes (diameter,
FIGURE 2. SAT characterisation test setup, using a 50 mL PP test tube filled with sodium acetate solutions ranging from 40 wt% to 56 wt% sodium acetate, two Ag-electrodes and a DS18B20 thermo sensor.
To test the success rate of the SAT solutions to supercool and electrically nucleate, the test tubes were heated in a water bath to a temperature of 70°C and left for a time of 30, 60 and 80 min before letting them cool down to room temperature of 25°C. The solutions were categorised as successfully supercooled when a continuous cooling curve was measured using the temperature sensor and no crystal growth was visible to the naked eye, as described (Dong et al., 2022). Following the successful supercooling, a DC voltage of 5 V was applied to the electrodes (at a depth (L1) of 50 mm and with a gap (L2) of 20 mm) for 5 s. Nucleation of the solutions was deemed successful if crystal growth was observed during the application of the voltage and a spike in temperature was measured. The test procedures were repeated for ten iterations with three batches of solutions of the prepared concentrations (40 wt% to 56 wt%).
The influence of electrode placement on the success rate of the nucleation was investigated by preparing three batches of solutions with 55 wt% sodium acetate concentration. The electrodes were placed at varied depths (L1, Figure 2) of 5–30 mm (for a 20 mm gap) and gaps (L2, Figure 2) of 10–40 mm (for a depth of 30 mm). The solutions were heated to 70 °C and left for a heating period of 80 min before cooling them slowly to room temperature, measuring the nucleation effectiveness post-cooling using the same criteria as described before.
Three sets of experiments were carried out using a TI Discovery-Hybrid-Rheometer 3 (DHR-3) with a Peltier concentric cylinder and a vane rotor setup to determine the viscosity of the SAT solutions. The first experiment used three batches of 45 wt%, 50 wt% and 55 wt% sodium acetate at 70°C to determine the viscosity in a liquid state. The crystallisation of the three solutions was then investigated with a temperature ramp from 70°C to 25°C, measuring the viscosity change upon cooling, with a constant movement to avoid supercooling of the solution substituting the need of electric nucleation. Thirdly, a torque ramp ranging from 10 to 200,000 μNm was systematically applied to the solidified material exploring the yield point of the three crystallised solution concentrations, over increased torque.
The integration of the phase change material as an actuator in a linkage fabric was realised using a two-part design. The linkage nodes consists of a rigid structure with a chamber in which the phase change material is placed to surround a movable joint that is partly suspended in the chamber and connects it to other node points, see Figures 3A, B To test electrical electric nucleation and cyclability of the phase change material in such a fabric, a larger scale version of a single node was designed to better facilitate insertion of electronics, see Figure 4.
FIGURE 3. Linkage fabric prototype with the sodium acetate solution: (A) as a conceptual drawing showing the link design containing phase change liquid; (B) the 3D printed prototype design assembled as a 3 × 3 fabric structure.
FIGURE 4. The link prototype with the sodium acetate solution: (A) as a conceptual drawing showing the possible movements of the link; (B,C) the 3D printed prototype design with Ag-electrodes and power supply connected.
Both prototypes were designed using Autodesk Inventor and 3D printed using an Elegoo Mars 3 MSLA printer with photo-responsive resins from the same company. For the first design shown in (Figure 3) consists of three printed parts, one movable joint structure and two parts making up the rigid support structure in which the phase change material is filled. The second design shown in (Figure 4), two printed parts are connected by a flexibl cover consisting of a latex sheet that was cut to size, placed, and fixated using rubber bands. The openings in the cover for the joint shaft and electrodes have been sealed using hot glue and silicone sealant. Both designs were manually assembled and filled with a 55 wt% SAT solution, subsequently heated to 60°C.
To assess the feasibility of using SAT as an actuator, a characterisation of the crystallisation and material properties was carried out. The success rate of supercooling the solution at different concentrations over different heating periods was investigated, as shown in Figure 5A. All the SAT solutions showed the ability to supercool. The effectiveness of the solution increases with longer heating periods. Specifically, average success rates for all concentrations of 46%, 59%, and 71% were observed for heating periods of 30, 60, and 80 min, respectively. The SAT of 52 wt% demonstrated the highest supercooling effectiveness with a mean of 83% (±5%) at 80 min of the heating period. For periods of 30 and 60 min, the SAT solution of 46 wt% was most successful having achieved success rates of 63% (±12%) and 67% (±13%), respectively. These results indicate that concentration of the solution does not directly affect the effectiveness of solutions to supercool within the tested range. However, high variability may indicate that there are unaddressed factors such as the heating and cooling rate of the solutions, the effect of movement of the PP test tubes during the cooling process, or the influence of electrodes and temperature sensor (Figure 2), which are submerged in the liquid during cooling.
FIGURE 5. Experimental testing results: (A) effectiveness of the solution to supercool at different heating times for different solutions; (B) electric nucleation effectiveness of different solutions; (C) effectiveness of a 55 wt% sodium acetate solution to nucleate at different electrode depths; (D) effectiveness of a 55 wt% sodium acetate solution to nucleate at different distance between electrodes; Error bars present standard deviation (n = 30).
Figure 5B shows the shows the success rate of electrical nucleation of SAT crystals for the different supercooled solutions. The graph shows that solutions with higher concentrations are easier to electrically nucleate. Solutions with 56 wt% SAT achieve a success rate of 65% (±5%) compared to 40 wt% SAT solutions with only 33% (± 5%) success rate. The highest success rate was achieved with a SAT concentration of 54 wt% having an effectiveness to electrically nucleate of 73% (± 5%). This is evidence to support the theory that electrical nucleation of the supercooled SAT is triggered by a higher SAT concentration that forms around the surface of the anode due to the electric field generated when applying voltage to the electrodes Wang et al. (2021a). Higher number of nucleation sites would therefore be present in the liquid making crystallisation more likely.
The influence of depth submerged and distance between electrodes were also investigated (see Figure 2 for experimental set-up). Figure 5C shows that the depth of submersion influences the nucleation success rate. Electrodes with depths below 15 mm achieved relatively low success rates between 3% and 13%, compared to depths >20 mm which had higher success rates in the range of 53%–67%. Figure 5D shows that the distance between electrodes weakly affects the success rate for the tested parameters. All distances achieve a nucleation success rate between 50% and 60%, with the distance of 20 cm showing the highest rate at 67% (±12%). Concluding that depths of >20 mm are desirable for electric nucleation achieving higher success rates, while gaps between electrodes do not affect the success rate for the tested lengths.
The mechanical properties of the solution when undergoing a phase transition from a liquid to a solid state was investigated to understand the capability of SAT to give adequate stiffness to the linkage nodes in fabrics. The viscosity change of the solution from its liquid to the solid state was measured to capture the change in material properties during crystallisation. The results show that viscosity is a function of SAT concentration with values of 2.66 mPa s, 3.28 mPa s, and 3.95 mPa s for the solutions of 45 wt%, 50 wt% and 55 wt% sodium acetate, respectively (Figure 6A). This shows that the viscosity increases by around 0.6–0.7 mPa s per 5 wt% SAT over this concentration range. At reduced temperatures, the viscosity of the three solutions is shown to remain steady until the phase transition point is reached, and crystal growth can be observed through a rapid increase of viscosity, see Figure 6B. The points at which phase transition is theoretically possible are depicted as dashed lines in Figure 6B and calculated using the following formula (Ma et al., 2017) where x is the weight percentage of the solution:
FIGURE 6. Mechanical testing results: (A) Viscosity of sodium acetate solutions at 70 °C at three different concentrations compared to distilled water (error bars present std deviation (n = 9)); (B) Viscosity change of three sodium acetate solutions following decreasing temperature (error bars present std deviation (n = 9)); (C) Viscosity change over increasing torque of three different sodium acetate solutions from a solid state.
The experimental results from Figure 6B demonstrate that solutions with lower SAT concentrations exhibit nucleation at comparatively lower temperatures when contrasted with solutions possessing higher concentrations. These findings affirm the underlying theoretical relationship shown in Eq. 1.
Lower-concentration SAT solutions also show a less steep increase in viscosity when approaching the phase transition. Over a temperature range of 3 °C, the 45 wt% solution only reached viscosity of 35 Pa s (±21 Pa s) whereas the 55 wt% achieved 5300 Pa s (±1400 Pa s). Corresponding to an increase of viscosity by a factor of 13,000 for 45 wt% solution and a factor of 1.3 M by the 55 wt% solution for the 3°C period.
Furthermore, the projected stiffness of the material is indicated to be proportional to the concentration of the solution, as higher concentrated SAT solutions achieve higher viscosities than lower ones, as shown in Figure 6C. Solutions with 45 wt% SAT reached a stable viscosity of around 378 Pa s (±48 Pa s) for torques of up to 10 mN m, before entering a rapid yielding condition (breaking of the crystals). The viscosity of SAT solids with a concentration of 50 wt%, were found to be stable at around 62 kPa s (±2 kPa s) before yielding at a torque of 87 mN m and solutions with 55 wt% showed a viscosity of 994 kPa s (±3 kPa) with torques up to 200 mN m, reaching the limits of the rheometer. Conventional mechanical testing using tensile and compression tests proved challenging due to the low cohesion of the solid SAT samples, which disintegrated during the moulding process.
A linkage fabric consisting of 3 × 3 arrangement of link nodes with encapsulated SAT solution was fabricated. The linkage fabric demonstrated a clear switch between a flexible and rigid state when the phase change was initiated, see Figure 7A. The phase change from a liquid (flexible) to a solid (rigid) state was nucleated through cooling the fabric below its transition temperature and dropping crystals into the chamber to generate crystal growth. The fabric was clamped at one corner, as shown in Figure 7A, flexible in a x-z plane when the solution was liquid. Made rigid when stretched along the x-axis it is able to resist gravitational forces. Applying the flexible structure on a forearm proved the concept of a wearable material, where the linkage structure can create a good fit around the forearm when flexible (Figure 7B) and maintain this shape when transformed to a rigid state (Figure 7C).
FIGURE 7. Two-dimensional linkage fabric: (A) flexible state of the fabric with the solution in liquid from (2) and fabric when the solution is solid (1); (B) fabric in liquid state wrapped around forearm; (C) fabric in solid state while maintaining curvature of forearm.
Although the fabric showed the desired locking behaviour and rigidity, mechanical tests showed that the strength imparted to the joints through solidification of SAT was small. The structure was found to be incapable of withstanding loads exceeding 10 g, above which it underwent structural failure at the nodes. We then looked at the reusability of the phase change material after its nucleation. Here, we identified challenges stemming from the inherent difficulty of reheating the structure without causing water evaporation or any form of the SAT leakage, thereby hindering the potential for cyclic use of this fabric design.
To test the potential of electrical nucleation in this design concept, a combination of three bigger-sized links was assembled into a simple one-dimensional linkage fabric able to deform in three degrees of freedom (x-y plane and rotation around the z-axis). Figure 8A shows this structure in both the flexible and rigid state. The structure could be moved freely when all links are set in a flexible state, the sodium acetate solutions being liquid. Upon electrical nucleation of the supercooled SAT the structure was stiffened within 1–5 s, fixating the movable shaft structure in position. The flexibility of movement of the shaft was restored by reheating the solution in the link structure using a hot water bath at 80°C.
FIGURE 8. One dimensional linkage structure: (A) flexible state of the structure with a solution in liquid form (2) and structure when the solution is solid without weight attached (1) with dots symbolising curvature calculation points; (B) plot showing the curvature of the structure measured as a function of weight.
The stiffness of the fixed fabric was tested by applying a load upon its free movable end and fixating it at the other. Curvature k was measured as shown in Figure 8A and calculated using the following formula, where x and y are the coordinates of the points as indicated in Figure 8A:
Figure 8B shows that the stiffened structure bent as the load increased reaching the curvature of the flexible structure when subjected to loads of 50 g. Heating up the links restored the linkage fabric flexibility. However, cyclic heating and stiffness of the link prototype proved difficult due to the degradation of the SAT solution. This resulted in observed decreased effectiveness of supercooling. After one to three cycles of nucleation and reheating the solutions were not able to supercool anymore. This is likely to be due to concentration changes in the SAT solution due to water evaporation due to the liquid being able to penetrate connection points between the elastic cover and electrodes/movable shaft structure when in motion. We also found that the 3D-printed plastics (photo polymeric resins) are not optimum to achieve repeated nucleation of the SAT because water absorption and evaporation through the plastic were observed when stored for multiple days and weeks.
Concerns about the cyclability of SAT (for thermal energy storage applications) have been previously mentioned in the literature (Hu et al., 2011; Wang et al., 2021a). The use of different vessel materials and better seals might improve cyclability (Wang et al., 2021a). However, as with all salt hydrates, SAT also suffers from phase separation over repeated cycles, reducing the heat storage capacity of the material as mentioned by (Dannemand et al., 2015). The addition of water has been cited as an effective way to increase cyclability while decreasing the energy density of the material (Araki et al., 1995). Others have used thickening agents such as carboxyl methyl cellulose (CMC) to reduce the phase separation in the solution over repeated cycles, however it has a detrimental impact on the supercooling effect (Ryu et al., 1992; Hu et al., 2011). There is also a need for further research to investigate the mechanical effects of additives to SAT before the true capabilities of the material’s use to stiffen linkage structures can be fully assessed.
Although there are issues to solve, what this work shows is the potential of the approach. We set out the novel approach that Sodium Acetate Trihydrate can be used as a stiffening agent at linkage nodes for a fabric structure without need of a constant energy supply. The use of phase change materials with the ability to transform from a low viscosity liquid to a stiff and strong solid rapidly upon electrical nucleation, opens a new possibility on stiffening in fluid actuated soft robots. Difficulties remain for the use of SAT, in terms of cyclability, mechanical properties and storage, nevertheless the work clearly shows that the concept does have clear promise and the search for a more ideal phase change material could result in significant progress.
We have shown the novel use of the phase change material sodium acetate trihydrate (SAT) to create mechanical stiffening through electric nucleation of the supercooled SAT solution. A material concentration of 55 wt% SAT was shown to be optimum for this application in terms of electric nucleation effectiveness and mechanical properties. We integrated SAT into a 3 × 3 two-dimensional fabric structure showing the capabilities of the material to induce mechanical stiffening within the fabric. We also prototyped a one-dimensional linkage fabric, showing that electrical actuation works and results in fabric rigidity without the continual application of power. Our study presents a novel advancement in the use of SAT for mechanical stiffening through electric nucleation of linkage structures. Our results establish a compelling foundation for future research in the field of phase change actuated linkage fabrics.
The raw data supporting the conclusion of this article will be made available by the authors, without undue reservation.
CP: Conceptualization, Methodology, Writing–original draft. EP: Conceptualization, Methodology, Supervision, Validation, Writing–review and editing. DP: Project administration, Writing–review and editing. MMc: Project administration, Supervision, Writing–review and editing. MMo: Project administration, Resources, Supervision, Writing–review and editing.
The author(s) declare financial support was received for the research, authorship, and/or publication of this article. This work was funded by the UKRI under grant EP/V011804/1; the UCL Institute of Making and the University College London, which we gratefully acknowledge.
The authors declare that the research was conducted in the absence of any commercial or financial relationships that could be construed as a potential conflict of interest.
All claims expressed in this article are solely those of the authors and do not necessarily represent those of their affiliated organizations, or those of the publisher, the editors and the reviewers. Any product that may be evaluated in this article, or claim that may be made by its manufacturer, is not guaranteed or endorsed by the publisher.
Araki, N., Futamura, M., Makino, A., and Shibata, H. (1995). Measurements of thermophysical properties of sodium acetate hydrate. Int. J. Thermophys. 16, 1455–1466. doi:10.1007/BF02083553
Dannemand, M., Schultz, J. M., Johansen, J. B., and Furbo, S. (2015). Long term thermal energy storage with stable supercooled sodium acetate trihydrate. Appl. Therm. Eng. 91, 671–678. doi:10.1016/j.applthermaleng.2015.08.055
Dong, C., Qi, R., Yu, H., and Zhang, L. (2022). Electrically-controlled crystallization of supercooled sodium acetate trihydrate solution. Energy Build. 260, 111948. doi:10.1016/J.ENBUILD.2022.111948
Doughty, K., and Appleby, A. (2016). Wearable devices to support rehabilitation and social care. J. Assist. Technol. 10, 51–63. doi:10.1108/JAT-01-2016-0004
Hu, P., Lu, D. J., Fan, X. Y., Zhou, X., and Chen, Z. S. (2011). Phase change performance of sodium acetate trihydrate with AlN nanoparticles and CMC. Sol. Energy Mater. Sol. Cells 95, 2645–2649. doi:10.1016/J.SOLMAT.2011.05.025
Hu, Z., Ahmed, A., Wan, W., Watanabe, T., and Harada, K. (2023). A stiffness-changeable soft finger based on chain mail jamming. IEEE International Conference on Robotics and Automation (ICRA 2023). Available at: https://ieeexplore.ieee.org/stamp/stamp.jsp?tp=&arnumber=10161061&tag=1 (Accessed July 27, 2023).
Jin, X., Zhang, S., Medina, M. A., and Zhang, X. (2014). Experimental study of the cooling process of partially-melted sodium acetate trihydrate. Energy Build. 76, 654–660. doi:10.1016/J.ENBUILD.2014.02.059
Ma, Z., Bao, H., and Roskilly, A. P. (2017). Study on solidification process of sodium acetate trihydrate for seasonal solar thermal energy storage. Sol. Energy Mater. Sol. Cells 172, 99–107. doi:10.1016/J.SOLMAT.2017.07.024
Marti, P., and Recupero, A. (2022). Body adornment and interaction aesthetics: a new frontier for assistive wearables. Int. J. Bus. Syst. Res. 1, 1. doi:10.1504/ijbsr.2022.10033864
Martinez-Hernandez, U., Metcalfe, B., Assaf, T., Jabban, L., Male, J., and Zhang, D. (2021). Wearable assistive robotics: a perspective on current challenges and future trends. Sensors (Basel) 21, 6751. mdpi.com. doi:10.3390/s21206751
Ploszajski, A. R., Jackson, R., Ransley, M., and Miodownik, M. (2019). 4D printing of magnetically functionalized chainmail for exoskeletal biomedical applications. London: Cambridge University Press. doi:10.1557/adv.2019.154
Ransley, M., Smitham, P., and Miodownik, M. (2017). Active chainmail fabrics for soft robotic applications. Smart Mater Struct. 26, 08LT02. doi:10.1088/1361-665X/aa7221
Ryu, H. W., Woo, S. W., Shin, B. C., and Kim, S. D. (1992). Prevention of supercooling and stabilization of inorganic salt hydrates as latent heat storage materials. Sol. Energy Mater. Sol. Cells 27, 161–172. doi:10.1016/0927-0248(92)90117-8
Sandnes, B., and Rekstad, J. (2006). Supercooling salt hydrates: stored enthalpy as a function of temperature. Sol. Energy 80, 616–625. doi:10.1016/J.SOLENER.2004.11.014
Shinohara, K., and Wobbrock, J. O. (2011). “In the shadow of misperception: assistive technology use and social interactions,” in Conference on Human Factors in Computing Systems - Proceedings, Vancouver, BC, Canada, May 07-12, 2011, 705–714. doi:10.1145/1978942.1979044
Thalman, C., and Artemiadis, P. (2020). A review of soft wearable robots that provide active assistance: trends, common actuation methods, fabrication, and applications. Wearable Technol. 1, e3. doi:10.1017/WTC.2020.4
Tian, Y., Chen, K., Zheng, H., Kripalani, D. R., Zeng, Z., Jarlöv, A., et al. (2023). Additively manufactured dual-faced structured fabric for shape-adaptive protection. Adv. Sci. 10, e2301567. doi:10.1002/advs.202301567
Walsh, C. J., Paluska, D., Pasch, K., Grand, W., Valiente, A., and Herr, H. (2006). “Development of a lightweight, underactuated exoskeleton for load-carrying augmentation,” in Proc IEEE Int Conf Robot Autom 2006, Orlando, Florida, USA, May 15-19, 2006, 3485–3491. doi:10.1109/ROBOT.2006.1642234
Wang, G., Xu, C., Kong, W., Englmair, G., Fan, J., Wei, G., et al. (2021a). Review on sodium acetate trihydrate in flexible thermal energy storages: properties, challenges and applications. J. Energy Storage 40, 102780. doi:10.1016/J.EST.2021.102780
Wang, Y., Li, L., Hofmann, D., Andrade, J. E., and Daraio, C. (2021b). Structured fabrics with tunable mechanical properties. Nature 596, 238–243. 7871 596. doi:10.1038/s41586-021-03698-7
Keywords: phase change material, sodium acetate trihydrate, assistive technology, soft robotic actuators, wearable, active matter, animate material
Citation: Partik C, Porte E, Purkiss D, Michalska M and Miodownik M (2023) The use of phase change material as an actuator in linkage fabric structures. Front. Mater. 10:1268975. doi: 10.3389/fmats.2023.1268975
Received: 28 July 2023; Accepted: 15 November 2023;
Published: 27 November 2023.
Edited by:
Pham Huy Nguyen, Imperial College London, United KingdomReviewed by:
Lining Yao, Carnegie Mellon University, United StatesCopyright © 2023 Partik, Porte, Purkiss, Michalska and Miodownik. This is an open-access article distributed under the terms of the Creative Commons Attribution License (CC BY). The use, distribution or reproduction in other forums is permitted, provided the original author(s) and the copyright owner(s) are credited and that the original publication in this journal is cited, in accordance with accepted academic practice. No use, distribution or reproduction is permitted which does not comply with these terms.
*Correspondence: Mark Miodownik, bS5taW9kb3duaWtAdWNsLmFjLnVr
Disclaimer: All claims expressed in this article are solely those of the authors and do not necessarily represent those of their affiliated organizations, or those of the publisher, the editors and the reviewers. Any product that may be evaluated in this article or claim that may be made by its manufacturer is not guaranteed or endorsed by the publisher.
Research integrity at Frontiers
Learn more about the work of our research integrity team to safeguard the quality of each article we publish.