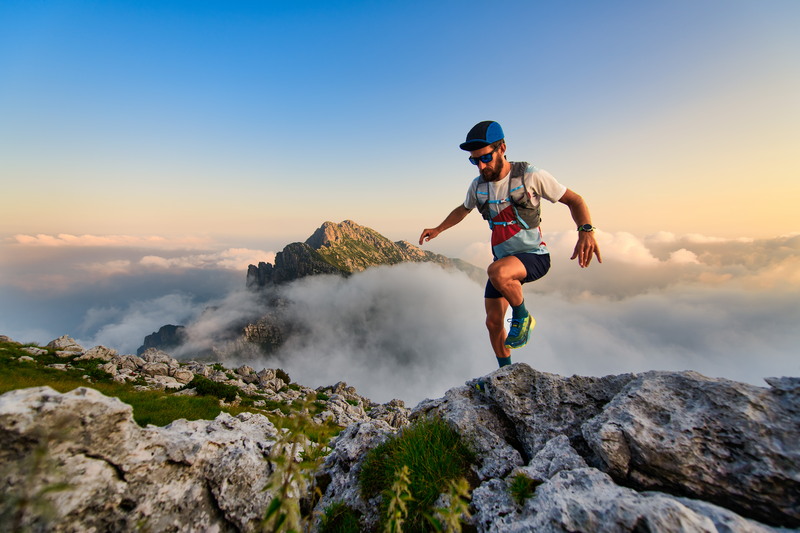
95% of researchers rate our articles as excellent or good
Learn more about the work of our research integrity team to safeguard the quality of each article we publish.
Find out more
ORIGINAL RESEARCH article
Front. Mater. , 24 August 2023
Sec. Ceramics and Glass
Volume 10 - 2023 | https://doi.org/10.3389/fmats.2023.1245121
With the continuing advancement in China’s exploration and development technologies of shale gas resources, there was a significant increase in shale gas oil-based drilling cuttings. In this paper, oil-based drilling cutting pyrolysis residues (ODCPRs) was used as the main raw material for preparing lightweight and high-strength building ceramsites to eliminate the environmental risks and recycle industrial waste. Firstly, orthogonal experiments were used to study the influences of raw material composition, preheating temperature, preheating time, sintering temperature, and sintering time on the properties of building ceramsites. From the results, the sintering temperature and the content of ODCPRs were discovered to be the key factors affecting the sintering process of ceramsites. Secondly, the influences of sintering temperature and heating rate on the properties of building ceramists were further explored to find the optimum sintering conditions. When the content of ODCPRs in the ceramsite was set to be 50%, the obtained building ceramsites presented excellent properties with particle compressive strength of 6.31 MPa, bulk density of 575.11 kg/m3, apparent density of 1097.24 kg/m3, and the water absorption of 1.89%. Finally, XRD, SEM, TG-DSC, and heavy metal leaching experiments were comprehensively conducted to analyze the composition structure variation and sintering mechanism of the building ceramsite. This paper presents an approach for the recycling, utilization, and disposal of oil-based drilling cuttings in the oil field waste management.
In recent years, natural gas as a clean energy source is increasingly favored in China’s energy consumption structure, which greatly stimulates the exploration and development of shale gas. To prevent wellbore collapse during the shale gas extraction process, a significant amount of oil-based drilling mud is typically used, which in turn generates substantial quantities of oil-based drilling cuttings. Due to the high concentration of petroleum pollutants, phenolic compounds, heavy metals, and other toxic substances contained in the cuttings, the environmental and safe disposal measures of oil-based drilling cutting present a remarkable challenge (Chaillan et al., 2006; Xiong and Wang, 2021). Currently, due to the high efficiency in recovering oil-based substances and low pollution risk during the treatment process, the pyrolysis treatment technology is the only large-scale industrial implementation method for oil-based drilling cuttings (Kingman et al., 2009; Abnisa and Alaba, 2021; Du et al., 2021; Mishra et al., 2021). However, the residual solid phases of oil-based drilling cuttings after pyrolysis may still contain trace amounts of petroleum hydrocarbons and partially dissolved heavy metal ions, thereby presenting persistent environmental risks. The substantial accumulation of oil-based drilling cutting pyrolysis residues (ODCPRs) not only occupied valuable land resources but also posed a significant threat to the environment (Ball et al., 2012; Owens and Santner, 2021; Li et al., 2022). Thus, there is still a need to explore and study effective ways to utilize ODCPRs as a valuable resource by eliminating environmental risks, increasing industrial additional value, and reducing production costs at the same time.
Extensive research is conducted on the resource utilization of ODCPRs, such as the raw materials applied in road fillers (Xiong and Wang, 2021), sintered bricks (Wang et al., 2017), non-sintered bricks (Liu et al., 2018; Wang et al., 2019), concrete (Bernardo et al., 2007; Foroutan et al., 2018), and glass ceramics (Abbe et al., 2009). Besides, the ODCPR content in these materials typically does not exceed 10% to ensure product quality, resulting rather low utilization rate of ODCPRs. Due to the low utilization of this alternative raw material, there is still a potential for applications needed. Therefore, it is still an important goal for addressing the massive accumulation of ODCPRs to find a resource utilization approach with higher ODCPRs consumption, lower costs, and broader applications.
Lightweight ceramsites, as an artificial lightweight aggregate with a hard surface and porous structure inside, are widely used in construction, environmental industries, and other fields owing to their characteristics of lightweight, thermal insulation, and excellent durability (He et al., 2015; Ji et al., 2015; Xie et al., 2016; Lau et al., 2017; Zhao et al., 2018; Hao et al., 2019). The raw materials for normal building ceramsites mainly include natural minerals such as shale and clay (Başaran Bundur et al., 2017; Ahmad and Chen, 2019; Omar Ahmed and Hassan Assem, 2021). However, with the depletion of natural mineral resources and the increasingly stringent environmental regulations, industrial wastes were becoming a substitute for natural raw materials in the building ceramsite production. The reported industrial solid wastes that have been used for the preparation of building ceramsites include tailings (Wang et al., 2014; Li et al., 2020), municipal sludge (Qi et al., 2009), red mud (RM) (Mi et al., 2021; Mi et al., 2022), and fly ash (FA) (Qin et al., 2015), which contain abundant silicon-aluminum components to obtain good properties. Meanwhile, previous studies indicate that ODCPRs have similar components to ordinary industrial solid wastes, which was also a proper candidate to generate sintering ceramsites. Thereinto, Liu et al. (2023) prepared a high-strength and low-density ceramsite proppant using 20% ODCPRs and 76% bauxite, with a denser structure and a breakage ratio of 8.6% under a closure pressure of 52 MPa after sintering at 1342°C. Yang et al. (2022) successfully prepared a low-density ceramsite proppant by utilizing a mixture of 30% water-based drilling cuttings and 70% bauxite after sintering at 1420°C with a breakage ratio lower than 5% under a closure pressure of 52 MPa. The aforementioned studies have demonstrated the potential for producing building ceramsites using ODCPRs, however, there is limited literature available on the preparation of lightweight and high-strength building ceramsites with ODCPRs.
The goal of this study is to prepare high-performance lightweight and high-strength building ceramsites with ODCPRs as the main raw material. Meanwhile, FA, RM, and quartz sand (QS) are taken as auxiliary materials, and SiC was a foaming agent. The influences of ODCPRs ratios and sintering procedures (preheating temperature, preheating time, sintering temperature, sintering time, and heating rate) on the properties of the ceramsites are systematically investigated, and the optimal sintering condition and formula are obtained, providing a new solution for approach in the resource utilization and industrial the waste utilization and disposal of solid waste co-disposal of oil-based drilling cuttings.
ODCPRs were obtained from a shale gas field in Southwest China, FA was collected from a power plant in Tangshan, Hebei, QS was provided by Chongqing Changjiang Group Co., Ltd., RM was obtained from Shandong, and the SiC foaming agent was purchased from Shanghai Macklin Biochemical Co., Ltd.
Different test methods were conducted on the raw materials to obtain the basic information. Firstly, X-ray diffraction (XRD) was used to analyze the phase composition of the raw materials. The results were shown in Supplementary Figure S1, indicating that the phases of ODCPRs included quartz, barite, calcite, and dolomite. The phases of FA contained quartz, mullite, and hematite. The main phases of RM included calcite, quartz, hematite, and boehmite; and the phases of QS were quartz and microcline.
X-ray fluorescence (XRF) spectrometer was utilized to determine the chemical compositions of all experimental raw materials, with the results shown in Supplementary Table S1. It can be observed that ODCPRs show relatively low contents of Si and Al as 38.53% and 17.87%, respectively. Additionally, other mineral elements such as Ca, Fe, and Ba were present, particularly with high concentrations of Ba and Ca, which would significantly impact the sintering process of the building ceramsites. Meanwhile, FA and QS were selected as auxiliary sintering materials to supply the silicon-aluminum phase in the raw materials. Furthermore, a small amount of RM was added caused of its property of containing iron phases that could be used as a foaming agent at relatively high temperatures, reducing the density of the ceramsite, and also serving as a flux component during granulation (Mi et al., 2021; Mi et al., 2022). According to Riley’s ternary phase diagram (Riley, 1951), the content of SiO2, Al2O3, and fusing components in the green body should be controlled within a certain range, in order to achieve a good sintering performance for preparation of the ceramsite. The content of SiO2 should be controlled within 48%–78%, Al2O3 content should be controlled at 10%–25%, and the content of the fusible component is 13%–26%, which was aimed at achieving good expansion and mechanical performance (Yang et al., 2005; Tsai et al., 2006). At present, many studies (Wang et al., 2020; Mi et al., 2021; Zhuo et al., 2023) have successfully used solid waste to prepare lightweight and high-strength ceramics by adjusting raw materials within the range of chemical components. Hence, the calculated ingredient proportions of ceramsites in our study were specified in Supplementary Table S2 and in Supplementary Figure S2, where the ODCPRs content ranged from 30% to 60%.
Through TG-DSC analysis, the physical and chemical reactions of raw materials (ODCPRs, FA, RM, QS and SiC) during the sintering procedure can be obtained, which can provide data support for the enactment of sintering system, with the results shown in Supplementary Figure S3. From Supplementary Figure S3A, ODCPRs exhibited a significant weight loss during the heating process, with a mass loss of over 25.00%, and there were three distinct weight loss temperature regions as “the room temperature to 550°C,” “550°C–900°C,” and “900°C–1300°C.” It was inferred that the first stage involved the combustion of residual water and organic matters, and there was an obvious exothermic effect caused by the oxidation reaction of oil-based organic matter within the range of 350°C–550°C (Jia et al., 2023) (mass loss reached 6.02%); the second stage involved the decomposition of carbonate, with endothermic peaks appearing around 700°C–900°C due to the decomposition of calcite and aragonite, respectively (Maitra et al., 2005) (mass loss reached 10.68%); the third stage corresponded to the decomposition of sulfate and other substances (mass loss reached 7.79%), and the position of the endothermic peak in this temperature range appeared at 1065°C, corresponding to the generation of the liquid phase and solid-phase reactions at high temperatures (Khalil et al., 2018).
As shown in Supplementary Figure S3B, from the TG results, the overall weight loss of FA was relatively small, only 4.46%, which two weight loss stages at room temperature to 650°C and 650°C–1300°C were observed. The first stage achieved a weight loss of 2.76%, which was inferred from the evaporation of moisture in FA and the combustion of unburnt carbon, while the DSC result indicated that this reaction was an obvious endothermic effect. The second stage achieved a weight loss of 1.70%, which was speculated to be due to the decomposition of hematite. The decomposition temperature of Fe2O3 under high temperatures was generally between 800°C and 1550°C. The decomposition reaction occurred in a wide temperature range and belonged to a slow-release type (Mi et al., 2022).
As shown in Supplementary Figure S3C, from the TG results, RM had a relatively larger weight loss of 20.28%, with three distinct weight loss stages at “room temperature to 450°C,” “450°C–900°C,” and “900°C–1300°C,” respectively. The first stage corresponded to the decomposition of bound water and organic matter (mass loss of 10.02%). The second stage corresponded to the dehydration of boehmite (AlO(OH)) and the decomposition of calcite (mass loss of 7.68%). The third stage was due to the decomposition of hematite (mass loss of 2.11%). From the result of DSC curve, the three distinct stages of weight loss were accompanied by clear endothermic effects.
As shown in Supplementary Figure S3D, QS had relatively stable thermal properties with no obvious weight loss steps than other raw materials in the TG curve. The endothermic peak appearing around 1100°C in DSC curve may be due to the transformation of the quartz crystal structure.
As shown in Supplementary Figure S3E, the TG curve of SiC in the temperature range of 0°C–1300°C showed a trend of first decreasing and then increasing, which was mainly related to the oxidation reaction of SiC. The oxidation reaction of SiC was mainly manifested in two parts: passive oxidation characterized by net mass increase and active oxidation characterized by net mass loss (Liang et al., 2021). Therefore, the overall mass showed a trend of first decreasing and then increasing. Simultaneously, SiC provided a sufficient gas phase for the matrix of ceramsite during the oxidation reaction. In addition, the DSC curve showed an overall endothermic trend starting from 300°C, which was related to the reaction of SiC.
The preparation process of ceramsite was illustrated in Figure 1: ① Raw materials were weighed according to the proportions listed in Supplementary Table S2 and well mixed with a small amount of water. The mixture was then ground by a ball grinding mill (QM-3, Changsha Tianchuang Powder Technology Co., Ltd.) for 1 h. Subsequently, the well-ground and filtered slurry were transferred to a drying oven (BXP-070Gx, Guangzhou Anfei Environmental Protection Technology Co., Ltd.), and dried to constant weight. After that, the filter cake was crushed using a pulverizer (HTY-800, Zhejiang Yongkang Red Sun Electromechanical Co., Ltd.). The crushed powders were fully dispersed and screened through a 0.25 mm sieve. Moreover, a laser particle size analyzer (Master Sizer 2000, Malvern Panalytical Ltd., United Kingdom) was used to test the particle size distribution of the mixed raw powders, as shown in Supplementary Figure S4A, which indicated that the particle size distribution of the grounded raw material powder was ranged from 0.3 to 100 μm, and with a D50 value of 14.91 μm. ② The raw material powder was granulated into a green body with a diameter of 12 mm ± 1 mm using a sugar coater (BY-300, Taizhou GEX Machinery Co., Ltd.). The granulated green bodies were subsequently dried until a constant weight was achieved. ③ The dry green body was sintered at high temperature in a muffle furnace (KSL 1750X, Hefei Kejing Material Technology Co., Ltd.) following the sintering procedure shown in Supplementary Figure S4B. After being cooled to room temperature, the samples were removed from the furnace and subjected to property testing.
The bulk density (ρ1, kg/m3), apparent density (ρ2, kg/m3), and 1 h water absorption (W1 h, %) of the ceramsite were tested according to the Chinese Standard “GB/T 17431.2-2010.” Each test group was repeated by three times, and the calculation formulas of different properties were shown as follows:
(1) The bulk density and apparent density
Where
Where,
(2) Water absorption
Where, m1 represented the mass (g) of the ceramsite after the water immersion test.
(3) Bloating index
To evaluate the bloating index of ceramsite (Qi et al., 2009), a uniformly mixed raw material powder was filled into a 12 mm square green body, and the volume change rate of the sample before and after the sintering process was measured and the bloating index (BI) was expressed as the following formula:
Where,
In this paper, the compressive strength of the ceramsite was evaluated using the single-particle strength method (Yashima et al., 1987; Li et al., 2000). Each series was tested with 15 samples by a press machine (ETM305D, Shenzhen Wance Test Equipment Co., Ltd.). The particle compressive strength of ceramsites was calculated as below:
Here, S was the compressive strength of the ceramsite (MPa); Pc was the failure load of the ceramsite (N); X was the distance between the upper and lower compression plates (mm).
The phase composition of the ceramsite was also analyzed using an X-ray diffractometer (XRD, X'Pert PRO MPD, PANalytical, Netherlands), with Cu-Kα radiation (40 Kv, 40 mA, scanning range: 5°–90°, scanning time: 5°/min), and the Inorganic Crystal Structure Database (ICSD) database was used to identify the crystalline phases. Furthermore, the chemical compositions of raw materials were characterized by X-ray fluorescence (XRF, RIGAKU ZSX Priums, Japan).
The mass changes and thermal behaviors of each raw material and green body were characterized using a thermogravimetric analyzer and differential scanning calorimeter (STA449F3, Netzsch, Germany) with a heating rate of 10°C/min under air atmosphere, and the test temperature range was from room temperature to 1300°C.
The cross-sectional morphology of the ceramsite before and after acid treatment was observed using a scanning electron microscope (Zeiss Gemini 300, Carl Zeiss, Germany), and their elemental compositions were further determined using energy-dispersive X-ray spectroscopy (EDX). The acid treatment was referred to the Chinese standard “SY/T 5108-2014.” The acid solution was first pre-fabricated as HCl: HF = 12: 3 (mass 12% HCl and mass 3% HF). Afterward, the ceramsite sample was immersed in the acid solution and then placed in a thermostatic water bath (CF-B, Cangchuan Road Test Apparatus Co., Ltd.) at a constant temperature of 66°C for 3 h to remove the soluble substances from the ceramsite.
The heavy metals leaching behavior of ceramsites was evaluated by the sulfuric-nitric acid method which was referred to the “Solid Waste-Extraction Procedure for Leaching Toxicity” (HJ/T 299-2007).
In this study, an orthogonal experiment was designed to investigate the optimal content of drilling cuttings and the sintering conditions for the preparation of ceramsites. The experiment included five influencing factors: A) ODCPRs contents, B) preheating temperature, C) preheating time, D) sintering temperature, and E) sintering time. At the same time, four-level factors were also settled. In addition, the heating rate was controlled at 10°C/min, the detail of the sintering parameters was shown in Table 1. The bulk density, particle compressive strength, and 1 h water absorption of ceramsites under different orthogonal experimental conditions were analyzed.
The results of the orthogonal test were shown in Table 2, a total of 16 groups of ceramsites have been tested. Thereinto, sample A2B4C4D4E4 has the lowest bulk density of 297.67 kg/m3, but the strength was only 1.95 MPa. Besides, sample A3B4C2D1E3 presented the highest strength of 11.59 MPa, while the bulk density was 1018.67 kg/m3, the density was higher than the maximum value of lightweight requirements of the standard. Hence, it was difficult to decide the optimum conditions for preparing ceramsite. In order to comprehensively analyze the test results and find out the primary factors impacting the performance of the ceramsite, the range analysis of orthogonal experiment was employed, as shown in Table 3. As presented in Table 3, Pi value represented the average value of the experimental results under the same factor level, while R value represented the difference between the maximum and minimum Pi values under the same factor, indicating the degree of dispersion of the experimental data. The larger the R value, the greater the impact of this factor on the properties of the ceramsites was obtained, indicating that this factor was the main factor. Hence, it can be concluded that sintering temperature was the most important factor affecting the ceramsite properties of compressive strength, followed by bulk density, and 1 h water absorption.
Furthermore, as shown in Figure 2, the bulk density and particle compressive strength of ceramsites decreased with the increase in sintering temperature, while the water absorption rate first decreased and then increased. At a sintering temperature of 1070°C, insufficient sintering reaction resulted in inadequate generation of both liquid and gas phases, leading to an average water absorption rate exceeding 10% for the ceramsites at this level. Additionally, the higher density failed to meet the requirement for lightweight materials. With an increase in sintering temperature, more liquid phase, and gas phase would be generated inside the ceramsites, promoting the formation of higher porosity and resulting in a reduction in bulk density and compressive strength (Zhuo et al., 2023). Meanwhile, the formation of a sufficient liquid phase resulted in the development of a glassy layer on the surface, effectively reducing water absorption by the ceramsite.
FIGURE 2. Influences of ODCPRs content, preheating temperature, preheating time, sintering temperature, and sintering time on (A) bulk density, (B) particle compressive strength, and (C) 1 h water absorption.
A significant impact of the ODCPRs content on the properties of ceramsites was observed through comparison. As the ODCPRs content increased, both the bulk density and particle compressive strength showed a trend of first increasing and then decreasing. This may be related to the balance between high-temperature melt components and gas components in the green body (Jia et al., 2023). When the ODCPRs content was low, the gas cannot be wrapped and was affected by the low liquid content in the ceramsite, leading to an outward overflow of gas and resulting in an excessively high density of the ceramsite (Zhuo et al., 2023). Gradually, with an increase in ODCPRs content, the sufficient liquid phase was generated inside the body, and gas accumulated within the ceramsites to promote liquid-phase expansion (Jia et al., 2023). This resulted in the formation of numerous internal pores, ultimately leading to a decrease in both bulk density and particle compressive strength (Zhuo et al., 2023).
As indicated by Table 3, the impact of preheating temperature had little influence on the compressive strength of the ceramic particles, meanwhile the preheating temperature was number 5 in the ranking on the bulk density and 1 h water absorption. Therefore, among the five factors, the preheating temperature was found to be negligible on the performance of ceramsites. But preheating served to remove water from the green body of the ceramsite to prevent cracking during the sintering process and to regulate gas release during the sintering stage. When the preheating process happened at rather lower temperatures, pores could be filled by the liquid phase generated at higher temperatures. Therefore, the preheating temperature displayed minimal influences on bulk density, particle compressive strength, and 1 h water absorption.
Besides, the optimal factor was determined based on the principle of achieving a ceramsite with enhanced strength, reduced density, and minimized water absorption while taking into account the consumption of cuttings and energy efficiency during preparation. The optimal sintering conditions were determined as follows: with an ODCPRs content of 50%, preheating-temperature-of 400°C for 20 min, the sintering temperature of 1100°C for 10 min, and heating rate of 10°C/min. Under these optimal sintering conditions, the ceramsites exhibited excellent properties, including a bulk density of 813.00 kg/m3, a particle compressive strength of 10.31 MPa, and water absorption of 2.56%.
Formulation S3 was selected as the test sample for investigating the impact of sintering temperature and heating rate on the properties of ceramsites containing 50% ODCPRs content.
Based on the orthogonal experiment results determined in Section 3.1, the optimal sintering conditions for ceramsites were established. Besides, it was found that sintering temperature had the greatest impact on the properties of ceramsites, with a wide range of temperature variations. Therefore, the range of sintering temperatures based on the optimal conditions from the orthogonal experiments was further investigated using a single-factor method, and formulation S3 was chosen for the further experiment.
Figure 3 presented the changes in properties of ceramsites at different sintering temperatures. It was observed that the ceramsites were highly sensitive to the sintering temperature. As the sintering temperature increased, the bulk density, apparent density, particle compressive strength, and water absorption of the ceramsites were all decreased. The bloating index showed a negative correlation with these factors, which was in accordance with the results of the orthogonal experiment. When a sintering temperature was set at 1080°C, the compressive strength of the ceramsites reached 11.85 MPa, but the bulk density and apparent density were also increased to 1038.33 and 1934.83 kg/m3, respectively, indicating poor foaming and swelling effects at lower sintering temperatures. Additionally, at lower sintering temperatures, the mass transfer process of the liquid phase was limited, which could lead to a thinner glassy layer formed on the surface of the ceramsites, more interconnected pores and micro-pores in the interior, and higher water absorption (4.76%) would occur. In contrast, when the sintering temperature increased to 1140°C, the liquid phase content in the green body increased, and the mass transfer process of the liquid phase intensified. A denser shell formed on the surface of the ceramsites, blocking the interconnected pores inside and effectively preventing water from infiltrating, resulting in reduced water absorption of 1.33%. Moreover, the increased liquid phase contributed to encapsulating the gas generated by high-temperature reactions and facilitating the formation of a closed porous structure. This manifested as a continuous decrease in the bulk density and apparent density of the ceramsites. In summary, when the sintering temperature was set at 1120°C, the ceramsites exhibited optimal properties: a bloating index of 159.15%, particle compressive strength of 6.07 MPa, bulk density of 634 kg/m3, apparent density of 1289.34 kg/m3, and water absorption of 2.22%.
FIGURE 3. Properties of ceramsites at different sintering temperatures: (A) bulk density, apparent density and bloating index; (B) particle compressive strength and 1 h water absorption.
The X-ray diffraction (XRD) spectra of the ceramsite samples at different sintering temperatures were shown in Figure 4. It was observed that the sample compositions were similar at different sintering temperatures, the main crystal phases consisted of celsian, quartz, hematite, anorthite, barite, and nepheline. Thereinto, celsian was the main crystalline phase of sintering ceramsite, while unreacted barite, quartz, and hematite still remained. Moreover, the generation of celsian crystals was closely related to the sintering temperature and liquid-phase content in the ceramsite. The generation of adequate liquid-phase production could reduce the activation energy for ion diffusion, immerse the internal fine particles of the ceramsite, enhance capillary forces between particles, promote liquid flow between pores, induce sliding, rotation, re-arrangement of the internal fine particles, and accelerate solid-solid and solid-liquid reactions, thereby promoting crystal formation (Yoon et al., 2003; Shih and Jean, 2017; Yang et al., 2018). From the XRD spectra, it could be observed that as the sintering temperature increased from 1080°C to 1140°C, the diffraction peak intensity of celsian first increased and then decreased, reaching the maximum intensity at 1100°C, indicating that a suitable liquid-phase content for foaming and sintering reactions could be achieved at this sintering temperature. However, with further increase in sintering temperature, the peak intensities of all crystals significantly decreased due to excessive formation of glass phase and larger internal porosity. These factors may potentially have adverse effects on the properties of the ceramsite (Ren et al., 2019).
Figure 5 showed the cross-sectional pictures of ceramsites at different sintering temperatures. It can be clearly observed that as the sintering temperature increased, the internal pores of the ceramsites became significantly larger. This was caused by the gradual increase of liquid phases and the decline of liquid phases viscosity during the sintering process. In this stage, the gas-producing components in the ceramsite would be released to generate a large amount of gas. When sufficient liquid phases were formed, the gas could be easier encapsulated by the liquid phase, thus forcing the matrix to expand and creating numerous pores inside the ceramsite (Jun et al., 2023). However, at excessively high sintering temperatures, the viscosity of the liquid phase decreased, which facilitated the migration and diffusion of gas phases, which resulted in the merging and enlargement of small enclosed pores to form larger ones, or even causing the gas escape. This was the main reason for the decrease in density and strength of the ceramsite.
FIGURE 5. Microstructure (×100) of ceramsites before acid treatment at different sintering temperatures: (A) 1,080°C, (B) 1,100°C, (C) 1,120°C, and (D) 1,140°C.
Figure 6 displayed the microstructure of the ceramsite after acid corrosion treatment. Combined with the EDS test (II, III), it could be inferred that celsian (BaAl2Si2O8) mainly appeared in the form of clusters or needles. In addition, a large amount of sulfur element was detected ascribed to the EDS results, indicating that the formation of celsian crystals was due to the solid-phase reaction between barite (BaSO4), quartz (SiO2), and Al2O3 in the matrix (Long-González et al., 2009; Yang et al., 2018). According to the EDS result (I), it was deduced that unreacted hematite (Fe2O3) mainly existed in the form of particles. According to the EDS result (IV), the blocky particles were unreacted quartz. At a lower sintering temperature (1080°C), a large amount of unreacted hematite was found, and the celsian phases mainly showed a cluster structure. However, when the sintering temperature increased to 1100°C, needle-shaped celsian gradually appeared and overlapped with each other to form a denser structure, thereby improving the mechanical properties of the ceramsite. Meanwhile, a notable augmentation in the internal porosity of the ceramsite was observed. As the sintering temperature gradually increased to 1140°C, there was a gradual reduction in the number of celsian crystal clusters but an increase in their size (as depicted in Figure 6D). Concurrently, it was discovered that the internal porosity of the ceramsite underwent significant expansion.
FIGURE 6. Microstructure (×5,000, ×10,000) of ceramsites after acid treatment at different sintering temperatures: (A) 1,080°C; (B) 1,100°C; (C) 1,120°C; (D) 1,140°C.
Through the single factor method study of the sintering temperature, the following ceramsites calcination conditions were determined: ODCPRs content of 50% for formulation S3, the preheating temperature of 400°C for 20 min, the sintering temperature of 1120°C for 10 min. In this section, the influence of heating rate (5°C/min, 10°C/min, 15°C/min, and 20°C/min) on the properties of the ceramsite was further investigated, as shown in Figure 7. It was found that the variation in heating rate had little influence on the water absorption of the ceramsite. The bulk density and apparent density both showed an upward trend followed by a downward trend, while the bloating index exhibited the opposite trend. This may be attributed to the slower rate of substance decomposition or gas generation during the reaction, compared to that of molten liquid phase formation, when the heating rate was ≤10°C/min, resulting in impeded pore formation. When the heating rate continued to increase, the decomposition reaction became more intense, and the generated gas was sufficient to form relatively large pores on the surface of the matrix, leading to a relatively lower bulk density and apparent density. Moreover, the particle compressive strength of the ceramsite decreased with the increase of the heating rate, especially at a heating rate of 20°C/min, where its particle compressive strength was only 2.78 MPa. In summary, when the heating rate was 5°C/min, the physical properties of the ceramsite were finest, with bulk density, apparent density, 1 h water absorption, particle compressive strength, and bloating index reaching 575.11 kg/m3, 1097.24 kg/m3, 1.89%, 6.31 MPa, and 162.38%, respectively.
FIGURE 7. Properties of ceramsites at different heating rates: (A) bulk density, apparent density and bloating index; (B) particle compressive strength and 1 h water absorption.
The XRD spectra of ceramsites were presented in Figure 8, showing the results of phase compositions at different heating rates. The experimental results showed that with the increase in heating rate, the diffraction peak intensity of each crystal decreased significantly. When the heating rate of the sintering process was 5°C/min, the diffraction peak intensity of crystals such as celsian, quartz, anorthite, and nepheline increased significantly compared to the sample sintered in 10°C/min. This was attributed to the prolonged residence time of the matrix in the high-temperature stage at a heating rate of 5°C/min, which facilitated phase reactions and resulted in an increased formation of highly crystalline crystals. However, when the heating rate exceeded 10°C/min, the particle’s residence time at high temperature continuously decreased, leading to insufficient phase reaction and a significant reduction in both diffraction peak intensity and compressive strength of the ceramsite particles.
Figure 9 showed the cross-sectional microstructure of ceramsites under different heating rates. It was observed that as the heating rate increased, the size of internal pores within the ceramsite exhibited a first-increasing-then-decreasing trend, which was consistent with the density variation pattern of ceramsites discussed in Section 3.3.1. While Figure 10 showed the cross-sectional microstructure of ceramsites after the acid treatment under different heating rates. It was found that when the heating rate was 5°C/min, celsian still mainly appeared in the form of interactive overlapping with needle-shaped or cluster crystals. As the EDS results (I, II) revealed that unreacted quartz particles and barite crystals appeared around the celsian crystals. Furthermore, it was noticed that with the increase in heating rate, the celsian in the green body tended to transform from a needle-shaped structure into a cluster structure, indicating the influence of the heating rate on the morphology change of celsian crystals.
FIGURE 9. Microstructure (×100) of ceramsites before acid treatment at different heating rates: (A) 5°C/min; (B) 10°C/min; (C) 15°C/min; (D) 20°C/min.
FIGURE 10. Microstructure (×5,000, ×10,000) of ceramsites after acid treatment at different heating rates: (A) 5°C/min; (B) 10°C/min; (C) 15°C/min; (D) 20°C/min.
In order to clarify the sintering behavior and phase reaction mechanism during the ceramsites sintering procedure, TG-DSC experimental analyses were conducted on the formulation S3, as shown in Figure 11.
As shown in Figure 11, the TG curve of the sample S3 exhibited a similar overall trend to that of the ODCPRs, which was with three weight loss stages observed at different temperature ranges: “room temperature to 550°C,” “550°C–900°C,” and “900°C–1300°C,” which were corresponding to the loss of moisture and combustion of organic compounds (6.46%), the decomposition of carbonates and the loss of bound water in boehmite (8.46%), and the decomposition of hematite and sulfates (3.54%), respectively. These observations indicated that gas-phase decomposition occurred during the entire sintering process, contributing to the reduction in the density of the ceramsite. Additionally, the DSC curve continued to decrease from 500°C, indicating that the process was continuously endothermic, which was related to the endothermic decomposition of carbonates, sulfates, and the oxidation reaction of SiC. Moreover, a distinctive endothermic peak appeared at 1104°C, corresponding to the occurrence of solid-state reactions at high temperatures. Compared with the endothermic peak of ODCPRs appearing at 1065°C, this peak was slightly delayed due to the introduction of fly ash and quartz sand with higher alumina-silica content, leading to a decrease in the liquid phase generation at high temperatures, thereby delaying the solid-phase reaction temperature range. Combining with the XRD analysis results that were discussed earlier, it was known that the main solid-phase reactions in this temperature range were the formation of celsian crystals (Long-González et al., 2009) and wollastonite crystals (Guzmán-Carrillo et al., 2017), involving the following chemical reaction equations in Supplementary Table S3.
The major raw material used in this study for the preparation the ceramsites was ODCPRs, which may still face some trace amounts of environmentally harmful substances. If these recycling products released heavy metal ions during the application, they would pose a threat to the natural environment and human beings. Therefore, it was important to evaluate the stabilization effect of ceramsites on heavy metal ions after the sintering process and their environmental safety during application. According to the Chinese standard “GB 5085.3-2007,” the heavy metal leaching concentration of sample S3’s ceramsites was tested under optimal preparation conditions, as presented in Table 4. The experimental results showed that after high-temperature sintering, the heavy metal leaching concentrations of the ceramsites were much lower than the national standard limits indicating a good environmental safey of the ceramsite.
The comparison of the bulk density, water absorption, and particle compressive strength of the ceramsite in this study with those reported in other literature was presented in Supplementary Table S4 (Sun et al., 2021; Pei et al., 2022; Shang et al., 2022; Jia et al., 2023; Li et al., 2023). It was worth noting that all primary raw materials utilized were industrial solid waste materials, and the produced ceramsite in this work demonstrated exceptional performance in terms of both compressive strength and density.
This study demonstrated the feasibility of using ODCPRs in combination with solid waste for the preparation ceramsites. The properties of the ceramsite were comprehensively investigated through orthogonal experiments, single-factor analysis, phase, morphological, and TG-DSC analysis, the following conclusions were drawn:
(1) By optimizing the sintering parameters, it was determined that the sintering temperature exerted the most significant influence on the properties of ceramsites. The order of impact on the particle compressive strength of ceramsites was found to be as follows: sintering temperature > ODCPRs content > sintering time > preheating time > preheating temperature.
(2) The independent influence of sintering temperature and heating rate on the properties of ceramsites was explored by a single-factor method. By combining XRD and SEM analysis, the phase composition and microstructure changes of the ceramsite were revealed. The results indicated that the physical properties of the ceramsite decreased with increasing sintering temperature, while reducing the heating rate was conducive to improving the particle compressive strength. Furthermore, the main crystal phases of the ceramsites were identified as celsian, quartz, hematite, zircon, and xenotime, and the best preparation process parameters were obtained as: “preheating temperature of 400°C for 20 min, sintering temperature of 1120°C for 10 min with a heating rate of 5°C/min and 50% content of ODCPRs”. The bulk density, apparent density, particle compressive strength, 1 h water absorption, and bloating index of the obtained ceramsites were 575.11 kg/m3, 1097.24 kg/m3, 6.31 MPa, 1.89%, and 162.38%, respectively.
(3) During high-temperature sintering, various gas-phase and solid-phase reactions occurred in the matrix, including water vapor vaporization, organic matter combustion, as well as carbonates, sulfates and hematite decomposition. These reactions contributed to the expansion and density reduction of ceramsites.
(4) The sintered ceramsites could well meet the Chinese standards of “GB 5985.3-2007” for the leaching toxicity of heavy metals.
The original contributions presented in the study are included in the article/Supplementary Material, further inquiries can be directed to the corresponding author.
HW, YY, and JL contributed to conception and design of the study. HL and TM organized the database. JY and LZ performed the statistical analysis. YY and HW wrote the first draft of the manuscript. DL, GJ, and HL wrote portion sections of the manuscript. All authors contributed to the article and approved the submitted version.
Authors HW, JL, DL, GJ, LZ, JY, TM, and XH were employed by Safety and Technology Supervision Research Institute of PetroChina Southwest Oil and Gas Field Company.
The remaining authors declare that the research was conducted in the absence of any commercial or financial relationships that could be construed as a potential conflict of interest.
All claims expressed in this article are solely those of the authors and do not necessarily represent those of their affiliated organizations, or those of the publisher, the editors and the reviewers. Any product that may be evaluated in this article, or claim that may be made by its manufacturer, is not guaranteed or endorsed by the publisher.
The Supplementary Material for this article can be found online at: https://www.frontiersin.org/articles/10.3389/fmats.2023.1245121/full#supplementary-material
Abbe, O. E., Grimes, S. M., Fowler, G. D., and Boccaccini, A. R. (2009). Novel sintered glass-ceramics from vitrified oil well drill cuttings. J. Mat. Sci. 44, 4296–4302. doi:10.1007/s10853-009-3637-y
Abnisa, F., and Alaba, P. A. (2021). Recovery of liquid fuel from fossil-based solid wastes via pyrolysis technique: a review. J. Environ. Chem. Eng. 9, 106593. doi:10.1016/j.jece.2021.106593
Ahmad, M. R., and Chen, B. (2019). Experimental research on the performance of lightweight concrete containing foam and expanded clay aggregate. Compos Part B. Eng. 171, 46–60. doi:10.1016/j.compositesb.2019.04.025
Ball, A. S., Stewart, R. J., and Schliephake, K. (2012). A review of the current options for the treatment and safe disposal of drill cuttings. Waste. manage. Res. 30, 457–473. doi:10.1177/0734242x11419892
Başaran Bundur, Z., Kirisits, M. J., and Ferron, R. D. (2017). Use of pre-wetted lightweight fine expanded shale aggregates as internal nutrient reservoirs for microorganisms in bio-mineralized mortar. Cem. Concr. Comp. 84, 167–174. doi:10.1016/j.cemconcomp.2017.09.003
Bernardo, G., Marroccoli, M., Nobili, M., Telesca, A., and Valenti, G. L. (2007). The use of oil well-derived drilling waste and electric arc furnace slag as alternative raw materials in clinker production. Resour. Conserv. Recy. 52, 95–102. doi:10.1016/j.resconrec.2007.02.004
Chaillan, F., Chaîneau, C. H., Point, V., Saliot, A., and Oudot, J. (2006). Factors inhibiting bioremediation of soil contaminated with weathered oils and drill cuttings. Environ. Pollut. 144, 255–265. doi:10.1016/j.envpol.2005.12.016
Du, H., Zhong, Z. P., Zhang, B., Zhao, D. Q., Lai, X. D., Wang, N. B., et al. (2021). Comparative study on intercalation-exfoliation and thermal activation modified kaolin for heavy metals immobilization during high-organic solid waste pyrolysis. Chemosphere 280, 130714. doi:10.1016/j.chemosphere.2021.130714
Foroutan, M., Hassan, M., M., Desrosiers, N., and Rupnow, T. (2018). Evaluation of the reuse and recycling of drill cuttings in concrete applications. Constr. Build. Mat. 164, 400–409. doi:10.1016/j.conbuildmat.2017.12.180
Guzmán-Carrillo, H. R., Pérez, J. M., and Romero, M. (2017). Crystallisation of nepheline-based glass frits through fast-firing process. J. Non-Cryst. Solids. 470, 53–60. doi:10.1016/j.jnoncrysol.2017.04.043
Hao, C. M., Cheng, Y. P., Wang, L., Liu, H. Y., and Shang, Z. (2019). A novel technology for enhancing coalbed methane extraction: hydraulic cavitating assisted fracturing. J. Nat. Gas. Sci. Eng. 72, 103040. doi:10.1016/j.jngse.2019.103040
He, H. T., Zhao, P., Yue, Q. Y., Gao, B. Y., Yue, D. T., and Li, Q. (2015). A novel polynary fatty acid/sludge ceramsite composite phase change materials and its applications in building energy conservation. Renew. Energy 76, 45–52. doi:10.1016/j.renene.2014.11.001
Ji, T., Zheng, D. D., Chen, X. F., Lin, X. J., and Wu, H. C. (2015). Effect of prewetting degree of ceramsite on the early-age autogenous shrinkage of lightweight aggregate concrete. Constr. Build. Mat. 98, 102–111. doi:10.1016/j.conbuildmat.2015.08.102
Jia, G. H., Wang, Y. L., Yang, F. L., and Ma, Z. B. (2023). Preparation of CFB fly ash/sewage sludge ceramsite and the morphological transformation and release properties of sulfur. Constr. Build. Mat. 373, 130864. doi:10.1016/j.conbuildmat.2023.130864
Jun, J., Song, C., Chao, J., Gui, W., Tie, L., Xu, T., et al. (2023). Preparation and properties of high-strength lightweight aggregate ceramsite from nepheline tailings. Constr. Build. Mat. 368, 130458. doi:10.1016/j.conbuildmat.2023.130458
Khalil, N. M., Algamal, Y., and Saleem, Q. M. (2018). Exploitation of petroleum waste sludge with local bauxite raw material for producing high-quality refractory ceramics. Ceram. Int. 44, 18516–18527. doi:10.1016/j.ceramint.2018.07.072
Kingman, S. W., Robinson, J. P., Snape, C. E., Barranco, R., Shang, H., Bradley, M., et al. (2009). Remediation of oil-contaminated drill cuttings using continuous microwave heating. Chem. Eng. J. 152, 458–463. doi:10.1016/j.cej.2009.05.008
Lau, P. C., Teo, D. C. L., and Mannan, M. A. (2017). Characteristics of lightweight aggregate produced from lime-treated sewage sludge and palm oil fuel ash. Constr. Build. Mat. 152, 558–567. doi:10.1016/j.conbuildmat.2017.07.022
Li, C. B., Zhang, G. F., Liu, D. Z., and Wang, M. T. (2023). Preparation of lightweight ceramsite from solid waste lithium slag and fly ash. Constr. Build. Mat. 398, 132419. doi:10.1016/j.conbuildmat.2023.132419
Li, X. G., Wang, P. Q., Qin, J. Y., Liu, Y. X., Qu, Y., Liu, J. J., et al. (2020). Mechanical properties of sintered ceramsite from iron ore tailings affected by two-region structure. Constr. Build. Mat. 240, 117919. doi:10.1016/j.conbuildmat.2019.117919
Li, Y. T., Zheng, B. P., Yang, Y. H., Chen, K. J., Chen, X. L., Huang, X., et al. (2022). Soil microbial ecological effect of shale gas oil-based drilling cuttings pyrolysis residue used as soil covering material. J. Hazard. Mat. 436, 129231. doi:10.1016/j.jhazmat.2022.129231
Li, Y., Wu, D., Zhang, J., Chang, L., Wu, D., Fang, Z., et al. (2000). Measurement and statistics of single pellet mechanical strength of differently shaped catalysts. Powder. Technol. 113, 176–184. doi:10.1016/S0032-5910(00)00231-X
Liang, B., Zhang, M. X., Li, H., Zhao, M., Xu, P. F., and Deng, L. B. (2021). Preparation of ceramic foams from ceramic tile polishing waste and fly ash without added foaming agent. Ceram. Int. 47, 23338–23349. doi:10.1016/j.ceramint.2021.05.047
Liu, D. S., Wang, C. Q., Mei, X. D., and Zhang, C. (2018). Environmental performance, mechanical and microstructure analysis of non-fired bricks containing water-based drilling cuttings of shale gas. Constr. Build. Mat. 183, 215–225. doi:10.1016/j.conbuildmat.2018.06.107
Liu, W. S., Xiong, X. Y., Zhao, Y. L., Liu, C. Y., Hou, Y. B., and Pu, X. C. (2023). Preparing high-strength and low-density proppants with oil-based drilling cuttings pyrolysis residues and red mud: process optimization and sintering mechanism. Fuel 331, 125777. doi:10.1016/j.fuel.2022.125777
Long-González, D., López-Cuevas, J., Gutiérrez-Chavarría, C. A., Pena, P., Baudin, C., and Turrillas, X. (2009). Synthesis of monoclinic celsian from coal fly ash by using a one-step solid-state reaction process. Ceram. Int. 36, 661–672. doi:10.1016/j.ceramint.2009.10.008
Maitra, S., Choudhury, A., Das, H. S., and Pramanik, M. J. (2005). Effect of compaction on the kinetics of thermal decomposition of dolomite under non-isothermal condition. J. Mat. Sci. 40, 4749–4751. doi:10.1007/s10853-005-0843-0
Mi, H. C., Yi, L. S., Wu, Q., Xia, J., and Zhang, B. H. (2021). Preparation of high-strength ceramsite from red mud, fly ash, and bentonite. Ceram. Int. 47, 18218–18229. doi:10.1016/j.ceramint.2021.03.141
Mi, H. C., Yi, L. S., Wu, Q., Xia, J., and Zhang, H. (2022). A review of comprehensive utilization of red mud. Waste. Manage. 40, 1594–1607. doi:10.1177/0734242X221107987
Mishra, A., Siddiqi, H., Kumari, U., Behera, I. D., Mukherjee, S., and Meikap, B. C. (2021). Pyrolysis of waste lubricating oil/waste motor oil to generate high-grade fuel oil: a comprehensive review. Renew. Sust. Energy Rev. 150, 111446. doi:10.1016/j.rser.2021.111446
Omar Ahmed, T., and Hassan Assem, A. A. (2021). Behaviour of expanded slate semi-lightweight SCC beams with improved cracking performance and shear capacity. Structures 32, 1577–1588. doi:10.1016/j.istruc.2021.03.108
Owens, E., and Santner, R. (2021). Integration of a shoreline response program (SRP) and shoreline assessment surveys into an incident management system for oil spill response. J. Environ. Manage. 279, 111637. doi:10.1016/j.jenvman.2020.111637
Pei, J. N., Pan, X. L., Qi, Y. F., Yu, H. Y., and Tu, G. F. (2022). Preparation of ultra-lightweight ceramsite from red mud and immobilization of hazardous elements. J. Environ. Chem. Eng. 10, 108157. doi:10.1016/j.jece.2022.108157
Qi, Y. F., Yue, Q. Y., Han, S. X., Yue, M., Gao, B. Y., Yu, H., et al. (2009). Preparation and mechanism of ultra-lightweight ceramics produced from sewage sludge. J. Hazar. Mat. 176, 76–84. doi:10.1016/j.jhazmat.2009.11.001
Qin, J., Cui, C., Cui, X. Y., Hussain, A., and Yang, C. M. (2015). Preparation and characterization of ceramsite from lime mud and coal fly ash. Constr. Build. Mat. 95, 10–17. doi:10.1016/j.conbuildmat.2015.07.106
Ren, Q., Ren, Y. H., Li, H. H., Wu, X. L., Bai, W., Zheng, J., et al. (2019). Preparation and characterization of high silicon ceramic proppants using low grade bauxite and fly ash. Mat. Chem. Phys. 230, 355–361. doi:10.1016/j.matchemphys.2019.04.009
Riley, C. M. (1951). Relation of chemical properties to the bloating of clays. J. Am. Ceram. Soc. 34, 121–128. doi:10.1111/j.1151-2916.1951.tb11619.x
Shang, S., Fan, H. H., Li, Y. X., Li, L., and Li, Z. (2022). Preparation of lightweight ceramsite from solid waste using SiC as a foaming agent. Materials 15, 325. doi:10.3390/ma15010325
Shih, Y. T., and Jean, J. H. (2017). Low-fire processing of microwave (Ca1−xSrx)(Zr1−yMny)O3 dielectric with Li2O-B2O3-SiO2 glass in H2/N2. Ceram. Int. 43, S306–S311. doi:10.1016/j.ceramint.2017.05.215
Sun, Y. H., Li, J. S., Chen, Z., Xue, Q., Sun, Q., Zhou, Y. F., et al. (2021). Production of lightweight aggregate ceramsite from red mud and municipal solid waste incineration bottom ash: mechanism and optimization. Constr. Build. Mat. 287, 122993. doi:10.1016/j.conbuildmat.2021.122993
Tsai, C. C., Wang, K. S., and Chiou, I. J. (2006). Effect of SiO2-Al2O3-flux ratio change on the bloating characteristics of lightweight aggregate material produced from recycled sewage sludge. J. Hazard Mat. 134, 87–93. doi:10.1016/j.jhazmat.2005.10.035
Wang, C. Q., Jin, J. Z., Lin, X. Y., Xiong, D. M., and Mei, X. D. (2017). A study on the oil-based drilling cutting pyrolysis residue resource utilization by the exploration and development of shale gas. Environ. Sci. Pollut. R. 24, 17816–17828. doi:10.1007/s11356-017-9199-7
Wang, C. Q., Lin, X. Y., Mei, X. D., and Luo, X. G. (2019). Performance of non-fired bricks containing oil-based drilling cuttings pyrolysis residues of shale gas. J. Clean. Prod. 206, 282–296. doi:10.1016/j.jclepro.2018.09.128
Wang, D., Huang, J. L., Peng, H. T., and Huang, J. L. (2014). Sinterability and expansion property of ceramsite made with lead-zinc mine tailings. Des. Manuf. Mechatron. 551, 23–27. doi:10.4028/www.scientific.net/AMM.551.23
Wang, L. K., Shao, Y. L., Zhao, Z. L., Chen, S., and Shao, X. H. (2020). Optimized utilization studies of dredging sediment for making water treatment ceramsite based on an extreme vertex design. J. Water. Process. Eng. 38, 101603. doi:10.1016/j.jwpe.2020.101603
Xie, X., Wang, D., Liu, D., Zhang, X., and Oeser, M. (2016). Investigation of synthetic, self-sharpening aggregates to develop skid-resistant asphalt road surfaces. Wear 348-349, 52–60. doi:10.1016/j.wear.2015.11.022
Xiong, D. M., and Wang, C. Q. (2021). Physical characteristics and environmental risks assessment of oil-based drilling cuttings residues used for subgrade materials. J. Clean. Prod. 323, 129152. doi:10.1016/j.jclepro.2021.129152
Yang, H., Liu, Y. L., Bai, G. L., Feng, Z., Zhang, Y., and Xia, S. B. (2022). Solidification and utilization of water-based drill cuttings to prepare ceramsite proppant with low-density and high performance. Pet. Sci. 19, 2314–2325. doi:10.1016/j.petsci.2022.06.006
Yang, H. Y., Li, E. Z., Yang, H. C., He, H. C., and Zhang, R. S. (2018). Synthesis of Zn0.5Ti0.5NbO4 microwave dielectric ceramics with Li2O-B2O3-SiO2 glass for LTCC application. Int. J. Appl. Glas. Sci. 9, 392–402. doi:10.1111/ijag.12334
Yang, Y. F., Inamori, Y. H., Ojima, H., Machii, H., and Shimizu, Y. (2005). Development of an advanced biological treatment system applied to the removal of nitrogen and phosphorus using the sludge ceramics. Water. Res. 39, 4859–4868. doi:10.1016/j.watres.2004.10.019
Yashima, S., Kanda, Y., and Sano, S. (1987). Relationships between particle size and fracture energy or impact velocity required to fracture as estimated from single particle crushing. Powder. Technol. 51, 277–282. doi:10.1016/0032-5910(87)80030-X
Yoon, K. H., Park, M. S., Cho, J. Y., and Kim, E. S. (2003). Effect of B2O3-Li2O on microwave dielectric properties of (Ca0.275Sm0.4Li0.25)TiO3 ceramics. J. Eur. Ceram. Soc. 23, 2423–2427. doi:10.1016/s0955-2219(03)00164-x
Zhao, D., Gao, Y. N., Nie, S., Liu, Z. C., Wang, F. Z., Liu, P., et al. (2018). Self-assembly of honeycomb-like calcium-aluminum-silicate-hydrate (C-A-S-H) on ceramsite sand and its application in photocatalysis. Chem. Eng. J. 344, 583–593. doi:10.1016/j.cej.2018.03.074
Keywords: oil-based drilling cutting pyrolysis residues, building ceramsite, sintering reaction, lightweight, high-strength
Citation: Wang H, Li J, Lin D, Jiang G, Zhao L, Yu J, Meng T, Huang X, Liu H and Yang Y (2023) Preparation and properties of lightweight and high-strength building ceramsites with oil-based drilling cuttings pyrolysis residues. Front. Mater. 10:1245121. doi: 10.3389/fmats.2023.1245121
Received: 23 June 2023; Accepted: 15 August 2023;
Published: 24 August 2023.
Edited by:
Sabrina Arcaro, University of the Extreme South of Santa Catarina, BrazilReviewed by:
Marcelo Tramontin, Universidade Estadual de Santa Cruz, BrazilCopyright © 2023 Wang, Li, Lin, Jiang, Zhao, Yu, Meng, Huang, Liu and Yang. This is an open-access article distributed under the terms of the Creative Commons Attribution License (CC BY). The use, distribution or reproduction in other forums is permitted, provided the original author(s) and the copyright owner(s) are credited and that the original publication in this journal is cited, in accordance with accepted academic practice. No use, distribution or reproduction is permitted which does not comply with these terms.
*Correspondence: Yuanyi Yang, eWFuZ3l1YW55aUBzd3B1LmVkdS5jbg==
Disclaimer: All claims expressed in this article are solely those of the authors and do not necessarily represent those of their affiliated organizations, or those of the publisher, the editors and the reviewers. Any product that may be evaluated in this article or claim that may be made by its manufacturer is not guaranteed or endorsed by the publisher.
Research integrity at Frontiers
Learn more about the work of our research integrity team to safeguard the quality of each article we publish.