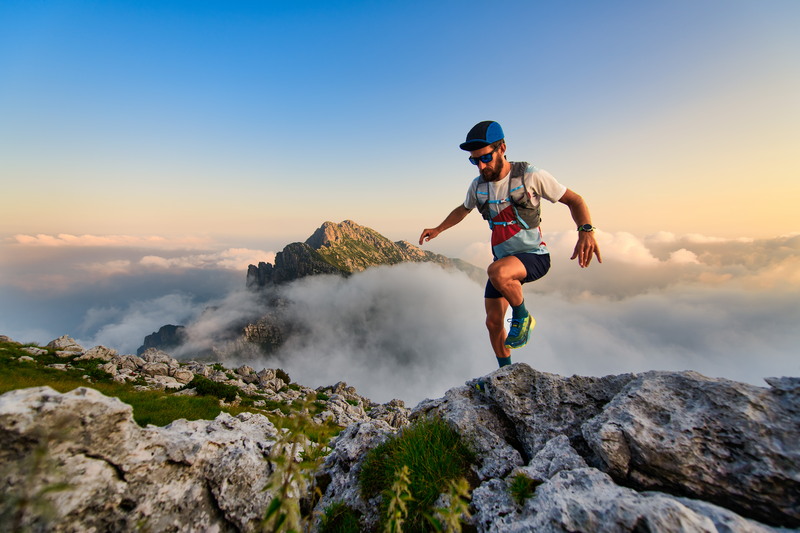
95% of researchers rate our articles as excellent or good
Learn more about the work of our research integrity team to safeguard the quality of each article we publish.
Find out more
REVIEW article
Front. Mater. , 17 August 2023
Sec. Structural Materials
Volume 10 - 2023 | https://doi.org/10.3389/fmats.2023.1243392
This article is part of the Research Topic Recent advances in eco-friendly construction materials: waste upcycling in building materials View all 3 articles
Recycled carbon fiber, as a novel form of regenerated fiber, exhibits exceptional properties such as high strength, high modulus, excellent electrical conductivity, and corrosion resistance. Consequently, it has garnered significant attention in recent years, owing to its potential to confer unique intelligent characteristics to cement-based materials. However, the dispersion of recycled carbon fiber remains an inevitable concern. Building upon existing research, this paper meticulously categorizes different types of recycled carbon fiber based on their mechanical properties and surface characteristics, while also exploring the impact of additives on fiber dispersion. Furthermore, a thorough evaluation of fiber dispersion methods is provided, considering the dimensions of stability, uniformity, and morphology at various stages, including fiber suspension, fresh mixture, and hardened matrix. Additionally, this paper offers a comprehensive summary and comparison of fiber dispersion methods, taking into account fiber pretreatment and preparation processes. Extensive literature reviews unequivocally support the notion that achieving a uniform dispersion of recycled carbon fiber serves as a fundamental requirement for enhancing and optimizing the properties of composites. Consequently, the utilization of dispersion and evaluation methods based on carbon fiber enables the exploration of appropriate dispersion methods tailored to different types of recycled carbon fiber in cement-based materials.
Concrete, as one of the most extensively utilized raw materials in various civil engineering applications, offers the advantages of convenient sourcing and cost-effectiveness, thereby playing a crucial role in fostering societal and technological advancements. However, with the shift towards high-strength, high-performance, and large-span structures, the inherent flaws of concrete, such as susceptibility to cracking and brittleness, have become increasingly evident, rendering it insufficient to meet the demands of contemporary engineering practices (Khaloo et al., 2008; Tsangouri et al., 2019). Consequently, the implementation of fiber has emerged as a prevalent method to enhance concrete performance, giving rise to the advent of fiber reinforced cement-based composite (Song and Hwang, 2004; Wille et al., 2014).
Different types of fiber, including synthetic fiber like polypropylene and polyvinyl alcohol, as well as basalt fiber, carbon fiber, and steel fiber, are commonly used in cement concrete. Among them, carbon fiber stands out due to its exceptional properties. It not only enhances the crack resistance and strength of the matrix but also imparts intelligent attributes such as conductivity (Belli et al., 2020), piezoresistivity (Han et al., 2020), electrothermal behavior (Tang et al., 2005), and electromagnetic shielding (Khalid et al., 2017), laying the theoretical foundation for the development and application of carbon fiber cement-based composites (CFCC) (Allam et al., 2022a).
However, the small diameter of carbon fiber makes it prone to agglomeration during the mixing process. Additionally, the resin on its surface significantly affects its compatibility with the matrix, resulting in uneven fiber dispersion. This phenomenon introduces an excessive number of weak interfacial regions, seriously compromising the mechanical properties of the matrix, and thereby limiting the extent of research and application in the field of CFCC (Wang et al., 2014; Li et al., 2019b). Therefore, investigating the dispersion of carbon fiber serves as a fundamental step in the subsequent research on CFCC (Zhu et al., 2021; Hao et al., 2023). It is of utmost importance to explore effective methods for carbon fiber dispersion and accurately evaluate the degree of fiber dispersion.
The dispersion of carbon fiber in cement-based materials is influenced by various factors, including fiber types, dispersion methods, and preparation processes. The use of dispersants is the most common method, as it improves the hydrophilicity of carbon fiber and forms a thin film on its surface, effectively preventing fiber entanglement and agglomeration (Chuang et al., 2018). Ultrasonic treatment is often employed in conjunction with dispersants to further enhance fiber dispersion and achieve a uniform monofilament state (Wang et al., 2008; Stynoski et al., 2015). Surface modification is another widely used method. It has been reported that carbon fiber treated with high-temperature oxidation exhibits increased active functional groups, enhancing fiber hydrophilicity and dispersion (Catala et al., 2011). Similarly, high-temperature removal of surface coupling agents improves the adhesion between carbon fiber and the cementitious matrix, thereby enhancing the mechanical performance of CFCC (Li et al., 2021). In addition, a well-designed preparation process promotes fiber dispersion. The combination of dispersant treatment and pre-mixing method is a commonly used method, resulting in improved overall dispersion of carbon fiber (Gao et al., 2017; Thomoglou et al., 2022). However, the inherent properties of the fiber and process cost must also be considered, and the use of co-mixing or after-mixing methods for CFCC preparation is prevalent (Mastali et al., 2017; Donnini et al., 2018; Akbar and Liew, 2020b).
Accurate evaluation methods for fiber dispersion are essential prerequisites for comparing different dispersion methods. Yang (2002) initially proposed four methods: the fresh mixture method, the scanning electron microscope method, the measurement of electrical resistance method, and the simulation experiment method. It was emphasized that a combination of multiple methods is necessary to precisely evaluate the dispersion of carbon fiber. With the advancement of graphic processing technology, optical microscope and X-ray computed tomography (X-CT) scanner have also been gradually employed to assess the dispersion of carbon fiber in cement-based materials (Wang et al., 2014; Gao et al., 2017). Furthermore, the unique electrical properties of CFCC can be utilized for fiber dispersion evaluation, such as contact resistivity (Fu et al., 1996), impedance spectroscopy (Ozyurt et al., 2006; Faneca et al., 2018), and electromagnetic shielding effectiveness (Zornoza et al., 2010).
However, due to the increasing popularity of carbon fiber reinforced plastics (CFRP) in recent years, the demand for carbon fiber has surged, with an astonishing annual growth rate of 11%. In fact, in 2022 alone, the global demand for carbon fiber surpassed 24,000 tons (Bledzki et al., 2021; Pakdel et al., 2021). This rapid growth inevitably leads to a substantial accumulation of carbon fiber waste, posing significant environmental challenges and concerns (Meng et al., 2018; Lefeuvre et al., 2019). The extracted recycled carbon fiber from such waste exhibits considerable variations in properties and surface characteristics, owing to the diverse sources and recycling methods involved, thereby further complicating the recycling and utilization processes (Pakdel et al., 2021). Fortunately, numerous scholars are currently involved in investigating the properties of recycled carbon fiber cement-based composites (RCFCC), not only promoting the development and application of environmentally friendly intelligent concrete but also contributing to waste management, aligning with the principles of sustainability and ecological consciousness (Akbar et al., 2021; Mobili et al., 2022a). However, a clear classification and systematic overview of commonly used recycled carbon fiber for cement concrete is currently lacking, indicating the need for a comprehensive and organized analysis.
Although there have been reviews on the evaluation methods for the dispersion of synthetic fibers in cement-based materials, some of these methods may not be directly applicable to carbon fiber due to its unique properties. Additionally, there is a notable absence of evaluation methods based on electrical properties, creating a gap in establishing an effective validation system for these methods (Cao et al., 2018; Hao et al., 2023). Therefore, conducting a comprehensive retrospective analysis of the dispersion of carbon fiber in cement-based materials becomes imperative. Moreover, given the intricate nature of recycled carbon fiber and the ongoing advancements in its incorporation into cement-based materials, addressing the dispersion challenges of recycled carbon fiber becomes indispensable as a prerequisite and fundamental aspect for subsequent investigations. Thus, a thorough survey and review of the existing dispersion evaluation methods pertaining to carbon fiber and recycled carbon fiber in cement-based materials significantly complement and enrich the field of research in fiber cement-based composites. Additionally, to ensure the inclusiveness of this review, a small portion will encompass research outcomes pertaining to nanofiber such as carbon nanofiber (CNF) and carbon nanotubes (CNTs). Consequently, this paper presents a comprehensive and systematic classification and summary of the factors affecting the dispersion of carbon fiber or recycled carbon fiber in cement-based materials, using relevant literature retrieved from Web of Science. Subsequently, the target literature is managed uniformly using Endnote software to avoid repeated citations of the literature. It encompasses the types of raw materials, dispersion evaluation methods, and dispersion methods, offering valuable reference for those interested in exploring the fiber dispersion in cementitious matrix.
This paper initiates with a comprehensive discussion on the influence of different raw materials on fiber dispersion in Section 2, encompassing carbon fiber, recycled carbon fiber, dispersants, admixtures, and additives. Subsequently, Section 3 discusses the evaluation methods employed at various stages to assess fiber dispersion, including the fiber suspension stage, fresh mixture stage, and hardened matrix stage. Lastly, Section 4 delves into the methods employed for fiber dispersion, categorized into two distinct segments: fiber pretreatment and preparation processes. The overall flowchart for all sections is illustrated in Figure 1.
The type, content, and length of fiber directly influence the dispersion state, which, in turn, significantly impacts the performance of CFCC and RCFCC. Therefore, in this section, we systematically discuss the various types of fiber and the admixtures or additives involved in achieving effective fiber dispersion.
Currently, CFCC predominantly utilizes chopped carbon fiber with an average length of approximately 6 mm and a diameter of around 7 µm. The fiber possesses an impressive length-to-diameter ratio of approximately 857, which is also one of the reasons for the difficulty of dispersion (Kerekes and Schell, 1992). In terms of mechanical properties, carbon fiber exhibits a widespread tensile strength range of 3,000–5,000 MPa and an elastic modulus range of 200–250 GPa. The specific properties indexs of carbon fiber are shown in Table 1.
Scanning electron microscopy (SEM) analysis reveals the smooth surface of carbon fiber, with a small amount of residual silane acting as the coupling agent between the fiber (Li et al., 2019b; Belli et al., 2020; Ji et al., 2021). Furthermore, atomic force microscopy and X-ray photoelectron spectroscopy results indicate that the carbon fiber surface primarily consists of carbon, oxygen, and nitrogen elements. Additionally, more than 60% of the surface functional groups are hydrophobic, making it challenging for water to wet the carbon fiber (Dilsiz and Wightman, 1999). Consequently, due to its high aspect ratio and hydrophobic surface characteristics, carbon fiber tends to agglomerate at the interfaces, impeding its dispersion within cement-based materials (Fu et al., 1996).
In the production and application of carbon fiber, a significant amount of waste is generated, which can be classified as carbon fiber scrap and CFRP waste (Pickering, 2006; Gopalraj and Karki, 2020; Pakdel et al., 2021). Carbon fiber scrap, which is not combined with other materials, can be directly processed into alternative products. However, CFRP waste requires specific treatment before it can be effectively utilized. Common recycling methods include thermal treatment, mechanical treatment, and chemical treatment (Wang et al., 2023), each corresponding to different properties of recycled carbon fiber.
Recycled carbon fiber can be broadly defined as the fiber obtained from the waste fiber generated during carbon fiber production and the recycling of CFRP waste, including recycled carbon fiber reinforced polymers. Based on the existing research, recycled carbon fiber can be classified into five categories: i) finished waste carbon fiber, ii) semi-finished waste carbon fiber, iii) pyrolysis carbon fiber, iv) chopped CFRP fiber and v) chemically recycled carbon fiber, as depicted in Figure 2.
FIGURE 2. Five types of recycled carbon fiber (Nguyen et al., 2016; Hasan et al., 2018; Xiong et al., 2021; Li et al., 2023).
Finished waste carbon fiber mainly consist of offcuts generated during the carbon fiber production process. Several researchers incorporated a mixture of carbon fiber and graphite fiber obtained from production line spools into cement-based materials (Belli et al., 2018; Mobili et al., 2021; Mobili et al., 2022a; Mobili et al., 2022b; Mobili et al., 2023). Yan et al. (2022) employed trimmed waste carbon fiber as chopped fiber mixed with concrete. Table 2 provides specific properties indexs of finished waste carbon fiber.
Remarkably, this recycled carbon fiber exhibits no significant differences in properties compared to virgin carbon fiber, particularly in terms of mechanical properties. The tensile strength generally ranges around 3,500 MPa, while the tensile modulus is approximately 230 GPa. Additionally, Belli et al. (2018) noted that the surface coating of finished waste carbon fiber obtained from production line spools consists of glycerol, which distinguishes it from the epoxy coatings found on carbon fiber.
During the production process, a significant amount of semi-finished waste is generated, mainly consisting of uncured and expired prepreg waste carbon fiber (Nilakantan and Nutt, 2018; Reis de Souza et al., 2019). Currently, there is limited research on the utilization of such recycled carbon fiber in cement-based materials. Only Nguyen et al. (2016) have incorporated prepreg waste carbon fiber sourced from the aerospace industry into cement mortar to study its impact on mechanical properties of the matrix. However, the lack of specific fiber performance indicators, especially regarding the alkali resistance of recycled carbon fiber, poses a uncertainty. It is essential to test the alkali resistance because the alkaline nature of cement-based materials necessitates fiber with high resistance to ensure optimal performance. It is determined that inadequate or incomplete processing steps may compromise fiber performance, resulting in significant disparities between semi-finished carbon fiber and virgin carbon fiber, thus classifying it as a type of recycled carbon fiber.
Considering the substantial proportion of finished and semi-finished waste carbon fiber in the overall carbon fiber waste, coupled with their lower production costs compared to virgin carbon fiber, the recycling and utilization of recycled carbon fiber generated during the production stage is expected to receive increasing attention in the future. Furthermore, this presents a promising and competitive alternative for incorporating fiber into cement-based materials.
The thermal recycling of CFRP waste primarily involves two methods: pyrolysis and fluidized bed processes (Pakdel et al., 2021). Pyrolysis carbon fiber refers to the fiber obtained by separating it from CFRP waste through the pyrolysis process. Pyrolysis offers an effective means to optimize the distribution of surface functional groups on the fiber and enhance the presence of oxygen-containing groups, which plays a crucial role in facilitating fiber dispersion (Fu et al., 1996; Chung, 2005). However, precise temperature control is essential during both the pyrolysis and oxidation stages to ensure the maximum preservation of pyrolysis carbon fiber properties (Mazzocchetti et al., 2018), with controlled fiber strength loss of approximately 10% (Pickering, 2006; Pimenta and Pinho, 2011).
Currently, there is a paucity of research on the utilization of the fluidized bed method for carbon fiber recovery, and its impact on surface oxidation of the recycled carbon fiber is limited (Pakdel et al., 2021). It has been observed that the application of the fluidized bed method in the recovery of glass fiber composite waste results in a significant decline in fiber performance, with a reduction in tensile strength of approximately 50% (Pickering et al., 2000). Conversely, the pyrolysis method has reached an industrial-scale level of development and exhibits higher efficiency in the recovery process. Consequently, the subsequent discussion primarily focuses on the properties and surface characteristics of pyrolysis carbon fiber.
In recent years, there has been a growing interest in utilizing pyrolysis carbon fiber as a reinforcing material in cement concrete, with researchers investigating its relevant properties. Nguyen et al. (2016) introduced carbon fiber obtained from carbon yarns through pyrolysis into cement mortar, utilizing fiber lengths ranging from 0.05 to 15 mm. Faneca et al. (2018) incorporated four different types of pyrolysis carbon fiber into both conventional and ultra-high performance concrete. Akbar and Liew (2020b); Akbar et al. (2021) added pyrolysis milled carbon fiber, measuring up to 80–100 µm in length, to cement mixtures. Li et al. (2021) integrated pyrolysis carbon fiber produced using microwave-assisted pyrolysis technology into concrete. Specific fiber properties are detailed in Table 3.
From Table 3, it becomes evident that the mechanical properties of pyrolysis carbon fiber are comparable to those of virgin carbon fiber. This compelling evidence strongly suggests that the implementation of appropriate pyrolysis treatment does not compromise the mechanical performance of recycled carbon fiber.
The recycling process of CFRP waste introduces variations in crystallinity, sizing, impurities, and pyrolysis procedures, resulting in subtle physicochemical differences in the resulting pyrolysis carbon fiber (Mazzocchetti et al., 2018; Pakdel et al., 2021). Akbar and Liew (2020b); Akbar et al. (2021) discovered residual epoxy resin on the surface of pyrolysis carbon fiber. They also highlighted that the surface functional groups of pyrolysis carbon fiber are more active than those of virgin carbon fiber, optimizing the interfacial transition zone between fiber and cement and forming stronger interfacial chemical bonds. Moreover, the surface of such fiber features numerous grooves and a rougher texture than virgin carbon fiber. These surface grooves provide additional inert hydration nucleation sites for cement and silica fume, thereby enhancing the bonding strength and improving the mechanical properties of the composites (Akbar and Liew, 2020b; Akbar et al., 2021; Li et al., 2021), as illustrated in Figure 3.
FIGURE 3. Surface morphology of pyrolysis carbon fiber (Akbar et al., 2021).
Based on the current research achievements in incorporating pyrolysis carbon fiber into cement-based materials, the advantages of pyrolysis carbon fiber over virgin carbon fiber are more pronounced. It can be regarded as undergoing an additional high-temperature oxidation treatment (as discussed in Section 4.1.2), which not only enhances the reactivity of surface functional groups but also facilitates the degree of fiber dispersion and effective bonding with the cementitious matrix. Furthermore, the cost savings of 30%–40% associated with pyrolysis carbon fiber compared to virgin carbon fiber undoubtedly contribute to the research and application of pyrolysis carbon fiber cement-based composites (Pimenta and Pinho, 2011; Faneca et al., 2018; Khalid et al., 2022).
Chopped CFRP fiber is produced by mechanically processing recycled CFRP waste through methods such as shredding, grinding, or milling, which effectively reduce the fiber length. This mechanical recycling approach offers several advantages, including lower cost, higher production efficiency, and suitability for industrial-scale production. Furthermore, the shortened fiber length enhances the compatibility of recycled carbon fiber with various engineering materials, including concrete and asphalt (Pakdel et al., 2021; Wang et al., 2023). Extensive literature exists on the investigation of the influence of chopped CFRP fiber on the properties of cement-based materials. For detailed fiber properties, please refer to Table 4.
From Table 4, it is evident that there is a considerable variation in the lengths of the chopped CFRP fiber. This discrepancy primarily arises from variations in parameters such as blade spacing, screen size, and rotational speed, which are specific to the equipment used for mechanical recycling, such as multiple shaft shredding and cutting mills (Pakdel et al., 2021). Additionally, it is important to note that the recycled carbon fiber exhibits a sheet-like morphology rather than a singular fiber structure, introducing considerations of width and thickness. For instance, Wang et al. (2019) utilized chopped CFRP fiber with a maximum width of 0.8 mm, while Xiong et al. (2020); Xiong et al. (2021) employed chopped CFRP fiber with widths and thicknesses of 2 and 0.2 mm, respectively. Given the substantial impact of fiber dimensions, it is worth mentioning that limited research has been conducted on investigating the influence of different-sized chopped CFRP fiber on the properties of cement-based materials.
Furthermore, it is noteworthy that mechanical recycling, devoid of any chemical reactions, maintains the density and mechanical performance indicators of the fiber on par with virgin carbon fiber. However, this process also results in the presence of residual resin and adsorption of minute particles on the fiber surfaces (Ogi et al., 2005; Xiong et al., 2020; Pakdel et al., 2021). Belli et al. (2020) employed SEM to examine the surface morphology of chopped CFRP fiber and discovered the presence of carbon micro-fragments generated during the mechanical processing. Given the intricate composition of this recycled carbon fiber, it can impact the interfacial behavior between the fiber and the matrix. Therefore, future investigations on the utilization of chopped CFRP fiber in cement-based materials will primarily focus on enhancing interfacial performance and related aspects.
Currently, there is a scarcity of research on the utilization of chemical treatment for recycling and incorporating CFRP waste into cement concrete. Li et al. (2023) are among the few researchers who have explored the use of different concentrations of hydrogen peroxide solution and varying reaction times for CFRP waste treatment. Their findings revealed that the treated fiber exhibited longitudinal grooves on the surface, and the reduced surface resin increased the contact area between the fiber and the matrix. This, in turn, facilitated the adhesion of hydration products on the fiber surface, ultimately improving the interfacial effect between the fiber and cement matrix.
However, it is essential to consider some challenges associated with chemical treatment methods. These methods demand high-end equipment, involve significant costs, and present potential hazards during the recycling process, making it challenging to establish large-scale recycling production lines (Oliveux et al., 2015; Khalil, 2018). Moreover, the chemical recycling process is akin to the liquid-phase surface oxidation of carbon fiber, as discussed in Section 4.1.2. If not executed with care, the residual chemicals on the fiber surface can adversely impact the cement hydration process, leading to the degradation of the matrix’s microstructure.
Silica fume is widely used as a mineral admixture in cement-based materials. It is an ultrafine amorphous powder composed of silica, with particle diameters approximately 1/100th that of cement. By optimizing the pore structure and enhancing the compactness of the cement matrix, silica fume improves the interfacial characteristics between fiber and cement (Poon et al., 2006; Rossignolo, 2009). Moreover, the small particles of silica fume act as wedges between carbon fiber, effectively separating and dispersing the fiber bundles and agglomerates, thereby enhancing the dispersion of carbon fiber within the cement-based matrix (Chung, 2005; Sanchez and Ince, 2009; Yazdanbakhsh and Grasley, 2014). It has been found that a 10% replacement of cement with silica fume yields optimal results, promoting the densification of the microstructure within the matrix (Poon et al., 2006; Rossignolo, 2009). Therefore, silica fume is a commonly employed mineral admixture in CFCC.
Different particle sizes of silica fume have varying effects on CFCC. According to reports, silica fume with an average particle size ranging from 5 to 15 µm demonstrates an effective improvement in the compressive strength and flexural strength of CFCC. However, silica fume with an average particle size ranging from 5 to 75 µm does not exhibit a noticeable enhancement in CFCC strength (Ivorra et al., 2010). Furthermore, Garg et al. (2020) pointed out that micron silica (silica fume) shows a greater ability to enhance the dispersion of carbon nanotubes and carbon fiber in water compared to nano silica. The silica particles form a robust interfacial bond with the fiber surface, reducing the porosity of the composite and improving both the mechanical and electrical properties of the matrix. Additionally, Stynoski et al. (2015) discovered that the combination of silica fume and fiber treated with silica functional groups effectively enhances the interfacial transition zone, facilitates the dispersion of fiber within the cementitious matrix, and significantly increases the fracture toughness of the matrix.
Similarly, numerous scholars have explored the incorporation of silica fume into RCFCC, aiming to enhance both fiber dispersion and the interfacial properties between fiber and the cementitious matrix, thereby improving the overall properties of the composites (Nguyen et al., 2016; Li et al., 2019a; Akbar and Liew, 2020a; Akbar and Liew, 2020b; Akbar et al., 2021). Akbar and Liew (2020a) demonstrated that substituting 10% of the total cement mass with silica fume further enhances the mechanical properties of RCFCC. Additionally, with the inclusion of recycled carbon fiber, the overall global warming potentia of the composites is reduced by 13.69% compared to the baseline group. Notably, for pyrolysis carbon fiber, the presence of channels and grooves on their surface provides additional hydration nucleation sites for fine silica fume particles, leading to the formation of a denser C-S-H gel and improved interfacial adhesion between the recycled carbon fiber and the cementitious matrix (Akbar et al., 2021).
Certainly, fly ash is a commonly utilized admixture in CFCC and has shown to aid in the dispersion of carbon fiber within the cementitious matrix (Demirel and Yazicioglu, 2008; Zornoza et al., 2010; Khaleel et al., 2021). The incorporation of fly ash has also been explored in RCFCC (Rangelov et al., 2016; Mastali et al., 2017; Wang et al., 2019). However, it is noteworthy that there is a scarcity of research investigating the mutual interactions between fiber and fly ash in such composites.
In the realm of CFCC, chemical additives such as water reducers, dispersants, and defoamers are commonly employed. Among these, dispersants hold particular significance due to their direct influence on the dispersion effectiveness of carbon fiber. Dispersants can be categorized as either ionic or non-ionic, each exhibiting distinct properties indicators, which are detailed in Table 5.
Upon careful examination of Table 5, it becomes apparent that the commonly employed dispersants in CFCC are predominantly non-ionic in nature, such as methylcellulose (MC) and hydroxyethyl cellulose (HEC). Conversely, for ionic dispersants, anionic dispersants like sodium carboxymethyl cellulose (CMC) are frequently utilized, owing to their interaction with the surface charge of carbon fiber. Additionally, some researchers have utilized water reducers as dispersants, especially polycarboxylate-based superplasticizers acting as anionic surfactants (Han et al., 2016; Du et al., 2022; Thomoglou et al., 2022). However, due to the significant variations in fiber properties and surface characteristics resulting from different recycling methods, the surface charge status of fiber may differ, thereby affecting the universal applicability of ionic dispersants in dispersing recycled carbon fiber.
Given the limited presence of active functional groups and low surface activity on carbon fiber, pre-treatment of the fiber surface is often conducted using various chemical agents (Cui et al., 2015), including hydrogen peroxide, concentrated nitric acid, concentrated sulfuric acid, sodium hydroxide, and others (Lavagna et al., 2018; Lu et al., 2018; Li et al., 2019b). These treatments aim to enhance the surface characteristics of the fiber by modifying its chemical composition and increasing its surface reactivity, thereby facilitating subsequent fiber dispersion processing and improving the interfacial bonding between the fiber and the cementitious matrix.
Due to the high aspect ratio and complex surface characteristics of carbon fiber and recycled carbon fiber, achieving uniform dispersion in cement-based materials is challenging. Therefore, it is essential to develop quantitative methods for characterizing the dispersion of carbon fiber or recycled carbon fiber in cement-based materials. In this section, we will provide a comprehensive review of the evaluation methods used to assess the dispersion of carbon fiber in cement-based materials.
Currently, the evaluation methods can be usually classified into two categories: direct methods and indirect methods (Gao et al., 2017; Zhu et al., 2021; Hao et al., 2023). Direct methods involve analyzing the individualization of carbon fiber or the formation of fiber clusters, while indirect methods rely on assessing the macroscopic properties that reflect the degree of fiber dispersion. Considering the interrelatedness of fiber dispersion at different stages of the preparation process and the complementary nature of multiple evaluation methods within each stage, this section will provide a detailed discussion of specific methods for assessing fiber dispersion in cement-based materials at the stages of fiber suspension, fresh mixture, and hardened matrix.
During the fiber suspension stage, which involves the pre-mixing process, the addition of dispersant is commonly employed. Furthermore, ensuring effective dispersion of carbon fiber in water is a prerequisite for achieving uniform dispersion in cement-based materials (Shu et al., 2015; Chuang et al., 2018). Hence, it is of utmost importance to evaluate the degree of fiber dispersion during the suspension stage. The assessment methods for fiber dispersion in this stage can be classified and elucidated based on the stability, uniformity, and morphology of the fiber suspension (Peng et al., 2016; Guan et al., 2017).
Due to the higher density of carbon fiber and recycled carbon fiber compared to water, the fiber tends to continuously settle in water, particularly when it forms bundles or clusters. However, when the fiber is effectively dispersed in the water, the proportion of individualized fiber increases, and it gradually interlocks, resulting in a reduced sedimentation rate. Therefore, the sedimentation height serves as an indirect measure of the degree of fiber dispersion in water and represents the stability of the fiber suspension.
Chen et al. (2014) conducted an assessment of the impact of various dispersants on the dispersion of glass fiber suspensions using sedimentation height as a measure. Their findings indicated that a slower sedimentation time and a smaller sedimentation height of fiber agglomerates corresponded to the formation of a uniform and stable suspension. Comparing the effects of three dispersants on the sedimentation height of the suspension, it was observed that the use of sodium hexametaphosphate resulted in a lower sedimentation height and superior fiber dispersion. Similarly, Cui et al. (2015) evaluated the influence of fatty alcohol ether phosphate salt on the dispersion of carbon fiber in water, employing sedimentation height as a parameter. They concluded that at appropriate dispersant concentrations, the carbon fiber dispersion was improved, leading to longer sedimentation times and increased suspension stability. Furthermore, the simulation experiment method, essentially measuring fiber sedimentation height, was employed (Yang, 2002). Zhu et al. (2021) observed the variation in carbon fiber suspension sedimentation height at different dispersant concentrations. They discovered that the suspension containing dispersants exhibited a gradual decrease in sedimentation height after 30 min of static settling. Nevertheless, once the dispersant concentration reached a certain threshold, the suspension stabilized, indicating that the dispersion effect would not further improve. The dispersion effect graph can be seen in Figure 4.
FIGURE 4. Dispersion of carbon fiber in suspension (Zhu et al., 2021).
Therefore, sedimentation height serves as a rapid and convenient method to assess fiber dispersion in water, particularly for determining the effectiveness of dispersants and establishing the minimum required dosage (Yang, 2002). However, it is important to note that sedimentation height alone cannot precisely determine the optimal dosage of dispersants. Excessive use of dispersants not only hinders fiber dispersion but also has an impact on various properties of cement-based materials (Zhu et al., 2021). On one hand, as fiber gradually individualize, the occurrence of sedimentation is slowed down, but on the other hand, dispersants reduce the Reynolds number of the liquid, leading to a significant increase in its viscosity, which in turn slows down fiber settling. Therefore, sedimentation height can only provide an approximate estimation of the critical dosage of dispersants, and it should be complemented with other methods to comprehensively evaluate the level of fiber dispersion in the suspension.
When dispersants are introduced into the carbon fiber suspension system, they induce changes in the surface potential of the fiber. In the case of ionic dispersants, they enhance the repulsive forces among fiber, thereby facilitating its dispersion. The effectiveness of fiber dispersion is directly correlated with the absolute value of the fiber surface potential, wherein a higher value indicates a superior degree of dispersion. Consequently, the zeta potential serves as a quantifiable and accurate measure of fiber dispersion in water, while also reflecting the stability of the fiber suspension (Alsharef et al., 2019).
Ma et al. (2011) employed zeta potential to compare the dispersion of CNTs in different solvents. They concluded that a zeta potential value of 40 mV corresponds to a highly dispersed state of CNTs, leading to significantly improved suspension stability. Wang et al. (2012) investigated the impact of MC on the zeta potential of CNF suspensions and observed an increasing zeta potential with rising MC concentration until reaching a saturation point. The optimal concentration ratio of MC to CNF was determined to be 2:1. Similarly, Alsharef et al. (2019) evaluated the dispersion stability of CNTs and CNF in water using zeta potential and found that ultrasonic treatment enhanced the dispersion stability of carbon nanomaterials in water, with zeta potential values maintained above 50 mV.
Thus, zeta potential serves as a valuable tool for quantitatively and accurately assessing the stability of fiber suspensions, including systems without dispersants. However, it is worth noting that the majority of studies focusing on zeta potential characterization of fiber dispersion in water have primarily centered on nanofiber materials, with limited research dedicated to examining the dispersion of carbon fiber or recycled carbon fiber using zeta potential analysis.
Absorbance is also a method to evaluate the dispersion of fiber in water. When a beam of light passes through a suspension, uneven fiber dispersion and rapid settling can prevent fiber from distributing well in the water, resulting in a higher transmittance and therefore lower absorbance of the suspension. Conversely, when fiber is adequately dispersed, individualized fiber permeates throughout the water, obstructing the majority of the light beam from passing through the suspension, thereby leading to a noticeable increase in absorbance. As the variation in absorbance conforms to the Beer-Lambert Law, it accurately reflects the concentration of fiber, particularly the concentration of individualized fiber. Therefore, the evaluation of fiber dispersion in a suspension using absorbance serves as an indication of dispersion uniformity.
Chen et al. (2014) argued that higher absorbance values in fiber suspensions reflect better fiber dispersion, while lower absorbance values indicate more pronounced fiber agglomeration. Additionally, they found that the absorbance of the suspension gradually increases with increasing dispersant concentration. However, beyond a certain threshold, the absorbance stabilizes or even decreases, providing evidence that an excessive amount of dispersant can hinder fiber dispersion. Li et al. (2018) utilized absorbance as a measure of CNTs dispersion in suspensions and observed a trend where the absorbance initially increases and then decreases as the dispersant concentration rises. This trend suggests the existence of an optimal dispersant dosage that maximizes fiber dispersion in water.
Unlike sedimentation height, absorbance provides a more precise method for assessing the effectiveness of different dispersants and their concentrations in fiber dispersion. It allows for a comparative analysis and determination of the optimal dispersant and dosage. However, considering the occurrence of fiber sedimentation in suspensions, it is necessary to wait for the suspension to reach a stable state before conducting the experiments. Moreover, when collecting samples, it is advisable to select from the upper layer of the suspension. Additionally, since fiber suspensions treated with dispersants exhibit higher absorbance values, it is crucial to subtract the absorbance of the blank control group to accurately evaluate the degree of fiber dispersion (Li et al., 2018).
However, due to the occurrence of light scattering when using a spectrophotometer to measure the suspension, it is necessary to wait for the tested liquid to reach a stable state before conducting experiments. Therefore, turbidity can also be used to assess the degree of fiber dispersion in the suspension. The principle of turbidity measurement is similar to that of absorbance, as both methods quantitatively measure the concentration of individualized fiber. Higher turbidity values indicate a greater quantity of individualized fiber, reflecting a higher level of fiber dispersion and uniformity.
The research conducted by Cui et al. (2015) demonstrated that the optimal dispersant concentration resulted in the highest turbidity value for the fiber suspension, indicating the superior dispersion effect of carbon fiber. Likewise, Du et al. (2022) investigated the dispersion of modified nano carbon fiber (MCNF) in a saturated calcium hydroxide solution, mimicking the conditions of a concrete environment. They observed an increasing turbidity value of the suspension with an increasing concentration of polycarboxylate superplasticizer, confirming the effective promotion of MCNF dispersion in an alkaline environment.
Therefore, turbidity can serve as a quantitative measure to evaluate the degree of fiber dispersion in water. It allows for a systematic evaluation of the dispersing effects of different dispersants on fiber dispersion in water, akin to absorbance. However, it is important to note that chopped fiber exhibits a certain degree of orientation in water. Thus, turbidity testing necessitates multiple measurements from different orientations to account for this directional characteristic. The coefficient of variation can be utilized as an supplementary evaluation parameter to assess the degree of dispersion.
Image analysis is a direct and quantitative method for evaluating the dispersion of fiber in water by transforming light signals into digital images through various processing techniques such as filtering, sharpening, and grayscale conversion. Several commonly employed methods for image analysis include quadrat analysis, defects analysis, and gray histogram analysis.
Quadrat analysis involves computing the coefficient of variation of fiber-covered areas within different quadrats, which serves as an indicator of fiber dispersion. Defects analysis quantifies the area occupied by agglomerated or bundled fibers, providing insights into the fiber dispersion degree. Gray histogram analysis evaluates the uniformity of fiber dispersion in water based on the brightness of the image. This method generates a histogram of pixel intensities, calculates the probability of occurrence for each intensity value, and utilizes the standard deviation (σ) of the normal distribution curve as a quantifiable metric. A smaller σ signifies a more concentrated brightness distribution, indicating a higher level of fiber dispersion uniformity (Fathi-Khalfbadam et al., 2011; Das et al., 2012; Guan et al., 2017).
Guan et al. (2017) conducted a study on the dispersion of polyester fiber in water, employing three different image analysis methods to investigate the influence of dispersants and agitation parameters. They observed that each of the three image transformation procedures had certain limitations, leading to some degree of bias in the conclusions drawn from the different analysis methods. However, overall, the quadrat analysis method emerged as a more accurate approach compared to the defects analysis and gray histogram analysis methods, offering a better assessment of fiber dispersion in water. Consequently, it is essential to complement the image analysis approach with other evaluation methods to achieve a more precise and comprehensive evaluation of fiber dispersion in water.
It is worth noting that ensuring an appropriate water-to-fiber ratio is critical when using the aforementioned evaluation methods, as it enables better differentiation of the effects of different variables on fiber dispersion. Furthermore, it is advisable to avoid using excessively long fiber for studying dispersion in water, as longer fiber tends to interlace with each other more easily, making dispersion more challenging and hindering the evaluation process (Kerekes and Schell, 1992).
Observing the morphology of fiber at macroscopic, microscopic, and even nanoscopic levels provides valuable insights into the degree of fiber dispersion. Thomoglou et al. (2022) employed visual observations to differentiate the dispersion states of carbon fiber under various dispersants and dispersion methods, revealing that polycarboxylate superplasticizer, in conjunction with ultrasonic vibration, yielded superior fiber dispersion. Garg et al. (2020) compared fiber dispersion morphology among different SP/CNTs using digital imaging and corroborated their findings through SEM analysis. Li et al. (2018) utilized transmission electron microscope to observe the impact of different dispersants on fiber morphology, as depicted in Figure 5. The figure clearly demonstrates that dispersants can effectively mitigate fiber entanglement, with AEP-4 exhibiting a pronounced reduction in entanglement phenomena. Likewise, Xu et al. (2008) employed SEM to observe and evaluate the impact of various factors on the dispersion of sepiolite fiber, revealing that well-dispersed fiber exhibited a noticeable decrease in fiber bundling and a significant increase in individualized fiber. Moreover, Peng et al. (2016) employed optical microscopy to examine the dispersion morphology of slag fiber under varying types and concentrations of dispersants, revealing that the use of composite dispersants effectively enhanced fiber dispersion while mitigating fiber agglomeration and clustering phenomena.
FIGURE 5. TEM images of fiber morphology under different dispersants (A) no surfactant; (B) under SDBS (sodium dodecyl benzenesulfonate); (C) under AEP-4 (dispersants with phenolic resin) (Li et al., 2018).
Morphological observation offers a direct means of evaluating fiber dispersion, enabling preliminary comparisons of the impact of factors such as dispersant type, concentration, and dispersion time on fiber dispersion. However, it is evident that morphological observation provides a qualitative evaluation of the degree of fiber suspension dispersion, and its efficacy is constrained by the limited number and specific locations of samples observed. Therefore, it serves as a complementary and corroborative indicator to enhance the quantitative evaluation of fiber dispersion.
The fiber mass dispersion coefficient serves as a method for quantifying the level of fiber dispersion during the fresh mixture stage, which is consistent with the fresh mixture method (Yang, 2002). The methodology involves extracting samples from various locations, subjecting the fresh mixture to continuous water rinsing, isolating the fiber content, and subsequently drying and weighing it. By applying Eqs 1–3, the coefficient of variation
where
Yang (2002) calculated the fiber mass dispersion coefficient in the mixtures at different stirring times using Eq. 3 and found that a 2-min stirring time resulted in a more significant enhancement of the dispersion coefficient. In a separate study, Sun et al. (2015) employed pre-dispersed carbon fiber and conducted six random samplings in fresh mixture. The calculated variation coefficient, according to Eq. 2, yielded a value of 3.61%. This result serves as evidence of the favorable dispersion effect of carbon fiber in the matrix. Similarly, Zhu et al. (2021) utilized the coefficient of variation to assess the dispersion level of carbon fiber in fresh mixtures. Remarkably, they observed that beyond a dispersant dosage of 0.2%, the variation coefficient remained relatively stable within the fluctuation range of 9%–10%.
The mass coefficient is a direct metric used to assess the dispersion level of fiber in fresh mixtures. However, the accuracy of this method is limited by the adequacy of the sample size and the rationality of sample positioning, thereby necessitating further refinement. Additionally, the mass coefficient may not accurately reflect the dispersion degree of the hardened matrix. Factors such as vibration molding can also impact fiber dispersion, emphasizing the importance of proper sampling after the vibration molding process (Yang, 2002).
Considering the direct impact of fiber dispersion on the properties of the matrix, it becomes imperative to study the dispersion state of carbon fiber during the hardened matrix stage. Furthermore, the research findings can directly guide the improvement of preparation processes for CFCC and RCFCC, facilitating a higher degree of fiber dispersion.
During the hardened matrix stage, the dispersion of carbon fiber in cement-based materials can also be evaluated using image analysis methods. Common methods for acquiring images include X-CT scanning and fluorescence imaging (Lee et al., 2009; Liu et al., 2013). While fluorescence imaging is frequently employed for synthetic fiber, its application to carbon fiber is relatively limited. Therefore, the following discussion primarily focuses on the use of X-CT image analysis method to investigate the dispersion of carbon fiber in cement-based materials (Cao et al., 2018).
Wang et al. (2014) utilized X-CT technology to capture and convert grayscale images of CFCC cross-sections. The grayscale values were used to distinguish the cement paste matrix, uniformly dispersed CFs, and carbon fiber bundles. To evaluate fiber dispersion, they introduced the fiber dispersion coefficient Deffective, which represents the average ratio of uniformly dispersed area to total area, and the dispersion variation coefficient φn(x). These metrics were used to evaluate the degree of fiber dispersion in each cross-section. The study revealed that the dispersion coefficient exhibited unpredictable variations across different cross-sections, fluctuating between 84% and 94%. However, the variation coefficient proved to be a reliable indicator of fiber dispersion uniformity, even when the dispersion coefficient was similar. A smaller variation coefficient corresponded to a more evenly carbon fiber dispersion.
Gao et al. (2017) conducted a comprehensive investigation on the dispersion of carbon fiber in cement-based materials using X-CT technology and image analysis method. The distribution patterns of carbon fiber under two distinct preparation processes are visually depicted in Figure 6. The presented image illustrates distinct regions: the black areas signify carbon fiber bundles, the purple areas represent uniformly dispersed fiber, and the gray areas denote fiber-free regions. It can be observed that the proportion of purple areas in the pre-mixing method is significantly higher than that in the after-mixing method, and gray areas without fiber are also smaller. This finding highlights the beneficial role of the water film formed during pre-wetting, reducing fiber-to-fiber friction and promoting effective dispersion of carbon fiber in the matrix.
FIGURE 6. The carbon fiber distribution characterization with different mixing methods (Gao et al., 2017).
Image analysis method offers a visually comprehensive method for evaluating the dispersion of fiber in cement-based materials. It provides valuable insights into the degree of fiber bundling and agglomeration, which can be further corroborated by subsequent investigations on mechanical properties, electrical properties, and related factors. However, the accuracy of image analysis is contingent upon the number of cross-sectional slices examined. Increasing the number of slices enhances the precision of evaluating fiber dispersion within the matrix.
Mechanical properties serve as fundamental indicators of fiber cement-based composites, and the fiber dispersion directly impacts the mechanical properties of the matrix. Currently, the dispersion of carbon fiber in cement-based materials predominantly focuses on strength, toughness, and impact resistance.
Surface treatments have demonstrated the ability to enhance the dispersion of carbon fiber in water, consequently leading to a certain degree of matrix strengthening, as elaborated in Section 4.1.2. Catala et al. (2011) conducted a comparative analysis of five oxidation methods on the influence of carbon fiber on matrix strength. Their findings revealed that fiber treated at 410°C exhibits the most pronounced strength enhancement, effectively anchoring it to the matrix. Similarly, Lavagna et al. (2018) investigated the effects of various solution treatments on the performance of carbon fiber in cement-based materials. They observed a significant improvement in both the strength and toughness of the cementitious matrix when utilizing fiber oxidized with piranha solution. Furthermore, Beroll et al. (2020) reported a remarkable increase in flexural strength of cement-based materials by incorporating carbon fiber treated at high temperatures, resulting in a strength enhancement of approximately 200%.
However, there are inherent limitations in using strength alone as a measure of fiber dispersion, particularly when achieved through the use of dispersants. On one hand, certain dispersant like MC and CMC can reduce the surface energy of the fresh mixture and introduce excessive air bubbles, thereby decreasing the strength of the matrix (Chuang et al., 2018; Lavagna et al., 2018; Zhu et al., 2021). On the other hand, cement-based materials themselves inherently possess matrix defects, and even with uniformly dispersed fiber incorporated, there can be additional interface weakening. Therefore, the final strength of the composites is influenced by both interface weakening and fiber reinforcement, and cannot be solely attributed to the degree of fiber dispersion (Zhu et al., 2021).
Due to its ability to account for the influence of matrix defects on strength, toughness is considered more suitable for evaluating fiber dispersion in cement-based materials. Lavagna et al. (2018) observed that carbon fiber treated with piranha solution exhibited the highest increase in fracture toughness of the matrix. Similarly, Zhu et al. (2021) employed flexural toughness analysis and found that the use of dispersant resulted in more complete load-deflection curves, with CMC-treated carbon fiber showing the most notable enhancement in toughness. Thomoglou et al. (2022) also investigated the relationship between fiber dispersion and toughness, revealing that well-dispersed fiber contributed to increased energy absorption capacity prior to composite failure. Moreover, researchers such as Li et al. (2019b) have explored the impact resistance of the matrix as an additional indicator of fiber dispersion, showing that carbon fiber treated at high temperatures significantly improved the impact resistance of the composite, attributed to excellent surface treatment imparting better fiber dispersion.
However, since mechanical properties are also influenced by the cementitious matrix, the impact of fiber dispersion on mechanical properties is not solely determined. Therefore, a comprehensive evaluation incorporating other methods is necessary.
Electrical properties are unique characteristics of CFCC and play a crucial role in assessing the viability of smart concrete applications. Currently, researchers primarily rely on evaluating carbon fiber dispersion within the hardened matrix through electrical conductivity and piezoresistive properties. It is important to note that electrical properties, unlike mechanical properties, are predominantly influenced by the fiber itself, with fiber dispersion directly impacting electrical properties.
The incorporation of carbon fiber, including recycled carbon fiber, forms a conductive network within the matrix, and the efficiency of network formation is contingent upon fiber dispersion. In cases where fiber is unevenly dispersed or agglomerated, the formation of an effective conductive network within the matrix is hindered. Consequently, not only does this impede the development of electrical conductivity, but it also gives rise to additional weak regions, resulting in an increase in the electrical resistivity. Conversely, uniformly dispersed fiber facilitates the formation of a well-connected conductive network, leading to a significant reduction in electrical resistivity. Fu et al. (1996) assessed the dispersion of carbon fiber under different oxidation methods by measuring contact resistivity and observed that ozone-treated carbon fiber exhibited notably reduced electrical resistivity, achieving optimal strength when combined with the cementitious matrix. Yang, (2002) suggested that resistivity is a reliable indicator to assess the impact of preparation processes on fiber dispersion, and the coefficient of variation of resistivity serves as a measure of fiber dispersion. Similarly, Zhu et al. (2021) investigated the impact of the types and dosage of dispersants on fiber dispersion using resistivity measurements. The experimental findings are depicted in Figure 7. It can be observed that there is an optimal value of dispersant concentration for reducing resistivity. Notably, the resistivity decrease was most pronounced with CMC treatment compared to other dispersants, indicating its superior effectiveness in achieving the best dispersion of fiber.
FIGURE 7. Relationship between the resistivity and dispersant content and type (A) varying with dispersant dosage; (B) varying with dispersant type (Zhu et al., 2021).
Due to the utilization of low-voltage direct current in most conductivity tests, polarization effects occur during the measurements. Therefore, in order to effectively evaluate the dispersion degree of carbon fiber in cement-based materials, it is beneficial to assess the impedance of the matrix through alternating current measurements. Allam et al. (2022b) have successfully demonstrated the efficacy of alternating current impedance in assessing fiber dispersion within the matrix. Faneca et al. (2018) investigated the impact of different preparation processes on fiber dispersion using alternating current impedance and observed a significant and stable decrease in impedance beyond a threshold testing frequency. Moreover, they noted that impedance at this specific frequency exhibited high sensitivity to fiber dispersion levels.
However, relying solely on conductivity measurements to assess the dispersion of carbon fiber in the hardened matrix has also certain inherent limitations. Firstly, the conductivity tends to increase with the age of the material, and the conductivity of the matrix is influenced by factors such as moisture content and porosity (Zhao et al., 2019; Zhou et al., 2020). Secondly, in cases where the fiber content is high, the conductivity may not accurately reflect the presence of fiber agglomerates. This could be attributed to the fiber content surpassing the percolation threshold, resulting in the matrix resistivity reaching a saturation point (Han et al., 2016; Zhu et al., 2021; Dinesh et al., 2023). Therefore, relying solely on conductivity measurements is insufficient to serve as the exclusive criterion for evaluating the dispersion degree of carbon fiber or recycled carbon fiber in the hardened matrix.
Certainly, some researchers have also sought to evaluate the dispersion of carbon fiber in the matrix by examining other electrical properties such as piezoresistivity and electromagnetic shielding. Thomoglou et al. (2022) conducted a study on the influence of different dispersion methods on the piezoresistive behavior of carbon fiber in the matrix. They emphasized the importance of employing suitable dispersants and adopting effective preparation processes to enhance the dispersion state of carbon fiber, thereby improving the piezoresistive response of the composite. Zornoza et al. (2010) investigated the use of magnetic fly ash and MC as dispersants for carbon fiber, and their findings revealed that uniformly dispersed carbon fiber can synergistically interact with magnetic fly ash, resulting in an enhanced electromagnetic shielding capability of the matrix.
In summary, electrical properties provide a quantitative and perceptible means of evaluating the dispersion degree of carbon fiber in the hardened matrix. However, it is important to note that at high fiber content, these properties may not fully capture the variation of dispersion. Therefore, it is advisable to combine them with mechanical properties such as toughness or impact resistance for a comprehensive evaluation.
Just like in the suspension phase, the dispersion of fiber in the hardened matrix can also be analyzed through morphological observations. Chuang et al. (2018) employed SEM to investigate the fiber dispersion in CFCC samples prepared using different preparation processes, revealing a reduced occurrence of fiber agglomeration in the samples fabricated using the three-step method. Li et al. (2019b) utilized optical microscopy to examine the damage to specimens after impact tests and observed that thermally oxidized carbon fiber exhibited superior dispersion within the concrete matrix compared to untreated fiber, resulting in enhanced resistance to tensile stresses during impact loading. Zhu et al. (2021) conducted SEM analysis of CFCC samples with varying fiber contents and found that excessive fiber content led to fiber agglomeration, thereby introducing additional defects and diminishing the performance of the composite. Furthermore, Mastali and Dalvand (2016) assessed the dispersion of chopped CFRP fiber in cement-based materials using microscopic images.
Hence, morphological observations provide a vivid and direct understanding of the distribution of fiber in the hardened matrix. However, these observations are constrained by the limited number and locations of the observed samples and cannot be directly equated with macroscopic dispersion. Therefore, it is essential to complement these findings with other analytical methods (Yang, 2002).
The above-mentioned methods serve as common approaches for evaluating the dispersion of carbon fiber in three distinct stages. Figure 8 summarizes these dispersion methods based on stability, uniformity, and morphology, providing a comprehensive elucidation. It is apparent that the evaluation of carbon fiber dispersion cannot be simplified to a single method; instead, it requires a holistic evaluation that integrates different dimensions and stages. Moreover, when evaluating the dispersion of recycled carbon fiber in cement-based materials, these methods can be utilized as a valuable reference to better understand the impact of various factors on the dispersion of recycled carbon fiber.
The uniform fiber dispersion is a fundamental requirement for achieving superior performance in cement-based composites and plays a critical role in enabling the expression of their intelligent properties. Therefore, it is essential to review the dispersion methods of carbon fiber. Based on current research findings, it can be concluded that the methods for dispersing carbon fiber, including recycled carbon fiber, can be broadly categorized into two groups: fiber pretreatment and composite preparation process.
Due to the predominantly inert and hydrophobic nature of carbon fiber surfaces, often accompanied by a resin coating, the challenges of achieving uniform dispersion in cement-based materials are undoubtedly heightened (Lavagna et al., 2018; Li et al., 2019b). However, fiber pretreatment plays a crucial role in mitigating uneven dispersion. This can be achieved through the addition of dispersants, which enhance the dispersion stability and uniformity of fiber in water, thereby facilitating dispersion within cement-based materials. Alternatively, surface treatments can be employed to improve the fiber’s hydrophilicity and wetting properties, thereby enhancing its dispersion within the matrix. Therefore, fiber pretreatment encompasses two key approaches: dispersant treatment and surface treatment.
The dispersant treatment is a cost-effective and easily manageable approach, commonly coupled with ultrasonic vibration to ensure effective fiber dispersion. Table 6 outlines the procedures for treating carbon fiber and recycled carbon fiber using dispersants.
Upon reviewing Table 6, it becomes apparent that dispersant treatment requires elevated temperatures and sufficient dispersing time. On one hand, higher temperatures are advantageous as they promote the dissolution of dispersants. For instance, Sun et al. (2015) initially dissolved the dispersant in hot water at 80°C to enhance its solubility before subsequently cooling it to 25°C for effective fiber dispersion through agitation. On the other hand, temperature affects the viscosity of the fiber suspension. As temperature increases, the viscosity decreases, which has a significant impact on the dispersion effectiveness of carbon fiber. Excessive viscosity hampers the proper fiber dispersion (Chuang et al., 2018). Additionally, an adequate duration of dispersing time is essential, especially when employing ultrasonic dispersion, which typically requires approximately 20 min. Prolonged exposure to ultrasonic energy facilitates the dispersion of carbon fiber in water. However, it is crucial to note that there exists a saturation point for ultrasonic dispersion, and excessively long dispersing times are not recommended (He et al., 2006). Hence, maintaining a dispersing temperature of around 40°C and employing an ultrasonic dispersing time of approximately 20 min are considered suitable methods for dispersant treatment.
Surface treatment of carbon fiber is an additional pre-treatment method aimed at enhancing fiber dispersion. This can be achieved through two approaches: surface oxidation and surface coating. Surface oxidation involves subjecting the fiber to either strong oxidizing agents or high temperatures in a controlled manner, which introduces active functional groups onto the fiber surface and improves its hydrophilicity. Liquid-phase oxidation and gas-phase oxidation are commonly used methods for surface oxidation. Conversely, surface coating involves applying a cured layer onto the fiber surface, often accompanied by an oxidation reaction. This not only promotes fiber dispersion but also strengthens the adhesion between the fiber and the cementitious matrix, ultimately enhancing the properties of the composite. The specific procedures for different surface treatment methods are outlined in Table 7.
From Table 7, it can be observed that for liquid-phase oxidation, CH3COOH, HNO3, NaOH, and H2O2 solutions are commonly employed. The reaction is typically conducted at room temperature and extends for a duration exceeding 24 h. In contrast, gas-phase oxidation requires a significantly shorter treatment time but demands a higher reaction temperature of approximately 500°C, resulting in a more vigorous oxidation process.
According to the current research findings, it is evident that gas-phase oxidation exhibits superior performance compared to liquid-phase oxidation in terms of treatment effectiveness. Fu et al. (1996) conducted a study on the influence of liquid-phase and gas-phase oxidation treatments on carbon fiber and its impact on the properties of cement-based materials. Their results revealed that O3 treatment yielded the most favorable outcomes, as it enriched the fiber surface with a greater number of oxygen-containing functional groups, thereby enhancing wettability, dispersion, bond strength, and reducing contact resistance within cement-based materials. Catala et al. (2011) investigated the variation in the quantity of oxygen-containing groups on carbon fiber under different oxidation methods. They discovered that fiber treated at approximately 410°C exhibited the highest concentration of oxygen-containing groups, surpassing those treated with H2O2 and HNO3. Additionally, they emphasized that carbon fiber enriched with abundant oxygen-containing groups significantly improved interfacial interactions with cementitious matrix, thereby enhancing anchorage and contributing to the overall strength enhancement of composite. Li et al. (2019b) compared the residual silane content on carbon fiber surfaces after treatment with acid/base solutions and high-temperature processing. Their findings indicated that carbon fiber subjected to high-temperature treatment exhibited minimal residual silane, followed by acid solution, pure water, and alkaline solution. Furthermore, high-temperature oxidation of carbon fiber not only reduced residual silane but also enhanced bonding effectiveness with cementitious matrix, resulting in remarkable improvements in compressive strength and impact resistance of concrete. These observed outcomes can be attributed to the presence of residual strong oxidizing agents on the fiber surface following liquid-phase oxidation, which may have a detrimental effect on the hydration process and performance development of cement-based materials. Therefore, it is crucial to consider the presence of residual strong oxidizing agents on the fiber surface. However, gas-phase oxidation requires precise control of reaction conditions, including temperature and reaction time. Inappropriate procedures can lead to performance degradation and even decomposition of carbon fiber (Beroll et al., 2020).
Surface coating represents a meaningful approach to significantly enhance the dispersion of carbon fiber. Jia et al. (2021) investigated the influence of nickel-coated carbon fiber on the conductivity and stability of cement-based materials. They found that increasing the thickness of the nickel coating improved the wettability and dispersion of carbon fiber, effectively enhancing and stabilizing the electrical conductivity of the composite. Furthermore, Ji et al. (2021) explored the utilization of MnO2-modified carbon fiber and observed remarkable results. The modified fiber exhibited a rougher surface profile, with attached MnO2 particles that effectively enhanced the electric-thermal effect within the matrix. Notably, the modified fiber displayed a seebeck coefficient of the composite that was an impressive 100 times greater than that of the unmodified fiber. Consequently, employing surface coating techniques offers a highly effective means of enhancing carbon fiber dispersion. Moreover, the presence of cured substances on the fiber surface not only improves interfacial properties but also enhances the electrical properties of the composite, thus facilitating the advancement and practical application of smart concrete.
In recent years, surface treatment has gained significant attention as a means to enhance the dispersion of recycled carbon fiber, thereby improving the performance of RCFCC. Wang et al. (2019) studied on the modification of recycled carbon fiber using alkaline solutions. Their findings revealed that saturated pore solution (SPS), triisopropanolamine (TIPA), and montmorillonite nanoclay emulsion (mNCE) effectively removed the resin from the fiber surface. However, it was observed that excessive treatment time led to the presence of alkali residues, which adversely affected the mechanical properties of the matrix. A comprehensive analysis suggested that employing SPS treatment for a duration of 0.5 h, followed by TIPA or mNCE modification of the recycled carbon fiber, yielded notable improvements in the mechanical properties of the matrix. Li et al. (2021) investigated the application of microwave-assisted pyrolysis for treating recycled carbon fiber and made significant discoveries. The high temperatures employed in the process efficiently decomposed the resin and coupling agents present on the surface of the recycled carbon fiber, resulting in enhanced bond strength with the matrix. Furthermore, the RCFCC exhibited superior strength and impact resistance compared to non-pyrolysis carbon fiber.
Therefore, the fiber pretreatment plays a pivotal role in achieving effective dispersion. While dispersant treatment offers a relatively lower cost and is more convenient for engineering applications, surface treatment provides the advantage of enriching the variety of functional groups. This optimization of the interface effects enhances the interfacial bonding strength with the cementitious matrix, thereby effectively improving multiple properties of the composite. Additionally, it is worth noting that the current research on pretreatment of recycled carbon fiber predominantly concentrates on surface treatment, with limited studies conducted on dispersant treatment.
In recent years, the improvement of fiber dispersion in CFCC and RCFCC has been achieved through the utilization of the preparation process, particularly in terms of the mixing process and forming process.
The mixing process of fiber cement-based composites can be categorized into three main methods: pre-mixing method, co-mixing method, and after-mixing method, based on the sequence of fiber or cement contact with the mixing water. Generally, carbon fiber treated with dispersants is commonly prepared using the pre-mixing method. In this approach, fiber, water, dispersant, and defoamer are combined to create a uniform fiber dispersion suspension, which is subsequently mixed with the cementitious materials and aggregates. Building upon the pre-mixing method, Chuang et al. (2018) developed a six-step mixing process that incorporates wet-mixing, dry-wet-mixing, and wet-mixing steps. Their study highlighted the superiority of the six-step process over the conventional three-step process, yielding more uniform fiber dispersion, particularly for high fiber content compositions. In a separate study, Sun et al. (2015) filtered dispersant-treated carbon fiber and obtained carbon fiber mats through subsequent drying. For further utilization, the six-step method was employed to prepare CFCC by combining a portion of cement and water with the carbon fiber mat. The presence of dissolved dispersants and cement facilitated enhanced fiber dispersion. This method proposed the bulk production of carbon fiber mats, simplifying the CFCC preparation process. Presently, the pre-mixing method for CFCC often follows with the six-step mixing process (Guo et al., 2021; Zhu et al., 2021).
Certainly, the co-mixing method and after-mixing method are also commonly employed in the mixing process. In the co-mixing method, fiber is pre-mixed with cementitious materials or aggregates, followed by the addition of mixing water. As discussed in Section 2.3, the incorporation of mineral admixtures, such as silica fume, has been found to promote fiber dispersion. Therefore, the co-mixing method is often combined with the use of mineral admixtures. Akbar and Liew (2020b), Akbar et al. (2021) noted that no additional dispersant treatment is required for pyrolysis carbon fiber. The fiber can be pre-mixed with cement and ultrafine silica fume for 2 min to facilitate effective fiber dispersion. In another study, Ouyang et al. (2022) first mixed CNF with fine quartz sand, followed by the sequential addition of cement, carbon fiber, and silica fume, with 1 min of stirring, ensuring excellent fiber dispersion.
The after-mixing method, conversely, entails the direct incorporation of carbon fiber into the fresh mixtures, with careful attention given to a gradual addition of the fiber to prevent clustering (Mastali et al., 2017). Clearly, from the perspective of enhancing fiber dispersion, the pre-mixing method yields the most favorable results, followed by the co-mixing method, and finally the after-mixing method. Gao et al. (2017) utilized X-CT and image analysis method to evaluate the influence of the pre-mixing and after-mixing methods on carbon fiber dispersion in cement-based materials. They discovered that the bundling area of fiber in CFCC prepared via the after-mixing method exceeded that of the pre-mixing method, thus suggesting a preference for the pre-mixing method in CFCC production. Similarly, Thomoglou et al. (2022) compared the effects of the pre-mixing and after-mixing methods on CFCC performance and observed a pronounced enhancement with the pre-mixing method. However, the after-mixing method offers lower economic costs and avoids the introduction of additional materials that may affect matrix development, thus demonstrating its potential application value in CFCC fabrication. Therefore, the after-mixing method is commonly employed for fiber with good dispersion, such as surface-treated carbon fiber, pyrolysis carbon fiber, and chopped CFRP fiber derived from partial recycled carbon fiber (Akbar and Liew, 2020a; Xiong et al., 2020; Li et al., 2021; Zaid et al., 2021). The choice of mixing method has a direct and discernible impact on fiber dispersion. However, when selecting an appropriate mixing process, consideration should also be given to the fiber type and cost-effectiveness.
The molding process also significantly influences the degree of fiber dispersion and the density of composites. Chuang et al. (2018) conducted a comparison of the cross-sectional morphology of CFCC specimens subjected to one-time and three-time vibration. Their findings revealed that thoroughly compacted specimens exhibited a uniform distribution of carbon fiber with tightly interconnected components. Furthermore, they highlighted the influence of the molding process on the electrical conductivity of CFCC. It was observed that CFCC produced using the vibrating pressing method demonstrated lower electrical resistivity compared to CFCC prepared using the vibrating method, indicating a more effective interlocking of fiber (Wang et al., 2017).
Therefore, employing appropriate and rational dispersion methods is crucial in not only effectively improving the dispersion of carbon fiber in cement-based materials but also enhancing the overall properties of composites, thereby expanding their range of applications. However, since research on the dispersion of recycled carbon fiber in cement-based materials is still in its initial exploratory stage, it is imperative to integrate the dispersion evaluation methods mentioned earlier and progressively investigate suitable dispersion methods for different types of recycled carbon fiber in cementitious matrix.
The degree of fiber dispersion is a critical factor that determines the effectiveness of carbon fiber and recycled carbon fiber in enhancing the properties of cement-based materials. It serves as a fundamental aspect in the field of fiber cement-based composites. This comprehensive review examines in detail the dispersion of carbon fiber and recycled carbon fiber, covering their various types and distinctions, evaluation methods for fiber dispersion, as well as methods employed to achieve optimal fiber dispersion. Based on the extensive literature review, the following conclusions can be drawn:
(1) Recycled carbon fiber, as a type of regenerated fiber, has garnered significant attention from both academia and the industry due to its exceptional mechanical properties and corrosion resistance, making it an ideal reinforcing material for cement concrete. Depending on the source and recycling method, recycled carbon fiber used in cement-based materials can be categorized as finished waste carbon fiber, semi-finished waste carbon fiber, pyrolysis carbon fiber, chopped CFRP fiber and chemically recycled carbon fiber.
(2) Different types of recycled carbon fiber exhibit noticeable variations in mechanical properties and surface characteristics, rendering the dispersion of recycled carbon fiber in cement-based materials more complex compared to carbon fiber. This necessitates further systematic research and comprehensive analysis.
(3) The fiber dispersion is mainly assessed in terms of stability, uniformity, and morphology, categorized into the fiber suspension stage, fresh mixture stage, and hardened matrix stage. However, due to the limitations of individual methods, a comprehensive evaluation of the dispersion level of carbon fiber or recycled carbon fiber in cement-based materials necessitates a holistic approach, combining different dimensions and methods at various stages.
(4) Achieving uniform fiber dispersion involves two key aspects: fiber pretreatment and preparation processes. The utilization of dispersants and pre-mixing method notably enhances the dispersion of carbon fiber in cement-based materials, particularly with optimal results observed at a dispersion temperature of 40°C and an ultrasonic vibration time of 20 min.
(5) Utilizing carbon fiber oxidized at around 500°C is found to significantly enhance fiber dispersion, surpassing other surface oxidation methods. Additionally, this process benefits the interface between the fiber and the matrix. Moreover, surface coating methods not only promote fiber dispersion but also contribute to the development of electrical properties.
(6) The pre-mixing method demonstrates superior effectiveness in improving carbon fiber dispersion. However, considering the unique properties and cost limitations of recycled carbon fiber, co-mixing or after-mixing methods, combined with the use of mineral admixtures like silica fume, can also achieve high levels of fiber dispersion.
Finally, as the principles of green and sustainable development continues to deepen, the research and application of recycled carbon fiber in cement-based materials will become increasingly widespread. However, the current lack of clear definitions for different types of recycled carbon fiber, coupled with the absence of relevant standards, and inadequate attention to fiber dispersion, hinder the further circular utilization of carbon fiber waste in the construction and building materials industry. Therefore, future research endeavors and focal points are likely to converge on the following key aspects:
(1) Based on the evaluation and dispersion methods for carbon fiber, it is imperative to optimize the dispersion methods of recycled carbon fiber in cement-based materials, aiming to discover more efficient, stable, and cost-effective dispersion methods. For instance, exploring the compatibility of various types of dispersants during the pre-treatment of recycled carbon fiber or considering the incorporation of novel dispersants or improvements in existing preparation processes.
(2) Thoroughly investigating the relationship between fiber dispersion performance and the diverse properties of cement-based composites is crucial to elucidate the mechanisms through which fiber dispersion impacts the overall performance of the composite.
(3) Establishing relevant standards for the application of recycled carbon fiber in cement concrete will further advance the utilization of recycled carbon fiber in cement-based materials and facilitate the resourceful utilization of carbon fiber waste.
HG: Writing—original draft, Conceptualization, Data curation, and Funding acquisition. YX: Writing—review and editing, Investigation, Methodology, and Validation. All authors contributed to the article and approved the submitted version.
Thanks for the financial support provided by Postgraduate Research and Practice Innovation Program of Jiangsu Province (SJCX22_1750).
The authors express their heartfelt appreciation to the authors whose works have been referenced in this paper. And they also gratefully acknowledge the support provided by above funding.
The authors declare that the research was conducted in the absence of any commercial or financial relationships that could be construed as a potential conflict of interest.
All claims expressed in this article are solely those of the authors and do not necessarily represent those of their affiliated organizations, or those of the publisher, the editors and the reviewers. Any product that may be evaluated in this article, or claim that may be made by its manufacturer, is not guaranteed or endorsed by the publisher.
Abreu, F. D., Ribeiro, C. C., Pinto, J. D. D., Nsumbu, T. M., and Buono, V. T. L. (2020). Influence of adding discontinuous and dispersed carbon fiber waste on concrete performance. J. Clean. Prod. 273, 122920. doi:10.1016/j.jclepro.2020.122920
Akbar, A., Kodur, V. K. R., and Liew, K. M. (2021). Microstructural changes and mechanical performance of cement composites reinforced with recycled carbon fibers. Cem. Concr. Compos. 121, 104069. doi:10.1016/j.cemconcomp.2021.104069
Akbar, A., and Liew, K. M. (2020a). Assessing recycling potential of carbon fiber reinforced plastic waste in production of eco-efficient cement-based materials. J. Clean. Prod. 274, 123001. doi:10.1016/j.jclepro.2020.123001
Akbar, A., and Liew, K. M. (2020b). Influence of elevated temperature on the microstructure and mechanical performance of cement composites reinforced with recycled carbon fibers. Compos. Part B Eng. 198, 108245. doi:10.1016/j.compositesb.2020.108245
Allam, H., Duplan, F., Amziane, S., and Burtschell, Y. (2022a). About the self-sensing behavior of smart concrete and its interaction with the carbon fiber percolation status, sand connectivity status and grain size distribution. Constr. Build. Mater. 324, 126609. doi:10.1016/j.conbuildmat.2022.126609
Allam, H., Duplan, F., Amziane, S., and Burtschell, Y. (2022b). Assessment of manufacturing process efficiency in the dispersion of carbon fibers in smart concrete by measuring AC impedance. Cem. Concr. Compos. 127, 104394. doi:10.1016/j.cemconcomp.2021.104394
Alsharef, J. M. A., Taha, M. R., Al-Mansob, R. A., and Govindasamy, P. (2019). Evaluation of the dispersion stability of nanocarbons using zeta potential in distilled water. Nano Hybrids Compos. 26, 8–19. doi:10.4028/www.scientific.net/nhc.26.8
Atiyeh, M., and Aydin, E. (2020). Carbon-fiber enriched cement-based composites for better sustainability. Materials 13, 1899. doi:10.3390/ma13081899
Belli, A., Mobili, A., Bellezze, T., Tittarelli, F., and Cachim, P. (2018). Evaluating the self-sensing ability of cement mortars manufactured with graphene nanoplatelets, virgin or recycled carbon fibers through piezoresistivity tests. Sustainability 10, 4013. doi:10.3390/su10114013
Belli, A., Mobili, A., Bellezze, T., and Tittarelli, F. (2020). Commercial and recycled carbon/steel fibers for fiber-reinforced cement mortars with high electrical conductivity. Cem. Concr. Compos. 109, 103569. doi:10.1016/j.cemconcomp.2020.103569
Beroll, P., Schmalzl, S., and Volkmer, D. (2020). Influence of surface-modification, length and volume fraction of carbon short fibers on the mechanical properties of calcium aluminate cement systems. Mater. Today Commun. 25, 101704. doi:10.1016/j.mtcomm.2020.101704
Bledzki, A. K., Seidlitz, H., Goracy, K., Urbaniak, M., and Roesch, J. J. (2021). Recycling of carbon fiber reinforced composite polymers-review-Part 1: volume of production, recycling technologies, legislative aspects. Polymers 13, 300. doi:10.3390/polym13020300
Cao, M., Mao, Y., Khan, M., Si, W., and Shen, S. (2018). Different testing methods for assessing the synthetic fiber distribution in cement-based composites. Constr. Build. Mater. 184, 128–142. doi:10.1016/j.conbuildmat.2018.06.207
Catala, G., Ramos-Fernandez, E. V., Zornoza, E., Andion, L. G., and Garces, P. (2011). Influence of the oxidation process of carbon material on the mechanical properties of cement mortars. J. Mater. Civ. Eng. 23, 321–329. doi:10.1061/(asce)mt.1943-5533.0000175
Chen, Q., Chen, Z.-F., Li, C.-D., Wu, W.-P., Boafo, F. E., and Li, B.-B. (2014). Effect of dispersants on dispersion of glassfiber suspensions. Asian J. Chem. 26, 5100–5104. doi:10.14233/ajchem.2014.16339
Chen, Z.-S., Zhou, X., Wang, X., and Guo, P. (2018). Mechanical behavior of multilayer GO carbon-fiber cement composites. Constr. Build. Mater. 159, 205–212. doi:10.1016/j.conbuildmat.2017.10.094
Chuang, W., Lei, P., Bing-Liang, L., Ni, G., Li-Ping, Z., and Ke-Zhi, L. (2018). Influences of molding processes and different dispersants on the dispersion of chopped carbon fibers in cement matrix. Heliyon 4, e00868. doi:10.1016/j.heliyon.2018.e00868
Chung, D. D. L. (2005). Dispersion of short fibers in cement. J. Mater. Civ. Eng. 17, 379–383. doi:10.1061/(asce)0899-1561(2005)17:4(379)
Cui, Y., Zheng, G., Wu, B., Sun, Y., and Wu, B. Y. (2015). The influence of fatty alcohol ether phosphate salt on carbon fiber's dispersion property. J. Appl. Polym. Sci. 132. doi:10.1002/app.41470
Das, D., Butola, B. S., and Renuka, S. (2012). An investigation into fiber dispersion behavior in water with reference to wet-lay nonwoven technology. J. Dispersion Sci. Technol. 33, 1225–1232. doi:10.1080/01932691.2011.590437
Demirel, B., and Yazicioglu, S. (2008). Thermoelectric behavior of carbon fiber reinforced lightweight concrete with mineral admixtures. New Carbon Mater. 23, 21–24. doi:10.1016/s1872-5805(08)60009-8
Dilsiz, N., and Wightman, J. P. (1999). Surface analysis of unsized and sized carbon fibers. Carbon 37, 1105–1114. doi:10.1016/s0008-6223(98)00300-5
Dinesh, A., Jayashree, J., Abhishek, S., and Prakash, A. (2023). Multifunctional properties of carbon fiber integrated cement composite – a review and insights. Mater. Today Proc. 2023. doi:10.1016/j.matpr.2023.05.559
Donnini, J., Bellezze, T., and Corinaldesi, V. (2018). Mechanical, electrical and self-sensing properties of cementitious mortars containing short carbon fibers. J. Build. Eng. 20, 8–14. doi:10.1016/j.jobe.2018.06.011
Du, Y., Lu, S., Xu, J., Xia, W., Wang, T., and Wang, Z. (2022). Experimental study of impact mechanical and microstructural properties of modified carbon fiber reinforced concrete. Sci. Rep. 12, 12928. doi:10.1038/s41598-022-17092-4
Faneca, G., Segura, I., Torrents, J. M., and Aguado, A. (2018). Development of conductive cementitious materials using recycled carbon fibres. Cem. Concr. Compos. 92, 135–144. doi:10.1016/j.cemconcomp.2018.06.009
Fathi-Khalfbadam, S., Latifi, M., Sheikhzadeh-Najar, S., and Towhidkhah, F. (2011). Analysis and simulation of fiber dispersion in water using a theoretical analogous model. J. Dispersion Sci. Technol. 32, 352–358. doi:10.1080/01932691003659833
Fu, X., Lu, W., Chung, D. J. C., and Research, C. (1996). Improving the bond strength between carbon fiber and cement by fiber surface treatment and polymer addition to cement mix. Cem. Concr. Res. 26, 1007–1012. doi:10.1016/0008-8846(96)00084-1
Gao, J., Wang, Z., Zhang, T., and Zhou, L. (2017). Dispersion of carbon fibers in cement-based composites with different mixing methods. Constr. Build. Mater. 134, 220–227. doi:10.1016/j.conbuildmat.2016.12.047
Garg, M., Das, C. S., and Gupta, R. (2020). Use of silica particles to improve dispersion of -COOH CNTs/carbon fibers to produce HyFRCC. Constr. Build. Mater. 250, 118777. doi:10.1016/j.conbuildmat.2020.118777
Gopalraj, S. K., and Karki, T. (2020). A review on the recycling of waste carbon fibre/glass fibre-reinforced composites: fibre recovery, properties and life-cycle analysis. Sn Appl. Sci. 2, 433. doi:10.1007/s42452-020-2195-4
Guan, X., Qian, X., and Yang, Z. (2017). Comparison of several image analysis methods for fiber dispersion uniformity in water. J. Dispersion Sci. Technol. 38, 19–25. doi:10.1080/01932691.2015.1088455
Guo, Z., Zhuang, C., Li, Z., and Chen, Y. (2021). Mechanical properties of carbon fiber reinforced concrete (CFRC) after exposure to high temperatures. Compos. Struct. 256, 113072. doi:10.1016/j.compstruct.2020.113072
Han, B., Zhang, L., Zhang, C., Wang, Y., Yu, X., and Ou, J. (2016). Reinforcement effect and mechanism of carbon fibers to mechanical and electrically conductive properties of cement-based materials. Constr. Build. Mater. 125, 479–489. doi:10.1016/j.conbuildmat.2016.08.063
Han, J., Wang, D., and Zhang, P. (2020). Effect of nano and micro conductive materials on conductive properties of carbon fiber reinforced concrete. Nanotechnol. Rev. 9, 445–454. doi:10.1515/ntrev-2020-0034
Hao, Y., Shi, C., Bi, Z., Lai, Z., She, A., and Yao, W. (2023). Recent advances in properties and applications of carbon fiber-reinforced smart cement-based composites. Materials 16, 2552. doi:10.3390/ma16072552
Hasan, M. M. B., Nitsche, S., Abdkader, A., and Cherif, C. (2018). Carbon fibre reinforced thermoplastic composites developed from innovative hybrid yarn structures consisting of staple carbon fibres and polyamide 6 fibres. Compos. Sci. Technol. 167, 379–387. doi:10.1016/j.compscitech.2018.08.030
He, P., Gao, Y., Lian, J., Wang, L., Qian, D., Zhao, J., et al. (2006). Surface modification and ultrasonication effect on the mechanical properties of carbon nanofiber/polycarbonate composites. Compos. Part a-Applied Sci. Manuf. 37, 1270–1275. doi:10.1016/j.compositesa.2005.08.008
Ivorra, S., Garces, P., Catala, G., Andion, L. G., and Zornoza, E. (2010). Effect of silica fume particle size on mechanical properties of short carbon fiber reinforced concrete. Mater. Des. 31, 1553–1558. doi:10.1016/j.matdes.2009.09.050
Ji, T., Zhang, S., He, Y., Zhang, X., Zhang, X., and Li, W. (2021). Enhanced thermoelectric property of cement-based materials with the synthesized MnO2/carbon fiber composite. J. Build. Eng. 43, 103190. doi:10.1016/j.jobe.2021.103190
Ji, Y., Zou, Y., Wan, X., and Li, W. (2022). Mechanical investigation on fiber-doped cementitious materials. Polymers 14, 1663. doi:10.3390/polym14091663
Jia, X.-W., Zhang, W.-X., Luo, J.-Y., and Tang, M.-H. (2021). Conductivity and conductive stability of nickel-plated carbon-fiber-reinforced cement composites. Iran. J. Sci. Technology-Transactions Civ. Eng. 45, 1611–1621. doi:10.1007/s40996-020-00532-4
Kerekes, R. J., and Schell, C. J. (1992). Characterization of fiber flocculation regimes by a crowding factor. J. Pulp Pap. Sci. 18 (1), 32–38.
Khaleel, O. R., Wahaibi, M. M. S., Abed, M. J., Dawood, M., and Fayyadh, M. M. (2021). Performance of carbon fibre concrete subjected to fire. Mater. Today Proc. 42, 1160–1165. doi:10.1016/j.matpr.2020.12.530
Khalid, M. Y., Ariff, Z. U., Ahmed, W., and Arshad, H. (2022). Recent trends in recycling and reusing techniques of different plastic polymers and their composite materials. Sustain. Mater. Technol. 31, e00382. doi:10.1016/j.susmat.2021.e00382
Khalid, T., Albasha, L., Qaddoumi, N., and Yehia, S. (2017). Feasibility study of using electrically conductive concrete for electromagnetic shielding applications as a substitute for carbon-laced polyurethane absorbers in anechoic chambers. Ieee Trans. Antennas Propag. 65, 2428–2435. doi:10.1109/tap.2017.2670538
Khalil, Y. F. (2018). Comparative environmental and human health evaluations of thermolysis and solvolysis recycling technologies of carbon fiber reinforced polymer waste. Waste Manag. 76, 767–778. doi:10.1016/j.wasman.2018.03.026
Khaloo, A. R., Dehestani, M., and Rahmatabadi, P. (2008). Mechanical properties of concrete containing a high volume of tire-rubber particles. Waste Manag. 28, 2472–2482. doi:10.1016/j.wasman.2008.01.015
Lavagna, L., Musso, S., Ferro, G., and Pavese, M. (2018). Cement-based composites containing functionalized carbon fibers. Cem. Concr. Compos. 88, 165–171. doi:10.1016/j.cemconcomp.2018.02.007
Lee, B. Y., Kim, J.-K., Kim, J.-S., and Kim, Y. Y. (2009). Quantitative evaluation technique of Polyvinyl Alcohol (PVA) fiber dispersion in engineered cementitious composites. Cem. Concr. Compos. 31, 408–417. doi:10.1016/j.cemconcomp.2009.04.002
Lefeuvre, A., Garnier, S., Jacquemin, L., Pillain, B., and Sonnemann, G. (2019). Anticipating in-use stocks of carbon fibre reinforced polymers and related waste generated by the wind power sector until 2050. Resour. Conservation Recycl. 141, 30–39. doi:10.1016/j.resconrec.2018.10.008
Li, H., Schamel, E., Liebscher, M., Zhang, Y., Fan, Q., Schlachter, H., et al. (2023). Recycled carbon fibers in cement-based composites: influence of epoxide matrix depolymerization degree on interfacial interactions. J. Clean. Prod. 411, 137235. doi:10.1016/j.jclepro.2023.137235
Li, W.-Q., Zhu, J.-H., Chen, P.-Y., Xing, F., Li, D., and Su, M. (2019a). Evaluation of carbon fiber reinforced cementitious matrix as a recyclable strengthening material. J. Clean. Prod. 217, 234–243. doi:10.1016/j.jclepro.2019.01.256
Li, Y.-F., Yang, T.-H., Kuo, C.-Y., and Tsai, Y.-K. (2019b). A study on improving the mechanical performance of carbon-fiber-reinforced cement. Materials 12, 2715. doi:10.3390/ma12172715
Li, Y. F., Li, J. Y., Ramanathan, G. K., Chang, S. M., Shen, M. Y., Tsai, Y. K., et al. (2021). An experimental study on mechanical behaviors of carbon fiber and microwave-assisted pyrolysis recycled carbon fiber-reinforced concrete. Sustainability 13, 6829. doi:10.3390/su13126829
Li, Y., Wei, H., Li, L., Wang, J., Qian, X., He, L., et al. (2018). High-efficiency surfactant prepared from phenolic resin for multi-walled carbon nanotube aqueous suspension. J. Nanoparticle Res. 20, 162. doi:10.1007/s11051-018-4264-9
Liu, J., Li, C., Liu, J., Cui, G., and Yang, Z. (2013). Study on 3D spatial distribution of steel fibers in fiber reinforced cementitious composites through micro-CT technique. Constr. Build. Mater. 48, 656–661. doi:10.1016/j.conbuildmat.2013.07.052
Lu, M., Xiao, H., Liu, M., Li, X., Li, H., and Sun, L. (2018). Improved interfacial strength of SiO2 coated carbon fiber in cement matrix. Cem. Concr. Compos. 91, 21–28. doi:10.1016/j.cemconcomp.2018.04.007
Lu, S., Bai, E., Xu, J., and Chen, J. (2021). Research on electromagnetic properties and microwave deicing performance of carbon fiber modified concrete. Constr. Build. Mater. 286, 122868. doi:10.1016/j.conbuildmat.2021.122868
Ma, P.-C., Siddiqui, N. A., Maeder, E., and Kim, J.-K. (2011). Correlation between electrokinetic potential, dispersibility, surface chemistry and energy of carbon nanotubes. Compos. Sci. Technol. 71, 1644–1651. doi:10.1016/j.compscitech.2011.07.014
Mastali, M., Dalvand, A., and Sattarifard, A. (2017). The impact resistance and mechanical properties of the reinforced self-compacting concrete incorporating recycled CFRP fiber with different lengths and dosages. Compos. Part B Eng. 112, 74–92. doi:10.1016/j.compositesb.2016.12.029
Mastali, M., and Dalvand, A. (2016). The impact resistance and mechanical properties of self-compacting concrete reinforced with recycled CFRP pieces. Compos. Part B-Engineering 92, 360–376. doi:10.1016/j.compositesb.2016.01.046
Mazzocchetti, L., Benelli, T., D'angelo, E., Leonardi, C., Zattini, G., and Giorgini, L. (2018). Validation of carbon fibers recycling by pyro-gasification: the influence of oxidation conditions to obtain clean fibers and promote fiber/matrix adhesion in epoxy composites. Compos. Part A Appl. Sci. Manuf. 112, 504–514. doi:10.1016/j.compositesa.2018.07.007
Mendonca, M. G. S., De Almeida, T. S., Daniel, C. R. A., and Barreto, L. S. (2020). Carbon fiber effect on the physico-mechanical and durability properties of a cement/coir pith composite. Sustain. Mater. Technol. 25, e00187. doi:10.1016/j.susmat.2020.e00187
Meng, F., Mckechnie, J., and Pickering, S. J. (2018). An assessment of financial viability of recycled carbon fibre in automotive applications. Compos. Part a-Applied Sci. Manuf. 109, 207–220. doi:10.1016/j.compositesa.2018.03.011
Mobili, A., Cosoli, G., Bellezze, T., Revel, G. M., and Tittarelli, F. (2022a). Use of gasification char and recycled carbon fibres for sustainable and durable low-resistivity cement-based composites. J. Build. Eng. 50, 104237. doi:10.1016/j.jobe.2022.104237
Mobili, A., Cosoli, G., Giulietti, N., Chiariotti, P., Bellezze, T., Pandarese, G., et al. (2023). Biochar and recycled carbon fibres as additions for low-resistive cement-based composites exposed to accelerated degradation. Constr. Build. Mater. 376, 131051. doi:10.1016/j.conbuildmat.2023.131051
Mobili, A., Cosoli, G., Giulietti, N., Chiariotti, P., Pandarese, G., Bellezze, T., et al. (2022b). Effect of gasification char and recycled carbon fibres on the electrical impedance of concrete exposed to accelerated degradation. Sustainability 14, 1775. doi:10.3390/su14031775
Mobili, A., Giosue, C., Bellezze, T., Revel, G. M., and Tittarelli, F. (2021). Gasification char and used foundry sand as alternative fillers to graphene nanoplatelets for electrically conductive mortars with and without virgin/recycled carbon fibres. Appl. Sciences-Basel 11, 50. doi:10.3390/app11010050
Nguyen, H., Carvelli, V., Fujii, T., and Okubo, K. (2016). Cement mortar reinforced with reclaimed carbon fibres, CFRP waste or prepreg carbon waste. Constr. Build. Mater. 126, 321–331. doi:10.1016/j.conbuildmat.2016.09.044
Nilakantan, G., and Nutt, S. (2018). Reuse and upcycling of thermoset prepreg scrap: case study with out-of-autoclave carbon fiber/epoxy prepreg. J. Compos. Mater. 52, 341–360. doi:10.1177/0021998317707253
Ogi, K., Shinoda, T., and Mizui, M. (2005). Strength in concrete reinforced with recycled CFRP pieces. Compos. Part A Appl. Sci. Manuf. 36, 893–902. doi:10.1016/j.compositesa.2004.12.009
Oliveux, G., Dandy, L. O., and Leeke, G. A. (2015). Current status of recycling of fibre reinforced polymers: review of technologies, reuse and resulting properties. Prog. Mater. Sci. 72, 61–99. doi:10.1016/j.pmatsci.2015.01.004
Ouyang, M., Tian, W., Liu, Y., and Wang, W. (2022). Gradient power modified ohmic heating curing to prepare hybrid carbon fibers/high performance concrete under deep-freeze low temperature. Constr. Build. Mater. 330, 127279. doi:10.1016/j.conbuildmat.2022.127279
Ozyurt, N., Woo, L. Y., Mason, T. O., and Shah, S. R. (2006). Monitoring fiber dispersion in fiber-reinforced cementitious materials: comparison of AC-impedance spectroscopy and image analysis. Aci Mater. J. 103, 340–347.
Pakdel, E., Kashi, S., Varley, R., and Wang, X. G. (2021). Recent progress in recycling carbon fibre reinforced composites and dry carbon fibre wastes. Resour. Conservation Recycl. 166, 105340. doi:10.1016/j.resconrec.2020.105340
Patchen, A., Young, S., and Penumadu, D. (2023). An investigation of mechanical properties of recycled carbon fiber reinforced ultra-high-performance concrete. Materials 16, 314. doi:10.3390/ma16010314
Peng, J., Yue, C., Qiu, G., Guo, M., and Zhang, M. (2016). Dispersion characterization of short slag fiber in aqueous solution. J. Dispersion Sci. Technol. 37, 1097–1103. doi:10.1080/01932691.2015.1082137
Pickering, S. J., Kelly, R. M., Kennerley, J. R., Rudd, C. D., and Fenwick, N. J. (2000). A fluidised-bed process for the recovery of glass fibres from scrap thermoset composites. Compos. Sci. Technol. 60, 509–523. doi:10.1016/s0266-3538(99)00154-2
Pickering, S. J. (2006). Recycling technologies for thermoset composite materials - current status. Compos. Part A Appl. Sci. Manuf. 37, 1206–1215. doi:10.1016/j.compositesa.2005.05.030
Pimenta, S., and Pinho, S. T. (2011). Recycling carbon fibre reinforced polymers for structural applications: technology review and market outlook. Waste Manag. 31, 378–392. doi:10.1016/j.wasman.2010.09.019
Poon, C. S., Kou, S. C., and Lam, L. (2006). Compressive strength, chloride diffusivity and pore structure of high performance metakaolin and silica fume concrete. Constr. Build. Mater. 20, 858–865. doi:10.1016/j.conbuildmat.2005.07.001
Rangelov, M., Nassiri, S., Haselbach, L., and Englund, K. (2016). Using carbon fiber composites for reinforcing pervious concrete. Constr. Build. Mater. 126, 875–885. doi:10.1016/j.conbuildmat.2016.06.035
Reis De Souza, C. S., Opelt, C. V., Candido, G. M., Brejao De Souza, S. D., Botelho, E. C., Fernandes Marlet, J. M., et al. (2019). Reuse of uncured carbon fiber/epoxy resin prepreg scraps: mechanical behavior and environmental response. Acs Sustain. Chem. Eng. 7, 2200–2206. doi:10.1021/acssuschemeng.8b04852
Rossignolo, J. A. (2009). Interfacial interactions in concretes with silica fume and SBR latex. Constr. Build. Mater. 23, 817–821. doi:10.1016/j.conbuildmat.2008.03.005
Sanchez, F., and Ince, C. (2009). Microstructure and macroscopic properties of hybrid carbon nanofiber/silica fume cement composites. Compos. Sci. Technol. 69, 1310–1318. doi:10.1016/j.compscitech.2009.03.006
Shu, X., Graham, R. K., Huang, B., and Burdette, E. G. (2015). Hybrid effects of carbon fibers on mechanical properties of Portland cement mortar. Mater. Des. 65, 1222–1228. doi:10.1016/j.matdes.2014.10.015
Song, P. S., and Hwang, S. (2004). Mechanical properties of high-strength steel fiber-reinforced concrete. Constr. Build. Mater. 18, 669–673. doi:10.1016/j.conbuildmat.2004.04.027
Stynoski, P., Mondal, P., and Marsh, C. (2015). Effects of silica additives on fracture properties of carbon nanotube and carbon fiber reinforced Portland cement mortar. Cem. Concr. Compos. 55, 232–240. doi:10.1016/j.cemconcomp.2014.08.005
Sun, M.-Q., Li, J., Wang, Y.-J., and Zhang, X.-Y. (2015). Preparation of carbon fiber reinforced cement-based composites using self-made carbon fiber mat. Constr. Build. Mater. 79, 283–289. doi:10.1016/j.conbuildmat.2015.01.060
Tang, Z. Q., Li, Z. Q., Qian, J. S., and Wang, K. J. (2005). Experimental study on deicing performance of carbon fiber reinforced conductive concrete. J. Mater. Sci. Technol. 21, 113–117.
Thomoglou, A. K., Falara, M. G., Gkountakou, F. I., Elenas, A., and Chalioris, C. E. (2022). Influence of different surfactants on carbon fiber dispersion and the mechanical performance of smart piezoresistive cementitious composites. Fibers 10, 49. doi:10.3390/fib10060049
Tsangouri, E., Gilabert, F. A., De Belie, N., Van Hemelrijck, D., Zhu, X., and Aggelis, D. G. (2019). Concrete fracture toughness increase by embedding self-healing capsules using an integrated experimental approach. Constr. Build. Mater. 218, 424–433. doi:10.1016/j.conbuildmat.2019.05.138
Wang, B.-M., Zhang, Y., Guo, Z.-Q., Han, Y., and Ma, H.-N. (2012). Dispersion of carbon nanofibers in aqueous solution. Nano 7, 1250052. doi:10.1142/s179329201250052x
Wang, C., Jiao, G.-S., Li, B.-L., Peng, L., Feng, Y., Gao, N., et al. (2017). Dispersion of carbon fibers and conductivity of carbon fiber-reinforced cement-based composites. Ceram. Int. 43, 15122–15132. doi:10.1016/j.ceramint.2017.08.041
Wang, C., Li, K.-Z., Li, H.-J., Jiao, G.-S., Lu, J., and Hou, D.-S. (2008). Effect of carbon fiber dispersion on the mechanical properties of carbon fiber-reinforced cement-based composites. Mater. Sci. Eng. a-Structural Mater. Prop. Microstruct. Process. 487, 52–57. doi:10.1016/j.msea.2007.09.073
Wang, Y., Li, A., Zhang, S., Guo, B., and Niu, D. (2023). A review on new methods of recycling waste carbon fiber and its application in construction and industry. Constr. Build. Mater. 367, 130301. doi:10.1016/j.conbuildmat.2023.130301
Wang, Y., Zhang, S., Luo, D., and Shi, X. (2019). Effect of chemically modified recycled carbon fiber composite on the mechanical properties of cementitious mortar. Compos. Part B Eng. 173, 106853. doi:10.1016/j.compositesb.2019.05.064
Wang, Z., Gao, J., Ai, T., Jiang, W., and Zhao, P. (2014). Quantitative evaluation of carbon fiber dispersion in cement based composites. Constr. Build. Mater. 68, 26–30. doi:10.1016/j.conbuildmat.2014.06.035
Wille, K., El-Tawil, S., and Naaman, A. E. (2014). Properties of strain hardening ultra high performance fiber reinforced concrete (UHP-FRC) under direct tensile loading. Cem. Concr. Compos. 48, 53–66. doi:10.1016/j.cemconcomp.2013.12.015
Xiong, C., Lan, T., Li, Q., Li, H., and Long, W. (2020). Study of mechanical properties of an eco-friendly concrete containing recycled carbon fiber reinforced polymer and recycled aggregate. Materials 13, 4592. doi:10.3390/ma13204592
Xiong, C., Li, Q. S., Lan, T. H., Li, H. D., Long, W. J., and Xing, F. (2021). Sustainable use of recycled carbon fiber reinforced polymer and crumb rubber in concrete: mechanical properties and ecological evaluation. J. Clean. Prod. 279, 123624. doi:10.1016/j.jclepro.2020.123624
Xu, L., Ni, W., Li, W., Liu, X., Yang, H., and Yang, X. (2008). Preparation of natural brucite nanofibers by the dispersion method. J. Univ. Sci. Technol. Beijing 15, 489–494. doi:10.1016/s1005-8850(08)60092-4
Yan, W., Tongxin, Z., Bingbing, G., and Ditao, N. (2022). Conductivity of recycling carbon fiber concrete. Acta Mater. Compos. Sin. 39, 2855–2863.
Yang, Y. X. (2002). Methods study on dispersion of fibers in CFRC. Cem. Concr. Res. 32, 747–750. doi:10.1016/s0008-8846(01)00759-1
Yazdanbakhsh, A., and Grasley, Z. (2014). Utilization of silica fume to stabilize the dispersion of carbon nanofilaments in cement paste. J. Mater. Civ. Eng. 26. doi:10.1061/(asce)mt.1943-5533.0001016
Zaid, O., Hashmi, S. R. Z., Aslam, F., and Alabduljabbar, H. (2021). Experimental study on mechanical performance of recycled fine aggregate concrete reinforced with discarded carbon fibers. Front. Mater. 8. doi:10.3389/fmats.2021.771423
Zegardło, B. (2022). Heat-resistant concretes containing waste carbon fibers from the sailing industry and recycled ceramic aggregates. Case Stud. Constr. Mater. 16, e01084. doi:10.1016/j.cscm.2022.e01084
Zhao, R., Weng, Y., Tuan, C. Y., and Xu, A. (2019). The influence of water/cement ratio and air entrainment on the electric resistivity of ionically conductive mortar. Materials 12, 1125. doi:10.3390/ma12071125
Zhou, Z., Xie, N., Cheng, X., Feng, L., Hou, P., Huang, S., et al. (2020). Electrical properties of low dosage carbon nanofiber/cement composite: percolation behavior and polarization effect. Cem. Concr. Compos. 109, 103539. doi:10.1016/j.cemconcomp.2020.103539
Zhu, H. B., Zhou, H. Y., and Gou, H. X. (2021). Evaluation of carbon fiber dispersion in cement-based materials using mechanical properties, conductivity, mass variation coefficient, and microstructure. Constr. Build. Mater. 266, 120891. doi:10.1016/j.conbuildmat.2020.120891
Keywords: carbon fiber, recycled carbon fiber, fiber dispersion, evaluation method, dispersion method, cement-based composite
Citation: Gao H and Xia Y (2023) Research on the dispersion of carbon fiber and recycled carbon fiber in cement-based materials: a review. Front. Mater. 10:1243392. doi: 10.3389/fmats.2023.1243392
Received: 20 June 2023; Accepted: 08 August 2023;
Published: 17 August 2023.
Edited by:
Muhammad Junaid Munir, RMIT University, AustraliaReviewed by:
Atefeh Soleymani, Shahid Bahonar University of Kerman, IranCopyright © 2023 Gao and Xia. This is an open-access article distributed under the terms of the Creative Commons Attribution License (CC BY). The use, distribution or reproduction in other forums is permitted, provided the original author(s) and the copyright owner(s) are credited and that the original publication in this journal is cited, in accordance with accepted academic practice. No use, distribution or reproduction is permitted which does not comply with these terms.
*Correspondence: Han Gao, Z2hhbi55enVAb3V0bG9vay5jb20=
Disclaimer: All claims expressed in this article are solely those of the authors and do not necessarily represent those of their affiliated organizations, or those of the publisher, the editors and the reviewers. Any product that may be evaluated in this article or claim that may be made by its manufacturer is not guaranteed or endorsed by the publisher.
Research integrity at Frontiers
Learn more about the work of our research integrity team to safeguard the quality of each article we publish.