- 1State Key Laboratory of High-performance Precision Manufacturing, Dalian University of Technology, Dalian, China
- 2Dalian Guangyang Bearing Company Limited, Dalian, China
- 3College of Applied Technology, Dalian Ocean University, Dalian, China
Bearings are widely used in the industry due to their ability to support the movement of rotating bodies. The spacer rings are a key component of double-row roller bearings; therefore, the characteristics and properties of the spacer rings have a significant impact on the bearing functions. However, the lack of the characteristics and performance analysis of the spacer ring limits the improvement of bearing performance. To analyze the characteristics of spacer rings and establish a basis for improving their performance, a new testing method for the characteristics and performance of the spacer ring was presented and corresponding experiments were developed. The test procedure entails the evaluation of basic characteristics, surface properties, and serviceability. Basic characteristics were determined through element testing and cross-section morphological observation; surface properties were assessed through surface morphology and surface roughness detection; and serviceability was identified by cross-section hardness and frictional wear tests. The results show that the proposed test method can comprehensively characterize the performance of the spacer rings. The spacer ring composition mainly contains Fe, Al, P, Si, Ca, and S, which contribute to excellent wear resistance, hardness, strength, and corrosion resistance. The cross-sectional morphology exhibits porous characteristics, which enhance lubricity. In terms of surface property, the surface of the spacer ring is relatively flat, and the surface roughness is generally less than 0.6 μm Sa. The average friction coefficient is 0.85, and the friction and wear properties of the spacer ring are good. This study contributes to establishing the testing and evaluation criteria for the performance of spacer rings in engineering, which helps to improve the performance of bearings.
1 Introduction
Bearings are one of the most important parts of mechanical equipment. The primary function of the bearing is to support the rotating bodies, ensure rotational accuracy, and reduce running friction. As a basic component, bearings are widely used in machine tool spindles (Dong et al., 2017), wind turbines (Jin et al., 2021), automotives (Khaire, 2018), and other sectors (Cheng, 2022). High-precision bearings are usually the core components of the equipment, and the reliability of bearings has a significant impact on life. A related study shows that about 30% of mechanical failures are caused by bearing failures in rotating parts (Guan et al., 2018). With the development of high performance manufacturing concepts (Guo, 2018; Guo, 2022), research on bearing performance will advance rapidly.
Currently, there are many angles of the overall study of bearings. The main purpose is to improve the bearing performance. The material used to manufacture a bearing is the most important factor affecting the bearing performance. Much research has been done on the bearing materials. Yadav and Chawla (2021) summarized different bearing materials and different bearing performance detection methods. Yu et al. (2005) focused on the properties of high carbon chromium type stainless bearing steel, high temperature stainless bearing steel, nitrogen-bearing steel, and other stainless bearing materials, as well as the influence of different smelting processes on the materials. Similarly, Yan et al. (2020) studied the TiNi60 alloy and discussed the melting and processing, mechanical properties, and tribological properties of the bearing materials. Bearing material is just part of the factors that impact bearing performance, but the preparation of the material is the most basic influencing factor, which determines the wear resistance and motion accuracy of the bearing. Additionally, some studies focus on the effect of the material on the bearing properties. Based on a new water-lubricated polymer composites for bearing material, Liu et al. (2020) studied the lubrication performance of water-lubricated bearings in terms of material parameters and structural parameters. It is also important to characterize the bearing performance, the Kolmogorov-Smirnov test based on an autoregressive model was proposed to assess the performance degradation of rolling bearings. The result shows that the proposed test method can obviously detect incipient weak defects and can reflect the performance degradation process well (Cong et al., 2011). However, there is still a lack of evaluation systems for the performance of bearing spacer rings.
Much research has focused on the friction and wear performance of bearings. Sun et al. (2016) analyzed the materials of the bearing, and showed the abnormal wear of the inner rings and shaft was related to the thermal expansion coefficient mismatch of the materials. Guan et al. (2017) studied the wear law of bearings and steel shafts and predicted the wear situation by using the online monitoring data of bearing lubricating oil. The research of Yuan et al. (2018) indicated that low micro-hardness and low shear strength of surface material, rough surface, and poor lubrication are important factors contributing to the wear of spherical plain bearings. The above study provided the possible reasons for frictional wear, and suggested that good lubrication can avoid serious wear phenomenon. Wang et al. (2014) investigated the influences of frictional characteristics of textured surfaces on sliding bearings. This study presented that the designed texture with a relatively small size and density ratio has an obvious effect of lubrication and antifriction improvement compared with other specimens.
In addition to the above research, there are also many other studies on the bearing processing technology and analysis method. Yu and Wu, (2020) established fundamental theoretical methods for improving surface quality through theoretical analysis of abrasive flow polishing of bearings with the high operating performance and research on surface integrity manufacturing technology. Wang et al. (2018) proposed a standardized bearing manufacturing process to conduct three-dimensional modeling, simulation processing, stiffness, and vibration tests of bearings, so as to provide a reference for high-precision bearing manufacturing. Xu et al. (2010) demonstrated the effects of manufacturing tolerance on bearing stiffness and damping and proposed a set of theoretical analysis techniques to predict the stiffness and damping properties of the system.
The above mentioned researches are focused on the bearing as a whole, and there are few studies that focus on the spacer ring. Yi et al. (1983) analyzed the materials of the spacer ring in 1983, however, there was no complete systematic study on the characteristics and performance of the spacer ring. As an important component of bearings, the spacer ring has a significant impact on improving the bearing performance. This paper proposed a new testing method for the characteristics and performance of the spacer ring, the basic characteristics, surface properties, and serviceability of the spacer rings were comprehensively characterized for the first time. This research can help to improve the performance of spacer rings and further help to improve the bearing performance.
2 Testing method
To study the characteristics and performance of the spacer ring, a test method was proposed. The tests were conducted on three aspects: basic characteristics, surface properties, and service performance. Firstly, the element composition, content and the cross-section morphology were analyzed to evaluate the characteristics of the spacer ring. Secondly, the surface morphology and surface roughness were observed to evaluate the surface properties of the spacer. Finally, the hardness distribution, friction, and wear were used to evaluate the service performance of the spacer ring. The proposed testing method for the spacer ring characteristics and performance is shown in Figure 1.
3 Experimental
Based on the testing method of the characteristics and performance for the spacer ring, the experimental procedure was divided into four parts, as shown in Figure 2. In the experiment, three spacer rings were used to test the characteristics and performance. Three spacer rings were defined in sample 1, sample 2, and sample 3, respectively. To analyze the elemental content, and observe the cross-sectional morphology, the spacer rings were cut into a sample of 6 mm in length by a wire cut electrical discharge machining. The samples were then embedded in a holder and the embedded sample was ground and polished using a grinding and polishing machine (Mopao3, China) to remove impurities caused by wire cutting and oxidation. To examine the elements, an X-ray Fluorescence Spectrometer (XRF, Japan) was employed. A microscope (VHX-600E, Japan) and a scanning electron microscope (QUANTA 450, United States) were used to observe the cross-sectional morphology of the polished samples. To observe the surface morphology and test the surface roughness, the spacer rings were first cut into 6 mm long samples, and a 3D optical profiler (Zygo 9000, United States) was used to detect their surface roughness and topography. To ensure the measurement results were as accurate as possible, three test points were selected to test the surface morphology and surface roughness. After grinding and polishing the sample, a micro hardness tester (HVS-1000, China) was used to test the hardness of the spacer ring, five evenly spaced points were selected from top to bottom of the sample to observe the variation of hardness with the position. The test force was 500 GF. Finally, friction-wear test was also carried out by reciprocating friction and wear tester (MZF-1, China) to evaluate the service performance of the spacer rings. Before testing, the spacer rings were cut into a sample 10 mm length. During the friction-wear test, the test force was set to 100 N, the test frequency to 1 Hz and the exposure time to 3,600 s. Figure 3 shows the test flow and experimental facilities.
4 Results and discussion
Basic characteristics, surface properties, and service performance tests were developed to understand spacer ring characteristics and performance. Basic characteristics testing was developed through elemental analysis and cross-sectional morphology. Surface property testing was characterized by surface morphology and surface roughness; the service performance testing was obtained by hardness and frictional wear performance.
4.1 Basic characteristics
4.1.1 Element content analysis
Different elemental and alloy contents have different effects on performance. This also reflects the performance requirements of the spacer ring in application. Testing revealed that the three samples have roughly the same amounts of the six primary types of elements—Fe, Al, P, Si, Ca, and S—in all three. The specific contents are shown in Table 1. In addition to the aforementioned components, sample 1 also contains 0.135% Ti and 0.119% V, sample 2 contains 0.074% Cr, and sample 3 contains 0.1042% V and 0.0694% Cr. Al element can improve the oxidation resistance and corrosion resistance of the alloy. P element can improve the hardness and strength of the materials. The addition of Si element can improve the elastic limit and tensile strength of the materials, and also increase the corrosion resistance. S element is not conducive to welding performance but can improve machinability. According to the main elements of the spacer ring and the main characteristics of each element, it can be seen that the spacer ring must meet certain hardness and strength requirements in the actual working process. In addition, corrosion resistance must also be ensured to extend the life of bearings.
4.1.2 Cross-section morphology
The analysis of cross-section morphology can help to establish the relationship between microstructure and properties of the spacer ring. From the microstructure of cross-sectional morphology, the mechanical properties of metals can be understood, which provides a basis for the scientific evaluation of characteristics. To understand the internal structure of the spacer ring, the cross-section morphology of the processed samples was observed. The observed results of the cross-sectional morphology are shown in Figures 4A–F. In the cross-section morphology of the three samples, irregular and dense pores can be seen as indicated by the arrows in Figure 4B. However, since the spacer rings are made from powder metallurgy, the porosity inside the processed spacer ring cannot be eliminated. Moreover, it can be seen that the pores are filled with lubricating oil. The spacer ring made by powder metallurgy contains pores, which can be used as countless small tanks to store oil, timely supplement the lubricating oil on the friction surface, maintain a better lubrication effect (Wang et al., 2022), and improve the wear resistance of the spacer ring. These results are supported by the findings of Xie et al. (2023a), Xie et al. (2023b). The existence of the lubrication grooves of the bearings is beneficial for vibration attenuation, friction reduction, and wear reduction. The pores shown in Figure 4 play the same role in the actual work of the bearing spacer ring. Scanning electron microscopy was performed on sample 1 to get a clearer view of the cross-sectional morphology, as shown in Figure 5.
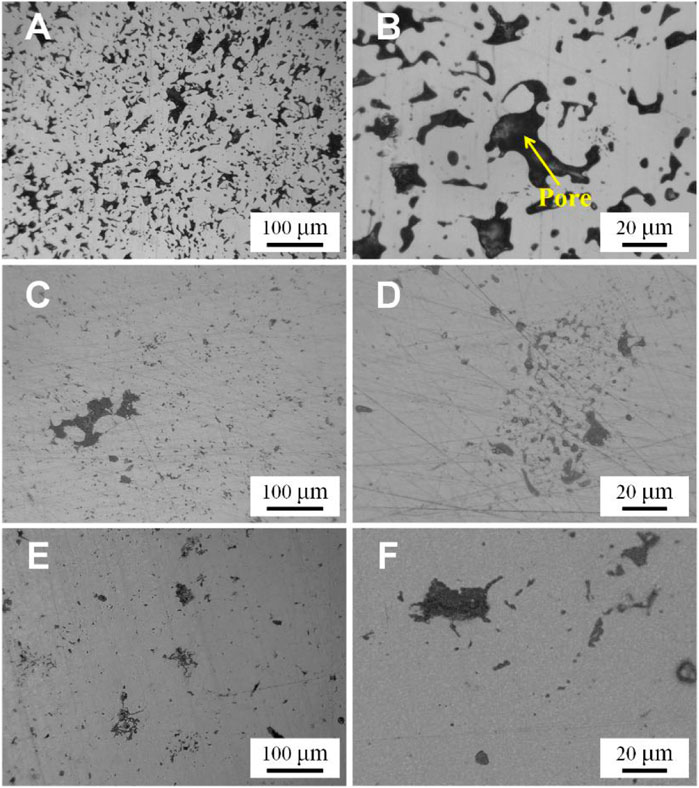
FIGURE 4. Cross-section microscopy of (A) sample 1–500 X, (B) sample 1–2000 X, (C) sample 2–500 X, (D) sample 2–2000 X, (E) sample 3–500 X, (F) sample 3–2000 X.
4.2 Surface properties
4.2.1 Surface morphology
The surface morphology can directly reflect the surface properties of the spacer rings. Furthermore, the surface morphology affects the wear resistance of the spacer rings. Figure 6 shows the surface morphology of various samples. To avoid coincidence, each sample was selected for testing at three points. As shown in Figure 6, most zone of the spacer rings were predominantly smooth, but many small pores appeared on the smooth surface. The surface pores are a typical feature of the spacer ring manufactured by powder metallurgy, the pores act as a reservoir of lubricant, thus improve the lubrication of the spacer ring.
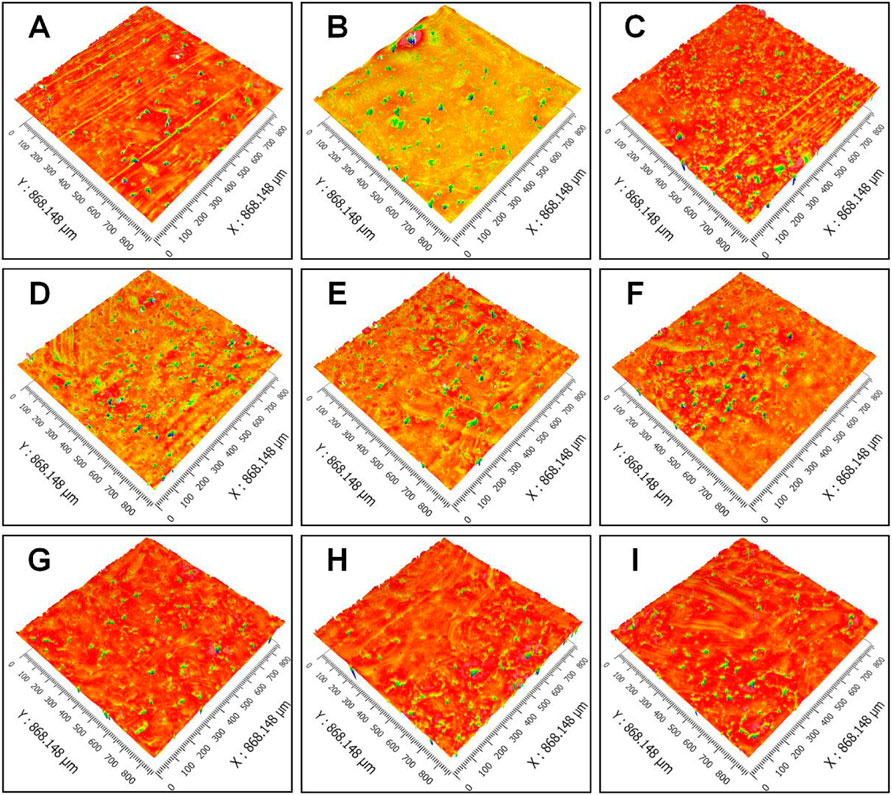
FIGURE 6. Surface morphology of (A) Test point 1 of sample 1, (B) Test point 2 of sample 1, (C) Test point 3 of sample 1, (D) Test point 1 of sample 2, (E) Test point 2 of sample 2, (F) Test point 3 of sample 2, (G) Test point 1 of sample 3, (H) Test point 2 of sample 3, (I) Test point 3 of sample 3.
4.2.2 Surface roughness
Surface roughness is the basic unit constituting the geometric characteristics of the machined surface and is closely related to the mating properties, wear resistance, fatigue strength, contact stiffness, vibration, and noise of mechanical parts. It has a significant effect on the service life and reliability of mechanical parts. The surface roughness values of the three samples are shown in Figure 7.
The roughness of sample 1 was slightly higher than sample 2 and sample 3, the roughness values of sample 1 was larger than 0.5 μm Sa, and the maximum value was 0.731 μm Sa, this phenomenon may be caused by the fact that sample 1 has more pores on the surface. In contrast, the surface roughness of sample 2 and sample 3 were relatively small compared to that of sample 1, the surface roughness of sample 1 and sample 2 were less than 0.375 μm Sa. Although there were some differences in the surface roughness of the three samples, but the roughness values were not large, and the low roughness can reduce the friction loss between the raceway and the rollers. The surface roughness significantly affects the lubrication effect of the bearing spacer ring. Surface morphology has a greater impact on the formation of lubricating film (Xie et al., 2023a; Xie et al., 2023b). As the surface roughness becomes greater, the conditions for forming the lubricating film become higher. Therefore, it is necessary to improve the surface roughness grade as much as possible.
4.3 Service performance
4.3.1 Hardness distribution
Hardness is the resistance of a solid to the invasion of external objects, and it is an index to compare the hardness of various materials. The Vickers hardness test has the lowest applicability limit, and almost all materials can be tested with the Vickers hardness method (Zhang, 2009; Wang, 2010). The average hardness values of Sample 1, Sample 2, and Sample 3 were 161.06, 173.06, and 123.50 HV, respectively. As shown in Figure 8, the hardest test points of the sample were mostly concentrated in the center of the sample, and the edge had a lower hardness. The reason for the low surface hardness was may be to avoid rolling elements damage. The higher hardness in the center area of the spacer rings improve the overall load rating to a certain extent, avoid bearing damage due to overload.
4.3.2 Friction and wear properties
The spacer rings have friction with rolling elements and retainer in the working process. The results show that the average friction coefficient of the sample was 0.85, and the wear loss was 0.03506 g. This result shows that the spacer ring has better friction and wear properties. The plot of the experimental force over time is shown in Figure 9. As shown in Figure 9, the experimental force was constant during the whole time of the experiment. The coefficient of friction over time is shown in Figure 10. The coefficient of friction becomes progressively high as the friction wear time increases.
It is noticeable that the coefficient of friction was stable at about 0.19 from the beginning of the experiment to 273 s when the experiment was conducted. This also indicates that the surface of the spacer ring has not yet shown wear damage and the surface properties have not changed. From 335 to 643 s, the coefficient of friction increased sharply, which is thought to be due to rapid wear of the sample surface, and the surface roughness changed significantly in a short period of time. Although the coefficient of friction is a characteristic of the object itself, it is derived from the ratio of the friction force detected by the sensor and positive pressure set in the experiment, as shown in Eq. 1. The increase of surface roughness leads to a greater friction force measured by the sensor, and therefore the calculated friction coefficient increases. After the experiment was conducted to 643 s, the friction coefficient showed a linear correlation with time. At this time, the roughness of the experimental location might not change significantly, but might be affected by the gradually rising temperature and the gradually deteriorating friction environment.
In the equation,
In the test, the variation of the wear loss is consistent with that of the corresponding friction coefficient. This shows that when the wear loss is large and the friction coefficient increases, the service performance of the spacer rings is seriously affected and the service life of spacer rings is reduced.
4.4 Error analysis
In the testing process, the introduction of errors needs to be controlled to obtain an accurate result. For element content analysis, the measurement error mainly comes from the contamination of the measured sample, the contaminants will disturb the accuracy of results. Therefore, thorough cleaning of the sample was required before the inspection was carried out. As for surface roughness and hardness testing, sampling points can have a significant impact on the magnitude of the test values, so, it is essential to measure multiple points and analyze them together to eliminate interfering factors. In particular, there are relatively more factors affecting the error of friction and wear test, the temperature and load of the experiment, the accuracy of the force sensor and precision balance may all introduce errors. To obtain relatively small error results in the friction and wear experiments, the stability of the experimental equipment and the standardization of the experimental process should be ensured.
5 Conclusion
This paper presented a study of characteristics and performance testing of bearing spacer rings. The basic characteristics, surface properties, and serviceability were tested. Based on the results obtained, following conclusions can be drawn:
(1) A testing method for the characteristics and performance of the spacer ring was proposed. The test method focuses on detecting basic characteristics, surface properties, and serviceability through the elements, cross-sectional morphology, surface morphology and roughness, as well as the hardness and frictional wear.
(2) The main elements of the spacer ring mainly contain Fe, Al, P, Si, Ca, and S, which contribute to the good hardness strength and good corrosion resistance of the spacer ring. The internal pores of the spacer ring can be used as tanks to store oil, thus improving the lubricating properties of the spacer ring.
(3) The surface morphology and surface roughness show that the surface of the spacer ring consists of a flat surfaces and fine pores. The fine pores can improve the lubrication of the spacer ring and the low roughness can reduce the frictional loss between bearings and rollers.
(4) Hardness in the centre of the spacer ring is higher than that of the surface, which helps to protect the rolling elements; The friction coefficient increases with friction wear time, and the average friction coefficient of the sample was 0.85, and the wear loss was 0.03506 g, which means that the spacer ring has good friction and wear properties.
As an important component of bearings, the research for the characteristics and performance of the spacer ring has a decisive impact on the overall performance of bearings. The research on the characteristics and performance of the spacer ring is conducive to promote the research and manufacturing of high-end bearings and support the development of high-end bearings.
The future work will focus on high performance manufacturing of spacer rings, through modelling the relationship between machining parameters and performance, leading to performance-driven manufacturing.
Data availability statement
The original contributions presented in the study are included in the article/Supplementary Material, further inquiries can be directed to the corresponding author.
Author contributions
YZ and JG contributed to the conception and design of the study. YZ and PL organized the database and wrote the manuscript. JW, BD, BR, and JT performed the statistical analysis, JG and ZJ contributed to checking the writing logic. All authors contributed to the article and approved the submitted version.
Funding
This research was funded by the Basic Scientific Research Project of Liaoning Provincial Education Department (Youth Project) (LJKQZ2021124).
Conflict of interest
Authors JW and BD were employed by Dalian Guangyang Bearing Company Limited.
The remaining authors declare that the research was conducted in the absence of any commercial or financial relationships that could be construed as a potential conflict of interest.
Publisher’s note
All claims expressed in this article are solely those of the authors and do not necessarily represent those of their affiliated organizations, or those of the publisher, the editors and the reviewers. Any product that may be evaluated in this article, or claim that may be made by its manufacturer, is not guaranteed or endorsed by the publisher.
References
Cheng, S. (2022). Benefit-finding intervention may alleviate caregiver insomnia, but more data are needed. China Plant Eng. 1, 113–114. doi:10.1016/j.jagp.2021.04.003
Cong, F. Y., Chen, J., and Pan, Y. (2011). Kolmogorov-Smirnov test for rolling bearing performance degradation assessment and prognosis. J. Vib. Control 17 (9), 1337–1347. doi:10.1177/1077546310384003
Dong, Y. F., Zhou, Z. D., and Liu, M. Y. (2017). Bearing preload optimization for machine tool spindle by the influencing multiple parameters on the bearing performance. Adv. Mech. Eng. 9 (2), 168781401668904–168781401668909. doi:10.1177/1687814016689040
Guan, J. L., Hu, Z. Y., Zhang, Y., Qi, Z. H., Sun, X. N., and Lu, W. W. (2018). Present situation and development of ultra-precision machining technology for high precision bearing rings. Tool. Eng. 52 (05), 3–7.
Guan, T., Hui, Z., and Gao, Y. (2017). “Condition monitoring of PTFE composite material bearing through the correlation between lubricant condition and wear simulation,” in 4th International Conference on Transportation Information and Safety (ICTIS), Banff, AB, Canada, 08-10 August 2017, 1028–1033. IEEE.
Jin, X., Chen, Y. M., Wang, L., Han, H. L., and Chen, P. (2021). Failure prediction, monitoring and diagnosis methods for slewing bearings of large-scale wind turbine: A review. Measurement 172, 108855. doi:10.1016/j.measurement.2020.108855
Khaire, M. V. (2018). Electrical vehicles' bearings: Technological impact, applications and requirements. Int. J. Electr. Hybrid Veh. 10 (4), 310–318. doi:10.1504/ijehv.2018.10019572
Liu, C., Yao, B., Gao, G., Wang, Y., and Mao, Y. (2020). Numerical calculation of composite water lubricated bearing considering effect of elastic deformation[C]//IOP Conference Series: Materials Science and Engineering. IOP Publ. 772 (1), 012114. doi:10.1088/1757-899x/772/1/012114
Sun, D., Zhao, Y., Zhang, J. J., Li, Z. H., Lin, D. P., Fernando, D. M., et al. (2016). KatG and KatE confer Acinetobacter resistance to hydrogen peroxide but sensitize bacteria to killing by phagocytic respiratory burst. Bearing 12, 31–40. doi:10.1016/j.lfs.2016.02.015
Wang, G. R., Zhong, L., He, X., Yang, Q. M., Yang, C. H., and Jiang, L. (2014). Experimental study of tribological properties of surface texture on rock bit sliding bearings. Proc. Institution Mech. Eng. Part J-Journal Eng. Tribol. 228 (12), 1392–1402. doi:10.1177/1350650114539937
Wang, J. L., Wang, Y. L., Zhang, C., Wang, D. P., Jia, Q., Cui, Y. H., et al. (2018). Preparation process of sliding bearing of precision motorized spindle[C]//IOP Conference Series: Materials Science and Engineering. IOP Publ. 417 (1), 012025.
Wang, R. (2010). Analysis and comparison of rockwell hardness and vickers hardness measurement methods. Sci. Technol. Econ. Mark. 1, 16–17.
Wang, R., Wang, L. S., Shi, T., Zhou, C., and Wang, L. M. (2022). Study on friction and wear properties metallurgy rigid gear of harmonic gear drive. Mater. Rep. 36 (13), 188–194.
Xie, Z. L., Jiao, J., and Wrona, S. (2023). The fluid-structure interaction lubrication performances of a novel bearing: Experimental and numerical study. Tribol. Int. 179, 108151. doi:10.1016/j.triboint.2022.108151
Xie, Z. L., Jiao, J., and Yang, K. (2023). Experimental and numerical study on the mixed lubrication performances of a new bearing. Tribol. Int. 182, 108334. doi:10.1016/j.triboint.2023.108334
Xu, W. B., Ogrodnik, P. J., Goodwin, M. J., and Bancroft, G. (2010). Effect of manufacturing tolerances on stiffness and damping of hydrodynamic journal bearings. Trans. Tech. Publ. Ltd. 139, 2662–2667. doi:10.4028/www.scientific.net/amr.139-141.2662
Yadav, E., and Chawla, V. K. (2021). An explicit literature review on bearing materials and their defect detection techniques. Mater. Today Proc. 50, 1637–1643. doi:10.1016/j.matpr.2021.09.132
Yan, C., Zeng, Q. F., and Yang, H. B. (2020). Research progress of new superelastic bearing material TiNi60 alloy. Chin. J. Nonferrous Metals 30 (05), 1038–1048.
Yi, J. M., Xu, X. L., Chai, S. Y., and Guo, C. H. (1983). Material analysis of activity spacer ring. Bearing 05, 19–21+63.
Yu, F., Wei, G. N., and Xu, D. (2005). Research and development of stainless bearing material. J. Iron Steel Res. 1, 6–9.
Yu, J. K., and Wu, M. Y. (2020). Research on manufacturing method of surface integrity of large-size bearing raceway with excellent service performance[C]//Journal of Physics: Conference Series. IOP Publ. 1578 (1), 012172. doi:10.1088/1742-6596/1578/1/012172
Yuan, Z. W., Qin, Y., Deng, C. L., and Zheng, P. (2018). Synergistic effects of surface strengthening and surface micro-texture on aviation spherical plain bearing tribological properties. Proc. Institution Mech. Eng. Part J-Journal Eng. Tribol. 232 (7), 797–808. doi:10.1177/1350650117730522
Keywords: bearing spacer ring, performance testing, characteristics, surface properties, serviceability
Citation: Guo J, Zhao Y, Long P, Wang J, Du B, Rajpar BM, Jin Z and Tang J (2023) Investigation on characteristics and performance of bearing spacer ring. Front. Mater. 10:1202041. doi: 10.3389/fmats.2023.1202041
Received: 07 April 2023; Accepted: 23 May 2023;
Published: 01 June 2023.
Edited by:
Gokhan Kilic, Eskişehir Osmangazi University, TürkiyeReviewed by:
Mustafa Kuntoğlu, Selcuk University, TürkiyeZhongliang Xie, Northwestern Polytechnical University, China
Copyright © 2023 Guo, Zhao, Long, Wang, Du, Rajpar, Jin and Tang. This is an open-access article distributed under the terms of the Creative Commons Attribution License (CC BY). The use, distribution or reproduction in other forums is permitted, provided the original author(s) and the copyright owner(s) are credited and that the original publication in this journal is cited, in accordance with accepted academic practice. No use, distribution or reproduction is permitted which does not comply with these terms.
*Correspondence: Jiwu Tang, dGFuZ2ppd3VAZGxvdS5lZHUuY24=