- 1Jiangxi Institute of Transportation Research Co., Ltd., Nanchang, China
- 2Research and Development Center on Technogies and Equipment of Long-span Bridge Co-nstruction Minsistry of Transport, PRC, Nanchang, China
- 3Jiangxi Provincial Communications Investment Group Co., Ltd., Nanchang, China
- 4School of Civil Engineering and Architecture, East China Jiaotong University, Nanchang, China
- 5Jiangxi Provincial Communications Investment Group Co., Ltd., Road Network Operation M-anagement Company, Nanchang, China
- 6Engineering Research Institute, China Construction Eighth Engineering Division Corp Ltd., Shanghai, China
This study aims to minimize the carbon emissions of cement and investigate the viability of employing activated coal gangue (CG) as an additional cementitious ingredient. This paper investigated the effects of water-cement ratio, ages, and amount of activated CG dosing on the compressive and flexural strength of cement mortar as well as the effects of activated CG on hydration products, hydration process, and hydration degree. The impacts of activated CG on the hydration products and microstructure of cement were examined using XRD, SEM, and TG/DTG systems. A large amount of active SiO2 and Al2O3 in the activated CG react with Ca(OH)2 leading to a secondary hydration reaction in cement. The hydrated calcium silicate and hydrated calcium aluminate gels produced by the subsequent hydration process can reduce the porosity of hardened cement and boost cement mortar strength. The 28 days flexural and compressive strengths of specimens with 30wt.% activated CG rise by 11.69% and 11.82%, respectively, in comparison to that of specimens with 30wt.% quartz powder. When activated CG is mixed with cement, the early hydration rate of the cement can be decreased while the later hydration rate is increased.
1 Introduction
Being one of the few nations where coal serves as the principal energy source, China has abundance of coal resources and is both the world’s largest producer and user of coal (Wang et al., 2016; Xue et al., 2020; Zhang et al., 2020; HU et al., 2022). According to statistics, China’s CG accumulation will reach 7 billion tons, and with an increase of 150 million t/a in 2023, it has become one of the largest solid wastes in China (He et al., 2023). 0.1–0.2 tons of solid CG trash are formed for every ton of coal produced (Zhou, 2009). In addition to heavily contaminating the environment and encroaching on a lot of territory, the large accumulation of CG is also lead to collapsing and silting up waterways (Zhang et al., 2013; Wang et al., 2021a; Li et al., 2021; Qiu et al., 2021; Chang et al., 2022). In conclusion, the CG can be harmful if improperly handled. It still has potential utility, and a lot of scholars are interested in how to resource utilization of CG.
As CG contains large quantities of SiO2 and Al2O3, it may be used to produce cement instead of clay, which is energy efficient, costless, and environment friendly (Xu et al., 2015; Monteiro-Paulo-J et al., 2017; Arreola-Sanchez et al., 2021; Wang et al., 2021b; Zhang et al., 2021; Liu, 2022). Additionally, kaolinite is abundant in CG. And kaolinite can be transformed into metakaolin under specific circumstances, which is rich in active SiO2 and Al2O3. Therefore, CG possess potential gelability. In order to realize the efficient utilization of CG in cement production and application, scholars have done a lot of research on the effect of CG on cement properties.
CG was studied as a possible addition as fine aggregate for concrete. The results of the trials carried out by Duan et al. (Duan et al., 2014a; Duan et al., 2014b) showed that 20% of CG is the ideal level, improving the early strength of concrete. According to the research of Dong et al. (2016), the CG fine aggregate calcined at various temperatures will significantly affect the pore structure of cement-hardened mortar. The secondary hydration reaction between CG and cement produces more hydration products, reducing the porosity of cement-hardened mortar. From the perspective of mineral composition, the main component of CG is aluminosilicate and exists in the form of mineral crystals, so it doesn't has the property of directly acting as a gelling material (Jiao et al., 2022). Liu et al. (2022) prepared alkali-activated cement using 800°C calcined CG powder. The tests showed that 3 days, 7 days, 28 days compressive strengths of alkali-activated cements rose by 8%, 25%, and 13%, respectively, when 10% calcined CG powder was added. Ding et al. (202) studied the effect of specific surface area and chemical initiator on compressive strength of CG specimens. And the results showed that the activity of CG would be significantly improved after mechanical grinding, as mechanical grinding destroyed the original mineral structure of CG, increased the fracture rate of silicon-oxygen bonds and improved the specific surface area. With the addition of 10wt.% CG and 2wt.% Ca(OH)2, the secondary hydration reaction will be accelerated leading to the significant increase of the compressive strength of specimen. The Ca(OH)2 increases the contact area between the alkali solution and CG, accelerates the dissolution rate of CG particles, and releases more alkali metal ions such as Si4+ and Al3+ in the system to produce new hydration products. High-temperature calcination activation method was utilized by Jiu et al. (Jiu et al., 2022) to treat CG. The study found that the kaolinite in the CG take place de-hydroxylation reaction during the calcination process and transforms into metakaolinite. The activity index of activated CG reach 114%–135%.
Guo et al. (2011) found that when 30% unactivated CG was added, the 28 days strength was reduced by 36% compared with the pure cement, and the strength could reach 42.5 MPa after calcination at 700°C and grinding treatment. According to the investigation of Shi et al. (2008), there are two phases in the hydration reaction of cement with CG: At first, the calcium hydroxide reacts with the CG to produce hydration products, and then the calcium hydroxide reacts with CaSO4 and CG to form AFt. According to the study of Wang et al. (2021c), the interface transition zone of concrete containing CG aggregate is a weak area. It is caused by the fact that insufficient ion migration led to the limit of secondary hydration reaction.
Scholars have done a lot of work on the application of CG in cement, and the existing research results show that CG after treated by thermal activation, mechanical activation, and chemical activation, can improve the mechanical properties of cement, and decrease the porosity of cement. Additionally, as CG is widely dispersed, it has a complicated and varied composition, and a variable influence on cement performance. The research of CG focuses on the optimal ratio of cement admixture, and there is less research on the influence mechanism of cement properties. Thus, the impact of CG on the hydration mechanism of cement needs to be revealed in order to use CG efficiently.
For finding substitutes for cement active mineral additive, this work investigated the impact of activated CG (from Yangquan, Shanxi, China) on mechanical performance and hydration mechanism of cement. The CG was activated by mechanical grinding and high temperature calcination. And the influence of activated CG on the mechanical properties were showed. XRD, SEM, TG/DTG were used to analyzed the effect of activated CG on hydration mechanism of cement.
2 Experiment
2.1 Raw materials
CG was obtained from Yangquan China. The cement is produced by using gypsum and cement clinker from the Huaxin cement factory. Moreover, the sand is Xiamen-produced ISO sand.
Table 1 shows the chemical compositions of cement and CG in the Yangquan region. Figure 1 shows the mineral compositions of cement and CG. The mineral compositions of the CG in the Yangquan region are shown in Table 2. According to Figure 1A, the primary minerals in cement are gypsum, C3S, C2S, C3A, and C4AF. According to Figure 1B, the primary minerals of CG in the Yangquan region are mica, kaolin, quartz, calcite, siderite, and dolomite. The primary oxide compositions of CG are SiO2 and Al2O3 as shown in Table 1. Table 2 demonstrates that kaolinite is one of the main minerals in CG at the Yangquan region. These indicate that the CG in the Yangquan region show potential activity as cement mineral additive.
The coal gangue was finely grounded by the vertical planetary mill (YXQM-4L) for better activity. The rotation speed is set to 600 r/min, and the grinding time is 30 min. The particle size distribution of CG is showed in Figure 2. It can be seen in Figure 2B that after 30 min of milling, the particle size of coal gangue powder is about 20 μm. Particles smaller than 20 μm accounted for 56.92% of the total, particles smaller than 50 μm accounted for 93.38% of the total, and particles smaller than 100 μm accounted for 100% of the total.
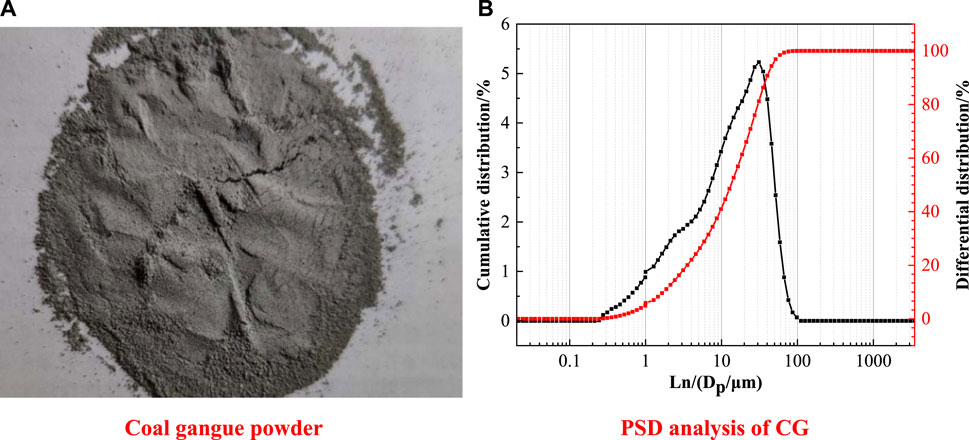
FIGURE 2. The image (A) and the PSD analysis (B) of CG. (A) Coal gangue powder. (B) PSD analysis of CG.
2.2 Specimen preparation and curing condition
Existing studies have shown that thermal activation is one of the most effective ways for improving the activity of CG (MAKO et al., 2006; TAO et al., 2014; Guo et al., 2022). When the activation temperature of CG in a range of 800°C–900°C, the kaolinite in CG can be converted into metakaolin with an amorphous structure. Amorphous metakaolin possess high activity. When the calcination temperature exceeds 900°C, metakaolin further converte to mullite and loses its activity (Wu et al., 2016; Cao et al., 2017; Qiang, 2020; Wang et al., 2022). Therefore, the CG was pulverized to a particle size of 20 μm after being calcined at 850°C for 2 h. The XRD analysis of CG following high temperature calcination is shown in Figure 3. The image demonstrates the changes in mineral species and structure of CG following high temperature calcination at 850°C. The interlayer water is removed from kaolinite and disruption of the kaolin’s structure by high temperature calcination led to the formation of metakaolinite (reactive SiO2 and Al2O3) (Cheng et al., 2018). Pure cement specimens (40 mm × 40 mm × 160 mm) and mortar specimens (40 mm × 40 mm × 160 mm) were prepared using the mix ratios in Tables 3, 4, respectively. After 24 h of curing (The relative humidity was 95% and at a temperature of 20 ± 1°C), they were demolded, and then further set in water at a temperature of 20 ± 1°C.
2.3 Testing methods
2.3.1 Mechanical properties test
The compressive and flexural strengths tests of specimens (40 mm × 40 mm × 160 mm) were determined at the curing age of 3, 28, and 90 days. The compressive and flexural strengths of specimens were determined by using an automated cement mortar strength testing machine. The loading rate of the flexural strength is 50 N/s and that of the compressive strength is 2400 N/s.
2.3.2 XRD test
XRD was employed to determine the mineral compositions of CG and cement. After mechanical properties test, hydration products of specimen per formulation were also analyzed by XRD. The samples in powder form were identified by XRD (copper radiation after nickel filtration) with acquisition range from 4° to 60° (2θ). The scan rate is 2°/min and the step size is 0.02°.
2.3.3 SEM/EDS test
SEM equipped with an EDS device system are used a scanning electron microscope (JEOLJSM-6460LV) with an accelerated voltage of 20 kV to investigate the hydration products of specimens after polishing and spraying with gold.
2.3.4 TG/DTG test
Thermal analyzer of Switzerland Mettler Toledo was utilized to semi-quantitatively analyze hydration products of specimen per formulation. The samples in the form of powder were heated in a nitrogen atmosphere. The maximum temperature of heating is 1,000°C, and the heating rate is 10°C per minute.
3 Results and discussion
3.1 Effect of activated coal gangue on the mechanical properties of cement
Figure 4 shows the flexural and compressive strengths of pure cement specimens, specimens with 30wt.% activated CG, and specimens with 30wt.% quartz powder at 3 days, 28 days, and 90 days. Pure cement specimens show the highest flexural and compressive strengths under the age of 3 days, 28 days, and 90 days, followed by specimens with 30wt.% activated CG, while specimens with 30wt.% quartz powder have the lowest flexural and compressive strengths. It was also shown that curing age greatly increases the flexural and compressive strengths of pure cement specimens, 30wt.% activated CG specimens, and 30wt.% quartz powder specimens. In comparison to specimens made of 30wt.% quartz powder, the flexural strength of 30wt.% activated CG specimens improves by 12.96%, 11.69%, and 10.98% at 3 days, 28 days, and 90 days, respectively, while the compressive strength increases by 14.53%, 11.82%, and 16.10%, respectively. This caused by the fact of that Al2O3 and SiO2 reacted with CaO in cement to form a significant number of hydration products, which can make up for the strength loss due to the reduction of partial cement (Xiao, 2015).
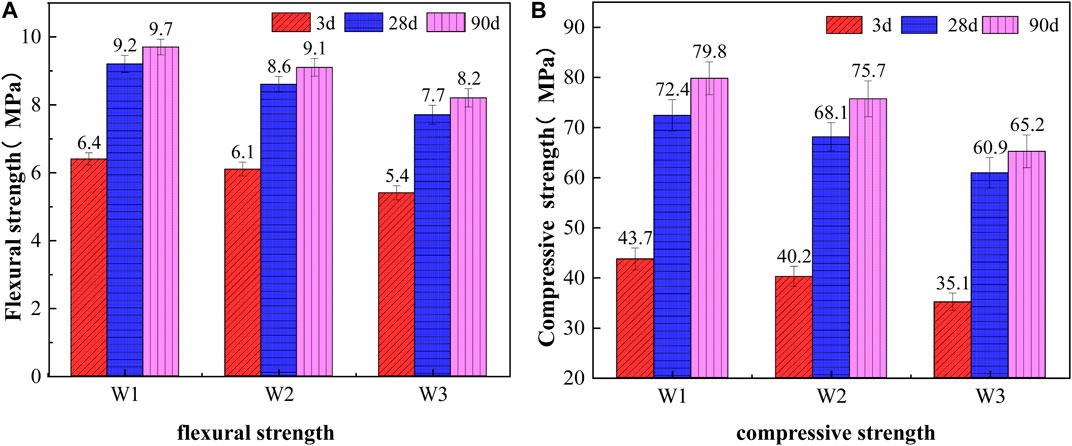
FIGURE 4. Effect of 30% activated coal gangue on the mechanical properties of cement. (A) flexural strength. (B) compressive strength.
3.2 The effect of activated CG on cement hydration products by XRD analysis
As seen in Figure 5, the 30wt.% activated CG cement’s hydration products are significantly influenced by the curing age. The diffraction intensity of quartz increases while that of C4AF and C3S decreases as curing age grows from 3 days to 90 days. This is because when the curing age rises, cement minerals like C4AF and C3S increasingly hydrate and produce a significant amount of amorphous hydration products. Quartz, on the other hand, is an inert additive and won’t take part in the reaction. Also, it is shown that with the increasing of the curing age, the amount of calcium hydroxide in the cement with 30wt.% activated CG steadily decreases. A significant amount of calcium hydroxide generated by C3S and C2S hydration is consumed, which caused by the fact that the active SiO2 and Al2O3 in activated CG reacted with calcium hydroxide to form hydrated calcium silicate and hydration calcium aluminate, during the subsequent hydration process. Consuming calcium hydroxide concurrently enhances the hydration process of C3S and C2S in a substantial way.
According to Figure 6A, the amount of activated CG significantly affects the cement hydration products at 3 days. When activated CG doping increases, the diffraction intensity of C4AF and C3S considerably decreases while quartz content dramatically rises. The relative cement content reduces with increasing CG doping in specimens, resulting in a decrease in C4AF and C3S content and an increase in quartz content. Moreover, an increase in the amount of activated CG will speed up the cement’s hydration process, producing a lot of amorphous hydration products and further lowering the levels of C4AF and C3S. The active SiO2 and Al2O3 in activated CG will react with calcium hydroxide to consume calcium hydroxide, as seen by the drop in the diffraction intensity of calcium hydroxide as the addition of activated CG rises. Combining Figures 6A, B, it can be shown that the diffraction intensity of calcium hydroxide decreases noticeably from 3 days to 28 days in specimens with various quantities of activated CG. This suggests that cement mineral hydration is faster than the secondary hydration reaction of calcium hydroxide in cement with active SiO2 and Al2O3 in activated CG.
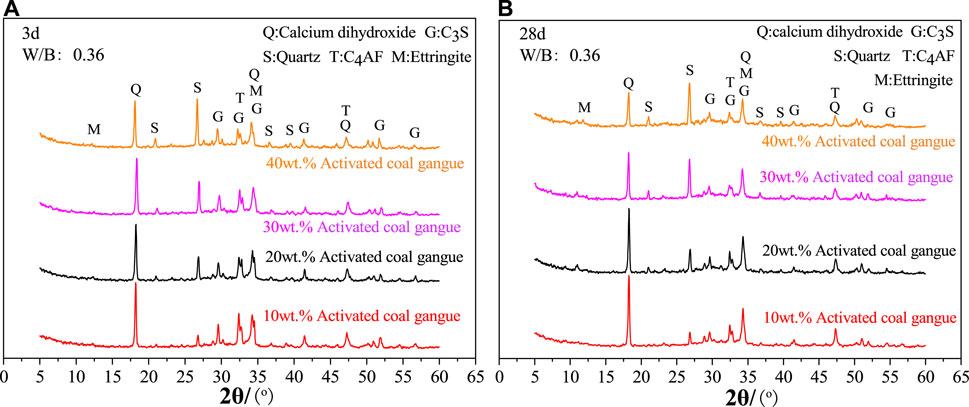
FIGURE 6. Effect of activated coal gangue dosing on hydration products at 3 days (A) and 28 days (B).
Figure 7 displays the XRD examination results of the hydration products in specimens with 30wt.% activated CG and 30wt.% quartz powder. Quartz powder is an inert additive that won't interact with the cement, meaning it won't effect the hydration products of the cement. As shown in Figure 7, the diffraction intensities of calcium hydroxide, C4AF, and C3S in the specimens with 30wt.% activated CG are significantly weaker than those in the specimens with 30wt.% quartz powder. This implies that activated CG significantly promotes the hydration of the cement by the reaction between Ca(OH)2 and active SiO2 and Al2O3 in activated CG, and further improve hydration rates of C4AF and C3S as the consumption of Ca(OH)2. Ettringite is present in the slurry of 30wt.% activated CG cement. Nevertheless, ettringite (AFt) is not present in the slurry of 30wt.% quartz powder CG cement. This suggests that ettringite is the hydration product of secondary hydration reaction in specimens with 30wt.% activated CG.
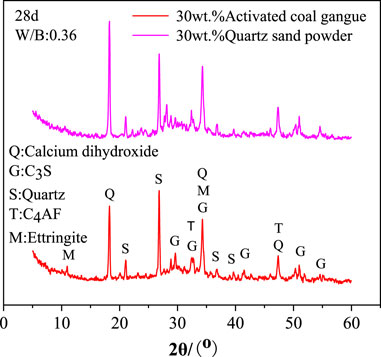
FIGURE 7. XRD analysis of hydration products of specimens with 30wt.% activated CG and 30wt.% quartz powder.
In conclusion, after mixing cement with 30wt.% activated CG and water, C2S and C3S in cement reacted with water to form hydrated calcium silicate and calcium hydroxide. And then the active SiO2 and Al2O3 in activated CG reacted with the Ca(OH)2 to form hydrated calcium silicate and hydrated calcium aluminate gel. Active Al2O3 also reacted with Ca(OH)2 and CaSO4 to produce ettringite. This is the reason that the flexural and compressive strength of the specimens with 30wt.% activated CG is higher than that of the specimens with 30wt.% quartz powder. These secondary hydration products filled the pores in the cement matrix, optimized the pore structure of the cement, and improved the mechanical properties of specimens.
3.3 SEM analysis of the effect of activated CG on hydration products
The shape of the hydration products of pure cement paste and cement with 30wt.% activated CG at 3 days, 7 days, and 28 days, as well as the element composition at the numbered locations, were examined using SEM to estimate the calcium-silica ratio of the hydrated calcium silicate gel.
The calcium-silica ratios of the hydrated calcium silicate in cement at the numbered locations are shown in Figure 8. With the increasing of age, the significant changes in the microscopic morphology of the hydration products of pure cement paste and cement with 30wt.% activated CG have occurred. At 3 days, the matrix of cement with 30wt.% activated CG (Figure 8B) and the pure cement paste (Figure 8A) both contain a large number of unhydrated cement particles while the pure cement paste contains the most unhydrated cement particles. The hydration products in pure cement paste are hydrated calcium silicate, Ca(OH)2 and small number of ettringite. However, the primary hydration products of cement with 30wt.% activated CG are hydrated calcium silicate (C-S-H) and large number of ettringite. This indicates that active Al2O3 in the activated CG reacting with Ca(OH)2 and CaSO4 will produce more ettringite, as described in Eq. 1. The addition of activated CG will reduce the ratio of calcium to silicate of C-S-H in cemet. The ratio of calcium to silicate of C-S-H in cement with 30wt.% activated CG decreased from 0.61 to 0.55, compared with pure cement paste. According to this, Ca(OH)2 will be consumed during the secondary hydration reaction, further accelerating the hydration of C2S and C3S (Zhang et al., 2004).
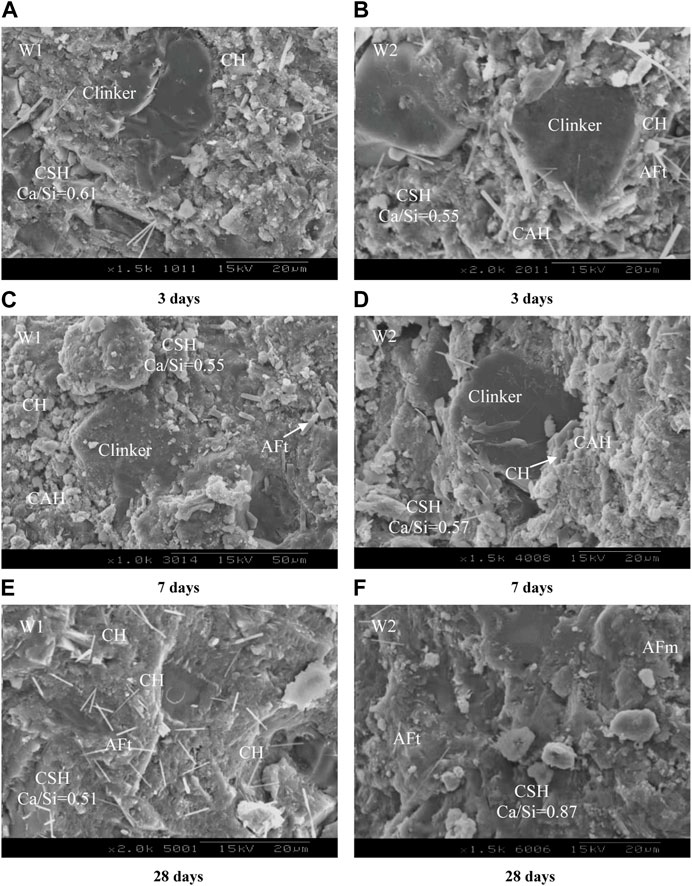
FIGURE 8. SEM/EDS analysis of the hydration products of pure cement and cement with 30wt.% activated CG. (A, B) 3 days. (C, D) 7 days. (E, F) 28 days.
As the curing period is extended to 7 days, there is a considerable reduction in the quantity of unhydrated cement particles in pure cement paste (Figure 8C), an increase in the Ca(OH)2 content. And significant amounts of hydrated calcium aluminate and hydrated calcium silicate is observed. Ca(OH)2, hydrated calcium aluminate and hydrated calcium silicate are the hydration products of C3S, C2S, and C3A in cement. Moreover, with increasing curing age the ratio of calcium to silicate of C-S-H decreased from 0.61 to 0.58, demonstrating that the hydration degree of C3S and C2S becomes more complete. Also, it is found that the calcium alumina content in pure cement paste starts to increase. According to Figure 8D), the unhydrated cement particles in the cement with 30wt.% activated CG greatly reduce as the curing age increases from 3 days to 7 days, and Ca(OH)2 begins to dramatically decrease. This suggests that the active SiO2 and Al2O3 in activated CG react vigorously with Ca(OH)2 and consume a significant quantity of Ca(OH)2 formed by the hydration of C3S and C2S. In the meantime, the amount of hydrated calcium aluminate in cement with 30wt.% activated CG dramatically decreased. This is because a large quantity of hydrated calcium aluminate is consumed as hydrated calcium aluminate react with CaSO4 forming ettringite. It is worth noting that the ratio of calcium to silicate of calcium silicate hydrate in cement with 30wt.% activated CG increases from 0.55 to 0.57 as the curing duration rises from 3 days to 7 days. This is caused by the reaction between activated SiO2 in activated CG and Ca(OH)2 resulting in the formation of C-S-H, which has a higher ratio of calcium to silicate.
The unhydrated cement particles in pure cement paste are nearly nonexistent when the curing period is extended to 28 days (Figure 8E), demonstrating that the cement has essentially finished the hydration reaction. Ettringite and Ca(OH)2 are abundant in pure cement, and the ratio of calcium to silicate of C-S-H falls to 0.51. According to this finding, the ratio of calcium to silicate of hydrated calcium silicate falls as age rises, suggesting the hydration reaction of C3S and C2S becomes more sufficient. As it can be seen in Figure 8F that there is few Ca(OH)2 and ettringite in the cement with 30wt.% activated CG, indicating the hydration reaction of cement with 30wt.% activated CG has completed. These results indicate that a secondary hydration reaction between activated CG and Ca(OH)2 produce a considerable quantity of C-S-H (see Eq. 2). Calcium sulfoaluminate monosulfide hydrate (AFm) is produced simultaneously by reaction between ettringite and hydrated calcium aluminate (see Eq. 3). As a consequence, the amount of Ca(OH)2 and ettringite in cement with 30wt.% activated CG are significantly reduced by the reaction between activated CG and Ca(OH)2, as well as ettringite and hydrated calcium aluminate. And the rections will produce more C-S-H and AFm leading to increase the density of cement with 30wt.% activated CG. It can be observed an increase in the ratio of calcium to silicate of C-S-H in cement with 30wt.% activated CG with the increase of age. As the age rise from 3 to 28 days, the ratio of calcium to silicate of C-S-H in cement with 30wt.% activated CG increase from 0.55 to 0.87.
As the activated CG show high reactivity, active SiO2 and Al2O3 in activated CG can react with gypsum and Ca(OH)2 in cement to form C-S-H, C-A-H, AFt and AFm. Thus, activated CG can promote the hydration reaction of cement. This is the reason that activated CG can enhance mechanical properties of cement. As a consequence, the W1 group with 30wt.% activated CG shows higher flexural and compressive strengths than that of W3 group with 30wt.% quartz powder.
3.4 TG/DTG analysis of the effect of activated CG on hydration products
The hydration products including C-S-H gel, AFt, Ca(OH)2, and CaCO3 in cement will decompose at a specific temperature. Therefore, the content of hydration products in cement can be measured by TG/DTG analysis. Figure 9 displays the results of TG/DTG analysis of cement with 30wt.% activated CG after hydrated for 28 days.
The TG/DTG analysis results reveal that the weight loss of the cement with 30wt.% activated CG consisted of the following four stages: the weight loss in a temperature range of 50–400°C due to the loss of the bound water of calcium silicate hydrate, calcium aluminate hydrate, and Aft (TG1); the weight loss in a temperature range of 400–500°C attributed to the decomposition of Ca(OH)2 (TG2); the weight loss in a temperature range of 500–760°C ascribed to the secondary dehydration of C-S-H, C-A-H, and AFt (TG3); and the weight loss in a temperature range of 760–950°C ascribed to the loss of CO2 of calcium (TG4). The weight loss of cement with 30wt.% activated CG in four stages is 9.05%, 2.81%, 2.61%, and 1.61%, respectively. These findings can be used to compute the total bound water in hydrated calcium silicate, hydrated calcium aluminate, AFt, calcium hydroxide, and the content of hydration products in cement with 30wt.% activated CG at 28 days can be obtained by the follow Eqs 4–6.
Where, M1 represents the mass percentage of C-S-H, C-A-H, and AFt in the total mass of the bound water; M2 represents the mass percentage of Ca(OH)2; and M3 represents mass percentage of the total bound water in all hydration products. According to above equations (Eqs 4–6), M1 = 11.66 wt.%, M2 = 14.26 wt.%, and M3 = 15.13 wt.%.
By using TG/DTG data and Eqs 4–6, the bound water content of hydration products in pure cement paste, cement with 30wt.% activated CG and cement with 30wt.% quartz powder at different ages can be obtained, which are shown in Figure 10. According to Figure 10, curing age greatly affects the amount of hydration products in pure cement paste, cement with 30wt.% activated CG and cement with 30wt.% quartz powder. Yet as the curing period grows, the bound water content of hydration products gradually increases, suggesting that the degree of hydration rises with the extension of age. However, the growth rate of the bound water gradually decreases, which is caused by fewer unhydrated components and slower rate of hydration. With the age growing from 1 day to 28 days, the bound water content in pure cement paste, cement with 30wt.% activated CG, and cement with 30wt.% quartz powder increases from 6.81wt.%, 6.47wt.%, and 5.41wt.% to 15.36wt.%, 15.03wt.%, and 12.09wt.%, respectively. In pure cement paste and cement with 30wt.% activated CG, the amount of bound water is almost equal, while it is significantly higher than that in cement with 30wt.% quartz powder. The activated CG involved in the secondary hydration reaction will form more hydration products, which makes up for the decrease in hydration products brought by the drop in cement content. In the first 14 days, the growth rate of total bound water in pure cement paste is higher than that in cement with 30wt.% activated CG, but it is lower than that of cement with 30wt.% activated CG after 14 days. This demonstrates that the addition of the activated CG will decrease the rate of cement hydration at early age. Due to interaction between activated CG and Ca(OH)2, it will boost the rate of cement hydration at later age.
The hydration of C3S and C2S lead to the formation of Ca(OH)2 in cement. As a result, the cement hydration process can be revealed by analyzing the content of calcium hydroxide in cement. The Ca(OH)2 content in the pure cement paste, cement with 30wt.% activated CG, and cement with the 30wt.% quartz powder considerably increase with curing time growing, as shown in Figure 11. However, the growth rates of Ca(OH)2 content slow down gradually. This is because that the amount of unhydrated C3S and C2S decrease as curing time increases, leading to less hydration reaction. Thus, the growth of Ca(OH)2 is slowed down. The Ca(OH)2 content in the pure cement paste, cement with 30wt.% activated CG, and cement with 30wt.% quartz powder increase from 10.04wt.%, 8.63wt.%, and 9.95wt.% to 21.36wt.%, 14.26wt.%, and 19.33wt.%, respectively, as the age increase from 1 day to 28 days. It can be concluded that the Ca(OH)2 content in cement with 30wt.% activated CG is the lowest, whereas the Ca(OH)2 content in pure cement paste is the highest level across all ages. The difference of Ca(OH)2 content between pure cement paste and cement with 30wt.% quartz powder varies little, but it does the other way between pure cement paste and cement with 30wt.% activated CG. This implies that activated CG will participate in secondary hydration reaction, which consumes lager number of calcium hydroxide.
In conclusion, activated CG possess high reactivity and can react with the Ca(OH)2 to form a significant number of hydration products, which can fill pores in cement and enhance its mechanical properties. The secondary hydration reaction is the interaction between Ca(OH)2 and activated CG. And the secondary hydration reaction is subsequent to the hydration reaction of cement.
4 Discussion
The results show that the incorporation of activated CG into cement can reduce the early hydration rate of cement (Wu and He, 2020). But the activated CG contains a large amount of active SiO2 and Al2O3, which can participate secondary hydration with Ca(OH)2, improving the late hydration rate of cement. And it will form AFt, hydrated calcium silicate, and calcium aluminate hydrate gels improving the compactness of the matrix and enhancing the mechanical properties of cement (Wang et al., 2022). As solid waste, CG has potential utilization value in the research of partially replacing cement to prepare green cementitious materials (Li and Wang, 2019). The current research results focus on the experimental study of the ratio of mineral admixtures, and the CG used by different scholars comes from different regions. Meanwhile, the proportioning scheme is different, which makes it difficult to obtain regular results for the properties of activated CG cement (Yang et al., 2021; Hao et al., 2022). The influence mechanism of activated CG on cement hydration is also not completely revealed (Zhao et al., 2022). Therefore, this paper selects CG in Yangquan area of Shanxi Province as the main research object, and studies the hydration products, microstructure changes and mechanical properties of activated CG cement through XRD analysis, SEM analysis, TG/DTG analysis and mechanical experiments. This work finds out that activated CG possess high reactivity and potential to be used as a mineral admixture to replace cement. It provides data support and theoretical basis for the utilization of CG in China, which can not only alleviate the environmental pressure caused by a large amount of CG, but also reduce the cost of concrete. However, the effects of thermal activation temperature and heat activation time on the activity of CG should be further analyzed to provide a more comprehensive theoretical support for the resource utilization of CG.
5 Conclusion
According to XRD, SEM and TG/DTG analyses as well as mechanical experiment results, the effect of activated CG on hydration products, microstructure, and mechanical properties of cement can be revealed. And the impact of activated CG on bound water in hydration products and Ca(OH)2 in cement are analysed. The conclusions are drawn as follow.
(1) At the age of 3 days, 28 days, and 90 days, the flexural strength of specimens with 30wt.% activated CG increase by 12.96%, 11.69%, and 10.98% as well as the compressive strength increase by 14.53%, 11.82%, and 16.10%, in comparison to that of specimens with 30wt.% quartz powder.
(2) The activated CG possess high reactivity, the active SiO2 and Al2O3 in activated CG can react with the Ca(OH)2 generated by the hydration of C3S and C2S to form C-S-H gels and C-A-H gels. Moreover, the active Al2O3 in activated CG can react with Ca(OH)2 and CaSO4 to produce AFt. The formation of secondary hydration products will improve the mechanical properties and decrease the porosity of specimens.
(3) When the age increase from 1 day to 28 days, the bound water content of pure cement paste is similar to that of cement with 30wt.% activated CG. And they are significantly higher than the bound water content of cement with 30wt.% quartz powder. Quartz will not affect the hydration products. The secondary hydration reaction between activated coal CG and Ca(OH)2 in cement cement will produce a large number of hydration products to compensate for the reduction of cement.
(4) When the age increase from 1 day to 28 days, the content of Ca(OH)2 in pure cement paste was similar to that of cement with 30wt.% quartz powder. And they are significantly higher than that of in cement with 30wt.% activated CG. The secondary hydration reaction between activated CG and cement consumes a large amount of calcium hydroxide.
(5) Activated CG added to cement can slow down the early stages of cement hydration. Contrarily, in the later stage, cement with activated CG can outperform pure cement in terms of hydration rate.
Data availability statement
The original contributions presented in the study are included in the article/Supplementary Material, further inquiries can be directed to the corresponding author.
Author contributions
All authors listed have made a substantial, direct, and intellectual contribution to the work and approved it for publication.
Acknowledgments
The authors thank funding from the Jiangxi Provincial Department of Transportation major engineering Science and technology project (2021C0008, 2022H0014, 2022C0007), the Jiangxi Provincial Natural Science Youth Fund(20202BABL214043) and the National Natural Science Foundationof China (Grant Nos. 52163034).
Conflict of interest
ZZ, LM, and ZH were employed by Jiangxi Institute of Transportation Research Co., Ltd. CL and HZ were employed by Jiangxi Provincial Communications Investment Group Co., Ltd. PY was employed by Jiangxi Provincial Communications Investment Group Co., Ltd. YZ was employed by China Construction Eighth Engineering Division Corp Ltd.
The remaining authors declare that the research was conducted in the absence of any commercial or financial relationships that could be construed as a potential conflict of interest.
Publisher’s note
All claims expressed in this article are solely those of the authors and do not necessarily represent those of their affiliated organizations, or those of the publisher, the editors and the reviewers. Any product that may be evaluated in this article, or claim that may be made by its manufacturer, is not guaranteed or endorsed by the publisher.
References
Arreola-Sanchez, M., Chavez-Garcia-Hugo, L., Martinez-Molina, W., Mercedes Alonso Guzman, E., Antonio Torres Acosta, A., and Maria Ponce Ortega, J. (2021). Use of metakaolin or coal gangue as a partial substitution of cement in mechanical performance of PC mortars. Eur. J. Environ. Civ. Eng. 25 (3), 502–515. doi:10.1080/19648189.2018.1532819
Cao, Y., Li, Y., Zhang, J., Cao, Z., and Sun, C., (2017). Effects of calcination temperature and particle size on pozzolanic activity and microstructure of coal gangue. J. Chin. Ceram. Soc. 45 (08), 1153–1158.[J]
Chang, J., Du, G., Du, J., and Shi, X., (2022). Current situation, problem and suggestion of comprehensive utilization of coal gangue. China Environ. Prot. Ind. (08), 13–17.[J]
Cheng, Y., Ma, H., Zhu, H., Li, W., Xin, M., Liu, Y., et al. (2018). Study on chloride binding capability of coal gangue based cementitious materials. Constr. Build. Mater., 167.[J]
Ding, S., Chen, J., and Guan, X., (2021). Experimental study on active excitation of coal gangue and mechanical properties of mortar. China Concr. Cem. Prod. (12), 79–83.[J]
Dong, Z., Xia, J., Duan, X., and Cao, J., (2016). Pore structure of fine aggregate mortar based on the activity of calcined coal gangue from Xuzhou mining area. Chin. J. Rock Mech. Eng. 35 (04), 819–825.[J]
Duan, X., Xia, J., and Yang, F., (2014). Experimental research on the influence of coal gangue fine aggregate-cement-based materials on the mechanical properties. Ind. Constr. 44 (02), 98–102.[J]
Duan, X., Xia, J., and Yang, J. (2014). Influence of coal gangue fine aggregate on microstructure of cement mortar and its action mechanism. J. Build. Mater. 17 (04), 700–705.[J]
Guo, W., Li, D., Chen, J., and Yang, N., (2011). Effect of heat activated and mechanical force activated method on coal gangue cementing performance. J. Build. Mater. 14 (03), 371–375.[J]
Guo, Z., Xu, J., Xu, Z., Gao, J., and Zhu, X. (2022). Performance of cement-based materials containing calcined coal gangue with different calcination regimes. J. Build. Eng. 56, 104821. doi:10.1016/j.jobe.2022.104821
Hao, R., Li, X., Xu, P., and Liu, Q., (2022). Thermal activation and structural transformation mechanism of kaolinitic coal gangue from Jungar coalfield, Inner Mongolia, China. Appl. Clay Sci. 223, 106508.[J]
He, X., Duan, X., and Guo, W., Research status and prospect of preparing building materials from coal gangue. Procedia Earth Planet. Sci. 2023 (02), 15–18.[J]
Hu, Y., Zhang, R., Qie, X., and Liu, H., (2022). Evaluation of China's coal resource energy carbon emission efficiency in the whole life cycle. China Environ. Sci. 42 (06), 2942–2954.[J]
Jiao, Y., Xu, S., Peng, D., and Liu, H., (2022). Research progress on activation and mechanism of coal gangue. Appl. Chem. Ind. 51 (08), 2362–2366+2372.[J]
Jiu, S., Wang, M., Chen, Y., Chen, J., and Gao, Q., (2022). Synthesis and characterization of low-carbon cementitious materials from suspended calcined coal gangue. Front. Mater., [J]
Li, J., and Wang, J. (2019). Comprehensive utilization and environmental risks of coal gangue: A review. J. Clean. Prod. 239, 117946.[J]
Li, Y., Liu, S., and Guan, X. (2021). Multitechnique investigation of concrete with coal gangue. Constr. Build. Mater., 301.[J]
Liu, C., Wang, C., Wu, J., and Gao, M. (2022). Calcined coal gangue fines as the substitute for slag in the production of alkali-activated cements and its mechanism. Processes 10 (8), 1557. doi:10.3390/pr10081557[J]
Mako, E., Senkar, Z., Kristof, J., and Vágvölgyi, V. (2006). Surface modification of mechanochemically activated kaolinites by selective leaching. J. Colloid Interface Sci. 294 (2), 362–370. doi:10.1016/j.jcis.2005.07.033
Monteiro-Paulo-J, M., Miller-Sabbie, A., and Horvath, Arpad (2017). Towards sustainable concrete. Nat. Mater. 16 (7), 698–699. doi:10.1038/nmat4930[J]
Qiang, L. (2020). Effect of calcination temperature on the activity of coal gangue and mechanism study. Non-Metallic Mines 43 (03), 100–102+106.[J]
Qiu, J., Zhou, Y., Guan, X., and Zhu, M., (2021). The influence of fly ash content on ITZ microstructure of coal gangue concrete. Constr. Build. Mater., 298.[J]
Shi, D., Shi, H., and Xu, B. (2008). Reaction properties of coal gangue calcium hydroxide system. J. Zhejiang Univ. Eng. Sci. (05), 900–904.[J]
Tao, Q., Su, L., Frost, R. L., Zhang, D., Chen, M., Shen, W., et al. (2014). Silylation of mechanically ground kaolinite. Clay Miner. 49 (4), 559–568. doi:10.1180/claymin.2014.049.4.06
Wang, A., Liu, P., Mo, L., Liu, K., Ma, R., Guan, Y., and Sun, D., (2022). Mechanism of thermal activation on granular coal gangue and its impact on the performance of cement mortars. J. Build. Eng. 45, 103616. doi:10.1016/j.jobe.2021.103616
Wang, C., Yang, J., and Xu, S. (2021). Experimental study of the mechanical and microstructure characteristics of coal gangue road stabilization materials based on alkali slag cementation. Mater. (Basel, Switz. 14 (13), 3601. doi:10.3390/ma14133601[J]
Wang, F., Liu, Z., Han, L., and Xie, F., (2021). Preparation and properties of activated coal gangue geopolymer. Bull. Chin. Ceram. Soc. 40 (03), 914–920.
Wang, Jiacheng, Liu, Feng, and Wang, Lei (2016). Sustainable coal mining and mining sciences. J. China Coal Soc. 41 (11), 2651–2660.[J]
Wang, Q., Ran, K., Wang, J., Huang, Y., and Zhang, Q., (2021). Study on the microscopic properties of the interfacial transition zone in spontaneous combustion coal gangue concrete. Concrete (08), 69–71.[J]
Wu, H., Kong, D., Zhang, X., and Zhang, M., (2016). Physicochemical properties and thermal activation of coal gangue in liupanshui mining area. Bull. Chin. Ceram. Soc. 35 (11), 3814–3818.[J]
Wu, Z., and He, J. (2020). Effect of coal gangue on compressive strength of cement. Concrete (07), 81–83.[J]
Xiao, Wei (2015). Physical mechanical properties and durability of airport rapid repairing materials of magnesium phosphate cement. Nanjing University of Aeronautics and Astronautics, Jiangning, Nanjing.[D]
Xu, D., Cui, Y., Hui, L., Yang, K., Xu, W., and Chen, Y. (2015). On the future of Chinese cement industry. Cem. Concr. Res. 78, 2–13. doi:10.1016/j.cemconres.2015.06.012
Xue, L., Wang, H., Zhu, B., Sheng, W., Zheng, Z., Ge, Y., et al. (2020). Evaluation of coal resources sustainability and analysis of system coordination development. Econ. Geogr. 40 (01), 114–124.[J]
Yang, J., Wu, C., Chen, X., Hu, L., Wang, L., and Gao, X., (2021). Influence of self-ignited coal gangue as mineral admixture on properties of concretes. Concrete (09), 86–89.[J]
Zhang, C., Xue, J., and Fang, L. (2004). Mechanical properties and microstructures of alkali activated burned coal gangue cementitious matrial. J. Chin. Ceram. Soc. (10), 1276–1280.[J]
Zhang, J., Ning, S., Chen, M., Gong, H., and Zhang, L., (2020). Development prospects and countermeasures of Chinese coal resources. Geol. Rev. 66 (S1), 143–145.[J]
Zhang, S., Liu, D., Shao, F., Luo, Y., and Li, W., (2013). Comprehensive utilization of coal gangue. Clean. Coal Technol. 19 (05), 92–95.[J]
Zhang, W., Chai, J., Feng, X., Dong, C., Sun, Q., Li, M., et al. (2021). Preparation and microstructure of coal gangue -based geopolymer. J. China Univ. Min. Technol. 50 (03), 539–547.[J]
Zhao, Y., Yang, C., Li, K., Qu, F., Yan, C., and Wu, Z., (2022). Toward understanding the activation and hydration mechanisms of composite activated coal gangue geopolymer. Constr. Build. Mater. 318, 125999.[J]
Keywords: coal gangue, low carbon materials, hydration products, activation, mechanical properties
Citation: Zhu Z, Liu C, Mao L, Han Z, Chen L, Zou H, Li L, Yu P, Dong J and Zhang Y (2023) Study on the effect of activated coal gangue on the mechanical and hydration properties of cement. Front. Mater. 10:1186055. doi: 10.3389/fmats.2023.1186055
Received: 14 March 2023; Accepted: 26 April 2023;
Published: 10 May 2023.
Edited by:
Mehran Khan, Hong Kong Polytechnic University, Hong Kong SAR, ChinaReviewed by:
Pshtiwan Shakor, Sulaimani Polytechnic University, IraqAyaz Ahmad, University of Galway, Ireland
Babar Ali, COMSATS University Islamabad, Pakistan
Copyright © 2023 Zhu, Liu, Mao, Han, Chen, Zou, Li, Yu, Dong and Zhang. This is an open-access article distributed under the terms of the Creative Commons Attribution License (CC BY). The use, distribution or reproduction in other forums is permitted, provided the original author(s) and the copyright owner(s) are credited and that the original publication in this journal is cited, in accordance with accepted academic practice. No use, distribution or reproduction is permitted which does not comply with these terms.
*Correspondence: Chaoqun Liu, 13677089341@163.com