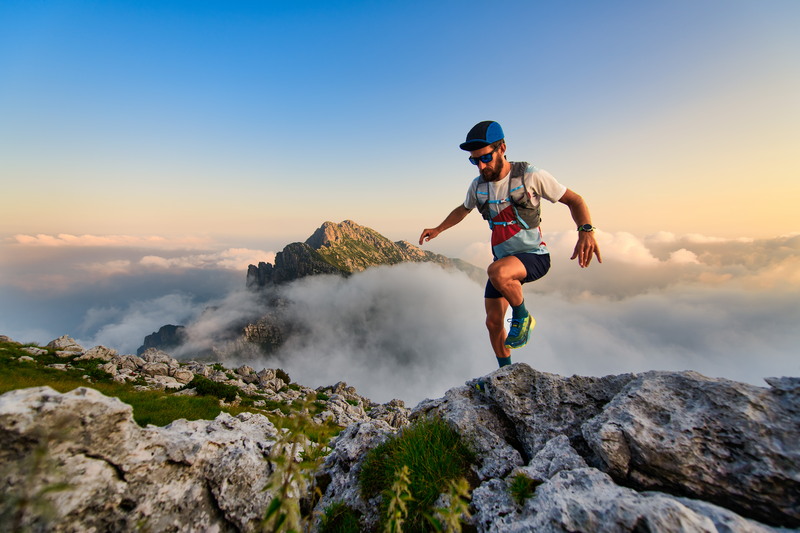
95% of researchers rate our articles as excellent or good
Learn more about the work of our research integrity team to safeguard the quality of each article we publish.
Find out more
MINI REVIEW article
Front. Mater. , 17 May 2023
Sec. Environmental Degradation of Materials
Volume 10 - 2023 | https://doi.org/10.3389/fmats.2023.1184610
This article is part of the Research Topic Machining Technology and Environmental Degradation Mechanism of Surface Microstructure of Special Materials- Volume II View all 5 articles
Titanium alloys are commonly used in industrial applications due to their exceptional mechanical and chemical properties. However, their low thermal conductivity and high chemical reactivity pose significant challenges in machining, leading to increased cutting forces, rapid tool wear, and poor surface quality. To overcome these issues, advanced cutting edge preparation techniques have been developed to enhance the machining performance of titanium alloys. This paper provides an overview of state-of-the-art cutting edge preparation techniques for titanium alloy machining and examines their effects on machining performance. It first presents a characterization method for cutting edge geometry and explores how it affects machining performance, demonstrating that strategic cutting edge preparation can significantly enhance performance by reducing cutting forces and improving surface finish. The paper also emphasizes the underlying mechanisms of cutting edge preparation and its impact on machining performance and subsequent cutting edge erosion. Finally, it concludes by discussing future research directions in this field, highlighting the need to develop new cutting edge preparation techniques and optimize existing ones. Overall, this paper serves as a valuable resource for researchers and engineers seeking to improve the cutting performance of titanium alloys in various applications.
Titanium alloy is a commonly used material in aerospace engines due to its excellent comprehensive properties, such as high specific strength, strong heat resistance, and low-temperature resistance (Amann et al, 2023). It not only prolongs the service life of aircraft but also reduces their weight and fuel consumption, significantly improving their flight performance (Yin et al, 2023). However, with increasingly demanding service performance requirements for aircraft engines, higher demands have been placed on their materials and manufacturing technology. As a typical difficult-to-process material, titanium alloy is often prone to material deformation and heat accumulation near the cutting edge during cutting processes, leading to tool wear and affecting processing quality. This is due to its low thermal conductivity, small elastic modulus, and small deformation coefficient (Chakradhar et al, 2023; Chen et al, 2023).
Cemented carbide tools are the most commonly used tool materials in metal cutting due to their toughness, wear resistance, and hardness. These properties are achieved by sintering high-hardness carbides like WC and TiC with binders such as Co and Ni at high temperatures (Ivanov et al, 2000; Kouadri et al, 2013; Kazymyrovych and Kryzhanivskyy, 2023). However, when cutting titanium alloy, hard alloy tools face a unique challenge. The low thermal conductivity of titanium alloy results in an increase in cutting force on the unit contact area due to the short contact length between the chips and the front cutting surface. This, in turn, leads to an extremely high cutting temperature at the cutting edge, with the heat generated during cutting concentrated within a small range near the cutting deformation zone and the cutting edge (Zhou et al, 2019). As the cutting temperature increases, the chemical affinity between the tool and the workpiece material strengthens, increasing the likelihood of the workpiece adhering to the front and back cutting surfaces of the tool, exacerbating the squeezing and friction between the cutting edge and the workpiece, and leading to cold welding between the tool and the workpiece (Yang et al, 2022). Additionally, as the chips flow, the binder is peeled off, taking away some of the tool material and worsening tool wear. As a result, reducing tool wear and ensuring high surface integrity in titanium alloy materials have become pressing challenges that require immediate attention (Liang et al, 2022).
Tool manufacturing success is dependent on several factors including tool materials, geometric structure, coatings, and cutting edge preparation technology. As cutting technology continues to develop, the tool manufacturing industry increasingly values cutting edge preparation technology (Hartig et al, 2022). This technology can meet the demand for specific geometric shapes and effectively eliminate microscopic geometric defects on the tool surface, thereby improving tool life and machining surface quality (Bergs et al, 2020). Passivation is currently a commonly used cutting edge preparation technique. After passivation treatment, various tool edges do not exhibit a regular rounded shape under the microscope. The edge shape can be divided into blunt round edges, sharp edges, and chamfer edges (Qi et al, 2021; Hu et al, 2022). Blunt round edges include arc-shaped edges, waterfall-shaped edges, and trumpet-shaped edges.
The cutting edge of a tool is responsible for the primary cutting action during the cutting process. The structural form of the cutting edge is crucial in determining the tool’s cutting performance and tool life (Hartig et al, 2022). The geometric shape of the cutting edge directly influences the force-heat characteristics of the tool. As the tool cuts the workpiece, the cutting edge structure changes, leading to changes in the contact area between the tool and workpiece, resulting in a fluctuation in cutting force. Changes in the cutting edge can initiate changes in the squeezing and friction between the cutting edge and the workpiece, which in turn affect the temperature change during cutting (Nemetz et al, 2020). Various physical parameters, such as cutting force and cutting temperature, impact the tool’s cutting stability, tool wear, and the quality of the machined surface to varying degrees during metal cutting. Therefore, the cutting edge structure becomes a crucial determinant in enhancing the machining quality and extending the tool life when selecting a turning tool for titanium alloy (Sidiq et al, 2020).
The structure of the cutting edge of a tool can be classified into two categories: symmetric and asymmetric, with the symmetrical cutting edge being a specific case of the asymmetric cutting edge (Bergs et al, 2020). The tool’s cutting edge shape can be described from two perspectives: macroscopic and microscopic. Macroscopic analysis defines the spatial dimensions of the tool, such as the front angle γ, back angle α, and wedge angle β, as the macroscopic geometric dimensions. Microscopic analysis establishes the cutting edge shape by examining the tiny geometry of the transition region between the front and back faces of the tool. However, there is currently no standard way to describe the geometric shape of cutting edges. Several methods have been proposed by different researchers, mainly including the following three types.
The single radius measurement method is a technique used to determine the ideal cutting edge radius rβ by fitting an arc segment in the transition area between the front and back faces of a cutting tool. This method is effective for blunt round cutting edges that are simple, as selecting three or more measurement points in the chosen area can fit an ideal circle. However, for complex-shaped cutting edges, this method is inadequate and may result in significant errors due to manual measurement point selection and external factors’ influence (Dodmani and Subbiah, 2022). Currently, there is no standardized method for describing the geometric shape of cutting edges, and many researchers have proposed various characterization methods.
In 2011, Denkena et al proposed the K-factor method, also known as the shape factor method, as an improvement to the single radius measurement method (Denkena et al, 2011). This approach employs five parameters to determine the shape of the cutting edge, as illustrated in Figure 1. The contour lines of the front and back cutting edges are extended, and the point where the extension lines intersect represents the hypothetical cutting tip. The distance from the virtual cutting tip to the separation point on the front cutting edge is called Sγ, which represents the front cutting edge segment value. Likewise, the distance from the separation point on the back cutting edge to the cutting tip is called Sα, representing the back cutting edge segment value. The cutting edge’s geometric shape is described by the ratio of Sγ to Sα, which is called the shape factor K. When K = 1, the cutting edge is symmetrical. When K < 1, the cutting edge tilts towards the back cutting edge, resulting in a waterfall-type cutting edge. When K > 1, the cutting edge tilts towards the front cutting edge, forming a trumpet-type cutting edge (Denkena et al, 2021). While the K-factor method can characterize non-symmetrical cutting edges, the separation points of the front and back cutting edges on the blunt circle cannot be accurately determined. Therefore, the cutting edge contour shape is obtained through optical scanning, and the separation points are determined by computer recognition to avoid errors caused by manual operation.
An alternative approach to determine the cutting edge profile is to use an iterative algorithm. Wyen et al introduced a characterization algorithm that does not require predetermined fitting areas to broaden the fitting area to the entire cutting edge profile (Wyen et al, 2012). The algorithm uses sets of three adjacent measuring points on the profile to estimate the least-squares fitting circle, as shown in Figure 2. This technique calculates the radius, uncertainty, and coefficient of determination, and selects the cutting edge radius with the lowest uncertainty. To measure cutting edge asymmetry, a bisector of the wedge angle is drawn, and a perpendicular line is drawn at the intersection with the cutting edge profile, intersecting the least-squares line at Dγ and Dα distances. The ratio of Dγ to Dα, represented by S, is used as a measure of cutting edge asymmetry.
In the development of cutting technology, researchers have extensively investigated the connection between the geometric shape of the cutting edge and the cutting efficiency of tools. Albrecht, in 1960, examined the effect of cutting edge radius on the metal cutting process and introduced the “plow effect” into the mechanism (Albrecht, 1960). Similarly, Liu et al delved into the impact of various cutting edge shapes on cutting forces, temperature, and surface quality of processed materials. Interestingly, they discovered that cutting edge performance was significantly enhanced once the edges became dulled. In conclusion, it is evident that different cutting edge shapes affect various aspects such as cutting forces, temperature, tool life, and machining surface integrity (Liu et al, 2022).
Yen et al explored the impact of different tool edge structures on carburized and quenched steel processing by analyzing chip shape, cutting force, cutting temperature, stress, and strain using finite element simulation (Yen et al, 2004). Meanwhile, Shao et al employed the finite element method to predict the temperature distribution in titanium alloy cutting, and verified simulation accuracy via experimentation (Shao et al, 2010). Hua et al investigated the effects of sharp edge, circular arc edge, reverse edge, and other tool edge shapes on residual stresses in turning. They discovered that circular arc edge and reverse edge tools resulted in more complex residual stresses on the machined surface and a larger stress influence zone (Hua et al, 2005). Additionally, Varela et al scrutinized the relationship between blunt tool edge morphology and residual stresses, and their experimental findings showed that tool blunting can improve the workpiece’s surface quality to a certain extent (Varela et al, 2014).
Fulemová et al attempted to enhance tool life when milling chromium-nickel-iron alloy 718 by modifying the shape factor K but found no improvement. Conversely, cutting experiments on tool steel revealed that a shape factor K greater than 1 prolonged tool life and reduced the workpiece’s surface roughness (Fulemová and Řehoř, 2015). Similarly, Ventura et al confirmed through cutting experiments that the shape factor K of passivated tools impacted blade edge wear. By selecting an appropriate shape factor, they could efficiently reduce tool wear during cutting (Ventura et al, 2015). To mitigate severe elastic-plastic deformation caused by circular blade edges during cutting, Childs et al recommended using waterfall-shaped blade edges (Childs et al, 2008). Bassett et al studied the effect of different shape factors K on the thermal-stress distribution and tool wear while cutting AISI1045 with W-Co coated tools. They found that the posterior cutting edge segment value Sα had a substantial effect on tool life (Bassett et al, 2012). Meanwhile, Denkena et al investigated the impact of cutting edge geometry on tool wear, cutting force, and other factors, developing a tool life chart based on the tool’s thermomechanical load curve. This revealed the law of cutting edge’s impact on tool wear (Denkena et al, 2011). Furthermore, Uhlmann et al utilized the vertical rotary passivation method to passivate micro cutting tools and investigated the influence of passivation time and passivation radius on tool wear. Their findings verified that appropriate tool edge passivation could minimize tool wear (Uhlmann et al, 2015). Finally, Padmakumar et al designed three different shape factor passivation circular edge tools using the K-factor method, with K values of 1, 1.3, and 1.6. By milling AISI4140 steel, they discovered that K values greater than 1 effectively reduced cutting force within a specific processing range (Padmakumar and Shiva Pradeep, 2020).
Cutting titanium alloy with hard alloy tools is often hampered by the issue of tool wear, which has been the focus of numerous experimental and theoretical studies worldwide (Gupta et al, 2022). In particular, Hartung et al has conducted extensive research on the tool wear mechanism and identified that the primary types of wear for hard alloy tools during titanium alloy cutting are diffusion wear and adhesion wear (Hartung et al, 1982). In addition, Li et al has investigated the impact of different tool types on the cutting performance of titanium alloys, and found that YG-class tools perform better than YT-class tools. Through cutting tests, it was observed that adhesion wear, diffusion wear, and oxidation wear are the primary wear mechanisms during titanium alloy cutting, with the front cutting surface experiencing more severe wear than the rear cutting surface (Li et al, 2008).
Konneh et al conducted an analysis of the influence of cutting parameters on the wear of hard alloy tools during milling of sodium calcium glass, which revealed that the predominant cause of tool wear was abrasive wear (Konneh et al, 2018). Li et al investigated the wear mechanism of PCBN cutting tools during high-speed cutting of titanium alloys and found that the wear was caused by multiple factors, including mechanical wear, adhesion, diffusion due to heat, and oxidation resulting from chemical reactions (Li et al, 2007). Liao et al studied the wear of hard alloy cutting tools when cutting Inconel718 and found that the diffusion of Ni and Fe elements from the workpiece into the Co of the tool weakened the bonding effect of the tool material, leading to shedding of the tool material during the contact between the workpiece and the tool (Liao and Shiue, 1996). Kitagawa et al analyzed the wear mechanism of cutting tools in the cutting process and determined that the predominant wear form was boundary wear, caused by friction between the tool and the workpiece (Kitagawa et al, 1997).
During the study of diffusion wear of hard alloy cutting tools in dry cutting of titanium alloy, Deng et al found that at a cutting temperature of 400°C, there was not a significant diffusion of W and Co elements from the tool into the titanium alloy. However, at 600°C, the diffusion of W and Co was observed to occur over a wide range, while at 800°C, the diffusion depth was as high as 20 μm, resulting in lower hardness at the diffusion layer as compared to the area further away from it (Jianxin et al, 2008). Meanwhile, Sheikh-Ahmad et al studied the wear characteristics of hard alloy cutting tools with varying grain sizes and found that the tool wear resulted from plastic deformation and oxidation of the WC grains as well as shedding of the bonding phase Co (Sheikh-Ahmad and Bailey, 1999).
Achieving good cutting performance is crucial for many materials, especially for titanium alloys which possess exceptional mechanical properties. These alloys find extensive use in industries such as aerospace and medicine due to their high strength, low density, and excellent corrosion resistance. However, machining titanium alloys can be challenging owing to their low elastic modulus, poor thermal conductivity, and high chemical reactivity. Therefore, improving their cutting performance is of great interest. One approach to achieve this is through cutting edge preparation, which involves intentionally modifying the cutting edge geometry of the tool to enhance its cutting ability. Future research can focus on improving cutting edge preparation techniques such as honing, grinding, and coating for the machining of titanium alloys.
The refinement of cutting tools by honing involves polishing the cutting edge using abrasive stones or diamond-coated tools (Yussefian and Koshy, 2013), resulting in reduced roughness and increased sharpness. This technique is particularly effective for micro-geometries such as micro-chamfers and micro-radii, which can improve cutting performance. Grinding is another technique that shapes and sharpens the cutting edge using a grinding wheel (Hartig et al, 2022). This process is used to create macro-geometries such as chip breakers, which aid chip evacuation and reduce cutting forces. Coating is a method where a thin layer of material is deposited onto the tool surface to enhance its wear resistance and decrease cutting forces (Meindlhumer et al, 2020). Common coatings include diamond-like carbon (DLC), titanium nitride (TiN), and titanium aluminum nitride (TiAlN). Research has shown that honing, grinding, and coating can improve cutting ability, reduce cutting forces, and increase tool life in machining titanium alloys. Combining different cutting edge preparation techniques can further enhance these benefits.
To sum up, cutting edge preparation is critical in improving the cutting performance of titanium alloys. Techniques like honing, grinding, and coating can modify the cutting edge geometry of the tool, leading to reduced cutting forces and improved tool life. As the demand for high-performance materials increases in different industries, cutting edge preparation’s importance in machining titanium alloys is set to grow.
FP contributed to conception and design of the study, organized the database, and wrote the first draft of the manuscript. HY revised this manuscript and charged the review process. All authors listed have made a substantial, direct, and intellectual contribution to the work and approved it for publication.
This research was funded by 2022 Major R&D Project of Lishui Economic Development Zone (2022KFQZDYF14), Open Foundation of the State Key Laboratory of Fluid Power and Mechatronic Systems (GZKF-202216), and the Lishui Science and Technology Plan Project (2022ZDYF04 and 2022SJZC002). Foundation of Key laboratory of digital degsin and intelligent manufacture in culture & creativity product of Zhejiang Province (2016E10007).
The authors declare that the research was conducted in the absence of any commercial or financial relationships that could be construed as a potential conflict of interest.
All claims expressed in this article are solely those of the authors and do not necessarily represent those of their affiliated organizations, or those of the publisher, the editors and the reviewers. Any product that may be evaluated in this article, or claim that may be made by its manufacturer, is not guaranteed or endorsed by the publisher.
Albrecht, P. (1960). New developments in the theory of the metal-cutting process: Part I The ploughing process in metal cutting. J. Eng. Industry 82, 348–357. doi:10.1115/1.3664242
Amann, F., Poulain, R., Delannoy, S., Couzinié, J. P., Clouet, E., Guillot, I., et al. (2023). An improved combination of tensile strength and ductility in titanium alloys via oxygen ordering. Mater. Sci. Eng. A 867, 144720. doi:10.1016/j.msea.2023.144720
Bassett, E., Köhler, J., and Denkena, B. (2012). On the honed cutting edge and its side effects during orthogonal turning operations of AISI1045 with coated WC-Co inserts. CIRP J. Manuf. Sci. Technol. 5, 108–126. doi:10.1016/j.cirpj.2012.03.004
Bergs, T., Schneider, S. A. M., Amara, M., and Ganser, P. (2020). Preparation of symmetrical and asymmetrical cutting edges on solid cutting tools using brushing tools with filament-integrated diamond grits. Procedia CIRP 93, 873–878. doi:10.1016/j.procir.2020.04.028
Chakradhar, B., Singaravel, B., Ugrasen, G., and Kiran Kumar, A. (2023). Prediction of cutting forces using MRA, GMDH and ANN techniques in micro end milling of titanium alloy. Mater. Today Proc. 72, 1943–1949. doi:10.1016/j.matpr.2022.10.209
Chen, J., Liu, D., Jin, T., and Qi, Y. (2023). A novel bionic micro-textured tool with the function of directional cutting-fluid transport for cutting titanium alloy. J. Mater. Process. Technol. 311, 117816. doi:10.1016/j.jmatprotec.2022.117816
Childs, T. H. C., Sekiya, K., Tezuka, R., Yamane, Y., Dornfeld, D., Lee, D. E., et al. (2008). Surface finishes from turning and facing with round nosed tools. CIRP Ann. 57, 89–92. doi:10.1016/j.cirp.2008.03.121
Denkena, B., Krödel, A., and Heckemeyer, A. (2021). Numerical and experimental analysis of thermal and mechanical tool load when turning AISI 52100 with ground cutting edge microgeometries. CIRP J. Manuf. Sci. Technol. 35, 494–501. doi:10.1016/j.cirpj.2021.08.006
Denkena, B., Lucas, A., and Bassett, E. (2011). Effects of the cutting edge microgeometry on tool wear and its thermo-mechanical load. CIRP Ann. 60, 73–76. doi:10.1016/j.cirp.2011.03.098
Dodmani, A., and Subbiah, S. (2022). Accurate measurement of cutting-edge radius on a single-crystal diamond tool. Manuf. Lett. 33, 469–478. doi:10.1016/j.mfglet.2022.08.004
Fulemová, J., and Řehoř, J. (2015). Influence of form factor of the cutting edge on tool life during finishing milling. Procedia Eng. 100, 682–688. doi:10.1016/j.proeng.2015.01.420
Gupta, M. K., Niesłony, P., Sarikaya, M., Korkmaz, M. E., Kuntoğlu, M., Królczyk, G. M., et al. (2022). Tool wear patterns and their promoting mechanisms in hybrid cooling assisted machining of titanium Ti-3Al-2.5V/grade 9 alloy. Tribol. Int. 174, 107773. doi:10.1016/j.triboint.2022.107773
Hartig, J., Kirsch, B., Zimmermann, M., and Aurich, J. C. (2022). Cutting edge preparation with elastic bonded diamond grinding wheels: Influence of the interaction of metalworking fluid and grinding wheel on the grinding wheel properties and preparation result. CIRP J. Manuf. Sci. Technol. 38, 350–371. doi:10.1016/j.cirpj.2022.05.001
Hartung, P. D., Kramer, B. M., and Von Turkovich, B. F. (1982). Tool wear in titanium machining. CIRP Ann. 31, 75–80. doi:10.1016/s0007-8506(07)63272-7
Hu, C., Wang, J., Lin, L., Lin, F., Fu, C., Outeiro, J., et al. (2022). Effects of asymmetric passivation of tool cutting edge on microstructure evolution when cutting Inconel 718 alloy. Procedia CIRP 108, 141–146. doi:10.1016/j.procir.2022.02.196
Hua, J., Shivpuri, R., Cheng, X., Bedekar, V., Matsumoto, Y., Hashimoto, F., et al. (2005). Effect of feed rate, workpiece hardness and cutting edge on subsurface residual stress in the hard turning of bearing steel using chamfer+hone cutting edge geometry. Mater. Sci. Eng. A 394, 238–248. doi:10.1016/j.msea.2004.11.011
Ivanov, Y. F., Rotshtein, V. P., Proskurovsky, D. I., Orlov, P. V., Polestchenko, K. N., et al. (2000). Pulsed electron-beam treatment of WC–TiC–Co hard-alloy cutting tools: Wear resistance and microstructural evolution. Surf. Coatings Technol. 125, 251–256. doi:10.1016/s0257-8972(99)00569-1
Jianxin, D., Yousheng, L., and Wenlong, S. (2008). Diffusion wear in dry cutting of Ti–6Al–4V with WC/Co carbide tools. Wear 265, 1776–1783. doi:10.1016/j.wear.2008.04.024
Kazymyrovych, V., and Kryzhanivskyy, V. (2023). Thermal properties of cemented carbides used for metal cutting. Int. J. Refract. Metals Hard Mater. 111, 106097. doi:10.1016/j.ijrmhm.2022.106097
Kitagawa, T., Kubo, A., and Maekawa, K. (1997). Temperature and wear of cutting tools in high-speed machining of Inconel 718 and Ti6Al6V 2Sn. Wear 202, 142–148. doi:10.1016/s0043-1648(96)07255-9
Konneh, M., Bagum, M. N., Ali, M. Y., and Mohamed Arif, T. F. B. (2018). Tool wear mechanisms during cutting of soda lime glass. IOP Conf. Ser. Mater. Sci. Eng. 290, 012039. doi:10.1088/1757-899x/290/1/012039
Kouadri, S., Necib, K., Atlati, S., Haddag, B., and Nouari, M. (2013). Quantification of the chip segmentation in metal machining: Application to machining the aeronautical aluminium alloy AA2024-T351 with cemented carbide tools WC-Co. Int. J. Mach. Tools Manuf. 64, 102–113. doi:10.1016/j.ijmachtools.2012.08.006
Li, J., Wang, Z. G., Lai, Y. Q., Wu, Y. Y., and Ye, S. L. (2007). Effect of structural parameters on the thermal stress of a NiFe2O4-based cermet inert anode in aluminum electrolysis. Acta Metall. Sin. Engl. Lett. 20, 139–147. doi:10.1016/s1006-7191(07)60018-0
Li, Y. S., Deng, J. X., Zhang, H., and Li, J. F. (2008). Wear mechanism of cemented carbide tool in high speed machining titanium alloy (Ti-6Al-4V). Tribology 28.
Liang, X., Du, P., Li, S., and Zhang, C. (2022). Tribological properties of additive manufactured Ti6Al4V against cemented carbide under dry sliding conditions. Tribol. Int. 167, 107358. doi:10.1016/j.triboint.2021.107358
Liao, Y. S., and Shiue, R. H. (1996). Carbide tool wear mechanism in turning of Inconel 718 superalloy. Wear 193, 16–24. doi:10.1016/0043-1648(95)06644-6
Liu, H., Ayed, Y., Birembaux, H., Rossi, F., and Poulachon, G. (2022). Impacts of flank wear and cooling strategies on evolutions of built-up edges, diffusion wear and cutting forces in Ti6Al4V machining. Tribol. Int. 171, 107537. doi:10.1016/j.triboint.2022.107537
Meindlhumer, M., Jäger, N., Spor, S., Rosenthal, M., Keckes, J. F., Hruby, H., et al. (2020). Nanoscale residual stress and microstructure gradients across the cutting edge area of a TiN coating on WCCo. Scr. Mater. 182, 11–15. doi:10.1016/j.scriptamat.2020.02.031
Nemetz, A. W., Daves, W., Klünsner, T., Praetzas, C., Liu, W., Teppernegg, T., et al. (2020). Experimentally validated calculation of the cutting edge temperature during dry milling of Ti6Al4V. J. Mater. Process. Technol. 278, 116544. doi:10.1016/j.jmatprotec.2019.116544
Padmakumar, M., and Shiva Pradeep, N. (2020). Effect of cutting edge form factor (K-factor) on the performance of a face milling tool. CIRP J. Manuf. Sci. Technol. 31, 305–313. doi:10.1016/j.cirpj.2020.06.004
Qi, H., Qin, S., Cheng, Z., Zou, Y., Cai, D., and Wen, D. (2021). DEM and experimental study on the ultrasonic vibration-assisted abrasive finishing of WC-8Co cemented carbide cutting edge. Powder Technol. 378, 716–723. doi:10.1016/j.powtec.2020.10.043
Shao, F., Liu, Z., Wan, Y., and Shi, Z. (2010). Finite element simulation of machining of Ti-6Al-4V alloy with thermodynamical constitutive equation. Int. J. Adv. Manuf. Technol. 49, 431–439. doi:10.1007/s00170-009-2423-y
Sheikh-Ahmad, J. Y., and Bailey, J. A. (1999). The wear characteristics of some cemented tungsten carbides in machining particleboard. Wear 225-229, 256–266. doi:10.1016/s0043-1648(98)00361-5
Sidiq, P., Abdalrahman, R. M., and Rostam, S. (2020). Optimizing the simultaneous cutting-edge angles, included angle and nose radius for low cutting force in turning polyamide PA66. Results Mater. 7, 100100. doi:10.1016/j.rinma.2020.100100
Uhlmann, E., Eulitz, A., and Dethlefs, A. (2015). Discrete element modelling of drag finishing. Procedia CIRP 31, 369–374. doi:10.1016/j.procir.2015.03.021
Varela, P. I., Rakurty, C. S., and Balaji, A. K. (2014). Surface integrity in hard machining of 300M steel: Effect of cutting-edge geometry on machining induced residual stresses. Procedia CIRP 13, 288–293. doi:10.1016/j.procir.2014.04.049
Ventura, C. E. H., Köhler, J., and Denkena, B. (2015). Influence of cutting edge geometry on tool wear performance in interrupted hard turning. J. Manuf. Process. 19, 129–134. doi:10.1016/j.jmapro.2015.06.010
Wyen, C.-F., Knapp, W., and Wegener, K. (2012). A new method for the characterisation of rounded cutting edges. Int. J. Adv. Manuf. Technol. 59, 899–914. doi:10.1007/s00170-011-3555-4
Yang, Y., Qin, Y., Yang, Y., Wu, M., and Yang, G. (2022). Enhancing the wear resistance of a cemented carbide/titanium alloy under magnetofluid lubrication via the magnetic response. Wear 500-501, 204370. doi:10.1016/j.wear.2022.204370
Yen, Y.-C., Jain, A., and Altan, T. (2004). A finite element analysis of orthogonal machining using different tool edge geometries. J. Mater. Process. Technol. 146, 72–81. doi:10.1016/s0924-0136(03)00846-x
Yin, F., Ma, S., Hu, S., Liu, Y., Hua, L., and Cheng, G. J. (2023). Understanding the microstructure evolution and mechanical behavior of titanium alloy during electrically assisted plastic deformation process. Mater. Sci. Eng. A 869, 144815. doi:10.1016/j.msea.2023.144815
Yussefian, N. Z., and Koshy, P. (2013). Parametric characterization of the geometry of honed cutting edges. Precis. Eng. 37, 746–752. doi:10.1016/j.precisioneng.2013.02.007
Keywords: cutting edge preparation, cutting performance, wear erosion, titanium alloy, surface integrity
Citation: Pan F and Yuan H (2023) State-of-the-art and perspectives of cutting edge preparation and its effect on the cutting performance of titanium alloy. Front. Mater. 10:1184610. doi: 10.3389/fmats.2023.1184610
Received: 12 March 2023; Accepted: 09 May 2023;
Published: 17 May 2023.
Edited by:
Guijian Xiao, Chongqing University, ChinaReviewed by:
Xiuqing Hao, Nanjing University of Aeronautics and Astronautics, ChinaCopyright © 2023 Pan and Yuan. This is an open-access article distributed under the terms of the Creative Commons Attribution License (CC BY). The use, distribution or reproduction in other forums is permitted, provided the original author(s) and the copyright owner(s) are credited and that the original publication in this journal is cited, in accordance with accepted academic practice. No use, distribution or reproduction is permitted which does not comply with these terms.
*Correspondence: Haiyang Yuan, eXVhbmhhaXlhbmcxMTU2QDE2My5jb20=
Disclaimer: All claims expressed in this article are solely those of the authors and do not necessarily represent those of their affiliated organizations, or those of the publisher, the editors and the reviewers. Any product that may be evaluated in this article or claim that may be made by its manufacturer is not guaranteed or endorsed by the publisher.
Research integrity at Frontiers
Learn more about the work of our research integrity team to safeguard the quality of each article we publish.