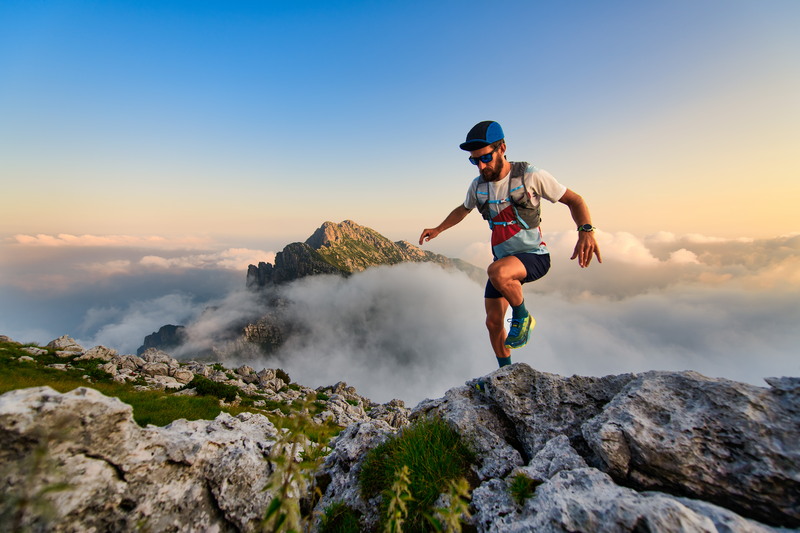
95% of researchers rate our articles as excellent or good
Learn more about the work of our research integrity team to safeguard the quality of each article we publish.
Find out more
ORIGINAL RESEARCH article
Front. Mater. , 26 April 2023
Sec. Polymeric and Composite Materials
Volume 10 - 2023 | https://doi.org/10.3389/fmats.2023.1170202
Basalt fibers play an indispensable role in aerospace as well as fireproof suits in specialty fields. However, basalt fibers usually have properties such as high temperature and corrosion resistance, severely lack comfort, and are prone to brittle fracture or splitting when subjected to bending or impact forces because of their high modulus. Although considerable efforts have been made to solve the above problems by wrapping soft staple fibers with basalt, but the problem of difficult stress balance exists in the composite process. Herein, we demonstrate that a stress balance spinning method to control the composite conformation between high stiffness basalt fibers and soft cotton fibers, possess significant modulus differences, for high spinnability and comfort composite yarns production on ring spinning. Geometric analysis demonstrated that the stress during retwisting adjusts the internal structure of the basalt fiber and changes the arrangement of exposed cotton fiber bundles, causing the fiber motion track to change from concentric helix to deformed non-concentric helix. The mechanical aspects show that over-twisted composite yarns lead to fiber exposure as well as detachment due to irregular fiber twisting, while low-twisted composite yarns can overcome residual torque and modulus differences. Afterwards, a systematic comparison of composite yarns with different parameters reveals that low-twisted composite yarns have a better helicoid structure, strength and uniformity than raw and over-twisted composite yarns.
Basalt fiber filaments, especially those with high modulus, high strength, and high temperature resistance are characterized by high stiffness; the properties usually used in aerospace; nevertheless, basalt fibers have a prickly sensation owing to their high rigidity and are prone to splitting under twisting (Chen et al., 2017; Pastsuk et al., 2020). Organic staple fibers, such as cotton, tencel, and viscose, normally have a low modulus as well as high spinnability and comfort (Karthik et al., 2017; Goergen et al., 2020). Generally, spinning composite technology has been used to compensate for the disadvantages of staple fibers and basalt fiber together. Unfortunately, problems of large modulus differences between staple fibers and basalt fiber exist, with high-modulus basalt fiber filaments breaking easily under high twist conditions (Kim et al., 2009; Li et al., 2018), while low-modulus staple fibers not cohesive yarns well in untwisted conditions (Qian et al., 2021; Dalfi et al., 2022).
Research has shown that the twist factor plays a dominant role in the residual torque of the yarn (Xu and Tao, 2008; Hua et al., 2010; Sarıoğlu et al., 2018). Low twist factor could eliminate yarn with low residual torque (Guo et al., 2011). However, the resulting low-twisted yarns have a loose structure and severe relative slippage between filament and staple fibers, which leads to uneven yarn stem and low breaking strength, making it difficult for the composite yarn quality to meet the process requirements (Anike et al., 2019). Fortunately, with the combination of staple fibers with higher modulus differences and basalt fibers, the residual torque of the yarn will be better released; then yarn formation performance will be better if localized twist control has been used.
Further studies found that both finishing and spinning techniques could reduce residual torque (Tao et al., 1997; Liu et al., 2019; Yin et al., 2020). Massive researches have found that the finishing technique of yarn steaming was an effective way to reduce the residual torque of the yarn. By reason of under the humid and hot conditions, not only yarn has better elongation, increased strength and soft handfeel, but also the phenomenon of residual torque become well improved (Boubaker et al., 2017). However, the steaming process makes it difficult to get the yarn steamed evenly, resulting in the non-functioning of the backend process. With the high conditions required and the huge energy consumption, the steaming process become hardly used in cotton yarn production. In addition, steaming as a finishing technique has difficulty in eliminating the torque caused by high modulus basalt fibers, so addressing the torque problem through spinning technology becomes necessary.
Nu-torque spinning technology, state-of-the-art spinning technology, has been widely used throughout the country. On the one hand, it was not solely reducing yarn hairiness and residual torque, but improved yarn strength and achieved low twist and high strength (Guo and Tao, 2018; Chu et al., 2021). On the other hand, fiber splitting phenomenon was clearly observed in the spinning triangle during the spinning process. As a result, each fiber forms a spatial helix, which the outer fibers having large centripetal curvature and the middle ones having a small curvature. Thus, outer fibers hold the inner fibers tightly, which helps to change the position of the fibers within the yarn and enhance the fiber cohesion between them. However, torsional spinning has not reduced torque enough to eliminate residual torque in high rigidity basalt fibers. A deeper investigation into the methods which enable the elimination of residual torque at the spinning stage will be required.
In order to solve the problem of severe twist shrinkage in ring spinning composite yarns of basalt fibers and staple fibers with high modulus differences, this study introduces a new method to improve the structure of yarn formation by stress balance to reduce the residual torque of the yarn and obtain low-torque composite yarns. The present work is different from previous studies, which focuses on achieving twist balance between a high modulus filament and a bundle of low modulus staple fibers. In particular, the mechanism of fiber movement during yarn formation was analyzed to predict the effect of stress balance on yarn structure and properties. Eventually, the structure and properties of all the composite yarns are comparatively investigated in detail.
In the conventional ring spinning process, the traveler spin in the yarn under the action of directional horizontal rotation, which transfers to the twisting triangle overhead. The staple fiber slivers and filaments with parallel arrangement (Figure 1A) output by the front nip line make a twisting rotary motion in a concentric helix track under the action of twist, forming a concentric helix structure (the axis of the yarn is aligned with the axis of the fiber helix) yarn (Figure 1B).
FIGURE 1. Geometrical illustration of fiber motion trace: (A) staple fiber and filament strands; (B) composite yarn twisted by the same direction and (C) composite yarn twisted by alternate direction.
The spatial structure of a yarn consists of single fiber trajectories on its surface, where the fiber tracks are influenced by variations in the morphology of the twisting triangle. According to the degree of regularity of the twisting triangle morphology, the fiber arrangement in the yarn could be classified as concentric cylindrical or concentric conical (Xia and Xu, 2013). In addition, the change of the twisting triangle morphology depends on the change of the twist factor, so the internal structure of the yarn would be adjusted by changing the twist factor parameter (Xu et al., 2021). Figure 2A shows the appearance model of original composite yarn. As the twist factor increases, the helix angle generated by the fiber movement becomes larger (Figures 2B–E).
FIGURE 2. Appearance model comparison of yarns spun by different twists: (A) original composite yarn; (B, C) against-twisted composite yarn produced by pre-twisting of filament with reverse low and high Z-twists and (D, E) against-twisted composite yarn produced by pre-twisting of staple fiber and filament composite with reverse low and high Z-twists.
In the experimental group of applying forward twist to the filament and against-twisting to the composite yarn with staple fibers, the filament was located in the axial part of the yarn, and the staple fibers were wrapped around the filament in an S-directional concentric cylindrical distribution; meanwhile, the filament would hold one end of the staple fibers in the process of releasing the residual torque, which had a good fixation effect on the yarn structure (Figures 2B, C). In addition, in the experimental group of applying positive twist to staple fibers and filaments at the same time and applying against-twisting to the composite yarn, the staple fibers and filaments always maintain the same helical motion in the same direction, with the difference that the staple fibers are not only affected by the helical distribution motion caused by the rotation of the traveler, but by the twisting torque of the filaments, resulting in the inconsistent degree of twisting of the staple fibers and filaments, and their spatial arrangement structure changes, showing an irregular deformed non-concentric helix alternating structure (Figure 1C). Unfortunately, the extent of twisting will largely change the appearance of the yarn due to the plasticity of the high stiffness inorganic fibers under strong twisting conditions, resulting in a wavy yarn with loose outer staple fibers and exposed inner filaments (Figures 2D, E).
The stress distribution of the twisting triangle plays an important role in affecting the fiber twisting torque (Li et al., 2011). By setting different twist factors the track of the staple fibers and filaments in the yarn could be changed to provide different torsional stresses to the yarn and thus adjust the residual torque of the yarn to a certain extent.
By changing the direction from the spiral motion of the fibers, which generates a force opposite to the original fiber driving direction, the torsional stress between the staple fibers and the filaments will be balanced and the residual torque of the yarn may be released. In addition, since the binding force of the gradually loosened external staple fibers on the internal filaments gradually decreases during the yarn untwisting process, the relative slip of the staple fibers and the filaments under the effect of the de-twisting torque affects the fiber cohesion. Moreover, with the increase of against-twisting, the fiber arrangement tends to be parallel, so that the yarn breaking strength mostly bears by the high modulus inorganic filament, which reduces the tensile properties of the yarn to a certain extent; meanwhile, the residual torque of the yarn obtains greater release, and the twist shrinkage of the composite yarn effectively improves.
The composite yarn analyzed in this study is a combination of basalt filaments and cotton fibers (Figures 3A, B). In order to explain and clarify the aforementioned theory, as shown in Figure 3C, firstly, the experiments were conducted on Dssp-01A ring-spinning frame (produced by Tianjin Jiacheng Electromechanical Equipment Co., Ltd). 11 tex basalt filament (produced by Huierjie New Material Technology Co., Ltd) and 750 tex cotton fiber (provided by Dongguan Texwinca Textile Co., Ltd) are selected, which was applied to manufacture original ring-spun yarn. The quantitative process parameters were introduced in detail, theoretical spindle speed was 5,500 r/min, the base yarn draft ratio was 25.8, exit speed was 12.68 m/min, forming angle was 9.0 degrees, bar spacer was 3.0 mm, ring type was PG1/2 3854, and traveler type was 6903 4/0.
FIGURE 3. Raw materials utilized for the experiments and actual spinning process: (A) basalt filament; (B) cotton fiber and (C) an optic image of ring spinning frame to produce composite yarns.
In this experiment, the staple fiber sliver is drawn and merged with the filament at the front nip line. Notably, both the filament and the composite yarn do not need to pass through the drawing machine, but are output directly from the front nip line after passing through the tension disc and the guide wheel (Figure 4). In addition, five kinds of yarns (Af, Ag, Ah, Aj, Ak) were set up in this experiment (Table 1), where the variable process parameters included twisting sequence, twist direction and twist degree.
FIGURE 4. Pictorial illustration of production process on yarns for experiment: (A) Af; (B) Ag and Ah and (C) Aj and Ak.
All the samples have occasion to be stored under specific conditions (temperature t = 20°C, relative humidity RH = 65%, standard atmospheric pressure) for at least 24 h. Images of the yarn structure were observed by RH-2000 automatic electron optical microscope. The resistance modulus difference was visually responded by the twist-back condition. 1 m of each sample was randomly intercepted and placed in the middle section of the yarn using a 15 g weight, the yarn was grasped both ends and merged from outside to inside, observe the twist-back condition of the twisted composite yarns in the case of free sagging and repeated for five sets.
The hairiness test was performed at 30 m/min for each sample using the H400 hairiness meter and the average results were obtained from 3 tests. Use YG068C single yarn tensile tester to test yarn tenacity at 500 mm specification length and 500 mm/min speed, calculate 10 consecutive measurements as the average values. Yarn irregularity and defects were evaluated using E500 capacitive evenness tester at CN GB/T 3292.1-2008 with a test speed of 400 m/min for each sample and a test length of 400 m in 10 tests. The modulus was tested at 20 mm/min using an instron 5,943 material testing machine and the average value was calculated from 5 sets of data.
Figure 5 indicates the modulus value of cotton fiber, basalt filament and the composite yarn of both, and it is evident that there exists a large difference in modulus between basalt and cotton fibers.
The microstructure indicates the hairiness and cohesion of the yarn. The Figure 6 clearly reveals that hairiness of Ah yarn is better than the other groups and has the tightest fiber cohesion. Noteworthy, the angle between the helix of Ah yarn and the yarn axis is only less than the original yarn. In addition, Figure 6F presents the cross-section morphology of low-torque composite yarn, which clearly reveal the fiber distribution.
FIGURE 6. Appearance comparison of yarns spun by different twists: (A) Af; (B) Ag; (C) Ah; (D) Aj; (E) Ak and (F) an optical micrograph of cross-section morphology of low-torque composite yarn.
On the surface of the yarn after back-twisted, almost most of the basalt was exposed as well as the fiber cohesion of the yarn was severely reduced. Pleasantly, the back-twisted effect kept excellent. That was mainly due to the fact that the yarn structure became loose during the against-twisting and the residual torque was gradually released. As can be seen from Figure 6 that yarn geometries all showed different morphologies, probably owing to the deformed non-concentric helix.
In contrast to the original yarn (Af 40°), the angles between the helix tracks and the yarn axis are shown in Figure 6 (Ag 22°, Ah 26°, Aj 17°, Ak 21°). Reasons for the irregularity of the angles are mainly attributed to the decrease of the interaction force between cotton fibers and basalt due to the relaxation of the yarn during the de-twisting.
The snarlings of the yarn is one of the important parameters to assess whether the composite yarn overcomes the modulus difference (Belov et al., 2002). The twisting of the yarn can be clearly seen in Figure 7.
Obviously, the original yarn was mostly in a low-twisted or even untwist situation compared to the yarn that had undergone second twist. Notably, Ag and Aj also differ compared to Ah and Ak. The low-twisted composite yarns showed almost no torque phenomenon, while a small amount of torque was present in the over-twisted composite yarns. This could be caused by the weakened friction between the fibers and the against-twist remodeling of the fiber arrangement, which leads to the twist redistribution and the resulting yarn torque regulation.
On the contrary, the low-twisted composite yarns also have a lower twist in its internal structure, which balances the internal forces of the yarn very well. The results illustrate that the yarn after second twist can overcome the problem of high and low modulus difference effectively, as can be visualized in Figure 7.
Table 2 shows that Ah yarn has the least amount of hairiness compared to other yarns due to the filament plays a positive role in clamping the staple fibers during the over-twisted process. Some residual torque still exists in the basalt filament, and the staple fiber ends are tightly wrapped inside the yarn body under the filament torsional stress, making the staple fiber ends embedded in the yarn backbone, thus greatly reducing the number of hairiness.
Analyzing the hairiness of the two groups of yarns (Af, Ag, Ah vs. Af, Aj, Ak), the number of hairiness can be clearly seen to demonstrate a trend of first increasing and then decreasing. It indicates that the yarn structure becomes loose during the reverse low-twisted process, and the staple fibers gradually got rid of ties with the filaments, then detached from the yarn backbone to form more and longer hairiness. Remarkable, during the process of applying reverse high twist, the fibers are arranged from S twist, which tends to be distributed in parallel, to Z twist due to the excessive Z-twisting effect, and the frequency of internal and external transfer of staple fibers is accelerated, which improves the quality of yarn hairiness.
The evenness of the stem reveals the degree of irregularity in thickness or weight of the yarn in shorter sections along the axial direction (Elmogahzy, 2019). Table 3 shows that the Af yarn has the worst stem evenness compared to the other yarns, which may be caused by the fact that the filaments do not have a good binding effect on the staple in the roving whiskers during the single twist process, causing the staple to accumulate in the twist triangle and form thick knots and neps.
Unfortunately, the over-twisted composite yarns have worse CVm values than the low-twisted composite yarns (Ah 8.3 > Ag 8.23; Ak 9.44 > Aj 8.84), since the fiber sliver oscillate slightly from side to side during the drafting process. Therefore, the increase of the twist factor is accompanied by an improvement of the drafting force of the front roller on the fiber sliver, which leads to a more irregular drafting effect on the sliver, thus making the yarn uneven. Unevenness of the yarn is increased.
At the same time, against-twisting of basalt filament yarn with cotton fiber double strand and basalt monofilament respectively, the former has worse CVm values compared to the latter (Aj 8.84 > Ag 8.23; Ak 9.44 > Ah 8.3), because cotton fiber of the former has gone through one more drafting and twisting process than cotton fiber of the latter, and as mentioned above, over-drafting adds some additional unevenness. Besides, the irregular second twist causes the loss of short fibers, increases the possibility of producing details and deteriorates the uniformity of the yarn stem.
In addition, the evenness of the stripes of the five composite yarns can be clearly seen in Figure 6. Af yarn has obvious thick and thin unevenness; Ag and Ah have a uniform appearance; Aj and Ak show an unstable wavy structure, and there are differences in the helix angle of both.
Table 4 shows the tensile properties of the original yarn and the composite yarn with different twist levels. As can be seen from the table, the strength of the original yarn to be almost not as strong as the yarn with second twist, which might be due to the fact that the basalt yarn is too rigid but breaks easily with only one twist. Surprisingly, in groups 2-5, the strength of the not over-twisted composite yarn was greater than the over-twisted one (Ag 669 cN > Ah 556 cN; Aj 667 cN > Ak 511 cN).
Another critical factor was the greater relative slip between cotton fibers and basalt during the process of retwisting and the loosening of the composite yarn, even if the cotton fibers were more exposed in the process of reverse-twisting, leading to a decrease in fiber utilization. The lower elongation of the over-twisted yarns was mainly due to the adjustment of the overall fiber arrangement reducing the space for relative fiber slippage.
The breaking strength of Ak yarn is the lowest at 521 cN. During the process of against-twisting, the friction of the yarn gradually decreases leading to a decrease in the fiber cohesion, which is one of the main reasons for reducing the breaking strength of the yarn. Aj has the highest breaking strength at 677 cN. From the above, it is clear that basalt fibers have high modulus, high rigidity and are susceptible to breakage at higher twist levels, but releasing their residual torque to low twist or relatively no twist, basalt fibers have high tenacity and strength.
In addition, comparing the friction resistance of Ag yarn with the highest average breaking strength and the lowest residual torque with that of pure basalt filament (Figure 8), it was found that the composite yarn contains cotton staple fibers has better friction resistance owing to the fact that the tightly distributed staple fibers have a large cohesive enough on each other to take up part of the frictional force, making the basalt fibers less likely to be fully exposed and thus not subject to a greater degree of abrasion.
FIGURE 8. Friction performances comparison between pure basalt filament and low-torque composite yarn: (A) apparent structure of basalt filament and low-torque composite yarn before friction ang (B) apparent structure of basalt filament and low-torque composite yarn after friction.
In this study, a composite spinning method to overcome the problem in ring spinning of difficult yarn formation of high and low modulus difference fibers was introduced, revealing that the layout of fibers could be rearranged by twice twisting to obtain a deformed non-concentric helix structure. At the same time, the residual torque inside the composite yarn to achieve the composite of high and low modulus difference fibers can be eliminated by means of stress balancing. In addition, experiments were created to compare the difference in characterization properties between single twisted composite yarn and second twisted composite yarns at different parameters.
According to the results of the study, the internal structure within the yarn using stress balance method can be adjusted, thus releasing the residual torque of the composite yarn. However, relative slippage between the staple fibers and the filaments occurs, leaving the filaments exposed. The characterization properties of the yarn are influenced by the amount of twist applied in the reverse direction. A low twist in the reverse direction distributes the stresses between the fibers more rationally, hence bringing the stresses within the yarn into equilibrium. In addition, against-twisting of single filament yarns is more beneficial in releasing the residual torque of high modulus filaments due to the absence of the binding effect of staple fibers.
The original contributions presented in the study are included in the article/Supplementary Material, further inquiries can be directed to the corresponding authors.
WL and ZP contributed equally to this article. WL, ZP, DX, KL, and WX contributed to conception and design of the study. RZ, JL, and XW conceived the theoretical analysis. YS performed the statistical analysis. WL and ZP wrote the first draft of the manuscript. All authors contributed to manuscript revision, read, and approved the submitted version.
The study was financially supported from the National Natural Science Foundation of China (No. U21A2095, 52203373), the Postgraduate Research & Practice Innovation Program of Jiangsu Province (No. KYCX22_3203), and the Key Research and Development Program of Hubei Province (No. 2021BAA068).
We acknowledge the State Key Laboratory of New Textile Materials and Advanced Processing Technologies.
The authors declare that the research was conducted in the absence of any commercial or financial relationships that could be construed as a potential conflict of interest.
All claims expressed in this article are solely those of the authors and do not necessarily represent those of their affiliated organizations, or those of the publisher, the editors and the reviewers. Any product that may be evaluated in this article, or claim that may be made by its manufacturer, is not guaranteed or endorsed by the publisher.
Anike, J. C., Belay, K., and Abot, J. L. (2019). Effect of twist on the electromechanical properties of carbon nanotube yarns. Carbon 142, 491–503. doi:10.1016/j.carbon.2018.10.067
Belov, E. B., Lomov, S. V., Truevtsev, N. N., Bradshaw, M. S., and Harwood, R. J. (2002). Study of yarn snarling part I: Critical parameters of snarling. J. Text. Inst. 93 (4), 341–365. doi:10.1080/00405000.2002.12027744
Boubaker, J., Mouna, G., and Sahnoun, M. (2017). Metaheuristic techniques to optimize the steaming process of elastic denim yarns. J. Nat. Fibers 14 (6), 814–822. doi:10.1080/15440478.2017.1279105
Chen, X., Zhang, Y., Huo, H., and Wu, Z. (2017). Improving the tensile strength of continuous basalt fiber by mixing basalts. Fibers Polym. 18 (9), 1796–1803. doi:10.1007/s12221-017-6804-9
Chu, P. Y., Choi, K. F., Chuang, Y. C., and Kan, C. W. (2021). Comparison of performance of fabrics made of torque-free and conventional ring spun yarn with different varieties of cotton fibres. Fibers Polym. 22 (7), 2036–2043. doi:10.1007/s12221-021-1024-8
Dalfi, H. K., Tausif, M., and Yousaf, Z. (2022). Effect of twist level on the mechanical performance of S-glass yarns and non-crimp cross-ply composites. J. Ind. Text. 51, 2921S–2943S. doi:10.1177/1528083720987206
Elmogahzy, Y. (2019). Structure and mechanics of yarns. Structure and mechanics of textile fibre assemblies. Sawston, Cambridge: Woodhead Publ, 1–25.
Goergen, C., Schommer, D., Duhovic, M., and Mitschang, P. (2020). Deep drawing of organic sheets made of hybrid recycled carbon and thermoplastic polyamide 6 staple fiber yarns. J. Thermoplast. Compos. Mat. 33 (6), 754–778. doi:10.1177/0892705718811407
Guo, Y., and Tao, X. (2018). Fiber packing density in the cross-section of low torque ring spun yarn. Text. Res. J. 88 (2), 191–202. doi:10.1177/0040517516677225
Guo, Y., Tao, X. M., Xu, B. G., Feng, J., and Wang, S. Y. (2011). Structural characteristics of low torque and ring spun yarns. Text. Res. J. 81 (8), 778–790. doi:10.1177/0040517510387213
Hua, T., Tao, X. M., Cheng, K. P. S., and Xu, B. G. (2010). Effects of geometry of ring spinning triangle on yarn torque: Part II: Distribution of fiber tension within a yarn and its effects on yarn residual torque. Text. Res. J. 80 (2), 116–123. doi:10.1177/0040517509102732
Karthik, T., Murugan, R., and Sakthivel, J. C. (2017). Comfort properties and dyeing behaviour of cotton/milkweed blended rotor yarn fabrics. Indian J. Fibre Text. Res. 42 (1), 25–30.
Kim, H. J., Yang, H. W., Zhu, C. Y., and Huh, Y. (2009). Influence of the core-sheath weight ratio and twist on the tensile strength of the ring core yarns with high tenacity filaments. Fibers Polym. 10 (4), 546–550. doi:10.1007/s12221-009-0546-2
Li, S. Y., Xu, B. G., Tao, X. M., and Feng, J. (2011). Numerical analysis of the mechanical behavior of a ring-spinning triangle using the Finite Element Method. Text. Res. J. 81 (9), 959–971. doi:10.1177/0040517510395998
Li, W. W., Kang, H. L., Xu, J., and Liu, R. G. (2018). Microstructures of high-strength high-modulus carbon fibers and high-modulus carbon fibers. Acta Polym. Sin. 49, 380–388.
Liu, S., Pan, X., Zheng, D., Du, Z., Liu, G., and Yang, S. (2019). Study on the structure formation and heat treatment of helical auxetic complex yarn. Text. Res. J. 89 (6), 1003–1012. doi:10.1177/0040517518760754
Pastsuk, V., Kiisk, M., Lõhmus, R., Merisalu, M., Kovaljov, S., Biland, A., et al. (2020). Selection of basalt fiber with resistance to concrete alkaline environment. SN Appl. Sci. 2 (11), 1842–1917. doi:10.1007/s42452-020-03677-z
Qian, W., Zhu, J., Chen, F., Ji, X., Wang, X., and Wang, L. (2021). Water footprint assessment of viscose staple fiber garments. Water Supply 21 (5), 2217–2232. doi:10.2166/ws.2021.040
Sarıoğlu, E., Babaarslan, O., and Avcı, M. E. (2018). Effect of filament fineness on composite yarn residual torque. Autex Res. J. 18 (1), 7–12. doi:10.1515/aut-2016-0036
Tao, X. M., Lo, W. K., and Lau, Y. M. (1997). Torque-balanced singles knitting yarns spun by unconventional systems: Part I: Cotton rotor spun yarn. Text. Res. J. 67 (10), 739–746. doi:10.1177/004051759706701006
Xia, Z. G., and Xu, W. L. (2013). A review of ring staple yarn spinning method development and its trend prediction. J. Nat. Fibers 10 (1), 62–81. doi:10.1080/15440478.2012.763218
Xu, B. G., and Tao, X. M. (2008). Techniques for torque modification of singles ring spun yarns. Text. Res. J. 78 (10), 869–879. doi:10.1177/0040517507087684
Xu, D., Fan, H., Li, J., Gao, C., Yang, W. W., Xu, W. L., et al. (2021). A novel concept to produce super soft characteristic ring-yarn with structural variation via against-twisting. J. Nat. Fibers., 1–13. doi:10.1080/15440478.2021.1881020
Keywords: modulus difference, residual torque, yarn structure, ring spinning, stress balance
Citation: Li W, Peng Z, Zhang R, Wang X, Li J, Sun Y, Xu W, Xu D and Liu K (2023) A spinning method for low-torsion composite yarn with basalt fibers and staple cotton fibers. Front. Mater. 10:1170202. doi: 10.3389/fmats.2023.1170202
Received: 20 February 2023; Accepted: 17 April 2023;
Published: 26 April 2023.
Edited by:
Wanjie Xie, Ghent University, BelgiumReviewed by:
Pibo Ma, Jiangnan University, ChinaCopyright © 2023 Li, Peng, Zhang, Wang, Li, Sun, Xu, Xu and Liu. This is an open-access article distributed under the terms of the Creative Commons Attribution License (CC BY). The use, distribution or reproduction in other forums is permitted, provided the original author(s) and the copyright owner(s) are credited and that the original publication in this journal is cited, in accordance with accepted academic practice. No use, distribution or reproduction is permitted which does not comply with these terms.
*Correspondence: Duo Xu, eHVkdW9fOTZAMTYzLmNvbQ==; Keshuai Liu, MjAxODAxOUB3dHUuZWR1LmNu
†These authors have contributed equally to this work
Disclaimer: All claims expressed in this article are solely those of the authors and do not necessarily represent those of their affiliated organizations, or those of the publisher, the editors and the reviewers. Any product that may be evaluated in this article or claim that may be made by its manufacturer is not guaranteed or endorsed by the publisher.
Research integrity at Frontiers
Learn more about the work of our research integrity team to safeguard the quality of each article we publish.