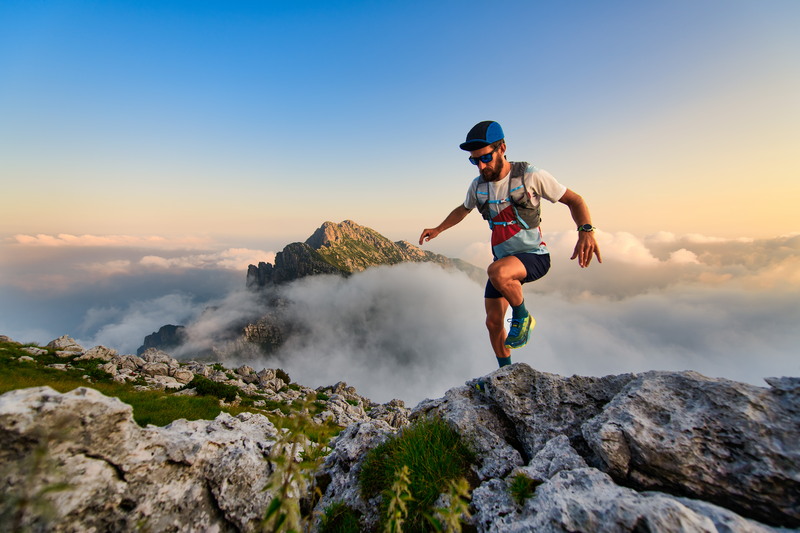
95% of researchers rate our articles as excellent or good
Learn more about the work of our research integrity team to safeguard the quality of each article we publish.
Find out more
ORIGINAL RESEARCH article
Front. Mater. , 23 March 2023
Sec. Polymeric and Composite Materials
Volume 10 - 2023 | https://doi.org/10.3389/fmats.2023.1166986
This article is part of the Research Topic ECCM Research Topic on Advanced Manufacturing of Composites View all 14 articles
Nanocomposite film heaters are promising for out-of-oven (OoO) and energy-efficient curing of fiber-reinforced polymer composites. However, the current techniques for manufacturing nanocomposite film heaters are intensive in terms of time and energy and require expensive resources. In this work, we present a facile and rapid approach for preparation of nanocomposite film heaters with excellent heat generation properties based on a frontally polymerizable resin system. This approach enables rapid fabrication of nanocomposite films within a few minutes and without the need for using expensive equipment, making it suitable for mass production of nanocomposite film heaters. Various characterization techniques are used to determine the morphology, composition, and mechanical properties of nanocomposite films. The electrothermal performance of nanocomposite film heaters are then evaluated under various conditions. Nanostructured heaters exhibit excellent Joule heating properties, where temperatures as high as ∼132°C can be reached within only 2 min using a low input power density of ∼2 W cm−2. Finally, a nanocomposite film heater is used for OoO curing of a small composite panel with minimal energy consumption. Using this approach, 0.1 MJ of energy is consumed during the 4-h cure cycle of a commercial prepreg system, which would otherwise require at least 40.5 MJ of energy to cure using a convection oven.
Fiber-reinforced polymer composites (FRPCs) exhibit excellent specific mechanical properties, chemical stability, and fatigue resistance, making them an ideal material for designing lightweight and durable structures in a variety of industries including aerospace, wind energy, defense, construction, and marine (Zhang et al., 2021; Chen et al., 2023). However, the widespread use of FRPCs in various applications is limited by their underlying challenging manufacturing processes. The traditional technology for manufacture of polymer composites involves elevated-temperature curing of the matrix thermoset resin for several hours (up to 24 h) in an autoclave or oven (Schlimbach and Ogale, 2012; Lee et al., 2018). This process is highly intensive in terms of time, energy, carbon footprint, and resources. In addition, the production rate and size of components are limited by the internal dimensions and availability of ovens and autoclaves.
Composite layups are typically heated in an autoclave or oven via convection, which is highly inefficient in terms of energy consumption, as a significant amount of energy is required to heat up a large volume of gas inside the equipment (Liu et al., 2020). Developing alternative heating methods that enable fast and efficient heating of a composite layup has been the focus of extensive research over the past decade. One of the alternative heating approaches is using electromagnetic waves (e.g., infrared, microwave, and ultraviolet) for supplying the energy required for composite curing. Although each of these radiation curing methods offers distinct advantages, they are challenging to use at an industrial scale due to their specific limitations. For example, the high cost of microwave ovens, use of special tooling materials, and microwave shielding effect of carbon fibers are key issues that limit the widespread adoption of microwave heating technique for composite processing (Nuhiji et al., 2019; Galos, 2021). Direct conductive heating is a promising heating method, which can substantially reduce the energy demand of curing process while eliminating the need for expensive autoclaves or ovens (Yue et al., 2022). In this curing approach, heat is directly supplied to the composite layup via conduction, either from a heated mold or direct resistive heating of a conductive material (Tu et al., 2022). The latter approach is advantageous as the acquisition and maintenance of heated tools are costly. In direct resistive heating approach, the heat required for curing of the matrix thermoset resin is supplied by passing electric current through a conductor, in which the electric energy is converted into heat via Joule’s effect (Silva et al., 2017; Moreira et al., 2021). A wide range of conductive materials including carbon fiber, metal meshes, and nanocomposite films have been used as a resistive element for direct heating of composite layups (Yao et al., 2019; Chen et al., 2020; Karalis et al., 2021). Nanocomposite films in particular show a great promise for curing polymer composites in part because of their excellent electrothermal conversion efficiency, low thermal mass, and deformability (Bobinger et al., 2019; Xu et al., 2021). Additionally, nanocomposite films can be integrated into a composite layup and remain advantageous in service conditions by imparting new functionalities (e.g., de-icing, damage sensing) to the host composite structure (Tarfaoui et al., 2019; Groo et al., 2020; Naseri et al., 2022).
Adoption of direct conductive curing technique using nanocomposite film heaters requires developing new approaches for scalable, rapid, and inexpensive preparation of nanocomposite films with excellent electrothermal properties. There are two main approaches for preparation of nanocomposite film heaters. In the more traditional approach, conductive nanoparticles (e.g., carbon nanotubes, graphene) are added to the polymer matrix of composites via solvent-based or direct mechanical mixing techniques to enhance the electrical conductivity of the matrix polymer for heat generation via Joule’s effect. While these approaches are useful for bulk preparation of polymer nanocomposites, they suffer from the challenging processing steps, safety hazards, and limited amount of nanoparticles that can be added to polymers (Chakraborty et al., 2011; Wan Dalina et al., 2019). For example, in preparation of carbon nanotube-modified polymers, often less than 1 wt.% of nanotubes can be added to polymers, as increasing the nanotube content substantially increases the resin viscosity and makes the processing conditions quite challenging (Ma et al., 2010). Additionally, it is extremely difficult to evenly disperse all nanotubes, resulting in agglomeration of nanoparticles in the polymer matrix and degradation of the mechanical properties of produced nanocomposites compared to the pristine polymer (Isaza M et al., 2018; Zeinedini et al., 2018; Xia et al., 2020). An alternative approach for preparation of polymer nanocomposite heaters with a high content of nanoparticles is creation of papers of nanoparticles followed by impregnation of the produced nanostructured papers by the polymer resin (Khan et al., 2015). Buckypaper, which is a macroscopic assembly of carbon nanotubes, is one of such papers that has been produced at large scales and allows for creating polymer nanocomposites with a high concentration of nanoparticles (up to 30 vol.%) while enabling easier and safer handling of nanoparticles compared to bulk processing methods (Lopes et al., 2010). The high concentration of nanotubes in buckypaper results in a high electrical conductivity in produced nanocomposites, which is crucial for obtaining the desired electrothermal performance via Joule heating effect; therefore, produced heaters deliver superior electrothermal properties compared to nanocomposite heaters produced using bulk mixing approaches. The preparation process of nanocomposite films typically involves infiltration of the nanoparticle network with a thermosetting resin (e.g., epoxy) under vacuum and often at elevated temperatures to reduce the resin viscosity and facilitate the impregnation of the highly dense, porous network of nanotubes (Ribeiro et al., 2017). Following the infiltration step, the material is cured in an oven according to the cure cycle of the thermosetting resin, which can typically take several hours to obtain a fully crosslinked polymer network. These processing steps make the manufacturing process of nanocomposite heaters slow and arduous.
Recently, frontal polymerization (FP) has emerged as an energy-efficient and rapid approach for curing of thermoset resins and their composites (Robertson et al., 2018; Pojman, 2022; Suslick et al., 2022; Ziaee et al., 2022). In FP, a monomer solution containing a latent catalyst is heated locally to activate the latent catalyst and initiate an exothermic polymerization reaction. The released heat is used to activate more catalyst and polymerize more resin. As a result, a self-propagating reaction wave is formed that propagates through the monomer solution until all available monomers are converted to polymer (Pojman, 2012; Ziaee and Yourdkhani, 2021; Naseri and Yourdkhani, 2022). FP has been demonstrated for a wide range of resin systems including cyclic olefins, epoxies, and acrylates (Mariani et al., 2008; Klikovits et al., 2017; Dean et al., 2020). Dicyclopentadiene (DCPD), a member of the cyclic olefin family, is one of the FP resin systems, which is of great interest due to its excellent front properties, long and tunable pot life, very low viscosity of ∼1.5 × 10−3 Pa s, and excellent thermo-mechanical properties of resulting polydicyclopentadiene (pDCPD) polymer (Ruiu et al., 2014; Robertson et al., 2017; Centellas et al., 2022).
The aim of this study is to introduce a facile approach for rapid and energy-efficient fabrication of thermoset-based nanocomposite film heaters at room temperature without using any vacuum conditions or ovens. To achieve this goal, we use a low-viscosity resin (η ∼1.5 × 10−3 Pa s) based on dicyclopentadiene (DCPD) that can readily impregnate buckypaper networks at room temperature and ambient pressure. Following the rapid impregnation, the DCPD-based resin is cured via through-thickness frontal polymerization. In this work, we first evaluate the quality of the produced nanocomposite films by characterizing their composition, morphology, and mechanical properties using various techniques including scanning electron microscopy, thermogravimetric analysis, and tensile testing. Then, electrodes are connected to the opposite sides of the nanocomposite films to create film heaters and determine the electrothermal performance of resulting heaters in response to various static and dynamic electrical loading conditions. Upon characterization of the electrothermal performance of film heaters, they are used to demonstrate direct conductive heating and curing of a composite panel using a commercial prepreg system.
Dicyclopentadiene (DCPD), 5-ethylidene-2-norbornene (ENB), second-generation Grubbs’ catalyst (GC2), and phenylcyclohexane (PCH) were purchased from Sigma Aldrich. DCPD is solid at room temperature; therefore a 95:5 wt.% solution of DCPD:ENB was prepared to depress the melting point of the resin solution. The DCPD/ENB solution will be referred to as DCPD resin hereafter in this article. Tributyl phosphite (TBP) was obtained from TCI America. PCH is used to facilitate the dissolution of the GC2 catalyst in the resin solution, whereas TPB is used as an inhibitor to control the reactivity and pot life of the resin system. In a typical experiment, 3.21 mg of GC2 was measured and dissolved in 1 mL of PCH. An appropriate amount of TBP (1 M equivalent with respect to GC2) was added to the GC2/PCH solution via a volumetric syringe. This solution was then added to 5 mL of DCPD and thoroughly mixed. Buckypaper with an average thickness of 60 μm was prepared in-house using multiwalled carbon nanotubes (Nanocyl NC7000) and based on the vacuum filtration technique following the procedure described in our previous work (Ashrafi et al., 2017). A silver-filled conductive paste (ConductiveX) was used for attaching copper electrodes to buckypaper films. A unidirectional carbon fiber prepreg (AX-6201XL, Axiom) was used for fabrication of composite panels.
Differential scanning calorimetry (DSC) measurements were carried out on uncured DCPD resin as well as pDCPD films cured at various temperatures to determine an appropriate cure cycle for preparation of nanocomposites. For measurement of the total heat of reaction of the uncured resin, ∼3 mg of resin was transferred into an aluminum hermetic DSC pan and sealed. DSC measurements were performed from 25°C to 250°C at a heating rate of 5°C min−1. The residual heat of reaction of cured pDCPD films was similarly measured by transferring 5 mg of cured resin into a DSC pan, followed by heating from 25°C to 250°C at a heating rate of 5°C min−1. Degree of cure was calculated as α = 1—Hr/Ht, where α is the degree of cure and Ht and Hr are the total heat of reaction of the liquid resin and the residual heat of reaction of the cured films, respectively. A Discovery HR-2 Rheometer (TA Instrument) with a 40 mm flat geometry and a gap of 500 μm was used to determine the rheological properties of the DCPD resin containing 1 M equivalent of inhibitor with respect to Grubbs’ catalyst. Time-sweep measurements were performed at 23°C with a frequency of 1 Hz. The wettability of pristine buckypaper by the DCPD resin was characterized by measuring the static contact angle at room temperature using a goniometer (Rame-Hart Instrument). A droplet of the DCPD resin was placed on the surface of a buckypaper specimen, and the contact angle was immediately measured. Five measurements were carried out and the average value is reported.
Nanocomposite films were prepared by droplet casting of resin onto the surface of buckypaper (Figure 1). Upon dropping a few droplets of resin, the resin was observed to quickly saturate the nanotube network, after which the excess resin was removed using a lint-free wipe. Through-thickness frontal polymerization was initiated by heating the DCPD-impregnated buckypaper using a laboratory-scale hot plate at ∼140°C. Since the thickness of the film is low (∼100–200 μm), the propagation of the FP reaction through the thickness of the film was not noticeable and the overall cure process, from initiation to full cure, was completed within a few minutes. In other words, the resin was used here as a cure-on-demand resin system rather than as a self-propagating FP resin system. Thermogravimetric analysis (TGA) was used to determine the resin and nanotube contents in the nanocomposite films, according to the procedure reported in our previous work (Ashrafi et al., 2010). Calculation of resin or nanotube content requires performing TGA experiments on neat polymer, pristine buckypaper, and nanocomposite film. TGA measurements were carried out from 25°C to 600°C at a heating rate of 10 °C min-1 under nitrogen environment. A 30-min hold was also added to the temperature profile at 470°C to obtain an accurate weight measurement of the residue from each specimen at this processing temperature. Two measurements were performed on each material. The resin content in the nanocomposite is calculated as (Ashrafi et al., 2010),
wR and wF are weight fraction of resin and carbon nanotube in the nanocomposite film, mR, mF, and mC are residual mass of neat resin, pristine buckypaper, and nanocomposite film measured at 470°C, respectively. The concentration of solid (i.e., metal) impurities in pristine buckypaper (wI) was determined by performing an additional TGA measurement on pristine buckypaper specimens from 25°C to 1,000°C at a heating rate of 10°C min−1 under air environment. The impurity content of the pristine buckypaper was calculated to be 9.5%. Scanning electron microscopy (SEM) was performed using a JEOL JSM-5800 field emission scanning electron microscope to observe the morphology of buckypaper films after impregnation. The cross-section of the nanocomposite film was sputter-coated with a 10 nm thick layer of gold and imaged at an accelerating voltage of 15 kV. Tensile tests were performed on rectangular specimens (2 × 30 mm2) to determine the mechanical properties of pristine buckypaper and nanocomposite films. All tests were performed at a displacement rate of 1 mm min−1. Electrothermal performance of nanocomposite films were characterized using specimens with an effective heating area of 10 × 20 mm2. Copper electrodes were attached to both ends of the nanocomposite films using a silver-filled conductive paste. A vacuum pressure of 81.3 kPa was applied to the heaters by vacuum-bagging them on a glass substrate to simulate boundary conditions that heaters undergo during the composite manufacturing process. Various voltages were supplied to the heater films using a direct current (DC) power supply (9206, B&K Precision). The voltage and current data during electrothermal tests were recorded to determine the power consumption. The temperature at the center of the heater was measured using a K-type thermocouple and recorded by a LabView program.
FIGURE 1. Schematic representation of the fabrication process of the nanocomposite film heater. A sample of buckypaper is first impregnated by the DCPD resin using droplet casting approach, followed by rapid curing via frontal polymerization. Nanocomposite film heaters are then prepared by connecting two copper electrodes to the two opposite sides of the produced films.
For fabrication of composite panels, a nanocomposite heater with an effective heating area of 30 × 30 mm2 was used. Eight plies of a unidirectional prepreg (40 × 30 mm2) were cured using the nanocomposite heater placed on top of the layup and separated from prepreg plies using a release film. The input power to the heater was gradually increased to ∼8.9 W within 45 min to increase the temperature of the heater to 82°C at a heating rate of 1.3°C min−1 and then the input power was held unchanged for 3 h to simulate the cure cycle recommended by the prepreg manufacturer (3 h at 82°C). Two K-type thermocouples were used to measure the temperature profiles at the bottom and top of the layup during the curing process. An infrared thermal camera (FLIR T540) was also used to monitor the spatial distribution of temperature during the cure cycle. A control composite panel was also prepared using the same layup strategy but with curing the layup in an oven at 82°C for 3 h. The degree of cure of the composite panels produced using direct conductive heating and oven curing approaches were determined using DSC measurements. The residual heat of reaction of the cured composites was measured by transferring 15 mg of the cured composites into a DSC pan, followed by heating from 25°C to 250°C at a heating rate of 5°C min−1. The total heat of reaction of the uncured prepreg was measured by performing DSC measurements on 5 mg specimens of the uncured prepreg using the same experimental procedure.
Facile fabrication of buckypaper-based nanocomposites with a high density of nanotubes and low void content requires using a resin system that has a low initial viscosity and long pot life at room temperature while being rapidly curable at elevated temperatures and also having good compatibility with buckypaper for easy impregnation. Additionally, the resulting polymer nanocomposite should exhibit excellent thermomechanical properties. DCPD meets such requirements and is a promising resin for facile preparation of polymer nanocomposite films; therefore, we studied processing of buckypaper impregnated with the DCPD cure-on-demand resin system to explore the feasibility of fabrication of pDCPD-buckypaper nanocomposite films under mild processing conditions compared with traditional approaches used for epoxy resins. The results of room-temperature rheological measurements on the DCPD resin show that the initial viscosity of the resin remained unchanged for approximately 2 h, after which it slowly increased and reached a value of 750 Pa s after 5 h (Figure 2A); however, no gelation was observed within 5 h of the measurement (Figure 2B). As opposed to conventional epoxy resins, which have a high initial viscosity and short pot life, the low initial viscosity along with the long pot life of the DCPD resin enable facile impregnation of buckypaper at room temperature and ambient pressure without the need for adding any solvents, which is highly desirable from the processing point of view. In addition, while the DCPD resin is stable for a few hours at room temperature, it rapidly cures at elevated temperatures and yields a fully cured solid polymer within a few minutes. Figure 2C shows the results of DSC measurements on an uncured DCPD resin sample as well as a sample cured at 100°C for 5 min. The tall and sharp exothermic peak observed in the thermal profile of the uncured resin sample, which indicates the range of cure temperature, clearly disappeared in the thermal profile of the cured sample. As a result, a high degree of cure (∼93%) could be achieved by curing the resin for only 5 min. Contact angle measurements were also carried out to evaluate the wettability of buckypaper by the DCPD resin (Figure 2D). While an initial contact angle of 17.3° ± 0.8° was formed between the DCPD resin and buckypaper, the resin completely infused into the porous structure of buckypaper within a few seconds, demonstrating the excellent compatibility of the resin and carbon nanotube network.
FIGURE 2. Characterization of DCPD resin system (A, B) Time-sweep viscosity and modulus profiles of an uncured DCPD resin containing 1 M equivalent of inhibitor with respect to Grubbs’ catalyst at 23°C. (C) Thermal profile of an uncured resin sample and a pDCPD film sample cured at 100°C for 5 min. (D) Contact angle measurement for a droplet of DCPD resin on the buckypaper substrate.
The appropriate cure temperature for preparation of nanocomposite films was determined by heating the neat DCPD resin samples for 5 min at various temperatures (100, 120, and 140°C) and measuring the degree of cure of the resulting pDCPD films using DSC experiments. The degree-of-cure data obtained from DSC measurements are presented in Table 1. An increase in the cure temperature from 100°C to 140°C increased the degree of cure of pDCPD films from 93.8% to 99.4%, indicating that fully cured pDCPD films can be prepared by heating the material for 5 min at 140°C. DSC measurements were also conducted on a nanocomposite film sample cured according to the developed cure cycle (i.e., heating for 5 min at 140°C) to determine the degree of cure of polymer in the nanocomposite film. A high degree of cure of ∼98.2% was obtained for the cured nanocomposite film, further verifying that highly cured nanocomposite films can be prepared using the developed cure cycle. The microstructure of the cured nanocomposite samples was examined by performing SEM imaging on the cross-section of cured nanocomposite films. Figures 3A, B show the SEM micrographs of the nanocomposite sample at two different magnifications. The low-magnification image (Figure 3A) indicates that a thin (∼10 μm) layer of neat resin is formed on the film surface, caused by the incomplete removal of the excess surface resin during the drop casting process. The average thickness of nanocomposite films is ∼77 μm, caused by the swelling of the nanotube network by the impregnated resin as well as the formation of the surface resin layer. The image captured at the higher magnification (Figure 3B) demonstrates the high quality of impregnation and low volume fraction of pores in the produced nanocomposite film, which are necessary for producing films with good mechanical performance. Nanotube content is one of the key factors that affect the mechanical and electrothermal properties of nanocomposite films. TGA measurements were performed to determine the carbon nanotube content in cured nanocomposite films (Figure 3C). The residual masses of constituents and nanocomposite at 470°C were used to determine the carbon nanotube content in produced nanocomposites using Eqs 1, 2. A carbon nanotube content of ∼12.6 wt.% was calculated, which is high enough to ensure excellent heat generation capability in nanocomposite films. Compared to the pristine buckypaper, which is mechanically weak and fragile, the nanocomposite films are mechanically robust and can withstand various forms of deformation including twisting and bending. Tensile tests were performed on pristine buckypaper and nanocomposite film specimens to compare the mechanical properties of the buckypaper before and after impregnation and encapsulation by the polymer resin (Figure 3D). In pristine buckypaper, carbon nanotubes in the porous network are held together only via van der Waals forces and physical entanglement resulting in poor tensile properties. Impregnation of the porous structure of buckypaper with the matrix polymer enhances the mechanical robustness of the paper, where its tensile strength is increased 22-fold from 1.4 MPa to 31.3 MPa and its tensile modulus is increased 5-fold from 0.150 to 0.708 GPa.
FIGURE 3. Characterization of polymer nanocomposite films. (A, B) Scanning electron microscopy (SEM) micrographs from the cross-section of a nanocomposite film. (C) TGA profiles of pristine buckypaper, neat cured pDCPD film, and nanocomposite film. (D) Tensile stress-strain curves of pristine buckypaper and nanocomposite films. The inset shows a nanocomposite film bent using a tweezer.
Use of the produced nanocomposite film heaters for successful conductive curing of FRPCs first requires characterizing the Joule heating performance of the nanocomposite films. We performed electrothermal tests on nanocomposite film specimens by applying various voltages across the specimens and measuring their time-dependent temperature profiles (Figure 4A). An increase in the applied input voltage results in an increase in the heating rate as well as the steady-state temperature of film heaters. The nanocomposite film heaters demonstrate an excellent electrothermal performance, where a temperature of ∼132°C can be reached in 2 min using a low input voltage of 11 V (equivalent power consumption of 6.16 W). The measured linear relationship between the input power density and steady-state temperature also demonstrates that the heat generation in the nanocomposite heaters follows Joule’s law (Figure 4B). Another important requirement for using nanocomposite films as a heater for curing of FRPCs is the stability and reproducibility of their electrothermal properties, as they must survive long and repeated cure cycles for composite manufacturing. The electrothermal stability of nanocomposite heaters were evaluated by applying both static and dynamic electric loads on the heater films and measuring their temperature response. Figure 4C shows the temperature response of a heater to an input voltage of 9 V when continuously applied for 1 h. After the initial transient stage, temperature remains almost unchanged, demonstrating the stable and reliable electrothermal performance of the nanocomposite heater. The response of the heater to a cyclic electric load was also measured to evaluate the reproducibility of heat generation by produced film heaters; the results of the cyclic electrothermal stability tests reveal that the temperature profile of the heater follows a similar pattern for a given electric loading condition, indicating the good reproducibility of the observed electrothermal properties in the nanocomposite films (Figure 4D).
FIGURE 4. Evaluation of the electrothermal performance of produced nanocomposite films. (A) Temperature profiles of a nanocomposite film heater in response to various input voltages. (B) Relationship between input power density and steady-state temperature. (C) Static electrothermal stability test at a constant input voltage of 9 V. (D) Cyclic stability test by varying the input voltage between 0 and 9 V.
Following the successful demonstration of the Joule heating performance of the produced buckypaper-DCPD nanocomposite films, we used the films as a heat source for direct conductive heating and curing of carbon FRPC laminates. Composite layups were prepared by stacking eight small (4 × 3 cm2) plies of an out-of-autoclave carbon fiber prepreg on a polyisocyanurate foam tool and placing the film heater (effective heating area of 3 × 3 cm2) on top of the prepreg stack. A thin layer of a release film was used under the film heater to separate it from the prepreg stack for easy removal and reuse of the heater following the curing process. The layup was then vacuum bagged, and then the cure process was initiated by supplying power to the film heater to generate heat according to the recommended cure cycle. Figure 5A shows temperature profiles measured using two thermocouples placed in the center of the composite layup at the top and bottom surfaces of the laminate during the applied cure cycle. The input power to the film heater was gradually increased until the temperature at the top (heater side) of the laminate reached the cure temperature of the prepreg (i.e., 82°C), after which the power was maintained unchanged for 3 h. A steady-state temperature of ∼76°C was measured at the bottom of the layup, which is slightly lower than the required cure temperature, caused by heat losses through tooling boundaries; however, the temperature distribution across the laminate is sufficient for proper curing of the composite laminate. Infrared thermal imaging was also used to monitor the spatial distribution of temperature throughout the top surface of the layup during the curing process. A uniform heat generation and temperature distribution was observed in the composite layup (Figure 5B), indicating the effectiveness of the nanocomposite film heater for uniform heating and curing of the composite laminate. The energy consumption of this direct conductive curing approach was calculated from the power consumption profile recorded during the applied cure cycle (Figure 5C). Using this approach, only 0.1 MJ of energy was required to successfully cure the composite laminate, whereas curing the same composite panel using a small convection oven in our laboratory (internal volume of 0.17 m3) is estimated to require 40.5 MJ of energy. The degree of cure of the composite laminate cured by the nanocomposite film heater was determined using DSC measurements. As a control, the degree of cure of a similar composite panel cured using the traditional, bulk oven curing approach was also measured. The degree of cure of the composite panels made using the heater and oven curing approaches was 91.3% and 96.3%, respectively (Table 1). The slightly lower degree of cure obtained in conductive curing approach is attributed to the observed temperature gradient across the thickness of the layup. This issue can potentially be mitigated by modifying the cure cycle by increasing the dwell temperature and/or the cure time or alternatively by placing the heater on the bottom (tool side) of the composite layup.
FIGURE 5. Direct conductive curing of a FRPC panel using a nanocomposite film heater. (A) Temperature profiles measured at the bottom and top of the composite layup during the cure cycle. (B) Thermal infrared image of the nanocomposite film heater during composite manufacturing. (C) Power consumption profile recorded during the cure cycle.
In this work, we used a frontally curable thermoset resin with a low initial resin viscosity to fabricate buckypaper-based polymer nanocomposites. The low viscosity of the resin system allows for quick impregnation of the carbon nanotube network at room temperature and ambient pressure. Following the impregnation step, complete curing of the matrix resin was achieved in a few minutes via through-thickness heating of the material. Produced nanocomposite films are mechanically robust and exhibit excellent electrical conductivity and electrothermal performance, which are ideal for using the films as a heater for curing of fiber-reinforced polymer composites. Finally, a nanocomposite film heater was used to cure a carbon fiber composite panel using a low energy consumption of 0.1 MJ, which is 350 times less than the energy required for producing a similar panel using the conventional oven curing approach.
The original contributions presented in the study are included in the article/supplementary material, further inquiries can be directed to the corresponding authors.
MY and BA directed the research. IN performed the experiments. MJ and YM-R fabricated the buckypaper samples. All authors participated in discussions and writing the manuscript.
This work was supported by the New Beginning Ideation Fund from the National Research Council Canada (Grant Agreement no. 967242).
Authors would like to thank the staff members of Colorado State University Analytical Resources Core Facility (RRID: SCR_021758) for their assistance with performing SEM, TGA, and DSC experiments.
The authors declare that the research was conducted in the absence of any commercial or financial relationships that could be construed as a potential conflict of interest.
All claims expressed in this article are solely those of the authors and do not necessarily represent those of their affiliated organizations, or those of the publisher, the editors and the reviewers. Any product that may be evaluated in this article, or claim that may be made by its manufacturer, is not guaranteed or endorsed by the publisher.
Ashrafi, B., Guan, J., Mirjalili, V., Hubert, P., Simard, B., and Johnston, A. (2010). Correlation between Young’s modulus and impregnation quality of epoxy-impregnated SWCNT buckypaper. Compos. Part A: Appl. Sci. Manuf. 41, 1184–1191. doi:10.1016/j.compositesa.2010.04.018
Ashrafi, B., Jakubinek, M. B., Martinez-Rubi, Y., Rahmat, M., Djokic, D., Laqua, K., et al. (2017). Multifunctional fiber reinforced polymer composites using carbon and boron nitride nanotubes. Acta Astronaut. 141, 57–63. doi:10.1016/j.actaastro.2017.09.023
Bobinger, M. R., Romero, F. J., Salinas-Castillo, A., Becherer, M., Lugli, P., Morales, D. P., et al. (2019). Flexible and robust laser-induced graphene heaters photothermally scribed on bare polyimide substrates. Carbon 144, 116–126. doi:10.1016/j.carbon.2018.12.010
Centellas, P. J., Yourdkhani, M., Vyas, S., Koohbor, B., Geubelle, P. H., and Sottos, N. R. (2022). Rapid multiple-front polymerization of fiber-reinforced polymer composites. Compos. Part A: Appl. Sci. Manuf. 158, 106931. doi:10.1016/j.compositesa.2022.106931
Chakraborty, A. K., Plyhm, T., Barbezat, M., Necola, A., and Terrasi, G. P. (2011). Carbon nanotube (CNT)–epoxy nanocomposites: A systematic investigation of CNT dispersion. J. Nanoparticle Res. 13, 6493–6506. doi:10.1007/s11051-011-0552-3
Chen, J., Wang, Y., Liu, F., and Luo, S. (2020). Laser-Induced graphene paper heaters with multimodally patternable electrothermal performance for low-energy manufacturing of composites. ACS Appl. Mater. Interfaces 12, 23284–23297. doi:10.1021/acsami.0c02188
Chen, X., Cheng, S., Wen, K., Wang, C., Zhang, J., Zhang, H., et al. (2023). In-situ damage self-monitoring of fiber-reinforced composite by integrating self-powered ZnO nanowires decorated carbon fabric. Compos. Part B: Eng. 248, 110368. doi:10.1016/j.compositesb.2022.110368
Dean, L. M., Wu, Q., Alshangiti, O., Moore, J. S., and Sottos, N. R. (2020). Rapid synthesis of elastomers and thermosets with tunable thermomechanical properties. ACS Macro Lett. 9, 819–824. doi:10.1021/acsmacrolett.0c00233
Galos, J. (2021). Microwave processing of carbon fibre polymer composites: A review. Polym. Polym. Compos. 29, 151–162. doi:10.1177/0967391120903894
Groo, L., Nasser, J., Zhang, L., Steinke, K., Inman, D., and Sodano, H. (2020). Laser induced graphene in fiberglass-reinforced composites for strain and damage sensing. Compos. Sci. Technol. 199, 108367. doi:10.1016/j.compscitech.2020.108367
Isaza, M. C. A., Herrera Ramírez, J., Ledezma Sillas, J., and Meza, J. (2018). Dispersion and alignment quantification of carbon nanotubes in a polyvinyl alcohol matrix. J. Compos. Mater. 52, 1617–1626. doi:10.1177/0021998317731151
Karalis, G., Tzounis, L., Dimos, E., Mytafides, C. K., Liebscher, M., Karydis-Messinis, A., et al. (2021). Printed single-wall carbon nanotube-based Joule heating devices integrated as functional laminae in advanced composites. ACS Appl. Mater. Interfaces 13, 39880–39893. doi:10.1021/acsami.1c10001
Khan, F., Kausar, A., and Siddiq, M. (2015). A review on properties and fabrication techniques of polymer/carbon nanotube composites and polymer intercalated buckypapers. Polymer-Plastics Technol. Eng. 54, 1524–1539. doi:10.1080/03602559.2015.1021486
Klikovits, N., Liska, R., D’Anna, A., and Sangermano, M. (2017). Successful UV-induced RICFP of epoxy-composites. Macromol. Chem. Phys. 218, 1700313. doi:10.1002/macp.201700313
Lee, J., Ni, X., Daso, F., Xiao, X., King, D., Gómez, J. S., et al. (2018). Advanced carbon fiber composite out-of-autoclave laminate manufacture via nanostructured out-of-oven conductive curing. Compos. Sci. Technol. 166, 150–159. doi:10.1016/j.compscitech.2018.02.031
Liu, Y., van Vliet, T., Tao, Y., Busfield, J. J. C., Peijs, T., Bilotti, E., et al. (2020). Sustainable and self-regulating out-of-oven manufacturing of FRPs with integrated multifunctional capabilities. Compos. Sci. Technol. 190, 108032. doi:10.1016/j.compscitech.2020.108032
Lopes, P. E., van Hattum, F., Pereira, C. M. C., Nóvoa, P. J. R. O., Forero, S., Hepp, F., et al. (2010). High CNT content composites with CNT Buckypaper and epoxy resin matrix: Impregnation behaviour composite production and characterization. Compos. Struct. 92, 1291–1298. doi:10.1016/j.compstruct.2009.11.003
Ma, P.-C., Siddiqui, N. A., Marom, G., and Kim, J.-K. (2010). Dispersion and functionalization of carbon nanotubes for polymer-based nanocomposites: A review. Compos. Part A: Appl. Sci. Manuf. 41, 1345–1367. doi:10.1016/j.compositesa.2010.07.003
Mariani, A., Fiori, S., Bidali, S., Alzari, V., and Malucelli, G. (2008). Frontal polymerization of diurethane diacrylates. J. Polym. Sci. Part A: Polym. Chem. 46, 3344–3352. doi:10.1002/pola.22675
Moreira, I. P., Sanivada, U. K., Bessa, J., Cunha, F., and Fangueiro, R. (2021). A review of multiple scale fibrous and composite systems for heating applications. Molecules 26, 3686. doi:10.3390/molecules26123686
Naseri, I., and Yourdkhani, M. (2022). Rapid and energy-efficient frontal curing of multifunctional composites using integrated nanostructured heaters. ACS Appl. Mater. Interfaces 14, 50215. doi:10.1021/acsami.2c15415
Naseri, I., Ziaee, M., Nilsson, Z. N., Lustig, D. R., and Yourdkhani, M. (2022). Electrothermal performance of heaters based on laser-induced graphene on aramid fabric. ACS Omega 7, 3746–3757. doi:10.1021/acsomega.1c06572
Nuhiji, B., Swait, T., Bower, M. P., Green, J. E., Day, R. J., and Scaife, R. J. (2019). Tooling materials compatible with carbon fibre composites in a microwave environment. Compos. Part B: Eng. 163, 769–778. doi:10.1016/j.compositesb.2019.01.047
Pojman, J. A. (2022). “Cure-on-Demand composites by frontal polymerization,” in Encyclopedia of materials: Plastics and polymers (Elsevier), 85–100. doi:10.1016/B978-0-12-820352-1.00201-7
Pojman, J. A. (2012). “Frontal polymerization,” in Polymer science: A comprehensive reference (Elsevier), 957–980. doi:10.1016/B978-0-444-53349-4.00124-2
Ribeiro, B., Botelho, E. C., Costa, M. L., and Bandeira, C. F. (2017). Carbon nanotube buckypaper reinforced polymer composites: A review. Polímeros 27, 247–255. doi:10.1590/0104-1428.03916
Robertson, I. D., Dean, L. M., Rudebusch, G. E., Sottos, N. R., White, S. R., and Moore, J. S. (2017). Alkyl phosphite inhibitors for frontal ring-opening metathesis polymerization greatly increase pot life. ACS Macro Lett. 6, 609–612. doi:10.1021/acsmacrolett.7b00270
Robertson, I. D., Yourdkhani, M., Centellas, P. J., Aw, J. E., Ivanoff, D. G., Goli, E., et al. (2018). Rapid energy-efficient manufacturing of polymers and composites via frontal polymerization. Nature 557, 223–227. doi:10.1038/s41586-018-0054-x
Ruiu, A., Sanna, D., Alzari, V., Nuvoli, D., and Mariani, A. (2014). Advances in the frontal ring opening metathesis polymerization of dicyclopentadiene. J. Polym. Sci. Part A: Polym. Chem. 52, 2776–2780. doi:10.1002/pola.27301
Schlimbach, J., and Ogale, A. (2012). “Out-of-autoclave curing process in polymer matrix composites,” in Manufacturing techniques for polymer matrix composites (PMCs) (Elsevier), 435–480. doi:10.1533/9780857096258.3.435
Silva, V. L. M., Santos, L. M. N. B. F., and Silva, A. M. S. (2017). Ohmic heating: An emerging concept in organic synthesis. Chem. Eur. J. 23, 7853–7865. doi:10.1002/chem.201700307
Suslick, B. A., Hemmer, J., Groce, B. R., Stawiasz, K. J., Geubelle, P. H., Malucelli, G., et al. (2022). Frontal polymerizations: From chemical perspectives to macroscopic properties and applications. Chem. Rev. doi:10.1021/acs.chemrev.2c00686
Tarfaoui, M., El Moumen, A., Boehle, M., Shah, O., and Lafdi, K. (2019). Self-heating and deicing epoxy/glass fiber based carbon nanotubes buckypaper composite. J. Mater. Sci. 54, 1351–1362. doi:10.1007/s10853-018-2917-9
Tu, R., Liu, T., Steinke, K., Nasser, J., and Sodano, H. A. (2022). Laser induced graphene-based out-of-autoclave curing of fiberglass reinforced polymer matrix composites. Compos. Sci. Technol. 226, 109529. doi:10.1016/j.compscitech.2022.109529
Wan Dalina, W. A. D., Mariatti, M., and Tan, S. H. (2019). Multi-walled carbon nanotubes buckypaper/epoxy composites: Effect of loading and pressure on tensile and electrical properties. Polym. Bull. 76, 2801–2817. doi:10.1007/s00289-018-2530-8
Xia, Q., Zhang, Z., Liu, Y., and Leng, J. (2020). Buckypaper and its composites for aeronautic applications. Compos. Part B: Eng. 199, 108231. doi:10.1016/j.compositesb.2020.108231
Xu, F., Aouraghe, M. A., Xie, X., Zheng, L., Zhang, K., and Fu, K. K. (2021). Highly stretchable, fast thermal response carbon nanotube composite heater. Compos. Part A: Appl. Sci. Manuf. 147, 106471. doi:10.1016/j.compositesa.2021.106471
Yao, X., Falzon, B. G., and Hawkins, S. C. (2019). Orthotropic electro-thermal behaviour of highly-aligned carbon nanotube web based composites. Compos. Sci. Technol. 170, 157–164. doi:10.1016/j.compscitech.2018.11.042
Yue, C., Zhang, Y., Lu, W., Zhang, Y., Wang, P., Li, Y., et al. (2022). Realizing the curing of polymer composite materials by using electrical resistance heating: A review. Compos. Part A: Appl. Sci. Manuf. 163, 107181. doi:10.1016/j.compositesa.2022.107181
Zeinedini, A., Shokrieh, M. M., and Ebrahimi, A. (2018). The effect of agglomeration on the fracture toughness of CNTs-reinforced nanocomposites. Theor. Appl. Fract. Mech. 94, 84–94. doi:10.1016/j.tafmec.2018.01.009
Zhang, Z., Liu, R., Li, W., Liu, Y., Pei, Z., Qiu, J., et al. (2021). Frontal polymerization-assisted 3D printing of short carbon fibers/dicyclopentadiene composites. J. Manuf. Process. 71, 753–762. doi:10.1016/j.jmapro.2021.10.014
Ziaee, M., Johnson, J. W., and Yourdkhani, M. (2022). 3D printing of short-carbon-fiber-reinforced thermoset polymer composites via frontal polymerization. ACS Appl. Mater. Interfaces 14, 16694–16702. doi:10.1021/acsami.2c02076
Keywords: out-of-oven curing, frontal polymerization, dicyclopentadiene, Joule heating, fiber-reinforced composites, energy-effcient, rapid manufacturing
Citation: Naseri I, Ashrafi B, Jakubinek M, Martinez-Rubi Y and Yourdkhani M (2023) Rapid and facile preparation of nanocomposite film heaters for composite manufacturing. Front. Mater. 10:1166986. doi: 10.3389/fmats.2023.1166986
Received: 15 February 2023; Accepted: 06 March 2023;
Published: 23 March 2023.
Edited by:
Veronique Michaud, Swiss Federal Institute of Technology Lausanne, SwitzerlandReviewed by:
Bodo Fiedler, Hamburg University of Technology, GermanyCopyright © 2023 Naseri, Ashrafi, Jakubinek, Martinez-Rubi and Yourdkhani. This is an open-access article distributed under the terms of the Creative Commons Attribution License (CC BY). The use, distribution or reproduction in other forums is permitted, provided the original author(s) and the copyright owner(s) are credited and that the original publication in this journal is cited, in accordance with accepted academic practice. No use, distribution or reproduction is permitted which does not comply with these terms.
*Correspondence: Behnam Ashrafi, QmVobmFtLkFzaHJhZmlAY25yYy1ucmMuZ2MuY2E=; Mostafa Yourdkhani, eW91cmRAY29sb3N0YXRlLmVkdQ==
Disclaimer: All claims expressed in this article are solely those of the authors and do not necessarily represent those of their affiliated organizations, or those of the publisher, the editors and the reviewers. Any product that may be evaluated in this article or claim that may be made by its manufacturer is not guaranteed or endorsed by the publisher.
Research integrity at Frontiers
Learn more about the work of our research integrity team to safeguard the quality of each article we publish.