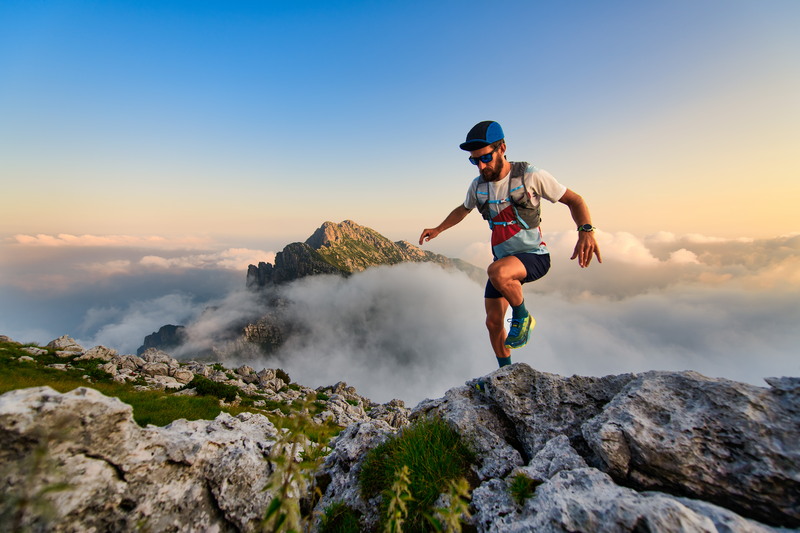
95% of researchers rate our articles as excellent or good
Learn more about the work of our research integrity team to safeguard the quality of each article we publish.
Find out more
ORIGINAL RESEARCH article
Front. Mater. , 05 April 2023
Sec. Structural Materials
Volume 10 - 2023 | https://doi.org/10.3389/fmats.2023.1166065
This article is part of the Research Topic Nano Science and Technology in Concrete Composites View all 5 articles
This study investigates the use of self-produced solid waste in mines to backfill the goaf, with energy saving and emission reduction technology requirements. Using a relevant backfill mixing proportion test and mechanical property test, we analyzed the strength variation law of backfill materials under different concentrations and cementation powder addition. The results showed that, for backfill materials at 7 days with an ash-tailings ratio of 1:6, the strength of specimens with 52% and 49% prepared concentrations, respectively, increased by 1.361 and 1.266 times over specimens with 49% and 46% concentrations. For backfill materials with 49% prepared concentrations and ash-tailings ratios of 1:6, 1:9, and 1:12, the specimen strength of the backfill materials with ratios of 1:6 and 1:9 improved by 0.616 MPa and 0.321 MPa—109.28% and 114.6%, respectively—compared with 1:9 and 1:12 backfill materials at 60 days. It is thus evident that the quantity of binding materials added plays a critical function in improving the strength of backfill materials, and in the subsequent application of goaf backfill. The strength of backfill materials can be enhanced by improving the gradation of backfill aggregates and increasing the amount of binding materials so as to achieve cost reductions and sustainable development.
Some hidden hazards have gradually emerged in current underground mine exploitation processes of various scales with the continuous upscale of mine exploitation and increasing exploitation depth. Mining operations are thus often faced with complex engineering geological hazards which impact daily operations to varying degrees (Gomes et al., 2016; Hidayat et al., 2022; Tobias et al., 2022). When mining some specific ore bodies, it is necessary to pay more attention to the disasters that can be caused by geological hazards so that reasonable technical measures can be taken to address them, thus creating a safe mining environment (Cao et al., 2019; Wang et al., 2022a; Krzysztof et al., 2022; Víctor et al., 2022). To avoid the collapse hazards of mine goaf roof rock formations, it is necessary to improve the stress state of the such formations to avoid the generation of large areas of tensile and shear stress due to concentrated stress in the rock formation. In this rock formation stress improvement study, an optimized layout of ground pressure in respect of factors such as the maintenance of underground mine goaf, functional chambers, underground sumps, and ore drop shafts can be achieved by filling the large-scale goaf. This can achieve the orderly management of the top ore body and surrounding rock to minimize the probabilities of mine disaster accidents such as the collapse of rock formations (Strzałkowski, 2021; Zhang, 2021; Yuan et al., 2022a; Yuan et al., 2022b; Hu, 2022).
In the safe mining of underground mineral resources, industrial solid waste self-produced or purchased by the mine is used as backfill aggregate in the daily production of various mine goaf treatments. After adding the appropriate amount of binding materials according to the design mixing proportion, the prepared filling slurry is mixed evenly through a one- or two-stage mixer and is continuously transported to the goaf along the long-distance backfill pipeline. The solidification and hardening process of the filling slurry effectively improves the resistance of the surrounding rock (Behera et al., 2021; Ahmed Haitham et al., 2022). The material particles in the low- or high-concentration filling slurry gradually sink under the action of self-weight, and the slurry concentration and density are improved after the water between the particle pores is extruded. The gradually exuded water makes the backfill materials denser, and this improved slurry concentration promotes the solidification and hardening of the hydration reaction of the binding materials. The cementation of the binding materials is enhanced, thus strengthening the backfill materials to different degrees. This produces circumferential pressure and lateral restriction on the surrounding exposed rock mass, changing part of the rock mass from a uniaxial to a triaxial stress state and thus greatly enhancing its stability. This highlights the effect of filling on maintaining the stability of the ore-bearing rock (Koupouli et al., 2016; Cui and Fall, 2017; Singalreddy et al., 2022).
In the practice of using filling slurry to backfill and treat goaf, the preparation and acquisition routes of backfill materials differ across various industrial and mining enterprises. For example, in the filling process of Jinchuan No. 2 mine, mineral processing tailings and rod mill sand are used as backfill aggregates; after introducing additives such as fly ash cement and water-reducing agent, the filling slurry is transported to the goaf along a pipeline through the filling industrial pump. After decades of application, this combination of backfill materials has been a powerful supporting factor in mine production safety (Zhao et al., 2013; Wang et al., 2022b; Lu, 2022). The Nanjing lead–zinc–silver mine is located in a densely populated urban area; for its excavating-filling engineering, surface runoff continuously flows through the upper part of the ore body, thus constituting a unique mineral resource development mode (Wang et al., 2003; Wang et al., 2008). The engineering case involved in this study is located in the densely populated Huaibei Plain, which has extensive surface fields and ponds. Its agricultural production activities are relatively intense, so surface collapse cannot be allowed in this area. This study combines the difficulties of tailings cemented backfill of ultrafine particles in a mining enterprise with the treatment requirements of filling in the mine goaf. It investigates the mechanical properties of cemented backfill materials and analyzes its variation in order to provide a reliable technical basis for the subsequent filling of the mine goaf.
The ore body of the copper and iron mine analyzed in this study is at a great depth and is relatively scattered, but the total ore reserves are considerable. The ore-bearing rocks are relatively broken due to geological and structural factors, thus leading to the technical problem of the surrounding rocks and roof plate frequently collapsing during the mining process and entailing hazard in daily production. In order to overcome the negative impact caused by the crushed nature of the surrounding rock, the mine has adopted technical measures of the coordinated mining of multiple mining areas and adopts layer filling or open stoping with subsequent filling for veins which are high-grade and easy to mine. The hazard of rock formation fracture in the mining progress is reduced as much as possible by staggered coordination of mining multiple areas. This spatial and temporal staggered mining of multiple mining areas allows the mine to produce 900,000 tons per annum. As a difficult-to-treat mine solid waste, ultrafine particle tailings are continuously applied to goaf backfill, which greatly reduces the quantity of tailings discharge from the tailing pond and also reduces expenditure on sewage charges. Therefore, this filling mining plays a positive role in both maintaining the safety and stability of the rock formation and in the resource utilization of the waste tailings.
Since the properties of the ore bodies mined at different times may vary—in turn causing differences in the properties of tailings—it was necessary to take tailings samples during the long-term stable production of the mine in order to avoid the reduction of the test effect due to the significant alteration of tailings properties. To ensure that test materials are representative, the collection of backfill aggregate and binding materials or other auxiliary materials occurred over the mine’s continuous normal production for 30–90 days of underground mining and mineral processing plant production. The mine uses ultrafine particle unclassified tailings discharged from the processing plant as backfill aggregate. Low-concentration tailings slurry were taken at the discharge port of the processing plant's waste slurry pump to prevent the loss of ultrafine tailings particles and thus avoid affecting the test results. The slurry was diverted to several 75-L plastic barrels using a 50-mm-inner diameter white plastic pipe, pouring out the upper clarified water after 24 h of natural settling and then using evaporative drying to spread the thin and dry. It was milled to the original particle size state after drying and held in a lidded container for the test user.
The binding materials used in the test are cementation powder, and the samples were taken from the cementation powder silo when the filling station was feeding. To ensure that the samples were inherently representative, they were taken several times at different feedings. The cementation powder was placed in a sealed container for backup in order to prevent the binding materials from deteriorating due to water absorption and moisture. In the process of testing the basic physical and mechanical properties of various test materials, quarter sampling was used to avoid adverse effects caused by discrete data. The testing contents of material properties were material-specific gravity, loose- and dense-bulk weight, and minimum and maximum porosity. These provided the basic performance parameters of the materials for the subsequent backfill materials proportioning test.
As aggregate for the production of mechanical property test specimens of backfill materials, unclassified tailings of ultrafine particles present as a gray-black powder; its coarse particles are felt to be less when rubbed by hand, and it is basically composed of microfine powder granular materials. The specific gravity, loose- and dense-bulk densities, and minimum and maximum porosity parameters of the ultrafine unclassified tailings particles were obtained through relevant physical property index experimental tests (Table 1). The particles’ size was tested using a laser particle size meter, obtaining the particle gradation characteristic parameters of the ultrafine particle unclassified tailings. The separate and cumulative counting particle size curve of the ultrafine particle unclassified tailings obtained after further statistical analysis is shown in Figure 1. The content of the different chemical components of the tailings was determined by chemical experimental analysis methods (Figure 2).
FIGURE 1. Separate and cumulative counting particle size curve of ultrafine particle unclassified tailings.
As the binding materials for the production of mechanical property test specimens of backfill materials, the cementation powder presents as a gray-white powder, with no coarse particles when rubbed by hand, and the materials are completely microfine powder granular materials. Through the relevant physical performance index experimental test, the specific gravity, loose and dense bulk densities, and minimum and maximum porosity parameters of the cementation powder were obtained (Table 2).
The test water was ordinary tap water, a transparent fluid at room temperature with clear water quality and a pH value slightly higher than 7.0. The specific gravity, room temperature density, room temperature volumetric weight, and pH value of tap water were obtained through relevant physical performance index experimental tests (Table 3).
The process parameters of filling slurry usually depend on the properties of the backfill materials. For coarse aggregate backfill, due to its larger particle size, the specific surface area of the particles is generally significantly smaller than fine aggregate backfill. The concentration of the filling slurry using coarse aggregate should be significantly higher to achieve the same slump. Combining the requirements of mining engineering for the backfill materials’ strength and taking into account the theme of resource utilization of the enterprise’s industrial solid waste, the ultrafine particle tailings involved in this study were used as the backfill aggregate. Since the tailings particles in this study were very fine and thus had a larger specific surface area, more water was required to dilute them to achieve the same flow state compared to other types of coarser backfill aggregates. Thus, according to the process conditions of these study materials, the concentration of the filling slurry was 52–46% at 24.5–28.5 cm particle size. Therefore, according to the mining process and the mining method used, the concentration of the filling slurry was set to 46%, 49%, and 52% in three groups, and the ash-tailings ratio was set to 1:6, 1:9, and 1:12 in three groups. The fabricated backfill materials test blocks were maintained for ages of 3, 7, 28, and 60 days and tested for the corresponding uniaxial compressive strength.
The strength performance index of the backfill materials was measured by the backfill mixing proportion test; the variation law is shown in Figures 3–5. In view of the variation law of the data points in each line diagram, the strength of the backfill materials gradually became larger as the curing age lengthened; the higher the initial weight concentration, the greater was the strength at each age. Through statistical analysis of the test data, the uniaxial compressive strength of the backfill materials prepared from the filling slurry with concentrations of 46%, 49%, and 52% changed with the variation of the ash-tailings ratio. This law is shown in Figures 6–8, where it can be seen from the three-dimensional line diagram that the mechanical properties of the backfill materials prepared from the same concentration of filling slurry with different ash-tailings ratios changed significantly with the variation of the concentration. The mechanical properties have an obvious positive correlation with the concentration, where the uniaxial compressive strength of the backfill materials also increased to different degrees when the concentration was increased.
FIGURE 6. Variation of the strength of backfill materials for 46% concentration with the ash-tailings ratio.
FIGURE 7. Variation of the strength of backfill materials for 49% concentration with the ash-tailings ratio.
FIGURE 8. Variation of the strength of backfill materials for 52% concentration with the ash-tailings ratio.
For all kinds of mineral resources buried in deep strata in the mining process of underground metal mines, as the ore body is extracted and gradually produces a certain scale of goaf, the force on the exposed ore-bearing rock mass changes from a triaxial to uniaxial compression state. The environment in which it is located has a gradual weakening impact on the stability of the ore body, and, over time, the uniaxially stressed ore-bearing rock mass will gradually destabilize and disintegrate, eventually leading to secondary geological disasters (Li et al., 2019; Zhang et al., 2020; Yu et al., 2021). For the engineering examples in this study, unclassified mine self-produced tailings were used as the backfill aggregates, and cementation powder, which is cheaper than cement, was used as the binding material to test the strength mixing proportion of the backfill materials. By applying this filling method, mining can act as lateral limit protection for the exposed ore-bearing rock mass. Filling slurry with 46–52% concentration has better material fluidity, and the material particles in the slurry will be more uniformly distributed after two-stage mixing and long-distance pipeline transportation. It can fill in the crevices of ore-bearing rock masses and isolate the intrusion of external water and gas, thus maintaining the stability of the ore-bearing rock mass itself to the maximum extent.
When ultrafine particle tailings are used as backfill aggregate, it is difficult for the finite binding materials to completely adhere to the surface of all tailings particles due to the generally large specific surface area that results from the fine particles; the cementation effect produced by the hydration reaction will thus also be affected to a certain extent (Ma, 2022; Meng et al., 2022). There is no other choice but to use ultrafine particle tailings as backfill aggregate in order to improve the strength of the cemented backfill materials. Current research on various types of binding materials that can match with ultrafine particle tailings has become active and is obtaining promising technological and economic results (Li et al., 2023; Zhenbang et al., 2023). In order to effectively reduce the discharge of difficult-to-handle solid waste and reduce or even eliminate the pollution of the surrounding ecology due to mining and beneficiation processes, ultrafine particle unclassified tailings with an average particle size of 29.72 μm were chosen as the backfill aggregates in this study, and purchased cementation powder was used as the backfill binding material, producing a filling slurry with excellent fluidity.
In order to overcome the negative impact of ultrafine unclassified tailings particles on strength, the cementation powder used in this study is a cement substitute, specially developed for use in combination with the properties of tailings. In the engineering examples in this study, the backfill materials’ strength of the cementation powder as a binding materials was significantly improved compared to cement for the three ash-tailings ratios of 1:12, 1:9, and 1:6, with concentrations of 46–52%; the backfill materials have a 3-day strength range of 0.143–0.732 MPa, a 7-day range of 0.213–1.023 MPa, a 28-day range of 0.261–1.131 MPa, and a 60-day strength range of 0.279–1.375 MPa. There are many mining methods, including upward slicing and filling, drift cut-and-fill stoping, and stage open stope and subsequent filling, so the requirements of these mining methods for the strength of backfill materials can vary widely. The strength of the backfill required for upward slicing and filling is usually 0.15–0.8 MPa, for drift cut-and-fill stoping is usually 0.6–0.85 MPa, and for stage open stope and subsequent filling is usually 0.45–1.25 MPa, so the strength parameters shown in the test results all satisfy the requirements of different mining methods for the strength of backfill materials.
The maintenance effect of backfill materials with different mixing proportions on ore-bearing rock mass can differ as backfill materials with higher strength can absorb more deformation elastic energy on the deformation process of ore-bearing rock masses and thus delay the rupture of the ore-bearing rock. From the test results, it can be seen that the strength of the backfill materials with ultrafine particles as backfill aggregate is lower than that of backfill materials with coarse particles as backfill aggregate; therefore, under the condition of satisfying the strength requirements of backfill materials for goaf backfill, the gradation of the backfill aggregate can be optimized to reduce mining and backfill costs while improving the mechanical properties of the backfill materials.
For thick and large ore veins overlaid by solid surrounding rock, the main body of the mine is mined by open stope and subsequent filling; the process of this method includes ore body cutting, drilling, charging, blasting, discharging, and filling. It thus takes a long time and is often only concerned with the long-term strength of the backfill materials. From this study’s results, the strength of backfill materials at 60 days curing with a concentration of 49–52% is 1.215–1.375 MPa, which corresponds to a backfill materials bulk density of 1.591–1.602 t/m³; therefore, if the homogeneity of the backfill materials is still acceptable, this backfill material strength range can meet the requirements of the subsequent backfill mining in the empty field.
In the process of mining unstable small-scale ore bodies by cut-and-fill stoping, low height and small space required for the mining process render the strength requirements for the backfill materials low, and the cut-and-fill stoping cycle is relatively short. Slurry filling with 49% concentration of an ash-tailings ratio of 1:12–1:9 can be used in the bottom and middle filling, and the strength that can be achieved in 7 days of curing is 0.223–0.462 MPa. A thickness of 0.5 m of the pouring surface layer is filled with high-strength backfill, and, when the surface is filled with a 1:6 ash-tailings ratio, the strength of 49% concentration of backfill materials is 0.752 MPa, which can fully meet the requirements for ore extraction using a scraper.
The original contributions presented in the study are included in the article/supplementary material; further inquiries can be directed to the corresponding author.
DD, YW, and YL wrote the main text of the manuscript. JF, YG, and YM collected and analyzed the data. All authors reviewed and commented on the manuscript.
This work was supported by the NSFC projects of China (51764009), the Guizhou Province Science and Technology Support Plan Project [Grant No. (2018)2836], the Provincial Natural Science Foundation of Hunan (2020JJ5538), the Scientific Research Fund of Hunan Province Education Department (20A475 and 19C1736),the Doctoral Research Project of Xiangtan University (22QDZ28 and 22QDZ35), and the High-level Talent Gathering Project in Hunan Province (2019RS1059). The authors are grateful for the financial support for this research.
The authors declare that the research was conducted in the absence of any commercial or financial relationships that could be construed as a potential conflict of interest.
All claims expressed in this article are solely those of the authors and do not necessarily represent those of their affiliated organizations, or those of the publisher, the editors, and the reviewers. Any product that may be evaluated in this article, or claim that may be made by its manufacturer, is not guaranteed or endorsed by the publisher.
Ahmed Haitham, M., Bharathan, B., Kermani, M., Hassani, F., Hefni, M. A., et al. (2022). Evaluation of rheology measurements techniques for pressure loss in mine paste backfill transportation. Minerals 12 (6), 678. doi:10.3390/min12060678
Behera, S. K., Mishra, D. P., Singh, P., Mishra, K., Mandal, S. K., et al. (2021). Utilization of mill tailings, fly ash and slag as mine paste backfill material: Review and future perspective. Constr. Build. Mater., 309. 125120. doi:10.1016/j.conbuildmat.2021.125120
Cao, G., Wang, W., Yin, G., and Wei, Z. (2019). Experimental study of shear wave velocity in unsaturated tailings soil with variant grain size distribution. Constr. Build. Mater. 228, 116744. doi:10.1016/j.conbuildmat.2019.116744
Cui, L., and Fall, M. (2017). Multiphysics modeling of arching effects in fill mass. Comput. Geotechnics 83, 114–131. doi:10.1016/j.compgeo.2016.10.021
Gomes, A. R. A., Rojas, E., and Ulloa, J. C. (2016). Severe rock mass damage of undercut and extraction level pillars at El Teniente Mine. Geomechanics Tunn. 9, 529–533. doi:10.1002/geot.201600058
Hidayat, W., Sahara, D. P., Widiyantoro, S., Suharsono, S., Wattimena, R. K., Melati, S., et al. (2022). Testing the utilization of a seismic network outside the main mining facility area for expanding the microseismic monitoring coverage in a deep block caving. Appl. Sci. 12, 7265. doi:10.3390/app12147265
Hu, J. (2022). Instability mode and control technology of goaf group in Xianglu mountain tungsten mine. Beijing, China: University of Science and Technology Beijing.
Koupouli, N. J. F., Belem, T., Rivard, P., and Effenguet, H. (2016). Direct shear tests on cemented paste backfill–rock wall and cemented paste backfill–backfill interfaces. J. Rock Mech. Geotechnical Eng. 8 (04), 472–479. doi:10.1016/j.jrmge.2016.02.001
Krzysztof, S., Gomez, R., Zagorski, K., Zagorska, A., and Gomez-Espina, R. (2022). Review of underground mining methods in world-class base metal deposits: Experiences from Poland and Chile. Energies 16 (1), 148. doi:10.3390/en16010148
Li, S., et al. (2019). Study on the warning signs of earthquake mechanism of mega mountain damage precursors based on moment tensor analysis. Chin. J. Rock Mech. Eng. 38 (10), 2000–2009. doi:10.13722/j.cnki.jrme.2019.0234
Li, Z., Sun, W., Gao, T., Zhao, J., Lu, K., et al. (2023). Experimental study on the evolution of pore structure of inclined layered cemented tailings backfill based on X-ray CT. Constr. Build. Mater., 366. 130242. doi:10.1016/j.conbuildmat.2022.130242
Lu, X. (2022). Study on optimization of mining access parameters of downward slicing and cemented filling method in Jinchuan No. 2 Mining Area. Wuhan, China, Wuhan University of Science and Technology.
Ma, Z. (2022). Test on characteristics of ultra-fine unclassified tailings paste filling materials. Min. Technol. 22 (06), 52–56. doi:10.13828/j.cnki.ckjs.2022.06.038
Meng, L., Zhang, J., Guo, Y., Pu, H., and Peng, Y. (2022). Influence of particle size distribution on fractal characteristics of waste rock backfill materials under compression. J. Mater. Res. Technol. 20, 2977–2989. doi:10.1016/j.jmrt.2022.08.056
Singalreddy, S. P., Cui, L., and Fang, K. (2022). Spatiotemporal evolution of thermo-hydro-mechanical-chemical processes in cemented paste backfill under interfacial loading. Int. J. Min. Sci. Technol. 32 (6), 1207–1217. doi:10.1016/j.ijmst.2022.10.002
Strzałkowski, P. (2021). Sinkhole hazard caused by inactive mining shafts as illustrated by a selected example. Pure Appl. Geophys., 178, 1697-1707. doi:10.1007/s00024-021-02716-z
Tobias, L., Wagner, H., Karlsson, M., Wimmer, M., and Grynienko, M. (2022). Raise caving A hybrid mining method addressing current deep cave mining challenges. BHM Berg Hüttenmännische Monatsh. 167 (2), 177–186. doi:10.1007/s00501-022-01217-3
Víctor, M., Samuel, K., and Marsheal, F. (2022). Mining method selection for extracting moderately deep ore body using analytical hierarchy process at mindola sub-vertical shaft, Zambia. Cogent Eng. 9 (1). doi:10.1080/23311916.2022.2062877
Wang, F., et al. (2003). Unclassified tailings cement filling test and system transformation at Nanjing lead-zinc-silver mine. Metal. Mine 328 (10), 16–17+70. doi:10.3321/j.issn:1001-1250.2003.10.004
Wang, G., et al. (2022). Study on reasonable support parameters of FRP bolt under large volume backfill in Jinchuan No.2 mine. Min. Res. Dev. 42 (01), 100–105. doi:10.13827/j.cnki.kyyk.2022.01.004
Wang, S., et al. (2008). Cemented backfill with unclassified tailings in Nanjing lead-zinc-silver mine. Nonferrous Met. 60 (02), 107–109. doi:10.3969/j.issn.2095-1744.2008.02.026
Wang, W., Cao, G., Li, Y., Zhou, Y., Lu, T., Wang, Y., et al. (2022). Experimental study of dynamic characteristics of tailings with different reconsolidation degrees after liquefaction. Front. Earth Sci. 10, 876401. doi:10.3389/feart.2022.876401
Yu, S., et al. (2021). Principle and application of controllable grouting of cement-water glass slurry in the large bulk loose body of mine collapse. J. Eng. Geol. 29 (04), 1094–1104. doi:10.13544/j.cnki.jeg.2021-0322
Yuan, B., Chen, W., Li, Z., Zhao, J., Luo, Q., Chen, W., et al. (2022). Sustainability of the polymer SH reinforced recycled granite residual soil: Properties, physicochemical mechanism and applications. J. Soils Sediments 228, 246–262. doi:10.1007/s11368-022-03294-w
Yuan, B., Chen, W., Zhao, J., Li, L., Liu, F., Guo, Y., et al. (2022). Addition of alkaline solutions and fibers for the reinforcement of kaolinite-containing granite residual soil. Appl. Clay Sci. 228, 106644. doi:10.1016/j.clay.2022.106644
Zhang, C., et al. (2020). Stability analysis of mining area slip shaft based on BLSS-PE and FLAC3D coupling modeling technology. Nonferrous Metal. Eng. 10 (02), 92–99.
Zhang, Z. (2021). Optimization study of mining method for slowly inclined medium-thick ore body. Xinjiang Nonferrous Met. 44 (04), 45–46. doi:10.16206/j.cnki.65-1136/tg.2021.04.020
Zhao, H., Zhang, Y., and Guo, J. (2013). Monitoring and mechanisms of ground deformation and ground fissures induced by cut-and-fill mining in the Jinchuan Mine 2, China. Environ. Earth Sci. 68 (7), 1903–1911. doi:10.1007/s12665-012-1877-7
Keywords: tailing sand of ultrafine particles, binding materials, geologic hazards, solid waste, sustainable development, backfill materials
Citation: Deng D, Wang Y, Liang Y, Fan J, Gao Y and Ma Y (2023) Strength variation characteristics of waste tailings cemented backfill materials with ultrafine particles. Front. Mater. 10:1166065. doi: 10.3389/fmats.2023.1166065
Received: 15 February 2023; Accepted: 13 March 2023;
Published: 05 April 2023.
Edited by:
Yu-Fei Wu, RMIT University, AustraliaReviewed by:
Bingxiang Yuan, Guangdong University of Technology, ChinaCopyright © 2023 Deng, Wang, Liang, Fan, Gao and Ma. This is an open-access article distributed under the terms of the Creative Commons Attribution License (CC BY). The use, distribution or reproduction in other forums is permitted, provided the original author(s) and the copyright owner(s) are credited and that the original publication in this journal is cited, in accordance with accepted academic practice. No use, distribution or reproduction is permitted which does not comply with these terms.
*Correspondence: Yihua Liang, MjAxNTA2MzFAZ2l0LmVkdS5jbg==
Disclaimer: All claims expressed in this article are solely those of the authors and do not necessarily represent those of their affiliated organizations, or those of the publisher, the editors and the reviewers. Any product that may be evaluated in this article or claim that may be made by its manufacturer is not guaranteed or endorsed by the publisher.
Research integrity at Frontiers
Learn more about the work of our research integrity team to safeguard the quality of each article we publish.